高密度型砂性能要求
高密度造型线的型砂性能管理百铸网于凤莲
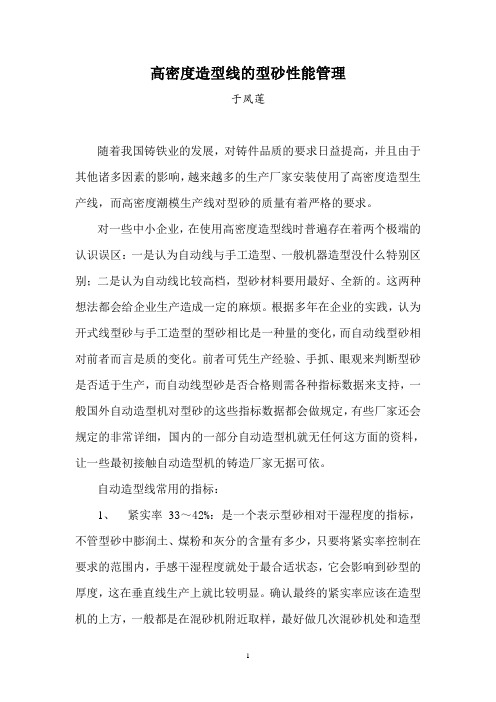
高密度造型线的型砂性能管理于凤莲随着我国铸铁业的发展,对铸件品质的要求日益提高,并且由于其他诸多因素的影响,越来越多的生产厂家安装使用了高密度造型生产线,而高密度潮模生产线对型砂的质量有着严格的要求。
对一些中小企业,在使用高密度造型线时普遍存在着两个极端的认识误区:一是认为自动线与手工造型、一般机器造型没什么特别区别;二是认为自动线比较高档,型砂材料要用最好、全新的。
这两种想法都会给企业生产造成一定的麻烦。
根据多年在企业的实践,认为开式线型砂与手工造型的型砂相比是一种量的变化,而自动线型砂相对前者而言是质的变化。
前者可凭生产经验、手抓、眼观来判断型砂是否适于生产,而自动线型砂是否合格则需各种指标数据来支持,一般国外自动造型机对型砂的这些指标数据都会做规定,有些厂家还会规定的非常详细,国内的一部分自动造型机就无任何这方面的资料,让一些最初接触自动造型机的铸造厂家无据可依。
自动造型线常用的指标:1、紧实率33~42%:是一个表示型砂相对干湿程度的指标,不管型砂中膨润土、煤粉和灰分的含量有多少,只要将紧实率控制在要求的范围内,手感干湿程度就处于最合适状态,它会影响到砂型的厚度,这在垂直线生产上就比较明显。
确认最终的紧实率应该在造型机的上方,一般都是在混砂机附近取样,最好做几次混砂机处和造型机上方取样对比,找出两处紧实率的系统差别,最后确定在混砂机处取样的数据,以方便操作。
2、湿压强度0.12~0.2MPa:湿压强度是保证造型及浇注过程正常进行的一个重要指标,高强度型砂可避免塌箱、胀箱、漏箱,特别是垂直生产线砂型要推动造好的砂型向前移动,浇注时又无砂箱协助承受金属液的压力,会对型砂强度要求更高。
如某厂一垂直生产线,自动造型机要求型砂湿压强度0.2~0.25MPa,一阶段其湿压强度在0.17~0.18MPa之间,砂眼缺陷占废品的70~80%。
后经调整,湿压强度连续几天在0.25~0.27MPa,砂眼减少,还出现连续4天无砂眼的情况,但气孔成倍增长。
型砂的性能指标一
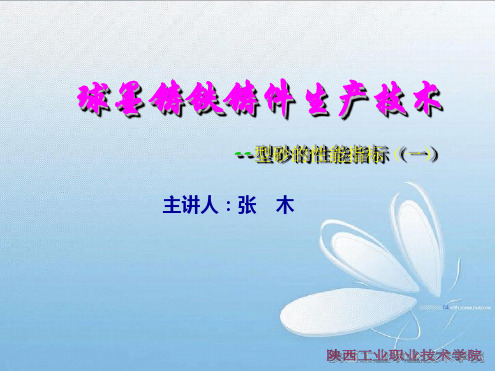
幻灯三 2/99
球墨铸铁铸件生产技术
情境三
讲解
※可 塑 性
可塑性好,能够获得并保持轮廓清晰,形状完整,尺寸精确的砂型; 容易起模及修型,夹砂少。
提高可塑性,可以采取下述经验:
使用更多小粒度的原砂; 使用钠基膨润土,比钙基膨润土好; 适当延长混砂时间; 灰分及失效粘土尽量少。
用手捏,可以 获得相应经验
型砂流动性良好,可以获得以下益处: 砂箱内上、下位置型砂紧实度比较均匀,模样附近紧实状态比较好; 型腔轮廓清晰,尺寸精确,表面光洁; 省力,效率高; 机器造型更显得重要,也是困扰机器造型的一个因素;
幻灯三 5/99
球墨铸铁铸件生产技术
情境三
讲解
※ 型砂流动性
改善型砂流动性可取得措施主要有:
使用圆形、小颗粒的原砂; 大小尽量均匀; 混砂后进行松砂处理; 型砂中加入少量重油。
张球墨铸铁铸件生产技术情境三情境三幻灯三299型砂的性能指标型砂的性能指标抗拉强度抗压强度抗剪强度抗劈强度热湿拉强度高温强度表面强度讲解讲解球墨铸铁铸件生产技术情境三情境三幻灯三399可可与流动性相矛盾可塑性应该适可而止
球墨铸铁铸件生产技术
--型砂的性能指标(一) 主讲人:张 木
球墨铸铁铸件生产技术
紧实率= H0 ? H1 ? 100% H1
锤击
紧实率测定试验
幻灯三 9/99
紧实率(含水率)测定试验过程
球墨铸铁铸件生产技术
情境三
讲解
※ 型砂保存性
型砂保存一段时间后,其使用性能保持不变的能力。 一般用型砂的可使用时间反映型砂的保存性。 树脂砂放置时间发生硬化(固化)现象,影响使用性能。
幻灯三 10/99
阶梯硬度差法测定型砂流动性
型砂
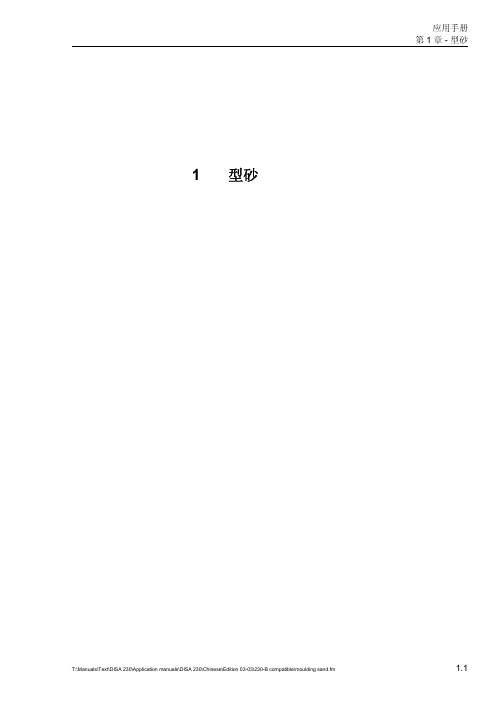
应用手册第1章 - 型砂1型砂T:\Manuals\Text\DISA 230\Application manuals\DISA 230\Chinese\Edition 03-03\230-B compatible\moulding sand.fm 1.12110平均砂粒度(洗选砂)0.14-0.28 DIN AFS 110-60粒度分布(洗选砂)对90%的粒度使用3-4个筛子湿压强度1500-2100 p/cm221-30 psi湿拉强度>200p/cm2>2.9 psi抗裂强度>300p/cm2>4.3 psi湿抗拉强度>20p/cm2>0.3 psi透气性>50>50紧实率40% ± 2%40% ± 2%水分含量调节直到紧实率达到40% ±2%活性粘土含量(MB)>7%>7%AFS粘土含量活性粘土为+3至4.5%烧损 3.5-5% 3.5-5%表1: 对标准型砂建议的物理特性2013 / 230 / 240平均砂粒度(洗选砂)0.14-0.22 DIN AFS 110-75粒度分布(洗选砂)对90%的粒度使用3-4个筛子湿压强度1700-2100 p/cm225-30 psi湿拉强度>200p/cm2>2.9 psi抗裂强度>300p/cm2>4.3 psi湿抗拉强度>20p/cm2>0.3 psi透气性>50>50紧实率40% ± 2%40% ± 2%水分含量调节直到紧实率达到40% ±2%活性粘土含量(MB)>7%>7%AFS粘土含量活性粘土为+3至4.5%烧损 3.5-5% 3.5-5%表2: 对标准型砂建议的物理特性1.2T:\Manuals\Text\DISA 230\Application manuals\DISA 230\Chinese\Edition 03-03\230-B compatible\moulding sand.fm应用手册第1.1节 - 高密度湿砂造型1.1高密度湿砂造型与用化学粘结剂的其它砂造型方法相比,用粘土做粘结剂型砂的费用低得多,其生产出的铸件质量和生产效率与后者相当,甚至更好些。
