钢水铁水
高温熔融金属作业安全管理制度

为有效防止钢铁冶金行业高温熔融金属(包括钢水、铁水、液态炉渣及其相关设备)事故,保障从事高温熔融金属作业的人员安全 , 结合公司的具体情况,特制定本制度。
合用于高温熔融金属作业的管理。
熔融金属事故主要起因于水汽化爆炸,高温金属液体容器坠落、倾翻、高温金属液体的反应气体喷溅、熔融金属泄漏等.钢铁企业在生产过程中,要特殊注重冶金设备和冶炼过程的防水、防潮以及起重运输设备的检测、检验,严格控制生产工艺条件,强化安全管理工作,从以下 6 个方面采取防范措施防止高温熔融金属伤害事故的发生。
4。
1 防止熔融金属遇水爆炸4.1。
1 熔融金属生产、处置和贮存设施附近、运输路线及附近区域不得有积水,正上方不得存在滴、漏水隐患。
4.1。
2 对原料、辅助材料严格检查 ,确保加入炉中的原料、辅助材料干燥无水。
4.1。
3 输送、转注熔融金属所使用的设备设施在输送、转注前须经充分干燥并保证畅通。
4。
2 熔融金属的安全吊运要求4.2。
1 吊运熔融金属应当采用带有固定龙门钩的冶金铸造起重机,司机室等高温作业岗位应当采取降温防护措施.冶金铸造起重机每年应定期检测一次(对外报检)。
4.2.2 起重机的吊具(钩)、钢丝绳、盛装熔融金属的容器 (设备) 的耳轴等应定期进行检测,凡耳轴浮现内裂纹、壳体焊缝开裂、明显变形、耳轴磨损大于直径的 10%、机械失灵、衬砖损坏超过规定,均应报修或者报废。
4.2.3 起重机应由经专门培训、考核合格的专职人员指挥,同一时刻只应一人指挥,指挥信号应符合要求。
吊运时应检查确认挂钩、脱钩可靠,方可通知司机起吊,起吊前应进行试重,人员应站在安全位置,并尽量远离起吊地点。
4.2.4 吊运装有铁水、钢水、液渣的罐 ,应与邻近设备或者建、构筑物保持大于 1.5m 的净空距离。
倾倒熔融金属时,容器(罐、包)周围 4m 内不可有非作业人员,防止熔融金属飞溅或者洒落伤人.4。
2.5 吊运的熔融金属液面应与盛装容器口保持至少 300mm 的距离。
钢材成本计算
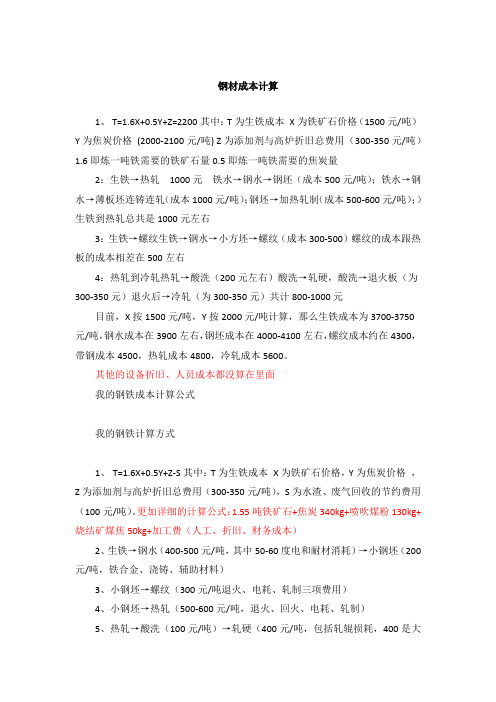
钢材成本计算1、T=1.6X+0.5Y+Z=2200其中:T为生铁成本X为铁矿石价格(1500元/吨)Y为焦炭价格(2000-2100元/吨) Z为添加剂与高炉折旧总费用(300-350元/吨)1.6即炼一吨铁需要的铁矿石量0.5即炼一吨铁需要的焦炭量2:生铁→热轧1000元铁水→钢水→钢坯(成本500元/吨);铁水→钢水→薄板坯连铸连轧(成本1000元/吨);钢坯→加热轧制(成本500-600元/吨);)生铁到热轧总共是1000元左右3:生铁→螺纹生铁→钢水→小方坯→螺纹(成本300-500)螺纹的成本跟热板的成本相差在500左右4:热轧到冷轧热轧→酸洗(200元左右)酸洗→轧硬,酸洗→退火板(为300-350元)退火后→冷轧(为300-350元)共计800-1000元目前,X按1500元/吨,Y按2000元/吨计算,那么生铁成本为3700-3750元/吨,钢水成本在3900左右,钢坯成本在4000-4100左右,螺纹成本约在4300,带钢成本4500,热轧成本4800,冷轧成本5600。
其他的设备折旧、人员成本都没算在里面我的钢铁成本计算公式我的钢铁计算方式1、T=1.6X+0.5Y+Z-S其中:T为生铁成本X为铁矿石价格,Y为焦炭价格,Z为添加剂与高炉折旧总费用(300-350元/吨),S为水渣、废气回收的节约费用(100元/吨)。
更加详细的计算公式:1.55吨铁矿石+焦炭340kg+喷吹煤粉130kg+烧结矿煤焦50kg+加工费(人工、折旧、财务成本)2、生铁→钢水(400-500元/吨,其中50-60度电和耐材消耗)→小钢坯(200元/吨,铁合金、浇铸、辅助材料)3、小钢坯→螺纹(300元/吨退火、电耗、轧制三项费用)4、小钢坯→热轧(500-600元/吨,退火、回火、电耗、轧制)5、热轧→酸洗(100元/吨)→轧硬(400元/吨,包括轧辊损耗,400是大钢厂指标)6、轧硬→退火(200元/吨)250罩退贵1007、轧硬→(退火50元/吨加热+锌层成本,按照50克锌层计算每平方米的)8、镀锌→彩涂(按每平米计算成本)。
炼钢金属原料的种类及对铁水、废钢、铁合金的要求

【本章学习要点】本章学习炼钢金属原料的种类及对铁水、废钢、铁合金的要求,常用的铁合金的作用,非金属料的种类、作用及其要求。
原材料的质量和供应条件直接影响炼钢的技术经济指标。
保证原材料的质量,既指保证原材料化学成分和物理性质满足技术要求,还指原材料化学成分和物理性质保持稳定,这是达到优质、高产、低耗的前提条件。
