型砂
型砂试验操作规程

型砂试验操作规程型砂试验操作规程是对进行型砂试验时的操作流程和方法进行规范化的一份文件,旨在确保试验的准确性和可重复性。
下面是一份1200字左右的型砂试验操作规程,供参考:一、试验目的型砂试验的目的是为了评估材料的物理力学性质和工程性能,以提供给设计和施工方案的依据。
二、试验设备及材料1. 型砂试验设备:型砂盒、压力机、程控仪表等。
2. 材料:测试样品、型砂、水等。
三、试验前的准备工作1. 安装和调试型砂试验设备,检查设备是否正常运转。
2. 准备型砂盒,进行必要的清洁和干燥,确保试验结果的准确性。
3. 准备型砂样品,通过筛选和处理,确保砂粒的均匀和干燥。
四、试验的具体操作步骤1. 样品制备:(1)根据试验需求,将型砂盒分为若干层,每一层厚度控制在5-10毫米。
(2)将干燥的型砂均匀地加入到型砂盒中,用压实器对型砂进行均匀的加压,直至达到试验要求的标准厚度。
(3)将试验样品嵌入到型砂中,确保样品与型砂的贴合度。
(4)进行任何必要的标记,以便于后续操作。
2. 试验过程控制:(1)将型砂盒放置在压力机上,调整好试验参数,如加载速度、加载方式等。
确保试验参数符合试验要求。
(2)开始加载,记录下试验的开始时间和加载的力值。
(3)以恒定速度加载样品,同时记录下加载过程中的力值和变形量。
(4)加载到规定的终点时停止加载,并记录下试验的结束时间和加载的最大力值。
3. 试验结果处理:(1)根据试验数据计算出样品的应力应变关系和其他力学参数。
(2)对试验结果进行分析和评价,得出对材料性能的评估。
五、试验安全注意事项1. 操作人员必须严格遵守试验操作规程,避免操作失误导致安全事故的发生。
2. 使用压力机时,应确保操作人员的安全距离,并佩戴好安全帽、护目镜等个人防护装备。
3. 在试验过程中,要随时观察设备的运行状态,发现异常情况及时停止试验并报告维修。
六、设备的日常维护和保养1. 每次试验结束后,对设备进行彻底的清洁和维护,保持设备的干净和整洁。
常用型砂种类

机器造 )’ %’&()*& &.,/&.&.* * — ,.-/*.+ — 2&/)+& ’-/%& +.— — 型活化砂, 铸造机床 铸件
・ 2&, ・
第三篇
造型材料
配 比 (!) 碳酸钠 煤 粉 (以膨润 其他 土为基) 含水量紧实率 ( ! )( ! ) 性 湿 压 热湿拉 透气性 强 度 强 度 能 含泥量 用 其 他 途
%
—
.,/ + -,. &’’ + )’’ %0 + 11 —
0
—
1’(&-’
&’’
1,%
—
—
—
.,% + -,’
2 &’’
%’ + 1% —
1
—
1’(&-’
&’’
-,%
—
—
煤粉 ) + - .,’ + -,’
2 /’
%’ + 1’ —
表.5)5序 号 旧 砂 新 砂
工厂有色合金铸件湿型砂配方及性能实例
第三篇
造型材料
配 比 ( !) 他 含水量 ( !) 性 透气性 能 湿压 紧实 用 途 强度 率 ( !) ("#$) 小型铸 钢件 3 &’’"4 碳 钢件 3 &’’"4 耐 热钢件
序 号 旧 砂
新 砂 膨润土 碳酸钠 糊 精 其 粒度组别 加入量 &’’()’’ &’’ * + && ’,) ’,) + ’,—
震击造 %* *( ,( 0/()-/( — — ./()2/( — !’( 2*)*0 — — — 型背砂, 铸 造灰铸铁 缸体 黏土 0( 2( 0(+.( -( &)’ — %)0 木屑 手工造 2/.)&/. — 1 ,.( &()*( — ,(),. — 型, 铸造灰 铸铁大件
型砂试验管理制度

型砂试验管理制度第一章总则为加强对型砂试验工作的管理,提高试验工作的质量和效率,保证试验数据的准确性和可靠性,特制定本制度。
第二章试验单位的责任与义务1、试验单位应当设置专门的试验室,配备必要的设备和仪器,确保试验工作的正常进行。
2、试验单位应当建立健全的试验管理制度,明确试验人员的职责和权限,保证试验工作的规范进行。
3、试验单位应当加强与相关单位的沟通和协作,确保试验工作与其他工作的衔接和协调。
第三章试验人员的素质与要求1、试验人员应当具备与岗位要求相适应的专业知识和技能,熟悉型砂试验工作的操作流程和标准要求。
2、试验人员应当具备良好的职业道德和团队合作精神,认真负责地完成试验工作。
3、试验人员应当保持学习和进步的态度,不断提高自身的技术水平和素质能力。
第四章试验管理制度1、试验人员应当严格遵守试验操作规程,按照相关标准和要求进行试验工作。
2、试验人员应当严格遵守试验安全操作规定,做好试验工作的安全保障。
3、试验人员应当认真填写试验记录,确保试验数据的真实和完整。
4、试验人员应当及时上报试验中出现的问题和异常情况,积极协助解决。
第五章试验设备和仪器的管理1、试验设备和仪器应当定期进行检测和校正,保证其准确性和稳定性。
2、试验设备和仪器应当科学合理地进行存放和维护,确保其正常使用和延长使用寿命。
3、试验设备和仪器的使用人员应当经过专门培训和考核,掌握相关操作技能和注意事项。
第六章试验数据的保存和利用1、试验数据应当按照规定的格式和方式进行保存和归档,确保其完整性和可追溯性。
2、试验数据应当按照规定的要求进行分析和利用,为相关工作提供可靠依据和支持。
第七章试验质量控制与提升1、试验单位应当建立健全的试验质量控制体系,明确工作目标和任务要求。
2、试验单位应当加强对试验工作的质量监督和检查,及时发现和纠正存在的问题和不足。
3、试验单位应当加强试验技术交流和经验分享,不断提升试验质量和水平。
第八章试验管理的监督与考核1、试验单位应当建立试验管理的监督机制,加强对试验工作的检查和评估。
第二节 型砂的制作

Logo
机械制造工艺基础
• (1)外浇口。小型铸件外浇口通常为漏斗状,大型铸件
的为盆状。作用是容纳浇入的金属液并缓解液态金属对型 砂的冲击。
• (2)直浇道。是连接外浇口与横浇道的垂直通道,改变
直浇道的高度可以改变金属液的流动速度,改善金属充型 能力。
• (3)横浇道。是将直浇道我金属液引入内浇道的水平通
Logo
机械制造工艺基础
Logo
机械制造工艺基础
• 三、造型
造型是利用模样和砂箱等工艺装备将型砂制成铸型的方法。 • 按操作方法不同,造型方法可分为手工造型和机器造型。
• 1.手工造型
• 手工造型的基本工序是填砂、紧砂、起模和合型。主要用
于单件、小批量生产。
Logo
机械制造工艺基础
• 2.手工造型的基本过程
• (4)透气性。浇注时产生的气体顺利通过型砂间隙逸出的性
能。
• (5)即让性。当铸件在固态冷却收缩时,型砂体积可被压缩
