基于Moldflow玩具汽车外壳注塑模优化设计
基于Pro/E和Moldflow的注塑件优化设计
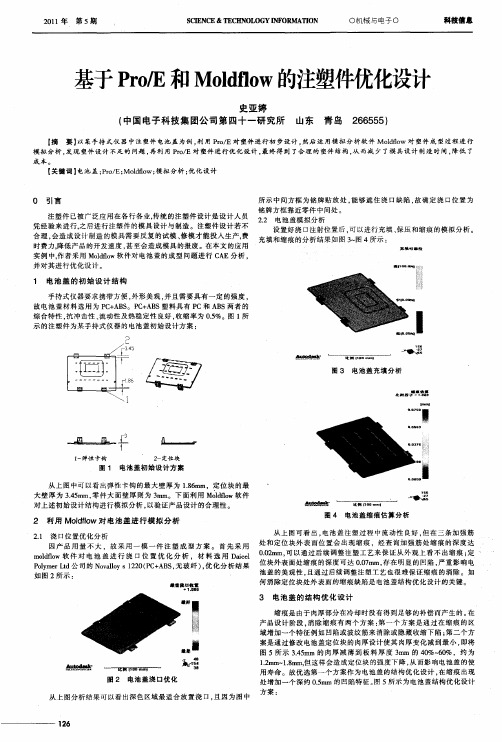
l抒
3 电池 盖 的 结 构优 化设 计
缩 痕 是 由于 肉厚 部 分 在 冷 却 时没 有 得 到 足 够 的补 偿 而 产 生 的 。 在 产 品设计 阶段 , 消除缩痕有 两个 方案 : 第一个 方案是通过在缩 痕的区 域 增 加 一 个 特 征 例 如 凹 陷 或 波 纹 筋来 消 除或 隐 藏 收缩 下 陷 ; 二 个 方 第 案是通过修改 电池盖定位块的 肉厚设 计使其 肉厚变化减到最小 , 即将 图 5所 示 34 mm 的 肉 厚 减 薄 到 板 料 厚 度 3 . 5 mm 的 4 %~ O ,约 为 O 6% 1 mm~ .m 但 这 样 会 造 成 定 位 块 的 强 度下 降 , 而 影 响 电池 盖 的 使 . 2 18 m。 从 用寿命 。故优选第一个方案作为电池盖的结 构优化设 计 , 在缩痕 出现 处 增 加 一个 深约 05 m 的 凹陷 特 征 。 5所 示 为 电 池盖 结 构 优 化 设 计 .m 图 方案 :
因产 品 用 量 不 大 .故 采 用 一 模 一 件 注 塑 成 型 方 案 。 首 先 采 用 处 和 定 位 块 外 表 面 位 置 会 出现 缩 痕 ,经 查 询 加 强 筋 处 缩 痕 的 深 度 达 00 m 可 以通 过 后 续调 整 注 塑 工 艺 来 保 证 从 外 观 上 看 不 出 缩 痕 ; .2 m. 定 m lf w 软 件 对 电 池 盖 进 行 浇 口 位 置 优 化 分 析 , 材 料 选 用 Da e od o l il e 位 块 外 表 面 处 缩 痕 的 深 度 可 达 00mm, 在 明显 的 凹 陷 , 重 影 响 电 .7 存 严 P lm r t 司 的 N vl ys12 ( C AB 无 玻 纤 )优 化 分 析 结 果 oy e d公 L oal 2 0 P + S, o , 池 盖 的美 观 性 , 通 过 后 续 调 整 注 塑工 艺 也 很 难 保 证 缩 痕 的 消 除 。 如 且 如 图 2所 示 : 何 消除 定 位 块 处 外 表 面 的 缩痕 缺 陷是 电池 盖 结 构 优 化 设 计 的 关 键 。 t筐矗 n畦 t
基于MoldFlow的注塑模具浇口优化设计

图3 划分网格后的模型
3.2 材料及工艺参数的确定
本文设计的手机上盖属于中小塑件。此制 品将直接与用户手部接触并需承受频繁的按 动。因此,要求很高的表观质量和手感,并具 有一定的强度。这里选用ABS塑料,工艺条件 如下:
()模温:60.0 ℃ (2)熔体温度:240 ℃ (3)注塑时间:.2 s (4)注塑机的压力控制模块的最大注塑压
4
力:80 MPa (5)模块中的最大锁模力:702.2 kN,其
余均采用默认值。
3.3 浇口位置优化的预分析
浇口设计应保证提供一个快速、均匀、平 衡、单一方向流动的充填模式,避免喷射、滞 流、凹陷等现象的发生,所以要在选定浇口方 案之前,对制品进行最佳浇口位置的预分析。 利用MPI软件中的Gate Location分析模块,在 前处理中将分析类型设为Gate Location,并设 置好工艺过程参数。运行Gate Location分析 后,得到一个最佳的浇口位置(图4中圆圈所 示)。Gate Location分析模块只是为设计分析 初步找到一个最佳的浇口位置区域,该浇口位 置只是一个参考位置,对将来的设计有很好的 参考价值。下一步需要根据现有的分析结果对 手机上盖进行注塑、保压及相应的翘曲计算, 再根据得到的结果进一步分析产品的质量及模 具设计的合理性,从而向最佳方案逼近。
基于moldflow的外壳注塑模具及工艺优化研究

