第4章 综合生产计划 - 生产计划与控制 兰秀菊
第7章 能力计划 - 生产计划与控制 兰秀菊
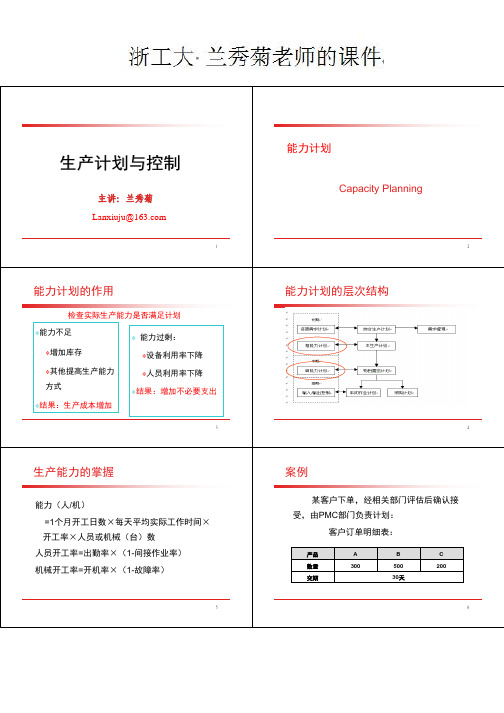
负荷(H) 96 54 125 86 72 170 45 40 50
负荷合计(H) 361 242 135
8
负荷计划步骤
1.依产品别、制程别计算出负荷; 2.依机械(人员)别、制程别作负荷合计; 3.进行负荷、能力的比较、分析; 4.对负荷、能力进行调整,使之一致。
10
粗能力计划的优点和缺点
优点:
周 期 (综合因子法)
心
例
1
2
3
4
5
6
7
8
9
10
100 60% 41.10 41.10 41.10 41.85 41.85 41.85 47.91 47.91 47.91 55.35
200 30% 20.55 20.55 20.55 20.93 20.93 20.93 23.96 23.96 23.96 27.68
33
细能力计划计算技术
期间 1
计划数量(个) 180
物料 A B C D E
产品A的主生产计划
周
2
3
4
5
6
7
8
200
220
250
200
150
200
160
产品A所有物料的批量等数据
批量 100 200 200 600 400
已有库存 100 450 300 1600 1000
提前期(周) 1 1 1 1 1
③负荷、生产能力分析调整 负荷、生产能力累计表
600
540(能力)
500
400
360(负荷)
360(能力)
300
242(负荷)
200
180
135(负荷)
100
生产计划与控制教材(PPT 58张)

财务计划
长期计划
需求管理
粗能力计划 细能力计划
年度生产计划 主生产计划
中期计划
物料需求计划
装配计划
短期计划
采购计划
2019/2/20
生产作业计划
21
生产作业计划
第四讲 需求管理与生产计划4讲
3生产计划体系 生产计划的内容
制造业的生产计划主要包括两种计划:综合计划与主 生产进度计划 综合计划又称年度生产大纲,它在对计划期内需求和 资源进行平衡的基础上,规定企业在计划年度内总的 生产目标 主生产进度计划是综合计划的具体化,表现为按产品 品种、规格规定的年度分季、分月的产量计划,实际 上是对企业产品生产进度的大致安排。
2019/2/20
8
第四讲 需求管理与生产计划4讲
不同生产环境下需求管理的核心任务比较
任务
信息
MTS
提供预测信息
ATO
MTO/ETO
提供产品配置管 提供产品定义信 理信息 息
计划
优化库存水平
交货期设置
提供工程能力需 求计划
控制
确保顾客服务水 平
根据顾客需求调 满足交货期要求 整工程资源
2019/2/20
2019/2/20
22
第四讲 需求管理与生产计划4讲
3生产计划体系 生产计划的指标体系
产量指标
B
品种指标
A 生产计划
C
质量指标
出产期
E
23
D
产值指标
2019/2/20
第四讲 需求管理与生产计划4讲
4生产能力
生产能力是指企业的固定资产或作业人员,在 一定时期内和一定的技术组织条件下,经过综 合平衡后所能生产一定种类产品的最大数量。
《生产计划与控制》PPT课件

工时(小时) 1266
10.0 1150
差距(-,+) -1.4 -116
(4) 协调可用资源与资源需求
资源短缺时,要采取必要的措施来协调这一差距。
29
第三讲生产计划与控制
(3)能力计划系数法确定资源需求
制定资源需求计划也常采用能力计划系数法 (CPF,Capacity Planning Factor)。能力计划系数是 表示单位生产量占用的制造过程中某种资源的关 系。能力计划系数可以通过历史数据由产量与所 用资源大致地经验估算。利用能力计划系数法编 制资源需求计划的方法如下: (1) 利用历史的经验数据计算CPF。 (2) 根据CPF和计划产量计算能力需求。
30
第三讲生产计划与控制
在过去6个月生产5800个综合单位产品,共用47 000个工时,分配如下:
