二次配系统简介
二次配系统简介

制程二次配排气系统简介
刘庆磊 2014年8月27日
上海盛剑环境系统科技有限公司
目录:
制程排气供应系统
1.系统介绍 2.技术说明 3.施工准备 4.施工技术要求
上海盛剑环境系统科技有限公司
系统介绍:
由制程机台至主管支管之间连接风管,统称二次配排气风管(Exhaust Hook-up Ducting)工程;其主要是将制程机台所产生之各种废气(例如酸碱性 废气、挥发性有机废气、一般性废气等等)经由二次配排气风管排至排气支管、 主风管等再导入废气处理设备处理,处理后废气再排放至大气中的整个排气系 统过程。
制 程 排 气 系 统
上海盛剑环境系统科技有限公司
技术说明: 排气系统分类: 制程流程中,使用机台种类相当烦多,各种排放物质种类更是不胜枚举, 若要针对单一种类设臵单独排放处理设施,不仅有其设臵上的因难,而且施工 上及日后维修保养更属不易,因而,依据排放之特性大致上区分为酸、毒性 (Acid Exhaust)、碱性(Alkali Exhaust)、有机溶剂(Solvent Exhaust)及一 般排气(General Exhaust)四个系统: (1) 酸、碱性废气:其主要来源为化学清洗工作站,清洗芯片时所产生之挥发 性气体,此气体部分含有浓烟,部分则对呼吸系统有刺激性作用有害人体,故 必须经过Central Scrubber做水洗中和处理后,再排入大气。 (2) 毒 性 废 气:其主要来源为化学气体沉积,(CVD)干蚀刻机、扩散、离子 植入机及磊晶等制程时所产生,由于以上之制程均使用大量的毒性气体,因此 在其机台本身即设臵有Local Scrubber 作先行处理,再送至Central Scrubber 做水 洗中和处理后,再排入大气。 (3) 有机溶剂废气:目前所见到大多以活性碳吸附塔或采用沸石浓缩转轮+燃气 式焚化炉,去除率可达90﹪以上,为目前较佳之空气污染控制技术。 (4) 一 般 废 气:其来源为机器运转发热产生不含有害物质,故可经由排气设备 直接排入大气。
二次配通俗解释
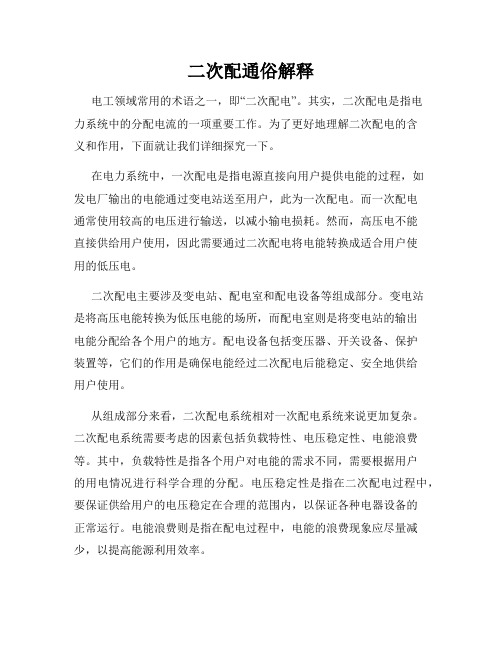
二次配通俗解释电工领域常用的术语之一,即“二次配电”。
其实,二次配电是指电力系统中的分配电流的一项重要工作。
为了更好地理解二次配电的含义和作用,下面就让我们详细探究一下。
在电力系统中,一次配电是指电源直接向用户提供电能的过程,如发电厂输出的电能通过变电站送至用户,此为一次配电。
而一次配电通常使用较高的电压进行输送,以减小输电损耗。
然而,高压电不能直接供给用户使用,因此需要通过二次配电将电能转换成适合用户使用的低压电。
二次配电主要涉及变电站、配电室和配电设备等组成部分。
变电站是将高压电能转换为低压电能的场所,而配电室则是将变电站的输出电能分配给各个用户的地方。
配电设备包括变压器、开关设备、保护装置等,它们的作用是确保电能经过二次配电后能稳定、安全地供给用户使用。
从组成部分来看,二次配电系统相对一次配电系统来说更加复杂。