基于moldflow的外壳注塑模具及工艺优化研究
外壳注塑是广泛应用于各行各业的工艺,被广泛应用到汽车行业、家电行业、建材行业和医疗行业等制造领域。
作为实时了解塑料模具塑性流动情况的一种重要手段,Moldflow(模流)逐步被采用到外壳注塑行业,助力外壳注塑模具和工艺优化研究。
Moldflow模具软件模拟了外壳注塑模具在注塑过程中的各种流动行为。
由于外壳注塑模具的设计复杂,需要考虑模具的凹模、凸模、热料罐、滑块等设计,以确保在注塑过程中注塑塑料能够达到设定的要求。
Moldflow通过模拟外壳注塑模具的温度、塑性流动路径等,让设计者更清楚地了解外壳注塑模具在注塑过程中的行为,进而预防和纠正可能出现的问题。
在外壳注塑模具设计中,Moldflow可以用以预测模具的流动性能,以确定塑料的注射压力和金属模具的热扩散性,了解材料塑性流变行为,以预防塑性流动的影响因素,如堵塞和气体弹性,以及优化前后端楔位的设计。
另外,Moldflow可以模拟完整的整体流程,包括注塑过程中的熔体流动、塑料模具热变形、模具温度、层物性变化、塑料成型质量、运动等流体分析,以提供更快捷、更完备的分析结果。
最后,可以用Moldflow技术来解决外壳注塑模具的设计和开发中遇到的各种问题,从而提高模具的效率和产品的质量。
基于Moldflow的玩具汽车外壳注塑模设计
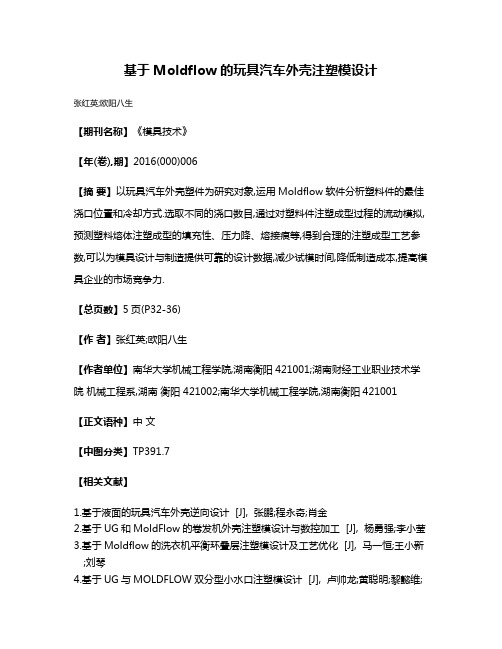
基于Moldflow的玩具汽车外壳注塑模设计
张红英;欧阳八生
【期刊名称】《模具技术》
【年(卷),期】2016(000)006
【摘要】以玩具汽车外壳塑件为研究对象,运用Moldflow软件分析塑料件的最佳浇口位置和冷却方式.选取不同的浇口数目,通过对塑料件注塑成型过程的流动模拟,预测塑料熔体注塑成型的填充性、压力降、熔接痕等,得到合理的注塑成型工艺参数,可以为模具设计与制造提供可靠的设计数据,减少试模时间,降低制造成本,提高模具企业的市场竞争力.
【总页数】5页(P32-36)
【作者】张红英;欧阳八生
【作者单位】南华大学机械工程学院,湖南衡阳421001;湖南财经工业职业技术学院机械工程系,湖南衡阳 421002;南华大学机械工程学院,湖南衡阳421001
【正文语种】中文
【中图分类】TP391.7
【相关文献】
1.基于液面的玩具汽车外壳逆向设计 [J], 张鹏;程永奇;肖金
2.基于UG和MoldFlow的卷发机外壳注塑模设计与数控加工 [J], 杨勇强;李小莹
3.基于Moldflow的洗衣机平衡环叠层注塑模设计及工艺优化 [J], 马一恒;王小新;刘琴
4.基于UG与MOLDFLOW双分型小水口注塑模设计 [J], 卢帅龙;黄聪明;黎懿维;
黄金培;林立;林权
5.基于Moldflow与Workbench的底座塑件推杆配置优化及偏心注塑模设计 [J], 林权; 陈丽军; 陈莲; 林鑫; 张道平
因版权原因,仅展示原文概要,查看原文内容请购买。
Moldflow软件在汽车零件注塑模具设计中的应用

万方数据枕料2009年第9期总第36卷计算机应用技术・41・求零件重心处为工作平面不允许有浇口或其它痕迹存在,同时指定浇口位置如图2所示,该浇口不满足熔料流动的平衡性,Moldflow分析零件变形量为0.85左右,无法满足要求,零件的翘曲变形趋势如图3所示。
图1汽车安全带上盖零件图2指定浇口位置图3翘曲变形分析发生严重翘曲变形的原凶在于指定浇口处材料太薄,阻碍熔料的流动与填充,流动不平衡,在模具进行保压时无法将压力传送到各个角落,成型注射压力情况如图4所示。
进浇口附近保压时熔料容易在薄壁处冷却,同时模具上下表面温差大,影响零件的保压,易缩水。
为改善翘曲,可更改冷却条件,采用将定模侧冷却温度低于动模侧5度左右的方法,Moldflow分析调整温度后翘曲变形量为o.27如图5所示,符合零件要求。
