PE管件注塑成型工艺优化设计
简析PE注塑管件的设计与成型工艺

简析PE注塑管件的设计与成型工艺作者:陈连成来源:《商情》2013年第24期【摘要】在我国,就最近几年的发展状况来看建筑行业在飞速发展,并成为新一代的热门行业,许多企业在陆陆续续的像一颗新星一样冉冉升起,为这个行业注入源源不断的新鲜血液,本文主要介绍了PE注塑管件在建筑行业中的应用的特点,提出了PE注塑管件系统的设计原则与其成型工艺中应考虑的问题。
【关键词】PE注塑管件设计成型工艺在我国,近几年来装修热潮不断向人们涌来,装修业也得到了很好的发展,就市场上来看,需求量不断增大的其中一个就是PE注塑管件,这个管件在现在来看缺口也是很大的,近年来不少企业纷纷投资该领域,限于各方面的因素,新投资的管件生产多集中在中小1:3径系列。
同时许多企业由于技术力量薄弱,生产的产品质量差,废品率高,严重影响企业的效益,为此本文特提出PE注塑管件的设计与成型工艺,供读者参考。
1、PE注塑管件的特点PE的中文全称就是硬质聚乙烯,这种硬质聚乙烯主要就是制成管材、管件等材料的,由于这种材料具有高抗热性、抗老化、轻度较高、不易开裂等优点,所以在人们的日常生活中也是被广泛应用的,主要是在室内外给排水、建筑给排水、燃气管、排污管等广阔的领域。
尤其是中密度聚乙烯/高密度聚乙烯(MDPE/HDPE)塑料管材上述优点更是尤为突出。
其各项技术指标均可达到国际和国家有关标准要求。
它主要有以下特点:(1)抗腐蚀性较强。
PE管主要的合成材料是惰性材料,所以这就决定了它对电流、盐分、酸和水气等电化学腐蚀具有良好的抵抗性,不易受到侵蚀,更不需要作进一步的抗酸防腐处理,这也就可以节约一些成本。
(2)使用年限长。
据国外实验室测定。
PE管的使用寿命远大于80年。
折旧成本远低于钢管。
(3)施工简便,易于运输。
小口径PE 管单管长度可进几十米甚至百米,减少了接口。
同种管径的PE管的每米重量约为钢管的l/5易于运输,施工简便,可太大降低施工费用。
(4)有较好的柔韧性。
塑料工程中的注塑成型工艺优化方法

塑料工程中的注塑成型工艺优化方法注塑成型是塑料工程中一种常用的加工方法,其优化方法对于提高产品质量、降低成本和提升生产效率至关重要。
本文将介绍塑料工程中的注塑成型工艺优化方法,帮助读者更好地理解和应用这些方法。
首先,优化注塑成型工艺的关键是选用合适的原料。
不同的塑料材料具有不同的熔化温度、流动性和收缩性等特性,因此在注塑成型之前需要根据产品要求选择合适的原料。
合适的原料能够保证产品的功能性能和外观质量,并且能够降低生产过程中的能耗和废料率。
其次,注塑成型的工艺参数调整对产品质量和生产效率都有着重要的影响。
例如,注塑温度的调整可以影响产品的缩水率和表面质量,过高或过低的温度都会导致产品瑕疵;注塑压力的调整可以控制产品的密实度和尺寸精度,过高的压力可能导致产品开裂,而过低的压力可能导致产品无法填充模腔。
因此,通过对注塑温度、注塑压力和冷却时间等参数的优化调整,可以达到最佳的成型效果。
此外,在注塑成型工艺中,模具的设计和制造也是很重要的一环。
合理的模具设计能够提高产品的质量和生产效率。
例如,增加模具的冷却系统可以加快产品的冷却速度,缩短成型周期;优化模腔和模芯的结构设计,可以减少产品的缩水率和变形。
因此,在进行注塑成型工艺优化时,需要注重模具的设计和制造,选择合适的模具材料和加工方式,以提高模具的寿命和使用效果。
此外,注塑成型过程中还应注意产品的后处理。
例如,对于高要求的产品,可以通过表面处理(如喷漆、打磨等)来提高产品的外观质量;对于某些产品,可以通过热处理或淬火等方法来改善产品的力学性能。
因此,了解并应用合适的后处理方法,可以满足不同产品的特定要求。
最后,注塑成型工艺优化还需要注重工艺参数的监控和调整。
通过对注塑机的监测和数据分析,可以实时了解工艺参数的变化和异常,及时调整以保证产品的质量和生产效率。
例如,通过定期维护注塑机,并进行设备清洁和润滑,可以减少设备故障和停机时间,提高生产效率。
总之,注塑成型工艺的优化是塑料工程中非常重要的一环。
注塑工艺参数优化

