数控木工雕刻机对刀的目的和步骤
数控机床对刀的方式及其对刀步骤

在进行加工之前,数控车床要进行对刀操作,以便确保产品加工的精度以及准度,在实际进行生产的过程中,数控车床对刀的操作有试切对刀和机外对刀仪这两种对刀方法,但是在进行对刀操作的时候也会出现一些问题,下面我们就来具体介绍一下数控车床对刀的操作步骤。
1、试切对刀试切对刀主要用在建立加工坐标系。
在安装好工件后,为了可以加工出需要的加工件,要将编程原点设定为加工原点,建立加工坐标系,用来确定刀具和工件的相对位置,使刀具按照编程轨迹进行运动,最终加工出所需零件。
试切对刀的步骤主要有:(1)选择机床的手动操作模式;(2)启动主轴,试切工件外圆,保持X方向不移动;(3)停主轴,测量出工件的外径值;(4)选择机床的MDI操作模式;(5)按下“off set sitting”按钮;(6)按下屏幕下方的“坐标系”软键;(7)光标移至“G54”;(8)输入X及测量的直径值;(9)按下屏幕下方的“测量”软键;(10)启动主轴,试切工件端面,保持Z方向不移动;2、机外对刀仪对刀机外对刀仪对刀需要将显微对刀仪固定于车床上,用于建立刀具之间的补偿值。
但是因为刀具尺寸会有一定差别,机床中刀位点的坐标值也会因此而出现不同。
如果不设立刀具之间的补偿值,运行相同的程序时就不可能加工出相同的尺寸,想要保证运行相同的程序时,运用不同的刀具得出相同的尺寸,则需要建立刀具间的补偿。
机外对刀仪对刀的步骤主要有:(1)移动基准刀,让刀位点对准显微镜的十字线中心;(2)将基准刀在该点的相对位置清零,具体操作是选择相对位置显示;(3)将其刀具补偿值清零,具体操作是按下“off set sitting”按钮,按下屏幕下方的“补正”软键,选择“形状”,在基准刀相对应的刀具补偿号上输入Xo、Zo;(4)选择机床的手动操作模式,移出刀架,换刀;(5)使其刀位点对准显微镜的十字线中心;(6)选择机床的MDI操作模式;(7)设置刀具补偿值,具体操作是按下“offset sitting”按钮,按下屏幕下方的“补正”软键,选择“形状”,在相对应的刀补号上输入X、Z;(8)移出刀架,执行自动换刀指令即可。
雕刻机对刀仪设备工艺原理
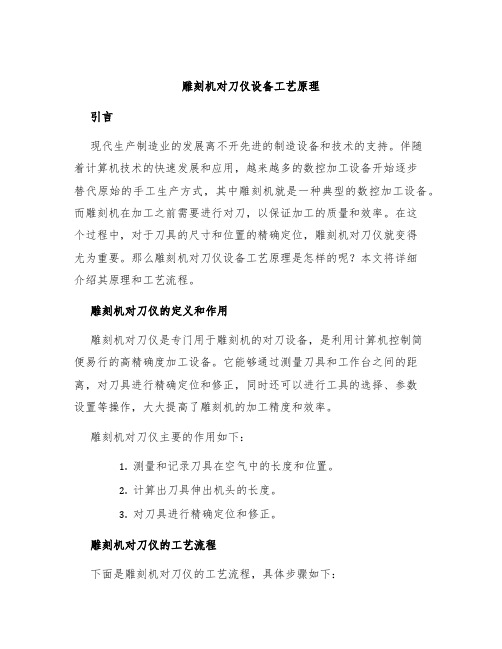
雕刻机对刀仪设备工艺原理引言现代生产制造业的发展离不开先进的制造设备和技术的支持。
伴随着计算机技术的快速发展和应用,越来越多的数控加工设备开始逐步替代原始的手工生产方式,其中雕刻机就是一种典型的数控加工设备。
而雕刻机在加工之前需要进行对刀,以保证加工的质量和效率。
在这个过程中,对于刀具的尺寸和位置的精确定位,雕刻机对刀仪就变得尤为重要。
那么雕刻机对刀仪设备工艺原理是怎样的呢?本文将详细介绍其原理和工艺流程。
雕刻机对刀仪的定义和作用雕刻机对刀仪是专门用于雕刻机的对刀设备,是利用计算机控制简便易行的高精确度加工设备。
它能够通过测量刀具和工作台之间的距离,对刀具进行精确定位和修正,同时还可以进行工具的选择、参数设置等操作,大大提高了雕刻机的加工精度和效率。
雕刻机对刀仪主要的作用如下:1.测量和记录刀具在空气中的长度和位置。
2.计算出刀具伸出机头的长度。
3.对刀具进行精确定位和修正。
雕刻机对刀仪的工艺流程下面是雕刻机对刀仪的工艺流程,具体步骤如下:1.安装刀具:将需要使用的刀具安装在机头上面。
2.停车位置设置:在加工前,需要先设置停车位置,将刀具抬起到空气中,避免意外碰到工作台。
3.机头下降:机头下降到刀具表面,一般需要使用快速下降,然后再使用慢速下降,使刀具接触到检测感应器。
4.雕刻机对刀仪测量:测量刀具在空气和工作台之间的距离,通常雕刻机对刀仪会通过使用机械开关或感应器测量出刀具位置。
5.计算刀具长度:通过测量,计算刀具伸出机头的长度。
6.对刀具进行修正:对刀具进行精确定位和修正。
雕刻机对刀仪的工艺原理雕刻机对刀仪的工艺原理主要是以测量刀具长度和位置为核心,包括机械和光电两种检测方法。
机械式检测方法机械式是将检验仪械放在刀头上,当触到工作台时,其测定刀头和工作台之间的距离,以确定刀头的位置、长度和高度。
机械式检测方法可以通过机构变化实现,即通过加装靠尺、刀片等机械装置来对刀,这样能避免使用显微镜的微小测量误差,精度相对高一些。
简述数控机床对刀的过程和注意哪些方面

数控机床对刀的过程和注意事项一、什么是数控机床对刀在使用数控机床进行加工过程中,正确的对刀操作是非常重要的。
数控机床对刀是指通过一系列的操作和调整,使刀具与工件之间达到理想的对刀状态,以便正常加工工件。
这个过程中还需要注意一些关键事项,以确保加工质量和安全。
二、数控机床对刀的过程数控机床对刀的过程可以分为以下几个步骤:1. 设定参考点首先,需要设定一个参考点作为对刀的基准点。
通常情况下,参考点会选择工件的一个角点或者边缘作为基准。
2. 加工刀具的设定接下来,需要对加工刀具进行设定。
这包括选择合适的切削刃、确定刀具安装位置以及设定刀具的刀尖与刀夹的距离。
3. 对刀工具的设定然后,需要对刀具进行设定。
这包括调整刀具的刀尖高度、刀具的半径补偿以及切削刃的长度设定。
4. 加工路径的设定在对刀过程中,还需要设置加工路径。
这包括确定刀具的进给速度、切削速度以及确定刀具的运动轨迹。
完成设置后,需要对刀具进行检查。
通过测量刀具的位置和角度,确定切削刃是否正确对准工件表面。
如果发现偏差,需要进行微调,直到达到理想的对刀状态。
6. 再次验证和修正最后,对刀完成后,需要再次验证对刀的准确性。
这可以通过测量加工后的工件尺寸和形状来进行验证。
如果出现偏差,需要进行修正,直到达到要求的加工精度。
三、数控机床对刀的注意事项在进行数控机床对刀的过程中,需要注意以下几个方面:1. 安全注意事项•在对刀过程中,必须确保机床处于安全状态,刀具处于停止状态。
避免对刀时发生意外伤害。
•切勿用手直接接触刀具,以免被刀具伤到。
应使用合适的工具进行调整和检查。
2. 刀具的选择和安装•根据加工工件的要求选择合适的切削刃和刀具。
不同的加工材料和工件形状需要选择不同的刀具。
•在安装刀具时,要确保刀具正确安装,不可有松动或倾斜现象。
否则可能导致加工精度下降或刀具偏差。
3. 对刀工具的设定•在对刀工具的设定过程中,应使用合适的测量工具进行测量和调整。
确保对刀工具的准确性和稳定性。
数控对刀原理