基 辅本 助序工 工—序 序假—设主工一时要12个21工0000工00序厂所、的占辅百生助分2产4比54工..5过638序程、单可位精产分加品为23所..工06462用91和个工装主时 配要。工在 精过加 去工 6个月50中00,在一条生10.6产4 线上,有0.8962个不同的产
2.4资源需求计划编制
(1)资源需求计划制定步骤 分在析生资产源计清划单大纲的编制过程中,当初步 确 定计了算各资产源品需系求列的生产量时,还要进行资 源 列 需 时比求,较计 需可划要用的占资核用源定多和。少需考有求虑效在资生源产;这如些果产现品有系资 源 不协足调,可应用如资何源协和调资这源些需差求距。
纲初稿,是使生产满足预测需求量和保持一定的 库存量,以此来确定月生产量和年生产量的。 编制目标:决定月产量,以满足预测需求,并保 持一定的库存水平和平稳的生产率。 考虑因素:保持库存的花销,改变生产率的花销。
生产计划与控制 综合生产计划共34页文档

生产计划与控制 综合生产计划
56、极端的法规,就是极端的不公。 ——西 塞罗 57、法律一旦成为人们的需要,人们 就不再 配享受 自由了 。—— 毕达哥 拉斯 58、法律规定的惩罚不是为了私人的 利益, 而是为 了公共 的利益 ;一部 分靠有 害的强 制,一 部分靠 榜样的 效力。 ——格 老秀斯 59、假如没有法律他们会更快乐的话 ,那么 法律作 为一件 无用之 物自己 就会消 灭。— —洛克
生产计划与控制 综合生产计划
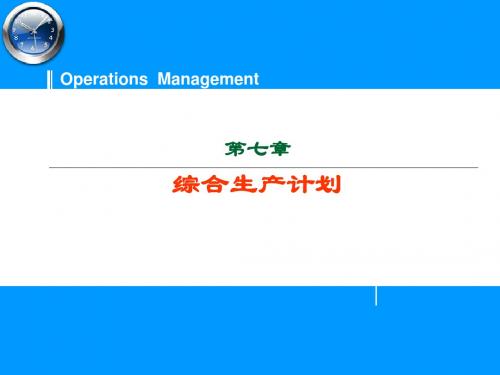
Operations Management
第七章
综合生产计划
第七章
综合生产计划
Operations Management
学习目标
(1)了解生产能力的含义,掌握生产能力的核 定方法。 (2)了解生产计划的种类和主要指标。 (3)掌握生产计划的编制及盈亏平衡分析法和 线性规划法等。
综合生产计划
第七章
Operations Management
单一品种条件下生产能力计算
4.车间生产能力的确定:在工段生产能力的基础上进行综 合平衡 5.企业生产能力的确定:在车间生产能力的基础上进行综 合平衡
第七章
综合生产计划
Operations Management
多品种条件下生产能力计算
综合生产计划
第七章
Operations Management
代表产品法(成批生产,品种数少)
例:某厂生产A、B、C、D四种产品,其年产量分别为 250,100,230和50台,各种产品在机械加工车间车床 组的计划台时定额分别为50,70,100和50台时,车床组 共有车床12台,两班制,每班8小时,设备停修率10%, 试求车床组的生产能力。(每周按六天工作计算) 解:(1)确定C为代表产品 (2)计算以C为代表产品表示的生产能力 (365-63)×2×8×(1-0.1) = 522 M代=S ×Fe / t代=12× 100 (3)计算各具体产品的生产能力如下表
综合生产计划
第七章
Operations Management
7.2 生产计划
生产计划编制方法
滚动计划法 量本利分析法 线性规划法
生产计划与控制4-综合生产计划
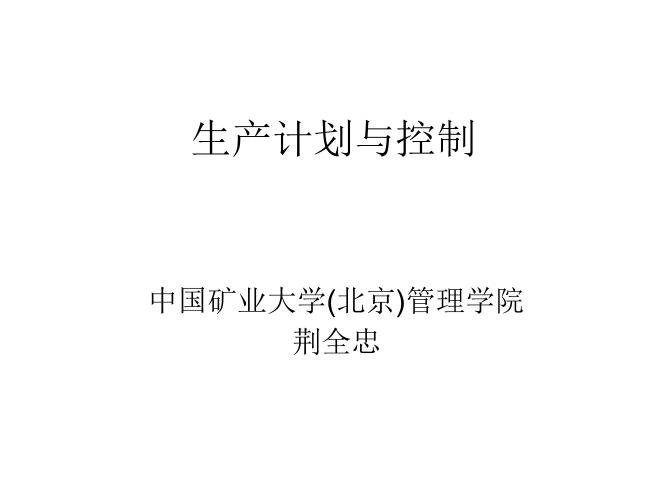
中国矿业大学(北京)管理学院 荆全忠
综合生产计划
1.概念
– 综合生产计划(Production Planning, PP)又称生产 大纲,是根据市场预测和企业拥有的生产资源,对企业 计划期内出产的内容、数量以及为保证生产所需的劳动 力水平、库存等措施所做的决策性描述。
2.综合计划的目的
– 改变价格 – 促销 – 积压订单待发货 – 加班操作 – 雇佣兼职工人 – 转包合同 – 增加或减少额外轮换 – 积压存货,等
综合生产计划
7.对市场需求波动的响应
数 需求量累积线
量数 量数
量
外购\库存\延期
生产量累积线
需求量累积线
库存量
需求量累积线
生产生量产累量积累线积线
时间
均衡安排
变动安排
时间 时间
动态规划法
• 动态规划(dynamic programming)是求解决 策过程最优化的一种数学方法。
动态规划法
