模具CAM实训报告
实习报告记录(共7篇)

实习报告记录(共7篇)CAD/CAM , ( .puter Aided Design )计算机辅助设计和(.puter Aided Manuf acturing )计算机辅助制造技术,是近些年出现的一种高效的先进工业生产技术,随着计算机技术的飞跃发展,近十多年来一些先进国家的模具制造行业,己广泛采用NC 和 .C 机床来加工模具,以提高模具精度和生产效率,在当前以信息工业为核心的新工业的兴起过程中,CAD/CAM 技术己成为新一代生产技术的核心,是实现自动化集成制造系统(CIMS)不可缺少的主要技术发展阶段。
1.CAD/CAM 的发展过程CAD/CAM 技术从出现到现在己经发展了50 多年了,无论是硬件技术还是软件技术都发生了很大的大变化,总的来说先后经历了三个阶段。
1.1单元技术的发展和应用阶段在这一阶段,分别针对一些特殊的应用领域开展了计算机辅助设计,分析,工艺,制造等单一功能的开发及应用,这些系统的通用性17差,应用不普及,系统之间的数据结构不统一,出现信息孤岛现象,系统之间不能进行数据交换。
1.2 CAD/CAM 集成阶段随着一些专业系统的应用普及,出现了通用的CAD/CAM 系统,而且系统的功能迅速增强,列如CAD 系统迅速从二维绘图发展到三维建模。
特征造型,参数化设计等先进技术被CAD 系统普遍采用,继而CAD, CAE, CAPP, CAM 系统实现集成或数据交换标准化,CAD/CAM 的应用取得显著成就。
l.3 C I M S技术推广应用阶段计算机技术除了在设计制造等领域截获与深入应用同时,几乎在企业生产的各个领域都获得应用,由于企业的开发活动与企业的其他经营活动是密切相关的,因此要求CAD/CAM 等计算机辅助系统与计算机管理系统实现进行信息交流,把正确的信息传递给正确的地方,这是一个高层次的企业内的信息集成,就是所谓的计算机集成应用系统。
1.4 我国CAD I CAM 技术的发展现状我国CAD/CAM 技术的开发应用水平与发达国家相比还有相当大的差距,我国的CAD I CAM 技术的开发是在7 0 年代末开始的,到目前为止先后通过国家有关部门进行鉴定的有 1 9 8 4 年华中工学院开发的精冲模CAD I CAM 系统,1985 年北京机电研究院开发的冲裁模CAD/CAM 系统,吉林大学开发的棍锻模和锤锻模CAD I CAM 系统,1 9 8 6 年华中工学院开发的冷冲模CAD/CAM 系统和上海交通大学模18具研究所开发的冷冲模CAD I CAM 系统,1 9 8 8 年华中工学院开发的塑压模CAD 系统等。
cam实训报告
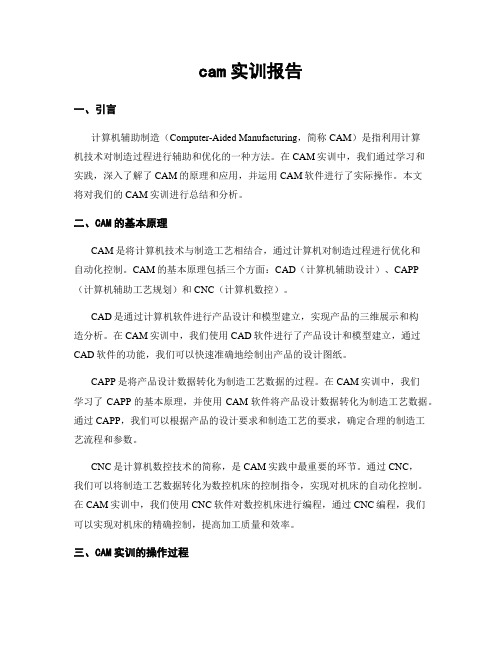
cam实训报告一、引言计算机辅助制造(Computer-Aided Manufacturing,简称CAM)是指利用计算机技术对制造过程进行辅助和优化的一种方法。
在CAM实训中,我们通过学习和实践,深入了解了CAM的原理和应用,并运用CAM软件进行了实际操作。
本文将对我们的CAM实训进行总结和分析。
二、CAM的基本原理CAM是将计算机技术与制造工艺相结合,通过计算机对制造过程进行优化和自动化控制。
CAM的基本原理包括三个方面:CAD(计算机辅助设计)、CAPP (计算机辅助工艺规划)和CNC(计算机数控)。
CAD是通过计算机软件进行产品设计和模型建立,实现产品的三维展示和构造分析。
在CAM实训中,我们使用CAD软件进行了产品设计和模型建立,通过CAD软件的功能,我们可以快速准确地绘制出产品的设计图纸。
CAPP是将产品设计数据转化为制造工艺数据的过程。
在CAM实训中,我们学习了CAPP的基本原理,并使用CAM软件将产品设计数据转化为制造工艺数据。
通过CAPP,我们可以根据产品的设计要求和制造工艺的要求,确定合理的制造工艺流程和参数。
CNC是计算机数控技术的简称,是CAM实践中最重要的环节。
通过CNC,我们可以将制造工艺数据转化为数控机床的控制指令,实现对机床的自动化控制。
在CAM实训中,我们使用CNC软件对数控机床进行编程,通过CNC编程,我们可以实现对机床的精确控制,提高加工质量和效率。
三、CAM实训的操作过程CAM实训的操作过程主要包括产品设计、工艺规划和数控编程。
在实际操作中,我们按照以下步骤进行:1. 产品设计:首先,我们使用CAD软件进行产品的三维建模和设计。
通过CAD软件的绘图功能,我们可以绘制出产品的外形和内部结构,并对产品进行构造分析和优化设计。
2. 工艺规划:在产品设计完成后,我们使用CAM软件进行工艺规划。
通过CAM软件的功能,我们可以将产品的设计数据转化为制造工艺数据,并确定合理的工艺流程和参数。
cam实训报告
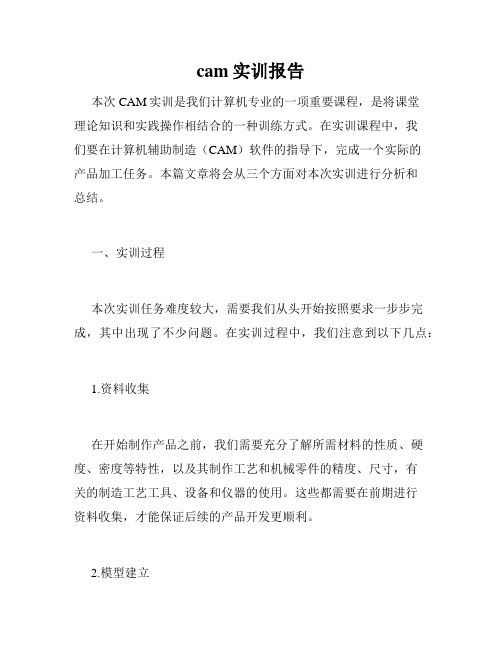
cam实训报告本次CAM实训是我们计算机专业的一项重要课程,是将课堂理论知识和实践操作相结合的一种训练方式。
在实训课程中,我们要在计算机辅助制造(CAM)软件的指导下,完成一个实际的产品加工任务。
本篇文章将会从三个方面对本次实训进行分析和总结。
一、实训过程本次实训任务难度较大,需要我们从头开始按照要求一步步完成,其中出现了不少问题。
在实训过程中,我们注意到以下几点:1.资料收集在开始制作产品之前,我们需要充分了解所需材料的性质、硬度、密度等特性,以及其制作工艺和机械零件的精度、尺寸,有关的制造工艺工具、设备和仪器的使用。
这些都需要在前期进行资料收集,才能保证后续的产品开发更顺利。
2.模型建立根据制作的产品要求,我们需要利用CAD软件进行模型建立。
在实际操作中,由于我们掌握了一定的基础知识和使用技巧,这一环节比较顺利,基本做到了精度和尺寸的控制。
3.加工路径规划和仿真路径规划对于整个实训过程非常重要,这是将CAD图纸转化为机床上加工参数的过程。
在规划路径时,需要根据实际情况考虑工件的方向、刀具的形状、尺寸等,否则可能会导致无法正确加工、损坏机床或刀具,影响产品的质量。
在路径规划完成后,需要进行仿真,通过模拟机床加工进行预估,以保证加工过程可行并且提高效率。
二、团队协作本次实训是以团队形式完成的,团队成员之间需要进行有效的通信和协作,以确保产品的按时完成。
在实训中,我们发现能与团队中人员直接进行有效的沟通能够提高生产效率。
同时,我们也学习到了聆听他人意见的重要性,哪怕是别人的想法与自己的不同,也应该认真考虑和尝试。
这能够使团队成员的工作更协调和高效,帮助我们达成共同目标。