二次配电系统需要考虑的因素包括负载特性、电压稳定性、电能浪费等。
其中,负载特性是指各个用户对电能的需求不同,需要根据用户的用电情况进行科学合理的分配。
电压稳定性是指在二次配电过程中,要保证供给用户的电压稳定在合理的范围内,以保证各种电器设备的正常运行。
电能浪费则是指在配电过程中,电能的浪费现象应尽量减少,以提高能源利用效率。
二次配电系统在实际应用中有着广泛的应用。
无论是城市的住宅小区、商业区还是工业园区,都需要通过二次配电系统来供给电能。
二次配电系统不仅需要满足电能的需求,还要保证供电的可靠性和安全性。
因此,在设计二次配电系统时,电力工程师需要充分考虑各种因素,并合理规划和配置电力设备。
总之,二次配电是电力系统中不可或缺的一环,它将高压电能转换为低压电能,以供给用户使用。
它需要经过变电站、配电室和配电设备等组成部分来实现,同时需要考虑负载特性、电压稳定性和电能浪费等因素。
二次配电系统对于保证电能的供给可靠性和安全性至关重要,因此在建设和维护二次配电系统时要充分考虑各种因素,以确保用户正常用电的需求得到满足。
二次配系统简介
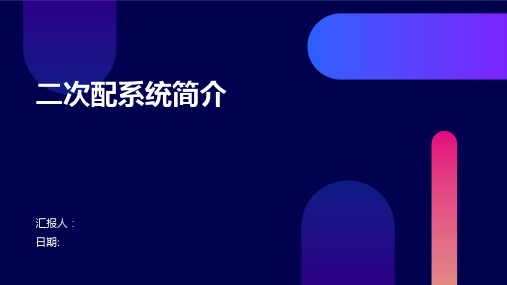
目的和意义
二次配系统的目的是为了满足电 力系统的安全、稳定和经济运行
要求。
通过二次配系统,可以实现对电 能的合理分配和调整,提高电力
系统的供电可靠性和经济性。
同时,二次配系统还可以提高电 力系统的运行效率和管理水平, 为电力企业的可持续发展提供有
07
参考文献
参考文献
参考文献1
二次配系统的研究论文,提供了系统的定义、组 成和运行原理等方面的详细介绍。
参考文献2
二次配系统的应用案例研究,介绍了二次配系统 在具体领域中的应用效果和优点。
参考文献3
二次配系统的设计手册,详细描述了二次配系统 的设计思路、实现方法和注意事项等。
THANK YOU
制。
网络通信技术可以实现数据的实时传输 、故障预警、远程维护等功能,提高二
次配系统的智能化和自动化水平。
04
二次配系统的应用场景
电力系统稳定运行
总结词
二次配系统在电力系统稳定运行中发挥关键作用,通过优化电力分配和调度, 提高系统稳定性和可靠性。
详细描述
二次配系统通过自动化技术和实时监测,对电力系统的运行状态进行评估和调 整,确保系统稳定。它还可以对电力负荷进行预测和管理,避免电力短缺或过 剩的情况,提高电力供应的可靠性。
二次配系统简介
汇报人: 日期:
contents
目录
• 引言 • 二次配系统概述 • 二次配系统的关键技术 • 二次配系统的应用场景 • 二次配系统的未来发展趋势 • 结论 • 参考文献
01
引言
背景介绍
二次配系统是指在电力系统中,通过 对电能进行二次分配和调整,以满足 不同区域、不同用户的需求。
二次配专题教育课件

Safety
Quality
Cost
Space Schedule
Hookup 驗收要項
* Electrical,HVAC,... * DI, PCW,CW,... * B-Gas,S-Gas,CDA,... * Chemical,Solvent,...
