回转窑窑后结圈原因分析及处理方法
回转窑过渡带异常结圈的处理

回转窑过渡带异常结圈的处理众所周知,烧成带正常窑皮的长度约为窑径的4.5倍,窑皮厚度≈耐火砖厚度,其余位置无副窑皮(圈)最为理想。
但实际生产中受风煤料匹配、原燃材料性质、热工制度稳定、热工设备结构性能变化等的影响,窑内容易出现副窑皮或结圈现象。
如副窑皮(圈)形成后不影响正常生产,不继续恶化,则不需要调整操作参数或热工设备,只需定时对窑尾结皮及燃烧器头部积料彻底清理,满足正常的通风及火焰形状。
配料、炉温、窑头负压等的正常控制,使窑处于稳定运行的状态,运行一段时间随着窑况的变化(成分、煤质上下波动,清理窑尾结皮及燃烧器顶部积料前后通风改变等,均会略改变窑内火点位置,达到了冷热交替的目的),其会自然脱落。
但当过渡带出现厚、宽圈时,窑尾出现倒料,操作者就不得不大幅度减产甚至停窑打圈。
笔者以一次过渡带位置结圈处置为例,结合理论知识剖析处理方法的得失,仅作参考。
1 异常结圈过程某次检修结束,从光点位置、对燃烧器与耐火材料的上下距离进行检验,相关数据和前几次校验结果基本一致;开窑运行后产质量受控,逐步恢复满负荷运行状态,7~9 m一档轮带后筒体温度偏高,整圈基本无窑皮(老砖140 mm厚度),9~26m烧成带窑皮均偏厚且不平整,35~45 m仅中班和夜班两个班形成近10 m宽的后圈,筒体温度在180~240 ℃(筒扫见图1、相关变化见表1),窑尾阶段性出现漏料。
图1 7∶00红外线筒体扫描图表1 筒体最高温度及液相量变化统计表当日14∶00~19∶00荧光分析仪出现故障,技术人员处理中,期间生料、熟料相关成分检测间断性测量,部分数据缺失。
20∶00左右35~45 m筒体表面温度慢慢降低,fCaO由18∶00的1.02%降低至20∶00的0.56%,因无相关荧光数据(不准确)进行指导,当班操作员从以往经验看属于KH 偏低(具体表现:窑电流上升50~100 A,二、三次风温上升30~50 ℃,篦冷机一段上熟料易推性变差,一段篦速较正常时提高1~2次/min),随即采取降低分解炉温度来降低入窑分解率的办法:炉温由885 ℃逐步降低至882 ℃,并联系质量控制人员手工测样品指导生产。
回转窑结圈的原因及处理方法

回转窑结圈的原因及处理方法1、结圈的危害回转窑“结圈”的部位一般在距窑口一定距离的固体燃料集中燃烧点附近的耐火窑衬上,厚度可达200-500 mm左右。
“结圈”对球团生产的危害有以下几方面:(1)降低产量,增加劳动强度窑圈一经形成,对燃料烧烧所产生的热气流势必起阻碍作用,如图-1所示。
热气流被部分阻挡在A区,影响了球团的焙烧效果。
同时,由于链篦机上生球的干燥、预热过程是利用窑尾废气进行的,故此,结圈也对生球的干燥、预热产生不良影响。
具体地说,就是透气性差,火焰不进,后部温度低,干燥时水分不易脱除,生球爆裂、粉化严重,成品率低,从而降低了劳动生产率。
另外,圈结形成后,如不及时处理,就会使圈的纵向长度、厚度增加,当圈掉下时,必然增加工人的劳动强度,有时甚至需停机处理,也影响了球团矿的产量。
(2) 增加了设备负荷如图-1所示,一定面积及厚度的结圈使物料流被阻于B区,此时,被阻的料量要高出正常时许多,加之圈本身的重量,必然增加了托轮、轴承的磨损,同时,增加了电机的负荷,甚至烧毁。
(3) 浪费能源在实际看火操作中,当出现“结圈”现象后,由于热气流被阻于A区,为保证链篦机的干燥和预热效果,看火工往往采用加大给煤量的方式,这无疑造成了能源浪费。
2、结圈的原因结圈的原因,在生产中主要可以归纳为操作不当。
具体地说,是由于上料量过大,干燥效果差,生球爆裂,粉化严重,致使透气性差,使得引风机抽动火焰的作用不明显,火焰只在窑内一定距离燃烧。
在大于1 200℃的高温下,未完全氧化的Fe3O4就与磁铁矿中一定数量的SiO2发生反应形成液相。
2Fe3O4+3SiO2+2CO=3Fe2SiO4+2CO22FeO+SiO2=Fe2SiO4另外,当给煤量较大时,在1 150℃条件下,Fe2O3也会部分分解为Fe3O4,与SiO2作用而生成2FeO·SiO2,形成渣相粘结。
这就使得物料在流经焙烧带时,所产生的液相、渣相极易粘附在窑衬的表面,同时粘结物料而产生结圈现象。
回转窑结圈的影响因素及解决措施

回转窑结圈的影响因素及解决措施-----龙仕连我司从11月23日开始窑内断断续续出现少量漏料,并出现了三次大料球,严重影响到窑的正常运转,公司及部门领导高度重视。
经分析是窑23米处结后圈导致窑尾漏料和结料球。
于25日开始处理后圈:1、窑减产到350 t/h煅烧;2、窑头煤管每个班移动两次,-200~+100冷热交替处理;3、每班清理煤管头部积料结焦4次,以保证头煤燃烧好,火焰集中;4、控制煤粉细度及水分,以保证煤粉燃烧效果(煤磨出磨温度控制在63~65度,入磨温度<300度。
内部控制煤粉细度<6.0);5、适当提高熟料KH。
通过3天的处理,23料处后圈薄了很多,并有缺口,于28日窑恢复了365 t/h正常生产。
出现这样的工艺事故,我们必须深度反思。
特别是工艺管理人员和窑操作员一定要密切关注窑皮的变化趋势及原燃材料的变化,及时调整窑参数,保证窑正常运转。