的性能。
Logo
机械制造工艺基础
• 3.型砂的配制
• 型砂的配制工艺一般由四
个部分组成:
Logo
机械制造工艺基础
• 二、模样和型芯盒
• 1.模样和型芯盒
• 模样和型芯盒是制造型砂的基本工具,模样是用来获得铸件
Logo
机械制造工艺基础
• 六、合箱
• 型砂的装配称为合箱,又称合型。 • 合型前要对砂型和型芯的质量进行检查,若有损坏,需要
进行修理;合型时要保证铸型型腔几何形状和尺寸。合型 后,上、下型应夹紧或在铸型上放置压铁,以防浇注时上 型被熔融金属顶起,造成事故。
Logo
机械制造工艺基础
•知识小结:
用型砂紧实成型进行铸造的方法

用型砂紧实成型进行铸造的方法,称为砂型铸造。
砂型铸造生产的铸件占铸件总产量的80%以上,而在砂型铸造中,重要而大量的工作是制造铸型。
与其它金属加工方法相比,铸造具有如下优点:(1)原材料来源广。
(2)生产成本低。
(3)铸件形状与零件接近,尺寸不受限制。
但铸造生产目前还存在着若干问题,如铸件内部组织粗大,常有缩松、气孔等铸造缺陷,导致铸件力学性能不如锻件高。
铸造工序多,而且一些工艺过程还难以精确控制,使得铸件质量不够稳定,废品率高。
砂型铸造所用的型(芯)砂由原砂和粘结剂组成,必要时,还加入各种附加物。
原砂是耐高温材料。
常用的是含SiO2较多的硅砂。
常用的粘结剂有粘土、水玻璃等。
型砂和芯砂应具有以下性能:(1)透气性(2)强度(3)耐火度(4)可塑性(5)退让性上述性能要求是最基本的,有时又是互相矛盾的,因此,要求型砂具有良好的综合性能。
生产中常采用砂子、粘土(常用膨润土)和水等经混制而成的粘土砂。
为满足透气性、型砂中还可加入锯末、煤粉等。
铸型一般由上型、下型、型芯、浇注系统等几部分组成。
图3-2为常用两箱造型的铸型示意图。
图中铸型各组成部分的作用列入表3-1。
表3-1铸型各部分的作用型芯的作用及形成3、型芯是砂型中的重要组成部分,在制造中空铸件或有妨碍起模的凸台铸件时,往往要使用型芯。
常用的型芯有:(1)水平型芯,(2)垂直型芯,(3)悬臂型芯,(4)悬吊型芯,(5)引伸型芯(有利于取模),(6)外型芯(可使三箱造型变为两箱造型)等。
图3-3是上述几种型芯的示意图。
造型方法按砂型紧实方式分为手工造型和机器造型两大类。
手工造型手工造型是全部用手工或手动工具紧实型砂、制成砂型的造型方法。
其优点是操作方便,灵活性强,特别适合于单件小批生产。
用机器全部完成或至少完成紧砂操作的造型方法称为机器造型。
按紧砂和起模方式不同,有多种不同类型的机器造型方法及相应的造型机。
手工造型工序流程。
根据铸件结构、生产批量和生产条件,可选用不同的手工造型方法。
型砂试验操作规程

型砂试验操作规程型砂(旧砂)含泥量的测试方法1范围本实验程序概述了型砂(旧砂)含泥量的测试方法。
2型砂水分的概念指型砂(旧砂)中直径小于20微米的细粉的含量。
3所需仪器虹吸式洗砂机;双盘红外线烘干器;感量为0.01的天平;漏斗,中速滤纸,玻璃棒;4实验程序4.1取300克左右型砂(旧砂),用四分法取100克烘干待用;4.2用天平称取50±0.1克旧砂,将试样放入容量为600ml专用洗砂杯中,加入390ml蒸馏水和10ml浓度为5%的焦磷酸钠溶液,煮沸3-5分钟,将洗砂杯置于洗砂机上,搅拌15分钟,取下洗砂杯。
4.3向洗砂杯中加入清水至标准高度125mm处,用玻璃棒搅拌30秒,静止10分钟,用虹吸管排除浑水。
第二次仍加清水至标准高度125mm处,用玻璃棒搅拌约30秒后,静置10分钟,用虹吸管排除浑水。
第三次操作与第二次相同,但每次仅需静置5分钟,这样反复多次,直至洗砂杯中的水已达到透明无泥类为止;4.4最后一次将洗砂杯中的水排除后,将试样和水到如直径为100毫米左右的玻璃漏斗中过滤,然后将试样连同滤纸置于玻璃皿中,在电烘箱中烘干至恒温(温度140-160度)。
烘干后置于干燥器中,待冷却至室温后称重量。
5型砂(旧砂)含泥量的计算试样含泥量=(试验前试样重量-试验后试样重量)÷试验前试样重量×100%型砂紧实率测试方法1范围本实验程序概述了型砂紧实率的测试方法。
2型砂紧实率的概念指型砂的可紧实程度。
3所需仪器锤击试样机Φ50标准装样筒,底座型砂透砂器6目标准筛4实验程序4.1从混砂机或造型机处取混好的型砂约2公斤,用密封容器密封带回实验室,以保持型砂的水分不损失;4.2将6目筛放在投砂器的上端对齐,再将标准样筒和底座安装好,放在投砂器的正下方,使样筒的外圈和投砂器的外圈对齐;4.3将取来的型砂均匀的透过6目筛落放到样筒中,直至装满;4.4刮平样筒顶部多余的砂,将整个组合(装样筒,底座杯和未紧实的砂)移至标准样锤击制样机上。
老师傅手把手教你配制铸造型砂,太实用了!

老师傅手把手教你配制铸造型砂,太实用了!型砂的配制包括三个方面,即原材料的准备、型砂的混制和将混制好的型砂调匀及松砂等工艺环节。
铸造生产中所使用的型砂,有的是由回用砂加适量的新砂、粘土和水经混合均匀配制成的,有的全部是由新的材料配制成的。
为了确保新砂质量,所有的原材料都须根据技术要求经验收合格后才能使用。
为此,在配砂前都必须进行加工准备。
(1)新砂新砂在采购、运输过程中常混有草根、煤屑及泥块等杂物,同时含有一定数量的分分。
潮湿的原砂不易过筛,配砂时不便于控制型砂的水分。
因此,除含水量低、用于手工造型的湿型砂可直接配制外,新砂在使用前必须进行烘干和过筛。
新砂的烘干用立式或卧式烘干滚筒,也可采用气流烘干的办法。
常用的筛砂设备有手工筛、滚筒筛和振动筛等。
(2)粘土刚开采的粘土往往含有较多的水分具多为块状,因此使用前必须烘干、破碎并磨成粘土粉,主要由专门的工厂进行加工,包装万袋供应。
有的工厂事先将膨润土或粘土与煤粉按比例制成粘土—煤粉粉浆,使粘土充分吸水膨胀,混砂时与原砂一起加入到混砂机里混合均匀。
这种做法可简化混砂操作,便于运输,改善劳动条件,提高型砂质量。
但必须严格控制粉浆的含水量,否则会影响型砂性能。
(3)附加物煤粉、硼配、氟化物和硫黄等附加物都必须粉碎、过筛后再使用。
(4)旧砂为了节省造型材料,降低铸件成本,旧砂应回用。
旧砂在型砂所占比例很大,它对型砂的成分及性能有着很大的影响。
旧砂中常混有各种杂物,如钉子、铁块和砂团等,在回用前必须进行处理,包括将砂块粉碎,用电磁分离器除去其中的铁质杂物然后过筛,必要时进行冷却。
在机械化程度高的铸造车间,型砂需求量大,周转速度很快,往往旧砂的温度还比较高,有的回用砂温度高达60摄氏度以上,如果采用这种型砂造型,容易粘附模样、芯盒及砂斗。
由于型砂温度过高,会使水分蒸发太快,使型砂性能不稳定,同时影响铸件表面质量,影响造型劳动生产率。
