大规格陶瓷薄板工艺生产
超薄陶瓷板生产方案(一)

超薄陶瓷板生产方案一、背景随着科技的快速发展和产业结构的不断升级,陶瓷行业正面临着新的挑战和机遇。
超薄陶瓷板作为一种新型材料,具有优异的机械性能、热稳定性和化学稳定性,被广泛应用于建筑、电子、医疗、航空等领域。
目前,市场上的超薄陶瓷板需求量逐年增长,但其生产成本较高,生产工艺不够成熟,限制了其大规模应用。
因此,本研究旨在开发一种高效、低成本的超薄陶瓷板生产方案,以满足市场需求,推动产业结构升级。
二、工作原理1. 材料制备超薄陶瓷板的制备材料主要包括高纯度的氧化物、氮化物、碳化物等粉末。
这些粉末通过球磨、混合等工艺制成均匀的浆料。
浆料的浓度、粘度等参数对后续工艺有很大影响,因此需要对浆料进行严格控制。
2. 加工成型将制备好的浆料倒入模具中,采用流延法、注射成型法等工艺制成生坯。
生坯的厚度、密度、均匀性等指标对最终产品的性能有很大影响,因此需要对生坯进行严格控制。
3. 热处理将生坯放入高温炉中进行热处理,通过控制温度、气氛等参数,使生坯发生固相反应、烧结等过程,最终制成超薄陶瓷板。
热处理过程中,材料的微观结构、化学成分等会发生改变,从而影响最终产品的性能。
因此,需要对热处理过程进行严格控制。
三、实施计划步骤1. 材料制备阶段(1)选用高纯度原料粉末,采用球磨、混合等工艺制成均匀的浆料;(2)对浆料的浓度、粘度等参数进行检测和控制,确保浆料的稳定性;(3)定期对原料粉末和浆料进行质量检测,确保产品质量稳定。
2. 加工成型阶段(1)选用合适的模具和成型工艺,将浆料制成生坯;(2)对生坯的厚度、密度、均匀性等指标进行检测和控制,确保生坯的质量;(3)定期对模具和成型设备进行维护和保养,确保设备的正常运行。
3. 热处理阶段(1)将生坯放入高温炉中进行热处理,控制温度、气氛等参数;(2)对热处理过程中的温度、气氛等参数进行检测和控制,确保热处理过程的稳定性;(3)定期对高温炉进行维护和保养,确保设备的正常运行。
科技成果——大规格陶瓷薄板生产技术

科技成果——大规格陶瓷薄板生产技术适用范围建材行业,建筑陶瓷行业现状陶瓷砖生产是高能耗、高污染产业,多年来一直是国家严控的产业。
目前我国陶瓷行业年消耗相关原材料资源超过2.5亿吨,消耗煤炭超过5000万吨,并向环境排放大量的废气、废水、固体废弃物等。
成果简介1、技术原理采用新技术、新工艺、新方法实现陶瓷砖的薄型化生产,其厚度是传统陶瓷砖的1/3,实现了陶瓷生产过程节约原材料资源超过60%,整体节能超过40%,SO2、CO2等气体的排放减少近20-30%。
2、关键技术大规格陶瓷薄板布料技术、液压成型技术、烧结技术、深加工技术、包装技术。
3、工艺流程大规格陶瓷薄板的生产工艺流程图如图1所示。
主要技术指标(1)装备的主要技术性能指标:①陶瓷板规格:≥900mm×1800mm;②瓷板厚度:3-5.5mm可调;③最高烧成温度<1250℃;④烧成周期<60分钟;⑤年产量≥100万m2。
图1 大规格陶瓷薄板的生产工艺流程图(2)装备所生产的产品主要技术性能指标:①平均吸水率≤0.2%;②破坏强度≥800N;③平均断裂模数≥45MPa;④耐磨性≤135mm3;⑤内照射指数≤0.5、外照射指数≤0.9。
各项指标均符合《陶瓷砖》国家标准规定。
应用情况该技术的各项核心装备已于2012年12月通过了省级科技成果鉴定,获得15项国家发明专利。
目前,该技术已经在广东蒙娜丽莎陶瓷有限公司和山东德惠来装饰瓷板有限公司投产使用,节能减排效果明显,具有良好的社会经济效益。
典型案例典型案例1案例名称:广东蒙娜丽莎陶瓷有限公司项目建设规模:日产量3500平方米。
建设条件:大中型规模的陶瓷墙地砖生产企业。
主要技改内容:生产线建设。
使用的主要设备包括:墙地砖布料及模具系统;全自动液压压砖机;高效节能辊道窑;大规格陶瓷薄板抛光线;大规格陶瓷砖自动包装线,并配套相关的水电、能源、仓储、运输等条件。
技改投资额1500万元,建设期4个月。
增强型大规格陶瓷薄板施工工艺

增强型大规格陶瓷薄板施工工艺摘要:本文结合工程实例对增强型大规格陶瓷薄板施工工艺进行分析与研究,以供同仁参考。
关键词:增强型大规格陶瓷薄板;施工工艺一、工程概况某市妇女儿童医院是某市新建的十大民生工程,室内装修工程总建筑面积198615.92m²,含1~6号六个单体楼。
本项目装修面积大,功能分区多,其中等候区、走廊等功能大空间的墙面采用大规格陶瓷薄板施工(900mm×1800mm×5.5mm),施工面作业面较大,约3.5万平方米。
陶瓷薄板(简称薄瓷板、PP板等)是一种由高岭土黏土和其它无机非金属材料,成形后、经1200度高温煅烧等生产工艺制成的板状陶瓷制品。
