胶合板课程设计 人造板工艺学 共34页
人造板课程设计

《胶合板生产工艺学》课程设计说明书项目名称:年产2万立方米胶合板生产工艺设计设计学生:班级:学号:指导老师:年月日目录1.设计任务书 32.生产大纲拟定 53.工艺过程 74.原材料计算 7 4.1木材需要量的计算 74.2胶料需要量的计算 105.设备需要量的计算 106.车间设备布置 16《胶合板生产工艺学》课程设计任务书产品种类:年产量2万m³胶合板合计(%) 规格名称占总产量的百分比(%)树种椴木70 100水曲柳30幅面1220X2440(4’x8’) 70 100 915X1830(3’x6’) 30厚度3mm(三层) 70 100 5mm(五层)30胶种脲醛树脂胶各种规格胶合板在总产量中的占得份额胶种脲醛树脂胶树种椴木水曲柳幅面4’x8’3’x6’4’x8’3’x6’三层34.3 14.7 14.7 6.3五层14.7 6.3 6.3 2.7合计70 30总计100编号规格树种幅面厚度第一种椴木4’x8’三层第二种椴木4’x8’五层第三种椴木3’x6’三层第四种椴木3’x6’五层第五种水曲柳4’x8’三层第六种水曲柳4’x8’五层第七种水曲柳3’x6’三层第八种水曲柳3’x6’五层设计名称:年产2万m³胶合板的生产工艺设计一、课程设计内容胶合板生产工艺一般包括以下内容:●根据产品品种拟定工艺流程;●计算原材料(包括木材、胶粘剂和其他辅助材料)消耗;●设备选型;●绘制车间工艺布置图;●编写工艺设计文字说明二、课程设计的要求:设计说明书一份一、 生产大纲的拟定1、根据产品规格选择热压机型号热压机生产某一种规格的产品时,生产率计算公式如下:Q i =T ·N ·m ·δ·Fo ·K Z 1+Z 2(米3/班)式中:T ——班工作时间(分) N ——热压机的工作间隔数m ——每间隔中压制的胶合板张数 δ——胶合板的成品厚度(米)Fo ——成品胶合板的幅面(米²)K ——热压机的工作时间利用系数K=0.97~0.98Z 1——胶合板在压机中的保压时间(设计按每毫米成品厚,压1分钟计)(分)Z 2——辅助操作时间(分):这一项包括装卸压机闭合和升压所需的时间。
人造板课程设计-文档

1.截锯机对年产量为二万立方米的胶合板厂(或车间)一般只需要?台截锯机。
2.剥皮机国内尚无定型产品,各使用厂可自行设计,而生产率则可根据设计数据求出。
3.蒸煮池N=QTVK+(1~3)只式中:N——所需的蒸煮池数量(只)Q——每小时的木段耗量(米3 /班)T——蒸煮周期(包括装、出池时间)(小时)椴木:24小时,40℃水曲柳:36小时,85℃V——蒸煮池容积(米3)K——蒸煮池充满系数,一般取K=0.5~0.6椴木:N1=水曲柳:N2=所以,N总=N1+N2+2=4.旋切机选?生产率Q=ZV·K/T(米3 /班)式中:Z——班工作时间(分)7.5*60=450分T——旋切一根木段所需要的时间(分)2分(其中旋切时间占1’38)V——一根木段的平均材积(米3)K——工作时间利用系数(K=0.8~0.85)Q=?(米3 /班)所需旋切机台数:N=V1/Q·n(台)式中:V1——一天内需在该型号旋切机上加的木段材积(米3)n ——旋切机工作班次椴木:Q=水曲柳:Q=N=?,取?台5.干燥机选?生产率:Q=T·K1·K2·m·S·B·u(米3/班)式中:T ——各班工作时间(分) T=450min K1——工作时间利用系数K1=0.9~0.95 K1=0.9K2——干燥机的进料充满系数,横向连续进料K2=0.9~0.95,K2=0.9 非连续进料时K2=0.8~0.85m ——干燥机层数m=1S ——单板厚(米)S=0.001mB ——每层干燥机上的单板宽(米):连续进料时B即为单板带宽度,非连续进料时B为干燥机的有效工作宽度。
B=2.5m u ——干燥机的进料速度(米/分)u=9m/min Q=?(米3/班)所需要干燥机台数:N=V/Q(台)式中:V——每班需干燥的单板材积(米3/班)V=26.87(米3/班)N=V/Q=?,取?台6.拼缝机选?%优等品%一等品生产率:Q=T·u·K/L·n(张/班)(纵拼机)式中:T——班工作时间(分)T=450minu——进料时间u=20m/minK——机床利用系数K=0.8~0.9 K=0.8L——单板长度(米)L=2500·10-3mn——一张单板的平均拼缝条数n=2Q1=Q2=Q cp=所需台数:N=V/Q式中:V——每班(纵拼机)或每小时(横拼机)所需拼的单板张数。
(完整版)人造板工艺学

一、名词解释1、人造板:人造板是以木材或其他纤维植物为原料,通过专门的工艺加工成单板、纤维或刨花,施加或不加胶粘剂,经过成型(或组坯)、热(冷)压所制成的一类板材。
2、胶合板:把由原木旋切或刨切成的单板按一定规则胶合起来形成的板材。
3、单板层积材(LVL):将单板基本按对称原则和沿长度方向顺纹排列的原则胶合而成的板材。