因此必须在铸件落砂、旧砂过筛、运输和混砂过程中加强通风冷却,降低型砂温度。
型砂理论知识培训1

6、煤粉
6.1煤粉的理解 6.1.1煤粉是以烟煤为原料经粉碎制成的产品,外观为黑色或黑褐色的细粉
6.1.2衡量煤粉的主要指标是挥发份、烧失量
6.2煤粉的作用 6.2.1铁液凝固时产生的碳氢化合物气体,高温作用下煤粉可以溶泡沫状,充斥砂粒间,曾加透气性防止气
孔的生成
300 3350 6
3、芯砂 3.1芯砂知识
3.1.1、芯砂是指------树脂与新砂的结合物,通过加热达到粘合成形的砂 3.1.2、芯砂的作用------通过不固定的模型加热成型后,形成多样的砂型产品
3.1.3、芯砂表面包裹的树脂是有机物能产生气体
3.1.4、加热后的砂芯具有吸潮能力(故此它有储存期限) 3.1.5、制造出来的砂芯具有一定的强度 3.2针对以上芯砂知识,砂芯检测项目以及影响 3.2.1、检测项目有如下: 3.2.2砂芯的影响
2.3.2砂粒度的图表认识
a、砂粒形图形
角 圆 形 长 石 圆 形
云母
多角形
2.3.3新砂的相关技术参数
a、新砂粒度大小等级可分为:①40-70目;②50-100目;③70-140目;④100-200目。
b、实验筛目与系数可分为:筛目AFS间距为10-20% 每个筛目不允许超过40% c、新砂SiO2烧结点为1713℃ d、新砂进厂含泥量0.5%以下 e、筛盘孔径大小如下(依国标) f、 AFS粒度指数控制在58-62之间产品质量良好
x x x x 混砂后来自重新吸水重新吸水, 小部分完成
未重新吸水
4.2.2鉴于膨润土与水的关系,建议在混炼过程中:先干混 (新旧砂+粘土+煤粉)-----均匀加水湿混 4.3膨润土的认识 4.3.1膨润土虽好但要注意它的加入量与混炼效果,以下介绍它的作用与危害 : a、膨润土加入--------加入量少,砂型强度低没有粘性掉砂砂眼。加入多带出量多,水多强度低产品气孔
型砂铸造
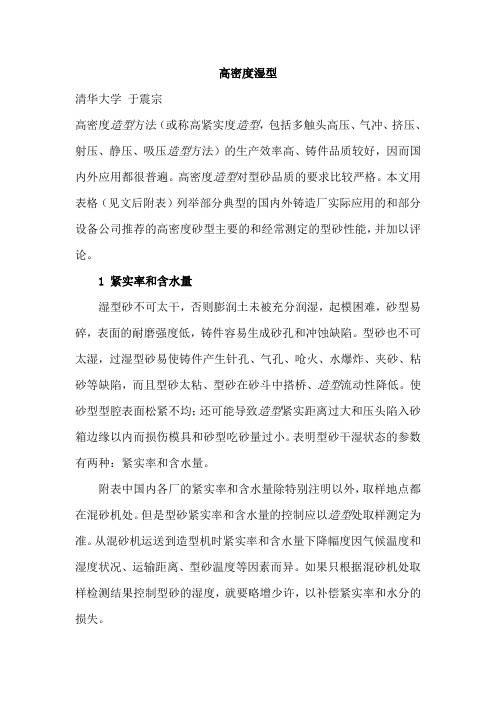
高密度湿型清华大学于震宗高密度造型方法(或称高紧实度造型,包括多触头高压、气冲、挤压、射压、静压、吸压造型方法)的生产效率高、铸件品质较好,因而国内外应用都很普遍。
高密度造型对型砂品质的要求比较严格。
本文用表格(见文后附表)列举部分典型的国内外铸造厂实际应用的和部分设备公司推荐的高密度砂型主要的和经常测定的型砂性能,并加以评论。
1 紧实率和含水量湿型砂不可太干,否则膨润土未被充分润湿,起模困难,砂型易碎,表面的耐磨强度低,铸件容易生成砂孔和冲蚀缺陷。
型砂也不可太湿,过湿型砂易使铸件产生针孔、气孔、呛火、水爆炸、夹砂、粘砂等缺陷,而且型砂太粘、型砂在砂斗中搭桥、造型流动性降低。
使砂型型腔表面松紧不均;还可能导致造型紧实距离过大和压头陷入砂箱边缘以内而损伤模具和砂型吃砂量过小。
表明型砂干湿状态的参数有两种:紧实率和含水量。
附表中国内各厂的紧实率和含水量除特别注明以外,取样地点都在混砂机处。
但是型砂紧实率和含水量的控制应以造型处取样测定为准。
从混砂机运送到造型机时紧实率和含水量下降幅度因气候温度和湿度状况、运输距离、型砂温度等因素而异。
如果只根据混砂机处取样检测结果控制型砂的湿度,就要略增少许,以补偿紧实率和水分的损失。
以前的观点认为手工造型和震压式机器造型最适宜于湿状态下的紧实率大约在45~50%;高压造型和气冲造型时为40~45%;挤压造型要求流动性好,紧实率为35~40%。
由表中可以看出,目前铸件品质较好的工厂,高密度造型的型砂紧实率(大多是从混砂机取样)通常都在25~45%范围内,比较集中于30~40%之间,比以前有明显降低。
这是由于高密度造型设备的起模精度提高,而且要求砂型各部位硬度均匀分布,使型砂的流动性成为重要因素。
工厂的控制原则大多是只要能够保证起模顺利就尽力降低紧实率。
从减少铸件气孔缺陷的角度出发,要求最适宜干湿状态下型砂的含水量尽可能低。
高强度型砂的膨润土加入量多,型砂中含有较多灰分,所购入煤粉和膨润土因品质低劣而需要增大加入量,混砂机的加料顺序不当、揉碾作用不强、刮砂板磨损、混砂时间太短,以致型砂中存在较多不起粘结作用的小粘土团块,都会提高型砂的含水量。
型砂性能试验
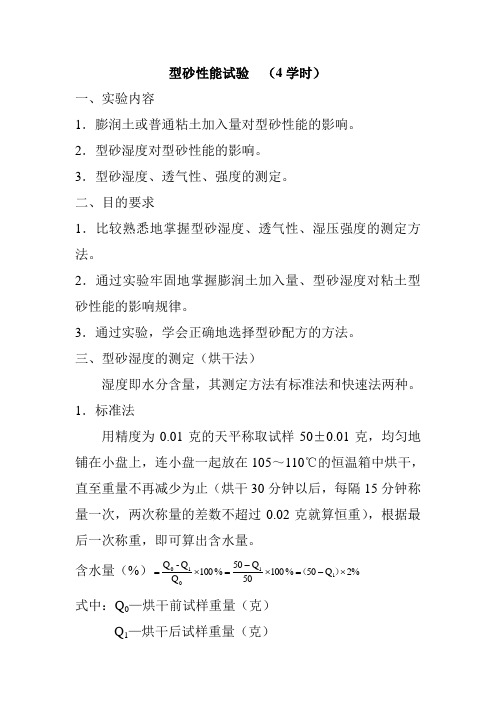
型砂性能试验 (4学时)一、实验内容1.膨润土或普通粘土加入量对型砂性能的影响。
2.型砂湿度对型砂性能的影响。
3.型砂湿度、透气性、强度的测定。
二、目的要求1.比较熟悉地掌握型砂湿度、透气性、湿压强度的测定方法。
2.通过实验牢固地掌握膨润土加入量、型砂湿度对粘土型砂性能的影响规律。
3.通过实验,学会正确地选择型砂配方的方法。
三、型砂湿度的测定(烘干法)湿度即水分含量,其测定方法有标准法和快速法两种。
1.标准法用精度为0.01克的天平称取试样50±0.01克,均匀地铺在小盘上,连小盘一起放在105~110℃的恒温箱中烘干,直至重量不再减少为止(烘干30分钟以后,每隔15分钟称量一次,两次称量的差数不超过0.02克就算恒重),根据最后一次称重,即可算出含水量。
含水量(%)2%Q 50%10050Q 50%100Q Q -Q 11010⨯-=⨯-=⨯=)( 式中:Q 0—烘干前试样重量(克)Q 1—烘干后试样重量(克)2.快速法铸工车间通常用图8示红外线烘干器测定型砂湿度。
其过程如下:用天平称取试料50±0.1克或20±0.1克,均匀无损地铺在承砂盘上,并将承砂盘插入红外线烘干器中,开启电源,型砂在红外线灯光照射下被烘干,直至恒重,大约需要4—8分钟,冷却后重新称重,便可按下式计算含水量。
含水量(%)%100Q Q -Q 010⨯=图8 红外线烘干器四、圆柱形标准试样的准备标准砂样是在图9示的摏砂样器上制成,其过程如下: ①称取型砂160~170克(一般根据经验取样)左右,倒入圆柱形试样筒中(注意试样筒中不要装倒)。
图9 摏砂样器②右手操纵手柄5使冲头举起,左手将砂样筒连同底座放于冲头下,然后放下手柄5,使冲头插入砂样筒内。
③转动凸轮手柄3三次,使重锤冲击试样三次。
此时,应检查冲击导杆顶端是否在公差刻线之内,如在刻线之内,试样便制成,否则试样应报废、重做。
④右手操纵手柄5使冲头举起,左手将试样筒取出,试样筒连同试样一起拿到透气性测定仪上去测定型砂透气性。
型砂测试操作规程(17)

