第四节机械加工工艺路线的拟定.
机械加工工艺路线的拟定

1.精基准的选择
4) “自为基准”原则
图7-10 在自为基准条件下磨削车床床身导轨面
机械加工工艺路线的拟定
2.精基准的选择
5) 一定要保证工件定位准确,夹紧稳定 可靠,夹具结构简单,工人操作简便。
机械加工工艺路线的拟定
2.粗基准的选择
1) 若工件必须首先保证某重要表面的加工余量 均匀,则应选择该表面为粗基准。
5.加工方法要与工厂现有生产条件相适 应
机械加工工艺路线的拟定
三、加工阶段的划分
1.粗加工阶段 2.半精加工阶段 3.精加工阶段 4.光整加工阶段
机械加工工艺路线的拟定
划分加工阶段的原因有:
1)为了保证加工质量。 2)可以及早发现毛坯缺陷,以便及时报废
或修补,避免继续加工造成浪费。 3)可以合理使用机床设备。
图7-11 床身加工粗基准的两种方案比较
机械加工工艺路线的拟定
2.粗基准的选择
1) 若工件必须首先保证某重要表面的加工余量 均匀,则应选择该表面为粗基准。
图7-11 床身加工粗基准的两种方案比较
机械加工工艺路线的拟定
2.粗基准的选择
2) 在没有要求保证重要表面加工余量均匀的情况 下,若零件的所有表面都要加工,则应以加工余 量最小的表面作为粗基准。
机械加工工艺路线的拟定
四、工序内容的合理安排
1.工序集中
如果在每道工序中所安排的加工内容多, 则一个零件的加工就集中在少数几道工序 里完成,这样,工艺路线短,工序少,称 为工序集中。
机械加工工艺路线的拟定
四、工序内容的合理安排
2.工序分散
如果在每道工序中所安排的加工内容少, 把零件的加工内容分散在很多工序里完成, Leabharlann 工艺路线长,工序多,称为工序分散。
机械加工工艺路线的拟定

机械加工工艺路线的拟定1. 引言机械加工工艺路线是指在制造过程中,针对特定零件的加工工艺步骤的拟定和安排。
它是实现零件加工的关键,直接影响到产品质量和生产效率。
本文将介绍机械加工工艺路线的拟定过程及其重要性,并提出一些方法和技巧,以帮助制造企业制定高效的工艺路线。
2. 机械加工工艺路线的拟定过程机械加工工艺路线的拟定是一个复杂的过程,需要考虑多种因素,包括材料特性、工艺装备条件、工艺控制要求等。
以下是机械加工工艺路线的拟定过程的主要步骤:2.1 确定零件的加工难度首先需要对零件的几何形状、尺寸和材料进行分析,确定零件的加工难度。
加工难度包括工艺性能、切削性能和热处理性能等因素。
根据这些因素,可以初步确定合适的加工方法和工艺路线。
2.2 选择合适的工艺装备根据零件加工的特点和要求,选择合适的加工设备和工艺装备。
这些设备包括机床、刀具、夹具等。
选择合适的设备对于提高加工效率和保证加工质量非常重要。
2.3 制定切削参数根据选择的加工方法和设备,制定合适的切削参数,包括切削速度、进给量和切削深度等。
切削参数的选取将直接影响到加工过程的效率和质量。
2.4 确定工装方案根据零件的形状和特点,确定合适的工装方案。
工装的设计和使用对于提高加工精度和保证零件一致性非常重要。
2.5 设计工艺文件根据前面的步骤,编制详细的工艺文件,包括加工顺序、工艺参数、工装设计、设备要求等。
工艺文件将作为实际加工的依据,对于保证产品质量和提高生产效率非常重要。
3. 机械加工工艺路线的重要性机械加工工艺路线的拟定对于制造企业来说具有重要的意义。
以下是几个方面的重要性:3.1 提高生产效率合理的工艺路线可以最大限度地利用设备和资源,提高生产效率。
通过合理的工艺路线规划,可以最大限度地减少加工次数和加工时间,实现生产的高效率。
3.2 保证产品质量合理的工艺路线可以确保产品在加工过程中的质量。
通过精确的工艺参数和工装设计,可以保证产品的尺寸精度和表面质量。
机械加工工艺路线的拟定
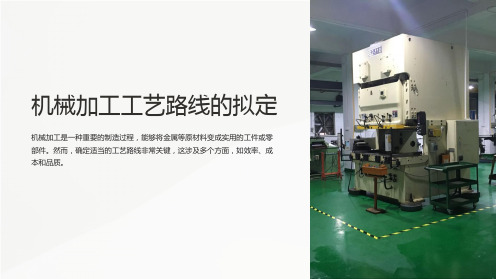
专业设备
先进的机械设备和工艺流程可提 高生产效率和产品质量。
精密工艺
严格的质量控制和工序管理可确 保产品的精度和质量。
人员素质
专业的操作技能和高效的管理决 策能力,是机械加工成功的关键。
3 可靠性
机械加工的过程严格控制,可以保证产品的质量和可靠性。
流程规划
1
制定计划
2
确定生产计划、生产线布局,评估生产
所需的成本和资源。ຫໍສະໝຸດ 3路线设计4
根据要求和资源,确定适当的工艺路线,
包括切削过程、加工顺序等。
5
风险评估
6
评估生产中可能存在的风险和问题,并
制定应对措施。
7
设定目标
明确产品的加工要求,包括尺寸、表面 处理、性能等。
机械加工工艺路线的拟定
机械加工是一种重要的制造过程,能够将金属等原材料变成实用的工件或零 部件。然而,确定适当的工艺路线非常关键,这涉及多个方面,如效率、成 本和品质。
背景介绍
机械加工是制造业的关键领域之一,广泛应用于汽车、航空、医药等行业。在全球市场中,中国是最大的钢铁 消费国,也是最大的工程机械市场之一。
现代设备
现代化技术和设备为机械加工提 供了更高效、质量更好的解决方 案。
设计和规范
精确的设计和规范能够确保工件 的精度和质量。
工艺流程
高效的工艺流程可以提高生产效 率和降低成本。
机械加工的重要性
1 高精度
机械加工能够获得高精度的工件,满足现代工业对产品精度的要求。
2 多样性
机械加工能够加工各种材料和形状的工件,具有很强的适应性和灵活性。
确定资源需求
确定需要的原材料、零部件、工具和设 备等资源,保证生产顺利开展。
车床铣床机械加工工艺路线拟定

表面精度越高,表面粗糙度越高,它经过的加 工次数就越多。(表1-10、11、12)
选经济精度
一个表面可有不同的加工方法获得――不同的加 工方法不同的技术经济特性(加工一定范围的精 度)
在I、Ⅲ段应用此法加工是不经济的。 在Ⅱ段,加工方法与加工精度是相互适应的,加
工误差与成本基本上是反比关系,可以较经济地 达到一定的精度,
Ⅱ段的精度范围就 称为这种加工方法的
经济精度:
在正常的生产条件下,
稳定可靠达到的精度
2、考虑零件的材料、结构形状及热处理方式
同一种加工精度、表面粗糙度有若干加工方法获得
例:箱体IT7级孔 选择镗?铰?不宜?
