钢水流动性差分析研究与改进
浅谈高炉冶炼过程中铁水流动性差的原因及对策
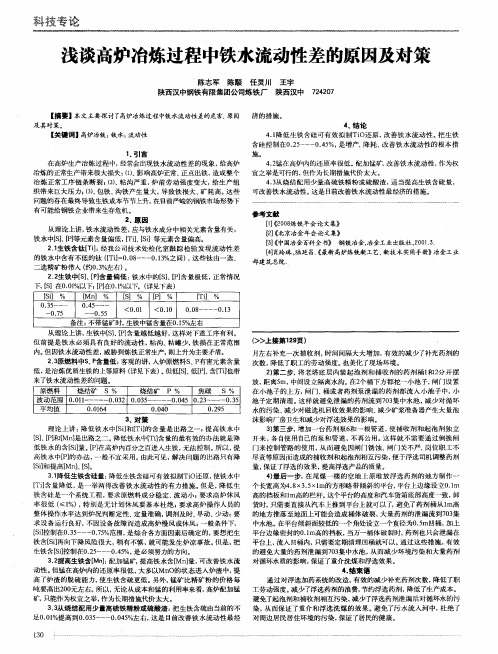
从 理论上讲 , 生铁 中【 s 】 、 [ P ] 含量越 低越好 , 这 样对下道工序 有利 。 >> . 上接 第1 2 9 页) 但前 提 是铁水 必须具 有 良好 的流动性 , 粘 沟、 粘罐少, 铁损在 正常范 围 ( 内。 但 因铁水流动性 差 , 威胁到炼铁 正常生产, 则上升为主要矛盾。 月左右 补充一次捕 收剂 , 时间 间隔大 大增加 , 有效 的减 少了补充药剂 的 2 . 3 原燃料 中s 、 P 含 量低 : 客观 的讲, 入炉原燃料S 、 P 有害元素 含量 次 数, 降低 了职 工的劳动强度 。 也美化了现场环境 。
的铁水 中含有 不低的钛 ( [ T i 】 =0 . 0 8 - - - 0 . 1 3 % 之 间) , 这些钛 由一选 、 部建筑总院. 二选 精矿粉 带入 ( 约0 . 3 % 左右) 。 2 . 2 生铁中[ [ P 】 含量 偏低 : 铁 水中的 【 s 】 、 【 P ] 含 量极低 , 正常情况 下, [ s ] 在0 . O 1 % 以下; [ P ] 在0 . 1 % 以] ( 详见下表 )
3 对 策 理 论上 讲 : 降低 铁 水中[ s i ] 和[ T i 】 的含 量是 出路 之一 ; 提 高铁 水 中 [ s ] 、 [ P 】 和【 Mn 】 是出路之二 。 降低 铁水中[ T i ] 含 量的最有效 的办法就 是降 低 铁水 的含【 S i ] 量。 [ P ] 在高炉 内百分之百进 入生铁 , 无法控制 。 所 以, 提 高铁 水 中[ P ] 的 办法 , 一般不宜采 用。 由此 可见 , 解 决问题 的出路只有降 【 S i 】 和提高 【 Mn ] 、 【 s ] 。 3 . 1 降低 生铁含硅量 : 降低生铁含硅可有效 拟f U T i O 还原, 使铁水 中
轴承钢GCrl5连铸钢水流动性差的原因和改进措施
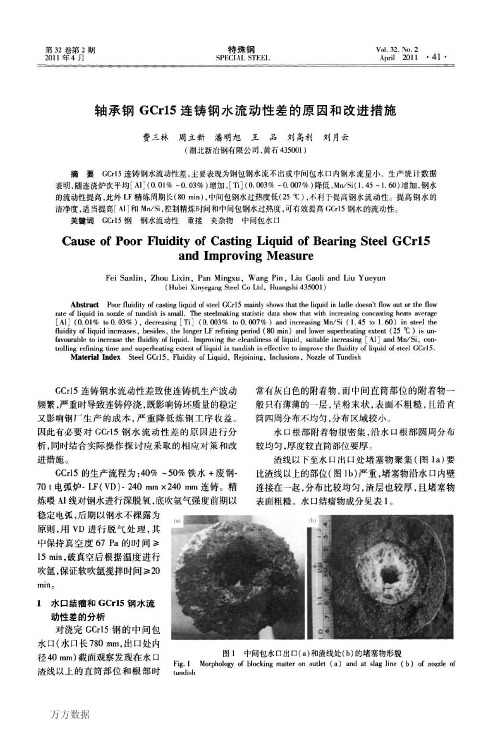
Jl
Zhuu Lixin,Pan Mingxu,Wang Pi..IJin GRail and I,iu Yueyun Co Ltd Huan95hi 435001) (Hubej
Xin)…Steel
uf sled refining
nk
7
ofliquid一…besid∞,IhlongerI,F favoaral31…t…th
小,阻碍钢流顺行,严重时将水口堵死u-。
2
T曲k
*Rt
2
3 4
2
啦2/%
0
Chemical~p蒯帅of∞ch
№
6 52
—
寰2围2各分析点的化学或分/%
analysis
GCrl5连铸钢水的重接特点
p枷m
《
100 00
2
1平均成品AI含量(T[AI])、Ti含量和Mn/Si
比对重接炉次的影响 图3(n)显示连浇炉次(一般连铸一次浇钢6~
The
sIeeI舳b%mall}“c
¨lfing
n洲m“liquid ImpmvingIhe eleanlin黜dliquid suitabLeine—ing【^l JⅫd M∥si,~ refiningtime¨djuperheafing—nI ufliquidintundlshis effectiveIoimpurethefluidit?ofliquid of sleel GC r15 MaterialI础x slw】cc【15 FLuidity of Liquid Rejoining.Inelu sions.№le of TurⅢI“
第32咎第2婀
特殊钢
Vol 32
Nu
2
2024年连铸结晶器钢水流动控制技术(四篇)
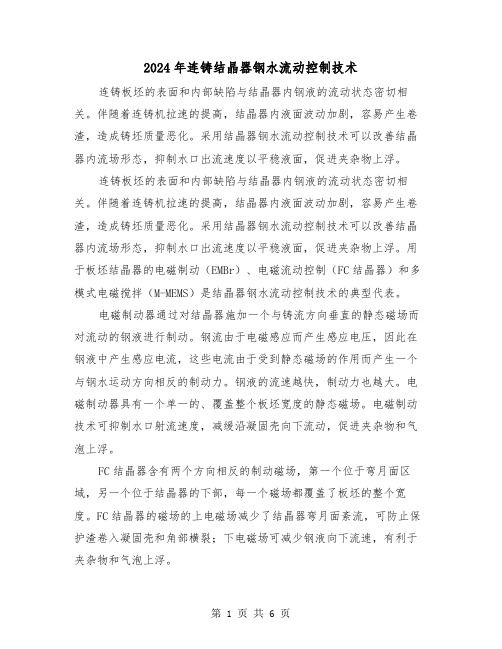
2024年连铸结晶器钢水流动控制技术连铸板坯的表面和内部缺陷与结晶器内钢液的流动状态密切相关。
伴随着连铸机拉速的提高,结晶器内液面波动加剧,容易产生卷渣,造成铸坯质量恶化。
采用结晶器钢水流动控制技术可以改善结晶器内流场形态,抑制水口出流速度以平稳液面,促进夹杂物上浮。
连铸板坯的表面和内部缺陷与结晶器内钢液的流动状态密切相关。
伴随着连铸机拉速的提高,结晶器内液面波动加剧,容易产生卷渣,造成铸坯质量恶化。
采用结晶器钢水流动控制技术可以改善结晶器内流场形态,抑制水口出流速度以平稳液面,促进夹杂物上浮。
用于板坯结晶器的电磁制动(EMBr)、电磁流动控制(FC结晶器)和多模式电磁搅拌(M-MEMS)是结晶器钢水流动控制技术的典型代表。
电磁制动器通过对结晶器施加一个与铸流方向垂直的静态磁场而对流动的钢液进行制动。
钢流由于电磁感应而产生感应电压,因此在钢液中产生感应电流,这些电流由于受到静态磁场的作用而产生一个与钢水运动方向相反的制动力。
钢液的流速越快,制动力也越大。
电磁制动器具有一个单一的、覆盖整个板坯宽度的静态磁场。
电磁制动技术可抑制水口射流速度,减缓沿凝固壳向下流动,促进夹杂物和气泡上浮。
FC结晶器含有两个方向相反的制动磁场,第一个位于弯月面区域,另一个位于结晶器的下部,每一个磁场都覆盖了板坯的整个宽度。
FC结晶器的磁场的上电磁场减少了结晶器弯月面紊流,可防止保护渣卷入凝固壳和角部横裂;下电磁场可减少钢液向下流速,有利于夹杂物和气泡上浮。
利用M-MEMS多模式电磁搅拌器可根据需要以不同的方式搅动结晶器内的钢水,显著减少板坯铸造缺陷。
该技术采用4个线性电磁搅拌器,位于结晶器高度方向的中部、浸入式水口两侧,每侧2个线圈并排设置,可用于使浸入式水口流出的钢水制动(EMIS)或加速(EMLA)。
第三种工作模式则用于使位于弯月面的钢水转动(EMRS),此项技术可有效控制热传导梯度和坯壳凝固前沿的均匀性,消除某些钢种存在的气孔、针孔和表面夹渣等铸造缺陷。
钢水絮流解决方法

钢水絮流解决方法全文共四篇示例,供读者参考第一篇示例:钢水絮流是一个常见的问题,它指的是钢水中存在大量的气泡或者固体颗粒,影响了钢水的质量和生产效率。
