车间现场改善与效率提升PPT课件
合集下载
车间现场改善与效率提升47页PPT

车间现场改善与效率提升
现场改善与生产效率提升
生产管理的铁三角
D
交
成
期 安全 本
Q
C
质量
用最低的成本 符合要求的质量 ห้องสมุดไป่ตู้成规定的交期
2021/7/25
3
企业管理面临的共同难题
内部 救火式生产 质量不稳定 浪费严重
人员流动大
2021/7/25
外部 小批量 多品种
低价格
快交货
4
以最少的投入来获取最大的产出
许振超的技术研究工作: 许振超和队员们在桥吊每个操作环节抠时间。桥吊启动时,说明书上写 着,达到最高时速需要5秒钟,许振超计算后提出,3.5秒钟就够用,一 些司机不以为然地提出,抠.1.5秒有什么用?许振超为大家算了一笔账: “如果一船有1000个集装箱,就能节约25分钟出来”。
2021/7/25
管建伟
16
_____车间1-5月管理目标改善计划表
序
计划改善项目
1 交货期 2 生产周期 3 改机时间 4 停机时间 5 操作人员数 6 在制品数量 7 零部件(半成品)数量 8 库存品总额 9 搬运距离 10 不合格品发生率 11 一次交验合格率 12 返工返修品
1月
2月
3月
4月
2021/7/25
7
案例分析
某班组自动车床经常发生故障,维修人员 只能通过维修和更换备件解决故障。目前该设 备故障平均约每半年发生一次,主要原因是主 轴轴承发生故障,一套轴承的备件价格为3000 元,每年更换备件费用达6000元。如何应用 “五问”活动对主轴轴承故障的原因进行分析。
2021/7/25
管建伟
13
现场管理的 “A B C” 法
现场改善与生产效率提升
生产管理的铁三角
D
交
成
期 安全 本
Q
C
质量
用最低的成本 符合要求的质量 ห้องสมุดไป่ตู้成规定的交期
2021/7/25
3
企业管理面临的共同难题
内部 救火式生产 质量不稳定 浪费严重
人员流动大
2021/7/25
外部 小批量 多品种
低价格
快交货
4
以最少的投入来获取最大的产出
许振超的技术研究工作: 许振超和队员们在桥吊每个操作环节抠时间。桥吊启动时,说明书上写 着,达到最高时速需要5秒钟,许振超计算后提出,3.5秒钟就够用,一 些司机不以为然地提出,抠.1.5秒有什么用?许振超为大家算了一笔账: “如果一船有1000个集装箱,就能节约25分钟出来”。
2021/7/25
管建伟
16
_____车间1-5月管理目标改善计划表
序
计划改善项目
1 交货期 2 生产周期 3 改机时间 4 停机时间 5 操作人员数 6 在制品数量 7 零部件(半成品)数量 8 库存品总额 9 搬运距离 10 不合格品发生率 11 一次交验合格率 12 返工返修品
1月
2月
3月
4月
2021/7/25
7
案例分析
某班组自动车床经常发生故障,维修人员 只能通过维修和更换备件解决故障。目前该设 备故障平均约每半年发生一次,主要原因是主 轴轴承发生故障,一套轴承的备件价格为3000 元,每年更换备件费用达6000元。如何应用 “五问”活动对主轴轴承故障的原因进行分析。
2021/7/25
管建伟
13
现场管理的 “A B C” 法
生产车间现场改善课件

培训员工
确保员工熟悉并掌握标准作业 指导书内容。
检查与改进
定期检查员工作业情况,对不 符合标准的作业进行纠正和改 进。
持续优化
根据生产实际情况,持续优化 标准作业指导书,提高生产效产计划中预留时间,用于换模前的准备 工作。
培训员工
确保员工熟悉快速换模操作流程和技巧。
标准化操作
生产车间现场改善课件
BIG DATA EMPOWERS TO CREATE A NEW
ERA
• 生产车间概述 • 生产车间现场改善的必要性 • 生产车间现场改善的方法与策略 • 生产车间现场改善的案例分析 • 生产车间现场改善的未来展望
目录
CONTENTS
01
生产车间概述