三、技能提高本次CAM实训让我们有机会学习和使用了各种机械切削工具,同时,掌握了CAM软件的基本操作和加工路径的规划。
在实际操作中,我们也发现,学习CAM对于我们日后的职业生涯发展具有非常重要的意义。
在这个时代,CAM技术的广泛应用已经深刻影响了人类的生产和制造方式,而这种技术会在未来更广泛地应用于汽车、医疗、玩具、航空和机械等众多行业,具有非常大的市场前景。
模具CAM模拟仿真加工实习实训报告

模具 CAM 模拟仿真加工实习实训报告一、试验目的1、学习把握 CAITA 模具设计模块并学会用不同软件进展磨具设计。
2、学会用 CAITA 软件进展简洁的磨具设计过程和模拟加工过程。
3、进一步稳固模具构造及制造工艺方面的学问,提高模具设计力量,并提高自己的学习力量。
二、试验内容1.生疏 CAITA 软件的使用过程生疏绘图界面各个工具的使用,能够娴熟使用并进展操作。
1)翻开CAITA 软件,利用鼠标中键和左键或右键进展旋转,缩放和移动,生疏绘图界面工具的使用2)点击草绘进入界面,进展简洁零件的设计并在设计过程中学习各种工具的使用➢在翻开的 CAITA 软件上从菜单栏选择【开头】| 【机械设计】 |【零件设计】命令,弹出|【建零部件】对话框,设置好对话框按|【确定】按钮即可进入零件设计平台➢在草绘界面上会看到很多零件设计常用的工具栏有:基于草图特征工具栏、修饰特征工具栏、参考元素工具栏、基于曲面特征、转换特征、等。
通过【基于草图特征】工具栏上的【填充器】工具,可以将草图绘制器中生成的二维草图以多种方式拉伸为三维实体。
单击【填充器】工具的下拉箭头,即可开放全部的【填充器】工具。
通过【基于草图特征】工具栏上的【凹槽】工具,可以通过二维草图,以多种方式在三维实体上进展挖切操作。
单击【凹槽】工具的下拉箭头,即可开放全部的【凹槽】工具,共有三个,分别为凹槽,拔模圆角凹槽,多凹槽;这三个工具与【凸台】的三个工具相对应,各项设置也根本一样。
所不同的是这三项操作是从实体上挖切材料的。
在绘制简洁草图时如以下图:图一图二●对于这种单一平面内的简洁零件只需要依据二维视图照尺寸进展画图,图画完后退出草绘界面,点击凸台进展拉伸即可,但在图一的草绘时要首先确定一个长度在画图过程中要对其加以掌握。
●在画不同截面内的草图如画花瓶时要先建立不同的基准面利用工具栏中参考元素,【参考元素】是指在设计中用到的一些关心的点、线、面。
在【参考元素】工具栏中包含了三个工具【点】工具、【线】工具和【面】工具。
cam实训报告
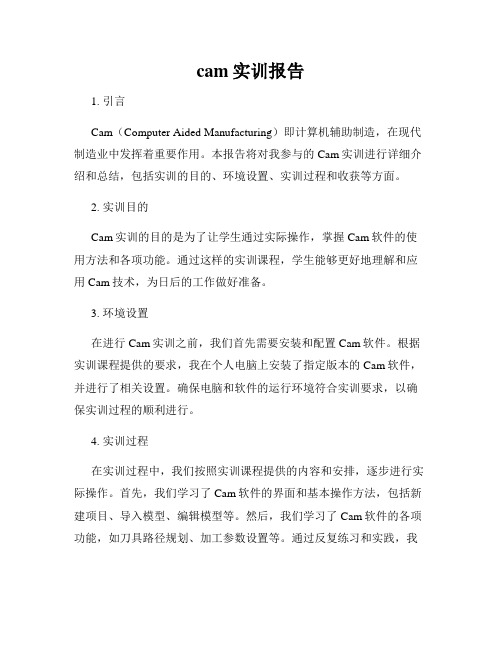
cam实训报告1. 引言Cam(Computer Aided Manufacturing)即计算机辅助制造,在现代制造业中发挥着重要作用。
本报告将对我参与的Cam实训进行详细介绍和总结,包括实训的目的、环境设置、实训过程和收获等方面。
2. 实训目的Cam实训的目的是为了让学生通过实际操作,掌握Cam软件的使用方法和各项功能。
通过这样的实训课程,学生能够更好地理解和应用Cam技术,为日后的工作做好准备。
3. 环境设置在进行Cam实训之前,我们首先需要安装和配置Cam软件。
根据实训课程提供的要求,我在个人电脑上安装了指定版本的Cam软件,并进行了相关设置。
确保电脑和软件的运行环境符合实训要求,以确保实训过程的顺利进行。
4. 实训过程在实训过程中,我们按照实训课程提供的内容和安排,逐步进行实际操作。
首先,我们学习了Cam软件的界面和基本操作方法,包括新建项目、导入模型、编辑模型等。
然后,我们学习了Cam软件的各项功能,如刀具路径规划、加工参数设置等。
通过反复练习和实践,我们逐渐熟悉了Cam软件的使用,并且能够灵活运用各项功能进行模型的加工和制造。
5. 实训收获通过参与Cam实训,我获得了以下收获:5.1 掌握Cam软件的使用方法和各项功能,能够熟练进行模型加工和制造。
5.2 提高了解决问题的能力和应变能力,能够在实际操作中灵活应对各种情况。
5.3 培养了团队合作意识和沟通能力,通过与同学的交流和讨论,我深刻认识到团队协作对于工作的重要性。
5.4 增进了对制造领域的了解,通过实际操作,我更好地理解了Cam技术在制造过程中的重要性和应用价值。
6. 总结通过本次Cam实训,我深刻体会到了理论与实践相结合的重要性。
通过实际操作,我不仅巩固了在课堂上学到的知识,还获得了更多的实际经验。
Cam技术的不断发展和应用,为制造业的发展带来了新的机遇和挑战。
我相信,在日后的工作中,我能够充分运用所学的Cam 技术,为工作的顺利进行做出贡献。
CAM实验报告
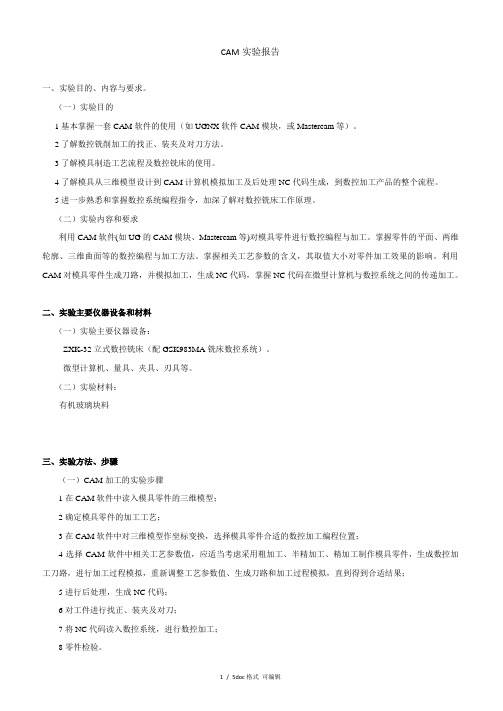
CAM实验报告一、实验目的、内容与要求。
(一)实验目的1基本掌握一套CAM软件的使用(如UGNX软件CAM模块,或Mastercam等)。
2了解数控铣削加工的找正、装夹及对刀方法。
3了解模具制造工艺流程及数控铣床的使用。
4了解模具从三维模型设计到CAM计算机模拟加工及后处理NC代码生成,到数控加工产品的整个流程。
5进一步熟悉和掌握数控系统编程指令,加深了解对数控铣床工作原理。
(二)实验内容和要求利用CAM软件(如UG的CAM模块、Mastercam等)对模具零件进行数控编程与加工。
掌握零件的平面、两维轮廓、三维曲面等的数控编程与加工方法。
掌握相关工艺参数的含义,其取值大小对零件加工效果的影响。
利用CAM对模具零件生成刀路,并模拟加工,生成NC代码,掌握NC代码在微型计算机与数控系统之间的传递加工。
二、实验主要仪器设备和材料(一)实验主要仪器设备:ZXK-32立式数控铣床(配GSK983MA铣床数控系统)。
微型计算机、量具、夹具、刃具等。
(二)实验材料:有机玻璃块料三、实验方法、步骤(一)CAM加工的实验步骤1在CAM软件中读入模具零件的三维模型;2确定模具零件的加工工艺;3在CAM软件中对三维模型作坐标变换,选择模具零件合适的数控加工编程位置;4选择CAM软件中相关工艺参数值,应适当考虑采用粗加工、半精加工、精加工制作模具零件,生成数控加工刀路,进行加工过程模拟,重新调整工艺参数值、生成刀路和加工过程模拟,直到得到合适结果;5进行后处理,生成NC代码;6对工件进行找正、装夹及对刀;7将NC代码读入数控系统,进行数控加工;8零件检验。
四、列出零件数控编程加工的方式及其主要工艺参数。