淬火的孔 因HRC高 磨孔
本节学习的主要任务: 了解工艺路线拟定要解决的主要问题:
加工方法的选择 加工阶段的划分 工序的集中和分散 工序顺序的安排
机加工艺规程的制定,大致为二个方面: 拟定工艺路线:(是最重要的工作,总体 布局)
加工方法、工序数目、工序顺序。 确定工序内容:
工序尺寸、设备、工艺装备等。
要求编制者:即有丰富的实际经验又有一定的理 论知识,还得具备正确的工作方法。
(特点)
考虑依据:
生产类型,零件形状,技术要求,设备、工厂现有情 况,全面分析各种因素。
一般情况下:
1、在单件小批生产中工序集中:
一般采用通用设备和工艺装备,尽可能在一台机床上完成 较多的表面加工,尤其是对重型零件的加工,为减少装夹 和往返搬运的次数,多采用工序集中的原则。
2、大批量可集中,可分散
――――加工阶段的划分不是绝对的 举例(毛坯余量大。 加工精度低。 重型等)
机械加工工艺路线

机械加工工艺路线机械加工工艺规程的制定,大体可分为两个步骤。
首先是拟定零件加工的工艺路线,然后再确定每一道工序的工序尺寸、所用设备和工艺装备以及切削规范、工时定额等。
这两个步骤是互相联系的,应进行综合分析。
工艺路线的拟定是制定工艺过程的总体布局,主要任务是选择各个表面的加工方法,确定各个表面的加工顺序,以及整个工艺过程中工序数目的多少等。
拟定工艺路线的一般原则1、先加工基准面零件在加工过程中,作为定位基准的表面应首先加工出来,以便尽快为后续工序的加工提供精基准。
称为“基准先行”。
2、划分加工阶段加工质量要求高的表面,都划分加工阶段,一般可分为粗加工、半精加工和精加工三个阶段。
主要是为了保证加工质量;有利于合理使用设备;便于安排热处理工序;以及便于时发现毛坯缺陷等。
3、先孔后面[1] 对于箱体、支架和连杆等零件应先加工平面后加工孔。
这样就可以以平面定位加工孔,保证平面和孔的位置精度,而且对平面上的孔的加工带来方便。
4、主要表面的光整加工(如研磨、珩磨、精磨等),应放在工艺路线最后阶段进行,以免光整加工的表面,由于工序间的转运和安装而受到损伤。
上述为工序安排的一般情况。
有些具体情况可按下列原则处理。
(1)、为了保证加工精度,粗、精加工最好分开进行。
因为粗加工时,切削量大,工件所受切削力、夹紧力大,发热量多,以及加工表面有较显著的加工硬化现象,工件内部存在着较大的内应力,如果粗、粗加工连续进行,则精加工后的零件精度会因为应力的重新分布而很快丧失。
对于某些加工精度要求高的零件。
在粗加工之后和精加工之前,还应安排低温退火或时效处理工序来消除内应力。
(2)、合理地选用设备。
粗加工主要是切掉大部分加工余量,并不要求有较高的加工精度,所以粗加工应在功率较大、精度不太高的机床上进行,精加工工序则要求用较高精度的机床加工。
粗、精加工分别在不同的机床上加工,既能充分发挥设备能力,又能延长精密机床的使用寿命。
(3)、在机械加工工艺路线中,常安排有热处理工序。
零件机械加工工艺路线的拟定
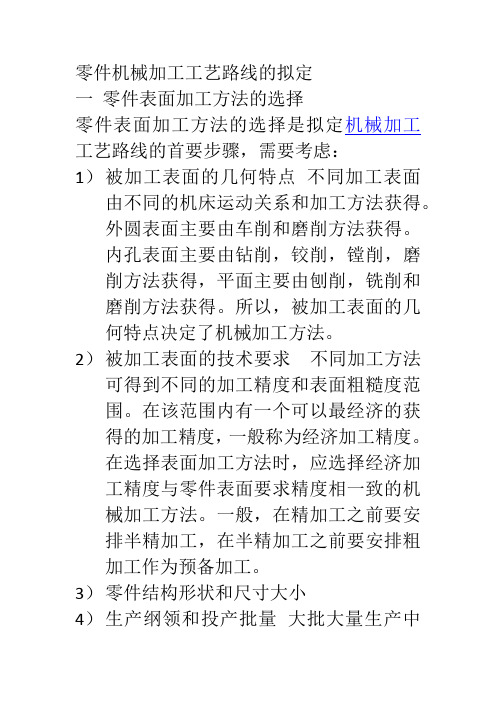
零件机械加工工艺路线的拟定
一零件表面加工方法的选择
零件表面加工方法的选择是拟定机械加工工艺路线的首要步骤,需要考虑:
1)被加工表面的几何特点不同加工表面由不同的机床运动关系和加工方法获得。
外圆表面主要由车削和磨削方法获得。
内孔表面主要由钻削,铰削,镗削,磨
削方法获得,平面主要由刨削,铣削和
磨削方法获得。
所以,被加工表面的几
何特点决定了机械加工方法。
2)被加工表面的技术要求不同加工方法可得到不同的加工精度和表面粗糙度范
围。
在该范围内有一个可以最经济的获
得的加工精度,一般称为经济加工精度。
在选择表面加工方法时,应选择经济加
工精度与零件表面要求精度相一致的机
械加工方法。
一般,在精加工之前要安
排半精加工,在半精加工之前要安排粗
加工作为预备加工。
3)零件结构形状和尺寸大小
4)生产纲领和投产批量大批大量生产中