注塑工艺参数优化首先,注塑工艺参数优化的目标是实现产品质量要求。
为了达到产品质量要求,可以从以下几个方面进行优化。
1.注射速度的优化:注射速度会影响到产品充填和冷却过程,过快的注射速度会造成产品表面烧焦、翘曲等质量问题,而过慢的注射速度则会导致产品充填不完整。
因此,需要根据产品的尺寸、材料等特性,选择合适的注射速度。
2.射压的优化:射压是指注塑机在注射过程中对熔融塑料施加的压力。
过高的射压会导致产品变形,过低的射压会造成产品表面不光滑。
因此,需要进行射压的优化,找到合适的射压范围,以保证产品的质量。
3.模具温度的优化:模具温度直接影响到产品的冷却速度和收缩率。
过高的温度会导致产品收缩不当,过低的温度则会造成产品表面瑕疵。
因此,需要根据材料的熔点和产品的尺寸等因素,确定合适的模具温度。
其次,注塑工艺参数优化还需要考虑生产效率的提高。
通过合理调整工艺参数,可以提高注塑工艺的生产效率。
1.提高注射速度:合理提高注射速度可以缩短注射周期,提高生产效率。
但需要注意,注射速度过高会增加回缩和收缩的问题,需要进行合理控制。
2.提高射压:射压是保证产品充填完整的关键因素。
适当提高射压可以缩短充填时间,提高生产效率。
3.缩短冷却时间:通过调整模具温度和冷却介质的流动速度等方式,可以缩短产品的冷却时间,从而减少生产周期。
最后,注塑工艺参数优化需要通过实验和数据分析来进行。
可以通过仿真软件进行模拟实验,找到最佳的工艺参数组合。
同时,还需要对生产过程中的数据进行采集和分析,及时发现并纠正问题,以不断提高注塑工艺的稳定性和可控性。
总结起来,注塑工艺参数优化是一个综合性的工作,需要根据产品的质量要求和生产效率的要求,通过调整注射速度、射压、模具温度等参数来实现最佳的工艺状态。
这需要通过实验和数据分析来进行,并且需要不断改进和完善,以满足不断提升的生产需求。
塑料注射成型中的流道设计优化
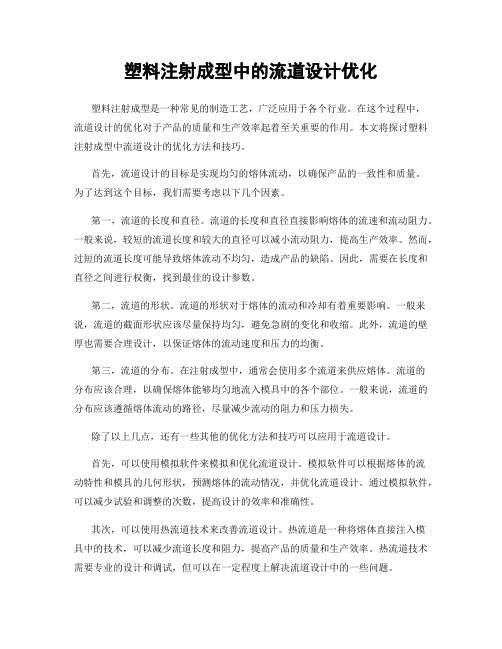
塑料注射成型中的流道设计优化塑料注射成型是一种常见的制造工艺,广泛应用于各个行业。
在这个过程中,流道设计的优化对于产品的质量和生产效率起着至关重要的作用。
本文将探讨塑料注射成型中流道设计的优化方法和技巧。
首先,流道设计的目标是实现均匀的熔体流动,以确保产品的一致性和质量。
为了达到这个目标,我们需要考虑以下几个因素。
第一,流道的长度和直径。
流道的长度和直径直接影响熔体的流速和流动阻力。
一般来说,较短的流道长度和较大的直径可以减小流动阻力,提高生产效率。
然而,过短的流道长度可能导致熔体流动不均匀,造成产品的缺陷。
因此,需要在长度和直径之间进行权衡,找到最佳的设计参数。
第二,流道的形状。
流道的形状对于熔体的流动和冷却有着重要影响。
一般来说,流道的截面形状应该尽量保持均匀,避免急剧的变化和收缩。
此外,流道的壁厚也需要合理设计,以保证熔体的流动速度和压力的均衡。
第三,流道的分布。
在注射成型中,通常会使用多个流道来供应熔体。
流道的分布应该合理,以确保熔体能够均匀地流入模具中的各个部位。
一般来说,流道的分布应该遵循熔体流动的路径,尽量减少流动的阻力和压力损失。
除了以上几点,还有一些其他的优化方法和技巧可以应用于流道设计。
首先,可以使用模拟软件来模拟和优化流道设计。
模拟软件可以根据熔体的流动特性和模具的几何形状,预测熔体的流动情况,并优化流道设计。
通过模拟软件,可以减少试验和调整的次数,提高设计的效率和准确性。
其次,可以使用热流道技术来改善流道设计。
热流道是一种将熔体直接注入模具中的技术,可以减少流道长度和阻力,提高产品的质量和生产效率。
热流道技术需要专业的设计和调试,但可以在一定程度上解决流道设计中的一些问题。
最后,流道设计的优化还需要考虑材料的选择和加工参数的调整。
不同的塑料材料具有不同的流动特性和熔体温度范围,需要根据具体情况来选择合适的材料。
此外,加工参数的调整也可以对流道设计产生影响,例如熔体温度、注射速度和压力等。
注塑成型工艺中的模具设计与优化

注塑成型工艺中的模具设计与优化一、引言随着全球化的发展和消费需求的不断增长,注塑成型工艺在生产制造中扮演着越来越重要的角色。
在注塑成型工艺中,模具设计与优化是关键环节,决定了产品质量、生产效率和生产成本。
本文将深入探讨注塑成型工艺中的模具设计与优化。
二、模具设计的基本原理1. 注塑成型工艺的基本流程注塑成型工艺是将熔化的塑料料施加于一定压力下充填到模具腔道中,经冷却硬化得到所需产品的过程。
基本流程包括注塑机料斗→注射装置→模具→冷却→开模→脱模→修整,所以模具的设计与优化必须充分考虑每个环节。
2. 模具设计的原则(1)合理的结构设计:模具结构应合理布局,便于加工和组装,以提高生产效率。
同时,需要考虑模具在使用过程中的稳定性和耐用性。
(2)充分考虑产品特性:模具设计时要充分考虑产品的特性,例如产品形状、尺寸、材料等,以确保产品的质量和性能。
(3)考虑冷却系统:冷却系统是模具设计的关键,直接影响产品的成型质量和生产效率。
冷却系统应具备良好的冷却效果,确保产品均匀冷却,并减少生产周期。
三、模具设计的优化方法1. 充分了解材料特性模具的设计与优化首先要充分了解材料的特性,包括熔点、流动性、尺寸稳定性等,以便在设计过程中选择合适的材料,并做出相应的调整和优化。
2. 仿真技术的应用利用计算机辅助设计(CAD)和计算机辅助工程(CAE)技术,进行模具设计的仿真分析。
通过仿真,可以模拟产品的充填、冷却和开模等过程,优化模具的结构和尺寸,提高产品的质量和生产效率。
3. 模具设计的标准化模具设计的标准化是改善模具设计质量和效率的重要手段。
建立规范化的设计流程和标准,提高设计效率和一致性,并减少设计的错误和修正。
四、模具设计的实践案例以汽车零部件为例,介绍一个模具设计的实践案例,以展示模具设计与优化的重要性。
汽车零部件的模具设计需要考虑到产品的形状复杂、尺寸精度高等特点。
在该案例中,设计团队利用CAD和CAE技术对模具进行了三维建模和仿真分析。
塑料注塑成型中的模具设计与优化
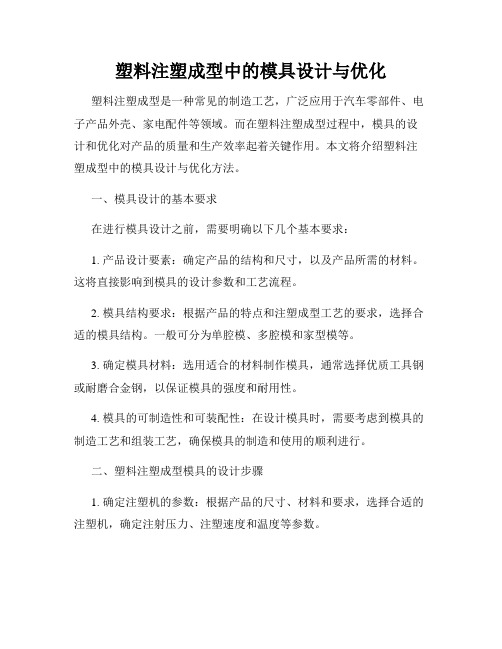
塑料注塑成型中的模具设计与优化塑料注塑成型是一种常见的制造工艺,广泛应用于汽车零部件、电子产品外壳、家电配件等领域。
而在塑料注塑成型过程中,模具的设计和优化对产品的质量和生产效率起着关键作用。
本文将介绍塑料注塑成型中的模具设计与优化方法。
一、模具设计的基本要求在进行模具设计之前,需要明确以下几个基本要求:1. 产品设计要素:确定产品的结构和尺寸,以及产品所需的材料。
这将直接影响到模具的设计参数和工艺流程。
2. 模具结构要求:根据产品的特点和注塑成型工艺的要求,选择合适的模具结构。
一般可分为单腔模、多腔模和家型模等。
3. 确定模具材料:选用适合的材料制作模具,通常选择优质工具钢或耐磨合金钢,以保证模具的强度和耐用性。
4. 模具的可制造性和可装配性:在设计模具时,需要考虑到模具的制造工艺和组装工艺,确保模具的制造和使用的顺利进行。
二、塑料注塑成型模具的设计步骤1. 确定注塑机的参数:根据产品的尺寸、材料和要求,选择合适的注塑机,确定注射压力、注塑速度和温度等参数。
2. 模具整体结构设计:根据产品的结构和尺寸,设计模具的整体结构,包括模具的型腔、型芯、导向机构等,并保证模具的生产效率和质量要求。
3. 流道系统设计:流道系统是模具中传递熔融塑料的管道系统,需要根据产品的结构和注塑工艺的要求进行设计,确保熔融塑料能够顺利注入模腔中。
4. 冷却系统设计:冷却系统是模具中的关键部分,可以通过冷却系统的设计合理调节模具温度,确保产品的质量和生产效率。
一般采用水冷却方式,需要在模具设计中合理布置冷却水路。
5. 塑料料斗和顶出机构设计:根据注塑成型的要求,设计合适的塑料料斗和顶出机构,以保证熔融塑料能够顺利注塑和产品能够从模具中顺利脱模。
三、模具设计的优化方法在塑料注塑成型过程中,模具设计的优化可以提高产品的质量和生产效率,降低生产成本。
以下是一些常用的模具设计优化方法:1. 流道长度和直径优化:流道的长度和直径对产品的注塑过程有着重要影响,应根据产品的尺寸和注塑机的要求进行合理设计,以减少产品的缩水和留痕。
聚乙烯塑料管道的优化设计

