(PFMEA)汽车行业过程失效模式分析
pfmea过程潜在失效模式及后果分析案例(从原材料-加工-出货整套案例分析)

1、注射压力大 2、锁模力不够 3.模具分型面有异物
4 调节注射压力 作业准备验证,适当调
整,并进行工艺监控 清理模具分型面
产品不合格
2
C 4.塑料温度太高
调节 56
5
制品质量符合 要求
气泡
1.原料含水分、溶剂或 易挥发物
3
原料检验
2.塑料温度太高或受热 时间长,易降聚或分解
标签贴错 漏检 纸箱受潮变形 数量不准确
产品型号错
误,顾客不满 2
意
不良品混入, 影响客户使用
5
纸箱变形破损 3
顾客不满意
1
C 包装人员粗心 C 检验人员操作失误 C 纸箱堆积太高 C 仓库计数错误
3 检查、更正 3 检验、及时标记 3 检查、更正 3 检查、更正
2 42
1 21
3 18 4 60 3 27 26
3.注射压力太小
调节注射压力
4.注射柱塞退回太早 产品不合格 7 A
5.模具温度太低
调节注射温度
6.注射速度快
调节注射速度
2 42
7.在料筒加料端混入空 气
6
制品质量符合 要求
凹痕、缩水
产品不合格 7
1、流道浇口太小
4
2、塑料件太厚或厚薄 不均
3、浇口位置不当
4、注射保压时间太短 A 5、加料量不夠
过程潜在失效模式及后果分析 (PFMEA)
类型/部件: 车型年:
核心小组:
设计责任: 关键日期:
RPN DETECT
OCCUR CLASS SEV
项目
设计功能/要 求
潜在失效模式
潜在失效后果
1 原材料采购 原材料不合格
PFMEA过程失效模式及后果分析
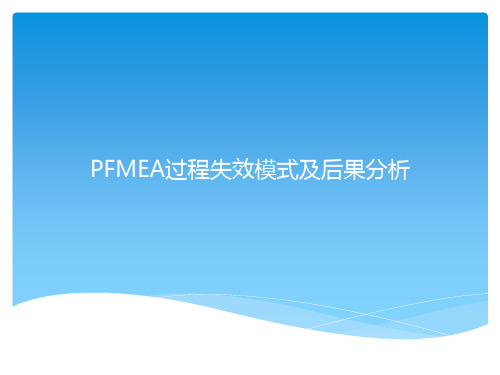
下列可以帮助确定是否将现有的PFMEA纳入最终范围: 新开发的产品和过程; 操作条件的变化; 要求变化(法律/法规,标准规范,客户,最新状态) 制造经验、场内问题,或现场问题/保修; 可能导致危险的过程失效; 人体工程学; 持续改进。
过程FMEA步骤一:规划和准备
PFMEA定义范围的目的---清晰定义过程范围: 识别项目----哪些过程需要分析; 项目计划----培训团队成员、创建项目时间; 定义分析界限---包括什么,不包括什么; 确定能使用的相关经验教训和决策,例如:最佳实践、标准、防错等。
示例:“磨削滑动油封”过程的功能结构
工作坊:步骤三-功能分析(绿色+蓝色笔)
1.过程项目、过程步骤、作业要素具有何种功能和要求? 填入结构树中各项功能和要求: 功能 +要求=绿色字体+蓝色字体 将各项功能填写 在过程项目、过程步骤及作业要素的下面。 备注:“发生什么?”如何从左到右实现产品/过程要求-(过程项目-过程步骤-作业
过程FMEA步骤二:结构分析
结构树按层次排列系统元素,并通过结构连接说明关联关系。这个形象化的结 构考虑了过程项目、过程步骤和过程工作要素之间的关系,在后面,将对他们 分别添加功能模块和失效模块。
对于过程来,查验的最基础层次—变差来源(Sources of Variation),是传统的 “4M(人Man、机Machine、料Material、环Milieu)”,即设备、工装、夹具、 刀/模具的硬件基本参数、动态的控制参数、辅助系统的参数、环境特性、影 响本序的前工序的加工余量、定位点的尺寸及形位公差等。
过程FMEA步骤四:失效分析
PFMEA失效分析的目的是: 1.为过程项目、过程步骤和作业要素的每个功能建立失效(一个或多个失效); 2.识别可能发生的失效/原因,并分配给作业要素和过程步骤; 3.失效关系的可视化(影响-模式-原因,基于功能网的失效网络); 4.通过链接失效链中的失效来创建失效结构; 5.是FMEA表格中记录的失效的基础; 6.失效分析对过程中的每个元素/过程步骤进行了失效描述(结构分析/步骤2和 功能分析/步骤3) 可能的失效从功能/任务推断出来,如设备特定目标状态的不合格、不能充分 完成工作任务、非预期或不必要的活动等; 对失效的描述必须要清晰。不符合、不OK、失效、中断及诸如此类的描述并不 不足以帮助我们去找到失效。 通常,某一功能可以有多种失效。
PFMEA潜在失效模式及后果影响分析案例
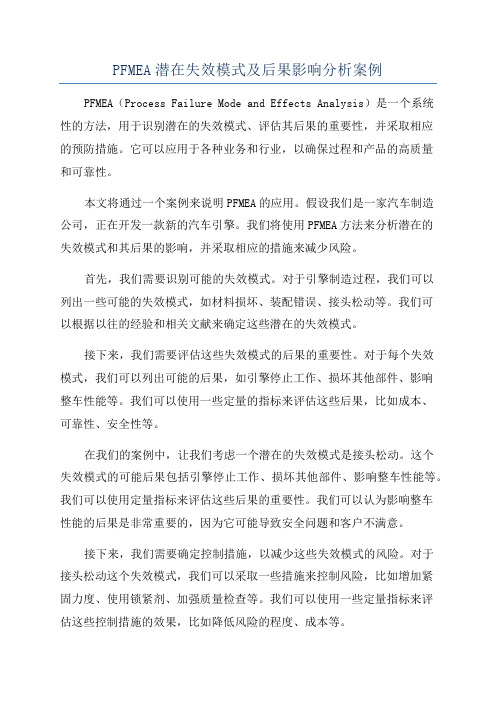
PFMEA潜在失效模式及后果影响分析案例PFMEA(Process Failure Mode and Effects Analysis)是一个系统性的方法,用于识别潜在的失效模式、评估其后果的重要性,并采取相应的预防措施。
它可以应用于各种业务和行业,以确保过程和产品的高质量和可靠性。
本文将通过一个案例来说明PFMEA的应用。
假设我们是一家汽车制造公司,正在开发一款新的汽车引擎。
我们将使用PFMEA方法来分析潜在的失效模式和其后果的影响,并采取相应的措施来减少风险。
首先,我们需要识别可能的失效模式。
对于引擎制造过程,我们可以列出一些可能的失效模式,如材料损坏、装配错误、接头松动等。
我们可以根据以往的经验和相关文献来确定这些潜在的失效模式。
接下来,我们需要评估这些失效模式的后果的重要性。
对于每个失效模式,我们可以列出可能的后果,如引擎停止工作、损坏其他部件、影响整车性能等。
我们可以使用一些定量的指标来评估这些后果,比如成本、可靠性、安全性等。
在我们的案例中,让我们考虑一个潜在的失效模式是接头松动。
这个失效模式的可能后果包括引擎停止工作、损坏其他部件、影响整车性能等。
我们可以使用定量指标来评估这些后果的重要性。
我们可以认为影响整车性能的后果是非常重要的,因为它可能导致安全问题和客户不满意。
接下来,我们需要确定控制措施,以减少这些失效模式的风险。
对于接头松动这个失效模式,我们可以采取一些措施来控制风险,比如增加紧固力度、使用锁紧剂、加强质量检查等。
我们可以使用一些定量指标来评估这些控制措施的效果,比如降低风险的程度、成本等。
最后,我们需要跟踪和更新PFMEA。
一旦我们实施了控制措施,我们需要不断跟踪失效模式的发生情况和其后果的重要性。