炼钢原材料可分为金属料和非金属料两大类。
第一节金属料炼钢用的金属料主要有铁水、废钢、生铁、原料纯铁、海绵铁、中间合金材料和铁合金。
一、铁水铁水是转炉炼钢最主要的金属料,一般占转炉金属料70%以上。
铁水的成分、温度是否适当和稳定,对简化、稳定转炉操作,保证冶炼顺行以及获得良好的技术经济指标都十分重要。
转炉炼钢对铁水有如下要求:1)温度:温度是铁水带入炉内物理热多少的标志,是转炉炼钢热量的重要来源之一。
铁水温度过低,将造成炉内热量不足,影响熔池升温和元素的氧化过程,不利于化渣和去除杂质,还容易导致喷溅。
一般要求入炉铁水温度不低于l250℃,而且要稳定。
2) 硅:铁水中硅的氧化能放出大量的热量,生成的Si02是渣中主要的酸性成分,是影响熔渣碱度和石灰消耗量的关键因素。
铁水含硅高,则转炉可以多加废钢、矿石,提高钢水收得率,但铁水含硅量过高,会因石灰消耗量的增大而使渣量过大,易产生喷溅并加剧对炉衬的侵蚀,影响石灰熔化,从而影响脱磷、脱硫。
如果铁水含硅量过低,则不易成渣,对脱磷、脱硫也不利。
因此,要求铁水含硅质量分数在0.2%~0.6%。
3)锰:锰是钢中有益元素,对化渣、脱硫以及提高炉龄都是有益的。
但冶炼高锰生铁将使高炉焦比升高,为了节约锰矿资源和降低炼铁焦比,一般采用低锰铁水,锰质量分数为0.2%~0.4%。
4)磷:磷是一个强发热元素。
一般讲磷是有害元素,但高炉冶炼中无法去除磷。
因此,只能要求进入转炉的铁水含磷量尽量稳定,且铁水含磷越低越好。
5)硫:硫也是有害元素。
炼钢过程虽然可以去硫,但会降低炉子生产率,增加原材料消耗。
炼钢流程及合金辅料
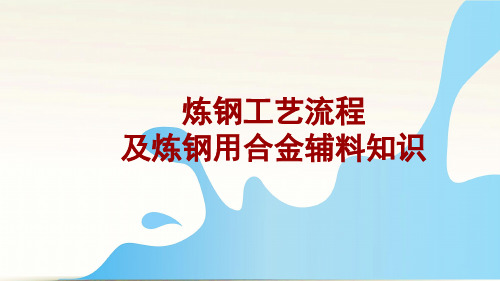
钢与生铁的区别: 元素 C Si Mn p s
(2)转炉吹炼
生铁货铸铁(%) 2.5-4.5 0.3-4.0 0.4-2.0 0.015-0.5 0.01-0.1
2.高炉是炼铁的主要设备,使用的原料有铁矿石(包括 烧结矿、球团矿和块矿)、铁水送炼钢厂炼钢; 高炉煤气主 要用来烧热风炉,同时供炼钢厂和轧钢厂使用;高炉渣经水 淬后送水泥厂生产水泥。
炼钢简述
3.炼钢,目前主要有两条工艺路线,即转炉炼钢工艺流 程和电弧炉炼钢流程。通常将“高炉——铁水预处理——转 炉——精炼——连铸”称为长流程,而将“废钢——电弧 炉——精炼——连铸”称为短流程。
硅钙合金牌号及化学成份
牌号 化学成份% Ca Si C Al P S ≥≤
Ca31Si60 31 55-65 1.0 2.4 0.04 0.05 Ca28Si60 28 55-65 1.0 2.4 0.04 0.05 Ca24Si60 24 55-65 1.0 2.5 0.04 0.04 Ca20Si55 20 50-60 1.0 2.5 0.04 0.04
几种常见铁合金
1.硅钙:
硅钙合金是由元素硅、钙和铁组成的复合合金,是一种较为理想的复合脱氧剂、脱硫 剂。被广泛应用于优质钢、低碳钢、不锈钢等钢种和镍基合金、钛基合金等特殊合金的生 产当中;并适合作转炉练钢车间用的增温剂;还可以作铸铁的孕育剂和球墨铸铁生产中的 添加剂。
钙和硅与氧都有很强的亲和力。特别是钙,不仅与氧有极强的亲和力,而且与硫、氮 都有很强的亲和力。所以硅钙合金是一种较理想的复合胶氧剂、脱硫剂。硅合金不仅脱氧 能力强,脱氧产物易于上浮,易于排出,而且还能改善钢的性能,提高钢的塑性、冲击韧 性和流动性。目前硅钙合金可以代替铝进行终脱氧。被应用于优质钢。特殊钢和特殊合金 生产中。例如低碳钢、不锈钢等钢种和镍基合金、钛基合金等特殊合金,均可用硅钙合金作 脱氧剂。硅钙合金也适合作转炉练钢车间用的增温剂,硅钙合金还可用作铸铁的孕育剂和 球墨铸铁生产中的添加剂。
铁水“三稳”供应对炼钢工艺的影响

铁水“三稳”供应对炼钢工艺的影响一、铁水温度对炼钢的影响铁水温度的高低对炼钢的影响很大,根据转炉冶炼工艺,转炉冶炼的热量基本来源于铁水的物理热和化学热,在化学热一定的情况下,铁水的物理热是决定冶炼能否顺利的关键因素。
铁水温度低造成吹损大,钢铁料消耗高,钢水质量无保障,炉龄下降等后果。
铁水温度不仅对炼钢工艺十分重要,对于铁水输送也有影响,如果铁水在输送过程中的温度过低,还会造成铁水罐车的结壳、结瘤,直接影响正常生产作业。
因此,铁水输送过程中的温降是冶金工作者普遍关注的问题。
多年来,国内外许多研究人员曾对这一问题进行研究。
铁水从高炉输送到炼钢厂转炉,要经过出铁、运输、扒渣、预处理、倒罐、空罐返回和等待等一系列工序,其中每一工序和铁水罐的自身状态对于铁水温降都有影响。