型砂测试操作规程1. 目的本规程为沙铸混砂工序中型砂测试的一般性工艺规则,为检验人员,技术人员在工作中提供依据.2. 使用范围本规程适用于本厂砂型铸造用沙的性能测试.3. 规程要求3.1 透气性的测定:a) 设备:SAC锤击式制样机,天平,STZ直读式透气性测定仪称取试样150-190克,倒入样筒内,将样筒连同底坐放在锤击式制样机上,轻轻放下锤杆扳手,使冲头压入筒内b) 转动凸轮摇手,转三转,使重锤冲击试样三次, 凸轮摇手,摇动速度以每3秒为宜,重锤落下冲击时,摇手要静止片刻,并注意重锤不要冲击凸轮边上,此时冲击导杆顶端应在公差刻度线内c) 右手拉下械杆扳手,使冲头举起,左手将试样筒取出,将试样样筒放在透气性测定仪的橡皮试座上,并轻微压紧d) 将三通阀旋至工作位置,钟罩下降,水柱上升,由水柱压力计读数, 读出透气性e) 试验前应首先检查仪器的准确程度,提起密封样筒,保持10分钟钟罩不下降.调节水柱压力计右上角的调整螺丝,使标尺的零位线与水柱内的水面齐平3.2 强度的测定3.2.1 设备:SWY液压强度机3.2.2 正强度的测定:将抗压夹具置于仪器上,把冲制的圆柱形试样放在夹具上(试样的制作同透气性测定2 , 3 )转动手轮,使压逐渐作用于试样上,直至试样破碎,破碎时压力表指针停留位置所指抗压圈刻度值即为测试的抗压值。
3.2.3 拉强度的测定:将抗拉夹具置于仪器上,将冲制的θ字型试样放入夹具中并使夹具中四个滚动栏的中面贴住试样腰部,使压力通过夹具顶板作用于试样上,直至试样断裂,压力表挡针停留,住圈所挡抗拄圈刻度值即为测试的抗拄强度值。
3.3 粒度的测试:a) 设备:SSZ震摆或筛砂机天平sgh双盘红外线烘干器b) 操作方法:将试验筛按照筛孔径大小顺序摆放,称50克型砂,放入烘干器烘6-9分钟后,倒入顶层SBSO1号6目筛内,盖好筛盖,并放在筛砂机筛座上逆时针旋转夹筛盘6上的手柄,将整个夹筛盘向上调得筛盖上然后顺时针旋转夹筛盘上的手柄,其内顶杆轴夹紧支承套,把标准筛固定.将定时器放钮拨到筛分所需的时间(3-15分钟)打开电源开关,筛砂机自动停止,逆时针旋转夹筛盘上手柄使夹筛松开,并上提固定滑套,取下试验筛,依次将残存在各号筛内的砂粒倒在纸上,分别用天平称重(精确到0.1克)筛内如嵌有砂粒不可敲击标准筛应用毛刷轻轻刷下,将各号筛内残存砂粒称重后并记录,最后计算出每种砂粒占试样总重(50)克的百分率.3.4 含水量(水分)的测定:a) 设备: 天平sgh双盘红外线烘干b) 操作方法:称砂20(+ -)0.05克倒入盛砂盘中,均匀铺平,将盛砂盘放置在红外线烘干器内,烘6-10分钟,取下试样,冷至室温,再用天平重新标重,精确至0.01克.含水量= (烘前重量-烘后重量)÷烘前重量×100%3.5 紧实率的测定:a) 设备: SAC锤击式制样机,SBS型标准筛b) 操作方法:将试样筒放在标准筛下面,把型砂倒入标准筛,使之自然漏入试样筒内,用刮刀将试样筒上多余的试样刮去,然后将装有试样的标筒在SAC锤击式制样机上冲击三次,试样体积压缩的程度,即为紧实率,其数值可直接从制样机上读取.3.6 灼烧减量的测定:a) 设备:SX2-4-10箱式电阻炉天平b) 操作方法: 称砂2(+ -)0.05克放在瓷舟中,电阻炉温度调到1000-1050度之间,把型砂放入电阻炉中,30分钟后拿出,称重.灼烧减量=(灼烧前重量—灼烧后重量)÷灼烧前重量×100%3.7 发气量的测定:a) 设备:GET—11智能发气性测试仪天平b) 操作方法:(1)按下船型主电源开关,接通主电源,参数显示区显示(HELLO)约30分钟左右,自动进入监控状态,参数显示区显示“)-”(2)在监控状态下,按下电源“通”按钮,指示灯亮,开始升温,约30分钟左右,炉温和系统温度将达到设定值.恒温10分钟左右,即可进行发气性的测试(3) 称取1.00克试样置于烧舟中,在监控状态下,将样舟推入炉膛的恒温区,迅速盖上密封盖并按“测量”键,仪器开始工作,试样的发气量和对应的时间将同步显示在参数显示区.(4) 当参数显示区的数值不再上升或下降时,按“结束”键,参数显示区显示出发气量和对应时间,再按“打印”键,发气量以图形方式输出,再按“0”键,发气量以数据方式输出.(5) 试验结束后,取下炉口的端盖,先按“断”按钮关断控制电源,然后切断主电源.4. 详情请参照使用说明书.5.1 焦碳的检测:5.1.1 检验设备:烘干箱天平5.1..2 水分(每次分析必须新到试样),称样1.00(+ -)0.05g,记录(1)皮重,(2)料重,将料置于烘干过圆坩锅中,放入105-110℃的烘干箱内烘90分钟,取出试样冷却至室温,备注:从保温箱中样品取出时,注意样品的完整性5.1.3 计算公式:水分含量%=(皮重+净料-烘后总重)÷净料×1005.2. 检验设备:电炉天平5.2.1 灰分:称样1(+ -)0.05g,置于燃烧过的方灰四(方舟)中,均匀撒开,不要将样品堆放在一起,防止燃烧不彻底,将方舟置于灰四架上,用长钳将灰四架,灰四放入已设定好的8.5(+ -)10℃的炉中.注意:刚放入的灰四架要在炉门处,并将炉门开一缝进氧,时间2分钟后再将灰四架移入电炉中心,保温90分钟,炉门一直留一条缝进氧备注:灰四,方舟,圆坩锅在815(+ -)10℃的温度中烘烤30分钟后方可使用,取出试样,冷至室温(注意避风,灰分流失)5.2.2 计算公式:灰分含量%=(烘烧后总重-皮重)÷净料×1005.3 检验设备:电炉天平5.3.1 挥发分: ,称样1.00(+ -)0.05g置于烘干过圆坩锅中,(1)记录坩锅皮重,(2)去皮记录净料重. 将置好试样盖上盖子放到灰四架上迅速将灰四架放入已设好的900℃电炉中,放置位置入炉中心,保温7分钟,将炉门关严,取出试样冷至室温,称量:烘后总重.5.3.2 计算公式:挥发分%=皮重+净料重烘后总重÷净料×1005.4 固定碳计算公式:固定碳%=100-挥发分-水分-灰分备注:焦碳的碳含量是经各步试验结果计算出来的,所以称固定碳.6. 亚甲基蓝吸附量(吸蓝量)的测定注:膨润土中蒙脱石具有吸附亚甲基兰的能力,其吸附量称吸蓝量以100克试样吸附的亚甲基蓝的克数表示.6.1 设备:天平(感量0.01g)电炉滴定管6.2 试剂配制:质量分数为1%的焦磷酸钠溶液.质量分数为0.2%的亚甲基兰溶液(化学试剂纯度为≥98.5%.亚甲基兰必须在干燥皿中保存)亚甲基兰溶液的配制:称取亚甲基兰2克溶于1000ml水中,即配成质量分数为0.2%的亚甲基兰溶液6.3 操作程序:称取烘干的试样0.20g(+ -)0.01g置于三角烧杯中,加入50ml蒸馏水使其预先润湿.然后加入质量分数为1.0%的焦磷酸钠溶液20ml摇晃均匀后在电炉上加热煮沸5分.在空气中冷却至室温,用滴定管滴入质量分数为0.2%的亚甲基兰溶液,滴定时第一次可加入预计的亚甲基兰溶液量的2/3左右,以后每次滴加1-2ml.