1001.酒精废水处理技术
酒精废水处理工艺

酒精废水处理工艺一、酒精废水生产的特点酒精工业的污染以水的污染最为严重,生产过程中的废水主要来自蒸馏发酵成熟醪后排出的酒精糟,生产设备的洗涤水、冲洗水,以及蒸煮、糖化、发酵、蒸馏工艺的冷却水等。
酒精废水是高浓度、高温度、高悬浮物的有机废水,处理技术起步较早,发展较快。
废液中的废渣含有粉碎后的木薯皮、根茎等粗纤维,这类物质在废水中是不溶性的COD;木薯中的纤维素和半纤维素是多糖类物质,在酒精发酵中不能成为酵母菌的碳源而被利用,残留在废液中,表现为溶解性COD;无机灰分的泥砂杂质。
这些物质增加了废水处理的难度。
二、酒精废水处理工艺3.1 高效全混厌氧污泥罐厌氧反应器采用钢结构,其外形结构类似于第三代厌氧反应器EGSB和IC,能承受高浓度的固体悬浮物(SS),是三代厌氧反应器EGSB和IC不具备的特点,采用高温发酵,容积负荷可高达7.0kgCOD/(m3.d),高于传统全渣厌氧发酵工艺的2~3倍,COD去除率高达90%。
3.2 UASB+缺氧池+接触氧化上流式厌氧污泥反应器(UASB)技术在国内外已经发展成为厌氧处理的主流技术之一,在UASB中没有载体,污水从底部均匀进入,向上流动,颗粒污泥(污泥絮体)在上升的水流和气泡作用下处于悬浮状态。
反应器下部是浓度较高的污泥床,上部是浓度较低的悬浮污泥层,有机物在此转化为甲烷和二氧化碳气体。
在反应器的上部有三相分离器,可以脱气和使污泥沉淀回到反应器中。
UASB的COD负荷较高,反应器中污泥浓度高达100~150g/L,因此COD去除效率比普通的厌氧反应器高三倍,可达80%~95%。
工艺流程如下所示:缺氧池具有双重作用,一是对废水进行生物预处理,改善其生化性,并吸附、降解一部分有机物;二是对系统的污泥进行消化处理。
可以与后续的接触氧化形成A/O模式,具有同步脱氮除磷作用,其中厌氧段主要作用是去除有机污染物和释放磷,缺氧段的主要作用是反硝化脱氮,由于具有同步去除有机污染物、脱氮、除磷作用,因而目前该工艺广泛应用在需要脱氮除磷的污水处理方案中。
污水处理之酒厂废水处理技术

污水处理之酒厂废水处理技术随着酒类产业的不断发展,大量的酒厂废水也随之产生。
这些废水中含有高浓度的有机物、酸性物质和化学物质等有害物质,如果随意排放到周围的环境中,将会对生态环境造成极大的影响。
因此,如何进行酒厂废水的有效处理成为了当前亟待解决的问题。
酒厂废水处理技术需要兼顾经济性、环保性和实用性。
基于这些原则,目前主流的废水处理技术主要包括生物处理、化学处理、物理处理和综合处理四种方法。
其中,生物处理技术由于其经济实用、环保性好的特点,已成为酒厂废水处理的首选技术。
生物处理技术就是通过利用好氧微生物或厌氧微生物对酒厂废水中有机污染物进行降解,最终实现去除废水中有害物质的目的。
对于好氧微生物而言,它们需要在氧气充足的环境中生长和繁殖,而对于厌氧微生物而言,则不需要氧气。
因此,生物处理过程主要分为好氧处理和厌氧处理两个模块。
好氧处理模块通常包括曝气池、活性池和沉淀池。
在曝气池中,通过机械方式将空气导入池中,增加溶氧量,使微生物在其中生长和繁殖。
而在活性池中,则会有大量好氧微生物与厌氧微生物降解酒厂废水中的有机物质。
这些微生物会利用有机物质作为碳源和能源进行生长繁殖,同时将有机物质转化为二氧化碳和水。
最后,在沉淀池中,将处理后的水进行沉淀,将沉淀下来的污泥进行回收与处理,形成可再利用的有机肥料。
厌氧处理模块通常包括厌氧池和生物反应器。
在厌氧池中,阻止氧气进入,利用厌氧微生物对有机物质进行分解,形成乙醇、有机酸、酮类等化合物。
而在生物反应器中,则会再将这些化合物进一步转化为沼气等可再生能源。
除了生物处理技术外,化学处理也是一种可行的酒厂废水处理方法。
它主要依靠化学方法将废水中的有害物质转化为无害物质,比如利用氧化剂氯气将酒厂废水中的有机物较彻底地氧化成二氧化碳和水。
但这种技术的处理成本较高,一般只在废水处理后期或废水中含有有毒重金属等不易降解有害物质时使用,常见的方法还有膜法和吸附法等。
物理处理技术则主要通过物理操作对酒厂废水进行处理,例如深度过滤、离子交换和超滤等技术。
酒精废水处理技术