在保证产品使用功能的情况下,最大限度实现产品的薄形化,产品厚度小于5.5mm,与同类产品相比,单位面积建筑陶瓷材料用量降低一倍以上,节约60%以上的原料资源,降低综合能耗50%以上,无论从原材料使用量、到生产过程中的能源消耗,都很好地实现“节材、节能”的低碳目标。
对于产品使用者而言,薄形化、轻量化大规格板材,既节约了物流运输成本,减轻建筑物的荷载,更是直接降低了物流、建筑施工的碳排放。
由于本工程为某市妇女儿童医院建设项目室内装修工程,施工质量要求严格,需达到国家装饰奖级别,而行业内大规格陶瓷薄板施工工艺参差不齐,施工质量不稳定。
基于此,我司根据项目要求及现场各项施工条件,通过多方调研,制定增强型大规格陶瓷薄板施工工艺。
我司总结以往各种墙面饰面的施工经验,结合增强型大规格陶瓷薄板施工工艺的工艺原理,认真总结形成了企业工法,并应用于我司施工的大型公装项目的施工,取得了良好的社会效益和经济效益。
二、成立项目研究小组为确保项目研究的顺利开展,我司以某市妇女儿童医院建设项目室内装修工程为研究实例,成立“增强型大规格陶瓷薄板施工工艺”为专题的研究小组,由我本人担任研究小组负责人,对“增强型大规格陶瓷薄板施工工艺”进行研究与实践,组织各专业人员参与研究,并明确了各人的分工和任务,为及时有效地完成研究成果提供了保证。
陶瓷薄板生产工艺过程探讨
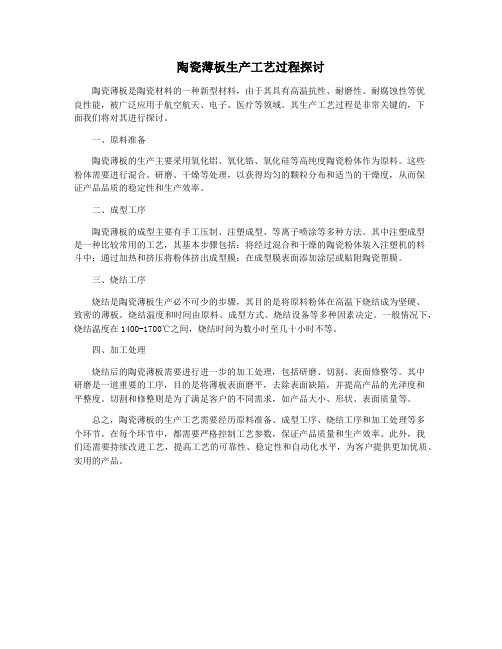
陶瓷薄板生产工艺过程探讨陶瓷薄板是陶瓷材料的一种新型材料,由于其具有高温抗性、耐磨性、耐腐蚀性等优良性能,被广泛应用于航空航天、电子、医疗等领域。
其生产工艺过程是非常关键的,下面我们将对其进行探讨。
一、原料准备陶瓷薄板的生产主要采用氧化铝、氧化锆、氧化硅等高纯度陶瓷粉体作为原料。
这些粉体需要进行混合、研磨、干燥等处理,以获得均匀的颗粒分布和适当的干燥度,从而保证产品品质的稳定性和生产效率。
二、成型工序陶瓷薄板的成型主要有手工压制、注塑成型、等离子喷涂等多种方法。
其中注塑成型是一种比较常用的工艺,其基本步骤包括:将经过混合和干燥的陶瓷粉体装入注塑机的料斗中;通过加热和挤压将粉体挤出成型膜;在成型膜表面添加涂层或贴附陶瓷帮膜。
三、烧结工序烧结是陶瓷薄板生产必不可少的步骤,其目的是将原料粉体在高温下烧结成为坚硬、致密的薄板。
烧结温度和时间由原料、成型方式、烧结设备等多种因素决定。
一般情况下,烧结温度在1400-1700℃之间,烧结时间为数小时至几十小时不等。
四、加工处理烧结后的陶瓷薄板需要进行进一步的加工处理,包括研磨、切割、表面修整等。
其中研磨是一道重要的工序,目的是将薄板表面磨平,去除表面缺陷,并提高产品的光泽度和平整度。
切割和修整则是为了满足客户的不同需求,如产品大小、形状、表面质量等。
总之,陶瓷薄板的生产工艺需要经历原料准备、成型工序、烧结工序和加工处理等多个环节。
在每个环节中,都需要严格控制工艺参数,保证产品质量和生产效率。
此外,我们还需要持续改进工艺,提高工艺的可靠性、稳定性和自动化水平,为客户提供更加优质、实用的产品。
陶瓷薄板生产工艺过程探讨

陶瓷薄板生产工艺过程探讨陶瓷薄板是一种高强度、高硬度、高耐磨、高耐温等优点的新型材料,广泛应用于工业、医疗、军事等领域。
其制造过程是一项复杂的工艺过程,需要经过多个步骤的精细加工,下面将对陶瓷薄板生产工艺过程进行探讨。
第一步:原料粉末的制备陶瓷薄板的主要成分为氧化铝、氧化锆、氧化硅等,并经过高温焙烧处理形成固态晶体结构。
因此,第一步是制备粉末原料。
一般情况下,这些原料是从矿山开采中得到,然后通过化学反应、磨碎等方法制成细粉末。
第二步:粉末的混合和均化在得到细粉末后,需要对不同比例的粉末进行混合,并进行物理方法的均化。
这样可以确保每一个颗粒的大小、形态、成分都能够得到均一分布,从而提高陶瓷薄板的均一度和成型精度。
第三步:陶瓷粘结剂的添加为了使得粉末能够紧密结合,并在成型过程中获得足够的塑性,需要添加陶瓷粘结剂。
通常采用聚乙烯醇、聚丙烯醇等有机粘结剂进行添加,混合后形成均匀的粘土状物料。
第四步:成型过程成型过程是陶瓷薄板生产的关键步骤,决定着产品的成型精度和机械性能。
常见的成型方法有注塑成型、挤出成型、压制成型等,其中压制成型最为常见。
成型前,需要对物料进行湿压干度的调节,严格控制湿度,以确保成型后的陶瓷薄片干燥均匀,没有裂纹。
第五步:烘干和烧结成型后的陶瓷薄板需要经过烘干和烧结等步骤。
烘干是将成型物料中的水分蒸发,使其达到干燥状态,以避免在烧结过程中产生裂纹等缺陷;烧结是将物料加热至高温,使其固结成型,形成陶瓷晶体,从而提高陶瓷薄板的强度和耐用性。
通常采用炉制烧结或者等离子烧结的方法进行。
第六步:加工和后处理成型后的陶瓷薄板还需要进行切割、抛光等加工处理,以获得更精确的尺寸和表面光洁度。