钢铁企业的特点一般是高炉多、铁水用户多、运输铁水的罐车多,而且铁水车在厂内各处游动,难以定位跟踪。
这些原因增加了控制铁水输送过程及减小铁水温降难度。
转炉冶炼工艺告诉我们,转炉冶炼的热量基本来源于铁水的物理热和化学热,在化学热一定的情况下,铁水的物理热是决定冶炼能否顺行的关键因素,特别是公司当前正处于低成本战略的关键时期,铁水温度如果波动大,常会影响转炉炉前一批料矿石摄入量不准确,造成终点温度过低或过高,导致钢水后吹严重,吹损大,钢铁料消耗高,成本高,钢水质量无保障,炉龄下降,并危及安全生产等严重后果。
所以,入炉铁水温度保持稳定对转炉工序意义重大。
二、铁水硅含量对炼钢工艺影响在实际生产中, 硅高时,点火开氧后便可加入造渣料,以形成具有一定碱度及脱磷效果的初渣,减少对炉衬的侵蚀,加强对金属液面的覆盖。
硅低时,由于先发生的是碳的氧化反应,没有早期生成的酸性初渣, 并且碳的氧化产物使渣中( FeO ) 减少,这时加入造渣料不但不会熔化,还由于造渣料的加入而形成很大的降温效应,从而起到一定的负面影响,这就是硅过低时造渣料加入过早使后期出现炉渣严重返干的原因,由于后期吹炼时主要是碳的氧化,不利形成有利化渣的( FeO )出现,降低渣的流动性,影响去硫、去磷效果,且渣不能很好的覆盖在金属液面上,加剧金属喷溅的发生,出现炉口、氧枪粘钢现象, 严重时甚至粘死烟道,造成停产事故。
高温熔融金属安全知识

3.一是在作业前,对作业人员进行安全教育, 介绍现场工作环境和注意事项,进行安全交底 。二是安排专人预先对电、煤气、蒸汽、氧气 、氮气等要害部位及安全设施进行确认,并办 理相关审批、确认手续;在确认安全的情况下 ,切割或拆除有关设备设施或装置,并采取有 效的安全防护措施。
•
• 高温金属液体伤害是冶金企业最典 型的职业伤害。高温金属液体包括熔 融金属(钢水、铁水、铝液、铜液、 镁液等)及其液态炉渣。熔融金属事 故主要起因于水汽化爆炸,高温金属 液体容器坠落、倾翻,高温金属液体 的反应气体喷溅,熔融金属泄漏,其 他爆炸等。
• 事故发生在2007年4月18日7时45分左 右,辽宁铁岭市清河特殊钢有限公司发生钢 水包整体脱落事故,装有30吨钢水的钢包 突然滑落,钢水撒出,冲进车间内5米远的 一间房屋,造成在屋内正在交接班的32人 全部死亡,6名操作工轻伤。
• 经专家对事故现场初步勘察分析,造成这起事故的 主要原因,一是该公司生产车间起重设备不符合国家规定 ,按照《炼钢安全规程》的规定,起吊钢水包应采用冶金 专用的铸造起重机,而该公司却擅自使用一般用途的普通 起重机;二是设备日常维护不善,如起重机上用于固定钢 丝绳的压板螺栓松动;三是作业现场管理混乱,厂房内设 备和材料放置杂乱、作业空间狭窄、人员安全通道不符合 要求;四是违章设置班前会地点,该车间长期在距钢水铸 锭点仅5米的真空炉下方小屋内开班前会,钢水包倾覆后 造成人员伤亡惨重。
原因,委托相关机构进行技术鉴定,以最终确集团公司2号100吨转炉 2013年4月1日11时22分发生爆炸,已造成4人 死亡,28人受伤。记者从事故新闻发布会现 场获悉,此次事故系系因处理氧枪结瘤时发
生放炮引起炉内高温红渣溅出所致,将挡火 门和主控室全部损毁。
• 熔融金属泄漏后,在保证安全的前 提下应及时用熔剂或砂土挡住已流出的 金属液体,防止熔融金属大面积流淌或 流入积水,尤其是半封闭空间环境中的 积水。当熔融金属引起可燃物着火时, 应使用干燥沙子或其他耐火材料扑救, 不得使用水或二氧化碳灭火器、水剂灭 火器灭火。
铁水预处理工艺

投资成本(—)
低
一般
较高
铁水预脱硫条件优于钢水脱硫条件,原因:
1.铁水中含有较高的C、Si、P等元素,提高了铁水中 硫的活度系数; 2.铁水中氧含量低,提高渣铁之间硫分配比,脱硫效 率高; 3.铁水含氧量低,因而可以使用强脱硫剂强化脱硫而 不会造成强烈氧化; 4.铁水脱硫费用低于高炉、转炉和炉外精炼的脱硫费 用。
4.3.3 铁水预脱硫的意义 4.3.4 铁水预脱硫的基本原理
A 金属、氧化物及碳化物脱硫 B 碱性渣脱硫 4.3.5 铁水预脱硫的方法 投掷法:将脱硫剂投入铁水中脱硫 喷吹法:用载气将脱硫剂喷入铁水中脱硫 搅拌法(KR法):通过中空机械搅拌器向铁水
内加入脱硫剂,搅拌脱硫
脱硫工艺的技术比较
脱硫工艺方法
2.Mg/CaC2复合脱硫剂 喷吹Mg/CaC2复合脱硫剂的体系,由于CaC2与[O]
反应生成CaO,MgS(固)不能稳定存在于该体系中,由于 Mg/CaC2复合脱硫剂体系与Mg/CaO复合脱硫体系的脱 氧、脱硫平衡反应是相同的,因此对脱氧、脱硫能力 而言,喷吹这两种复合脱硫剂效果是一样的。
