改进报告书模板(8D)
质量问题分析改进报告模板(8D精简版)
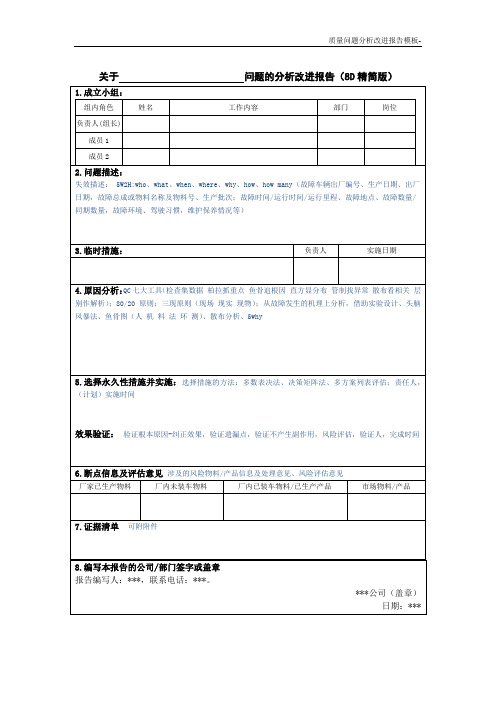
壳体对接处通过人工打胶进行密封,经对生产线壳体装配工位进行跟踪,工艺操作指导书明确了打胶的顺序、标准要求,但仍发现个别物料打胶不连续、胶量忽多忽少,胶枪出胶量难以控制,要求工人有较高的技能。因此确定打胶质量保证能力差是造成壳体对接处密封失效的主要原因。
2018年7月12日接到徐工环境公司反馈我司供应的摄像头,在车辆到市场上使用期间出现多台车摄像头损坏问题。经与徐工环境质量人员王某及服务人员李某进一步落实故障,具体为:
我司在3月16日生产的一批摄像头(物料号:83550996,型号:CQ-SB17-W,批次号:20180316),于4月20日配送20件至徐工环境,后由环境公司装车。其中一批多功能抑尘车于5月8日销售至深圳市场,客户反馈在使用不到1个月内陆续出现累计5台车摄像头损坏问题。经与服务人员落实摄像头位置未发生外部碰撞、车辆电路系统正常,摄像头内部存有大量水珠。
3.临时措施:
负责人
实施日期
4.原因分析:QC七大工具(检查集数据 柏拉抓重点 鱼骨追根因 直方显分布 管制找异常 散布看相关 层别作解析);80/20原则;三现原则(现场 现实 现物);从故障发生的机理上分析,借助实验设计、头脑风暴法、鱼骨图(人 机 料 法 环 测)、散布分析、5why
5.选择永久性措施并实施:选择措施的方法:多数表决法、决策矩阵法、多方案列表评估;责任人,(计划)实施时间
5.选择永久性措施并实施:选择措施的方法:多数表决法、决策矩阵法、多方案列表评估;责任人,(计划)实施时间
经与技术部门沟通,为避免人为操作不一致,更改密封方式,将打胶改为安装防水橡胶圈。经重新设计,在壳体上增加密封圈安装槽,匹配合适大小的密封圈,并进行密封性测试后批量实施。责任人:张三,计划完成时间:***。
完整8D报告模板
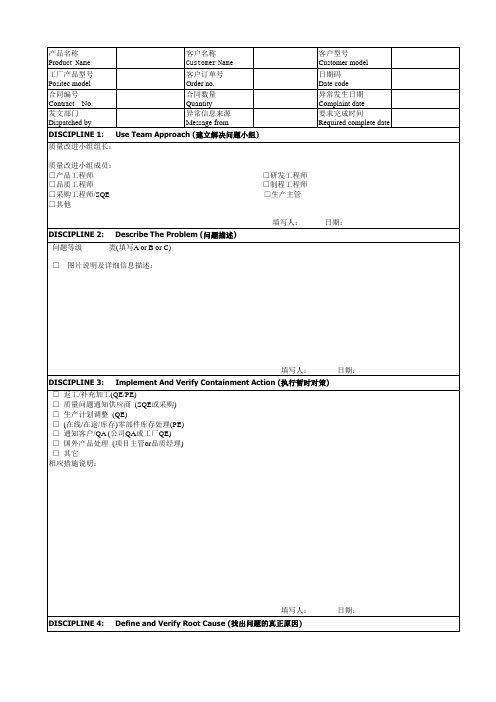
说明:D1-第一步骤: 建立解决问题小组----由品质部召集相关人员若问题无法独立解决,通知你认为有关的人员组成团队。
团队的成员必需有能力执行,例如调整机器或懂得改变制程条件,或能指挥作筛选等。
备注:执行者不列入。
D2-第二步骤: 描述问题----由品质部收集,并向小组人员传达向团队说明何时、何地、发生了什么事、严重程度、目前状态、如何紧急处理、以及展示照片和收集到的证物。
想象你是FBI的办案人员,将证物、细节描述越清楚,团队解决问题将越快。
D3-第三步骤: 执行暂时对策---由小组人员负责执行若真正原因还未找到,暂时用什么方法可以最快地防止问题?如全检、筛选、将自动改为手动、库存清查等。
暂时对策决定后,即立刻交由团队成员带回执行。
备注:为了防止遗漏,纠正措施五要→客户仓库、在途、客户生产线、工厂生产线& 工厂仓库。
D4-第四步骤: 找出问题真正原因----由小组人员讨论后确定找问题真正原因时,最好不要盲目地动手改变目前的生产状态,先动动脑。
您第一件事是要先观察、分析、比较。
列出您所知道的所有生产条件(即鱼骨图),逐一观察,看看是否有些条件走样,还是最近有些什么异动?换了夹具吗?换了作业员?换了供应商?换了运输商?修过电源供应器?流程改过?或比较良品与不良品的检查结果,看看哪个数据有很大的差异?尺寸?重量?电压值?CPK?耐电压?等等不良的发生,总是有原因,资料分析常常可以看出蛛丝马迹。
这样的分析,可以帮助您缩小范围,越来越接近问题核心。
当分析完成,列出您认为最有可能的几项,再逐一动手作些调整改变,并且观察哪些改变可使品质回复正常及影响变异的程度,进而找到问题真正的原因。
这就是著名田口式方法最简单而实际的运用。
D5-第五步骤: 选择永久对策----由小组人员讨论后确定找到造成问题的主要原因后,即可开始拟出对策的方法。
对策的方法也许有好几种,例如修理或更新模具。
试试对可能的选择列出其优缺点,要花多少钱?多少人力?能持续多久? 再对可能的方法作一最佳的选择,并且确认这样的对策方法不会产生其它副作用。
完整8D报告模板
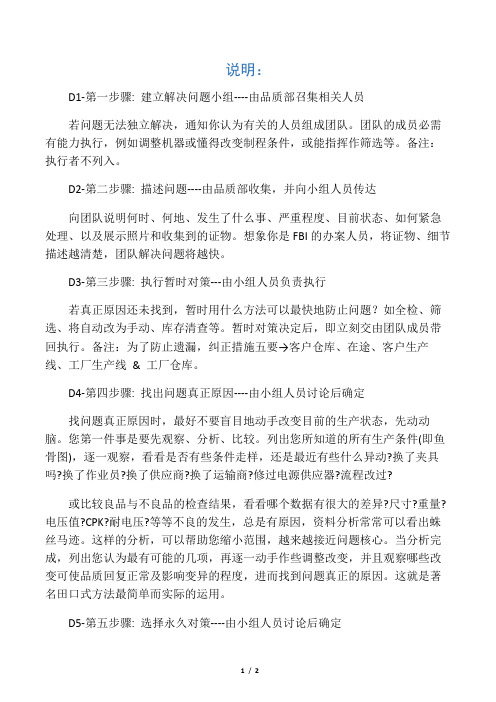
说明:D1-第一步骤: 建立解决问题小组----由品质部召集相关人员若问题无法独立解决,通知你认为有关的人员组成团队。
团队的成员必需有能力执行,例如调整机器或懂得改变制程条件,或能指挥作筛选等。
