优选压铸工艺参数选择和计算
压铸原理及工艺参数选择
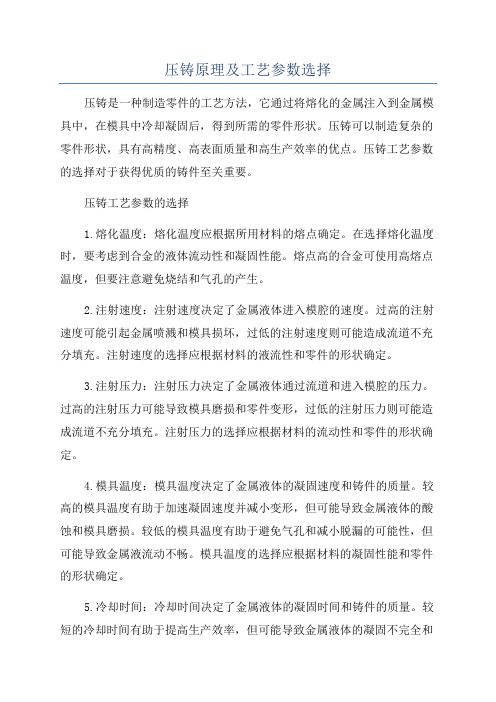
压铸原理及工艺参数选择压铸是一种制造零件的工艺方法,它通过将熔化的金属注入到金属模具中,在模具中冷却凝固后,得到所需的零件形状。
压铸可以制造复杂的零件形状,具有高精度、高表面质量和高生产效率的优点。
压铸工艺参数的选择对于获得优质的铸件至关重要。
压铸工艺参数的选择1.熔化温度:熔化温度应根据所用材料的熔点确定。
在选择熔化温度时,要考虑到合金的液体流动性和凝固性能。
熔点高的合金可使用高熔点温度,但要注意避免烧结和气孔的产生。
2.注射速度:注射速度决定了金属液体进入模腔的速度。
过高的注射速度可能引起金属喷溅和模具损坏,过低的注射速度则可能造成流道不充分填充。
注射速度的选择应根据材料的液流性和零件的形状确定。
3.注射压力:注射压力决定了金属液体通过流道和进入模腔的压力。
过高的注射压力可能导致模具磨损和零件变形,过低的注射压力则可能造成流道不充分填充。
注射压力的选择应根据材料的流动性和零件的形状确定。
4.模具温度:模具温度决定了金属液体的凝固速度和铸件的质量。
较高的模具温度有助于加速凝固速度并减小变形,但可能导致金属液体的酸蚀和模具磨损。
较低的模具温度有助于避免气孔和减小脱漏的可能性,但可能导致金属液流动不畅。
模具温度的选择应根据材料的凝固性能和零件的形状确定。
5.冷却时间:冷却时间决定了金属液体的凝固时间和铸件的质量。
较短的冷却时间有助于提高生产效率,但可能导致金属液体的凝固不完全和热裂纹的产生。
较长的冷却时间有助于提高铸件的密度和表面质量,但可能导致产量降低。
冷却时间的选择应根据材料的凝固性能和零件的形状确定。
总结压铸是一种高效、高精度的制造方法,工艺参数的选择对于获得优质的铸件至关重要。
在选择工艺参数时,要综合考虑材料的性质、零件的形状和制造要求,以及设备和模具的性能。
通过合理选择工艺参数,可以提高铸件的质量和生产效率,降低生产成本。
压铸参数计算
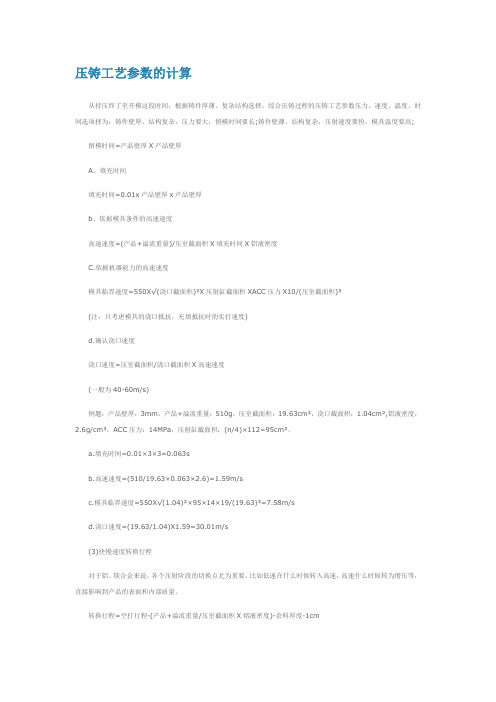
压铸工艺参数的计算从持压终了至开模这段时间,根据铸件厚薄、复杂结构选择。
综合压铸过程的压铸工艺参数压力、速度、温度、时间选项择为:铸件壁厚、结构复杂,压力要大,留模时间要长;铸件壁薄、结构复杂,压射速度要快,模具温度要高;留模时间=产品壁厚X产品壁厚A、填充时间填充时间=0.01x产品壁厚x产品壁厚b、依据模具条件的高速速度高速速度=(产品+溢流重量)/压室截面积X填充时间X铝液密度C.依据机器能力的高速速度模具临界速度=550X√(浇口截面积)²X压射缸截面积XACC压力X10/(压室截面积)³(注:只考虑模具的浇口抵抗,充填抵抗时的实打速度)d.确认浇口速度浇口速度=压室截面积/浇口截面积X高速速度(一般为40-60m/s)例题:产品壁厚:3mm,产品+溢流重量:510g,压室截面积:19.63cm²,浇口截面积:1.04cm²,铝液密度:2.6g/cm³,ACC压力:14MPa,压射缸截面积:(π/4)×112=95cm²。
a.填充时间=0.01×3×3=0.063sb.高速速度=(510/19.63×0.063×2.6)=1.59m/sc.模具临界速度=550X√(1.04)²×95×14×19/(19.63)³=7.58m/sd.浇口速度=(19.63/1.04)X1.59=30.01m/s(3)快慢速度转换行程对于铝、镁合金来说,各个压射阶段的切换点尤为重要,比如低速在什么时候转入高速,高速什么时候转为增压等,直接影响到产品的表面和内部质量。
转换行程=空打行程-(产品+溢流重量/压室截面积X熔液密度)-余料厚度-1cm(一般考虑到行程开关的反应时间,转换行程可以延长1cm)例题:产品+溢流重量:510g,压室截面积:19.63 cm²,空打行程:368mm,余料厚度:23mm,铝液密度:2.6g/cm³转换行程=36.8-(510/19.63X2.6)-2.3-1=235mm二、压力参数(1)铸造压力铸造压力是获得铸件组织致密和轮廓的主要因素,又是压铸区别于其他铸造方法的主要特征.其大小取决于压铸机的结构及功率。
第3讲 压铸工艺参数的选择
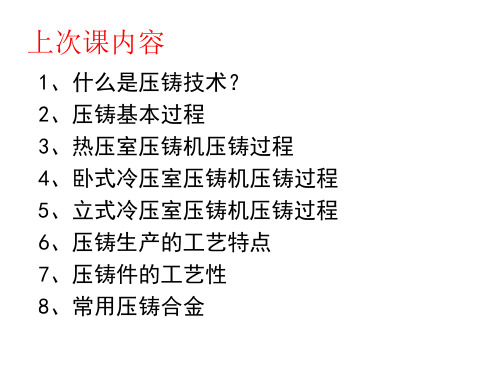
Fz主 pb A
式中:Fz主——主胀型力(N); pb ——压射比压(MPa); A ——压铸件在分型面的投影面积总和,一般另加30%作为浇注
系统与溢流排气系统的面积(mm2)。
(2)分胀型力
分胀型力:作用在滑块锁紧面上的法向分力引起的胀型力之和。 采用斜销抽芯、斜滑块抽芯机构时的分胀型力可按下式计算:
pb
Fy A
4Fy
d 2
式中:pb ——压射比压(MPa); Fy ——压射力; A ——压射冲头截面积(mm2); d ——压射冲头直径(mm)。
(2)压射比压的选择和调整
生产中根据铸件的形状尺寸、结构复杂程度、壁厚大小以 及压铸合金的特性和压铸温度,模具的浇注系统及排溢系统 设计情况等确定压射比压。
一般压铸件可按计算数值提高1.2倍,对有较大镶件的压铸 件或大模具压小铸件时可提高1.5~2倍。
2.充填速度
在压射冲头作用下,熔融合金通过内浇口进入型腔的线速度 称为充填速度。
充填速度偏低易造成铸件轮廓不清晰;采用较高的充填速度 可获得轮廓清晰、表面光洁的铸件。但是充填速度过高,易使 压铸件产生气泡,还会加速模具工作零件的磨损。
一.压力
1.压射力
压铸机压射缸内的工作液作用于 压射冲头,使其推动熔融合金充填 模具型腔的力。
(1)压射力变化规律 分为四个阶段: 第Ⅰ阶段:排气阶段; 第Ⅱ阶段:熔融合金堆积阶段; 第Ⅲ阶段:充填阶段; 第Ⅳ阶段:增压阶段。