最新(1)湿型砂的性能要求
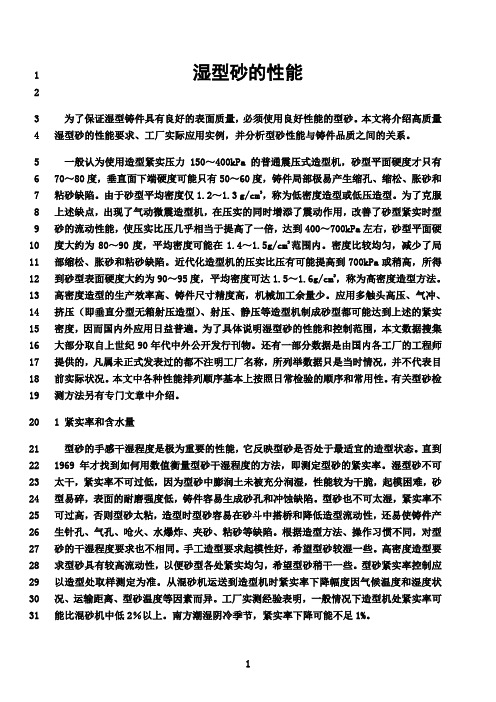
湿型砂的性能123为了保证湿型铸件具有良好的表面质量,必须使用良好性能的型砂。
本文将介绍高质量4湿型砂的性能要求、工厂实际应用实例,并分析型砂性能与铸件品质之间的关系。
5一般认为使用造型紧实压力150~400kPa的普通震压式造型机,砂型平面硬度才只有670~80度,垂直面下端硬度可能只有50~60度,铸件局部极易产生缩孔、缩松、胀砂和7粘砂缺陷。
由于砂型平均密度仅1.2~1.3 g/cm3,称为低密度造型或低压造型。
为了克服8上述缺点,出现了气动微震造型机,在压实的同时增添了震动作用,改善了砂型紧实时型9砂的流动性能,使压实比压几乎相当于提高了一倍,达到400~700kPa左右,砂型平面硬10度大约为80~90度,平均密度可能在1.4~1.5g/cm3范围内。
密度比较均匀,减少了局部缩松、胀砂和粘砂缺陷。
近代化造型机的压实比压有可能提高到700kPa或稍高,所得1112到砂型表面硬度大约为90~95度,平均密度可达1.5~1.6g/cm3,称为高密度造型方法。
高密度造型的生产效率高、铸件尺寸精度高,机械加工余量少。
应用多触头高压、气冲、1314挤压(即垂直分型无箱射压造型)、射压、静压等造型机制成砂型都可能达到上述的紧实15密度,因而国内外应用日益普遍。
为了具体说明湿型砂的性能和控制范围,本文数据搜集16大部分取自上世纪90年代中外公开发行刊物。
还有一部分数据是由国内各工厂的工程师17提供的,凡属未正式发表过的都不注明工厂名称,所列举数据只是当时情况,并不代表目18前实际状况。
本文中各种性能排列顺序基本上按照日常检验的顺序和常用性。
有关型砂检测方法另有专门文章中介绍。
19201 紧实率和含水量21型砂的手感干湿程度是极为重要的性能,它反映型砂是否处于最适宜的造型状态。
直到221969年才找到如何用数值衡量型砂干湿程度的方法,即测定型砂的紧实率。
湿型砂不可23太干,紧实率不可过低,因为型砂中膨润土未被充分润湿,性能较为干脆,起模困难,砂24型易碎,表面的耐磨强度低,铸件容易生成砂孔和冲蚀缺陷。
砂处理
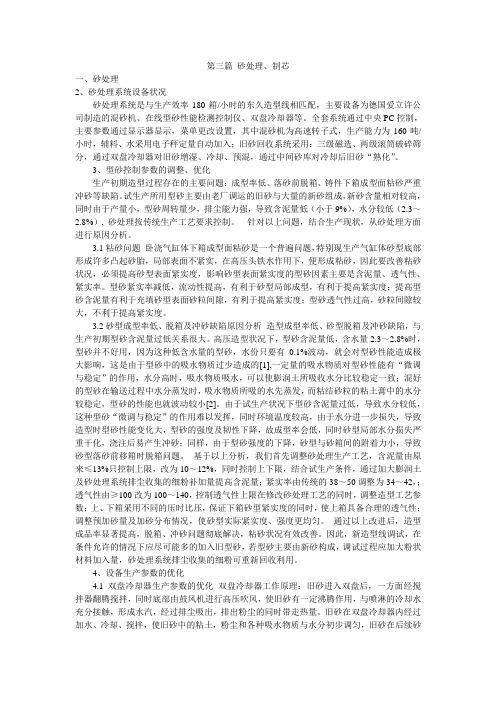
第三篇砂处理、制芯一、砂处理2、砂处理系统设备状况砂处理系统是与生产效率180箱/小时的东久造型线相匹配,主要设备为德国爱立许公司制造的混砂机、在线型砂性能检测控制仪、双盘冷却器等。
全套系统通过中央PC控制,主要参数通过显示器显示,菜单更改设置,其中混砂机为高速转子式,生产能力为160吨/小时,辅料、水采用电子秤定量自动加入;旧砂回收系统采用:三级磁选、两级滚筒破碎筛分,通过双盘冷却器对旧砂增湿、冷却、预混,通过中间砂库对冷却后旧砂“熟化”。
3、型砂控制参数的调整、优化生产初期造型过程存在的主要问题:成型率低、落砂前脱箱、铸件下箱成型面粘砂严重冲砂等缺陷。
试生产所用型砂主要由老厂调运的旧砂与大量的新砂组成,新砂含量相对较高,同时由于产量小,型砂周转量少,排尘能力强,导致含泥量低(小于9%),水分较低(2.3~2.8%), 砂处理按传统生产工艺要求控制。
针对以上问题,结合生产现状,从砂处理方面进行原因分析。
3.1粘砂问题卧浇气缸体下箱成型面粘砂是一个普遍问题,特别现生产气缸体砂型底部形成许多凸起砂胎,局部表面不紧实,在高压头铁水作用下,便形成粘砂,因此要改善粘砂状况,必须提高砂型表面紧实度,影响砂型表面紧实度的型砂因素主要是含泥量、透气性、紧实率。
型砂紧实率减低,流动性提高,有利于砂型局部成型,有利于提高紧实度;提高型砂含泥量有利于充填砂型表面砂粒间隙,有利于提高紧实度;型砂透气性过高,砂粒间隙较大,不利于提高紧实度。
3.2砂型成型率低、脱箱及冲砂缺陷原因分析造型成型率低、砂型脱箱及冲砂缺陷,与生产初期型砂含泥量过低关系很大。
高压造型状况下,型砂含泥量低,含水量2.3~2.8%时,型砂并不好用,因为这种低含水量的型砂,水份只要有0.1%波动,就会对型砂性能造成极大影响,这是由于型砂中的吸水物质过少造成的[1],一定量的吸水物质对型砂性能有“微调与稳定”的作用,水分高时,吸水物质吸水,可以使膨润土所吸收水分比较稳定一致;混好的型砂在输送过程中水分蒸发时,吸水物质所吸的水先蒸发,而粘结砂粒的粘土膏中的水分较稳定,型砂的性能也就波动较小[2]。
射压造型型砂性能要求

前言高密度造型方法(或称高紧实度造型,包括多触头高压、气冲、挤压、射压、静压、吸压造型方法)的生产效率高、铸件品质较好,因而国内外应用都很普遍。
高密度造型对型砂品质的要求比较严格。
本文用表格(见文后附表)列举部分典型的国内外铸造厂实际应用的和部分设备公司推荐的高密度砂型主要的和经常测定的型砂性能,并加以评论。
1 紧实率和含水量湿型砂不可太干,否则膨润土未被充分润湿,起模困难,砂型易碎,表面的耐磨强度低,铸件容易生成砂孔和冲蚀缺陷。
型砂也不可太湿,过湿型砂易使铸件产生针孔、气孔、呛火、水爆炸、夹砂、粘砂等缺陷,而且型砂太粘、型砂在砂斗中搭桥、造型流动性降低。
使砂型型腔表面松紧不均;还可能导致造型紧实距离过大和压头陷入砂箱边缘以内而损伤模具和砂型吃砂量过小。