备注:执行者不列入。
D2-第二步骤: 描述问题----由品质部收集,并向小组人员传达向团队说明何时、何地、发生了什么事、严重程度、目前状态、如何紧急处理、以及展示照片和收集到的证物。
想象你是FBI的办案人员,将证物、细节描述越清楚,团队解决问题将越快。
D3-第三步骤: 执行暂时对策---由小组人员负责执行若真正原因还未找到,暂时用什么方法可以最快地防止问题?如全检、筛选、将自动改为手动、库存清查等。
暂时对策决定后,即立刻交由团队成员带回执行。
备注:为了防止遗漏,纠正措施五要→客户仓库、在途、客户生产线、工厂生产线& 工厂仓库。
D4-第四步骤: 找出问题真正原因----由小组人员讨论后确定找问题真正原因时,最好不要盲目地动手改变目前的生产状态,先动动脑。
您第一件事是要先观察、分析、比较。
列出您所知道的所有生产条件(即鱼骨图),逐一观察,看看是否有些条件走样,还是最近有些什么异动?换了夹具吗?换了作业员?换了供应商?换了运输商?修过电源供应器?流程改过?或比较良品与不良品的检查结果,看看哪个数据有很大的差异?尺寸?重量?电压值?CPK?耐电压?等等不良的发生,总是有原因,资料分析常常可以看出蛛丝马迹。
这样的分析,可以帮助您缩小范围,越来越接近问题核心。
当分析完成,列出您认为最有可能的几项,再逐一动手作些调整改变,并且观察哪些改变可使品质回复正常及影响变异的程度,进而找到问题真正的原因。
这就是著名田口式方法最简单而实际的运用。
D5-第五步骤: 选择永久对策----由小组人员讨论后确定找到造成问题的主要原因后,即可开始拟出对策的方法。
对策的方法也许有好几种,例如修理或更新模具。
试试对可能的选择列出其优缺点,要花多少钱?多少人力?能持续多久? 再对可能的方法作一最佳的选择,并且确认这样的对策方法不会产生其它副作用。
完整8D报告模板
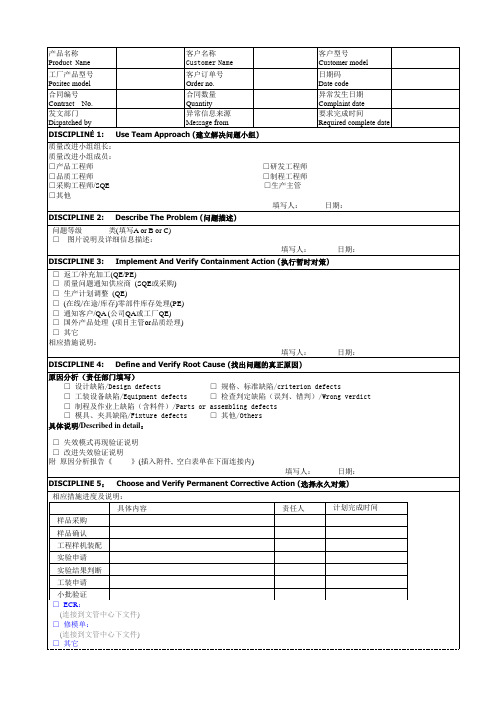
D1-第一步骤: 建立解决问题小组----由品质部召集相关人员若问题无法独立解决,通知你认为有关的人员组成团队。
团队的成员必需有能力执行,例如调整机器或懂得改变制程条件,或能指挥作筛选等。
备注:执行者不列入。
D2-第二步骤: 描述问题----由品质部收集,并向小组人员传达向团队说明何时、何地、发生了什么事、严重程度、目前状态、如何紧急处理、以及展示照片和收集到的证物。
想象你是FBI的办案人员,将证物、细节描述越清楚,团队解决问题将越快。
D3-第三步骤: 执行暂时对策---由小组人员负责执行若真正原因还未找到,暂时用什么方法可以最快地防止问题?如全检、筛选、将自动改为手动、库存清查等。
暂时对策决定后,即立刻交由团队成员带回执行。
备注:为了防止遗漏,纠正措施五要→客户仓库、在途、客户生产线、工厂生产线& 工厂仓库。
D4-第四步骤: 找出问题真正原因----由小组人员讨论后确定找问题真正原因时,最好不要盲目地动手改变目前的生产状态,先动动脑。
您第一件事是要先观察、分析、比较。
列出您所知道的所有生产条件(即鱼骨图),逐一观察,看看是否有些条件走样,还是最近有些什么异动?换了夹具吗?换了作业员?换了供应商?换了运输商?修过电源供应器?流程改过?或比较良品与不良品的检查结果,看看哪个数据有很大的差异?尺寸?重量?电压值?CPK?耐电压?等等不良的发生,总是有原因,资料分析常常可以看出蛛丝马迹。
这样的分析,可以帮助您缩小范围,越来越接近问题核心。
当分析完成,列出您认为最有可能的几项,再逐一动手作些调整改变,并且观察哪些改变可使品质回复正常及影响变异的程度,进而找到问题真正的原因。
这就是着名田口式方法最简单而实际的运用。
D5-第五步骤: 选择永久对策----由小组人员讨论后确定找到造成问题的主要原因后,即可开始拟出对策的方法。
对策的方法也许有好几种,例如修理或更新模具。
试试对可能的选择列出其优缺点,要花多少钱?多少人力?能持续多久? 再对可能的方法作一最佳的选择,并且确认这样的对策方法不会产生其它副作用。
8D报告步骤【范本模板】

8D报告步骤D1-第一步骤: 建立解决问题小组若问题无法独立解决,通知你认为有关的人员组成团队。
团队的成员必需有能力执行,例如调整机器或懂得改变制程条件,或能指挥作筛选等。
D2-第二步骤: 描述问题向团队说明何时、何地、发生了什么事、严重程度、目前状态、如何紧急处理、以及展示照片和收集到的证物。