例题:某企业生产大型变压器,预测知前四个月的需求量。 生产成本随着生产数量变化。除调试费4元外,每月生产 的头两台花费各为2元,后两台各1元。最大生产能力为每 月4台。每台变压器储存1个月的成本为1元,仓库最多存3 台。已知1月1日仓库有1台变压器。要求4月底库存为零。
)+
fk+1(Sk+1)]
动态规划法
以下我们从第4阶段开始计算。 • 对于每个S4的可行值, f4的值列表于下
X4
S4
0
0
1
2
3
0
f4
1
2
8 6
生产 生产 3 成本 数量
9
9
3
8
2
生产计划与控制综合计划教学课件

项目管理
通过项目管理方法,协调不同部 门和团队的合作,实现综合计划。
生产计划编制方法
材料需求计划(MRP)
通过分析产品结构和订单需 求,确定所需原材料和零部 件,并进行合理的采购计划。
产能规划(CAP)
根据生产设备和人力资源的 情况,制定合理的产能规划, 确保生产能力与市场需求相 匹配。
作业计划(SOP)
将整个生产过程拆分为具体 的作业任务,并按照一定的 顺序和时间安排进行执行。
生产计划与控制综合计划 教学课件PPT
欢迎来到生产计划与控制综合计划教学课件PPT!本课程旨在帮助您深入了 解生产计划与控制的重要性以及编制、执行和控制计划的方法。让我们开始 吧!
教学目标
通过本课程,您将能够:
1 了解生产计划与控制的概念和流程。 2 掌握生产计划的编制方法和步骤。
3 了解生产计划的执行过程和关键指
生产计划执行过程
生产计划执行过程是实际操作生产计划并确保生产正常进行的关键步骤。
1
物料准备
确保所需物料和工具准备充足,以便顺
任务分配
2
利进行生产。
将不同的任务分配给相应的人员,以提
高效率和质量。
3
生产监控
监控生产过程,及时处理异常情况,并 确保生产按计划进行。
生产计划控制指标பைடு நூலகம்
1 交货准时率
衡量生产计划执行的准确性和能力,以按时 交付产品。
2 生产效率
用于评估生产资源的利用率和生产活动的效 率。
3 库存周转率
衡量原材料和半成品的周转速度和库存管理 的效果。
4 质量指标
评估产品质量并监控生产过程中的问题和改 进措施。
综合计划概述
综合计划是根据市场需求和资源情况,综合考虑各种因素并制定合理的生产计划。
生产计划与控制教材(PPT 96页)

2021/3/5
第七讲 项目管理
24
项目管理
项目管理
技术背景
技术背景
业务技能
一个重新设计航空器机翼的8 人研发项目的项目经理
注:三维图表示不同项目环境 下项目经理应具备的技能要求
业务技能
领导一个集成多种信息 和电信技术的60人IT咨 询企业的项目经理
2021/3/5
2021/3/5
第七讲 项目管理
27
8.2 项目计划
▪ 项目计划的主要问题(4W2H)
▪ 做什么(What):项目经理与团队应该完成什 么工作。
▪ 如何做(How):如何完成这些工作和任务如 工作分解结构图(WBS)
▪ 谁去作(Who); ▪ 何时作(When)(进度表) ▪ 花费多少(How much)(预算) ▪ 哪里(Where):确定各项工作在什么地方进
▪ 项目的特点
▪ 独特性 ▪ 时限性 ▪ 开放性 ▪ 客户性 ▪ 不确定性
2021/3/5
第七讲 项目管理
5
8.1项目管理 ▪ 项目的层次性
大项目、项目群 项目 任务或活动 工作包
2021/3/5
第七讲 项目管理
6
8.1项目管理
▪ 项目的寿命周期
C
D
E
F
Concept 概念阶段
Development 发展阶段
▪ 项目计划是项目组织根据项目目标的规定,对项目实 施工作进行的各项活动做出周密安排。
▪ 项目计划是项目实施的基础。
▪ 项目计划的目的
▪ 确定并描述为完成项目目标所需的各项任务(活动) 范围;
▪ 确定负责制性项目各项任务的全部人员; ▪ 制定各项任务的时间进度表; ▪ 阐明每项任务所需的人力、物力、财力; ▪ 确定每项任务的预算。
新编文档北京科技大学生产管理第四章综合生产计划 - 幻灯片1精品文档PPT课件
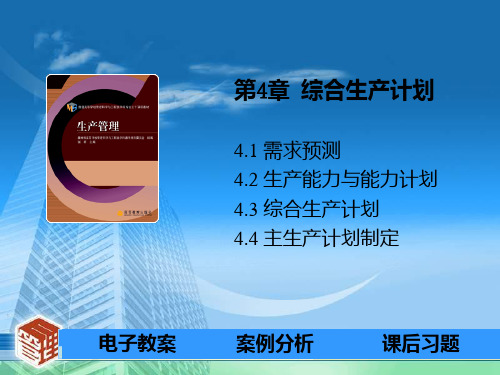
Week 1 2 3 4
