批次需求计划LRP
BOM、LRP、MRP、MPS基本知识

bom基本概念一.基本定义材料用量清单 (Bill of Material,简称BOM) 的观念对制造业而言可说是应用十分普遍且非常便利的一项工具,特别是对于电子,电机,机械类等装配业或化学配方产品制造业尤其重要.本节将先对材料用量清单的观念,意义与应用做一简单的介绍.所谓BOM的定义即是『记载一项产品的组成零件 (或配方原料) 用量信息的清单』.它能够非常清楚的指出为了生产一个单位 (或一个批量) 的产品一共需要用到多少种类及多少数量的零件或原料,同时亦可反映在正常的生产过程中,对于该些零件或原料可能发生的损坏或耗损数量,甚至可以反映在生产过程中各种零件或原料的插件位置或使用顺序及可代替使用的料件.二.产品结构 (Product Structure)我们可用如下图例表示出一项产品的材料用量清单:图 4-1上例中A是一项产品而料件B,C,D是A的组成材料.1个B,1个C及2个D可以在经过装配过程或合成反应过程后制成1个A.这种树状的结构常被用来做为描述由多种不同的低阶零件或原料制造生产成一项成品的方式,我们称其为『产品结构』在产品结构中亦可以『主件』 (PARENT) 及『元件』 (COMPO-NENT) 的观念来表达组成材料与生产成品的关系.一项主件即产品结构图中位于顶端者,如上例中的A;而元件则指位于产品结构图中底部者,如上例中的B,C,D.上例中,A为B,C,D的主件,而B,C,D即为A的元件.最单纯的产品结构即如上例所举,主件A为一项最终成品或为可以销售的产品.而B,C,D则为最原始的原料零件或为直接购入的材料.而A的整项产品结构仅呈现出一个阶层,此为最简单的产品结构.三.单阶及多阶结构在许多的制造业中,其产品结构并不如上例所举例者那么简单.如下图所示:图 4-2上例中A是一项最终产品,由料件B,C,D所组成.故A是B,C,D的主件,而B,C,D则为A的元件.但D本身并非最原始材料,而是由材料E及F所组成的半成品.故D为E,F的主件,而E,F则为D的元件.其中D扮演了两个角色,即:(1).D为A的元件(2).D为E,F的主件因此如果要生产出A,必须先用E及F生产出D.但上图中对于产品A的组成结构仅描述出其次一低阶组成料件,此种方式我们可称之为『单阶结构』的BOM.如果我们将两个『单阶结构』BOM 衔接在一起即可表达出产品A 的『多阶结构』BOM.如下图所示:通常组成料件众多或制造程序复杂的产品,往往其组成结构会由许多的『单阶结构』所构成而成为多阶层次的复杂树状图.如下图例:图 4-3四.单阶BOM 展开一项主件 (可能是最终产品亦可能仅为半成品) 的单阶BOM 乃表达组成一个单位 (或一个批量) 的主件需要用到多少数量的次阶组成元件.故如果要生产某一数量的该主件就必须要由其BOM 加以计算才能得到对各组成元件的需要数.如图4-1为例,如果需要生产100个A,则对B,C,D 的需求量可计算如下:五.多阶BOM 展开如果我们对于产品A 的组成结构不仅希望了解其次一阶的组成用量,对于更低阶次的组成料件的用量亦需要有整体的了解就必须经过多次的展开计算了.以图4-2为例,如果需生产100个A,则对各料件的需求量可计算如下:六.尾阶BOM展开虽然『多阶BOM展开』可以完整的了解一项产品对各层次料件的需求情形.但在实际应用时却不会去直接利用它.例如现在要领用生产100个A 的料件,如果领用了200个D就不必再领用600个E及200个F;相反的,如果领用了600个 E及200个F则不必再同时领用200个D.因此在实际的运用上,仅会采用单阶BOM的展开,或者尾阶BOM的展开.所谓尾阶BOM的展开即为完全避开所有的中间半成品,而直接对最原始的材料来计算其需求.如下表所示:七.材料用途清单 (Where Used)由材料用量清单 (BOM) 可以了解主件 (成品或半成品) 对其次阶或更低阶的组成料件需用数量.相反的,如果想要了解一项料件到底可以用来组成那些主件;或者说,一项料件到底会被那些主件的制造所需要使用,就必须利用『材料用途清单』作为工具了.材料用途清单的表达亦可利用『单阶』,『多阶』及『尾阶』三种不同的方式.所谓『单阶材料用途清单』乃是对每一料件仅列出其上一阶主件,亦即仅列出直接会使用到该料件的主件.以图4-2 中所示者举例,各料件在其上一阶直接主件中的使用情形如下表所示.其中,单位用量乃指生产一个单位的主件对元件的需用数量.所谓『多阶材料用途清单』乃是对每一料件不仅列出其上一阶直接主件而且亦将其更高阶的间接主件也予列出.以图4-2 中所示者举例,各料件的各种直接,间接主件如下表所示:所谓『尾阶材料用途清单』乃是对每一料件仅列出其最终主件 (通常即为可销售的产品) 而对于中间半成品的主件则不予列出.以图4-2中所示者举例,各料件的最终主件如下表所示:MRP基本概念一、基本定义对制造业而言,最令人困扰的两个问题便是生产排程计划及料件的供应问题.其中对于料件的供应问题,如果补充太多或太快将造成闲置积压的现象.如果补充太少或太慢则又将发生停工待料影响生产或出货的进度.因此如何去准确的计算出在什么时间需要多少数量的某种料件才能满足生产的需要又不造成闲置的现象,一直是不分古今中外,各行各业的制造业者努力追求,希望克服的技术.我们甚至可以说,在今天这种竞争激烈的商业环境下,谁能够有效的解决料件的供应问题,谁就掌握了致胜的条件.『物料需求计划-MRP』的目的即在提供一套有效可靠的方法,来协助制造业编制其各阶产品的生产计划与材料的采购计划.并对采购计划进行模拟分析,以评估其可行性.因此,其所能发挥的效益将十分可观,对制造业者的帮助应该是非常具体而肯定的.二、计划依据物料需求计划的来源依据,销售预测与客户订单为基础自动生成各阶产品的生产计划,再依据生产计划及工单为基础自动生成料件的采购计划三、模拟计划可针对需要补充的料件于计划展算存货不足时,自动取用其取替代料并做出取替代的计划,有效提升存货周转率与减少存货成本.计算时提供交期调整的建议与报表,可建议在需求日期一定范围内的工单或采购单能够建议提早完成,避免之前已发出的单据因无法满足此次需求而再采购一次的窘境,进而降低成为呆滞料的可能.可运行多个版本便于模拟供需变更后的对比,也可以多人同时运行,且同时其他系统仍可正常运作.四、九大量1.预计生产量=未结工单的未完工量 (已发放的工单预计生产量-已生产量).2.预计请购量=未转成采购单的请购数量.3.预计进货量=未结采购单的预计进货量 (已审核的采购预交量-已交-借入未进货数量).4.计划生产量=生产计划档内的计划生产量 (未发放审核的工单生产).5.计划采购量=采购计划档内的计划采购量 (未发放审核的采购订单)..6.预计销货量=未结订单的预计订单量 (已审核的订单预计出货量-已出货量-借出未销数量).7.预计领料量=未结工单的预计领料量 (已发放工单的预计领用量-已领用量).8.计划销售量=订单系统的销售预测量 (应有纳入生产计划及应扣除已受订量).9.