应采用高生产率的加工方法。
综合上述,选择零件表面加工方法时,要首先根据表面种类和技术要求,找出可供选用而最后精加工方法及路线。
机械加工工艺规程制订课题三机械加工工艺路线的拟定

模块四 机械加工工艺规程制订
课题三 机械加工工艺路线的拟定
教案配套教材
1、如有错误及需改
进之处 2、如需要其他相关 资料 请留言:
ssss75828@
课题三 机械加工工艺路线的拟定
知识点
基准及其分类 定位基准的选择 表面加工方法的确定 加工顺序的安排
技能点
图4-16工件用夹具定位
1-定位键 2-夹具体 3-对刀块 4-偏心轮5-支承套 6、7-V形块
2.定位基准的选择
在各加工工序中,保证被加工表面的尺寸和位置精度的方法是 制定工艺过程的重要任务,而定位基准的作用主要是保证工件各表面 之间的相互位置精度。因此,在研究和选择各类工艺基准时,首先 应选择定位基准。 (1)定位基准选择的基本原则
01
2)基准统一原则 即选择同一定位基准来加工尽可能多的 表面,以保证各加工表面的相互位置精度,避免产生因基准变 换所引起的误差。 例如,加工较精密的阶台轴时,通常采用两中心孔作定位 基准,这样在同一定位基准下加工的各档外圆表面及端面容易 保证高的位置精度,如圆跳动、同轴度、垂直度等。采用同一 定位基准,还可以使各工序的夹具结构单一化,便于设计制造。
表4-8
序号 1 2 粗车 粗车-半精车
外圆加工方案
加工方法 经济精度 I12~IT11 IT9~IT8 表面粗糙度Ra 50~12.5 6.3~3.2 适用范围
3
4 5 6 7 8
粗车-半精车-精车
粗车-半精车-精车-滚压(或抛光) 粗车-半精车-磨削 粗车-半精车-粗磨-精磨
IT7~IT6
IT6~IT5 IT7~IT6 IT6~IT5 IT5 IT6~IT5
基准。
图4-23 基准不重合误差最小条件
《工艺路线拟定》课件

案例一:机械加工工艺路线拟定
确定加工顺序和装夹 方式,确保加工稳定 性和精度。
优化工艺流程,减少 加工时间和成本。
制定加工工艺参数, 如切削速度、进给量 、切削深度等。
案例二:化学合成工艺路线拟定
• 总结词:针对目标化合物,设计高效、低成本的 合成路径。
案例二:化学合成工艺路线拟定
详细描述 分析目标化合物的结构,确定关键的反应位点和合成步骤。
优化步骤
确定优化目标
根据评估结果,明确优化的具 体目标,如提高效率、降低成 本等。
实施优化方案
将优化方案付诸实践,进行试 验和验证,确保方案的有效性 和可行性。
现状评估
对现有工艺路线进行全面评估 ,了解存在的问题和改进空间 。
制定优化方案
根据优化目标,制定具体的优 化方案,包括改进工艺流程、 调整工艺参数等。
效果评估
对优化后的工艺路线进行效果 评估,比较优化前后的差异和 改进程度。
05
工艺路线拟定案例
案例一:机械加工工艺路线拟定
• 总结词:针对复杂机械零件的加工,制定高效、低成本的 工艺流程。
案例一:机械加工工艺路线拟定
详细描述 分析零件图纸,明确加工要求和精度要求。
选择合适的加工设备和工具,如车床、铣床、钻床等。
工艺路线的重要性
确保生产过程的顺畅和高效
合理的工艺路线能够和浪费。
提高生产效率和产品质量
通过优化工艺路线,可以减少生产过 程中的等待和重复加工时间,提高生 产效率和产品质量。
降低生产成本
合理的工艺路线可以减少设备和人力 资源的浪费,降低生产成本。
案例三:电子产品装配工艺路线拟定
详细描述 分析产品结构和装配要求,确定装配顺序和装配方法。
第4讲工艺路线的拟定
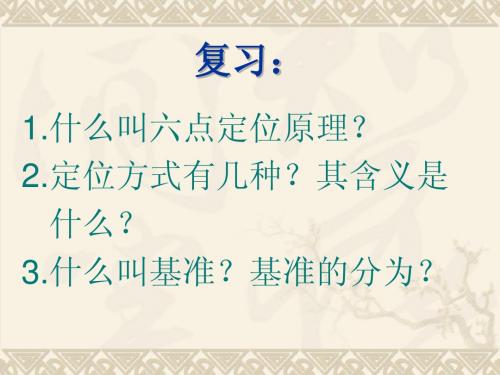
输出轴
设计 绘图 审阅
比例 数量
1:1 1
图号 材料
45 钢
广西电力职业技术学院
技能练习
在批量生产下图箱体零件时, 其工艺路线如下:
粗、精铣底面—粗、精铣上表
面—在卧式镗床上粗镗、半精镗、
精镗Φ70h7的孔—粗镗、半精镗、
精镗Φ90h7的孔?