Actual 650 678 720
Forecast 693.4
F 4 = . 5 ( 7 2 0 ) + . 3 ( 6 7 8 ) + . 2 ( 6 5 0 )
▪需求预测定性方法
德尔菲法预测的步骤如下:(1)设计调查 问卷;(2)选择调查专家;(3)征询专家意见; (4)综合归纳分析结果,再反复进行调查;(5) 提出预测结论。预测过程如图4-1所示。
德尔菲法的特点:(1)匿名性。(2)反馈性。 (3)统计性。
▪需求预测定性方法
德尔菲法应用的原则:(1)问题要集中。(2) 不能将调查小组的意见强加专家,防止诱导。(3) 避免组合事件。 (4)考虑可能的偏差。
▪需求预测定性方法
4.销售人员集中法 销售人员集中法是根据每个销售人员对需
求预测的情况进行综合得出预测结果。
▪需求预测定量方法
因果关系模型:回归预测法 时间序列模型:移动平均、加权移动平均和指 数平滑法
▪需求预测定量方法
1.一元线性回归法 设X、Y两变量满足趋势变动直线方程:Y=a+bX
举例
简单线性回归模型 Simple Linear Regression Model
营销部门、生产运作部门、财务部门等管理人 员,聚集在一起进行集体讨论,对产品需求作 出预测。
▪需求预测定性方法
这种方法的优点是:(1)预测简单、经济易行; (2)不需要准备和统计历史资料;(3)汇集了 各主管的丰富经验与聪明才智;(4)如果市场 情况发生变化,可以立即进行修正。 不足之处是:(1)个别人(权威)的观点可能 左右其他人发表意见;(2)预测的责任分散,会 导致管理者发表的意见过于草率。这种方法常用 于制定长期规划以及开发新产品预测。
2024年生产计划与控制课本

在2024年的生产计划与控制领域,企业将面临前所未有的挑战和机遇。
全球经济的变化、技术的快速发展、以及消费者需求的多样化,都要求企业能够快速响应市场变化,同时保持高效的生产和供应链管理。
因此,制定一份科学合理、具有前瞻性的生产计划与控制课本显得尤为重要。
一、引言在数字化时代的背景下,生产计划与控制已经不再是单纯的资源调配和流程管理,而是涉及到信息技术的深度整合、跨部门协作以及智能化决策。
本课本旨在为企业的生产管理人员提供一套系统的理论知识和实践指导,帮助他们在复杂多变的环境中,实现生产效率的最大化、成本的最小化以及客户满意度的提升。
二、生产计划的基础生产计划是企业运营的核心,它决定了企业将生产什么、何时生产以及如何生产。
在课本的这一部分,我们将深入探讨生产计划的制定流程,包括需求预测、生产能力规划、物料需求计划、以及生产进度控制等。
同时,我们也将介绍不同类型的生产系统,如流水线生产、大规模定制和精益生产等,帮助读者理解如何根据企业的具体情况选择合适的生产模式。
三、供应链管理供应链管理是连接供应商、制造商、分销商和客户的桥梁。
本课本将详细介绍供应链的各个环节,包括采购、库存管理、物流配送等,以及如何通过供应链优化来提高整个系统的效率和响应能力。
此外,我们还将在信息技术和物联网的背景下探讨供应链的数字化转型,以及如何利用区块链、人工智能等新技术来提升供应链的透明度和智能化水平。
四、质量管理与持续改进产品质量是企业竞争力的关键要素。
本课本将重点介绍质量管理的理论和方法,包括全面质量管理、六西格玛、精益质量等,以及如何通过持续改进来不断提升产品质量和客户满意度。
我们还将探讨如何利用大数据和人工智能技术来实现质量问题的预测和预防。
五、成本管理与控制成本管理是企业保持竞争力的关键。
本课本将探讨成本分析的方法和工具,如成本会计、生命周期成本分析等,以及如何通过成本控制来优化生产流程和资源配置。
此外,我们还将在绿色制造和可持续发展的大背景下,讨论如何实现成本效益和环境责任的平衡。
生产计划与控制_习题集(含答案)
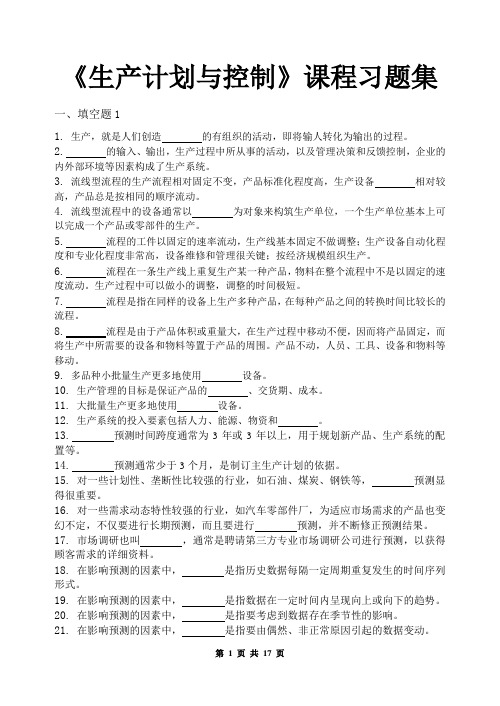
《生产计划与控制》课程习题集一、填空题11.生产,就是人们创造的有组织的活动,即将输人转化为输出的过程。
2.的输入、输出,生产过程中所从事的活动,以及管理决策和反馈控制,企业的内外部环境等因素构成了生产系统。
