2020年浅析高速冲压模具参照模板
2020年中国冲压模具行业现状发展走向及技术环境分析报告
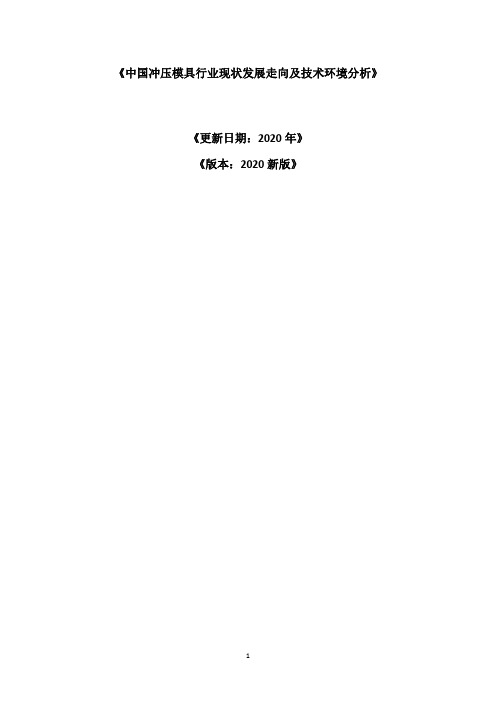
《中国冲压模具行业现状发展走向及技术环境分析》《更新日期:2020年》《版本:2020新版》目录第一章冲压模具行业概述 (3)第一节冲压模具概述 (3)一、冲压模具定义 (3)二、冲压模具分类 (3)三、冲压模具原理 (4)四、冲压模具发展历程 (4)第二节冲压模具设计 (4)第三节冲压模具产业链分析 (6)第二章2019-2020年中国冲压模具行业环境分析 (6)第一节2019-2020年中国冲压模具行业政策环境分析 (6)第二节2019-2020年中国冲压模具行业社会环境分析 (7)第三节2019-2020年中国冲压模具行业技术环境分析 (7)一、行业技术水平及特点分析 (7)二、国内外技术差距分析 (8)第三章2019-2020年中国冲压模具行业发展现状分析 (9)第一节2019-2020年中国冲压模具发展现状分析 (9)一、冲压模具行业发展现状分析 (9)二、中国冲压模具行业形势乐观 (10)三、冲压模具行业发展层次分析 (10)四、我国冲压模具行业走向分析 (11)第二节2019-2020年中国冲压模具产品技术分析 (12)一、冲压模具产品市场的新技术 (12)二、冲压模具产品技术现状分析 (12)第三节2019-2020年中国冲压模具行业问题仍存在 (13)一、产品质量不高 (13)二、标准化水平不高 (13)三、缺迁相关人才 (14)四、受到外资企业的挑战 (14)五、缺乏自有品牌 (15)第一章冲压模具行业概述第一节冲压模具概述一、冲压模具定义冲压模具是在冷冲压加工中,将材料(金属或非金属)加工成零件(或半成品)的一种特殊工艺装备,称为冷冲压模具(俗称冷冲模)。
冲压,是在室温下,利用安装在压力机上的模具对材料施加压力,使其产生分离或塑性变形,从而获得所需零件的一种压力加工方法。
二、冲压模具分类冲压模具的形式很多,冲模也依工作性质,模具构造,模具材料三方面来分类根据工艺性质分类a.冲裁模沿封闭或敞开的轮廓线使材料产生分离的模具。
冲压模具简介[1]
![冲压模具简介[1]](https://img.taocdn.com/s3/m/41eee28c67ec102de3bd8969.png)
工作零件
沖子 刀口
導向零件
導柱 導套
定位零件
導正銷 導料板 側刃
壓料 卸料零件 脫料板 壓邊圈 頂桿
固定及其他零件 螺絲 彈簧 定位銷
PPT文档演模板
冲压模具简介[1]
沖模構成
上模座 下料沖子
固定螺絲
止高塊
刀口固定板
下模座
PPT文档演模板
成型沖子 定位銷 主導柱 成型模仁
主導柱襯套
冲压模具简介[1]
冲压模具简介
PPT文档演模板
2020/11/7
冲压模具简介[1]
目錄
加工範疇 沖模構成 沖模分類 標 準TYPE 模具材料 模具加工 模具組立
PPT文档演模板
冲压模具简介[1]
加工範疇
分離工序: 沖孔 切邊 切斷 落料 成形工序 : 拉伸 壓印 脹型 彎曲
PPT文档演模板
冲压模具简介[1]
沖模構成
模具加工
n 加工機械:
切削加工 鑽床. 車床. 銑床. 鏜床. 刨床
CNC加工中心.