课后作业:
1.机械加工工艺过程可划分为哪几个阶段?
该轴段的 精度和表面粗 糙度分别是多 少?
IT6 0.8
二、加工方法和加工方案的选择
2.典型表面加工路线 机械零件都是由外圆、孔、平面及成 型表面等组合而成,因此,零件的工艺 路线就是这些表面加工路线的恰当组合。
三、加工阶段的划分
1.粗加工阶段:切除大部分余量。
2.半精加工阶段:使次要表面达到图纸要
各加工工序的先后顺序。
拟定工艺路线就是根据零件每个加工表面的精度、
粗糙度及技术要求,确定每个表面的工序,然后按
顺序将各个工序排列起来。
二、加工方法和加工方案的选择
1.经济精度和经济表面粗糙度 在正常的加工条件下(采用符合质量 标准的设备、工装和标准技术等级的工 人,合理的加工时间)所能保证的加工 精度,相应的粗糙度称为经济表面粗糙 度。
2.简述机械加工工序安排的原则?
3.工序集中和工序分散的特点?
复习:
1.什么叫六点定位原理? 2.定位方式有几种?其含义是 什么? 3.什么叫基准?基准的分为?
P 96~
教学目标
一、能合理选择零件表面的加工 方法; 二、能拟定简单工件的工艺路线
教学重点
一、拟定工艺路线
教学难点
一、拟定工艺路线。
车
铣
磨
机械制造技术课程教案6
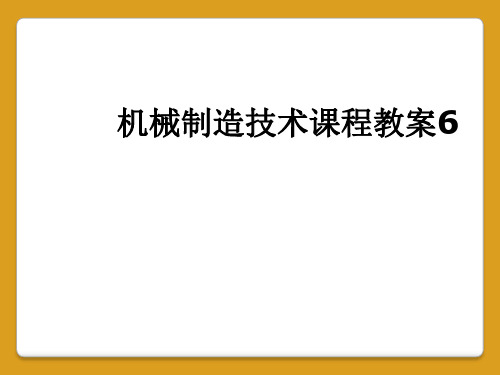
二、加工阶段的划分
加工阶段
划分加工阶段的原因
1、保证加工质量 2、合理使用设备 3、便于安排热处理工序 4、便于及时发现毛坯缺陷 5、避免重要表面损伤。
粗加工阶段 半精加工阶段 精加工阶段 光整加工阶段
切除大量多余材 料,主要提高生 产率。
完成次要表面加工(钻、 攻丝、铣键槽等)主要表 面达到一定要求,为精 加工作好余量准备安排 在热处理前。
•便于分解独立装配单元 •便于平行、流水作业 •调整方便、减轻装配劳动 •便于达到装配精度
第三节 定位基准选择
定位基准
1、粗基准 2、精基准
采用毛坯上未经加工 的表面作为定位基准。
采用经过加工的表面 作为定位基准。
一、精基准选择
重点考虑: •减少定位误差 •保证加工精度
1、基准重合原则
举例
(1)设计基准与定位基准不重合误差只发生在用调整法获得加工尺寸的情况。 (2)基准不重合误差值等于设计基准与定位基准之间尺寸的变化量。 (3)基准不重合一般发生在下列情况:
四、加工顺序的安排 1.机械加工顺序的安排
基面先行 先粗后精 先主后次 先面后孔 进给路线短 换刀次数少
2. 热处理工序的安排
位置:粗加工前 目的:改善切削性能,消除内应 力
位置:半精加工后,精加工前 目的:提高强度、硬度
位置:粗加工前、后,半 精加工后,精加工前 目的:消除内应力,防止 变形、开裂。
二、机械加工工艺过程及其组成
机械加工工艺过程是指用机械加工方法(主要是切削加工方法)逐步改变毛坯的形态(形状、 尺寸以及表面质量),使其成为合格零件所进行的全部过程。它一般由工序、工步、走刀等不同层 次的单元所组成。
1. 工 序
一个或一组工人在一个工作地点,对一个或同时对几个工件所连续完成的那部分工艺过程叫 工序。例如图3-4
第四节 机械加工工艺路线的拟定综述

4.粗车-半精车-粗磨-精磨-研磨、超精加工、砂带磨、 镜面磨等
• 最终工序:光整加工 • 适用范围:要求高的钢件的精加工 • 加工精度:加工精度低于IT5,表面粗糙度等 于或大于Ra0.006
(二)孔的加工路线
(二)孔的加工路线
2. 加工经济精度的评价
• 生产上加工精度的高低用可控制的加工误差大 小表示。加工误差小则加工精度高;加工误差 大,则加工精度低。统计资料表明:加工成本 与加工误差成反比关系
(1)同种加工方法,精度越高,加工 成本越高,呈指数增长 ( 2)精度有一定极限,当超过 A点, 即使成本再增加,加工精度提高极少; ( 3)成本有一定极限,但超过 B点, 即使再减低加工精度,加工成本降低极 少;
(4)曲线AB段,加工成本与加工精 度互相适应,属于经济精度的范围;
3. 加工经济精度的发展
• 加工精度随机械工业发展,不断提高, 加工成本不断降低,因此各种加工方法 的经济精度不是不变的。
4. 各种加工方法的加工经济精度
(1)外圆加工中各种加工方法的加工经济精 度及表面粗糙度
4. 各种加工方法的加工经济精度
4. 各种加工方法的加工经济精度
• (2)孔加工中各种加工方法的加工经济精度 及表面粗糙度
4. 各种加工方法的加工经济精度
4. 各种加工方法的加工经济精度
(3)平面加工中各种加工方法的加工经济精 度及表面粗糙度
4. 各种加工方法的加工经济精度
(二)加工ห้องสมุดไป่ตู้法的选择