3.流线型流程的生产流程相对固定不变,产品标准化程度高,生产设备相对较高,产品总是按相同的顺序流动。
4.流线型流程中的设备通常以为对象来构筑生产单位,一个生产单位基本上可以完成一个产品或零部件的生产。
5.流程的工件以固定的速率流动,生产线基本固定不做调整;生产设备自动化程度和专业化程度非常高,设备维修和管理很关键;按经济规模组织生产。
6.流程在一条生产线上重复生产某一种产品,物料在整个流程中不是以固定的速度流动。
生产过程中可以做小的调整,调整的时间极短。
7.流程是指在同样的设备上生产多种产品,在每种产品之间的转换时间比较长的流程。
8.流程是由于产品体积或重量大,在生产过程中移动不便,因而将产品固定,而将生产中所需要的设备和物料等置于产品的周围。
产品不动,人员、工具、设备和物料等移动。
9.多品种小批量生产更多地使用设备。
10.生产管理的目标是保证产品的、交货期、成本。
11.大批量生产更多地使用设备。
12.生产系统的投入要素包括人力、能源、物资和。
13.预测时间跨度通常为3年或3年以上,用于规划新产品、生产系统的配置等。
14.预测通常少于3个月,是制订主生产计划的依据。
15.对一些计划性、垄断性比较强的行业,如石油、煤炭、钢铁等,预测显得很重要。
16.对一些需求动态特性较强的行业,如汽车零部件厂,为适应市场需求的产品也变幻不定,不仅要进行长期预测,而且要进行预测,并不断修正预测结果。
17.市场调研也叫,通常是聘请第三方专业市场调研公司进行预测,以获得顾客需求的详细资料。
18.在影响预测的因素中,是指历史数据每隔一定周期重复发生的时间序列形式。
19.在影响预测的因素中,是指数据在一定时间内呈现向上或向下的趋势。
《生产计划与控制》课件

生产计划控制方法
1 生产进度监控
2 库存管理
3 质量ቤተ መጻሕፍቲ ባይዱ制
通过监控生产进度,及时 发现并解决生产中的问题。
合理控制原材料和成品的 库存,减少资金占用并避 免过期或报废。
实施严格的质量控制措施, 确保产品符合标准。
实例分析:某公司生产计划与控制
规模化生产
公司通过规模化生产降低成本, 提高效率。
智能化监控
利用智能化系统实时监控生产进 度和质量。
精细化库存管理
采用精细化库存管理系统,减少 库存和资金占用。
结论与展望
生产计划与控制是企业生产管理中的重要环节,随着技术的发展,未来的生 产计划与控制将更加智能化和高效。
《生产计划与控制》PPT 课件
本课程介绍生产计划与控制的基本概念和流程,包括不同类型的生产计划, 编制的流程,控制的意义以及实例分析。
生产计划的类型
长期计划
规划未来一年或更长时间范围内的生产目标与计划。
中期计划
详细规划一个月到半年的生产计划,考虑产品需求和资源可用性。
短期计划
制定每天或每周的生产计划,确保生产线能够高效运作。
生产计划编制的流程
1
需求分析
分析市场需求和客户需求,确定产品类型和数量。
2
资源评估
评估所需的人力、设备和原材料资源。
3
计划制定
制定详细的生产计划,包括时间表和分工。
4
计划调整
根据实际情况进行调整,确保计划的可行性和合理性。
生产计划控制的意义
生产计划控制能够提高生产效率、降低生产成本,确保产品质量和交货时间。
生产计划与控制概述(PPT 50页)

生产计划与控制
主生产计划 例5-2 某农用泵厂1~6月份综合生产计划(台) (P.195)
表5-3 自吸泵系列1~2月份主生产计划(台)
18
工业工程概论
5.2 生产计划
生产计划与控制
主生产计划制定的步骤和程序
MPS的确定过程是一个反复试行、不断修正的过程(滚动计划), 主要包括计算现有库存量、确定主生产计划产品的生产量与生产时 间、计算待分配库存等,然后经过粗能力计划分析,最后批准下达。
D
10
每万件产品利润(万元) 6
材料消耗定额(吨/万件)
X2
X3
8
7
10
6
20
10
6
8
10
6
材料供应量(吨)
680 500 860 440
max Z 6 x 1 10 x 2 6 x 3
x1 0 , x 2 0 , x3 0
s.t.