BIG DATA EMPOWERS TO CREATE A NEW
02
生产车间现场改善的必要性
BIG DATA EMPOWERS TO CREATE A NEW
ERA
提高生产效率
减少生产过程中的浪费
通过优化生产流程、减少等待时间和 消除无效劳动,提高整体生产效率。
强化生产计划管理
合理安排生产计划,优化排产顺序, 确保生产线的稳定高效运行。
提升设备利用率
合理安排设备维护和检修计划,确保 设备处于良好状态,提高设备利用率 。
提高员工质量意识
加强员工的质量培训和教育,培养员工的质量意识和责任心。
严格把控关键工序
对关键工序进行严格的质量控制和监督,确保产品质量的合格率。
保障生产安全
加强安全管理制度建设
01
建立完善的安全管理制度和操作规程,确保员工的安全操作。
提高员工安全意识
02
加强员工的安全培训和教育,培养员工的安全意识和应急处理
确保员工熟悉并掌握标准作业 指导书内容。
检查与改进
定期检查员工作业情况,对不 符合标准的作业进行纠正和改 进。
持续优化
根据生产实际情况,持续优化 标准作业指导书,提高生产效产计划中预留时间,用于换模前的准备 工作。
培训员工
确保员工熟悉快速换模操作流程和技巧。
标准化操作
生产车间现场改善课件
BIG DATA EMPOWERS TO CREATE A NEW
ERA
• 生产车间概述 • 生产车间现场改善的必要性 • 生产车间现场改善的方法与策略 • 生产车间现场改善的案例分析 • 生产车间现场改善的未来展望
目录
CONTENTS
01
生产车间概述
BIG DATA EMPOWERS TO CREATE A NEW
02
生产车间现场改善的必要性
BIG DATA EMPOWERS TO CREATE A NEW
ERA
提高生产效率
减少生产过程中的浪费
通过优化生产流程、减少等待时间和 消除无效劳动,提高整体生产效率。
强化生产计划管理
合理安排生产计划,优化排产顺序, 确保生产线的稳定高效运行。
提升设备利用率
合理安排设备维护和检修计划,确保 设备处于良好状态,提高设备利用率 。
提高员工质量意识
加强员工的质量培训和教育,培养员工的质量意识和责任心。
严格把控关键工序
对关键工序进行严格的质量控制和监督,确保产品质量的合格率。
保障生产安全
加强安全管理制度建设
01
建立完善的安全管理制度和操作规程,确保员工的安全操作。
提高员工安全意识
02
加强员工的安全培训和教育,培养员工的安全意识和应急处理
最新现场改善与生产效率提升76页PPT

最新现场改善与生产效率提升
21、没有人陪你走一辈子,所以你要 适应孤 独,没 有人会 帮你一 辈子, 所以你 要奋斗 一生。 22、当眼泪流尽的时候,留下的应该 是坚强 。 23、要改变命运,首先改变自己。
24、勇气很有理由被当作人类德性之 首,因 为这种 德性保 证了所 有其余 的德性 。--温 斯顿. 丘吉尔 。 25、梯子的梯阶从来不是用来搁脚的 ,它只 是让人 们的脚 放上一 段时间 ,以便只有永远躺在泥坑里的人,才不会再掉进坑里。——黑格尔 32、希望的灯一旦熄灭,生活刹那间变成了一片黑暗。——普列姆昌德 33、希望是人生的乳母。——科策布 34、形成天才的决定因素应该是勤奋。——郭沫若 35、学到很多东西的诀窍,就是一下子不要学很多。——洛克
21、没有人陪你走一辈子,所以你要 适应孤 独,没 有人会 帮你一 辈子, 所以你 要奋斗 一生。 22、当眼泪流尽的时候,留下的应该 是坚强 。 23、要改变命运,首先改变自己。
24、勇气很有理由被当作人类德性之 首,因 为这种 德性保 证了所 有其余 的德性 。--温 斯顿. 丘吉尔 。 25、梯子的梯阶从来不是用来搁脚的 ,它只 是让人 们的脚 放上一 段时间 ,以便只有永远躺在泥坑里的人,才不会再掉进坑里。——黑格尔 32、希望的灯一旦熄灭,生活刹那间变成了一片黑暗。——普列姆昌德 33、希望是人生的乳母。——科策布 34、形成天才的决定因素应该是勤奋。——郭沫若 35、学到很多东西的诀窍,就是一下子不要学很多。——洛克