(2)压射力计算
有增压机构时:
Fy
1 4
p zg D 2
无增压机构时:
Fz分 (A分 pb tan)
胀型力:
Fz FZ主 FZ分 (A A分 tan) pb
压铸件铸造工艺参数计算表
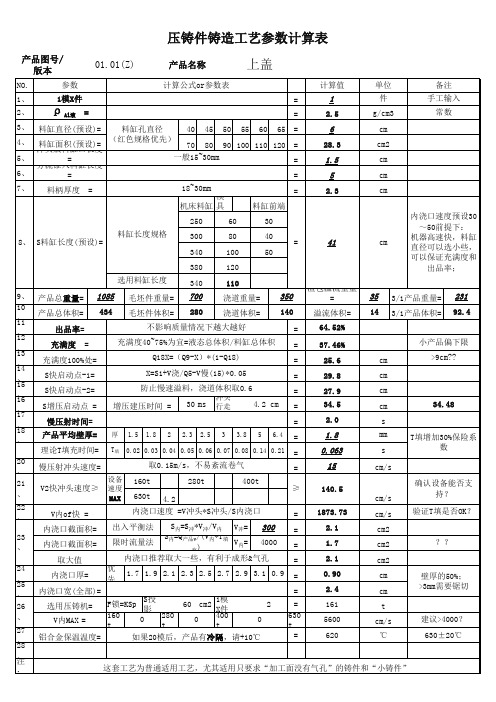
T填增加30%保险系 数
确认设备能否支 持?
验证T填是否OK?
内浇口截面积= 出入平衡法 S内=S冲*V冲/V内 V冲= 300
=
23 、
内浇口截面积=
限时流量法
S内=Q产品v/(V内*T填 充)
V内=
4000
=
取大值
内浇口推荐取大一些,有利于成形&气孔
=
24 、25
内浇口厚=
优 先
1.7 1.9 2.1 2.3 2.5 2.7 2.9 3.1 0.9
t cm/s
℃
??
壁厚的50%; >3mm需要锯切
建议>4000? 630±20℃
、注
:
这套工艺为普通适用工艺,尤其适用只要求“加工面没有气孔”的铸件和“小铸件”
1、
Al合金件
比压范围
一般件 30~50
受力件 45~80
外观或薄壁件 40~60
耐压件 80~120
耐压件
耐压件
耐压件
铝 合
280t
V2快冲头速度≥ 速度
MAX 630t 4.2
400t
≥
140.5
22
、
V内of快 =
内浇口速度 =V冲头*S冲头/S内浇口
= 1873.73
35 3/1产品重量= 231 14 3/1产品体积= 92.4
cm cm cm cm s mm s cm/s
cm/s cm/s
小产品偏下限 >9cm??
溢流体积= 64.52%
37.46% 25.6 29.8 27.9 34.5 2.0 1.8
理论T填充时间= T填 0.02 0.03 0.04 0.05 0.06 0.07 0.08 0.14 0.21 =
压铸工艺参数的计算调整
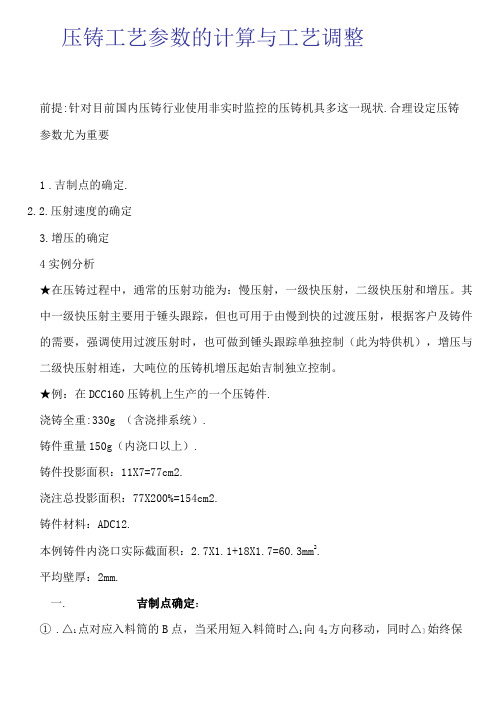
压铸工艺参数的计算与工艺调整前提:针对目前国内压铸行业使用非实时监控的压铸机具多这一现状.合理设定压铸参数尤为重要1.吉制点的确定.2.2.压射速度的确定3.增压的确定4实例分析★在压铸过程中,通常的压射功能为:慢压射,一级快压射,二级快压射和增压。
其中一级快压射主要用于锤头跟踪,但也可用于由慢到快的过渡压射,根据客户及铸件的需要,强调使用过渡压射时,也可做到锤头跟踪单独控制(此为特供机),增压与二级快压射相连,大吨位的压铸机增压起始吉制独立控制。
★例:在DCC160压铸机上生产的一个压铸件.浇铸全重:330g (含浇排系统).铸件重量150g(内浇口以上).铸件投影面积:11X7=77cm2.浇注总投影面积:77X200%=154cm2.铸件材料:ADC12.本例铸件内浇口实际截面积:2.7X1.1+18X1.7=60.3mm2.平均壁厚:2mm.一. 吉制点确定:①.△1点对应入料筒的B点,当采用短入料筒时△1向42方向移动,同时△]始终保持对应B点.②.△,点:当料温低或充填率低亦或薄壁铸件时,△2接近对应A点,反之接近43点.③.43点:通过计算L H来确定,通常锤头压射到43点时,合金液达到C点,如果需要提前及滞后充填,43相应右移及左移.④.△点:对应模具分型面,(同时不能超过射出行程的极限)4⑤为了确定43点,需要计算L HM=A P*L H* P ------------------------------- ⑴M:铸件重量(内浇口以上,含集渣包)A p:锤头截面积P :合金液体密度将数值代入6:150=兀R2*L H*P=3.14*2.52*L H*2.5求得 L =3.06cm H二.压射过程之速度确定:1.慢压射速度Vs的大小一般以合金液不从入料口溢出为原则。
通常Vs为0.2-0.4m/s之间为宜(可以不做调整)2.一级快压射速度的确定需要考虑锤头跟出及过渡性速度两种情况充填率$ =M总/ A p*LK* P -------------------- ⑵M总:包括浇排系统在内的铸件总重A p:锤头截面积4:空打行程代入数值:$二(3 3 0/0 . 78 5 *52 *32 *2 . 5)*100%=21% (标准 30%-70%)充填高:H=(D/2)*(1.66*$+0.17)H=(50/2)*(1.66*0.21+0.17)=13mm一级快压射速度V L=0.2* {(D-H)*(1-0)/(1+0)}1/2 ------------------------- ⑷V L=0.2* {(50-13)*(1-0.21)/(1+0.21)}1/2=0.98m/s 二级快压射速度的确定及二级手轮的调节方法:V PC tV H:V D0 V p0V g P a充填时间:t=(7/1000)*T2 ----------------- ⑸T:铸件平均壁厚t=(7/1000)*22 =0.028(s)内浇口速度:Vg*t*Ag* P =M -------------------- ⑹M:铸件重量(内浇口之上含集渣包)Vg*0.028*60.3*0.0025=150Vg=35500mm/s=35.5m/s(内浇口最小速度) 锤头实打速度:Qg二Qp(合金液通过任何截面的流量相等)Qg:内浇口处的流量Qp:锤头处的流量(入料筒处流量)Ag*Vg=Ap*Vp ----------------------------⑺60 . 3 *35 . 5=0 . 78 5*502 *V PVp=1.1m/s(此为最小锤头速度)Vp= 1.1m/s.取Vp=1.5m/s (模具所需)模具界限速度:当Pa=140kg/cm2 (系统压力)Vpc=550*(Pa*As*Ag2 /Ap3) 1/2 ------------------------------------ ⑻Vpc=550*{140*0 . 