18 x 1 8 x 2 8 x 1 10 x 2
生产计划的控制: ✓订单接受控制 ✓投料控制 ✓生产进度控制 ✓库车控制。
4
工业工程概论
生产计划体系
产品开发与设计
5.2 生产计划
经营目标
产品需求及预测 生产过程规划
综合生产计划 主生产计划
物料需求计划
材料采 购计划
外购件需 求计划
自制件生产计划
生产计划与控制
生产能力测定 生产能力综合平衡
生产能力粗平衡 能力需求计划
生产计划与控制
销售量 生产量
追赶策略
时间
适时改变劳动力水平或调节生产速率来适应需求变化
10
5.2 生产计划
工业工程概论
综合生产计划 综合生产计划编制策略
生产计划与控制教材

生产计划与控制教材1. 简介本教材旨在介绍生产计划与控制的基本概念、原理与方法,帮助学生全面了解生产计划与控制的重要性和作用,掌握现代企业生产计划与控制的基本技术与方法,并培养学生的实际操作能力。
2. 生产计划与控制概述2.1 生产计划的定义生产计划是指根据企业的销售计划和市场需求,制定可行的生产目标和计划,合理安排生产资源,确保产品按时交付的过程。
2.2 生产计划的目标生产计划的目标包括: - 确保产品按时交付,满足市场需求; - 提高生产效率和资源利用率; - 控制生产成本,提高企业的竞争力。
2.3 生产控制的定义生产控制是指通过对生产过程的监控和调控,以确保生产过程按照计划进行,达到预期的生产目标。
2.4 生产控制的重要性生产控制对企业的重要性体现在: - 控制生产成本,提高经济效益; - 提高产品质量,满足市场需求; - 降低生产风险,提高供应链的稳定性。
3. 生产计划与控制的基本原理3.1 生产计划与控制的层次生产计划与控制的层次包括三个层次: 1. 长期生产计划:根据市场需求和企业发展战略,制定长期生产目标和计划; 2. 中期生产计划:将长期生产计划细化为中期生产目标和计划,精确安排生产资源和工艺流程; 3. 短期生产计划:根据中期生产计划,制定具体的短期生产计划,安排具体的生产任务和工序。
3.2 生产计划与控制的基本原则生产计划与控制应遵循以下基本原则: - 准确性原则:生产计划要准确反映市场需求和产品特性,生产控制要准确监控和调控生产过程; - 可行性原则:生产计划要合理安排生产资源和工艺流程,生产控制要保证生产目标的可行性; - 灵活性原则:生产计划和控制要具备一定的灵活性,能够及时适应市场变化和生产环境的变化; - 经济性原则:生产计划和控制要追求最佳的经济效益,实现资源的最优配置。
4. 生产计划与控制的方法和工具4.1 生产计划与控制的方法生产计划和控制的方法包括: - MRP(物料需求计划)法:通过对物料需求进行计划和控制,确保原材料和零部件的供应和库存满足生产需要; - JIT(即时生产)法:根据市场需求,以尽量减少库存和缩短生产周期为目标,实现生产计划和控制的一种方法; - TOC(约束优化理论):通过识别生产过程中的瓶颈环节,优化瓶颈环节的资源利用率,实现生产计划和控制的一种方法。
第4章生产计划
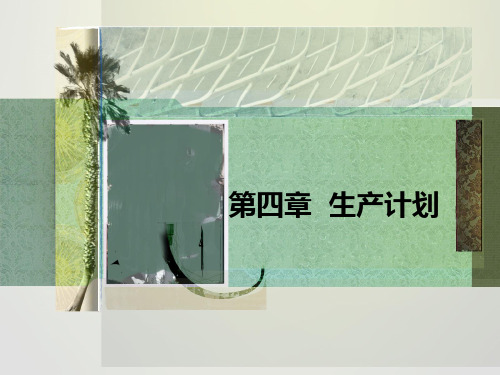
3) 建立预测模型
求出:
xtT at btT
at
M (1) t
(
M
(1) t
M
( t
2)
)
2M
(1) t
M (2) t
得出:bt
2
(
M
(1) t
M
(2) t
)
(N 1)
a15
2
M
(1) 15
一次指数平滑值:
S (1) t
Xt
(1 )St(11)
St(1)——第t期的一次指数平滑值; St-1(1)——第(t-1)期的一次指数平滑值; Xt——第t期的实际值;
α——平滑指数(0≤α≤1)
• 进一步展开:
S (1) t
Xt
(1 )Xt1
(1 )2
X t2
...