如果我们发现控制措施不够有效,我们可以采取进一步的改进措施,以减少风险。
通过以上的分析,我们可以有效地识别潜在的失效模式和其后果的重要性,并采取相应的预防措施来减少风险。
PFMEA是一个强大的工具,可以帮助我们提高产品和过程的质量和可靠性,从而提高客户满意度并降低成本。
过程失效模式及后果分析(PFMEA)

XXX汽车技术股份有限公司潜在失效模式及影响分析 PFMEA螺纹孔内无铝屑,机加工面边缘毛刺清理干净;螺纹孔内有铝屑,机加工面边缘未清理干净影响客户装配,客户抱怨61.丝锥损坏2.夹具松动3.切削液未正确喷淋,铝屑未吹掉31.首检记录表2.巡检记录表354None5XΦ0.341±0.01深0.55(英制)尺寸超差 1.毛坯不合格或尺寸变化大4XΦ0.232±0.01深0.5(英制)尺寸超差 2.夹具松动;3.程序错误2XΦ0.232±0.01深0.5(英制)尺寸超差 4.装夹失误2X4.34±0.02(英制)尺寸超差 1.毛坯不合格或尺寸变化大27.19±0.02(英制)尺寸超差 2.夹具松动;3.程序错误2X7.05±0.02(英制)尺寸超差 4.装夹失误2X11.72±0.02(英制)尺寸超差1.毛坯不合格或尺寸变化大1.25±0.02(英制)尺寸超差2.夹具松动;3.程序错误2.38±0.02(英制)尺寸超差 4.装夹失误1.56±0.02(英制)尺寸超差 1.毛坯不合格或尺寸变化大2.44±0.02(英制)尺寸超差 2.夹具松动;3.程序错误8XΦ0.118±0.01(英制)尺寸超差 4.装夹失误尺寸超差1.毛坯不合格或尺寸变化大2X45°±0.5°尺寸超差2.夹具松动;None3影响装配和功能7631.首检记录表2.巡检记录表3★3影响装配和功能7★31.首检记录表2.巡检记录表363NoneNone63影响装配和功能7★31.首检记录表2.巡检记录表3影响装配和功能7★31.首检记录表2.巡检记录表None影响装配和功能7★31.首检记录表2.巡检记录表36363None。
电动汽车充电机过程潜在失效模式及后果分析PFMEA

5 8 5
漏打螺钉 / ★ 风机线脱位
/ 线有弹性
客户拒收
6 / 网罩漏打螺钉
螺丝刀点检 机器打完检查
3 全检
安装前整理,设备优 先打带线端螺钉
2
全检
点胶后拉扯别在V卡 孔
2 全检
机器打完检查
3 全检
网罩不良 客户不满意
5
/ 网罩螺钉不到位
螺丝机/螺丝刀设备 点检
4 全检
防水透气阀 不到位
机器进水,性 能下降,客户 拒收 机器进水,性 能下降 机器进水,性 能下降 机器进水,性 能下降 机器进水,性 能下降
70
无
70
无
72
电烙铁加 入点检
90
更换模具 时记录
72
无
72
无
28
无
108
自检,互 检
EV-JL-702-YF-033(A/0)
威海天力电源有限公司
A4(210mm*297mm)
微卡尺寸大 安装困难
6
模具尺寸不合适 模具首次/定期检查
/
温度/压力不合适
温度/压力设置检查 开机试制
3
首件检查,100条检 查
无
4 64
无
4 80
无
4
120
工装清理 、检查
3 42
无
3 18
无
4 24
无
4 72
无
4 24
无
4 24
无
3 21
无
4 96 增加标识
2 16
无
4 32
无
EV-JL-702-YF-033(A/0)
威海天力电源有限公司
pfmea过程失效模式与后果分析报告

通过深入分析,我们确定了导致这些失效的潜在原因,包 括设备老化、操作规程不完善、员工培训不足、原材料质 量控制不严格以及工艺参数设置不合理等。
对未来工作的建议和展望
改进措施建议
持续改进计划
未来研究方向
基于PFMEA的结果,我们提出了一系 列改进措施,包括更新设备、优化操 作规程、加强员工培训、严格控制原 材料质量以及调整工艺参数等。这些 措施旨在减少失效发生的风险,提高 生产过程的可靠性和稳定性。
为了确保改进措施的有效实施,我们 制定了持续改进计划。该计划包括定 期评估改进效果、监测潜在问题的出 现以及调整改进措施等。通过持续改 进,我们期望能够不断优化生产过程 ,提高产品质量和客户满意度。
在报告的最后,我们提出了一些未来 可能的研究方向。这些方向包括进一 步探索失效模式与潜在原因之间的关 系、研究新的失效分析方法以及开发 更加智能化的失效预测模型等。通过 深入研究,我们期望能够为企业的持 续改进提供更有力的支持。
失效模式
汽车发动机性能下降
后果
影响汽车动力性能,可能导致油耗增加、排放超标
潜在原因
制造过程中材料、工艺、设备等方面的问题
风险评估
高风险,需采取措施进行改进
案例二:电子产品制造过程的PFMEA分析
失效模式
电子元件短路
潜在原因
制造过程中元件组装、焊 接等环节出现问题
后果
产品功能失效,可能引发 安全事故
提前发现和预防问
题
PFMEA是一种预防性的质量工具 ,它通过提前发现和预防潜在的 问题,减少后期修改和返工的成 本。
优化设计和过程
PFMEA分析结果可以为设计和过 程的改进提供指导,帮助企业优 化产品和过程的性能、可靠性和 安全性。
过程失效模式与后果分析PFMEA

过程失效模式与后果分析PFMEA一、PFMEA的定义和目标PFMEA是一种系统性的过程分析方法,用于评估潜在的失效模式、错误或缺陷,以及这些失效模式或错误对产品质量和工作过程的潜在影响。
它的主要目标是提前识别和减轻过程中可能导致质量问题的潜在风险,以便采取适当的预防和纠正措施,提高产品质量和客户满意度。
二、PFMEA的基本概念和步骤1.风险识别:通过审核过程文档、历史数据、专家经验等方式,识别可能存在的失效模式。
2.评估失效的严重程度:对每个失效模式进行定量或定性评估,确定其对产品质量和安全性的潜在影响,此项评估需要专业知识和经验的支持。
3.识别可能的失效原因:找出导致失效发生的根本原因,可以通过使用逻辑树、鱼骨图、5W1H等工具进行分析。
4.评估失效的频度:对每个失效模式进行评估,确定其在过程中发生的概率或频次。
5.识别已有的控制措施和预防措施:列举已有的预防和控制措施,以评估其对失效模式的控制效果。