磨削加工
手搖磨床. 平面磨床. 外圓磨床. 治具磨床. 光學磨床
電解加工 放電. 線割
PPT文档演模板
冲压模具简介[1]
模具組立(一)
付導柱襯套膠合 治具定位 定位銷襯套膠合
PPT文档演模板
主導柱干涉配合
主導柱襯套膠合
沖模分類 簡單模
沖子
模柄 模仁
PPT文档演模板
冲压模具简介[1]
沖模分類
圓孔沖子
復合模
頂桿
外形沖子
上脫料板 下脫料板
PPT文档演模板
冲压模具简介[1]
沖模分類 連續模
落料沖子
冲压模具成本分析表(模板)

备 料/hr
钻床加工/hr
磨床加工/hr
精密加工
¥19,152.5 50 12 600
外导向 模具 元件
单 价/个 数 量 金 额
5%材料损耗、人工浪费以及其他费用支出
核 准:
审 核:
制 表:
开料尺寸 0.2*20*10 设计成本/元 ¥1,665.0 材料成本/元
¥9,321.3
加工成本/元
¥25,299.0
配件费用 ¥6,080.0 ¥44,480.00
冲压模具成本分析表
基本资料 设计费用 客户名称 基本工资/hr 45 模板名称 上模座板 上 垫 板 上 夹 板 材料费用 脱 背 板 上 脱 板 下 模 板 下 垫 板 下模座板 冲 头 料 入 块 料 加工费用 基本工资/hr 40 CNC 加工 单 价/hr 时 间/hr 金 额/元 单 价/套 数 量 金 额 长 350 300 300 300 300 300 300 350 100 100 4 120 10 1200 580 4 2320 放电 加工 产品编号 产品工艺/hr 1 材料规格 宽 300 180 180 180 180 180 180 300 100 100 高 45 22 22 22 22 22 22 50 60 22 4 单 价/hr 时 间/hr 金 额/元 单 价/套 数 量 金 额 产品名称 设 计/hr 32 材 质 45# SKD11 SKD11 SKD11 SLD SLD SKD11 45# SKH-9 SKH-9 铣床加工/hr 4 45 5 225 320 8 2560 弹簧 月估产量 20KK 设计审查/hr 1 数量 1 1 1 1 1 1 1 1 1 单位 件 件 件 件 件 件 件 件 件 件 4 线割及其他 加 工费用 Hr 模具寿命 100KK 设计修改/hr 1 重量kg 42.5 12.0 12.0 12.0 12.0 12.0 12.0 46.7 5.6 0.0 模具工序 1 审 图/hr 1 材料单价 kg/元 22.0 55.0 55.0 55.0 80.0 80.0 55.0 22.0 210.0 210.0 组 立/hr 32 mm2 热处理 模具名称 连续模 出 图/hr 1 加工费用/元 315.0 162.0 162.0 162.0 162.0 162.0 162.0 315.0 30.0 0.0 试 模/hr 12 单 价/kg 重 量/kg 金 额/元 固定销 及其它 单 价/个 数 量 金 额 使用设备 高速冲床 共计时间/hr 37 金 额/元 1250.0 819.8 819.8 819.8 1118.7 1118.7 819.8 1343.5 1211.4 0.0 共计时间/hr 60 30 77.4 2321 40 15 600 配件费用 ¥6,080.0 ¥44,480.00 ¥25,299.0 加工成本/元 ¥9,321.3 开料尺寸 0.2*20*10 设计成本/元 ¥1,665.0 材料成本/元
冲压模具各大模板的作用

冲压模具各大模板的作用
冲压模具由几大模板组成,各大模板的作用又是什么,还记得吗?今天,让小编我带大家回顾一遍吧!
冲压模具由8大模板组成,分别是:上模座、上垫板、上夹板、脱背板、脱料板、下模板、下垫板、下模座。
上模座作用:
1.固定上夹板和上垫板在一起。
2.在模具冲切/成形时承载上垫板传递的冲裁(成形)力。
上垫板作用:
1.承载夹板上冲子的作用力。
2.保证弹性元件有足够的压缩距离。
3.上模座的硬度小于上垫板,故上垫板还起到保护上模座。
上夹板作用:
1.固定冲子
2.确保冲子的位置。
3.保证弹性元件有足够的压缩距离。
脱背板作用:
1.承载压料(成型)力。
2.保护脱料板。
脱料板作用:
1.冲子导向.
2.压料/脱料作用。
下模板作用:
1.固定刀口
2.确保刀口的位置。
注:落料:刀口的形状要与产品的实际要求相符。
冲孔:(冲子与产品的实际要求相符)刀口的形状与冲子的形状相似性良好,四周均匀地按产品的材质及料厚放出合理间隙。
下垫板作用:
1.承载下模板上刀口冲切的冲击力。
2.下模座的硬度小于下垫板,下垫板还起到保护下模座。
下模座作用同上模座。
现在,大家对冲压模具的各大模板是否已经记忆犹新了吧!。
0.1mm薄壁不锈钢高速冲压模具设计与制造