+(1-
)t
S (1) 0
3.生产能力的计算方法
(1)对于大量生产企业,流水线的生产 能力可按下式计算:
P Te r
•
• 式中,P——流水线的生产能力; • Te——计划期有效工作时间; • r——流水线节拍(流水线上出产两
个相同 制品的时间间隔)。
(2)对于成批生产企业,单台设备的生
产能力P的计算式为:
P
Te q
Te t
(3)建立预测模型: XtT at btT
(4)求系数
at
S (1) t
(
S (1) t
St(2) )
2St(1)
S (2) t
bt
1
(
- 1、下载文档前请自行甄别文档内容的完整性,平台不提供额外的编辑、内容补充、找答案等附加服务。
- 2、"仅部分预览"的文档,不可在线预览部分如存在完整性等问题,可反馈申请退款(可完整预览的文档不适用该条件!)。
- 3、如文档侵犯您的权益,请联系客服反馈,我们会尽快为您处理(人工客服工作时间:9:00-18:30)。
时间 预测 正常 产出 加班 转包 期初 存货 延迟交货 成本计算 产出 聘人 存货 延迟交货 (元) 正常 加班 转包 期末 平均
1 200 280 0 0 0 80 40 0 560 0 0 0 40 0
2 200 280 0 0 80 160 120 0 560 0 0 0 120 0
三种策略的延迟交货成本比较 600 500 400 300 200 100 平准策略 调整工时 同步策略
同步策略
3600 0 0 400 460 400 4860
19
160 140 120 100 80 60 40 20 0 1 2 3 4 5 6
平准生产 调整工时 同步策略
0 1 2 3 4 5 6
9 10
员工人数不变,加班或减班改变工作时数 优缺:
提供员工稳定的工作 减少招聘和解聘费用 需求变动不是很大
制定综合生产计划的策略4
外包
工人人数固定,满足最小的需求预测量 超过部分外包 优缺点: 交货期与质量难控制 需求波动较大时,保持自身稳定的生产 能力
11
综合生产计划制定方案
30
四月 6000 5600 4000 600 1000
五月 5000 5000 4000 600 400
六月 4400 4400 4000 400
小结:综合生产计划的作用
总结:
1. 企业未来一段时间的产能规划 2.是企业战略经营目标实现的基本计划 3.是制定主生产计划的基础和依据
一月 3000 3000 3000
二月 3600 4000 4000
三月 5200 5200 4000 600
四月 6000 5600 4000 600
五月 5000 5000 4000 600 400
六月 4400 4400 4000 400
400
27200 27200
400 4000 600 1000 4000 600 400
运输表法
假定1:产量、生产成本等有关变量间关系是线性的 假定2:简单的有三种生产方式的生产系统:
单位资源 约束1 约束2 约束3 约束4 3 2 2 0
单位资源 1 4 0 1
使用时间 400 600 200 100 ≤ ≤ ≤ ≤
可用时间 4650 9600 2400 2000
第一种为正常班次生产 第二种为加班时间生产 第三种转包生产
假定3:产品可以在计划期长度内储存,不允许缺货
生产数量(试算) 产品 100 100
总利润 ¥9,000.00
23 24
表上作业法基本原理
计划方案
单位计划期 期初库存 正常生产 1 加班生产 外协 正常生产 2 加班生产 外协 正常生产 3 加班生产 外协 正常生产 4 加班生产 外协 需求
0 r c s D1
总计 1800 1680 120 0
期末 平均
80 3360 360 0 520 400 4640
18
4700
同步策略制定综合生产计划方案
临时工聘用、培训费用100元/人,生产率15单位/人,正常 20单位/人。缺工8个工期,聘4人。若聘5人?