4、纤维板 : 以木材或其它非木材植物纤维原料,经分离纤维、干燥、铺装、热压而制成的板材。
5、刨花板、碎料板:以小径木、间伐材、人工速生林为原料,通过刨片机加工成刨花,然后经过干燥、施胶、铺装板坯、热压制成的板材。
6、华夫板:用扁平大片刨花胶合而成的板材。
7、E0级刨花板:甲醛释放量低于5mg/100mg的刨花板8、静曲强度(MOR :静曲强度是指人造板抵抗外力而不破坏的最大能力。
9、弹性模量(MOE:)弹性模量是人造板在比例极限内应力与应变的关系。
10、内结合强度(IB):内结合强度是测定人造板胶接性能的重要指标表面结合强度:表面结合强度是测定人造板表面性能的指标11、蠕变:人造板是弹塑性材料,当人造板在弯曲载荷作用下,除产生弹性变形外,还会产生塑性变形,人造板变形随时间的延长,变形增加,这种现象称为人造板的蠕变。
12、握钉力:人造板对钉子的握持能力称为握钉力绝对握钉力:指拔出钉子的最大阻力值比握钉力:指最大拔出阻力与钉子钉入部分展开表面积的比值握螺钉力:指人造板对木螺钉的握持能力13、胶合强度:胶合板试件承受平行于板面的拉力作用时,胶层抵抗剪切破坏力的能力。
14、胶合板的比强度:比强度是强度与密度的比值。
该比值反映了某些运动构件材料的重要特性。
硬度:抵抗其他不会产生残余变形物体凹入的能力耐磨性:指板抵抗磨损的能力抗冲击强度:人造板的抗冲击强度反映了产品抵抗动载荷破坏的能力工艺性质:是人造板的可加工性能(机械加工性能、拼缝的性能和表面装饰性能)15、集成材(Glued Laminated Timber):是一种沿板材或枋材平行纤维方向,用胶粘剂沿其长度、宽度或厚度方向胶合而成的实木板枋材。
【课程大纲】《人造板工艺学实习》
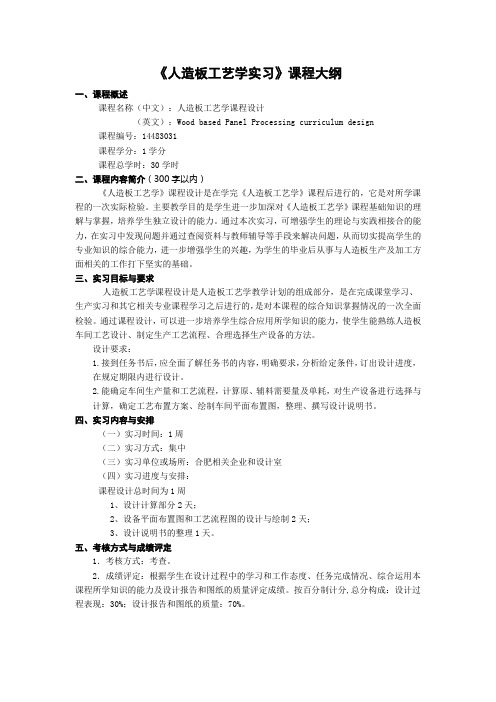
一、课程概述课程名称(中文):人造板工艺学课程设计(英文):Wood based Panel Processing curriculum design 课程编号:14483031课程学分:1学分课程总学时:30学时二、课程内容简介(300字以内)《人造板工艺学》课程设计是在学完《人造板工艺学》课程后进行的,它是对所学课程的一次实际检验。
主要教学目的是学生进一步加深对《人造板工艺学》课程基础知识的理解与掌握,培养学生独立设计的能力。
通过本次实习,可增强学生的理论与实践相接合的能力,在实习中发现问题并通过查阅资料与教师辅导等手段来解决问题,从而切实提高学生的专业知识的综合能力,进一步增强学生的兴趣,为学生的毕业后从事与人造板生产及加工方面相关的工作打下坚实的基础。
三、实习目标与要求人造板工艺学课程设计是人造板工艺学教学计划的组成部分,是在完成课堂学习、生产实习和其它相关专业课程学习之后进行的,是对本课程的综合知识掌握情况的一次全面检验。
通过课程设计,可以进一步培养学生综合应用所学知识的能力,使学生能熟练人造板车间工艺设计、制定生产工艺流程、合理选择生产设备的方法。
设计要求:1.接到任务书后,应全面了解任务书的内容,明确要求,分析给定条件,订出设计进度,在规定期限内进行设计。
2.能确定车间生产量和工艺流程,计算原、辅料需要量及单耗,对生产设备进行选择与计算,确定工艺布置方案、绘制车间平面布置图,整理、撰写设计说明书。
四、实习内容与安排(一)实习时间:1周(二)实习方式:集中(三)实习单位或场所:合肥相关企业和设计室(四)实习进度与安排:课程设计总时间为1周1、设计计算部分2天;2、设备平面布置图和工艺流程图的设计与绘制2天;3、设计说明书的整理1天。
五、考核方式与成绩评定1.考核方式:考查。
2.成绩评定:根据学生在设计过程中的学习和工作态度、任务完成情况、综合运用本课程所学知识的能力及设计报告和图纸的质量评定成绩。
人造板工艺学课程设计

人造板工艺学课程设计专业: 木材科学与工程班级:姓名:学号:指导老师:目录............................................................. 3一、计条件和设计内容(一)设计目的.. (3)(二)设计条件 (3)(三)设计内容 (3)................................................ 4二、细木工板的生产工艺流程设计(一)生产工艺流程 (4)(二)主要工序参数 (4)..................................... 8 三、干法中密度纤维板的生产工艺流程设计(一)生产工艺流程 (8)(二)主要设备 (8)(三)工艺说明 (8).................................................... 10 四、制造刨花板生产工艺流程(一)生产工艺流程. (10)(二)主要设备 (10)(三)工艺说明 (11)(四)主要工序的参数.............................................................................. 