酒精废水处理技术工业化酒精生产作为我国重要的产业, 其废水的处理和资源化利用一直受到人们的广泛关注.在酒精生产过程中的废水主要来源于蒸馏馏出液, 设备清洗液, 冷却液以及酒精漕液等工序, 含有较高浓度的有机物和悬浮物, 可生化性良好.目前对于蒸馏馏出液, 酒精漕液的处理一般采用厌氧发酵-好氧氧化的处理工艺, 而对于设备清洗液, 冷却液等则需要通过处理后回用.由于原料中的含氨基团在发酵中的脱落, 所以设备清洗废水, 冷却废水在含有一定量的有机物及悬浮物的同时, 也含有较高浓度的氨氮.而对于这部分废水的处理, 运用传统的脱氮方法需要较高成本的投入, 并且面临着污泥处置等问题.近年来, 厌氧氨氧化(ANAMMOX)技术的发展, 为解决这一问题提供了一个切实有效的方法.该技术具有耗能低, 效率高, 无需要添加有机碳源, 污泥产量低等诸多优点, 适用于许多高氨氮废水的处理.而ANAMMOX反应需要氨氮和亚硝氮作为反应基质, 所以通常通过前置短程硝化(PN)组成PN-ANAMMOX联合工艺来实现氮素的去除.目前, ANAMMOX技术成功运用于多种有机含氨废水的处理, Dosta等采用分体式PN-ANAMMOX处理污泥消化液, 在进水C/N比为0.5的条件下达到了1kg·(m3·d)-1平均总氮去除速率; 王凯等利用SBR短程硝化联合ASBR厌氧氨氧化处理垃圾渗滤液, 进水BOD5在50~80 mg·L-1, 总氮去除速率可以达到0.76 kg·(m3·d)-1且进水中难降解COD不会对ANAMMOX菌产生影响.可以看出, 利用ANAMMOX技术处理此类有机废水, 可以获得较高的总氮去除速率, 且更多地是用分体式反应器实现亚硝化、厌氧氨氧化的联合.而目前, 利用PN-ANAMMOX处理酒精废水的报道较少, 在一体式PN-ANAMMOX反应器内处理酒精废水更是鲜见报道.因此, 本文以酒精废水作为NH4+-N源, 研究其对一体式PN-ANAMMOX反应器的影响, 以及长时间运行下, 在一体式反应器内能否通过参数调控和ANAMMOX反应阶段的驯化, 协同异养菌、亚硝化菌和ANAMMOX菌, 实现氮素和有机物的同步去除, 通过拓宽ANAMMOX运用领域, 以期为该行业处理回用废水提供参考依据.1 材料与方法1.1 实验装置反应装置由有机玻璃制成, 如图 1所示, 总有效体积3.62 L, 主要包括部分好氧区2.8 L, 厌氧氨氧化区0.23 L和沉淀区0.59 L.其中厌氧区出水通过回流装置回流至好氧区.进水方式由兰格蠕动泵控制为稳定连续流, 运行温度在32℃左右, 反应器整体pH控制在8.0左右.图 1 一体式PN-ANAMMOX联合工艺流程示意1.2 接种污泥好氧区接种的亚硝化生物膜来源于实验室的亚硝化反应器.厌氧区接种的厌氧氨氧化颗粒污泥源于实验室长期运行的厌氧氨氧化种泥反应器, 平均粒径1.5mm, 污泥性状较好, MLVSS/MLSS=0.67.1.3 反应器进水水质以酒精废水为研究对象, 酒精废水取自连云港某以木质素为原料的酒精生产厂, 并经过三级厌氧甲烷化处理, 其主要水质指标如表 1所示, 处理出水氨氮小于300 mg·L-1即可达到回用要求.表 1 废水主要水质指标1)部分进水为人工模拟废水, 其中NH4+-N, NO2--N由NH4Cl和NaNO2提供, 以及微量元素浓缩液(mg·L-1):5000EDTA, 5000 MnCl2·H2O, 3000 FeSO4·7H2O, 50 CoCl2·6H2O, 40 NiCl2·6H2O, 20 H3BO3, 20 (NH4)2MoO4, 10 CuSO4, 3ZnSO4, 添加量为1mL·L-1.进水中加入碳酸氢钠调节pH并作为缓冲剂.1.4 实验方法1.4.1 PN-ANAMMOX反应器的启动采用人工配水, 通过提高进水氨氮浓度和缩短水力停留时间(HRT)交替的方式提高反应器的氮容积负荷.进水氨氮的浓度从150 mg·L-1逐渐提升到430 mg·L-1左右, 保持反应器整体pH 7.8±0.5, 温度30~35℃, 好氧区ORP值120~150mV, 通过测定进出水氮素指标的变化, 评估PN-ANAMMOX反应器的运行状况.1.4.2 酒精废水对PN-ANAMMOX的影响实验进水先采用固定NH4+-N浓度400 mg·L-1左右酒精废水(稀释50%, 可生物降解TOC约50 mg·L-1), 逐步添加0、20、50 mg·L-1的TOC(葡萄糖), 使可生物降解TOC恢复至原酒精废水中的浓度水平, 通过反应器总氮去除速率及各区域的氮转化速率, 评估原酒精废水中可生物降解TOC对PN-ANAMMOX反应器的影响.在反应器受到较大影响之后, 将进水改为人工配水, 加入100 mg·L-1的TOC, 通过前后反应器总氮去除速率的变化, 判断酒精废水中惰性有机物及其他物质是否对PN-ANAMMOX产生影响.1.4.3 驯化实验先采用稀释度为20%的酒精废水作为进水(避免高浓度有机物冲击), 调控HRT, 以20%的酒精废水作为进水, 氨氮浓度在160 mg·L-1左右, 所以HRT先经过缩短, 待反应器运行稳定之后, 逐步采用稀释度为50%, 100%的酒精废水作为进水并适当提高PN阶段溶解氧, 而以50%和100%的酒精废水作为进水, 氨氮浓度在400 mg·L-1和800 mg·L-1左右, 故需将HRT逐渐延长, 测定进出水氮素的变化, 探究此过程中是否可以通过参数的调控, 协同异养菌、亚硝化菌和ANAMMOX菌, 实现氮素的去除.1.5 计算方法因联合工艺具有回流特征, 所涉及到的亚硝化菌和厌氧氨氧化菌的氮素转化效能计算公式如下:(1)(2)(3)(4)式中, ΔN表示进出水总氮的差值, mg·L-1; NH4+-Ninf表示进水NH4+-N浓度mg·L-1; NH4+-Neff、NO2--Neff、NO3--Neff表示出水NH4+-N、NO2--N和NO3--N浓度, mg·L-1; HRTa、HRTana和HRTT表示好氧区、厌氧区和联合工艺总的HRT, d; NPRa表示好氧区NO2--N生成速率, kg·(m3·d)-1; NRRana和NRRT表示厌氧区ANAMMOX脱氮速率和联合工艺整体的脱氮效能, kg·(m3·d)-1.1.6 分析项目与方法NH4+-N采用纳氏分光光度法(哈希2800, 美国); NO2--N和NO3--N采用离子色谱法(戴安IS-9001, 美国); pH、ORP和温度采用WTW在线监测仪(德国); TOC采用TOC仪测定(Multi N/C3100, 德国); MLSS和MLVSS:重量法.2 结果与讨论2.1 PN-ANAMMOX反应器的启动同时将成熟的亚硝化生物膜和厌氧氨氧化颗粒污泥分别接种入反应器的好氧和厌氧区域, 采用提高进水氨氮浓度和缩短HRT的方式提高反应器整体的总氮去除速率(如图 2).在启动初期, 控制进水氨氮浓度为150 mg·L-1, HRT为0.31 d, 出水NH4+-N、NO2--N、NO3--N 浓度分别为50.7、48.9、19.8 mg·L-1, 总氮去除速率为0.125kg·(m3·d)-1.分别在反应器运行5 d和9 d通过进一步缩短HRT提升反应器氮负荷, HRT分别缩短为0.19 d和0.17 d, 总氮去除速率升高至0.24kg·(m3·d)-1, 此时反应器出水NH4+-N和NO2--N均低于50 mg·L-1, 表明反应器的脱氮效能还可以进一步提升; 于是在第11 d, 将进水氨氮浓度提高至260 mg·L-1, 同时延长HRT至0.48 d, 此时出水NH4+-N、NO2--N、NO3--N浓度有所升高, 分别为65.8、60.1、26.7 mg·L-1, 此后8 d, 随着亚硝化菌和厌氧氨氧化菌的活性逐渐增强, HRT也逐步下调至0.40 d, 此时总氮去除速率上升至0.35kg·(m3·d)-1; 在第20 d, 将进水氨氮浓度提高至350 mg·L-1, HRT控制在0.54 d, 此后9 d, 出水NH4+-N和NO2--N浓度均维持在较低水平, HRT也逐步下调至0.39 d, 总氮去除速率上升至0.66kg·(m3·d)-1; 在第30 d, 再次提高进水氨氮浓度至430 mg·L-1, 此进水氨氮浓度与后期影响实验进水氨氮浓度相近, HRT先延长至0.46 d, 再下调至0.4 d, 在第40 d时总氮去除速率稳定在0.75 kg·(m3·d)-1左右, 表明PN-ANAMMOX启动成功.图 2 PN-ANAMMOX反应器启动过程中氮素的变化对于PN-ANAMMOX反应器的启动, 国内外许多学者做过相关研究.冯佳珺等利用部分亚硝化-厌氧氨氧化串联工艺处理餐厨垃圾厌氧消化液时, 历时49 d先启动了部分亚硝化反应器后, 接种成熟的ANAMMOX污泥再经21 d成功启动了PN-ANAMMOX反应器, TN去除率达83%; Vázquez-Padín等先接种硝化污泥通过逐渐降低溶解氧实现亚硝酸盐的积累, 最后再接种ANAMMOX污泥启动PN-ANAMMOX, 运行35 d后, 氮去除速率达到0.25 kg·(m3·d)-1.可以看出, ANAMMOX菌作为PN-ANAMMOX脱氮工艺的核心功能菌群, 实现ANAMMOX菌的富集培养, 快速地提升ANAMMOX反应阶段的负荷才能实现反应器的成功启动, 无疑直接接种成熟的ANAMMOX颗粒污泥减少了ANAMMOX菌的富集培养时间, 而接种成熟的亚硝化生物膜进一步缩短了PN阶段亚硝酸盐的积累所需的时间, 因此本研究可以达到40 d成功启动PN-ANAMMOX 反应器的效果.2.2 酒精废水对PN-ANAMMOX的影响将酒精废水稀释50%(氨氮浓度在400 mg·L-1左右), 相应可生物降解的TOC约为50 mg·L-1, 在第41 d, 以其作为反应器进水.如图 3(a)所示, 采用酒精废水作为进水后, 反应器受到有机物冲击, 出水NH4+-N、NO2--N升高至74.3 mg·L-1、64.8 mg·L-1, NO3--N 浓度下降至11.3 mg·L-1, 总氮去除速率快速下降至0.57kg·(m3·d)-1, 为避免对反应器造成过度的影响, 延长HRT至0.42 d, 此后反应器总氮去除速率逐步上升至0.68kg·(m3·d)-1, 说明此可生物降解的TOC浓度对PN-ANAMMOX反应器影响不大, 延长HRT能有效缓解有机物的冲击作用; 为进一步确定酒精废水中的其他物质是否可能对反应器造成影响, 逐步人工添加(避免过度的有机物冲击)可生物降解TOC至原酒精废水中.在第49 d, 先在进水中人工添加20 mg·L-1TOC(葡萄糖), 此时出水NH4+-N、NO2--N升高至118.2 mg·L-1、109.5 mg·L-1, NO3--N浓度依然维持在较低的浓度水平, 总氮去除速率快速下降至0.45kg·(m3·d)-1, 此后6 d内一直在这范围内波动; 于是在第55 d[图 3(b)], 进水中加入50 mg·L-1TOC, 此时与原酒精废水中可生物降解的TOC浓度相近, 总氮去除速率呈快速下降趋势, 在第69 d下降至0.25kg·(m3·d)-1, 这表明酒精废水中所含可生物降解TOC的浓度(100 mg·L-1), 可以对反应器的脱氮速率产生抑制; 随后, 将进水改为人工配水, 直接加入100 mg·L-1 TOC, 在第69~80 d内, 反应器总氮去除速率并没有明显的变化.考虑到后期需要对PN-ANAMMOX进行驯化, 而在TOC存在下必然导致反应器内异养菌的存在, 为了维持这部分异养菌的活性, 在第81 d[图 3(c)], 采用低有机物浓度的人工配水(30 mg·L-1TOC)对反应器脱氮效能进行恢复, 降低有机物浓度后, 反应器总氮去除速率逐步上升, 第98 d, 出水NH4+-N和NO2--N下降至88.7 mg·L-1和70.6 mg·L-1, NO3--N 上升至17.7 mg·L-1, 总氮去除速率上升至0.60kg·(m3·d)-1左右, 反应器脱氮效能有所恢复.通过对好氧区NO2--N生成速率以及厌氧区的脱氮速率进行对比[图 3(d)]表明, 在100 mg·L-1以下的TOC对PN阶段NO2--N生成速率影响不大, 一直维持在0.6~0.7kg·(m3·d)-1左右, 而随着TOC浓度的提升厌氧区的脱氮速率由9.2kg·(m3·d)-1下降至3.7kg·(m3·d)-1左右, 降低TOC浓度后逐渐恢复.图 3 不同有机物浓度的酒精废水及人工配水下PN-ANAMMOX反应器出水氮素的变化酒精废水对PN-ANAMMOX的影响, 主要是由于酒精废水中TOC对亚硝化阶段和厌氧氨氧化阶段产生的冲击作用. De Prá等在研究部分亚硝化中TOC与TSS同时去除时表明, 控制有机负荷1.14kg·(m3·d)-1, DO 1.84 mg·L-1左右, 可以实现较好的亚硝化效果且TOC和TSS去除率可达到80%以上; Mosquera-Corral等在研究有机碳源对部分亚硝化的影响时表明, 200 mg·L-1TOC(CTOC/N=0.2) 不会对PN过程产生影响, 当TOC浓度达到300 mg·L-1时(CTOC/N=0.3), PN过程出现失稳; 金仁村等以乙酸钠为有机碳源研究对部分亚硝化反应器运行性能的影响时表明, 随着乙酸钠的添加, 反应器出水氨氮浓度不变, 亚硝氮、硝氮和总氮浓度减小, 且变化程度与有机物浓度呈正相关, 并且认为引发反硝化是影响部分亚硝化的主要原因.本研究中, 进水总CTOC/N在0.375~0.75左右, 高于大部分报道的抑制阈值, 但此过程中, PN阶段的NO2--N生成速率变化不大, 没有出现明显失稳的现象, 而可生物降解CTOC/N在0.125~0.25左右, 处于较低的CTOC/N水平, 故可以认为酒精废水对PN-ANAMMOX的影响, 主要是由于总TOC中可生物降解的TOC对ANAMMOX阶段产生的影响, 对于PN-ANAMMOX反应器, 有机物的添加首先导致了ANAMMOX反应区的氮去除速率的下降, 继而影响了反应器整体的脱氮效能.采用人工配水并加入与原酒精废水中等浓度的可生物降解TOC, 反应器整体的总氮去除速率没有明显的变化, 说明酒精废水中惰性有机物及其他物质对PN-ANAMMOX反应的影响不大.目前TOC对ANAMMOX菌的影响的报道差异较大, Li等采用市政污水和模拟废水研究表明, TOC>50 mg·L-1时, ANAMMOX菌活性开始受到影响.在研究利用ANAMMOX技术处理含惰性有机物浓度较高的废水时, 这一抑制值往往被大幅度提高, Ruscalleda等在研究用ANAMMOX工艺处理晚期渗滤液时表明, COD在400 mg·L-1左右时氮去除率可达到85%, 而其测定其中BOD5小于45 mg·L-1, 处于一个较低的浓度水平, 可以看出, BOD5与可生物降解的TOC之间具有一定的一致性, 两者均可用来表征废水中有机物能被生物降解的难易程度, 因此研究总TOC对ANAMMOX反应的影响时, 测定其中可生物降解的TOC更具有说服力.在本研究采用的酒精废水中, 可生物降解的TOC在100 mg·L-1左右, 若想利用ANAMMOX技术实现脱氮, 就必需强化PN阶段对可生物降解的TOC的去除.当TOC处于较低的浓度水平时, ANAMMOX阶段存在反硝化的作用, 反而有利于氮素的去除, 这与本研究中出现低TOC浓度下PN-ANAMMOX反应器总氮去除速率上升的现象一致.2.3 PN-ANAMMOX中异养菌与亚硝化菌、厌氧氨氧化菌的协同处理实际酒精废水采用低有机物浓度的人工配水对PN-ANAMMOX反应器的脱氮效能进行恢复后, 分别以20%、50%、100%的酒精废水对其进行驯化.如图 4所示, 第99 d, 采用20%的酒精废水作为进水, 氨氮浓度在160 mg·L-1左右, 缩短HRT至0.08 d, 出水NH4+-N、NO2--N、NO3--N 浓度分别为69.6、27.5、24.4 mg·L-1, 总氮去除速率为0.63kg·(m3·d)-1, 随后100~110 d逐步上升至0.84 kg·(m3·d)-1, 说明低TOC浓度可以提高反应器总氮去除速率; 在第111 d, 将进水改为50%的酒精废水, 氨氮浓度在400 mg·L-1左右, 延长HRT至0.18 d, 出水NH4+-N、NO2--N、NO3--N浓度分别为142.6、43.8、43.2 mg·L-1, 总氮去除速率呈快速下降趋势, 在第114 d, 总氮去除速率下降至0.44kg·(m3·d)-1, 此后115~122 d, 延长HRT至0.42 d, 总氮去除速率恢复至0.82kg·(m3·d)-1, 表明延长HRT可缓解有机负荷, 有利于脱氮效能的提高; 第123 d, 进水改为100%的酒精废水, 氨氮浓度在800 mg·L-1左右, 延长HRT至0.84 d, 出水NH4+-N和NO2--N浓度升高至251.2 mg·L-1和173.1 mg·L-1, NO3--N浓度也有所升高, 原因可能与曝气量提高有关.随后出水NO3--N浓度逐步下降, 出水NO2--N浓度出现先上升后下降的趋势, 此过程中出水NH4+-N一直处于150~250 mg·L-1高浓度水平, 而总氮去除速率先下降至0.34kg·(m3·d)-1再升高至0.65kg·(m3·d)-1, 出现了先下降后上升的趋势.图 4 酒精废水对PN-ANAMMOX驯化过程中氮素的变化由于经历过30 mg·L-1TOC浓度下的恢复阶段, 采用20%的实际酒精废水作为进水时, 实际可生物降解TOC只有20 mg·L-1左右, 此TOC浓度下, ANAMMOX菌活性逐渐增强, 并且低浓度的TOC为反硝化菌利用NO3--N及ANAMMOX反应未消耗的NO2--N进行反硝化创造了条件, 故在99~110 d总氮去除速率呈上升趋势.随后采用50%实际酒精废水作为进水, 其中可生物降解TOC在50 mg·L-1左右, 出现了总氮去除速率先下降后上升的趋势, 此过程中延长了HRT, 出水NH4+-N浓度出现先快速升高再逐步下降的趋势, NO2--N却没有出现明显的升高现象, 此时出水的NH4+-N和NO2--N 比值远高于ANAMMOX反应比, 而该可生物降解TOC浓度并不会对ANAMMOX反应产生明显的影响, 故可以认为此时PN阶段的NO2--N生成速率受到了影响, 这与短期影响实验中结果不同, 分析原因为长时间TOC的存在下, PN阶段大量异养菌的生成, 附着在亚硝化生物膜的表面, 从而影响了溶解氧的传质, 导致NO2--N生成速率下降. Daverey等在利用生物载体填料启动同步亚硝化-厌氧氨氧化-反硝化(SNAD)工艺时表明, 长时间的运行条件下, 随着NLR和OLR的提升, 溶解氧的供给不足, 会导致系统内氨氮浓度的升高. Liang等采用PN-ANAMMOX进行垃圾渗滤液的脱氮研究, PN单元为固定床生物膜反应器, DO为0.8~2.3 mg·L-1的条件下, 出水NH4+-N, NO2--N的比例接近1.0~1.3, NO3--N浓度小于43 mg·L-1且垃圾渗滤液中96%的COD被降解, 而0.8~2.3 mg·L-1的DO高于一般的PN阶段DO的控制.这些结果表明DO并非亚硝化实现的唯一影响因素, 长时间TOC的存在下, 亚硝化生物膜变厚导致氧分子传质变差, 生物膜内部依旧可以维持低DO水平, 从而实现稳定的亚硝化.因此为了维持NO2--N生成速率的稳定, 适当地提高PN阶段的溶解氧, 既有利于好氧异养型细菌的生长, 也不会影响生物膜内部亚硝化与反硝化作用.此时TOC及氮素的去除可以通过PN阶段的好氧异养菌、反硝化作用以及ANAMMOX区的ANAMMOX反应和反硝化作用.最后完全以酒精废水作为进水, 可生物降解TOC在100 mg·L-1左右, 延长HRT, 出水NH4+-N, NO2--N均出现了先上升再下降的趋势, 但两者浓度差十分明显, 分析原因一方面有机负荷提高后PN阶段的亚硝化生物膜进一步加厚传质变差; 另一方面, 通过PN阶段参数的调控不能实现PN阶段TOC的完全去除, 可生物降解TOC进入ANAMMOX反应区, 反硝化作用逐渐增强.从出水NO3--N浓度可以看出, 随着进水酒精废水比例的增加, NO3--N反而呈逐步下降的趋势, 说明有机负荷的提高, 反应器内反硝化作用逐渐明显.2.4 PN-ANAMMOX处理回用酒精废水控制策略TOC对PN阶段的影响主要是因好氧异养菌对电子受体(氧气)的竞争作用, 采用生物膜时异养菌的生成则会导致分子氧的传质下降, 进而影响NO2--N的生成.而TOC对ANAMMOX反应的影响主要是由于在高TOC浓度下, 反硝化菌的增殖会导致与ANAMMOX菌竞争电子受体NO2--N, 使得ANAMMOX菌处于饥饿状态, 而反硝化菌的产率系数y=0.27±0.3, ANAMMOX菌的产率系数y=0.066±0.01, 因此在高TOC浓度下, ANAMMOX菌很难占据主导地位.而对于酒精废水, 不可避免地带有一些醇类物质(主要是甲醇和乙醇), 而这些物质对ANAMMOX菌产生抑制作用, 并且这种抑制往往是不可逆的. Güven等研究表明0.5mmol·L-1的甲醇能够导致ANAMMOX不可逆地失活, 2 mmol·L-1的乙醇能够使ANAMMOX活性降低30%.本研究采用的酒精废水经过三级厌氧甲烷化处理, 这种前置厌氧的方式, 一方面可以调节水质水量,另一方面可以利用厌氧发酵消除醇类物质对后续工艺的影响并且可以去除部分可生物降解有机物, 降低后续工艺的有机负荷.在较高浓度的TOC下, 延长HRT并适当提高PN阶段的溶解氧既有利于好氧异养菌的生成, 也不会过度影响整体工艺中反硝化和厌氧氨氧化作用,降低了ANAMMOX阶段的有机负荷, 同时可以缓解长时间TOC存在下, 亚硝化生物膜变厚, 氧分子传质导致NO2--N不足的问题.而延长HRT实际上是延长了有机物在好氧区的停留时间, 强化了有机物在好氧区的去除, 从而减弱了有机物对ANAMMOX反应区的影响, 有利于反应器整体脱氮效能的提高.对于PN-ANAMMOX一体化反应器, 可以通过扩大好氧区的体积来实现好氧区HRT的延长, 并且可以维持厌氧区较高的氮去除负荷.具体参见污水宝商城资料或更多相关技术文档。
酒精废水处理技术(总10页)
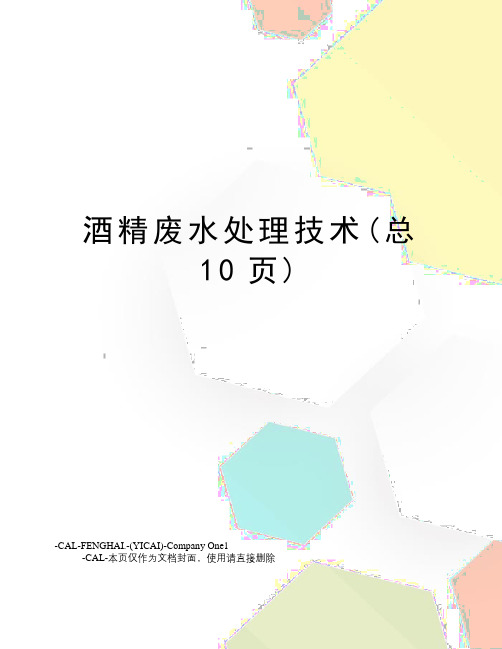
酒精废水处理技术(总10页)-CAL-FENGHAI.-(YICAI)-Company One1-CAL-本页仅作为文档封面,使用请直接删除酒精废水处理技术交流资料有限公司目录一.概述 ............................................................ 错误!未指定书签。
二.酒精生产废水特点................................................. 错误!未指定书签。
三、酒精废水处理主要方法............................................. 错误!未指定书签。
1、玉米酒精糟的综合利用.............................................. 错误!未指定书签。
2、薯干酒精糟的综合利用.............................................................................................. 错误!未指定书签。
3、糖蜜酒精糟处理方法 (4)4、酒精废水常用处理工艺.............................................................................................. 错误!未指定书签。
4.1高效全混厌氧污泥罐(EASB)...................................................... 错误!未指定书签。
4.2 UASB+HASB+接触氧化.................................................................. 错误!未指定书签。
4.3 EGSB+SBR ....................................................................................... 错误!未指定书签。
千吨酒精废水处理方案