安全
Local Regulation Semi S2-0200 FM / FM 7-7 NFPA / NFPA-318 UL, CE,... HPM/ERT/First Aid Tool
1. Definition
Exhaust
Raised Floor PCW
Chemical PV
CW UPW
Tool
Power
Foundation
Gas Drain
Pumping Line
Hook-up: 以设备机台为服务对象,按其详细技术要求, 在合理时间 内,将动力主系统旳多种动力源安全/优质地衔接到机台,并确保机 台长久连续正常运作.
2.1.2 Gas
2.2.1 PCW
2.2.2 PCW
PCW
2.2.3 PCW
PCW
2.3.1 UPW
2.3.2 UPW
2.4.1 PUMPING LINE
2.4.2 PUMPING LINE
2.5.1 VEX
2.5.2 SCX
2.5.3 GEX
2.5.4 TEX
2.6.1 FWW
Etc
1.2 合理旳进度
Hook up 工程进度从2023-3-15开始严格按照: Array, C/F、Cell、 etc. , should complete leveling and assembling .
电气二次系统简介ppt课件

20.04.2020
.
4
1.1 控制系统
• 控制系统的作用:对变电站的开关设备进行就地 或远方跳、合闸操作,以满足改变主系统运行方
式及处理故障的要求。
• 控制系统的构成:由控制器具(装置)、控制对象及 控制网络构成。
• 在实现了综合自动化的变电站中,控制系统控制 方式包括远方控制和就地控制。
• 远方控制有变电站端控制和调度(或集控中心)端 控制方式。
20.04.2020
.
14
20.04.2020
.
15
2.2 布置图
• 布置图是以整体规化和有关原理图为依据,满足 二次接线设计的有关规定所绘制的图纸。
• 常用的有控制室平面布置图,控制屏、保护屏面 布置图,控制室、配电室小母线布置图等。
20.04.2020
.
16
20.04.2020
.
17
2.3 安装接线图
.
20
20.04.2020
.
21
3 互感器
• 作用 (1)变换作用 (2)电气隔离作用 (3)二次标准化
20.04.2020
.
22
3.1 电压互感器二次回路
3.1.1 对电压互感器二次回路的要求
• 接线方式应满足测量仪表、远动装置、继电保护 和自动装置等的具体要求。
• 应有一个可靠的安全接地点。 • 应设置短路保护。 • 应有防止从二次回路向一次回路反馈电压的措施。 • 对于双母线上的电压互感器,应有可靠的二次切
20.04.2020
.
8
1.4 继电保护及自动装置系统
• 作用:当电力系统发生故障时,能自动、快速、 有选择地切除故障设备,减小设备的损坏程度, 保证电力系统的稳定,增加供电的可靠性;及时 反映主设备的不正常工作状态,提示运行人员关 注和处理,保证主设备完好及系境的安全。
第十一章-发输变配电系统的二次系统 PPT课件

次接线或一次系统,它是发电、输变电和配电的主体。
二次设备及二次系统 二次设备包括监察测量仪表、控制及信号器具、
继电保护装置、自动装置、远动装置等。这些设备通常 是由电流互感器、电压互感器、蓄电池组或厂(所)用 低压电源供电。
电路电源小母线
华中科技大学电气学院
5
四、安装接线图
安装接线图是制造厂加工制造屏(屏盘)和现场 施工安装所必不可少的图,也是运行试验、检修和 事故处理等的主要参考图。
安装接线图包括屏面布置图、屏背面接线图和端 子排图三个组成部分,它们相互对应,相互补充。
屏面布置图:说明屏上各个元件及设备的排列位置 和其相互间距离尺寸的图,要求按照一定的比例尺 绘制。
回路编号由4个及以下的数字组成,对于交流电 路为了区分相别,在数字前面还加上A、B、C、N等 文字符号。对于不同用途的回路规定了编号数字的范 围,对于一些比较重要的常见回路(例如直流正、负 电源回路,跳、合闸回路)都给予固定的编号。
华中科技大学电气学院
9
第二节 断路器的控制和信号回路
断路器的控制方式:集中控制和就地控制。
表明二次设备互相连接关系的电路称为二次接线或 二次系统。
二次接线图: 原理接线图、展开接线图和安装接线图。
华中科技大学电气学院
3
二、原理接线图
原理接线图:是用来表示继电保护、测量仪表和自 动装置等工作原理的一种二次接线图。
特点:二次回路中的元件及设备以整体形式表示, 同时将相互联系的电气部件和连线画在同一张图上, 给人以明确的整体概念。
15
5.熔断器与跳、合闸回路完整性的监视
监视方式:灯光监视、音响监视
二次配系统简介
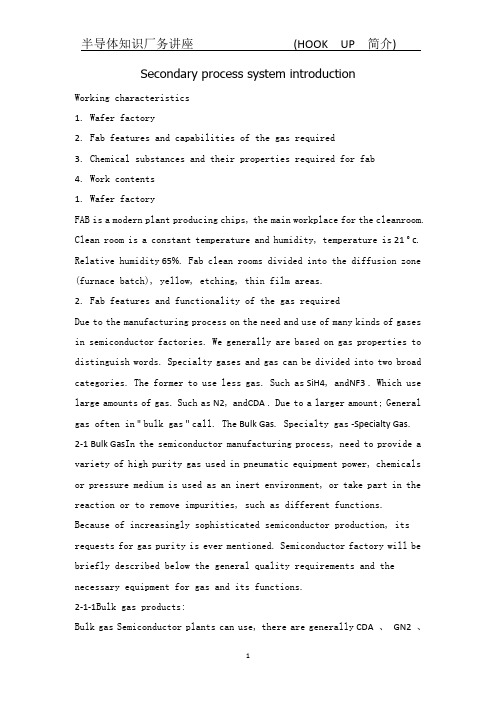