2.2困气分析零件在成型的过程中,气体如不能及时排出模腔就会产生困气现象,将会影响零件成型以及脱模后的质量。
Moldflow分析零件成型时,困气的位置主要分布在合模线附近,如图6所示,尤其是零件的四个卡扣处困气问题较严重,因此四个卡扣分别在凸凹模侧安装镶件,同理模仁中也做镶件,这样能将产品中大部分的易困气部分解除,达到熔料流动均匀的目的。
图4成型注射压力图5调整温度后翘曲变形分析.2.3熔接痕分析熔接痕是由于来自不同方向的熔料前端部分被冷却,而在结合处未能完全融合而产生的。
熔接痕主要影响外观,严重时对零件强度产生影响。
因此在零件成型的过程中应尽量避免熔接痕,在不可避免的情况下应当尽量将熔接痕推至不受力区,以达到零件的使用寿命要求。
Moldflow分析产生熔接痕的位置如图7所示,主要集中在零件的角落,对外观和强度的影响较小。
图6困气位置图7熔接痕位置万方数据・42・计算机应用技术扔柳2009年第9期总第36卷2.4冷却方式分析3结论注塑模温度对熔料的充模流动,固化定型、生产率以及零件的形状和精度等有着直接影响。
该模具采用对称单循环水路冷却,水管直径8mm。
基于Moldflow的薄壁注塑件的工艺参数优化

基于Moldflow的薄壁注塑件的工艺参数优化刘晓红(九江职业技术学院,九江332000)摘要以充电器外壳为例采用Moldflow软件对各工艺参数进行注射成型过程的模拟。
运用信噪比分析分别研究各工艺参数对收缩、锁模力和翘曲变形的影响权重,得到最小目标值对应的最优工艺组合。
利用最优组合对应的工艺参数,模拟试验验证了正交试验的有效性。
利用正交试验对该薄壁注塑件进行了工艺参数优化的可靠性验证。
关键词注射成型参数优化正交试验Moldflow随着科学水平的不断提高,人们对于传统工业有了更高的要求,一些新的方法被引用到这些行业中,其中CAE技术是目前各行业的大体趋势。
传统工业中,塑料以其应用范围广、质量轻的优点迅速成为一大行业。
面对现代塑料注塑件的品种繁多、结构复杂、精度高和生产周期短的要求,传统工业中注塑模具依靠设计人员的经验进行模具设计、反复修模和试模是无法满足的[1]。
采用计算机技术可对塑料模具进行辅助设计,通过CAE技术模拟成型质量,预知注塑件可能存在的缺陷并提出优化方案。
实际生产中,经常会遇到薄壁类注塑件,这类注塑件的长径比大,降低了其可见成型性,在成型过程中,常会出现壁厚不均匀、短射、翘曲变形和熔接痕等缺陷,不能很好地满足要求[2-3]。
笔者采用Moldflow软件对薄壁注塑件的注射成型过程进行模拟分析,预测填充时间、收缩值、锁模力和翘曲变形的位置和大小,在正交试验的基础上采用信噪比和方差分析提出并验证优化方案。
1注塑件成型过程模拟1.1注塑件概况图1所示为某充电器塑料外壳的三维几何模型和有限元模型。
该注塑件属于薄壁件,其长为95 mm,宽为45mm,高为13mm,厚度为1mm。
有限元模型经手动修改后的网格匹配率达到91.8%(>90%),确保了CAE分析的可靠性。
由于三维模具中给出了特定的浇注系统和冷却系统,且为一模两腔,所以在Moldflow中通过手动建立浇注系统和冷却系统,最终的分析模型如图2所示。
如何使用MOLDFLOW来帮助产品设计优化,模具设计优化和工艺优化

优化前
25
优化后
案例 6 优化模具设计解决产品变形问题
优化前
优化后
优化后相应产生模温差,并且省掉了加工隔水片的费用和工时。
26
三、优化工艺参数
1、优化保压曲线 2、优化冷却水路温度 3、优化螺杆曲线
27
案例 1 优化工艺
产品: 材料: 目的: 车灯配光镜 PMMA 工艺调试变形 透明 优化工艺
原始方案: 流道完全冷却所需时间117秒, 如果 按照流道冷却50%时顶出, 成型周 期约75秒.
优化方案: 流道完全冷却所需时间68秒, 如果 按照流道冷却50%时顶出, 成型周 期约50秒.