千吨酒精废水处理方案一、引言酒精废水是一种常见的工业废水,由于其含有高浓度的有机物、酸碱度高以及毒性较大,对环境造成严重的污染。
因此,针对千吨酒精废水的处理需求,本文提出一种综合的废水处理方案,旨在达到高效、低成本的处理效果。
二、工艺流程1.确定处理工艺:采用生化处理工艺为主的综合处理工艺,结合物理、化学处理工艺进行辅助处理。
2.酸碱中和:初步调节酒精废水的酸碱度,降低废水的腐蚀性,减少对设备的损伤。
3.预处理:采用物理处理方法,包括搅拌、过滤、沉淀等,以去除悬浮物、杂质、油脂等有机污染物。
4.生物处理:通过生物反应器进行生物降解,利用微生物将有机物转化为有机酸、二氧化碳和水等无害物质。
5.活性炭吸附:采用活性炭对废水中的有机物进行吸附,以提高废水的处理效果。
6.深度处理:通过进一步的过滤、沉淀等工艺,去除残余的悬浮物、杂质等,提高废水的净化程度。
7.消毒处理:采用紫外线/臭氧消毒装置对处理后的废水进行消毒处理,确保排放达到国家标准。
三、主要设备介绍1.反应器:采用生物反应器进行生物处理,可选择活性污泥法、接触氧化法或人工湿地法等。
2.混合槽:用于调节废水的酸碱度和混合废水中的药剂,包括酸、碱、酶等。
3.沉淀池:用于沉淀废水中的固体颗粒和重金属离子等。
4.过滤器:用于去除残余的悬浮物和杂质。
5.活性炭吸附柱:用于吸附废水中的有机物。
6.消毒装置:采用紫外线或臭氧消毒装置对处理后的废水进行消毒处理。
四、操作流程1.酸碱中和:根据废水的具体情况,逐渐加入酸碱药剂,调节废水的酸碱度至中性。
2.预处理:将废水经过均匀搅拌后,进入过滤器进行初步过滤,去除较大颗粒的悬浮物和杂质。
3.生物处理:将预处理后的废水进入生物反应器,通过调节反应器的温度、曝气量、进水量等参数,利用微生物降解废水中的有机物。
4.活性炭吸附:将生物处理后的废水进入活性炭吸附柱,通过活性炭对废水中的有机物进行吸附,提高废水的处理效果。
5.深度处理:将经过活性炭吸附处理的废水进入深度处理装置,通过过滤、沉淀等工艺,去除残余的悬浮物和杂质。
污水处理之酒厂废水处理技术