计划领料量=相关需求档内的材料需求量 (未发放审核的工单领料). LRP基本概念一、基本定义批次需求计划管理(Lot Requirements Planning 简称 LRP)是材料需求计划(MRP Materials Requirements Planning) 的一种弹性且实务的子系统,其系统虽未能含括MRP子系统的全部,但其观念是以对比弹性且运行上较可行的批 (订单批或工单批或计划批) 来实时运行生产及材料需求计划.对于中小型以下的企业无法确实掌控营业预测 (Sales Forecast) 的状况,提供另外一种物料需求的计算方法,以达确实掌控材料的库存及生产的进度.二、计划依据批次需求计划的来源依据,分为按订单的批、按工单的批、按运行计划的批供选择.三、计划批号运行批次需求计划所汇集的批次号码,并可按此计划批次进行汇总及跟催.四、相关需求需求的来源为工单所生成的用料,亦为九大量中的计划领料量.于生产计划量内的主件的单身材料用量,其用量需求日期为生产计划量开工日的前一工作日.此相关需求是计算机运算时对于下一阶的需求依据,可展出生产计划或采购计划量.相关需求计划变更时其下阶的计划量无法随即调整,所以可以先行发放或锁定已能确定的计划量,其它可以重新计算.五、九大量计划销售量=订单系统的销售预测量(应有纳入生产计划及应扣除已受订量).计划生产量=生产计划档内的计划生产量(未发放审核的工单生产量).计划采购量=采购计划档内的计划采购量(未发放审核的采购订单量).计划领料量=相关需求档内的材料需求量(未发放审核的工单领料量).预计销货量=未结订单的预计订单量(已审核的订单预计出货量-已出货量-借出未销数量).预计生产量=未结工单的未完工量(已发放的工单预计生产量-已生产量).预计请购量=未更新为采购单的请购量(已审核但未更新采购的请购单的请购量).预计采购量=未结采购单的预计进货量(已审核的采购预交量-已交量-借入未进货数量).预计领料量=未结工单的预计领料量(已发放工单的预计领用量-已领用量).六、库存数量此为需求日当日的预计库存数量 (当日可用库存数+计划生产量+预计生产量+计划.采购量+预计采购量+预计请购量-计划销售量-预计销货量-计划领用量-预计领用量).MPS基本概念一、基本定义对制造业而言,最令人困扰的两个问题便是生产排程计划及料件的供应问题.其中对于生产排程的问题,通常因为多种产能上的限制而导致生产排程计算上的困难,如过再依赖人员以人工的经验法则或临时派工,常常导致工作分派紊乱,采购或生产现场无法事前准备等问题生成.想要以有限的产能及最低的库存水平来满足客户订单,就必须运行适时而有效的多厂生产排程,模拟及工令的发放程序, 提供广泛的计划性模拟功能,从销售预测,实际接单,产能计划,主生产排程,发放生产计划皆能有效且迅速协助制造业编制产品的生产计划,并对生产计划进行模拟分析,以评估其可行性,大幅提升生产的有效性,增加至成品的周转率与产能的稼动率.二、系统特色1.按不同生产类型可定义排程优先顺序的设置,透过不同的优先顺序,进而模拟找出最佳排程方法.2.可以针对订单与销售计划排定须要生产的项目,并可以追朔原订单,并且对比是否满足订单的交期.3.可以自动按照瓶颈资源自动生成每日瓶颈资源产能信息.4.可针对每日的瓶颈资源产能事前排定产能计划,便于满足客户交期的需求.5.排程信息可按用户的需求自行调整生产优先顺序,生产数量与预定生产的日期,以满足特别的需求.6.调整后的排程计划可再与产能计划对比,并建议排定加班或外包计划.7.可提供排程反复运算,以便于产能计划修正后的调整.8.排程前自动计算每张订单所需要的净需求数量,便于安排生产数量,大幅减少制成品存货.9.依据产品对于产能的负荷,自动按照每日瓶颈资源产能排定生产时程(有限产能).10.确定的排程计划可自动发放成工单.三、排程依据生产排程的来源依据,销售预测与客户订单为基础自动生成各阶产品的生产计划.四、MPS实施时应注意事项:1.应先收集所有瓶颈资源的信息,及该瓶颈资源会被那些品号所使用,及其各会占用多少的固定耗用,变动耗用,耗用批量.2.需批次生成其每日资源产能,才来做后续的作业较佳,若无录入各品号的瓶颈资源时,则MPS无法运行出结果.五、生产数量计算传播优秀Word版文档,希望对您有帮助,可双击去除!生产数量计算时,若参数设置中,需求计算方式可选毛需求或净需求,若选净需求则库存数量会计算九大量的状况,纯接单时因零库存固为毛需求.1.预计生产量=未结工单的未完工量 (已发放的工单预计生产量-已生产量).2.预计请购量=未转成采购单的请购数量.3.预计进货量=未结采购单的预计进货量 (已审核的采购预交量-已交).4.计划生产量=生产计划档内的计划生产量 (未发放审核的工单生产).5.计划采购量=采购计划档内的计划采购量 (未发放审核的采购订单)..6.预计销货量=未结订单的预计订单量 (已审核的订单预计出货量-已出货量).7.预计领料量=未结工单的预计领料量 (已发放工单的预计领用量-已领用量).8.计划销售量=订单系统的销售预测量 (应有纳入生产计划及应扣除已受订量).9.计划领料量=相关需求档内的材料需求量 (未发放审核的工单领料).-----精心整理,希望对您有所帮助!。
ERP上机实验LRP流程

采购件或委外件:品号属性为“采购件”或“委外件”,补
货政策为“L:按LRP需求”,采购人员、主供应商为非空。另外,主 要仓库、固定前置天数、批量、最低补量、补货倍量、领用倍量需要 设定。
北京化工大学北方学院
LOGO
第8章 LRP
Company Logo
一、主作业流程 二、批次需求计划子系统基础信息设置 三、批次需求计划子系统日常业务处理
Company Logo
一、主作业流程
基础信息设置 设置批次计划 客户订单 生成批次需求计划 基 础 设 置
维护批次生产计划 发放LRP工单
步骤1、维护批次生产计划 开工日、完工日、
生产数量、预计 领料日由系统算 出
Company Logo
2、维护批次需求计划
步骤2、锁定生产计划
Company Logo
2、维护批次需求计划
步骤3、维护批次采购计划
交货日、采 购日、采购 数量由系统 算出
Company Logo
2、维护批次需求计划
自制件330001:核查工作中心、计划人员、 标准工艺路线品号及编号
书中案例为自 制件410001、 330001
410001和330001 的工艺路线前面 做过设置(可返 回“产品结构子 系统”核查一下, 再在此处进行选 择。
Company Logo
所有采购件和委外件,如390001 :核查品号 属性、会计
书中案例为390001、 340001、190004等 三十余种品号
340001为半成品, 其它为原材料
实验1 订单与批次需求计划(LRP)实验答案

实验1 订单与批次需求计划(LRP)实验答案1. 实验背景订单与批次需求计划(LRP)是供应链管理中的重要环节,用于确定未来一段时间内的订单量和批次需求,以便进行合理的物流规划和备货策略。
本实验的目标是通过实际数据,学习和掌握LRP的计算方法和应用。