打一个产品可以节约25s
24
案例 6 优化模具设计解决产品变形问题
产品: 材料: 问题: 结果: 配光镜 PC 变形 解决了变形问题
底部镶块的水温设置为25度 其他冷却水路温度不变, 为55度
32
案例 2 优化冷却水温度解决翘曲变形
5倍放大效果图,最大整体变形为: 1.119mm
5倍放大效果图,最大Z向收缩变形 为:1.2 mm
可见,变形量大大降低
33
16
二、优化模具设计
1、为模具设计人员提供最佳浇口位置和数量方案------浇口位置和数量的好坏是一幅 模具成功的一半 2、优化浇口尺寸和流道尺寸, 流动平衡, 缩短成型周期 3、优化冷却水路, 降低成型周期
17
案例 1 向模具设计提供最佳浇口方案
产品: 材料: 手套箱外观件 PA66+40% 目的:浇口位置对熔接线的影响
蓝色区域壁厚从3mm 增加至4.5mm,
6
案例 1 优化产品设计解决翘曲变形
优化结果
1.87mm
基于Moldflow的汽车盒体件注塑模具设计
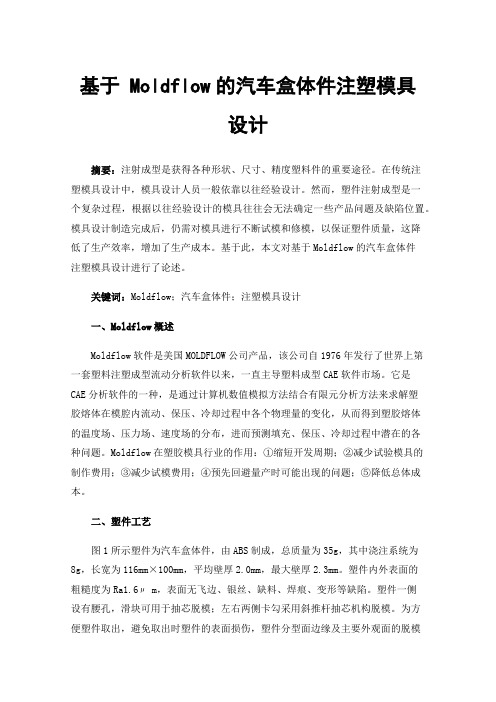
基于 Moldflow的汽车盒体件注塑模具设计摘要:注射成型是获得各种形状、尺寸、精度塑料件的重要途径。
在传统注塑模具设计中,模具设计人员一般依靠以往经验设计。
然而,塑件注射成型是一个复杂过程,根据以往经验设计的模具往往会无法确定一些产品问题及缺陷位置。
模具设计制造完成后,仍需对模具进行不断试模和修模,以保证塑件质量,这降低了生产效率,增加了生产成本。
基于此,本文对基于Moldflow的汽车盒体件注塑模具设计进行了论述。
关键词:Moldflow;汽车盒体件;注塑模具设计一、Moldflow概述Moldflow软件是美国MOLDFLOW公司产品,该公司自1976年发行了世界上第一套塑料注塑成型流动分析软件以来,一直主导塑料成型CAE软件市场。
它是CAE分析软件的一种,是通过计算机数值模拟方法结合有限元分析方法来求解塑胶熔体在模腔内流动、保压、冷却过程中各个物理量的变化,从而得到塑胶熔体的温度场、压力场、速度场的分布,进而预测填充、保压、冷却过程中潜在的各种问题。
Moldflow在塑胶模具行业的作用:①缩短开发周期;②减少试验模具的制作费用;③减少试模费用;④预先回避量产时可能出现的问题;⑤降低总体成本。
二、塑件工艺图1所示塑件为汽车盒体件,由ABS制成,总质量为35g,其中浇注系统为8g,长宽为116mm×100mm,平均壁厚2.0mm,最大壁厚2.3mm。
塑件内外表面的粗糙度为Ra1.6 m,表面无飞边、银丝、缺料、焊痕、变形等缺陷。
塑件一侧设有腰孔,滑块可用于抽芯脱模;左右两侧卡勾采用斜推杆抽芯机构脱模。
为方便塑件取出,避免取出时塑件的表面损伤,塑件分型面边缘及主要外观面的脱模斜度设为3.0°,滑块及斜推机构的脱模斜度设为1.0°。
为避免塑件应力集中产生裂痕,在塑件连接处进行圆角过渡处理。
为保证塑件的外观质量,采用三板潜伏式浇口进料。
图1 塑件结构及浇注系统三、基于Moldflow的塑件模流1、浇注系统设计。
基于MoldFlow的注塑模具浇口优化设计

0
引言
注 塑 模 具 cAD/ CAE 术 的发 展 和 应 用 使 技
浇 口数 量 和 位 置 是 重 要 的模 具 结 构 参 数 ,它 与
塑料性能 、塑件形状和尺寸 、模具结构及注塑 工艺等 因素有关 。因此 ,对浇 口数量及位置进 行优化设计 ,特别是对复杂结构 的注塑件具有
位置主要影响充填模式 ,而浇 口的形状 与尺寸 影 响熔 体 流动 性质 。它可 以 设置 在制 件 的一 处或 多处 ,而 且可 有 多种 类型 ,如薄 片浇 口
( i Gae 、侧 浇 口 ( g / ieGae 、 Fl m t) Ed eSd t )
截面又很狭 窄的料流通道 ( 直浇 口除外 )。注 塑件的质 量在 很大程度上取决于模具设计 ,而
重 要 的应 用 价值 。
模 具 设 计 、加 工 的 成本 大大 降 低 ,效 率 成倍 提
高 ,其 中以Mod lw lfo 软件的应用最具代表性 。
它 不 仅 能 够 模 拟 分 析热 塑性 塑料 熔 体 进 入 模 具
的 流 动 过 程 ,而 且还 能 对 塑件 的浇 口位 置 、压
( elpGae 、 凸耳 式 浇 I ( a t) Ov ra t ) 3 T bGae 、
pl s i ol i a tc m d ng, M o dfo , s e i ofwa e f r a l ng t e pl s i o i ll w p c als t r o nayzi h a tc f w n mol l d, wa s
ap i o te o t z t n d s no aei i e t nmod T kn h omig o el p l d t h pi ai ei fg t n n ci l. a igtefr n fac l e mi o g j o
