制程改善与案例分析资料
「cpk」过程能力指数附案例分析报告和改善要求措施
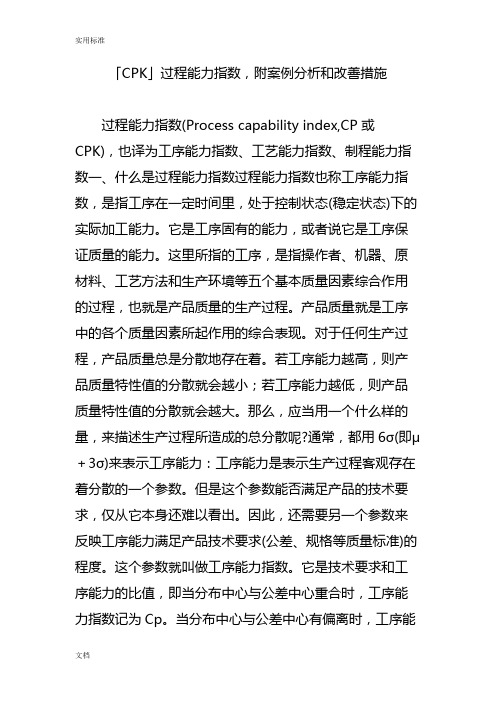
「CPK」过程能力指数,附案例分析和改善措施过程能力指数(Process capability index,CP或CPK),也译为工序能力指数、工艺能力指数、制程能力指数一、什么是过程能力指数过程能力指数也称工序能力指数,是指工序在一定时间里,处于控制状态(稳定状态)下的实际加工能力。
它是工序固有的能力,或者说它是工序保证质量的能力。
这里所指的工序,是指操作者、机器、原材料、工艺方法和生产环境等五个基本质量因素综合作用的过程,也就是产品质量的生产过程。
产品质量就是工序中的各个质量因素所起作用的综合表现。
对于任何生产过程,产品质量总是分散地存在着。
若工序能力越高,则产品质量特性值的分散就会越小;若工序能力越低,则产品质量特性值的分散就会越大。
那么,应当用一个什么样的量,来描述生产过程所造成的总分散呢?通常,都用6σ(即μ+3σ)来表示工序能力:工序能力是表示生产过程客观存在着分散的一个参数。
但是这个参数能否满足产品的技术要求,仅从它本身还难以看出。
因此,还需要另一个参数来反映工序能力满足产品技术要求(公差、规格等质量标准)的程度。
这个参数就叫做工序能力指数。
它是技术要求和工序能力的比值,即当分布中心与公差中心重合时,工序能力指数记为Cp。
当分布中心与公差中心有偏离时,工序能力指数记为Cpk。
运用工序能力指数,可以帮助我们掌握生产过程的质量水平。
二、过程能力指数的意义制程能力是过程性能的允许最大变化范围与过程的正常偏差的比值。
制程能力研究在於确认这些特性符合规格的程度,以保证制程成品不符规格的不良率在要求的水准之上,作为制程持续改善的依据。
当我们的产品通过了GageR&R的测试之后,我们即可开始Cpk值的测试。
CPK值越大表示品质越佳。
CPK=min((X-LSL/3s),(USL-X/3s))三、过程能力指数的计算公式CPK= Min[ (USL- Mu)/3s, (Mu - LSL)/3s]四、过程能力指数运算方法过程能力指数运算有5种计算方法:直方图(两种绘图方法);散布图(直线回归和曲线回归)(5种);计算剩余标准差;排列图(自动检索和排序);波动图(单边控制规范,也可以是双边控制规范)。
质量控制要点及案例分析

纠正措施
案例四:
06070037-1 红芙蓉小盒 问题
原因分析 临时措施 烫金工序第5联烫金版走位 ,5万个小盒超出质量 标准允许范围 版走位未及时发现 特许放行 1、机台自检要注意隐蔽的质量问题; 2、IPQC一定要按项目清单上的要求抽检,特别 是较为隐蔽的质量问题。
纠正措施
SQE制订 纠正措施
IQC检验?
Y
原材料入仓
续二
印刷机台 批量生产
技术部/QE 现场改善
N
IPQC确认?
IPQC主任 通知停机
IPQC巡检?