计过 程 中遇到 的二个 问题 ,就是 聚 乙烯 塑料 管道 的加 固工 作 不 到位 。因为 聚乙烯 塑料具 有硬 度较低 的特 性, 因此 在遇 到 尖 锐物 的碰撞 时很 容易发 生破裂 ,这样 一来就 会 导致管 内物 体 发生 泄漏 ,产 生极 大的危 害。 聚乙烯管 道优 化设计 过程 中 遇到 的第三个 问题,就是 聚乙烯塑料管道 的材料利 用率较低 。 聚 乙烯 塑料 管道在 生产过 程 中会遇到 材料 浪费 的现象 ,这对 于 提升 产 品质量 ,提 高产 量具 有极 大的 阻碍 。因此 ,必 须要 提 高聚乙烯 塑料管道的材料利用率 。 2 解决聚 乙烯管道优化设计 工作 中遇到问题的方法
Op t i mu m De s i g n o f Po l y e t h y l e n e P l a s t i c Pi p e l i n e
Ze n g Gua n g- yu e
Ab s t r a c t: P o l y e t h y l e n e a s a n i mp o r t a n t p e t r o c h e mi c a l r a w ma t e r i a l s ,i t s a p p l i c a t i o n r a n g e i s v e r y wi d e ,l a r g e t o t h e a r c h i t e c t u r a l d e s i g n, s ma l l p l a s t i c p i p e ma n u f a c ur t i n g wi l l b e u s e d i n p o l y e t h y l e n e p l a s t i c ma t e r i a 1 . T h e u s e o f p o l y e t h y l e n e p l a s t i c p i p e n o t o n l y
PE管件注塑成型工艺优化设计

A 的较好水平为 A3、因素 B 的较好水平为 B2、因素 D 的较好水平为 D1、因素 E 的较好水平为 E1、因素 F 的较好水平为 F2, 它们变化的趋如图 3所示, D E 交互作用虽然不显著, 但也有一定影响, 可用二元 表算出 D 和 E 在各种水平组合下的平均结果, 如表 4所示。由表 4可知, D1E1值最小, 故该搭配使得变 形最小, 即 A、B、C、D、E、F 的最佳组合为 A3 B2 C2 D 1 E1 F2。
本试验为多因素正交试验, 各因素、因素之间的 交互作用和误差对试验指标的影响通过其相应的离
差平方和来表示, 各离差平方和中独立数据的个数 仍用相应的自由度表示。方差分析见表 3。
表 3中 e表示误差, e 为 C、F、e之和, 表中各均 方差是为了消除数据个数对离差平方和的影响, 采 用平均离差平方和 Sj2 /f j ( j取各因素 ) 来进行比较, F 反应因素水平的改变对指标的影响与试验误差对 指标的影响之间的关系, 在一些假定条件下, 可以证 明 F j服从自由度为 ( f j, f e )的 F 分布, 对于给定的显 著水平 , 查 F 分布可得一临界值 F ( fj, fe ), 从而判 定在 水平下因素 j对指标的影响是否显著。在显 著性方差表中, 误差的平方和记为 S2e, 用 所有空列 的离差平方和之和来估计, 因 S2C、SD2 E较小, 将三者 合并为 S2e , 据此求得的 Fj如表 3所示。查 F0. 05 ( f j, fe ) 及 F0. 01 ( fj, f e ) 可知 F 值的临界值如表 3所示。 表中显著性一栏内, 对于 = 0. 05, 检验结果显著则 标以记号 * , 若对 = 0. 01, 若显著则标以 记号
注塑成型工艺优化技术(余成根)

注塑成型工艺优化技术(余成根)注塑成型工艺优化技术(余成根)“调机就是浪费,调机就是犯罪”,越来越多的注塑工作者已经意识到优化注塑工艺参数的重要性和紧迫性。
如果注塑工艺条件设定得不合理,就会造成注塑生产过程中出现不良率高、料耗大、效率低、模具故障多及胶件质量不稳定等一系列问题,严重的会出现粘模、顶白、翘曲变形、内应力开裂、尺寸变化大、批量报废或退货等现象。
学习“注塑成型工艺优化技术”,掌握优化注塑工艺条件的方法,实行科学注塑,是每一个注塑工作者追求的目标;长期以来,很多注塑工作者对每个注塑工艺参数的作用、设定依据及调机顺序搞不清楚,不但造成盲目调机时间长、原料浪费大、生产成本高,而且工艺条件和产品质量很不稳定。
“注塑成型工艺优化技术”培训课程是专为深入学习科学调机方法和优化注塑工艺参数,欲快速提高注塑工艺技术水平、减少盲目调机的注塑技术/管理人员而开设的。
培训内容1、注塑成型工艺参数的五要素2、注塑成型工艺的真正作用3、设定注塑工艺参数的条件4、设定注塑工艺参数的正确顺序5、料筒温度的作用、设定与优化6、注塑成型工艺窗口的确定与优化7、喷嘴温度的作用、设定与优化8、螺杆转速的作用、设定与优化9、背压的作用、设定与优化10、缓冲垫(残留量)的作用、设定与优化11、倒索(抽胶)的作用、设定与优化12、熔胶终点位置(射胶量)的确定与优化13、射胶各段位置的设定与优化14、模温的作用、设定与优化15、注塑速度的作用、设定与优化16、注射压力的作用、设定与优化17、保压的作用及前提条件18、保压切换位置的确定与优化19、保压压力的确定与优化20、保压时间的确定与优化21、保压曲线的分析与解读22、锁模力的作用、设定与优化23、注射时间的设定与优化24、冷却时间的确定与优化25、新模初始调机的方法与技巧26、几种特殊的注塑成型方。
PE注塑管件的设计与成型工艺探讨