基于Moldflow的PDA外壳注塑模浇口优化设计
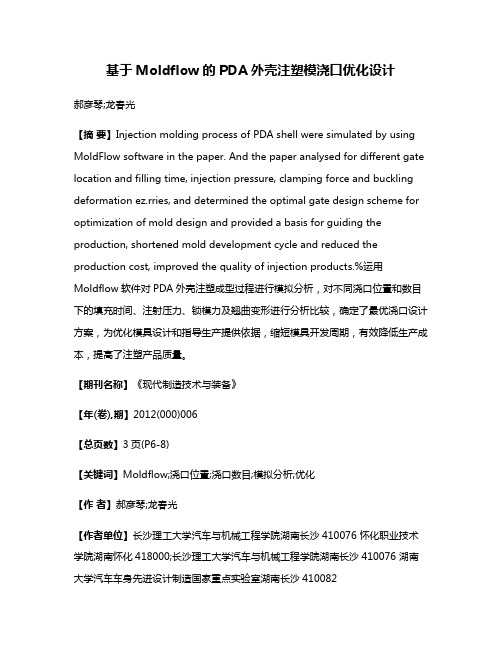
基于Moldflow的PDA外壳注塑模浇口优化设计郝彦琴;龙春光【摘要】Injection molding process of PDA shell were simulated by using MoldFlow software in the paper. And the paper analysed for different gate location and filling time, injection pressure, clamping force and buckling deformation ez.rries, and determined the optimal gate design scheme for optimization of mold design and provided a basis for guiding the production, shortened mold development cycle and reduced the production cost, improved the quality of injection products.%运用Moldflow软件对PDA外壳注塑成型过程进行模拟分析,对不同浇口位置和数目下的填充时间、注射压力、锁模力及翘曲变形进行分析比较,确定了最优浇口设计方案,为优化模具设计和指导生产提供依据,缩短模具开发周期,有效降低生产成本,提高了注塑产品质量。
【期刊名称】《现代制造技术与装备》【年(卷),期】2012(000)006【总页数】3页(P6-8)【关键词】Moldflow;浇口位置;浇口数目;模拟分析;优化【作者】郝彦琴;龙春光【作者单位】长沙理工大学汽车与机械工程学院湖南长沙410076 怀化职业技术学院湖南怀化418000;长沙理工大学汽车与机械工程学院湖南长沙410076 湖南大学汽车车身先进设计制造国家重点实验室湖南长沙410082【正文语种】中文【中图分类】TQ320.662引言浇口是熔体流进型腔的最后通道,也是浇注系统的最关键部位。
基于Moldflow的中心罩类注塑模具的优化设计
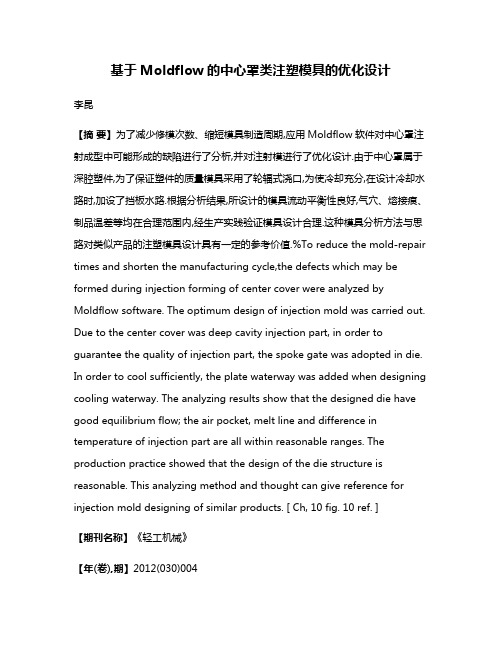
基于Moldflow的中心罩类注塑模具的优化设计李昆【摘要】为了减少修模次数、缩短模具制造周期,应用Moldflow软件对中心罩注射成型中可能形成的缺陷进行了分析,并对注射模进行了优化设计.由于中心罩属于深腔塑件,为了保证塑件的质量模具采用了轮辐式浇口,为使冷却充分,在设计冷却水路时,加设了挡板水路.根据分析结果,所设计的模具流动平衡性良好,气穴、熔接痕、制品温差等均在合理范围内,经生产实践验证模具设计合理.这种模具分析方法与思路对类似产品的注塑模具设计具有一定的参考价值.%To reduce the mold-repair times and shorten the manufacturing cycle,the defects which may be formed during injection forming of center cover were analyzed by Moldflow software. The optimum design of injection mold was carried out. Due to the center cover was deep cavity injection part, in order to guarantee the quality of injection part, the spoke gate was adopted in die. In order to cool sufficiently, the plate waterway was added when designing cooling waterway. The analyzing results show that the designed die have good equilibrium flow; the air pocket, melt line and difference in temperature of injection part are all within reasonable ranges. The production practice showed that the design of the die structure is reasonable. This analyzing method and thought can give reference for injection mold designing of similar products. [ Ch, 10 fig. 10 ref. ]【期刊名称】《轻工机械》【年(卷),期】2012(030)004【总页数】4页(P18-21)【关键词】注塑模;轮辐式浇口;Moldflow软件【作者】李昆【作者单位】东莞市讯通发展公司,广东东莞523009【正文语种】中文【中图分类】TQ320.5;TP391.90 引言Moldflow的设计分析解决方案是塑料注射成型行业中应用最广泛的软件产品。