表明型砂干湿状态的参数有两种:紧实率和含水量。
附表中国内各厂的紧实率和含水量除特别注明以外,取样地点都在混砂机处。
但是型砂紧实率和含水量的控制应以造型处取样测定为准。
从混砂机运送到造型机时紧实率和含水量下降幅度因气候温度和湿度状况、运输距离、型砂温度等因素而异。
如果只根据混砂机处取样检测结果控制型砂的湿度,就要略增少许,以补偿紧实率和水分的损失。
以前的观点认为手工造型和震压式机器造型最适宜于湿状态下的紧实率大约在45~50%;高压造型和气冲造型时为40~45%;挤压造型要求流动性好,紧实率为35~40%。
由表中可以看出,目前铸件品质较好的工厂,高密度造型的型砂紧实率(大多是从混砂机取样)通常都在25~45%范围内,比较集中于30~40%之间,比以前有明显降低。
这是由于高密度造型设备的起模精度提高,而且要求砂型各部位硬度均匀分布,使型砂的流动性成为重要因素。
工厂的控制原则大多是只要能够保证起模顺利就尽力降低紧实率。
从减少铸件气孔缺陷的角度出发,要求最适宜干湿状态下型砂的含水量尽可能低。
高强度型砂的膨润土加入量多,型砂中含有较多灰分,所购入煤粉和膨润土因品质低劣而需要增大加入量,混砂机的加料顺序不当、揉碾作用不强、刮砂板磨损、混砂时间太短,以致型砂中存在较多不起粘结作用的小粘土团块,都会提高型砂的含水量。
谈砂型铸造表面缺陷

漫谈湿砂型铸件表面缺陷与其它铸造方法相比,湿型铸件是较容易产生粘砂、砂孔、夹砂、气孔等缺陷的。
如果铸造工厂注意控制湿型砂的品质,这些缺陷本来是有可能减少或避免。
以下用实例说明型砂性能与铸件表面缺陷的关系。
一.粘砂研究工作表明,一般湿砂型铸件,不论铸钢还是铸铁,粘砂缺陷都是属于机械粘砂,而不是化学粘砂。
机械粘砂的产生原因有多种,最多见的如下的实例:1.砂粒太粗和透气性过高,金属液容易钻入砂粒间孔隙,使铸件表面粗糙,或将砂粒包裹固定在表面上。
江苏某外资工厂的铸铁旧砂中不断混入大量30/50目粗粒芯砂,以致型砂透气性达到220以上,铸件表面极为粗糙。
内蒙某工厂铸钢车间的气动微震造型机生产中、小铸件。
使用主要集中在40目的40/70粗粒石英砂混制型砂,铸件表面产生严重粘砂。
平时不检测型砂透气性,认为已经符合工艺规程规定的≥80。
为了找到粘砂原因而专门检测一次,发现透气性居然高达1070左右,表明这就是产生粘砂的原因。
因此型砂透气性必须有上限,型砂粒度粗细和透气性应当处于适宜范围内。
一般震压机器造型单一砂最适宜的型砂粒度大多为70/140目,透气性大致为70~100,高密度造型的型砂粒度最好是50/140或100/50,透气性为80~140。
有些生产发动机的铸造厂大量使用50/100目粗原砂制造砂芯,落砂时不断混入旧砂中,使型砂透气性可能达到180以上,就应加入100/140目细砂,或将旋流分离器中的细颗粒部分返回到旧砂中,以便纠正型砂粒度。
2.铸铁型砂中煤粉含量不足或煤粉品质不良。
北京某铸造厂生产高速列车刹车盘,铸件材质符合要求,而表面有严重粘砂,需整体打磨后才能交货。
型砂中所用煤粉来自郊区一家关系密切的私营小供应商。
粘砂的产生原因可能是煤粉品质太差,还可能是型砂中有效煤粉量也不足够。
安徽某阀门总厂使用的“煤粉”是生产焦炭洗选下来的废料,灰分高达76%。
使用后整个型砂性能遭破坏,铸件废品超过一半。
铸造工厂应该对购入的煤粉品质加强检验。
(1)湿型砂的性能要求
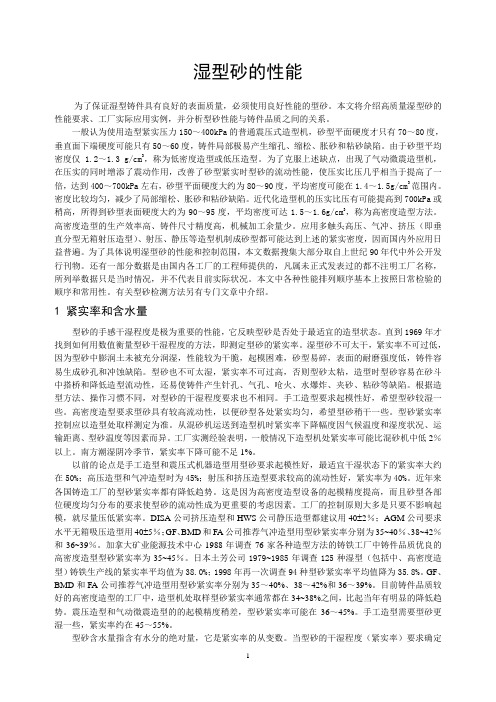
湿型砂的性能为了保证湿型铸件具有良好的表面质量,必须使用良好性能的型砂。
本文将介绍高质量湿型砂的性能要求、工厂实际应用实例,并分析型砂性能与铸件品质之间的关系。
一般认为使用造型紧实压力150~400kPa的普通震压式造型机,砂型平面硬度才只有70~80度,垂直面下端硬度可能只有50~60度,铸件局部极易产生缩孔、缩松、胀砂和粘砂缺陷。
由于砂型平均密度仅1.2~1.3 g/cm3,称为低密度造型或低压造型。
为了克服上述缺点,出现了气动微震造型机,在压实的同时增添了震动作用,改善了砂型紧实时型砂的流动性能,使压实比压几乎相当于提高了一倍,达到400~700kPa左右,砂型平面硬度大约为80~90度,平均密度可能在1.4~1.5g/cm3范围内。
密度比较均匀,减少了局部缩松、胀砂和粘砂缺陷。
近代化造型机的压实比压有可能提高到700kPa或稍高,所得到砂型表面硬度大约为90~95度,平均密度可达1.5~1.6g/cm3,称为高密度造型方法。
高密度造型的生产效率高、铸件尺寸精度高,机械加工余量少。
应用多触头高压、气冲、挤压(即垂直分型无箱射压造型)、射压、静压等造型机制成砂型都可能达到上述的紧实密度,因而国内外应用日益普遍。
为了具体说明湿型砂的性能和控制范围,本文数据搜集大部分取自上世纪90年代中外公开发行刊物。
还有一部分数据是由国内各工厂的工程师提供的,凡属未正式发表过的都不注明工厂名称,所列举数据只是当时情况,并不代表目前实际状况。
本文中各种性能排列顺序基本上按照日常检验的顺序和常用性。
有关型砂检测方法另有专门文章中介绍。
1 紧实率和含水量型砂的手感干湿程度是极为重要的性能,它反映型砂是否处于最适宜的造型状态。
直到1969年才找到如何用数值衡量型砂干湿程度的方法,即测定型砂的紧实率。
湿型砂不可太干,紧实率不可过低,因为型砂中膨润土未被充分润湿,性能较为干脆,起模困难,砂型易碎,表面的耐磨强度低,铸件容易生成砂孔和冲蚀缺陷。
高致密镁砂的定义

高致密镁砂的定义
高致密镁砂的定义
一、概述
高致密镁砂是一种常见的非金属材料,其主要成分为氧化镁和氧化铝。