想象你是FBI的办案人员,将证物、细节描述越清楚,团队解决问题将越快.D3-第三步骤:执行暂时对策若真正原因还未找到,暂时用什么方法可以最快地防止问题?如全检、筛选、将自动改为手动、库存清查等。
暂时对策决定后,即立刻交由团队成员带回执行。
D4-第四步骤: 找出问题真正原因找问题真正原因时,最好不要盲目地动手改变目前的生产状态,先动动脑。
您第一件事是要先观察、分析、比较。
列出您所知道的所有生产条件(即鱼骨图),逐一观察,看看是否有些条件走样,还是最近有些什么异动?换了夹具吗?换了作业员?换了供应商?换了运输商?修过电源供应器?流程改过?或比较良品与不良品的检查结果,看看那个数据有很大的差?,尺寸?重量?电压值?CPK?耐电压?等等不良的发生,总是有原因,资料分析常常可以看出蛛丝马迹。
这样的分析,可以帮助您缩小范围,越来越接近问题核心.当分析完成,列出您认为最有可能的几项,再逐一动手作些调整改变,并且观察那一些改变可使品质回复正常及影响变异的程度,进而找到问题真正的原因.这就是著名田口式方法最简单而实际的运用。
D5—第五步骤: 选择永久对策找到造成问题的主要原因后,即可开始拟出对策的方法.对策的方法也许有好几种,例如修理或更新模具。
试试对可能的选择列出其优缺点,要花多少钱?多少人力?能持续多久?再对可能的方法作一最佳的选择,并且确认这样的对策方法不会产生其它副作用。
D6-第六步骤: 执行及验证永久对策当永久对策准备妥当,则可开始执行及停止暂时对策。
并且对永久对策作一验证,例如观察不良率已由4000 PPM降为300PPM,CPK由0.5升为1.8等,下游工段及客户己能完全接受,不再产生问题。
完整8D报告模板

版本:产品名称Product Name 客户名称Customer Name客户型号Customer model工厂产品型号Positec model 客户订单号Order no.日期码Date code合同编号Contract No. 合同数量Quantity异常发生日期Complaint date发文部门Dispatched by 异常信息来源Message from要求完成时间Required complete dateDISCIPLINE 1: Use Team Approach (建立解决问题小组)质量改进小组组长:质量改进小组成员:□产品工程师_______________________ □研发工程师______________ □品质工程师_______________________ □制程工程师______________ □采购工程师/SQE___________________ □生产主管________________ □其他_____________________________填写人:日期:DISCIPLINE 2: Describe The Problem (问题描述)问题等级______类(填写A or B or C)□图片说明及详细信息描述:填写人:日期:DISCIPLINE 3: Implement And Verify Containment Action (执行暂时对策)□返工/补充加工(QE/PE)□质量问题通知供应商(SQE或采购)□生产计划调整(QE)□(在线/在途/库存)零部件库存处理(PE)□通知客户/QA (公司QA或工厂QE)□国外产品处理(项目主管or品质经理)□其它相应措施说明:填写人:日期:版本:DISCIPLINE 4: Define and Verify Root Cause (找出问题的真正原因)原因分析(责任部门填写)□设计缺陷/Design defects □规格、标准缺陷/criterion defects□工装设备缺陷/Equipment defects □检查判定缺陷(误判、错判)/Wrong verdict□制程及作业上缺陷(含料件)/Parts or assembling defects□模具、夹具缺陷/Fixture defects □其他/Others具体说明/Described in detail:□失效模式再现验证说明□改进失效验证说明附原因分析报告《》(插入附件, 空白表单在下面连接内)填写人:日期:DISCIPLINE 5:Choose and Verify Permanent Corrective Action (选择永久对策)相应措施进度及说明:具体内容责任人计划完成时间样品采购样品确认工程样机装配实验申请实验结果判断工装申请小批验证□ECR:(连接到文管中心下文件)□修模单:(连接到文管中心下文件)□其它填写人:日期:DISCIPLINE 6: Implement Permanent Corrective Action (执行及验证永久对策)□品质标准(品质人员提供,需明确清晰):□正向模式验证:□反向失效模式验证:实际完成情况确认人实际完成时间样品采购样品确认工程样机装配实验申请实验结果判断工装申请小批验证(工程人员提供正/反验证需包含详细数据,如实验申请号,验证结果等.)