(一)零件数控编程加工的方式(1)型腔铣去除大量余料(2)平面铣削精加工(3)固定轮廓铣精加工(二)主要工艺参数表操作名刀具刀具选择类型切削方式主轴转速步进量吃刀深度进给率CA VITY_ MILL D12 mill_contour型腔铣1500rpm 刀具平直50%0.5mm 500mmpmFACE_MI LLING_A REA D12 mill_planar平面铣1750rpm 恒定10mm0.2mm 350mmpmFIXED_C ONTOUR B8 mill_contour固定轮廓铣750rpm 恒定0.25550mmpm五、模具零件的三维CAD模型及加工后的模具零件图片。
cam实训报告
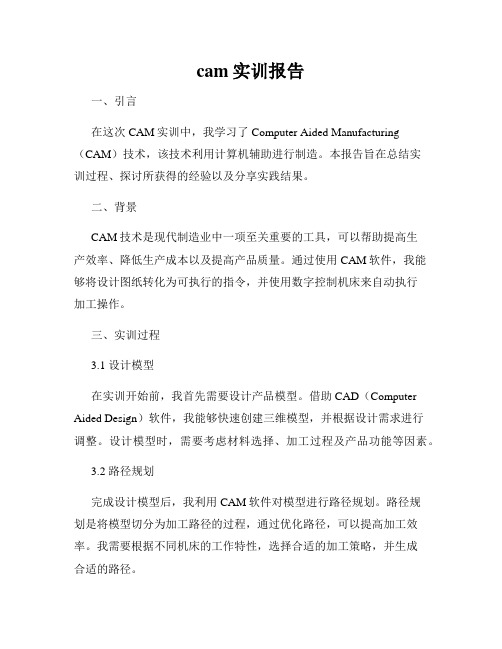
cam实训报告一、引言在这次CAM实训中,我学习了Computer Aided Manufacturing (CAM)技术,该技术利用计算机辅助进行制造。
本报告旨在总结实训过程、探讨所获得的经验以及分享实践结果。
二、背景CAM技术是现代制造业中一项至关重要的工具,可以帮助提高生产效率、降低生产成本以及提高产品质量。
通过使用CAM软件,我能够将设计图纸转化为可执行的指令,并使用数字控制机床来自动执行加工操作。
三、实训过程3.1 设计模型在实训开始前,我首先需要设计产品模型。
借助CAD(Computer Aided Design)软件,我能够快速创建三维模型,并根据设计需求进行调整。
设计模型时,需要考虑材料选择、加工过程及产品功能等因素。
3.2 路径规划完成设计模型后,我利用CAM软件对模型进行路径规划。
路径规划是将模型切分为加工路径的过程,通过优化路径,可以提高加工效率。
我需要根据不同机床的工作特性,选择合适的加工策略,并生成合适的路径。
3.3 制造过程经过路径规划后,我将路径数据导入数字控制机床,进行实际制造过程。
在实际操作中,我需要根据路径要求设置刀具和夹具,并在机床上进行操作。
通过数字控制系统,我能够直观地观察到加工过程,并对其进行调整和优化。
四、实践结果通过CAM实训,我成功完成了一项产品的制造过程。
在实际操作中,我发现CAM技术具有以下优点:1. 提高生产效率:CAM技术将机床操作自动化,减少人工操作时间,提高了加工效率。
2. 降低生产成本:相比传统手工加工,CAM技术大大减少了人力和耗材的使用,降低了生产成本。
3. 提高产品质量:CAM软件可以精确计算每一步操作,消除了人为错误的可能性,提高了产品质量。
4. 灵活性和可重复性:CAM技术可以根据产品设计的不同批次进行快速调整和大规模生产,提高了生产的灵活性和可重复性。
五、总结与展望通过这次CAM实训,我深刻理解了CAM技术对现代制造业的重要性,并获得了实操经验。
cam实训报告

cam实训报告前言近年来,随着机器人技术和智能制造技术的发展,计算机辅助制造(CAM)技术被广泛应用于各行各业。
而在工程领域中,CAM 技术也越来越得到重视。
为了提高学生的实践经验和技能,本文将介绍我在CAM实训课程中的学习和实践经历。
课程介绍CAM是指计算机辅助制造,也就是利用计算机相关软件来协助制造过程的技术。
在CAM课程中,我们学习了AutoCAD和SolidWorks等CAD软件的基础知识和技巧,用来绘制产品的三维模型。
然后我们学习了G代码,这是一种数字语言,用于告诉机床如何移动以制造物品。
最后我们使用MasterCAM软件将三维模型转换为对应的数字化CNC程序,并将其传输到数控机床进行加工。
学习过程在课程的初期,我们主要学习了CAD软件。
我们学习了如何使用SolidWorks创建三维模型,并学习了如何在AutoCAD中进行正交和透视投影。
这些基础知识是理解CAM技术的关键。
接下来,我们学习了数字控制技术。
我们学习了G代码,并了解了在G代码中如何定义坐标系、刀具半径和速度等参数。
我们在课堂上编写了一些简单的G代码程序,并将其上传到数控机床进行加工。
为了更深入地了解数字控制技术,我们分组进行了一个实验。
我们的任务是制作一个简单的立方体零件。
我们首先使用SolidWorks设计了立方体的三维模型,然后将其导出为STL文件,并将其导入到MasterCAM中生成CNC程序。
在数控机床上,我们将预先编写的程序上传到控制器中,并将工件夹在机床上。
经过加工,我们成功地制作了一个小零件。
整个过程都是无人值守的,我们只需等待机床完成加工。
最后,我们在课程的最后阶段使用CAM技术制作了一个大型的零件,其形状为一个大型螺旋体。
我们使用SolidWorks设计了螺旋体的三维模型,并在MasterCAM中编写了数字化CNC程序。
由于零件过于庞大,我们将其分为多个较小的部分,然后将其送到数控机床上进行加工。
整个加工过程持续了数小时,但最终我们成功地制造了一整个螺旋体。
cam实训报告
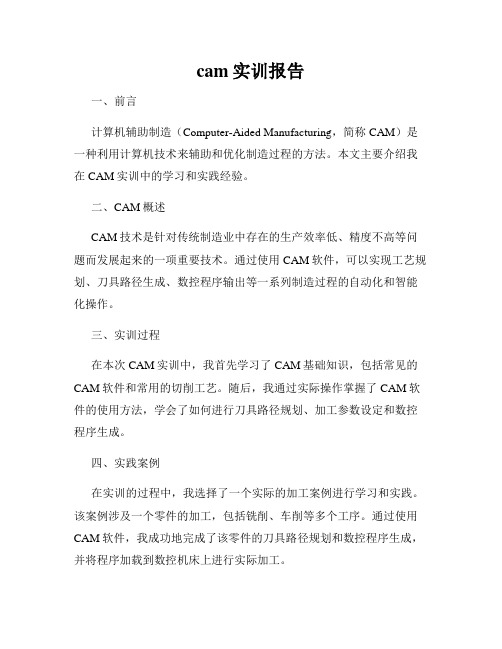
cam实训报告一、前言计算机辅助制造(Computer-Aided Manufacturing,简称CAM)是一种利用计算机技术来辅助和优化制造过程的方法。
本文主要介绍我在CAM实训中的学习和实践经验。
二、CAM概述CAM技术是针对传统制造业中存在的生产效率低、精度不高等问题而发展起来的一项重要技术。
通过使用CAM软件,可以实现工艺规划、刀具路径生成、数控程序输出等一系列制造过程的自动化和智能化操作。
三、实训过程在本次CAM实训中,我首先学习了CAM基础知识,包括常见的CAM软件和常用的切削工艺。
随后,我通过实际操作掌握了CAM软件的使用方法,学会了如何进行刀具路径规划、加工参数设定和数控程序生成。
四、实践案例在实训的过程中,我选择了一个实际的加工案例进行学习和实践。
该案例涉及一个零件的加工,包括铣削、车削等多个工序。
通过使用CAM软件,我成功地完成了该零件的刀具路径规划和数控程序生成,并将程序加载到数控机床上进行实际加工。
五、实训收获通过本次CAM实训,我对CAM技术有了更深入的了解。
首先,我掌握了CAM软件的使用方法,能够独立完成基本的刀具路径规划和数控程序生成。
其次,我对切削工艺的选择和参数设定有了更清晰的认识,能够根据不同的加工要求进行合理的设置。
最重要的是,我了解到CAM技术在制造业中的巨大潜力,它能够大大提高生产效率和产品质量,降低成本和资源浪费。
六、总结与展望通过本次CAM实训,我不仅增加了实践经验,还拓宽了自己的专业视野。
CAM技术是现代制造业的重要组成部分,熟练掌握CAM技术对于我今后的就业和发展具有重要意义。
我将继续深入学习和研究CAM技术,努力提升自己的实践能力,为未来的工作做好准备。
七、致谢在此,我要特别感谢实训教师的辛勤付出和耐心指导,没有他们的帮助和支持,我无法顺利完成这次实训。