2. 实验目的1.了解订单与批次需求计划(LRP)的概念和作用;2.学习LRP的计算方法,包括需求预测、订单量计算和批次需求确定;3.掌握LRP的应用场景和实际操作。
3. 实验步骤3.1 数据准备首先,我们需要准备一些实际的数据,包括历史销售数据、需求预测数据和库存信息等。
这些数据将用于计算LRP的各个指标和参数。
3.2 需求预测根据历史销售数据和其他相关信息,我们可以使用不同的预测方法进行需求预测。
常用的预测方法包括移动平均法、指数平滑法和回归分析法等。
根据实际情况选择适当的预测方法,并计算出预测的需求量。
3.3 订单量计算在得到需求预测之后,我们需要计算出实际的订单量。
订单量的计算方法通常包括补货周期法、经济订货量法和剩余需求量法等。
根据实际情况选择适当的计算方法,并计算出订单量。
3.4 批次需求确定在计算出订单量之后,我们需要确定合理的批次需求量。
批次需求量的确定通常涉及到多个因素,包括供应商的最小订购量、物流成本和库存成本等。
根据实际情况选择适当的确定方法,并计算出批次需求量。
3.5 结果分析最后,我们需要对计算结果进行分析,并评估计划的可行性和有效性。
通过分析结果,我们可以了解到计划中存在的问题和改进的空间,并提出相应的建议和措施。
4. 实验总结通过本次实验,我们学习并掌握了订单与批次需求计划(LRP)的计算方法和应用。
订单与批次需求计划是供应链管理中的重要环节,对于合理的物流规划和备货策略具有重要意义。
通过实际数据的计算与分析,我们可以准确预测需求量、确定订单量并合理安排批次需求,从而提高供应链的效率和管理水平。
5. 参考文献[1] Chopra, S., & Meindl, P. (2007). Supply chain management: strategy, planning, and operation (Vol. 2). Pearson Education India.[2] Simchi-Levi, D., Kaminsky, P., & Simchi-Levi, E. (2008). Designing and managing the supply chain: concepts, strategies, and case studies (Vol. 3). Tata McGraw-Hill Education.。
LRP培训重点

LRP(批次需求计划)重点讲解1、11大量中的9大量是哪几个量?入库:计划采购、预计请购、预计进货、计划生产、预计生产出库:计划领料、预计领料、计划销售、预计销货详解:·计划销售量=未达成之销售预测量·计划生产量=生产计划内之预计生产量·计划采购量=采购计划内之预计采购量·计划领料量=相依需求之用料需求量·预计领料量=未完工工单单身之应领未领料量·预计生产量=未完工工单单头之未生产量·预计进货量=未结束采购单之未进货量·预计销货量=未结束订单之未销数量·预计请购量=未更新之请购数量·被取替代=根据BOM取替代关系,被其他料件取替代的数量·替代他料=根据BOM取替代关系,取替代其他料件的数量问题:取替代料在哪里选择纳入计算?2、毛需求+计算九大量,于净需求有何区别?净需求:以原需求量计算9大量,即以(原需求量-库存可用量)展算需求;毛需求:以原需求量展算需求;毛需求+9大量:以原需求量展算需求,9大量仅供查询参考;问题:库存可用量是什么数量?3、需求日期后的需求纳入计算?需求日期后的供给纳入计算?a.需求日期,针对订单而言,是预交货日期。
针对工单而言是预计完工;b.供给\其它需求一般而言是指预计进货单,或计划生产量等量;c.理想状态下,就是严格的一单对一单,勾不勾选没什么区别,但这种情况较少;远水近火型:需求日期后的供给不考虑,需求日期后的其它需求考虑;结果:库存将会过剩\\LRP算出的需求大于供给(本来是相等的)学术理想型:需求日期后的供给考虑,需求日期后的其它需求考虑;结果:理想零库存\\LRP算出的需求等于供给(本来是相等的),虽整体供需平衡,但可能会造成局部的供需不平衡(本公司推行模式)实时行乐型:需求日期后的供给不考虑,需求日期后的其它需求不考虑;结果:库存不足无奈挪料型:需求日期后的供给考虑,需求日期后的其它需求不考虑;结果:后续供给前挪5、生成需求为零的物料?理解其中的逻辑:比如产品A由B,和B1组成,B1由c,d组成当生成计划并发放后,B1要调整,而A不需要调整,如果不勾选“生成需求为零的物料”则,调整后重新跑计划,B1也没有需求,因为,本次A的需求为0,而B1属于A的元件,本阶物料都没有需求量,其下阶自然而然无需求;所以,一般情况下,“生成需求为零的物料”需打钩;计划上会显示该物料,生产(采购)数量为0,当计划发放后,数量为0的采购计划或工单计划不会生成请购单或工单,且系统将自动清除计划内容;6、合并计算最低补量?该选项是新增功能,比如采购件a,它的最低补量是10PCS,当有几个工单(我们的流程是先跑出工单,按工单跑采购计划)涉及到采购a物料时,是否合并需求数量再去和最低补量比较,如,本次由3个工单的需求,工单A需物料a 2PCS,工单B需物料a 5PCS,工单C需物料a 1PCS,如果合并计算,则是2+5+1<10,生成的采购计划数量为10PCS,如果不合并计算,则2<10 , 5<10 ,1<10,分别对比最低补量,生成采购计划数量为30PCS若选择“合并计算最低补量”,则采购计划来源无法追溯!7、“锁定”计划的作用与程序逻辑“锁定”功能,是维护批次计划,特别是工单计划很重要的一个功能;锁定的目的主要有2个:一、确认维护OK的计划,然后在发放计划(发放LRP工单、LRP采购单)的时候,可以选择只发放已经确认的计划;二、锁定还有一个重要的功能,就是在跑LRP时,如果某个计划批次,重新跑LRP,程序会将“未锁定”的计划先清空,然后重新生成计划;如果锁定了,则不变;在这里还要重点提一下,因为“成型件”损耗率是根据其“预计产量”变化的(不同预计产量、不同损耗率),一个亟待解决的问题是在公司规定的预计产量区间,跑LRP时自动匹配不同的损耗率,所以我们的二次开发计划从成型件工单计划着手,将成型件及其他以上阶次的工单计划锁定,获取成型件匹配的损耗率,然后重新跑一次计划,算出正确的需求数;功能尚在预开发阶段,不做详述,如有好的建议,请联系ERP工程师;8、填充料根据公司实际制程情况,注塑工单和喷油工单,均需要一定的设备填充原料;本需求的二次开发计划是从发放LRP 工单程序着手,判断如果有填充料,则自动抓品号信息里的填充数量;同时可根据实际情况选择是否发放填充数量;功能尚在预开发阶段,不做详述,如有好的建议,请联系ERP工程师;9、报表工作中心负荷明细表:打印某一段期间,厂内各工作中心的产能负荷资料,以作为后续产能调整的参考依据;生产计划排程表:以品号的角度,打印产能优先级以及交期;品号供需明细表:以品号及截止时点呈现未来供需的九大量及库存预计结余数量,用以确实掌握料件供需平衡;品号供需统计表:以日、周、旬、半月、月为日期区间,来汇总品号某时点的九大量及库存预计结存数量;其他注意逻辑:A.维护计划来源记录:这只作业的程序逻辑很重要,比如原有批次A的工单计划,重新运行LRP计算时,如果批次仍然是A,则系统将没有锁定的计划清空,重新计算并给出结果,如果批次不是A,那么系统将不会清空原批次A的工单计划,而是结合批次A的工单计划相依供给于需求,生成新的工单计划;在后续作业中,一定要注意这个逻辑关系。