下面让我们再次学习一下窑内结圈的成因、危害及解决措施:结圈是指回转窑在正常生产中,由于原燃材料的变化,或者操作和热工制度的影响,窑内因物料过度粘结,在特定的区域形成一道阻碍物料运动的环形、坚硬的圈。
这种现象在回转窑内是一种不正常的窑况,它破坏了正常的热工制度,影响窑内通风,造成窑内来料波动很大,直接影响到回转窑的产量、质量、消耗和长期安全运转。
而且处理窑内结圈费时费力,严重时需停窑停产,危害极其严重。
结圈的成因及危害:结圈的形成: 结圈实际上是在烧成带末端与放热反应带交界处形成的窑皮,是回转窑内危害最大的结圈。
在熟料煅烧过程中,当物料温度达到1280℃时,其液相黏度较大,最容易形成结圈,而且冷却后比较坚固,不易除掉。
在正常的煅烧情况下,后结圈体的内径部分往往被烧熔而掉落,保持正常的圈体内径。
如果在1 250~l 280℃温度范围内出现的液相量偏多,往往会形成妨碍生产的后结圈。
后结圈一般结在烧成带的边界或更远,开始是烧成带后边的窑皮逐渐增长、增厚,发展到一定程度即形成后结圈。
窑内结圈、结球的原因及处理措施

窑内结圈、结球的原因及处理措施中控室侯素克结圈是指窑内在正常生产中因物料过度黏结,在窑内特定的区域形成一道阻碍物料运动的环形、坚硬的圈。
这种现象在回转窑内是一种不正常的窑况,他破坏正常的热工制度,影响窑内通风,造成来料波动很大,直接影响回转窑的产量、质量、消耗和长期安全运转。
尤其频繁结圈的回转窑,不仅破坏了窑内正常热工制度,而且损害操作人员的身体健康,给生产造成经济损失。
引起回转窑结圈的因素很多,它与原料性质、生料成分、燃料的灰分和细度、窑型、窑内还原气氛及热工制度等有关。
1 结圈的形成回转窑内形成结圈的因素很多,但液相的产生和固化是结圈的主要形成过程。
而衬料温度、物料温度、煤灰和生料组成又是决定液相的生成和固化的主要因素。
在正常情况下,窑皮保持在200mm左右的厚度,该温度条件及区域内若熔化和固化的过程达到平衡,窑皮就不会增厚。
当熔化的少固化的多,其厚度增长到一定程度,即形成圈。
当衬料与物料的温差大时,在足够液相的条件下,圈体越结越厚。
1.1前结圈的形成前圈结在烧成带和冷却带交界处,由于风煤配合不好,或者煤粉粒度过粗,煤灰和水分大,影响煤粉燃烧,使黑火头长,烧成带像窑尾方向移动,熔融的物料凝结在窑口处使“窑皮”增厚,发展成前圈,或者由于煤粉落在熟料上,在熟料中形成还原性燃烧,铁还原成亚铁,形成熔点低的矿物或者由于煤灰分中氧化铝含量高而使熟料液相量增加,黏度增大,当遇到入窑二次风温降温、冷却,就会逐渐凝结在窑口处形成圈。
前圈形成的主要原因是煤粉的质量,熟料中溶剂矿物含量过高或氧化铝含量过高,燃烧器在窑口断面的位置不合理,影响煤粉燃烧,使结圈速度加快,前温急烧,导致温差相差大,造成液相冷却凝固形成前圈,1.2熟料圈的形成原因熟料圈(又称后圈),是结在窑内烧成带与放热反应带之间的圈,也是回转窑内危害最大的结圈。
造成熟料圈的原因很多,主要有生料化学成分,熟料圈行成往往在物料刚出现液相的地方,物料在1200~1300度范围内为防止结圈,配料时应考虑液相不易过多,液相黏度不易过大;原燃材料中的有害成分,原燃材料中的有害成分过多,降低物料的熔点,结圈的可能性就增大,正常情况下,此类结圈大多发生在放热反应带以后的地方;煤的影响,煤灰中氧化铝的含量较高,当煤灰掺入物料中时,使物料液相量增加往往易结圈;操作和热工制度的影响,头煤加入量较多,产生还原气氛,形成低熔点矿物,使液相提前出现,容易结圈,二三次风配合不当,火焰过长,液相提前出现,特别是在分解率高的情况下,结圈的可能性更大。
窑内结圈形成原因及处理

• 2、减少原燃料带入的有害成分 • 一般粘土中碱含量高,煤中含硫量高。因此,如果窑上经常 • • • •
出现结圈时,视结圈料分析结果,最好能改变粘土或原煤的供 货矿点,以减少有害成分对结圈的影响。 3、控制煤粉细度,确保煤粉充分燃烧 。 4、调整燃烧器控制好火焰形状确保风、煤混合均匀并有一定的 火焰长度。经常移动喷煤管,改变火点位置。 5、提高快转率 三个班统一操作方法,稳定烧成系统的热工制度。在保持喂 料喂煤均匀,加强物料预烧的基础上尽量加快窑速。采取薄料 快转、长焰顺烧,提高快转率,这对防止煤、料量可以不变,只要把喷煤管往外拉出一定距离, •
就可以把前圈烧垮。 (2)如果前圈离下料口比较近,并在喷嘴口前则将喷嘴往里伸, 使圈体温度下降而脱落。如果圈体不垮,则有两种处理方法 ① 把喷煤管往外拉出,同时适当增加内流风和二次风温度,这 样可以提高烧成温度,使烧成带前移,把火点落在圈位上。一 般情况下,圈能在2~3h内逐渐被烧掉。但在烧圈过程中应根 据进入烧成带料量多少,及时增减用煤量和调整火焰长短,防 止损伤窑皮或跑生料。 ② 如果用前一种方法无法把圈烧掉时,则把喷煤管向外拉出并 把喷嘴对准圈体直接烧。待窑后预烧较差的物料进入烧成带后, 火焰会缩得更短,前圈将被强火烧垮。但是必须指出,采用这 种处理方法,由于喷煤管拉出过多,生
• 在高温的热气流中被烧熔而掉落下来。当它再次被物料覆盖,
•