同时,我也要感谢我的同学们,他们的鼓励和合作使我更加坚定地学习和实践。
八、参考文献[1] 王小明. 计算机辅助制造(CAM)技术应用研究[J]. 机械制造与自动化, 2018(05): 96-98.[2] 张国栋. CAM技术在模切加工中的应用[J]. 机械工程师, 2019(01): 120-122.以上就是我在CAM实训中的学习和实践经验,希望这篇报告能够对CAM技术的学习和应用有所帮助。
模具CAD、CAM实训报告
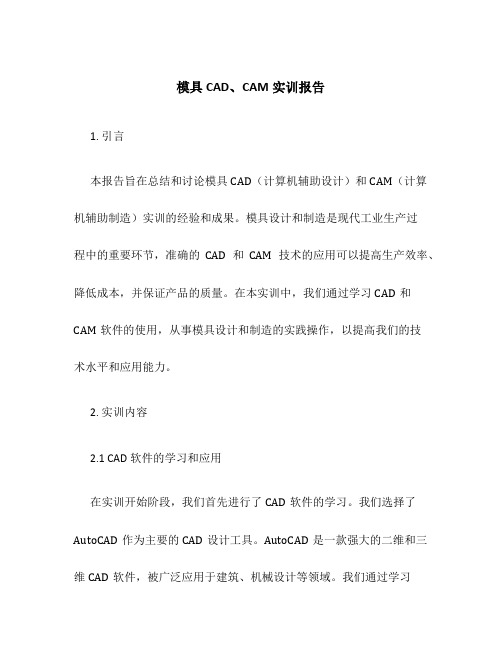
模具CAD、CAM实训报告1. 引言本报告旨在总结和讨论模具CAD(计算机辅助设计)和CAM(计算机辅助制造)实训的经验和成果。
模具设计和制造是现代工业生产过程中的重要环节,准确的CAD和CAM技术的应用可以提高生产效率、降低成本,并保证产品的质量。
在本实训中,我们通过学习CAD和CAM软件的使用,从事模具设计和制造的实践操作,以提高我们的技术水平和应用能力。
2. 实训内容2.1 CAD软件的学习和应用在实训开始阶段,我们首先进行了CAD软件的学习。
我们选择了AutoCAD作为主要的CAD设计工具。
AutoCAD是一款强大的二维和三维CAD软件,被广泛应用于建筑、机械设计等领域。
我们通过学习AutoCAD的基本操作和常用工具,掌握了绘图技巧和命令的使用。
在实际操作中,我们使用AutoCAD进行了模具零件的绘制和装配、尺寸标注、剖视图的生成等工作。
2.2 CAM软件的学习和应用在完成CAD设计后,我们进一步学习了CAM软件的使用。
CAM软件可以将CAD设计转化为机器可执行的代码,实现自动化的加工过程。
我们选择了Mastercam作为CAM软件进行学习和实践。
Mastercam是一款功能强大的CAM工具,广泛应用于数控加工和模具制造领域。
通过学习Mastercam的操作界面和基本功能,我们能够将CAD设计文件导入Mastercam中,进行刀具路径的生成、工艺参数的设定,并最终生成可供数控机床加工的代码。
3. 实训成果3.1 模具CAD设计成果通过实训,我们完成了多个模具CAD设计任务。
我们首先进行了模具零件的绘制,绘制了主要的模具零件包括模具座、上模板、下模板等。
我们使用AutoCAD进行了绘制、编辑和尺寸标注,保证了设计的准确性和可读性。
然后,我们将这些模具零件进行了装配,使用AutoCAD的装配功能,生成了模具的三维装配图。
通过装配图,我们可以清晰地了解模具的结构和组成,并进行必要的修正和优化。
cam实习报告

cam实习报告在实习期间,我有幸加入了一家名为CAM的公司,这是一家专注于计算机辅助制造领域的公司。
在这段时间里,我有机会接触到了许多新的知识和技能,也收获了不少宝贵的经验。
以下是我在CAM公司实习的报告。
首先,我在实习期间主要负责了CAD软件的学习和应用。
在CAM公司,CAD软件是我们日常工作中不可或缺的工具,它可以帮助我们进行产品设计和制造过程中的各种模拟和分析。
通过实际操作,我掌握了CAD软件的基本操作技巧,包括绘制图形、编辑图形、三维建模等,这些技能对我未来的工作和学习都将大有裨益。
其次,我还参与了一些项目的实际操作和管理工作。
在CAM公司,我们通常会根据客户的需求,进行一些定制化的项目,包括产品设计、模具制造等。
我有幸参与了其中一些项目,通过和团队成员的合作,我学会了如何有效地协调各个环节的工作,确保项目能够按时高质量地完成。
这些经验对我今后的团队合作和项目管理都将大有裨益。
另外,我还有机会参与了一些专业技能培训和学习交流。
CAM公司非常重视员工的专业素养和技能提升,因此定期会组织各种培训和学习交流活动。
在这些活动中,我结识了许多行业内的专家和同行,从他们身上学到了很多宝贵的经验和技巧。
这些培训和学习交流对我的职业发展有着非常积极的影响。
总的来说,我在CAM公司的实习经历是非常宝贵和难忘的。
通过这段时间的实习,我不仅学到了许多专业知识和技能,还收获了许多宝贵的人际关系和工作经验。
我相信这些经历将对我的未来职业发展产生积极的影响,我会继续努力,不断提升自己,为公司的发展贡献自己的力量。
感谢CAM公司给我这次宝贵的实习机会,我会倍加珍惜,努力学习和成长。
cam实训报告
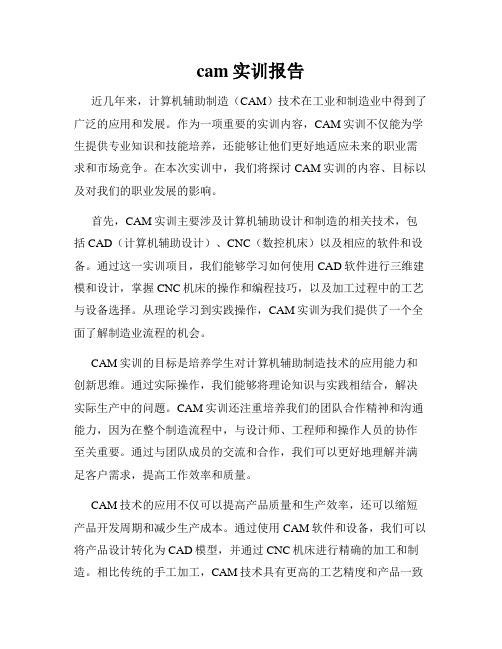
cam实训报告近几年来,计算机辅助制造(CAM)技术在工业和制造业中得到了广泛的应用和发展。
作为一项重要的实训内容,CAM实训不仅能为学生提供专业知识和技能培养,还能够让他们更好地适应未来的职业需求和市场竞争。
在本次实训中,我们将探讨CAM实训的内容、目标以及对我们的职业发展的影响。
首先,CAM实训主要涉及计算机辅助设计和制造的相关技术,包括CAD(计算机辅助设计)、CNC(数控机床)以及相应的软件和设备。
通过这一实训项目,我们能够学习如何使用CAD软件进行三维建模和设计,掌握CNC机床的操作和编程技巧,以及加工过程中的工艺与设备选择。
从理论学习到实践操作,CAM实训为我们提供了一个全面了解制造业流程的机会。
CAM实训的目标是培养学生对计算机辅助制造技术的应用能力和创新思维。
通过实际操作,我们能够将理论知识与实践相结合,解决实际生产中的问题。
CAM实训还注重培养我们的团队合作精神和沟通能力,因为在整个制造流程中,与设计师、工程师和操作人员的协作至关重要。
通过与团队成员的交流和合作,我们可以更好地理解并满足客户需求,提高工作效率和质量。
CAM技术的应用不仅可以提高产品质量和生产效率,还可以缩短产品开发周期和减少生产成本。
通过使用CAM软件和设备,我们可以将产品设计转化为CAD模型,并通过CNC机床进行精确的加工和制造。
相比传统的手工加工,CAM技术具有更高的工艺精度和产品一致性,大大提高了产品的质量和可靠性。
此外,CAM技术还可以实现自动化生产,减少了人工操作的错误和劳动强度,提高了生产效率。
CAM实训还对我们的职业发展产生了积极的影响。
随着制造业的发展,对CAM技术人才的需求也越来越大。
通过参与CAM实训,我们能够获得与市场需求相符的技术和工作经验,增加我们的竞争力。
此外,CAM实训还为我们提供了和企业进行真实合作的机会,将我们所学的知识应用到实际生产中,从而更好地适应未来工作的需求。
CAM实训还培养了我们的解决问题和创新思维的能力,使我们在职场中能够面对和应对各种挑战。
CAMUG实训报告总结(共3篇)