企业 的 效益 , 此本 文 特 提 出 P 注塑 管 件 的设 计 与 成 型工 艺 , 读 为 E 供 者参 考 。
1 E 注 塑 管 件 的 特 点 P
3 P 注 塑 管 件 的 设 计 原 则 与 思 路 E
注 塑 管 件 的 设 计 主 要 是 根 据 制 品 的 结 构 来 确 定 , 浇 注 系 统 的 设
计 也是 根 据注 塑 模具 的结 构进 行设 计 。设 计 原 则与 思路 的改 进是 提
P 是 硬 质 聚 乙 烯 的 简 称 , 品 主 要 有 管 材 、 材 及 其 管 件 等 . 高 P 管 件 制 品 性 能 的 一 条 重 要 途 径 。 P 注 塑 管 件 系 统 一 般 是 由 主 E 制 型 E E 可 广 泛 应 用 于 室 内 外 给 排 水 、 筑 给 排 水 、 气 管 、 污 管 等 广 阔 的 浇 道 、 浇 道 、 口、 料 穴 等组 成 , 则 上流 道 的 长度 应 尽 量短 , 建 燃 排 分 浇 冷 原 以 领 域 。 尤 其 是 中 密 度 聚 乙 烯 /高 密 度 聚 乙 烯 ( P H P ) 料 管 材 利 于 保 证 在 管 件 注 塑 过 程 中 的 顺 利 填 充 和 补 缩 。 时 在 能 保 证 冷 却 MD E/ D E 塑 同 具 有 耐 热 、 老 化 、 械 强 度 高 、 环 境 应 力 开 裂 性 、 蠕 变 性 能 好 、 脱 模 的 基 础 上 浇 道 直 径 应 尽 量 大 。浇 注 系 统 尺 寸 设 计 。 据 经 验 , E 耐 机 耐 抗 根 P 韧 性 刚 度 适 当 等 特 出 优 点 。 各 项 技 术 指 标 均 可 达 到 国 际 和 国 家 有 注 塑 管 件 模 具 浇 注 系 统 的 设 计 比 较 适 合 采 用 主 浇 道 直 接 进 料 方 式 。 其 关 标 准 要 求 。它 主 要 有 以 下 特 点 :1 抗 腐 蚀 性 。P 管 由惰 性 材 料 台 主 浇 道 长 度 的 设 计 要 尽 量 短 。 在 新 时 期 , 保 证 注 塑 模 具 有 较 高 的 () E 为 成 , 诸 如 电 流 . 壤 中 的 盐 分 , 和 水 气 等 电 化 学 腐 蚀 具 有 良好 的 成 型 精 度 。 了 利用 高精 度 的 机加 工手 段 完 成 钢 模 的制 造 外 , 模 对 土 酸 除 在 抗 腐 蚀 性 , 须 做 任 何 防 腐 处 理 , 可 使 用 并 节 约 投 资 。 (1 命 长 。 具 结 构 的 合 理 性 设 计 、 射 流 道 平 衡 设 计 、 却 水 道 高 效 化 设 计 等 无 即 2寿 注 冷 据 国外 实验 室 测定 .E管 的使 用寿 命 远大 于 8 P 0年 。 旧 成 本 远 低 于 方 面 已 经 大 量 应 用 利 用 计 算 机 软 件 、 速 成 形 等 先 进 技 术 , 精 密 折 快 在 钢 管 。( ) 工 简 便 , 于 运 输 。小 口 径 P 3施 易 E管 单 管 长 度 可 进 几 十 米 甚 注 魍 理 论 的 基 础 上 改 进 传 统 注 塑 模 设 计 与 制 造 过 程 。 至 百 米 , 少 了 接 口 。 种 管 径 的 P 管 的 每 米 重 量 约 为 钢 管 的 l5 减 同 E / 4 P 注 塑 管 件 的 成 型 工 艺 E
PE注射成型课程设计

题目:PE注塑成型工艺设计学院:化学化工学院专业:高分子材料与工程班级: 0801学号:200806190102学生姓名:唐杰导师姓名:黄先威刘拥君刘艳丽禹新良完成日期: 2011年 7 月 2日课程设计任务书学院:化学化工学院专业:高分子材料与工程班级:0801 姓名:唐杰同组人员姓名:唐文军刘卫唐尧张磊邓锋指导教师:黄先威刘拥君刘艳丽禹新良教研室主任:黄先威教学副院长:陈建芳2011 年6 月17 日目录1实验目的……………………………………………………………………………2实验原理……………………………………………………………………………2.1聚乙烯特点……………………………………………………………………2.2聚乙烯的成型加工性能………………………………………………………2.3聚乙烯的主要成型条件………………………………………………………3实验步骤……………………………………………………………………………4实验数据与分析……………………………………………………………………4.1 PE拉伸样条的工艺参数………………………………………………………4.2PE扁平试样的注塑工艺参数…………………………………………………4.3制品图像………………………………………………………………………4.4数据分析…………………………………………………………………………………PE注射成型工艺设计1实验目的1.1解塑料熔体流动速率(MFR)的概念,熟悉其测定原理及操作。
1.2了解螺杆式注塑机的结构、性能参数、操作规程及注塑工艺参数的设定及整,掌握注塑机的基本操作技能。
1.3解塑料冲击性能的测试原理、制样方法及操作。
2实验原理:注射机的工作原理与打针用的注射器相似,它是借助螺杆(或柱塞)的推力,将已塑化好的熔融状态(即黏流态)的塑料注射入闭合好的模腔内,经固化定型后取得制品的工艺过程。
注射成型是一个循环的过程,每一周期主要包括:定量加料──熔融塑化──施压注射──冲模冷却──启模取件。
PE注塑工艺设计和拉伸性能实验设计