该材料具有高硬度、高耐磨性、高耐腐蚀性等特点,被广泛应用于建筑、冶金、化工等领域。
二、物理性质
1. 颜色:白色或灰色
2. 密度:
3.0-3.3g/cm³
3. 硬度:6-7(莫氏硬度)
4. 熔点:2850℃
三、制备方法
1. 电解法制备:将氧化铝和氧化镁混合后,在电解槽中进行电解,得
到高纯度的高致密镁砂。
2. 碳热还原法制备:将混合了碳粉和氧化铝的原料在高温下还原,得
到高致密镁砂。
四、应用领域
1. 建筑领域:作为建筑材料中的防火材料,可以有效防止火灾。
2. 冶金领域:作为冶金原料,可以用于钢铁冶炼和铸造。
3. 化工领域:用于制备各种化学试剂和催化剂。
五、优点
1. 高硬度:具有很强的抗磨损性,可以有效延长使用寿命。
2. 高耐腐蚀性:能够在酸碱环境中稳定运行。
3. 高防火性:能够有效防止火灾,提高建筑安全系数。
4. 环保:无毒无害,不会对环境造成污染。
六、缺点
1. 价格较高:由于制备方法较为复杂,其价格相对较高。
2. 脆性较大:在受到外力冲击时容易破裂。
七、注意事项
1. 避免长时间接触皮肤和呼吸道,以免引起不适。
2. 存放时要避免与水接触,以免影响质量。
高密度湿型的型砂原材料品质要求

高密度湿型的型砂原材料品质要求于震宗(清华大学)2002年5月摘要高密度湿型对型砂的原材料提出比较高的要求。
应当选购高品质的膨润土和煤粉。
使用淀粉的铸造工厂应注意其中是否含有杂质。
文章还对回用砂和原砂的性能提出要求。
此外,也不可使用含电解质过多的和被污染的水。
关键词高密度湿型型砂原材料The Quality Requirement of Raw Materials for High Density MoldingYu Zhenzong (Tsinghua University)Abstract The high density molding set a comparative higher requirement on the quality of raw materials for molding sand. Bentonite and seacoal of excellent quality should be choiced. The starch user should be aware whether it contains any impurities. This paper also speaks of the property requirements of reused sand and new sand. In addition, the water containing high level electrolyte or contaminated water cannot be used for sand preparation.Keywords High Density Molding Raw Materials of Molding Sand前言高密度造型(或称高紧实度造型)包括多触头高压、气冲、挤压、射压、静压、吸压等造型方法对型砂品质的要求比较严格[1]。
制备出高品质型砂的最主要关键之一是选用优良品质的型砂原材料。
垂直分型射压造型线型砂质量控制及生产应用

垂直分型射压造型线型砂质量控制及生产应用在粘土砂铸造生产过程中,型砂是关键,其性能控制得好与坏,质量稳定与否,将对铸件质量产生巨大的影响。
我公司的造型线为ZZ416垂直分型射压造型线,铁液采用中频电炉熔炼,铸件以薄壁铸铁(灰铸铁和球墨铸铁)件为主,产品包括汽车零配件、管道件、阀门件等。
我公司经过多年生产实践,在型砂质量控制方面做了大量工作,并取得了良好效果。
1原材料质量要求1.1原砂选用河北围场擦洗砂,含泥量<1.0%,SiO2>85%,原砂粒度70/140目。
由于垂直分型射压造型属高密度造型,为减少砂型受热膨胀,避免因砂粒受挤压从砂型表面脱落而引起铸造缺陷,粒度要求不宜过于集中,原砂最好采用4筛集中率85%以上,主峰筛(100目)量控制在40%以内。
新砂补加量在5%以下。
1.2煤粉煤粉灰份应<10%,煤粉含灰量过高,使得型砂含泥量增加,影响型砂使用性能。
含硫量≤1.5%;煤粉粒度≥95%以上的颗粒通过140目筛,并且煤粉不允许有大颗粒存在,因其在浇注过程中遇金属液燃烧时间长,阻止铁液靠近型壁,待铁液凝固后,便会造成铸件表面凹坑,影响铸件表面粗糙度。
挥发分的高低是衡量煤粉质量好坏的主要指标之一,好的煤粉挥发分含量较高,浇注时,型腔内易形成还原性气体,析出大量的光亮碳,提高铸件的外观质量。
但挥发分超过40%,型砂发气量增大,铸件易产生气孔、浇不足等缺陷。
因此,挥发分一般在30%-38%。
1.3膨润土选用钠基膨润土。
湿压强度≥120kPa,吸蓝量(g/100g)≥38,粒度过200目≥90%。
2型砂性能质量控制2.1湿压强度如果型砂湿态强度不足,在起模、搬运砂型、下芯、合型等过程中,砂型有可能破损和塌落;浇注时砂型承受不住金属液的冲刷和冲击造成砂孔缺陷,甚至铁液泄漏。
一般用湿压强度来表示型砂湿态强度,一般控制在150-200kPa。
2.2透气性型砂的透气率不可太低以免浇注过程中发生呛火和铸件产生气孔缺陷,但绝不能理解为型砂透气率越高越好。
高密度自动造型的型砂控制
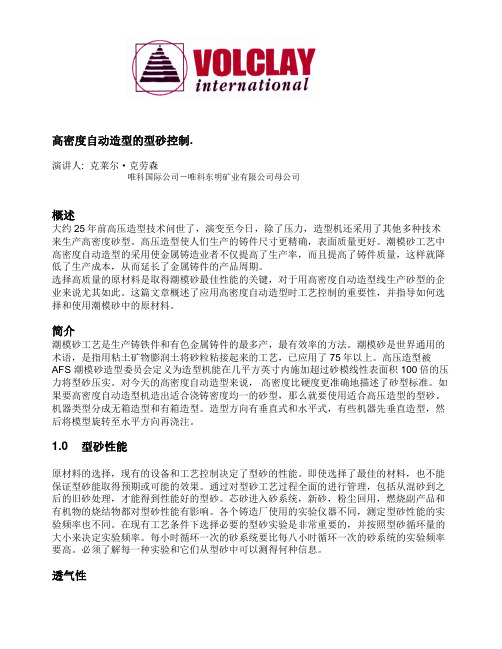
高密度自动造型的型砂控制.演讲人: 克莱尔·克劳森唯科国际公司-唯科东明矿业有限公司母公司概述大约25年前高压造型技术问世了,演变至今日,除了压力,造型机还采用了其他多种技术来生产高密度砂型。