Secondary process system introductionWorking characteristics1. Wafer factory2. Fab features and capabilities of the gas required3. Chemical substances and their properties required for fab4. Work contents1. Wafer factoryFAB is a modern plant producing chips, the main workplace for the cleanroom. Clean room is a constant temperature and humidity, temperature is 21 ° c. Relative humidity 65%. Fab clean rooms divided into the diffusion zone (furnace batch), yellow, etching, thin film areas.2. Fab features and functionality of the gas requiredDue to the manufacturing process on the need and use of many kinds of gases in semiconductor factories. We generally are based on gas properties to distinguish words. Specialty gases and gas can be divided into two broad categories. The former to use less gas. Such as SiH4, and NF3 . Which use large amounts of gas. Such as N2, and CDA . Due to a larger amount; General gas often in " bulk gas " call. The Bulk Gas. Specialty gas -Specialty Gas.2-1 Bulk Gas In the semiconductor manufacturing process, need to provide a variety of high purity gas used in pneumatic equipment power, chemicals or pressure medium is used as an inert environment, or take part in the reaction or to remove impurities, such as different functions.Because of increasingly sophisticated semiconductor production, its requests for gas purity is ever mentioned. Semiconductor factory will be briefly described below the general quality requirements and the necessary equipment for gas and its functions.2-1-1Bulk gas products:Bulk gas Semiconductor plants can use, there are generally CDA 、GN2 、PN2 、PAr 、PO2 、PH2 、PHe 7 Species.2-1-2 Bulk gas manufacturing:<1> CDA/ICA(Clean Dry Air)Clean, dry air.CDA Sources taken from the air compressed by compressor dehumidifier, then by a filter or activated carbon adsorption to remove dust and hydrocarbons to supply the clean room CDA/ZCD 。
变电站二次系统介绍
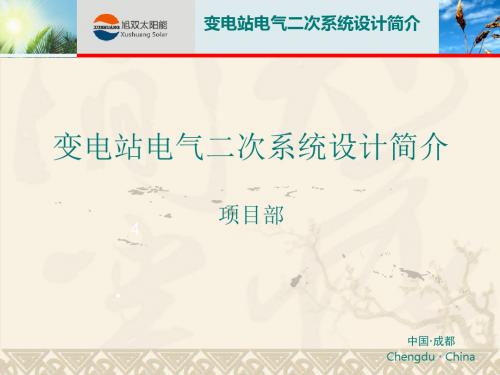
中国· 成都 Chengdu · China
变电站信号系统 8、直流系统相关断路器跳开或者熔断器熔 断充电机失电故障等,均应有相关告警信号 发出,并且应该设置有直流系统总告警信号 9、根据信号的不同性质,可以选择强电或 者弱电对信号量进行采集,弱电一般采用 ±48V以及±24V,由于电压低,因此弱电不 允许引出继保室,即不允许采集变电站场地 一次设备设备信号
中国· 成都 Chengdu · China
变电站控制系统
二、变电站控制系统
1、断路器控制回路需满足下列几点要求 能监视电源及跳合闸回路的完整性 能指示断路器跳合闸状态,并且在断路器发生 跳合闸时发出明显的信号 有防止断路器跳跃的装置 合闸或跳闸完成后,应使控制脉冲自动消失 接线应该简单可靠,电缆芯数尽量少
中国· 成都 Chengdu · China
中国· 成都 Chengdu · China
变电站测量系统
2、仪表的附件和配件的准确度等级
中国· 成都 Chengdu · China
电流互感
器铭牌
中国· 成都 Chengdu · China
变电站测量系统 3、仪表和互感器测量范围,宜选择在发电 机、主变压器、送配电线路等电 力设备额定 值运行及仪表指示在标度尺2/3以上时;对于 有可能过负荷运行的电 力设备和回路,测量 仪表宜留有适当的过负荷指示裕度 4、对重载起动的电动机以及有可能出现短 时冲击电流的电力设备和回路, 宜采用具有 过负荷标度尺的电流表
中国· 成都 Chengdu · China
变电站控制系统