0.1mm薄壁不锈钢高速冲压模具设计与制造刘钧良;张光宇;褚雁鹏;唐政馨【摘要】介绍了N2光驱中压盘簧片的高速级进冲模的结构设计及特殊的加工工艺方法.【期刊名称】《模具制造》【年(卷),期】2011(011)005【总页数】3页(P22-24)【关键词】压盘簧片;高速冲压;模具结构;设计制造【作者】刘钧良;张光宇;褚雁鹏;唐政馨【作者单位】中国华录松下电子信息有限公司模具部,辽宁,大连,116000;中国华录松下电子信息有限公司模具部,辽宁,大连,116000;中国华录松下电子信息有限公司模具部,辽宁,大连,116000;中国华录松下电子信息有限公司模具部,辽宁,大连,116000【正文语种】中文【中图分类】TG385.2当前社会的发展趋势是向着节能降耗、少投入多产出的方向发展。
研制高速冲模正是为适应这种发展要求,在激烈的市场竞争中立于不败地位,提高自主创新的竞争能力。
图1所示零件是一个平板类零件,壁厚0.1mm,材SUS301-CSP 3/4H(不锈钢),孔径要求较高,表面要求无压痕,产量为1,800万/年。
对于0.1mm壁厚的不锈钢零件,如果模具精度不够,掉渣现象严重,会造成表面压痕严重,无法保证零件的设计要求。
综合以上分析,决定设计高精度的高速冲模,以满足薄壁、高精度、无压痕、产量大的要求。
图2为该零件的排样图,首先冲导正钉孔,接着冲小孔,冲裁,校平,冲裁,出件。
模具结构如图3所示,从模具结构来看,导柱、导尺、浮料钉、误送料钉等都与普通模具与普通冲模结构有很大差异,下面对具体结构做一下详细说明。
图4所示滚动导柱是用卸料板固定的,该结构可以减小导柱的悬臂长度,根据力学计算公式,导柱挠度δ=WL3/48EI(δ——挠度,W——总载荷,L——悬臂长度,E——弹性模量,I——转动惯量),导柱的挠度与导柱长度的3次方成正比(见图5简化原理图),所以卸料板导柱固定形式大大地减小了导柱的变形误差,从而有效地提高了模具精度。
精密冲压模具项目评估报告参考范文

精密冲压模具项目评估报告参考范文一、项目背景精密冲压模具是冲压行业中的关键工具之一,广泛应用于汽车、电子、航天、家电等领域。
随着现代工业的快速发展和市场对产品质量和效率的要求不断提高,精密冲压模具市场需求也在增加。
本报告对开展一项精密冲压模具项目进行评估,为决策者提供参考。
二、项目概述本项目旨在开发并生产高质量的精密冲压模具,满足市场对各种精密冲压产品的需求。
项目主要包括市场调研、技术研发、设备采购、生产制造、销售推广等环节。
三、市场分析1.行业发展态势:随着汽车、电子等领域的快速发展,精密冲压模具市场出现了巨大的增长空间。
2.市场需求:精密冲压模具广泛应用于汽车零部件、手机零件、航天器件等各个领域,市场需求量大。
3.市场竞争格局:目前市场上存在一些精密冲压模具供应商,但绝大部分产品技术水平有待提高,市场竞争激烈。
四、项目投资估算1.市场调研费用:50,000元2.技术研发费用:100,000元3.设备采购费用:300,000元4.厂房建设费用:200,000元5.人员招聘与培训费用:150,000元6.原材料采购费用:200,000元7.其它费用:100,000元总投资估算:1,000,000元五、项目预期收益和风险评估1.预期收益:市场需求量大,预计项目开始运营后,能够迅速满足市场需求,获取稳定的销售收入。
预计年销售收入为500,000元。
2.风险评估:市场竞争激烈,项目面临多种风险,如市场需求不稳定、技术难题等。
同时,原材料价格波动可能导致成本增加,影响项目利润。
六、项目实施方案1.市场调研:调研市场需求、竞争对手情况,为后续产品开发提供参考。
2.技术研发:组建专业研发团队,进行精密冲压模具的技术开发,提高产品质量和生产效率。
3.设备采购:根据项目需求,选购符合技术要求的精密冲压模具设备。
4.生产制造:建立完善的生产流程,确保产品质量和产能,并提高生产效率。
5.销售推广:开展有效的销售推广活动,拓展市场份额,提高产品知名度和竞争力。
冲压模具成本分析表(模板)资料讲解

300 180 22
SKD11
1
件 12.0
55.0
材料费用
上脱板
300 180 22
SLD
1
件 12.0
80.0
162.0 162.0
819.8 1118.7
下模板
300 180 22
SLD
1
件 12.0
80.0
162.0
1118.7
Байду номын сангаас
下垫板
300 180 22
SKD11
1
件 12.0
55.0
162.0
材质
数量
单位 重量kg
材料单价 kg/元
加工费用/元
金 额/元
上模座板
350 300 45
45#
1
件 42.5
22.0
315.0
1250.0
上垫板
300 180 22
SKD11
1
件 12.0
55.0
162.0
819.8
上夹板
300 180 22
SKD11
1
件 12.0
55.0
162.0
819.8
脱背板
金 额/元 2321
单 价/套
580
单 价/套
320
单 价/个
50
单 价/个
40
模具配件
外导向 元件
数量
4
内导向 元件
数量
8 弹簧
数量
12
固定销 及其它
数量
15
金额
2320
金额
2560
金额
600
金额
600
