加氢裂化质量控制指标和工艺技术条件
加氢工艺

1.4加氢催化剂
催化剂有生产初期(SOR)和生产末期(EOR) 的差异:催化剂随运转时间的增长,催化剂的 活性逐步下降,需要提高温度来弥补活性的损 失,而同时操作苛刻度和产品分布也逐渐变差, 到达末期时需要换剂或再生。 保护剂:在催化剂床层顶部分级装填保护剂, 沿床层向下粒度逐步变小,空隙率也逐渐变小, 活性逐渐增大。目的是容纳更多的杂质,减轻 对主催化剂的污染,减缓床层压降上升的速度。
2.1高压窜低压的防范重点
高分液位的监控是全装置操作的第一重点。 DCS监盘人员必须时刻监控高分液位,高分差 压、沉筒液位计要相互对照,外操巡检必须与 玻璃板对照;高液位和低液位联锁开关与 LISA1104的高低联锁、快速切断阀KV1104必 须处于完好投用状态;监盘人员必须清楚液控 调节阀LCV1103的阀位和手自动状态;清楚液 位指标控制范围和联锁设定值
2.3飞温—危害
飞温会致使催化剂结构受到破坏,反应 系统的设备造成损伤,高压法兰高温变 形泄漏等。 加拿大石油炼制公司曾发生反应器“飞温” 事故,造成反应器大面积堆焊层剥离和 347SS堆焊层熔敷金属裂纹和破坏现象
2.3飞温的防范措施
在床层温度异常升高初期,只要及时发现并立 刻采取降温措施如打入大量冷氢、降低炉温等, 是可以控制住温度骤升的。因此DCS监盘人员 对裂化床层所有温度指示点都要时刻监视。 裂化冷氢阀正常控制开度在50%内以备应急 原料性质变化对温度影响非常大,罐区油品调 和不均,会使反应器温度出现波浪式变化,易 发生飞温;焦蜡调和比例调整时要控制幅度; 每次切罐初期都要密切观察判断油品性质。
2.4高压临氢设备损伤的防范
工艺操作必须要保护设备。 在正常生产和开停工和检修过程中有很多工艺操 作规定,都是针对设备保护的:如开停工过程中 温度和压力的升降速度要求、氢气加热炉管壁 温度<550℃等等。有些操作容易被忽视,短 期内也看不出后果,但对设备的长远影响却是 很大的,所以必须要严格按规定操作,避免设 备损伤
加氢裂化反应影响因素
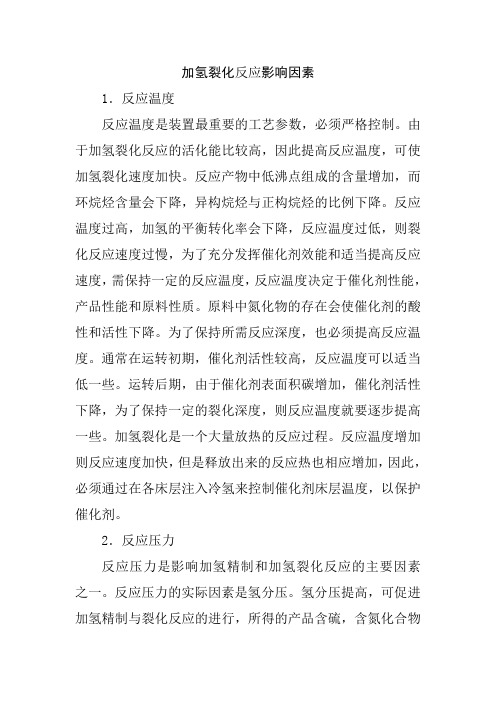
加氢裂化反应影响因素1.反应温度反应温度是装置最重要的工艺参数,必须严格控制。
由于加氢裂化反应的活化能比较高,因此提高反应温度,可使加氢裂化速度加快。
反应产物中低沸点组成的含量增加,而环烷烃含量会下降,异构烷烃与正构烷烃的比例下降。
反应温度过高,加氢的平衡转化率会下降,反应温度过低,则裂化反应速度过慢,为了充分发挥催化剂效能和适当提高反应速度,需保持一定的反应温度,反应温度决定于催化剂性能,产品性能和原料性质。
原料中氮化物的存在会使催化剂的酸性和活性下降。
为了保持所需反应深度,也必须提高反应温度。
通常在运转初期,催化剂活性较高,反应温度可以适当低一些。
运转后期,由于催化剂表面积碳增加,催化剂活性下降,为了保持一定的裂化深度,则反应温度就要逐步提高一些。
加氢裂化是一个大量放热的反应过程。
反应温度增加则反应速度加快,但是释放出来的反应热也相应增加,因此,必须通过在各床层注入冷氢来控制催化剂床层温度,以保护催化剂。
2.反应压力反应压力是影响加氢精制和加氢裂化反应的主要因素之一。
反应压力的实际因素是氢分压。
氢分压提高,可促进加氢精制与裂化反应的进行,所得的产品含硫,含氮化合物减少,更重要的是可减少结焦,保持催化剂活化,提高催化剂的稳定性。
反应器中的氢分压等于油汽加上循环氢的总压与氢气占全部气体分子数的乘积。
本装置补充氢纯度确定为99.9%。
从经济角度出发,不采用提高补充氢纯度的办法来提高氢分压。
3.氢油比氢油体积比有两种,其一是反应器入口的氢油比,其二是总冷氢油比。
反应器入口氢油比是每小时通过反应器内氢气(循环氢气+新氢)体积与每小时通过的原料油体积之比。