检验终点的方法是:每次滴加亚甲基兰溶液后摇晃30秒,用玻璃棒蘸一滴试液在中速定量滤纸上,观察在中央深兰色的周围在无出现淡兰色的晕环,若末出现,继续滴加亚甲基兰溶液.如此反复操作,当开始出现兰色晕环时,将试液静置1分后,再用玻璃棒蘸一滴试液,若四周还末出现淡兰色的晕环,说明末到终点,应再滴加亚甲基兰溶液,直到出现明显的淡兰色晕环为试验终点.6.1 计算公式: P B VMB =----------×100%mMB:100g膨润土试样的吸兰量(g)P B:亚甲基兰溶液的质量浓度(g/ ml)V: 亚甲基兰溶液的滴定量(ml)M: 膨润土试样的质量(g)100: 膨润土的质量(g)7. 有效膨润土含量的测定:7.1 设备:电烘箱电热板滴定装置7.2 试剂配制:质量分数为1%的焦磷酸钠溶液.质量分数为0.2%的亚甲基兰溶液7.2.1操作程序:测定有效膨润土含量,是根据膨润土中含蒙脱石矿物能吸附亚甲基兰,等染料的特性,而粉尘,砂粒被烧死的无效膨润土等元素粘结作用,物料则不吸附或极少吸附亚甲基兰染料的原理进行的.为了测定旧砂中有效膨润土含量,取车间所用原砂和膨润土在105-110℃烘干到恒重后,置于一组(5)个250ml的烧杯中,分别加入膨润土0.1g, 0.2g, 0.3g, 0.5g及原砂4.9g, 4.8g, 4.7g, 4.6g,4.5g,使每份试样原砂和膨润土总量为5.0g,先分别加入质量分数为1%的焦磷酸钠溶液20ml,摇晃均匀后在电炉上加热煮沸5分.在空气中冷却至室温,按吸兰量的测试步骤测定出每份试样的亚甲基兰滴定量,然后以试样中的膨润土量为横坐标, 亚甲基兰滴定量为纵坐标,绘制标准附曲线.备注:试验时取旧砂(或型砂) 5g用亚甲基兰溶液滴定,根据滴定量从标准吸附曲线上可直接查出旧砂或型砂中有效膨润土含量8. 有效煤粉含量的测定:备注:粘土砂中有效煤粉含量是指在旧砂中除去已失效的而能起着相当于新鲜煤粉作用组分的质量分数8.1 设备:SFL型记录式发气性测定仪, 天平(感量0.01g)8.2 操作程序:将发气性测定仪开温至900℃,称取生产中使用的煤粉试样0.01 g,放入瓷舟中,(瓷舟使用前预先在1000℃灼烧30分钟表, 并保存在干燥器中)然后再将盛有试样的瓷舟放入发气性测定仪的石英管红热的部分,立即塞上塞子,记录仪开始工作,记下被测试样的发气量,保温7分钟至无气体产生为止.按上述同样的方法测定0.01 g膨润土及其它附加物的发气量,最后再按上述方法测定除去含铁物质和风干过的1.0 g(精确至0.01 g)型砂(芯)砂或旧砂的发气量.备注:按上述方法对同一试样测定三次取其平均值,若其中任一结果与平均值的差大于10%试验需重新进行8.3 的计算公式: Q1-∑Q2W (M) =-----------------------×100%QW (M):旧砂中有效煤分的质量分数%Q1: 1克旧砂的发气量∑Q2: 1.0克旧砂中除煤粉外的膨润土和其它附加物的总发气量Q: 0.01克煤粉的总发气量(ml)本文件根据铸钢件造型对型砂的要求并结合酚醛树脂的基本特性而编制1. 原材料及基本要求:原砂:硅砂SiO2≥98% 粒度40/70目角形因数≤1.45含泥量≤0.3% 含水量≤0.2%酚醛树脂砂:比强度24(h)≥0.6MPa 游离酚≤0.5% 游离醛≤0.2%粘度(mPa.s)20℃≤120固化剂:脂含量≥98% 游离酸≤0.2% 粘度(mPa.s)20℃≤52. 型(芯)砂的配比碱性酚 醛树脂砂的配比如表11各种材料的具体加放量,应概据现场温度及使用要求来确定.在型砂的各项指标达到表2要求的情况下,应尽可能减少树脂和固化剂的加入量表24. 酚醛树脂砂的混砂及控制(1) 将酚醛树脂和固化剂分别加入带有保温装置的液料桶内,使树脂和固化剂的使用温度控制在20℃-40℃之间.当树脂或固化剂液面低于标定的下料位时,应及时补添.切记,勿将两者错加入对方的液料桶内.(2)将混砂机控制界面调至首页,进入自动计时菜单,分别调整卸砂闸析及树脂和固化剂的电机频率数,然后对放出的砂,树脂和固化剂分别进行计量称重,使混砂机单位时间的出砂量及泵出树脂和固化剂量达到预定值.(3) 从按设定比例混制好的型砂中取砂制样,按表2进行检测,符合要求后进行正常生产.不符合要求,再按(2)的步骤要求调整砂,树脂,固化剂之间的比例.(4)旧砂经过再生,应符合表3要求表3当再生砂不能满足表3中的指标要求时则应及时整修再生或除尘设备.表3 中的PH 值,灼烧减量每天检定一次,其余每个工作日检测一次(5)在环境温度较高或旧砂循环使用频率较高时,再生砂的温度会随着旧砂热量的积累越来越高,当进入混砂机的砂温超过35℃时,就需开启冷却水来降低砂温.如果砂温仍温合肥市不能降至35℃以下,则需在落砂前开箱,让其充分冷却后再落砂.如条件允许,也可通过增加新砂比例的办法来降低砂温.(6)在正常生产中,为确保砂,树脂,固化剂相互之间的比例符合要求,至少每周按(2)的步骤要求,对砂,树脂,固化剂进行称重检测,并做好记录,不符合要求时,及时调整.根据我公司的设备特点及粘土砂既要生产铸铁件,以要生产铸钢件这一实际情况,制定本工艺规程1. 粘土砂用原材料及要求(1)原砂:硅砂SiO2≥98% 粒度50/100目或70/140目含泥量≤0.3% 含水量≤0.2%(2)膨润土:采用钠基或钠化膨润土,其指标如表1表1(3)煤粉:指标及要求见表2表2(4)氧化铁红:Fe2O3含量≥67%2. 粘土砂的配比粘土砂配比如表3表33. 粘土砂的性能粘土砂砂样是在全部主要辅材料都加入混砂机,并按规定时间进行充分混合后,从混砂机的取样口取砂制样.粘土砂的性能应达到表4的要求表4粘土砂的性能检测,在各种加入材料的各项指标都有明确掌握,检测结果符合要求且稳定的情况下,可每班检测二次,否则,每碾必须进行检测. 4.粘土砂的混制按照定量器定量,每碾加入砂800Kg,其它材料根据表3设定计量加入.如有特殊要求,可适当调整型砂的配比比例或在型砂中增加其它辅助材料型砂经过反复使用,其中的膨润土,煤粉就会失效形成粉尘,当粉尘含量超过一定比例后,会使型砂的紧实率,透气性,热湿拉强度明显下降,型砂性能恶化,造成铸件气孔等缺陷增加,当型砂中的总含泥量超过16%时,应开启旧砂再生装置,.使回用的旧砂通过旧砂再生机降低粉尘的含量..旧砂经过反复浇铸使用,热量积蓄,旧砂温度不断升高,会造成型砂性能恶化,造型困难,砂处理设备因粘砂而不能正常工作.因此,须把混砂机混出的砂温控制在≤40℃.由于本砂处理线末配备砂温调节装置,所以在旧砂回用较频繁时,一方面适当延长打箱时间或现场开箱让砂型充分冷却,另一方面增加新砂加入量,以降低砂温.。
粘土型砂分类及制备.