N
印刷机台 生产调试
Y
N
IPQA检验? Y 标识正品板 续三 彩盒部质量 控制流程 标识次品板
彩盒部质量 控制流程
IPQA抽检大张 填写检验报告
确定主要 缺陷项目
4.3 掌握不同产品的工艺要求
目前,我司有胶印,丝印,移印以及成熟的印后加工工 艺,各工序加工精度不同,导致在质量控制标准方面存在一 定的差异。 例如: 1.有些印品在连机过油与分机过油后表面光亮度存在一 定的差异; 2. 套烫与无套烫产品误差标准的差异。
4.4 不同客户的品质要求
注:标
为客户特别关注的项目
4.1 了解公司质量标准
质量标准是质量工程处根据客户的要求以及公司的 工艺所能达到的水平而专门制定的一套标准,并分类编制 了通用操作指引、各岗位分产品检验项目清单、产品限 度样板册等,它是 IPQC、IPQA、 QC及OQA检查作业 时的唯一标准。
在批量生产之前,品控人员及机台人员必须首先熟 悉公司的质量标准,做到有章可循,以便生产出品质优 良的印品。
次品板
模切工序加工
大张检测 机检验? 正品板
最新smt制程不良原因及改善措施分析ppt课件
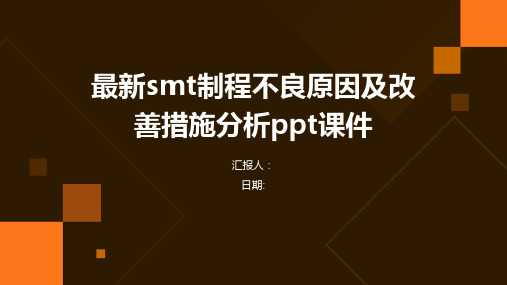
汇报人: 日期:
目录
• SMT制程概述 • SMT制程不良原因分析 • SMT制程改善措施分析 • 案例分析与实施效果评估
01
SMT制程概述
SMT制程简介
表面组装技术
SMT是表面组装技术(Surface Mounted Technology)的缩写,是一种将电 子元件直接安装在印刷电路板(PCB)表面的技术。
降低成本
SMT技术提高了生产效率 ,降低了生产成本,使得 电子产品更加普及和个性 化。
SMT制程常见问题
锡膏印刷问题:锡膏印刷是SMT制程中的关键步 骤之一,常见问题包括锡膏量不足、偏移、桥接 等,影响焊接质量。
焊接问题:焊接过程中可能出现虚焊、冷焊、焊 接不良等问题,主要原因包括温度设置不当、焊 接时间不足、PCB污染等。
元件贴装问题:元件贴装过程中可能出现元件偏 移、翻转、损坏等问题,主要原因包括设备参数 设置不当、元件供料器故障等。
针对以上问题,我们将详细介绍不良原因分析及 改善措施,以提高SMT制程的良率和生产效率。
01
SMT制程不良原因分析
设备故障导致的不良
设备老化
长时间运行的设备可能出 现磨损和老化,导致定位 不准、传输错误等不良现 象。
维护不足
设备缺乏定期维护和保养 ,可能导致精度下降、故 障率增加。
操作不当
操作人员对设备不熟悉或 操作不规范,可能引发误 操作,造成产品不良。
材料问题导致的不良
原材料缺陷
原材料本身存在缺陷,如PCB 板翘曲、元器件引脚氧化等,
影响制程质量。
储存条件不当
材料储存环境湿度过高、温度过高 或过低可能导致材料性能发生变化 。
smt制程不良原因及改善措施

03 员工技能水平参差不齐,操作不规范,导致不良 品率上升。
展望未来发展趋势并提出应对策略建议
未来SMT制程将朝着高 精度、高效率、高自动
化方向发展。
01
加强原材料质量管控, 确保产品品质稳定。
03
建立完善的品质管理体 系,加强品质监控和数 据分析,及时发现并解
决问题。
05
建议企业加大设备投入 ,引进先进技术和设备
,提高制程效率。
02
定期对员工进行技能培 训和操作规范教育,提
高员工技能水平。
04
THANKS
谢谢您的观看
案例背景介绍
01
某SMT生产线在生产过程中出现 多种制程不良,如焊点不良、元 件偏移等,导致产品良品率下降 。
02
生产线面临生产压力大、交期紧 张等挑战,急需解决制程不良问 题。
原因分析及定位关键问题
对生产线上的各个环节进行详细分析 ,找出可能造成制程不良的原因,如 设备老化、操作不规范、物料问题等 。
建立原材料库存管理制度
对原材料进行分类管理,建立合理的库存管理制度,避免原材料积 压和浪费。
加强设备维护与保养
制定设备维护计划
01
根据设备的使用情况和生产需求,制定合理的设备维护计划,
包括定期检查、保养、维修等。
提高设备维护水平
02
加强设备维护人员的培训和管理,提高设备维护水平,确保设
备的正常运行。
smt制程不良原因及改善措施
汇报人: 2023-12-19
目录
• SMT制程简介 • SMT制程不良原因分析 • SMT制程改善措施探讨 • 案例分享:成功改善SMT制