CAMUG实训报告总结(共3篇)(经典版)编制人:__________________审核人:__________________审批人:__________________编制单位:__________________编制时间:____年____月____日序言下载提示:该文档是本店铺精心编制而成的,希望大家下载后,能够帮助大家解决实际问题。
文档下载后可定制修改,请根据实际需要进行调整和使用,谢谢!并且,本店铺为大家提供各种类型的经典范文,如工作总结、工作计划、合同协议、条据书信、讲话致辞、规章制度、策划方案、句子大全、教学资料、其他范文等等,想了解不同范文格式和写法,敬请关注!Download tips: This document is carefully compiled by this editor. I hope that after you download it, it can help you solve practical problems. The document can be customized and modified after downloading, please adjust and use it according to actual needs, thank you!Moreover, our store provides various types of classic sample texts for everyone, such as work summaries, work plans, contract agreements, document letters, speeches, rules and regulations, planning plans, sentence summaries, teaching materials, other sample texts, etc. If you want to learn about different sample formats and writing methods, please pay attention!CAMUG实训报告总结(共3篇)CAMUG实训报告总结第1篇材料工程系模具设计与制造专业 UG实训报告姓名:班级:学号:指导教师: 日期:河南机电高等专科学校目录第一章 XXX模具典型零件建模凹模绘制凹模固定板的绘制....凸模绘制凸模固定板绘制.卸料板绘制....垫板绘制模座绘制第二章 XXX冲压模具装配模具的上模装配过程..模具的上模装配过程.模具的总装配过程.第三章 XXX冲压模具工程图凹模工程图绘制..凹模固定板的工程图绘制凸模工程图绘制..凸模固定板工程图绘制..模具总装工程图绘制垫板工程图绘制..模座工程图绘制..(红色为必写内容,黑色内容为选写内容)CAMUG实训报告总结第2篇实验报告课程名称:汽车计算机辅助设计院系名称:汽车与交通工程学院专业班级:车辆14-1班______学生姓名:______学号:______指导教师:杨兆石现明______黑龙江工程学院教务处制实验报告(一)实验类型□验证性V综合性□设计性□其他、实验目的1熟悉UG的用户界面及工具栏定制方法; 2熟悉模型空间中高级曲线建模 3?熟练掌握草图的绘制的方法。
模具CAD、CAM实训报告

目录第1章绪论.................................................. (1)1.1Pro/E模具设计简介 (1)1.2Pro/E数控加工简介 (2)第2章典型塑件模具设计 (5)2.1塑件表壳工艺性 (5)2.2塑件表壳模具设计 (6)第3章塑件凹模数控加工 (17)3.1 表壳凹模数控加工 (17)第4章总结 (23)模具CAD/CAM实训报告专业:材料成型及控制工程班级:材料成型0941姓名:刘文帝学号:10指导教师: 王东明机械工程学院2012年12月第一章绪论一.Pro-E模具设计简介①.Pro-E模具设计简介Pro/E第一个提出了参数化设计的概念,并且采用了单一数据库来解决特征的相关性问题。
另外,它采用模块化方式,用户可以根据自身的需要进行选择,而不必安装所有模块。
Pro/E的基于特征方式,能够将设计至生产全过程集成到一起,实现并行工程设计。
它不但可以应用于工作站,而且也可以应用到单机上。
Pro/E采用了模块方式,可以分别进行草图绘制、零件制作、装配设计、钣金设计、加工处理等,保证用户可以按照自己的需要进行选择使用。
1.参数化设计相对于产品而言,可以把它看成几何模型,而无论多么复杂的几何模型,都可以分解成有限数量的构成特征,而每一种构成特征,都可以用有限的参数完全约束,这就是参数化的基本概念。
2.基于特征建模Pro/E是基于特征的实体模型化系统,工程设计人员采用具有智能特性的基于特征的功能去生成模型,如系列化快餐托盘设计腔、壳、倒角及圆角,您可以随意勾画草图,轻易改变模型。
这一功能特性给工程设计者提供了在设计上从未有过的简易和灵活,特别是在设计系列化产品上更是有得天独到的优势。
3.单一数据库Pro/Engineer是建立在统一基层上的数据库上,不象一些传统的CAD/CAM系统建立在多个数据库上。
所谓单一数据库,就是工程中的资料全部来自一个库,使得每一个独立用户在为一件产品造型而工作,不管他是哪一个部门的。
cam实训报告
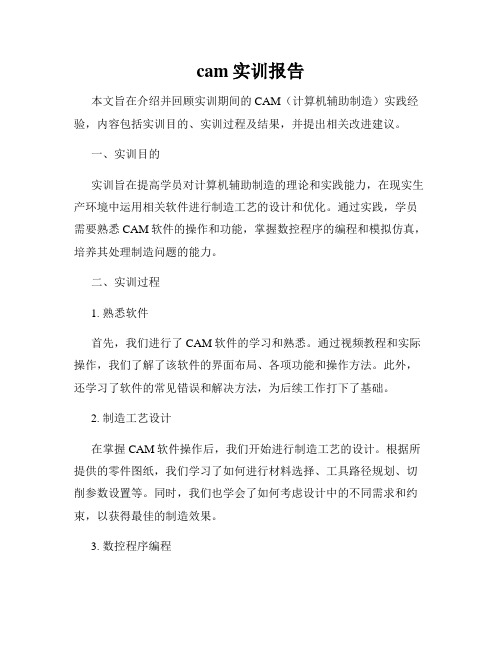
cam实训报告本文旨在介绍并回顾实训期间的CAM(计算机辅助制造)实践经验,内容包括实训目的、实训过程及结果,并提出相关改进建议。
一、实训目的实训旨在提高学员对计算机辅助制造的理论和实践能力,在现实生产环境中运用相关软件进行制造工艺的设计和优化。
通过实践,学员需要熟悉CAM软件的操作和功能,掌握数控程序的编程和模拟仿真,培养其处理制造问题的能力。
二、实训过程1. 熟悉软件首先,我们进行了CAM软件的学习和熟悉。
通过视频教程和实际操作,我们了解了该软件的界面布局、各项功能和操作方法。
此外,还学习了软件的常见错误和解决方法,为后续工作打下了基础。
2. 制造工艺设计在掌握CAM软件操作后,我们开始进行制造工艺的设计。
根据所提供的零件图纸,我们学习了如何进行材料选择、工具路径规划、切削参数设置等。
同时,我们也学会了如何考虑设计中的不同需求和约束,以获得最佳的制造效果。
3. 数控程序编程在制造工艺设计完成后,我们需要进行数控程序编程。
通过学习G代码和M代码的语法和规范,我们能够编写出适合加工零件的程序。
同时,我们也学会了如何进行程序的调试和修改,以确保其正常运行。
4. 模拟仿真与优化为了确保程序的正确性和优化加工效果,我们使用CAM软件进行了模拟仿真。