(品质)填写人:日期:(工程)填写人:日期:DISCIPLINE 7: Prevent Recurrence & Standardization (防止再发生措施及标准化)版本:产品工程师PE:□ECN□BOM□PQC检指/培训□IQC检指/培训制程工程师:□总装工艺卡/装配人员培训品质工程师QE:□FQC检指/培训采购部SQE:□供应商培训□供应商检指□供应商检具□供应商工艺□供应商库存处理其它填写人:日期:DISCIPLINE 8: Congratulate Our Team (批量验证/团队激励)改善情况的追踪:□ECN□BOM□供应商培训□供应商检指□供应商检具□供应商工艺□供应商库存处理□IQC检指/检验结果□PQC检指/检验结果□FQC检指/检验结果□总装工艺卡□试验/检验考核结果填写人:日期:经办/drafted by: 部门审核/checked by: 品质经理审核: 批准/Approved by:一、QC培训记录二、QC检指记录三、供应商方面培训、检(插入相关支持文件)指、检具、工艺、协议记录四、工艺文件备注:1.对异常问题或改进状态的描述要尽量有图片说明或详细的信息记录。
8D报告模板
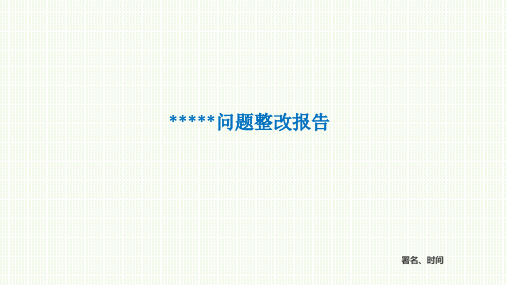
D2:问题描述
问题接收时间: 问题发现部门/人: 问题如何发现的:
零件名称: 零件号:
发生了什么问题? 为什么是个问题?
NG图片
问题发生时间: 问题发现位置:
故障数量: 故障批次: 顾客名称: 问题描述
OK图片
要点:D2
1、问题描述按表格内容填写,越是详细、准确对解决 问题越有帮助; 2、“发生了什么问题?”要使用最简单,并通俗易懂 样件等)对比的差异; 4、要有故障件/合格件对比图片。
写本次问题处理个人认为做的不 足的方面
D6:实施永久纠正措施——实施进度
鱼骨编号
实施进度
实际完成 时间
实施证据
计划断点时 间
1
3 4
D6:实施永久纠正措施——跟踪
1) 临时措施实施效果
2) 永久措施是否按计划实施 3) 永久措施实施效果
故障数量
2.5 2
1.5 1
0.5 0
投诉时间 遏制措施 临时措施 永久措施
11-16
11-19
11-22
原因分析后必须重新评估临时措施的有效性
D5:选择和验证永久纠正措施
鱼骨编号 问题点
计划实施措施
1
责任人
计划完成期 限
3 4
要点:D5
1、每一条原因对应制定一条有效的措施,不能多也不 能少(措施少了,说明潜在风险未被排除,措施多了, 说明原因没分析到位);
2、尽量考虑机械自动防呆、自动检测等,不接受只有 培训、考核员工的措施;
外检站封样件
装配线封样件 供应商封样件 缺陷警示卡
其他 名称
是否改善
要点:D7
1、针对本次质量问题,找出同类的产品/工序等,筛 选出同样可能出现此问题的,按相同的思路进行整改; 2、固化文件,保留变更记录。
质量8d报告完整版范文(汇总14篇)

质量8d报告完整版范文(汇总14篇)通过对不同的纠正措施定量化的试验筛选出纠正措施,依据风险评估,确定必要时的应急措施。
而解决问题的方案应确保可以保持长期效果。
曾经看到供应商的8D报告中该D5里面一排七行整齐的出现7句“加强’,加强工人培训,加强巡检次数,加强督察力度,加强过程控制---空话一堆。
加强到什么程度没有量化。
具体方案都写具体,数据说话,比如原来检验频次10个检1个,现在加强到5个检1个;同样的加强培训,原来培训次数多少,现在培训计划附在这里,这样我们的对策才有支撑。
质量8d报告完整版范文最新第2篇D1:建立所需的团队应该是多功能覆盖所需的所有布门的参与。
我们的D1包括QC、工程、项目的代表,制造和采购。
D2:问题描述成型零件,显示不可接受的水平周围的顶布边缘周围的损坏,由于热暴露。
我们包括照片的问题,有效的说明维生素D3:临时措施1。
客户已经有布分100%的检验检疫发现有缺陷的布件。
2。
生产现场有100%检查所有布件库存,并隔离任何有缺陷的零件D4:根本原因分析在试图纠正一个不同的问题,成型参数进行了调整,导致收缩的增加。