车间现场5S标准化管理企业工作效率与能力提升培训PPT模板课件
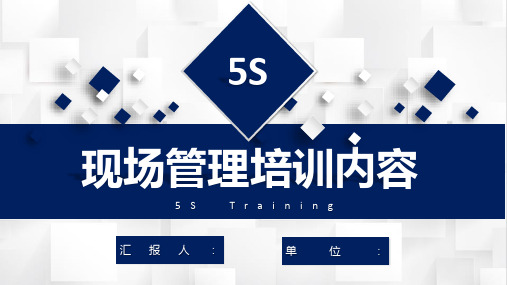
整顿
01
目的:不浪费时间寻找物品,提高工作效率和产品质量,保障
生产安全。
意义:把需要的人、事、物加以定量、定位。通过前一步整理
02
后,对生产现场需要留下的物品进行科学合理的布置和摆放,
以便用最快的速度取得所需之物,在最有效的规章、制度和最
简洁的流程下完成作业。
整顿
要点:① 物品摆放要有固定的地点和区域,以便于 寻找,消除因混放而造成的差错;② 物品摆放地点 要科学合理。例如,根据物品使用的频率,经常使 用的东西应放得近些(如放在作业区内),偶尔使 用或不常使用的东西则应放得远些(如集中放在车 间某处);③ 物品摆放目视化,使定量装载的物品 做到过目知数,摆放不同物品的区域采用不同的色 彩和标记加以区别。
五大原则
在采用看板作为管理工具时, 应遵循以下五个原则:
⑴后工序只有在必要的时候,才向 前工序领取必要数量的零部件:需 要彻底改变现有流程和方法。
⑵前工序应该只生产足够的数 量,以补充被后工序领取的零 件:在这两条原则下,生产系 统自然结合为输送带式系统, 生产时间达到平衡。
⑶不良品不送往后工序:后 工序没有库存,后工序一旦 发现次品必须停止生产,找 到次品送回前工序。
清洁
目的:认真维护并坚持整理、整顿、清扫的 效果,使其保持最佳状态。
意义:通过对整理、整顿、清扫活动的坚持 与深入,从而消除发生安全事故的根源。创 造一个良好的工作环境,使职工能愉快地工 作。
清洁
要点:① 车间环境不仅要整齐,而且要做到清洁卫生,保证工人身 体健康,提高工人劳动热情;② 不仅物品要清洁,而且工人本身也 要做到清洁,如工作服要清洁,仪表要整洁,及时理发、刮须、修 指甲、洗澡等;③ 工人不仅要做到形体上的清洁,而且要做到精神 上的“清洁”,待人要讲礼貌、要尊重别人;④ 要使环境不受污染, 进一步消除浑浊的空气、粉尘、噪音和污染源,消灭职业病。
精益改善项目案例生产效率提升PPT课件(42页)(2024版)

项目范围: 项目通过推进精益生产,减少生产制造全流程内的浪费,有效减少作业人员、提升产量,缩短交付周期,在降低制造成本的同时,快速满足客户的需求。以工厂为试点,三地工厂同步实施,在制冷集团各事业部推广。
变量
名称
CTQ
单位
Y
生产效率提升
月人均产出
套/人
Y1
生产组织模式变革
订单交付周期
天
Y2
制造技术提升
大线组长 柔性线组长 柔性线巡检
减少1人 两两合并 两两合并
15
Y2改善(节选)—管理优化减员
改善效果:计划减员101人,实际减员101人,计划达成率100%。
部门(分厂)
总一
总二
总三
部装
注塑
财务
品质
职能部
目标(人)
7
2
6
3
31
14
18
20
推进 方向
Y1的改善 摘录1
改善项目名称:订单下达规范性
改善类别
技术
管理
设备
材料
费用
其它
√
改善前
改善后
问题点
改善方案
1、针对计划下达准确率、计划完成及时性的责任划分不明晰,产销责权关系不清,存在管理真空; 2、相关流程时间节点不规范、不合理,且操作随意性较强; 3、产销信息传递不畅。经常出现生产计划与销售计划间的信息不对称;
1、以文件形式彻底固化尾数清理流程、明确激励考核要求; 2、计划管理建立专人监控机制,按周、月通报 3、物资管理监督车间生产过程物料损耗,并每日统计滚动输出; 4、供应商建立安全库存,保证欠产物料补缺的及时性,减少超期作业任务产生; 5、车间物料管护规范每周稽查不少于2次。
《现场改善技巧》课件
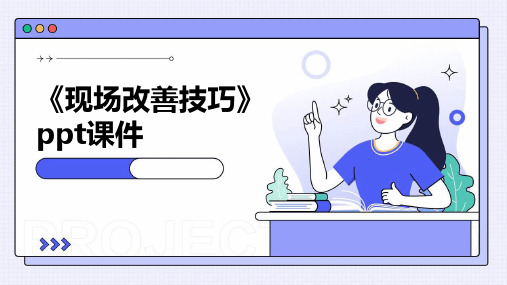
针对评估和审查中发现的问题,制定改进措施并组 织实施。
标准的更新与完善
