硬质合金压制过程中的压力分布
浅析硬质合金棒材压制模具的设计

管理及其他M anagement and other 浅析硬质合金棒材压制模具的设计彭 聪摘要:硬质合金是由难熔性金属的硬化物与黏结金属通过一定技术手段制成的合金材料,它的硬度高,耐磨性和韧性都非常好,即便是在1000℃的温度中,硬度依然很高。
由于此类材料的优势突出,因此在我国的汽车、钢铁以及交通运输等众多行业中都有非常广泛的应用。
但是由于我国硬质合金工业的起步比较晚,在压制模具方面还有很多不足,需要不断提升自身的技术水平,为我国工业发展提供技术支持。
本文主要介绍了硬质合金棒材压制模具的原理,并对模具设计的关键因素和内容进行了重点分析,以此来改进模具结构,提高工艺水平,延长模具的使用寿命。
关键词:硬质合金;棒材;压制模具硬质合金凭借自身的优势,在机床道具、采掘工具以及各种成型装置中的应用都非常广泛,其中应用比较多的就是机床刀具材料,例如车刀、刨刀等,它们能够完成各种钢材的切割。
例如自蔓延高温合成技术,已经作为新的材料制备技术而深受大家关注。
该技术的应用合成过程更加简单,耗能低,不需要额外再提供其他能量,而且反应温度比较高,能够将反应物中的杂质充分挥发出去,获得性能更好的原材料。
我国也要在各种先进方法的基础上,不断提升硬质棒材的加工质量,为我国工业发展做出更多贡献。
1 硬质合金棒材压制模具的成型原理当混合材料通过模拟鉴定没有任何问题之后,就可以正式进入硬质压制成型的阶段,由于硬质合金的主要成分是WC和TiC等硬质相,它们的硬度和抗压强度都很高,在压制过程中很难成型,需要添加成型机,以此来提高材料的流动性和润滑性,加速粉末的黏结,使压坯密度分布更加均匀,以便于后期的加工。
当压坯脱模时,即是将压力除去,由于弹性内应力产生的松弛作用而造成体积膨胀现象,统称为弹性后效。
压坯的三大缺陷分别是分层、裂纹和未压好,是对于工作人员而言,尽量降低缺陷问题十分重要。
首先是混合料的成分,弹性后效值会随着粉末硬度的提高而提升;如果粉末粒度比较细、颗粒之间黏结性比较差等都会导致弹性后效增大。
硬质合金的生产工艺流程

硬质合金的生产工艺流程
硬质合金生产包括混合料制备、成形、烧结3个主要工艺流程、生产产品或所用装备流程图如下:
配料
湿磨
掺胶、干燥、制粒
混合粒
成形
烧结
硬质合金
硬质合金生产中的形成剂
(1)形成剂的作用
硬质合金混合料在形成前一般应加入形成剂。
形成剂的主要作用都是增加粉末粘性,方便实现形状,提高压胚强度。
由于作为硬质合金基体成分的难溶金属硬质合化物具有高硬度、高弹性模量、高抗压强度等特性,其粉末在压制过程中难以生产塑性变形,应添加足够数量的成型剂,使粉末能在较低的压力下回想粘结而成形。
添加成型剂的另一个作用是便于制粒,改善粉末的流动性和润滑性,有利于压胚密度的均匀分布。
硬质合金混合料粉末添加成型剂后,粉末颗粒被形成剂所包裹,这种起保护作用,可大幅度降低粉末的氧化速度,使压胚经较长时间存放而不发生明显氧化。
加入成型剂时,要特别注意成型剂的增碳作用和随之带入杂质,这些都会对硬质合金性能生产不良影响。
浅谈硬质合金粉末压模设计制造中的常见问题及对策

浅谈硬质合金粉末压模设计制造中的常见问题及对策硬质合金粉末压模是一种制造高硬度和高强度零件的重要工艺。
然而,在设计和制造过程中,常常会出现一些常见问题。
本文将就这些问题及其对策进行浅谈。
问题一:压制后零件表面粗糙度过高造成表面粗糙度过高的原因可能是压模表面粗糙度太高或模具的非对称性造成的不均匀变形。
对策是先充分优化模具表面质量,保证其表面粗糙度在需要范围内,一般不超过Ra0.4μm,然后在开发模具前应通过模拟的方法寻找非对称性变形的原因,采取相应的对策,如优化压力分布等,以保证零件表面粗糙度在合理范围内。
问题二:零件误差过大零件误差大多数情况下是由模具设计不合理或者制造过程中的误差引起的。
对策是优化模具的设计,要考虑到零件的形状,尺寸和结构特征,确保模具的尺寸和精度要求在合理范围内。
在制造过程中,需要对模具进行精确加工和组装,减少模具制造中的误差,如对模具中的每个部件进行测量和校正,并且在每个步骤结束后进行全面检查。
问题三:零件的强度不均匀零件的强度不均匀可能由压模时的非对称变形和热处理不均匀引起。
对策是通过模拟工具预测和优化变形,避免非对称变形,同时在热处理过程中采取适当的温度和时间控制,确保零件中的铸造组织均匀,并且使用高精度的测量设备检查其强度。
问题四:模孔磨损模具工作时,由于力的作用及颗粒的冲击导致模孔磨损。
对策是在设计和制造时考虑到硬质合金材料的特性,选择适当的硬质合金材料,保证其硬度高,耐磨性好。
这样不仅可以延长模具寿命,而且可以减少换模次数和其它维护费用。
总之,硬质合金粉末压模设计制造中的常见问题及其对策需要从多个方面入手,如合理的设计,优化工艺参数和使用合适的材料,并始终保持高质量的制造和检测,才能确保零件的品质和稳定性。