同时进行后处理,如热处理、喷涂等,以进一步提高产品的性能和使用寿命。
总之,陶瓷薄板生产工艺涉及到多个步骤,需要进行全面而细致的加工处理,才能最终得到具有高强度、高硬度、高耐磨和高耐温性能的优质产品。
大规格陶瓷薄板工艺生产[精选5篇]
![大规格陶瓷薄板工艺生产[精选5篇]](https://img.taocdn.com/s3/m/1e914e7bbf1e650e52ea551810a6f524ccbfcb9f.png)
大规格陶瓷薄板工艺生产[精选5篇]第一篇:大规格陶瓷薄板工艺生产大规格陶瓷薄板生产工艺★★★1.前言陶瓷薄板最初是日本利用废料研发并生产的,主要生产1200×2400×(3~6)(mm)规格的陶板,用来做推门板。
而国内生产只是这两年的事,目前有三家生产过陶瓷薄板,加上佛山樵东陶瓷马上要生产,一共四家而已。
生产这种规格的产品主要销往日本,如果内销的话可根据客户对尺寸不同要求进行切割。
而且也没必要做这种规格,可适当做小一点,做厚一点,可烧瓷化做仿古地砖。
这类产品由于薄,受热快,可大幅减少热用量,对企业发展起战略性作用。
而目前国外有一些陶瓷厂家生采用这种工艺生产渗花釉。
与施釉砖不同,它不需要淋釉,要把素烧改为干燥,印渗花釉。
2.生产工艺陶瓷薄板采用真空挤压成型,然后滚压制成6mm左右,并切割成略大1200×2400(mm)尺寸。
最后干燥素烧、施釉、印花、釉烧等。
具体工艺流程如下所示:坯体配方—泥条制备—真空粗练—真空挤压成型—对滚压制—切割—微波干燥—低温素烧(可免)—釉料制备—直线淋釉(底、面釉)—大规格印花机印花—釉烧—切割—分级包装 1)坯体配方(1)坯体配方类型最初由于陶瓷薄板特殊用途,只能做成陶质的。
瓷质的容易变形,且重量太大做门板不太适宜。
但随着陶瓷薄板用途的广泛,最近一年出现了瓷质陶瓷薄板。
A、陶质坯体目前陶瓷行业陶质薄板吸水率控制在(6~10)%,一般陶坯化学组成范围(Wt%)如下:SiO2:65~73,Al2O3:16~23,CaO和MgO:4~10,K2O和Na2O:﹤2,Fe2O3:﹤1.5,TiO2:﹤1,I.L:6~10。
其属于CaO--Al2O3--SiO2三元系统。
而陶瓷薄板普通采用挤压成型,其坯体化学组成与普通不同,其化学成分(Wt%)如下:SiO2:66,Al2O3:19,CaO和MgO:4~10,K2O和Na2O:﹤2,Fe2O3:﹤1.5,TiO2:﹤1,I.L:6~10。
超大规格陶瓷薄板(PP板)薄法施工工法

超大规格陶瓷薄板(PP板)薄法施工工法超大规格陶瓷薄板(PP板)薄法施工工法一、前言超大规格陶瓷薄板(PP板)薄法施工工法是一种全新的施工技术,它通过采用超大规格的陶瓷薄板,以及精确的施工工具和设备,实现了对建筑表面进行快速、高效、耐久的装饰。
二、工法特点该工法具有以下特点:1. 超大规格:超大规格陶瓷薄板的尺寸可达到3m×1.5m,相比传统瓷砖大大减少了接缝,提高了装饰效果。
2. 薄法施工:采用薄法施工,将陶瓷薄板直接粘贴到建筑表面,减少了空间占用,快速并且高效。
3. 轻质材料:陶瓷薄板采用无机材料制成,具有轻质、坚固的特点,适用于各种建筑类型,同时减少了地面负荷。
4. 耐温耐水:陶瓷薄板具有优异的耐温耐水性能,适用于室内外各种环境。
5. 美观耐用:陶瓷薄板纹理清晰,色彩丰富,表面光滑耐磨,不易褪色,使用寿命长。
三、适应范围超大规格陶瓷薄板(PP板)薄法施工工法适用于各种建筑装饰,如外墙、立面、地面、天花板等,特别适用于高档公共建筑、商业中心、酒店、豪宅等。
四、工艺原理超大规格陶瓷薄板(PP板)薄法施工工法通过对施工工法与实际工程之间的联系,采取了以下技术措施:1. 基层处理:对基层进行清洁、平整、除尘、防潮处理,以确保陶瓷薄板施工的稳定性。
2. 使用粘结剂:选择优质粘结剂,通过辊涂、刷涂等方式涂覆在基层上,确保陶瓷薄板与基层的牢固粘合。
3. 采用导向框架:在基层上设置导向框架,以确保陶瓷薄板的规整和平整。
4. 使用机械工具:采用专业的机械工具,如吸盘、压板等,帮助将陶瓷薄板精准定位、压实,并确保施工过程中的准确性和稳定性。
五、施工工艺1. 基层处理:清理、平整、除尘、防潮处理基层。
2. 安装导向框架:在基层上安装导向框架。
3. 应用粘结剂:将粘结剂涂覆在基层和导向框架上。
4. 定位陶瓷薄板:用机械工具将陶瓷薄板精准放置在基层上。
5. 压实陶瓷薄板:使用压板等工具将陶瓷薄板压实固定。
浅谈大规格陶瓷薄板的性能优势及生产工艺

浅谈大规格陶瓷薄板的性能优势及生产工艺摘要:在我国现代化工业发展持续深入推进的背景下,绿色发展、可持续发展成为行业发展的主流理念,以陶瓷薄板为代表的系列绿色环保型材料受到业内的高度重视。