根据改进效果和生产环境的变化,对作业标准进行 更新和完善,以保持标准的适用性和有效性。
05 目视化管理
目视化管理的定义和作用
01
目视化管理是一种利用视觉信息来管理和控制工作 场所的方法。
02
目视化管理能够提高工作效率,减少错误和浪费, 提升员工的安全意识。
认可和奖励
对积极参与改善活动的员工给予适当的认可和奖励,激发员工的积 极性。
团队合作与竞赛
组织跨部门的团队合作项目或竞赛,激发员工的团队合作精神和竞争 意识。
感谢您的观看
THANKS
作业标准的制定与实施
培训与教育
对员工进行作业标准的培训和教育,确保员工理解和 掌握标准。
监督与检查
建立监督检查机制,确保员工在实际工作中执行标准 。
反馈与改进
收集员工的反馈意见,对标准进行持续改进和优化。
作业标准的持续改进
定期评估与审查
定期对作业标准进行评估和审查,以发现存在的问 题和不足。
改进措施的实施
培养员工的问题意识
发现问题的能力
培养员工敏锐的观察力,能够及时发现现场存在的问题和改进空 间。
分析问题的能力
通过培训和引导,帮助员工学会分析问题产生的原因,并提出有 效的解决方案。
解决问题的能力
鼓励员工勇于承担责任,积极主动地解决问题,提高工作效率和 质量。
鼓励员工参与改善活动
提供培训和支持
为员工提供必要的培训和支持,使其具备参与改善活动的能力和信 心。
现场改善不仅关注单个环节的优化, 更强调整体流程的协同和整合。
现场改善的重要性
提高生产效率
标准的更新与完善
根据改进效果和生产环境的变化,对作业标准进行 更新和完善,以保持标准的适用性和有效性。
05 目视化管理
目视化管理的定义和作用
01
目视化管理是一种利用视觉信息来管理和控制工作 场所的方法。
02
目视化管理能够提高工作效率,减少错误和浪费, 提升员工的安全意识。
认可和奖励
对积极参与改善活动的员工给予适当的认可和奖励,激发员工的积 极性。
团队合作与竞赛
组织跨部门的团队合作项目或竞赛,激发员工的团队合作精神和竞争 意识。
感谢您的观看
THANKS
作业标准的制定与实施
培训与教育
对员工进行作业标准的培训和教育,确保员工理解和 掌握标准。
监督与检查
建立监督检查机制,确保员工在实际工作中执行标准 。
反馈与改进
收集员工的反馈意见,对标准进行持续改进和优化。
作业标准的持续改进
定期评估与审查
定期对作业标准进行评估和审查,以发现存在的问 题和不足。
改进措施的实施
培养员工的问题意识
发现问题的能力
培养员工敏锐的观察力,能够及时发现现场存在的问题和改进空 间。
分析问题的能力
通过培训和引导,帮助员工学会分析问题产生的原因,并提出有 效的解决方案。
解决问题的能力
鼓励员工勇于承担责任,积极主动地解决问题,提高工作效率和 质量。
鼓励员工参与改善活动
提供培训和支持
为员工提供必要的培训和支持,使其具备参与改善活动的能力和信 心。
现场改善不仅关注单个环节的优化, 更强调整体流程的协同和整合。
现场改善的重要性
提高生产效率
车间管理与现场改善方法PPT课件

③ 以现状为基础找出问题(发现浪费)
④ 问题对策与防止再发生
⑤制作新的标准作业表 ⑥ 按① 至⑤的步骤
无止境地反复很重要
作业的指导与训练
标准作业 标准作业的改善 把握问题(现状)
发现浪费
标准作业
改善
原因追究
13
如何进行现场改善
3-2 从作业改善到设备改善
① 作业改善 (A) 作业步骤、组合的改变 (B) 物品摆放, 作业工具及作业台摆放的改变 (C)简单的小工具, 滑道, 自动弹出, 吊具等的安装、改变等 (D) 改善现有设备
=面
(d) 公司的改善
= 立方体
27
如何进行现场改善
3 1
③ 总结
(a) 改善从观察现场开始
(b) 要热爱改善
(c) 事实胜于雄辩,实践是首要
改善是细而慢 不如粗而快! 不动则无成功!
28
如何进行现场改善
3 2
Ⅳ. 标准作业的制作
1. 标准作业的再确认
1-1 标准作业是现场改善的原点, 不标准的地方不存在改善.