但是,由于CaC2比CaO 昂贵且不安全,因此从脱 硫成本及储运、使用的安全性方面考虑,使用Mg/ CaO复合脱硫剂更安全、成本更低。
高碱度烧结矿
颗粒
0
20-40
O2+烧结矿 50%
40-80
反应速率常数 (min-1) 0.25
0.06
处理后 [Si]%
0.13 0.10 ≤0.10%
4.3 铁水预脱硫工艺 4.3.1 国外铁水预脱硫技术的发展背景与现状
历史背景:60年代,氧枪转炉炼钢的崛起工业的发展 给钢铁材料质量提出了更高要求。
钢铁水喷溅的原因及防止措施

仅供参考[整理] 安全管理文书钢铁水喷溅的原因及防止措施日期:__________________单位:__________________第1 页共5 页钢铁水喷溅的原因及防止措施一、喷溅原因在钢铁冶炼过程中,钢水和铁水是高温融熔液体,本身并不致喷溅或爆炸.炼钢过程主要是氧化过程,它的反应主要是钢渣之间的反应,反应速度与温度和气相压力有密切关系。
碳氧反应的同时,产生大量一氧化碳气体,产生的气体能否顺利排除,与熔渣的沸腾有直接关系。
熔渣的碱度适当、流动性好,促使熔池有较活跃的沸腾,达到碳的氧化反应条件。
依据碳的氧化反应机理,分析平炉冶炼期间产生大喷溅或爆炸的原因是:(1)在熔池中熔渣过多、渣子粘,流动性不好以及熔池沸腾差的情况下,便加入氧化剂。
由于碳氧反应产生大量一氧化碳气体,因溶渣的粘性太大,使气体不能顺利排除,同时促使溶池产生巨大压力,在此瞬间形成大喷溅或大爆炸。
(2)由于低温操作,在熔池尚未形成一定性能的碱性渣或温度低的情况下,就急于集中往炉内加入氧化剂,所加入的氧化剂未完全起作用浮在熔渣中,当熔池温度上升或从炉门抽管吹氧时,达到碳氧反应条件,突然进行急剧的碳氧化反应,产生大量气体,这些气体不能顺利排除,导致产生大喷溅或爆炸。
(3)由于熔池温度过高或熔池的上下温差大。
当炉子倾动或抽管吹氧时,促使熔池形成对流作用而引起激烈反应,产生大喷溅或爆炸。
二、防止措施(1)补炉时要高温正压,分层投补,保证烧结好。
防止一次投补大量耐火材料,保持炉床形状和出钢口形状正常,防止剩留残钢、残渣,防止炉床局部上浮。
第 2 页共 5 页(2)熔渣碱度要适当,流动性好,沸腾活跃,通常称为高温、薄渣,活跃,沸腾。
为此要尽量多放初期渣,提前在熔化期进行,造渣,使熔渣碱度控制在2.0~2.5。
(3)严禁低温操作,并在熔池温度低的情况下,加入氧化剂(矿石,铁皮)。
(4)严禁氧化剂集中和大批量加入,特别要防止所加入的氧化剂未完全进行碳氧反应,又连续加入,同时要注意所加入的氧化剂未反应完全时,不能从炉门插管吹氧。
钢铁水喷溅的原因及防止措施

钢铁水喷溅的原因及防止措施姓名:XXX部门:XXX日期:XXX钢铁水喷溅的原因及防止措施一、喷溅原因在钢铁冶炼过程中,钢水和铁水是高温融熔液体,本身并不致喷溅或爆炸.炼钢过程主要是氧化过程,它的反应主要是钢渣之间的反应,反应速度与温度和气相压力有密切关系。
碳氧反应的同时,产生大量一氧化碳气体,产生的气体能否顺利排除,与熔渣的沸腾有直接关系。
熔渣的碱度适当、流动性好,促使熔池有较活跃的沸腾,达到碳的氧化反应条件。
依据碳的氧化反应机理,分析平炉冶炼期间产生大喷溅或爆炸的原因是:(1)在熔池中熔渣过多、渣子粘,流动性不好以及熔池沸腾差的情况下,便加入氧化剂。
由于碳氧反应产生大量一氧化碳气体,因溶渣的粘性太大,使气体不能顺利排除,同时促使溶池产生巨大压力,在此瞬间形成大喷溅或大爆炸。
(2)由于低温操作,在熔池尚未形成一定性能的碱性渣或温度低的情况下,就急于集中往炉内加入氧化剂,所加入的氧化剂未完全起作用浮在熔渣中,当熔池温度上升或从炉门抽管吹氧时,达到碳氧反应条件,突然进行急剧的碳氧化反应,产生大量气体,这些气体不能顺利排除,导致产生大喷溅或爆炸。
(3)由于熔池温度过高或熔池的上下温差大。
当炉子倾动或抽管吹氧时,促使熔池形成对流作用而引起激烈反应,产生大喷溅或爆炸。
二、防止措施(1)补炉时要高温正压,分层投补,保证烧结好。
防止一次投补大量耐火材料,保持炉床形状和出钢口形状正常,防止剩留残钢、残渣,第 2 页共 5 页防止炉床局部上浮。
(2)熔渣碱度要适当,流动性好,沸腾活跃,通常称为高温、薄渣,活跃,沸腾。
为此要尽量多放初期渣,提前在熔化期进行,造渣,使熔渣碱度控制在2.0~2.5。
(3)严禁低温操作,并在熔池温度低的情况下,加入氧化剂(矿石,铁皮)。
(4)严禁氧化剂集中和大批量加入,特别要防止所加入的氧化剂未完全进行碳氧反应,又连续加入,同时要注意所加入的氧化剂未反应完全时,不能从炉门插管吹氧。