78 5*102 *0 . 62 /(0 . 78 5 *52尸}I/2=3.97 m/s 实打速度:Vp={(V产V)/( V D2+V PC2)} 1/2 --------------------------------- ⑼pc2Vp={(62*3.972)/( 62+3.972)}1/2=3.31 m/s(压铸机所供)3.31远大于1.5 能量过剩.即Pa不需要取140kg/cm2那么当Pa=100 kg/cm2时情况如下:V=3.97*(100/140)1/2=3.35 m/spc此时空打速度 V =6*(100/140)1/2=5 m/sDV J{(52*3.352)/( 52+3.352)}1/2=2.78 m/s通过比较可知:降低系统压力让压铸机与压铸模系统更匹配由上面公式⑼:V P={(V D2*V PC2)/( V D2+V PC2)} 1/2可以导出:丫:{"长2*丫//( V PC2-V P2)} 1/2 ------------------------------- ⑽当 V P =1.5m/s 时可得出二级快压射设定速度:V D={(3.352*1.52)/( 3.352-1.52)}1/2=1.68m/s手轮设置:【(12*12/5)为每1m/s时的格数】(12*12/5)*1.68=49 格即:手轮调节为4圈1格三.增压确定:P 取 100Mpa 时锁模力=A 总*P=154*100=154(T)A P * P = P Z * P Z ------------------------------------------------------- (11)(锤头部)(增压缸处)0 . 78 5 *52*100MPa=0.785*162*PZP =9.76 Mpa (增压缸需设置的压力)ZA P * P = A S * P S ------------------------------------------------------- ⑫(锤头部)(射出缸处)0 . 78 5 *52*100MPa=0.785*102*PSP S =25 MPa (射出缸压力表显示值)通过查看射出缸压力表(大表)读数核实是否为25MPa如数据不符,需要调整增压储能器的压力,另外,原则上增压流量手轮从3圈调起充填时间允许时,可调小增压流量,否则反之触发压力一般为50kg/cm2,充填时间允许时也可调小触发压力,否则反之四.实例分析:1.当 Vj1.5m/s 时通过 Ag * Vg = A P * V P60.3*Vg=0.785*502*1.5Vg = 48.8 m/s (标准为 20-60 m/s)说明内浇口截面积较小,内浇口处的龟裂现象也证实了这一点。
压铸工艺参数公式
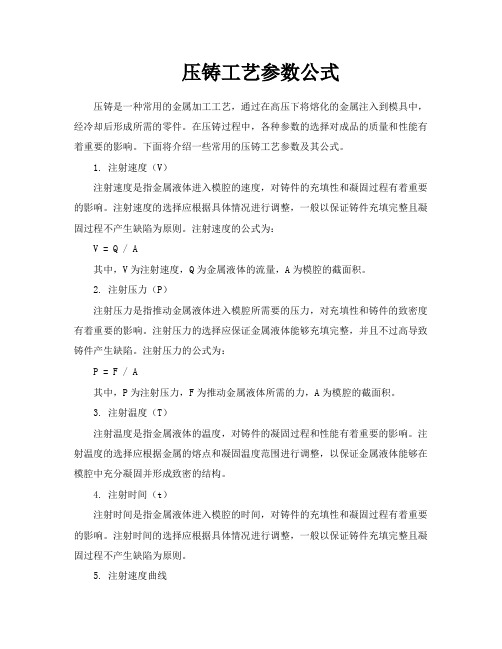
压铸工艺参数公式压铸是一种常用的金属加工工艺,通过在高压下将熔化的金属注入到模具中,经冷却后形成所需的零件。
在压铸过程中,各种参数的选择对成品的质量和性能有着重要的影响。
下面将介绍一些常用的压铸工艺参数及其公式。
1. 注射速度(V)注射速度是指金属液体进入模腔的速度,对铸件的充填性和凝固过程有着重要的影响。
注射速度的选择应根据具体情况进行调整,一般以保证铸件充填完整且凝固过程不产生缺陷为原则。
注射速度的公式为:V = Q / A其中,V为注射速度,Q为金属液体的流量,A为模腔的截面积。
2. 注射压力(P)注射压力是指推动金属液体进入模腔所需要的压力,对充填性和铸件的致密度有着重要的影响。
注射压力的选择应保证金属液体能够充填完整,并且不过高导致铸件产生缺陷。
注射压力的公式为:P = F / A其中,P为注射压力,F为推动金属液体所需的力,A为模腔的截面积。
3. 注射温度(T)注射温度是指金属液体的温度,对铸件的凝固过程和性能有着重要的影响。
注射温度的选择应根据金属的熔点和凝固温度范围进行调整,以保证金属液体能够在模腔中充分凝固并形成致密的结构。
4. 注射时间(t)注射时间是指金属液体进入模腔的时间,对铸件的充填性和凝固过程有着重要的影响。
注射时间的选择应根据具体情况进行调整,一般以保证铸件充填完整且凝固过程不产生缺陷为原则。
5. 注射速度曲线注射速度曲线是指注射过程中注射速度随时间的变化规律。
注射速度曲线的选择应根据具体情况进行调整,一般以保证铸件充填完整且凝固过程不产生缺陷为原则。
6. 注射压力曲线注射压力曲线是指注射过程中注射压力随时间的变化规律。
注射压力曲线的选择应根据具体情况进行调整,一般以保证铸件充填完整且凝固过程不产生缺陷为原则。
以上所述的压铸工艺参数及其公式只是一些常用的参考,实际应用中还需要根据具体情况进行调整和优化。
压铸工艺的优化是一个综合性的问题,需要考虑材料的性质、模具的设计、设备的性能等多个方面因素的综合影响。
压铸工艺参数计算表

理论T填充时间= T填 0.02 0.03 0.04 0.05 0.06 0.07 0.08 0.14 0.21 =
0.063
20 、 慢压射冲头速度=
取0.15m/s,不易紊流卷气
=
15
21 、
设备 160t
280t
V2快冲头速度≥ 速度
1、
Al合金件
比压范围
一般件 30~50
受力件 45~80
外观或薄壁件 40~60
耐压件 80~120
耐压件
耐压件
备注 手工输入
常数
内浇口速度预设30 ~50前提下:
机器高速快,料缸 直径可以选小些, 可以保证充满度和
出品率;
3/1产品重量= 231 3/1产品体积= 92.4
小产品偏下限 >9cm??