[2] 设备是瓶颈的时候
1. 不要让瓶颈工位闲下来 2. 将按启动钮的时间提前 3. 缩小送料行程(快送, 切削送料) 4. 使机器动作叠加起来,看 是否能缩短加工以外的时间 5. 加快快送, 快退的速度
2 5
22
如何进行现场改善
好的排位的思考方法
(A) 考虑了流线的排位 ― 有灵活性的排位 ― 可根据变化移动
生产过 剩的浪 费
加工的 浪费
4
如何进行现场改善 Ⅱ. 生产方法的两大支柱
1. Just-In-Time的生产
1-1 使工序流线化
S・P・S
新技术生产体系
④ 问题对策与防止再发生
⑤制作新的标准作业表 ⑥ 按① 至⑤的步骤
无止境地反复很重要
作业的指导与训练
标准作业 标准作业的改善 把握问题(现状)
发现浪费
标准作业
改善
原因追究
13
如何进行现场改善
3-2 从作业改善到设备改善
① 作业改善 (A) 作业步骤、组合的改变 (B) 物品摆放, 作业工具及作业台摆放的改变 (C)简单的小工具, 滑道, 自动弹出, 吊具等的安装、改变等 (D) 改善现有设备
=面
(d) 公司的改善
= 立方体
27
如何进行现场改善
3 1
③ 总结
(a) 改善从观察现场开始
(b) 要热爱改善
(c) 事实胜于雄辩,实践是首要
改善是细而慢 不如粗而快! 不动则无成功!
28
如何进行现场改善
3 2
Ⅳ. 标准作业的制作
1. 标准作业的再确认
1-1 标准作业是现场改善的原点, 不标准的地方不存在改善.
[2] 设备是瓶颈的时候
1. 不要让瓶颈工位闲下来 2. 将按启动钮的时间提前 3. 缩小送料行程(快送, 切削送料) 4. 使机器动作叠加起来,看 是否能缩短加工以外的时间 5. 加快快送, 快退的速度
2 5
22
如何进行现场改善
好的排位的思考方法
(A) 考虑了流线的排位 ― 有灵活性的排位 ― 可根据变化移动
生产过 剩的浪 费
加工的 浪费
4
如何进行现场改善 Ⅱ. 生产方法的两大支柱
1. Just-In-Time的生产
1-1 使工序流线化
S・P・S
新技术生产体系
生产现场改善及效率提升76页PPT

谢谢
11、越是没有本领的就越加自命不凡。——邓拓 12、越是无能的人,越喜欢挑剔别人的错儿。——爱尔兰 13、知人者智,自知者明。胜人者有力,自胜者强。——老子 14、意志坚强的人能把世界放在手中像泥块一样任意揉捏。——歌德 15、最具挑战性的挑战莫过于提升自我。——迈克尔·F·斯特利
1、不要轻言放弃,否则对不起自己。
2、要冒一次险!整个生命就是一场冒险。走得最远的人,常是愿意 去做,并愿意去冒险的人。“稳妥”之船,从未能从岸边走远。-戴尔.卡耐基。
梦 境
3、人生就像一杯没有加糖的咖啡,喝起来是苦涩的,回味起来却有 久久不会退去的余香。
生产现场改善及效率提升 4、守业的最好办法就是不断的发展。 5、当爱不能完美,我宁愿选择无悔,不管来生多么美丽,我不愿失 去今生对你的记忆,我不求天长地久的美景,我只要生生世世的轮 回里有你。
精益生产系列现场管理和改善PPT
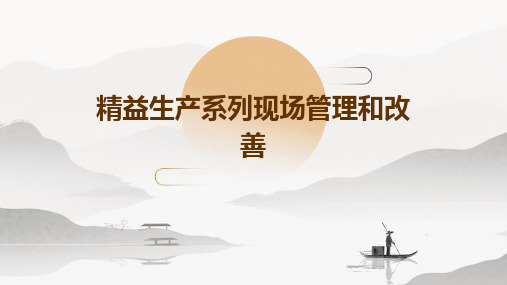
制定物品定置管理的标准操作流程,确保员 工能够按照标准执行。
目视化管理
01
视觉识别
利用颜色、图形、文字等视觉元素, 使信息传递更加直观。
异常预警
通过红、黄、绿等颜色标识,及时 发现异常情况并进行处理。
03
02
标准化操作流程
通过可视化的方式展示操作步骤和 要点,提高工作效率。
目视化沟通
促进员工之间的信息交流和协作, 提高整体工作效率。
生产布局优化
• 总结词:通过合理规划生产布局,降低物料搬运成本和时间。
• 详细描述:生产布局是指生产设备和人员在工作场所的布局方式。合理的生产布局可以降低物料搬运成本和时间,提高 生产效率。在传统生产模式下,设备和人员布局可能存在不合理之处,导致物料搬运距离过长、时间浪费等问题。通过 优化生产布局,企业可以将设备和人员集中在一起,减少物料搬运距离和时间。这不仅可以降低生产成本,还可以提高 产品质量和客户满意度。为了实现生产布局优化,企业需要对工作场所进行重新规划和设计,并加强员工培训和标准化 操作。
跨部门协作与沟通
加强部门间的沟通和协作, 共同推进持续改进工作。
培训与知识分享
开展相关培训和知识分享 活动,提高员工的质量意 识和持续改进能力。
05
员工参与与多技能培养
员工建议系统
鼓励员工提出改进意见