专业方向课程设计题目: PE注塑工艺设计及其拉伸性能学院:化学化工学院专业:高分子材料与工程班级: xxxx学号:xxxxxx 学生: xxxx 导师: xx xx 方xx 禹xx完成日期: xxxxxxxxx课程设计任务书学院:化学化工学院专业:高分子材料与工程班级:xxxxx : xxxxx 同组人员: xxxxx指导教师:xxxxxx教研室主任: xxx教学副院长: xxx2016 年 6 月 15 日目录1 引言 (3)一、聚乙烯PE的成型加工性能 (3)1、聚乙烯PE的成型加工性能: (3)2、PE的主要成型条件: (4)3、工艺特性: (5)4、制品与模具: (5)5、成形工艺: (6)二、注塑机的工作原理 (6)1、工艺流程 (6)2、工艺参数 (8)三、拉伸的测定实验原理 (10)2 实验部分 (12)一、注塑实验 (12)二、拉伸实验 (14)3 结论 (15)4 参考文献 (20)1 引言一、聚乙烯PE的成型加工性能1、聚乙烯PE的成型加工性能:PE为结晶性原料,吸湿性极小,不超过0.01%,因此在加工前无需进行干燥处理。
PE分子联链柔性好,键间作用力小,熔体粘性低,流动性极好,因此成型时无需太高压力就能成型出薄壁长流程制品。
PE的收缩率围大,收缩值大,方向性明显,LDPE收缩率为1.22%左右,HDPE收缩率在1.5%左右。
因此容易变形翘曲,模具冷却条件对收缩率的影响很大,故应该控制好模具温度,保持冷却均匀、稳定。
PE的结晶能力高,模具的温度对塑件的结晶状况有很较大的影响。
模温高,熔体冷却慢,塑件结晶度高,强度也就高。
PE的熔点不高,但比热容较大,因此塑化时仍需要消耗较多的热量,故要求塑化装置要有较大的加热功率,以便提高生产效率。
PE的软化温度围较小,且熔体易氧化,因此在成型加工中应尽可能避免熔体与氧发生接触,以免降低塑件质量。
PE制件质地较软,且易脱模,因此当塑件有浅侧凹槽时可以强力脱模。
注塑工艺优化方案

注塑工艺优化方案注塑工艺优化方案注塑工艺是一种常见的制造工艺,广泛应用于各个行业的产品制造过程中。
然而,注塑工艺的优化对于提高产品质量、降低成本、提高生产效率至关重要。
在本文中,我们将介绍一种注塑工艺的优化方案,以帮助企业提升其制造过程的效率和质量。
首先,注塑工艺的优化需要从材料选择开始。
选择合适的塑料材料对于产品的质量和性能至关重要。
在选择材料时,需要考虑到产品的用途、使用环境、力学性能等因素。
同时,还要考虑材料的成本和可供性。
通过选择合适的材料,可以有效地提高产品的质量和性能。
其次,注塑工艺的优化还需要考虑模具设计。
模具的设计对于产品的成型质量和生产效率有着重要的影响。
在模具设计中,需要考虑到产品的结构、形状、尺寸等因素。
同时,还要考虑到模具的制造工艺、使用寿命等因素。
通过合理的模具设计,可以提高产品的成型质量,减少模具的损耗和维护成本。
另外,注塑工艺的优化还需要注重生产过程的控制。
在注塑过程中,需要控制好注塑机的温度、压力、注射速度等参数,以保证产品的成型质量。
同时,还需要进行合理的工艺调整和优化,以提高生产效率和降低生产成本。
通过合理的生产过程控制,可以有效地提高产品的质量和生产效率。
最后,注塑工艺的优化还需要注重质量控制。
通过建立完善的质量控制体系,可以及时发现和纠正生产过程中的问题。
同时,还可以通过统计分析和数据挖掘等手段,对生产过程进行监控和分析,以提供合理的改进措施。
通过有效的质量控制,可以提高产品的质量稳定性和一致性。
综上所述,注塑工艺的优化是一个复杂而综合的过程。
需要从材料选择、模具设计、生产过程控制和质量控制等方面进行综合考虑。
通过合理的优化方案,可以提高产品的质量和性能,降低生产成本,提高生产效率。
因此,企业在注塑工艺中应加强优化方案的研究和实施,以提升其在市场竞争中的竞争力。
注塑成型加工工艺的优化
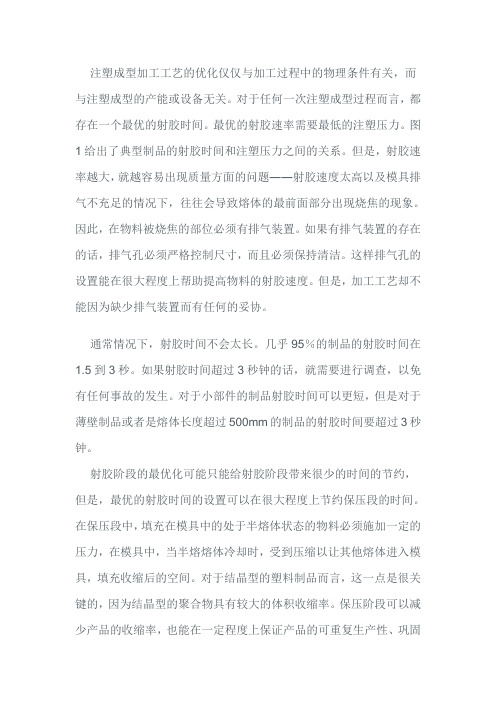
注塑成型加工工艺的优化仅仅与加工过程中的物理条件有关,而与注塑成型的产能或设备无关。
对于任何一次注塑成型过程而言,都存在一个最优的射胶时间。
最优的射胶速率需要最低的注塑压力。
图1给出了典型制品的射胶时间和注塑压力之间的关系。
但是,射胶速率越大,就越容易出现质量方面的问题――射胶速度太高以及模具排气不充足的情况下,往往会导致熔体的最前面部分出现烧焦的现象。
因此,在物料被烧焦的部位必须有排气装置。
如果有排气装置的存在的话,排气孔必须严格控制尺寸,而且必须保持清洁。
这样排气孔的设置能在很大程度上帮助提高物料的射胶速度。
但是,加工工艺却不能因为缺少排气装置而有任何的妥协。
通常情况下,射胶时间不会太长。
几乎95%的制品的射胶时间在1.5到3秒。
如果射胶时间超过3秒钟的话,就需要进行调查,以免有任何事故的发生。
对于小部件的制品射胶时间可以更短,但是对于薄壁制品或者是熔体长度超过500mm的制品的射胶时间要超过3秒钟。
射胶阶段的最优化可能只能给射胶阶段带来很少的时间的节约,但是,最优的射胶时间的设置可以在很大程度上节约保压段的时间。
在保压段中,填充在模具中的处于半熔体状态的物料必须施加一定的压力,在模具中,当半熔熔体冷却时,受到压缩以让其他熔体进入模具,填充收缩后的空间。
对于结晶型的塑料制品而言,这一点是很关键的,因为结晶型的聚合物具有较大的体积收缩率。
保压阶段可以减少产品的收缩率,也能在一定程度上保证产品的可重复生产性、巩固产品的焊接以及改善产品的表面光泽度。
射胶胶口的尺寸必须合理以保证进行合理的保压。
胶口的冷却将取决于保压阶段所用的时间。
制品的冷却时间取决于制品的壁厚以及聚合物的类型。
这一点是很容易确定的,可以直接从数据表格中查到效应的数据或者可以通过利用CAE软件来做精确的确定。
在通常情况下,保压时间大概是冷却时间的80%,一般情况下,冷却时间要比设定的时间短。
冷却的速率与温度和时间之间存在这一个指数关系。
塑料制品生产中的注塑工艺的研究与优化方案