压制压力对合金产品的影响

表1 原料球磨制粒后 的参数
牌号 编号
A
B
前常用的仿 D o r s t 压机是通过控制产品的单 重与高 度 来压 制产 品 , 将 压力 作 为 一 个 变量 。而 在 实 际情
况 中, 不 使用 一定 的压力 将 粉 末 压 制成 一 定 密 度 的
压坯 , 仅 靠 自然堆 积 而成 的粉 或 者 压力 不 够 的产 品
2 0 1 5年第 4 9卷 N o . 6 的影 响
王权 , 彭建财 , 陈德 平 , 朱 国丽 , 任 达平
成 都工 具研 究所 有 限公 司
摘 要 :选 用 不 同粗 细 粒 度 的 原 材 料 , 采用进 口 D o r s t 压机, 研 究 了压 力 大 小 对 压 坯 密 度 以及 线 收 缩 系 数 的 影
1 引 言
作为硬质合金毛坯制备工艺三要素之一 , 压制 对 硬质 合 金制 品 的性 能存 在 决 定 性 的影 响 , 是保 证
毛坯几 何形 状 、 尺 寸精 度 以及 内在质 量 的关 键技 术 , 它 综合 反 映 了粒 料 的性能 以及模 具 的制作 水平 。制 品单重 、 高 度尺 寸 以及 压力 综合 控制 产 品的质 量 , 目
指导意义 。 2 试 验 原 料 及 方 法
本试 验采 用原 料粒 度 分别 为 l O p  ̄ m、 4 m、 3 i x m、
l m的 WC, 经 过成 分 配 比后 , 采 用 滚 筒 球磨 , 为使 石蜡混 合更 加均 匀 , 采用 己烷 作为 湿磨介 质 , 球磨 后 采用滚 筒 制粒 , 制粒 后 参 数 如 表 1 所示 , 其 中, 相对 松装 密度 是指料 的松 装密 度 与烧结 致密 后产 品密 度
浅谈硬质合金粉末压模设计制造中的常见问题及对策

浅谈硬质合金粉末压模设计制造中的常见问题及对策在硬质合金粉末压模设计制造过程中,常常会遇到一些常见问题,这些问题会对产品质量和生产效率造成一定的影响。
下面我将就硬质合金粉末压模设计制造中常见问题及对策进行浅谈。
第一个常见问题是模具设计时出现的粉末堆积问题。
硬质合金粉末在模具中的堆积会导致压制过程中出现气孔或者不均匀的密度分布,从而影响产品的机械性能。
解决这一问题的对策是根据不同的产品形状和工艺要求,设计合理的模具结构,确保粉末能够均匀分布,避免堆积现象的发生。
第二个常见问题是模具磨损问题。
在硬质合金粉末压模的制造过程中,模具会受到高压和摩擦的作用,容易出现磨损现象。
模具的磨损会导致产品尺寸不稳定、形状偏差增大等问题。
为了解决这一问题,可以采取以下对策:在模具材料的选择上尽量选择硬度高、耐磨性好的材料;在模具的表面上添加一层涂层,以增加模具的使用寿命;定期对模具进行维护保养,及时修复磨损。
第三个常见问题是模具结构设计不合理导致成型瑕疵。
硬质合金粉末压模制造过程中,模具的结构设计不合理可能导致产品成型瑕疵,比如出现裂纹、扭曲等问题。
为了避免这些问题的发生,应该根据产品的具体要求,合理设计模具结构,确保产品的成型质量。
第四个常见问题是模具加工精度不高。
模具加工精度的高低直接影响到产品的尺寸精度和形状精度。
在硬质合金粉末压模制造过程中,如果模具加工精度不高,将会导致产品的尺寸偏差过大,形状精度下降。
为了提高模具加工精度,可以采取以下对策:选用加工设备和工具要求精度高;制定严格的加工工艺规范,确保每个加工环节的准确性;进行工装夹具的检测和校验,确保模具加工的准确性。
在硬质合金粉末压模设计制造过程中,常见的问题包括粉末堆积、模具磨损、模具结构不合理和模具加工精度不高等。
针对这些问题,可以采取一些对策,如设计合理的模具结构、选择耐磨性好的模具材料、定期进行模具维护保养以及严格控制模具加工工艺等。
这样可以有效地解决这些问题,提高硬质合金粉末压模制造的生产效率和产品质量。
浅谈硬质合金粉末压模设计制造中的常见问题及对策
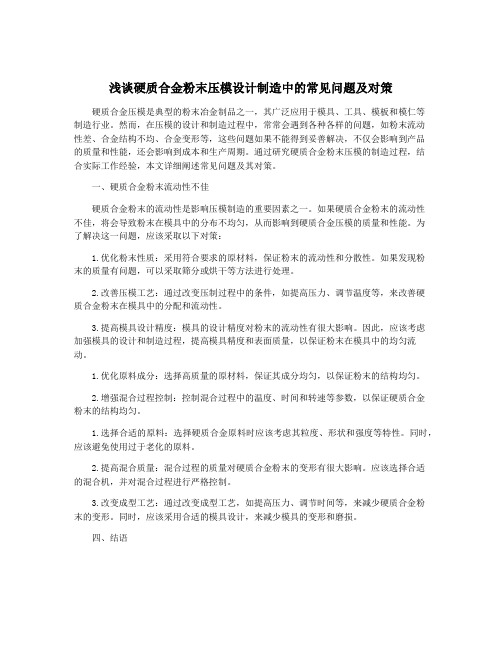
浅谈硬质合金粉末压模设计制造中的常见问题及对策硬质合金压模是典型的粉末冶金制品之一,其广泛应用于模具、工具、模板和模仁等制造行业。
然而,在压模的设计和制造过程中,常常会遇到各种各样的问题,如粉末流动性差、合金结构不均、合金变形等,这些问题如果不能得到妥善解决,不仅会影响到产品的质量和性能,还会影响到成本和生产周期。
通过研究硬质合金粉末压模的制造过程,结合实际工作经验,本文详细阐述常见问题及其对策。
一、硬质合金粉末流动性不佳硬质合金粉末的流动性是影响压模制造的重要因素之一。
如果硬质合金粉末的流动性不佳,将会导致粉末在模具中的分布不均匀,从而影响到硬质合金压模的质量和性能。
为了解决这一问题,应该采取以下对策:1.优化粉末性质:采用符合要求的原材料,保证粉末的流动性和分散性。