建立一个平台或渠道,让员工可以随时提出对生产流程、设备、 工作环境等方面的改进意见。
定期评审与实施
持续学习与发展
鼓励员工持续学习和提升,提供进一步培训和认证的机会,促进 个人职业发展。
员工激励措施
薪酬激励
提供具有竞争力的薪酬待遇,激励员工努力工作。
晋升机会
为员工提供明确的晋升通道和机会,激发员工的 积极性和工作动力。
目视化管理
01
视觉识别
利用颜色、图形、文字等视觉元素, 使信息传递更加直观。
异常预警
通过红、黄、绿等颜色标识,及时 发现异常情况并进行处理。
03
02
标准化操作流程
通过可视化的方式展示操作步骤和 要点,提高工作效率。
目视化沟通
促进员工之间的信息交流和协作, 提高整体工作效率。
生产布局优化
• 总结词:通过合理规划生产布局,降低物料搬运成本和时间。
• 详细描述:生产布局是指生产设备和人员在工作场所的布局方式。合理的生产布局可以降低物料搬运成本和时间,提高 生产效率。在传统生产模式下,设备和人员布局可能存在不合理之处,导致物料搬运距离过长、时间浪费等问题。通过 优化生产布局,企业可以将设备和人员集中在一起,减少物料搬运距离和时间。这不仅可以降低生产成本,还可以提高 产品质量和客户满意度。为了实现生产布局优化,企业需要对工作场所进行重新规划和设计,并加强员工培训和标准化 操作。
跨部门协作与沟通
加强部门间的沟通和协作, 共同推进持续改进工作。
培训与知识分享
开展相关培训和知识分享 活动,提高员工的质量意 识和持续改进能力。
05
员工参与与多技能培养
员工建议系统
鼓励员工提出改进意见
建立一个平台或渠道,让员工可以随时提出对生产流程、设备、 工作环境等方面的改进意见。
定期评审与实施
持续学习与发展
鼓励员工持续学习和提升,提供进一步培训和认证的机会,促进 个人职业发展。
员工激励措施
薪酬激励
提供具有竞争力的薪酬待遇,激励员工努力工作。
晋升机会
为员工提供明确的晋升通道和机会,激发员工的 积极性和工作动力。
车间深入管理提效 ppt课件

1.合理的预估 2.量试效率 3.使用者付费 4.落实资源使用 监督
制造/生管
制造/工程
原因多元的管理 盲点:
1.非主要材料断 料才是问题
2. 前制程排配 与质量造成 待料
3. 人力安排
生管/品管/工程
✓ 断料与待料是 制造需要严格 督促生管与质 量单位
✓ 工程单位消耗 制造资源的管 理
✓ 快速换线是持 续改善的机会
C D E ACD
E A
setup
1
Click to add工T时itle说明
项目
总时间 负荷时间 作业时间 标准产出工时
说明
设备可提供的总时间 可用于排产的时间
公式
周:7D*24H; 月:日历天数*24H
总时间-未排配
用于生产的时间
总时间-停机时间-未排配
生产产品所耗用的时间 产品数量*T.T/3600
3 准Cl确ick数to a据dd收Tit集le 及机制运作
1.详细生产记录 2.异常处理流程 3.一套表单 4.各司其职 5.资讯化系统
4 Click to aIEdd七Tit大le 手法
①流程法 ②人机法 ③动改法 ④双手法 ⑤防呆法 ⑥五五法 ⑦抽查法
4 ClicIkEto手ad法d T一itle﹕流程法
Uti li n z1atTio ot.oaR pl eurna.ttiimoen Run Set uEpng
Utilizn2atTioo.toaplera .titm ioen Run
Utilizan3tioUpDown
2 Cl满ick载to稼ad动d T率itle/设备可动率
满产稼动率是指设备可提供的最大产能状况下的稼动率
标准良品产出工时 生产良品所耗用的工时 良品数量*T.T/3600
制造/生管
制造/工程
原因多元的管理 盲点:
1.非主要材料断 料才是问题
2. 前制程排配 与质量造成 待料
3. 人力安排
生管/品管/工程
✓ 断料与待料是 制造需要严格 督促生管与质 量单位
✓ 工程单位消耗 制造资源的管 理
✓ 快速换线是持 续改善的机会
C D E ACD
E A
setup
1
Click to add工T时itle说明
项目
总时间 负荷时间 作业时间 标准产出工时
说明
设备可提供的总时间 可用于排产的时间
公式
周:7D*24H; 月:日历天数*24H
总时间-未排配
用于生产的时间
总时间-停机时间-未排配
生产产品所耗用的时间 产品数量*T.T/3600