污水处理之酒厂废水处理技术随着我国经济的迅速发展,工业化进程不断加快,污水处理成为了必不可少的环境保护工作。
而在污水处理中,酒厂废水处理技术占据了重要地位。
本文就酒厂废水处理技术进行探讨,以期能更好地保护水环境。
一、酒厂废水的污染特征酒厂一般采用蒸馏方法生产酒类,每生产一吨白酒就会产生5-15吨的酒精废水,这些废水通常都不能直接排放到自然环境中,因为它们含有较高的COD、BOD、有机物质和氨等污染物。
这些污染物不仅可以影响当地水质,还会危害生物健康。
二、酒厂废水处理技术目前,酒厂废水处理主要采取物理、化学和生物处理三种方法。
适当的处理方法能够有效地去除酒厂废水中的有害物质。
(一)物理处理物理处理主要是通过沉淀、过滤、吸附等方式去除污染物。
主要措施包括:格栅池、沉淀池、过滤池、沙滤池、臭氧反应器等。
这些方法的优点是工艺简单,效果稳定,操作成本低,但它也有一些缺点,例如处理能力有限,不能彻底去除所有的污染物。
(二)化学处理化学处理主要是通过添加化学药剂促进废水中污染物结合或分解,从而达到净化的效果。
例如采用氧化剂如氯、臭氧等强氧化剂进行氧化,采用离子交换、吸附、混凝、沉淀等方法进行处理,可有效去除污染悬浮物、有机物、无机物。
但这种方法有一定的投资和运营成本,还会产生新的化学物质,可能对环境造成影响。
(三)生物处理生物处理主要是使用微生物将酒厂废水所含的有机物质分解成无害物质,适用范围广,效果显著。
主要措施有A/O、MBR、SBR、MBBR、活性污泥法、生物浸泡法等。
其中,活性污泥法和生物浸泡法是最常用的处理方式,具有处理量大、效果好、节能等优点。
三、结论酒厂废水处理技术的选择应从实际情况出发,并结合治理效果和成本因素进行评估。
针对酒厂废水的治理,生物处理更被认为是最可行的方式,而且经济效益明显,同时也是环保操作方式。
只有全面采取科学的管理和锻炼,以及合理的污水治理方法,我们才能实现实现环境保护目标,建设优美、和谐的水环境。
酿酒废水处理技术及其工业应用

酿酒废水处理技术及其工业应用一、前言酒精是一种广泛使用的有机化合物,但酿制过程中会产生大量的酿酒废水,其中含有大量的有机物和无机盐等污染物,对环境造成严重影响。
因此,酿酒废水的处理一直是酒精工业的一个重要问题。
本文将介绍一些酿酒废水处理技术及其工业应用。
二、酿酒废水的特点酿酒废水的主要特点是有机物含量高,氮、磷含量较低,COD/CODCr比值高。
废水中还含有一定量的总悬浮物(SS)、总溶解物(TDS)和低浓度有害物质。
由于废水中有机物含量高,不易生物降解,因此处理难度较大。
三、酿酒废水处理技术1. 生物处理技术生物处理技术是一种比较常见的酿酒废水处理方法,它是通过天然的微生物来分解和降解酒精中的有机物。
生物处理技术的主要包括活性池、厌氧、好氧、深层床和曝气池等方法。
其中,活性池和曝气池是目前应用最广泛的生物技术。
2. 传统的化学处理法传统的化学处理法包括沉淀、絮凝、氧化和吸附等方法。
沉淀法通常采用氢氧化钙或氢氧化铁等化学剂,其主要作用是通过化合反应将污染物转化为沉淀物。
絮凝法主要用于处理废水中的悬浮物,它通过加入多种化学剂来形成粒状絮凝物,从而实现悬浮物的分离。
氧化法采用氧化剂来降解废水中的有机物,其主要作用是将有机物中的氢、碳、氧等元素分离。
吸附法则是将活性炭、树脂和膜等吸附材料应用于酿酒废水的处理中,通过吸附和分离效果来减少废水中的有毒物质。
3. 新型的处理技术随着科技的不断进步,有不少新型的处理技术应用到酿酒废水处理工作中。
这些新型技术包括:高效氧化技术、微波辐射技术、超声波分解技术等等。
四、酿酒废水处理技术的应用酿酒废水处理技术已经广泛应用于酒精工业,这种技术除了能够有效地处理废水,还能帮助企业合法合规,避免造成环境污染的问题。
正如前文所述,酿酒废水处理技术主要包括生物处理技术、传统化学机理和新型的处理技术。
在实际应用中,各种技术方案常常会进行组合,并且针对酒精生产工厂废水特性进行定制化处理。
酒精行业废水处理工艺