(单位为Nm3 /m3)。
总冷氢油体积比是每小时通入反应器的总冷氢气体积总和与每小时通过的原料油体积之比。
在加氢反应器中只有一部分氢气起反应。
大部分氢气仍以自由状态存在。
采用高氢油比,可提高氢分压,有利于传质和加氢反应的进行,在一定范围内防止油料在催化剂表面结焦。
加氢裂化转化率和调节手段

加氢裂化转化率和调节手段加氢裂化是石油化工中一种重要的催化裂化工艺,可以生产出丰富的石油产品。
但是,加氢裂化转化率是影响产品质量和经济效益的一个重要指标,需要得到有效的控制。
加氢裂化转化率主要受到压力、温度、氢气流量、试剂比例等工艺参数的影响。
在确定合理的工艺参数时,需要考虑到反应的热力学和动力学条件。
通常来说,加氢裂化的反应热量较大,因此需要控制反应的温度,以避免反应失控。
同时,氢气也是加氢裂化反应中的重要参与者,需要保证氢气流量的充足,以提高反应效率。
除了工艺参数的控制之外,还可以采用催化剂的调节手段来增强加氢裂化转化率。
催化剂是加氢裂化反应中的关键因素,对反应速率和选择性都有着重要的影响。
通常来说,催化剂需要具备活性高、稳定性好、抗中毒性强等特点。
在使用催化剂时,可以采用以下几个调节手段:1. 催化剂的再生。
在催化剂的使用过程中,会受到碳积累、焦炭沉积等因素的影响,导致催化剂的活性下降。
因此,在一定周期内需要对催化剂进行再生,以恢复其活性。
2. 催化剂的表面改性。
通过物理或化学手段改变催化剂的表面结构和化学性质,可以有效提高其反应活性和选择性。
3. 催化剂的物理或化学混合。
将具有不同化学性质的催化剂物理或化学混合使用,可以将各种催化剂的优点充分发挥,提高反应效率和选择性。
4. 催化剂载体的改性。
通过改变催化剂的载体结构和性质,可以调节催化剂的酸碱性、孔径大小等特性,从而实现催化剂的选择性调节。
总之,加氢裂化转化率是影响石油加工生产的重要因素,需要通过合理的工艺参数和催化剂调节手段来实现控制。
加氢裂化工艺流程介绍

加氢裂化工艺流程介绍加氢裂化是一种重要的石油化工工艺,主要用于将重质石油馏分或原油中的长链烃类分子切割成较短链烃类分子,以提高产品的转化率和降低其粘度,从而达到提高产品质量和增加产品产量的目的。
该工艺主要包括催化剂的选择、反应装置的设计、反应条件的控制等几个方面,下面将对加氢裂化工艺的流程进行详细介绍。
一、催化剂的选择加氢裂化反应的催化剂通常为金属催化剂,如镍、钴、铂、钒等。
这些金属催化剂能够在合适的条件下催化烃类分子的裂解反应,生成较短链烃类分子和氢气。
通常还需在催化剂中加入一定量的活性组分,如氧化物、氧化钠、氧化铝等,以增加催化剂的活性和稳定性。
二、反应装置的设计加氢裂化反应通常在催化裂化装置中进行。
这种反应装置通常由裂化炉、加氢装置、冷却装置和分离装置等组成。
裂化炉是反应装置的核心部件,是将原料石油馏分或原油送入裂化反应器进行加热和裂化的地方。
加氢装置用于向裂化反应器中注入氢气,以提高裂化反应的效率和选择性。
冷却装置用于冷却反应产物,并将其中的气态产物液化。
分离装置则用于将反应产物中的各种组分进行分离,并提取所需的产品。
三、反应条件的控制加氢裂化反应的温度、压力、空速、氢油比等条件对反应的效率和选择性具有重要影响。
通常情况下,加氢裂化反应的温度为400-500℃,压力为2-8 MPa,空速为1-10 h-1,氢油比为1000-2000 Nm3/m3。
在这些条件下,可获得较高的产品转化率和较好的产品选择性。
加氢裂化工艺通常包括以下几个步骤:1. 原料处理:原料石油馏分或原油经过脱盐、脱硫等处理后,送入加氢裂化装置进行加热和裂化。
在这个过程中,通过加热将原料加热至裂化反应所需温度,并将其中的一部分烃类分子裂解成较短链烃类分子和氢气。
3. 冷却和分离:经过加氢裂化反应后,产生大量的气态产物和液态产物需要进行冷却和分离。