并且要适当控制供给燃料。
钢铁企业新型铁水运输方法

钢铁企业新型铁水运输方法铁水运输将高炉炼铁与转炉炼钢车间自然而然的结合在一起,实现了炼铁与炼钢之间距离最短、铁水运送方式最直接、最便利的衔接,中间无任何多余的运输工具,最简洁的“一包到底”,工艺布局紧凑、合理,节省大量建设成本及运行费用。
标签:短流程;高炉;炼钢;铁水运送铁水运输是钢铁企业关键工艺运输之一,由于铁路运输方式具有载重量大、运行成本低、对运输货物适应性强等优势,自我国现代意义的钢铁企业诞生以来,铁路运输一直是钢铁企业内部铁水转运的主导方式。
铁水输送的方式需要配置大量的机车,而且占地面积大、投资高、运转周期长、铁水温降大;铁路运输的灵活性差,线路限制条件多,钢铁企业总平面布置往往受限于铁路线路设计的要求。
铁路运送铁水方式突显单一化、低速化,已经不能适应钢铁企业运输方式多样化,高速化的发展方向,变革铁水运输方式的要求十分迫切。
近年来,铁水运输方式也有所改变,鱼雷罐车的使用及一包到底铁水运输方法的应用,节省了铁水运输的投资及运输成本,这些方法仍以铁路运输为主,而公路运输铁水方式受到运量及稳定性的影响目前仅在部分高炉使用。
随着国民经济的高速发展,土地制约因素对钢铁企业的发展影响越来越明显,变革铁路运输的要求十分迫切。
“紧凑性”总图布置成为技术发展的方向。
炼铁炼钢车间距离更近,铁路运输的局限性更加突出。
在钢铁联合企业的设计过程中,需要有更好的运输方式来解决铁水厂内运输问题。
1 简述2002年山西某地建设年产100万吨钢铁企业,内容包括原料场、石灰窑、烧结、炼铁、炼钢、连铸、线棒材等主要生产工艺设施和配套公辅设施,由于建设场地十分有限,公司要求车间内部不设铁路运输,线棒材成品可由铁路外运。
本着总图布置紧凑这一原则,优化工艺流程,全厂的运输基本上采用吊车运铁水、钢水、钢坯,铁水到炼钢采用短流程、连铸坯到轧钢采用热装热送工艺流程,降低各道工序能耗,以创造高效益为最终目标。
2 平面布置及车间设施炼铁车间设计2座380m3高炉,两座高炉呈一列式镜像布置,高炉中心距70m,高炉冷却壁为汽化冷却形式,3座球式热风炉布置在高炉列线上,矿焦槽与重力除尘器、布袋除尘器呈对称布置在高炉两侧,分别与高炉中心线相距35.742m和19.72m,高炉铁水罐(容量50t)布置在出铁场端头,高炉水冲渣系统布置在斜桥侧。
钢水铁水

钢水铁水1、钢水温度与钢熔点温度之差。
比如钢熔点1400度,钢水温度为1410度,过热度即为10度。
2、过热度太小,钢水易被夹杂物污染,同时易使水口发生堵塞甚至冻结,在连铸开浇初期,中间包尚未“热透”时,此问题尤为突出;而过热太大,则使铸坯中心偏析加重,甚至诱发拉漏事故,或者因形成的坯壳较薄而出现裂纹,同时使柱状晶得到发展。
因此,控制过热度是保证连铸产量和铸坯质量的关键工艺参数之一。
3、以上各位所说的“铁水”,是按化学元素的“铁”定义的。
但在钢铁厂里所说的铁,和铁水都是指含碳量高的生铁,和生铁水。
“发现他们老在钢水里加入铁水”,你误解了!炼钢工人是把含碳量高的铁水加到炼钢炉里,经过冶炼,按要求加入适当的合金成份,保留适当的碳,除掉多余的碳,和有害的杂质。
最后成为具有特定成份的钢4、含碳量区别,严格地说,含碳量大于2.14%即为铁,小于2.14%即为钢,实际的钢生产中含碳量一般较低,为亚共析钢.加入炉中的石灰等是为了脱磷\脱硫,其他合金应该是脱氧的作用和产品要求的成分.5、铁水怎么会变成钢水呢??!!这门技术目前国际上还没有人能突破。
首先你要明白铁水和钢水的区别:钢是含碳量为0.03%~2%的铁碳合金,含碳量2%~4.3%的铁碳合金称生铁。
所以说你的题目出错啦!只有“钢水能变成铁水”,而且还应在特定的条件下采取特定的手段。
目前我国只有几家公司能成功的利用工业纯废钢增碳技术把钢水变成铁水,这种手段能有效的控制铁液中的杂质元素和S、P含量,铁水很干净,而且成本较Q12生铁熔炼节省300~500元/吨。
6、冶炼195钢种为什么有钢水不流的现象那就是所谓的高温套眼啊,也有叫做高温截流或者是流动性差的。
最主要的原因就是钢水里面氧和脱氧剂里面的铝形成了三氧化二铝的高熔点物质,而且在水口内壁上凝结,影响钢水的流动性,初期是拉速下降,时间长了就会造成中包因为钢水置换的太慢而形成低温,如果没有新的钢水置换的话就会造成停机。
(新)高温熔融金属作业安全管理制度
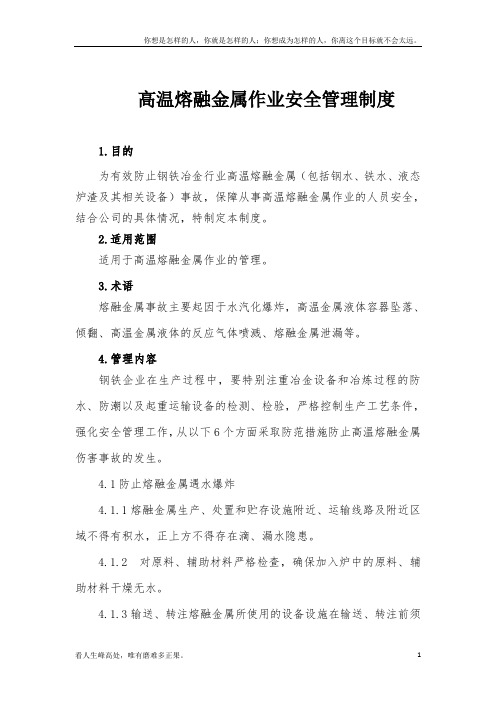
高温熔融金属作业安全管理制度1.目的为有效防止钢铁冶金行业高温熔融金属(包括钢水、铁水、液态炉渣及其相关设备)事故,保障从事高温熔融金属作业的人员安全,结合公司的具体情况,特制定本制度。