基于Moldflow软件的注塑件浇注系统优化
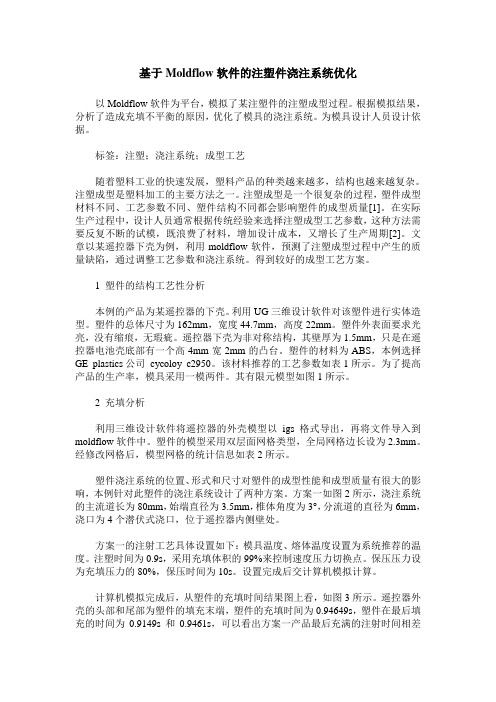
基于Moldflow软件的注塑件浇注系统优化以Moldflow软件为平台,模拟了某注塑件的注塑成型过程。
根据模拟结果,分析了造成充填不平衡的原因,优化了模具的浇注系统。
为模具设计人员设计依据。
标签:注塑;浇注系统;成型工艺随着塑料工业的快速发展,塑料产品的种类越来越多,结构也越来越复杂。
注塑成型是塑料加工的主要方法之一。
注塑成型是一个很复杂的过程,塑件成型材料不同、工艺参数不同、塑件结构不同都会影响塑件的成型质量[1]。
在实际生产过程中,设计人员通常根据传统经验来选择注塑成型工艺参数,这种方法需要反复不断的试模,既浪费了材料,增加设计成本,又增长了生产周期[2]。
文章以某遥控器下壳为例,利用moldflow软件,预测了注塑成型过程中产生的质量缺陷,通过调整工艺参数和浇注系统。
得到较好的成型工艺方案。
1 塑件的结构工艺性分析本例的产品为某遥控器的下壳。
利用UG三维设计软件对该塑件进行实体造型。
塑件的总体尺寸为162mm,宽度44.7mm,高度22mm。
塑件外表面要求光亮,没有缩痕,无瑕疵。
遥控器下壳为非对称结构,其壁厚为1.5mm,只是在遥控器电池壳底部有一个高4mm宽2mm的凸台。
塑件的材料为ABS,本例选择GE plastics公司cycoloy c2950。
该材料推荐的工艺参数如表1所示。
为了提高产品的生产率,模具采用一模两件。
其有限元模型如图1所示。
2 充填分析利用三维设计软件将遥控器的外壳模型以igs格式导出,再将文件导入到moldflow软件中。
塑件的模型采用双层面网格类型,全局网格边长设为2.3mm。
经修改网格后,模型网格的统计信息如表2所示。
塑件浇注系统的位置、形式和尺寸对塑件的成型性能和成型质量有很大的影响,本例针对此塑件的浇注系统设计了两种方案。
方案一如图2所示,浇注系统的主流道长为80mm,始端直径为3.5mm,椎体角度为3°,分流道的直径为6mm,浇口为4个潜伏式浇口,位于遥控器内侧壁处。
基于Moldflow的玩具汽车外壳注塑模设计
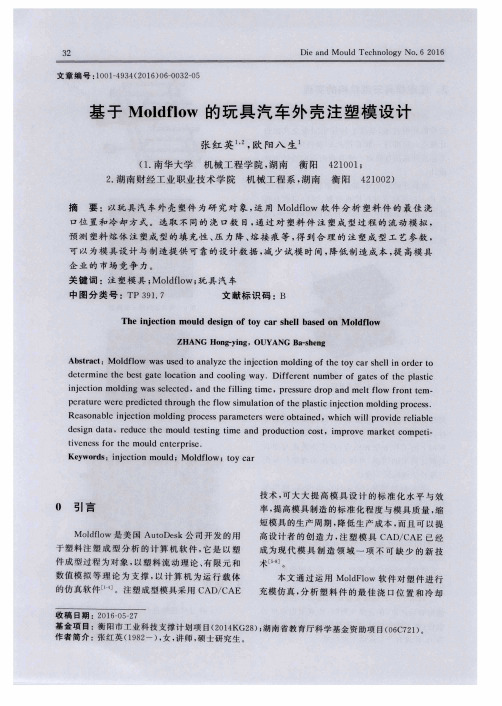
A b s t r a c t : Mo l d f l o w w a s u s e d t o a n a l y z e t h e i n j e c t i o n mo l d i n g o f t h e t o y c a r s h e l l i n o r d e r t o
d e t e r mi n e t h e b e s t g a t e l o c a t i o n a n d c o o l i n g wa y .D i f f e r e n t n u mb e r o f g a t e s o f t h e p l a s t i c
张 红 英 ~, 欧 阳 八 生
( 1 . 南华大学 机械工程学 院, 湖南 衡阳 4 2 1 0 0 1 ; 4 2 1 0 0 2 )
2 . 湖南 财 经 工 业 职业 技 术 学 院 机 械 工 程 系 , 湖 南 衡 阳
摘 要 :以玩 具 汽 车 外 壳塑 件 为研 究 对 象 , 运 用 Mo l d f l o w 软 件 分 析 塑 料 件 的 最 佳 浇
于塑料注塑 成 型分析 的计 算机 软件 , 它 是 以 塑 件成型过程为对象 , 以塑料流动 理论 、 有 限 元 和
数值模拟等 理论 为支 撑 , 以计 算 机 为 运 行 载 体
的 仿 真 软 件 。注 塑 成 型 模 具 采用 CAD / CAE
本 文 通 过 运 用 Mo l d F l o w 软 件 对 塑 件 进 行
企 业 的 市场 竞 争 力 。 关 键 词 :注 塑模 具 ; Mo l d f l o w; 玩 具 汽 车 中 图分 类 号 : T P 3 9 1 . 7 文 献 标 识 码 :B
基于Moldflow的中心罩类注塑模具的优化设计
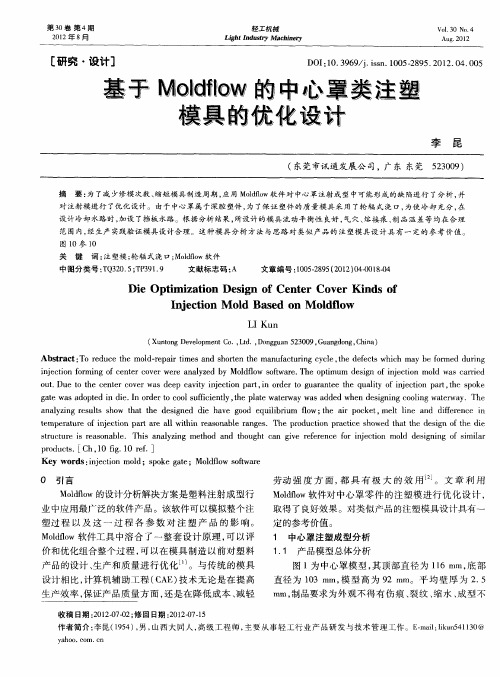