这种问题在钢铁生产中经常发生,需要及时有效的解决方法来保证生产的顺利进行。
本文将探讨钢水絮流的成因及解决方法,帮助生产厂家更好地解决这一难题。
一、钢水絮流的成因1. 原料质量不过关:原料中含有大量固体颗粒或者氧化物质,会导致在冶炼过程中产生絮流。
2. 冶炼工艺不当:冶炼过程中温度、流速、搅拌不均匀等因素都会影响钢水的品质,导致絮流问题的发生。
3. 设备老化损坏:冶炼设备长期使用容易受到损坏,这些损坏可能会导致钢水絮流的发生。
4. 操作不当:操作人员不熟练或者操作不规范也可能引起钢水絮流的问题。
以上几个方面是导致钢水絮流的常见原因,只有找到问题的根源才能找到解决问题的方法。
二、解决钢水絮流的方法1. 加强原料质量管理:要严格把关原料质量,选择优质原料,减少固体颗粒和杂质的含量。
3. 维护设备:定期检查冶炼设备的运行状态,及时维护和更换老化损坏的部件,确保设备的正常运行。
4. 培训操作人员:加强操作人员的培训和管理,使其熟练掌握操作技巧,规范操作流程,减少操作失误的发生。
5. 使用絮凝剂:在钢水中添加一定量的絮凝剂,可以促使气泡或者固体颗粒尽快聚集在一起,减少絮流的产生。
6. 排除气体:及时排除钢水中的气泡,可以通过提高搅拌强度或者采取其他气体排除措施来减少絮流。
7. 增加过滤设备:增加过滤设备,能够有效地过滤掉钢水中的固体颗粒,减少絮流的产生。
通过以上方法的综合应用,可以有效地解决钢水絮流的问题,提高钢水的质量和生产效率。
钢铁生产是一个复杂的过程,需要不断地改进和完善,才能够提高生产效率,降低生产成本,保证产品的质量。
在日常生产中,钢水絮流的问题是不可避免的,但只要我们用心去解决,总会找到有效的方法。
希望本文提到的解决方法对于解决钢水絮流问题有所帮助,让钢铁生产更加顺利和高效。
液相炼钢过程中钢液流动特性的模拟与优化

液相炼钢过程中钢液流动特性的模拟与优化摘要:本研究旨在模拟和优化液相炼钢过程中钢液的流动特性。
通过使用计算流体力学(CFD)方法,我们建立了一个钢液流动模型,并对其进行了数值模拟。
通过优化流动参数,如流速、温度和液相混合情况,我们改进了炼钢过程中钢液的流动性能。
模拟结果表明,优化后的流动条件可以提高钢液的混合效率和温度均匀性,从而提高产品质量和生产效率。
本研究为液相炼钢过程中的钢液流动特性提供了一种可行的模拟和优化方法。
关键词:液相炼钢,钢液流动,模拟,优化,计算流体力学引言:液相炼钢是现代钢铁工业中至关重要的过程之一。
钢液的流动特性对于产品质量和生产效率具有重要影响。
然而,传统的经验方法往往无法准确描述钢液的流动行为,因此需要借助模拟和优化方法来改进炼钢过程。
本文旨在利用计算流体力学(CFD)模拟技术,对液相炼钢过程中钢液的流动特性进行研究和优化。
通过合理的流动参数优化,我们可以提高钢液的混合效率和温度均匀性,从而提高产品质量和生产效率。
本研究将为液相炼钢过程中的钢液流动特性提供新的理论和实践指导,促进钢铁行业的发展。
一液相炼钢过程中钢液流动特性的数值模拟建模在液相炼钢过程中,钢液的流动特性对于产品质量和生产效率具有重要影响。
传统的经验方法难以准确描述钢液的流动行为,因此采用数值模拟建模成为一种有效的方法。
在本研究中,我们使用计算流体力学(CFD)方法建立了液相炼钢过程中钢液流动的数值模型。
(一)我们考虑了流动过程中的连续性方程和动量方程,以描述钢液的流动行为。
通过在模型中考虑液相的不可压缩性和牛顿流体的黏性特性,我们可以准确地捕捉钢液的流动现象。
(二)我们在模型中引入了热传导方程,以考虑液相炼钢过程中的温度变化。
通过在模型中考虑加热和冷却源以及边界条件,我们能够模拟钢液在炉内的温度分布和变化趋势。
在数值模拟建模过程中,我们需要对流动参数进行合理的设定。
流速、温度、液相混合等参数对钢液流动特性起着重要的影响。
炼钢厂钢水流动性问题探讨与实践
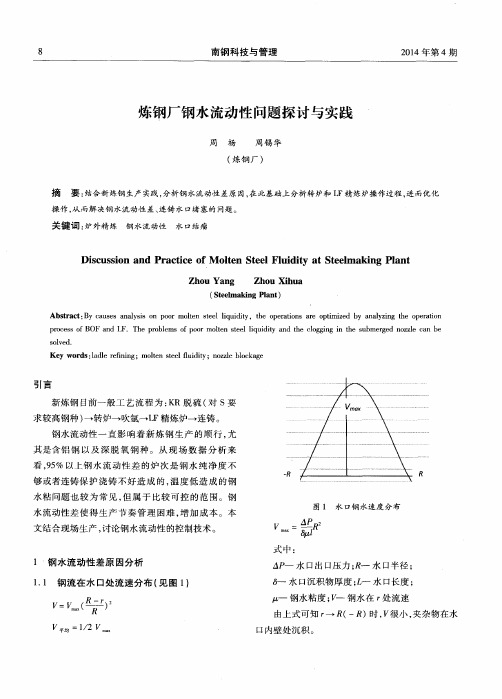
引起钢水流动性变差 的主要原 因是高熔 点 的脱 氧产物 ( 如A 1 : 0 , ) 在连铸过程 中先 于钢水 凝 固, 这些 固态脱氧产物凝 固沉积 于水 口内壁 使孑 L 径变 小 , 阻
碍钢流顺 行 , 严 重 时水 口甚 至完 全堵 死 , 导致 断 流 , 需 用吹氧管烧开水 口才能继 续生产 。 目前炼 钢厂产 品全部 为方矩坯 , 水 口较小 , 对水 口堵塞 敏感性 强 于 板坯 , 因此解 决 好钢 水流 动性 问题 对 于提 升炼 钢厂 产 品质量 、 产量 以及降低成本都有重大意义 。 水 口结瘤物 为复 合夹 杂物 与残 钢 的混 合 物 , 该 复相夹 杂物以纯 A 1 0 为 主体 。对 于水 口结瘤 一般
有 以下 两 种 原 因 :
化铝 夹杂 、 部 分铁 和铁 氧化 物堵 塞物 中 的氧化 铝和 铁 氧化物部 分发 生反 应 , 形 成高 熔点 的铁 铝尖 晶石 类等化合物 。
2 改 善钢水 流 动性 的措 施
结合 以上对 水 口堵塞 物 的分析 可知 , 影 响钢 水
流动性 的原 因 和机理 较清楚 , 它 与钢水 的成 分 以及 操作水平密切相关 : 成分 的合 理控制 , 有利 于钢 中形
一
钢水 粘 度 ;
钢水在 r 处 流 速
)
由上 式 可 知 卜 R( 一 )时 , V q t  ̄ &, 夹 杂 物 在 水
…
口内 壁 处沉 积 。
2 0 1 4年第 4期
1 . 2 钢 水流 动性 差 机理 分析
南钢 科技 与管 理
9
着过热钢液 的大量通 过 , 将 大 为缓解 这种 因凝 固造 成的堵塞。在渣线 以下部位 堵 塞较严 重 , 尤 其是 水
连铸钢水流动性差的原因及改进措施探讨

2010特钢年会论文集2010年10月连铸钢水流动性差的原因及改进措施探讨费三林潘明旭王品刘高利刘月云(湖北新冶钢有限公司,黄石435001)摘要:连铸钢水流动性差,主要表现为大包内钢水流不出或中包水口内的钢水流量小,究其原因,一是钢水温度不适宜,二是水口结瘤。
本文主要着手分析影响中包钢水流动性的结瘤物成分,弄清其来源,再结合实际生产,对造成适铸钢水流动性差的原因进行分析,并对如何采取相应的措施进行探讨。