三种策略相关成本的对比分析(部分指标)
三种策略正常生产成本比较 800 700 600 500 400 300 200 100 0 1 2 3 4 5 6
约束条件3:2*生产数量(甲)≤2400 约束条件4:1*生产数量(乙)≤2000 总利润=60*生产数量(甲)+30*生产数量(乙) 约束条件1:3*生产数量(甲)+1*生产数量(乙)≤4650 约束条件2:2*生产数量(甲)+4*生产数量(乙)≤9600
21
22
建模
甲产品 单位利润 ¥60.00 乙产品 ¥30.00
方案:单一策略 或 混合策略
12
综合生产计划技术
试误法
综合生产计划的编制步骤
数学技术
线性规划法 动态规划法 表上作业法 模拟模型技术
确定市场需求 确定生产能力
利用各种生产策略组 合
正常时间、加班时间、转包合同
计算各组合的成本 选择最佳的组合
为正常时间、加班时间、转包合同、持有存货、延迟 交货和临时解聘确定成本 提供选择方案,计算各自成本 确定满意方案
生产方式 正班生产 加班生产(可多生产) 分包生产(可多生产)
生产能力(吨) 单位制造成本(元)
4000 600 1000
20000 21000 22000
运输成本表
3000 3600 400 4000 600 200 400 1000 400 0
综合生产计划表(辆)
方案1
总计 需求量
800 400
总计 1800 1800 0 0
三种策略加班成本比较 140 120 100
平准策略 调整工时 同步策略
80 60 40 20
平准策略 调整工时 同步策略
三种策略的总生产成本比较
0 1 2 3 4 5 6
80
三种策略的存货成本对比 180
4700 4650 4600 4550 4500 平准策略 调整工时
计划数 正班生产 加班生产
2200 2000 400
4000 400
600
分包生产 库存数
27
200+400 100Leabharlann 400000
400 0
0
0
28
综合生产计划表(辆)
方案2
总计 需求量 计划数 正班生产 加班生产 分包生产 库存数 2200 2000 400 800 27200 27200 一月 3000 3400 3400 二月 3600 4000 4000 三月 5200 4800 4000 600 200 400
29
综合生产计划表(辆)
方案3
四月 6000 5600 4000 600 1000 五月 5000 5000 4000 600 400 六月 4400 4400 4000 400 需求量 计划数 正班生产 加班生产 分包生产 库存数 2200 2000 800 总计 27200 27200 一月 3000 3000 3000 二月 3600 4400 4000 400 三月 5200 4800 4000 600 200 400
提前做好规划,生产规划有序 发现问题提前解决:
人员问题 设备问题 厂房问题 物料问题 库存问题
出现问题时,有据可查 年产量与月均产量较明确:方便制定主生产计划
31
32
谢谢!
33
全部生 产能力
例:某汽车制造厂2001年1-6月大轿车预计的市场需求量分别为3000辆、 3600辆、5200辆、6000辆、5000辆、4400辆,共计27200辆,一月份期初库 存量为零。该厂在三种不同生产方式下的生产能力和相应的单位制造成本数据 如表所示,单位产品每月的存储成本为1000元,请确定该厂2001年1-6月的 综合生产计划。
3 300 280 40 0 160 180 170 0 560 120 0 170 0
4 400 280 40 0 180 100 140 0 560 120 0 140 0
5 500 280 40 0 100 0 50 80 560 120 0 50 400
6 200 280 0 0 0 0 0 0 560 0 0 0 0 总成本
例:某企业的基本信息
假设:期初库存=0,工人数15人。
200
15
16
平准策略的综合生产计划
时间 预测 正常 产出 加班 转包 期初 存货 延迟交货 成本计算 产出 存货 延迟交货 (元) 正常 加班 转包 600 0 0 50 0 600 0 0 150 0 600 0 0 200 0 600 0 0 150 0 600 0 0 50 500 600 0 0 0 0 总成本 3600 0 0 600 500
运输表法
计划期
1 2 h r +h c +h s+h r c s D2 3 2h r +2h c +2h s+2h r +h c +h s+h r c s D3 4 3h r +3h c +3h s+3h r +2h c +2h s+2h r +h c +h s+h r c s D4 25 R1 C1 S1 R2 C2 S2 R3 C3 S3 R4 C4 S4 26
17
调整工时策略的综合生产计划方案 缺1人,加班工作最大产出是每期40单位
1 200 300 0 0 0 100 50 0
2 200 300 0 0 100 200 150 0
3 300 300 0 0 200 200 200 0
4 400 300 0 0 200 100 150 0
5 500 300 0 0 100 0 50 100
月/周产量 雇佣人数 存货量
将需求量设定成生产量 通过招聘 解聘员工改变工人数量对应生产变 动
优缺点:
存在大量欲就业且容易训练的应征者 需求减少时,员工因恐失业工作较慢
成本 最低 最优化
7
8
制定综合生产计划的策略2
调整工时策略
制定综合生产计划的策略3
平准策略
员工人数和产量维持固定 调整库存,不外包不增加人员 优缺点: 缺货时有些顾客会转向竞争对手 可能会产生滞销存货 减少招聘解聘费用,人员稳定
3 300 280 0 0 160 140 150 0 560 0 0 0 150 0