通过模拟,我们能够了解加工过程中的问题和不足,并进行相应的调整和优化。
这一步骤对于提高加工效率和质量至关重要。
三、实训结果通过实训的努力,我们取得了以下成果:1. 认识到CAM软件的重要性,将其应用于实际制造工艺的设计中,提高了工作效率和质量。
2. 掌握了数控程序的编写和调试技巧,能够根据需求自主进行程序的修改和优化。
3. 通过模拟仿真,我们能够发现并解决加工过程中的问题,提高了工件加工的准确性和精度。
4. 通过与团队成员的合作和讨论,我们不仅共同解决了许多技术问题,也加深了对CAM技术的理解和应用。
综上所述,实训期间我们通过学习和实践,不仅提高了对CAM软件的熟练度,也提升了对制造工艺的认识和应用能力。
cam实习报告
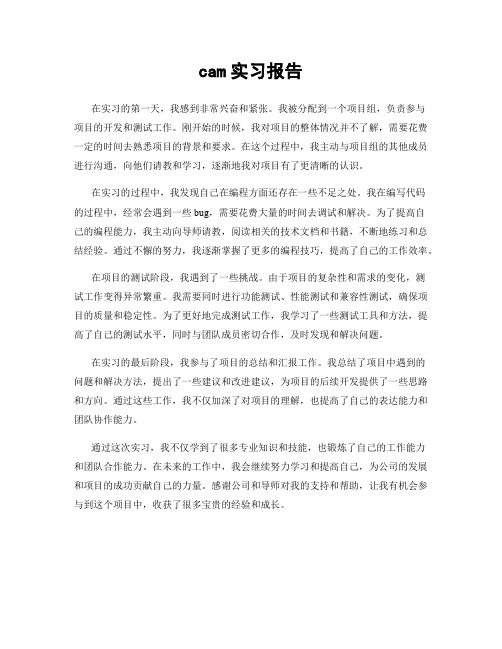
cam实习报告在实习的第一天,我感到非常兴奋和紧张。
我被分配到一个项目组,负责参与项目的开发和测试工作。
刚开始的时候,我对项目的整体情况并不了解,需要花费一定的时间去熟悉项目的背景和要求。
在这个过程中,我主动与项目组的其他成员进行沟通,向他们请教和学习,逐渐地我对项目有了更清晰的认识。
在实习的过程中,我发现自己在编程方面还存在一些不足之处。
我在编写代码的过程中,经常会遇到一些bug,需要花费大量的时间去调试和解决。
为了提高自己的编程能力,我主动向导师请教,阅读相关的技术文档和书籍,不断地练习和总结经验。
通过不懈的努力,我逐渐掌握了更多的编程技巧,提高了自己的工作效率。
在项目的测试阶段,我遇到了一些挑战。
由于项目的复杂性和需求的变化,测试工作变得异常繁重。
我需要同时进行功能测试、性能测试和兼容性测试,确保项目的质量和稳定性。
为了更好地完成测试工作,我学习了一些测试工具和方法,提高了自己的测试水平,同时与团队成员密切合作,及时发现和解决问题。
在实习的最后阶段,我参与了项目的总结和汇报工作。
我总结了项目中遇到的问题和解决方法,提出了一些建议和改进建议,为项目的后续开发提供了一些思路和方向。
通过这些工作,我不仅加深了对项目的理解,也提高了自己的表达能力和团队协作能力。
通过这次实习,我不仅学到了很多专业知识和技能,也锻炼了自己的工作能力和团队合作能力。
在未来的工作中,我会继续努力学习和提高自己,为公司的发展和项目的成功贡献自己的力量。
感谢公司和导师对我的支持和帮助,让我有机会参与到这个项目中,收获了很多宝贵的经验和成长。
cam实训总结
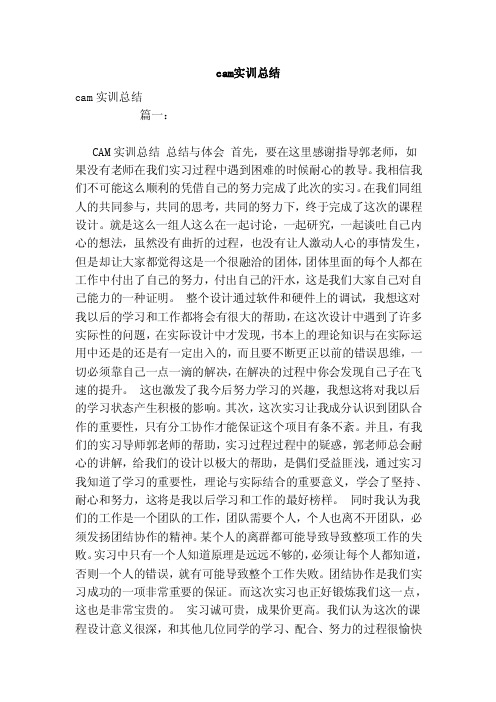
cam实训总结ca m实训总结篇一: CA M实训总结总结与体会首先,要在这里感谢指导郭老师,如果没有老师在我们实习过程中遇到困难的时候耐心的教导。
我相信我们不可能这么顺利的凭借自己的努力完成了此次的实习。
在我们同组人的共同参与,共同的思考,共同的努力下,终于完成了这次的课程设计。
就是这么一组人这么在一起讨论,一起研究,一起谈吐自己内心的想法,虽然没有曲折的过程,也没有让人激动人心的事情发生,但是却让大家都觉得这是一个很融洽的团体,团体里面的每个人都在工作中付出了自己的努力,付出自己的汗水,这是我们大家自己对自己能力的一种证明。
整个设计通过软件和硬件上的调试,我想这对我以后的学习和工作都将会有很大的帮助,在这次设计中遇到了许多实际性的问题,在实际设计中才发现,书本上的理论知识与在实际运用中还是的还是有一定出入的,而且要不断更正以前的错误思维,一切必须靠自己一点一滴的解决,在解决的过程中你会发现自己子在飞速的提升。
这也激发了我今后努力学习的兴趣,我想这将对我以后的学习状态产生积极的影响。
其次,这次实习让我成分认识到团队合作的重要性,只有分工协作才能保证这个项目有条不紊。
并且,有我们的实习导师郭老师的帮助,实习过程过程中的疑惑,郭老师总会耐心的讲解,给我们的设计以极大的帮助,是偶们受益匪浅,通过实习我知道了学习的重要性,理论与实际结合的重要意义,学会了坚持、耐心和努力,这将是我以后学习和工作的最好榜样。
(完整版)模具cam实训
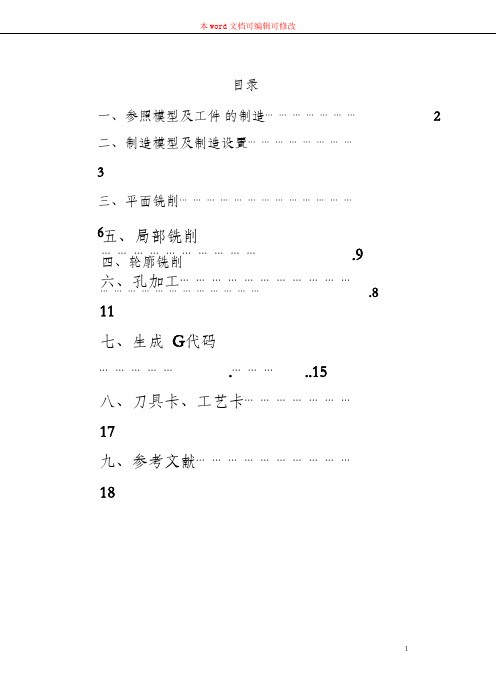
目录一、参照模型及工件 的制造⋯⋯⋯⋯⋯⋯⋯ 2二、制造模型及制造设置⋯⋯⋯⋯⋯⋯⋯⋯ 3三、平面铣削⋯⋯⋯⋯⋯⋯⋯⋯⋯⋯⋯⋯⋯ 6 四、轮廓铣削⋯⋯⋯⋯⋯⋯⋯⋯⋯⋯⋯⋯ .8五、局部铣削⋯⋯⋯⋯⋯⋯⋯⋯⋯⋯ .9六、孔加工⋯⋯⋯⋯⋯⋯⋯⋯⋯⋯⋯11七、生成 G 代码⋯⋯⋯⋯⋯ .⋯⋯⋯ ..15八、刀具卡、工艺卡⋯⋯⋯⋯⋯⋯⋯ 17九、参考文献⋯⋯⋯⋯⋯⋯⋯⋯⋯⋯ 18一、参照模型及工件的制造1、参照模型参照模型是所有 NC加工操作的基础。
在 NC加工前就要确定好参照模型,凹摸的参照模型加工如下:2、工件工件在 NC加工中可以看作是一个加工零件的毛坯,此工件留有2毫米的加工余量,如下图:二、制造模型及制造设置1、制造模型打开 Pro/E,单击【文件】→【新建】→【制造】命令,将系统默认的制造名更改为CAMSX,单击【确定】按钮选择公制模板mmns_part_solid,如下图所示:单击【确定】进入 Pro/E NC主界面,单击【制造】→【制造模型】→【装配】→【参照模型】命令,选择 MX文件【打开】,如图所示 :单击【自动】后面的【 v】,再选择【缺省】选项,单击右下角的【√】。
以此类推装配工件制造模型设定完毕后单击【完成 /返回】,如图所示:2、制造设置制造模型设定好后单击【制造设置】命令,进入【操作设置】对话框单击进入【机床设置】单击【确定】即可,单击【加工零点】中的,在 NC 的主界面中单击按住 Ctrl键,单击 FRONT平面、RIGHT平面和上表面选择【定向】单击 Y后面的【反向】使 Z轴朝上,点击确定完成坐标系的建立。
建立退刀平面,在【操作设置】对话框中单击退刀曲面后面的【↖】,在出现的对话框中点击【沿 Z轴】,输入 8或 10,点击【确定】。
三、平面铣削完成制造设置后,点击【 NC序列】→【新序列】→【加工、表面、 3 轴】→【完成】命令。
【序列设置】:选中【刀具、参数、曲面】→【完成】命令。
(精编)模具CADCAM实训报告

(精编)模具CADCAM实训报告目录第1章绪论 (1)1.1Pro/E模具设计简介……………………………………………11.2Pro/E数控加工简介 (2)第2章典型塑件模具设计 (5)2.1塑件表壳工艺性 (5)2.2塑件表壳模具设计 (6)第3章塑件凹模数控加工 (17)3.1表壳凹模数控加工 (17)第4章总结 (23)模具CAD/CAM实训报告专业:材料成型及控制工程班级:材料成型0941姓名:刘文帝学号:10指导教师:王东明机械工程学院2012年12月第一章绪论一.Pro-E模具设计简介①.Pro-E模具设计简介来解决特征的相关性问题。