大规格陶瓷薄板由高岭土和其他无机非金属材料经1200℃高温锻烧而成,可以有效降低能耗、节约资源。
基于此,本文将简要分析大规格陶瓷薄板的优势,并重点阐述挤压成型大规格陶瓷薄板的生产工艺,希望对工艺优化具有参考价值。
关键词:大规格;陶瓷薄板;性能优势;生产工艺引言:凭借其低碳环保、绿色节能的特点,大规格陶瓷薄板的热度近几年来居高不下。
目前,陶瓷薄板的生产工艺主要分为挤压成型生产工艺和湿法挤出成型生产工艺,前者对技术材料的要求更低,应用相对更为广泛。
但是,挤压成型大规格陶瓷薄板的生产工艺流程繁琐,涉及到诸多细节问题,需要技术人员高度重视,保障陶瓷薄板的生产质量和效率。
一、大规格陶瓷薄板性能优势大规格陶瓷薄板材料被广泛应用于建筑装饰行业,其设计理念的发展实际上是我国建筑陶瓷装饰材料领域变革的一个缩影,突破了装饰材料面幅小、砖体厚、质量大的系列瓶颈。
与此同时,陶瓷薄板兼具耐磨、耐火,防腐、无静电、吸收噪音、耐日晒雨淋、抗酸碱、抗污染、易清洗、弹性好等一系列优势,为施工单位美化建筑提出了更优选择。
除此以外,大规格陶瓷薄板还具备良好的美学价值和环保价值,不仅可以提升建筑装饰艺术魅力,同时可以改善人民居住环境,缓解环境污染问题,由此具有较好的市场潜力和发展前景。
二、挤压成型大规格陶瓷薄板生产工艺流程(一)坯体配方挤压成型大规格陶瓷薄板生产工艺对于坯体配方、坯料选择存在严格要求,相关技术人员必须按照技术规范合理控制,避免陶瓷薄板出现变形情况。
首先,关于坯用原料选择,相关负责人员应综合考虑坯体干燥强度、可塑性、吸水率等参数,在此基础上优先选择储量丰富、质量稳定的原料品种。
整体来说,坯料类型不同,选择标准也存在差异。
其中,泥料决定了挤压成型大规格陶瓷薄板的干坯强度、可塑性以及收缩等工艺参数,因此需要密切关注其烧失量,选择二次粘土,若受条件限制无法使用高粘度粘土,可以用甲基替代。
大规格陶瓷超薄板的烧成技术

中节点之 间仍处 于相对信息孤 立的状态 , 其网络通信能力没
预混系统烧 嘴有四大优点 , 一是燃烧器 可根据不 同燃气 成份 , 改变喷气板 的孔径 , 调整鼓 风进气量 , 可满 足液化石 油
2 0 1 3年第 1期
中 国 陶 瓷 工 业
大规格陶瓷超薄板的烧成技术

( 建 筑 陶 瓷 ) 2018 年 04 月
陶 瓷 Ceramics
· 57 ·
������������������������������������������������������������������������������������������������������������������������������������������������������������������������������������������������������������������������������������������������������������������������������������������������������������������������
现在已超过40余个;超 高 层 建 筑,有 杭 州 生 物 科 技 大 种),无釉抛光的和无釉不抛光的。广东摩德娜科技股
楼、包头国际金融中心等高度超过 130m、应用面积超 份有限公司自主研发 的“挤 出 法 一 次 烧 大 规 格 陶 瓷 薄
过12万 m2。如图1所示为 蒙 娜 丽 莎 PP 板 在 佛 山 海 板”样 品 试 生 产 获 得 成 功。 该 薄 板 厚 度 仅 为 3~5
观念的影响较大,比如厚的砖比薄板强度就会高,故在 造薄板烧成窑内宽为1.8m,由 于 断 面 小,同 水 平 断 面
· 56 ·
陶 瓷 Ceramics
( 建 筑 陶 瓷 ) 2018 年 04 月
������������������������������������������������������������������������������������������������������������������������������������������������������������������������������������������������������������������������������������������������������������������������������������������������������������������������
大规格陶瓷薄板幕墙施工工法(2)

大规格陶瓷薄板幕墙施工工法大规格陶瓷薄板幕墙施工工法一、前言大规格陶瓷薄板幕墙作为一种新兴的建筑幕墙形式,具有优雅的外观和出色的性能,受到越来越多建筑师和业主的青睐。