塑料制品生产中的注塑工艺的研究与优化方案注塑工艺是目前塑料制品生产中最常用的一种方法。
它通过将熔融的塑料材料注入到模具中,经过冷却和固化后,得到所需的塑料制品。
注塑工艺具有高效、成本低、生产规模大等优点,因此广泛应用于各个领域。
然而,在注塑工艺中存在着一些问题,如产品质量不稳定、生产效率低、能耗高等,为了解决这些问题,需要进行注塑工艺的研究与优化。
首先,注塑工艺的研究与优化需要从原材料的选择和准备开始。
不同的塑料材料具有不同的熔体流动特性和收缩率,因此需要根据产品的要求选择合适的塑料材料。
此外,还需要对原料进行配方和熔融处理,以确保材料的熔融质量和稳定性。
通过控制原材料的质量和熔融过程的参数,可以有效提高注塑工艺的稳定性和产品的一致性。
其次,注塑工艺的研究与优化还包括模具设计和加热冷却系统的优化。
模具是注塑工艺中的关键因素之一,合理的模具设计可以提高产品的质量和产量。
通过优化模具的结构和流道设计,可以改善塑料在模具中的流动性和充填性,减少产品的缺陷。
同时,加热冷却系统的优化可以提高模具的生命周期和注塑的效率。
通过合理安排加热和冷却系统的位置和参数,可以有效控制塑料的熔融和固化过程,提高产品的尺寸精度和表面质量。
另外,注塑工艺的研究与优化还需要注重生产过程中的控制和监测。
通过采用先进的注塑设备和自动控制系统,可以实时监测和调整注塑过程中的温度、压力、流量等参数,保证产品的质量稳定。
同时,还可以利用质量反馈和数据分析技术,对生产过程进行持续改进和优化,提高生产效率和产品质量。
除了以上的技术优化,还可以通过改变工艺方法和模具结构,进行进一步的优化。
例如,可以采用多腔模具或叠层注塑技术,提高生产效率和产品的一致性。
同时,还可以应用先进的模具材料和涂层技术,减少注塑过程中的磨损和摩擦,延长模具的使用寿命。
总之,塑料制品生产中的注塑工艺的研究与优化是提高产品质量和生产效率的关键。
通过合理选择原材料、优化模具设计和加热冷却系统、控制和监测生产过程,以及改变工艺方法和模具结构,可以有效解决注塑工艺中存在的问题,提高产品的质量稳定和生产效率,推动塑料制品行业的发展。
注塑成型工艺的优化及其应用研究

注塑成型工艺的优化及其应用研究一、前言注塑成型工艺是一种广泛应用于制造业的成型技术,其在消费品、电子产品、汽车零部件等领域都有着不可替代的地位。
然而,注塑成型工艺的优化仍然是一个研究热点。
本文将从工艺优化方法、应用领域、未来趋势等方面探讨注塑成型工艺的优化及其应用研究。
二、工艺优化方法1.模具设计优化模具是注塑成型工艺中不可或缺的组成部分,其设计合理与否直接影响成型产品质量和生产效率。
因此,模具设计优化是注塑成型工艺优化的重要手段。
包括以下几个方面:(1)模具结构设计优化模具结构设计应考虑如何更好地满足产品质量、生产效率和模具寿命等要求。
在模具结构设计中,应合理安排模腔、模芯、排气道等组成部分。
(2)模具材料选择优化模具材料是影响模具寿命和生产效率的重要因素。
合适的模具材料可以有效提高模具的使用寿命和生产效率。
(3)模具加工工艺优化模具加工工艺的优化可以有效提高模具加工质量和加工效率,从而提高注塑成型的生产效率和产品质量。
2.注塑工艺参数优化注塑工艺参数对成型产品的尺寸精度、表面质量、生产率等方面都有着重要影响。
因此,注塑工艺参数优化也是注塑成型工艺优化的重要手段。
工艺参数优化主要包括:(1)注塑温度的优化注塑温度是影响成型产品表面质量和性能的重要因素,因此,优化注塑温度可以有效提高成型产品的品质。
(2)保压时间的优化保压时间对成型产品的尺寸精度和表面质量有着重要影响。
因此,保压时间的优化也是注塑成型工艺优化的重要环节。
(3)注塑压力的优化注塑压力是影响成型产品材料流动和充填性能的重要因素。
优化注塑压力可以提高生产效率和产品的表面质量。
三、应用领域注塑成型工艺的应用领域涵盖非常广泛,主要应用于以下几个方面:1.消费品制造消费品制造包括电器、食品、化妆品、家居用品等行业。
注塑成型技术可以生产各种大小形状的产品,从而能够满足此类行业对于产品外观、性能、尺寸等要求。
2.汽车零部件制造汽车零部件制造是注塑成型应用的重要领域。
塑料注塑工艺流程优化分析

塑料注塑工艺流程优化分析注塑工艺是塑料制品生产过程中的重要环节,它直接关系到产品的质量和生产效率。
优化注塑工艺流程,可以提高产品的性能和稳定性,降低生产成本。
本文将围绕塑料注塑工艺流程的优化进行分析,并提出一些实用的优化方案。
一、注塑工艺流程简介塑料注塑工艺是将熔化的塑料通过注射机注入到模具中,经过一系列的流动、冷却、封闭、固化等工序,最终得到所需的塑料制品。
注塑工艺流程包括以下几个主要环节:1. 模具设计:根据产品的形状、尺寸和结构要求,设计出合适的模具,确保产品的精度和一致性。
2. 塑料材料选择:根据产品的用途和性能需求,选择合适的塑料材料,如聚丙烯(PP)、聚乙烯(PE)等。
3. 塑料熔化:将选定的塑料颗粒放入注射机的料斗中,通过加热和搅拌,使其完全熔化成为可注射状态的熔体。
4. 注射过程:将熔融的塑料注入到模具的腔室中,保持一定的注射压力和速度,填充整个腔室,形成塑料制品的初步形状。
5. 冷却和固化:在注射完成后,通过冷却系统将模具中的熔体迅速冷却,使其变硬,并具有一定的强度。
6. 脱模:当塑料制品固化后,打开模具,取出成品,完成整个注塑工艺流程。
二、注塑工艺流程存在的问题在实际生产中,注塑工艺流程存在一些问题,主要包括以下几个方面:1. 注射压力不稳定:注射过程中,由于注射机的设定问题或注射系统的故障,注射压力不稳定,导致制品的外观质量不佳,如翘曲、色差等。
2. 注塑周期长:注塑周期是指一次注射加模具脱模的时间,周期越长,生产效率越低。
影响注塑周期的因素包括注射速度、冷却时间等。
3. 成品的尺寸不稳定:受到注射压力和冷却时间等因素的影响,塑料制品的尺寸可能存在一定的浮动,不符合产品的设计要求。
三、注塑工艺流程优化方案为了解决上述问题,可以采取以下优化方案:1. 确定合理的注射参数:通过试验和实际生产验证,确定合理的注射参数,包括注射速度、注射压力、保压时间等。
合理的注射参数可以保证制品的充填性能和质量。
如何优化注塑成型生产