4.表干型铸造法
工艺规范:仅将砂型表面层烘干,烘干的深度一般为5–20㎜,或 将砂型、砂芯自然干燥24–48h后再合型浇注。
基本特点:表面层强度高、湿度小,因而浇注质量较大的铸件时 不易产 生气孔、粘砂、夹砂、冲砂等缺陷。
技术要求:要采用粗砂,型砂水分要严格控制,而且在造型、制 芯、合型、浇注等方面应严格按照工艺法 基本特点:砂型(芯)无需烘干,不存在硬化过程。 主要优点: 生产灵活性大,生产率高,生产周期短,便于组织流水生产; 易于实现生产过程的机械化和自动化; 材料成本低; 节省了烘干设备、燃料、电力及车间生产面积; 延长了砂箱使 用寿命; 容易落砂等。 主要缺点:采用湿型铸造,也容易使铸件产生一些铸造缺陷,例如夹砂结 疤、鼠尾、粘砂、气孔、砂眼、胀砂等。 应用范围:主要用于机械化流水生产和手工造型 500Kg以下的铸件。
应用范围:粘土干型主要用于铸件表面质量要求高,或结构特 别复杂的单件或小批生产及大型、重型铸件。
5.干型铸造法 基本特点: 将粘土砂湿型经过烘干而成 。 主要优点:砂型烘干后,显著提高了 砂型的强度、透气性、 降低发气量,使铸件减少气孔、砂眼、粘砂、夹砂 等缺陷,采用涂料后铸件的表面质量亦会得到改善。
主要缺点:干型铸造需要烘干设备,增加燃料消耗,增加吊车 作业次数,延长生产周期,缩短砂箱使用寿命,使 铸件的成本增加,生产率降低,干型落砂比较困难, 还会产生大量灰尘。
粘土型(芯)砂分类及制备
1.粘土型砂根据在合型和浇注时的状态不同可分为:
湿型(湿砂型或潮型)——湿型是造好的砂型不经烘干,直接浇 入高温金属液体。
干型——在合型和浇注前将整个砂型送入烘干窑中烘干。 表面烘干型——在浇注前对型腔表层用适当方法烘干一定深度。
2.湿型用湿型砂按造型时情况不同,可分为: 面砂——指特殊配制的在造型时铺覆在模样表面上构成型腔表面层的型砂。 背砂——指填充在面砂背面起填充作用的造型砂。 单一砂 ——指不分面砂和背砂,只有一种类型的造型砂。
型砂试验检验规程全
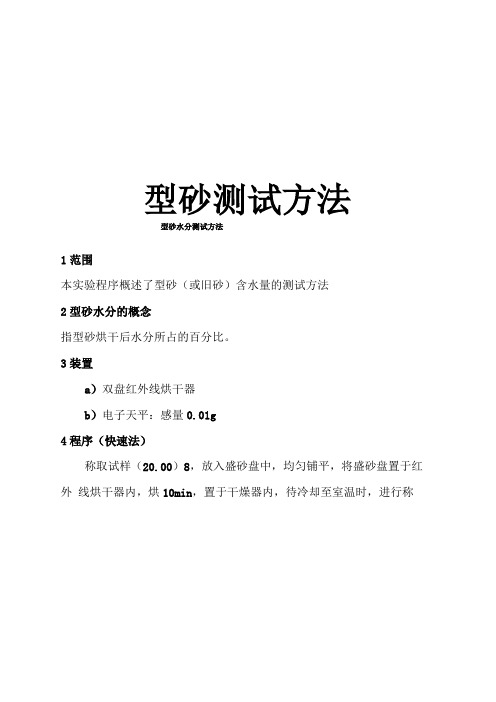
型砂测试方法型砂水分测试方法1范围本实验程序概述了型砂(或旧砂)含水量的测试方法2型砂水分的概念指型砂烘干后水分所占的百分比。
3装置a)双盘红外线烘干器b)电子天平:感量0.01g4程序(快速法)称取试样(20.00)8,放入盛砂盘中,均匀铺平,将盛砂盘置于红外线烘干器内,烘10min,置于干燥器内,待冷却至室温时,进行称量。
5结果的表述含水量X按下式计算:X = G1 ―G2 X 100%G1式中:G1——烘干前试样的质量,单位为克(g);G2——烘干后试样的质量,单位为克(g)。
计算结果保留到小数点后两位。
1范围本实验程序概述了型砂紧实率的测试方法。
2型砂紧实率的概念指型砂的可紧实程度。
3装置a) 6目标准筛b)投砂器c)①50圆柱形标准试样筒d)锤击式制样机4程序将试样通过带有6目筛子的漏斗,落入到有效高度为120mm的圆柱形标准试样筒内(筛底至标准试样筒的上端面距离应为140mm),用刮刀将试样筒上多余的试样刮去,然后将装有试样的样筒在锤击式制样机上冲击三次,从制样机上读出数值。
5结果的表述紧实率V按下式计算V = H 0 —H i x 100%H式中:H0——试样紧实前的高度,单位为毫米(120mm);H1——试样紧实后的高度,单位为毫米(mm)。
计算结果保留到小数点后两位。
1范围本实验程序概述了型砂湿压强度的测试方法。
2型砂湿压强度的概念湿压强度指型砂标准试样在达到破坏时所能承受的最大压力。
3装置a)锤击式制样机b) 液压型砂强度测定仪c)①50圆柱形标准试样筒d) 感量为0.01的天平4试样的制备测定各种强度用的标准试样除特殊规定外都是在锤击式制样上冲击三次而制成的。
称取一定量的试样放入圆柱形标准试样筒中,在锤击式制样机上冲击三次,制成高度为50mm± 1mm的标准试样。
5程序测定湿压强度时,将湿压夹具置于仪器上,然后将试样置于湿压夹具上,转动手轮或启动仪器,逐渐加载,直至试样破裂,其湿压强度值,从压力表或仪表上读出。
铸造湿型砂的检测要求与质量控制

湿型砂检测项目1、含水量型砂含水量高,铸件的针孔、气孔、呛火、胀砂、夹砂、水爆炸粘砂等缺陷增加。
在保证型砂的使用性能的前提下,应尽可能降低水分。
一般在造型机处含水量在2.5~4.0%之间,手工造型可以再放宽一点,紧实率/含水量的比率应控制在10~12:1。
型砂的含水量只是型砂中所含自由水的绝对数量,并不反映型砂的干湿程度。
如果型砂含有大量吸水粉尘,那么含水量高达5%,可能型砂还会显得太干,起模困难,这在许多中小型铸造企业都存在这种情况,一方面是没有人去管理,有些企业型砂反复使用10多年,连简单的除尘都不做,一方面是因为用的原材料不好,原砂是就近购买,膨润土和煤粉也没有什么要求。
2、紧实率型砂的干湿程度可以用紧实率来表示。
无论型砂的粉尘含量多少,它都有一个适宜的紧实率,只是含水量不同。
一般手工造型紧实率控制在46%左右,射压、挤压、静压造型紧实率控制在30~40%,夏季略高一点。
型砂检测一般宜在造型机处取样,在混砂机处取样应补偿运输和储存过程中的水分流失。
有些高压造型或气冲造型的砂型,3次锤击的试样并不能代表实际生产情况,有时候可能需要经过10次之多的锤击制样,具体应做对比确定次数,由此制作的试样其他方面的数据也会有明显变化。
3、透气率型砂必须具有良好的透气能力,以免浇注过程中发生呛火和铸件产生气孔缺陷。
透气能力也不能过高,否则会造成铸件表面粗糙和机械粘砂。
大多数型砂要求透气率在80~140,手工使用的面砂透气率可以低至60。
4、湿压强度目前国内的试样筒工作表面粗糙,耐磨性差,较易磨损,使测得强度值偏低,透气率偏高,制样器不宜放置在木桌上,在水泥台上也需垫上6mm以上的橡胶板,否则测得的湿压强度可能会偏低25%左右。
有条件的可以自己制作试样筒,工作表面硬度HRC65~70,表面粗糙度Ra≤0.20μm。
具体造型时需要的湿压强度,丹麦DISA挤压线推荐200±20Kpa,德国BMD和瑞士GF推荐180~220 Kpa,东久公司推荐无箱射压110~140 Kpa,新东公司水平无箱射压推荐80~140 Kpa,具体还得根据铸件的厚薄程度作适当调整。
型砂的主要成分

型砂的主要成分一、前言型砂是铸造中常用的材料,它具有良好的流动性和塑性,可以填充模具中的空隙,并保持模具形状。
型砂的主要成分对于其性能起着至关重要的作用。
本文将详细介绍型砂的主要成分及其特点。
二、型砂概述1. 型砂的定义型砂是铸造过程中用于制作模具和芯子的材料,它可以填充模具中的空隙,并保持模具形状。
2. 型砂的种类根据不同原材料和制备工艺,型砂可以分为天然型砂和人工型砂两大类。
其中天然型砂包括海滩沙、河滩沙、湖泊沉积物等;人工型砂包括化学合成型砂、水玻土等。
三、天然型砂1. 海滩沙海滩沙是指在海岸线上堆积形成的一种天然沉积物,其主要成分为二氧化硅(SiO2)和氧化铁(Fe2O3)。