略小的布分意味着随后的过程中损坏的布分。
加上一个无效的操作人员的培训和遏制站上的指令意味着该问题没有被拾起和不合格的布分已被允许进入客户。
D5:实现PCA(永久性纠正措施)调整模具参数以控制零件收缩。
实现增加零件整体尺寸检测和SPC。
监控记录。
在随后的操作中执行100%检查损坏发生的地方实施控制和遏制措施高兴提高操作人员的培训D6:实施并验证PCA状态的日期的主成分分析已经实施。
主成分分析的验证是对SPC数据分析的形式来检查布分的变化(收缩率)和检查的遏制记录检查,看看是否问题再次被注意到。
D7:防止再发生我们已经简单地保持控制实施的主成分分析,但降低检查频率的控制计划D8:最后的小组讨论/评论回顾主成分分析过程中收集的数据和调查的方式,这种错误可以避免在未来。
PFMEA更新符合本时使用的类似产品进行产品实现过程。
完整8D报告模板
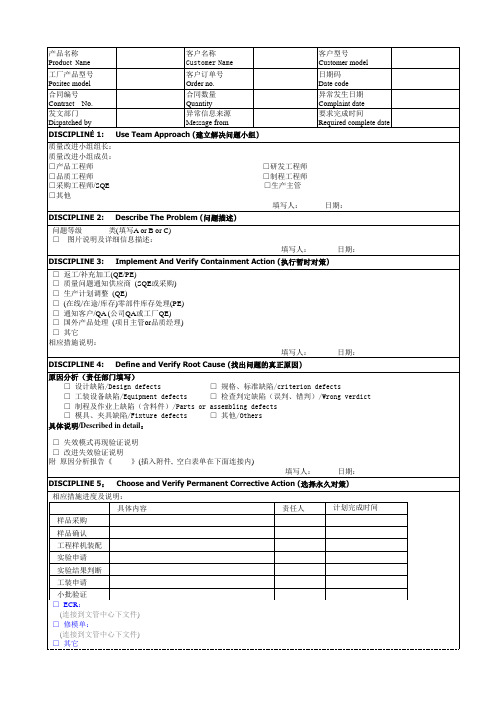
D1-第一步骤: 建立解决问题小组----由品质部召集相关人员若问题无法独立解决,通知你认为有关的人员组成团队。
团队的成员必需有能力执行,例如调整机器或懂得改变制程条件,或能指挥作筛选等。
备注:执行者不列入。
D2-第二步骤: 描述问题----由品质部收集,并向小组人员传达向团队说明何时、何地、发生了什么事、严重程度、目前状态、如何紧急处理、以及展示照片和收集到的证物。
想象你是FBI的办案人员,将证物、细节描述越清楚,团队解决问题将越快。
D3-第三步骤: 执行暂时对策---由小组人员负责执行若真正原因还未找到,暂时用什么方法可以最快地防止问题?如全检、筛选、将自动改为手动、库存清查等。
暂时对策决定后,即立刻交由团队成员带回执行。
备注:为了防止遗漏,纠正措施五要→客户仓库、在途、客户生产线、工厂生产线& 工厂仓库。
D4-第四步骤: 找出问题真正原因----由小组人员讨论后确定找问题真正原因时,最好不要盲目地动手改变目前的生产状态,先动动脑。
您第一件事是要先观察、分析、比较。
列出您所知道的所有生产条件(即鱼骨图),逐一观察,看看是否有些条件走样,还是最近有些什么异动?换了夹具吗?换了作业员?换了供应商?换了运输商?修过电源供应器?流程改过?或比较良品与不良品的检查结果,看看哪个数据有很大的差异?尺寸?重量?电压值?CPK?耐电压?等等不良的发生,总是有原因,资料分析常常可以看出蛛丝马迹。
这样的分析,可以帮助您缩小范围,越来越接近问题核心。
当分析完成,列出您认为最有可能的几项,再逐一动手作些调整改变,并且观察哪些改变可使品质回复正常及影响变异的程度,进而找到问题真正的原因。
这就是着名田口式方法最简单而实际的运用。
D5-第五步骤: 选择永久对策----由小组人员讨论后确定找到造成问题的主要原因后,即可开始拟出对策的方法。
对策的方法也许有好几种,例如修理或更新模具。
试试对可能的选择列出其优缺点,要花多少钱?多少人力?能持续多久? 再对可能的方法作一最佳的选择,并且确认这样的对策方法不会产生其它副作用。
8D纠正预防措施报告

纠正预防改进报告(8Disciplines报告)
TO:为华公司制品(过程)最终产品
FROM:雄润公司发出部门:品质部
CC:雄润业务/陈经理发出日期:2011/11/24
D1.组织团队:D2:问题描述或潜在的问题描述:
团队领导者:
品质部:胡奎制造部:宋臻琦:客户投诉盖子有批锋/涂层掉皮/断裂现象
4.每批出货QA都需做酒精擦拭及百格测试,此批在测试时未发现有涂层脱落现象。
D5.采取永久措施:
针对掉皮现象我司在喷油烘烤取出后放置4小时再装胶袋。
3.在每日早会上对作业员进行品质意识宣导,以提升品质意识。
4.严格要求作业人员按照作业指导书要求进行作业。
表单编号:XR-FOR-Q031-A/0
5.检验员在检验时,由之前单次抽样检验改为加严检验。
确认日期:
2011/11/24
D6.验证措施:
1.用改良后的治具进行喷油,连续喷2000PCS未发现有批锋现象。
2.经对作业人员宣导后,有严格按照SOP要求作业且品质意识有明显提升,检验时未发现有断裂现象。
3.现生产的每批次取3PCS进行百格测试和酒精擦拭,未发现有掉皮现象。(建议:贵司在检测涂层符著力时不可用指甲刮,应该通过百格测试及酒精擦拭来判断。)
执行日期:
2011/11/24
D7.预防再发生(实施总结)