6.评估失效的检测度:确定失效模式是否可以在目前的检测过程中被发现。
7.进行风险评估:通过对失效模式的严重程度、频度和检测度进行组合评估,计算出风险优先级数(RPN)。
8.制定预防和纠正措施:根据风险优先级,确定应采取的预防和纠正措施,并将其确定为优先处理的问题。
9.追踪改进:追踪和记录已实施的预防和纠正措施,并评估其有效性。
三、PFMEA的优势和应用1.优势:PFMEA有助于企业识别和应对过程中的风险,提前预防可能导致质量问题的问题,并减少相关成本。
通过完善的PFMEA过程,可以提高产品质量、可靠性和客户满意度。
2.应用:PFMEA广泛应用于制造业,尤其在汽车、医疗器械和航空航天等高风险行业中。
它通常在新产品开发过程中进行,也可以应用于现有产品或过程的改进。
四、PFMEA存在的挑战和解决方法1.数据收集的困难:获取过程相关数据和知识的困难是PFMEA面临的主要挑战之一、解决方法包括培训和指导工作人员,建立数据收集和共享机制等。
PFMEA_失效模式分析

PFMEA_失效模式分析PFMEA(Process Failure Mode and Effects Analysis)是一种用于识别并评估过程中潜在失效模式及其影响的工具。
它是在设计阶段早期或产品推出前执行的一种质量工具,旨在识别和消除可能导致质量问题的潜在失效模式。
本文将详细介绍PFMEA的定义、目的、执行步骤以及其在改善和优化过程中的应用。
PFMEA在制造和生产领域被广泛使用,特别是在汽车、电子、航空等高风险行业。
它的目的是通过确定潜在失效模式和评估其潜在影响来减少生产过程中的错误。
它通过三个主要方面的分析来完成:失效模式(Failure Mode)、影响评估(Effect Analysis)和失效原因(Cause Analysis)。
首先,失效模式是指可能在过程中发生的失效或故障,例如零件破裂、接头松脱或设备停止工作等。
对于每个失效模式,需要确定其严重性、发生概率和检测性。
严重性是指失效对产品或过程的影响程度,包括安全风险、客户满意度和产品可靠性。
发生概率是指失效模式发生的频率,包括供应商质量、使用寿命和环境因素。
检测性是指在出现失效后,能够及时检测到并采取纠正措施的能力。
其次,影响评估是对每个失效模式的影响进行定量评估。
通过评估严重性、发生概率和检测性的分级来确定每个失效模式的风险优先级。
风险优先级可以帮助团队确定应该优先处理的失效模式,以便采取相应的预防和纠正措施。
最后,失效原因分析是为了确定导致各个失效模式的潜在原因。
这可以通过使用工程知识和经验、故障树分析、故障模式与影响分析等工具来实现。
确定失效原因有助于在改善和优化过程中提出有效的纠正和预防措施。
此外,执行PFMEA的步骤可以总结为以下六个步骤:1.确定分析对象:确定要进行PFMEA的流程或产品。
2.列出所有失效模式:与团队合作,列出所有可能的失效模式和潜在问题。
3.评估失效影响:评估每个失效模式的严重性、发生概率和检测性。
4.识别失效原因:确定每个失效模式可能的原因,并识别潜在风险。
PFMEA过程失效模式及后果分析

PFMEA过程失效模式及后果分析PFMEA(Process Failure Mode and Effects Analysis)过程失效模式及后果分析是一种常用的质量管理工具,用于评估和改进产品制造过程中的潜在问题和风险。
它旨在预测和预防可能导致产品失效的过程步骤。
1.确定过程步骤:首先,识别和定义产品制造过程中的每个关键步骤,包括原材料采购、加工、装配、测试等。
2.确定失效模式:对于每个过程步骤,识别可能导致失效的模式。
失效模式可以是设备故障、人为错误、材料质量问题等。
3.评估失效后果:对于每个失效模式,评估其可能导致的后果和影响。
后果可以涉及到产品质量问题、安全风险、客户满意度等。
4.定义风险优先级:根据失效模式的严重性、发生频率和检测能力,为每个失效模式分配一个风险优先级。
这可以帮助制定合理的风险控制策略。
5.制定改进计划:对于评估出的高优先级失效模式,制定相应的改进计划和控制措施。
这可能包括优化生产工艺、提供培训和教育、改进设备维护等。
6.实施和监控措施:执行改进计划,并监控其有效性。
定期对PFMEA进行更新,以反映过程改进和新的风险评估。
通过实施PFMEA,可以有效地识别和消除潜在的制造过程问题,并降低产品质量问题的风险。
下面以汽车制造业为例,具体分析PFMEA的应用。
在汽车制造过程中,每个制造步骤都可能存在潜在的失效模式。
例如,原材料采购环节可能存在材料质量问题的风险,加工环节可能存在操作错误或设备故障的风险,装配环节可能存在组装错误或安装不良的风险,测试环节可能存在测试不准确或设备故障的风险。
针对这些潜在问题,可以使用PFMEA来识别并评估其风险。
例如,在加工环节,识别可能的失效模式可能包括不正确的参数设置、设备故障、操作错误等。
然后,评估这些失效模式可能导致的后果和影响,如产品偏差、生产延误、设备故障等。
根据评估结果,确定失效模式的风险优先级,以便制定相应的改进计划和控制措施。
例如,对于评估为高风险的加工失效模式,可以采取以下改进措施:加强对操作员的培训和教育,确保他们正确操作设备和设置参数;增加设备维护和保养频率,以减少设备故障的风险;实施过程监控和自动化控制,以确保稳定的生产环境。
PFMEA-失效模式分析

02
失效模式分析
失效模式定义
失效模式定义
01
失效模式是指产品或过程中可能出现的不满足设计意图、技术
要求或操作规范的状或现象。
失效模式分类
02
根据失效的性质和影响程度,失效模式可以分为功能失效、性
能失效、安全失效、适应性失效等类型。
失效模式分析方法
03
失效模式分析方法包括故障树分析、事件树分析、故障模式与
制定改进措施和预防措施
01
根据分析结果,制定针对性的改进措施,以提高产品或过程的 性能、安全性和可靠性。
02
制定预防措施,降低失效模式的发生风险,包括设计优化、工
艺改进、环境控制和使用指导等。
跟踪改进措施和预防措施的实施效果,持续改进,确保产品质