11 ............................. 14 五、以稻壳为原料模压成型的生产工艺流程设计(一)生产工艺流程. (14)(二)主要设备 (14)(三)工艺说明.......................................................................................... 15 51.................................................................................. (四)主要工序参数.一、计条件和设计内容(一)设计目的通过进行人造板生产工艺流程设计,加深所学过的有关人造板生产理论和工艺知识,进一步明确不同种类胶合板,刨花板,纤维板各自不同的生产工艺流程,体现不同的原料要求不同的工艺和设备。
(完整word版)福建农林大学人造板工艺学课程实验设计说明书

福建农林大学材料工程学院人造板工艺学课程设计说明书课程名称人造板工艺学课程设计专业年级姓名学号教师成绩日期 2014 年 7月 10日年产30000m3刨花板生产线工艺设计1,设计要求1.1 ,年产30000m3渐变结构刨花板车间工艺布置图1.2,原料:小径原木马尾松,胶合板木芯1.3,生产方法:连续式平压机1.4,产品规格:2440×1220×16mm 密度:0.75g/cm3 含水率:10%1.5,生产质量:符合GB/T4897-032,设计方案2.1工艺流程图2.2,工艺参数2.2.1,原材料2.2.1.1,主要原料来源:马尾松绝干密度:0.44g/cm3 含水率:60% 2.2.1.2,辅助材料胶黏剂:固含量为60%的脲醛树脂胶用量为绝干刨花的10%固化剂:氯化铵溶液用量为固态胶黏剂的1%防水剂:石蜡乳液用量为绝干刨花的1%捕捉剂:氨水溶液用量为固态胶黏剂的5%2.2.2施胶量:表层刨花12% 芯层刨花8%2.2.3板坯表芯层刨花量:表层刨花40% 芯层刨花60%2.2.4单层连续式热压机压力P=3.0MPa 温度T=200℃加压时间t=0.4min/mm 2.2.5转子式干燥机压力P=1.3MPa干燥前刨花含水率=60%干燥后刨花含水率=5%3设计验算3.1制定和验算生产能力热压机幅面宽2540mm ,毛板厚度17mm完成产品设计产量,热压机输送带理论运行速度0745.298.0016.044.2605.2228030000'=⨯⨯⨯⨯⨯==YTBHK Q μm/min 式中:μ——热压机理论运输平均速度;Q ——年产量,设计任务书给定量30000 m 3; T ——日工作时,22.5小时; B ——刨花板净宽,取 2.44m ; H —- 刨花板净厚,取0.016 m ;K ——压机工作时间利用系数,为0.96~0.98 这里取0.98; Y ——车间年工作日,取280 d ;热压机输送带理论平均运行速度min /205.210174.0150003"m h t L =⨯⨯=⨯=-μ取热压机真正运行速度'μ<μ<"μ 取μ=2.2m/mina m BHK YT Q /32.3519098.0017.054.22.2605.222803=⨯⨯⨯⨯⨯⨯==μ考虑砂光量和裁边量,规格锯割量10%,产品合格率为98%,则实际年产量 Q =35190.32×(1-10%)×0.98=31037.86m 3 >30000m ³满足条件3.2 原、辅材料的需求量以年产3万m 3单层连续式压机生产线为设计依据,计算厚度为17mm ,计算密度为750kg /m 3,工作制度:年工作日为280天,每天3班,每天有效工作小时为22.5小时,毛板含水率10%,胶耗量为绝干刨花重的10%,防水剂石蜡耗量为绝干刨花重的1%,固化剂耗量为胶耗量的1%,捕捉剂耗量为胶耗量的5%。
人造板工艺学课程
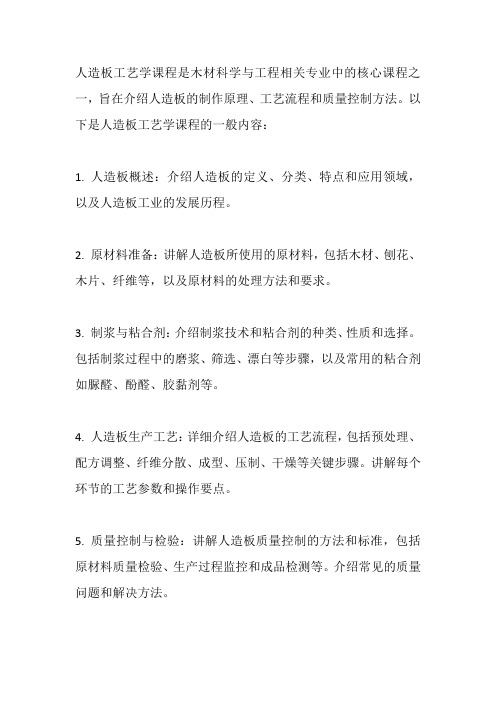
人造板工艺学课程是木材科学与工程相关专业中的核心课程之一,旨在介绍人造板的制作原理、工艺流程和质量控制方法。
以下是人造板工艺学课程的一般内容:
1. 人造板概述:介绍人造板的定义、分类、特点和应用领域,以及人造板工业的发展历程。
2. 原材料准备:讲解人造板所使用的原材料,包括木材、刨花、木片、纤维等,以及原材料的处理方法和要求。
3. 制浆与粘合剂:介绍制浆技术和粘合剂的种类、性质和选择。
包括制浆过程中的磨浆、筛选、漂白等步骤,以及常用的粘合剂如脲醛、酚醛、胶黏剂等。
4. 人造板生产工艺:详细介绍人造板的工艺流程,包括预处理、配方调整、纤维分散、成型、压制、干燥等关键步骤。
讲解每个环节的工艺参数和操作要点。
5. 质量控制与检验:讲解人造板质量控制的方法和标准,包括原材料质量检验、生产过程监控和成品检测等。
介绍常见的质量问题和解决方法。
6. 环境保护与安全:强调人造板生产中的环境保护和安全问题,如废气处理、废弃物处置、粉尘防护、火灾防护等。