另外,它采用模块化方式,用户可以根据自身的需要进行选择,而不必安装所有模块。
Pro/E的基于特征方式,能够将设计至生产全过程集成到一起,实现并行工程设计。
它不但可以应用于工作站,而且也可以应用到单机上。
Pro/E采用了模块方式,可以分别进行草图绘制、零件制作、装配设计、钣金设计、加工处理等,保证用户可以按照自己的需要进行选择使用。
1.参数化设计相对于产品而言,可以把它看成几何模型,而无论多么复杂的几何模型,都可以分解成有限数量的构成特征,而每一种构成特征,都可以用有限的参数完全约束,这就是参数化的基本概念。
2.基于特征建模Pro/E是基于特征的实体模型化系统,工程设计人员采用具有智能特性的基于特征的功能去生成模型,如系列化快餐托盘设计腔、壳、倒角及圆角,您可以随意勾画草图,轻易改变模型。
这一功能特性给工程设计者提供了在设计上从未有过的简易和灵活,特别是在设计系列化产品上更是有得天独到的优势。
3.单一数据库Pro/Engineer是建立在统一基层上的数据库上,不象一些传统的CAD/CAM系统建立在多个数据库上。
所谓单一数据库,就是工程中的资料全部来自一个库,使得每一个独立用户在为一件产品造型而工作,不管他是哪一个部门的。
换言之,在整个设计过程的任何一处发生改动,亦可以前后反应在整个设计过程的相关环节上。
cam实训报告总结
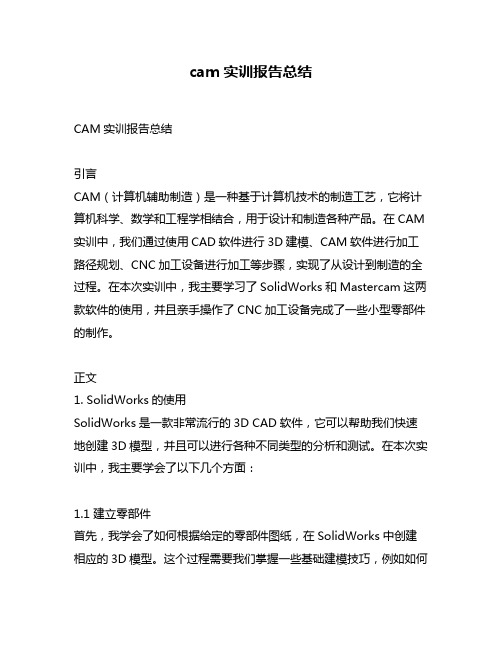
cam实训报告总结CAM实训报告总结引言CAM(计算机辅助制造)是一种基于计算机技术的制造工艺,它将计算机科学、数学和工程学相结合,用于设计和制造各种产品。
在CAM 实训中,我们通过使用CAD软件进行3D建模、CAM软件进行加工路径规划、CNC加工设备进行加工等步骤,实现了从设计到制造的全过程。
在本次实训中,我主要学习了SolidWorks和Mastercam这两款软件的使用,并且亲手操作了CNC加工设备完成了一些小型零部件的制作。
正文1. SolidWorks的使用SolidWorks是一款非常流行的3D CAD软件,它可以帮助我们快速地创建3D模型,并且可以进行各种不同类型的分析和测试。
在本次实训中,我主要学会了以下几个方面:1.1 建立零部件首先,我学会了如何根据给定的零部件图纸,在SolidWorks中创建相应的3D模型。
这个过程需要我们掌握一些基础建模技巧,例如如何选择适当的平面、线条和曲线等等。
1.2 组装零部件其次,在创建好各个零部件之后,我们需要将它们组装在一起,形成最终的产品。
在SolidWorks中,我们可以使用各种不同的组装工具,例如约束、关系等等,来确保各个零部件之间的正确位置和相互作用。
1.3 绘制工程图最后,在完成3D模型和组装之后,我们需要创建一份详细的工程图纸,以便CNC加工设备进行加工。
在SolidWorks中,我们可以使用自动绘图功能或手动绘图功能来生成这些图纸。
2. Mastercam的使用Mastercam是一款非常流行的CAM软件,它可以帮助我们规划CNC 加工路径,并且生成G代码以供CNC加工设备使用。
在本次实训中,我主要学会了以下几个方面:2.1 导入模型首先,在使用Mastercam进行加工路径规划之前,我们需要将SolidWorks中创建好的3D模型导入到Mastercam中。
这个过程需要我们掌握如何选择适当的导入格式,并且如何调整模型大小和位置。
- 1、下载文档前请自行甄别文档内容的完整性,平台不提供额外的编辑、内容补充、找答案等附加服务。
- 2、"仅部分预览"的文档,不可在线预览部分如存在完整性等问题,可反馈申请退款(可完整预览的文档不适用该条件!)。
- 3、如文档侵犯您的权益,请联系客服反馈,我们会尽快为您处理(人工客服工作时间:9:00-18:30)。
华东交通大学材料科学与工程学院模具CAM课程设计说明书题目:清新剂盖子数控加工专业:材料成型及控制工程班级:材料(模具)2013-2 学号:姓名:指导教师:目录第一章零件的三维造型 (3)第二章注塑模向导操作 (3)第三章工艺路线的规划 (4)第四章机械加工设备的选择 (6)第五章机械加工参数的确定 (7)第六章型腔数控加工过程及参数设置 (9)第七章数控加工程序后处理 (17)零件剖视图 (18)总结 (18)第一章零件的三维造型该制件为固体清新剂盒子上盖,外观主要尺寸为直径70mm、高5mm,零件主体厚度为1mm,如图1-1所示:图1-1零件图第二章注塑模向导操作通过注塑模向导进行初始化项目、定义工件、型腔布局、模具分型、加载模架(如图2-1)、建浇口、冷却水道、创建腔体等一系列操作,最终得到一模两腔型腔零件(这是转成stp格式之后的)如图2-2。
整个型腔零件包括浇口衬套、分流道孔、浇口、冷却水道孔、螺钉孔以及型腔。
图2-1图2-2第三章工艺路线的规划3.1 毛胚材料的选择和刀具材料的选择1.毛胚材料从零件的结构组成和几何形状来看,确定该工件为单件生产,主体为平面,局部有圆弧面、凸台及孔加工,主要加工方法为型腔铣和平面铣。
工件的长宽高为(120×110×20mm),采用长方体料,长宽高(122×122×22mm)。
本凹模零件的精度和表面质量要求高,所有采用模锻。
材料选用优质碳素结构钢(中碳钢),45号钢。
2. 刀具材料刀具的强度、刚度、硬度均要比毛坯材料更高,采用高速钢材料。
高速钢(HSS)是一种具有高硬度、高耐磨性和高耐热性的工具钢。
3.2 加工方法的选择⑴平面加工方法的选择:对于面型腔件来说,平面粗糙度要求最高的为Ra3.2,所以选择粗铣-半精铣-精铣这一加工方法就能达到要求。
(2)内外轮廓加工方法的选择:此零件轮廓中的表面粗糙度最高为Ra3.2所以可以采用粗铣-半精铣-精铣的加工方法-。
(3)孔表面加工方法的选择:此零件中因为孔的直径度小于20,且有精度要求,内孔表面采用钻-铰孔这一加工方法。
3.3 加工工序划分为了减小装夹次数,缩短定位时间,采取各表面集中进行加工。
机械加工工序的顺序原则为:基准先行,先主后次,先粗后精,先面后孔。
因此对该零件进行工序的划分为:(1)以粗基准定位铣上表面,因为上表面作为的设计基准和定位基准,表面粗糙度为3.2μm,粗铣-精铣。
(2)加工型腔内表面,粗糙度要求 3.2μm:粗铣--半精铣--精铣。
(3)加工上表面入水口圆孔,粗糙度要求 3.2μm,采用点钻—钻孔。