为了确保施工过程中的质量和效果,需要采用专门的施工工法。
本文将详细介绍大规格陶瓷薄板幕墙施工工法的特点、适应范围、工艺原理、施工工艺、劳动组织、机具设备、质量控制、安全措施、经济技术分析和工程实例。
二、工法特点1. 大规格:大规格陶瓷薄板具有较大的尺寸,可以达到3000×1500mm甚至更大。
这种特点确保了幕墙的整体美观性和外观效果。
2. 轻质:由于采用的是薄型材质,大规格陶瓷薄板幕墙相比传统石材幕墙更轻盈,减轻了建筑结构的负荷。
3. 耐候性:大规格陶瓷薄板具有优异的耐候性能,可以抵抗紫外线、雨水和恶劣的气候条件,确保幕墙的长期美观和性能稳定。
4. 高强度:大规格陶瓷薄板幕墙具有高强度和耐冲击性,可以应对外部压力和碰撞,提供更好的安全保护。
5. 易清洁:陶瓷材料光滑平整,不吸附灰尘和脏污,易于清洁和维护。
三、适应范围大规格陶瓷薄板幕墙适用于各类高层建筑、商业综合体和办公楼等场所,尤其适合于追求高质量和个性化外观的建筑项目。
其独特的外观效果和性能特点能够满足不同需求的建筑项目。
四、工艺原理大规格陶瓷薄板幕墙的施工工法与实际工程之间的联系主要包括以下几个方面:1. 硬件连接:采用特殊的陶瓷幕墙系统,通过铝合金或不锈钢连接件将陶瓷板固定在幕墙承载结构上。
2. 形象塑造:通过调整陶瓷板的尺寸、排列方式和颜色等,塑造具有创意和个性化的建筑外观。
3. 构造设计:根据实际工程情况进行幕墙结构设计,确保陶瓷板的固定和连接稳定可靠。
4. 材料选择:选择符合规格和质量要求的大规格陶瓷薄板,确保施工过程中的材料质量和施工效果。
五、施工工艺大规格陶瓷薄板幕墙的施工工艺包括以下几个阶段:1. 基础处理:对幕墙的基础进行检查和处理,确保基础平整、牢固和符合施工要求。
湿法大规格陶瓷薄板的制造工艺及应用方法

个 理想 的选择 , 对美 化 建筑 , 升 建筑 装饰 的 品位和 提
艺术魅 力 、 改善人 们 的居住 质量 具有 不 可估 量的价 值 。 其 用途 广泛 , 场潜力 巨 大。 市
项 目来 源 :十一 五” 家 科 技 支 撑 计 划 “ 色 制 造 关 键 技 术 与 装 备 ” 目(0 6 A 0 A 8 “ 国 绿 项 20 B F 2 2 )
摘 要 对 湿 法 挤 出 成 形 大 规 格 陶 瓷 薄板 的制 造 工 艺 和 应 用 方 法 进 行 了较 为详 细 的 阐述 。 关 键 词 陶 瓷 薄 板 泥 料 流 变 性 微 波 干 燥 器 专 用 粘着 剂 干挂 施 工 方 法
1 湿 法 成 形 大 规 格 陶 瓷 薄 板 的 制 造 工
塑 性 状 态 , 有 “ 性 一 塑 性 ” 变 特 性 。 它 是 基 于 粘 具 弹 流
土 的结 合性 与 可塑性 , 粘 土 的基 础 上 加 入 其 它 组 分 在 与水 构成 。 可 以认 为是 被 石 英 、 石 等 天 然 矿 物 原 料 长 所瘠 化 了 的粘土 泥料 。
维普资讯
・
3 ・ 6
陶 瓷
20 No. 08 9
.
与水 之 间 , 必须 按照 一 定 的 比例 配 合 才 能产 生 良好 的
可 塑 性 。含 水 量 不 足 , 塑 性 显 示 不 出 来 或 显 示 不 完 可
进行 切 割 , 成所 需 的 规格 。 切割 后 的 外 围边 料 可 回 切 收利 用 。成形 厚度 一 般 控制 在 3 2~ 2m , 格 有 : . 4. m 规
前 言
高 污染 、 高能 耗 、 高成 本 似乎 是人 们对 陶 瓷业最 根 深 蒂 固的 印象 , 规格 陶瓷 薄板 的问 世 , 大 改变 了陶 瓷行 业 以往 高能 耗 、 污染 、 高 高成 本 的三 高 局 面 , 节 约 能 对
陶瓷薄板生产工艺过程探讨

陶瓷薄板生产工艺过程探讨陶瓷薄板是一种常见的建筑装饰材料,其在建筑装饰行业中有着广泛的应用。
陶瓷薄板的生产工艺对产品的质量和性能具有至关重要的影响,因此对陶瓷薄板的生产工艺过程进行深入的探讨,对于提高产品质量和生产效率具有重要意义。
一、原料准备陶瓷薄板的原料主要包括粘土、石英砂、长石粉等。
需要对原料进行严格的筛分和配比,确保原料的粒度和成分符合生产要求。
然后将原料送入球磨机进行粉碎和混合,使其达到一定的细度和均匀度。
经过原料的粉碎和混合,形成了均匀的陶瓷浆料,为后续的成型工艺提供了基础条件。
二、成型成型是陶瓷薄板生产工艺中的重要环节,其成型方式主要包括干法压坯和湿法成型两种。
在干法生产工艺中,通过将陶瓷浆料压制成型,然后经过干燥和烧结而成;在湿法生产工艺中,则是通过滚压成型、涂布成型等方式,将陶瓷浆料均匀地涂布在基材上,然后经过干燥和烧结。
三、干燥成型后的陶瓷薄板需要进行干燥处理,以去除其内部的水分。