数控对刀原理数控对刀是数控加工中非常重要的一环,它直接影响到加工精度和加工效率。
数控对刀原理是指在数控机床上进行刀具对刀的方法和原理。
正确的数控对刀原理能够保证刀具的正确安装和定位,从而确保加工的精度和质量。
下面将介绍数控对刀的原理及其操作方法。
数控对刀原理主要包括以下几个方面,刀具长度的补偿、刀具半径的补偿、刀具偏移的补偿和刀具的安装和定位。
首先是刀具长度的补偿,数控系统可以通过输入刀具的实际长度和系统中设定的长度进行补偿,从而保证刀具的正确位置。
其次是刀具半径的补偿,数控系统可以通过输入刀具的实际半径和系统中设定的半径进行补偿,确保刀具的加工轨迹正确。
再次是刀具偏移的补偿,数控系统可以通过输入刀具的实际偏移量和系统中设定的偏移量进行补偿,保证刀具的加工位置准确。
最后是刀具的安装和定位,操作人员需要根据加工工件的要求,正确安装刀具并进行定位,确保刀具的位置和方向正确。
在进行数控对刀时,操作人员需要按照以下步骤进行操作,首先是准备工作,包括检查刀具和夹具的状态,确保刀具和夹具的完好无损。
其次是选择合适的对刀工具,根据加工工件的要求选择合适的对刀工具。
然后是进行刀具长度的补偿,根据实际情况输入刀具的实际长度和系统中设定的长度进行补偿。
接着是进行刀具半径的补偿,输入刀具的实际半径和系统中设定的半径进行补偿。
再次是进行刀具偏移的补偿,输入刀具的实际偏移量和系统中设定的偏移量进行补偿。
最后是安装刀具并进行定位,根据加工工件的要求,正确安装刀具并进行定位,确保刀具的位置和方向正确。
总之,数控对刀原理是数控加工中非常重要的一环,它直接影响到加工精度和加工效率。
正确的数控对刀原理能够保证刀具的正确安装和定位,从而确保加工的精度和质量。
操作人员在进行数控对刀时需要严格按照操作步骤进行,确保对刀的准确性和可靠性。
只有这样,才能保证数控加工的顺利进行,达到预期的加工效果。
数控机床对刀的原理分析以及常用对刀方法

数控机床对刀的原理分析以及常用对刀方法进行数控加工时,数控程序所走的路径均是主轴上刀具的刀尖的运动轨迹。
刀具刀位点的运动轨迹自始至终需要在机床坐标系下进行精确控制,这是因为机床坐标系是机床唯一的基准。
编程人员在进行程序编制时不可能知道各种规格刀具的具体尺寸,为了简化编程,这就需要在进行程序编制时采用统一的基准,然后在使用刀具进行加工时,将刀具准确的长度和半径尺寸相对于该基准进行相应的偏置,从而得到刀具刀尖的准确位置。
所以对刀的目的就是确定刀具长度和半径值,从而在加工时确定刀尖在工件坐标系中的准确位置。
对刀仪演示视频(时长1分10秒,建议wifi下观看)一、对刀的原理和对刀中出现的问题1、刀位点刀位点是刀具上的一个基准点,刀位点相对运动的轨迹即加工路线,也称编程轨迹。
2、对刀和对刀点对刀是指操作员在启动数控程序之前,通过一定的测量手段,使刀位点与对刀点重合。
可以用对刀仪对刀,其操作比较简单,测量数据也比较准确。
还可以在数控机床上定位好夹具和安装好零件之后,使用量块、塞尺、千分表等,利用数控机床上的坐标对刀。
对于操作者来说,确定对刀点将是非常重要的,会直接影响零件的加工精度和程序控制的准确性。
在批生产过程中,更要考虑到对刀点的重复精度,操作者有必要加深对数控设备的了解,掌握更多的对刀技巧。
(1)对刀点的选择原则在机床上容易找正,在加工中便于检查,编程时便于计算,而且对刀误差小。
对刀点可以选择零件上的某个点(如零件的定位孔中心),也可以选择零件外的某一点(如夹具或机床上的某一点),但必须与零件的定位基准有一定的坐标关系。
提高对刀的准确性和精度,即便零件要求精度不高或者程序要求不严格,所选对刀部位的加工精度也应高于其他位置的加工精度。
选择接触面大、容易监测、加工过程稳定的部位作为对刀点。
对刀点尽可能与设计基准或工艺基准统一,避免由于尺寸换算导致对刀精度甚至加工精度降低,增加数控程序或零件数控加工的难度。
6数控车床的对刀操作

说明Z坐标已经对好!
6、检验
1、粗略检验 手轮方式下移动刀具至工件右端面,按位置键看看 工件X、Z坐标是否接近0。 2、精确检验 录入方式下输入程序段检验。
光标移动至X值——通过面板的MDI键盘编辑区输入X24——出现下 图所示情况
按测量对应的F2键——按POS按键——出现下图
说明X轴已经对好。
2、对Z轴:
启动主轴——移动刀具车工件端面——保证Z坐标值不动—— 移动X轴远离工件——光标移动至Z值——输入Z0——按F2测量
按POS按键——出现下图
4、对刀的方法
三种方法: 1、光学对刀法
2、定位对刀法 3、试切对刀法(掌握)
5、试切对刀法
1、对X轴 启动主轴——车削工件外圆——保证X坐标值不变——移动Z轴 ——刀具远离工件——停止主轴——测量刚车削的工件直径
假设测量结果为Ф24mm——按OFS/SET按键——出现下图画面
再按F2按键——出现下图画面
数控车床的对刀操作P27
相互学习、相互提高、共同进步
1、对刀概念
什么是对刀? 在加工程序执行前,调整每把刀的刀 位点,使其尽量重合于某一理想基准点 ,这一过程就叫对刀。
2、刀位点Байду номын сангаас
刀位点就是在加工程序编制中,用以 表示刀具特征的点,也是对刀和加工的 基准点。
3、对刀的作用
对刀是数控加工中的主要操作和重要 技能,在一定条件下,对刀的精度可以 决定零件的加工精度,同时,对刀效率 还直接影响数控加工效率。
对刀对机床加工的重要性和对刀方法介绍
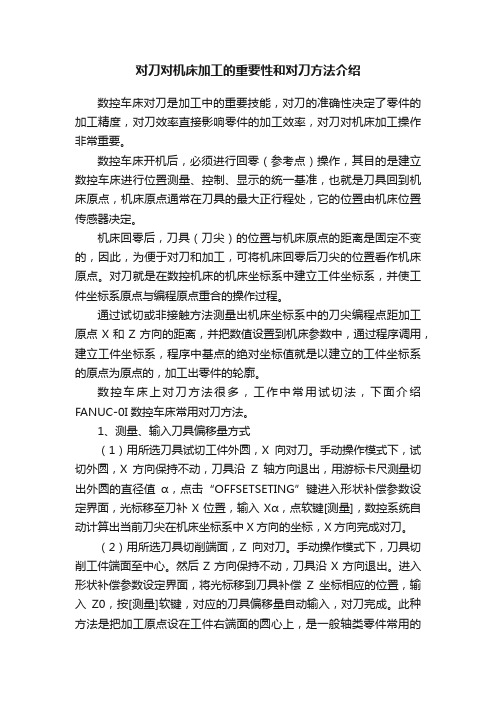
对刀对机床加工的重要性和对刀方法介绍数控车床对刀是加工中的重要技能,对刀的准确性决定了零件的加工精度,对刀效率直接影响零件的加工效率,对刀对机床加工操作非常重要。
数控车床开机后,必须进行回零(参考点)操作,其目的是建立数控车床进行位置测量、控制、显示的统一基准,也就是刀具回到机床原点,机床原点通常在刀具的最大正行程处,它的位置由机床位置传感器决定。
机床回零后,刀具(刀尖)的位置与机床原点的距离是固定不变的,因此,为便于对刀和加工,可将机床回零后刀尖的位置看作机床原点。
对刀就是在数控机床的机床坐标系中建立工件坐标系,并使工件坐标系原点与编程原点重合的操作过程。
通过试切或非接触方法测量出机床坐标系中的刀尖编程点距加工原点X和Z方向的距离,并把数值设置到机床参数中,通过程序调用,建立工件坐标系,程序中基点的绝对坐标值就是以建立的工件坐标系的原点为原点的,加工出零件的轮廓。