5、具有分相操动机构的断路器,一般采用 三相联动的控制回路 机械联动 电气联动 6、采用液压、空气等操动机构的断路器, 在压力低至一定时,应分别闭锁重合闸、合 闸及跳闸 7、对电流或电压具有自保持特性的继电器, 在接线中应标明极性
二次配系统简介

1、风管的安装标高,对于矩形风管是从管底算起,而圆形风管是从风管中 心计算,在安装吊架时应引起注意。圆形风管的管径由大变小时,为保持 风管中心线的水平,托架的标高应按变径的尺寸相应地提高。 2、为保证法兰接口的严密性,法兰之间应有耐高温、防腐蚀PTFE密封垫。 制 在无特殊要求情况下,法兰垫料按标准选用。 程 3、 风管安装:根据施工现场情况,可以在地面连成一定的长度,然后采 排 用吊装的方法就位;也可以把风管一节一节地放在支架上逐节连接。一般 气 安装顺序是先干管后支管。应及时固定和调整支架,支架位置应准确,安 系 装应平整牢固,与管子接触应紧密。 统 4、对于暂时不安装的孔洞不要提前打开;暂停施工时,应加盖板,以防坠 人坠物事故发生。 5、 防火阀安装,方向位置应正确,易熔件应迎气流方向。排烟阀手动装 置(预埋导管)不得出现死弯及瘪管现象,手动密闭阀安装时阀门上标志 的箭头方向应与受冲击波方向一致。 6、安装必须牢固,位置、标高和走向符合设计要求,部件方向正确,操作 方便。防火阀检查孔的位置必须设在便于操作的部位。 9、洁净系统风管连接必须严密不漏;法兰垫料及接头方法必须符合设计要 求和施工规范规定。
程 所以人员必须按照规定的人员动线行进,从单一的管制口登记后进出,并接受管
排 制人员检查,服从管制。
气 禁止携入非必须用品,如香烟、打火机。非洁净纸张等物品。
系 统
洁净室内禁止吸烟,食用任何物品,禁止随意丢弃物品。 人员进入无尘室流程 1.在脱鞋区将鞋整齐放在鞋架上,赤脚(必须穿袜子)进入一次风淋室、接受工
安检查,填写登记表格。
2.口罩、网帽、无尘服、鞋、手套、安全帽依次按规定穿戴整齐,二次洗手烘干,
进入二次风淋室。
3.严禁穿洁净服出入室外,从其他物料口出入。
半导体二次配系统介绍
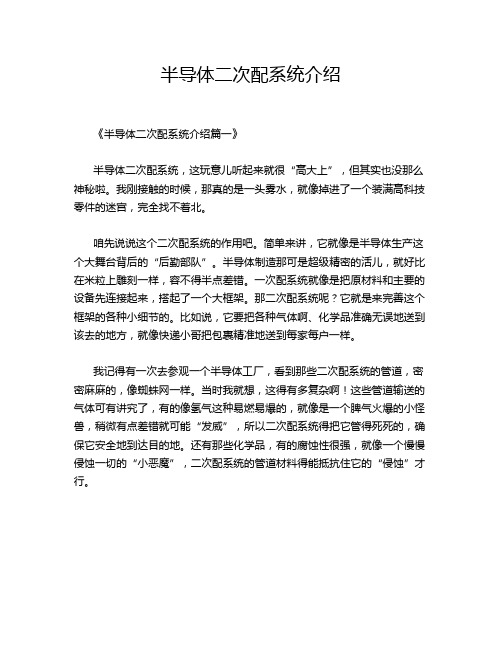
半导体二次配系统介绍《半导体二次配系统介绍篇一》半导体二次配系统,这玩意儿听起来就很“高大上”,但其实也没那么神秘啦。
我刚接触的时候,那真的是一头雾水,就像掉进了一个装满高科技零件的迷宫,完全找不着北。
咱先说说这个二次配系统的作用吧。
简单来讲,它就像是半导体生产这个大舞台背后的“后勤部队”。
半导体制造那可是超级精密的活儿,就好比在米粒上雕刻一样,容不得半点差错。
一次配系统就像是把原材料和主要的设备先连接起来,搭起了一个大框架。
那二次配系统呢?它就是来完善这个框架的各种小细节的。
比如说,它要把各种气体啊、化学品准确无误地送到该去的地方,就像快递小哥把包裹精准地送到每家每户一样。
我记得有一次去参观一个半导体工厂,看到那些二次配系统的管道,密密麻麻的,像蜘蛛网一样。
当时我就想,这得有多复杂啊!这些管道输送的气体可有讲究了,有的像氢气这种易燃易爆的,就像是一个脾气火爆的小怪兽,稍微有点差错就可能“发威”,所以二次配系统得把它管得死死的,确保它安全地到达目的地。
还有那些化学品,有的腐蚀性很强,就像一个慢慢侵蚀一切的“小恶魔”,二次配系统的管道材料得能抵抗住它的“侵蚀”才行。
也许有人会说,二次配系统不就是些管道和连接装置嘛,有那么重要吗?嘿,这可就大错特错了。
要是没有二次配系统,那些昂贵的半导体制造设备就像是没了粮草的士兵,根本没法正常工作。
你想啊,设备都“饿肚子”了,还怎么生产出那些高科技的半导体芯片呢?这就好比你要做饭,没有燃气或者水,那你只能干瞪眼。
从技术层面来说,二次配系统的设计也是很有挑战性的。
它得考虑到流量的控制,就像控制水龙头流水的大小一样。
流量太大了,可能会把设备给“撑坏”;流量太小了,又达不到生产的要求。
而且不同的生产环节对气体和化学品的纯度要求也不一样,这就像是不同的人对食物的口味要求不同一样。
二次配系统就得像个超级大厨,能根据需求调整“菜肴”的“口味”。
这中间的技术难度啊,可能只有那些真正搞这个的工程师才能深刻体会到。
- 1、下载文档前请自行甄别文档内容的完整性,平台不提供额外的编辑、内容补充、找答案等附加服务。
- 2、"仅部分预览"的文档,不可在线预览部分如存在完整性等问题,可反馈申请退款(可完整预览的文档不适用该条件!)。
- 3、如文档侵犯您的权益,请联系客服反馈,我们会尽快为您处理(人工客服工作时间:9:00-18:30)。
Secondary process system introductionWorking characteristics1. Wafer factory2. Fab features and capabilities of the gas required3. Chemical substances and their properties required for fab4. Work contents1. Wafer factoryFAB is a modern plant producing chips, the main workplace for the cleanroom. Clean room is a constant temperature and humidity, temperature is 21 ° c. Relative humidity 65%. Fab clean rooms divided into the diffusion zone (furnace