3 准Cl确ick数to a据dd收Tit集le 及机制运作
1.详细生产记录 2.异常处理流程 3.一套表单 4.各司其职 5.资讯化系统
4 Click to aIEdd七Tit大le 手法
①流程法 ②人机法 ③动改法 ④双手法 ⑤防呆法 ⑥五五法 ⑦抽查法
4 ClicIkEto手ad法d T一itle﹕流程法
Uti li n z1atTio ot.oaR pl eurna.ttiimoen Run Set uEpng
Utilizn2atTioo.toaplera .titm ioen Run
Utilizan3tioUpDown
2 Cl满ick载to稼ad动d T率itle/设备可动率
满产稼动率是指设备可提供的最大产能状况下的稼动率
标准良品产出工时 生产良品所耗用的工时 良品数量*T.T/3600
- 1、下载文档前请自行甄别文档内容的完整性,平台不提供额外的编辑、内容补充、找答案等附加服务。
- 2、"仅部分预览"的文档,不可在线预览部分如存在完整性等问题,可反馈申请退款(可完整预览的文档不适用该条件!)。
- 3、如文档侵犯您的权益,请联系客服反馈,我们会尽快为您处理(人工客服工作时间:9:00-18:30)。
天
50 10
天
30 6
小时 75 15
小时 50 10
个
5
千件 25 5 千件 20 4
万元 10 2
米/件 30 6
%
60 10
%
+50 10
%
50 10
20
30
40
50
12
18
24
30
30
45
60
75
20
30
40
50
2
5
10
15
20
25
8
12
16
20
4
6
8
10
12
18
24
30
20
35
50
60
20
管建伟
13
现场管理的 “A B C” 法
把现场所看到的东西或感想用笔记下来 把自己希望改进或与要求不符的部分分为 A B C 三级 A 是明天马上要改善的 B 是一周后需要改善的 C 是一个月后计划改善的 策划具体改善措施 检查改善情况并予以奖励
2020/7/26
管建伟
14
管理的根本 在于不断改善
2020/7/26
管建伟
16
_____车间1-5月管理目标改善计划表
序
计划改善项目
1月
2月
3月
4月
5月划
实计 绩划
实计 绩划
实 绩
加权 平均
1 交货期 2 生产周期 3 改机时间 4 停机时间 5 操作人员数 6 在制品数量 7 零部件(半成品)数量 8 库存品总额 9 搬运距离 10 不合格品发生率 11 一次交验合格率 12 返工返修品
现场改善与生产效率提升
1
标题添加
点击此处输入相 关文本内容
标题添加
点击此处输入相 关文本内容
总体概述
点击此处输入 相关文本内容
点击此处输入 相关文本内容
2
生产管理的铁三角
D
交
成
期 安全 本
Q
C
质量
用最低的成本 符合要求的质量 达成规定的交期
2020/7/26
管建伟
3
企业管理面临的共同难题
内部 救火式生产 质量不稳定 浪费严重
2020/7/26
管建伟
12
现场管理的“五字检查”法
听 听设备运转过程中是否有异常声音
摸 有无异常的发热或抖动、振动等现象
查
监测,关键、特殊工序受控情况 油管阀门等有无跑、冒、滴、漏数据
看
有无松动、晃动、移动、错位、开裂、缺损现象 设备运行参数是否符合规定要求
闻
有无泄漏或其他引起的焦味、异常气味
2020/7/26
现阶段的IE(工业工程)的主要工作范围大致是: 价值分析、动作分析、工程分析、时间分析、平面布 置、搬运设计、可视化管理、员工多能化、快速换模等
2020/7/26
管建伟
19
工业工程可以让生活与工作井然有序
北京市某机构的办事人潮不断,要办事有排不完的队;领表要排队、 申办要排队、照相要排队、缴费要排队、领证要排队。由于当时设计并 未考虑到现在的人潮,而现在的需求已经远超过几年前的情况,所以排 队的空间、设施以及规则都已经不适用。因此几乎每天都发生这样的情 况:让有礼貌的市民排得心烦意乱,让急着办事的市民直跺脚,让不守 规矩的人拼命钻空子;甚至因排队起的争吵与冲突此起彼落。
人员流动大
2020/7/26
管建伟
外部 小批量 多品种 低价格 快交货
4
以最少的投入来获取最大的产出
最少资金 最少人力 5M 最少设备 最少材料 最佳方法
2020/7/26
管建伟
P 最佳品种 Q 最优质量 C 最低成本 D 准时交货 S 安全环保 M 良好情绪
5
为什么要加强生产 现场管理?