数控车床上对刀方法很多,工作中常用试切法,下面介绍FANUC-0I数控车床常用对刀方法。
1、测量、输入刀具偏移量方式(1)用所选刀具试切工件外圆,X向对刀。
手动操作模式下,试切外圆,X方向保持不动,刀具沿Z轴方向退出,用游标卡尺测量切出外圆的直径值α,点击“OFFSETSETING”键进入形状补偿参数设定界面,光标移至刀补X位置,输入Xα,点软键[测量],数控系统自动计算出当前刀尖在机床坐标系中X方向的坐标,X方向完成对刀。
(2)用所选刀具切削端面,Z向对刀。
手动操作模式下,刀具切削工件端面至中心。
然后Z方向保持不动,刀具沿X方向退出。
进入形状补偿参数设定界面,将光标移到刀具补偿Z坐标相应的位置,输入Z0,按[测量]软键,对应的刀具偏移量自动输入,对刀完成。
此种方法是把加工原点设在工件右端面的圆心上,是一般轴类零件常用的方法。
如果是左右对称零件,需把加工原点设在工件的对称中心,则输入Zβ,β为零件轴向长度的一半。
然后根据刀具的几何尺寸和安装位置输入刀尖圆弧半径R和刀位号T的值,例如:一号刀,刀尖圆弧半径R=0.8mm,将光标移至R下方1号刀对应的位置,键入0.8,在T对应位置输入刀位号,按“INPUT”输入,即可用来加工。
数控车床对刀的原理及方法
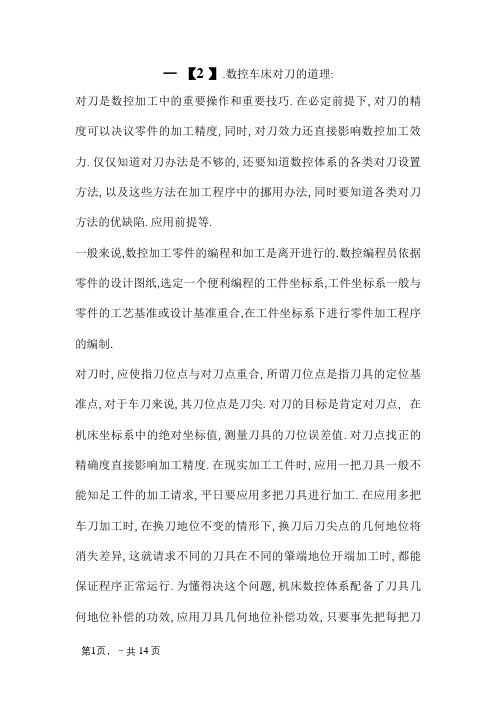
一【2 】.数控车床对刀的道理:对刀是数控加工中的重要操作和重要技巧.在必定前提下,对刀的精度可以决议零件的加工精度,同时,对刀效力还直接影响数控加工效力.仅仅知道对刀办法是不够的,还要知道数控体系的各类对刀设置方法,以及这些方法在加工程序中的挪用办法,同时要知道各类对刀方法的优缺陷.应用前提等.一般来说,数控加工零件的编程和加工是离开进行的.数控编程员依据零件的设计图纸,选定一个便利编程的工件坐标系,工件坐标系一般与零件的工艺基准或设计基准重合,在工件坐标系下进行零件加工程序的编制.对刀时,应使指刀位点与对刀点重合,所谓刀位点是指刀具的定位基准点,对于车刀来说,其刀位点是刀尖.对刀的目标是肯定对刀点, 在机床坐标系中的绝对坐标值,测量刀具的刀位误差值.对刀点找正的精确度直接影响加工精度.在现实加工工件时,应用一把刀具一般不能知足工件的加工请求,平日要应用多把刀具进行加工.在应用多把车刀加工时,在换刀地位不变的情形下,换刀后刀尖点的几何地位将消失差异,这就请求不同的刀具在不同的肇端地位开端加工时,都能保证程序正常运行.为懂得决这个问题,机床数控体系配备了刀具几何地位补偿的功效,应用刀具几何地位补偿功效,只要事先把每把刀相对于某一预先选定的基准刀的地位误差测量出来,输入到数控体系的刀具参数补正栏指定组号里,在加工程序中应用T 指令,即可在刀具轨迹中主动补偿刀具地位误差.刀具地位误差的测量同样也需经由过程对刀操作来实现.临盆厂家在制作数控车床,必须树立地位测量.掌握.显示的同一基准点,该基准点就是机床坐标系原点,也就是机床机械回零后所处的地位.数控机床所设置装备摆设的伺服电机有绝对编码器和相对编码器两种,绝对编码器的开机不用回零,体系断电跋文忆机床地位,机床零点由参数设定.相对编码器的开机必须回零,机床零点由机床地位传感器肯定.编程员按工件坐标系中的坐标数据编制的刀具运行轨迹程序,必须在机床坐标系中加工,因为机床原点与工件原点消失X向偏移距离和Z向偏移距离,使得现实的刀尖地位与程序指令的地位有同样的偏移距离,是以,须将该距离测量出来并设置进数控体系,使体系据此调剂刀具的活动轨迹,才能加工出相符零件图纸的工件.这个进程就是对刀,所谓对刀其本质就是测量工件原点与机床原点之间的偏移距离,设置工件原点在以刀尖为参照的机床坐标系里的坐标.二.对刀办法对刀的办法有许多种,按对刀的精度可分为粗略对刀和精确对刀;按是否采用对刀仪可分为手动对刀和主动对刀;按是否采用基准刀,又可分为绝对对刀和相对对刀等.但无论采用哪种对刀方法,都离不开试切对刀,试切对刀是最根本的对刀办法.1.数控车床试车对刀办法图1(1)如图1,夹持工件,换须要对的刀具到刀架当前位..图2(2)如图2,在手动操作方法下,启动主轴,用当前刀具在加工余量规模内试切工件外圆,车的长度必须可以或许便利测量,X轴不要移动,沿Z的正偏向退出来,停主轴,测量所车的外圆尺寸Xa,如图3.图3(3)按“OFS/SET”键如图4,按刀偏如图5,将光标移到与刀具号相对应的地位后,输入“Xa”,如图6,按操作面板上的“刀具测量”,再按显示器下面的软键“测量”,在对应的刀补位上生成对应刀补值.图4留意:刀具补偿包括“磨损”和“外形”补偿两部分,刀偏分外形和磨损,刀尖的地位放在外形里,尺寸的调剂和刀具的磨耗放在磨损里.两者之和组成车刀偏移量补偿参数.如图5显示.图5图6(4)如图7在手动方法下,再用该把刀去平工件端面,平完端面后,沿X正偏向退出来,Z偏向不动,停主轴,测量工件原点到工件端面的距离Lz.图7(5)同(3)一样.按“OFS/SET”键,进入“外形”补偿设定界面,将光标移到与刀位号相对应的地位后,输入“Lz”,按操作面板上的“刀具测量”,再按显示器下面的软键“测量”,在对应的刀补位上生成精确的刀补值.(6)当前刀具对刀完毕好,换程序中须要用到的其他刀具,反复(1)到(5)进程,生成响应的刀补.加工中间对刀对刀的本质是肯定程序原点在机床坐标系中的地位.对刀消失误差,对刀误差在某种程度内是许可产生的,也是不可避免的,但却可以尽量削减.对刀的精确程度直接影响加工精度,是以,对刀办法必定要与零件加工精度请求相顺应.当零件加工精度请求过高时可采用千分表.对刀时一般以机床主轴轴线与断面的交点为刀位点,即假设基准刀的刀长为0,其他刀的长度就是其刀补值,故无论采用哪种刀具对刀,成果都是机床主轴轴线与端面的交点与对刀点重合,应用机床的坐标显示肯定对刀点在机床坐标系中的地位,从而肯定工件坐标系在机床坐标系内的地位.再应用对刀仪肯定其他刀的长度,就解决了工件坐标系肯定问题和多刀加工时的刀补肯定问题.2 .对刀办法在数控加工中,对刀的根本办法有试切法.对刀仪对刀和主动对刀等.本文以数控铣床为例,介绍几种常用的对刀办法.2. 1 试切对刀法这种办法简略便利,但会在工件表面留下切削陈迹,且对刀精度较低.如图1 所示,以对刀点在工件表面中间地位为例采用双边对刀方法.