实验1 订单与批次需求计划(LRP)实验答案
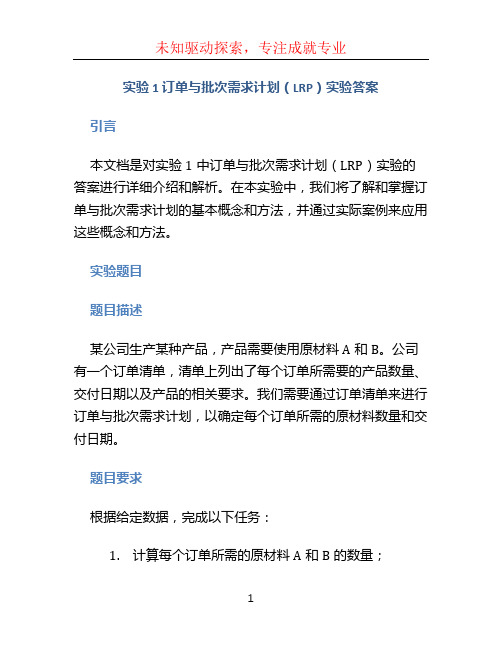
实验1 订单与批次需求计划(LRP)实验答案引言本文档是对实验1中订单与批次需求计划(LRP)实验的答案进行详细介绍和解析。
在本实验中,我们将了解和掌握订单与批次需求计划的基本概念和方法,并通过实际案例来应用这些概念和方法。
实验题目题目描述某公司生产某种产品,产品需要使用原材料A和B。
公司有一个订单清单,清单上列出了每个订单所需要的产品数量、交付日期以及产品的相关要求。
我们需要通过订单清单来进行订单与批次需求计划,以确定每个订单所需的原材料数量和交付日期。
题目要求根据给定数据,完成以下任务:1.计算每个订单所需的原材料A和B的数量;2.根据原材料的库存情况和订单的交付日期,确定最终的交付日期;3.给出订单清单的总需求量和总交付日期。
数据准备为了进行实验,我们需要准备以下数据:•原材料A和B的库存情况•订单清单,包括订单号、所需产品数量、交付日期和产品要求实验步骤步骤1:计算订单所需的原材料数量根据订单清单,我们可以计算每个订单所需的原材料A和B的数量。
假设订单清单的数据如下:订单号产品数量交付日期产品要求001102022-01-10要求1002202022-01-15要求2假设原材料A和B的比例为2:1,即每生产1个产品需要2单位的原材料A和1单位的原材料B。
那么根据订单数量和原材料比例,我们可以计算每个订单所需的原材料数量:•订单001:所需原材料A数量 = 10 * 2 = 20,所需原材料B数量 = 10 * 1 = 10•订单002:所需原材料A数量 = 20 * 2 = 40,所需原材料B数量 = 20 * 1 = 20步骤2:确定最终交付日期在实际生产过程中,原材料的供应可能存在延迟或不足的情况。
因此,在进行订单与批次需求计划时,我们需要根据原材料的库存情况和订单的交付日期,确定最终的交付日期。
假设原材料A的库存为30,原材料B的库存为15。
根据步骤1计算的订单所需的原材料数量,我们可以计算出每个订单所需的原材料的总量:•订单001:所需原材料A总量 = 20,所需原材料B 总量 = 10•订单002:所需原材料A总量 = 40,所需原材料B 总量 = 20根据原材料的库存情况和订单所需的原材料总量,我们可以确定实际可交付的订单数量和交付日期:•订单001:实际可交付数量 = min(30 / 20, 15 / 10) = min(1.5, 1.5) = 1,实际交付日期 = 2022-01-10•订单002:实际可交付数量 = min(30 / 40, 15 / 20) = min(0.75, 0.75) = 0.75,实际交付日期 = 2022-01-15步骤3:计算总需求量和总交付日期最后,我们计算订单清单的总需求量和总交付日期。
易飞ERP9.0 LRP

LRP上线前置条件
基本信息之正确性
产品结构系统
录入BOM信息 单头: ·标准批量 ·工单单别 单身: ·组成用量 ·底 数 ·生效日期 ·失效日期 ·交叉排程 ·变动损耗 ·考虑上阶固定前置天数 录入取替代料 单头: ·取替代料 单身: ·数量 ·生效日期 录入料件认可信息 ·制造商 ·认可型号 ·主要来源 ·生效日期 ·核准状况 ·损 耗率 ·投料间距 ·固定损耗量
批次生产计划维护
工单发放或生产计划锁定
产生采购计划
采购计划维护 发放采购单据
与其他系统的关联
销售子系统
存货子系统
批次需求 计划系统
产品结构子系统
工单/委外子系统 主生产计划 子系统
采购子系统
基 本 信 息 创 建
LRP解决生产管理之困扰 LRP上线前置条件
重要名词解释
上线前准备 设置批次计划
·替代他料
= 根据BOM取替代关系,取替代其他料件的数量
重要名词解释
净需求数量
出 +计划销售 +计划领料 +预计销售 +预计领料 +被取替代 入 -库存可用量 -计划生产 -计划采购 -预计进货 -预计生产 -预计请购 -取代他料
净需求数量
重要名词解释
生产计划及采购计划之数量计算
·P件 净需求>0时 产生批次采购计划 ·M/S件 净需求>0时 产生批次生产计划
实例说明
交叉排程说明(以“考虑上阶固定前置天数”=“Y”为例)
检验天数2天
工单Ax:需求日为10-25号,扣除(1+1)天,预计10-21号完工(22、23日为假日),批量300,变 动前置天数3天,故10-14预计开工-----------------------------------------------------600PC 工单Bx :预计10-14完工,10-03预计开工,检验2天,10-18检验完成--------------600PC 交叉条件:在匀速生产的情况下,上下阶可并行生产,但上阶不能因下阶供应不上导致停工待料 交叉逻辑:下阶第一个批量完工,检验后,可供应上阶开工(含准备时间在内),并且,下阶完 工,检验后,可供应上阶最后批量开工;如果上下阶进度不是刚好匹配,则提前下阶计划,以同 时满足上阶的第一个批量和最后一个批量的开工要求 上例中:Ax、Bx各2个生产批量,Bx第一批量完工是10-07,检验完成是10-11,能满足上阶开工 (10-14),第二批量完工是10-14,检验完成是10-18,能满足上阶最后批量开工(10-19)---两个 条件同时满足,其中,Bx的第一批量超前完成,以便最后批量能赶上上阶最后批量开工需求
国家开放大学电大《ERP原理与应用》实验1订单与批次需求计划(LRP)实验作业答案
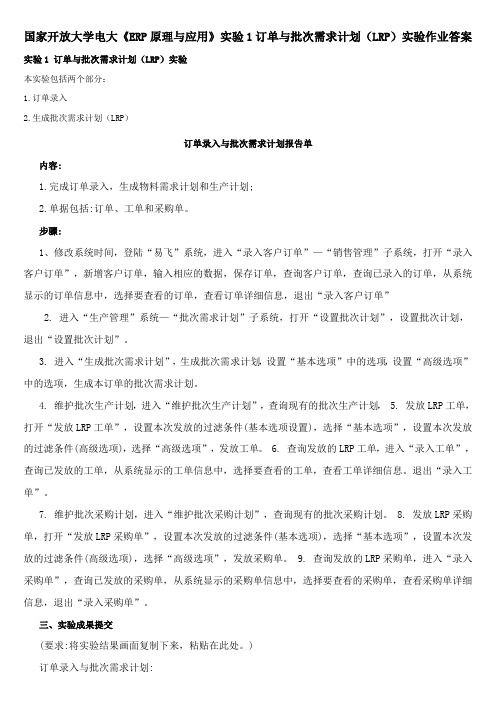
国家开放大学电大《ERP原理与应用》实验1订单与批次需求计划(LRP)实验作业答案实验1 订单与批次需求计划(LRP)实验本实验包括两个部分:1.订单录入2.生成批次需求计划(LRP)订单录入与批次需求计划报告单内容:1.完成订单录入,生成物料需求计划和生产计划;2.单据包括:订单、工单和采购单。
步骤:1、修改系统时间,登陆“易飞”系统,进入“录入客户订单”—“销售管理”子系统,打开“录入客户订单”,新增客户订单,输入相应的数据,保存订单,查询客户订单,查询已录入的订单,从系统显示的订单信息中,选择要查看的订单,查看订单详细信息,退出“录入客户订单”2. 进入“生产管理”系统—“批次需求计划”子系统,打开“设置批次计划”,设置批次计划,退出“设置批次计划”。
3. 进入“生成批次需求计划”,生成批次需求计划,设置“基本选项”中的选项,设置“高级选项”中的选项,生成本订单的批次需求计划。