2.适用范围适用于高温熔融金属作业的管理。
3.术语熔融金属事故主要起因于水汽化爆炸,高温金属液体容器坠落、倾翻、高温金属液体的反应气体喷溅、熔融金属泄漏等。
4.管理内容钢铁企业在生产过程中,要特别注重冶金设备和冶炼过程的防水、防潮以及起重运输设备的检测、检验,严格控制生产工艺条件,强化安全管理工作,从以下6个方面采取防范措施防止高温熔融金属伤害事故的发生。
4.1防止熔融金属遇水爆炸4.1.1熔融金属生产、处置和贮存设施附近、运输线路及附近区域不得有积水,正上方不得存在滴、漏水隐患。
4.1.2 对原料、辅助材料严格检查,确保加入炉中的原料、辅助材料干燥无水。
4.1.3输送、转注熔融金属所使用的设备设施在输送、转注前须经充分干燥并保证畅通。
4.2熔融金属的安全吊运要求4.2.1吊运熔融金属应当采用带有固定龙门钩的冶金铸造起重机,司机室等高温作业岗位应当采取降温防护措施。
冶金铸造起重机每年应定期检测一次(对外报检)。
4.2.2起重机的吊具(钩)、钢丝绳、盛装熔融金属的容器(设备)的耳轴等应定期进行检测,凡耳轴出现内裂纹、壳体焊缝开裂、明显变形、耳轴磨损大于直径的10%、机械失灵、衬砖损坏超过规定,均应报修或报废。
4.2.3起重机应由经专门培训、考核合格的专职人员指挥,同一时刻只应一人指挥,指挥信号应符合要求。
吊运时应检查确认挂钩、脱钩可靠,方可通知司机起吊,起吊前应进行试重,人员应站在安全位置,并尽量远离起吊地点。
4.2.4吊运装有铁水、钢水、液渣的罐,应与邻近设备或建、构筑物保持大于1.5m的净空距离。
倾倒熔融金属时,容器(罐、包)周围4m内不可有非作业人员,防止熔融金属飞溅或洒落伤人。
4.2.5吊运的熔融金属液面应与盛装容器口保持至少300mm的距离。
铁水和钢水的密度

铁水和钢水的密度铁水和钢水是我们日常生活中常见的金属材料,它们具有重要的工业应用价值。
本文将从铁水和钢水的密度角度来探讨这两种金属材料的特点和应用。
我们先来了解一下铁水的密度。
铁水是指在高炉中冶炼出的含有铁的熔融金属,它的密度约为6.9克/立方厘米。
铁水具有较高的密度,这是由于铁的原子量较大,原子之间的排列比较紧密。
铁水的密度决定了其在重力作用下的重量,也是铁水在工业生产中的一项重要物理性质。
接下来,我们再来了解一下钢水的密度。
钢水是指含有碳元素的铁合金,它的密度约为7.8克/立方厘米。
相比铁水,钢水的密度稍大一些,这是由于钢中加入了碳等元素,使得钢的原子间距变小,密度增大。
钢水的密度也是钢材的一个重要特性,它决定了钢材的重量和物理性能。
铁水和钢水的密度不仅仅是一个物理性质,它还对工业生产和应用有着重要的影响。
首先,在钢铁冶炼过程中,根据铁水和钢水的密度差异,可以通过重力分离的方式将铁水和钢水进行分离。
这是基于密度差异的物理分离方法,可以有效提高冶炼效率和质量。
铁水和钢水的密度也对钢材的性能产生影响。
由于钢水的密度较大,所以在钢材冷却过程中,钢水会向下沉积,从而形成均匀的结晶组织。
这种均匀的结晶组织使得钢材具有较好的力学性能和工艺性能。
因此,在钢材的生产过程中,合理控制钢水的密度,能够提高钢材的质量和性能。
铁水和钢水的密度也对钢材的使用产生影响。
由于钢水的密度较大,所以在制造钢质构件时,需要考虑到钢水的重量和对结构的影响。
合理设计和使用钢质构件,可以充分利用钢水的密度优势,使得构件在承受载荷时具有较好的稳定性和安全性。
铁水和钢水的密度是决定其重量和物理性质的重要因素。
这两种金属材料在工业生产和应用中都有着重要的地位。
通过合理控制和利用铁水和钢水的密度特点,可以提高钢铁冶炼的效率和质量,提高钢材的质量和性能,同时也促进了钢材在工程领域的广泛应用。
铁水和钢水的密度是我们理解和应用这两种金属材料的基础,值得我们深入研究和探索。
铁水和钢水的密度

铁水和钢水的密度
铁水和钢水是钢铁生产过程中的两种重要物质,它们的密度是钢铁生产中的重要参数之一。
铁水和钢水的密度不同,这是由它们的成分和温度等因素决定的。
铁水是指在高炉中熔化的铁矿石和焦炭等原料经过还原反应后得到的液态铁。
铁水的密度一般在 6.9~7.2g/cm³之间,具体数值取决于铁水的成分和温度等因素。
铁水的成分主要包括铁、碳、硅、锰、磷等元素,其中铁的含量最高,占铁水总质量的大部分。
铁水的温度一般在1400℃左右,高炉内的铁水温度会随着高炉的操作变化而有所波动。
钢水是指在转炉、电炉等钢铁冶炼设备中熔化的铁水经过调质、脱碳等工艺处理后得到的液态钢。