图11) 将工件经由过程夹具装在工作台上,装夹时,工件的四个侧面都应留出对刀的地位.2) 启动主轴中速扭转,快速移动工作台和主轴,让刀具快速移动到接近工件左侧有必定安全距离的地位,然后下降速度移动至接近工件左侧.3) 接近工件时改用微调操作( 一般用0. 01 mm) 来接近,让刀具慢慢接近工件左侧,使刀具正好接触到工件左侧表面( 不雅察,听切削声音.看切痕.看切屑,只要消失一种情形即表示刀具接触到工件) ,再回退0. 01 mm.或者显示页面切换到相对坐标显示页面,将X坐标值清零.4) 沿z 正偏向退刀,至工件表面以上,用同样办法接近工件右侧,记下此时相对坐标系中显示的坐标值,如- 340. 500.5) 据此可得工件坐标系原点在机床坐标系中坐标值为-340.5/2 = -170.25.然后向左移念头床到相对坐标显示为-170.25,此时主轴中间在工件坐标系X0的地位.6)在OFFSET页面,在响应的工件坐标页面G54-G59中输入X0,按软键测量,即可生成X的工件原点坐标值,此值与此时的机械坐标值一样. 7)同理可测得Y工件坐标系原点在机床坐标系中的坐标值.Z向对刀.1) 将刀具快速移至工件上方.2) 启动主轴中速扭转,快速移动工作台和主轴,让刀具快速移动到接近工件上表面有必定安全距离的地位,然后下降速度移动让刀具端面接近工件上表面.3) 接近工件时改用微调操作( 一般用0. 01 mm) 来接近,让刀具端面慢慢接近工件表面( 留意刀具特殊是立铣刀时最好在工件边缘下刀,刀的端面接触工件表面的面积小于半圆,尽量不要使立铣刀的中间孔在工件表面下刀) ,使刀具端面正好碰着工件上表面,再将轴再举高,记下此机会床坐标系中的z 值, - 140. 400,则工件坐标系原点W 在机床坐标系中的坐标值为- 140. 400.c) 将测得的x,y,z 值输入到机床工件坐标系存储地址G5* 中( 一般应用G54 ~ G59 代码存储对刀参数) .d) 进入面板输入模式( MDI) ,输入“G5* ”,按启动键( 在主动模式下) ,运行G5* 使其生效.e) 磨练对刀是否精确.2. 2 塞尺.标准芯棒.块规对刀法此法与试切对刀法类似,只是对刀时主轴不迁移转变,在刀具和工件之间加人塞尺( 或标准芯棒.块规) ,以塞尺正好不能自由抽动为准,留意盘算坐标时如许应将塞尺的厚度减去.因为主轴不须要迁移转变切削,这种办法不会在工件表面留下陈迹,但对刀精度也不够高. 2. 3 采用寻边器.偏幸棒和轴设定器等具对刀法操作步骤与采用试切对刀法类似,只是将刀具换成寻边器或偏幸棒. 这是最常用的办法.效力高,能保证对刀精度.应用寻边器时必须当心,让其钢球部位与工件稍微接触,同时被加工工件必须是良导体,定位基准面有较好的表面光滑度.z 轴设定器一般用于转移( 间接) 对刀法.2. 4 转移( 间接) 对刀法加工一个工件常常须要用到不止一把刀,第二把刀的长度与第一把刀的装刀长度不一样,须要从新对零,但有时零点被加工失落,无法直接找回零点,或不许可损坏已加工好的表面,还有某些刀具或场合不好直接对刀,这时刻可采用间接找零的办法.a) 对第一把刀.1) 对第一把刀的时仍然先用试切法.塞尺法等.记下此时工件原点的机床坐标z1.第一把刀加工完后,停转主轴.2) 把对刀器放在机床工作台平整台面上( 如虎钳大表面) .3) 在手轮模式下,应用手摇移动工作台至合适位置,向下移动主轴,用刀的底端压对刀器的顶部,表盘指针迁移转变,最好在一圈以内,记下此时轴设定器的示数并将相对坐标轴清零.4) 确举高主轴,取下第一把刀.b) 对第二把刀.1) 装上第二把刀.2) 在手轮模式下,向下移动主轴,用刀的底端压对刀器的顶部,表盘指针迁移转变,指针指向与第一把刀雷同的示数A 地位.3) 记载此时轴相对坐标对应的数值z0( 带正负号) .4) 举高主轴,移走对刀器.5) 将本来第一把刀的G5* 里的z1坐标数据加上z0( 带正负号) ,得到一个新的坐标.6) 这个新的坐标就是要找的第二把刀对应的工件原点的机床现实坐标,将它输人到第二把刀的G5* 工作坐标中,如许,就设定好第二把刀的零点.其余刀与第二把刀的对刀办法雷同.注: 假如几把刀应用同一G5* ,则步骤5) ,6) 改为把z0存进二号刀的长度参数里,应用第二把刀加工时挪用刀长补正G43H02 即可.2. 5 顶尖对刀法a) x,y 向对刀.1) 将工件经由过程夹具装在机床工作台上,换上顶尖.2) 快速移动工作台和主轴,让顶尖移动到近工件的上方,查找工件画线的中间点,下降速度移动让顶尖接近它.3) 改用微调操作,让顶尖慢慢接近工件画线的中间点,直到顶尖尖点瞄准工件画线的中间点,记下此机会床坐标系中的x,y 坐标值.b) 卸下顶尖,装上铣刀,用其他对刀办法如试切法.塞尺法等得到z 轴坐标值.6 百分表( 或千分表) 对刀法( 一般用于圆形工件的对刀)1) x,y 向对刀.将百分表的安装杆装在刀柄上,或将百分表的磁性座吸在主轴套筒上,移动工作台使主轴中间线( 即刀具中间) 大约移到工件中间,调节磁性座上伸缩杆的长度和角度,使百分表的触头接触工件的圆周面,( 指针迁移转变约0. 1 mm) 用手慢慢迁移转变主轴,使百分表的触头沿着工件的圆周面迁移转变,不雅察百分表指针的便移情形,慢慢移动工作台的轴和轴,多次反复后,待迁移转变主轴时百分表的指针根本在同一地位( 表头迁移转变一周时,其指针的跳动量在许可的对刀误差内,如0. 02 mm) ,这时可以为主轴的中间就是轴和轴的原点.2) 卸下百分表装上铣刀,用其他对刀办法如试切法.塞尺法等得到z 轴坐标值.2. 6 专用对刀器对刀法传统对刀办法有安全性差( 如塞尺对刀,硬碰硬刀尖易撞坏) 占用机时多( 如试切需反复切量几回) ,工资带来的随机性误差大等缺陷,已经顺应不了数控加工的节拍,更不利于施展数控机床的功效.用专用对刀器对刀有对刀精度高.效力高.安全性好等长处,把繁琐的靠经验保证的对刀工作简略化了,保证了数控机床的高效高精度特色的施展,已成为数控加工机上解决刀具对刀不可或缺的一种专用对象.。
数控木工雕刻机对刀的目的和步骤
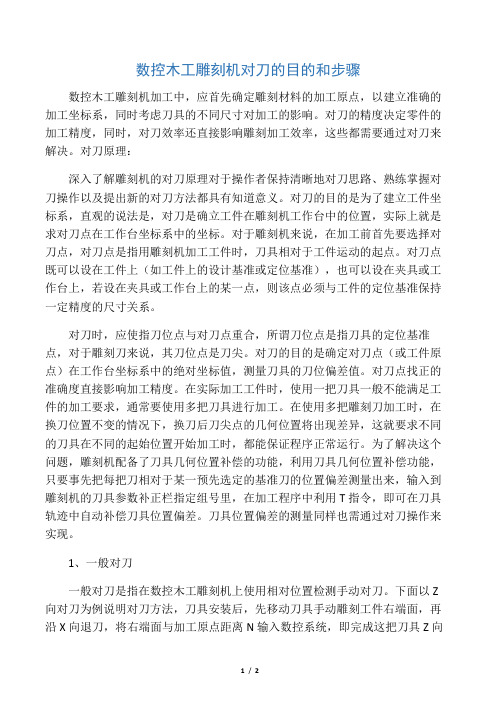
数控木工雕刻机对刀的目的和步骤数控木工雕刻机加工中,应首先确定雕刻材料的加工原点,以建立准确的加工坐标系,同时考虑刀具的不同尺寸对加工的影响。