由于其颗粒度均匀,流动性好,因此被广泛应用于铸造中。
2. 河滩沙河滩沙是指在河床上堆积形成的一种天然沉积物,其主要成分为二氧化硅(SiO2)和氧化铝(Al2O3)。
由于其颗粒度均匀,流动性好,因此被广泛应用于铸造中。
3. 湖泊沉积物湖泊沉积物是指在湖泊底部堆积形成的一种天然沉积物,其主要成分为二氧化硅(SiO2)和钙质。
由于其颗粒度均匀,流动性好,因此被广泛应用于铸造中。
四、人工型砂1. 化学合成型砂化学合成型砂是指通过化学反应合成的一种人工型砂,其主要成分为二氧化硅(SiO2)和氧化铝(Al2O3)。
由于其颗粒度均匀、流动性好、耐高温等优点,在高精密度铸造领域得到了广泛应用。
2. 水玻土水玻土是指通过水洗、筛选等工艺处理后制备而成的一种人工型砂,其主要成分为蒙脱石和伊利石。
由于其具有良好的粘结性和塑性,因此被广泛应用于铸造中。
五、型砂的主要成分特点1. 二氧化硅(SiO2)作为型砂的主要成分之一,二氧化硅具有高熔点、高硬度、耐酸碱腐蚀等优点。
同时,它还可以增加型砂的强度和耐火性能。
2. 氧化铝(Al2O3)氧化铝是一种重要的陶瓷材料,它具有高硬度、高强度、耐高温等优点。
在型砂中加入适量的氧化铝可以提高型砂的耐火性能和抗压强度。
型砂
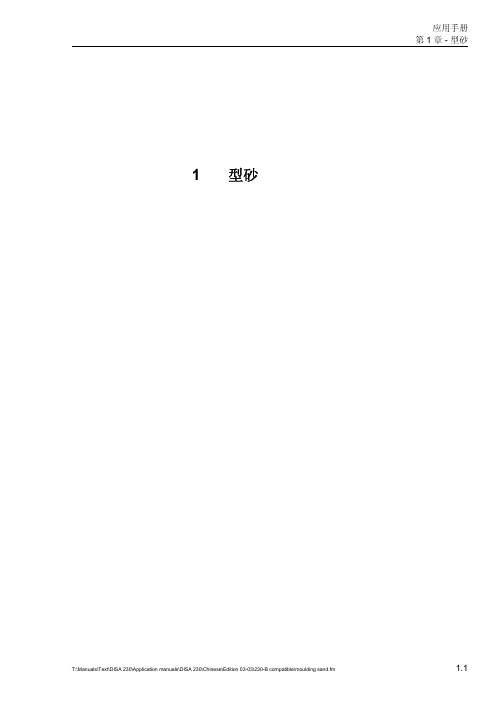
应用手册第1章 - 型砂1型砂T:\Manuals\Text\DISA 230\Application manuals\DISA 230\Chinese\Edition 03-03\230-B compatible\moulding sand.fm 1.12110平均砂粒度(洗选砂)0.14-0.28 DIN AFS 110-60粒度分布(洗选砂)对90%的粒度使用3-4个筛子湿压强度1500-2100 p/cm221-30 psi湿拉强度>200p/cm2>2.9 psi抗裂强度>300p/cm2>4.3 psi湿抗拉强度>20p/cm2>0.3 psi透气性>50>50紧实率40% ± 2%40% ± 2%水分含量调节直到紧实率达到40% ±2%活性粘土含量(MB)>7%>7%AFS粘土含量活性粘土为+3至4.5%烧损 3.5-5% 3.5-5%表1: 对标准型砂建议的物理特性2013 / 230 / 240平均砂粒度(洗选砂)0.14-0.22 DIN AFS 110-75粒度分布(洗选砂)对90%的粒度使用3-4个筛子湿压强度1700-2100 p/cm225-30 psi湿拉强度>200p/cm2>2.9 psi抗裂强度>300p/cm2>4.3 psi湿抗拉强度>20p/cm2>0.3 psi透气性>50>50紧实率40% ± 2%40% ± 2%水分含量调节直到紧实率达到40% ±2%活性粘土含量(MB)>7%>7%AFS粘土含量活性粘土为+3至4.5%烧损 3.5-5% 3.5-5%表2: 对标准型砂建议的物理特性1.2T:\Manuals\Text\DISA 230\Application manuals\DISA 230\Chinese\Edition 03-03\230-B compatible\moulding sand.fm应用手册第1.1节 - 高密度湿砂造型1.1高密度湿砂造型与用化学粘结剂的其它砂造型方法相比,用粘土做粘结剂型砂的费用低得多,其生产出的铸件质量和生产效率与后者相当,甚至更好些。
- 1、下载文档前请自行甄别文档内容的完整性,平台不提供额外的编辑、内容补充、找答案等附加服务。
- 2、"仅部分预览"的文档,不可在线预览部分如存在完整性等问题,可反馈申请退款(可完整预览的文档不适用该条件!)。
- 3、如文档侵犯您的权益,请联系客服反馈,我们会尽快为您处理(人工客服工作时间:9:00-18:30)。
目前,型砂冷却装置的品种、规格很多,主要有冷却滚筒、双盘冷却器和冷却沸腾床等,都是利用水分蒸发冷却型沙。其中,冷却沸腾床效果较好。
2.旧砂的水分控制
几乎所有的铸造厂都检查和控制混成砂的水分,但是,对于严格控制旧砂水分的重要性,很多铸造厂的领导和技术人员还缺乏足够的认识。
进入混砂的旧砂水分太低,对混砂质量的影响可能并不亚于砂温过高。
3.旧砂温度和水分的控制
通常把40℃以上的旧砂称为热砂,使用热砂会导致混砂效率降低及型砂水分波动,造型机模板粘砂,起模困难,不易紧实,铸件容易出现粘砂、冲砂、气孔等缺陷。因此,应把砂温作为旧砂管理的重要项目,并控制在低于室温15℃(夏季<40℃)。
理论上,旧砂每蒸发1%的水可使旧砂降温25℃。目前旧砂冷却设备如双盘冷却器、沸腾冷却床等已比较成熟,并配备测温增湿系统,能有效控制旧砂的冷却。在旧砂降温后,使旧砂保持一定的水分是十分必要的,让膨润土有充分的膨润时间,旧砂增湿系统尽可能提前,并保持一定的砂量,保证旧砂在进入混砂机之前至少有2h以上的膨润时间。旧砂水分的控制范围一般为型砂水分的60%~70%,并做到定期检测、及时调整。
值得注意的是,在各种化学粘结砂蓬勃发展的今天,粘土湿型砂仍是最重要的造型材料,其适用范围之广,耗用量之大,是任何其他造型材料都不能与之比拟的。据报道,美国钢铁铸件中,用粘土湿型砂制造的占80%以上;日本钢铁铸件中,用粘土湿型砂制造的占73%以上
适应造型条件的能力极强,也是粘土湿型砂的一大特点。1890年震压式造型机问世,长期用于手工造型条件的粘土湿型砂,用于机器造型极为成功,并为此后造型作业的机械化、自动化奠定了基础。近代的高压造型、射压造型、气冲造型、静压造型及无震击真空加压造型等新工艺,也都是以使用粘土湿型砂为前提的。
(4)型砂水分下降,湿压(剪)强度不变(或水分不变,湿压(剪)强度下降),在起模时型腔容易损坏,铸件夹砂、砂眼等缺陷增加,则表明型砂中有效膨润土含量降低了,应适当提高膨润土加入量。
(5)水分和湿压强度未变,透气性下降,则表明砂的粒度已变细,或砂中的粉尘已增加,应适当提高新砂加入量。
(6)新砂加入量不变,而型砂含泥量增加,粘土、煤粉加入量提高,则型砂的除尘系统有问题。
各种新工艺的实施,使粘土湿型砂在铸造生产中的地位更加重要,也使粘土湿型砂面临许多新的问题,促使我们对粘土湿型砂的研究不断加强、认识不断深化。
现今,随着科学技术的速发展,各产业部门对铸件的需求不断增长,同时,对铸件品质的要求也越来越高。现代的铸造厂,造型设备的生产率已提高到前所未有的水平,如果不能使型砂的性能充分适应具体生产条件,或不能有效的控制其稳定、一致,则不用多久就可能将铸造厂埋葬于废品之中。
(1)紧实率正常,有效膨润土含量在工艺要求范围内,而水分增高(或降低),说明型砂死粘土粉尘已增多(或降低),应增加(或降低)新砂加入量。
(2)有效膨润土、紧实率、水分都在工艺要求范围内,湿压(剪)强度降低,表明混砂效率降低,应检查混砂机和混砂工艺。