如果发现粉末的质量有问题,可以采取筛分或烘干等方法进行处理。
2.改善压模工艺:通过改变压制过程中的条件,如提高压力、调节温度等,来改善硬质合金粉末在模具中的分配和流动性。
3.提高模具设计精度:模具的设计精度对粉末的流动性有很大影响。
因此,应该考虑加强模具的设计和制造过程,提高模具精度和表面质量,以保证粉末在模具中的均匀流动。
1.优化原料成分:选择高质量的原材料,保证其成分均匀,以保证粉末的结构均匀。
2.增强混合过程控制:控制混合过程中的温度、时间和转速等参数,以保证硬质合金粉末的结构均匀。
1.选择合适的原料:选择硬质合金原料时应该考虑其粒度、形状和强度等特性。
同时,应该避免使用过于老化的原料。
2.提高混合质量:混合过程的质量对硬质合金粉末的变形有很大影响。
应该选择合适的混合机,并对混合过程进行严格控制。
3.改变成型工艺:通过改变成型工艺,如提高压力、调节时间等,来减少硬质合金粉末的变形。
同时,应该采用合适的模具设计,来减少模具的变形和磨损。
四、结语综上所述,硬质合金粉末压模的制造过程中存在着众多的问题。
然而,通过仔细分析和掌握制造过程的关键要素,采取适当的对策,我们就能够解决这些问题,提高硬质合金压模的质量和性能。
模压压制参数管理规范

模压压制参数管理规程1 压制试压和工艺参数决定程序图2 压制成型的常见符号及其含义2.1 范围本标准规定了硬质合金生产过程中压制成型的常见符号及其含义。
2.2 内容D(或ρs)——烧结密度( g/cm3 );Ρp ——压制密度( g/cm3 );ρrel ——相对密度( g/cm3 );C1 ——烧损( 2~4 % );Vs ——烧结毛坯体积( cm3 );Vp ——压坯体积( cm3 );Hs ——烧结毛坯高度(压制方向)尺寸(mm);Hp ——压制高度(压制方向)尺寸(mm);Bs ——烧结毛坯宽度尺寸(mm);Ls ——烧结毛坯长度尺寸(mm);K ——收缩系数(%);Ms ——烧结毛坯单重(g);Mp ——压制单重(g);PV ——压制行程(mm);L ——压制位置值(mm);OB ——顶压行程(mm);AB ——下拉行程(mm);P ——压力;F ——压强;f ——摩擦力;μ——摩擦系数;σ——法向应力;τ——剪切应力;Pd ——粉末的松装密度(g/cm3);Fr ——粉末的霍尔流量(s/25cc);PR ——软质返回料(如: 喷雾干燥的尾料、压制的废压坯等);3 压制工艺参数及其计算3.1 范围本标准规定了硬质合金生产过程中压制工艺参数及其计算。
3.2 范围3.2.1 工艺参数计算的条件(1). 毛坯图:查取毛坯尺寸(Hs、Bs 、Ls、等)及其允许公差;(2). 压模图:查取毛坯体积(Vs)、收缩系数(K)、压制位置值(L);(3). 混合料参数:查取烧结密度(D)、烧损(C1)。
3.2.2 工艺参数内容及其计算(1) 压制单重(Mp):计算如下式(1)Mp = Vs×D×C1/1000 (1)(2) 压制高度(Hp):计算如下式(2)Hp = Bs×(K宽+ 0.015) (2)(3) 压制行程(PV):计算如下式(3)PV ≈0.5×Hp (参考值,最终以Mp来定) (3)(4) 压制位置(L):计算如下式(4)L = 1.5×Hp (4)(5) 下拉行程(AB):计算如下式(5)AB = L +(0~0.3)(参考值,最终以压坯推出来定) (5)4 压制品的质量标准4.1 范围本标准规定了硬质合金生产过程中压制品的质量标准。
压制压强对WC-8%Ni硬质合金性能的影响

制造教育部重点实验室,山东大学机械工程学院,山东大学 航空构件制造技术及装备研究中心,250061济南市
FirstAuthor:TianHaidong,Postgraduate,KeyLaboratoryof HighEfficiencyandCleanMechanicalManufacture,Shandong University,MinistryofEducation,SchoolofMechanicalEngineer ing,ShandongUniversity,ResearchCenterforAeronauticalCom
ponentManufacturingTechnologyandEquipment,ShandongUni versity,Jinan250061,China
通信作者:国凯,助理研究员,山东大学高效洁净机械制 造教育部重点实验室,山东大学机械工程学院,山东大学航 空构件制造技术及装备研究中心,250061济南市
40
工具技术
压制压强对 WC8%Ni硬质合金性能的影响
李亚军1,3,栾道成1,袁宏辉2,孙文文1,王正云1,邓天鑫1,李缘1,任阳1,左城铭1