关键词:钢水流动性重接夹杂物中间包水口The cause for poor fluidity of GCrl5liquid steel and corrective measure probeFE I S an.1in,PA N Ming·XU,WANG Pin,LI U Gao.1i,LIU Y ue-y un(H u be i Xinyegang St eel C o Ltd,Huan gshi435001)Abst rac t:t he poo r flui dity of ca st in g li quid steel mainly s ho w s that t he re is n o liqu id steel outflowing f r om l ad le furnace O r the flow rat e is small in tundish,which is caused by e ith er impr ope r liqu id steel t e m p e r a t u r e o r noz z l e c l o g g i ng.T h i s pape r i s f o c u s o n an al y s i n g the co mp o ne nt of n o d u la t i o n whic h a ffect t he li qu id steel f l ui di t y,a nd cle ar ifi ng its SOUrCe,thereafter analysing the c a u s e fo r p o o r fluidity of liqui d steel c o mb i ng a ct ua l p r o d u c t i on,a n d at las t study o n ho w to tak e measures is p ro ce ed ed.Key Words:FI_uidity of liquid,Rejoining,Inclusion,Tundish no z z l e1前言现实生产中经常发生因连铸钢水流动性差致使连铸机生产波动频繁,严重时导致连铸停浇,既影响铸坯质量的稳定又影响钢厂生产的成本,严重降低炼钢工序收益。
精炼钢水流动性差的原因分析与改进
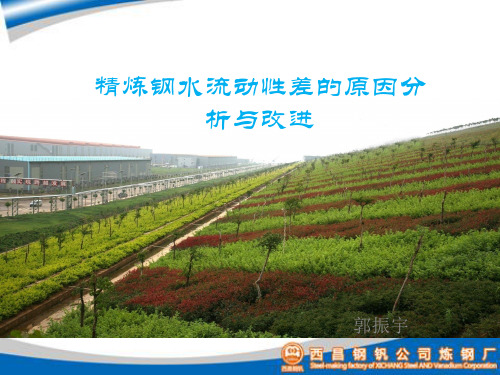
3、过程分析及解决办法
3.6 精炼喂钙线
解决办法
钢水中Al2O3变性成为12CaO〃7 Al2O3 夹杂的前提条件为[Ca]与[Al] 的比值在0.13~0.20。因此,需要根据钢水中[Al]含量的多少喂入相应的
钙线数量,而不是一味按钢种控制钙线喂入量。
3、过程分析及解决办法
3.7 强化钢水温度控制及铸机操作
转炉终点钢水
吹炼后期造渣剂的加入、终点温度和C含量等因素直接影响 钢水氧化性,因此要根据不同钢种的要求,最大限度地提 高出钢碳含量和控制出钢温度,降低钢水氧化性。
出钢过程控制
转炉渣为强氧化性炉渣,应严格控制出钢时的下渣量。 脱氧合金化过程控制
氧含量过高时
造成钢中[Al] 大量氧化的主 要原因,需严 格控制钢水终 点氧活度。
10~15℃为宜。 保证连铸大包-中间包、中间包液面、中间包-结晶器 保护浇注密封性,提高了精炼钢水流动性。
解决 办法
4、结论
结论一
通过强化转炉吹炼控制,降低钢水氧含量,改进精炼造渣、吹氩和喂线等 工艺操作,降低钢水中夹杂物,可以提高含铝钢水流动性。
结论二
严格控制中间包钢水温度,以高于液相线温度10~15℃为宜,从而保证铸 机的拉速,避免夹杂物在水口的聚集。
解 决
改进精炼造渣工艺,一方面根据钢种成分要求,采用碳粉、铝粒和SiC 进行前期快 速脱氧操作,控制渣中FeO<0.5%,形成流动性良好的白渣;另一方面采用新型预熔精
办
法
炼渣来促进炉渣熔化和调整炉渣成分,改进精炼渣吸附夹杂的能力,促进钢种的[O][N]
含量降低。
3、过程分析及解决办法
3.5精炼喂铝线
钢水温度对钢水流动性有双重影响,一方面温度高
轴承钢GCr15连铸钢水流动性差的原因和改进措施
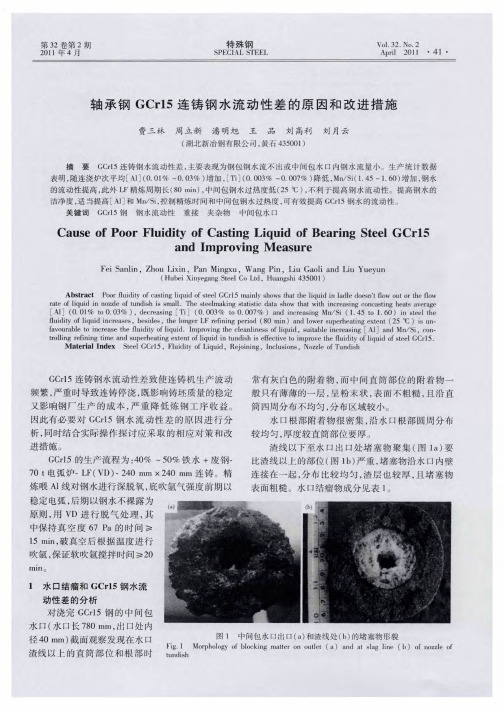
钢 随钢流加入 的活性 石灰 , 与钢 液进行 混 冲 , 出完钢 再调 整 A 气进 行搅 拌 ,昆冲 和 搅 拌 都 极 有 可 能 将 r ? C O卷 入 钢液 而滞 留其 中 ; 是精 炼 过程 中加入 的 a 二
活性石 灰 ( 3 与 钢 中的酸溶铝 反应 , 表 ) 生成 的 c a进
结合 以上 水 口氧 化物 的成分 分 析 和其来 源 , 认 为 G r5连铸 钢 水 流 动性 差 , 接 ( 浇 钢 手 柄 由 Cl 重 将
自动改 为手动 , 为增 大 钢水 流 量 以 冲刷 水 口壁 的 人
结 瘤物 , 改善 钢 水 的流 动 性 ) 繁 的直 接 原 因是 脱 频
物沉积 于水 口, 这两 部 分 氧化 物 聚 集碰 撞 形成 颗 粒
更大 的复合 夹 杂 物 ( 点依 然 很 高 ) 水 口孑 径 变 熔 使 L 小 , 碍钢流顺 行 , 重时将 水 口堵 死 。 阻 严
2 GC l r5连铸钢 水 的重 接特 点
so k i o ze E tc n n z l ,S M
在 钢液里 ¨ 。另外 一种 情 况就 是在 水 口区 随着 S 、 J i A 的析 出 , 氧气 反 应 生 成 氧 化 夹 杂 物 , 1 与 这两 部 分 夹杂 物在浇钢 的过 程 中向水 口壁迁 移 , 而在 水 口 从
内表 面沉积 。 ( ) a 。C O有 两个来 源 , 是 电弧 炉炉后 出 2 CO a 一
表 2 图 2各 分 析 点 的 化学 成 分 / %
Ta l b e2 Ch m ia o p st n o a h a a y i o n n e c l c m o ii f e c n l ss p i t i o F g 2 /% i.