液相又凝固下来,如此周而复始。假如这个过程达到平衡,窑 皮就不会增厚,这属正常状态。如果粘挂上去的多,掉落下来 的少,窑皮就增厚。反之则变薄。当窑皮增厚达一定程度就形 成结圈。形成结圈的原因主要有如下几点: 1、入窑生料成分波动大,喂料量不稳定 实际生产过程中,窑操作员最头疼的事是人窑生料成分波动太 大和料量不稳定。窑内物料时而难烧时而好烧或时多时少,遇 到高KH料时,窑内物料松散,不易烧结,窑头感到“吃火”, 熟料fCaO高,或遇到料量多时都迫使操作员加煤提高烧成温度, 有时还要降低窑速;遇到低KH料或料量少时,窑操作上不能及 时调整,烧成带温度偏高
窑结大球原因分析
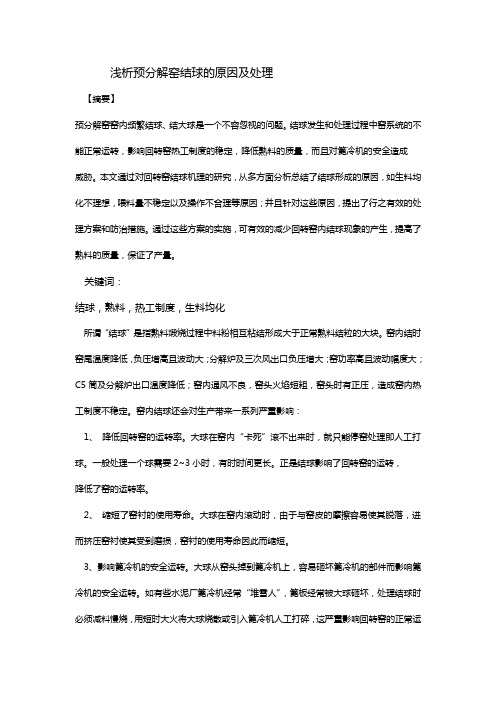
浅析预分解窑结球的原因及处理【摘要】预分解窑窑内频繁结球、结大球是一个不容忽视的问题。
结球发生和处理过程中窑系统的不能正常运转,影响回转窑热工制度的稳定,降低熟料的质量,而且对篦冷机的安全造成威胁。
本文通过对回转窑结球机理的研究,从多方面分析总结了结球形成的原因,如生料均化不理想,喂料量不稳定以及操作不合理等原因;并且针对这些原因,提出了行之有效的处理方案和防治措施。
通过这些方案的实施,可有效的减少回转窑内结球现象的产生,提高了熟料的质量,保证了产量。
关键词:结球,熟料,热工制度,生料均化所谓“结球”是指熟料煅烧过程中料粉相互粘结形成大于正常熟料结粒的大块。
窑内结时窑尾温度降低,负压增高且波动大;分解炉及三次风出口负压增大;窑功率高且波动幅度大;C5筒及分解炉出口温度降低;窑内通风不良,窑头火焰短粗,窑头时有正压,造成窑内热工制度不稳定。
窑内结球还会对生产带来一系列严重影响:1、降低回转窑的运转率。
大球在窑内“卡死”滚不出来时,就只能停窑处理即人工打球。
一般处理一个球需要2~3小时,有时时间更长。
正是结球影响了回转窑的运转,降低了窑的运转率。
2、缩短了窑衬的使用寿命。
大球在窑内滚动时,由于与窑皮的摩擦容易使其脱落,进而挤压窑衬使其受到磨损,窑衬的使用寿命因此而缩短。
3、影响篦冷机的安全运转。
大球从窑头掉到篦冷机上,容易砸坏篦冷机的部件而影响篦冷机的安全运转。
如有些水泥厂篦冷机经常“堆雪人”,篦板经常被大球砸坏,处理结球时必须减料慢烧,用短时大火将大球烧散或引入篦冷机人工打碎,这严重影响回转窑的正常运转,影响回转窑的热工制度的稳定,降低了熟料的质量。
因此,研究结球极其重要,绝不容忽视。
一、结球的机理简析近年来,很多人对回转窑结球的机理进行了探讨,研究报道中都有对结蛋料和正常料化学成分的对比,并探讨结蛋形成的机理。
有水泥专业技术人员曾经从预分解窑生料圈后面(过渡带)发现许多直径达1m的大球,并从中取出10个大球,从中间锯开,发现这些球中间都有一个褐色、细粒、白垩状的内核及灰褐色多孔状的外壳。
陶粒砂煅烧回转窑前后结圈不同处理办法
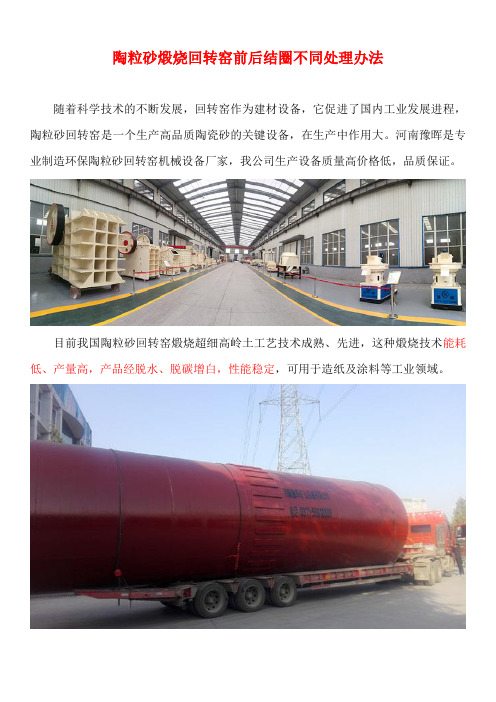
陶粒砂煅烧回转窑前后结圈不同处理办法随着科学技术的不断发展,回转窑作为建材设备,它促进了国内工业发展进程,陶粒砂回转窑是一个生产高品质陶瓷砂的关键设备,在生产中作用大。
河南豫晖是专业制造环保陶粒砂回转窑机械设备厂家,我公司生产设备质量高价格低,品质保证。
目前我国陶粒砂回转窑煅烧超细高岭土工艺技术成熟、先进,这种煅烧技术能耗低、产量高,产品经脱水、脱碳增白,性能稳定,可用于造纸及涂料等工业领域。
在陶粒砂回转窑烧结过程中结圈是经常发生的,在结圈前如果预防的得当会减少陶粒砂回转窑结圈的故障;在陶粒砂回转窑结圈后的处理方法也一定要得当,要不然会造成巨大损失的,下面我们就来看看豫晖小编总结的回转窑前结圈和后结圈的不同处理办法。
结圈分为前结圈和后结圈两种,一般都是在窑速较慢的情况下才能形成的。
(1)前结圈的处理。
当前结圈不高时,对锻烧操作影响不大,但会增加烧成的料层厚度,延长物料在烧成带的停留时间;当前结圈比较高时,会对窑况或热工制度产生较大影响,引起窑内通风变差,窑头时有正压现象,火焰伸不进去且火焰的形状不好;大块熟料也不易滚出,容易砸坏窑皮,等等。
处理时,只要将喷煤管拉出,使高温集中在结圈的位置,就可以逐步将前结圈烧掉。
(2)后结圈的处理。
后结圈主要在烧成带与过渡带之间形成,它会影响整个系统的通风、产量及质量,处理时通常要采用冷热交替法。
其中:当后结圈结得长而不高时,只要将喷煤管向外拉出,调整火焰形状,使火焰粗而短,就可降低结圈处的温度,使之逐渐垮落(此法称为冷烧法);若圈已经长高并严重影响了窑内的通风时,要先减喂料量(为正常喂料量的80%左右),并采用冷热交替法各烧2h左右,直到把圈烧垮为止。
后者,往往圈后会积有很多生料粉,当圈垮落后,会迅速涌向烧成带,这时应将喷煤管及时拉出,减慢窑速(通常称为预打小慢车),适当关小排风,让火力强度集中在烧成带,以尽量避免跑生料或久烧料出现。
(3)用陶粒砂回转窑窑内结圈快速处理机。
结圈形成的原因、预防措施和处理方法
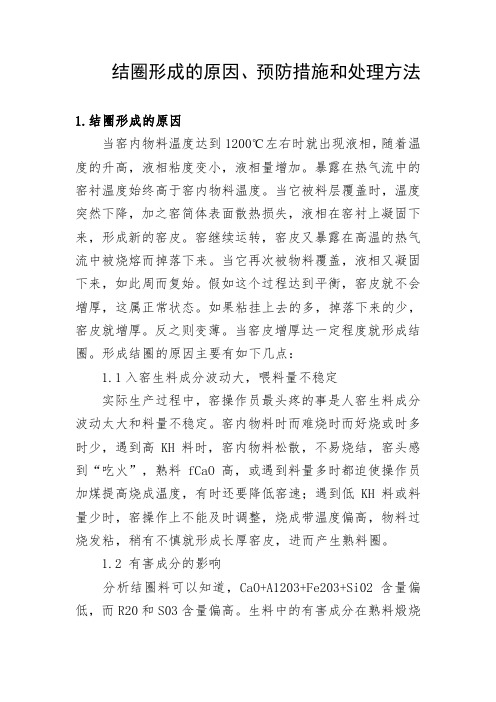
结圈形成的原因、预防措施和处理方法1.结圈形成的原因当窑内物料温度达到1200℃左右时就出现液相,随着温度的升高,液相粘度变小,液相量增加。
暴露在热气流中的窑衬温度始终高于窑内物料温度。