如何优化注塑成型生产注塑成型生产是现代工业生产中常见的一种生产工艺,优化注塑成型生产可以提高生产效率和产品质量。
以下是几种优化注塑成型生产的方法:1.优化原材料选择:-选择合适的原材料,根据产品要求选择适合的塑料类型和牌号,确保原材料质量稳定,避免出现不均匀溶解、熔断、气泡等问题。
-避免回料使用过多,回料使用过多可能会影响产品的物理性能和外观质量。
-进行材料配方优化,通过调整不同原料的比例,可以提高产品的性能和成本效益。
2.优化模具设计和制造:- 设计合理的注塑模具,减少产品缺陷的可能性。
合理设计产品形状、壁厚、流道等参数,防止模具内部出现气泡、短-shot等问题。
-优化模具材质,选择高强度、高耐磨、高导热的材料,延长模具寿命,减少维护与更换的频率。
-使用先进的模具加工设备,如CNC机床、电火花等,提高模具制造的精度和效率。
3.优化注塑工艺参数:-合理设置注塑机的温度、压力、速度等参数,以保证塑料的熔融、流动、充实和冷却等过程的顺利进行,避免产品缺陷的产生。
-优化冷却系统,确保注塑件在注射后能迅速降温固化,快速脱模,提高生产效率。
-确定合适的注射时间和保压时间,以提高产品的密实性和抗拉强度。
4.优化生产管理:-采用先进的生产管理系统,对注塑成型生产过程进行实时监控和数据分析,及时发现问题和异常,进行调整和改进。
-通过对生产设备的定期维护和保养,保证设备的正常运转和稳定性,减少生产故障和停机时间。
-建立完善的质量管理体系,通过严格的质量控制和检验,确保产品的质量稳定,减少次品率。
-增强员工的培训和技能提升,提高操作人员的技术水平,增强团队协作能力和问题解决能力。
5.推广绿色生产:-推广节能、环保的注塑成型生产工艺和设备,减少资源消耗和排放,降低对环境的污染。
-优化产品设计,减少使用材料和能源的数量,降低产品的包装和运输成本。
-建立可持续发展的生产模式,鼓励循环再利用和废弃物的再处理,减少对自然环境的负面影响。
聚丙烯注塑成型条件的优化
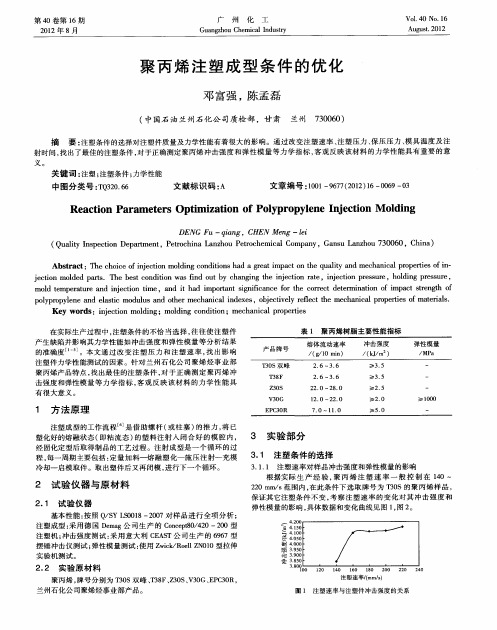
关键 词 : ; 注塑 注塑条件; 力学性能
中图分 类号 :Q 2.6 T 306
文献标 识码 : A
文章编 号 :0 1 97 (02 1 - 09 0 1 — 67 21 )6 06 — 3 0
R at n P r meesOpi z t no oy r p ln net nModn e ci a a tr t ai fP lp o ye eIjci lig o mi o o
DEN G Fu —q a g, CHEN e g —li in M n e
( ulyIset nD p r e t P t c iaL nh uP t ce ia C m a y a s a zo 3 0 0 C ia Q a t npci eat n , e ohn azo e oh m cl o p n ,G nu L nhu7 0 6 , hn ) i o m r r
Ke o d :net n m lig od gcn io ; c a i rp re yw r s i c o o n ;m li o dt n meh nc po e is j i d n i l a t
在实际生产过程 中, 注塑条件 的不恰 当选 择 , 往往使 注塑件 产生缺陷并影响其力学性能如 冲击 强度和弹性模 量等分 析结果 的准确度 。J 。本文 通过 改变 注塑 压力 和注 塑速 率 , 出影 响 找 注塑件力学性能测试 的因素 。针对 兰州石化公 司聚烯烃 事业部 聚丙烯产 品特点 , 找出最佳的注塑条件 , 对于正确 测定 聚丙烯 冲 击强度 和弹性模 量等 力学指 标 , 客观反 映该材 料 的力学性 能具
jc o oddpr .T ebs cn io a n u yca g gtei et nrt, net npesr,hli rs r , et nm le at h et o d i w s dot hn i jc o a i c o r ue o n pes e i s tn i f b n h n i e j i s dg u m l m e tr ad i et nt e n t a m o a t i ic c o ecr c d t m n t no pc s eg f o t p r ue n jc o m ,ad i hd i pr n s nf a ef t or t e r iai fi at t nt o de a n i i t g in rh e e o m r h pl rp l ea deat ouu n t r ehnc dxs ojci l rf c tem caia poe i f a r l. o poy n n l i m dls do e c aia i ee , bet e l t h ehncl rpre o t i s y e sc a h m l n v yee ts m ea
- 1、下载文档前请自行甄别文档内容的完整性,平台不提供额外的编辑、内容补充、找答案等附加服务。
- 2、"仅部分预览"的文档,不可在线预览部分如存在完整性等问题,可反馈申请退款(可完整预览的文档不适用该条件!)。
- 3、如文档侵犯您的权益,请联系客服反馈,我们会尽快为您处理(人工客服工作时间:9:00-18:30)。
3. 31 3. 30 0. 34 6. 95 5. 96 1. 81
0. 62
0. 64
不圆度 /mm
6. 70 6. 78 6. 41 6. 99 7. 00 7. 83 6. 69 6. 94 6. 43 6. 84 6. 95 7. 76 7. 41 7. 84 7. 17 8. 04 8. 01 8. 68 6. 98 7. 61 7. 05 7. 55 7. 45 8. 45 5. 81 6. 33 6. 19 6. 77 6. 5 7. 59 6. 37 6. 92 6. 97 7. 49 7. 32 8. 14 6. 34 6. 93 6. 6 7. 41 6. 67 7. 51 6. 51 7. 05 6. 55 7. 45 7. 31 8. 06 6. 23 6. 37 6. 39 6. 96 6. 69 7. 33
2
3
1
2
1
2
3
3
1
2
2
3
1 6. 36
2
3
1
2
2
3
1
1
2
3
3
1
2 6. 84
2
3
1
2
3
1
2
2
3
1
1
2
3 7. 28
3
1
3
2
1
3
2
1
3
2
1
3
2 6. 32
3
1
3
2
2
1
3
2
1
3
2
1
3 6. 54
3
1
3
2
3
2
1
3
2
1
3
2
1 6. 64
3
2
1
3
1
3
2
2
1
3
3
2
1 6. 45
3
2
1