连铸结晶器钢水流动控制技术范文

连铸结晶器钢水流动控制技术范文一、引言连铸结晶器是连铸过程中的核心设备之一,在钢水凝固过程中起着至关重要的作用。
钢水的流动控制技术对铸坯质量和生产效率具有重要影响。
本文将介绍连铸结晶器钢水流动控制技术的发展现状和研究进展。
二、连铸结晶器钢水流动的基本原理连铸结晶器钢水流动的基本原理是通过控制钢水的流动速度和流动方向来控制结晶器内的温度场分布和结晶器壁面温度。
钢水的流动速度和流动方向影响了结晶器内的温度分布,进而影响了铸坯的凝固过程和凝固组织的形成。
三、连铸结晶器钢水流动控制技术的分类连铸结晶器钢水流动控制技术可分为机械控制技术和流场控制技术两大类。
1. 机械控制技术机械控制技术主要通过调整结晶器内的导流板、转轴和转子等机械装置来改变钢水的流动速度和流动方向。
通过改变机械装置的结构参数和运行参数来实现流动控制。
2. 流场控制技术流场控制技术主要通过改变结晶器内的钢水流动状态来实现流动控制。
主要包括利用激振器产生的振动力改变钢水流动状态,利用电磁场改变钢水流动状态,以及利用气体喷射改变钢水流动状态等。
四、连铸结晶器钢水流动控制技术的研究进展1. 机械控制技术的研究进展机械控制技术主要包括导流板的设计和优化、转轴和转子的结构设计等方面。
近年来,研究者通过数值模拟和实验研究等手段,对机械控制技术进行了深入研究。
通过优化导流板的形状和位置,可以改变钢水的流动速度和流动方向,进而改善结晶器内的温度分布和凝固组织形成。
2. 流场控制技术的研究进展流场控制技术的研究主要集中在利用激振器、电磁场和气体喷射等手段改变钢水流动状态的方法上。
研究者通过对结晶器内流场的数值模拟和实验研究,探索了不同流场控制方法对钢水流动的影响。
研究结果表明,适当的振动力、电磁场和气体喷射等手段可以改变钢水的流动状态,进一步优化铸坯的凝固过程和凝固组织形成。
3. 综合控制技术的研究进展综合控制技术是机械控制技术和流场控制技术的结合,旨在通过相互协调和优化,实现更好的流动控制效果。
钢水絮流解决方法

钢水絮流解决方法全文共四篇示例,供读者参考第一篇示例:钢水絮流是钢铁冶炼过程中常见的问题,造成不良影响的情况也屡见不鲜。
要解决钢水絮流问题,需要在加强管理、优化工艺等方面下功夫。
本文将详细介绍钢水絮流的成因及解决方法,希望为解决这一问题提供一些参考。
一、钢水絮流的成因1. 温度梯度大:在冶炼过程中,钢水的温度会随着时间和空间的变化而发生变化。
当温度梯度过大时,易造成结晶沉淀现象,从而导致絮状物沉积在钢水中。
2. 不洁净的饱和剂:在冶炼中加入的饱和剂,如果不洁净或含有杂质,会加剧絮状物的生成。
这些杂质会促使絮状物的形成和积聚。
3. 高速浇铸:在高速浇铸的过程中,钢水因受到快速冷却的作用,易形成絮状物。
这些絮状物会随着钢水流动,沉积在浇铸件表面,导致表面质量下降。
4. 浇注温度不稳定:在浇注过程中,如果温度不稳定或波动过大,容易造成絮状物的形成。
这些絮状物会污染钢水,降低钢水的质量。
以上是钢水絮流的成因,下面将介绍钢水絮流的解决方法。
二、钢水絮流的解决方法1. 控制温度梯度:在钢水冶炼过程中,要尽量减小温度梯度,使钢水的温度保持稳定。
可以采取措施,如加热均匀、控制浇铸速度等,减少絮状物的生成。
2. 优化饱和剂的选择:选择洁净的饱和剂,避免使用含有杂质的饱和剂。
对饱和剂进行筛选和检查,确保其质量优良,避免带来絮状物的形成。
3. 控制浇铸速度:在进行钢水浇铸时,要控制浇铸速度,避免过快的浇铸速度造成钢水急速冷却,导致絮状物的生成。
要根据具体情况,合理控制浇铸速度,保持适宜的温度。
4. 稳定浇注温度:在进行浇注过程中,要保持浇注温度的稳定。
可以采取措施,如加热设备的调节、监测工艺参数等,确保钢水的温度稳定,避免温度的波动造成絮状物的形成。
以上内容是关于钢水絮流的成因和解决方法,希望对解决这一问题有所帮助。
只要我们在冶炼过程中严格控制各项参数,优化工艺流程,相信钢水絮流问题能够得到有效解决,提高钢水质量,确保生产的顺利进行。
连铸机钢水流动性差的原因分析与改进
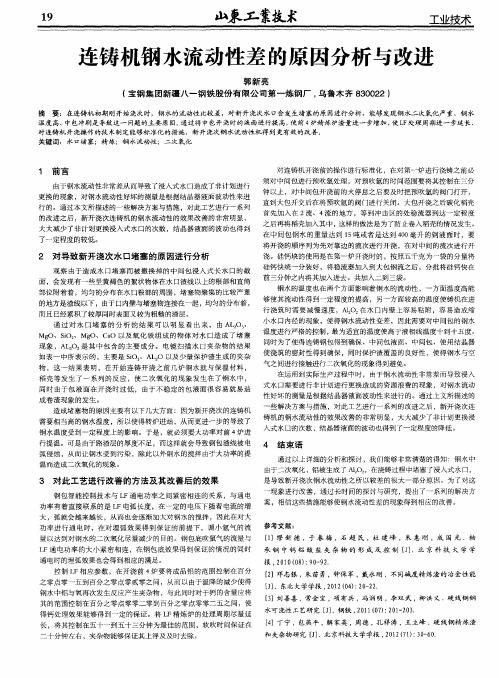
行提温 。可是 由于路渣层 的厚度不足 ,而这样就会导致钢包渣线被 电 4 结束 语 弧侵蚀 ,从而让 钢水 受到污染 ,除此 以外钢水 的搅拌 由于大 功率的提 通过 以上详 细的分析 和探讨 ,我们能够非常清 楚的得 知 :钢水中 温而造成二次氧化的现象 。 由于二次氧化 ,铝被生成 了 A l 0 ,在浇铸过程 中堵塞 了浸入式水 口,
同时为了使得连铸钢包得 到确保 、中间包液面、中 间包 、使用结 晶器
如 表一 中所表 示的 ,主要 是 S i O 、A L o 以及少量保护渣 生成的夹杂 物 ,这 一结果 表 明,在开始 连铸 开浇之 前几 炉钢水就 与保 温材料 , 稻壳等 发生 了一 系列的反 应 ,使 二次氧 化的 现象发 生在 了钢水 中 , 同时 由于包 液面在 开浇 时过低 ,由于不稳 定 的包 液面 很容易 就易造
Mg O、S i O 、Mg O、Ca O 以及氧 化铁 组成 的物体 对 水 口造成 了堵塞 现 象 ,AL o 是其 中包含 的 主要成 分 。电镜 扫描水 口夹 杂物 的结果