4. 维护批次生产计划,进入“维护批次生产计划”,查询现有的批次生产计划,5. 发放LRP工单,打开“发放LRP工单”,设置本次发放的过滤条件(基本选项设置),选择“基本选项”,设置本次发放的过滤条件(高级选项),选择“高级选项”,发放工单。
6. 查询发放的LRP工单,进入“录入工单”,查询已发放的工单,从系统显示的工单信息中,选择要查看的工单,查看工单详细信息。
退出“录入工单”。
7. 维护批次采购计划,进入“维护批次采购计划”,查询现有的批次采购计划。
8. 发放LRP采购单,打开“发放LRP采购单”,设置本次发放的过滤条件(基本选项),选择“基本选项”,设置本次发放的过滤条件(高级选项),选择“高级选项”,发放采购单。
9. 查询发放的LRP采购单,进入“录入采购单”,查询已发放的采购单,从系统显示的采购单信息中,选择要查看的采购单,查看采购单详细信息,退出“录入采购单”。
三、实验成果提交(要求:将实验结果画面复制下来,粘贴在此处。
批次需求计划系统知识分享

(三)、交易信息之时效及正确 性
1·订单系统 : ·正确之销售信息 ·订单指定结束管制 ·即时销货资讯
2·采购系统 : ·采单指定结束管制 ·即时收料资讯
3·工单系统 : ·工单指定完工管制 ·即时库存交易资讯
2020/5/3
(三)、交易信息之时效及正确性
4·产品结构 : ·正确的品号用量信息 ·正确之损耗率
5·库存系统 : ·正确之品号基本信息资讯 ·即时库存交易资讯
2020/5/3
(四)、基本信息字段信息之正 ●库存管理子系确统性
录入品号 单头: ·低 阶 码 ·计划人员 ·主要库别 ·主供应商 ·补货政策 ·前置天数 ·批 量 ·最低补量 ·补货倍量 ·领用倍量 单身: ·库 别 ·库存数量 ·安全存量
叁. 基本信息录入及信息字段 说明
1.前序作业信息 2.系统基本信息录入
2020/5/3
(一)前序作业信息
1.录入假日表 2.录入工作中心 3.录入工厂及仓库
2020/5/3
基本信息之检测
【生产计划异常检测表】--检测执行生产 计划时所需相关信息是否异常并列印成册. 可用其检测上线前基本信息之完整度。
(六)、LRP系统上线前置条件
(一)、基础系统 1.库存管理子系统 2.产品结构子系统 3.订单管理子系统 4.采购管理子系统 5.工单/委外子系统
2020/5/3
(二)、管理需求条件
1.库存帐务正确性及即时性高。 2.订单之生产排程周期内变更少。 3.生产排程稳定及正确。 4.制程稳定、制造前置时间稳定。 5.料件品质稳定、采购前置时间稳定。
工单发放或生产计划锁定作业 采购计划产生作业 采购计划调整作业
采购单发放
批次需求计划系统ppt课件

(三)、买卖信息之时效及正确性
1·订单系统 : ·正确之销售信息 ·订单指定终了控制 ·即时销货资讯
2·采购系统 : ·采单指定终了控制 ·即时收料资讯
3·工单系统 : ·工单指定完工控制 ·即时库存买卖资讯
(三)、买卖信息之时效及正确性
4·产品构造 : ·正确的品号用量信息 ·正确之损耗率
5·库存系统 : ·正确之品号根本信息资讯 ·即时库存买卖资讯
(二)、九大量
·方案销售量=未达成之销售预丈量 ·方案消费量=消费方案内之估计消费量 ·方案采购量=采购方案内之估计采购量 ·方案领料量=相依需求之需求量 ·估计领料量=未完工工单独身之应领未领料量 ·估计消费量=未完工工单单头之未消费量 ·估计进货量=未终了采购单之未进货量 ·估计销货量=未终了订单之未销数量 ·估计请购量=未更新之请购数量
序。
(二).系统功能及效益
〔一〕、系统功能
1.根据客户订单或已开工单自动产生本阶或下阶各阶产 品之批次消费方案。
2.根据批次消费方案自动拟定批次采购方案。 3.可自动将批次消费方案发放至工单/委外子系统成为
正式之工单 。 4.可自动将批次采购方案发放至采购子系统成为正式
之请购单或采购单。 5.可对批次消费方案及工单排程提供产能负荷分析。
易飞管理软件
批次需求方案系统培训 (LRP)
部门: 讲师:
课程大纲
1.前言 2.系统架构 3.根本信息录入及信息字段阐明 4.LRP计算逻辑阐明 5.批次作业阐明 6.报表管理 7.产能负荷管理 8.检验及问卷
壹.前言
一、教育训练课程之目的 二、系统功能及效益引见
(一)、教育训练课程之目的
1·了解系统之效益及功能。 2·了解信息搜集及整理重点。 3·熟习系统之操作方式。 4·了解系统例行作业程序。 5·了解系统上线的步骤及导入程
LRP培训知识(ppt62张)
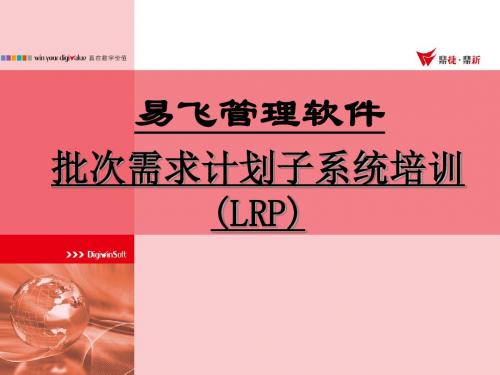
批次需求计划子系统培训 (LRP)
课 程 大 纲
一、系统主画面 二、系统主作业流程 三、基本信息创建 四、 LRP计算逻辑说明 五、作业说明 六、管理报表
系 统 主 画 面
系 统 主 作 业 流 程
客户订单/源工单/销售预测/生产计划
产生批次生产计划 批次生产计划调整作业 工单发放或生产计划锁定作业 采购计划产生作业
维护计划来源记录
将产生过计划的来源单号记录,避免重复执行
管理报表
生产计划排程表
工作中心负荷明细表
批次计划检视表 品号供需明细表
品号供需统计表
生产计划排程表
按工作中心将商品按完工日排列, 产生排程报表
工作中心负荷明细表
可将各工作中心在一段期间中的 负荷明细打印成表
批次计划检视表
设置批次计划
采购计划由生管决定并发布的,可直接发放采购单, 否则,发放请购单,由采购人员维护后再发放
设置批次计划
• 设置补货数量以来源单据需求 数量为上限,或是允许超出 • 考虑安全存量时,补货数量可 能超过来源单据需求数量 • 如: • ItemA安全存量100 • 现有库存80 • OrderA需求ItemA 300 • 若计算原则为’不超出来 源单据数量’,则对 OrderA跑LRP计划,需采 购ItemA为300 • 否则为320
LRP计算逻辑说明
LRP适用范围
LRP系统特色
实例说明
LRP适用范围
接单型生产模式或计划生产模式中紧急 订单或插单 以订单/源工单/销售预测/主生产计划 为依据产生 生产计划计划需按来源进行追溯者
LRP系统特色
1.来源明确(订单、源工单、销售预测、MPS等) 2.计划结果可追溯计划来源 3.可选择毛需求或净需求 4.可选择十一大量判断时间点 5.系统运算时间短 6.可选择是否考虑BOM损耗率
001订单与批次需求计划(LRP)实验
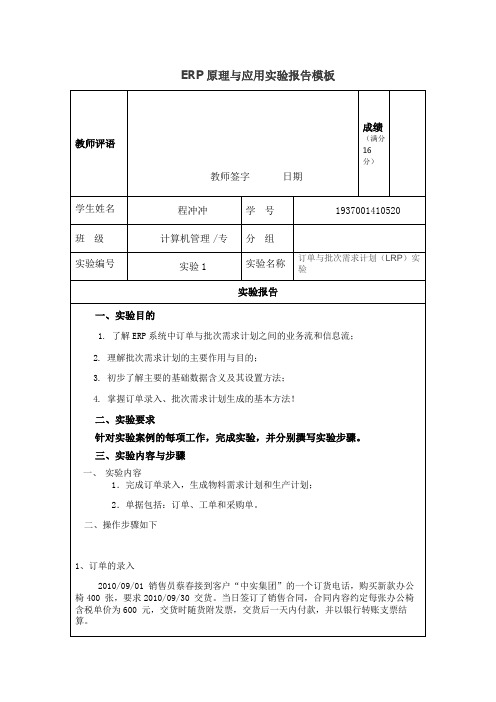
ERP原理与应用实验报告模板(1)启动易飞ERP系统首先进入ERP系统。
在WINDOWS界面下,点选“易飞ERP”系统。
出现启动界面:出现登录界面,输入相应的帐号和口令。
则可进入易飞ERP系统。