程不良的实践经验 • 总结与展望:未来SMT制程
精益改善案例

精益改善案例某公司生产线的产品存在质量问题,经过分析发现,主要原因是制程中存在一些不合理的环节和操作不规范的问题。
于是公司决定进行精益改善,以下是改善过程的案例。
首先,公司进行现场调查,了解每个环节的具体操作流程和问题所在。
通过观察和采访,发现生产线上存在很多浪费的环节,比如物料的搬运和存储浪费、操作流程不规范导致的错工错料等。
调查结果表明,这些问题严重影响了产品质量的稳定性和生产效率。
在调查的基础上,公司开始制定改善计划。
首先,对物料的存储和搬运进行优化。
通过调整仓库布局和材料的摆放顺序,缩短了从仓库到生产线的距离,减少了搬运时间和能量消耗。
同时,引入物料盘点管理系统,有效避免了物料的过期和损耗问题。
其次,对操作流程进行规范化。
通过标准化操作流程,减少人为因素对产品质量的影响。
采用可视化管理的方法,对员工进行培训和指导,确保操作规范的贯彻执行。
此外,通过控制生产环境的温湿度等因素,减少外界因素对产品质量的干扰。
再次,公司提供培训和技术支持,改善员工的技能水平和生产能力。
通过定期培训和知识分享会,提高员工的操作技能和质量意识。
此外,鼓励员工提供改善建议,并给予奖励以鼓励员工参与到精益改善中来。
最后,公司建立了一个持续改进的机制。
成立了质量改进小组,定期召开改进汇报会,评估改善效果并提出新的改进方案。
公司将改善思想和方法融入到企业文化中,鼓励每个员工积极参与到改善工作中。
经过以上的改进措施,公司生产线的产品质量得到了明显提升。
产品的不良率从10%下降到3%,生产效率也提高了20%。
公司的品牌形象得到了改善,客户满意度和市场份额也逐渐提升。
在这个案例中,公司通过精益改善的方法解决了生产线上存在的质量问题。
通过调查分析、制定改善计划、培训员工和建立持续改进机制,公司取得了显著的改进效果。
这个案例证明了精益思想和方法对企业的生产和管理是有积极作用的。
生产现场改善案例分析
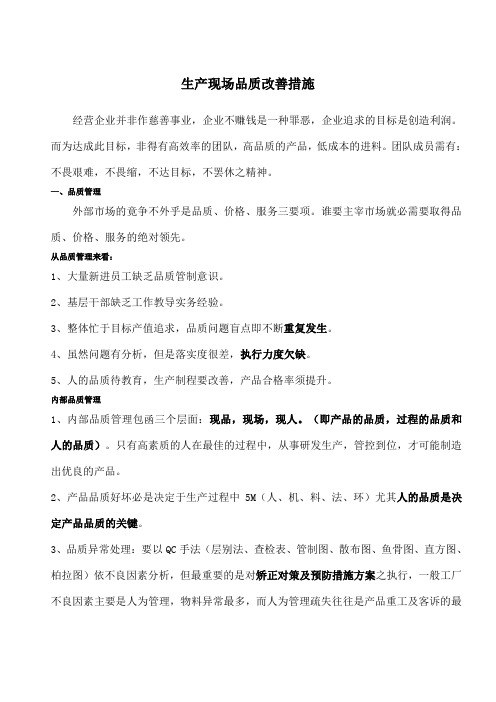
生产现场品质改善措施经营企业并非作慈善事业,企业不赚钱是一种罪恶,企业追求的目标是创造利润。
而为达成此目标,非得有高效率的团队,高品质的产品,低成本的进料。
团队成员需有:不畏艰难,不畏缩,不达目标,不罢休之精神。
—、品质管理外部市场的竟争不外乎是品质、价格、服务三要项。
谁要主宰市场就必需要取得品质、价格、服务的绝对领先。
从品质管理来看:1、大量新进员工缺乏品质管制意识。
2、基层干部缺乏工作教导实务经验。
3、整体忙于目标产值追求,品质问题盲点即不断重复发生。
4、虽然问题有分析,但是落实度很差,执行力度欠缺。
5、人的品质待教育,生产制程要改善,产品合格率须提升。
内部品质管理1、内部品质管理包函三个层面:现品,现场,现人。
(即产品的品质,过程的品质和人的品质)。
只有高素质的人在最佳的过程中,从事研发生产,管控到位,才可能制造出优良的产品。
2、产品品质好坏必是决定于生产过程中5M(人、机、料、法、环)尤其人的品质是决定产品品质的关键。
3、品质异常处理:要以QC手法(层别法、查检表、管制图、散布图、鱼骨图、直方图、柏拉图)依不良因素分析,但最重要的是对矫正对策及预防措施方案之执行,一般工厂不良因素主要是人为管理,物料异常最多,而人为管理疏失往往是产品重工及客诉的最大要因。
4.、对策:以教育训练提升人的品质,并落实改善品质措施。
A:短期(立即执行)用QC手法对问题进行探讨,认真实施对策,依循PDCA时时从不同角度考量如何改善。
B:中期(有效训练措施)实施班QCC活动(每周两小时)针对每个岗位一周以来报表反应出来的品质状况(当然最起码报表必须是真实的)让作业员对品质管理提出看法与问题,使其有参与感,进而加重其责任心,品管圈活动中可运用QC手法,品质改善提案,QCC竟赛等各类管理训练措施。
C:长期(积极教育训练)1、不定期或按计划全面实施职前,在职,重点,机会品质教育。
2、公司举办年度品管圈竟赛,品质征文,征图,品质标语,并品质演讲等意识教育,用来凝聚形成公司全体品质意识,从而提升全员无形中的品质观念。
锂电池制程异常案例分析