对刀的精度决定零件的加工精度,同时,对刀效率还直接影响雕刻加工效率,这些都需要通过对刀来解决。
对刀原理:深入了解雕刻机的对刀原理对于操作者保持清晰地对刀思路、熟练掌握对刀操作以及提出新的对刀方法都具有知道意义。
对刀的目的是为了建立工件坐标系,直观的说法是,对刀是确立工件在雕刻机工作台中的位置,实际上就是求对刀点在工作台坐标系中的坐标。
对于雕刻机来说,在加工前首先要选择对刀点,对刀点是指用雕刻机加工工件时,刀具相对于工件运动的起点。
对刀点既可以设在工件上(如工件上的设计基准或定位基准),也可以设在夹具或工作台上,若设在夹具或工作台上的某一点,则该点必须与工件的定位基准保持一定精度的尺寸关系。
对刀时,应使指刀位点与对刀点重合,所谓刀位点是指刀具的定位基准点,对于雕刻刀来说,其刀位点是刀尖。
对刀的目的是确定对刀点(或工件原点)在工作台坐标系中的绝对坐标值,测量刀具的刀位偏差值。
对刀点找正的准确度直接影响加工精度。
在实际加工工件时,使用一把刀具一般不能满足工件的加工要求,通常要使用多把刀具进行加工。
在使用多把雕刻刀加工时,在换刀位置不变的情况下,换刀后刀尖点的几何位置将出现差异,这就要求不同的刀具在不同的起始位置开始加工时,都能保证程序正常运行。
为了解决这个问题,雕刻机配备了刀具几何位置补偿的功能,利用刀具几何位置补偿功能,只要事先把每把刀相对于某一预先选定的基准刀的位置偏差测量出来,输入到雕刻机的刀具参数补正栏指定组号里,在加工程序中利用T指令,即可在刀具轨迹中自动补偿刀具位置偏差。
刀具位置偏差的测量同样也需通过对刀操作来实现。
1、一般对刀一般对刀是指在数控木工雕刻机上使用相对位置检测手动对刀。
下面以Z 向对刀为例说明对刀方法,刀具安装后,先移动刀具手动雕刻工件右端面,再沿X向退刀,将右端面与加工原点距离N输入数控系统,即完成这把刀具Z向对刀过程。
公共基础知识数控对刀基础知识概述

《数控对刀基础知识综合性概述》一、引言在现代制造业中,数控技术的应用越来越广泛。
数控加工以其高精度、高效率、高自动化程度等优势,成为了制造业的重要发展方向。
而数控对刀作为数控加工中的关键环节,直接影响着加工精度和效率。
本文将对数控对刀的基础知识进行全面的阐述与分析,包括基本概念、核心理论、发展历程、重要实践以及未来趋势。
二、数控对刀的基本概念(一)定义数控对刀是指在数控加工过程中,确定刀具与工件之间相对位置的操作。
通过对刀,可以使刀具的切削刃准确地对准工件的加工部位,从而保证加工精度。
(二)目的数控对刀的主要目的是确定刀具的位置和长度补偿值,以便在加工过程中能够准确地控制刀具的运动轨迹,实现高精度的加工。
(三)对刀方法1. 试切对刀法试切对刀法是最常用的对刀方法之一。
通过手动操作机床,使刀具与工件表面接触,然后测量刀具与工件之间的相对位置,确定刀具的位置和长度补偿值。
2. 对刀仪对刀法对刀仪是一种专门用于对刀的仪器。
它可以快速、准确地测量刀具的长度、直径等参数,并将测量结果传输给数控系统,实现自动对刀。
3. 光学对刀法光学对刀法是利用光学原理进行对刀的方法。
它通常采用激光干涉仪或光学显微镜等设备,对刀具与工件之间的相对位置进行测量,具有高精度、非接触等优点。
三、数控对刀的核心理论(一)坐标系在数控加工中,通常采用直角坐标系来描述刀具和工件的位置。
数控系统中的坐标系分为机床坐标系、工件坐标系和编程坐标系。
机床坐标系是机床固有的坐标系,它是确定刀具和工件在机床上位置的基准。
工件坐标系是为了方便编程和加工而建立的坐标系,它通常与工件的设计基准重合。
编程坐标系是编程人员在编程时所采用的坐标系,它通常与工件坐标系重合。
(二)刀具补偿刀具补偿是数控加工中的重要概念。
它包括刀具长度补偿和刀具半径补偿。
刀具长度补偿是指在加工过程中,由于刀具长度的变化而需要对刀具的位置进行补偿。
刀具半径补偿是指在加工过程中,由于刀具半径的变化而需要对刀具的运动轨迹进行补偿。
数控对刀操作的实训报告
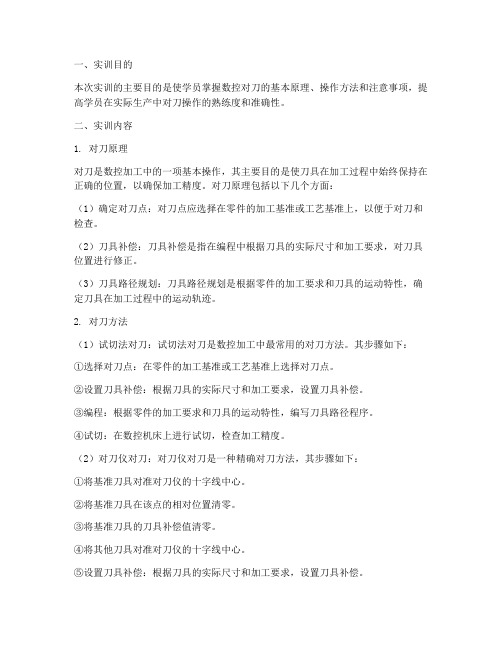
一、实训目的本次实训的主要目的是使学员掌握数控对刀的基本原理、操作方法和注意事项,提高学员在实际生产中对刀操作的熟练度和准确性。
二、实训内容1. 对刀原理对刀是数控加工中的一项基本操作,其主要目的是使刀具在加工过程中始终保持在正确的位置,以确保加工精度。
对刀原理包括以下几个方面:(1)确定对刀点:对刀点应选择在零件的加工基准或工艺基准上,以便于对刀和检查。
(2)刀具补偿:刀具补偿是指在编程中根据刀具的实际尺寸和加工要求,对刀具位置进行修正。
(3)刀具路径规划:刀具路径规划是根据零件的加工要求和刀具的运动特性,确定刀具在加工过程中的运动轨迹。
2. 对刀方法(1)试切法对刀:试切法对刀是数控加工中最常用的对刀方法。
其步骤如下:①选择对刀点:在零件的加工基准或工艺基准上选择对刀点。
②设置刀具补偿:根据刀具的实际尺寸和加工要求,设置刀具补偿。
③编程:根据零件的加工要求和刀具的运动特性,编写刀具路径程序。
④试切:在数控机床上进行试切,检查加工精度。
(2)对刀仪对刀:对刀仪对刀是一种精确对刀方法,其步骤如下:①将基准刀具对准对刀仪的十字线中心。
②将基准刀具在该点的相对位置清零。
③将基准刀具的刀具补偿值清零。
④将其他刀具对准对刀仪的十字线中心。
⑤设置刀具补偿:根据刀具的实际尺寸和加工要求,设置刀具补偿。
⑥编程:根据零件的加工要求和刀具的运动特性,编写刀具路径程序。
3. 对刀注意事项(1)确保刀具补偿的准确性。
(2)编程时要充分考虑刀具的路径规划。
(3)在试切过程中,要密切观察加工情况,及时调整刀具位置。
(4)注意安全操作,避免发生意外事故。
三、实训过程1. 实训准备(1)准备好数控机床、刀具、对刀仪、编程软件等设备。
(2)了解实训内容,明确实训目的。
2. 实训操作(1)按照对刀原理,选择对刀点。
(2)设置刀具补偿,编写刀具路径程序。
(3)在数控机床上进行试切,检查加工精度。
(4)根据试切结果,调整刀具位置,直至达到加工要求。
数控机床对刀操作

数控机床对刀操作随着自动化程度不断提高,数控机床在现代制造业中的应用越来越普遍。
其高速、高精度、高效率的特点使得其在今后的制造领域中将扮演举足轻重的角色。
在数控机床的使用过程中,对良好的对刀操作非常重要,因为它会直接影响机床的维护和性能。