易飞——ERP系统主画面如下:(2)订单的录入鼠标点击进销存管理系统-销售管理子系统(3)、录入客户订单-新增(4)、选择订单单别-确定2、生成批次需求计划生管人员焦永涛根据这张订单去做批次需求计划;生成生产计划:生产办公椅400 张,2010/09/18开工;由于生产办公椅需要的原材料底座的现有库存量不能满足生产的需求,所以生成这类原材料的采购计划,预计进货日2010/09/17;生管人员审查生产计划与采购计划,审核后确认无误,将生产计划发放成工单到办公椅加工中心。
操作:从左边的树状结构处选择“生产管理”之“批次需求计划系统”。
按图中顺序进行操作。
按图中顺序进行操作。
定的采购计划发放到采购管理子系统的正式采购单或请购单。
步骤:发放LRP采购单-选择供应商-确定-选择供应商信息-确定-计划批号-确定-高级选项-单别信息查询-采购单据-确定-输入采购人员-002李文确定-直接处理6、发放LRP工单将批次生产计划全部发放至工单管理系统成为正式工单,发入的工单可以到工单作业中查询。
步骤:发放LRP工单-单别信息查询-确定-工单单别-高级选择项-直接处理四、实验成果提交(要求:将实验结果画面复制下来,粘贴在此处。
)1、录入客户订单截图2、按批次需求计划截图3、维护批次生产计划截图4、维护批次采购计划截图5、发放LRP采购单截图6、发放LRP工单截图五、实验中遇到的难点及解决办法在实验操作过程中,我遇到了一些问题。
第一,在填写客户订单的时候没有注意到单价和数量,因为在默认状态下数量为零,如果没有修改,则会在财务方面结算的时候发现金额为零,造成错误。
第二,在整个实验过程中,进行每一项操作都需要注意时间的改动,否则在之后的操作过程中会出现问题,比如填写打磨完工日时如果距离完工日较远,则在此后的操作过程中会出现提前交货的提示。
LRP批次需求计划系统课后测验(A)
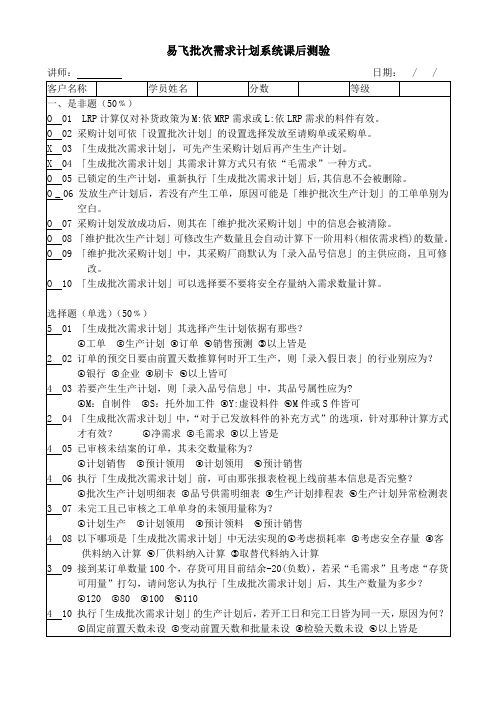
O _06发放生产计划后,若没有产生工单,原因可能是「维护批次生产计划」的工单单别为空白。
O07采购计划发放成功后,则其在「维护批次采购计划」中的信息会被清除。
O08「维护批次生产计划」可修改生产数量且会自动计算下一阶用料(相依需求档)的数量。
406执行「生成批次需求计划」前,可由那张报表检视上线前基本信息是否完整?
批次生产计划明细表品号供需明细表生产计划排程表生产计划异常检测表
307未完工且已审核之工单单身的未领用量称为?
计划生产计划领用预计领料预计销售
408以下哪项是「生成批次需求计划」中无法实现的考虑损耗率考虑安全存量客供料纳入计算厂供料纳入计算取替代料纳入计算
银行企业刷卡以上皆可
403若要产生生产计划,则「录入品号信息」中,其品号属性应为?
M:自制件S:托外加工件Y:虚设料件M件或S件皆可
204「生成批次需求计划」中,“对于已发放料件的补充方式”的选项,针对那种计算方式才有效?净需求毛需求以上皆是
405已审核未结案的订单,其未交数量称为?
计划销售预计领用计划领用预计销售
易飞批次需求计划系统课后测验
讲师:日期:/ /
客户名称
学员姓名
分数
等级
1、是非题(50﹪)ຫໍສະໝຸດ O01 LRP计算仅对补货政策为M:依MRP需求或L:依LRP需求的料件有效。
O02采购计划可依「设置批次计划」的设置选择发放至请购单或采购单。
X03「生成批次需求计划」,可先产生采购计划后再产生生产计划。
X04「生成批次需求计划」其需求计算方式只有依“毛需求”一种方式。
309接到某订单数量100个,存货可用目前结余-20(负数),若采“毛需求”且考虑“存货可用量”打勾,请问您认为执行「生成批次需求计划」后,其生产数量为多少?
易飞LRP补充方式说明

LRP补充方式说明在我们的系统中,作业生成批次需求计划中提供了针对跑毛需求的三种补充方式,分别是:重新补充;补充差额;不再补充。
下面分别针对这三种方式进行说明以及系统演示。
一.三种补充方式的说明首先介绍一下已发放量的概念。
针对自制件以及委外件,当计划的来源是订单的时候,已发放量指工单单头订单单号为此订单,并且工单的产品品号为对应品号的这些非作废的工单上的预计产量之和。
当计划来源为工单时,则指工单工单单头来源工单单号为此工单,并且工单的产品品号为对应品号的这些非作废的工单上的预计产量之和。
当计划来源为LRP生产计划时,则指工单单头计划批号为为此来源计划批号,并且工单的产品品号为对应品号的这些非作废的工单上的预计产量之和。
当计划来源为销售预测时,则指工单单头订单单号为此预测号,订单单别为‘****’,并且工单的产品品号为对应品号的这些非作废的工单上的预计产量之和。
针对采购件,采购单单身的参考单号为来源单号以及请购单的参考单别单号序号为来源单别单号序号,并且采购单以及请购单上的品号为来源上的品号,汇总这些非报废的采购单以及请购单上的数量即为已发放量。
重新补充是指不考虑计划生成的单据,也即不考虑已发放量。
还是像第一次跑计划一样处理,生成对应的计划信息。
补充差额则是会考虑已经发放计划生成的单据,即考虑已发放量。
生成的计划数量是毛需求与已发放量的差额。
不再补充是指不管之前毛需求和已发放量之间的差额是多少,只要有已发放量,生成的计划中的生产数量、加工数量、采购数量、需求数量就是0 。
二.三种补充方式的系统演示首先我们先看一下品号信息,目前存在三个品号各自信息如下表,均为新建的品号,所以库存量为0并且安全存量设置为0。
品号属性补货政策最低补量补货倍量领用倍量K M.自制件L.按LRP需求0 0 0K01 P.采购件L.按LRP需求0 0 0K02 P.采购件L.按LRP需求0 0 0BOM结构如下图:目前有一张订单信息如下:订单数量为10这个订单执行生成计划的时候,三种补充方式任选其一就可以了。
ERP生产管理实务第三章LRP

(2)计划之净需求量
出 +计划销售 +计划领料 +预计销售 +预计领料 +被取替代 -库存可用量 -计划生产 -计划采购 -预计进货 -预计生产 -预计请购 -取代他料
入
净需求数量
17
(3)生产计划量及计划采购量
· 净需求>0时 P件 产生批次采购计划 · M/S件 净需求>0时
产生批次生产计划
客户供料、取替 代料可选择纳入 计算
22
3、维护批次生产计划
23
4、发放LRP工单
24
4、发放LRP工单
25
5、维护批次采购计划
26
6、发放LRP采购单
27
6、发放LRP采购单
28
实验要求:
1、开立一张客户订单,根据该订单生成批次需求计 划。 2、在运行计划时,需要以下基础数据: 所有料件必须有库存量和安全存量 所有自制件和委外加工件必须有:预计生产 量、 预计销售量; 所有采购件必须有:预计进货量、预计请购量、 预计领用量。 3、实验报告中要记录一个自制件的计划中运算的数 量、一个采购件的计划中运算的数量的推导过程, 所有的参与运算的数据的来源,最终的数量的原 因。 29
生产计划计划需按来源进行追溯者
12
3.2 LRP的计算逻辑(一)
13
计划人员的烦恼
现有一客户需求, 要求企业在预定的 交货期,保质保量 的交货给客户
到底应该在 什么时间采 购多少原料 料呢
到底应该在 什么时间生 产多少自制 件呢
?