1西华大学;2 成都工具研究所有限公司; 3中国石油集团济柴动力有限公司成都压缩机分公司
摘要:采用不同的压制压强 160MPa、240MPa、320MPa、400MPa压制 WC8%Ni硬质合金 B型试样,在真空烧
Keywords:compactingpressure;WC8%Nicementedcarbides;relativedensity;hardness;traversestrength
硬质合金刀片生产工艺流程

硬质合金刀片生产工艺流程英文回答:The production process of hard alloy blades involves several steps. Let's take a look at the detailed process:1. Material selection: The first step in the production process is to select the appropriate materials for the hard alloy blades. Typically, hard alloy blades are made from a mixture of tungsten carbide and cobalt. The proportion of these materials can vary depending on the desired properties of the blades.2. Mixing: Once the materials are selected, they are mixed together in a ball mill. This process ensures that the tungsten carbide particles are evenly distributed throughout the mixture. The mixing time and speed are carefully controlled to achieve a homogeneous mixture.3. Pressing: After the mixing process, the mixture ispressed into the desired shape using a hydraulic press. This step is crucial as it helps in compacting the powder and forming a solid shape. The pressure applied during pressing is carefully controlled to ensure uniformity and density.4. Pre-sintering: The pressed blades are then subjected to pre-sintering. This involves heating the blades in a furnace at a specific temperature. Pre-sintering helps in removing any binders or lubricants that were used during the pressing process. It also helps in further strengthening the blades.5. Shaping and grinding: After pre-sintering, the blades are shaped and ground to the desired dimensions. This is done using precision grinding machines. The blades are carefully measured and ground to achieve the required shape, size, and sharpness.6. Sintering: The shaped blades are then subjected to a high-temperature sintering process. This involves heating the blades in a furnace at a temperature close to themelting point of tungsten carbide. During sintering, the tungsten carbide particles bond together, forming a dense and hard