i et nf m n f etr o e w r aaye yMo f w s tae T eo t u eino jc o o a a i n ci r igo ne vr e n l db l l o w r. h pi m d s f n t nm l w sc ̄e j o o c c e z do f m g ie i d d o tD et tecne cvr a epcv yijc o ati re u rn eteq ai f net np r, eso e u. u e t oe sd e a i et np r, od r ogaa t u lyo i ci att p k oh r w t n i n t e h t j o h
基 子 Mo f w 的 中心 罩 类 洼 塑 [l do 模 具 优 设 计
李 昆
( 东莞市讯通 发展公 司,广 东 东莞
摘
5 30 ) 209
要 : 了减 少修 模 次数 、 短 模 具 制 造 周 期 , 用 Mo f w软 件 对 中心 罩 注射 成 型 中可 能形 成 的 缺 陷 进 行 了分 析 , 为 缩 应 lo d l 并
tm ea r f net np r a lwti rao a l rn e.T epou t npat eso e a ted s no ede e p r ueo jc o a r a i n e sn b gs h rd ci rc c h w dt th ei f h i t i i t e l h ea o i h g t s utr i raoa l.T i a a z g m to n hu h a i e rnefri et nmo ei igo i i r t c e s esn be hs nl i e d ad to gtcn g e r ee c o n c o l d s nn fs l r u yn h v f j i d g m a
基于Moldflow汽车配件注塑工艺参数优化

基于Moldflow汽车配件注塑工艺参数优化王善凯;李晶;胡激涛;孙晓盼;范晓健【期刊名称】《西安工程大学学报》【年(卷),期】2015(029)006【摘要】为了确定实际生产中的注塑工艺参数,降低模具设计过程中试模、修模的次数,以比亚迪汽车配件为分析对象,利用Moldflow软件对比亚迪汽车配件的注塑工艺参数进行优化.以注塑件的翘曲变形为主要指标,分析、优化注塑成型过程中的注塑温度、模具温度、充填时间、保压压力及时间等参数.最终通过实验设计,保压曲线优化及拟合等方法得到一个较优的工艺参数组合,进一步改善注塑件翘曲变形、缩短模具设计周期,降低模具设计制造成本.【总页数】6页(P692-697)【作者】王善凯;李晶;胡激涛;孙晓盼;范晓健【作者单位】西安工程大学机电工程学院,陕西西安710048;西安工程大学机电工程学院,陕西西安710048;惠州市银宝山新科技有限公司,广东惠州516000;西安工程大学机电工程学院,陕西西安710048;西安工程大学机电工程学院,陕西西安710048【正文语种】中文【中图分类】TQ320.66【相关文献】1.基于Moldflow的PUR车轮注塑工艺参数优化 [J], 吴军;蔡建臣2.基于Moldflow的输液瓶胚注塑工艺参数优化设计 [J], 孙丽丽;苏学满3.基于Moldflow与正交试验设计的汽车前格栅注塑工艺参数优化 [J], 王家涛;田梦婕;尚昌华;孟丹琦;陈旭4.基于Moldflow与均匀试验设计的汽车前格栅注塑工艺参数优化 [J], 陈旭;田梦婕;周杨;孟丹琦;王家涛5.基于响应曲面法与Moldflow的热固性塑料反应注塑工艺参数优化 [J], 凌杰;刘强;徐晓鸣因版权原因,仅展示原文概要,查看原文内容请购买。
- 1、下载文档前请自行甄别文档内容的完整性,平台不提供额外的编辑、内容补充、找答案等附加服务。
- 2、"仅部分预览"的文档,不可在线预览部分如存在完整性等问题,可反馈申请退款(可完整预览的文档不适用该条件!)。
- 3、如文档侵犯您的权益,请联系客服反馈,我们会尽快为您处理(人工客服工作时间:9:00-18:30)。
精选PPT
侧浇口的二次分析:
工艺参数设置如图所示,模具温度选择 35ºC,料温选择250ºC,填充控制选择 自动,速度/压力控制转换方式与初次 分析相同,分三次保压,保压时间为4, 12,4。提高保压压力。
19
精选PPT
20
二次分析结果比较:
初次分析:
二次分析:
精选PPT
0-0.5879
21
4
精选PPT
PP材料的简介:
比重:0.9-0.91克/立方厘米 成型收缩率:1.0-2.5% 成型 温度:160-220℃ 干燥条件