一般15~30mm
=
6、
=
=
7、 料柄厚度 =
18~30mm 模
机床料缸 具
= 料缸前端
计算值 1 2.5 6
28.3 1.5
5 2.3
250
60
30
料缸长度规格 8、 S料缸长度(预设)=
300
80
40
=
41
340
100
50
380
120
选用料缸长度
340
110
渣包溢流重量
9、 产品总重量= 1085 毛坯件重量= 700
34.48
T填增加30%保险系 数
确认设备能否支 持?
验证T填是否OK?
??
壁厚的50%; >3mm需要锯切
压铸工艺计算公式---6页

(如计算转换行程要再加料 饼厚+1.75cm=11.75cm)
VL=
700 + 3 = 10cm 38.5 × 2.6
VD---模具界限速度m/s=550× (内浇口截面积 cm2 )2 ×压射缸剖面积cm2×Acc管道压力kg/cm2÷(冲头剖面积cm2)3÷100
十一 VD= 550 ×
( Ag )2 × Ah × Acc ÷ 100 ( Ap )3
389 417 444 611 694 778 833 889
678 726 774 1065 1210 1355
471 504 538 739 840 941 1008 1076 1176 1277
346 370 395 543 617 691 741 790 864 938
560 600 640 880 1000 1120 1200 1280
2
压铸条件参数及公式代
10.Vg--- 内浇口速度:52m/s 11. Vp---冲头速度:1.75m/s 12. Vd---低速速度:0.22m/s 13. VL---高速区间:10cm 14. VD---模具界限速度:3.45m/s 15. qa---排气槽剖面积:0.9cm2 16. qv---排气槽气体速度: 75m/s 17. K----填充率: 27% 18. t----填充时间:0.04s 19. W---浇铸铝液重量:900g 20. WG--填充铝液重量:700g 21. L---空压射行程:33.7cm 22. P--- 压力 Q---流量
700
1.Vg---浇口速度m/s=冲头面积cm2×冲头速度m/s÷浇口面积cm2 Vg=
八
Vg=
极速了所以一般件不要超过此速度,主要
压铸工艺参数及计算公式

1、低速流量Q1=V1*AV1=冲头面积 3.14/4*D*D (D为锤头直径)A1=0.2M/S (低速速度为30CM每秒 为预估值)2、低速时间T1=V2/Q1V2流道系统体积由CAD内计算Q1低速流量公式1计算3、高速流量QH=V3进料口截面积*A2进料口速度进料口速度估计值与产品平均壁厚有关进料口速度估计为40M/S 转成4000CM/S进料口面积由CAD内计算4、高速时间TH=V4(产品+渣包的体积)/QH高速流量V4产品+渣包的体积由CAD内计算5、四段设定341 22点到3点加上0.005S时间4点时间为(3点时间+4点时间)的2-3倍计算公式 (单位:Q1低速流量T1低速时间V1锤头面积V2流道系统体积A1低速速度QH高速流量A2进料口速度V4产品+渣包的体积V3进料口截面积A3高速锤头速度TH高速时间单位:cm)Q1V1A1(CM/S)锤头直径MM圆周率3078.76153.9420140 3.14159T1V2Q10.3962636612203078.76QH进料口面积V3进料口速度A299600.0024.94000TH体积V4QH0.017317771724.8599600.001234时间00.39630.0223流量3078.763078.7699600.0099600.00低速冲头速度高速冲头速度0.2 6.47M/SQ1V1A1(CM/S)锤头直径MM圆周率3078.76153.9420140 3.14159 T1V2Q10.3962636612203078.76QH进料口面积V3进料口速度A2104580.0024.94200TH体积V4QH0.00192675201.5104580.001234时间00.39630.0069流量3078.763078.76104580.00#########低速冲头速度高速冲头速度0.21631.98M/S。
压铸工艺参数(二)
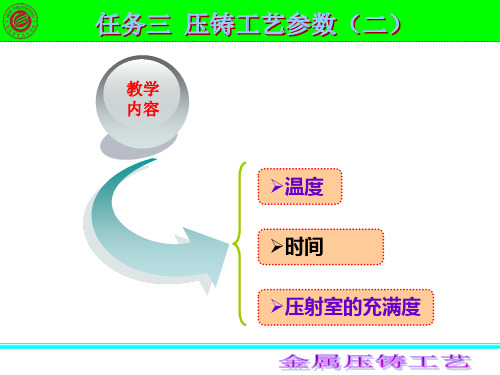
三、压射室的充满度
浇入压射室的金属液量占压射室总容量的程度称为压射室的充满度,通常 以百分数表示。
充满度对于卧式冷压室压铸机有着特殊 的意义。因为卧式压铸机的压射室在浇入金 属液后,并不是完全充满,而是在金属液面 上方留有一定的空间。 这个空间所占的体积越大,存有空气越 多,对于填充型腔时的气体量的影响越大。 其次,充满度小,合金液在压射室内的激冷 度过多,对填充也不利。因此,压射室充满 度不应过小,以免上部空间过大,一般充满 度应在40%~80%范围内,而以75%左右最 为适宜。
1 2 mv n mcT s 2 2 vn Ts 2c
式中 m——运动中的合金质量,kg; vn——内浇口速度,m/s; c ——合金的比热容,J/kg· ℃; Ts——因摩擦加热后升高的温度,℃。
上述公式计算得出内浇口速度与温升的关系见图3-17。
图3-17 内浇口速度与合金温升的关系
当内浇口速度为80m/s时,镁合金液进入型腔时的温度将增加25℃。 而内浇口速度越大,则温度增加得越多,这对准确地控制浇注温度有一 定的意义。
④避免模具因激热而胀裂;
⑤缩小模具工作时冷热交变的温度差,延长模具寿命。
(1) 影响模具温度的主要因素 1) 合金浇注温度、浇注量、热容量和导热性。 2) 浇注系统和溢流槽的设计,用以调整平衡状态。 3) 压铸比压和压射速度。 4) 模具设计。模具体积大,则热容量大,模具温度波动较小。模具 材料导热性越好,则温度分布就越均匀,有利于改善热平衡。 5) 模具合理预热提高初温,有利于改善热平衡,可提高模具寿命。 6) 生产频率快,模具温度升高,这在一定范围内对铸件和模具寿命 都是有利的。 7) 模具润滑起到隔热和散热的作用。