1.针对贵司投诉的此类问题点,我司专门指派操作熟练及工作认真之作业员进行作业。
2.生产部门每日在早会上对作业员进行品质意识宣导。
3.品质部将对此问题点进行重点跟踪管控。
执行日期:
2011/11/24
D8.跟进结果:YESNO
关闭时间:
2011/11/30
8D改善案例措施报告

8D改善案例措施报告包装方式8D实施步聚1WK2WKD1主题选定与问题描述√D2紧急处理与目标设定√D3问题现状分析√√D4初步原因分析与验证√D5根本原因分析与对策√D6效果确认D7防呆及标准化D8水平展开(结案)D1:改善主题选定与问题描述问题描述:what:挡板断裂包装不良D1:问题定义who:pet储运how many:2次D2:紧急处置与目标设定发生中:挡板折断未发生:反馈生产,质量,注意避免发生类式挡板折断现象已发生:薄膜损失处理,重新改包target避免不良再次发生(改善)预计完成时间:8周D3:现状分析现状分析,数据收集(5w2h管理,鱼骨图类)5WHY分析挡板折断鱼骨图分析5W2H分析1挡板质量跟踪原辅材检验和成品检验包装方式合理性控制流程管理材料质量改善包装方式合理化从以上可以看出,挡板质量,质量管理和包装方法改善的原因是最多的D4:初步原因分析与验证;拟定执行暂时对策找出有可能原因:不良缺陷可能原因出现频次-暂定加强对供应商管理和监督2浙江南洋科技股份序号工作项目(what 做什么,什么事,实现功能时产生什么,具备什么,要求)现状及问题(why为什么要这样做,为什么产生这个问题,目的)加强对来料检验和厂内成品检验过程2加强人员培训和监督作用2制定包装作业指导书,形成一套流程2打包方式采用井字形打法3更换30mm厚锯末挡板1叉车人员技术提高1铁架包装方式1可能原因可能原因。
14一。
现场稽查二。
业务流程审查发现问题确认主因:消除法不良缺陷挡板断裂可能原因加强对供应商管理和监督加强对来料检验和厂内成品检验过程加强人员培训和监督作用制定包装作业指导书,形成一套流程15% 14% 14% 14%22% 7%7%7% 原因出现概率分析加强对供应商管理和监督加强对来料检验和厂内成品检验过程加强人员培训和监督作用制定包装作业指导书,形成一套流程打包方式采用井字形打法更换30mm 厚锯末挡板方式8D实施3WK1WK1WK√√√√when:2018/8/25 where:PET二线how much:6033元+9800 挡板折断现象预计完成日期2018/9/25主负责人协办人2018.08.25-2018.09.25PET4车间 1.采购明确质量要求2.质检加强材料检验和成品检验3.合理选择供应商4.搞好质量保证工作5.包装方法的准确性和合理化G F 挡板折断避免发生良率良率累计14.2857142914.28571429技股份有限公司5W2H法完成时间(when 什么时候产生问题,何时完成)启动地点(where 什么地点产生,在何处产生问题,在哪里做)实施方法/措施(how 如何才能更好使用该产品,怎样才能充分利用,怎么做)负责人(who 谁产生,谁使预期目标(how much,how many 做到什么程度,效。
8D报告模板及实例

完成时间:2014-6-13
完成情况:已完成 完成情况:进行中
什
对
发现此问题前,产品成品检验方式为检具测量,由于产品不良问题点基本在产品冲扁部位中段,而检具检
验不能够保证100%测量到中段部位。中间不良,两头尺寸合格的不良品,照样能通过检具检验,所以无法 对包装检验人员进行测量指导,减少检具厚度,使检具能够测量到产品冲扁部位中段,有效的检验出中段尺寸不合格的不良品,另
备注
发现时间 XXX 发现人员 客户IQC 发现地点 客户进料区
类别 普通□ 较重□ 严重□ 缺陷图片:
说 --48小时无结果 72小时无结果
明 首次发生 重复发生
三次以上发生
管理层支持
部门经理
厂长 总/副总经
理
顾客现场
2400
现场挑选不良品
XXX
已完成
成品库
1955
调出库存,返工卡尺全检
XXX
已完成
2.冲边:改前:3.2 ,改后:3.2+0.08/-0.05 ;
3.冲孔:改前:3.2 ,改后:3.2±0.08
; 更改冲边,冲孔公差,弥补产品在冲边,冲孔过程中减少的厚度差,对产品
生
签
XXX
加工过程进行监督测量,避免不良影响,减少不良品的产生。 责任人:XXX 完成时间:2014-6-13 完成情况:进行中
XXX
货,并在外箱标示“已全检”
XXX
2014/6/6 进行中
XXX
D4.
(4 D5.