酒精行业废水处理工艺一、基本原理前置水解酸化均质均量技术与改良UASB结合,水解酸化可去除部分SS并降低改良UASB进水负荷,改良UASB通过增设内循环系统利用回流使反应器的升流速度恒定,而恒定的升流速度可以显著提升泥水混合效率,提升改良UASB的负荷,改善厌氧生物处理效果;可缓冲冲击负荷的不利影响;降低三相分离器的泥水分离压力。
填料CASS通过在填料表面形成生物膜增加反应器内生物量和生物种类,且形成的生物膜表面到内部存在溶解氧梯度,达到深度脱氮的目的。
深度处理“混凝沉淀-过滤-消毒”出水可满足循环冷却水补充用水要求,达到酒精废水回用的目的。
二、工艺流程三、关键技术及优势“前置水解酸化+强制内循环改良UASB+填料CASS+混凝沉淀-过滤+消毒”集成技术1、强制内循环改良UASB主要采用在反应器内三相分离器下部增设回流装置,通过增设内循环系统,利用回流使反应器的升流速度恒定,而恒定的升流速度可以保持污泥床稳定的膨胀和搅动,避免产生配水不均匀和沟流等现象,从而显著提升泥水混合效率,改善厌氧生物处理效果。
优势:(1)内循环可保证形成足够的水量“洗出”絮状污泥,加快颗粒污泥的形成;可以稀释突然增高的COD浓度,缓冲冲击负荷的不利影响;(2)当UASB反应器工作不正常或需要关停时,可以通过内循环尽可能地降低厌氧池内的挥发性脂肪酸(VFA);(3)提高反应器内水力上升流速,有利于颗粒污泥的形成;(4)通过三相分离器内泥水的回流,可有效避免液面浮渣的形成,最大程度的降低三相分离器的泥水分离压力,达到提高分离效率的目的。
2、前置水解酸化在去除SS的同时也起到了均质均量的效果,对于难降解废水还可提高其可生化性,所以整体集成工艺应用领域不仅限于酒精废水行业,同时可应用于高浓度难降解废水的处理。
3、填料CASS技术通过投加一种自主研发的填料篮装置,改善了反应池的流体动力学状态,提高了溶解氧的转移效率,增加生物膜的稳定性,具有增加生物量、生物种类以及促进深度脱氮的作用,达到污染负荷削减的同时并实现废水回用。
酒精废醪液废水处理技术

酒精废醪液废水处理技术酒精废醪液废水是指国内外酒精生产过程中产生的含有浓度高达2%-12%的有机物、挥发性酸、氨气、矿物质和细菌及其代谢物等物质的废液。
这种废水的处理对酒精工业和环境保护产生了重要的影响,如不经过科学处理,处理和排放都会给环境造成不良影响,所以酒精废醪液废水处理技术的重要性不言而喻。
酒精废醪液废水的主要污染物包括有机物、挥发性酸、氨气、矿物质和细菌及其代谢物等。
有机物含量高,挥发性酸含量较高,氨气含量也较高,这使得酒精废醪液废水的处理变得比较困难,不同的工艺会对其处理效果产生不同影响。
下面我们将介绍几种常用的酒精废醪液废水处理技术:1.氧化处理技术氧化处理技术是将酒精废醪液废水加入一定量的氧化剂,通过氧化作用将污染物质氧化成CO2和H2O等简单环保物质。
在处理酒精废醪液废水中,选择的氧化剂可根据化学性质进行选择,包括氢氧化钾(KOH)、高锰酸钾、双氧水、臭氧等等。
氧化处理技术简单,处理效果稳定,适用于处理含有机质较多的酒精废醪液废水,但消耗的氧化剂较大,处理成本稍高。
2.生物处理技术生物处理是一种利用微生物菌群对废水进行处理的技术,适用于有机质含量较高的污水的处理。
生物处理过程包括接种微生物菌群、好氧生物处理和厌氧生物处理,其中好氧生物处理过程中,微生物菌群可以在氧气的作用下将污染物质转化为二氧化碳和水等无毒性物质,处理效果好。
不过在生物处理酒精废醪液废水过程中,存在着与其他生物竞争、氧气不足等问题,厌氧生物处理可以降低处理过程中所需氧气量,减少控制难度。
但是,厌氧处理需要一段较长的反应时间,较难控制,处理效果较为不稳定。
3.浓缩技术浓缩技术是将酒精废醪液废水中有机物、挥发性酸、氨气等透过半透膜的方法分离出来,减少废水的体积和浓度,同时也利用废水中的营养物质和有机物质进行再利用。
浓缩技术具有处理成本低、处理效果稳定的特点,但是与物质密度相关的半透膜容易被堵塞,还需要半透膜的定期维护和更换。
000.乙醇废水处理技术工艺

乙醇废水处理技术工艺乙醇废水处理是一种具有挑战性的过程,因为乙醇废水通常含有高浓度的有机物和其他污染物。
以下是一些常见的乙醇废水处理技术和工艺:1.生物处理:生物处理是一种常用的乙醇废水处理方法,通过利用微生物对有机物进行降解来达到净化的目的。
常见的生物处理方法包括活性污泥法、厌氧消化和生物膜法等。
这些方法需要提供适宜的环境条件和营养物质供给,以维持微生物的活性和降解效率。
2.物理-化学处理:物理-化学处理方法可以辅助生物处理,提高净化效果。
常见的物理-化学处理方法包括沉淀、吸附、离子交换和氧化等。
这些方法可以去除悬浮物、重金属离子、油脂和其他难降解的有机物。
3.活性炭吸附:活性炭是一种高效吸附材料,常用于乙醇废水中有机物的吸附和去除。
乙醇废水经过预处理后,通过将废水流经活性炭床,有机物会被吸附在活性炭表面上,从而实现净化效果。
4.膜分离技术:膜分离技术包括超滤、逆渗透和蒸发等方法,可以通过膜的选择性通透性,将乙醇废水中的有机物和溶解性固体分离出来。
这些技术可以实现高效的固液分离和浓缩处理。
5.化学氧化:通过氧化剂如氢过氧化物、二氧化氯或臭氧等,在合适的反应条件下,对乙醇废水中的有机物进行氧化分解。
这种方法可以快速降解有机物,并提高废水的生物可降解性。
需要根据具体的乙醇废水特性和排放标准选择合适的处理技术和工艺。
通常,针对高浓度的乙醇废水,可以采用多级处理的方法,结合不同的技术和工艺进行综合处理,以达到符合环境标准的水质要求。
此外,废水处理过程中,还应注意护理和处理废水处理产生的污泥等辅助物质,以确保整个处理过程的环保性和可持续性。
酒厂污水处理技术