对刀的定义对刀是指在数控机床上按照刀具参数进行刀具位置调整,使得切削刃正确的与工件接触,使得切削刃所在的刀具轴与工件上的零点重合,以达到工件加工的精度要求。
对刀操作旨在将刀具轴与机床坐标系原点重合,从而使得机床运动的精确度和加工的精度达到最优。
以下将详细阐述数控机床对刀的规范化操作流程。
1. 软件设置在机床上进行对刀操作之前,首先要进行软件设置。
根据机床品牌和型号的不同,具体的操作流程也有所不同。
一般而言,需要进行的操作包括:选择相应的刀具系统、插入对应的刀具、选择刀具参数、设置刀补半径、选择刀具类型、设置刀座参数等。
2. 机床坐标系确定机床坐标系决定了刀具位置,因此,在进行对刀操作前,必须首先确定机床坐标系。
机床坐标系可以分为床式和立式两种类型。
床式数控机床机床坐标系通常以工件夹紧点和床身为基准;立式数控机床机床坐标系则以主轴中心为基准。
3. 切削力平衡在机床上进行对刀操作时,需要确保刀具在切削时受到的切削力是平衡的。
否则,在操作过程中可能造成切削刃损坏甚至机床的损坏。
为了保证切削力的平衡,可以使用专用的力计测量力矩,根据测量结果调整刀具位置。
4. 刀具位置测量在进入机床坐标系后,需要进行刀具位置测量。
常用的测量方法是使用刀具测高仪进行刀具的测高定位。
测高时需要控制好测量力度,将测量从外向内进行,防止测量时对工件造成损伤。
5. 刀补半径设置刀补半径是指刀具实际半径与理论半径之间的差值,一般在数控机床加工过程中需要使用刀补,该工作在对刀后输入指令,调整刀补半径大小,以确保切削刃与工件的接触点精确地控制在预定位置上。
6. 切削参数设置在进行对刀操作时,还需要设置切削参数,包括切削速度、切削深度、进给量等。
数控机床对刀步骤方法
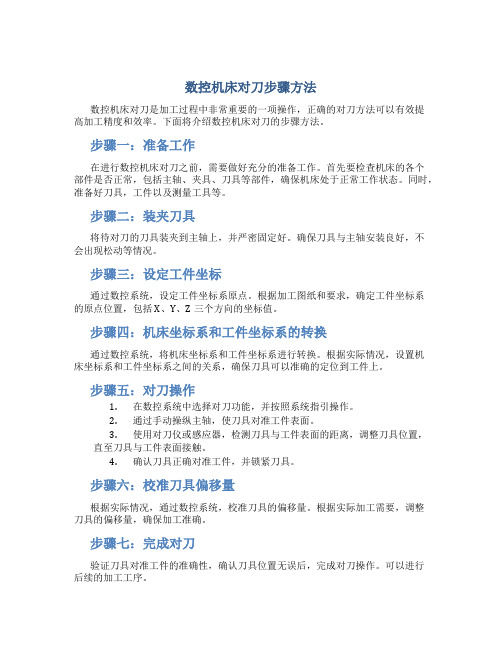
数控机床对刀步骤方法数控机床对刀是加工过程中非常重要的一项操作,正确的对刀方法可以有效提高加工精度和效率。
下面将介绍数控机床对刀的步骤方法。
步骤一:准备工作在进行数控机床对刀之前,需要做好充分的准备工作。
首先要检查机床的各个部件是否正常,包括主轴、夹具、刀具等部件,确保机床处于正常工作状态。
同时,准备好刀具,工件以及测量工具等。
步骤二:装夹刀具将待对刀的刀具装夹到主轴上,并严密固定好。
确保刀具与主轴安装良好,不会出现松动等情况。
步骤三:设定工件坐标通过数控系统,设定工件坐标系原点。
根据加工图纸和要求,确定工件坐标系的原点位置,包括X、Y、Z三个方向的坐标值。
步骤四:机床坐标系和工件坐标系的转换通过数控系统,将机床坐标系和工件坐标系进行转换。
根据实际情况,设置机床坐标系和工件坐标系之间的关系,确保刀具可以准确的定位到工件上。
步骤五:对刀操作1.在数控系统中选择对刀功能,并按照系统指引操作。
2.通过手动操纵主轴,使刀具对准工件表面。
3.使用对刀仪或感应器,检测刀具与工件表面的距离,调整刀具位置,直至刀具与工件表面接触。
4.确认刀具正确对准工件,并锁紧刀具。
步骤六:校准刀具偏移量根据实际情况,通过数控系统,校准刀具的偏移量。
根据实际加工需要,调整刀具的偏移量,确保加工准确。
步骤七:完成对刀验证刀具对准工件的准确性,确认刀具位置无误后,完成对刀操作。
可以进行后续的加工工序。
数控机床对刀是数控加工过程中的一项关键工序,正确的对刀方法可以有效提高加工精度和效率。
希望通过以上步骤方法的介绍,能够帮助操作人员更好地进行数控机床对刀操作。
简述数控机床对刀的过程和注意哪些方面
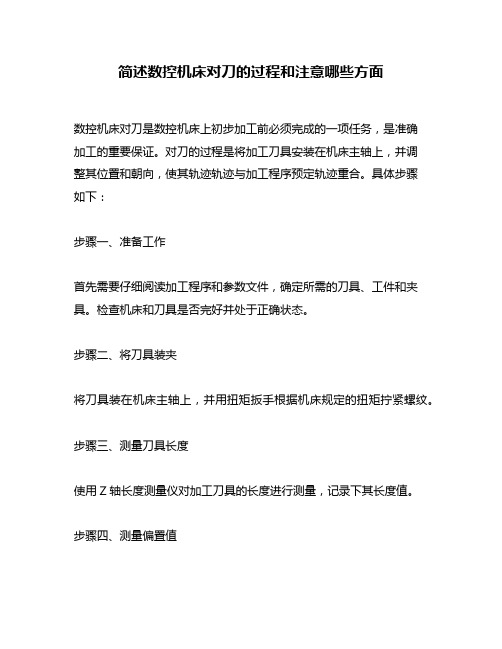
简述数控机床对刀的过程和注意哪些方面数控机床对刀是数控机床上初步加工前必须完成的一项任务,是准确加工的重要保证。
对刀的过程是将加工刀具安装在机床主轴上,并调整其位置和朝向,使其轨迹轨迹与加工程序预定轨迹重合。
具体步骤如下:步骤一、准备工作首先需要仔细阅读加工程序和参数文件,确定所需的刀具、工件和夹具。
检查机床和刀具是否完好并处于正确状态。
步骤二、将刀具装夹将刀具装在机床主轴上,并用扭矩扳手根据机床规定的扭矩拧紧螺纹。
步骤三、测量刀具长度使用Z轴长度测量仪对加工刀具的长度进行测量,记录下其长度值。
步骤四、测量偏置值将加工刀具向工件表面靠近一定距离,并使用刀具偏置仪测量其在X 轴和Z轴的偏置值。
步骤五、编写偏置值将测得的偏置值输入到机床的偏置寄存器中,从而把刀具的实际位置与计算机编制的程序所给位置一致。
步骤六、调整朝向进行刀位校准,判断刀具的朝向是否正确,在X、Z平面上和Y、Z平面上分别测量角度,确保刀具与工件表面的交角满足要求。
步骤七、测试刀具参照机床的相关操作手册对加工刀具进行测试,确认其在加工中没有出现异常情况,并对数控机床进行必要的维护保养。
需要注意的方面有:1. 设备的准备和保养应当充分,必须调节配合工作的关键参数,包括工件、刀具、夹紧装置、机床等选择。
2. 切削刀具的材料应符合切削加工要求,刃口尺寸不得超出精度范围。
3. 数字伺服系统一定要进行检查,机床各项参数、机床磨损和各零部件状态等都需要详细了解,保持最佳工作状态。
4. 加工完成后需要对机床进行充分清洗和维护保养,剩余的金属碎屑和油污都需要处理好,以及代替液压油,维护机床的清洁和起到优化机床工作状态的作用。
数控机床对刀的过程需要经过严格而细致的操作,过程中需要对各个要素进行精确定位和调整。
只有通过严格的操作流程和注意各方面细节,才能确保加工工件的精度和工作效率。
数控机床对刀方法
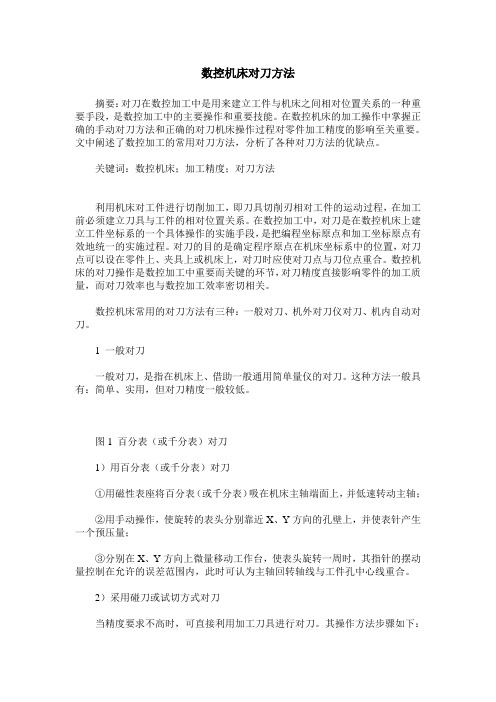
数控机床对刀方法摘要:对刀在数控加工中是用来建立工件与机床之间相对位置关系的一种重要手段,是数控加工中的主要操作和重要技能。
在数控机床的加工操作中掌握正确的手动对刀方法和正确的对刀机床操作过程对零件加工精度的影响至关重要。
文中阐述了数控加工的常用对刀方法,分析了各种对刀方法的优缺点。
关键词:数控机床;加工精度;对刀方法利用机床对工件进行切削加工,即刀具切削刃相对工件的运动过程,在加工前必须建立刀具与工件的相对位置关系。
在数控加工中,对刀是在数控机床上建立工件坐标系的一个具体操作的实施手段,是把编程坐标原点和加工坐标原点有效地统一的实施过程。
对刀的目的是确定程序原点在机床坐标系中的位置,对刀点可以设在零件上、夹具上或机床上,对刀时应使对刀点与刀位点重合。