03
量和过程稳定。
04
PFMEA案例分析
案例一:汽车刹车系统PFMEA分析
识别关键特性,确定分析的重点,确 保分析的准确性和有效性。
列出潜在的失效模式
通过头脑风暴、历史数据分析和经验总结等方法,列出可能的失效模式,确保覆盖全面。
对失效模式进行分类和整理,以便后续分析。
分析失效模式的后果
分析失效模式对产品或过程性能、安 全性、可靠性和符合性等方面的影响 。
评估失效模式对客户满意度和生产成 本的影响,以便制定有效的改进措施 。
主观性
在评估失效模式的严重程度、发生频率和检测难度时,可能存在 主观性,导致结果的不一致。
静态性
PFMEA通常在产品开发阶段进行,而后期的更改和改进可能未 被考虑。
PFMEA未来发展方向
人工智能与机器学习应用
利用人工智能和机器学习技术辅助PFMEA分析,提高识别失效模式 的准确性和效率。
过程失效模式及效果分析(PFMEA)

GQP-012b
例 31 / 小时 16 / 小时 6 / 小时 3 / 小时 2 / 小时 5/ 班 5/ 天 13 / 周 10 / 月 13 / 年
*Example一栏中的数值是按两班制,每天5,000件下得到的 重复计算Example 中的数值可以得到精确值 Example中的整数是用四舍五入的方法计算的
当潜在失效模式到达最终客户或者生产装 配出不合格产品会有以下分类。最终客户 总是最优先考虑的,如果两者都发生,考 虑相对严重的 失效在无预警情况下威胁操作工(机床或 流水线上的)的安全 失效在有预警情况下威胁操作工(机床或 流水线上的)的安全 100%的产品必须报废,或者部件在维修部 的维修时间需超过一小时 产品须分类或者部分( 小于100 %)报废, 或部件在维修部的维修时间在半小时和一 小时之间 部分产品( 小于100 %)未经分类即报废, 或部件在维修部的维修时间小于半小时。 这是生产线上的主要停机原因。 100 %的产品需要返修,或部件可直接离线 维修而不必由维修部维修。这是生产线上 的次要停机原因。 产品须分类而不报废,部分( 小于100 %) 返修,失效会导致后续操作的不便及其引 起的小返修 部分产品( 小于100 %)需在线而不在岗返 修而不是报废,失效会导致后续操作的轻 微不便及其引起的小返修 部分产品( 小于100 %)需在线在岗返修而 不是报废,失效会导致后续操作的轻微不 便及其引起的小返修 给操作或操作工带来轻微不便或毫无影响
通用动力总成厂
严重度
无预警下就可能威胁操作工(生产或装配)安全的失效。
车身车间
GQP-012a
实例
Field
10
对于顾客或操作工的安全隐患 , OBD II 项目. OBD II 项目. 调整项目。 车辆抛锚 返回市场 难以解决的问题 经销商修理/返修 ( 噪音, 振动, 泄漏等) 。 车辆返回总装、质量溢出
PFMEA过程潜在失效模式和后果分析

度、温度和压力
9ⅹ.10.01
安装限值控制器。控制图
显示过程已受控制。
CPK=1.85
1
5
35
最小厚度 的蜡,以延 缓腐蚀
损害
7
因 撞 击 使 喷 2 依 预 防 维 护 程 每小时进行目测检 5
头变形
序维修喷头
查,每班检查一次喷
膜厚度(深度计)和
70
无
范围
7
喷蜡时间不 8
按作业说明书进行 7
392 安装喷蜡定时器
潜在过程失效模式应注意的问题
然而,在准备FMEA时,应假定所接收的零 件/材料是正确的。 当历史数据表明进货零件质量有缺陷时, FMEA小组可做例外处理。 根据零组件、子系统、系统或过程特性,对特 定的作业列出每一个潜在的失效模式。前提是 假设这种失效可能发生,但不一定必然发生。
潜在过程失效模式应注意的问题
或可能在无警告的情况下对(机器或组装) 1
作业员造成危害
0
有警 告的 危害 很高
高
严重度定级很高 。当潜在的失效
模式在有警告的情况下影响到车辆 安全运行和/或涉及不符合政府法 规的情况时。
或可能在有警告的情况下对(机器或组装) 操作员造成危害
9
车辆/系统不能工作(丧失基本功 能)
或100%的产品可能需要报废;或者车辆 /系统在修理部门花1个小时以上来修理
FMEA文件完全按照本手册填写,包含 “措施行动”和新的RPN值。
对一个增值的结果而言, FMEA小组尽 可能提早所花费的时间,是时间最有效 和效率的利用。这是假设措施已依需求 被鉴别,其措施都已实施。
过程FMEA中的“顾客”定义
过程FMEA中“顾客”的定义通常是指 “最终使用者”。然而,顾客也可以是随后 或下游的制造或装配工序,维修工序或政府 法规。
PFMEA分析范例
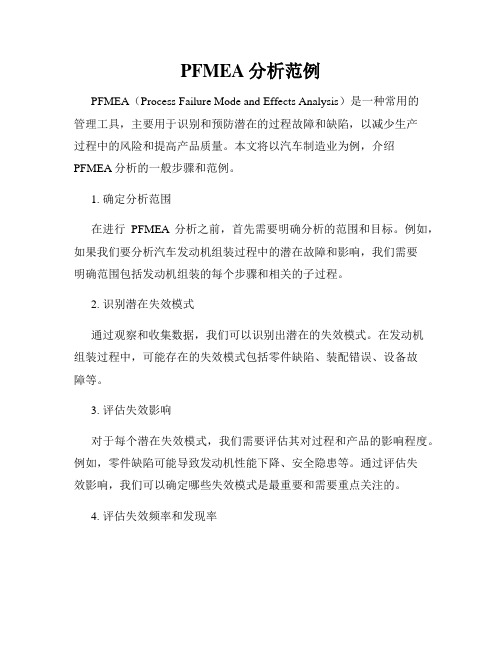
PFMEA分析范例PFMEA(Process Failure Mode and Effects Analysis)是一种常用的管理工具,主要用于识别和预防潜在的过程故障和缺陷,以减少生产过程中的风险和提高产品质量。
本文将以汽车制造业为例,介绍PFMEA分析的一般步骤和范例。
1. 确定分析范围在进行PFMEA分析之前,首先需要明确分析的范围和目标。
例如,如果我们要分析汽车发动机组装过程中的潜在故障和影响,我们需要明确范围包括发动机组装的每个步骤和相关的子过程。
2. 识别潜在失效模式通过观察和收集数据,我们可以识别出潜在的失效模式。
在发动机组装过程中,可能存在的失效模式包括零件缺陷、装配错误、设备故障等。
3. 评估失效影响对于每个潜在失效模式,我们需要评估其对过程和产品的影响程度。
例如,零件缺陷可能导致发动机性能下降、安全隐患等。
通过评估失效影响,我们可以确定哪些失效模式是最重要和需要重点关注的。
4. 评估失效频率和发现率在这一步骤中,我们需要评估潜在失效的频率和发现率。
频率指的是该失效模式在特定时间段内发生的次数,发现率指的是我们能在生产过程中或产品出厂之前检测到该失效模式的概率。
5. 确定风险优先级通过综合考虑失效影响、频率和发现率,我们可以确定每个失效模式的风险优先级。
通常采用风险优先数(RPN)计算方法,RPN = 失效影响 ×频率 ×发现率。