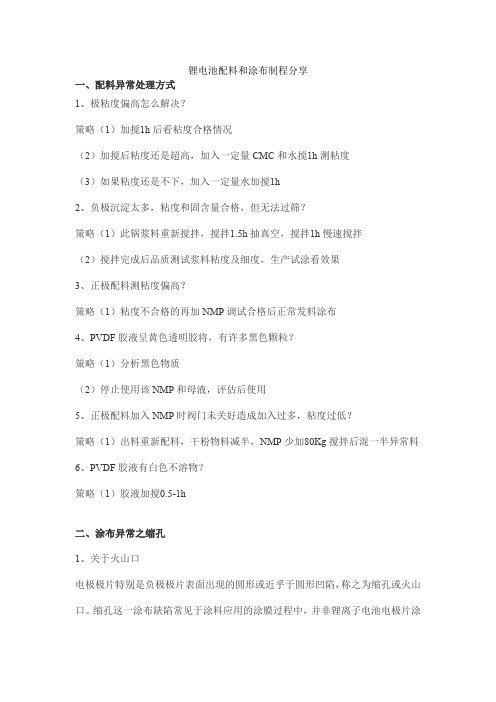
锂电池配料和涂布制程分享一、配料异常处理方式1、极粘度偏高怎么解决?策略(1)加搅1h后看粘度合格情况(2)加搅后粘度还是超高,加入一定量CMC和水搅1h测粘度(3)如果粘度还是不下,加入一定量水加搅1h2、负极沉淀太多,粘度和固含量合格,但无法过筛?策略(1)此锅浆料重新搅拌,搅拌1.5h抽真空,搅拌1h慢速搅拌(2)搅拌完成后品质测试浆料粘度及细度,生产试涂看效果3、正极配料测粘度偏高?策略(1)粘度不合格的再加NMP调试合格后正常发料涂布4、PVDF胶液呈黄色透明胶将,有许多黑色颗粒?策略(1)分析黑色物质(2)停止使用该NMP和母液,评估后使用5、正极配料加入NMP时阀门未关好造成加入过多,粘度过低?策略(1)出料重新配料,干粉物料减半,NMP少加80Kg搅拌后混一半异常料6、PVDF胶液有白色不溶物?策略(1)胶液加搅0.5-1h二、涂布异常之缩孔1、关于火山口电极极片特别是负极极片表面出现的圆形或近乎于圆形凹陷,称之为缩孔或火山口。
缩孔这一涂布缺陷常见于涂料应用的涂膜过程中,并非锂离子电池电极片涂布时特有的现象。
如下图2、缩孔的形成在涂布过程中可能会产生各种各样的缺陷,气泡、肥边、火山口、多边形凹陷、橘皮状等,缩孔是最常见的问题之一。
从根本上意义讲由于成膜时所产生的表面张力梯度造成的,这种现象称之为Maragoni效应。
材料间表面张力不匹配,是产生缩孔的主要诱因。
粘度、流动性以及干燥风速和烘箱温度等都可能改变表面张力及其作用过程,从而诱发缩孔的产生。
固化前可流动膜面中存在低表面张力的微粒(如粉体,油滴等),造成中央表面张力较低,流体以污染物为中心向四周迁移,最终形成边缘高于中心的圆形下陷(缩孔)。
3、缩孔的预防选用相容性好的分散剂或分散介质,减少涂料本体中低表面张力大颗粒(包括大液滴)的存在;添加疏水表面活性分散剂和溶剂等也可以控制缩孔的程度。
4、涂布缩孔解决方案1)材料表面结构的进一步改性通过对石墨材料表面进一步的改性,提高极性基团,提高其亲水性;2)调整粘合剂有效成分的分子结构通过调整粘合剂有效成分的分子结构,降低其极性基团的含量,有效降低LA型水性粘合剂产品的表面张力,提高其对石墨材料的润湿程度。
SMT制程改善方案8

改善对象
0402类物料少 件、移位
不良数量
9493
不良比率
预计检测率 提高
1.38% 1%
AOI光学 检测设备
Aux communications equipment limited co
PCBA各生产工序代码标示说明
• 目前SMT对各检验工序以及生产工序做代码标记来跟踪各工序作业情况。 便于 对异常问题的追溯以及责任的划分。
封装问题案例一 PCB板阻焊工艺 CPU不良批次案
不良案例二
例三
Aux communications equipment limited co
人-改善对策
存在问题: 人员流动性大;现有工资待遇无法很好吸引员工,12年SMT人员平均流失率为9.6 %,
车间配置为;88 人员流失数量为;93人一年中更换2个批次人员,平均在职时间 为6个月,经常出现人员招聘不及时,生产任务只能通过加班加点或者新手短期急 促上岗来解决,对产品质量控制带来很大压力。 作业员熟练度不够;由于员工流动频繁车间对员工的培训工作欠缺,出现部分员工不 熟悉全部的工作内容就安排上岗的情况。 作业员责任心不强;目前的激励制度不能实现良好效果,员工对待工作不重视。产品 经常出现漏检现象。
检测对象
芯片类连锡、 虚焊
不良数量
100883
不良比率
预计检测率 提高
1.46% 1.2%
MMI功 能测试 夹具
Aux communications equipment limited co
增加终端QC抽检
链接 OQC抽检
目前SMT贴片只有炉前、炉后安排人员自检,外面OEM一般检验
模式为;生产 自检 炉后 AOI设 备检验 QC专检的模式,这 种模式虽然会增加人工成本但可以检出大部分主板的外观质量问题减 少维修成本。鉴于目前贴片外观问题比较多情况下SMT已与品管部门 协商增加OQC抽检对主板外观问题进行专检把关。
制程改善与案例分析ppt课件
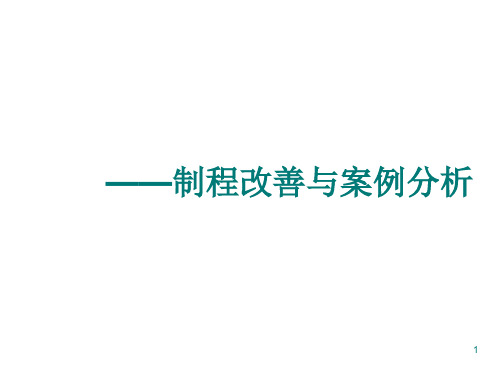
-有无电力,水的浪费?