structure.7. Cooling and finishing: Once the sintering process is complete, the blades are cooled down gradually to room temperature. This helps in relieving any residual stresses and ensures dimensional stability. After cooling, the blades undergo finishing processes such as polishing and coating to enhance their performance and durability.中文回答:硬质合金刀片的生产工艺流程包括以下几个步骤:1. 材料选择,生产硬质合金刀片的第一步是选择合适的材料。
硬质合金混合与成形

汽油溶液1800毫升。
✓ 灰分问题:
• 橡胶汽油溶液
浓度(wt%)
4-4.5
灰分(wt%)
≤ 0.035
• 石蜡汽油溶液:基本无灰分
10-11 ≤0.07
13.5-14 ≤0.11
12
粒料的制备
料粒的制备主要包括掺胶(或掺蜡)和制粒两道主要工序 掺胶(蜡)过程:掺和-干燥-擦筛
拌和机
电热干燥箱、蒸汽干燥柜
烧结后制品的强度、硬度及性能的同一性,皆取决于密度分布的 均匀程度。此外,压坯密度分布不均匀,在烧结时,将使制品中 产生很大的应力,从而导致收缩的不均匀、翘曲,甚至产生裂纹。 影响压坯密度分布均匀性的因素中,压坯的侧正面积比、压制方 式和摩擦系数是起决定性作用的。
提高坯件密度分布的方法:减小模壁摩擦;增大压制压力;双向 压制工艺;运用浮模原理;减小坯件高度直径比;利用预压工艺。
三种基本压制方式
单向压制:单向压制时凹模和下凸模不动,由上凸模单向加压。此时, 因摩擦力作用使得制品上下两端的密度不均匀。单向压制的优点是模具 简单,操作方便,生产效率高。缺点是只适于压制高度较小的制品。
双向压制:双向压制时,凹模固定不动,上下凸模以大小相等方向相反 的压力同时加压。这种压坯中间密度低,二端密度高而且相等。正如两 个条件相同的单向压坯,从尾部连接起来一样。适于压制较长的制品。
1
硬质合金粉末的混合
相同化学组成的粉末的混合叫做和批。两种以上的化学组元相 混合,叫做混合。混合的目的是使性能不同的组元形成均匀的 混合物,以利压制和烧结时状态均匀一致。
混合好的硬质合金粉末通常需要过筛,以除去较大的夹杂和润 滑剂的快状凝聚物。混好的粉末尽可能及时使用,否则应密封 贮存起来,运输时应减少振动,防止混合料发生偏析。
硬质合金制备过程中的基本原理、烧结工艺及应用培训
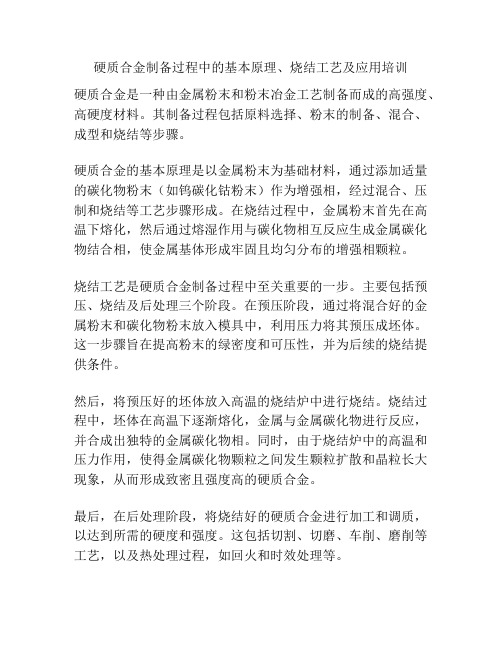
硬质合金制备过程中的基本原理、烧结工艺及应用培训硬质合金是一种由金属粉末和粉末冶金工艺制备而成的高强度、高硬度材料。
其制备过程包括原料选择、粉末的制备、混合、成型和烧结等步骤。
硬质合金的基本原理是以金属粉末为基础材料,通过添加适量的碳化物粉末(如钨碳化钴粉末)作为增强相,经过混合、压制和烧结等工艺步骤形成。
在烧结过程中,金属粉末首先在高温下熔化,然后通过熔湿作用与碳化物相互反应生成金属碳化物结合相,使金属基体形成牢固且均匀分布的增强相颗粒。
烧结工艺是硬质合金制备过程中至关重要的一步。
主要包括预压、烧结及后处理三个阶段。
在预压阶段,通过将混合好的金属粉末和碳化物粉末放入模具中,利用压力将其预压成坯体。
这一步骤旨在提高粉末的绿密度和可压性,并为后续的烧结提供条件。
然后,将预压好的坯体放入高温的烧结炉中进行烧结。
烧结过程中,坯体在高温下逐渐熔化,金属与金属碳化物进行反应,并合成出独特的金属碳化物相。
同时,由于烧结炉中的高温和压力作用,使得金属碳化物颗粒之间发生颗粒扩散和晶粒长大现象,从而形成致密且强度高的硬质合金。
最后,在后处理阶段,将烧结好的硬质合金进行加工和调质,以达到所需的硬度和强度。
这包括切割、切磨、车削、磨削等工艺,以及热处理过程,如回火和时效处理等。
硬质合金的应用非常广泛,常见的应用包括切削工具、矿业工具、电子元件等领域。
由于硬质合金具有极高的硬度、耐磨性和耐腐蚀性,因此在切削加工领域被广泛应用于车削、钻孔、铣削和切割等工艺中。
同时,在矿业工具领域,硬质合金可以用作凿岩钻头、矿山钻头等,因为它的耐磨性和强度能够满足严苛的工况要求。
在电子元件领域,由于硬质合金具有优异的导热性和耐腐蚀性能,因此常用于制造散热器、金属工具接触点等。
总之,硬质合金的制备是一个复杂的过程,包括原料选择、混合、成型和烧结等多个步骤。
通过控制工艺参数和多次迭代优化,可以获得具有优异性能的硬质合金材料,满足不同领域的应用需求。
硬质合金压制保压时间