高压造型使人们生产的铸件尺寸更精确,表面质量更好。
潮模砂工艺中高密度自动造型的采用使金属铸造业者不仅提高了生产率,而且提高了铸件质量,这样就降低了生产成本,从而延长了金属铸件的产品周期。
选择高质量的原材料是取得潮模砂最佳性能的关键,对于用高密度自动造型线生产砂型的企业来说尤其如此。
这篇文章概述了应用高密度自动造型时工艺控制的重要性,并指导如何选择和使用潮模砂中的原材料。
简介潮模砂工艺是生产铸铁件和有色金属铸件的最多产,最有效率的方法。
潮模砂是世界通用的术语,是指用粘土矿物膨润土将砂粒粘接起来的工艺,已应用了75年以上。
高压造型被AFS 潮模砂造型委员会定义为造型机能在几平方英寸内施加超过砂模线性表面积100倍的压力将型砂压实。
对今天的高密度自动造型来说,高密度比硬度更准确地描述了砂型标准。
如果要高密度自动造型机造出适合浇铸密度均一的砂型,那么就要使用适合高压造型的型砂。
机器类型分成无箱造型和有箱造型。
造型方向有垂直式和水平式,有些机器先垂直造型,然后将模型旋转至水平方向再浇注。
1.0 型砂性能原材料的选择,现有的设备和工艺控制决定了型砂的性能。
即使选择了最佳的材料,也不能保证型砂能取得预期或可能的效果。
通过对型砂工艺过程全面的进行管理,包括从混砂到之后的旧砂处理,才能得到性能好的型砂。
芯砂进入砂系统,新砂,粉尘回用,燃烧副产品和有机物的烧结物都对型砂性能有影响。
各个铸造厂使用的实验仪器不同,测定型砂性能的实验频率也不同。
在现有工艺条件下选择必要的型砂实验是非常重要的,并按照型砂循环量的大小来决定实验频率。
每小时循环一次的砂系统要比每八小时循环一次的砂系统的实验频率要高。
必须了解每一种实验和它们从型砂中可以测得何种信息。
黏土湿型砂高密度造型时型砂的组成配比如何确定
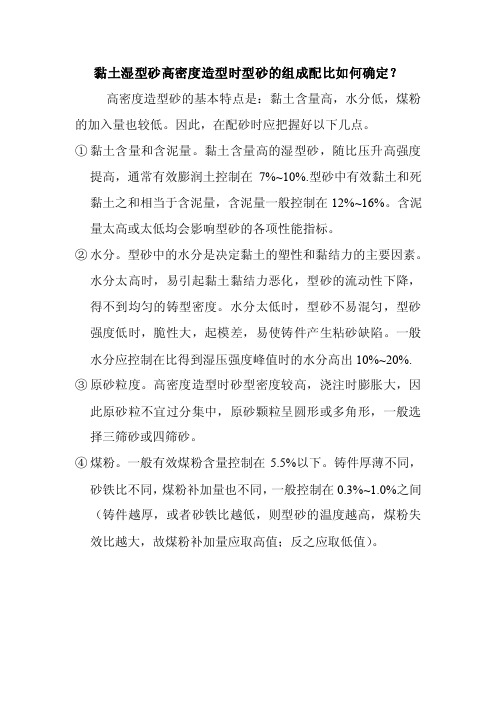
黏土湿型砂高密度造型时型砂的组成配比如何确定?
高密度造型砂的基本特点是:黏土含量高,水分低,煤粉的加入量也较低。
因此,在配砂时应把握好以下几点。
①黏土含量和含泥量。
黏土含量高的湿型砂,随比压升高强度
提高,通常有效膨润土控制在7%~10%.型砂中有效黏土和死黏土之和相当于含泥量,含泥量一般控制在12%~16%。
含泥量太高或太低均会影响型砂的各项性能指标。
②水分。
型砂中的水分是决定黏土的塑性和黏结力的主要因素。
水分太高时,易引起黏土黏结力恶化,型砂的流动性下降,得不到均匀的铸型密度。
水分太低时,型砂不易混匀,型砂强度低时,脆性大,起模差,易使铸件产生粘砂缺陷。
一般水分应控制在比得到湿压强度峰值时的水分高出10%~20%. ③原砂粒度。
高密度造型时砂型密度较高,浇注时膨胀大,因
此原砂粒不宜过分集中,原砂颗粒呈圆形或多角形,一般选择三筛砂或四筛砂。
④煤粉。
一般有效煤粉含量控制在5.5%以下。
铸件厚薄不同,
砂铁比不同,煤粉补加量也不同,一般控制在0.3%~1.0%之间(铸件越厚,或者砂铁比越低,则型砂的温度越高,煤粉失效比越大,故煤粉补加量应取高值;反之应取低值)。
型砂的使用要求

型砂的使用要求
一、强度和耐久性
型砂应具有一定的强度和耐久性,以确保在铸造过程中能够承受住金属液体的压力和热冲击,同时保持其形状和尺寸的稳定性。
二、透气性
型砂应具有良好的透气性,以便在铸造过程中能够将气体排出型腔,减少气孔、砂眼等缺陷的产生。
三、收缩性
型砂的收缩性对于防止铸件产生收缩缺陷具有重要意义。
型砂的收缩率应与所使用的铸件材料相匹配,以确保铸件尺寸的准确性。
四、耐火性
型砂应具有一定的耐火性,以便在高温环境下保持其结构和性能的稳定性,防止因高温而产生的烧结、熔融等现象。
五、易用性
型砂应具有良好的易用性,包括良好的流动性、可塑性和填充性等,以便于在制造砂型时能够方便地操作和控制。
六、环保性
型砂的环保性对于铸造行业的可持续发展至关重要。
型砂应采用环保材料制成,减少对环境的污染和破坏,并遵守国家和地方的环保法规。
七、经济性
在满足性能要求的前提下,型砂的成本应尽可能低,以提高铸造生产的经济效益。
选择价格合理、性能优良的型砂材料是关键。
八、稳定性
型砂在使用过程中应保持其性能的稳定性,以确保铸造生产的稳定性和铸件质量的可靠性。
通过合理选择型砂材料、优化配方和控制加工工艺等措施可以提高其稳定性。
砂型铸造——黏土砂型
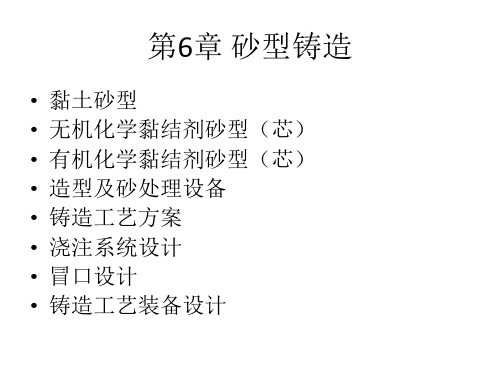
固整体的岩石则称为石英岩。
6.1 黏土砂型
对原砂提出的质量要求:
1)含泥量――含泥量指原砂中直径小于0.02mm(20µm)的细小颗 粒的含量(质量分数),其中既有黏土,也包括极细的砂子和其它 非粘土质点。 原砂含泥量检测方法: 利用不同颗粒尺寸的砂粒在水中下降速度不同,将原砂中颗粒 直径>20µm 与直径<20µm的颗粒分开。检验时,称量烘干的原砂并 置入烧杯中,加入水及分散剂,煮沸及搅拌使其充分分散;然后反 复按规定时间沉淀,虹吸排除浑水和冲入清水。直到水清后,由烘 干的残留砂样质量即可计算出原砂含泥量。
适宜干湿程度的水分一也不同。
6.1 黏土砂型
6.1.2 湿型砂性能要求
1.水分和紧实率
2)紧实率:湿型砂用1 MPa的压力压实或者在锤击式制样机上打击3
次,用试样紧实前后高度变化的百分数来表示。 (1)测定方法的依据:较干的型砂自由流入试样筒中时,砂粒松散 密度较高,在相同的紧实力作用下,型砂体积减小较少。 (2)根据型砂紧实率大小的变化,就可以检查出型砂水分是否合
6.1 黏土砂型
6.1.2 湿型砂性能要求
5.起模性、变形量、韧性和破碎指数