酒厂污水处理技术一、背景介绍酒厂是一种特殊的工业企业,其生产过程会产生大量的废水。
酒厂废水中含有高浓度的有机物质、悬浮物、油脂、酸碱等污染物,如果不经过有效的处理,将对环境造成严重的污染。
因此,酒厂污水处理技术的研究和应用具有重要的意义。
二、技术原理1. 初级处理:酒厂废水首先经过初级处理,主要包括预处理、调节和沉淀等步骤。
预处理阶段通过格栅和砂池等设备去除大颗粒悬浮物和杂质,调节阶段通过调节池对废水的流量和水质进行调节,沉淀阶段通过沉淀池使废水中的悬浮物沉淀下来。
2. 生物处理:经过初级处理后的废水进入生物处理系统。
生物处理是利用微生物对废水中的有机物进行降解的过程。
常用的生物处理方法包括活性污泥法、固定化生物膜法和生物接触氧化法等。
这些方法通过提供适宜的环境条件,让微生物在废水中进行生长和代谢,将有机物转化为无害物质。
3. 深度处理:经过生物处理后的废水仍然含有一定量的难降解有机物和微量污染物。
为了进一步提高废水的处理效果,需要进行深度处理。
常用的深度处理方法包括活性炭吸附、臭氧氧化、高级氧化等。
这些方法能够有效去除废水中的难降解有机物和微量污染物,提高废水的水质。
三、技术应用1. 活性污泥法:活性污泥法是目前应用最广泛的生物处理方法之一。
通过在反应器中培养大量的活性污泥,利用污泥中的微生物对废水中的有机物进行降解。
活性污泥法具有处理效果好、稳定性高、操作简单等优点,适用于中小型酒厂的废水处理。
2. 固定化生物膜法:固定化生物膜法是利用生物膜对废水进行降解的方法。
通过将生物膜固定在载体上,形成固定化生物膜反应器。
生物膜能够提供更大的接触面积,提高废水的降解效率。
固定化生物膜法具有生物膜稳定、抗冲击负荷能力强等优点,适用于大型酒厂的废水处理。
3. 生物接触氧化法:生物接触氧化法是利用生物膜和氧气对废水进行处理的方法。
通过将废水与生物膜和氧气充分接触,利用生物膜中的微生物进行降解。
生物接触氧化法具有处理效果好、对负荷波动适应性强等优点,适用于中小型酒厂的废水处理。
浅谈酒精废水处理技术
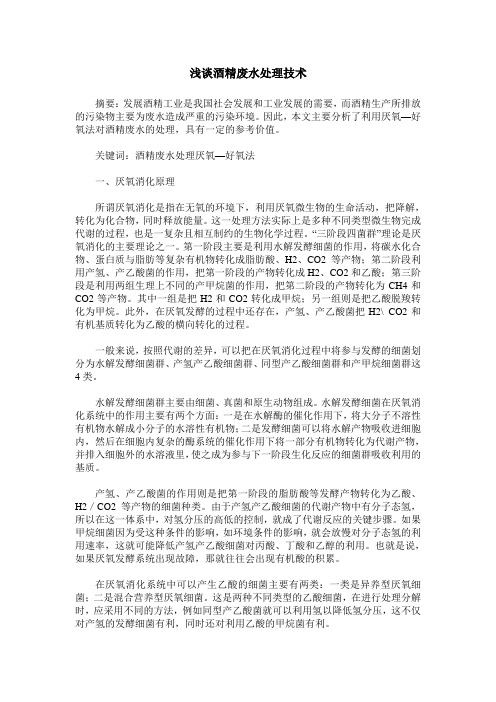
浅谈酒精废水处理技术摘要:发展酒精工业是我国社会发展和工业发展的需要,而酒精生产所排放的污染物主要为废水造成严重的污染环境。
因此,本文主要分析了利用厌氧—好氧法对酒精废水的处理,具有一定的参考价值。
关键词:酒精废水处理厌氧—好氧法一、厌氧消化原理所谓厌氧消化是指在无氧的环境下,利用厌氧微生物的生命活动,把降解,转化为化合物,同时释放能量。
这一处理方法实际上是多种不同类型微生物完成代谢的过程,也是一复杂且相互制约的生物化学过程。
“三阶段四菌群”理论是厌氧消化的主要理论之一。
第一阶段主要是利用水解发酵细菌的作用,将碳水化合物、蛋白质与脂肪等复杂有机物转化成脂肪酸、H2、CO2等产物;第二阶段利用产氢、产乙酸菌的作用,把第一阶段的产物转化成H2、CO2和乙酸;第三阶段是利用两组生理上不同的产甲烷菌的作用,把第二阶段的产物转化为CH4和CO2等产物。
其中一组是把H2和CO2转化成甲烷;另一组则是把乙酸脱羧转化为甲烷。
此外,在厌氧发酵的过程中还存在,产氢、产乙酸菌把H2\ CO2和有机基质转化为乙酸的横向转化的过程。
一般来说,按照代谢的差异,可以把在厌氧消化过程中将参与发酵的细菌划分为水解发酵细菌群、产氢产乙酸细菌群、同型产乙酸细菌群和产甲烷细菌群这4类。
水解发酵细菌群主要由细菌、真菌和原生动物组成。
水解发酵细菌在厌氧消化系统中的作用主要有两个方面:一是在水解酶的催化作用下,将大分子不溶性有机物水解成小分子的水溶性有机物;二是发酵细菌可以将水解产物吸收进细胞内,然后在细胞内复杂的酶系统的催化作用下将一部分有机物转化为代谢产物,并排入细胞外的水溶液里,使之成为参与下一阶段生化反应的细菌群吸收利用的基质。
产氢、产乙酸菌的作用则是把第一阶段的脂肪酸等发酵产物转化为乙酸、H2/CO2等产物的细菌种类。
由于产氢产乙酸细菌的代谢产物中有分子态氢,所以在这一体系中,对氢分压的高低的控制,就成了代谢反应的关键步骤。
如果甲烷细菌因为受这种条件的影响,如环境条件的影响,就会放慢对分子态氢的利用速率,这就可能降低产氢产乙酸细菌对丙酸、丁酸和乙醇的利用。
酒精废水处理

1200t、d酒精污水处理成套工程第一章概述§1-1生产工艺简介酒精是重要的基础化工原料,广泛应用于化学工业、食品工业、日用化工、医药卫生等领域,同时发酵酒精企业酒精糟的污染是食品与发酵工业最严重的污染源之一。
据不完全统计,我国发酵酒精生产能力近600万吨,1998年我国酒精生产量为218万吨。
2002年全国酒精生产主要企业为100多家,发酵酒精产量为212.86万吨,酒精生产遍布了26个省市和自治区。
发酵酒精工业的污染主要为水污染。
生产过程的废水主要来自蒸馏发酵成熟醪后排出的酒精糟,生产设备的洗涤水、冲洗水、以及蒸煮、糖化、发酵、蒸馏工艺的冷却水等。
每生产1吨酒精约排放13~16吨酒精糟。
酒精糟呈酸性,CODCr高达(5~7)×104mg/L,是酒精行业最主要的污染源。
据调查结果测算,2002年全国生产发酵酒精212.86万吨的年排放废水总量约2.1亿m3,其中酒精糟为4000多万m3,年排有机污染物CODCr约7.2万吨。
酒精废水占全国工业废水排放总量的1%(2002年全国工业废水量为207.2亿吨),所排CODCr占全国工业废水中CODCr排放总量的1.2%(2002年全国工业废水中CODCr为584万吨),污染物排放量大,对环境污染严重。
因此开发经济高效的酒精废水处理技术日益成为当今环保行业关注的课题。
第二章设计依据、原则和范围§2-1设计依据-略§2-2设计原则略§2-3设计范围1200m3/d废水治理工程设计包括以下内容:1、废水处理站总平面布置图设计。
2、工艺设计(包括污泥处理设计工艺)。
3、土建构(建)筑物设计。
4、设备工艺、管道等设计。
5、电气及自动控制设计。
6、其它配套设施设计(消防、照明、道路、绿化等)。
第三章水量、水质和处理后标准§3-1设计水量我们根据厂方的要求及废水排放情况确定水量为:1200 m3/d。
§3-2设计水质酒精进水水质:§3-3处理后水质标准第四章工艺方案设计§4-1工艺设计说明酒精生产废水含有大量有机物,生化性好。
酒精废水处理工艺流程

酒精废水处理工艺流程
酒精废水处理的工艺流程通常包括以下几个步骤:
1. 调整pH值:酒精废水通常具有酸性或碱性倾向,因此第一步是通过添加酸或碱来调节废水的pH值,使其接近中性范围(pH 6-8)。
2. 前处理:在酒精废水进入主要处理过程之前,可能需要进行前处理以去除悬浮固体、油脂、颜色、异味等。
常见的前处理方法包括筛网过滤、油水分离、活性炭吸附等。
3. 生物处理:生物处理是酒精废水处理中常用的方法之一。
通过利用生物物种(如细菌、微生物等)以及其新陈代谢和降解能力,将有机物质分解为较简单的无害物质。
常见的生物处理方法包括活性污泥法、生物膜法、生物滤池等。
4. 化学处理:化学处理可以帮助进一步去除废水中的有机物和污染物。
常见的化学处理方法包括氧化还原方法、氧化法、絮凝沉淀等。
其中,常用的氧化剂有氯化铁、过氧化氢等。
5. 深度处理:此步骤用于进一步处理经过前述步骤仍含有高浓度污染物的酒精废水。
常见的深度处理方法包括高级氧化反应、活性炭吸附、膜过滤等,以确保废水达到排放标准。
6. 消毒处理:在废水处理的最后阶段,常常需要进行消毒处理,以消除残留的细菌、病毒和其他微生物。
常用的消毒剂包括氯、臭氧、紫外线辐射等。
在整个废水处理过程中,实施监测和控制,确保废水的处理效果达到环境排放标准,以保护环境和人类健康。
值得注意的是,不同的酒精废水含有不同的组分和浓度,因此最佳的处理过程可能会因具体情况而有所不同。
建议在实施处理工艺前,进行废水的初步分析和评估,以选择最适合的处理方法。
酿酒厂废水处理技术