如果压力升高时间过短,金属尚未完全凝固,增压压力早已建成并作 用于其上,则将增大胀型力,从而引起胀型力超过允许值,发生机器锁模 力不足的现象。 因此,机器压射系统的增压装置上,压力升高时间的可调性十分重要。 其调整范围在0.015~0.3s内比较适宜。
压铸工艺参数公式[整理版]
![压铸工艺参数公式[整理版]](https://img.taocdn.com/s3/m/5f767a000a4e767f5acfa1c7aa00b52acfc79c03.png)
∙压铸工艺参数公式∙铸造计算公式1.铸造重量WC=W件+W溢+W排+W浇+W馀铸造容积4WC/ ρ——熔液密度2.填充率R= ———————— = ————————料筒容积πD2L筒长3.通过浇口重量Wf = W件+W溢4 Wf4.高速区间Sf = —————————(※溶汤比重一般而言为铝 2.64、ρπd料 2 镁 1.75g/cm2)Sf5.高速速度VH` = ————————tf——填充时间tf = 0.01X2铸件平均壁厚6.压铸机的射出力Fs(射出油缸的推进力)Fs=油压压力Ph ×射出油缸截面积Ah(KN)7.铸造压力Pp(传递到制品的压力)射出油缸截面积Ah 射出力FsPp=油压压力Ph × =柱塞截面积Ap 柱塞截面积Ap8.内浇口速度VgVg(V2)= 射出速度Vp(V1) ×柱塞截面积Ap(A1)(m/s)浇口截面积Ag(A2)9.充填时间tt= 制品体积= 制品重量/比重(sec)浇口流量浇口速度Vg×浇口截面积Ag10.浇口凝固时间t =B×α×(浇口厚度)2此时的B 为Al:2.0、Mg:1.5 α为Al:0.01、Mg:0.00511.开模力是指铸造时施加在制品上的压力而使模具打开的力量,开模力可以铸造面积×铸造压力计算出。
11.1.铸造面积的计算铸造面积A1=a1+a2+a3+a4=料饼面积+浇道面积+制品面积+溢流面积11.2.开模力的计算开模力F1=铸造压力Pp×铸造面积A1+中子分力Fc详细计算以各部分承受的压力分类。
制品部=计算铸造压力× 75%溢流部=计算铸造压力× 25%料饼,浇道部=计算铸造压力×100%11.3.如有滑块中子,则计算中子分力。
中子复位力Fr=制品面积Ac×计算铸造压力×75%中子分力Fc=中子复位力Fr×tanθ11.4.开模力F1=(a1+a2)×Pp+a3×Pp×0.75+a4×Pp×0.25+Fc压铸机关模力>开模力F1×1.112.充填完了力量冲突力量E =W(V)2/2gW : 射出油缸活塞杆+活塞杆重量kgV : 射出速度m/sg : 重力加速度9.8 m/sec2。
压铸件质量如何计算公式
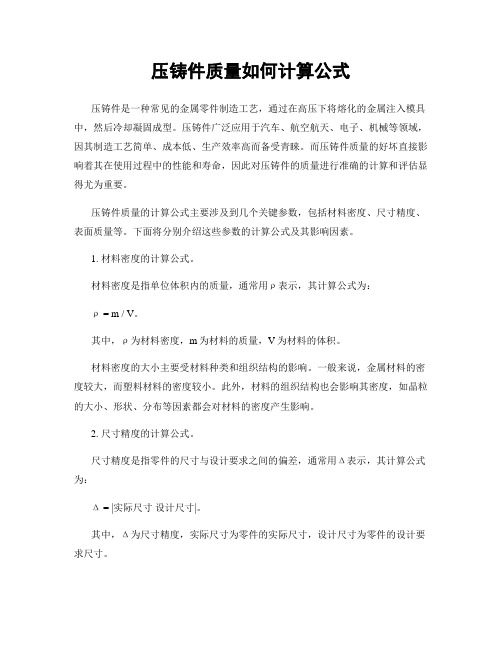
压铸件质量如何计算公式压铸件是一种常见的金属零件制造工艺,通过在高压下将熔化的金属注入模具中,然后冷却凝固成型。
压铸件广泛应用于汽车、航空航天、电子、机械等领域,因其制造工艺简单、成本低、生产效率高而备受青睐。
而压铸件质量的好坏直接影响着其在使用过程中的性能和寿命,因此对压铸件的质量进行准确的计算和评估显得尤为重要。
压铸件质量的计算公式主要涉及到几个关键参数,包括材料密度、尺寸精度、表面质量等。
下面将分别介绍这些参数的计算公式及其影响因素。
1. 材料密度的计算公式。
材料密度是指单位体积内的质量,通常用ρ表示,其计算公式为:ρ = m / V。
其中,ρ为材料密度,m为材料的质量,V为材料的体积。
材料密度的大小主要受材料种类和组织结构的影响。
一般来说,金属材料的密度较大,而塑料材料的密度较小。
此外,材料的组织结构也会影响其密度,如晶粒的大小、形状、分布等因素都会对材料的密度产生影响。
2. 尺寸精度的计算公式。
尺寸精度是指零件的尺寸与设计要求之间的偏差,通常用Δ表示,其计算公式为:Δ = |实际尺寸设计尺寸|。
其中,Δ为尺寸精度,实际尺寸为零件的实际尺寸,设计尺寸为零件的设计要求尺寸。
尺寸精度的大小主要受加工工艺和设备精度的影响。
在压铸过程中,模具的精度、注射压力、冷却速度等因素都会对零件的尺寸精度产生影响。
另外,材料的收缩率也是影响尺寸精度的重要因素,不同材料的收缩率不同,需要在设计时进行合理的补偿。
3. 表面质量的计算公式。
表面质量是指零件表面的光洁度和平整度,通常用Ra值表示,其计算公式为:Ra = 1/n Σ|yi|。
其中,Ra为表面质量,n为样本长度,yi为样本点的偏离值。
表面质量的大小主要受加工工艺和模具质量的影响。
在压铸过程中,模具的表面光洁度、冷却系统的设计、喷砂处理等因素都会对零件的表面质量产生影响。
此外,材料的流动性和凝固性也会影响表面质量,流动性差、凝固速度快的材料容易产生气孔、夹杂等缺陷,从而影响表面质量。
压铸工艺参数选择和计算
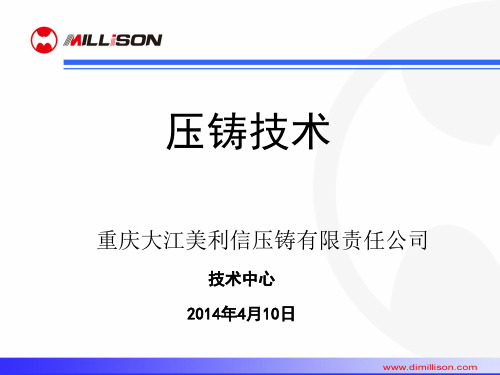
3. 内浇口速度推荐值
4. 充填时间推荐值
三.压室充满度计算 压室充满度
1.每次浇注金属液的总量占压室容积的百分数,称为压室充满度。 其计算公式如下: Φ=W/G100% Φ=压室充满度 % W=压室容量 Kg G=每次浇注金属液的总量Kg (包括浇注系统、集渣包在内的重量)
压室充满度应在30%以上,以30~50%为宜。 2.分流锥的主要作用。 .提高压室压室充满,减少水平压室中的气体。 .防止金属液自流。 .帮助直浇道带到动模。 .帮助自动取件手取件。
0.047 0.0376 0.036 0.0288换点计算
快压转换点验证
压铸工艺参数的调整方法
1.慢压射速度调至0.2~0.3m/s,通常认为0.2m/s以 下较为合适。 2.通常内浇口速度为40~60m/s,根据铸件的情况将 其换算为快压射速度。 3.根据计算和验证,确定快压射转换位置,考虑到 电磁阀的反映时间,应在计算的位置 上20~30mm。 4.设定增压启动位置,一般在冲头停止前30mm的 位置应使增压阀启动。 5.调整增压启动阀的开度,以模具不出现飞边,跑 水现象为准,并开至较大的位置。 6.合金液浇注量需稳定,一般以余料饼厚度来确定, 通常料饼厚度为20~30mm。