数控机床的对刀操作是数控加工中重要而关键的环节,对刀精度直接影响零件的加工质量,而对刀效率也与数控加工效率密切相关。
数控机床常用的对刀方法有三种:一般对刀、机外对刀仪对刀、机内自动对刀。
1 一般对刀一般对刀,是指在机床上、借助一般通用简单量仪的对刀。
这种方法一般具有:简单、实用,但对刀精度一般较低。
图1 百分表(或千分表)对刀1)用百分表(或千分表)对刀①用磁性表座将百分表(或千分表)吸在机床主轴端面上,并低速转动主轴;②用手动操作,使旋转的表头分别靠近X、Y方向的孔壁上,并使表针产生一个预压量;③分别在X、Y方向上微量移动工作台,使表头旋转一周时,其指针的摆动量控制在允许的误差范围内,此时可认为主轴回转轴线与工件孔中心线重合。
2)采用碰刀或试切方式对刀当精度要求不高时,可直接利用加工刀具进行对刀。
其操作方法步骤如下:①将刀具安装在主轴上,并使之中速旋转;②分别沿X、Y方向,使刀具靠近工件被测边,直到与工件表面轻微接触;③保持X、Y坐标不变,沿Z向使刀具离开工件表面;④将X、Y坐标值置零;⑤分别沿X、Y方向,使刀具偏置移动一个刀具半径值;⑥此时的X、Y坐标值就是被测边的坐标偏置值,对其进行坐标偏置设置即可。
数控操作中对刀的操作方法
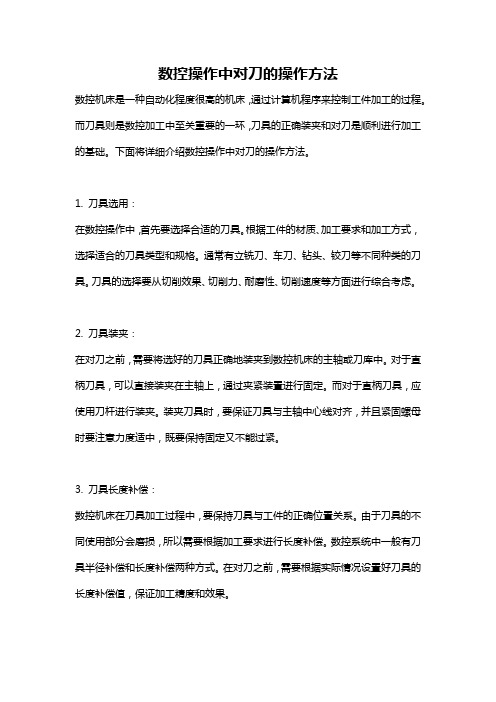
数控操作中对刀的操作方法数控机床是一种自动化程度很高的机床,通过计算机程序来控制工件加工的过程。
而刀具则是数控加工中至关重要的一环,刀具的正确装夹和对刀是顺利进行加工的基础。
下面将详细介绍数控操作中对刀的操作方法。
1. 刀具选用:在数控操作中,首先要选择合适的刀具。
根据工件的材质、加工要求和加工方式,选择适合的刀具类型和规格。
通常有立铣刀、车刀、钻头、铰刀等不同种类的刀具。
刀具的选择要从切削效果、切削力、耐磨性、切削速度等方面进行综合考虑。
2. 刀具装夹:在对刀之前,需要将选好的刀具正确地装夹到数控机床的主轴或刀库中。
对于直柄刀具,可以直接装夹在主轴上,通过夹紧装置进行固定。
而对于直柄刀具,应使用刀杆进行装夹。
装夹刀具时,要保证刀具与主轴中心线对齐,并且紧固螺母时要注意力度适中,既要保持固定又不能过紧。
3. 刀具长度补偿:数控机床在刀具加工过程中,要保持刀具与工件的正确位置关系。
由于刀具的不同使用部分会磨损,所以需要根据加工要求进行长度补偿。
数控系统中一般有刀具半径补偿和长度补偿两种方式。
在对刀之前,需要根据实际情况设置好刀具的长度补偿值,保证加工精度和效果。
4. 工件装夹:对刀之前,还需要将工件正确地装夹在数控机床上。
对于不同形状和尺寸的工件,有不同的装夹方式,可以使用机械夹具、气动夹具、液压夹具等进行固定。
工件装夹时,要注意工件的位置关系,使其与刀具的相对位置能够满足加工要求。
5. 对刀操作:对刀操作的目标是确定刀具与工件表面之间的相对位置关系。
对刀操作通常包括粗对刀和精对刀两个步骤。
(1) 粗对刀:首先使用手动操作,将刀具靠近工件表面,调整刀具位置,使其与工件表面相切或稍微超过。
然后,通过手动操作数控机床的手轮、微调装置或数字控制面板,移动刀具,使刀具呈与工件表面垂直或指定角度。
通过目视检查和测量,调整刀具位置,直到满足加工要求。
(2) 精对刀:在粗对刀的基础上,使用专用的对刀仪器,精确测量刀具与工件表面的相对位置,进行微调。
数控机床对刀操作实训报告
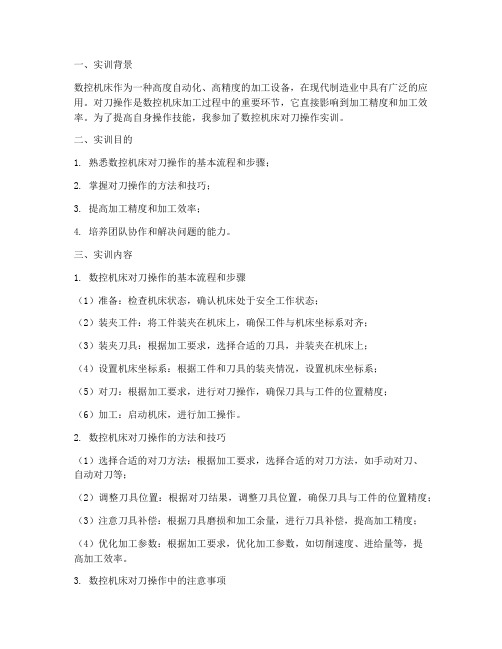
一、实训背景数控机床作为一种高度自动化、高精度的加工设备,在现代制造业中具有广泛的应用。
对刀操作是数控机床加工过程中的重要环节,它直接影响到加工精度和加工效率。
为了提高自身操作技能,我参加了数控机床对刀操作实训。
二、实训目的1. 熟悉数控机床对刀操作的基本流程和步骤;2. 掌握对刀操作的方法和技巧;3. 提高加工精度和加工效率;4. 培养团队协作和解决问题的能力。
三、实训内容1. 数控机床对刀操作的基本流程和步骤(1)准备:检查机床状态,确认机床处于安全工作状态;(2)装夹工件:将工件装夹在机床上,确保工件与机床坐标系对齐;(3)装夹刀具:根据加工要求,选择合适的刀具,并装夹在机床上;(4)设置机床坐标系:根据工件和刀具的装夹情况,设置机床坐标系;(5)对刀:根据加工要求,进行对刀操作,确保刀具与工件的位置精度;(6)加工:启动机床,进行加工操作。
2. 数控机床对刀操作的方法和技巧(1)选择合适的对刀方法:根据加工要求,选择合适的对刀方法,如手动对刀、自动对刀等;(2)调整刀具位置:根据对刀结果,调整刀具位置,确保刀具与工件的位置精度;(3)注意刀具补偿:根据刀具磨损和加工余量,进行刀具补偿,提高加工精度;(4)优化加工参数:根据加工要求,优化加工参数,如切削速度、进给量等,提高加工效率。
3. 数控机床对刀操作中的注意事项(1)确保机床和工件处于安全状态;(2)正确装夹工件和刀具;(3)设置机床坐标系时要准确;(4)对刀过程中要细心操作,避免刀具与工件发生碰撞;(5)加工过程中要密切观察机床状态,发现异常情况及时处理。
四、实训过程1. 实训准备:了解数控机床对刀操作的基本流程和步骤,熟悉各种对刀方法;2. 实训操作:按照实训内容,进行数控机床对刀操作,包括装夹工件、装夹刀具、设置机床坐标系、对刀、加工等环节;3. 实训总结:对实训过程中遇到的问题进行分析和解决,总结实训经验和教训。
五、实训结果通过本次实训,我掌握了数控机床对刀操作的基本流程和步骤,熟悉了各种对刀方法,提高了加工精度和加工效率。
简述数控车床对刀过程及注意事项
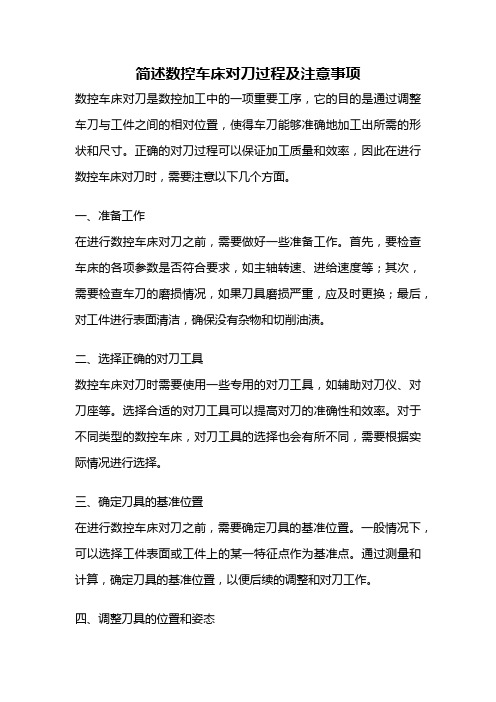
简述数控车床对刀过程及注意事项数控车床对刀是数控加工中的一项重要工序,它的目的是通过调整车刀与工件之间的相对位置,使得车刀能够准确地加工出所需的形状和尺寸。
正确的对刀过程可以保证加工质量和效率,因此在进行数控车床对刀时,需要注意以下几个方面。
一、准备工作在进行数控车床对刀之前,需要做好一些准备工作。
首先,要检查车床的各项参数是否符合要求,如主轴转速、进给速度等;其次,需要检查车刀的磨损情况,如果刀具磨损严重,应及时更换;最后,对工件进行表面清洁,确保没有杂物和切削油渍。
二、选择正确的对刀工具数控车床对刀时需要使用一些专用的对刀工具,如辅助对刀仪、对刀座等。
选择合适的对刀工具可以提高对刀的准确性和效率。