7. 人造板工艺改进与创新:探讨人造板工艺技术的改进和创新方向,如新型粘合剂研发、生产自动化、节能减排等。
8. 实践与案例分析:开展实验室实践和工厂参观,进行人造板样品制作和测试,以及实际工艺问题的案例分析。
通过人造板工艺学课程的学习,学生将了解人造板的生产过程和关键技术,掌握质量控制的方法和工艺改进的思路,为从事相关行业的工作和研究提供基础知识和技能。
人造板工艺学课程设计
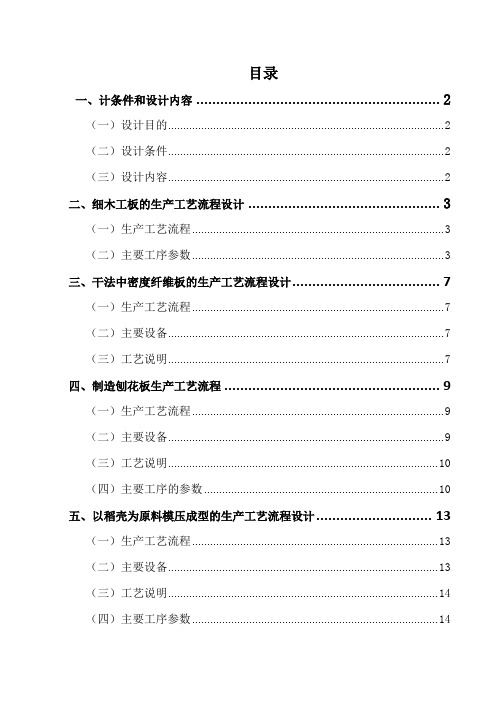
预压方式:周期式平面预压和连续式预压。
设备:辊式连续预压机和履带式预压机。
(6)板坯热压:
工艺要求:刨花板热压温度:140~160℃(UF), 188~200℃(PF);
热压压力:1.2~4.0Mpa热压时间:0.5~0.9(min/mm)。
生产上希望制得施胶量小而强度高、质量好、成本低的刨花板,因此施胶工序和设备都要严格操作,而且正确选定刨花和胶量的合适比例,以及使胶液均匀的分散到大量的刨花面上。本工艺中采用摩擦法施胶。刨花热压之前要预压,可以防止热压时水分冲出损伤板坯,缩短生产周期,防止固化层的出现,还可以增加板子的强度。
(四)主要工序的参数
一、计条件和设计内容
(一)设计目的
通过进行人造板生产工艺流程设计,加深所学过的有关人造板生产理论和工艺知识,进一步明确不同种类胶合板,刨花板,纤维板各自不同的生产工艺流程,体现不同的原料要求不同的工艺和设备。
(二)设计条件
1、以杨木为原料制造细木工板的生产工艺流程;
2、以棉杆为原料制造中密度纤维板的生产工艺流程;
(1)刨花制备:
工艺过程:
枝丫材、小径材和森林采伐剩余物削片机湿木料仓
双鼓轮刨片机湿刨花料刨花干燥
机械干燥气流分选打磨机
表层细料芯层细料
(2)刨花干燥:
目的:合理控制刨花含水率;使刨花含水率均匀一致。
要求:三层结构刨花板:表层刨花含水率为4~6%;芯层刨花含水率为2~4%。
单层结构刨花板:含水率为3~5%。
(三)工艺说明
刨花板生产的原料要求是材性相同或相近,针阔叶材不宜混用,单一树种最好。工厂刨花搭配使用,大片刨花板的原料要剥皮或者树皮用量小于10%,且刨花原料的含水率要控制在40%--60%。三层刨花板的表层含水率控制在4%--6%,芯层控制在2%--4%。刨花的尺寸,刨花原料的初含水率,干燥剂的进料装置干燥机的外界条件都要严格控制,否则影响刨花干燥的质量。
胶合板课程设计

胶合板课程设计一、课程目标知识目标:1. 学生能理解并掌握胶合板的定义、分类及用途。
2. 学生能描述胶合板的制作工艺流程,了解其原材料及性质。
3. 学生能了解我国胶合板产业现状及其在国民经济中的作用。
技能目标:1. 学生能通过观察、触摸等方式,辨别不同类型的胶合板。
2. 学生能运用所学知识,分析胶合板的优缺点,并能在实际应用中提出改进措施。
3. 学生能运用胶合板制作简单的家具或模型,提高动手实践能力。
情感态度价值观目标:1. 学生培养对木材资源的珍惜和合理利用意识,增强环保观念。
2. 学生通过了解我国胶合板产业的发展,激发民族自豪感,培养家国情怀。
3. 学生通过实际操作,体验胶合板制作的乐趣,培养对木工工艺的兴趣。
课程性质:本课程属于技术与设计领域,注重理论知识与实践操作相结合。
学生特点:五年级学生对新鲜事物充满好奇心,具备一定的动手能力,喜欢实践操作。
教学要求:结合学生特点,以实践为主,理论联系实际,培养学生的动手操作能力和创新意识。
通过课程学习,使学生能够将所学知识应用于实际生活,提高生活品质。
教学过程中,关注学生的情感态度价值观的培养,提升其综合素质。
将课程目标分解为具体的学习成果,便于教学设计和评估。
二、教学内容1. 胶合板的定义与分类- 介绍胶合板的定义,了解其作为一种人造板材的特点。
- 分类介绍不同类型的胶合板,如素板、饰面板、防火板等。
2. 胶合板制作工艺流程- 详细讲解胶合板的制作工艺,包括原木加工、刨片、施胶、热压等环节。
- 分析各环节对胶合板质量的影响,探讨提高产品质量的方法。
3. 胶合板原材料及性质- 介绍常用木材作为胶合板原材料的种类、特点及其对胶合板性质的影响。
- 分析胶粘剂的选择和使用,了解不同胶粘剂对胶合板性能的影响。
4. 胶合板的应用与优缺点- 探讨胶合板在建筑、家具、船舶等领域的应用。
- 分析胶合板的优缺点,如强度高、变形小、成本低等。
5. 胶合板产业现状与环保意识- 了解我国胶合板产业的发展现状、市场前景及在国际市场的地位。
胶合板制造工艺学
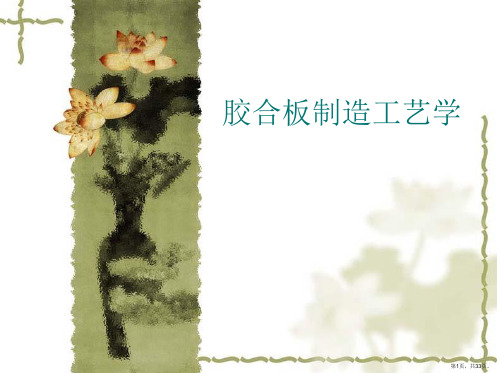
在于细胞壁内,失去吸着水,
℃ %
( )
木材就会发生干缩。这一阶 )
段时间很短。
干燥时间(min)
第9页,共33页。
III 减速干燥期 (1)减速干燥第一阶段:
蒸发掉全部自由水和大部分吸着水,在此阶段单板表面 水分的蒸发速度和单板里面水分向外传导的速度已经不相适 应了,单板干燥速度开始下降。