酿酒厂废水处理技术酿酒厂是一个产生大量废水的行业,废水中含有大量的有机物质、悬浮物、油脂和微生物等。
如果这些废水不经过处理直接排放到水体中,将会对环境和生态系统造成严重的污染。
因此,酿酒厂废水处理技术的研发和应用具有重要意义。
本文将详细介绍酿酒厂废水处理技术,并列出几种常用的处理方法。
1. 传统废水处理方法:传统的废水处理方法主要包括物理处理、化学处理和生物处理三个阶段。
物理处理:物理处理主要是通过粗滤、沉淀、澄清等方式将废水中的悬浮物、油脂等固体杂质去除,一般使用格栅、沉淀池、澄清池等设备。
化学处理:化学处理主要是利用化学反应将废水中的有机物质、重金属离子等进行沉淀、吸附或氧化还原等处理,一般使用草酸盐、氯气、活性炭等材料。
生物处理:生物处理主要是通过利用微生物对废水中的有机物质进行降解、氧化等处理,一般使用生物滤池、生物接触氧化池等装置。
2. 利用新技术进行废水处理:传统的废水处理方法存在效率低、消耗能源高等问题,因此,近年来逐渐出现了一些新的废水处理技术。
膜分离技术:膜分离技术主要是利用特殊的膜材料,通过渗透、过滤、离子交换等原理将废水中的不同成分进行分离,一般使用微滤膜、超滤膜、反渗透膜等。
高级氧化技术:高级氧化技术主要是通过添加氧化剂或利用高能量的辐射将废水中的有机物质进行氧化降解,一般使用臭氧、紫外线等。
生物膜技术:生物膜技术是一种集物理、化学和生物处理于一体的综合性废水处理技术,主要利用微生物膜对废水中的有机物质进行处理,一般使用固定化生物膜、活性炭生物膜等。
3. 废水处理技术的应用案例:下面列举几个酿酒厂废水处理技术的应用案例,以说明不同技术的效果。
案例一:某酿酒厂采用传统的物理、化学和生物处理工艺进行废水处理,能有效地去除废水中的悬浮物、油脂和有机污染物,达到排放标准要求。
案例二:某酿酒厂引进了膜分离技术,通过反渗透膜对废水进行处理,获得了更高的废水处理效率和水质净化程度。
案例三:某酿酒厂采用生物膜技术进行废水处理,通过活性炭生物膜反应器对废水中的有机物质进行降解,处理效果显著,且设备占地面积小,操作简便。
酒精1废水处理工艺
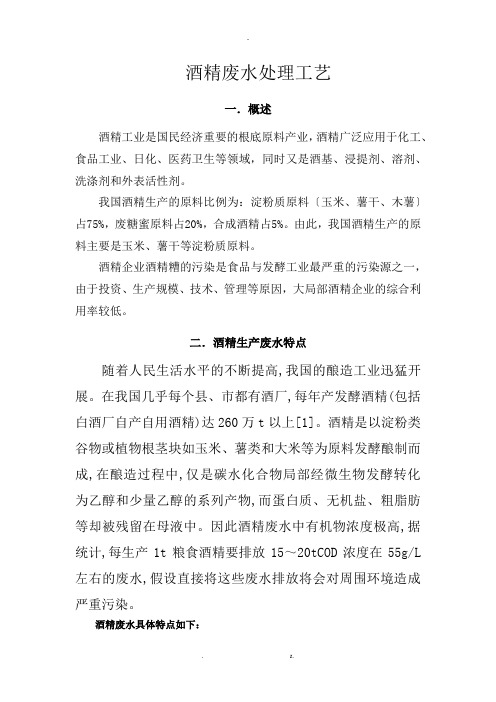
酒精废水处理工艺一.概述酒精工业是国民经济重要的根底原料产业,酒精广泛应用于化工、食品工业、日化、医药卫生等领域,同时又是酒基、浸提剂、溶剂、洗涤剂和外表活性剂。
我国酒精生产的原料比例为:淀粉质原料〔玉米、薯干、木薯〕占75%,废糖蜜原料占20%,合成酒精占5%。
由此,我国酒精生产的原料主要是玉米、薯干等淀粉质原料。
酒精企业酒精糟的污染是食品与发酵工业最严重的污染源之一,由于投资、生产规模、技术、管理等原因,大局部酒精企业的综合利用率较低。
二.酒精生产废水特点随着人民生活水平的不断提高,我国的酿造工业迅猛开展。
在我国几乎每个县、市都有酒厂,每年产发酵酒精(包括白酒厂自产自用酒精)达260万t以上[1]。
酒精是以淀粉类谷物或植物根茎块如玉米、薯类和大米等为原料发酵酿制而成,在酿造过程中,仅是碳水化合物局部经微生物发酵转化为乙醇和少量乙醇的系列产物,而蛋白质、无机盐、粗脂肪等却被残留在母液中。
因此酒精废水中有机物浓度极高,据统计,每生产1t粮食酒精要排放15~20tCOD浓度在55g/L 左右的废水,假设直接将这些废水排放将会对周围环境造成严重污染。
酒精废水具体特点如下:1、悬浮物含量高,平均悬浮物含量高达40000mg/L;2、温度高,平均水温达70℃,蒸馏釜底排出的废水温度高达100℃;3、浓度高,废水的COD高达2-3万,包括悬浮固体、溶解性COD和胶体,有机物占93%-94%,无机物占6%-7%,有机物的成分是碳水化合物,其次是含氮化合物,生物菌和未分解出去的产品:如丁醇、乙醇等,此外还有500mg/L的有机酸;4、废水含有约500mg/L左右的有机酸,废水呈酸性,运行初期可考虑加碱或污泥的回流以平衡废水的酸碱度,运行稳定后系统具备足够的缓冲能力,则不需要加碱或回流;5、无机物主要是来自原料中的灰尘和杂质。
***酒精年产酒精1.5万t其主要以玉米为原料,日排放废糟液750m3左右,pH值为4.0左右,COD达80g/L,BOD达45g/L以上,废水最后注入附近的河流,造成严重的污染。
酿酒废水的处理技术

酿酒废水的处理技术摘要:酿酒废水成分复杂,但大多数的废水中都含有 BOD、COD、有机物和多酚物质等,这些物质都能对环境造成严重污染。
介绍了微生物法、电解法、絮凝法以及催化法处理酿酒废水方面的研究现状及进程,并对酿酒废水今后的研究方向提出了几点建议。
关键词:酿酒废水;微生物;电解;絮凝;催化酿酒废水主要来源于酿酒工艺的清洗和发酵液蒸馏两个过程,具有有机物浓度高、悬浮颗粒多、BOD/COD 比值大等特点,是酿造业较难处理的一种废水,并且排放到河流中就会引起水体的严重富营养化,导致赤潮等现象。
国家在“十一五”期间就指出,要力争使万元产值综合能耗降低20%以上,主要污染物排放总量减少20%,鼓励酿酒企业承担起应负的社会责任,处理酿酒废水,达到国家排放标准,并且国家在十八大期间又将也非常重视废水的处理。
迄今为止,国内外很多学者都对酿酒废水的处理技术进行了深入的研究,本笔者主要介绍了微生物法、电解法、絮凝法、以及催化法处理酿酒废水的研究现状及进程,并对今后的研究方向提出了几点建议,为今后的有关研究提供参考。
1.酿酒废水处理技术1.1 微生物法微生物法处理酿酒废水就是在适宜的降解条件下利用已经培养驯化好的废水降解菌,对废水中有害物质进行高效率的降解的过程,从而降低废水中 COD、BOD 以及 SS 等的含量。
黄武[1]以水解酸化-UASB 法对黄酒生产过程中产生的高浓度米浆废水进行了处理,这种方法是在酸化池中自然富集菌种,并对富集的菌种进行培养繁殖,以培养繁殖的酸化菌对酿酒废水进行处理。
结果显示:解酸化池能够把浓度 31 500 mg/L 的 COD 降解为 22 150 mg/L 的 COD,降解效果比较明显,而且酸化池还能有效的减少对厌氧消化的冲击,大幅度改善厌氧消化的效果,提高对酿酒废水的处理效率。
黄钧[2]等以酿酒废水为研究对象,研究厌氧-好氧工艺与微生物菌剂相结合的方法对酿酒废水 COD 浓度、BOD 浓度的影响。
酒精废水处理工艺的特点分析