2020/7/26
2020/7/26
管建伟
8
生产现场管理普遍存在问题
生产无计划 质量无标准 作业无方法 堆放无区域 物品无标识
消耗无定额 过程无记录
2020/7/26
管建伟
9
现场管理的五大要素(4M1E)
人
思想意识 配合度 能力 个体差异
设备
设备功能 精确度 设备能力 故障预警
材料
及时 适宜 合格
方法
方法合理 过程受控 标准化
30
40
50
20
30
40
50
2020/7/26
管建伟
17
在当今的工业时代,用“农业头脑”办事 肯定是不行的,但也不是一步跨越到“电子计 算机头脑”就行得通。在“农业头脑”和“电 子计算机头脑”之间应该还应该有一个“工业 头脑”的时代。
2020/7/26
管建伟
18
IE工业工程简介
工业工程(IE)是一门应用科学,它将传统的工程 技术融合于现代的科学管理技巧之中 ,弥补原有管理 及工程技术之脱节。IE是藉着设计、改善或设定人、料 机的工作系统,以求得到更高生产力的专门技术。IE要 求以工程技术为基础,配合科学管理的技巧来发现问题、 解决问题、预防问题。
许振超的技术研究工作: 许振超和队员们在桥吊每个操作环节抠时间。桥吊启动时,说明书上写 着,达到最高时速需要5秒钟,许振超计算后提出,3.5秒钟就够用,一 些司机不以为然地提出,抠.1.5秒有什么用?许振超为大家算了一笔账: “如果一船有1000个集装箱,就能节约25分钟出来”。
管建伟
6
现场管理的五项要求
一、当问题发生时,要先去现场; 二、检查现物(有关的物品); 三、当场采取暂行处置措施; 四、发掘真正原因并将其排除; 五、标准化以防止再发生。
2020/7/26
管建伟
7
案例分析
某班组自动车床经常发生故障,维修人员 只能通过维修和更换备件解决故障。目前该设 备故障平均约每半年发生一次,主要原因是主 轴轴承发生故障,一套轴承的备件价格为3000 元,每年更换备件费用达6000元。如何应用 “五问”活动对主轴轴承故障的原因进行分析。
一个流
生产过程“一个流”
一天班长 员工多能化培养
2020/7/26
管建伟
11
现场管理的“三五”要求
操作“五按”: 按图纸、按标准、按程序、按时间、按操作指令
工作“五干”: 干什么、怎么干、什么时间干、按什么方法干、 干到什么程度
结果“五查”: 由谁来检查、什么时间检查、检查什么项目、检 查的标准是什么、检查的结果由谁来落实
环境
温度 湿度 灰尘 污染
2020/7/26
管建伟
10
现场管理的“单一最好”原则
一处保管 户口管理
一日处理 今日事,今日毕
一个资料夹 资料夹一册化
一小时会议 一事一议,半小时更好
一张纸
报告、表格一张篇幅完全表达
一分钟电话 长话短说,不拖泥带水
一件工具 多样工具简化成一件
一个单元 在一个小组或一组设备内完工
改善
维持
改善的能力 是评价管理者的重要基 准
2020/7/26
管建伟
15
改善的十条基本原则
1、“存在的都是不合理的” 2、强调理由是不思进取的表现 3、立即改进,及时比正确更重要 4、反复追问为什么,总能找到问题根源 5、许多问题的解决,就在于否定不可能 6、更应该重视的是不花大钱的改善 7、不要追求完美,完美都是从不完美开始的 8、最清楚改善的是处于第一线的操作人员 9、只要是改善,最小的事也值得去做 10、改善永无止境,没有最好,只有更好