当它被料层覆盖时,温度突然下降,加之窑简体表面散热损失,液相在窑衬上凝固下来,形成新的窑皮。
窑继续运转,窑皮又暴露在高温的热气流中被烧熔而掉落下来。
当它再次被物料覆盖,液相又凝固下来,如此周而复始。
假如这个过程达到平衡,窑皮就不会增厚,这属正常状态。
如果粘挂上去的多,掉落下来的少,窑皮就增厚。
反之则变薄。
当窑皮增厚达一定程度就形成结圈。
形成结圈的原因主要有如下几点:1.1入窑生料成分波动大,喂料量不稳定实际生产过程中,窑操作员最头疼的事是人窑生料成分波动太大和料量不稳定。
窑内物料时而难烧时而好烧或时多时少,遇到高KH料时,窑内物料松散,不易烧结,窑头感到“吃火”,熟料fCaO高,或遇到料量多时都迫使操作员加煤提高烧成温度,有时还要降低窑速;遇到低KH料或料量少时,窑操作上不能及时调整,烧成带温度偏高,物料过烧发粘,稍有不慎就形成长厚窑皮,进而产生熟料圈。
1.2 有害成分的影响分析结圈料可以知道,CaO+A1203+Fe203+Si02含量偏低,而R20和S03含量偏高。
生料中的有害成分在熟料煅烧过程中先后分解、气化和挥发,在温度较低的窑尾凝聚粘附在生料颗粒表面,随生料一起人窑,容易在窑后部结成硫碱圈。
在人窑生料中,当MgO和R20都偏高时,R20在MgO引起结圈过程中充当“媒介”作用形成镁碱圈。
根据许多水泥厂的操作经验,当熟料中MgO>4.8%时,能使熟料液相量大量增加,液相粘度下降,熟料烧结范围变窄,窑皮增长,浮窑皮增厚。
有的水泥厂虽然熟料中MgO<4.0%,但由于R20的助熔作用,使熟料在某一特定温度或在窑某一特定位置液相量陡然大量增加,粘度大幅度降低,迅速在该温度区域或窑某一位置粘结,形成熟料圈。
回转窑后结圈的原因分析与解决措施

回转窑后结圈的原因分析与解决措施发布时间:2022-04-25T02:30:40.147Z 来源:《工程管理前沿》2022年1期作者:田硕[导读] 近年来,由于国家倡导节能减排的生产,从而加大了对一些浪费资源和污染比较大的企业改革田硕山东申丰水泥集团有限公司山东省枣庄市 277300引言:近年来,由于国家倡导节能减排的生产,从而加大了对一些浪费资源和污染比较大的企业改革,这就给了新型熟料回转窑一个重要的市场,让他们可以快速的发展起来。
熟料回转窑设备结构坚固、运转平稳、出窑产品质量高。
此外,在环保方面,利用熟料窑焚烧危险废物、垃圾,这不仅使废物减量化、无害化,而且将废物作为燃料利用,节省煤粉,做到废物的资源化。
关键词:回转窑后结圈解决措施摘要:熟料回转窑后结圈往往形成于烧成带和过渡带之间。
在熟料煅烧过程中,当窑内温度达到1280℃时,其液相粘度较大,此时,如果生料的KH、n率值较低,操作使窑内拉风较大,火焰太长,烧成带后边浮窑皮逐渐增长、增厚,发展到一定程度就形成了熟料回转窑的后结圈。
一、后结圈情况A企业配置一条5000t/d预分解熟料回转窑。
于2021年10月份在窑尾38米、43米处出现两道结圈,严重时窑尾出现漏料,窑投料量下降,熟料质量波动,窑况很不稳定。
二、原因分析2.1原煤内水偏高加剧了结圈的发生2021年煤价不断上涨,原煤库存为0吨,原煤随来随用,严重影响煤的均化效果。
煤粉内水偏高,窑头喷煤管燃烧速度慢、燃烧时间长,火焰的热力分散,燃烧时热力强度低,高温点后移,烧成带拉长,高温点不集中,熟料烧结不致密,二次风温偏低,恶性循环更加加剧了火焰燃烧速度。
物料预烧不好,容易产生不完全燃烧,没有燃尽的煤粉颗粒和CO不能在烧成带燃烧,部分聚集在窑尾燃烧,促使液相在过渡带提前出现,将未熔的物料黏结在一起,形成后结圈。
停窑后取结圈料化学分析结果发现:正常熟料烧失量为0.42%,结圈料为1.66%、2.06%也验证了这一点。
回转窑结圈的原因及处理方法
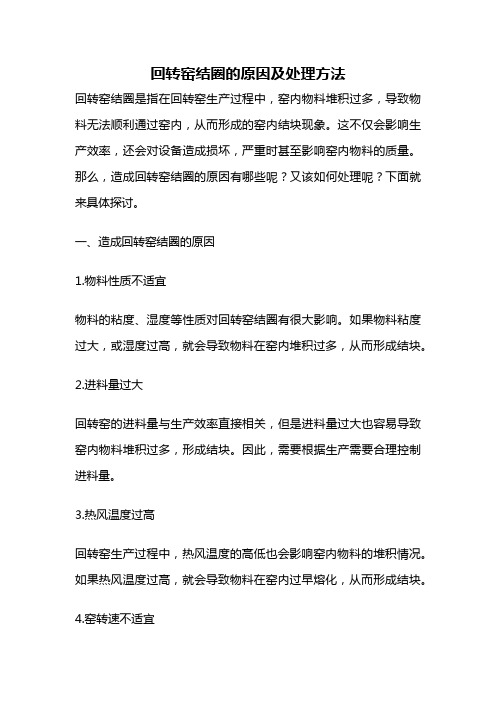
回转窑结圈的原因及处理方法回转窑结圈是指在回转窑生产过程中,窑内物料堆积过多,导致物料无法顺利通过窑内,从而形成的窑内结块现象。
这不仅会影响生产效率,还会对设备造成损坏,严重时甚至影响窑内物料的质量。
那么,造成回转窑结圈的原因有哪些呢?又该如何处理呢?下面就来具体探讨。
一、造成回转窑结圈的原因1.物料性质不适宜物料的粘度、湿度等性质对回转窑结圈有很大影响。
如果物料粘度过大,或湿度过高,就会导致物料在窑内堆积过多,从而形成结块。
2.进料量过大回转窑的进料量与生产效率直接相关,但是进料量过大也容易导致窑内物料堆积过多,形成结块。
因此,需要根据生产需要合理控制进料量。
3.热风温度过高回转窑生产过程中,热风温度的高低也会影响窑内物料的堆积情况。
如果热风温度过高,就会导致物料在窑内过早熔化,从而形成结块。
4.窑转速不适宜回转窑的转速也会影响窑内物料的堆积情况。
如果转速过快,就会导致物料在窑内无法均匀分布,从而形成结块。
二、回转窑结圈的处理方法1.减少进料量当回转窑结圈发生时,可以适当减少进料量,以缓解窑内物料堆积过多的情况。
2.调整热风温度如果回转窑结圈是由于热风温度过高导致的,可以适当降低热风温度,以减少窑内物料的过早熔化。
3.调整窑转速如果回转窑结圈是由于窑转速不适宜导致的,可以适当调整窑转速,以保证物料在窑内均匀分布。