(4
根为 什
8小 1.为保证提升检具通过率,减少冲边模损耗故首件尺生产时调机按照为公差的中下限进行调整,下限公差 在生产过程中出现偏差。
确 针
8D报告-模板

不良发生地点SQ 影响主方案件主 题供 方供方代码零件名称物料编码/规格开启日期不良等级A 1件总装零件批次整改目标不再发生D1-建立小组D2-问题描述:姓名职务电话E-mail D3-临时纠正措施临时纠正遏制措施排查/挑选点总数不良数实施措施客户端筛查安排人员对总装工序件、生产区域焊装线边在途、库存D4-根本原因和流出原因根本原因:(采用5Why方式)实施者分析日期1why为什么 OP40模具切边刃口在出现缺损情况,产线停机修复时(需要把模具取出,到返修区进行维修),操作者误将OP30工序件从模具内取出,没有检查孔数数量就放入OP40中,导致漏工序零件流入下工序;2why为什么 《冲压全检作业指导书》中未要求产品下线时对孔数数量进行检查(重点检查流水槽外观);3why为什么 胶条安装时,操作者重点确认胶条安装位置和粘贴情况,未对孔数进行确认;流出原因:(采用5Why方式)1why 为什么 没有快速全检识别重要孔,导致未冲孔不合格件流出2why 为什么 重点确认胶条安装位置和粘贴情况,未对孔数进行确认;D5/D6-永久纠正措施的提出和实施永久纠正措施方案验证日期计划实施日期计划完成日实施者在《异常处理流程》中增加异常停机时,要求模具内不放工序件,如果已经放入工序件的需要本工位操作者自己取出,不能由下工序操作者取出,并对操作者进行培训;更新《冲压全检作业指导书》,增加产品下线时,孔数数量的检查(对孔进行贯穿式划记)规定;D7-永久纠正措施效果确认:供应商(包括备库)不良现象描述:2022年7月号上午10:15左右,总装操作者在装配过程中,发现我司目箱流水槽左(451A07-AF)孔未冲穿1例;缺陷图片:8D报告分析过程描述:外径小或者大,无法合理装配整改前制品数量措施方案验证实施时间实施者断点时间DO 应急性措施:产品下线后和后工序装胶条时,操作者该孔进行贯穿式划记检查;性能功能外观尺寸其它。
中文8D报告模板

XT
(1)
(2)原始缺陷照片
是否具体
责任2.遏
分类
可能存在的数
量
区域确认人可疑品发现的数量可疑品处置确认人
供应商
原料在制品完成品在途公司内部
原材料库实验室现场在制品返工区待入库区成品库装箱区已出库
在途
纠正/预防措施表(8D报告) A/0
1.不合格现象/趋势描述:产品名称(产品代码)缺陷现象发现时间?缺陷数量/比例?
缺陷产品批次号谁发现此缺陷?哪里发现?(具体工位)是否
责任部门/责任人:
完成日期:
责任
部
门
/
责
任
人:
完成日期:责任部门/责任人:完成日期:
8.水平展开情况:
责任部门/责任人:
完成日期:
SQ E :
6. 涉及需更改的文件:
7. 效果验证(包括措施有效性、文件化等,按限制时间进行效果验证,如有,后附证明资料):
同类产品排查
相关文件/台帐更新
其它
建立/进入经验教训库工艺流程图
FMEA 控制计划工艺单
订货技术要求标准作业指导书设备文件产品标识方法搬运操作规程检验计划
包装作业指导书检具操作说明
其它文件及记录。
完整8D报告模板
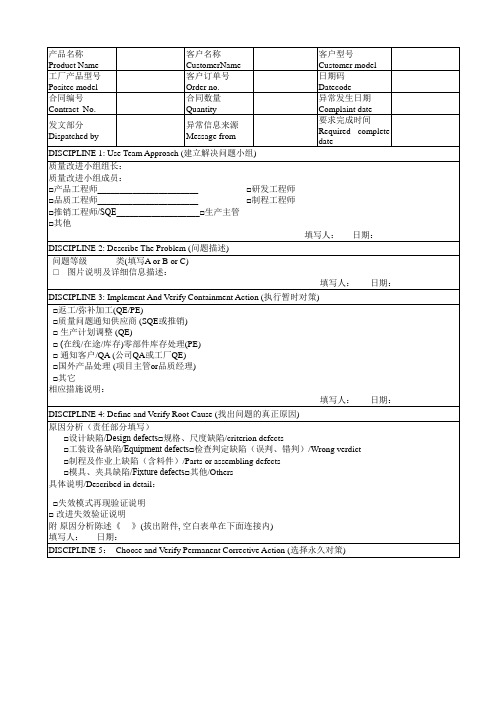
D1第一步调: 建立解决问题小组由品质部召集相关人员若问题无法独立解决,通知你认为有关的人员组成团队。
团队的成员必须有能力执行,例如调整机器或懂得改变制程条件,或能指挥作筛选等。
备注:执行者不列入。
D2第二步调: 描述问题由品质部收集,并向小组人员传达向团队说明何时、何地、发生了什么事、严重程度、目前状态、如何紧急处理、以及展示照片和收集到的证物。
想象你是FBI的办案人员,将证物、细节描述越清楚,团队解决问题将越快。
D3第三步调: 执行暂时对策由小组人员负责执行若真正原因还未找到,暂时用什么方法可以最快地防止问题?如全检、筛选、将自动改为手动、库存清查等。
暂时对策决定后,即立刻交由团队成员带回执行。
备注:为了防止遗漏,纠正措施五要→客户仓库、在途、客户生产线、工厂生产线 & 工厂仓库。
D4第四步调: 找出问题真正原因由小组人员讨论后确定找问题真正原因时,最好不要盲目地动手改变目前的生产状态,先动动脑。
您第一件事是要先观察、分析、比较。
列出您所知道的所有生产条件(即鱼骨图),逐一观察,看看是否有些条件走样,还是最近有些什么异动?换了夹具吗?换了作业员?换了供应商?换了运输商?修过电源供应器?流程改过?或比较良品与不良品的检查结果,看看哪个数据有很大的差别?尺寸?重量?电压值?CPK?耐电压?等等不良的发生,总是有原因,资料分析经常可以看出蛛丝马迹。
这样的分析,可以帮忙您缩小范围,越来越接近问题核心。
当分析完成,列出您认为最有可能的几项,再逐一动手作些调整改变,而且观察哪些改变可使品质回复正常及影响变异的程度,进而找到问题真正的原因。
这就是著名田口式方法最简单而实际的运用。
D5第五步调: 选择永久对策由小组人员讨论后确定找到造成问题的主要原因后,即可开始拟出对策的方法。
对策的方法也许有好几种,例如修理或更新模具。
试试对可能的选择列出其优缺点,要花多少钱?多少人力?能持续多久? 再对可能的方法作一最佳的选择,而且确认这样的对策方法不会发生其它副作用。