干燥的过程需要控制好温度和湿度,避免产生裂纹和变形。
通常采用空气循环干燥的方式,使得热风能够均匀地吹入产品内部,将水分带出。
干燥的时间一般较长,需要根据产品的厚度和湿度进行调整。
四、烧结烧结是陶瓷薄板生产工艺中最关键的一步,其烧结温度和时间直接影响着产品的质量和性能。
在烧结过程中,需要将陶瓷薄板置于窑炉中,逐渐升温至一定温度,然后保持一定时间,使得其内部的结晶结构得以完全形成。
还需要对烧结气氛进行控制,避免产生氧化还原反应,影响产品的表面光泽和颜色。
五、表面处理经过烧结后的陶瓷薄板需要进行表面处理,以提高其表面的平整度和光泽度。
通常采用抛光、喷釉等方式进行表面处理,使得产品表面光滑、均匀和具有一定的光泽度。
表面处理的质量关系着产品的外观效果和装饰效果,因此需要严格控制处理工艺和材料选择。
六、质检包装经过表面处理的陶瓷薄板需要进行质量检测和包装。
质量检测主要包括外观检验、尺寸检测、力学性能测试等多个方面,以确保产品符合相关标准和要求。
大型陶瓷薄板外墙施工工法(2)

大型陶瓷薄板外墙施工工法一、前言大型陶瓷薄板外墙施工工法是一种现代化的外墙装饰材料及施工工艺,其采用大型陶瓷薄板作为外墙装饰材料,通过特定的施工工法,将陶瓷薄板固定在建筑物外墙上,实现外墙的美观与保护。
本文将介绍大型陶瓷薄板外墙施工工法的特点、适应范围、工艺原理、施工工艺、劳动组织、机具设备、质量控制、安全措施、经济技术分析以及一个工程实例。
二、工法特点 1. 美观性强:大型陶瓷薄板外墙具有平整、光滑、亮丽的特点,可以呈现出多种颜色、纹理和图案,满足建筑物外墙的设计要求。
2. 耐候性好:大型陶瓷薄板具有良好的耐候性,能够抵抗紫外线、酸雨等外部环境的侵蚀。
3.耐污性强:大型陶瓷薄板的表面平整光滑,不易附着尘埃和污渍,易于清洁和保养。
4. 安装方便:施工过程简单,可以采用现场切割、粘贴或预制板悬挂的方式进行安装。
5. 轻质化:大型陶瓷薄板重量轻,减轻了外墙负荷,降低了建筑物结构的要求。
6. 环保健康:大型陶瓷薄板采用天然材料,无污染、无辐射、无甲醛等有害物质,对人体和环境无害。
三、适应范围大型陶瓷薄板外墙施工工法适用于各类建筑物,包括商业综合体、高档写字楼、酒店、别墅等。
由于其外墙装饰效果好、耐候性强、维护成本低等优点,已经成为当今建筑外墙装饰的主流。
四、工艺原理大型陶瓷薄板外墙施工工法主要通过下述工艺原理实现:首先确定外墙的施工要求和装饰效果,然后进行材料采购和加工,例如预制板悬挂时需要对预制板进行槽口切割和钢结构固定孔制作。
在施工现场,根据墙体结构进行墙面处理,如修补不平整的墙面。
接下来进行薄板粘贴,采用特殊粘结剂将薄板固定在墙面上,并进行排版和固定。
最后进行收尾工作,如处理连接处、边缘处理和防水处理等。
五、施工工艺1. 墙面处理:清理墙面,修补不平整的墙面,施工阶段需注意保持墙体的垂直度和平整度。
2. 材料准备:采购大型陶瓷薄板,进行槽口切割和钢结构固定孔制作,按照设计要求进行预制板的生产和加工。
挤压成形大规格陶瓷薄板的生产工艺

这 种 规 格 的 产 品 主 要 销 往 日本 .如 果 内 销 的 话 可 根
目前 陶瓷行 业 的陶质 薄板 吸水率 控制在 6 1%, ~ 0 而
陶瓷薄板 普遍采 用挤压成 形工艺 .其坯体化 学组成与普
通 陶 坯 不 同 , 学 成 份 ( t ) :i 2 6 A 231 、a 化 w % 为 S : 、1 :9 C O和 O6 0 6 1 。其 配 方 为 : 料 :0 4 % 泥 料 :5 4%、 灰 石 : ~ 0 砂 3 ̄ 0 、 3~ 5 石 5 1% 硅 灰 石 :~ 1% 膨 润 土 :~ 5 、 石 :~ 5 。其 ~ 0、 0 0、 0 %长 0 %
3 2 1泥 料 的选 择 ..
对 于 超 薄 陶 瓷 板 来 说 , 坯 强 度 极 为 重 要 , 接 影 响 干 直
到淋釉印花 的成功 与否 , 因此必须满 足强度要求 。 一般 一
次 烧 成 的 干 坯 强 度 要 求 > 15 P ,而 陶 瓷 薄 板 对 强 度 要 .Ma
求更高 , 最好大 于>2 O P 。 . M a 在配方配制过程中最好使 用 二次粘土 , 如广 东黑泥 等 , 或加入少量 的膨润 土。
6 结 论
由于超 高 压微 雾 加 湿 系统 同时具 有 降尘 与 加湿 作
相信 超高压 微雾加湿 系统在 陶瓷企业 的应用 ,能显 著地 为企 业提高 生产 效益 , 将有更 广阔的应用前景 。
维普资讯
再 加膨润 土。
成形方法 。 一般挤压 、 滚压成形 的坯料含水率为 1 ~2 % 9 2。
陶 瓷 薄 板 最 初 由 日 本 研 发 并 生 产 , 主 要 生 产
3 坯 体 配 方
3 1坯 体配方类 型 .