4.清理窑内物料当回转窑结圈严重时,需要停窑清理窑内物料。
清理时需要注意安全,避免对设备造成损坏。
5.加入流化剂在窑内加入一定量的流化剂,可以有效地缓解回转窑结圈现象。
流化剂可以使物料在窑内均匀分布,减少结块的情况。
6.调整物料配比如果回转窑结圈是由于物料配比不合理导致的,可以适当调整物料配比,以保证物料在窑内均匀分布,减少结块的情况。
回转窑结圈是一种常见的生产问题,多种因素都可能导致其发生。
因此,在回转窑生产过程中,需要做好预防措施,保证物料在窑内均匀分布,避免结块的发生。
同时,一旦发生回转窑结圈,需要及时采取相应的处理措施,以保证生产效率和产品质量。
球团回转窑结圈诊断

球团回转窑结圈诊断球团回转窑是一种重要的水泥生产设备,广泛应用于水泥生产过程中。
然而,由于生产过程中的各种因素,球团回转窑的结圈问题经常发生,影响生产效率和产品质量。
因此,球团回转窑的结圈诊断显得尤为重要。
结圈是指在球团回转窑内墙面和转筒内壁上形成厚而坚固的结合层的现象,这可能会导致生产过程中的下列问题:1.增加能耗:由于结圈层的存在,火焰与物料之间的热交换效率降低,导致能耗的增加。
2.降低生产能力:结圈层会堵塞球团回转窑的内部空间,使物料无法自由流动,从而降低生产能力。
3.降低产品质量:结圈层的存在可能导致产生大量的灰渣,降低水泥产品的质量。
为了诊断球团回转窑的结圈问题,可以采取以下步骤:1.观察结圈形态:通过观察球团回转窑内壁上的结圈形态,可以初步判断结圈的原因。
例如,如果结圈形态较为均匀,可能是由于煤气流量不足或者煤粉燃烧不完全所造成的。
2.分析排放气体:通过分析球团回转窑排放的气体成分,可以了解燃烧过程中的变化。
例如,高CO和CO₂含量可能是煤粉燃烧不完全的表现,需要调整煤粉供给和燃烧风量。
3.检测内部温度:利用红外热像仪等设备,检测球团回转窑内部的温度变化。
高温区域可能是结圈问题的主要发生地点,因此需要对高温区域进行进一步的分析和处理。
4.样品分析:采集球团回转窑内物料和结圈层的样品进行分析。
通过分析物料中的成分和结圈层的组成,可以判断结圈层的形成机制。
例如,结圈层中含有较高的氧化铁或氧化钙,可能是由于煤粉中矿物质含量过高所导致的。
5.优化工艺参数:根据诊断结果,调整球团回转窑的工艺参数,以减少结圈问题的发生。
例如,可以调整煤粉供给量、燃烧风量和冷却风量等参数,以优化燃烧和冷却过程。
总结起来,球团回转窑的结圈诊断是一项复杂而重要的工作。
通过观察结圈形态、分析排放气体、检测内部温度和样品分析等方法,可以找出结圈问题的原因,并优化工艺参数,以减少结圈的发生。
这将有助于提高球团回转窑的生产效率和产品质量。
回转窑结圈的原因及处理方法

回转窑结圈的原因及处理方法回转窑是制造水泥的重要设备,而回转窑结圈是影响生产效率和质量的常见问题。
结圈的原因有很多,如窑内温度不均、烧成温度过低、原材料成分不合适等。
本文将从原因和处理方法两个方面详细介绍回转窑结圈问题。
一、结圈的原因1. 窑内温度不均:回转窑内部温度分布不均会导致部分区域的烧成程度不够,形成未熟料,容易粘在窑壁上,最终导致结圈。
2. 烧成温度过低:如果烧成温度过低,则无法将原材料完全反应,也容易导致未熟料粘附在窑壁上。
3. 原材料成分不合适:原材料中含有过多的游离SiO2、Al2O3等物质,会使得反应速率变慢,在高温下难以完全反应。
同时,如果含有过多的碱金属氧化物,则会使得产生大量液态相,增加了结圈的风险。
4. 进出料方式不当:进出料口位置设置不合理,或者进出料速度过快或过慢,都会导致窑内物料分布不均,从而增加结圈的风险。
二、处理方法1. 调整窑内温度:调整窑内温度是解决结圈问题的关键。
可以通过改变燃烧器位置、调整燃料供给量等方式来调整窑内温度分布,使得各个区域的温度均匀。
2. 提高烧成温度:提高烧成温度可以促进原材料反应,减少未熟料生成的可能性。
但是需要注意控制好温度,避免超出窑的承载能力。
3. 调整原材料成分:在生产过程中要严格控制原材料的成分,避免含有过多的游离SiO2、Al2O3等物质和碱金属氧化物。
如果发现原材料成分不合适,则需要及时停机清理,并重新投入符合要求的原材料。
4. 改善进出料方式:调整进出料口位置和速度可以改善窑内物料分布不均的问题。
可以采用多点进出料口、减缓进出料速度等方式来改善这一问题。
5. 定期清理窑壁:定期清理窑壁可以有效减少未熟料的积累,降低结圈的风险。
清理时需要注意安全,避免对设备造成损伤。
综上所述,回转窑结圈是影响水泥生产效率和质量的常见问题。
通过调整窑内温度、提高烧成温度、调整原材料成分、改善进出料方式和定期清理窑壁等方式可以有效解决这一问题。
回转窑结圈的原因分析及防治
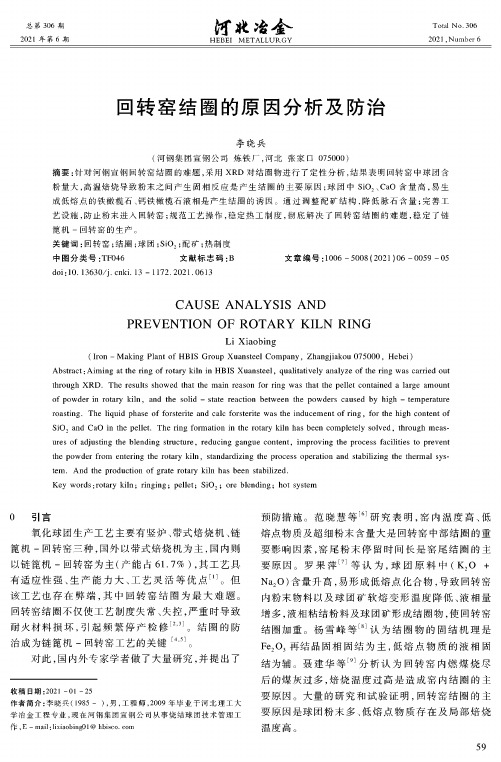
关键词:回转窑;结圈;球团;SiO2;配矿;热制度
中图分类号:TF046
文献标志码:B
doi:10. 5630/(. ccki. 03 -152.2021.0613
文章编号:1006 -5008(2021)06 -0059 -05
CAUSE ANALYSIS AND PREVENTION OF ROTARY KILN RING