冲压模具试模报告模板

冲压模具试模报告模板一、试模目的说明试模的目的是什么,例如:检查模具的制造质量、验证模具设计是否合理、确认模具的寿命等。
二、试模条件1.材料:说明试模所使用的材料种类和规格。
2.轧辊:说明轧辊的直径、柔度和工作状况。
3.润滑:说明使用的润滑剂种类和润滑方式。
三、试模装置1.模具尺寸:列出模具的尺寸和毛坯的尺寸。
2.模具材料:说明模具所使用的材料种类和规格。
3.模具结构:用文字或图纸简要描述模具的结构。
4.模具制造:说明模具的加工工艺和加工精度。
四、试模流程1.试模前准备:检查模具和轧辊是否清洁,调整模具的位置和固定方式。
2.试模过程:按照设定的参数进行模具试模,包括试模速度、模具的运动轨迹等。
3.试模结果:记录试模过程中的问题和异常情况,记录试模的周期和次数。
五、试模结果1.表面质量:对试模的毛坯进行外观检查,包括表面是否有划痕、变形等。
2.尺寸精度:对试模的成品进行尺寸测量,检查尺寸是否符合要求。
3.模具使用寿命:记录试模过程中模具的使用寿命,包括可以试模的次数和模具的损耗情况。
六、试模结论根据试模结果,给出对模具的评价和结论,例如:模具质量良好,符合设计要求,或者模具存在一些问题,需要进行修复或改进。
七、优化建议针对试模过程中出现的问题,提出合理的优化意见,包括调整模具的结构、改变模具材料、修改模具的加工工艺等。
八、试模总结对整个试模过程进行总结,包括试模的目的是否达到、试模结果的准确性和稳定性等方面进行评价。
以上是一个冲压模具试模报告的简单模板,可以根据实际情况进行修改和完善。
在撰写报告时,要注意提供足够的数据和细节,客观地记录试模过程和结果,以及给出合理的结论和建议。
冲压模具设计参考模板1

冲压与塑料成型设备(课程设计)题目 XXX模具设计班级机电模具ZB421301 姓名拉尔木吉指导教师魏良庆目录第一章止动片冲压工艺分析及模具设计 (3)1.1设计零件 (3)1.2冲压件工艺分析 (3)1.3冲压工艺方案的确定 (3)1.4模具结构形式的确定 (4)1.5排样设计 (4)1.6冲压力的计算 (6)1.7压力中心的计算 (7)1.8初选压力机 (9)第二章模具总体设计 (10)2.1模具类型的选择 (10)2.2定位方式的选择 (10)2.3卸料方式的选择 (10)2.4出件方式 (11)2.5确定送料方式 (11)2.6导向方式的选择 (11)第三章模具工作部分尺寸计算 (12)3.1工作零件刃口尺寸计算 (12)3.2卸料装置中弹性元件的计算 (14)第四章主要零部件设计 (17)4.1工作零件的结构设计 (17)4.2其它模具零件结构尺寸 (23)4.3模架的选用 (27)4.4其它标准零件的选用 (31)第五章压力机的校核 (35)第六章模具的装配总图 (36)第一章止动片冲压工艺分析及模具设计1.1设计零件图1-1为止动片制件,材料为20,厚度为3mm,大批量生产。
试设计图1-1 止动片零件图相应的模具及其主要的零部件,工件结构分析、工艺分析、模具方案的论证、进行总体结构设计、制定主要件的工艺规程、必须的工艺计算、制造工艺以及一定的技术经济分析等。
1.2 冲压件工艺分析(1)材料:该冲裁件的材料Q235-A是普通碳素钢,具有较好的可冲压性能。
(2)零件结构: 零件结构简单对称,无尖角,外形有多处圆弧,中间有一个圆孔,孔的最小尺寸24mm,满足冲裁最小孔径Dmin>=10t=12mm的要求,成型后须保证各尺寸公差要求。
顶部和底部各有三个孔,孔的最小尺寸7mm,孔与边缘的最小壁厚为10mm ,孔与孔之间的最小距mm 12.025±,满足冲裁件最小孔边距m m 35.1min =≥t l 的要求,满足许用壁厚要求,因此,该制件具有良好的冲压工艺性,比较适合冲裁。
冲压模具[1]
![冲压模具[1]](https://img.taocdn.com/s3/m/edbf71a84431b90d6d85c75a.png)
一、材料的合理利用
1.材料利用率
材料利用率: 冲裁件的实际面积与所用板料面积的百分比, 它是衡量合理利用材料的经济性指标。
一个步距内的材料利用率
A——一个步距内冲裁件的实际面积 B——条料宽度 s——步距
PPT文档演模板
冲压模具[1]
第二章 冲裁工艺与冲裁模设计
第五节 冲裁排样设计
PPT文档演模板
冲压模具[1]
第二章 冲裁工艺与冲裁模设计
第五节 冲裁排样设计
三、搭边和条料宽度的确定
3.搭边值的确定 表2.5.2(P65)为最小搭边值的经验数表之一,供设计时参考。
PPT文档演模板
冲压模具[1]
第二章 冲裁工艺与冲裁模设计
第五节 冲裁排样设计
三、搭边和条料宽度的确定
条料宽度的确定
冲压模具[1]
第二章 冲裁工艺与冲裁模设计
四、条料宽度与导料板间距离的计算
3.用侧刃定距时条料的宽度与导料板间距离 条料宽度:
导料板间距离:
PPT文档演模板
冲压模具[1]
第二章 冲裁工艺与冲裁模设计
第五节 冲裁排样设计
五、排样图