钢水的密度一般在7.8~7.9g/cm³之间,比铁水要高。
这是因为钢水中的碳含量比铁水低,而碳是影响密度的重要因素之一。
钢水的成分除了铁、碳、硅、锰、磷等元素外,还包括钼、铬、镍、钴等合金元素,这些元素的含量和比例会影响钢水的性能和用途。
钢水的温度一般在1500℃左右,高温下钢水的流动性和稳定性都比铁水要好。
在钢铁生产中,铁水和钢水的密度是重要的物理参数,它们的密度不仅影响着钢铁的质量和性能,还会影响到钢铁生产的工艺和设备的设计。
因此,在钢铁生产中,需要对铁水和钢水的密度进行精确
的测量和控制,以确保钢铁的质量和生产效率。
铁水和钢水的密度

铁水和钢水的密度密度是物质的一种性质,用来描述物质的质量与体积之间的关系。
铁水和钢水作为常见的金属材料,其密度是研究和生产过程中重要的参数之一。
本文将介绍铁水和钢水的密度以及其相关知识。
一、铁水的密度铁水是指在高炉中炼铁过程中产生的液态铁。
铁水的密度是指单位体积铁水所含的质量。
根据不同的含碳量和温度,铁水的密度也会有所不同。
在高炉炼铁过程中,一般会得到熔融铁和炉渣两种物质。
熔融铁的密度通常为 6.8~7.2g/cm³,而炉渣的密度则相对较低,一般为2.5~3.0g/cm³。
铁水的密度受到多种因素的影响,其中最主要的因素是温度和成分。
在高温下,铁水的密度会随着温度的升高而减小,这是由于温度升高会使铁水的体积膨胀,从而导致密度降低。
而铁水的成分对密度的影响主要表现在不同元素的含量和相互作用上。
例如,含碳量较高的铁水密度较大,而含有氧化物等杂质的铁水密度则相对较小。
二、钢水的密度钢水是指含有一定碳量的铁水,在冶炼过程中通过调整成分和温度等参数来得到所需的钢种。
钢水的密度与铁水类似,也是指单位体积钢水所含的质量。
钢水的密度通常为7.8~7.9g/cm³,略高于熔融铁的密度。
这是因为钢水中含有较高的碳量和其他合金元素,使得钢水的密度相对较大。
钢水的密度同样受到温度和成分的影响。
随着温度的升高,钢水的密度会逐渐降低,这是由于高温下钢水的体积膨胀。
而钢水的成分对密度的影响主要表现在合金元素的含量和相互作用上。
不同种类的钢水由于合金元素的不同,其密度也会有所差异。
三、密度的应用密度是研究和生产过程中常用的参数之一,对于金属材料的加工和应用具有重要意义。
通过测定铁水和钢水的密度,可以准确地控制金属的成分和质量。
在冶炼和铸造过程中,通过测量密度可以判断金属的纯度和含杂情况,从而调整工艺参数,提高产品质量。
密度也是金属材料的重要物理性质之一,在材料选择和设计中起到重要的指导作用。
不同密度的金属具有不同的机械性能和热学性能,可以根据具体的应用要求选择合适的材料。
吨钢综合能耗计算公式

公式:
吨钢综合能耗 = 铁水熔解能耗 + 钢水冷却能耗 + 钢水转炉能耗 + 钢水转炉冷却能耗 + 钢水转炉热回收能耗 + 钢水再熔能耗
吨钢综合能耗计算公式:吨钢综合能耗=铁水熔解能耗+钢水冷却能耗+钢水转炉能耗+钢水转炉冷却能耗+钢水转炉热回收能耗+钢水再熔能耗
铁水熔解能耗:铁水熔解需要使用大量的能源,这部分能耗称为铁水熔解能耗。
钢水冷却能耗:钢水冷却需要使用大量的能源,这部分能耗称为钢水冷却能耗。
钢水转炉能耗:钢水转炉需要使用大量的能源,这部分能耗称为钢水转炉能耗。
钢水转炉冷却能耗:钢水转炉冷却需要使用大量的能源,这部分能耗称为钢水转炉冷却能耗。
钢水转炉热回收能耗:钢水转炉热回收需要使用大量的能源,这部分能耗称为钢水转炉热回收能耗。
钢水再熔能耗:钢水再熔需要使用大量的能源,这部分能耗称为钢水再熔能耗。
转炉炼钢物料平衡计算
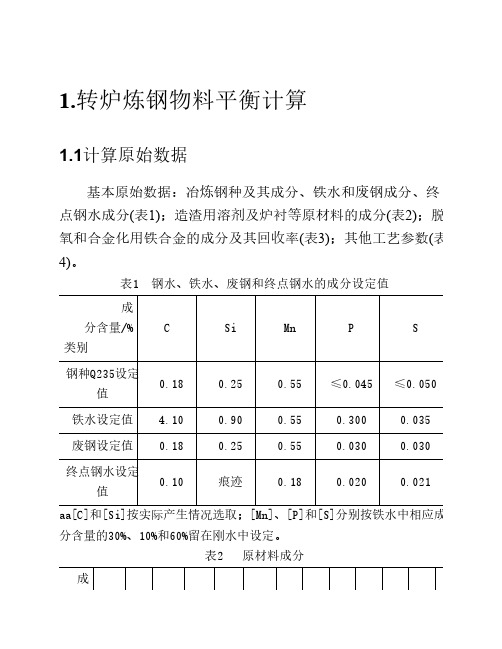
成
分/% CaO SiO2 MnO Al2O3 Fe2O3 CaF2 P2O5 S CO2 H2O C 灰分 挥发 类别
石灰 87.00 2.80 2.70 1.80 0.60
0.10 0.06 4.84 0.10
萤石 0.30 5.40 0.70 1.60 1.50 88.00 0.90 0.10 1.50
炉气总体积V∑: V∑=Vg+0.5%V∑+1/99×(22.4/32Gs+0.5%V∑-Vx) V∑==(99×8.375+0.7×8.155-
0.002×22.4/32)/98.50=8.475㎡ 式中 Vg—CO、CO2、SO2和H2O各组分总体积,m3。本计算中,
其值为: 8.677×22.4/28+2.729×22.4/44+0.010×22.4/64+ 0.016×22.4/18=8.375m3。
支出项有:钢水、炉渣、烟尘、渣中铁珠、炉气、喷溅。