硬质合金压制保压时间1.引言1.1 概述概述:硬质合金作为一种重要的工程材料,在现代制造业中扮演着重要角色。
其独特的硬度、耐磨性以及高温抗腐蚀性使得它广泛应用于切削工具、矿山设备、粉末冶金等领域。
在硬质合金的制备过程中,压制保压时间是一个关键参数。
本文旨在探讨硬质合金压制保压时间对其性能的影响,以及确定最佳保压时间的方法。
通过对硬质合金的研究,我们了解到压制保压时间是指将混合粉末放入模具中,施加压力并保持一定时间的过程。
在此过程中,粉末颗粒相互间的结合会得到加强,形成致密的结构,从而提高硬质合金的机械性能。
保压时间的长短决定了合金中的气孔、缺陷等问题的解决程度,对硬质合金的性能起着重要作用。
研究表明,过短的保压时间会导致硬质合金中气孔的残留,破坏了其致密性,降低了硬度和抗磨性能。
而过长的保压时间则会使得硬质合金中晶粒长大,从而降低了合金的硬度和强度。
因此,确定适当的保压时间是硬质合金制备过程中必须重视的问题。
在确定最佳保压时间时,首先需要考虑硬质合金的成分、颗粒大小和形状等因素。
此外,还需要考虑硬质合金的用途和要求的性能指标。
通过实验和经验总结,可以根据具体情况确定最佳保压时间,以达到理想的性能。
总之,硬质合金压制保压时间是影响合金性能的关键因素。
不同的保压时间会对合金的致密性、硬度和强度产生不同的影响。
因此,为了获得优质的硬质合金产品,合理选择和控制保压时间至关重要。
在未来的研究中,我们还可以进一步探索保压时间与其他制备参数的相互关系,为硬质合金的制备提供更加准确和有效的指导。
1.2 文章结构文章结构是指文章的组织框架和布局,它对于读者来说非常重要,可以帮助读者更好地理解文章的内容和脉络。
本文的结构分为引言、正文和结论三个部分。
引言部分主要是对硬质合金压制保压时间这个主题进行概述和介绍。
首先,我们会对硬质合金的定义和应用进行简要说明,以便读者了解硬质合金的基本概念。
接着,我们会引出本文的研究重点——硬质合金压制保压时间,并解释为什么这个问题值得研究。
硬质合金b类孔的原因

硬质合金b类孔的原因硬质合金是一种非常重要的工程材料,广泛应用于各个领域。
其中,硬质合金b类孔是硬质合金中常见的一种缺陷。
那么,硬质合金b类孔的产生原因是什么呢?下面我们就来详细了解一下。
首先,我们需要了解硬质合金的组成和制备过程。
硬质合金是由钴基或镍基粘结相和硬质相组成的复合材料。
其中,粘结相起到固定和连接硬质相的作用,而硬质相则主要负责硬度和耐磨性。
在制备过程中,通常会将粘结相和硬质相混合,并通过高温高压下的烧结工艺进行烧结,最终形成硬质合金。
然而,在烧结过程中,由于各种因素的影响,很容易产生各种缺陷,其中b类孔就是其中之一。
b类孔指的是硬质合金中的气孔,也称为气泡孔。
这种孔隙通常呈圆形或椭圆形,大小不一,分布不均匀。
那么,为什么会产生b类孔呢?首先,烧结过程中的气体释放是产生b类孔的主要原因之一。
在烧结过程中,由于原料中含有一定的挥发性成分,当温度升高时,这些挥发性成分会逐渐释放出来。
而这些释放出来的气体在烧结过程中会形成气泡,从而导致b类孔的产生。
其次,原料中的杂质也是产生b类孔的重要因素。
在制备硬质合金时,原料中往往会存在一些杂质,如氧化物、碳化物等。
这些杂质在烧结过程中会发生化学反应或物理变化,从而产生气体,并形成b类孔。
此外,烧结温度和压力也会对b类孔的产生产生影响。
如果烧结温度过高或者压力不足,就会导致原料中的气体无法完全排出,从而形成b类孔。
另外,在烧结过程中如果温度和压力不均匀分布,也会导致b类孔的产生。
除了上述因素外,制备工艺和设备的问题也可能导致b类孔的产生。
例如,如果烧结时间过长或者烧结过程中存在振动或冲击等问题,都会对b类孔的形成造成影响。
总之,硬质合金b类孔的产生原因是多方面的。
烧结过程中的气体释放、原料中的杂质、烧结温度和压力以及制备工艺和设备等因素都会对b类孔的形成起到重要作用。
因此,在制备硬质合金时,需要严格控制这些因素,以减少b类孔的产生,提高硬质合金的质量和性能。
硬质合金压制保压时间 -回复

硬质合金压制保压时间-回复硬质合金压制保压时间的问题是一个涉及到材料科学和工艺学的重要议题。
硬质合金是一种由金属粉末和钎剂混合制备的材料,常用于切削工具、矿山钻头和金属加工等领域。
在硬质合金的制备过程中,压制保压时间起着至关重要的作用,直接影响到最终产品的质量和性能。
本文将一步一步回答硬质合金压制保压时间的问题,从材料选取、工艺设计到最佳保压时间的确定。
第一步:材料选取硬质合金的制备离不开合适的材料选择。
常见的主要成分有钨碳化物和钴。
其中,钨碳化物为硬质合金的硬质相,钴则起到连接硬质相的作用。
合适的材料选取应综合考虑硬度、熔点、热稳定性等因素。
硬度要足够高以保证刀具的耐磨性,熔点不能过低以免影响制备过程,热稳定性要好以防止在高温下发生相反应。