压室充满度的选择 压室充满度对填充时间和压射速度的影响
1.关于压室充满度,美国认为40~60%为最佳,日本认为理想的充满度是30~60%、东芝 是20~50%,中国《压铸模设计手册》中认为压室的充满度一般为70±10%,也有认为 40~75%。我观察是30~50%比较好。这样使用高速充填的行程比较短,在比较低的高速 压射速度下,就能满足填充时间的要求。大家知道:填充时间是压铸工艺设计中最基础也 是最重要的参数。 我认为考虑充满度时,不仅要考虑到压射比压,还要考虑到造压射冲头的实际压射速 度和充填时间 。 2.举例如下:某汽车产品,平均壁厚在2.5mm,局部壁厚1mm和12mm,充填资料970g,浇 注重量1638g,为了使产品有较好的帮忙质量,选用的充填时间为‹0.029S。 计算得知:用Φ70压室的充满度是71%,需要高速充填行程是9.4cm;用Φ80压室的充 满度是52.2%,需要高速充填行程是7.2cm;下表计算得出了不同的冲头直径和不同冲头高 速充填速度时的充填时间,从表中可以看出:充满度较低的Φ80压室比充满度较高的Φ70 压室,更容易用较低的压射速度来保证产品所需的充填时间。 压室充满度 Φ70=71% Φ80=52.2% 冲头速度m/s 充填时间 秒 充填时间 秒 2 2.5 3 0.0313 0.024 3.5 0.0269 0.0206 4 0.0235 0.018
压铸参数的计算(精)
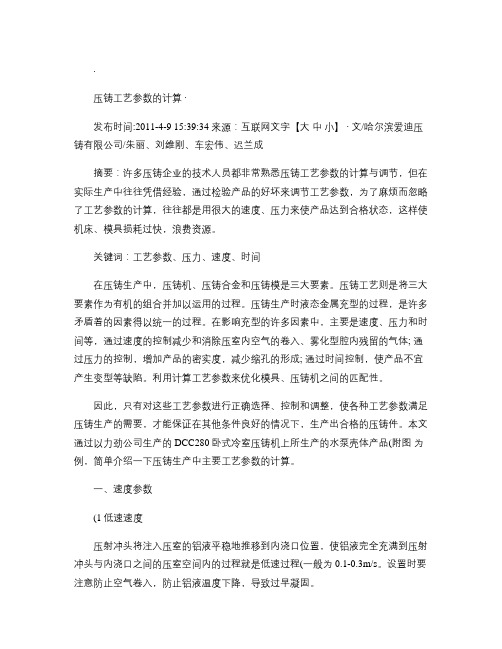
∙压铸工艺参数的计算∙发布时间:2011-4-9 15:39:34 来源:互联网文字【大中小】∙文/哈尔滨爱迪压铸有限公司/朱丽、刘维刚、车宏伟、迟兰成摘要:许多压铸企业的技术人员都非常熟悉压铸工艺参数的计算与调节,但在实际生产中往往凭借经验,通过检验产品的好坏来调节工艺参数,为了麻烦而忽略了工艺参数的计算,往往都是用很大的速度、压力来使产品达到合格状态,这样使机床、模具损耗过快,浪费资源。
关键词:工艺参数、压力、速度、时间在压铸生产中,压铸机、压铸合金和压铸模是三大要素。
压铸工艺则是将三大要素作为有机的组合并加以运用的过程。
压铸生产时液态金属充型的过程,是许多矛盾着的因素得以统一的过程。
在影响充型的许多因素中,主要是速度、压力和时间等,通过速度的控制减少和消除压室内空气的卷入、雾化型腔内残留的气体; 通过压力的控制,增加产品的密实度,减少缩孔的形成; 通过时间控制,使产品不宜产生变型等缺陷。
利用计算工艺参数来优化模具、压铸机之间的匹配性。
因此,只有对这些工艺参数进行正确选择、控制和调整,使各种工艺参数满足压铸生产的需要,才能保证在其他条件良好的情况下,生产出合格的压铸件。
本文通过以力劲公司生产的DCC280卧式冷室压铸机上所生产的水泵壳体产品(附图为例,简单介绍一下压铸生产中主要工艺参数的计算。
一、速度参数(1低速速度压射冲头将注入压室的铝液平稳地推移到内浇口位置,使铝液完全充满到压射冲头与内浇口之间的压室空间内的过程就是低速过程(一般为0.1-0.3m/s。
设置时要注意防止空气卷入,防止铝液温度下降,导致过早凝固。
压室充满度=注入重量/压室截面积×空打行程×溶液密度X100%(压室充满度的标准一般为20-50%低速速度=0.7X√压室直径/压室充满度例题:压室直径:Φ50mm,注入重量:830g ,空打行程:368mm ,压室截面积:(π/4×52=19.63cm²,溶液密度:2.6 g/cm³压室充满度=(830/196.63×36.8×2.6X100%=44.18%低速速度=(0.7X√50/44.18=0.122M/S(2高速速度压射冲头将铝液完全充满到压室内(一般为1.5-2.5m/s。
压铸工艺参数及计算公式.xls
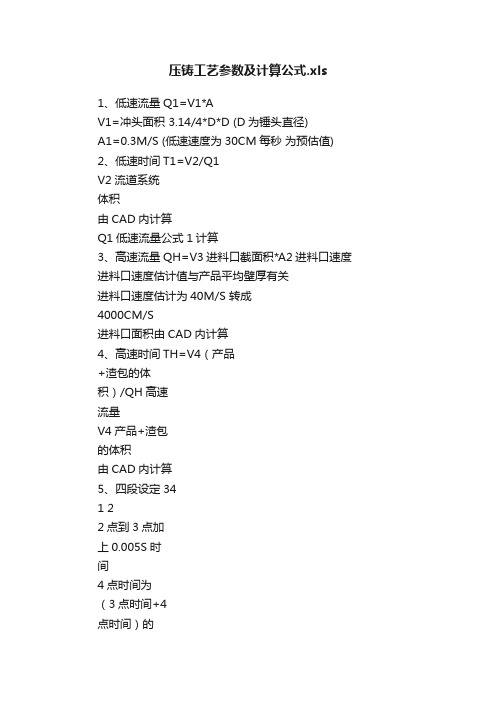
压铸工艺参数及计算公式.xls1、低速流量Q1=V1*AV1=冲头面积 3.14/4*D*D (D为锤头直径)A1=0.3M/S (低速速度为30CM每秒为预估值) 2、低速时间T1=V2/Q1V2流道系统体积由CAD内计算Q1低速流量公式1计算3、高速流量QH=V3进料口截面积*A2进料口速度进料口速度估计值与产品平均壁厚有关进料口速度估计为40M/S 转成4000CM/S进料口面积由CAD内计算4、高速时间TH=V4(产品+渣包的体积)/QH高速流量V4产品+渣包的体积由CAD内计算5、四段设定341 22点到3点加上0.005S时间4点时间为(3点时间+4点时间)的2-3倍计算公式 (单位:Q1低速流量T1低速时间V1锤头面积V2流道系统体积A1低速速度QH高速流量A2进料口速度V4产品+渣包的体积V3进料口截面积A3高速锤头速度TH高速时间单位:cm)Q1V1A1(CM/S)锤头直径MM圆周率0.000.00 3.14159T1V2Q1#DIV/0!0.00QH进料口面积V3进料口速度A20.00TH体积V4QH#DIV/0!0.001234时间0#DIV/0!#DIV/0!流量0.000.000.000.00低速冲头速度高速冲头速度0#DIV/0!M/SQ1V1A1(CM/S)锤头直径MM圆周率0.000.00 3.14159 T1V2Q1#DIV/0!0.00QH进料口面积V3进料口速度A20.00TH体积V4QH#DIV/0!201.50.001234时间0#DIV/0!#DIV/0!流量0.000.000.000.00 低速冲头速度高速冲头速度0#DIV/0!M/S。
压铸参数计算范文

压铸参数计算范文压铸是一种常用的金属加工工艺,通过将熔融的金属注入模具中,并在模具中进行冷却固化,最终得到所需形状的金属制品。
在进行压铸过程中,需要对一些参数进行合理的计算和选择,以确保产品的质量和生产的效率。
本文将重点介绍压铸的参数计算方法。