前三分钟之 内将其加入进去 。共加入二到三袋 。 钢水 的温度也在两个方面影 响着钢 水的流动性 ,一方面温度 高能
的改进之 后 ,新开浇次连铸机的钢水流动性 的效 果改善的非常 明显 ,
大大减 少了非计划更换浸入式水 口的次数 ,结晶器液面的波动也得到
了一定程度的较低 。
在 中 间包 钢水 的重量达 到 1 5吨或 者是达 到 4 0 0 毫升 的钢液 面时 ,要
将开 浇的顺序列为先对靠边 的流 次进行 开浇 ,在对中间的流次进行开 浇 。硅钙块 的使用是在第一炉开浇 时的,按 照五千 克为一袋的分量将 硅钙 快统 一分装好 ,将稳流器加入到大包钢 流之后 ,分批将硅钙快在
连铸机钢水流动性差的原因分析与改进
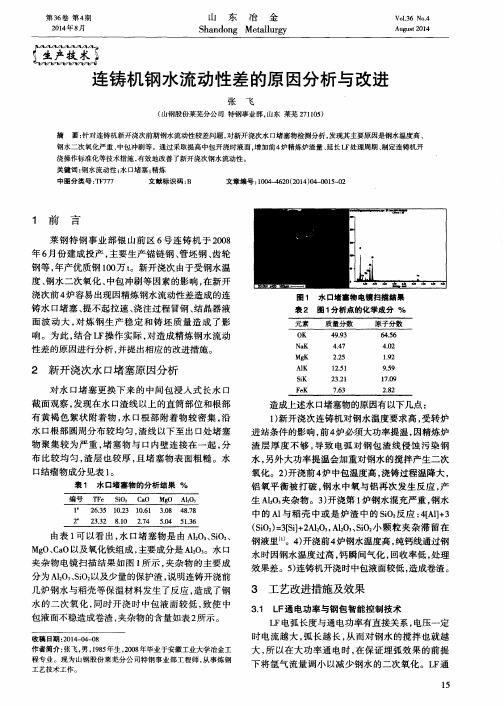
由表 1 可 以看 出 , 水 口堵 塞 物 是 由 A 1 : 0 、 S i O : 、 Mg O、 C a O以及 氧化铁 组成 , 主要 成分是 A 1 O 。水 口 夹 杂 物 电镜 扫 描结 果 如 图 1 所示 , 夹 杂 物 的主 要成
分为A 1 : O 、 S i O 以及少量的保护渣 , 说 明连铸开浇前 几炉钢水与稻壳等保温材料发生了反应 , 造成 了钢
渣 层厚度不够 , 导 致 电弧 对 钢 包 渣 线 侵 蚀 污 染 钢
物 聚集 较 为严 重 , 堵 塞 物 与 口内壁 连接 在 一 起 , 分 布 比较 均 匀 , 渣 层 也 较厚 , 且 堵 塞物 表 面 粗 糙 。水
口结瘤 物成分见 表 1 。
表1 水 口 堵 塞 物 的 分 析 结 果 %
( S i O 2 ) = 3 [ S i ] + 2 A 1 0 , , A 1 0 , 、 S i O : 小颗粒夹杂滞 留在
钢 液里 [ 1 ] 。4 ) 开浇 前 4 炉钢水 温度 高 , 纯钙线 通过钢 水时 因钢 水温 度过 高 , 钙 瞬间气 化 , 回收 率低 , 处 理 效果差 。5 ) 连铸 机开浇 时 中包液 面较低 , 造 成卷渣 。
钢等 , 年产优质钢 1 0 0 万t 。新开浇次 由于受钢水温
度、 钢 水二 次 氧化 、 中包 冲刷 等 因素 的影 响 , 在 新开 浇 次前 4 炉容 易 出现 因精 炼钢 水流 动性差 造成 的连 铸 水 口堵 塞 、 提不 起拉 速 、 浇注 过 程 冒钢 、 结 晶器液
面波动大 , 对 炼 钢 生 产 稳 定 和 铸 坯 质 量 造 成 了影
3 工艺改 进措施 及效果
3 . 1 L F 通 电功 率与钢包 智能控 制技术
连铸机钢水流动性差的原因分析与改进
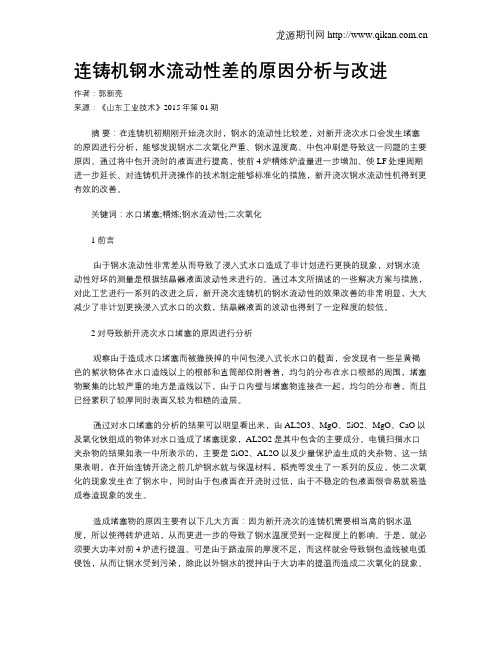
连铸机钢水流动性差的原因分析与改进作者:郭新亮来源:《山东工业技术》2015年第01期摘要:在连铸机初期刚开始浇次时,钢水的流动性比较差,对新开浇次水口会发生堵塞的原因进行分析,能够发现钢水二次氧化严重、钢水温度高、中包冲刷是导致这一问题的主要原因。
通过将中包开浇时的液面进行提高,使前4炉精炼炉渣量进一步增加、使LF处理周期进一步延长、对连铸机开浇操作的技术制定能够标准化的措施,新开浇次钢水流动性机得到更有效的改善。
关键词:水口堵塞;精炼;钢水流动性;二次氧化1 前言由于钢水流动性非常差从而导致了浸入式水口造成了非计划进行更换的现象,对钢水流动性好坏的测量是根据结晶器液面波动性来进行的。
通过本文所描述的一些解决方案与措施,对此工艺进行一系列的改进之后,新开浇次连铸机的钢水流动性的效果改善的非常明显,大大减少了非计划更换浸入式水口的次数,结晶器液面的波动也得到了一定程度的较低。
2 对导致新开浇次水口堵塞的原因进行分析观察由于造成水口堵塞而被撤换掉的中间包浸入式长水口的截面,会发现有一些呈黄褐色的絮状物体在水口渣线以上的根部和直筒部位附着着,均匀的分布在水口根部的周围,堵塞物聚集的比较严重的地方是渣线以下,由于口内壁与堵塞物连接在一起,均匀的分布着,而且已经累积了较厚同时表面又较为粗糙的渣层。
通过对水口堵塞的分析的结果可以明显看出来,由AL2O3、MgO、SiO2、MgO、CaO以及氧化铁组成的物体对水口造成了堵塞现象,AL2O2是其中包含的主要成分。
电镜扫描水口夹杂物的结果如表一中所表示的,主要是SiO2、AL2O以及少量保护渣生成的夹杂物,这一结果表明,在开始连铸开浇之前几炉钢水就与保温材料,稻壳等发生了一系列的反应,使二次氧化的现象发生在了钢水中,同时由于包液面在开浇时过低,由于不稳定的包液面很容易就易造成卷渣现象的发生。
造成堵塞物的原因主要有以下几大方面:因为新开浇次的连铸机需要相当高的钢水温度,所以使得转炉进站,从而更进一步的导致了钢水温度受到一定程度上的影响。
宁钢浇注过程钢包钢水流动性研究
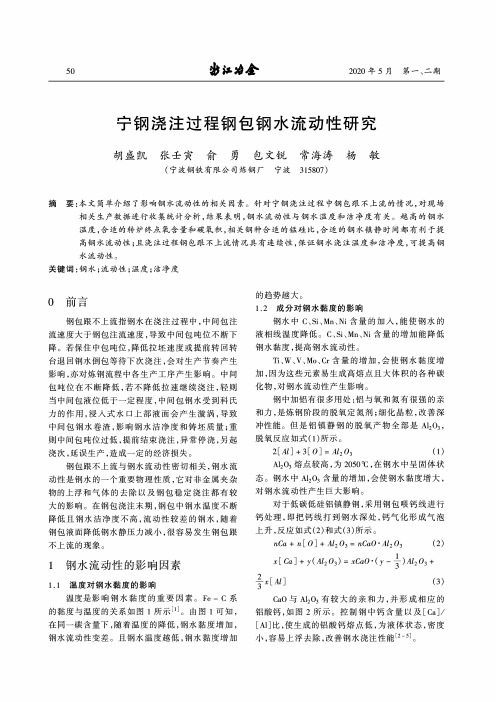
宁钢浇注过程钢包钢水流动性研究胡盛凯张壬寅俞勇包文锐常海涛杨敏(宁波钢铁有限公司炼钢厂宁波315807)摘要:本文简单介绍了影响钢水流动性的相关因素。
针对宁钢浇注过程中钢包跟不上流的情况,对现场相关生产数据进行收集统计分析,结果表明,钢水流动性与钢水温度和洁净度有关。