粉量大,高温焙烧导致粉末之间产生固相反应是产生结圈的主要原因;球团中SiCO'CaO含量高,易生 成低熔点的铁橄榄石、钙铁橄榄石液相是产生结圈的诱因。通过调整配矿结构,降低脉石含量;完善工
艺设施,防止粉末进入回转窑;规范工艺操作,稳定热工制度,彻底解决了回转窑结圈的难题,稳定了链
篦机-回转窑的生产。
B
61.94
4.88
C
63.05
2. 34
D
60 .90
8 90
CaO 5. 91 2 33 1.3 3 0 34
MgO 1. 5 1.91 1.39 1. 5
TO. 0 89 2. 42 4 06 5. 5
S 0 57 0 09 5. 9 7 0 69
P 5. 52 0 07 0 06 0 06
AS2 O3
(b)黏结球团结圈物
图2结圈物衍射能谱
Fig. 2 Diffraction eneroy spactram of the ringing
由图2可知,两种结圈物的成分相似,其中 铁橄榄石(2FeO・St?)和钙铁辉石;对于黏结球团
Fa2O3代表赤铁矿,Fa2SiO4代表铁橄榄石,CaFx 结 ,其主要矿
2.2.2布料系统优化
布料系统主要设备有布料车、辐筛、流料板等,
回转窑结圈的原因及处理方法

水泥回转窑结圈的形成机理与处理方法水泥回转窑结圈的形成机理与处理方法 ______________________________________ 1一、窑皮是如何形成 ____________________________________________________________________________ 1二、结圈的机理与成因__________________________________________________________________________ 2三、圈的种类____________________________________________________________________________________ 3四、避免结圈的方式和方法_____________________________________________________________________ 3五、窑皮窑圈的几个根本性问题 ________________________________________________________________ 4六、处理结圈的方式 ____________________________________________________________________________ 5水泥回转窑结圈的形成机理与处理方法不管现今悬浮预热窑外分解窑多么先进,出现非正常窑况——结圈,也是煅烧中的正常现象。
虽然经过多年水泥人努力及水泥专家的研究,对出现不正常窑况的问题基本上能够解决,并且已经形成了完整的理论。
但话又说回来一旦出现不正常现象,运用理论解决问题的时候,问题又不能很好的解决,这也是事实。
我们不能否认理论,但是也不能完全把希望寄托于原有的理论中,这就是矛盾的两面性。
如何才能够快速及时的解决问题其实是我们关注的主要问题,所以本文主要是从几个主要方面来探讨结圈的机理和处理结圈的措施,以及时帮助读者解决所面临的不正常窑况。
回转窑窑后结圈的原因和处理结果

回转窑窑后结圈的原因和处理结果一、回转窑窑后结圈的原因回转窑是一种常用于石灰生产和水泥生产的设备,但在使用过程中,有时会出现窑后结圈的情况。
结圈是指窑内物料在烧结过程中出现结块现象,导致窑内热量传递不畅,影响生产效率和产品质量。
而窑后结圈的原因主要有以下几个方面:1.原料成分不稳定:回转窑生产过程中,原料成分的不稳定性是导致结圈的主要原因之一。
原料成分中的各种氧化物、硅酸盐和铝酸盐等物质,对烧结过程中的矿物相转化和结构稳定性起着重要作用。
如果原料成分的变化超出了窑内控制范围,就容易引起结圈。
2.燃烧条件不理想:回转窑的燃烧条件对结圈问题也有一定影响。
燃料的选择、供氧方式、燃烧温度等因素都会影响窑内气氛的稳定性和热量分布情况。
如果燃烧条件不理想,窑内温度分布不均匀,就容易导致结圈的发生。
3.窑内温度过高:窑内温度是影响回转窑结圈的重要因素之一。
当窑内温度过高时,原料中的一些物质会发生过度烧结,形成块状物质,从而导致结圈。
窑内温度过高可能是由于燃烧条件不理想、窑内热量分布不均匀等原因引起的。
4.窑内物料层厚度不均匀:窑内物料层厚度的不均匀也容易导致结圈。
如果窑内物料层厚度不均匀,热量传递不均匀,就会导致部分物料温度过高,发生结圈。
二、回转窑窑后结圈的处理结果针对回转窑窑后结圈的问题,可以采取一系列措施进行处理,以保证生产的正常进行和产品质量的稳定。
1.优化原料配比和成分控制:通过对原料配比和成分的优化,可以减少原料成分的波动范围,降低结圈的发生概率。
同时,加强对原料成分的在线监测和调控,及时发现和处理原料成分异常,以避免结圈的发生。
2.改进窑内燃烧条件:优化燃料选择、供氧方式和燃烧温度等因素,改善窑内燃烧条件,提高窑内气氛的稳定性和热量分布的均匀性。
通过调整燃烧条件,可以有效预防和减少结圈的发生。
3.控制窑内温度:合理控制窑内温度,避免温度过高或过低,对窑内物料进行适当的保护和调控。