batch), yellow, etching, thin film areas.2. Fab features and functionality of the gas requiredDue to the manufacturing process on the need and use of many kinds of gases in semiconductor factories. We generally are based on gas properties to distinguish words. Specialty gases and gas can be divided into two broad categories. The former to use less gas. Such as SiH4, andNF3 . Which use large amounts of gas. Such as N2, andCDA . Due to a larger amount; General gas often in " bulk gas " call. The Bulk Gas. Specialty gas -Specialty Gas.2-1 Bulk GasIn the semiconductor manufacturing process, need to provide a variety of high purity gas used in pneumatic equipment power, chemicals or pressure medium is used as an inert environment, or take part in the reaction or to remove impurities, such as different functions.Because of increasingly sophisticated semiconductor production, its requests for gas purity is ever mentioned. Semiconductor factory will be briefly described below the general quality requirements and the necessary equipment for gas and its functions. 2-1-1Bulk gas products:Bulk gas Semiconductor plants can use, there are generally CDA 、GN2 、PN2 、PAr 、PO2 、PH2 、PHe 7 Species.2-1-2 Bulk gas manufacturing:<1> CDA/ICA(Clean Dry Air)Clean, dry air.CDASources taken from the air compressed by compressor dehumidifier, then by a filter or activated carbon adsorption to remove dust and hydrocarbons to supply the clean room CDA/ZCD 。
CDA System:Air compressor Buffer storage tank cooling dryerFilter CDA<2> GN2Compressed using compressor cooling gas into liquid gas. Catalytic converter, CO reaction to CO2, H2, reaction to H2O, then sieve absorption of CO2, andH2O And then slip separation O2&CnHm.N2=°C O2=-183°CPN2GN2 Through the Purifier (Purifier) Purification, producing high purity N2 。
Liquid original nitrogen %After purification for purification of nitrogen %GN2&PN2 System(See attached map)<3> PO2Compressor compressed cooled gas into liquid gas, awarded by second slip 99% Above in purity O2 And then drop N2 、Ar 、CnHm 。
Another by electrolytic dissociationH2&O2PO2 System(See photos)<4> PArCompressor compressed cooled gas into liquid gas, awarded by second slip % More purity argon. Ar content in the air is only %. Production costs are relatively high. PAr System (See attached map)<5> PH2Compressor compressed cooled gas into liquid gas, awarded by second slip % Abovein purity H2 。