(3)型砂的水分未变,湿压强度升高(或水分升高,湿压强度未变),铸件表面比较光洁,起模性好,则表明型砂中有效膨润土含量已升高,应适当降低膨润土加入量。
为尽可能达到上述控制状态,应减少砂处理系统整体砂量的波动,时刻关注铸件种类、材质、砂铁比、铸件模数的变化,通过在线检测或型砂化验室的检测数据及时调整型砂配方,控制型砂组分的变化,控制好砂温和稳定旧砂水分,严格控制型砂紧实率及强度的波动,达到有效控制砂处理系统和保证型砂质量的目的。
1.砂量的控制
使型砂冷却,最有效的办法是加水,但是,简单的加水,效果是很差的。一定要吹入大量空气使水分蒸发,才能有效地冷却。
以下,给出一个简略的计算比较:
型砂的比热大致是:9.22×102J/kg·℃,水的比热是:4.19×103J/kg·℃,水的蒸发热是:2.26×106J/kg,1吨砂中加20℃的水10kg(加水1%),使其温度升到50℃,所能带走的热量为4.19×103 ×10×30,即12.57×105J。1吨砂温度降低1℃,需散热9.22×102×1000 J,即9.22×105 J。
一.旧砂的处理
用粘土湿型砂造型,浇注以后,除贴近铸件的部分型砂中活性膨润土受热失效成为死粘土外,大部分型砂可以回收使用。这是粘土湿型砂的主要优点之一。
配制粘土湿型砂时,旧砂用量一般都在90%以上,如果对旧砂的处理不当,无论怎样加强混砂,无论添加什麽辅助材料,都不可得到好的型砂。所以,对旧砂进行有效的处理,是保证型砂质量的前提。
所以,在旧砂中加水1%,只能使温度降低24.5℃。
使1吨砂中的水分蒸发1%(10kg),能带走的热量为2.26×107J,却可使砂温降低24.5℃。
以上的分析表明:简单地向皮带机上加水或向砂堆洒水,冷却效果是很差的。即使加水后向砂表面吹风,也不能有多大的改善。加水后,要使水在型砂中分散均匀,然后向松散的砂吹风,使水分迅速蒸发,同时将蒸汽排除。
】介绍高密度造型砂处理系统旧砂的质量要求及含泥量、旧砂温度和水分等方面的控制经验,阐述了通过对型砂性能的检测及分析来保证型砂品质的方法。
近年来,我国铸造企业特别是新兴铸造企业采用高压造型、气冲造型、无箱射压造型等高密度造型方式的越来越多,造型工艺水平起点高,相应地对砂处理质量的控制要求也越来越高。高密度造型型砂管理与常规型砂管理有很大不同,特别是对旧砂控制要求更为严格。对型砂质量控制的首要任务是稳定型砂系统的砂量平衡,减少型砂各组分的波动。型砂系统控制好的理想状态应满足以下几个条件:
较好的做法是:在旧砂冷却过程中充分加水冷却后所含的水分略低于混成砂。这样,从砂冷却到进入混砂机还有一段相当长的时间,水可以充分润湿旧砂砂粒表面上的膨润土。
(1)旧砂(或新旧砂混合)有效周转量为造型线型砂需求量的两倍以上。
(2)砂芯流人量及新砂加入量总和<3%。
(3)旧砂破碎筛分系统良好,旧砂均匀无砂团。
(4)旧砂砂温不高于室温15℃(夏季<40℃)。
(5)混砂前旧砂保持在型砂水分的60%~70%。
(6)旧砂(或新旧砂混合)含泥量控制在7%~11%。
试验研究和经验都已证明,加水润湿干膨润土比润滑湿膨润土难得多。型砂中的膨润土和水,并非简单的混在一起就行,要对其加搓揉,使之成为可塑状态。这就像用陶土和水制陶器一样,将水和土和一和,是松散的,没有粘接能力;经过搓揉和摔打,使每粒土都充分吸收了水分,就成为塑性状态,才可以成形,制成陶器毛坯。
铸型浇注以后,由于热金属的影响,很多砂粒表面上的土-水粘结膜都脱水干燥了,加水使其吸水恢复塑性是很不容易的。旧砂的水分较低,在混砂机中加水混碾使之达到要求性能所需要的时间就越长。由于生产中混砂的时间是有限的,旧砂的水分越低,混成砂的综合质量就越差。目前,各国铸造工作者已有了这样一种共识:进入混砂机的旧砂,水分只能比混成砂略低一点。
砂处理系统中的砂量是不断变化的,保持旧砂系统适当砂量是型砂管理的基础,随着铸件种类的不同,砂芯带人量的多少不一样,旧砂总量不断波动。随着覆膜砂芯、冷芯的推广使用,砂系统中的砂量一般是过剩的。砂量过剩时应将品质不好的旧砂从系统中排掉,并定点存放,以备砂量不足时投入系统中循环使用,时刻保持旧砂量的稳定。
2.含泥量的控制
含泥量主要指粒度<0.022mm的微粉含量。型砂含泥量是影响型砂含水量、强度、韧性和透气性等性能的重要参数,因此运行良好的砂处理要经常检测旧砂中的含泥量,旧砂中的含泥量一般控制在7%~11%之间,当含泥量>11%时,会造成型砂性能恶化;当含泥量<7%时,型砂中吸水组分含量太低,造成型砂水分波动大而不易控制,同时型砂透气性高影响铸件的表面粗糙度。旧砂含泥量主要来源于以下几个方面:
随着科学技术的发展,目前采用粘土湿型砂的铸造厂,一般都适合其具体条件的砂处理系统,其中包括:旧砂的处理、新砂及辅助材料的加入、型砂的混制和型砂性能的监控。
粘土湿砂系统中,有许多不断改变的因素。如某一种或几种关键性能不能保持在控制范围之内,生产中就可能出现问题。一个有效的砂处理系统,应能监控型砂的性能,如有问题,应能及时加以改正。
由于各铸造厂砂处理系统安排不同,选用的设备也不一样,要想拟定一套通用的控制办法是做不到的。这里,打算提出一些目前已被广泛认同的控制要点。各铸造厂认真地理解了这些要点之后,可根据自己的具体条件确定可行的控制办法。而且,还要随着技术的进步和工厂的实际能力(包括人员和资金)不断改进对型砂系统的控制。
多高温度的砂算是热砂?判断热砂的温度界限,是看其是否使混砂、造型及铸件质量方面出现问题。对此,许多研究者从个方面进行了研究;有人研究了型砂温度对其性能稳定性的影响;有人研究了温度对膨润土-水系统流变性的影响;有人研究了型砂温度与铸件质量的关系。各方面的研究,得到了一致的结论,即:为保证型砂的性能稳定,温度应保持在50℃以下。
我公司砂处理系统型旧砂的控制工艺及检测项目如表1、表2所示
11111111111111111111111111111111111111111111111111111111111111111111111111111111111111111111111111111111111111111111111111111111111111111111111111111111111111111
(1)膨润土在600℃左右失去结品水,成为死粘土,这是含泥量的主要来源。
(2)辅料在浇注过程中燃烧而成为灰分并残留在旧砂中。
(3)浇注过程中,硅砂受热膨胀,复合砂粒破碎而微粉化。
(4)混砂时的机械力ຫໍສະໝຸດ 部分硅砂颗粒破碎而微粉化。 (5)添加新砂、膨润土、辅料时带入的微粉。
含泥量的控制:①主要是控制膨润土及辅料的加入量,在保证起模良好,铸件无落砂及冲砂的前提下,尽量降低加人量,同时最大程度地发挥?昆砂机的}昆砂效果,保证合适的混砂时间。②通过除尘系统除去旧砂中的微粉,振动落砂机处除尘器中的灰分是严禁回用的,双盘冷却器及精细筛处除尘器中的灰分视控制能力是可以回用的(其中有效成分在60%以上)。③补加新砂(溃散砂芯)稀释旧砂中的泥分所占的比例,同时保持膨润土量与补充砂加入量的平衡。