-蒸汽,压缩空气有无泄露处?
-是否不必要地使用电力、水、蒸汽,燃料,压缩空气?
-设备,机器有无不必要的空转?
-电力是否过负荷?
-能否有效地利用不必要的热量?
25
⑤各部门业务改善的检查清单
对 象 检查项目
-检查资料是否反馈到制造部门应用?
-能否废除或简略工序检查?
-能否废除或简略出厂检查?
步 骤
---避免现行方法影响 (3).现状分析
---IE技巧观察,数据分析
9
IE与现场改善
方
(4).比较分析结果 用5W2H将现状与理想方法比较,使差异
法 明确化.
研
(5).改良方法设计 ---生产数量/使用空间/质量.机能/过多的
究 人员
步 骤
---管理复杂化/费用/实施过程/劳务关系 (6).标准化及实施
IE的基础是“工作研究”
6
IE与现场改善
工作研究的对象 工 ---生产过程最理想?
---工作方法最好? 作 ---机器及工具是否最恰当? 研 ---物料是否最正确?
目的 究 ---生产过程可否简化或省略
---工作方法更完善 ---作业标准化/决定标准时间
7
IE与现场改善
方 探討項目
內容
分析手法
法 制造整個工程系統
-机器
-方法(Method) -交货(Delivery)
-手和脚 - 身体 - 疲劳 - 安全 - 操作
-布置 - 环境 - 照明 - 整理 - 搬运
-产品的设计质量 -原资财的设计品质 -原资财的品质,价格 –原材料使用法 -人-机械装备-库存-制造-检查-搬运 -修理费用-办公费-电力,动力
制程异常分析(典型案例)报告
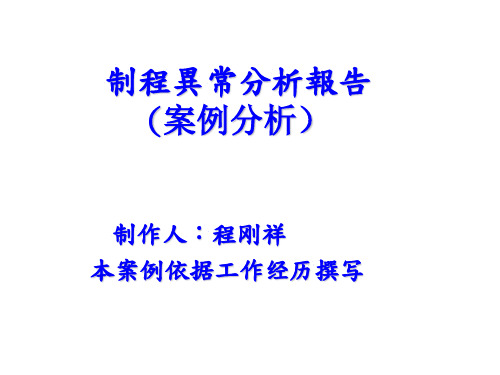
制作人:程刚祥 本案例依据工作经历撰写
一、不良现象描述
a.日期: 2019/12/25
工位: 孔规
b.機型:XXXXX-0X USB 3.1 TYPE-3 沉板母座
c.不良現象及不良率:
USB 3.1 TYPE-3 沉板母座上在做孔规测量,放入孔规不顺畅(不平贴,严
重者可能导致SMT装板不良) 。
剪除毛刺或剪短
孔规检测
五、长期对策
a.图面,作业指导书标准化: 1、修订SIP,补充内容:料带预断点检验毛刺环节并加以组装实配5PCS; 2、来料通过CCD和二次元量测把握冲压件上毛刺的缺陷等级,不得大于 0.01mm。 b.JIG/TOOL工治具修复合理化: 1、通知冲压工序,对该模具进行确认并修复; c.防呆(POKA YOKE)措施(颜色形状方向,声音左右,夹治具布局设变): 1、首件重点检验此异常,重点抽查并以实配检测是否平贴,是否顺畅。
不良圖片說明
12月12日、量化数据求出: 1、抽查料带库存品发现: 其中12月21日2500*7(外强);3500*4; 3500*6外发、 共
计420.9KPCS,经检查铁壳预断面宽度为:0.147-0.125mm,切断后有毛刺(高度超出 0.02mm)现象;
b.现场,现物,现状调查: 1、抽查来料7托盘/ 420.9KPCS ;成品2280PCS各5PCS; c. 调查制程,物料,设备5M1E因子: 1、可能因子:法/机/料。(人/机/物/环/法)
三、验证可能因子(分析)
a. 预计验证时间表: 1、12月26日现场检讨并确认SOP(作业指导); 2、12月26日已抽查来料库存/成品; b. 验证可能因子: 装配不到位;胶芯来料不良,铁壳来料异常; c.验证报告分析提出说明: 1、USB 3.1 TYPE-3 沉板母座上的铁壳预断位点应力异常,手工掰 断有毛刺,高出胶芯界面0.02mm;