酒精废水处理工艺的特点分析1.高浓度有机废水:酒精生产废水中含有大量的有机物质,如酒精、蔗糖、酒糟等,浓度较高。
这就要求处理工艺对于高浓度有机废水具有良好的处理效果。
2.变化多样的废水成分:酒精废水的成分随着酿制酒精的生产工艺和原料的不同而有所变化,可能含有酸、碱、酶、色素等成分,造成废水成分的复杂性。
因此,处理工艺需要具备对多种成分的去除能力。
3.水量大、流量变化大:酒精生产中的废水产量大,处理工艺需要具备处理大量废水的能力。
此外,废水流量大,且随着酒精生产的周期性变化,废水流量会有所波动,处理工艺需要能够适应这种变化。
4.高效、低成本:酒精生产废水处理工艺需要高效地去除有机物质和其他污染物,达到排放标准。
同时,处理工艺需要具备较低的运营成本,以降低企业的经济负担。
5.综合处理技术:酒精废水处理不仅需要对有机物质进行高效去除,还需要对废水中的其他污染物进行处理,如悬浮物、有毒物质、重金属等。
处理工艺需要综合运用物理、化学和生物等技术手段,以实现全面的废水处理效果。
6.循环利用:酒精废水中有机物质的浓度较高,适合进行资源化利用。
因此,处理工艺需要考虑在废水处理过程中对有机物质的回收利用,如生物发酵、沉淀、蒸发等,以提高资源利用率。
7.适应性强:酒精废水处理工艺需要适应不同规模的酒精生产企业,能够满足不同酒精废水的处理要求。
同时,处理工艺需要具备一定的灵活性,能够应对废水成分和流量的变化。
总之,酒精废水处理工艺的特点是高浓度有机废水、变化多样的废水成分、水量大、流量变化大、高效、低成本、综合处理技术、循环利用和适应性强。
只有综合运用多种技术手段,针对这些特点进行有效处理,才能实现酒精废水的环保处理和资源化利用。
- 1、下载文档前请自行甄别文档内容的完整性,平台不提供额外的编辑、内容补充、找答案等附加服务。
- 2、"仅部分预览"的文档,不可在线预览部分如存在完整性等问题,可反馈申请退款(可完整预览的文档不适用该条件!)。
- 3、如文档侵犯您的权益,请联系客服反馈,我们会尽快为您处理(人工客服工作时间:9:00-18:30)。
酒精废水处理技术酒精漕液废水属高浓度有机废水,采用现有技术进行处理,通过工艺流程和费用分析,可以看出,处理效率低下,成本高,而采用本文提出的新技术进行处理,效率可提高四倍以上。
1 概述1.1 生产原料及其水质特征采用液体发酵法生产酒精,其原料一般以薯干、木薯、玉米和高粱等为主。
淮河流域地区的山东省和安徽省等以采用薯干为原料者居多。
其生产过程中所产生的高浓度有机污水主要为酒精蒸馏塔的釜底残液,即酒精蒸馏塔所排出的酒精糟液。
糟液的排出量一般为10~15m3/t酒精,其水质特征为(1)温度高,一般在70℃以上;(2)所含悬浮物浓度高,一般在3万mg/L 以上;(3)有机物(COD)浓度高,一般在4万mg/L~5万mg/L;(4)pH低,一般为4~5。
因此是一种高温,高悬浮物的高浓度有机污水。
对于污水中溶解性的有机污染成分来说,薯干类污水主要以糖类和脂肪酸类化合物为主,玉米、高粱等污水中含有较多的蛋白质。
前者容易进行厌氧沼气发酵处理,后者较难。
1.2 现有处理技术的缺陷目前,在酒精糟液处理方面主要采取固体物(悬浮物)分离作饲料厌氧产沼气处理法。
固体物分离采用离心机或沉淀过滤池,产沼气则采用全混式沼气发酵罐。
由于投资和国产设备的性能所限,糟液中的固体物分离很低,残存在分离液中的悬浮物浓度仍在1万mg/L水平上,同时,这种老式的沼气发酵罐效率很低,体积很大,一般水力停留时间要在10天左右,而且要靠水泵循环进行搅拌动力消耗大,搅拌不均匀。
从环保角度看,这种处理工艺所存在的最重要的问题是处理水质不达标。
一般,经这种厌氧大罐处理后的水,COD浓度仍在1.0~1.4万mg/L以上,悬浮物浓度仍在1.0万mg/以上,分别超出《污水综合排放标准》GB8978-1996标准中所规定的相应二级标准(COD≤300mg/L,悬浮物≤200mg/L)30倍以上和50倍以上。
为了排放达标,近几年不少厂家和环保公司采用[厌氧+好氧]的处理工艺。
对于处理高浓度的有机污水,国外已普遍采用这种工艺。
但是,同样是[好氧+厌氧]工艺,在系统组成和处理单元的设计上却有很大不同。
现在普遍存在的问题是处理构筑物体积大,运转能耗高、处理水质仍然达标困难。
具体举例分析如下。
1.3 处理工艺及其造价和运转能耗现以酒精生产量1.5万t/a的薯干酒精糟液污水处理工厂为例进行分析。
1.3.1 糟液量及其浓度糟液量:750m3/d;COD:50kg/m31.3.2 处理工艺流程糟液→除砂→离心机物体分离→分离液(污水)→温度调整至60℃→加石灰调整pH值为7以上→进料泵→全混式沼气发酵罐→出水→冷却至30℃左右→气浮池去除悬浮物→活性污泥曝气池→沉淀池→排放1.3.3 处理构筑物容积a. 污水有机物负荷量(L1)一般,离心机固体物的体积占糟液体积的10%,COD的去除率为30%。
因此,分离液的有机物负荷为 L1=[750×(1-0.1)]m3/d×[50×(1-0.3)]kg/m3=23625kgCOD/db. 全混式沼气发酵罐容积(V1)一般,全混式沼气发酵罐容积负荷为3kgCOD/m3·d,则其有效容积为:V1=23625COD/d÷3kgCOD/m3·d=7875m3 水力停留时间=7875m3÷[750×(1-0.1)]m3/d=9.45 d 按照以上计算,发酵罐的进水COD浓度为35000mg/L,去除率为70%,出水的COD浓度为10500mg/L。
c. 活性污泥曝气池容积(V2)一般,全混式沼气发酵罐的COD去除率为70%,气浮池的COD去除率为30%,浮渣体积占污水体积5%,所以,进入曝气池的有机物负荷(L2)为:L2=[750×(1-0.15)]m3/d×[50×(1-0.3)×(1-0.7)]kgCOD/m3=6693.75kgCOD/d曝气池的容积一般取1.0kgCOD/m3·d,则: V2=6693.75kgCOD/d÷1.0kgCOD/m3·d=6693.75m3 水力停留时间=6693.75m3÷[750×(1-0.15)]m3/d=7.59 d按照以上计算,曝气池的进水COD浓度为7350mg/L,如果要求出水的COD浓度满足二级排放标准,即COD浓度不大于300mg/L,则曝气池的COD去除率不得小于96%。
这是很难达到的。
有酒精废水需要处理的单位,也可以到污水宝项目服务平台咨询具备类似污水处理经验的企业。
也就是说,即使采用上述所谓的[厌氧+好氧]处理工艺,其处理结果也很难达标。
1.3.4 运转费用核算我们再来看其运转费用。
以下仅以上述工艺所获得的经济效益(沼气)和曝气池电耗进行考虑。
a. 沼气产量一般,厌氧处理段每去除1kgCOD可产沼气0.5Nm3,其甲烷含量为60%左右。
即1Nm3沼气的发热量相当于1kg原煤。
因此,上述沼气罐的沼气产量为:23625kgCOD/d×0.7×0.5=8268.75Nm3 即,可获得相当于8吨原煤的经济效益。
这就是为什么多半酒厂都积极上厌氧处理的原因。
b. 曝气池电能消耗根据日本的活性污泥法处理厂运行资料统计,每去除1kgCOD,曝气池的电能消耗(鼓风机电耗)为1.3-1.8kw·h。
在此按二级处理标准(COD=300mg/L)并以去除电耗为1.5kw·h/kgCOD计算上述曝气池的能耗,则为:[750×(1-0.15)]m3×[50×(1-0.3)×(1-0.7)-0.3]kgCOD/m3×1.5kw·h/kgCOD=6502.5kw·h/d 即,每天的处理电耗至少为6500kw·hc. 运转费用核算设原煤每吨售价为240元,电费每度为0.6元。
则上述情况下的运转费用(不含设备折旧费、人工工资等)为: 8吨煤/天×240元/吨煤-6500度电/天×0.6元/度电=-1980元/天即,每天需要支出运转费至少1980元,年累计额为59.4万元(以年300天工作日计)。
折合成每吨污水的处理费用为2.64元。
建造上述形式的污水处理设施大约要投资500万元,再加上如此高的运转费,对于企业是一笔沉重的负担。
我国的酒厂数量非常多,而且多半分布在经济基础较薄弱的地区。
因此,开发投资省、运转费用低的处理技术具有非常重要的意义。
2 新技术介绍根据上述情况,我们开发了针对酒精漕液污水的综合处理技术,其具体特点介绍如下。
2.1 指导思想采用酒厂现有在锅炉节煤和能源充分利用方面所积累的成熟经验,即:(1)将燃煤型锅炉改造为煤-沼气混合燃烧型。
通过加入助燃既节省一部分燃料煤,又因沼气燃烧快而使炉膛温度快速提高,使送入的煤得以燃烧充分,提高煤的利用率,减少煤灰中的含碳率。
(2)将锅炉供汽压力提高到16kgf/cm2,后接背压发电机,实行热-电联产,以提高锅炉的热效率。
在以上基础上,对于糟液污水处理采用先进的沼气发酵工艺,最大限度地从糟液中提取沼气,以创造污水处理的经济效益。
同时,由于沼气产率的提高造成后续好氧处理单元的进水浓度降低,因而减少了好氧处理的运转能耗,并可保证处理结果达标。
同时可以查看中国污水处理工程网更多技术文档。
2.2 处理工艺流程糟液→除砂→离心机物体物分离→分离液(污水)→温度调整至60℃→加石灰调整pH值为7以上→进料泵→全混式沼气发酵罐→出水→冷却至40℃左右→气浮池去除悬浮物→两级串联型高效厌氧污泥床(UASB)沼气发酵装置→高效生物接触氧化池→沉淀池→排放其中,自动内循环型全混式气发酵罐、高效厌氧污泥床(USSB)沼气发酵装置和高效生物接触氧化池是本工艺的特有技术。
高效厌氧污泥床(UASB)沼气发酵装置及其颗粒污泥的快速形成方法已在日本和中国申请发明专利。
2.3 技术参数2.3.1 自动内循环型全混式沼气发酵罐容积负荷:10kgCOD/m3·d去除率:70%COD2.3.2 高效厌氧污泥床(UASB)沼气发酵装置容积负荷:第一级10-15kgCOD/m3·d,第二级5-8kgCODm3·d去除率:第一级70%COD,第二级70%COD2.3.3 高级生物接触氧化池容积负荷:3kgCOD/m3·d去除率:70COD以上2.4 处理构筑物容积及能耗计算仍以上述同类酒厂进行计算比较2.4.1 自动内循环型全混式沼气发酵罐有效容积=23625kgCOD/d÷10kgCOD/m3·d=2362.5m3水力停留时间=2362.5m3÷[750×(1-0.1)]m3/d=3.5d进水COD浓度为35000mg/L,去除率为70%,出水的COD浓度为10500mg/L。
沼气产量=23625kgCOD/d×0.7×0.5Nm3/kgCOD=8268.8Nm3/d2.4.2 高效厌氧污泥床(UASB)沼气发酵装置a. 第一级有机负荷=[750×(1-0.15)]m3/d×7.35kgCOD/m3 =4685.6kgCOD/d÷10kgCODm3·d =468.6m3有效容积=4685.6kgCOD/d÷10kgCODm3·d=468.6m3水力停留时间=468.6m3÷[750×(1-0.15)]m3/·d=0.74d进水COD浓度为73500mg/L,去除率为70%,出水的COD浓度为2200mg/L。
沼气产量=5685.6kgCOD/d×0.7×0.5Nm3/kgCOD=1640Nm3/db. 第二级有机负荷=[750×(1-0.15)]m3/d×2.2kgCOD/m3=1402.5kgCOD/d有效容积=1402.5kgCOD/d÷5kgCODm3·d=280.5m3水力停留时间=280.5m3÷[750×(1-0.15)]m3/d=0.44d进水COD浓度为2200mg/L,去除率为70%,出水的COD浓度为660mg/L。
沼气产量=1402.5kgCOD/d×0.7×0.5Nm3/kgCOD=490Nm3/d2.4.3 高效生物接触氧化池有机负荷=[750×(1-0.15)]m3/d×0.66kgCOD/m3=420.8kgCOD/d有效容积=420.8kgCOD/d÷2kgCODm3·d=210m3水力停留时间=210m3÷[750×(1-0.15)]m3/d=0.33d进水COD浓度为660mg/L,去除率为70%,出水的COD浓度为200mg/L,达到排放标准。