在此阶段热空气供给的热量
一般管孔粗大的树种,水分排出阻力小,所以干燥速度快(如水曲柳), 相反管孔细小树种排除阻力大,干燥速度慢(如椴木),水曲柳、桦木、椴 木、杨木干燥速度依次为水曲柳>桦木>椴木>杨木,因此不同树种干燥速 度不同,不能同时进行干燥。
第19页,共33页。
⑵ 初含水率 初含水率高,干燥速度慢。
⑶单板厚度 单板在干燥过程中,水分主要是沿厚度
❖ ⑵ 如果含水率过高,在热压过程中易产生分层鼓泡。 ❖ ⑶ 如果含水率过高,热压胶合后胶合板含水率很低,要排除
更多水分,在胶合板热压胶合过程中,各层单板收缩变形很大, 因此胶合板内应力较大,易变形。
❖ ⑷ 如果含水率过高,胶固化不充分,胶合强度不好。
❖ (5) 湿单板在贮存中易产生边缘开裂、中间发霉变色等缺陷。
(一)按传热方式分: 空气对流式
接触式
联合式
(二)按单板传送方式: 网带式 辊筒式
(三)按干燥机内热空气流动方向与干燥机纵向中心线之间的关系
纵向通风 横向通风: 气流气流平行于单板表面
气流与单板便面垂直喷射
第22页,共33页。
二、喷气式网带干燥机
1
23 45 6 7
8
9
1-电动机 2-排湿管 3-离心式风机 4-网带 5-喷气箱 6-加热器 7-蒸气管 8-单板 9-新鲜空气入口
人造板工艺学课程设计
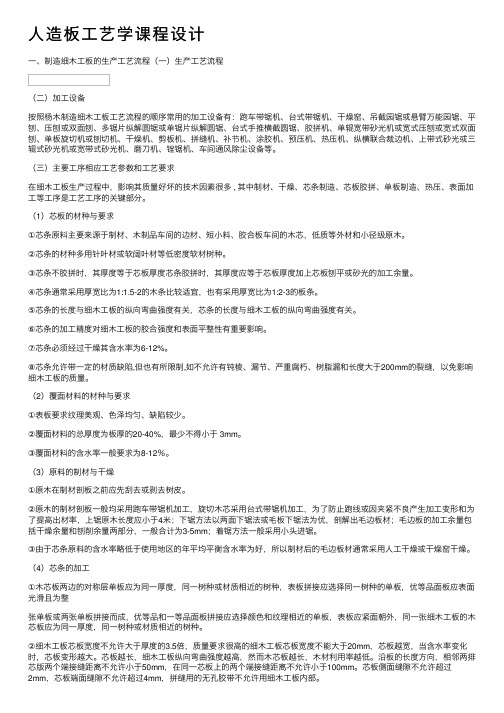
⼈造板⼯艺学课程设计⼀、制造细⽊⼯板的⽣产⼯艺流程(⼀)⽣产⼯艺流程(⼆)加⼯设备按照杨⽊制造细⽊⼯板⼯艺流程的顺序常⽤的加⼯设备有:跑车带锯机、台式带锯机、⼲燥窑、吊截园锯或悬臂万能园锯、平刨、压刨或双⾯刨、多锯⽚纵解圆锯或单锯⽚纵解圆锯、台式⼿推横截圆锯、胶拼机、单辊宽带砂光机或宽式压刨或宽式双⾯刨、单板旋切机或刨切机、⼲燥机、剪板机、拼缝机、补节机、涂胶机、预压机、热压机、纵横联合裁边机、上带式砂光或三辊式砂光机或宽带式砂光机、磨⼑机、锉锯机、车间通风除尘设备等。
(三)主要⼯序相应⼯艺参数和⼯艺要求在细⽊⼯板⽣产过程中,影响其质量好坏的技术因素很多 , 其中制材、⼲燥、芯条制造、芯板胶拼、单板制造、热压、表⾯加⼯等⼯序是⼯艺⼯序的关键部分。
(1)芯板的材种与要求①芯条原料主要来源于制材、⽊制品车间的边材、短⼩料、胶合板车间的⽊芯,低质等外材和⼩径级原⽊。
②芯条的材种多⽤针叶材或软阔叶材等低密度软材树种。
③芯条不胶拼时,其厚度等于芯板厚度芯条胶拼时,其厚度应等于芯板厚度加上芯板刨平或砂光的加⼯余量。
④芯条通常采⽤厚宽⽐为1:1.5-2的⽊条⽐较适宜,也有采⽤厚宽⽐为1:2-3的板条。
⑤芯条的长度与细⽊⼯板的纵向弯曲强度有关,芯条的长度与细⽊⼯板的纵向弯曲强度有关。
⑥芯条的加⼯精度对细⽊⼯板的胶合强度和表⾯平整性有重要影响。
⑦芯条必须经过⼲燥其含⽔率为6-12%。
⑧芯条允许带⼀定的材质缺陷,但也有所限制,如不允许有钝棱、漏节、严重腐朽、树脂漏和长度⼤于200mm的裂缝,以免影响细⽊⼯板的质量。
(2)覆⾯材料的材种与要求①表板要求纹理美观、⾊泽均匀、缺陷较少。
②覆⾯材料的总厚度为板厚的20-40%,最少不得⼩于 3mm。
③覆⾯材料的含⽔率⼀般要求为8-12%。
(3)原料的制材与⼲燥①原⽊在制材剖板之前应先刮去或剥去树⽪。
②原⽊的制材剖板⼀般均采⽤跑车带锯机加⼯,旋切⽊芯采⽤台式带锯机加⼯,为了防⽌跑线或因夹紧不良产⽣加⼯变形和为了提⾼出材率,上锯原⽊长度应⼩于4⽶;下锯⽅法以两⾯下锯法或⽑板下锯法为优,剖解出⽑边板材;⽑边板的加⼯余量包括⼲燥余量和刨削余量两部分,⼀般合计为3-5mm;着锯⽅法⼀般采⽤⼩头进锯。
(完整版)人造板工艺学

(完整版)人造板工艺学一、名词解释1、人造板:人造板是以木材或其他纤维植物为原料,通过专门的工艺加工成单板、纤维或刨花,施加或不加胶粘剂,经过成型(或组坯)、热(冷)压所制成的一类板材。
2、胶合板:把由原木旋切或刨切成的单板按一定规则胶合起来形成的板材。
3、单板层积材(LVL):将单板基本按对称原则和沿长度方向顺纹排列的原则胶合而成的板材。
4、纤维板:以木材或其它非木材植物纤维原料,经分离纤维、干燥、铺装、热压而制成的板材。
5、刨花板、碎料板:以小径木、间伐材、人工速生林为原料,通过刨片机加工成刨花,然后经过干燥、施胶、铺装板坯、热压制成的板材。
6、华夫板:用扁平大片刨花胶合而成的板材。
7、E0级刨花板:甲醛释放量低于5mg/100mg的刨花板8、静曲强度(MOR):静曲强度是指人造板抵抗外力而不破坏的最大能力。
9、弹性模量(MOE):弹性模量是人造板在比例极限内应力与应变的关系。
10、内结合强度(IB):内结合强度是测定人造板胶接性能的重要指标表面结合强度:表面结合强度是测定人造板表面性能的指标11、蠕变:人造板是弹塑性材料,当人造板在弯曲载荷作用下,除产生弹性变形外,还会产生塑性变形,人造板变形随时间的延长,变形增加,这种现象称为人造板的蠕变。