(1)加工经济精度
任何一种加工方法能获得的加工精度和表面粗 糙度都有一个相当大的范围,但只有在某一个 较窄的范围才经济,这个范围的加工精度就是 加工经济精度。为此,在选择加工方法时,应 选择相应的能获得经济加工精度的加工方法。
一、工艺路线的拟定课件

2.工件的形状和尺寸 IT7孔:镗,铰,拉,磨; 箱体:大孔,镗; 小孔,钻,扩,铰。
(三)各种表面的典型加工路线
1.外圆表面加工路线
(1)粗车—半精车—精车 精度低
(2)粗车—半精车—粗磨—精磨黑色金 属,IT6,Ra0.4um,精度高
(3)检验
(4)铣C面保证尺寸70及Ra5,铣B面保证
尺寸26及Ra5 。 (5)钻、扩、铰Ф15孔至Ф150+0.019 及
Ra2.5。
(6)修毛刺,倒锐棱 (7)插键槽100.0200.075 及Ra10,保证尺寸
39.60+0.14 (8)检验
为何A面用车削,B、C面却用铣削
A面与Φ360+0.027 轴线有垂直度要求,应
2. 工艺装备的选择 考虑因素:工件材料、形状、尺寸、精 度、生产率、生产类型及机床、工艺方案 等,与之相适应。
(1)夹具 单件小批:通用夹具;机床附 件;组合夹具; 大批大量:专用夹具 中小批生产:可调夹具或成组夹具
(2)刀具 单件小批:标准刀具; 大批大量:专用或复合刀具;多刃刀具
(3)量具 单件小批:通用量具(游标卡尺、百 分尺、千分表等) 大批大量:极限量规、检验夹具、检验仪器
3.生产类型
大批大量生产: 选高生产率,质量稳定的 加工方法 平面、孔—拉削,轴—仿形车 单件小批生产,通用加工方法 平面—刨,铣, 孔—钻,扩,铰,镗。 数控机床,加工中心。
4.具体生产条件 利用现有设备和工艺手段,工人的技术水 平,挖掘潜力,重视新工艺,新技术,兼 顾设备的负荷平衡。
(二)选择表面加工方法考虑的因素
机械制造工艺学
机械加工中工艺路线的拟定原则

机械加工中工艺路线的拟定原则作者:裴加梅来源:《环球市场信息导报》2016年第02期表面加工方法的选择根据不同的加工类型选择合适的加工方法,不但能保证加工质量,还能提高生产率并降低生产成本。
加工同一类型的工件表面会有多种加工方法,如何合理选择加工方法主要考虑以下几个因素:工件的表面形状、加工技术要求、加工精度、以及工件的整体形状和材料性能等,此外生产量和生产条件也是重要考虑因素。
常见的表面加工方法外圆表面加工方案。
根据不同的加工精度等级和表面粗糙度要求选择合理的加工方案。
精度等级为IT12-IT10.精度要求不高,一般选择粗车一半精车加工方案;IT9-IT6,精度要求较高,此时一般选择粗车一半精车一精车加工方案;当加工精度为IT5以上时,加工精度高,此时一般选择粗车一半精车一精车一精磨一超精磨加工方案。
孔加工方案。
精度等级为ITl2-ITl0,精度要求不高,一般选择钻一铰加工方案;IT9-IT6,精度要求较高,此时一般选择钻一粗铰一精铰加工方案;当加工孔径大于20mm时,选择钻-扩-粗铰-精铰等加工方案。
平面加工方案。
精度等级为IT9-IT8,精度要求不高,一般选择粗车一半精车加工方案;IT7-IT6,精度要求较高,此时一般选择粗车一半精车一精车加工方案;当加工精度为IT5以上时,加工精度高,此时一般选择粗车-半精车-精车-精磨-超精磨加工方案。
加工阶段的划分划分加工阶段可以有效的较少变形对加工精度的影响;合理选择和使用设备,有效的避免浪费,节约成本;合理组织生产工艺过程,提高生产效率。
根据加工精度的不同划分不同的阶段,精度要求较高的。
结构形状较复杂的一般需要划分为粗加工、半精加工、精加工三个阶段。
并不是所有的工件加工过程都需要划分为这三个阶段,对于一些工件简单,余量较小的毛坯可以省略掉粗加工,对于毛坯余量比较大的工件一般需要粗加工去皮。
工序的划分工序分集中和分散俩个基本原则,工序集中主要指在一道工序中尽可能多的包含加工内容,使工艺过程中总的工序数量减少,最集中的工艺过程只包含一道工序,直接把工件加工到图样要求。
工艺路线的拟定

根据是否热处理及热处理方法选择
例6: 挡块和平行垫铁平面加工案
① 挡块(调质240HBS): 粗铣(或粗刨)—调质—半精铣(或半精刨)—精铣(或精刨)。 ② 平行垫铁(淬火50HRC): 粗铣(或粗刨)—半精铣(或半精刨)—淬火—磨。
加工方法选择的步骤 首先确定被加工零件主要表面的最终加 工方法,然后再选择前面一系列的预备工 序加工方法和顺序。由于获得同一精度和 粗糙度的加工方法往往有几种,可提出几 个方案进行比较,选择其中一个比较合理 的方案。
铰孔