3
2
1
3
3
2
1
1
3
2 6. 52
对于圆筒状注塑管件, 由于大分子链的柔顺性,
图 1 Y 型三通管件
当制品完全冷却时, 体积收缩和线性收缩变化较小,
产品的尺寸较稳定, 但随着内部残余应力的释放, 当 管件不足以抵抗变形时, 整个孔口沿径向因不均匀
的拉力作用而发生变形, 当某方向拉应力较大时, 整
个圆形便会向朝着与其垂直的方向发生椭圆形变。 不圆度的度量可以采用以下公式计算 [ 5 ] :
致, 我们采用三个孔口变形 的平均值来衡 量, 值越 小, 不圆度越好。将模拟分析的变形数据列于表 2。
1 定模座板; 2 管件; 3 浇口套; 4 定模板; 5 动模板; 6 复位杆; 7 动模固定板; 8 顶针板; 9 推杆固定板; 10 推板; 11 定模座板; 12 推杆; 13 抽芯机构 ; 14 型芯 ; 15 型芯冷却水路 ; 16 型腔冷却水路 ; 17 型芯 ; 18 抽芯机构 ; 19 浇注系统 图 2 Y型三通管件注塑模
很多, 而在一般设置工艺中可控制的主要工艺参数
有注射时间 ( A ) 、模具温度 ( B) 、熔体温度 ( C) 、保压
收稿日期: 2011-02-25
宋财福, 等: PE管件注塑成型工艺优化设计
45
压力 ( D) 、保压时间 ( E) 、冷却时间 ( F )等, 每个因素 水平的变化对制品质量都有一定的影响。此外, 保 压压力和保压时间的交互作用较明显, 亦不能忽略, 将它们记作 D E, 每个因素取 3个水平, 以三通管 件孔口的平均不圆度作为评价产品质量的指标, 其 因素水平设置见表 1。
不同密度 PE 的收缩率变化范围都很大 ( 低密 度 PE 收缩率在 1. 5% ~ 5. 0% 之间, 高密度 PE 在 2. 5% ~ 6. 0% 之间 ), 使得管件的区域收缩不均更 加突出。聚烯烃分子 取向导致的各向 收缩不均是 PE 管件收缩不均的原因, 而收缩不均、分子取向及 制品各处冷却速率不同又导致残余应力, 这是管件 孔口变形的直接原因 [ 3] 。一般而言, 产品结构决定 了 40% 的变形, 模具结 构及材料决定 了 30% 的变 形, 工艺 决定了 10% 的变形, 在制 品结构、模具结 构、材料确定的情况下, 只有利用科学合理的方法设 计制品成型工艺, 才能减少 PE管件孔口的变形 [ 4] 。 1 实例分析
不圆度 = 最大直径 - 最小直径
( 1)
1. 2 正交试验设计
正交试验是试验 设计 ( DOE ) 最常用的试 验方 法之一, 它以概率论及数理统计为理论基础, 依据多
因素、多水平试验中数据的正交性来设计试验, 充分
利用标准化的正交表来安排实验方案, 并对实验结 果进行计算分析, 利用它可以确定在影响产品质量
为了 计算方便, 式中不圆度数 据都已扩大 10 倍, 表中 、 、 分别为各因素在水平 1、2、3时所 对应的不圆度之和, T 为所有试验不圆度平均值的
和, R 为极差, 是不同水平下实验结果离差平方和的 差值。由表 2可以很容易地看出, 第 13号试验的数 据值最小, 对于实验来说, 评价的标准是变形越小越 好, 仅从 、 、 各水平不圆度之和来看, A、B、C、 D、E、F 的水平选择分别为 A3、B2、C2、D1、E1、F2时, 实验结果最佳, 但这只是 729个全面试验中的极少 一部分, 因此所得的结果未必就是最佳的工艺组合; 此外, R 值越大, 说明对应的因素对结果的影响程度 越大, 这个因素就越重要, 反之则表明该因素对指标 的影响小, 通常是不重要因素。根据表 2的结果, 进 行主次排序, 可得各因素对变形影响的大小依次为: D、E、A、B、F、D E、C。 2 方差分析及最佳成型工艺的确定
本试验为多因素正交试验, 各因素、因素之间的 交互作用和误差对试验指标的影响通过其相应的离
差平方和来表示, 各离差平方和中独立数据的个数 仍用相应的自由度表示。方差分析见表 3。
表 3中 e表示误差, e 为 C、F、e之和, 表中各均 方差是为了消除数据个数对离差平方和的影响, 采 用平均离差平方和 Sj2 /f j ( j取各因素 ) 来进行比较, F 反应因素水平的改变对指标的影响与试验误差对 指标的影响之间的关系, 在一些假定条件下, 可以证 明 F j服从自由度为 ( f j, f e )的 F 分布, 对于给定的显 著水平 , 查 F 分布可得一临界值 F ( fj, fe ), 从而判 定在 水平下因素 j对指标的影响是否显著。在显 著性方差表中, 误差的平方和记为 S2e, 用 所有空列 的离差平方和之和来估计, 因 S2C、SD2 E较小, 将三者 合并为 S2e , 据此求得的 Fj如表 3所示。查 F0. 05 ( f j, fe ) 及 F0. 01 ( fj, f e ) 可知 F 值的临界值如表 3所示。 表中显著性一栏内, 对于 = 0. 05, 检验结果显著则 标以记号 * , 若对 = 0. 01, 若显著则标以 记号
表 1 因素水平表
水平
注射 时间 / s
模具 温度 /
1 2. 8
30
2 3. 5
40
3 4. 3
50
熔体 温度 /
200 210 220
保压
保压
压力 /M Pa 时间 / s
20
15
27
20
35
25
冷却 时间 / s
20 30 40
( 2) 正交试验方案 本实验 6个因素都是 3水平, 而且 D、E 存在交 互作用, 因此选用 L27 ( 313 ) 正交表安排试验, 表头设 计时, 将 A、B、C、D、E、F 等因素分别排 在表的第 1 列 ~ 第 6列, 同时根据 L27 ( 313 ) 的交互列表, 将 D、E 交互列 D E 分别放在第 10列、第 12列, 正交试验 方案见表 2。 图 2为所设计的模具图, 在利用 CAE 软件进行 模拟时, 可以根据模具中相应的浇注系统和冷却系 统建模。进行模拟分析时, 对于没有列入正交表的 其它因素, 如注塑压力、注射速度等每次都确保它们 固定在稳定、良好的状态。因每个孔口的变形不一
1
3
3
3
2
2
2
1
1
1
3
3
3 7. 05
1
3
3
3
3
3
3
2
2
2
1
1
1 7. 94
2
1
2
3
1
2
3
1
2
3
1
2
3 6. 98
2
1
2
3
2
3
1
2
3
1
2
3
1 7. 21
2
1
2
3
3
1
2
3
1
2
3
1
2 7. 32
2
2
3
1
1
2
3
2
3
1
3
1
2 5. 74
2
2
3
1
2
3
1
3
1
2
1
2
3 6. 15
2
2
3
1
3
1
2
1
2
3
2
3
1 6. 43
3
2
1
3
3
2
1
1
3
2
2
1
3 7. 13
3
3
2
1
1
3
2
3
2
1
2
1
3 6. 21
3