12、握钉力:人造板对钉子的握持能力称为握钉力绝对握钉力:指拔出钉子的最大阻力值比握钉力:指最大拔出阻力与钉子钉入部分展开表面积的比值握螺钉力:指人造板对木螺钉的握持能力13、胶合强度:胶合板试件承受平行于板面的拉力作用时,胶层抵抗剪切破坏力的能力。
14、胶合板的比强度:比强度是强度与密度的比值。
该比值反映了某些运动构件材料的重要特性。
硬度:抵抗其他不会产生残余变形物体凹入的能力耐磨性:指板抵抗磨损的能力抗冲击强度:人造板的抗冲击强度反映了产品抵抗动载荷破坏的能力工艺性质:是人造板的可加工性能(机械加工性能、拼缝的性能和表面装饰性能)15、集成材(Glued Laminated Timber):是一种沿板材或枋材平行纤维方向,用胶粘剂沿其长度、宽度或厚度方向胶合而成的实木板枋材。
人造板生产工艺演示文稿
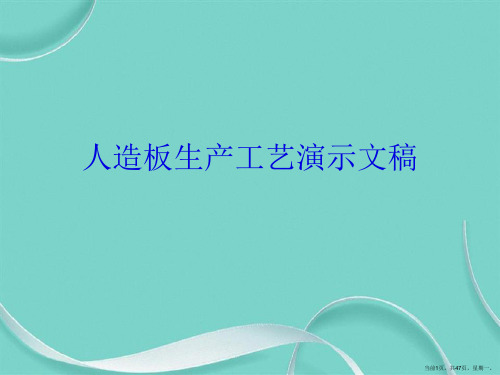
细木工板的选购
2、听 将细木工板放在地面上,用手或其它钝器在板
面不同的部位进行敲击,如果声音差异很大,说明板 材内部存在空洞木条缝隙大。
3、摸 用手触摸细木工板表面,优质的板材手感
干燥,平整光滑,横向触摸无波浪形,说明含水 率低,平整度好
当前30页,共47页,星期一。
• 2、奇数层
奇数层的胶合板对称中心平面在木材上,可保证强度。
• 3、纹理交错
• 组成胶合板的相邻层单板的纤维方向互相垂直或成一定角度。保 证各方向上的抗拉强度基本趋于一致。
• 原木制成胶合板,物理力学性质有所改变
当前7页,共47页,星期一。
二、胶合板的分类
(1)普通胶合板:
Ⅰ耐气候耐沸水胶合板(酚醛树脂胶) Ⅱ 耐水胶合板 (脲醛树脂胶 ) Ⅲ 耐潮胶合板 (血胶) Ⅳ 不耐潮胶合板 (豆胶)
当前43页,共47页,星期一。
纤维板
当前44页,共47页,星期一。
二、特性
密度板表面光滑平整、材质细密、性能稳定 、边缘牢固,而且板材表面的装饰性好。内部 结构均匀,密度适中,尺寸稳定性好,变形量 小,物理力学性能适中。但密度板耐潮性较差 ,且相比之下,密度板的握钉力较刨花板差, 螺钉旋紧后如果发生松动,由于密度板的强度 不高,很难在固定。
• 4、按表面状况分:
未饰面刨花板(砂光、未砂光);
饰面刨花板:
• 5、按原料分:
木质刨花板
非木质刨花板(亚麻、甘蔗渣、棉杆、芦苇等)。
当前39页,共47页,星期一。
三、刨花板的优缺点
刨花板的优点:
1、有良好的吸音和隔音性能;刨花板绝热、吸声 2、内部为交叉错落结构的颗粒状,各部方向的性能基
【课程大纲】《人造板工艺学》

《人造板工艺学》课程大纲一、课程概述课程名称(中文):人造板工艺学(英文):Wood based Panel Processing课程编号:14351047课程学分:3.0课程总学时:48课程性质:专业课二、课程内容简介《人造板工艺学》是一门研究保存木(竹)材自身的优点,通过同其他材料的复合技术而成为一种新型材料的应用科学。
这种新型材料既保留了原组成材料的主要特色,又能通过复合效应获得原组分不具备的性能;还可以通过材料设计使组杨的性能互相补充并彼此关联,获得新的优越性能,为开发先进复合材料开辟了一条新途径。
本课程应着重于系统讲授人造板生产工艺的基本理论和应用技术,适当地讲授当代国内外人造板制造的先进工艺与设备技术,并通过实验教学,结合专业课程设计、认识实习、生产实习与毕业实习,使学生掌握人造板生产工艺理论,具有从事人造板生产技术、实验研究、工艺设计的初步能力。
三、教学目标与要求《人造板工艺学》是木材科学与工程本科专业的专业核心课,通过本课程的学习,使学生熟悉人造板生产工艺流程,了解人造板生产原料的物理、力学与化学性能对产品最终性能的影响,熟悉人造板生产设备的结构与工作原理,具备分析与解决人造板生产过程中的制造工艺及质量控制问题的能力。
四、教学内容与学时安排绪论(4学时)1. 教学目的与要求:了解人造板的生产方法、生产过程和生产工艺;理解国内、外人造板的研究概况及研究方向、人造板工业的发展状况及前景;掌握人造板的定义、分类、性质和用途。
2. 教学重点与难点:人造板的定义、分类、性质和用途;国内、外人造板的研究概况及研究方向。
第一章原料(4学时)1. 教学目的与要求:了解常用贴面材料及其原材料的贮存与保管;理解胶合板、纤维板和刨花板常用胶粘剂应具备的条件以及常用的胶粘剂和其他添加剂的种类与性质;掌握胶合板、纤维板和刨花板的木质原料的基本要求和主要性质。
2. 教学重点与难点:胶合板、纤维板、刨花板的木质原料、胶粘剂和添加剂的基本要求、种类与性质。
人造板生产工艺学课程设计

人造板生产工艺学课程设计说明书一设计目的通过进行人造板生产工艺流程设计,加深所学过的有关人造板生产理论和工艺知识,进一步明确不同种类胶合板,刨花板,纤维板各自不同的生产工艺流程,体现不同的原料要求不同的工艺和设备。