现场改善案例集范文
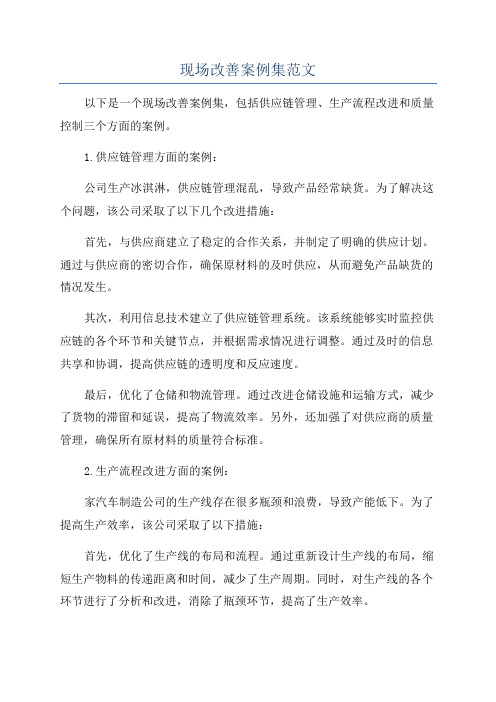
现场改善案例集范文以下是一个现场改善案例集,包括供应链管理、生产流程改进和质量控制三个方面的案例。
1.供应链管理方面的案例:公司生产冰淇淋,供应链管理混乱,导致产品经常缺货。
为了解决这个问题,该公司采取了以下几个改进措施:首先,与供应商建立了稳定的合作关系,并制定了明确的供应计划。
通过与供应商的密切合作,确保原材料的及时供应,从而避免产品缺货的情况发生。
其次,利用信息技术建立了供应链管理系统。
该系统能够实时监控供应链的各个环节和关键节点,并根据需求情况进行调整。
通过及时的信息共享和协调,提高供应链的透明度和反应速度。
最后,优化了仓储和物流管理。
通过改进仓储设施和运输方式,减少了货物的滞留和延误,提高了物流效率。
另外,还加强了对供应商的质量管理,确保所有原材料的质量符合标准。
2.生产流程改进方面的案例:家汽车制造公司的生产线存在很多瓶颈和浪费,导致产能低下。
为了提高生产效率,该公司采取了以下措施:首先,优化了生产线的布局和流程。
通过重新设计生产线的布局,缩短生产物料的传递距离和时间,减少了生产周期。
同时,对生产线的各个环节进行了分析和改进,消除了瓶颈环节,提高了生产效率。
其次,引入了自动化设备和机器人技术。
通过引入自动化设备和机器人技术,减少了人工操作的时间和错误率,提高了生产线的生产能力和质量稳定性。
另外,还利用数据分析和预测技术,实现了产能的动态管理和优化。
最后,加强了员工培训和团队合作。
通过加强员工的培训和技能提升,提高了员工的生产能力和质量意识。
同时,注重团队合作和沟通,促进了生产线各个环节的协同和高效运转。
3.质量控制方面的案例:家电子产品公司的产品经常出现质量问题,影响了公司的声誉和销售。
为了改善产品质量,该公司采取了以下几种措施:首先,加强了原材料的质量管理。
与供应商建立了长期合作关系,并对原材料进行严格的质量检验和筛选。
通过提高原材料的质量,有效降低了产品的良品率。
其次,建立了完善的质量管理体系。
SMT生产制程改善案例答辩

2.3数据的统计 和分析- 主要 不良的分析和 改善
2.针对一些常见不良,可通过 案例学习,深入了解其产生原 理,再结合具体情况,从而制 定有效的改善措施---列举 “碑立不良分析报告”.
胡红华 胡志坚
9月4日 进行中
3.针对每日前三项不良分析, 集聚PE/PD/QE共同讨论制定改 善措施.
【改善对策执行计划表】
项目
对策
SMT
负责人 完成日期 状态 备注
3.1 SPC的运用 -锡膏厚度测试
1.将现有的锡膏厚度测试仪 Lascan-L3000运用于锡膏印 刷工位制程控制;
胡红华
9月1日
进行中
在培训 操作员
2.使用SPC Xbar-Rchart.
3.2 SPC的运用 -锡点外观检查
1.评估现有的P-chart控制 的合理性;
试效率
板PCM功能,效率不高
制作测试架,通过电脑控制能同 时进行多板测试.
对策 先做出具体方案,再行改变现有的单板测试法为多板测试.
效果分析
优点:若运用多板测试,可减少测试人员,测试效率提高.
缺点:多板测试对测试点定位提出更高要求,会出现顶针未对 准测试点而造成误测.同时,对不同机型需要制作专用针床.