1)型砂的起模性是表示起模时模样或模板与砂型分离时,砂型是
否容易损坏,产生开裂或掉落的性能。
6.1 黏土砂型
6.1.2 湿型砂性能要求
起模性的好坏与型砂的湿态抗压强度是两种不同的特性。
(1)抗压强度不仅反映了型砂的黏结力大小,还反映了砂粒受压
(1)湿型(简称湿型):造好的砂型不经烘干,直接浇人高温金属 液体; (2)干砂型(简称干型):在合箱和浇注前将整个砂型送入窑中烘 干;
(3)表面烘干砂型(简称表干型):在浇注前对型腔表层用适当方
建设用砂的标准要求
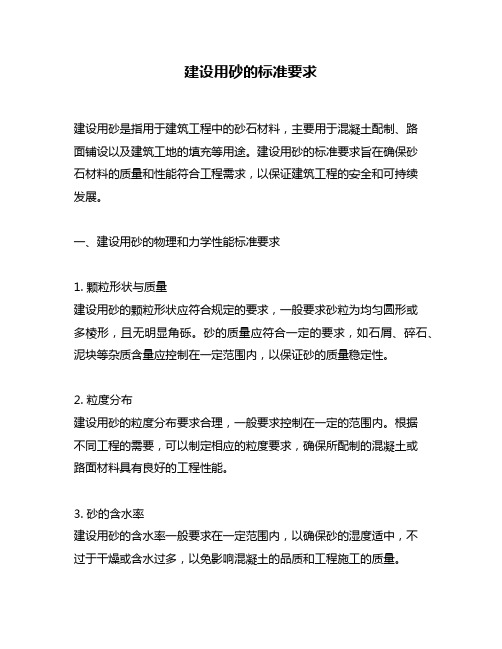
建设用砂的标准要求建设用砂是指用于建筑工程中的砂石材料,主要用于混凝土配制、路面铺设以及建筑工地的填充等用途。
建设用砂的标准要求旨在确保砂石材料的质量和性能符合工程需求,以保证建筑工程的安全和可持续发展。
一、建设用砂的物理和力学性能标准要求1. 颗粒形状与质量建设用砂的颗粒形状应符合规定的要求,一般要求砂粒为均匀圆形或多棱形,且无明显角砾。
砂的质量应符合一定的要求,如石屑、碎石、泥块等杂质含量应控制在一定范围内,以保证砂的质量稳定性。
2. 粒度分布建设用砂的粒度分布要求合理,一般要求控制在一定的范围内。
根据不同工程的需要,可以制定相应的粒度要求,确保所配制的混凝土或路面材料具有良好的工程性能。
3. 砂的含水率建设用砂的含水率一般要求在一定范围内,以确保砂的湿度适中,不过于干燥或含水过多,以免影响混凝土的品质和工程施工的质量。
4. 砂的密度建设用砂的密度要求一般根据具体工程的需要来确定,以保证砂的稳定性和工程施工的质量。
通常情况下,砂的密度应符合一定的要求,以确保其在工程中的使用性能。
二、建设用砂的化学性能标准要求1. 含泥量建设用砂的含泥量应符合一定的标准要求,以免过高的泥含量影响到混凝土的强度和稳定性。
2. 碱碳反应性建设用砂的碱碳反应性也是需要注意的一个指标,过高的反应性可能导致混凝土的开裂和损坏。
三、建设用砂的质量控制要求1. 材料来源建设用砂的原材料应来自正规的矿山或砂石加工厂,确保砂的质量可靠可控。
2. 技术标准与检测建设用砂的生产过程需要符合相关的技术标准和规范,并进行必要的质量检测。
包括对颗粒形状、粒度分布、含水率、密度、含泥量、碱碳反应性等指标的检测。
3. 监督与管理建设用砂的生产过程需要进行监督与管理,如质量监督、供应链管理、质量安全控制等,以确保生产出的建设用砂材料质量符合标准要求。
四、对建设用砂的可持续发展要求1. 矿山资源合理利用建设用砂的生产过程中需要合理利用矿山资源,进行矿山生态环境的保护和维护,减少对自然环境的破坏。
砂的技术要求

砂的技术要求:4.1 品种:砂按产源分为海砂、河砂、湖砂、山砂。
4.2 规格:砂按细度模数(Mx 分为粗、中、细、特细四种规格,其细度模数分别为:粗:3.7-3.1中,3.0~2.3细:2.2-1.6特细:1.5-0.74.3 等级:砂按其技术要求分为优等品、一等品、合格品。
注:砂的实际颗粒级配与表中所列数字相比,除5.00mm 和0.630mm 筛档外,可以允许略有超出分界线,但总量应小于5%。
一:砂的级配:是表示砂子大小颗粒的搭配情况。
砂的颗粒级配配置混难题是宜先选用2区砂。
当采取1区砂时,应提高砂率。
并保持足够的水泥用量,满足混凝土的和易性;当采取3区砂时,宜适当的降低砂率。
二:天然砂中含泥量技术要求对于有抗冻,抗渗或其它的要求的小于或等于C25混凝土用砂,其含泥量不应大于3.0%三:砂中的泥块含量技术要求对于有抗冻,抗渗或其它的要求的小于或等于C25混凝土用砂,其泥块量不应大于1.0%。
人工砂的总压碎值指标应小于30%试验方法:引用标准GB 177 水泥胶砂强度试验方法GB 601 化学试剂滴定分析(容量分析)用标准溶液的配制GB 602 化学试剂杂质测定用标准溶液的制备GB 2419 水泥胶砂流动度测定方法GB 6003 试验用筛GBJ81 普通混凝土力学性能试验方法3 术语3.1 砂指粒径小于5mm,在湖、海、河等天然水域中形成和堆积的岩石碎屑。
也可以是岩体风化后在山间适当地形中堆积下来的岩石碎屑。
3.2 泥指粒径小于0.08mm 的岩屑、淤泥与粘士的总和。
3.3 粘土块指水浸后粒径大于0.630mm 的块状粘土。
3.4 砂的细度模数(Mx)细度模数(Mx 是衡量砂粗细程序的指标,它是2.500,1.250,0.630,0.315 和0.160mm 等五种孔径的筛累计筛余百分率的总和。
3.5 坚固性指砂在自然风化和其他外界物理化学因目作用下抵抗研裂的能力。
3.6 碱集料反应指水泥和混凝土的有关添加剂中的碱性氧化物质(K2O,Na2O)与砂中活性二氧化硅等物质在常温常压下缓慢反应生成碱硅胶后,吸水膨胀导致混凝土破坏的现象。
高密度造型型砂的质量控制

砂至合格 ,此
后 2次 / h
发气量 温度 有效膨 润土含量 有效 煤粉含 量 水分 、温度
有效 膨 润 土含 量
1次/ 班 1次/ h
1 / 次 班
混砂机泄料 口 混砂机泄料 口 紧实 率 后 的 试 样混合
()紧实率正常 , 1 有效膨润 土含量在工艺 要求范 围
维普资讯
维普资讯
混砂效率降低及型砂水分波动,造型机模板粘砂,起模 困难,不易紧实, 铸件容易出现粘砂、冲砂、气孔等缺
陷 。因此 , 应把砂温作为 旧砂管理 的重要项 目,并控制
在低于室温 1 ℃ ( 5 夏季 <4 ℃) 0 。
\ 项目
类 \ 检验项目
水分
检验 频率
每班 开 始 混
取样地 点和 方法
混砂 机 泄 料 口
4 型砂性能的检测与控制 .