风险优先级高的失效模式意味着需要优先采取预防和纠正措施。
6. 制定预防和纠正措施根据风险优先级,我们可以制定相应的预防和纠正措施来降低潜在失效的风险。
例如,对于零件缺陷,我们可以建立更严格的质量控制流程,提高零件的检验和筛选标准。
7. 实施和监控措施制定好措施后,需要将其实施到实际生产过程中,并进行监控和评估。
通过不断追踪和更新PFMEA表格,我们可以及时发现并纠正新的失效模式,不断提升生产过程的稳定性和产品质量。
总结:本文以汽车制造业为例,介绍了PFMEA分析的一般步骤和范例。
过程失效模式及后果分析PFMEA
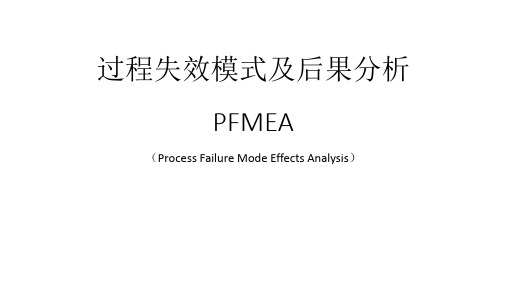
100~500 10~100
1~10
≥1.20
3
≥1.30
2
≥1.67
1
FMEA开发要点
8)当前控制方式
• 当前控制措施包括预防控制(error/mistake proofing or Statistical Process Control)和探测控制(post-process evaluation),“当前措施”应是在本过程或类似过程的中已落实的措施或已证明有效的措施。
Very High: 非常高 Persistent failures 持续失效
High:高 Frequent failures 频繁失效
Suggested PFMEA Occurrence Evaluation Criteria
Likely Failure Rates
以一百万块板里的缺陷计数
Ppk
Ranking
四、FMEA开发要点
下图展示了PFMEA模板。我们今天把理解最容易跑偏的板 块跟大家做一个梳理。
FMEA开发要点
1)功能要求 A 功能要求既包括过程特性和产品特性两大类。 • 过程特性: 过程参数及过程要求,即加工条件和加工参数 • 产品特性:产品规范,如尺寸\性能 B 对于同一个Operation上有多个操作动作的(an operation for a multistation machine or sequential process in one piece of equipment), 不管是人工操作还是极其操作,需要细化到每一个操作,比如:
Criteria: Severity of Effect 标准:后果严重性
This ranking results when a potential failure mode results in a final customer and/or a manufacturing/assembly plant defect. The final customer should always be considered first. If both occur, use the higher of the two severities.
汽车驾驶室主线束PFMEA过程失效模式分析
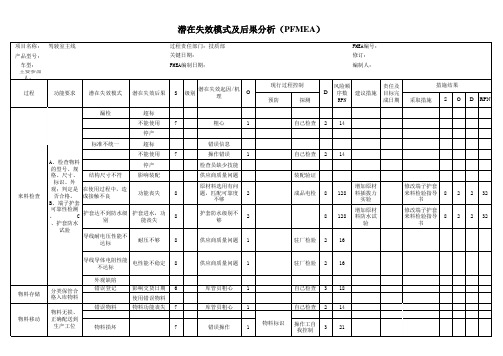
项目名称:产品型号:车型: 主要参加人:预防探测采取措施SODRPN漏检超标不能使用7粗心1自己检查214停产标准不统一超标错误信息不能使用7操作错误1自己检查214停产检查员缺少技能结构尺寸不符影响装配供应商质量问题装配验证在使用过程中,造成接触不良功能丧失8原材料选用有问题,匹配可靠度不够2成品电检8128增加原材料插拔力实验修改端子护套来料检验指导书82232护套达不到防水级别护套进水,功能丧失8护套防水级别不够28128增加原材料防水试验修改端子护套来料检验指导书82232导线耐电压性能不达标耐压不够8供应商质量问题1驻厂检验216导线导体电阻性能不达标电性能不稳定8供应商质量问题1驻厂检验216外观缺陷错误登记影响交货日期6库管员粗心1自己检查318使用错误物料错误物料物料功能丧失7库管员粗心1自己检查214物料损坏7错误操作1操作工自我控制321责任及目标完成日期DOS建议措施风险顺序数RPN 潜在失效起因/机理物料标识A、检查物料的型号、规格、尺寸、标识、外观;判定是否合格。
B、端子护套可靠性检测。
C、护套防水试验分类保管合格入库物料物料无损、正确配送到生产工位来料检查物料存储物料移动FMEA编制日期:编制人:现行过程控制措施结果过程功能要求级别潜在失效模式潜在失效后果驾驶室主线过程责任部门:技质部FMEA编号:关键日期:修订:项目名称:产品型号:车型: 主要参加人:预防探测采取措施SODRPN责任及目标完成日期DOS 建议措施风险顺序数RPN 潜在失效起因/机理FMEA编制日期:编制人:现行过程控制措施结果过程功能要求级别潜在失效模式潜在失效后果驾驶室主线过程责任部门:技质部FMEA编号:关键日期:修订:断线芯,伤线芯。
性能下降6设备设置错误3100%自检236首件检验下错导线不能使用6缺标识2100%自检224切线、波纹管不能使用7设备设置错误1321尺寸过短下料尺寸超差长影响组装5输入值错误5培训操作者8200首末检查52220剥皮过长影响外观及 组装6设备设置错误1培训操作者318首件检验剥皮过短影响拉脱力7设备设置错误2培训操作者228首件检验线体波纹管影响外观4原材料缺陷2操作者100%自检216表面有缺陷压接拉力过小拉脱力不够,导线脱落搭铁9模具调整错误3首件/过程检验381设专人调整模具92354压接拉力过大断线芯7模具调整不当2过程控制342线芯伸出过长影响装配7操作失误2100%自检342线芯伸出过短影响拉脱力7操作失误2100%自检342压绝缘皮,压断导线电路不通8送料不到位2培训操作者100%自检348端子压接操作失误2100%检验342首件检验培训操作者检查标识培训操作者不能装配7按照裁线压接工艺表标注的导线数量、型号、颜色、长度、剥皮方向及长度加工按照裁线压接工艺表压接端子、超声波焊★切线剥皮 波纹管切断★端子压接、超声波焊项目名称:产品型号:车型: 主要参加人:预防探测采取措施SODRPN责任及目标完成日期DOS 建议措施风险顺序数RPN 