1、分类 (1)粗铰:IT8~IT7, Ra:1.6~0.8μm。 (2)精铰:IT7~IT6, Ra:0.4~0.2μm。 2、刀具:铰刀:φ10~100 常用 φ10~40 3、设备:钻床、镗床、车床、铣床。 4、铰削特点 (1)精度高,表面粗糙度小。 (2)铰孔纠正位置误差的能力很差,位置精度需由前工序 保证。 (3)铰刀是定径刀具,易保证铰孔质量。 (4)铰削的适应性差。 (5)铰削可加工钢、铸铁和有色金属零件,不宜加工淬火 或硬度过高的工件。
粗车—半精车—粗磨—精磨—研磨。 ② 锡青铜阀杆( 25h4,Ra0.05 m)
粗车—半精车—精车—研磨。
例3:三种块状零件小孔加工方案。
① T10A(已淬火,1000件):电火花穿孔。 ② 玻璃(1000件):超声波穿孔。 ③ 尼龙(1000件):激光打孔。
根据表面所在零件的结构选择
)粗拉:IT8~IT7, Ra:1.6~0.8 μm (2)精拉:IT7~IT6, Ra:0.8~0.4 μm 2、拉削的特点 (1)精度高,表面粗糙度小。 (2)生产率高。 (3)不能纠正孔的轴线歪斜。 (4)拉削对前道工序要求不高。 (5)拉削不能加工台阶孔、盲孔、薄壁零件的孔。
机械加工工艺路线的拟定

法。
3、机床设备与工艺装备的选择
机床设备和工艺装备的选择:
1、所选机床设备的尺寸规格应与工件的形体尺寸相适应;
2、精度等级应与本工序加工要求相适应;
3、电机功率应与本工序加工所需功率相适应;
4、机床设备的自动化程度和生产效率应与工件生产类型相适应。
工艺装备的选择将直接影响工件的加工精度、生产效率和制造成本,应根据不同情况适当选择:
1、在中小批生产条件下,应首先考虑选用通用工艺装备(包括夹具、刀具、量具和辅具);
2、在大批大量生产中,可根据加工要求设计制造专用工艺装备。
机床设备和工艺装备的选择不仅要考虑设备投资的当前效益,还要考虑产品改型及转产的可能性,应使其具有足够的柔性。
第五章 机械加工工艺规程制定
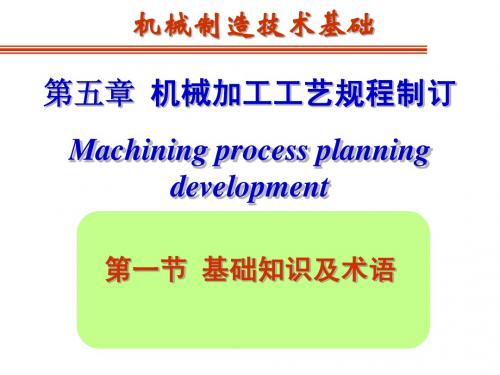
第一节 基础知识及术语
一、生产过程和工艺过程 生产过程 在机械产品制造中,将 原材料(或半成品)转变为成 品的全过程。
第一节 基础知识及术语
工艺过程 在生产过程中,毛坯的制造、零件的机械加工与热处理、 产品的装配等工作将直接改变生产对象的采用形状、尺寸、 相对位置和性质等,使其成为成品和半成品的过程。 主要内容 毛坯和零件成形——铸造、锻压、冲压、 毛坯和零件成形——铸造、锻压、冲压、焊接 、压制、烧结、 压制、烧结、 注塑、 注塑、压塑 … 机械加工——切削、磨削、 机械加工——切削、磨削、特种加工 材料改性与处理——热处理、电镀、转化膜、涂装、 材料改性与处理——热处理、电镀、转化膜、涂装、热喷涂 … 机械装配——把零件按一定的关系和要求连接在一起, 机械装配——把零件按一定的关系和要求连接在一起,组合成 部件和整台机械产品, 包括零件的固定、 连接、 调整、 平衡、 部件和整台机械产品 ,包括零件的固定、 连接、 调整、 平衡 、 检 验和试验等工作
第一节 基础知识及术语
获得尺寸精度的方法 试切法 试切—测量—调整—再试切,反复进行直到被加工 尺寸(工序尺寸)达到要求精度为止的加工方法。 调整法 在机床上先调整好刀具和工件在工序尺寸方向上的 相对位置,并在一批工件的加工过程中保持这个位置不变,以 保证工件工序尺寸精度的方法。 定尺寸刀具法 用刀具的相对尺寸来保证工件被加工部位工 序尺寸的方法。 主动测量法 在加工过程中,利用自动测量装置边加工边测 量加工尺寸,并将测量结果与要保证的工序尺寸比较后,或使 机床继续工作,或使机床停止工作的方法。 自动控制法 在加工过程中,利用测量装置或数控装置等自 动控制加工过程的加工方法。
- 1、下载文档前请自行甄别文档内容的完整性,平台不提供额外的编辑、内容补充、找答案等附加服务。
- 2、"仅部分预览"的文档,不可在线预览部分如存在完整性等问题,可反馈申请退款(可完整预览的文档不适用该条件!)。
- 3、如文档侵犯您的权益,请联系客服反馈,我们会尽快为您处理(人工客服工作时间:9:00-18:30)。
(二)划分加工阶段的目的(原因)
• 4.便于安排热处理工序 • 一般零件在工艺过程中插入了必要热处理工序, 热处理通常安排在粗加工精加工之间。如粗加 工后,一般要安排去应力的热处理,以消除内 应力。精加工前安排淬火等最终热处理,其变 形可以通过精加工给以消除。 注意:粗、精加工分开的原则既适用于某一表 面的加工过程,也适用于整个零件的工艺过程。 但加工阶段的划分也不应绝对化,应根据零件 的质量要求、结构特点和生产纲领灵活掌握。 对加工质量要求不高、工件刚性好、毛坯精度 高、加工余量小、生产批量不大时,可不必划 分加工阶段。