对于不同类型的数控车床,对刀工具的选择也会有所不同,需要根据实际情况进行选择。
三、确定刀具的基准位置在进行数控车床对刀之前,需要确定刀具的基准位置。
一般情况下,可以选择工件表面或工件上的某一特征点作为基准点。
通过测量和计算,确定刀具的基准位置,以便后续的调整和对刀工作。
四、调整刀具的位置和姿态在确定了刀具的基准位置之后,需要调整刀具的位置和姿态,使其与工件的轮廓和要求相吻合。
调整刀具的位置可以通过调整刀具的坐标值来实现,可以通过数控系统的操作界面进行调整。
调整刀具的姿态可以通过调整刀具的角度来实现,可以通过调节刀具座或刀具夹持装置来实现。
五、进行对刀试车在完成了刀具位置和姿态的调整之后,需要进行对刀试车,以检查刀具是否正确对刀。
对刀试车时需要注意以下几个方面:首先,要选择合适的进给速度和主轴转速,以保证加工质量和效率;其次,要观察加工过程中的切削情况,如切削力、切削声音等,以判断刀具是否正确对刀;最后,要对加工后的工件进行检查,检查加工的形状和尺寸是否满足要求。
六、调整和优化对刀结果在对刀试车的过程中,如果发现刀具没有正确对刀,需要及时进行调整和优化。
可以根据试车结果,调整刀具的位置和姿态,再次进行试车,直到达到满意的对刀效果为止。
数控操作中对刀的操作方法

数控操作中对刀的操作方法
数控操作中的对刀操作通常有以下几种方法:
1. 使用对刀仪进行自动对刀:首先将对刀仪夹在主轴上,并将刀具安装在主轴上。
然后通过数控系统的操作界面进入对刀模式,按照系统提示进行操作,待系统自动完成对刀后即可。
2. 使用对刀仪进行手动对刀:与自动对刀类似,将对刀仪夹在主轴上,并将刀具安装在主轴上。
但是此时需要手动操作对刀仪,根据对刀仪上的刻度调整刀具位置,使其与对刀仪相匹配。
3. 使用机床自带的对刀功能:某些数控机床具备对刀功能,可以通过机床的操作界面进行对刀操作。
通常需要将一个特殊的对刀卡具夹在主轴上,将对刀杆插入对刀卡具中,然后根据机床操作界面的指示进行操作。
4. 手动对刀:如果没有对刀仪或对刀功能,可以通过手动对刀的方法进行操作。
先将刀具装在主轴或刀架上,然后通过微调手轮或手柄调整刀具位置,使其与工件表面平行或垂直。
无论采用哪种方法,对刀时需要注意以下几点:
- 保证刀具的安全性:在对刀过程中,要确保刀具及其夹持装置的牢固性,以防
止刀具在对刀过程中脱落或变形。
- 调整刀具位置:根据对刀操作的目的,调整刀具位置使其与工件表面保持适当的距离。
通常情况下,刀具与工件表面之间的间隙应越小越好,以确保加工精度。
- 确认刀具位置:在完成对刀操作后,应使用测量工具如千分尺或高度规等测量刀具与工件表面的距离,以确认刀具位置是否准确。
- 记录刀具位置:为了方便后续的加工操作,应将对刀后刀具的坐标位置记录下来,为下次对刀时提供参考。
- 1、下载文档前请自行甄别文档内容的完整性,平台不提供额外的编辑、内容补充、找答案等附加服务。
- 2、"仅部分预览"的文档,不可在线预览部分如存在完整性等问题,可反馈申请退款(可完整预览的文档不适用该条件!)。
- 3、如文档侵犯您的权益,请联系客服反馈,我们会尽快为您处理(人工客服工作时间:9:00-18:30)。
数控木工雕刻机对刀的目的和步骤
数控木工雕刻机加工中,应首先确定雕刻材料的加工原点,以建立准确的加工坐标系,同时考虑刀具的不同尺寸对加工的影响。
对刀的精度决定零件的加工精度,同时,对刀效率还直接影响雕刻加工效率,这些都需要通过对刀来解决。
对刀原理:
深入了解雕刻机的对刀原理对于操作者保持清晰地对刀思路、熟练掌握对刀操作以及提出新的对刀方法都具有知道意义。
对刀的目的是为了建立工件坐标系,直观的说法是,对刀是确立工件在雕刻机工作台中的位置,实际上就是求对刀点在工作台坐标系中的坐标。
对于雕刻机来说,在加工前首先要选择对刀点,对刀点是指用雕刻机加工工件时,刀具相对于工件运动的起点。
对刀点既可以设在工件上(如工件上的设计基准或定位基准),也可以设在夹具或工作台上,若设在夹具或工作台上的某一点,则该点必须与工件的定位基准保持一定精度的尺寸关系。
对刀时,应使指刀位点与对刀点重合,所谓刀位点是指刀具的定位基准点,对于雕刻刀来说,其刀位点是刀尖。
对刀的目的是确定对刀点(或工件原点)在工作台坐标系中的绝对坐标值,测量刀具的刀位偏差值。
对刀点找正的准确度直接影响加工精度。
在实际加工工件时,使用一把刀具一般不能满足工件的加工要求,通常要使用多把刀具进行加工。
在使用多把雕刻刀加工时,在换刀位置不变的情况下,换刀后刀尖点的几何位置将出现差异,这就要求不同的刀具在不同的起始位置开始加工时,都能保证程序正常运行。
为了解决这个问题,雕刻机配备了刀具几何位置补偿的功能,利用刀具几何位置补偿功能,只要事先把每把刀相对于某一预先选定的基准刀的位置偏差测量出来,输入到雕刻机的刀具参数补正栏指定组号里,在加工程序中利用T指令,即可在刀具轨迹中自动补偿刀具位置偏差。
刀具位置偏差的测量同样也需通过对刀操作来实现。
1、一般对刀
一般对刀是指在数控木工雕刻机上使用相对位置检测手动对刀。
下面以Z向对刀为例说明对刀方法,刀具安装后,先移动刀具手动雕刻工件右端面,再沿X向退刀,将右端面与加工原点距离N输入数控系统,即完成这把刀具Z向对刀过程。
手动对刀是基本对刀方法,但它还是没跳出1325木工雕刻机的“试切--测量--调整”的对刀模式,占用较多的在机床上时间。
此方法较为落后。
2、机外对刀仪对刀
对刀仪对于浮雕机雕刻的客户很重要重要。
对刀仪极大的方便用户确定Z轴的工作零点位置,在雕刻加工过程中如出现断刀、粗精加工更换不同型号的刀具等都可以利用对刀仪来完成精确地Z轴定位。
用户必需将对刀仪块的厚度输入到参数中,执行文件时系统自动将零点位置下移对刀仪块厚度的深度,这样才能真正确定了Z轴工作零点。
机外对刀的本质是测量出刀具假想刀尖点到刀具台基准之间X及Z方向的距离。
利用机外对刀仪可将刀具预先在机床外校对好,以便装上机床后将对刀长度输入相应刀具补偿号即可以使用,刀具碰了就记录进去位置了。
所以如果是多种类小批量加工最好使用对刀仪,节约时间。
3、自动对刀
自动对刀是通过刀尖检测系统实现的,刀尖以设定的速度向接触式传感器接近,当刀尖与传感器接触并发出信号,数控系统立即记下该瞬间的坐标值,并自动修正刀具补偿值。
自动对刀过程。
济南金刻数控提供参考:/。