挤压成形大规格陶瓷薄板的生产工艺

挤压成形大规格陶瓷薄板的生产工艺作者:陈迪晴来源:《佛山陶瓷》2008年第04期1前言陶瓷薄板最初由日本研发并生产,主要生产 1200mm×2400mm×(3~6)mm规格的陶瓷板材,用来做推门板。
而国内生产陶瓷薄板也是这两年才兴起,目前已有三家企业生产过陶瓷薄板,加上佛山樵东陶瓷,总共四家企业。
这种规格的产品主要销往日本,如果内销的话可根据客户对尺寸不同的要求进行切割,也可适当做小一点、做厚一点,可做成仿古、渗花抛光地砖。
这类产品由于薄,受热快,可大幅减少热用量,对企业的可持续发展起重要作用。
2生产工艺流程陶瓷薄板采用真空挤压成形,然后对辊压制成厚度为6mm左右,并切割成略大于1200mm×2400mm尺寸的湿坯体,依次经干燥、素烧、施釉、印花、釉烧等工序制得产品。
具体工艺流程如下:坯体配方→原料制备→真空粗练→真空挤压成形→对辊压制→切割→微波干燥→低温素烧(可免)→直线淋釉(底、面釉)→大规格印花机印花→釉烧→切割→分级包装3坯体配方3.1 坯体配方类型最初由于陶瓷薄板的特殊用途,只能做成陶质的。
由于瓷质薄板容易变形,且重量太大做门板不太适宜。
随着陶瓷薄板用途不断广泛,最近一年出现了瓷质陶瓷薄板。
3.1.1陶质坯体目前陶瓷行业的陶质薄板吸水率控制在6~10%,而陶瓷薄板普遍采用挤压成形工艺,其坯体化学组成与普通陶坯不同,化学成份(wt%)为:SiO2:66、Al2O3:19、CaO和MgO:4~10、K2O和Na2O:﹤2、Fe2O3:﹤1.5、TiO2:﹤1、I.L:6~10。
其配方为:砂料:30~40%、泥料:35~45%、石灰石:5~10%、硅灰石:0~10%、膨润土:0~5%、长石:0~5%。
其含铝量高,可加入少量的长石助熔,降低吸水率。
3.1.2 瓷质坯体瓷质陶瓷薄板是最近半年才出现的,据传最初由马来西亚一家陶瓷薄板生产厂家首先生产出来,其吸水率为﹤0.5%。
- 1、下载文档前请自行甄别文档内容的完整性,平台不提供额外的编辑、内容补充、找答案等附加服务。
- 2、"仅部分预览"的文档,不可在线预览部分如存在完整性等问题,可反馈申请退款(可完整预览的文档不适用该条件!)。
- 3、如文档侵犯您的权益,请联系客服反馈,我们会尽快为您处理(人工客服工作时间:9:00-18:30)。
大规格陶瓷薄板生产工艺★★★
1. 前言
陶瓷薄板最初是日本利用废料研发并生产的,主要生产1200×2400×(3~6)(mm)规格的陶板,用来做推门板。
而国内生产只是这两年的事,目前有三家生产过陶瓷薄板,加上佛山樵东陶瓷马上要生产,一共四家而已。
生产这种规格的产品主要销往日本,如果内销的话可根据客户对尺寸不同要求进行切割。
而且也没必要做这种规格,可适当做小一点,做厚一点,可烧瓷化做仿古地砖。
这类产品由于薄,受热快,可大幅减少热用量,对企业发展起战略性作用。
而目前国外有一些陶瓷厂家生采用这种工艺生产渗花釉。
与施釉砖不同,它不需要淋釉,要把素烧改为干燥,印渗花釉。
2. 生产工艺
陶瓷薄板采用真空挤压成型,然后滚压制成6mm左右,并切割成略大1200×2400(mm)尺寸。
最后干燥素烧、施釉、印花、釉烧等。
具体工艺流程如下所示:
坯体配方—泥条制备—真空粗练—真空挤压成型—对滚压制—切割—微波干燥—低温素烧(可免)—釉料制备—直线淋釉(底、面釉)—大规格印花机印花—釉烧—切割—分级包装
1)坯体配方
(1)坯体配方类型
最初由于陶瓷薄板特殊用途,只能做成陶质的。
瓷质的容易变形,且重量太大做门板不太适宜。
但随着陶瓷薄板用途的广泛,最近一年出现了瓷质陶瓷薄板。
A、陶质坯体
目前陶瓷行业陶质薄板吸水率控制在(6~10)%,一般陶坯化学组成范围(Wt%)如下:SiO2:65~73,Al2O3:16~23,CaO和MgO:4~10,K2O和Na2O:﹤2,Fe2O3:﹤1.5,TiO2:﹤1,I.L:6~10。
其属于CaO--Al2O3--SiO2三元系统。
而陶瓷薄板普通采用挤压成型,其坯体化学组成与普通不同,其化学成分(Wt%)如下:SiO2:66,Al2O3:19,CaO和MgO:4~10,K2O和Na2O:﹤2,Fe2O3:﹤1.5,TiO2:﹤1,I.L:6~10。
其配方如下:沙料:30~40%,泥料:35~45%,石灰石:5~10%,硅灰石:0~10%,膨润土:0~5%,长石:0~5%。
其含铝量高,可加入少量的长石助熔,降低吸水率。
B、瓷质坯体
瓷质陶瓷薄板是最近半年才出来的,最初听说是马来西亚一家陶瓷薄板生产厂家生产出来的。
其吸水率为﹤0.5%。
瓷质砖坯体化学组成范围(Wt%)如下:SiO2:65~73,Al2O3:16~23,CaO和MgO:﹤2,K2O和Na2O:4~7,Fe2O3:﹤1.5,TiO2:﹤1,I.L:﹤8。
其属于K2O、Na2O--Al2O3--SiO2三元系统。
超薄瓷板化学组成与普通瓷质砖比较,其含铝量要高、含硅量要低,另外含钾、钠量也要高一些。
化学组成(Wt%)如下:SiO2:66,Al2O3:19,CaO和MgO:﹤2,K2O和Na2O:4~7,Fe2O3:﹤1.5,TiO2:﹤1,I.L:﹤8。
其配方如下:石粉:45~55%,泥料:40~50%,滑石泥:0~3%,其配方要加入滑石泥和黑泥,其粘度好,不用再加膨润土。
(2)坯用原料