潜在失效起因/机理FMEA编制日期:编制人:现行过程控制措施结果过程功能要求级别潜在失效模式潜在失效后果驾驶室主线过程责任部门:技质部FMEA编号:关键日期:修订:不能装配7接工艺表压接端子、超声波焊超声波焊项目名称:产品型号:车型: 主要参加人:预防探测采取措施SODRPN责任及目标完成日期DOS建议措施风险顺序数RPN潜在失效起因/机理FMEA编制日期:编制人:现行过程控制措施结果过程功能要求级别潜在失效模式潜在失效后果驾驶室主线过程责任部门:技质部FMEA编号:关键日期:修订:86.0mm 2导线压接状态,影响整车对插装配3端子插接听“咔”声,轻轻回拉确认100%自检248专用模具压接首件装配验证目视9119平齿影响电性能9端子压接搬运3插接原则38192236造成操作不规范锁紧件未上可靠性能下降8操作失误1100%自检216作业工艺卡未按规定布线影响外观线束6导线无理顺1返修自检318尺寸端子插反影响客户装配7拿错方向1100%目测214护套方向错影响客户装配5拿错方向1案板直观注明210零件正反易混淆方向目测检查漏装线影响电路6未进行检查1按案板示意318图进行组装100%目视自检插错孔位混路烧车9未进行检查4100%电检272100%自检92236波纹管装配影响分支尺寸6未装配到位1装配图标明318有偏差影响客户装配长度,直径位置100%自检按照产品图纸,把分装子件组合成线束组装线束项目名称:产品型号:车型: 主要参加人:预防探测采取措施SODRPN责任及目标完成日期DOS 建议措施风险顺序数RPN 潜在失效起因/机理FMEA编制日期:编制人:现行过程控制措施结果过程功能要求级别潜在失效模式潜在失效后果潜在失效模式及后果分析(PFMEA )驾驶室主线过程责任部门:技质部FMEA编号:关键日期:修订:穿波纹管时绝缘性能下降7导线未防护1装波纹管时214纸,把分装子件组合成线束项目名称:产品型号:车型: 主要参加人:预防探测采取措施SODRPN责任及目标完成日期DOS建议措施风险顺序数RPN 潜在失效起因/机理FMEA编制日期:编制人:现行过程控制措施结果过程功能要求级别潜在失效模式潜在失效后果潜在失效模式及后果分析(PFMEA )驾驶室主线过程责任部门:技质部FMEA编号:关键日期:修订:全尺寸功。
【行业分析】(PFMEA)汽车行业过程失效模式分析

Who performs a PFMEA 四、何人做PFMEA
由跨部门小组进行(A cross-functional team should be used).
小组的组长应由过程设计工程师(项目 负责人)(the leader should be the process responsible engneer)
何时进行Pfmea
Do a pfmea (or at least review the old one) if : 以下情况需要进行pfmea(或至少评审过去的pfmea)
法律环境发生变化(legal envoriment changes)
发生实际实效(actual failures occur) (FMEA是一个动态的文件)(且也可以是 纠正措施,从实际使用上)
前言
“我先… …所以没有”
我先 我先 我先 我先
看了气象预报 所以没有 淋成落汤鸡 评估金融大楼高度 所以没有 影响飞机安全 设计电脑防火墙 所以没有 被骇客入侵 作好桥梁设计 所以没有 造成重庆彩虹大桥倒塌
有些 我先 是必需的!有些 所以没有 是可预期避免的
有效运用 FMEA 可减少事后追悔
When do we do a PFMEA
三、一何时进行Pfmea
Do a pfmea (or at least review the old one) if : 以下情况需要进行pfmea(或至少评审过去的pfmea)
新过程 原有过程发生变化时 顾客要求发生变化时
When do we do a PFMEA
失效模式:由于过程未达到而导至产品缺陷、 瑕疵等不良状态
典型的失效模式:
A机械类:磨损、变形、腐蚀、破损、脱落等
热处理PFMEA失效模式分析实例

德信诚培训网潜在失效模式及后果分析FMEA编号:(过程FMEA)编号:PFMEA-21项目名称:N 系列过程责任部门:DXC热处理厂编制者:车型年/车辆类型:CA-153系列关键过程:01。
07。
15 FMEA日期(编制):0 1.06.24 (修订)主要参加人:过程/功能要求潜在的失效模式潜在的失效后果严重度级别潜在的失效原因/机理频度数现行过程控制可探测度风险顺序数RPN建议的措施责任及目标完成日期措施结果采取的措施严重度频度数不可探测度数风险顺序数RPN热处理过程硬度符合技术要求金相1-2级产品应无淬裂硬度超过技术要求缺乏韧性产生脆断,影响整车的安全性。
10 ▲设备上的仪表失灵2 每季度送计量局校准仪表一次8 160 增加仪表验证次数DXC热处理厂01.07.15每班校对仪表一次10 2 2 40操作者控制回火时间低于工艺要求3 利用人工计时8 240 增加定时报警装置DXC热处理厂01.07.15增加可设定时间的电子时钟警报器并每季度校对一次10 3 1 30回火温度低于工艺要求3 专人监视设备上温度仪表5 150 增加超温温度警报装置DXC热处理厂01.07.155增加温度传感器连接警报器,在温度达到要求时发出提示并每季度校对一次10 3 1 30材料含C量不明确影响2 验证质保单,每批化验2-3根后再热处理2 40 无德信诚培训网潜在失效模式及后果分析FMEA编号:(过程FMEA)编号:PFMEA-21 项目名称:N 系列过程责任部门:DXC热处理厂编制者:车型年/车辆类型:CA-153系列关键过程:01。
07。
15 FMEA日期(编制):0 1.06.24 (修订)主要参加人:过程功能要求潜在的失效模式潜在的失效后果严重度数级别潜在的失效原因/机理频度数现行过程控制可探测度风险顺序数建议的措施责任及目标完成日期措施结果采取的措施严重度频度数不可探测度数风险顺序数RPN热处理过程硬度符合技术要求金相1-2级产品应无淬裂硬度达不到技术要求抗拉强度不够,产品延伸变形,影响整车的安全性。