通过冷却装置将气态产物冷却成液态产物,并通过分离装置将其中的各种组分进行分离,提取所需的产品。
TP321钢高压临氢管道焊接和质量控制-2019年精选文档

TP321钢高压临氢管道焊接和质量控制一、前言目前,在TP321钢高压临氢管道焊接过程中,还存在很多问题,由于焊接过程较为复杂,需要控制的因素较多,所以,做好TP321钢高压临氢管道焊接的质量控制工作非常重要。
二、焊缝裂纹缺陷分析某厂加氢裂化装置高压管线投产仅2年,就在多道焊缝、熔合线及母材处发现裂纹。
1、焊缝裂纹的表征和特点该加氢装置2008年建成投产,在初次停工检修时,先后在反应器、高压换热器的进出口等高压管线焊缝处发现裂纹,裂纹最深达48mm.后经过对全部焊缝PT检查发现,有裂纹的管道规格从4,27mrnx5mm至4,559mmx54mm不等(其中绝大多数的为大El径管道),主要为纵向裂纹,少部分是横向裂纹,部分焊缝上还存在树枝状裂纹,这些裂纹分布在熔合线、焊缝、母材以及热影响区等处。
2、焊接裂纹缺陷原因分析(一)焊接热裂纹TP321奥氏体不锈钢具有优良的焊接性能,但是在焊接过程中与其他不锈钢相比,奥氏体不锈钢具有较高的热裂纹倾向性和敏感性,其根本原因是由于奥氏体不锈钢的热导率小,线膨胀系数大。
因此,在焊接局部加热和冷却的条件下,焊接接头部位的高温停留时间较长。
焊缝金属及近焊缝在高温承受较高的拉伸应力与拉伸应变,对于管壁较厚不易散热的高压临氢管线来说,这一现象就更加明显。
在焊接过程中,若道间温度过高,焊接电流过大,产生热裂纹的倾向就更加明显。
当这些热裂纹较微小或沿管子径向分布时。
射线探伤将很难发现。
这些微裂纹在管道运行条件下由于受到内应力、外力或腐蚀介质的作用下就很容易扩展。
(二)焊接接头的耐蚀性降低奥氏体不锈钢具有较好的耐蚀性能,但若采用的焊接方法及工艺不当,则容易发生晶间腐蚀和应力腐蚀。
TP321高压奥氏体不锈钢因焊缝金属的化学成分中含有稳定化元素Ti并经过稳定化处理。
一般不会在焊缝处发生晶间腐蚀。
但若焊接方法不当,就很容易在焊缝、紧靠熔合线的过热区以及热影响区的敏化温度区发生晶界上析出碳化铬.造成晶界贫铬而发生晶间腐蚀,晶间腐蚀主要表现为沿晶开裂。
加氢裂化航煤产品质量控制

(7)侧线抽出温度 侧线抽出温度可以灵敏的反应航煤产品质量。表一为在相
同的工况下,侧线抽出温度对航煤产品的影响,随侧线抽出温度 降低,航煤产品变轻,冰点下降。侧线抽出温度由航煤出装置量 决定,当航煤收率不变时通过中段回流调节。航煤侧线抽出温度 和航煤抽出量是影响航煤产品质量最关键的两个因素。
95%/终馏点 总硫/mg·Kg-1
183. 2/ 193. 2
184. 6/192. 8 184. 5/192. 5
196. 3/ 201. 3
195. 4/199. 9 194. 9/199. 4
216. 8/ 248. 7
255. 8/ 262. 4
0. 1
213. 8/245. 5 212. 9/243. 0 253. 1/257. 3 250. 3/257. 4
四川石化加氢裂化装置工艺流程复杂,根据分馏系统稳定操 作的原则,应尽量保持定性参数(温度、压力)不变,通过调节定量 参数(流量)来调节产品质量。即在正常操作中应稳定分馏塔顶 压力、温度、液面及各中段回流量,通过侧线航煤产品抽出量来调 整航煤产品质量,当此操作无法满足时,应分析原因,再相应的进 行调节。 参考文献:
(5)分馏塔顶压力、温度 装置,侧线抽出产品组分变轻;减小塔顶压力,增加了塔气 相流速易产生液泛。控制在 0. 03±0. 01MPa 之间。
塔顶温度升高,分馏塔所有产品变重,闪点升高,低温流动性 变差。
(6)航煤汽提塔 航煤产品由分馏塔第 49 层塔盘抽出,进入航煤气提塔汽
[1] 韩崇仁. 加氢裂化工艺与工程[M]. 北京:中国石化出版 社,2001.