文件的制定
和完善
修订<全自动印刷机作业指引>
胡红华 9月1日 进行中 胡红华 9月1日 Open
1.要求外观检查位、测试工位和
2.1数据的统 修理位记录报表. 计和分析-建 2.拉长监督生产线日报表记录情 立生产数据 况,IPQC抽查产线报表记录. 胡红华 DATABASE 3.生产文员统计当日外观检查位
SMT
改善报告
项目
改善前
生产线制程品质生产效率改善案例

生产线制程品质生产效率改善案例在制造业中,保证生产线制程品质和生产效率的改善是非常重要的。
本文将以公司的生产线制程品质和生产效率改善案例为例,详细介绍该公司在此方面的改进措施和取得的成果。
公司是一家生产汽车零部件的制造企业,其主要产品包括发动机零部件、传动系统零部件等。
由于市场竞争日益激烈,客户对产品的质量和交货时间要求越来越高,因此该公司决定对生产线制程品质和生产效率进行改进。
首先,该公司进行了生产线的现状分析和问题定位。
经过调研和数据分析,发现该生产线存在以下问题:一是制程品质不稳定,产品中出现了一定比例的次品率;二是生产效率较低,生产周期长,无法满足客户的需求。
针对问题一,该公司采取了多项措施来提高制程品质。
首先,引进了先进的质量检测设备,以提高产品的检测精度和准确性。
其次,对员工进行了质量培训,强调质量意识和细节要求,提高员工的质量意识和责任感。
此外,还加强了供应商的质量管理和协作,提前对进货物料进行检验和筛选,减少次品率。
对于问题二,该公司着重优化了生产流程和管理系统,提高生产效率。
在生产流程方面,通过对生产线进行布局调整和工艺优化,减少了生产环节和工序的数量,缩短了生产周期。
在管理系统方面,该公司引入了先进的工业互联网技术,实现了设备的智能化和信息的实时传递。
此外,还采用了生产线平衡和产能规划技术,实现了生产资源的最优配置和生产进度的有效控制。
通过以上改进措施的实施,该公司取得了明显的改善效果。
首先,制程品质得到了显著提升。
产品的次品率明显下降,满足了客户对品质的要求,提高了客户满意度。
其次,生产效率得到了大幅度的提高。
生产周期缩短,大大提高了生产线的产能,减少了生产成本,提高了企业的利润率。
此外,还改善了员工的工作环境和工作质量,提高了员工的工作满意度。
综上所述,通过对生产线制程品质和生产效率的改进,该公司取得了显著的成果。
然而,改进工作并不是一次性任务,而是一个持续改进的过程。
该公司将继续关注生产线的制程品质和生产效率,不断改善和优化,以适应市场和客户的需求,提高企业的竞争力。
工厂质量改善案例

工厂质量改善案例工厂质量改善是现代生产企业中非常重要的一项工作。
通过不断改进和优化生产流程,提高产品质量,企业可以增强竞争力,提升市场份额。
本文将介绍一个工厂质量改善的案例,以帮助读者更好地了解如何在实践中改善质量。
该案例发生在一家汽车零部件生产工厂中。
该工厂生产的产品用于汽车的制造,产品质量直接影响到汽车的性能和安全性。
在一段时间内,该工厂的产品出现了质量问题,频繁出现客户的投诉和产品的退货。
为了解决这个问题,工厂决定进行质量改善。
首先,工厂成立了一个质量改善团队,由质量部门的专业人员和相关生产部门的代表组成。
该团队的任务是分析产品质量问题的根本原因,并提出改进方案。
团队成员通过对生产线的观察和数据的分析,确定了几个主要的问题,包括生产过程中的不良工艺、设备的老化和工人的操作不规范等。
接下来,质量改善团队制定了一系列改进措施。
首先,他们针对生产过程中的不良工艺进行了改进。
通过引入先进的生产设备和工艺技术,以及加强操作规范的培训,工厂成功地提高了生产过程中的质量稳定性。
其次,他们对老化的设备进行了维修和更换,确保设备的正常运转。
最后,他们加强了对工人的培训和管理,提高了操作的标准化程度和质量意识。
改进措施的实施效果显著。
经过一段时间的生产和客户的反馈,工厂的产品质量得到了明显的改善。
客户的投诉和退货率大幅下降,产品的一致性和稳定性得到了提高。
同时,工厂的生产效率也得到了提升,生产成本得到了降低。
这不仅提高了工厂的竞争力,也增强了企业的声誉和市场形象。
通过这个案例,我们可以看到,质量改善是一个系统工程,需要全面的分析和解决。
首先,需要找出质量问题的根本原因,确定改进的方向和重点。
其次,需要制定具体的改进措施,并确保其有效的实施。
最后,需要持续跟踪和评估改进的效果,及时进行调整和优化。
在实践中,工厂质量改善需要广泛的参与和合作。
除了质量部门的专业人员,生产部门和技术部门的代表也需要参与其中。
只有通过各部门之间的密切合作和信息共享,才能实现质量改善的目标。
- 1、下载文档前请自行甄别文档内容的完整性,平台不提供额外的编辑、内容补充、找答案等附加服务。
- 2、"仅部分预览"的文档,不可在线预览部分如存在完整性等问题,可反馈申请退款(可完整预览的文档不适用该条件!)。
- 3、如文档侵犯您的权益,请联系客服反馈,我们会尽快为您处理(人工客服工作时间:9:00-18:30)。
②对生产合理化三要素的检查清单 检查项目 -什么产品,什么工程多发生不良? -能否保证产品的性能,耐久性? -是否存在要求以上的精密度? -是否确定检查标准? 品质(Quality) -是否施行对职员的品质PR? -检查标准是否合理? -是否灵活使用管理,统计图表等进行管理 改善? 对 象
交货期 (Deli (Machine) -材料(Material) -品质(Quality) -成本(Cost) -机器 -方法(Method) -交货(Delivery)
①对4M的检查清单
②对生产合理化三要素的检查清单
③对作业动作的检查清单
④对作业者环境的检查清单
-手和脚 - 身体 - 疲劳 - 安全 - 操作
-延迟交货期的最大原因是什么? -工程怎样进行重编,才能缩短生产周期? -减少半成品的诀窍? -订单同生产能力是否平衡? -是否正确地布置材料,入库? 14 -外协厂家管理上的困难是什么?