一张完整的排样图应标注条料宽度尺寸、 条料长度L、板料厚 度t 、端距L、步距S、工件间搭边和侧搭边a。并习惯以剖面线表 示冲压位置。
冲压模具
PPT文档演模板
2020/11/7
冲压模具[1]
第二章 冲裁工艺与冲裁模设计
第五节 冲裁排样设计
排样: 冲裁件在条料、带料或板料上的布置方法。 合理的排样: 提高材料利用率、降低成本,保证冲件质量及
模具寿命的有效措施。
排样方案是模具结构设计的依据之一。
PPT文档演模板
- 1、下载文档前请自行甄别文档内容的完整性,平台不提供额外的编辑、内容补充、找答案等附加服务。
- 2、"仅部分预览"的文档,不可在线预览部分如存在完整性等问题,可反馈申请退款(可完整预览的文档不适用该条件!)。
- 3、如文档侵犯您的权益,请联系客服反馈,我们会尽快为您处理(人工客服工作时间:9:00-18:30)。
注意点:1)一般先裁边,冲导正,打预断,压线,打凸点,撕口,(切口,拉伸),后冲孔落料,压毛边,成形,分两步折弯的,先成形一半,后成形另一半2)在冲孔落料时,一般先冲小孔,后冲大孔;先冲落成形周边的废料,再落其它部位的余料:因為冲小孔若放在后面,那麼它在冲裁时,冲子四周对应料带上的部位可能有缺口(前面已冲过的孔),这样,冲子在冲压过程中,将会引起受力不均(会產生侧向力),本来小孔冲子强度很弱,加之受力不均,极容易折断,当然这仅是大多数情况,有时根据实际情况需要,小孔冲隻能排在后面,不过办法还是有的,如果冲子厚度实在太小,可入行补强:A:採用脱板精密导向;B:冲子採用PG(光学研磨)加工.4:确定是否采用裁边:裁边一般用在连续模和落料模上,它的作用起粗定位,在试模时便于送料;有的裁边还兼有冲外形的作用,如果模具先冲定位针孔,接著马上用引导针导正,一般不用裁边了;没有引导针的,要先裁边,用来定距,一般用在落毛胚的落料模中.裁边的冲子形状有以下几种﹕a:这种冲子常用於落料模和厚材裁边中,定位精度低,它的长=步距,宽隻要保証冲子强度即可,常取3.0~6.0b:这种冲子头部有一个3/4的圆弧(R常取0.3~0.6),它的长<=步距,目的裁边废料卡在裡面,防止跳屑,常用於冲薄材高速模具c;这种冲子同B一样,是它的变羿,其中V形的作用用来卡隹裁边废料防止翻转跳屑,它的角度為50°~70°d:这种冲子既裁边又兼落外形.这种台阶头部目的起导向作用,减少侧向力.5:预断,将要断,但未断的意思(一般放在工站前面)由於小五金电子產品往往有电镀要求,為电镀方便,冲出来的小產品并不直接落料,而是打个预断留在料带上,电镀后,再用手或机械折两下即可取下来.预断:两面都要切,每边切进的深一般為材料厚度的4/1,这样隻需折两下(往上-往下)就可以產品摘下来;预断冲子和入子头部的宽度為0.02~0.05,角度50°~70°,其长度比预断线的长度每边大0.2~0.5即可.说明:為了便於加工和备料以及校模,一般每个厂的各块模板的厚度实行了标準化,厚度大小都规定了(特殊情况除外),在连续模中由於是料带的形式,為了方便控制料带的预压量和模板的平衡性,常在脱料板中间磨出一个料带槽:其槽的深度=材料厚度-0.03~0.05(也就是说预压量為3~5条),槽的宽度比料带的宽度大2~4mm即可.因此脱料板的厚度常随材料厚度变化而变化,其大小=脱料板规定厚度+材料厚度-0.03~0.05不过在工程模中,一般不需磨產品槽:因為工程模產品一般较大而不像连续模料带那样窄而细长,也就是说工程模脱料板厚度一般不变. 6:确导正孔的大小及位置一般的连续模都要冲导正,以便后工序的精确定位,在工程模中常用產品零件上的内孔或外形来实现下一工序的定位,若既无内孔,外形又不能用来定位,那麼隻得借助工艺孔了:如第一工程打凸胞,第二工程落外形这种情况,那麼隻好在第一工程中在外形的对角同时冲两个工艺孔(孔大小与材料厚度有关:常用?3.0~6.0)以便下一工序的定位高速冲压模具设计知识(1)第一步:產品图的公差缩放缩放原理:由于產品冲出来之后,总是存微小的毛边:其内孔一般偏小,外形一般偏大,至于毛边的大小,与冲裁间隙和冲子,刀口的锋利程度有关:冲裁间隙越大,毛边俞大,冲子,刀口钝化后,毛边也会增大,故冲子,刀口冲了一定的时间后,常常需要将刃口磨去0.3~1.0,其毛边到底大多少也与材料厚度有关:一般薄材(T<=0.5)双边大0.01~0.02,厚材(T>0.5)大0.01~0.05第二步:產品图的尺寸展开展开原理:利用体积不变的原则:用某一截面的总面积去除以材料厚度可得到该方向的展开长度,其实展开就是同一尺寸也因各人经验而羿,没有绝对的一个数值,只要在公差范围即可. 