二设计条件1.以杨木为原料制造细木工板的生产工艺流程2.以棉杆为原料制造中密度纤维板的生产工艺流程3.以枝丫材、小径材和森林采伐剩余物为原料制造刨花板的生产工艺流程4.以稻壳或竹材为原料模压成型的生产工艺流程三设计内容1 写出制造胶合板的生产工艺流程、注明主要工序所用设备并附带工艺说明。
2 写出制造干法中密度纤维板的生产工艺流程、画出工艺流程图画出工艺流程图、注明主要工序所用设备并附带工艺说明。
3写出制造刨花板的生产工艺流程、画出工艺流程图画出工艺流程图、注明主要工序所用设备并附带工艺说明。
4以稻壳或竹材为原料模压成型的生产工艺流程、画出工艺流程图画出工艺流程图并、明主要工序所用设备并附带工艺说明。
一 .以杨木为原料制造细木工板的生产工艺流程1 工艺流程图2 设备(1)剥皮工序所用设备:切削型剥皮机(2)定中心工序所用方法及设备:计算机扫描定心法计算机X-Y定心系统(3)旋切工序所用设备:无卡轴旋切机(4)干燥工序所用设备:喷气式网带干燥机(5)剪切工序所用设备:机械传动剪切机(6)涂胶工序所用设备:四辊筒施胶机(7)预压工序所用设备:辊式连续预压机(8)热压工序所用设备:多层热压机3工艺说明杨木截断:杨木长度选择6m,要按工艺要求的长度和质量进行锯断,截取的目段按应为胶合板成品尺寸外加加工余量的长度。
原木长度和原木的弯曲度、缺陷等直接影响胶合板的出材率,生产的肥料有小木段、截头和锯屑等,原木锯断耗损率在3-10%。
剥皮:由于树皮结构和性能与木质部完全不同,在胶合板生产中无使用价值;树皮韧皮部多为细长纤维,不剥皮而直接旋切时易阻塞刀门;树皮内夹有金属和泥沙等杂物,会损伤旋刀,影响正常旋切和单板的质量。
人造板工艺设计指导

---人造板工艺学课程设计指导书木材科学教研室刨花板制造学课程设计指导书一、课程设计的依据──设计任务书设计任务由指导教师提出,在设计任务书中通常给定设计年产量,也可以给定热压机的型号和台数,由学生计算出实际产量。
设计任务书还要给定刨花板的生产方式(主要指热压成板方式)、成品幅面及厚度、成品密度等有关数据,根据原料种类和品质的不同,还可以规定原料的要求。
二、实际生产能力的计算课程设计一般是只限于生产车间的简单设计,相当于正规设计的初步方案设计阶段,不涉及厂区的总体设计和相关配套工程的设计,如土建、供热、供电、给排水、暖通、环保、厂区道路和料场规划等项工程的设计均不涉及。
车间(或生产线)年实际生产能力的计算方法(一)当给定设计产量时:1. 依给定的设计产量:首先选定热压机,通常按设计产量来计算生产给定幅面规格产品所需热压机的层数m :21K K T h b L t A m ••••••= (层) ………………………………………………(1) 式中:A ─为车间的设计班产量,一般车间的工作日制度为每年有效工作日280天,每天三班生产每班有效工时7.5小时,可按以上规定换算产量。
单位:米3/班。
t ─ 一个热压周期的时间,包括装卸板时间,单位:分钟。
L ─刨花板成品长度。
单位:米。
b ─刨花板成品宽度。
单位:米。
h ─刨花板成品厚度。
单位:米。
T ─每班有效工作时间。
单位:分钟K 1─压机工时利用系数,一般取0.96-0.98K 2─成品合格率,一般取0.93-0.052.由计算层数选择压机型号,m 计算值通常不是整数,首先要凑成整数,用对照现有国产热压机的目录,选择与计算层数最接近的热压机层数,并依产品幅面要求和热压方式选定压机型号。
3.依选定的热压机型号再计算实际产量As 。
tK K T h b L As 21•••••= (立方米/班)……………………………………………(2) 上式中各项含义同前式所述。
- 1、下载文档前请自行甄别文档内容的完整性,平台不提供额外的编辑、内容补充、找答案等附加服务。
- 2、"仅部分预览"的文档,不可在线预览部分如存在完整性等问题,可反馈申请退款(可完整预览的文档不适用该条件!)。
- 3、如文档侵犯您的权益,请联系客服反馈,我们会尽快为您处理(人工客服工作时间:9:00-18:30)。
胶合板课程设计任务书
一、设计题目
1、设计年产量为20000m3胶合板车间
2、产品规格 3、树种:柳桉(表板)
意杨(芯板)
二、设计内容
1、生产大纲的拟定 2、工艺流程的确定 3、原木和辅料需要量的计算 4、设备的选型与计算
规格
胶种
UF胶 PF胶
占总产量百 分比(%)
90
10
4’×8’
80
技术损耗系数:60.5~2.5% ,考虑同定心偏差 造成的损失。
7、原木需要量
Q原
Q木
1 I7
工艺损耗系数:I7=3~4%,考虑截头和锯路损失。
胶合板出材率: Q成 100%
幅面
3’×7’
20
3层 (厚3mm)
70
层数 5层 (厚5mm)
20
合计 100 100 100
5、绘制车间平面布置图(2号图纸)
5层 (厚7mm)
10
答辩材料内容及要求
内容: 1、设计说明书一份 2、车间平面布置图 说明书要求: 设计说明书内容应包括:封面、设计任务书、生产大纲、
工艺流程、原料需要量计算、设备选型。 设计说明书格式:在正文的右边部需注明计算过程中各