Also by H2O electrolytic dissociation H2&O2. High hazard manufacturing cheap but easy to trigger explosions.PH2 System (See attached map)<6> PHeRare and rich He Extracted from natural gas, its main origin for the United States, and Russia. Air compressors compressed cooled gas in liquid, easily obtained from the slip.He lium=°C Methane (Methane)= °CPHe System (See attached map)2-1-3 Use of bulk gases in semiconductor plantsCDAMain supply FAB Pneumatic device powered air source and blowing (Purge),Local Scurruber Fuel it.ICAMain facility system pneumatic equipment-powered gas source and blowing.N2Main supply part of the pneumatic equipment air supply or supply blowing and dilute source of pressure of inert gas and chemical delivery.O2Supply ETCH -Process oxidizer needed and CPCVD Supplies oxidation process with business routine supply O3 Generator Required O2 Supplies and other processes required.ArSupply Sputter Manufacturing process and ion sputtering heat transfer media Chamber Dilution and inert gas environment.H2Feeding tube devices burning mix of oxygen, POLY Manufacturing process H2 BAKE Purposes. W-PLUG manufacturing process as WF6 for the reduction of gas and other processes.HePressure medium supply chemicals and processing chips cool.Bulk GasAlthough not as Specialty Gas , Some with highly toxic and corrosive. But we still need to pay attention to safety using a bulk gas. GN2, andPN2, andPAr, andPHe has the danger of suffocating, that gas is colorless and odorless, massive emission of lead in the air contain O2 ( Usually 21%), decreased to 16% below, namely, headachesand nausea. Dang O2 less to 10% Shi, who will be in a State of the will is not clear,6% , instantly Faints, unable to breathe,6 minutes less than death. PH2 due to leakage or when mixing, concentration of his own as long as the H2 of the blast RADIUS(4%-75%) (air), if they got the fire burning this gas is mixed. PO2 will make material easily oxidized to yield burning, causing fire mishap. Therefore, our works in the semiconductor, in the design, construction, and how to avoid leaks, and how to protect themselves from, you are one of our hard work.2-2 Specialty GasUsed by the semiconductor factory Specialty Gas A wide range of about 40 or 50, according to risks can