展开要点:步骤如下1:看懂產品图,想象出它的立体形状以及详细细节的形状(展开前的基本要求)2:弄清楚產品的材厚和材质3:具体展开计算1):用体积法(一般适合有变薄的弯曲)2):用展开计算公式由于產品在弯曲过程中有的地方被拉长或压缩但总可以找到某一层的弯曲线长度是不变的,这一不变的层叫中心层(不是中间层),我们就是利用中心层来进行展开的;因此,我们要想入行展开,就必须找出中心层,如图2设中心层系数為K,弯曲内半径為r,材料厚度為t,弯曲角為a,L1,L2為直线部分长度,展开长度值為L,,那麼则有L=L1+L2+2π(r+kt)a/360中心层系数K的大小根据实践经验可按下列公式选取1):当r/t<=0.50时 k=0.252):当0.5<r/t<=1.0时 k=0.25~0.303):当1.0<r/t<=2时 k=0.30~0.354):当2.0<r/t<=4时 k=0.35~0.405):当r/t>4.0时 k=0.40~0.50此公式适合一切材料厚度的弯曲展开计算,具体在实践应用中,当R/t取上限时, K也应取上限值,如当R/t=1.0时,K=0.304:当包圆时,此时展开计算公式已和上面不一样,因為包圆时,内圆受到挤压,外圆被拉伸,但挤压大於拉伸,所以材料变薄很小,或者几乎不变,中性层接近中间层其展开长度中心层K的系数与材料厚度和包圆内r有关1):当r/t<=3.0时,中心层系数K=0.45~0.552):当3.0<r/t<=6.0时,中心层系数K=0.55~0.653):当6.0<r/t<=15.0时,中心层系数K=0.65~0.704):当15.0<r/t<=30.0时,中心层系数K=0.70~0.505):当r/t>30.0时,中心层系数K=0.505:通过查表,找出中心层系数的大小,再进行展开计算也行,在此不作详细叙述6:產品的圆角处理:產品上的圆角一般保持不变它,但若是尖角,当t<=0.5时,一般用最小圆角R0.15去拟化它;当t>0.5时,用最小圆角R0.2~0.3去拟化它,对于產品上R0.1的圆角,尽量用R0.15去代替;对于R<0.1的圆角或清角,如果是重要尺寸(改变会影响功能)则不变它,採用过切来达到要求.第三步:料带排样设计排样原理:一根料带经过冲孔落料压毛边拉伸抽蕊弯曲成形各个工序,最后形成產品的过程,现在你做的如何组织这些工步:哪个在前,哪个在后,总共要多少工步,各工序之间互相调协,使其承前继后,合情合理排样设计:步骤如下1:确定產品展开尺寸后,根据產品的毛边方向,确定冲裁和成形方向,无毛边要求时一般不受限制;若產品上有毛边方要求时,这时一定要注意它的冲裁和成形方向:向下还是向下成形)冲孔毛边留在刀口面,落料毛边留在冲子面:一般机箱外壳类零件出于使用美看和安全性能要求,其毛边要留在產品的里边(成形的内边)如果图纸上有毛边要求时,则要按要求去做,没写毛边要求应尽量让毛边留在裡边,若成形更方便,也可留在外边.2:依据產品展开尺寸,粗畋估算步距(PITCH=產品该方向最大长度+1.0~2.0-中间有连接带除外)用ARRAY命令作出横排,纵排,对称排,交错排,斜排(很少用)几种方案,进行分析,比较,综合,在保証產品顺利生產出来的前提下,选择最佳方案.具体注意以下几点:1):第一要考虑这样排成形是否容易和稳定,后一工步是否对前一工步已成形好的產生破坏作用,或者后一工步无法成形,冲子和渗透子强度是否足够2):第二要考虑料带在模具中能否顺利送料,前一工步成形之后能否继续平稳送到下一工步包括考虑浮升高度和连接带的位置及强度浮升高度越低越好,一般不起过下模板厚度的1/2:因為太高易引起摆动,料带定位不淮和变形;连接带(又叫载体-CARRY)有以下几种形式:1>:无连接带,属於无废料排样,零件外形往往具有对称性和互补性,通常採用单PIN切断落料或双PIN一个落料一个切断,2>:边料连接带,是利用条料搭边废料作為载体的一种形式,这种载体传送料带强度较好,简单,主要用於落料型排样中,3>:单连接带,是在產品条料的一侧留出一定宽度的材料,并在适当位置与產品相连接,实现对產品条料的运送,一般适合切边型排样,4>:双连接带,是在產品条料的两侧分别留出一定宽度的材料,并在适当位置与產品两边相连接,实现对產品条料的运送,它比单连带运送更顺利,料带定位精度更高,它适合產品两端都有接口可连,特别适合材料(t<=0.4)较薄时,料带运送强度较弱的情况5>:中心连接带,与单载体相似,是在產品条料的中间留出一定宽度的材料,并与產品前后两边相连它比前者节省材料,在弯曲工件排样中应用较多;因為导正梢孔在中间常引起拉料,故常需在引导针中间交错加一些弹性顶料定位针,连接带的选取总结如下:產品展开之后,仔细分析產品的各个部位,哪些地方需要成形,哪些地方是仅仅落料,然后在落料的地方选择恰当的位置引出连接带,使之既能保証料带的平稳运送,又不影响產品的成形;至於选择什麼类型的连接带,要根据產品的特点而定. 确定產品展开尺寸后,根据產品的毛边方向,确定冲裁和成形方向,无毛边要求3):第三当碰到L形弯曲或產品单排时材料利用率太低,可考虑对称排交错排,这样对称成形受力均匀,成形稳定;或者材料利用率可大大提高4):第四要考虑冲裁PIN数和步距(主要针对接插件类小端子產品,一般五金外壳类或较大工件為单PIN).5):第五要考虑材料利用率,尽可能提高材料利用率,降低生產成本3:确定排样方案后,这时应该对整个產品冲压和成形过程有一个基本的认识,怎样去安排这些工序的先后关系,应做到心中有数:即先冲哪里,后冲哪里,先成形哪步,后成形哪步,以及某一成形工序能否一次成形出来还是分两步导正孔的大小选择在前面表一已经说明了,其位置一般放在连续带上,有时放在废料上到最后时随废料一起冲掉;一般一个步距一个导正孔或几PIN几个导正孔.7:冲子刀口设计制作冲子刀口:对於连续模,就是把料带上废料部分冲掉,留下来的產品的展开外形和连接带;对於工程模,一般来讲,就是冲孔落料.