脲胶 酚胶
4’×8’
3层 (厚3mm) 5层 (厚5mm)
5层 (厚7mm)
3’×7’
3层 (厚3mm) 5层 (厚5mm)
5层 (厚7mm)
4’×8’
3层 (厚3mm) 5层 (厚5mm)
5层 (厚7mm)
3’×7’
3层 (厚3mm) 5层 (厚5mm)
5层 (厚7mm)
合计
0.9×0.8×0.7=0.504 100%
参数及计算结果。 设计说明书一律不能用计算机打印。 平面布置图要求: 设备应按参考资料上的外型绘制,不可用方框表示。 要求手工绘制
设计内容
一、生产大纲拟定 二、工艺流程确定 三、原料需要量计算 四、设备选型 五、绘制车间平面布置图
一、生产大纲拟定
1、求出各种不同规格胶合板在总产量中占的比例
5、干燥前的湿单板量
Q湿1I5Q干 15
干燥工艺损耗系数:I5=5~8%,考虑木材弦向干缩 率6~12%, 径向干缩率1~3%。
技术损耗系数:50.3~0.5%,考虑单板进入干燥 机以及出干燥机运输过程中的损失。
6、用于旋切的木段材积
Q木1I6Q湿 16
旋切工艺损耗系数:I6=25%,考虑旋出不可用单 板的损失。
3、热压前的板坯材积
Q干 1I3Q1未13
热压工艺损耗系数:
I3
S板坯S毛板10% 0 S毛板
技术损耗系数: 3=0.1~0.5%,考虑涂胶及 组坯时损失。
4、经干燥后的干单板量
Q干
Q干
1 I4
干单板加工工艺损耗系数:I4=8~12%,考虑单板 整理、分等、修补等损失。
一、生产大纲拟定
3、热压机加权平均生产率
) Q C Pa 1/Q 1a 2/1 Q 2 0 0 a i/Q i(m 3/班
式中:QCP——热压机的加权平均生产率 a1,a2…ai——各种规格的胶合板在总产量中占百分率
Q1,Q2…Qi——热压机单独生产某种产品的生产率
一、生产大纲拟定
4、热压机实际年产量
三、原料需要量计算
(一)木材需要量计算 不同规格胶合板构成初步设计:
胶合板规 格
压缩 率(%)
3层 (3mm) 10
单面砂 光量 (mm)
0.1
热压后 毛板厚 度(mm)
3.1
最小 板坯 厚度 (mm)
3.5
表板 厚度 (mm)
芯板 厚度 (mm)
中板 厚度 (mm)
实际 板坯
厚
(mm)
5层 (5mm) 10
一、生产大纲拟定
2、求出热压机生产某一种规格产品的生产能力
QTNmFK(m 3/班 )
Z1Z2
式中: T——每班工作时间(分) 取T=8小时 N——热压机的层数(层) m——每层压板中压制的胶合板张数,一般取m=1 δ——胶合板的成品厚度(米) F——成品胶合板的幅面(米2) K——热压机的工作时间利用系数 0.97~0.98 Z1——胶合板在压机中的保压时间(分) 取Z1=1min/mm Z2——辅助操作时间(分)(包括装卸板、压机闭合和升压所需时间) 人工装卸板Z2=90秒,机械装卸板Z2=40秒
5层 (厚7mm)
合计
占总量比例 0.504
实际年产量
实际班产量
二、工艺流程确定
画工艺流程框图(每道工序都要列出)
Raw Material
Debarking
Particle preparation
Blending
Screening
Drying
Forming
Hot Pressing
Finishing
表面加工工艺损耗系数: I1S10% 0
——表面加工余量,单面砂光量=0.1~0.15mm
S ——热压后毛板厚度
裁边加工工艺损耗系数:
I2
ห้องสมุดไป่ตู้
F未F已10% 0 F未
式中: F未 ——未裁边胶合板的面积 F已 ——已裁边胶合板的面积 裁边余量一般取60mm(两边)
技术损耗系数: 1,2=1~3% 由于表面加工和裁边、检验操作 不当所致。
一、生产大纲拟定
6、各种不同规格胶合板年产量和班产量
胶种 脲胶
酚胶
规格
厚度
3层 (厚3mm)
4’×8’
5层 (厚5mm)
5层 (厚7mm)
3层 (厚3mm)
3’×7’
5层 (厚5mm)
5层 (厚7mm)
3层 (厚3mm)
4’×8’
5层 (厚5mm)
5层 (厚7mm)
3层 (厚3mm)
3’×7’
5层 (厚5mm)
QQ CP 每天工 年 作 工 班 (作 m 3/次 年 )日
每天工作班次=2 年工作日=275天 要求:Q>20000(1+5%),即压机设计生产能力符
合预留总量5%的要求,上述所选压机是 合适的。
一、生产大纲拟定
5、确定热压机型号 对于生产4’×8’胶合板选择型号为: 负荷系数:规定产量/实际产量*100% 对于生产3’×7’胶合板选择型号为: 负荷系数:
0.1
5.1
5.7
5层 (7mm) 10
0.1
7.1
7.9
1、入库成品数
Q 成 Q 已 1I0
式中:Q成——入库成品数 Q已——已加工好的待检验合板数 Q已= QCP I0 ——抽样检验百分数 (普通胶合板I0=1%,进口板I0=4%)
2、未经裁边和表面加工的合板量
Q未1I11 Q I已 211,2