越高的钢水温度,合适的转炉终点氧含量和碳氧积,相关钢种合适的镒硅比,合适的钢水镇静时间都有利于提高钢水流动性;且浇注过程钢包跟不上流情况具有连续性,保证钢水浇注温度和洁净度,可提高钢水流动性。
关键词:钢水;流动性;温度;洁净度0前言钢包跟不上流指钢水在浇注过程中,中间包注流速度大于钢包注流速度,导致中间包吨位不断下降。
若保住中包吨位,降低拉坯速度或提前转回转台退回钢水倒包等待下次浇注,会对生产节奏产生影响,亦对炼钢流程中各生产工序产生影响。
中间包吨位在不断降低,若不降低拉速继续浇注,轻则当中间包液位低于一定程度,中间包钢水受到科氏力的作用,浸入式水口上部液面会产生漩涡,导致中间包钢水卷渣,影响钢水洁净度和铸坯质量;重则中间包吨位过低,提前结束浇注,异常停浇,另起浇次,延误生产,造成一定的经济损失。
钢包跟不上流与钢水流动性密切相关,钢水流动性是钢水的一个重要物理性质,它对非金属夹杂物的上浮和气体的去除以及钢包稳定浇注都有较大的影响。
在钢包浇注末期,钢包中钢水温度不断降低且钢水洁净度不高,流动性较差的钢水,随着钢包液面降低钢水静压力减小,很容易发生钢包跟不上流的现象。
1钢水流动性的影响因素1.1温度对钢水黏度的影响温度是影响钢水黏度的重要因素。
Fe-C系的黏度与温度的关系如图1所示⑴。
由图1可知,在同一碳含量下,随着温度的降低,钢水黏度增加,钢水流动性变差。
且钢水温度越低,钢水黏度增加的趋势越大。
1.2成分对钢水黏度的影响钢水中C、Si、Mn、Ni含量的加入,能使钢水的液相线温度降低。
C、Si、Mn、Ni含量的增加能降低钢水黏度,提高钢水流动性。
炼钢过程中钢水凝固方法的改进
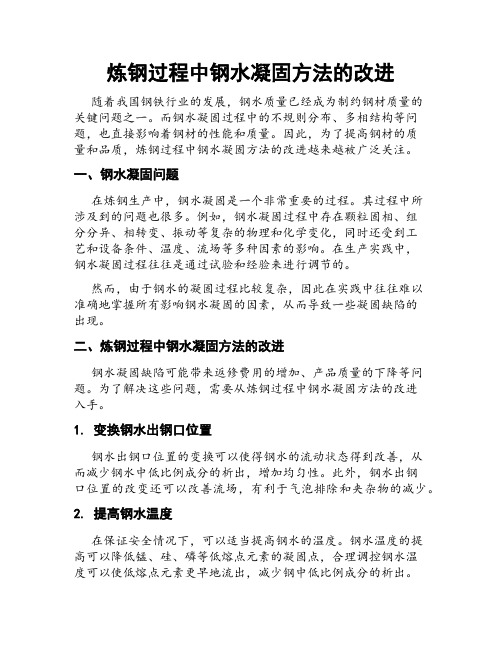
炼钢过程中钢水凝固方法的改进随着我国钢铁行业的发展,钢水质量已经成为制约钢材质量的关键问题之一。
而钢水凝固过程中的不规则分布、多相结构等问题,也直接影响着钢材的性能和质量。
因此,为了提高钢材的质量和品质,炼钢过程中钢水凝固方法的改进越来越被广泛关注。
一、钢水凝固问题在炼钢生产中,钢水凝固是一个非常重要的过程。
其过程中所涉及到的问题也很多。
例如,钢水凝固过程中存在颗粒固相、组分分异、相转变、振动等复杂的物理和化学变化,同时还受到工艺和设备条件、温度、流场等多种因素的影响。
在生产实践中,钢水凝固过程往往是通过试验和经验来进行调节的。
然而,由于钢水的凝固过程比较复杂,因此在实践中往往难以准确地掌握所有影响钢水凝固的因素,从而导致一些凝固缺陷的出现。
二、炼钢过程中钢水凝固方法的改进钢水凝固缺陷可能带来返修费用的增加、产品质量的下降等问题。
为了解决这些问题,需要从炼钢过程中钢水凝固方法的改进入手。
1. 变换钢水出钢口位置钢水出钢口位置的变换可以使得钢水的流动状态得到改善,从而减少钢水中低比例成分的析出,增加均匀性。
此外,钢水出钢口位置的改变还可以改善流场,有利于气泡排除和夹杂物的减少。
2. 提高钢水温度在保证安全情况下,可以适当提高钢水的温度。
钢水温度的提高可以降低锰、硅、磷等低熔点元素的凝固点,合理调控钢水温度可以使低熔点元素更早地流出,减少钢中低比例成分的析出。
3. 降低钢水凝固速度降低钢水凝固速度可以缓解钢水凝固过程中分异问题的出现,从而提高钢材的品质。
同时,对于高锰钢、高硅钢等低柔韧性、高硬度的钢类,降低钢水凝固速度也可以减少细晶铁的析出,提高钢材的韧性。
4. 应用电磁搅拌技术电磁搅拌技术作为一种新型炼钢技术,它可以改善钢水中的流动状态,从而提高钢水的均匀性。
在电磁搅拌的作用下,可以消除钢水中的气泡,遏制钢水流动中的湍流和漩涡等,这样可以使钢中低比例成分的析出减少,从而提高钢材的品质。
5. 液相反应炼钢法液相反应炼钢法是最近几年研究的新型炼钢技术。
提高钢水质量反思

提高钢水质量反思
钢水质量的提高是一个多方面的问题,需要从生产工艺、原材料选择、设备维护等方面进行反思和改进。
以下是一些可能的反思方向:
1. 生产工艺的改进:在生产过程中,需要对炉温、氧气供应、冶炼时间等各项参数进行精细调控,确保炉内温度均匀,氧气供应充足,炼钢时间适宜,以确保钢水的化学成分和温度达到标准要求。
2. 原材料选择的改进:选择合适数量的优质原料,如高品质的铁矿石、煤炭和合金等,以确保钢水的成分和纯度符合要求。
3. 设备维护的改进:定期进行设备的检修和维护,确保设备的稳定运行和准确度,减少设备故障对钢水质量的可能影响。
4. 人员素质和管理的改进:提高工人的技能和质量意识,加强对工艺的管理和监控,确保生产过程中的操作规范和流程的合理性。
5. 检测手段和质量控制的改进:引入先进的检测手段,如在线实时监测仪器和设备,提高对钢水质量的监控和控制能力,及时发现和纠正问题。
6. 环境保护和资源循环利用的改进:采用节能环保的生产工艺,减少对环境的污染,同时,对废渣、废水等进行科学处理和资源回收利用,实现可持续发展。
总之,提高钢水质量需要从多个方面进行反思和改进,充分考虑各个环节对钢水质量的影响,并采取相应的措施加以改进。
- 1、下载文档前请自行甄别文档内容的完整性,平台不提供额外的编辑、内容补充、找答案等附加服务。
- 2、"仅部分预览"的文档,不可在线预览部分如存在完整性等问题,可反馈申请退款(可完整预览的文档不适用该条件!)。