通过优化燃烧条件、改善窑内热量分布等措施,可以有效降低窑内温度的波动,减少结圈的发生。
回转窑焚烧炉窑内结圈原因分析及对策
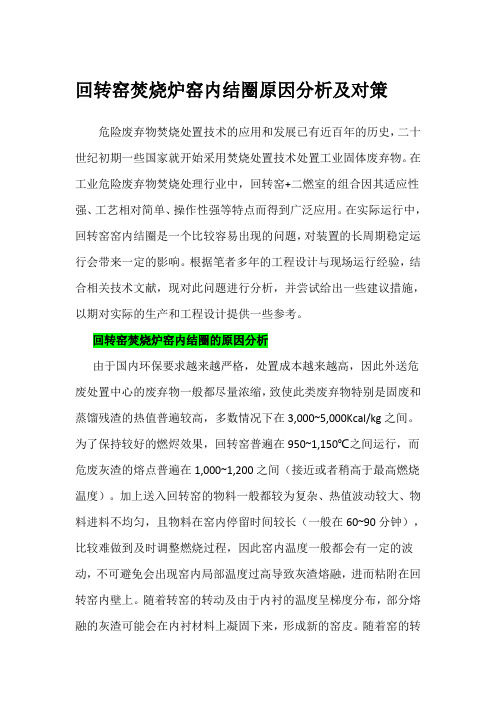
回转窑焚烧炉窑内结圈原因分析及对策危险废弃物焚烧处置技术的应用和发展已有近百年的历史,二十世纪初期一些国家就开始采用焚烧处置技术处置工业固体废弃物。
在工业危险废弃物焚烧处理行业中,回转窑+二燃室的组合因其适应性强、工艺相对简单、操作性强等特点而得到广泛应用。
在实际运行中,回转窑窑内结圈是一个比较容易出现的问题,对装置的长周期稳定运行会带来一定的影响。
根据笔者多年的工程设计与现场运行经验,结合相关技术文献,现对此问题进行分析,并尝试给出一些建议措施,以期对实际的生产和工程设计提供一些参考。
回转窑焚烧炉窑内结圈的原因分析由于国内环保要求越来越严格,处置成本越来越高,因此外送危废处置中心的废弃物一般都尽量浓缩,致使此类废弃物特别是固废和蒸馏残渣的热值普遍较高,多数情况下在3,000~5,000Kcal/kg之间。
为了保持较好的燃烬效果,回转窑普遍在950~1,150℃之间运行,而危废灰渣的熔点普遍在1,000~1,200之间(接近或者稍高于最高燃烧温度)。
加上送入回转窑的物料一般都较为复杂、热值波动较大、物料进料不均匀,且物料在窑内停留时间较长(一般在60~90分钟),比较难做到及时调整燃烧过程,因此窑内温度一般都会有一定的波动,不可避免会出现窑内局部温度过高导致灰渣熔融,进而粘附在回转窑内壁上。
随着转窑的转动及由于内衬的温度呈梯度分布,部分熔融的灰渣可能会在内衬材料上凝固下来,形成新的窑皮。
随着窑的转动,部分灰渣可能会被再次熔融,并达到一定的平衡,这样窑皮就不会增厚。
但是如果没有达到平衡,掉落下来的灰渣少,窑皮就会逐步增厚,达到一定程度后就形成结圈,如下图所示:形成结圈的主要原因有如下几点:1.回转窑的操作模式根据操作温度的不同,回转窑有两种操作模式:干渣模式和熔渣模式。
干渣操作模式在危废焚烧中最为常见,也被证明是最为可靠的一种操作模式,常规一般认为925℃以下为干渣模式,正常配伍可以保证灰渣不会熔融,此种操作模式结圈的可能性比较小。
回转窑结圈的原因及处理方法

回转窑结圈的原因及处理方法回转窑是一种常用于水泥生产过程中的设备,它通过高温和旋转运动将原料进行煅烧,以产生水泥熟料。
然而,有时候在回转窑的运行过程中,会出现结圈现象,这会严重影响设备的正常运行和水泥生产的质量。
了解回转窑结圈的原因及处理方法是至关重要的。
一、回转窑结圈的原因1. 原料成分不理想:回转窑的结圈问题与原料中的成分有很大的关系。
如果原料的化学成分不理想,其中含有过多的硫酸钠、硫酸镁等物质,将会导致煅烧过程中产生黏性物质,从而引起结圈。
2. 烧成温度过低:回转窑烧成温度过低也是导致结圈的一个重要原因。
当烧成温度过低时,原料中的化学反应无法完全进行,会导致部分物质残留在窑内,形成结圈。
3. 运行时间过长:长时间的运行也是回转窑结圈的一个重要原因之一。
当回转窑的运行时间超过其设计要求时,窑内结构会变得粘性,给结圈问题的发生提供了条件。
二、回转窑结圈的处理方法1. 优化原料配比:通过调整原料的化学成分,合理设计原料的配比,可以减少结圈问题的发生。
降低硫酸钠和硫酸镁等物质的含量,增加硅酸盐等成分,从而降低结圈的风险。
2. 提高烧成温度:增加回转窑的烧成温度可以有效地解决结圈问题。
适当提高温度可以加速化学反应的进行,降低黏性物质的生成,从而减少结圈发生的可能性。
3. 控制运行时间:合理控制回转窑的运行时间,确保在规定的运行时间内对窑内进行清理和维护。
定期对窑内进行清扫,清除可能产生结圈的物质,可以预防结圈问题的发生。
4. 使用防结圈剂:可以考虑在回转窑的煅烧过程中添加一定量的防结圈剂。
这些防结圈剂可以改变物料表面的化学性质,降低物料的粘性,减少结圈的风险。
5. 加强设备维护:定期对回转窑进行维护保养,保持设备的正常运行状态。
清理窑内的积存物,检查窑体和内衬的磨损情况,修复和更换损坏的部件,可以有效地预防结圈问题的发生。
总结与回顾:回转窑结圈问题是水泥生产过程中的常见现象,它会严重影响生产效率和产品质量。
- 1、下载文档前请自行甄别文档内容的完整性,平台不提供额外的编辑、内容补充、找答案等附加服务。
- 2、"仅部分预览"的文档,不可在线预览部分如存在完整性等问题,可反馈申请退款(可完整预览的文档不适用该条件!)。
- 3、如文档侵犯您的权益,请联系客服反馈,我们会尽快为您处理(人工客服工作时间:9:00-18:30)。
回转窑窑后结圈原因分析及处理方法
巩义市恒昌冶金建材设备厂生产的1000t/d熟料生产线是由天津水泥工业设计研究院有限公司设计的,主要包括TDF型分解炉、单系列五级旋风预热器、Φ3.2m×50m回转窑及TC-836篦式冷却机。
自2007年2月以来,窑后频繁发生结圈、结球的工艺事故,巩义市恒昌冶金建材设备厂技术人员现将原因分析及解决措施介绍如下,供同仁参考。
1、结圈情况
2007年3月19日最为严重,窑前返火,窑尾有漏料现象,无法操作煅烧,迫使停窑处理。