PFMEA过程失效模式及后果分析
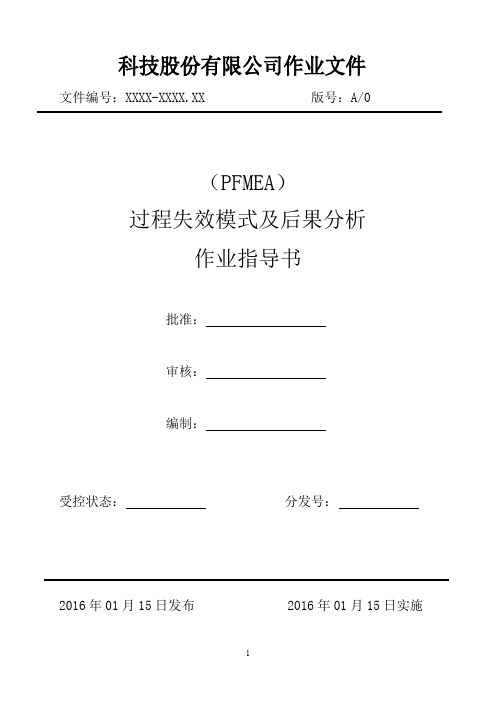
科技股份有限公司作业文件文件编号:XXXX-XXXX.XX 版号:A/0(PFMEA)过程失效模式及后果分析作业指导书批准:审核:编制:受控状态:分发号:2016年01月15日发布2016年01月15日实施过程潜在失效模式及后果分析作业指导书(PFMEA)XXXX-XXXX.XX1目的过程潜在失效模式及后果分析,简称PFMEA。
是一种信赖度分析的工具,可以描述为一组系统化的活动,是对确定产品/过程必须做哪些事情才能使顾客满意这一过程的补充。
其目的是:(a)并评价产品/过程中的潜在失效以及该失效的后果;(b)确定能够消除或减少潜在失效发生机会的措施;(c)将全部过程形成文件。
2范围:适用于公司用于零组件的所有新产品/过程的样品试制和批量生产。
适用于过程设计的风险性及后果的分析;适用于过程重复,周期性永不间断的改进分析。
3术语和定义:1)PFMEA:指Process Failure Mode and Effects Analysis(过程失效模式及后果分析)的英文简称。
由负责制造/装配的工程师/小组主要采用的一种分析技术,用以最大限度地保证各种潜在的失效模式及其相关的起因/机理已得到充分的考虑和论述。
2)失效:在规定条件下(环境、操作、时间),不能完成既定功能或产品参数值和不能维持在规定的上下限之间,以及在工作范围内导致零组件的破裂卡死等损坏现象。
3)严重度(S):指一给定失效模式最严重的影响后果的级别,是单一的PFMEA范围内的相对定级结果。
严重度数值的降低只有通过设计更改或重新设计才能够实现。
4)频度(O):指某一特定的起因/机理发生的可能发生,描述出现的可能性的级别数具有相对意义,但不是绝对的。
5)探测度(D):指在零部件离开制造工序或装配之前,利用第二种现行过程控制方法找出失效起因/机理过程缺陷或后序发生的失效模式的可能性的评价指标;或者用第三种过程控制方法找出后序发生的失效模式的可能性的评价指标。
PFMEA过程失效模式及后果分析

PFMEA过程失效模式及后果分析PFMEA(Process Failure Mode and Effects Analysis)是一种通过系统地识别和评估潜在的失效模式及其后果来预防产品和过程问题的方法。
它有助于组织在设计和开发阶段就发现并解决潜在的问题,从而提高产品质量和生产效率。
在这篇文章中,我们将重点讨论PFMEA过程中的失效模式及其后果分析。
失效模式是指导致产品或过程失效的特定原因或机制。
它可以是由于设计缺陷、材料问题、加工误差、操作失误等引起的。
失效模式常常以不同的方式出现,在不同的环境下可能会有不同的后果。
在进行PFMEA过程中,首先需要识别潜在的失效模式。
这可能涉及到对产品、过程和相关文档的仔细研究,以了解可能存在的问题。
接下来,需要对每个失效模式的影响进行评估,这也就是后果分析。
后果分析可以帮助确定失效对产品质量、生产效率和安全性等方面造成的影响,从而决定需要采取的预防措施。
在进行PFMEA过程失效模式及后果分析时,以下是一些常见的失效模式和其可能的后果:1.设计缺陷:-可能的后果:产品性能不达标、产品寿命缩短、安全隐患、产品被召回等-预防措施:加强设计评审、使用可靠的设计工具、进行模拟测试等2.材料问题:-可能的后果:产品强度不足、耐腐蚀性差、产品寿命缩短等-预防措施:严格选择、测试和审查材料供应商、加强入库检查等3.加工误差:-可能的后果:产品尺寸偏差、表面质量不良、装配困难等-预防措施:加强生产工艺控制、使用先进的制造设备、严格执行质量标准等4.操作失误:-可能的后果:生产过程中出现错误、设备损坏、人员伤亡等-预防措施:提供员工培训、实施作业规程、设立安全警示标志等除了上述提到的失效模式和后果,还有许多其他可能的情况需要被考虑和分析。
在进行PFMEA过程中,团队成员需要全面了解产品和过程,积极参与讨论和决策,以确保有效识别和评估潜在的问题。
此外,通过对失效模式及后果进行分析,团队还可以确定应对措施的优先级和实施计划。
- 1、下载文档前请自行甄别文档内容的完整性,平台不提供额外的编辑、内容补充、找答案等附加服务。
- 2、"仅部分预览"的文档,不可在线预览部分如存在完整性等问题,可反馈申请退款(可完整预览的文档不适用该条件!)。
- 3、如文档侵犯您的权益,请联系客服反馈,我们会尽快为您处理(人工客服工作时间:9:00-18:30)。
补充
前题:
1、来料是好的 2、产品的设计是满足顾客要求的
6、列出每一项失效模式所有的可能 后果
可能后果主要从以下几个方面来考虑: A、最终用户 B、中间用户 C、法律法规 D、下序 (顾客报怨或投诉就是很好的信息来源)
后果可能为:
A、功能完全丧失 B、质量或性能下降 C、设备受损 D、员工受伤 E、停线 ……
4、列出质量要求
以顾客为关注焦点
顾客的希望或者要求
有可能导至顾客的投诉
5、列出可能的过程失效模式
什么叫失效模式:由于过程未达到而导至产
品缺陷、瑕疵等不良状态.(失效模式体现 在产品上) 典型的失效模式 A、直径超差;B、漏装密封垫;C、切破线 皮;D、未充满;
考虑:
我们公司有哪些失效模式?
How do we do a PFMEA 如何进行PFMEA
计算风险顺序数(RPN)以确定应优先采取
的措施,caculate the risk priority number (RPN) prioritize corrective action(S) 制定纠正措施并落实责任人,plan corrective action(s) and assign owner(S) 采取措施以提高产品和过程质量,perform corrective actions to improve the product and process qualit (ies) y .
思考
跨部门小组在FMEA建立过程中是非常重要的, 哪些人不能作为小组成员?如果小组成员有有 这些人,我们如何处理?