1.3计算步骤
以100kg铁水为基础进行计算。
1.3.1计算脱氧和合金化前的总渣量及其成分
总渣量包括铁水中元素氧化,炉衬蚀损和加入溶剂的成渣
量。其各项成渣量分别列于表5-表7。总渣量及其成分如表8所
示。
表5 铁水中元素的氧化产物及其成渣量
元 反应产物 素
0.065②
81.93 16.70 0.05 0.24 0.5 0.6
合计
11.607
8.475
100.00
炉气中O2的体积为8.475×0.5%=0.042m³;质量为 0.042×32÷22.4=0.060kg。 炉气中N2的体积系炉气总体积与其他成分的体积之差;质量为 0.052×28÷22.4=0.065kg。
- 1、下载文档前请自行甄别文档内容的完整性,平台不提供额外的编辑、内容补充、找答案等附加服务。
- 2、"仅部分预览"的文档,不可在线预览部分如存在完整性等问题,可反馈申请退款(可完整预览的文档不适用该条件!)。
- 3、如文档侵犯您的权益,请联系客服反馈,我们会尽快为您处理(人工客服工作时间:9:00-18:30)。
钢水铁水
1、钢水温度与钢熔点温度之差。
比如钢熔点1400度,钢水温度为1410度,过热度即为10度。
2、过热度太小,钢水易被夹杂物污染,同时易使水口发生堵塞甚至冻结,在连铸开浇初期,中间包尚未“热透”时,此问题尤为突出;而过热太大,则使铸坯中心偏析加重,甚至诱发拉漏事故,或者因形成的坯壳较薄而出现裂纹,同时使柱状晶得到发展。
因此,控制过热度是保证连铸产量和铸坯质量的关键工艺参数之一。
3、以上各位所说的“铁水”,是按化学元素的“铁”定义的。
但在钢铁厂里所说的铁,和铁水都是指含碳量高的生铁,和生铁水。
“发现他们老在钢水里加入铁水”,你误解了!
炼钢工人是把含碳量高的铁水加到炼钢炉里,经过冶炼,按要求加入适当的合金成份,保留适当的碳,除掉多余的碳,和有害的杂质。
最后成为具有特定成份的钢
4、含碳量区别,严格地说,含碳量大于2.14%即为铁,小于2.14%即为钢,实际的钢生产中含碳量一般较低,为亚共析钢.
加入炉中的石灰等是为了脱磷\脱硫,其他合金应该是脱氧的作用和产品要求的成分.
5、铁水怎么会变成钢水呢??!!这门技术目前国际上还没有人能突破。
首先你要明白铁水和钢水的区别:钢是含碳量为0.03%~2%的铁碳合金,含碳量2%~4.3%的铁碳合金称生铁。
所以说你的题目出错啦!
只有“钢水能变成铁水”,而且还应在特定的条件下采取特定的手段。
目前我国只有几家公司能成功的利用工业纯废钢增碳技术把钢水变成铁水,这种手段能有效的控制铁液中的杂质元素和S、P含量,铁水很干净,而且成本较Q12生铁熔炼节省300~500元/吨。
6、冶炼195钢种为什么有钢水不流的现象
那就是所谓的高温套眼啊,也有叫做高温截流或者是流动性差的。
最主要的原因就是钢水里面氧和脱氧剂里面的铝形成了三氧化二铝的高熔点物质,而且在水口内壁上凝结,影响钢水的流动性,初期是拉速下降,时间长了就会造成中包因为钢水置换的太慢而形成低温,如果没有新的钢水置换的话就会造成停机。
我们这里主要冶炼195,也经常有这个问题的。
195这个钢种主要的问题就是碳低,造成钢水的含氧量高,脱氧的任务比较重,绝大多数的脱氧剂里面都含有铝,一旦脱氧剂加入量过多就会造成钢中的脱氧产物形态不好,不能形成大颗粒的脱氧产物,形成数量比较多的三氧化二铝,同时,有时候吹氩不到位,也会造成脱氧产物不能上浮,存在钢水里面。
另外,现在因为控制成本,195的成分控制的都是非常低的,合金成分低也是造成钢水流动性差的原因之一,对了,还有那个锰硅比低的话也会影响钢水的流动性。
想减少这个问题的话可以从一下几个方面入手。
一,提高操作水平,终点碳上限控制,从而减轻脱氧压力,减少脱氧剂的加入量。
二,使用复合脱氧剂,使用含有钙的脱氧剂,有利于钢水的脱氧产物
形成大颗粒,容易上浮。
三,提高合金的锰硅比,达到2.5以上,锰最好高一点,锰高有利于提高钢水的流动性。
四,加强吹氩,保证吹氩时间在8分钟以上,从而最大程度的使脱氧产物上浮。
五,保证温度,不能出低温。
六,一旦出现高温套眼,不要拖,如果后面有钢水,马上关大包,待中包液面下去之后再开浇下包钢水,如果在下一包出钢前面就知道已经套眼了,后面的钢水要高温才能把水口冲开。
如果这些条件都没有,可以采取钢水富氧的办法,就是在大包钢流上直接用氧气管吹,这样可以为事故的处理争取时间,可以争取不停机,从而把损失降低到最小程度。
这些是我一些经验,估计课本上也是学不全面的,希望对你有帮助
原因有三:一钢水过热度低,流动性不好;二脱氧不好,浇注过程二次生成高熔点化合物多;三钢水净化不好。