1.压铸机的锁模力计算压铸机的锁模力是指在压铸过程中用于保持模具封闭的力量。
锁模力的大小直接影响着产品的尺寸精度和外观质量。
锁模力的计算公式如下:F=K*A其中,F为锁模力,K为系数,A为模具的投影面积。
系数K一般可以根据实际情况取值。
当模具结构复杂,浇注系统复杂时,一般取K=350-500。
当模具结构简单,浇注系统简单时,可以取K=100-150。
模具的投影面积A计算方法依据浇注系统的数量和间距而定。
如果浇注系统数量较多或间距较小,模具投影面积会增大,锁模力也会增大。
2.注射压力的计算注射压力是指金属熔融物质在进入模腔时所受到的压力。
注射压力的大小直接影响到金属的充型能力和充型速度。
注射压力的计算公式如下:P=F/A其中,P为注射压力,F为锁模力,A为模具的注射面积。
注射面积的计算方法根据模具的冷却系统不同而有所区别。
一般来说,注射面积等于模具投影面积减去冷却系统的面积。
3.充型重量的计算充型重量是指每次注射过程中进入模腔的金属量。
充型重量的计算公式如下:W=V*D其中,W为充型重量,V为模腔容积,D为金属的密度。
模腔容积的计算方法根据模具的形状不同而有所区别。
在模具设计时,一般应根据产品的设计要求计算出模腔的容积。
金属的密度根据不同的金属材料而有所差异。
在进行压铸前,需要明确所使用金属材料的密度。
4.注射速度的选择注射速度是指金属进入模腔的速度,它直接影响到产品的成型质量和生产效率。
注射速度的选择应综合考虑产品的尺寸、形状复杂程度、金属的充型能力等因素。
一般来说,注射速度应根据产品的具体要求进行选择。
对于较大尺寸、形状复杂的产品,注射速度应适当减缓,以防止金属充填不均匀而导致的缺陷。
压铸工艺参数理论计算

压铸工艺参数理论计算在压铸行业,工艺参数对产品质量的影响更多的是靠试验的方法,许多工程技术人员不能深入的进行分析,生产铸件的条件无法用数据来描述。
本文就压铸工艺参数理论计算和实践两方面进行讨论研究。
压力铸造的主要工艺参数有行程(速度转换点)、速度、时间和压力等。
而本文重点分析速度和行程两个主要参数。
1. 压铸的四阶段压射计算压力铸造工艺参数,首先要定义压铸的四个压射阶段。
1.1.1 第一阶段:慢压射1为防止金属液溅出,冲头越过浇料口的过程,压射的第一阶段通常是缓慢的。
1.1.2 第二阶段:慢压射2金属液以较低的速度运动至内浇口的阶段,主要目的是排出压室内的空气,集中铝液于压室内。
1.1.3 第三阶段:快压射金属液由内浇口填充型腔直至充满为止,主要目的是成型并排出型腔中气体。
1.1.4 第四阶段:增压阶段型腔充满后建立最后的增压,使铸件在高压压力下凝固,从而使铸件致密。
1.2 计算模型1.2.1 根据1.1定义(参照图1),可以得到金属液在各阶段合金液的重量关系式。
G2=G浇G3+G4=G铸+G溢流其中:G3+G4为金属液刚达到内浇口处时冲头端面至冲头停止之间的铝液重量,即为快压射起始点位置至冲头停止行程内金属液的容量。
G铸为铸件重量G溢为溢流系统的重量G2为慢压射2行程内压室能容纳的金属液重量G浇为浇注系统的重量1.2.2 流道中单位时间内不同位置截面中通过合金液的流量关系式(见图2)金属液在流动过程中,单位时间内通过截面的流量Q相等,则Q=V1×S1=V2×S2= V3×S3 (注:V3 × S3是利用等式,而非金属液流量)其中V1:冲头速度S1:冲头面积V2:内浇口速度S2:内浇口面积V3:排气槽气体速度(推荐值75m/s)S3:排气槽的面积1.2.3 压铸时间[1]压铸时间包括充填时间,持压时间及铸件在压铸模型中停留的时间。
1.2.3.1 充填时间:金属液开始进入内浇口到型腔充满所需的时间。
压铸成型工艺参数的选择

结构复杂 120~150 150~200 150~180 180~200 170~190 200~240 150~180 180~220 200~230 300~350
4、压铸时间的选择
压铸时间包含充填、持压及压铸件在压铸 模中停留的时间。它是压力、速度、温度 这三个因素,再加上液态金属的物理特性 、铸件结构(特别是壁厚)、模具结构( 特别是浇注系统和排溢系统)等各方面的 综合结果。
第I阶段:压射冲头推动金属液越过浇料口,低压低速运 行,防止金属液从浇料口溢出,有利于气体排出。压力 p1主要用于克服冲头与压室、液压缸与活塞之间的摩擦 阻力,只有小部分用于推动金属液。
第II阶段:压射冲头通过浇料口,压力上升,速度加快, 金属液充满压室至内浇口处。
第III阶段:金属液流经内浇口充填型腔。由于内浇口处截面 面积大幅缩小,流动阻力剧增,要保持足够的填充速度,需更 高的压射压力。压射速度快慢非常重要,主要取决于压铸件复 杂程度、壁厚和质量要求等。
转向器真空压铸模在不同填充时间下的表现
(2)压铸模温度 压铸模温度是指压铸模的工作温度。压铸 模在使用前要进行充分预热,并保持在一 定的温度范围内。
模温机
压铸模预热的作用:
➢避免金属液激冷急剧,而很快失去流动性,使 铸件不能成型,或即使成型,但因激冷而增大线 收缩,引起裂纹和开裂。 ➢避免铸型因激热而胀裂,延长压铸模的工作寿 命。 ➢降低型腔中的气体密度,有利于型腔中气体的 排除,从而获得表面光洁、轮廓清晰及组织致密 的铸件。
压铸成型工艺参数的选择 单击此处编辑母版标题样式
单击此处编辑母版副标题样式
压铸成型工艺参数的选择
【能力目标】
1.根据具体压铸产品、压铸模具合理的选择压铸工艺参数 。
压铸工艺自动计算表
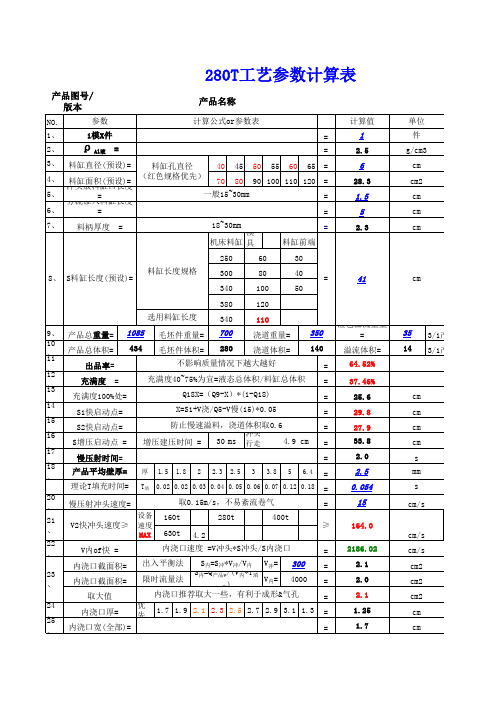
1、
Al合金件
比压范围
一般件 30~50
受力件 45~80
外观或薄壁件 40~60
耐压件 80~120
备注 手工输入
常数
内浇口速度预设30 ~50前提下:
机器高速快,料缸 直径可以选小些, 可以保证充满度和
出品率;
3/1产品重量= 231 3/1产品体积= 92.4
小产品偏下限 >9cm??
33.78
280T工艺参数计算表
产品图号/ 版本
产品名称
NO.