高密度型砂质量 的控制主要依靠 日常型砂性能 的检
测及 数据 统计分析 ,定期对型砂组分 的检验与调 整 ,根
砂至合格 ,此 紧实率
透气率
我公 司砂处理系统的 旧砂处理工艺及 控制流程 如下
图 所示 :
O. 0. 6~ 3~
2. O. 3~ 0. 2 3 1 8~ 1 0 5~ 2~ 00~
冬 季
O. O. 8 5
3
3. 2 O. 6 1 0. 4 0 0 3 8 10 4
表 2 型 砂 与 旧砂 检 验 项 目及 频 率
让膨润土 有充分 的 膨润 时 间,旧砂 增湿 系统尽 可 能提
性能参数
前 ,并保持一定 的砂量 ,保证 旧砂在进入 混砂机 之前至 少有 2 以上 的膨润时 间。旧砂水 分 的控 制 范围一般 为 h
型砂性能的测定方法+version+2

型砂性能的测定方法SOP编号:QI8.2.4-JQA-12版本:2.0BU FMCN18 Zhen Jiang PlantQM05.01.2017检测项目1)水分2)紧实率以及铸造性能3)吸蓝量/有效膨润土含量4)灼烧减量5)含泥量6)AFS细度分析仪器设备水分仪(红外或卤素)恒温干燥箱SIMPSON:锤式制样机,电子万能型砂强度测量仪,热湿拉强度仪,数显透气性仪1000 ℃马弗炉涡洗式洗砂机标准筛和振动机水分A.均匀取样5-10g采用红外水分测定仪进行测试B.也可取50g样品放入105℃恒温干燥箱至恒重C.试样水分可根据以下公式计算:m1—m2M= ×100m1M——样品水份,%;m1——试样的质量,g;m2——烘干后试样的质量,g紧实率以及铸造性能---紧实率A.样品筒检查:每次使用样品筒前必须确保样品筒内壁光滑,且无混合料或型砂残留;B.装砂:将样品筒连同底座放在投入器的下方,使样品通过投入器上部的筛网均匀流入样品筒,直到从样品筒上方溢出为止。
C.用刮砂板轻轻的刮除样品筒上多余的样品,刮砂时应从中央开始分别向左右刮平。
D.轻轻的将样品筒连同底座移至制样锤底部,用右侧手轮慢速旋转使主杆均匀的施加三次压力。
E.通过主杆左侧的50mm紧实率用游标尺读出相对应的紧实率结果。
F.注:制样机需固定在有支撑的水平台面上。
紧实率以及铸造性能---铸造性能标准试样的制备A.样品筒检查:每次使用样品筒前必须确保样品筒内壁光滑,且无混合料或型砂残留;B.装砂:将样品筒连同底座放在投入器的下方,取走投入器上部的筛网,称取适量的样品倒入样品筒,倒入时小心样品洒落C.轻轻的将样品筒连同底座移至制样锤底部,轻轻旋转左侧手轮降下主杆并将主杆压脚压入样品筒内的样品上,用右侧手轮慢速旋转使主杆均匀的施加三次压力给样品。
D.敲击三锤后,利用主杆左侧的50mm游标尺确认试样高度在50±1mm以内。
记录此时样重E.注:保持划轮完好,如有磨损需及时更换。
- 1、下载文档前请自行甄别文档内容的完整性,平台不提供额外的编辑、内容补充、找答案等附加服务。
- 2、"仅部分预览"的文档,不可在线预览部分如存在完整性等问题,可反馈申请退款(可完整预览的文档不适用该条件!)。
- 3、如文档侵犯您的权益,请联系客服反馈,我们会尽快为您处理(人工客服工作时间:9:00-18:30)。
高密度型砂性能要求(2010/09/04 17:08)目录:公司动态浏览字体:大中小前言高密度造型方法(或称高紧实度造型,包括多触头高压、气冲、挤压、射压、静压、吸压造型方法)的生产效率高、铸件品质较好,因而国内外应用都很普遍。
高密度造型对型砂品质的要求比较严格。
本文用表格(见文后附表)列举部分典型的国内外铸造厂实际应用的和部分设备公司推荐的高密度砂型主要的和经常测定的型砂性能,并加以评论。
1 紧实率和含水量湿型砂不可太干,否则膨润土未被充分润湿,起模困难,砂型易碎,表面的耐磨强度低,铸件容易生成砂孔和冲蚀缺陷。
型砂也不可太湿,过湿型砂易使铸件产生针孔、气孔、呛火、水爆炸、夹砂、粘砂等缺陷,而且型砂太粘、型砂在砂斗中搭桥、造型流动性降低。
使砂型型腔表面松紧不均;还可能导致造型紧实距离过大和压头陷入砂箱边缘以内而损伤模具和砂型吃砂量过小。
表明型砂干湿状态的参数有两种:紧实率和含水量。
附表中国内各厂的紧实率和含水量除特别注明以外,取样地点都在混砂机处。
但是型砂紧实率和含水量的控制应以造型处取样测定为准。
从混砂机运送到造型机时紧实率和含水量下降幅度因气候温度和湿度状况、运输距离、型砂温度等因素而异。
如果只根据混砂机处取样检测结果控制型砂的湿度,就要略增少许,以补偿紧实率和水分的损失。
以前的观点认为手工造型和震压式机器造型最适宜于湿状态下的紧实率大约在45~50%;高压造型和气冲造型时为40~45%;挤压造型要求流动性好,紧实率为35~40%。
由表中可以看出,目前铸件品质较好的工厂,高密度造型的型砂紧实率(大多是从混砂机取样)通常都在25~45%范围内,比较集中于30~40%之间,比以前有明显降低。
这是由于高密度造型设备的起模精度提高,而且要求砂型各部位硬度均匀分布,使型砂的流动性成为重要因素。
工厂的控制原则大多是只要能够保证起模顺利就尽力降低紧实率。
从减少铸件气孔缺陷的角度出发,要求最适宜干湿状态下型砂的含水量尽可能低。
高强度型砂的膨润土加入量多,型砂中含有较多灰分,所购入煤粉和膨润土因品质低劣而需要增大加入量,混砂机的加料顺序不当、揉碾作用不强、刮砂板磨损、混砂时间太短,以致型砂中存在较多不起粘结作用的小粘土团块,都会提高型砂的含水量。
根据资料,世界各国高密度砂型的型砂含水量基本上都在2.5~4.2%,比较集中于2.8~3.5%。
如果生产的铸件具有大量树脂砂芯(如发动机铸件),型砂含水量大多偏于下限,这是由于大量树脂砂芯溃散后混入型砂使含泥量下降和型砂吸水量降低。
我国有些铸造厂的型砂含水量很高,例如表中C-8厂实测高达5.0%,可能与旧砂含泥量高达16.7~18.0%有关。
型砂的紧实率/含水量比值可表示每1%型砂含水量能够形成多少紧实率,最好在10-12或稍高些。
由几家外商独资或合资企业的检验结果计算比值大多在10-12.7范围内。
曾测定三家乡镇铸造厂的比值在5.0~8.3之间,说明型砂吸水物质过多。
2 透气率砂型的透气率不可过低,以免浇注过程中发生呛火和铸件产生气孔缺陷。
但是绝不可理解为型砂的透气率越"高"越"好"。
因为透气率过高表明砂粒孔隙较大,金属液易于渗透而造成铸件表面粗糙,还可能产生机械粘砂。
所以湿型用面砂和单一砂透气性能应控制在适当的范围内。
对湿型砂透气率的要求需根据浇注金属的种类和温度、铸件的大小和厚薄、造型方法、是否分面砂和背砂、型砂的发气量大小、有无排气孔和排气冒口、是否上涂料和是否表面烘干等等各种因素而异。
用单一砂生产中小铸件时,型砂透气性能的选择必须兼顾防止气孔与防止表面粗糙或机械粘砂两个方面。
高密度造型的砂型排气较为困难,要求型砂的透气率通常稍高些。