因此,在选择硬质合金材料时,需结合具体应用要求和工艺条件进行综合考虑。
第二步:工艺设计硬质合金的制备过程主要包括混合、压制和高温烧结三个步骤。
工艺设计是决定硬质合金质量和性能的关键因素之一。
压制保压时间在工艺设计中占据重要地位,其目的在于使混合料在压制过程中达到足够的密实度,从而保证烧结后具有良好的物理性能。
保压时间过短会导致材料密实度低,从而降低硬质合金的硬度和耐磨性;保压时间过长则会造成成本和时间上的浪费。
因此,合理确定保压时间对于硬质合金制备非常重要。
第三步:最佳保压时间的确定确定最佳保压时间需要综合考虑材料的固相反应速率、热稳定性以及其他工艺参数的相互作用。
一般来说,保压时间应该充分考虑反应速率和材料的热稳定性,以使得材料颗粒之间得到充分的结合和反应。
实际上,最佳保压时间还受到其他因素的影响,如保压力、压制温度等。
保压时间的确定需要进行多次实验,并根据实验结果进行优化和调整。
总结:硬质合金压制保压时间是一个涉及到材料科学和工艺学的重要议题。
在硬质合金的制备中,合适的材料选取和工艺设计至关重要。
最佳保压时间的确定需要综合考虑材料的固相反应速率、热稳定性,以及其他工艺参数的相互作用。
硬质合金废品的特征及成因

硬质合金常见不合格品的特征、产生原因及判定A1 脏化1、特征:制品内部有大小不等的孔洞,并在其相应部位的表面出现凸起(臌泡)、孔洞。
2、原因⑴高温烧结阶段,烧结体内部反应所生成的气体已经逸出或转移到制品的表面,此时液相已开始凝固,气体逸出所留下的小眼来不及恢复,转移到表面的气体没有完全排除。
⑵某些难还原氧化物在出现液相的温度才被还原,还原产生的气体的压力大于液相收缩的阻力而形成鼓泡;⑶温度过高(过烧),使液相大量增加和外聚,形成鼓泡;⑷压块中的杂质,如合金碎削,铜丝等也可产生鼓泡(脏化);⑸压制品严重分层,烧结时也可以表现为鼓泡。
3、脏化来源⑴ 氧化块料、氧化颗粒料、废压坯⑵ 金属杂质:筛网屑、钴屑⑶ 非金属杂质:陶瓷片、玻璃片、装舟填料、灰尘、毛刷屑等⑷ 成型剂:未去除的机械杂质,未过滤的凝胶,不均匀的的成型剂、老化的成型剂等。
4、判断:表面轻微脏化,允许加工,加工表面没有孔洞,作合格品放行;表面严重脏化、膨泡,应判为废品。
A2 变形和弯曲1、特征:制品几何形状发生不规则的变化,弯曲制品在某一平面呈现某种有规律的曲面变形。
2、原因⑴ 压制品密度不均匀,因而烧结时收缩不均匀,密度大的部位收缩少,密度小的部位收缩图27用圆钢模圧制的棒材和用平钢模屋制的一字型钎头烧结后的变形行为⑵ 压坯周围不均匀的碳气氛造成产品的变形⑶ 压坯在烧结过程中所处环境温度的不均匀造成其变形⑷其他几种原因:装舟不合理、垫板不平。
3、判定:按标准或产品图样要求检查,超差的返回生产单位处理,无法处理的判废。
A3 起皮1、特征:制品边缘棱角部位出现分枝状不规则裂纹、龟裂或翘壳。
轻者呈网状龟裂,重者呈小片剥落;严重时则爆裂剥落,在起皮部位可清楚地看到棉絮状碳黑聚积物。
2、原因:⑴在低温带气相中含碳气体浓度过高,高浓度的含碳气体进入制品的薄弱部位(制品的棱角处往往密度较低或弹性后效严重),在钻的接触作用(催化)下,产生碳的沉淀反应:CH—C+H 2CO f C+CO沉淀出的碳破坏了合金的连续性,造成合金的起皮,即含碳气氛分解出大量游离碳是产生起皮的主要原因。
硬质合金刀片压制工艺的顶压行程
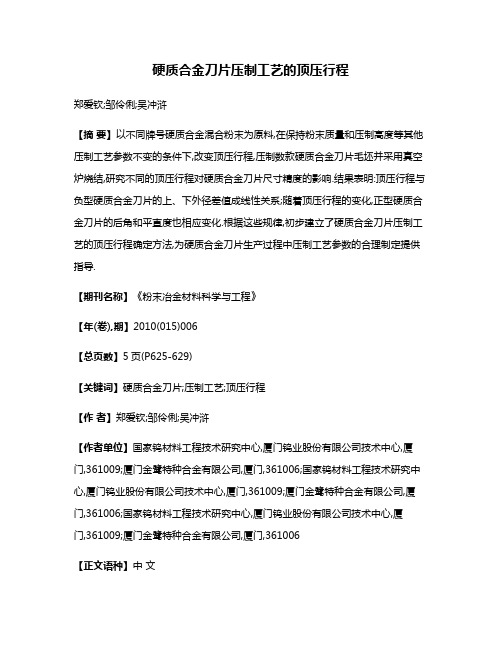
硬质合金刀片压制工艺的顶压行程郑爱钦;邹伶俐;吴冲浒【摘要】以不同牌号硬质合金混合粉末为原料,在保持粉末质量和压制高度等其他压制工艺参数不变的条件下,改变顶压行程,压制数款硬质合金刀片毛坯并采用真空炉烧结,研究不同的顶压行程对硬质合金刀片尺寸精度的影响.结果表明:顶压行程与负型硬质合金刀片的上、下外径差值成线性关系;随着顶压行程的变化,正型硬质合金刀片的后角和平直度也相应变化.根据这些规律,初步建立了硬质合金刀片压制工艺的顶压行程确定方法,为硬质合金刀片生产过程中压制工艺参数的合理制定提供指导.【期刊名称】《粉末冶金材料科学与工程》【年(卷),期】2010(015)006【总页数】5页(P625-629)【关键词】硬质合金刀片;压制工艺;顶压行程【作者】郑爱钦;邹伶俐;吴冲浒【作者单位】国家钨材料工程技术研究中心,厦门钨业股份有限公司技术中心,厦门,361009;厦门金鹭特种合金有限公司,厦门,361006;国家钨材料工程技术研究中心,厦门钨业股份有限公司技术中心,厦门,361009;厦门金鹭特种合金有限公司,厦门,361006;国家钨材料工程技术研究中心,厦门钨业股份有限公司技术中心,厦门,361009;厦门金鹭特种合金有限公司,厦门,361006【正文语种】中文【中图分类】TF124.3随着制造业的高速发展,汽车工业、航空航天工业以及模具行业等重点产业部门对切削加工不断提出更高的要求,数控机床、加工中心等先进设备向高速方向发展[1]。