?
?
时间
计划人员
?
数量
14
例如:
有一张订单A 要求 25日要出货,200PCS
第三章 批次需求计划(LRP)子系统
第7章 ERP生产管理:批次需求

预计领料日=预计开工日+投料 间距
默认的信息在哪呢?
系统会先找出需求日,再扣掉检验天数,推算此 品号的“交货日”,再以该品号的前置天数,推
算该品号的“采购日”(预计)。
来算算吧
半成品310001-PCBAAssembly MainSL系列预计7月16日开工,会用到 110001主开关联动板,该品号 的相 关信息如下: 检验天数:1天 固定前置天数:4天 变动前置天数:1天 批量:1000PCS 预计采购数量:1008PCS
三种补充方式算一算?
维护批次生产计划
1:不在补充 2:重新补充 3:补充差额
生产数量为0
生产数量为120 你算对了吗?
生产数量为20
依BOM用量资料展算计划数量时, 选择是否加上损耗数量
当计算库存可用量时,是否要考虑安全存量 勾选考虑安全存量: 库存可用量=库存数量+预计供给量-预计需求 量-安全存量
日 一 二三 四 五 六
12345 6 7 8 9 10 11 12 13 14 15 16 17 18 19 20 21 22 23 24 25 26 27 28 29 30 31
企业假日表:星期六、星期日休息
日期的推算
预计完工日=订单预交货日(7/26)-1-检验天数(1)=7/24 生产前置天数=【(预计产量/批量*变动前置天数)】+固定前置天数
客户供料是指此原物料由客户提供,不需自行 采购,在【录入BOM】中设定材料类型, LRP才能进行运算。
若此选项勾选,表示此次的客户供料需自行 采购,因此系统会产生采购计划,未勾选则 不产生采购计划 而生产计划的相关需求,不论是否勾选,一 定会产生
LRP 批次需求计划9.0
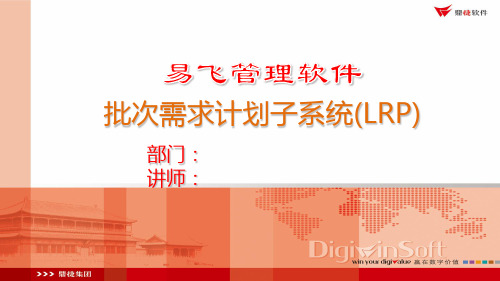
可用其检测LRP系统上线前基本信息之完整度。
设置批次计划
采购计划由生管决定并发布的,可直接发放采购单, 否则,发放请购单,由采购人员维护后再发放
设置批次计划
设置补货数量以来源单据需求数量为 上限,或是允许超出 考虑安全存量时,补货数量可能超过 来源单据需求数量 如: ItemA安全存量100 现有库存80 OrderA需求ItemA 300 若计算原则为’不超出来源单据 数量’,则对OrderA跑LRP计划, 需采购ItemA为300 否则为320
实例说明
交叉排程说明
检验天数,扣除(1+1)天,预计10-21号完工(22、23日为假日),批量300,变 动前置天数3天,故10-14预计开工-----------------------------------------------------600PC Bx :预计10-14完工,10-03预计开工,检验2天,10-18检验完成--------------600PC 工单 交叉条件:在匀速生产的情况下,上下阶可并行生产,但上阶不能因下阶供应不上导致停工待料 交叉逻辑:下阶第一个批量完工,检验后,可供应上阶开工(含准备时间在内),并且,下阶完 工,检验后,可供应上阶最后批量开工;如果上下阶进度不是刚好匹配,则提前下阶计划,以同 时满足上阶的第一个批量和最后一个批量的开工要求 上例中:Ax、Bx各2个生产批量,Bx第一批量完工是10-07,检验完成是10-11,能满足上阶开工 (10-14),第二批量完工是10-14,检验完成是10-18,能满足上阶最后批量开工(10-19)---两个
2)采购系统 :
采单指定结束管制 即时收料资讯
3)工单/委外系统 :
工单指定完工管制
LRP上线前置条件
- 1、下载文档前请自行甄别文档内容的完整性,平台不提供额外的编辑、内容补充、找答案等附加服务。
- 2、"仅部分预览"的文档,不可在线预览部分如存在完整性等问题,可反馈申请退款(可完整预览的文档不适用该条件!)。
- 3、如文档侵犯您的权益,请联系客服反馈,我们会尽快为您处理(人工客服工作时间:9:00-18:30)。
下达生产/委外
下达采购
物料供需资料 明细
计划执行状况 表
计划明细表
yonyou software Corporation
LRP主流程之接口关系
销售子系统
出口子系统
批次需求 计划系统
产品结构子系统
生产订单子系统 委外子系统
采购子系统
yonyou software Corporation
LRP应用价值
+ 接单型客户的需求 + 项目应用基本需求 + MRP与LRP的区别
+主作业流程 +LRP操作 +报告分析
yonyou software Corporation
接单型客户的需求和基本经营方式
接单、外向型企业:东莞某汽配散热器公司。接单制造,直接一对一对应海外客户出口销售。 客户250-300,60多个国家。经营散热器因为客户的不同,包装变化繁复,产品标准型,多 种包装变型 计划就是对销售订单进行干预式的计划,对于不同交期的订单采取不同的时间下达,并依照 销售订单排单
上线前置条件-业务属性设置
LRP将针对纳入MPS/MRP计划的采 购销售类型单据进行计算。 非计划属性业务不能被选中进行计划
名词解释-供需数量(十一大量)
预测订单量
•未达成之有效销售预测量,结束日期大于等于系统日期的预测订单的余量; •表示销售/出口订单之未完成数量,未关闭销售/出口订单的订单余量; •有效计划订单之用料需求量,计划订单需求数量; •表示尚未完工生产/委外订单表体之应领未领料量,状态为“审核、锁定”之生 产/委外订单之子件需求; •表示即将出库但尚未出库的数量,已有出库记录尚未出库的库存数量;审核后 记库存帐的库存选项 •表示计划订单之供应数量,计划订单之订单余量; •表示尚未完工生产/委外订单表体之未完成数量,状态为“审核、锁定”之生产 /委外订单之未完成数量; •表示尚未完成采购订单/进口之订单余量,状态为“审核、锁定”之采购订单/ 进口订单之未到货数量; •表示尚未执行采购订单之订单余量,状态为“审核、锁定”之请购单之未下达 数量; •表示到货尚未入库的数量,已有入库记录尚未入库的库存数量;审核后记库存 帐的库存选项 •为库存现存量-冻结量-PE预留量;
接单跟踪的需求
• 企业(尤其是接单生产型企业)为保证销售订单的完成,需要能够对内部执行过程进行有效监控,这就要求企 业运营活动中物料的供应与需求都可以根据销售订单进行跟踪 • 对于接单生产型企业,由于需求来源的不稳定,无法制定出相对稳定、合理的计划,需要根据需求来源单独的 编制出相对稳定计划,再由销售人员或计划人员进行人工的干预: • 按照新来的需求来源编制计划,已有的计划维持不变;
MRP和LRP区隔:
• LRP作为MRP的一个计划模式补充。