但型砂含水量较小时,透气率可稍低些。
从附表可以看出较为适当的高密度造型型砂透气率大多在100~140之间。
如果型砂透气率在160以上,说明砂粒较粗,除非在砂型表面喷涂料,否则铸件表面会出现粗糙甚至有局部机械粘砂。
附表中A-2的透气率实测结果竟达250,上、下型都需要喷醇基涂料。
另一外资工厂的透气率不作为控制项目,偶尔测得透气率大约为200-280。
观察其铸件表面相当粗糙,原因是型砂中混入大量粗粒溃碎砂芯。
实际上,有很多生产发动机的铸造厂都遇到溃碎砂芯混入旧砂而使型砂透气率偏高的问题。
C-13的铸件表面并不粗糙,而测得透气率高达230-240,是仪器的通气塞孔洞尺寸过大所致。
3 湿态强度如果型砂湿态强度不足,在起模、搬运砂型、下芯、合型等过程中,砂型有可能破损和塌落;浇注时砂型可能承受不住金属液的冲刷和冲击,而造成砂孔缺陷甚至跑火(漏铁水);浇注铁水后石墨析出会造成型壁移动而导致铸件出现疏松和胀砂缺陷。
生产较大铸件的高密度砂型所用砂箱没有箱带,高强度型砂可以避免塌箱、胀箱和漏箱,无箱造型的砂型在造型后缺少砂箱支撑也需要具有一定的强度,挤压造型时顶出的砂型要推动先前造好的砂型向前移动,更对型砂的强度提出较高要求。
但是,强度也不宜过高。
因为高强度的型砂需要加入更多的膨润土,不但影响型砂的水分和透气性能,还会使铸件成本增加,而且给混砂、紧实和落砂等工序带来困难。
3.1 湿压强度一般而言,欧洲铸造行业对铸铁用高密度造型型砂的湿压强度值要求较高,欧洲造型机供应商推荐的湿压强度值范围在130~250kpa(下文各种型砂强度的单位均为kpa)之间,大多数为180~220。
有些日本铸造工厂对型砂湿压强度的要求偏低。
除表上所列的丰田公司和三菱川崎强度较高以外,很多工厂都在80~180。
北美铸造行业的型砂强度似乎介于欧洲和日本之间。
例如福特汽车厂Cleveland铸造厂排气管高压造型型砂为172,万国收割机公司Loisville铸造厂生产拖拉机缸体高压型砂为134~156。
有人认为欧洲铸造工厂的型砂湿压强度比美、日两国工厂高的原因之一是由于欧洲铸铁用原砂含SiO2较高,型砂中必须加入大量膨润土才能避免铸件产生夹砂结疤缺陷。
我国工厂高密度造型的型砂湿压强度比较接近美国和日本工厂,对于铸铁件而言,除个别铸造工厂外,高密度造型的湿压强度大多在120~200范围内,比较集中在140~180。
湿压强度控制值较低的原因之一是所使用的振动落砂机破碎效果不好,大砂块会随铸件跑掉。
而且很多铸造厂选用的膨润土品质较差,型砂的湿压强度稍低些,就无需加入大量膨润土,型砂含水量也可低些。
高密度湿型铸钢需要防止铸件生成热裂缺陷,因而所用型砂的湿压强度大多在70~130之间。
3.2 湿拉强度和湿劈强度从材料力学角度来看,抗压强度除代表型砂粘结强度以外,也还受砂粒之间摩擦阻力的影响,而抗拉强度无此因素。
但是测定型砂的湿态抗拉强度必须使用特制的试样筒和试验机,所以很多中小铸造厂不测定型砂的抗拉强度。
通常要求湿拉强度>20。
有人按照混凝土试验中曾使用过的办法将圆柱形标准试样横放,使它在直径方向受压应力,就可以得出近似抗拉强度的湿态劈裂强度值。
我国几家工厂的要求在30~50之间。
DISA公司推荐的湿劈强度是30~34,还给出了用劈裂强度估算抗拉强度的近似公式:湿拉强度=湿劈强度×0.65。
3.3 湿剪强度湿剪强度比湿压强度更能表明型砂的粘结力而且容易测定。
国外设备公司建议高密度造型线的型砂湿剪强度值为30-50(剪切力作用在标准试样的两端平面上),A-5实测为52,B-1实测为38-55。
另一种较新的测试方法,剪切力作用在试样圆周面上。
这种仪器可以同时测出抗剪强度和剪切断裂时的变形量。
两种湿剪强度数值是一致的。
通常生产用型砂的变形量多在0.40~0.70mm范围内。
例如A-6测得挤压造型型砂剪切强度约为60,变形量约为0.50mm。
3.4 表面强度(表面耐磨性)湿砂型应有足够高的表面强度,能够经受起模、吹净、下芯、浇注等过程的擦磨作用。
否则型腔表面砂粒在外力作用下容易脱落,可能造成铸件的表面粗糙、砂孔、粘砂以及夹砂等缺陷。
在有些铸造厂中,从起模到合箱之间砂型敞开放置较长时间,以致铸型表面水分不断蒸发,即"风干",可能导致表面耐磨性急剧下降。
间隔时间长,天气干燥,型砂温度过高时,风干现象尤其严重。
美国Dietert 公司推荐利用测定造型性的圆筒筛,将两只圆柱标准试样并列放置其中,转动1min后称量掉落的砂量,用来代表型砂的耐磨性。
日本较多使用的方法是将标准试样放置在6目筛上,在震摆式筛砂机上震动60s,以震摆前、后试样重量的比率称作为"表面安定度(SSI)"。
日本东久公司推荐水平分型无箱射压线的型砂试样湿态即时表面安定率为>88%,调查6家铸造厂的表面安定度都在88.9-91.0%范围内。
土芳公司调查8家静压和气冲线在77.6-86.6%范围内,平均82.5%。
我国A-1实测结果在70-89%范围内;A-4实测结果是89.9-90.6%。
在湿砂型喷涂表面稳定剂或涂料和在型砂中加入淀粉都能提高表面耐磨性,为了避免表面安定度试验的试样在筛上出现不规则的颠簸翻滚,而使掉落砂量波动,耐磨性测定装置使用钢丝针布对试样表面刷磨,称量1min的磨下量即可代表湿型砂试样的表面耐磨性。
用内蒙精洗砂100%,天然钠基膨润土或钙基膨润土8%,α淀粉0-1%配制型砂,紧实率按45%控制。
不加α淀粉的钠基膨润土空白试样,即时磨损量约为8g,风干2h后磨损量增加到40g以上;加入1%α淀粉的钠基膨润土试样即时磨损量降为0.37g,风干2h后磨损量仅约为2g左右。
钙基膨润土试样即时磨损量高达16g,加入α淀粉后即时磨损量降为1.8g。
4 型砂含泥量型砂和旧砂的泥分是由有效膨润土、煤粉以及无效的灰分组成的。
通常型砂比旧砂的泥分含量多0.5~3.0%。
型砂含泥量直接影响型砂的各种性能,所以应当以型砂含泥量的检测和控制为主。
附表中含泥量除专门注明外大都是指旧砂而言。
有些铸造厂的型砂和旧砂含泥量过高,原因可能是所使用的原砂、膨润土和煤粉品质不良,旧砂缺乏有效地除尘处理造成的。
还有些发动机铸造厂的型砂出现含泥量过低现象,是旧砂中混入大量溃碎树脂砂芯造成的,以致型砂适宜含水量太低,透气率太高,性能难以控制。
一些国外生产铸铁件工厂型砂含泥量的情况举例如下:美国的汽车制造厂型砂含泥量大多较低,例如John Deere生产球墨铸铁的高压造型型砂含泥量为7.5~8.8%。
International Harvester生产拖拉机缸体的型砂含泥量为9~10%。
GMC生产雪佛兰缸体型砂为9~11%;德国Meinheim的John Deere分厂的三种型砂含泥量的控制指标分别为10.0~12.5%、11.0~13.0%和11.0~13.5%;Luitpold铸造厂生活大众汽缸体用型砂为12~13.5%。