• 特点:用于中、小孔的加工。扩孔能纠 正位置精度。铰孔只能保证尺寸、形状 精度和减小孔的表面粗糙度
(二)孔的加工路线
3.钻(粗镗)-半精镗-精镗-浮动镗(金刚镗) • (1)单件小批生产中的箱体孔系加工 • (2)位置精度要求很高的孔系加工 • (3)直径比较大的孔 • (4)材料为有色金属,需要用金刚镗来保证 尺寸、形状和位置精度以及表面粗糙度的要求 4.钻(粗镗)-粗磨-半精磨-精磨-研磨或珩磨 • 主要用于淬硬零件加工或精度要求高的孔加工
(二)加工方法的选择
(6)选择加工方法应考虑零件结构、加 工表面的特点和材料性质等因素。 •零件结构和表面特点不同,所选择的加工 方法也不同。
(二)加工方法的选择
(7)对于那些有特殊要求的加工表 面
例如,相对于本厂工艺条件来说,尺寸 特别大或特别小,工件材料难加工,技 术要求高,则首先应考虑在本厂能否加 工的问题,如果在本厂加工有困难,就 需要考虑是否需要外协加工。
回转体加工视频
(三)平面加工路线
(三)平面加工路线
1.粗铣-半精铣-精铣-高速铣 • 通用加工路线,生产率比较高。 2.粗刨-半精刨-精刨-宽刀细刨、刮研或研磨 • 刮研多用于单件小批生产中配合表面要求高且 不淬硬平面的加工。当批量较大时,可用宽刀 细刨代替刮研。宽刀细刨特别适用于狭长平面 3.粗铣(刨)—半精铣(刨)—粗磨—精磨— 研磨、精密磨、砂带磨或抛光 • 磨削适用于直线度及表面粗糙度要求高的淬硬 工件和薄片工件,也适用于未淬硬钢件上面积 较大的平面的精加工。但不宜加工塑性较大的 有色金属。
2. 加工经济精度的评价
• 生产上加工精度的高低用可控制的加工误差大 小表示。加工误差小则加工精度高;加工误差 大,则加工精度低。统计资料表明:加工成本 与加工误差成反比关系
(1)同种加工方法,精度越高,加工 成本越高,呈指数增长 ( 2)精度有一定极限,当超过 A点, 即使成本再增加,加工精度提高极少; ( 3)成本有一定极限,但超过 B点, 即使再减低加工精度,加工成本降低极 少;
4. 各种加工方法的加工经济精度
• (2)孔加工中各种加工方法的加工经济精度 及表面粗糙度
4Hale Waihona Puke 各种加工方法的加工经济精度4. 各种加工方法的加工经济精度
(3)平面加工中各种加工方法的加工经济精 度及表面粗糙度
4. 各种加工方法的加工经济精度
(二)加工方法的选择
(1)加工经济精度
任何一种加工方法能获得的加工精度和表面粗 糙度都有一个相当大的范围,但只有在某一个 较窄的范围才经济,这个范围的加工精度就是 加工经济精度。为此,在选择加工方法时,应 选择相应的能获得经济加工精度的加工方法。
• (1)粗加工阶段:
• 粗加工主要是切除毛坯上大部分多余金属,为 半精加工提供定位精基准。这个阶段关键问题 是提高生产率。 • (2)半精加工阶段:
• 在这个阶段中应为主要表面的精加工作好准备 (达到一定的精度和表面粗糙度,保证一定的 精加工余量),并完成一些次要表面的加工 (如钻孔、攻丝、铣键槽等)。一般在热处理 之前进行。
第四节 机械加工工艺路线的拟定
表面加工方法的选择 加工阶段的划分 工序顺序的安排
第四节 机械加工工艺路线的拟定
• (1)拟定零件的工艺路线;
• ( 2 )确定各道工序的工序尺寸及公差、所用 设备及工艺装备、切削规范和时间定额。 • 工艺路线的拟定是制定工艺过程的总体布局, 其主要任务是:
• 机械加工工艺规程的制定,大体可分为两部分:
(二)加工方法的选择
(5)要考虑到生产类型,即要考虑生产 率和经济性的问题
• 大批大量生产时,应采用高效率的先进工艺和 专用设备.如平面和孔的加工采用拉削代替普 通的铣、刨和镗孔等加工方法,轴类零件可采 用半自动液压仿型车床加工。 • 从根本上改变毛坯的制造方法,如用粉末冶金 来制造油泵齿轮,用石腊铸造柴油机上的小尺 寸零件等,均可大大减少机械加工的劳动量。
4.粗车-半精车-粗磨-精磨-研磨、超精加工、砂带磨、 镜面磨等
• 最终工序:光整加工 • 适用范围:要求高的钢件的精加工 • 加工精度:加工精度低于IT5,表面粗糙度等 于或大于Ra0.006
(二)孔的加工路线
(二)孔的加工路线
1.钻(粗镗)-粗拉-精拉
• 适用范围:大批大量生产盘套类零件的 圆孔、单键孔和花键孔加工,加工质量 稳定、生产效率高 2.钻-扩-铰-手铰
(二)加工方法的选择
(3)加工方法选择的步骤总是首先确定 被加工零件主要表面的最终加工方法, 然再选择其他表面一系列的加工方法和 顺序。 • 可提出几个方案进行比较,选择其中一 个比较合理的方案。