be divided into the following categories:2-2-1 Flammable gasesWhen some leaks gas when mixed with, as long as his own concentration in a certain range (air), if they got the fire, this gas is burning from the mix. This called the explosion of the gas range. Such as:SiH4 %-100% SiH2CL2 %% PH3 %-100%2-2-2 Low pressure gasSome gases under normal for the viscous liquid gas at room temperature of saturated vapor pressure is less than 10Psi , Can also interfere with pipeline blocked, need to pack heat, improving the air vapor pressure can be an adequate supply of gas. For example:DCS, andCLF3, andWF62-2-3 Toxic gasSome gases due to its strong reaction of animals (including humans) respiratory and mucous membranes, skin and other features with a strong impact. Such as:NF3,PH3 2-2-4 Corrosive gasesSome gas and water effects, that is produced by hydrolysis HCL HF Acidic substances such as, the human body (including eyes, nose, skin, respiratory system, etc) and equipment (such as piping and valves) have a corrosive effect. This gas has the following:<1> HCL、CL2 、SiH2CL2 、BCL3 CL Elements of gas---HCL<2> BF3、SiF4 、WF6 F Element---HF<3> NH3---Ammonia water Very irritating2-2-5 Asphyxiant gasesSuch as: CO2 、CF4 、C2F6 Such gases, odorless and tasteless. If a large number of emission of air caused by O2 content reduced to 16% when the headache and nausea. Dang O2 less to 10% Shi, who will be in a State of the will is not clear,6% , instantly Faints, unable to breathe,6 minutes less than death.2-2-6 Spontaneous combustion gasesSome of the gases, mixed with the air, even without the fire catches fire spontaneously burst into flames. This is called spontaneous combustion gases. Its fire at room temperature. This gas are:SiH4、PH3 、B2H6Though we cannot exclude these gases can cause various adverse effects on us. But we working in semiconductor plants, may be included in the design, construction, and stop loss. To avoid leaks, he stressed.3.Fabs require chemical substances and their properties3-1 Types of chemicals (solvents)C260、EKC-270 、NMP 、OK-73 、A515 、IPA In addition to EKC-270 PFA/304 BA Tube, others use 316L EP Tube. Take over the way with VMB outlet and the machine inlet side takes over.3-2 Chemical species (pH class)HF1%、HF49% 、H2O2 、NH4OH29% 、DEVELOPER 、M1 、BOE 200:1 、BOE 500:1、BOE 50:1 、HNO3 、HCL 、H3PO4 、H2SO4 。