完整8D报告模板---精品模板

说明:版本:D1-第一步骤: 建立解决问题小组-——-由品质部召集相关人员若问题无法独立解决,通知你认为有关的人员组成团队.团队的成员必需有能力执行,例如调整机器或懂得改变制程条件,或能指挥作筛选等。
备注:执行者不列入。
D2-第二步骤: 描述问题——-—由品质部收集,并向小组人员传达向团队说明何时、何地、发生了什么事、严重程度、目前状态、如何紧急处理、以及展示照片和收集到的证物。
想象你是FBI的办案人员,将证物、细节描述越清楚,团队解决问题将越快.D3—第三步骤: 执行暂时对策—--由小组人员负责执行若真正原因还未找到,暂时用什么方法可以最快地防止问题?如全检、筛选、将自动改为手动、库存清查等.暂时对策决定后,即立刻交由团队成员带回执行。
备注:为了防止遗漏,纠正措施五要→客户仓库、在途、客户生产线、工厂生产线& 工厂仓库。
D4—第四步骤: 找出问题真正原因-——-由小组人员讨论后确定找问题真正原因时,最好不要盲目地动手改变目前的生产状态,先动动脑.您第一件事是要先观察、分析、比较。
列出您所知道的所有生产条件(即鱼骨图),逐一观察,看看是否有些条件走样,还是最近有些什么异动?换了夹具吗?换了作业员?换了供应商?换了运输商?修过电源供应器?流程改过?或比较良品与不良品的检查结果,看看哪个数据有很大的差异?尺寸?重量?电压值?CPK?耐电压?等等不良的发生,总是有原因,资料分析常常可以看出蛛丝马迹。
这样的分析,可以帮助您缩小范围,越来越接近问题核心。
当分析完成,列出您认为最有可能的几项,再逐一动手作些调整改变,并且观察哪些改变可使品质回复正常及影响变异的程度,进而找到问题真正的原因。
这就是著名田口式方法最简单而实际的运用。
D5-第五步骤: 选择永久对策—-—-由小组人员讨论后确定找到造成问题的主要原因后,即可开始拟出对策的方法。
对策的方法也许有好几种,例如修理或更新模具。
试试对可能的选择列出其优缺点,要花多少钱?多少人力?能持续多久?再对可能的方法作一最佳的选择,并且确认这样的对策方法不会产生其它副作用。
8D报告格式

DISCIPLINE 4:Define and Verify Root Cause (定义及验证根本原因)
担当者(Executed by):执行日期(Effective Date):
DISCIPLINE 5:Permanent Corrective Action (纠正措施)
作成
(Maker)
DISCIPLINE 8:Closure结案
Judgement: (判定)
□Accept
(接受)
□Reject
(退回)
Person incharge(责任人)
Checked
(审核)
Approved
(核准)
Conclusion:(结案描述)
Actual close date:(实际结案日)
Attached documents(附檔):□Yes□No
表单编号:XXX-XX-001版本:A/0
DISCIPLINE 7:Recurrence Prevention & Standardization (预防再发及标准化)
是否修改相關文件□Yes□QC工程图□SOP□承认书□其它
□No
担当者(Executed by):执行日期(Effective Date):
核准(Approved)
审核
(Check)
8 Discipline Report
客户名称Hale Waihona Puke Customer):交货数
(P/O ntity):
编号
Report No.
料号
(Part No):
不良数
(DefectiveQuantity):
- 1、下载文档前请自行甄别文档内容的完整性,平台不提供额外的编辑、内容补充、找答案等附加服务。
- 2、"仅部分预览"的文档,不可在线预览部分如存在完整性等问题,可反馈申请退款(可完整预览的文档不适用该条件!)。
- 3、如文档侵犯您的权益,请联系客服反馈,我们会尽快为您处理(人工客服工作时间:9:00-18:30)。
□1个工作日
产品编码 检查数量
LOT NO.
□3个工作日
问题描述
□1周
发生时间
不良数量
□2周
□1个月以
填写 发生工序
不良率
□1个月以上
日期
不良现象
不良严重程度 致命:
□
主缺: □ 次缺:
□
围堵措施
填写
日期
确认根本原因 短期对策
填写 填写
日期 不良原因分类:
设 □结构 计 □硬件 问 题 □软件 □ 部品质量 □ 总装工艺 □ 贴片工艺 □ 作业原因 □ 客服原因
日期
Discipline 6
长期对策
填写
日期
Discipline 7 Discipline 8
效果验证 CHECKLIST及相应培训
填写 填写
日期 日期
产品名 称: Discipline 1 参与部门 团队成员 计划完成时间 Discipline 2
故障描述
Discipline 3 行动 一 行动 二
Discipline 4
Discipline 5
改进报告书
REV:A2
□产品质量 □部品质量 □生产异常
编号:
团队组成
日期
组长:PE □ QE □ SMT □ IQC □ 生产 □ 供应商 □ 装配 □ ____