下面主要针对连续模来讲.用產品展开图排出料带成形方案后,接下来就是如何安排这些工步,一般先打凸点,打预断,冲导正,撕口,落料,再压毛边,成形.由於產品的形状常常奇形怪状,其展开图形状也必然不规则:可能有的地方有凹进去很深的狭槽,如果整个外形落料冲子做成一个整体,那麼在该冲子部位可能常常发生崩柝;可能有的地方有凸出来很长的悬壁,那麼在该部位的刀口强度肯定不够;有的地方要求是尖角,事实上刀口冲子割出来不可能是百分之百的尖角,总存在一个最小R值(通常是R0.15);还有的是為了保持后一工步成形的稳定性(增大压料面积),而先切去一部分,成形后,再切另一部分因此,為了解决上述问题,就必须进行刀口分解,把那些薄弱的地方单独分离出来做成不同的刀口,用2个或2个以上的工步先后互切来完成整体外形落料,分解时注意以下几点﹕1):对于產品上要求必须是尖角的部分,此时必须采刀口互切2):对于產品上某条轮廓直线边有较严的公差要求(<=%%P0.05)时,一般不得在该直线上有刀口接头3):分解出来的冲子形状简单,尽量采用普通研磨或线割加工4):分解出来的冲子要有一定的强度,尽量减少PG加工,如有空地方,尽量做大一点5):对于互切刀口採用相交(一般是直线与直线或直线与圆弧)或圆弧60~75%%D处作切线相交的互切方式(直线与圆弧),有时也採用圆弧相切(圆弧与圆弧)或重合相切,其互切直线长度(一般0.3~0.5不包括两者圆弧)不宜过长,过长会產生粉屑:其目的是不要產生过大的毛头,影响產品尺寸和美看6):注意刀口冲子上的圆角处理:通常线割min圆角為R0.15,也可以割R0.1的圆角但需要换铜丝(成本增加),故不重要的圆角尽量把它到R0.15,或更大R0.2~0.3,但是不能把它的功能尺寸改变:其刀口冲子上的圆角必须表示出来或者加说明未注圆角R為多少,至于脱板夹板转角处圆角既可以画清角,也可以和刀口一样,它仅仅起定位作用,线割时,它会自动清角.对于小R0.1的圆角采用PG加工.8:刀口镶块的(通常鸣入子)大小设计制作:1)做入子的目的:其主要目的是方便维修:由於许多精密五金件大都有毛边要求,不得超过其规定值,而模具在冲压一段时间后,冲子和刀口因经常互相磨擦刃口发生钝化,变得不锋利,导致毛边加大.如果做入子,发现哪裡毛边偏大隻需把该处冲子刀口折下在刃口磨0.2~0.5,再在其背面垫上相应厚度的垫片即可.如果不做入子,那麼整个模板要折下来,再在刀口面磨一定的高度,这样维修起来比较麻烦且降低模具的寿命;另外在连续模和工程模中,那些易崩裂的刀口和產品上某处尺寸要求很严时,可在该处做入子,这样方便维修.不过,并不是所有的模具做渗透子,因為一做入子,模具的成本,将会增加1.5~3倍,因此具体情况还要看產品的要求精度以及生產批量和模具类型.下面简要说明要不要做入子的情况:1>高速精密冲床模具(冲速>150次/每分鐘 ,如端子模)脱板下模一般要做渗入渗出子,夹板可做可不做发,建义(从节约成本出发):不做2>普通连续模:如果生產批量较大时,下模一般要入子,其它两板不做入子;生產批量较小时,下模可以不做入子;如果產品上某处尺寸要求经常变动或特严或展开很难把握和易崩裂的刀口部位,可在该处设计入子3>工程模:一般不做入子,隻有在那些易崩裂的刀口部位才设计入子2):刀口镶块(入子)大小制作,主要由冲压材料的厚度和硬度以及刀口材料强度决定,入子做得太大,步距排得较鬆,这样会加长模板,同时对模板强度有影响,做得太小,刀口强度又不够,因此要到恰当的数值,既不浪费模板又保証渗透子的强度:实践証明一般入子制作时,刀口最大外形尺寸再往外偏3~6mm,适当取整数就可得到刀口渗入渗出子的大小:对于薄材(T<=0.5),刀口常偏3~4mm;建义:取4mm為佳;厚材(T>0.5),刀口常偏4~6mm,建义:取5.01>模板入子常用材料:夹板渗入渗出子常用SKD11,脱板入子常用SKD11或SKH9(SKH9比SKD11要好),下模入子常用SKD11或SKH9,当大批量冲裁精密细小零件时(如端子)也可虑用双层结构钨钢WC形式(刀口為WC常取4~8mm,垫块為SKD11,其厚度=下模厚度-上层刀口厚度) ﹐注:冲子材料常用:SKD11,SKH9,当冲子过小时(如PG)也可用WC.2>下模入子和夹板渗透子為了防止装反,常进行倒C角处理:C角大小常取C1.0~3.0,脱板入子由於有吊耳存在,可防止装反,一般不倒C角;成形冲子有吊耳或压板槽的存在,也可防止装反,故常不倒C角,成形入子可倒C角注:倒不倒C角,并没严格要求,由设计人员习惯决定,不过对於那些极容易误认為对称而实际不对称的零件必须倒C角处理3>模板入子在线割时,一般先打一穿线孔才能线割,所以在画模板框口和入子时要在冲子刀口封闭线内画一个?0.6~1.5穿线孔标识符﹐功能有两个:A>:这一穿