(4)加工四周表面上的水道圆孔,粗糙度要求 3.2μm,采用点钻—钻孔(5)加工上表面的浇口套孔,粗糙度3.2μm,采用点钻—钻孔(6)检验。
3.4.1型腔表面及孔和流道的加工以上表面进行定位,进行型腔表面的加工。
加工面如图所示:加工该面的各结构由以下工步内容组成:第四章机械加工设备的选择4.1加工机床选择数控铣床X8120。
基本参数如下表:4.2 刀具与量具的选择刀具的选择时数控加工工序设计的重要内容之一,它不仅影响机床的加工效率,而且直接影响加工质量。
所以在选择刀具时应考虑工件材质、加工轮廓类型及刀具的耐用度等因素。
一般情况下应优先选择标准刀具(特别是硬质合金可转位刀具),综合考虑之后决定铣刀、麻花钻的材料为高速钢。
量具的选择:对于双面型腔件在加工过程中测量及完成加工后检验的工具可以选择游标卡尺,游标卡尺是常用的一种量具,它能直接测量零件的外径、内径、长度、宽度、深度和孔径等。
使用简便。
所用的刀具有铣刀,钻刀。
查《机械加工工艺装备设计手册》表2-128和《金属切削手册》表6-2参数如下表:4.3铣床夹具和切削液的选择因为该零件为规则的板类零件,所以选用通用夹具——平口钳冷却方法有浇注法、高压冷却法、喷雾冷却法和二液冷却法,本次加工时选用溶化油水溶液冷却。
第五章机械加工参数的确定5.1加工余量的确定采用锻件、铸造毛坯时,因锻模时的欠压量与允许的错模量不等,铸造时也会因砂型误差、收缩量及毛坯的挠曲与扭曲变形量的不同也会造成加工余量不充分、不稳定,所以,除金属液体的流动性差不能充满型腔等造成余量的不等,此外,锻造、铸造后,毛坯无论锻件、铸件还是型材,只要准备采用数控加工,其加工表面均应有较充分的余量。
根据锻件毛坯余量表,可以查的毛坯在厚度方向的余量为2.1,长度和宽度上的余量为2.5.2铣削方式的确定由于铣床选用的是数控铣床,不具有专一性,且工件为锻件,硬度较高。
所以选择铣削方式为逆铣。
逆铣的方式是铣刀的旋转方向与工件的进给方向相反,铣刀切下的切削层由薄变厚,切削力由小变大。
在铣削力的作用下由于丝杆与螺母总保持接触,因而没有丝杆与螺母间隙对铣削的影响。
5.3切削用量的选择铣削时的铣削用量由切削速度、进给量、背吃刀量(铣削深度)和侧吃刀量(铣削宽度)四要素组成。
切削速Vc,切削速度Vc即铣刀最大直径处的线速度,可由下式计算:一般立铣刀粗铣时的背吃刀以不超过铣刀半径原则,一般不超过7mm ,以防止背吃刀量过大而造成刀具损坏,充分利用刀具的切削性能和铣床的功率、转矩等性能,在保证工序质量的前提下,获得高的生产率和低的加工成本的切削用量。
由《机械加工实用手册》表5.3.16确定粗铣后毛坯余量1.5mm ,半精铣后毛坯余量为1.0mm 。
剩下的由精加工去除。
5.4 切削速度和每齿进给量确定铣削速度V=πDn/1000.(D 为铣刀外径,n 为铣刀转速) 钻削速度V=πDn/1000.(D 为钻刀外径,n 为钻刀转速)铣削时S 齿=S 分/z*n (S 齿为每转过一个齿的走刀量,z 为齿数,n 为转速) 钻削时S 钻头前进的距离=(钻头每分钟前进距离/主轴转速) 计算得:(由5.3的图确定)D=20mm 主轴转速n=20*1000/3.14*20=318.47 r/min ,圆整取318r/min。
进给率=齿数x主轴转速x每齿进给率(看上表)D=24mm 主轴转速n=20*1000/3.14*24=265.39r/min,圆整取265 r/min。
D=6mm 主轴转速n=8*1000/3.14*6=424.63 r/min,圆整取425r/min。
D=4mm 主轴转速n=8*1000/3.14*3=636.94 r/min,圆整取637r/min。
d=6mm 孔加工主轴转速n=15*1000/3.14*6=796.18r/min,圆整取796r/min。
d=4mm 孔加工主轴转速n=15*1000/3.14*4=1194.27r/min,圆整取1194 r/min。
d=3mm 孔加工n=8*1000/3.14*3=849r/min,圆整取850 r/min。
第六章型腔数控加工过程及参数设置6.1型腔表面及四周粗加工过程及参数6.2型腔粗加工过程及参数设置6.3型腔表面粗加工过程及设置型腔表面精加工6.46.5型腔内面精加工过程及参数设置因为是精加工,所以余量为06.5 平面精工过程及参数设置加工效果如下6.6浇口衬套孔钻孔过程及参数设置6.7浇口衬套孔钻孔过程及参数设置6.8 水道钻孔水道加工与上平面螺钉孔加工方法相同,刀具直径同样选择3mm 和6mm 的,但是!定义坐标系时要将加工坐标系移动到侧面!这里不做赘述。
第七章数控加工后处理由于加工程序太长,这里只给出前一部分和后一部分前部分后一部分总结通过这次独立的完成课程设计,从模型设计的建立到最后的模型自动编程,让我更加清楚的认识到了对于UG软件本身及其操作的不足,激发了我玩好这个软件的态度。
并且通过这次课程设计课题的制作,我不仅学会了如何自主学习,如何在不知的情况下于别人合作并且学会了如何在大量的文字图书,电子图书中,如何快速有效的遭到自己所需的信息,从而解决问题。
现在,我敢大胆自信的说,我已经基本掌握了UG建模、自动编程方面的知识,生活中的日用品,只要给我点时间,我都能利用UG建出来。
综合这次实训中,零件图的审查、工艺的设计、刀具和机床夹具的选择、切削用量的选择、UG的建模和编程及后处理等,这一系列的操作完成对零件型腔的设计及加工任务。
在这次实训中,总结了一下几点教训和经验:1、建腔时提示发生错误,可能是目标体和工具体不小心选到了同样的部件:2、孔刀具选择后不能加工不在同一个平面的直径相同的孔:3、在加工处理看加工效果时,如果碰到需要定义毛胚的情况,可能是workpiece里没定义毛坯尺寸,导致后面一直出现需要定义毛胚的情况4、对于刀具的认识还有一些不足,目前知道了刀具加工面时刀具直径应占面的20%,刀具长度在50~70mm时通常选用50mm,产品公差在+-0.05时,刀具产生误差在+-0.01;产品公差在+-0.1时,误差在0.02。
选用多长的刀具,刀刃多长,他们之间的关系以及他们和加工板厚、加工深度之间的关系不清楚5、碰到新问题时,可以用以前做的零件进行试验,观察与现有零件的差别,从而找到解决问题的方法、。
6、加工孔的刀具和加工面的刀具带来的误差是不一样的,之前一直认为是一样的。
总的来说,这次课设让我加强了独立处理事情的能力、分析和解决问题的能力,这对于我的生活和学习都有很大的好处,在此感谢我的同学和老师,让我有了一次充实的课设之旅。