挤压成型与干压成型不同,其对坯料有特殊要求。
主要是坯体干燥强度、可塑性吸水率等方面的要求。
除此之外,原料还要选择储量丰富,质量稳定的。
特别是泥料的性能必须满足。
A、泥料的选择
增加干坯强度、可塑性以及收缩等工艺参数主要是粘土(泥料)起作用;因此要注意选择粘土,最好选二次粘土,烧失量太大的泥料在普通瓷砖无法使用,但可在超薄陶瓷板中使用。
砖薄,不用担心排气问题。
如果在无法找到高粘度的粘土时,可用甲基代替。
球磨时加水较多,用甲基代替粘土时,粘度虽然较大,但也能放浆。
挤压成型要把泥浆榨泥练泥后才使用;因此在某种程度上讲超薄陶瓷板对坯料的要求并不高。
B、沙料的选择
沙料要求白度好即可,无其它要求。
C、石粉的选择
石粉在陶质薄板中用量很少,可以不用。
它主要用在瓷质薄板中做助熔剂,要求白度高,烧成熔融温度低。
D、其它原料的选择
一般陶质薄板中会加入一部分石灰石和硅灰石。
一般一次半烧、二次烧成的话可以多加一些
石灰石;而一次烧成的话尽可能少加。
而瓷质薄板中还会加入(1~3)%的滑石泥,用来助熔、增白。
(3)陶瓷薄板对坯料的工艺要求
由于超薄陶瓷薄板采用挤压成型;因此坯料必须满足挤压成型的要求。
A、可塑性
可塑性是塑性坯料的主要性能,是成型的基础。
5)对滚挤压成型
真空挤压后,还需对滚挤压。
挤成需要的厚度,并切割成所需要的长度和宽度。
经过第一次挤压,泥坯厚度为20 mm;第二次挤压后的厚减为一半为10 mm;第三次对滚挤压后的厚度为(5~8)mm。
如果烧后要达到厚度为3mm,要加多一道挤压滚。
对滚挤压如图(4)、(5)、(6)、(7)所示。
图(4)第一次对滚挤压
图(5)第二次对滚挤压
图(6)第三次对滚挤压
图(7)切割后的坯体
6)微波干燥
相对窑炉干燥,微波干燥效率高,占用面积极小,节省能源。
此外,用微波干燥器干燥的坯体水分均匀,成品率高。
微波干燥器一般安两组,一组9个,干燥后坯体水分控制在:2~8%之间。
微波干燥与窑炉干燥比较如表(3)所示:
7)低温素烧(可以不用)
素烧是为了提高坯体强度,以便于釉线走砖、淋釉和印花。
大规格陶瓷薄板素烧窑很短,且温度低。
其属于一次半烧。
一般素烧窑长:30~50米,窑体内宽1.5米以上,烧成温度:800~900℃,一般烧:45~60分钟。
如果坯体强度够高,可以不素烧。
但目前陶瓷薄板都是陶质的,大多经过两次淋釉,因此不素烧无法达到生产要求。
据说马来西亚某厂已经生产出了瓷质薄板,吸水率在0.5%以下。
如果是生产渗花砖则无需素烧。
其实我国研发瓷质薄板较早,但没正式投入生产。
最近佛山樵东陶瓷准备上800×1800(mm)规格瓷质陶瓷薄板。
8)直线淋釉(渗花砖不用)
由于超薄陶瓷板短边为1200mm,只能使用1500mm宽度的直线淋釉器。
由于尺寸太大,它在生产时容易出现釉路缺陷;因此其对釉浆性能要求非常高,要求有良好的粘度、润滑性能和流速。
两台淋釉器之间相隔6米。
直线淋釉器如图(8)所示。
图(8)直线淋釉器
9)超大规格印花
超大规格印花机与小规格印花不同,其印花方向和釉线走砖方向相同。
其它的都与普通规格瓷砖相差不多,对花釉要求都一样。
对于宽度小于600mm的产品,也可采用胶滚印花。
超大规格印花机如图(9)所示。
图(9)超大规格产品印花机
图(10)1200×2400规格陶质薄板
10)釉烧
和普通瓷砖一样釉烧窑烧成温度和烧成曲线都差不多,使窑炉滚棒较细且密一些。
釉烧窑长100米左右,烧成温度根据产品不同而定,釉面砖烧成温度1100℃,瓷质砖(仿古砖和渗花釉)烧成温度为1200℃左右。
釉烧窑如图(11)所示。
图(11)釉烧窑
11)切割
对于出口日本的产品无需切割,但是销售国内的产品并不需要这么大,可根据使用要求切割成各种不同的规格,如:30×45、30×60、30×90、30×30、60×60等等。
还可切成各种不同的形状。
可做腰线、做内墙砖,也可做地砖。
不但省掉了压机和模具,还节省了许多其它工序和机械设备。
12)分级包装
根据客户要求对不同规格产品进行分级打包入库。
3 . 总结
1)与普通工艺对比
A、超薄砖工艺程序
坯体配方(釉料制备)—球磨—榨泥—泥条真空粗练—真空挤压成型—对滚压制—切割—微波干燥—低温素烧(可免)—直线淋釉(底、面釉)—大规格印花机印花—釉烧—切割抛光—分级包装
B、普通砖工艺程序
坯体配方(釉料制备)—球磨—粉料制备—压机压制—高温素烧(可免)—钟罩淋釉(底、面釉)—印花—釉烧—磨边抛光—分级包装
由上可以看出,两者区别在原料制备和成型方法不同。
挤压成型原
料制备程序要多,但由于是湿法成型,没有废气和粉尘,也减少了喷雾塔及压机等设备。
2)与普通砖工艺能源对比
与普通砖生产相比,超薄砖工艺,特别是一次烧成瓷质超薄砖生产工艺生产,可大幅减少原料用量,其厚度为3~6mm,只有现行墙地砖厚度的1/4,原料用量可减少60%以上,能源节约至少40%以上。
除此之处,还可减少生产设备、减少人工,也利于工厂管理,设备简单,利于操作,缩短设备问题解决时间,提高生产率和成品率。
由于其本身薄,废品返球球磨也很容易,球磨时间短。
一次烧成超薄瓷板、一次半烧超薄陶板产品属于绿色产品。
是陶瓷行业发展的一种必然趋势。
本文有部分图片和工艺参数由佛山市希望陶瓷机械有限公司陈灿基先生提供,在此一并致谢。
佛山市精博釉料有限公司陈迪晴。