②对生产合理化三要素的检查清单 对 象 检查项目 -是否节约机器,材料,电力等? -是否建立管理及提高生产效率的对策? -是否提高人和机器的运转效率? -能否提高效率及品质,降低成本? -报价单同实际成本是否合理? -购买计划或布置的样式,单价的决定是 否良好(正确)? -是否制定提高职员成本意识的对策? -有无更廉价的购买处,更廉价的制造地? -作业方法的改善及机械化等能否节约劳 动成本?
4
常用改善方法
一般性
---5W2H法
---脑力激荡法 ---愚巧法----防呆 ---比较法
IE 7大手法
5
IE与现场改善
对 Industrial Engineering工业工程 协助以最小的投入(Input)得到最大的产 出 (Output),以致获得最大的效益. IE是借着设计,改善或设定人.机.料.法的 工作 系统,以求得到更高生产力的专门技术. IE的基础是“工作研究”
研
究
工廠布置物料移動
流程圖分析 模型配置分析 動作研究
作業區域配置
分 析 技
作業中的作業 組合作業或自動機作業
作業者位置及周圍物品的放置 方法,作業者物品移動的方法
動作經濟原則 作業簡化原則 連合工程分析
以組合進行的共同作業或以自 動機器作業的人機配合
工作抽樣 作業簡化原理
巧
短的作業周期且高反復度的作 業員動作
基本動作的分析 動作經濟原則
8
IE与现场改善
方 法 研
究
步 骤
(1).选择问题,并将问题的目的明确化 ---现有资料整理出问题 ---将来可预测的问题 ---认为应该解决的问题 (2).设定理想方法 (牙膏) ---认清目的与手段关系 ---避免现行方法影响 (3).现状分析 ---IE技巧观察,数据分析
9
IE与现场改善
方 法 研
究
步 骤
(4).比较分析结果 用5W2H将现状与理想方法比较,使差异 明确化. (5).改良方法设计 ---生产数量/使用空间/质量.机能/过多的 人员 ---管理复杂化/费用/实施过程/劳务关系 (6).标准化及实施 新的最佳方法,经认可后标准化,训练教导 10 员工执行.
12
①对4M的检查清单
对 象 检查项目
-能否使用容易购买且物美价廉的材料? -能否减少不良品和废品? -切割尺寸是否非常恰当? -材料堆放处是否整顿好? 材料(Material) -是否遵守有关材料的标准? -是否做好半成品的管理? -是否做好材料的区分? -能否使搬运材料的方法更合理化? -能否采用更方便的作业姿式和方法? -能否使手工作业发展成工具化,机械化? -能否将作业方法改成女人也能干的作业? 方法(Method) -有无缩减工时的方法? -能否使用其它机器? -能否一人操作2,3台或者更多的机器? -能否简化现在的作业?
3
改善的十大抵抗
1.那种东西没有用. 2.确实是这样,但我们公司则不同. 3.虽然是个好的方案,但. . . . . . . 4.成本无法再降低. 5.我们也一直这样努力着. 6.不喜欢接受别人的建议而做. 7.要降低成本,质量也会降低. 8.目前不是很理想吗?为何要改变. 9.这种方法行不通,早在20年前我们就试过. 10.我们对这件事情已清楚了.
-布置 - 环境 - 照明 - 整理 - 搬运 -产品的设计质量 -原资财的设计品质 -原资财的品质,价格 –原材料使用法 -人-机械装备-库存-制造-检查-搬运 -修理费用-办公费-电力,动力
11
⑤各部门改善业务的检查清单
①对4M的检查清单
对 象 检查项目 -有无使人容易疲劳,危险之处? -作业者的工作知识是否充分? -能否减少作业者人数? -温度,照明是否合适? 作业者(Man) -加工品,工具是否在互相干涉的范围内? -是否有效地发挥作业者的技能? -作业者的自主性是否发挥出来? -作业分配量是否均匀? -能否使两个以上的工具结合起来? -切削工具的使用是否适合于作业? -工具类是否备齐? -是否处于最佳运行状态? 机器(Machine) -是否正确使用? -是否有效地运用机器的能力? -是否被有效地利用自动移送,加热时间等? -机器的高度有无不合理之处?
6
IE
的
认 识
IE与现场改善
工 工作研究的对象 ---生产过程最理想? ---工作方法最好? ---机器及工具是否最恰当? ---物料是否最正确? 目的 ---生产过程可否简化或省略 ---工作方法更完善 ---作业标准化/决定标准时间
7
作
研
究
IE与现场改善
方 法
探討項目 制造整個工程系統 內容 從原料→生產→成品→出貨止 工廠內部與部門之間及人與物 料之活動 分析手法 制造流程圖分析 操作標準書分析
——制程改善与案例分析
1
1
2 3 4
改善的十种基本精神 改善的十大抵抗
常用改善手法 IE与现场改善 改善类型清单 案例分析
2
目录
5 6
一改善的十种基本精神
1.舍去原有的观念,凡事求新求变. 2.不要找理由,而是找方法. 3.不能满足现状. 4.改善对策愈多愈好.,要因分析至少50点. 5.错误立即改正. 6.改善就是赚钱. 7.问题末改善之前不休息. 8.保持怀疑态度,连续追问5次为什么这样. 9.一个人的创意可供十个人共分享. 10.改善永无止境.