(二)加工方法的选择
• (4)在被加工零件各表面加工方法分别 初步选定以后,还应综合考虑为保证各 加工表面位置精度要求而采取的工艺措 施。
(一)加工阶段的划分
• (3)精加工阶段:对于零件上精度和表面粗 糙度要求高(精度在IT7以上,表面粗糙度在 Ra0.8以下)的表面,要安排精加工。这个阶 段的任务是保证各主要表面达到图纸规定的质 量要求。 • (4)光整加工阶段:对于精度要求高(IT6级 以上),表面粗糙度小(Ra0.2以下)的零件, 在工艺过程的最后安排研磨、精密磨、超精加 工,金刚石车等加工。主要目标是提高尺寸精 度、减小表面粗糙度,一般不能提高位置精度 达到最终精度要求。
(二)孔的加工路线
2)加工精度为IT8级的孔 • 当孔径小于20mm时,可采用钻—铰方案; • 当孔径大于20mm时,可采用钻—扩—铰, 3)加工精度为IT7级的孔 • 当孔径小于12mm时,可采用钻—粗铰—精铰; • 当孔径在12mm到60mm之间时,可采用 钻—扩—粗铰—精铰方案或钻—扩—拉 4)加工精度为IT5级的孔 • 最终工序可采用手铰、精细镗、研磨或珩磨等 • 韧性较大的有色金属不宜采用珩磨,可采用研 磨或精细镗。研磨对大、小孔加工均适用,而 珩磨只适用于大直径孔的加工。
(4)曲线AB段,加工成本与加工精 度互相适应,属于经济精度的范围;
3. 加工经济精度的发展
• 加工精度随机械工业发展,不断提高, 加工成本不断降低,因此各种加工方法 的经济精度不是不变的。
4. 各种加工方法的加工经济精度
(1)外圆加工中各种加工方法的加工经济精 度及表面粗糙度
4. 各种加工方法的加工经济精度
• 例如,公差为IT7级和表面粗糙度为Ra0.4外 圆表面,通过精心车削是可以达到精度要求的, 但这不如采用磨削经济。
(二)加工方法的选择
(2)满足零件精度要求: 零件表面的加工方法,首先取决于加工表面的 技术要求。 但应注意,这些技术要求不一定就是零件图所 规定的要求。有时还可能由于工艺上的原因而 在某些方面高于零件图上的要求。 例如:由于基准不重合而提高对某些表面的加 工要求,或由于被作为精基准而可能对其提出 更高的加工要求。
五、工序顺序的安排
(一)切削加工工序的安排 • 1.基面先行原则 • 用作精基准的表面,应优先加工。因为后续加 工其它表面要它来定位,定位基准的表面越精 确,装夹误差就越小。所以任何零件的加工过 程,总是首先对定位基准面进行粗加工和半精 加工,必要时还要进行精加工。 • 例如,轴类零件总是先加工中心孔,再以中心 孔为精基准加工外圆表面和端面。箱体类零件 总是先加工定位用的平面及两个定位孔,再以 平面和定位孔为精基准加工孔系和其它平面。
(三)平面加工路线
4.粗拉—精拉 • 这条加工路线主要在大批量生产中的加工质量 要求较高且面积较小的平面,生产率高。尤其 对有沟槽或台阶的表面,拉削加工的优点更加 突出。但是由于拉刀和拉削设备昂贵,因此, 这条加工路线只适合在大批大量生产中使用。 5· 粗车—半精车—精车—金刚石车 • 这条加工路线主要用于有色金属零件的平面加 工,以及回转体零件的端面的加工,以保证端 面与回转轴线的垂直度。如果被加工零件是黑 色金属,则精车后可安排精密磨、砂带磨或研 磨,抛光等。
(二)划分加工阶段的目的(原因)
• 1.保证加工质量 • 工件在粗加工时,切除的金属较厚, 切削力和夹紧力都比较大,切削温度也 比较高,这将引起工件较大的变形。若 不划分加工阶段,粗、精加工混在一起, 就无法避免上述原因引起的加工误差。 按加工阶段进行加工,粗加工造成的加 工误差可以通过半精加工和精加工来纠 正,从而保证零件的加工质量。
三、典型表面的加工路线
• 外圆、内孔和平面加工量大而面广,习 惯上把机器零件的这些表面称作典型表 面。 • 掌握典型表面的加工路线对制定零件加 工工艺过程是十分必要的。
(一)外圆表面加工路线
1.粗车-半精车-精车 (最通用路线)
• 最终工序:车削 • 适用范围:除淬火钢以外的各种金属 • 加工精度:加工精度低于IT7,表面粗糙度等 于或大于Ra0.8
A选择各个表面的加工方法和加工方案
B确定各个表面的加工顺序
C整个工艺过程中工序数目的多少
一、表面加工方法选择
(一)加工经济精度 • 各种加工方法(车、铣、刨、磨、钻、 镗、铰等)所能达到的加工精度和表面 粗糙度都有一定范围。 • 任何一种方法,只要精心操作,细心调 整选择合适的切削用量,其加工精度就 可以得到提高,其加工表面粗糙度就可 以减少,但是,加工精度的提高,就会 耗费较多时间,降低生产率,提高成本, 因此提出了加工经济精度的问题。