线孔位置可供线切割参考:合理的话,加工人员就在该位置打出穿线孔,不合理,加工人员不一定在该处打穿线孔B>:另一个作用方便设计和组模人员检验和查询内孔和外形之间的相对位置关系以便发现错误,至於这一孔打在那个位置,由刀口大小而定:如果冲子刀口的最小宽度尺寸>10mm,那麼就在离内孔边缘线5mm任一处打一穿线孔标识符减少线割面积,节约成本;如果<10mm就在内孔长宽最大处打一穿线孔标识符,尽量用钻床钻出穿线孔常為%%C3,如果最小宽度尺寸均<4mm,常用打孔机(同放电原理相同)打出穿线孔;如果<0.3,其刀口常採用镶拼式组合而成4>模板入子之间距离的设定:两入子之间距离既不能太大也不能小,太大工站排得鬆散加长了模板尺寸,增加了材料成本;太小模板强度减弱,降低了模具寿命,通常两入子(包括成形入子)之间的距离至少要>1.5,如少於 1.5:要麼割通两入子连在一起,要麼把这一工站排到下一工站去;有时还要考虑料带被抬起的平稳性该位置有必要安装导正浮升梢或顶料梢或浮升块时而该处有没有位置:如没位置,这一工站同样要排到下一工站去5>模板冲子刀口入子加工间隙的确定:a:硬材和碎材:冲子与刀口之间的单边间隙一般取材料厚度的5~7%,常取5%﹐如不锈钢SUS304-1/2H,3/4Hb:软材:冲子与刀口之间的单边间隙一般取材料厚度的3~5%,常取4%如黄铜,磷铜,铝材,不锈钢301c:对於冲压材料厚度<=0.2时,其冲子刀口单边间隙常取0.01,因為再小时受到模具精度的限制d:间隙究竟放在冲子上还是刀口上呢?:对於冲孔,一般以凸模為基準,间隙放在刀口上,对於落料,一般以凹模為基準,间隙放在冲子上;在连续模中一般是冲產品以外的废料部分,相当冲孔,因此间隙放在刀口上,对於单边切断型,相当落料,其间隙放在刀口上,不过这种形式,也可以不放间隙;在冲孔落料复合模中,一般凸凹模,内外脱共用,因此存在间隙回属问题,一般以凹模(又叫母模)為基準,凸模(又叫公模)单边负多少.至於内外脱,其间隙一般以公母模来相配合.至於这个间隙要不要画出来因各厂习惯而羿:有的厂不画出来,冲子和刀口一样大,隻是在刀口旁边加注解说明如:下模入子:单+0.01 T=25.0 SKD11 刀口深2.0以下斜1.0%%d落屑;而有的厂要求直接画出来,隻须写刀口直线位落屑斜度冲子:单+0.0 L=50.5 SKD11下模入子:单+0.01 T=25.0SKD11 刀口深2.0以下斜1.0%%d落屑内外模共用:以外模為基准内模单边-0.01公母模直线位各3.0B>:刀口直线位及落屑斜度:直线位过长和落屑斜度太小时,易出现堵料,直线位过短和落屑斜度太大,双削弱对刀口强度,因此必有一恰当的值,实践証明:对於t<0.8的材料,刀口直线位取2.0,落屑斜度取1°较佳;t>0.8时,刀口直线位取3.0,落屑斜度取1°;对於那些弱小的冲子,為了防止常断,其刀口常採取直接割斜度0.2°不留直线位且刀口常做双层结构,这样减小冲裁力C>:入子(包括刀口入子,成形入子及冲子)内外形间隙的确定由於这些入子或冲子要直接装入模板或入子,因此存在要不要间隙问题,且这个间隙放在模板上还是渗透子外形上:為了画图的方便,一般都习惯把间隙放在模板上,并且这个间隙也不画出来,隻是在加工注解栏裡说明:如羿形孔,单边正多少,有冲子圆孔要在旁边加代号,再在注解栏说明:如F:3-?4.00(冲子孔,割单+0.007),下面就夹板脱板下模渗入渗出子间隙进行说明:a:夹板仅仅起固定冲子或渗入渗出子作用,因此它的间隙取得较大,这样便於装配,如果夹板做入子,入子外形与夹板的单边间隙通常取+0.005~0.01,不做入子,刀口冲子与成形冲子和夹板的单边间隙取+0.005~0.01.b:脱板起导向冲子和脱料作用,因此它的间隙取得较小,如果脱板做渗入渗出子,渗透子外形与脱板的单边间隙通常取+0.003~0.005,不做入子,刀口冲子与成形冲子和脱板的单边间隙取+0.003~0.005.如果冲子与刀口之间的单边间隙>=0.02时,刀口冲子与成形冲子和脱板的单边间隙也可以取+0.005~0.01不过必须保証它的间隙<冲子与刀口的间隙.c:下模板為刀口板,在冲压过程中,冲子和入子存在磨擦力,在分模冲子往上走时,其入子受到一种向上的磨擦力,有一种向上的运行的趋势,為了防止入子带出模面,其入子与模板的单边间隙通常取0.0的紧配合,為了安全起见,下模入子常常还要压隹:究竟要不要压与冲速和冲裁料厚有关,观情况而定.D>:下模渗入渗出子要不要压隹:分几种情况:a:对於高速冲床模具(如端子模),当冲速每分鐘>150次时,下模入子在磨擦惯性力的作用下,极易跳出模面,因此端子模具常用导料板导向,同时起压隹入子的作用,如果入子不够长,要把某方向拉长超过导料板底线0.5~1.0既可,特别对於那些镶拼式或双层式刀口,一定要把它压隹,以防带出模面.导料板压不隹时,可採用以下几种形式:图30-1的刀口入子,导料板都压隹了0.5~1.0,成形入子一般不用压;注意导料板压裁边入子的位置:裁边的目的是用来粗定位,因此导料板要压到裁刀口的尾端线之间的间隙留0.02~0.04即可。