• 属于非标准的计划分解算法,专门针对接单型按单排产的计划模式。 • 以类似库存展望滚动模拟来源单对应汇总需求和汇总供给的平衡
产品形态:
• 作为MRP模块的计划方式的切换选项出现。 • 不需要报价
支持范围:
• PE件 • 不支持LP和PE跟单;
些是可用量满足,哪些是不够的。
手工计划情况下生管人员的困难
Байду номын сангаас客 户 订 单
生 产 计 划
销 售 预 测
主 生 产 计 划
人工主排程或最终产品排程
大量单据
采购人员
生管或计划人员
MRP与LRP的区别
MRP
MRP是按照时间顺序对“料”进行 供需平衡。 MRP会合并交期相同的供应, 针对插单情况,MRP会对全局计划 进行重排,已有排产内容进行计划 建议。。 中小企业计划员对于全局供给需求 平衡,很难进行准确性判别和调整 MRP对于生产计划和采购计划同时 生成
U8V11.1批次需求计划
用友软件股份有限公司 U8生产制造 讲师: 2013年08月01日
yonyou software Corporation
目录
Contents
+应用背景 +主作业流程 +LRP操作 +报告分析
yonyou software Corporation
目录
Contents
+应用背景
1. 实现挑单计划计算,能够快速响应客户需求。 2. 计划维护中能够看到计划行对应的在单量、预计 出入库数量、库存量信息,便于计划员参考和 调 整,一目了然计划如何得来,减轻计划员核对计 划准确性,
3. 支持插单模拟和运算,不影响原有计划安排,计
划编制符合手工编制下的思路 4. 通过LRP运用,快速建立起企业应用计划的信心,
生产部门
生产订单(记 录计划批号, 来源单据号)
批号可追溯范围
生产部门根据计划部门下达计 划批号,以及计划批号下的来 源定单号进行指定采购
完工入库时候业务员 能够了解来源批号, 单据号
入库(记录来 源单号)
库存部门
采购部门
采购订单(记 录计划批号, 来源单据号)
采购部门根据计划部门下达计 划批号,以及计划批号下的来 源定单号进行指定采购。
• 由于LRP是在模拟手工编制计划,编制计划时是针对什么样的来源订单,或者哪些来源订单发生变化需要重 新产生计划,计划员是清楚的: • 知道对哪些来源订单编制计划; • 知道哪些订单需求修改计划:或重新生成、或手工修改; • 知道哪些订单可以执行:采购、生产、委外计划。
计划与执行要跟踪、物料耗用不跟踪
上线前置条件-管理业务要求
1. 库存帐务正确性,及时录入系统。 2. 销售订单在生产在线上生产时候,变更较少。 3. 生产排程稳定及正确,不会来回大幅变动。 4. 工艺稳定、制造提前期时间稳定。 5. 料件品质稳定、采购前置时间稳定。
上线前置条件-业务系统数据检查
• 订单指定完工日期 • 实时进行发货数据 更新 • 采购单指定到货日 期 • 实时进行到货数据 更新 1)销售/出口 2)采购管理: 3)生产订单/ • 工单指定完工日期 • 实时领退料/入库数 据更新
上线前置条件-存货档案计划方法调整
使用LRP计算时候,需要将存货【计划 方法】属性从R,N改为L。 只有L物料能够参与LRP计算。 只有L物料架设了BOM方能够分解 可以通过存货批量修改工具进行计划 方法属性的调整
上线前置条件-仓库设置
计算LRP时候,将仅仅针对 【参与MRP计算】属性的 仓库进行现存量和可用量 的计算,解决某些物料仓 不参与计算的需求
到货,入库时候业务 员能够了解来源批 号,单据号
入库(记录来 源单号)
库存品根据需要会有跨批挪 用等,或者公用
yonyou software Corporation
LRP主流程
工作日历 设置批次计划 方案 销售订单
存货属性
LRP计划生成
预测单
物料清单
LRP计划维护
生产订单
LRP计划工作 台 生产计划 采购计划
2. 计划结果可追溯计划来源
3. 供应链单据携带来源单据号,用于追溯 4. 可选择毛需求或净需求 5. 可选择十一大量判断时间点 6. 系统运算时间补偿
7. 供需平衡在数量上以累计需求减累计供应,在时间
上不再对系统中所有的供需进行时间上的平衡;
LRP基本特征
面向客户:
• 完全接单生产企业。外贸型,或者OEM定制,大客户定销企业。 • 集团内加工企业,为集团做订单配套
为未来企业运用MPS,MRP等全局优化算法奠定
良好基础。减少项目交付难度。
yonyou software Corporation
目录
Contents
+应用背景 +主作业流程 +LRP操作
+ + + + + + + +
LRP上线前置条件 名词解释 LRP计划生成-场景应用 LRP计划生成-操作流程 LRP计划生成-生成逻辑 LRP计划生成-逻辑说明
维护批次需求计划
计划工作台
+报告分析
yonyou software Corporation
上线前置条件-业务假设
当前计划是正确的
• 由于LRP为保证计划的连续性、可追踪,对系统中已有的计划假设为是正确的,在编制新的计划时,不会对 其他未选择的来源订单重新计划,也不会对现有的计划给出建议。
信息沟通是畅通的-计划员了解计划来源和下达去向
yonyou software Corporation
LRP基本原理
1. 支持参照多个单据来源, 挑单进行LRP计算 2. 计算过程中靠11大供给 与需求数量,结合选单 需求进行净需求或者毛 需求计算 3. LRP可以分次计算生产 计划和采购计划,也可 以一次性同时生成两个 计划 4. 订单会记录计划批号, 来源单据号,保证单据 查询追溯性 5. LRP会基于具体批次号,
应用计划能力不足
• 有些接单生产企业,企业管理水平规范化程度较低,希望能够提供一种类似模拟手工的计划编制
方法,能够方便进行计划编制和掌控
• MRP计划维护界面上,只看到最终的建议计划量信息,无法获知结果的取数关系,象预计出库 数量、预计入库数量、库存量、可用数量都没有显示出来 • 计划生成后,计划维护界面清楚地看出销售订单中某款产品的完整BOM结构,可查子件物料哪
以一张或数张客户订单(或工单)为单位(批次)进行生产计 划与采购计划计算,经必要的调整与发放,自动生成对 应的工单及采购单后,允许用户以该单位(批次)号码为 基础进行生产及采购计划执行状况的跟踪,并提供用户 在执行管理工作时所需信息的管理信息系统
一般ERP具有的料件属 性外,另新增"按批补货 "的料件属性
LRP
LRP是一种以“单”为中心,按 “单”占用供应的计划方法。 不同订单的计划订单不合并,以保 证能有效追踪需求来源。 允许用户以该批次号码为基础进行 生产及采购计划执行状况的跟踪, 插单计划可以做到不调整原有订单 计划 以库存展望滚动模拟来源单需求和 供给的平衡,并产生各类计划建议 量的算法 LRP可以分别计算生产计划和采购 计划