- 3、如文档侵犯您的权益,请联系客服反馈,我们会尽快为您处理(人工客服工作时间:9:00-18:30)。
钢水流动性差的原因分析及改进原因:LF炉精炼钢水粘的主要原因是由于精炼过程中或钢水浇注过程中钢水中铝氧化,由于钢水中存在大量尖锐、带刺状且熔点较高的A12O3夹杂,容易在浇注过程中粘附到水口内壁上,从而逐渐堵塞水口,造成钢水流动性变差,即钢水粘现象。
生产实际中大多采用钙处理控制铝脱氧产物在炼钢连铸温度下呈液态,促进铝夹杂物上浮。
铝夹杂物组成随着钙含量增加按以下顺序变化:A12O3一CaO•6A12O3一CaO•A12O3一CaO•A12O3—12CaO•7A12O3—3CaO•A12O3—CaO当夹杂物成分位于CaO•A12O3,12CaO•7A12O3和3CaO•A12O3的低熔点区域时,在浇铸温度下,钙铝酸盐类夹杂物在钢水中以液相存在。
另一方面,钙的加入量过多,形成高熔点的CaS(熔点为2450℃),此时同样会恶化钢水的浇铸性能。
生产含铝钢时随着钢中铝含量的增加,氧的活度降低,有利于硫化物的形成;随着钢中硫含量的增加,有利于形成高熔点的CaS;钢水温度降低时,氧的活度降低,也有利于CaS的形成,影响钢水流动性。
具体地说,LF 精炼钢水流动性差的主要原因是在精炼或浇注过程中钢水中的[Al]氧化,生成大量尖锐、带刺状且熔点较高的Al2O3夹杂,在浇注过程中粘附到水口内壁上,堵塞水口,造成钢水流动性变差。
在生产实际中,常规做法是采用钙处理的方式,使铝脱氧产物呈液态,促进铝夹杂物上浮。
铝夹杂物组成随着钙含量增加呈以下变化形态:Al2O3—CaO·6Al2O3—CaO·2Al2O3—CaO·Al2O3—12CaO·7Al2O3—3CaO·Al2O3—CaO。
当夹杂物成分位于CaO·Al2O3、12CaO·7Al2O3和3CaO·Al2O3的低熔点区域时,在适当的浇铸温度下,钙铝酸盐类夹杂物在钢水中以液相存在。
若钙的加入量过多,易形成高熔点CaS(熔点为2 450 ℃),会恶化钢水的流动性。
生产含铝精炼钢种时,随着[Al]含量的增加,氧的活度呈降低趋势,有利于硫化物的形成;随着硫含量的增加,易形成高熔点的CaS。
钢水温度降低时,氧的活度降低也有利于CaS的形成,从而影响钢水的流动性。
采取措施:总:严格控制好钢水成分。
如Al、Ti、Si等易氧化元素,在保证产品性能的前提下,应尽可能减少其含量;尽量提高Mn/Si、Mn/S比;炼钢脱氧尽量采用复合脱氧剂。
(2)严格做好保护浇注,防止钢水二次氧化。
(3)控制合适的钢水温度。
(4)净化钢液。
可以采取炉外精炼、塞棒吹氩、中间包加过滤器等措施。
1 控制转炉钢水氧化性转炉终点钢水含氧量过高是造成钢中[Al]大量氧化的主要原因,需严格控制终点钢水的氧化性。
1)吹炼过程控制:吹炼后期造渣剂的加入、终点温度和C 含量等因素直接影响钢水氧化性,因此要根据不同钢种的要求,最大限度地提高出钢C 含量和控制出钢温度,降低钢水氧化性。
2)出钢过程控制:转炉渣为强氧化性炉渣,应严格控制出钢时的下渣量。
3)脱氧合金化过程控制:脱氧合金化过程对钢水中氧含量起着决定性作用,应强化精炼钢种终脱氧,适当增加终脱氧剂用量,同时脱氧合金化过程严格按规程操作。
2 出钢顶渣加入工艺的改进提高钢水流动性,促进精炼钢水夹杂物上浮吸收的前提是造好低氧化性、碱度适合的精炼渣,精炼渣要求有良好的流动性和发泡能力及适宜的渣量。
在原转炉造渣料称量加料系统基础上,新增了部分管路和料仓,利用转炉造渣料加入系统来完成精炼顶渣剂的加入,解决了原顶渣加入工艺加入时间集中、且不宜熔融的弊端。
具体操作是:生产精炼钢种时,在吹炼过程中按照钢种成分和质量要求,提前设定好顶渣剂(石灰等)加入量,并将称量好的顶渣剂放至石灰下料仓,出钢过程中操作炉后放料插板阀将顶渣剂放入钢包,同时加入部分萤石以保证化渣质量。
由于实现了提前称量、储运并自动加料,保证了出钢过程中顶渣剂及时加入,并能够在钢水搅拌作用下促进顶渣及时熔化,促进钢水脱氧合金化过程夹杂物的及时上浮。
3 出钢挡渣工艺改进依靠人工投掷挡渣球,极易造成挡渣球定位不准,挡渣效果不理想,钢包下渣量大。
氧化性炉渣对钢水中合金成分氧化严重,导致钢水成分不稳定,合金收得率低,钢水中夹杂物含量高,影响到钢水纯净度和钢水流动性。
为此,经过反复试验,设计出转炉出钢简易定位投掷挡渣装置。
在出钢后期利用由支架和推杆组成的定位投掷挡渣装置将挡渣球加入,使挡渣球定位于出钢口上方。
从实际应用情况看,采用挡渣球定位投掷挡渣工艺后,钢包下渣量平均降低约100 kg 左右,减少了钢水中铝的氧化,提高了钢水流动性。
同时挡渣成功率提高至98%,避免了因出钢下渣量过大造成的钢包回磷现象,确保了钢水成分的稳定。
4 出钢吹氩工艺改进采取出钢过程顶渣加入工艺,一方面是为缩短钢水的精炼周期,使之与铸机浇铸时间相匹配,另一方面是为缩短造渣剂熔融时间。
为避免在出钢过程中加入顶渣剂易造成结块及包裹合金现象,顶渣剂的加入时间需在合金加完之后。
由于整个出钢过程时间较短,加入顶渣剂后时间所剩不多,造成顶渣剂熔融效果不好而堆积在钢包表面,起不到提前化渣的效果。
另外,由于顶渣堆积后结壳,在精炼过程进行吹氩操作时钢水无法正常翻动,加之提温操作时电极下探时极易折断,达不到顶渣剂预先加入的效果。