从窑内看,主窑皮长达22m,副窑皮长到窑尾,35~37m处形成后结圈,结圈最小孔洞呈不规则状,直径约l.5m,进窑观察该圈明显分为两层,且层次明确、清晰,第一层厚约150mm,呈黄白色,第二层厚约460mm,呈黑色,圈体非常致密。
对圈体取样分析见表1。
表1 圈体取样分析结果
从表l可以看出,第一层硫碱含量较高,是硫碱圈,第二层明显是煤粉圈,熟料液相出现过早、过多导致结圈。
2、原因分析
(1)由于2006年煤价不断上涨,加之公路运输距离远,为了降低成本,采用当地劣质煤煅烧,煤质下降,灰分高,挥发分低,发热值低,煤工业分析如表2、3。
实际生产中,煤可燃性差,煤粉燃烧不完全,大量煤灰不均掺入生料中,液相在窑后面提前出现,而未燃尽的煤灰产生沉积及液相的提前出现结圈。
(2)2007年以来,由于机械原因,高温风机l号轴与密封圈强烈摩擦,产生局部高温,使轴侧曲,水平振动最高达6.4mm/s。
为了降低振动,不得不降低高温风机转速,由原来的1130r/min降至l060r/min,有时更低,严重影响了窑内通风,加上煤质又差,更多的窑头燃烧不完全的煤粉沉积在窑后燃烧,使窑内后部温度升高,液相量增加,加速了窑后结圈的形成。
(3)为了处理窑后结圈,我厂在迫不得已的情况下停窑烧后圈,由于煤质差,
二、三次风温低,燃料不完全或未燃烧的煤粉落在圈上及圈后的积料上,不断燃烧,造成物料发粘,不但圈未烧掉,反而越结越厚,这也是第一层圈形成的主要原因。
(4)我厂石灰石矿点较多,且含土量较大,石灰石所占比例在92%左右,石灰石堆厂又小,均化不好,出磨生料质量不尽理想,生料三率值合格率较低,物料成分波动大,操作更难控制。
3、解决措施
(1)加强原煤进厂和煤粉制备过程中的管理,煤粉细度一定控制在80μm筛筛余30%以下,水分控制在1.5%以下。
在操作过程中,适当提高篦冷机料层,一般控制在500~600mm左右,使二次风温从880℃左右提高到945℃,以加强煤的燃烧,并开大内风,内外风比例由原来的6:4调为7:3,提高窑前温度,保证煤粉燃烧完全。
(2)在停窑打圈期间,钳工更换高温风机新轴承,同时修理密封圈,开启后,高温风机运行正常,彻底解决了窑内通风不够的问题。
(3)严格控制头、尾煤比例,稳定在4:6,防止窑内出现还原气氛,导致窑内煤粉燃烧不充分。
(4)根据石灰石矿含土量大的特点,在石灰石进料处架筛网,对石灰石进行筛土处理。
严格物料堆放作业程序,提高物料的预均化效果,避免由于石灰石波动大而引起生料化学成分波动。
(5)当煤质差,SiO2、MgO较高时,结圈后严禁干烧窑。
(6)三个班统一操作方法,稳定烧成系统的热工制度。
在保持喂料喂煤均匀、加强物料预烧的基础上尽量加快窑速,采取薄料快转,严禁慢窑大料,提高快转率,抑制窑后结圈。
4、效果
通过采取以上措施,我厂再也没发生过窑后结圈事故,而且产、质量较好,2007年4月份熟料生产30744t,fCaO平均0.76%。
一般来说,回转窑形成结圈的原因主要有如下几点:①入窑生料成分波动大,喂料量不稳定,势必造成窑内热工制度的紊乱。
当成分高和喂料量大时,必须加头煤,提高烧成温度,甚至降低窑速,当成分低或喂料量少时,操作上不能及时调整,烧成带温度过高,物料过烧发黏,容易形成长厚窑皮,进而形成熟料圈。
②有害成分的影响。
R2O和SO3含量偏高,易形成硫碱圈。
MgO高时,特别是大于4.8%时,能使熟料液相量大量增加,液相黏度下降,熟料烧结范围变窄,窑皮增厚形成熟料圈。
③煤粉质量的影响。
灰分高、细度粗、水分大的煤粉容易
产生不完全燃烧,煤灰沉落相对比较集中,容易形成熟料圈。
另外,喂煤量不稳定,使窑内温度忽高忽低,也易形成结圈。
回转窑结圈(rotary kiln accretion)
回转窑内高温带内壁发生的炉料环状粘附现象。
轻微的粘附现象称为窑皮,如果发生粘附,影响炉子正常操作时,即谓结圈。
回转窑内的温度分布、球团内FeOMFe含量的变化和窑内发生粘附现象的实况如图1所示。
粘附成长的主要原因是窑内的氧化气氛,其次是窑内温度过高、料层内还原剂不足或低还原的浮氏体(FeO)进入高温带。
炉料窑皮
横轴距卸料端/m
纵轴炉温分布 T/℃
图1 回转炉冶炼过程球团成分的变化与冶炼1100h后炉内的
粘附状况
图2回转炉内还原过程的自动粘附
窑皮和结圈料的化学成分
窑内发生粘附的机理可由图2说明:球团在窑内受摩擦与应力产生的矿粉和煤灰的混合物自A点向B点转动时受到炉气的氧化作用,使部分还原的矿粉氧化成浮士体(FeO),并与煤灰中的SiO2。
形成低熔点的硅酸铁,在1050~1100℃温度下就会软化粘附在炉壁上。
当
形成的FeO不多时,粘附的粉料会靠自重剥落下来。
而当氧化气氛强或温度过高时,形成较多的低熔物料,黏性增大,直至C点也不剥落,这就形成窑皮,如果粘附不断长厚,就成结圈。
窑皮和结圈料的成分如表中所示。
根据结圈形成机理分析可知,在工艺操中防止回转窑结圈的主要措施有:(1)提高球团矿强度,增加球团矿的抗磨性;(2)采用反应性好、灰分熔点高的煤作还原剂;(3)窑内高温带保持强还原性操作;(4)采用尽可能低的还原温度(<1050℃)。
在工业上采用机械的方法,定期处理回转窑高温带内壁的粘结物。