与此同时,被加工工件材料也向难加工材料如钛合金等方向发展[2],而且被加工工件的形状也越来越复杂,要求的精度和表面光洁度越来越高,致使金属切削领域对硬质合金刀片的尺寸精度提出了越来越高的要求。
除了通过粉末成形设备的不断改进以提高压坯精度外[3],硬质合金刀片的尺寸精度主要通过磨削工序控制,这不仅导致材料的浪费,而且导致刀片的生产工序长、生产成本较高。
因此,通过研究精密压制技术,生产出尺寸精度较高的刀片毛坯,减小磨削余量,有利于节约生产成本[4],缩短数控刀片生产周期,提高生产效率。
硬质合金孔隙度

硬质合金孔隙度硬质合金是一种由金属粉末和粉末冶金技术制成的复合材料,具有高硬度、高强度、耐磨损等优良性能,广泛应用于工业领域。
然而,在硬质合金的制备过程中,孔隙度是一个重要的参数,它直接影响着合金的性能和使用寿命。
硬质合金的孔隙度是指合金中存在的空隙或孔洞的百分比。
通常情况下,合金的孔隙度越低,材料的密度和硬度就越高。
因此,减小硬质合金的孔隙度是提高其性能的关键。
在硬质合金的制备过程中,合金粉末经过混合、压制和烧结等工艺步骤,形成致密的块状材料。
然而,由于粉末的颗粒性质和工艺条件的限制,合金中往往会存在一定的孔隙。
这些孔隙可以是微观的,如粉末颗粒之间的间隙,也可以是宏观的,如烧结过程中形成的气孔或裂纹。
孔隙度的大小与合金的制备工艺密切相关。
合金制备工艺中的每个步骤都会对孔隙度产生影响。
首先,合金粉末的选择和处理对孔隙度有重要影响。
粉末的颗粒大小、形状和分布会影响合金的致密性。
其次,压制工艺中的压力和温度也会影响合金的孔隙度。
较高的压力和温度可以减少孔隙的形成,提高合金的致密性。
最后,烧结工艺中的温度和时间也会对孔隙度产生影响。
适当的烧结温度和时间可以消除或减小孔隙,使合金更加致密。
降低硬质合金的孔隙度对于提高其性能至关重要。
首先,较低的孔隙度可以提高合金的硬度。
孔隙的存在会导致应力集中,从而降低合金的硬度和强度。
其次,较低的孔隙度可以提高合金的耐磨性。
孔隙会导致摩擦表面的不均匀磨损,降低了合金的耐磨性能。
最后,较低的孔隙度可以提高合金的耐腐蚀性能。
孔隙是腐蚀介质的易侵入通道,会导致合金的腐蚀速率增加。
为了降低硬质合金的孔隙度,可以采取以下措施。
首先,选择合适的合金粉末。
粉末的颗粒应均匀细小,并具有良好的流动性。
其次,优化压制工艺。
合金粉末在压制过程中应受到均匀的压力分布,以减少孔隙的产生。
最后,合理控制烧结工艺参数。
烧结温度和时间应根据合金的成分和性能要求进行调整,以获得最佳的致密度和孔隙度。
硬质合金的孔隙度是影响其性能的重要参数。
- 1、下载文档前请自行甄别文档内容的完整性,平台不提供额外的编辑、内容补充、找答案等附加服务。
- 2、"仅部分预览"的文档,不可在线预览部分如存在完整性等问题,可反馈申请退款(可完整预览的文档不适用该条件!)。
- 3、如文档侵犯您的权益,请联系客服反馈,我们会尽快为您处理(人工客服工作时间:9:00-18:30)。
硬质合金压制过程中的压力分布
引起压力分布不匀的主要原因是粉末颗粒之间以及粉末与模壁之间的摩擦力。
压块高度越高,压力分布越不均匀。
实行双向加压或增大压坯直径,能减少压力分布的不均匀性。
四,压块密度分布:越是复杂的压块,密度分布越不均匀;除压力分布的不均匀(压力降)外,装粉方式不正确,使压块不同部位压缩程度不一致,也会造成压块密度不均匀。
1,填充系数:是指压块密度Y压与料粒的松装密度Y松的比值;压缩比:是指粉末料粒填装高度h粉与压块高度h压之比;在数值上填充系数和压缩比是相等的。
K=Y 压÷Y松=h粉÷h压2,为了减少压块密度分布的不均匀性:(1)提高模具的表面光洁度;(2)减少摩擦阻力;(3)提高料粒的流动性;(4)采用合理的压制方式; 3,粉末粒度对压制的影响;(1)粉末分散度越大(松装越小),压力越大。
压块密度越小;有较大的强度值,成型性好。
(2)料粒较粗,压块容易达到较高的压块密度,但其密度分布往往是不均匀的;一般情况下,压块强度随成型剂的加入量而提高。
五,硬质合金压块的弹性后效:1,弹性内应力:粉末颗粒内部和颗粒间接触表面上,由于原子间引力和吸力的相互作用,会产生一个与颗粒受力方向相反,并力求阻止颗粒变形,以便达到与压制压力平衡的作用力叫弹性内应力。
2,弹性后效:在除去压制压力和把压块脱模后,由于弹性内应力的松弛作用而引起压块体积膨胀的现象叫弹性
后效。
3,在许多情况下,压块脱模后发生弹性膨胀是造成压块裂纹和分层的原因。
4,粉末粒度细,颗粒粗糙程度降低,颗粒间结合强度降低(成型不足或含水量大)以及氧化物和杂质含量增加都会增加弹性后效。
料粒干燥太干而变硬,也会增加弹性后效.。