How do we do a PFMEA?A Summary. 五、如何进行PFMEA?提要。
组建跨部门PFMEA小组,assemble the crossfunctional team 列出生产过程流程图 针对过程流程图列出过程的潜在失效模式、后 果及原因,list the failure modes、their effects and their causes 失效模式:由于过程未达到而导至产品缺陷、 瑕疵等不良状态
思考:
针对所列出的失效模式来分析有哪些失效后
果?
7、评估每种后果的严重度
8、确定每一项失效模式的可能原因
失效原因:过程为何会失效
如人的过失、工装的磨损、环境条件及因素间 的变化等 建议针对每一种失效模式,找出原因,记入 FMEA表中
9、评估每种失效原因产生的可能性 (频度)
1、利用历史资料
二、Fmea 发展史
1、FMEA的前身为FMECA,是在1950由格鲁曼 飞机提出,用在飞机主控系统的失效分析 2、波音与马丁公司在1957年正式编订FMEA的 作业程序,列在其工程手册中 3、60年代初期,美太空总署将FMECA成功的应 用于太空计划。美军同时也开始应用FMECA技 术,并于1974年出版MIL-STD-1629 FMECA作 业程序。 4、1985由国际电工委员会(IEC)出版的 FMECA国际标准(IEC812),即参考MIL-STD1629A加以部分修改而成。
表8.推荐的PFMEA探测度评价准则
12.风险顺序数
风险顺序数是严重度数(S)、频度数(O)和探测数(D) 的乘积,见公式。 RPN = (S) ×(O) ×(D) 风险顺序数作为(S) ×(O) ×(D) 的积,是对设计 风险性的度量。风险顺序数应当用于对过程中那些 担心事项进行排序(如用柏拉图)。RPN取值在1~1000 之间。 ★★关注的是:RPN值较高过程和严重度大于8的过程
法律环境发生变化(legal
envoriment
changes) 发生实际实效(actual failures occur) (FMEA是一个动态的文件)(且也可以是 纠正措施,从实际使用上)
Who performs a PFMEA 四、何人做PFMEA
由跨部门小组进行(A
cross-functional team should be used). 小组的组长应由过程设计工程师(项目 负责人)(the leader should be the process responsible engneer)
3、List the function(s) of each operation 列出每个操作功能
功能系指该操作所起的作用������ A function is what the operation does State the function as,说明功能为: Verb + Object + Qualifier 动词+宾语++修饰词 例如: 1、零件成型mold part 2、在线端压接端子crimp terminal onto cable 3、零件弯曲成型form bend in part, examples
11、探测度
探测度是对列在过程控制栏位的最差的检
查控制的相应分数。对每一个FMEA的范 围探测度是一个相对的分数。为了达成较 低的分数,通常计划的过程控制应当改善。 随机质量抽查不大可能查明某一缺陷的存 在,也不影响探测度数值的大小。以统计 原理为基础的抽样检查是一种有效的探测 的控制方法。
以下情况需要进行pfmea(或至少评审过去的pfmea)
新过程 原有过程发生变化时 顾客要求发生变化时
When do we do a PFMEA
何时进行Pfmea
Do a pfmea (or at least review the old one) if : 以下情况需要进行pfmea(或至少评审过去的pfmea)
评估,Assess 1、后果的严重程度 the severity of the effect(s)(S) 2、原因出现的可能性 The likelihood of the cause(s) (0) 3、过程控制控测失效模式和(或)原因的能力 And the ability of controls to defect failure mode(s) and/or their cause(s)(D)
Pfmea 十六个步骤
1、assemble a team and plan your activeties
成立小组并制定计划
绝不能由个人单独进行pfmea,因为:
Pfmea must never be done by an individual,because: 由个人进行会使结果出现偏差 Individual efforts produce bases results 进行任何活动都需要从不同的组织获取信息 Any actions will riquire buy-in from various groups
前言
“我先… …所以没有”
我先 我先 我先 我先
看了气象预报 所以没有 淋成落汤鸡 评估金融大楼高度 所以没有 影响飞机安全 设计电脑防火墙 所以没有 被骇客入侵 作好桥梁设计 所以没有 造成重庆彩虹大桥倒塌
有些 我先 是必需的!有些 所以没有 是可预期避免的 有效运用 FMEA 可减少事后追悔
PFMEA
理
念
如果,你总时做你过去常做的 那么,你总是得到你过去得到的;
重点
老方法 问题的解决 浪费的监视 可靠性的量化 新方法 防止问题的发生 消除浪费 消除不可靠性
中国质量管理存在的七大不良现象
表现症状: 1抓壮丁现象 2疲劳现象 3惯性现象 4守株待兔现象 5被同一块石头多次绊倒现象 6邻居现象 7脚底抹油现象
How do we do a PFMEA? A suggesting! 如何进行PFEA?建议。
先在一张草稿纸上进行分析,当小组达成一
致意见后,再将有关信息填写在PFMEA表上。 Do your work on scratch paper first,as the team reaches consensus,record the information on the FMEA from. 充分利用鱼刺图和树形图,use fishbone and diagrams libarally
典型的失效模式: A机械类:磨损、变形、腐蚀、破损、脱落等 B电气类:开路、短路、接触不良、过热、断 线等 C化学类:腐蚀、老化、变色、固化、污染、 过热等
失效后果应从以下方面来考虑: A、最终用户 B、中间用户 C、法律法规 D、下序 如:员工受伤、不能使用等
How do we do a PFMEA 如何进行PFMEA
早知道...就不会
“早知道… …就不会”
早知道 早知道 早知道 早知道
作好防震设计 就不会 造成大楼倒塌 改进电力输配设计 就不会 造成美国等国的大停电 不滥砍滥伐 就不会 造成泥石流 作好桥梁设计 就不会 造成重庆彩虹大桥倒塌
有些 早知道 是必需的!有些 就不会 不允许发生的事就不会发生了 有效运用 FMEA 可减少事后追悔
Fmea分类
设计(D)fmea:是由负责设计的工程师/小组主要 采用的一种分析技术,用以最大限度地保证各种潜 在的失效模式及相关的起因/机理已得到充分的考虑 和说明。对最终的项目以及与之相关的每个系统、 子系统和部件都有应进行评估 制造或装配(P)fmea:是由负责制造/装配的工程 师/小组主要采用的一种分析技术,用以最大限度地 保证各种潜在的失效模式及其相关的起因/机理已得 到充分的考虑和论述。FMEA以最严密的方式总结 了开发一个过程时小组的思想。(其中包括根据以 往的经验可能会出错的一些项目的分析)
三:为什么要做fmea呢?
认可并评价产品或过程中存在哪些潜在的失
效后果; 这些失效后果对顾客会造成什么样的影响 为了减少失效后果对顾客的影响我们应采取 哪些措施防止失效后果的产生以使顾客满意