聚丙烯是继尼龙之后发展的又一优良树脂品种,它是 一种高密度、无侧链、高结晶必的线性聚合物,具有 优良的综合性能。未着色时呈白色半透明,蜡状;比 聚乙烯轻。透明度也较聚乙烯好,比聚乙烯刚硬。物 料性能 密度小,强度刚度,硬度耐热性均优于低压聚乙 烯,可在100度左右使用.具有良好的电性能和高频绝 缘性不受湿度影响,但低温时变脆,不耐模易老化. 适于 制作一般机械零件,耐腐蚀零件和绝缘零件
课题内容包括:利用CAE软件,对设计塑件进行注塑 成型过程进行充填模拟分析,根据分析结果优化浇注 系统,实现模具的优化设计。
2
精选PPT
玩具汽车外壳塑件的工艺分析:
3
精选PPT
塑件汽车外壳的工艺分析:
从图2-1分析,壁厚均匀,易于填充;汽车外壳属于 外置件,对表面质量和综合机械性能要求较高,这就 要求塑件成型后要有良好的表面光洁度和较小的形状 误差,并具有较高的强度、韧性和抗冲击能力。由于 该塑件面板处有孔,易形成熔接线和应力集中,尤其 是熔接线对塑件的外观质量和机械强度影响较大。壳 体上有销状连接体,根据一般经验,该连接销易出现 短射,而这些位置又恰好是安装位置,必须进行正常 填充。为此材料选择强度高、韧性好、易于加工成型 的热塑性高分子材料——PP。
顶出时体积收缩率:
精选PPT
0.3363-13.18
0.5285-11.95
14
凝固层厚度因子:
精选PPT
0-0.7725
0-1
15
剪切应力:
精选PPT
0-2.761
16
0-2.567
精选PPT
熔接痕:
17
精选PPT
比较分析结果:
由以上分析结果所得,侧浇口的效果明 显优于点浇口的效果。但由于汽车覆盖 件是表面件。对表面质量要求较高,所 以针对体积收缩率问题较严重,采取以 下措施;提高保压压力,保压时间,降 低模温,料温降低来提高产品的表面质 量。
精选PPT
致谢:
本次毕业设计首先非常感谢我的指导老师,导师渊博 的专业知识,严谨的治学态度,精益求精的工作作风 对我影响深远。在此表示深深地感谢。
与此同时我也感谢在场的每一位老师,希望您们能严 格审核,提出宝贵的意见。对于我来说这可能是终身 财富。
最后,我感谢\每一位教过我的老师,他们对我的关 心和教导会让我受益终身。
5
精选PPT
Moldflow分析前准备:
网格划分是任何一种CAE分析软件必不可少的前处理 工作,网格划分质量对于分析精度及分析结果有关键 性的影响。同样道理,在使用Moldflow软件进行分析 时,首先要获得高质量的网格,才能保证分析结果的 正确性与准确度。 由于各种主流3D软件之间的内核 不同及精度之间差异,使得他们的模型输出后在 Moldflow中进行网格划分时不可 避免出现自由边或 网格重叠相交及纵横比匹配率等错误。
8
精选PPT
9
浇注系统的设置:
点浇口:
侧浇口:
精选PPT
10
初次流动分析(充填时间):
点浇口:
侧浇口:
精选PPT
0-0.6188
11
0-0.5879
流动前沿温度:
精选PPT
181.5-230.5
12
203.0-230.5
缩痕指数:
精选PPT
-3.324-4.371
13
-3.788-3.613
精选PPT
0-2.567
26
0-3.986
精选PPT
熔接痕:
27
精选PPT
分析结果:
汽车覆盖件是表面制品,减少溶接痕至 关重要,通过两种浇注系统相比较,取 溶解痕较小的侧浇口形式,再通过延长 保压时间,降低模温来提高表面质量。 由上表可知,塑件的表面质量得到明显 改善。所以选取第二种方案。
28
0-0.6859
流动前沿温度:
精选PPT
203.0-230.5
175.9-210.5
Hale Waihona Puke 22缩痕指数:精选PPT
-2.789-3.613
23
-3.527-2.634
顶出时收缩率:
精选PPT
-0.5285-11.95
24
-0.8945-10.72
凝固层厚度因子:
精选PPT
0-1
0-1
25
剪切应力:
向亲爱的您们致敬!!!
29
精选PPT
基于MOLDFLOW玩具汽车 外壳注塑模 优化设计
1
作者: 指导老师:
精选PPT
课题意义:
引入CAE技术是塑料模具设计的必然发展趋势,通过 CAE模拟,可以使模具设计者尽早发现模具设计问题, 及时修改制件和模具设计,避免了传统模具设计反复 试模、修模,可有效提高制品质量,降低成本,缩短 了开发周期等。玩具车外壳注塑模具来源于生产实际, 所选塑件具有一定复杂程度,通过本设计,可使学生 初步掌握如何通过Moldflow软件对设计塑件进行注塑 成型过程模拟,并根据模拟结果优化确定模具结构。
6
精选PPT
7
精选PPT
最佳浇口位置分析:
分析前处理完毕后,首先进行最佳浇口位置的分析。 因为准备采用单个浇口进浇方式,所以不需设定浇口, 其分析结果会显示放置单个浇口的最佳位置。在设定 分析次序中选择Gate Location选项,材料为Bayer USA 公司的pp 材料,其牌号为Novodur M3FR。工艺参数 选择默认,执行分析。