为解决这些问题,对钢水出钢吹氩工艺进行进,吹氩控制由静态变为动态,即根据钢包内钢水量及渣量的多少,在出钢及钢水转运过程中采用变氩气流量控制操作,通过提高吹氩效果来控制LF 顶渣化渣效果,间接提高钢水流动性及精炼效果。
5 精炼造渣工艺改进提高精炼钢水流动性的根本是降低钢水中夹杂物特别是Al2O3夹杂物的含量,包括减少精炼过程夹杂物的生成和促进钢水中夹杂物的上浮吸收。
LF 钢水精炼过程主要是钢水和还原性顶渣反应的过程,因此要求精炼渣具有高碱度、低氧化性、低熔点的特点,具有进一步脱硫和脱氧吸附夹杂的能力;而转炉炉渣FeO 含量一般在15%~20%,氧化性较强,必须采取快速还原造渣工艺,减少钢水和炉渣中氧含量。
为此,改进精炼造渣工艺,一方面根据钢种成分要求,采用碳粉、铝粒和SiC 进行前期快速脱氧操作,控制渣中FeO<0.5%,形成流动性良好的白渣;另一方面采用新型预熔精炼渣来促进炉渣熔化和调整炉渣成分,改进精炼渣吸附夹杂能力,促进钢中的[O]、[N]含量降低。
由于采用高碱度预熔精炼渣生产工艺,精炼渣化渣速度较快,缩短了精炼时间,提高了LF精炼炉生产率。
6 精炼吹氩过程工艺改进氩气的精炼去夹杂效果与耗氩量、吹氩压力、氩流量、处理时间及气泡大小等因素有关。
当吹氩量偏低时,相应限制了氩气的精炼作用,大部分只起到搅拌作用,从而使氩气的脱氧、去气、去夹杂和保护钢水等作用得不到充分发挥。
当氩气压力大时,搅动力也大,气泡上升速度快,但氩气流涉及到的范围趋于减少,甚至出现破裂致使氩气泡与钢液的接触面积减小,精炼效果反而降低。
理想的状况是氩气流(泡)遍布整个钢包,增大与钢水接触面积,延长氩气(流)泡上升的流程和时间。
因此,为提高氩气的精炼效果,在保持一定氩气压力的同时,保持相应的氩气流量。
底吹氩对钢水实施搅拌作用,搅拌强度不同,精炼效果也不同。
钢包吹氩时,钢液中夹杂物的去除量由夹杂物与气体的有效碰撞来决定,而小气泡与夹杂物发生碰撞的概率大于大气泡与夹杂物发生碰撞的概率,即从钢液中去除夹杂物的数量取决于吹入钢液的气泡数量及气泡尺寸。
根据实际情况,采用了分阶段氩气控制操作:精炼前期控制氩气压力约0.3 MPa,促进精炼剂的熔融;精炼中期氩气压力约0.5 MPa,促进脱硫去夹杂;精炼后期氩气压力约0.2 MPa,促进小型夹杂物上浮,并要求钢水不裸露,有效促进了精炼过程夹杂物的去除,提高了钢水的流动性。
7 精炼喂铝线工艺改进LF 开始投用的初期,由于考虑到精炼前期钢水氧含量较高,此时喂铝线易形成Al2O3夹杂,因而采用了精炼后期喂铝线工艺。
经过一段时间的应用发现,大部分精炼钢水以低碳钢为主,钢水中氧含量相对较高,即使经过精炼前期的脱氧操作,钢水中氧含量仍然较高。
同时,由于铝的还原性极强,采取后期喂入铝线的工艺不可避免地造成Al 与钢水及炉渣中氧化物夹杂反应形成大量Al2O3夹杂,又因为精炼后期吹氩时间较短,夹杂物上浮慢,造成钢水中Al2O3较多,从而影响了钢水纯净度和钢水的流动性。
由于采取精炼后期喂铝线,铝的收得率不稳定,为保证钢水含铝量,通常喂入大量铝线,造成钢水中铝含量偏高,有进一步使钢水流动性变差的趋势。
为合理控制钢水中铝含量和酸溶铝比例,需要对铝线喂入操作进行调整。
经试验,采取了分段铝线喂入法:首先在精炼钢水进入LF 工位时立即喂铝线,进行强化脱氧和初期铝含量控制。
根据氧含量水平,将酸溶铝目标值按0.02%~0.03% 控制,然后用碳粉或以SiC 进行顶渣还原操作。
其次在精炼后期根据钢水化验酸溶铝含量,采取在精炼终点前补喂Al 线的方式,加强前期钢水快速深度脱氧,保证了夹杂物有充分上浮的时间。
同时,钢水容易保持合适的酸溶铝含量和比例,脱氧效果稳定。
据统计,精炼结束后平均[O]含量(喂Ca 线前)由原来的0.003%~0.005%下降到0.002% 以下,酸溶铝比例提高了10%,钢水铝含量达到目标铝含量值,铝收得率提高20%。
8 精炼喂钙线工艺改进采用精炼后期钢水喂钙线,目的是对Al2O3进行变性处理,改善钢水流动性。
在工艺改进之前,主要是控制精炼钢种的钙线喂入量,对改善钢水流动性未提出相应要求。
通过对水口结瘤的残留物成分分析,发现其主要组成物为CaS 和2CaSiO3。
结合相关理论得出:造成上述现象的主要因素为钙线喂入量不当。
当钙线喂入量少时,不能对钢水中的Al2O3进行充分的变性处理;钙线喂入量大时,又容易产生高熔点的CaS 和2CaSiO3。
此2 种情况均会造成钢水流动性变差。
钢水中Al2O3变性成为12CaO·7 Al2O3 夹杂的前提条件为[Ca]与[Al]的比值在0.13~0.20。
因此,需要根据钢水中[Al]含量的多少喂入相应的钙线数量,而不是一味按钢种控制钙线喂入量。
在实际生产中,一方面通过改变转炉终脱氧工艺,适当增加SiAlBa 用量,避免因SiAlBa 加入不足形成大量硅酸盐夹杂;另一方面控制钙线喂入速度在1.5~2 m/min,保证钙的收得率。
为了防止生成CaS 夹杂物,需降低钢水中S 含量。
经验表明,部分钢种的硫含量应控制在0.015%以下。
9 强化钢水温度控制及铸机操作钢水温度对钢水流动性有双重影响,一方面温度高可以提高钢水流动性,另一方面温度高迫使铸机低速浇铸,Al2O3易粘附到水口内壁上,导致水口内径缩小,降低钢水流动性。