参数
计算公式or参数表
1、
1模X件
=
2、
ρAl液 =
=
3、 料缸直径(预设)=
料缸孔直径
40 45 50 55 60 65 =
4、 冲料头缸放面料积缸(预口设长)度= (红色规格优先) 70 80 90 100 110 120 =
5、 分流锥入=料缸长度
一般15~30mm
=
6、
=
=
7、 料柄厚度 =
18~30mm 模
机床料缸 具
= 料缸前端
计算值 1 2.5 6
28.3 1.5
5 2.3
250
60
30
料缸长度规格 8、 S料缸长度(预设)=
300
80
40
=
41
340
100
50
380
120
选用料缸长度
340
110
渣包溢流重量
9、 产品总重量= 1085 毛坯件重量= 700
cm cm
26 、
27
选用压铸机= V内MAX =
F锁=KSp 160 t
S投 影 0
- 1、下载文档前请自行甄别文档内容的完整性,平台不提供额外的编辑、内容补充、找答案等附加服务。
- 2、"仅部分预览"的文档,不可在线预览部分如存在完整性等问题,可反馈申请退款(可完整预览的文档不适用该条件!)。
- 3、如文档侵犯您的权益,请联系客服反馈,我们会尽快为您处理(人工客服工作时间:9:00-18:30)。
序号
内容
一 锁模力计算和压铸机的选择
二 内浇口速度计算
三 压室充满度计算Fra bibliotek四 快压转换点计算和验证
五 浇注系统重点
六
七
合计时间
目录
时间
页数 1~5 6~8 9~10 11~15 16~21
40页
一.锁模力计算和压铸机的选择
1.胀型力 压铸过程中,充填型腔的金属液将压射活塞的比压传递至模具型腔壁面的力,称为胀
二.内浇口速度计算
1.内浇口速度 金属液通过内浇口导入型腔时的线速度称为金属液的内浇口速度(也称填充速度)。 其计算公式如下: ω=V/f*Τ 式中 ω —内浇口速度 V—包括集渣包在内的压铸件体积 T —填充时间(见推荐值) f —内浇口截面积( mm²)
2.冲头速度与内浇口速度的关系 计算公式如下: ω =A*Vc/Fn
快压转换点验证
验证项目4:速度切换位置不当 a
开始切 换高速
高速切 换点LS
Gas
A 浇口
▪高速切换位置
Gas AL液
提前时
高速切 换点LS
B
高低 速速
▪高速切换位置
Gas
延迟时
a
AL液
高速切 换点LS
Gas
▪铝液刚入产品
范围时切换高速
AL液
高速切
A
换点LS
▪充填率<100%时,气体范围大(A+B) 气体残留在产品内的可能性大
(该零件属强度要求高的结构件,需要较大的压射比压以保证组织致密,提高强度。同压射速度可选择低一点,以免产生气孔 。)
(1)锁模力: 1000×1151.8=1151800N (2)根据以上计算,压铸机的锁模力理论上应该大于1152吨. (3)由于该产品壁厚不均匀,零件结构复杂,根据经验,我们选择DM1250吨压铸设备生产该产品。
我认为考虑充满度时,不仅要考虑到压射比压,还要考虑到造压射冲头的实际压射速 度和充填时间 。 2.举例如下:某汽车产品,平均壁厚在2.5mm,局部壁厚1mm和12mm,充填资料970g,浇 注重量1638g,为了使产品有较好的帮忙质量,选用的充填时间为‹0.029S。
计算得知:用Φ70压室的充满度是71%,需要高速充填行程是9.4cm;用Φ80压室的充 满度是52.2%,需要高速充填行程是7.2cm;下表计算得出了不同的冲头直径和不同冲头高 速充填速度时的充填时间,从表中可以看出:充满度较低的Φ80压室比充满度较高的Φ70 压室,更容易用较低的压射速度来保证产品所需的充填时间。
▪充填率>100%时,气体范围小(a) 未加速前铝液过度进入产品部份使冷却过度/出现缩松
▪100%≤充填率≤105%时 保证品质前提下气体范围最小(A)
●通过计算公式分别设置: 铝液大约刚进入产品范围时、速度切换提前和延迟三组位置进行验证。
五.浇注系统重点
浇注设计原则:使金属能有效地、平稳地流动充填型腔,避免气体混入。
1.慢压射速度调至0.2~0.3m/s,通常认为0.2m/s以 下较为合适。 2.通常内浇口速度为40~60m/s,根据铸件的情况将 其换算为快压射速度。 3.根据计算和验证,确定快压射转换位置,考虑到 电磁阀的反映时间,应在计算的位置 上20~30mm。 4.设定增压启动位置,一般在冲头停止前30mm的 位置应使增压阀启动。 5.调整增压启动阀的开度,以模具不出现飞边,跑 水现象为准,并开至较大的位置。 6.合金液浇注量需稳定,一般以余料饼厚度来确定, 通常料饼厚度为20~30mm。
压室充满度 Φ70=71% Φ80=52.2%
冲头速度m/s 充填时间 秒 充填时间 秒
2 0.047 0.036
2.5 0.0376 0.0288
3 0.0313 0.024
3.5 0.0269 0.0206
4 0.0235 0.018
四.快压转换点计算和验证
快压转换点计算
快压转换点验证
压铸工艺参数的调整方法
4.滑块面胀型力案例(264/1#模)
Fc=Fr x tgθ 式中 Fr—滑块面胀型力(N)
θ—契紧面斜度(度)
滑块胀型力计算
压铸机的选择案例
•压铸机选择: (1)零件的投影面积约为:886cm2 采用一模一件。 (2)加上浇注系统后总的面积(按浇注投影面积为零件投影面积的30%计算)约为:886×1.3=1151.8cm2 (3)压射比压: 1000Kg/ cm2
压室充满度应在30%以上,以30~50%为宜。 2.分流锥的主要作用。
.提高压室压室充满,减少水平压室中的气体。 .防止金属液自流。 .帮助直浇道带到动模。 .帮助自动取件手取件。
压室充满度的选择
压室充满度对填充时间和压射速度的影响
1.关于压室充满度,美国认为40~60%为最佳,日本认为理想的充满度是30~60%、东芝 是20~50%,中国《压铸模设计手册》中认为压室的充满度一般为70±10%,也有认为 40~75%。我观察是30~50%比较好。这样使用高速充填的行程比较短,在比较低的高速 压射速度下,就能满足填充时间的要求。大家知道:填充时间是压铸工艺设计中最基础也 是最重要的参数。
型力。 其计算公式如下:
Pz=Pzb*A 式中 Pz—胀型力(N)
Pzb —增压比压(Pa) A —承受胀型力的投影面积(指铸件、浇注系统和集渣包的投影面积)(mm²) 2.锁模力 计算公式如下:
Pzf=Pzf1+Pzf2 式中 Pzf—分型面胀型力(N)
Pzf1—金属投影面积在分型面上的胀型力(N) Pzf2—侧向(滑块)胀型力分解到沿锁模方向上的分力(N) 其中 Pzf2 =Phk*tgα Phk —侧壁成形滑块上的总压力(N) α —抽芯结构中契紧块与分型面的夹角 3.压铸机的选择 Pz≥K*Pzf 式中 Pz —压铸机的锁模力 ; K —安全系数,一般取K=1.2~1.3。
式中 ω—内浇口速度(填充速度)(m/s) Vc—冲头速度(压射速度)(m/s) Fn —内浇口截面积(mm²) A — 压室截面积(mm²)
3. 内浇口速度推荐值
4. 充填时间推荐值
三.压室充满度计算
压室充满度
1.每次浇注金属液的总量占压室容积的百分数,称为压室充满度。 其计算公式如下: Φ=W/G100% Φ=压室充满度 % W=压室容量 Kg G=每次浇注金属液的总量Kg (包括浇注系统、集渣包在内的重量)