《加氢裂化工艺》课件
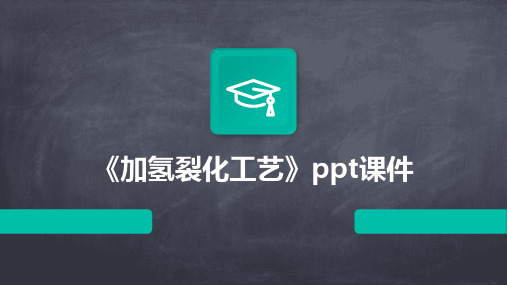
反应器的设计应考虑压力降、温度分布、催化剂装填量等因素,以确 保原料油在最佳条件下进行反应。
04
反应器的操作应控制适当的反应温度和压力,以获得所需的加氢裂化 产物。
加热炉
加热炉是加氢裂化工艺中用于 加热原料油的关键设备。
加热炉通常采用管式加热炉, 炉管内通过原料油,炉管外燃 烧燃料油或天然气,通过热传 导和热辐射将热量传递给原料
技术发展趋势与展望
高效催化剂
研发高效、稳定的催化剂是加氢裂化工艺的重要 发展方向。新型催化剂可提高反应活性和选择性 ,降低能耗和原料消耗,提高产品收率和质量。
智能化控制
智能化控制技术可以提高加氢裂化工艺的安全性 和稳定性。通过实时监测、自动控制和优化操作 ,可降低人工操作成本和事故风险,提高生产效 率。
压缩机的设计应考虑压缩比、 输送能力、机械效率等因素, 以确保气体和液体能够被顺利 压缩和输送。
压缩机的操作应控制适当的入 口和出口压力,以防止气体和 液体在压缩过程中发生泄漏和 堵塞。
分离器
分离器是加氢裂化工艺中用 于分离液体和气体的关键设
备。
1
分离器通常采用立式或卧式 分离器,通过重力或离心力 的作用将液体和气体进行分
绿色低碳发展
随着环保意识的提高,低碳、环保的加氢裂化工 艺成为未来的发展趋势。通过优化反应条件、降 低能耗和减少废物排放,实现加氢裂化工艺的绿 色低碳发展。
拓展应用领域
随着市场需求的变化,加氢裂化工艺的应用领域 也在不断拓展。例如,在生产高品质润滑油、石 蜡、高纯度溶剂等化学品方面,加氢裂化工艺具 有广阔的应用前景。
环保要求与处理措施
01
02
03
04
加氢裂化工艺应符合国家和地 方环保法规要求,确保排放的 废气、废水等污染物达到标准
加氢装置工艺防腐导则

加氢装置工艺防腐导则前言:为保证加氢装置正常运行,设备良好运行和备用,根据加氢装置的不同部位腐蚀要素,制定了本工艺防腐规定,并在日常管理中进行控制和检查落实。
导则内容:一、正常生产运行中的控制1、原料性质控制2、新氢性质控制3、反冲洗过滤器控制4、加热炉控制壁板,延壁板上升运动,到达炉顶与炉墙相交部位后聚集,浓度达到最大,随着环境温度的变化,H2SO4凝结在炉壁板,发生低温硫酸腐蚀。
SO2与水蒸气化和生成亚硫酸气,它的露点温度低,在较低温度下凝结,发生低温亚硫酸腐蚀。
少量的H2S在一定浓度、温度、条件下易发生硫化物腐蚀。
反应式2SO2+O2 = 2SO3 (可逆反应,当降低温度时,平衡向右方移动,所以随着烟气温度的降低,SO2转化成SO3的转化率越大)SO3↑+ H2O↑= H2SO4↑,H2SO4 ↑+ H2O→H2SO4(浓)* H2OH2SO4(浓)+ H2O→H2SO4(稀)* H2O加热炉露点腐蚀温度的计算影响烟气露点温度的主要因素1 含硫量烟气中硫酸蒸气大部分由瓦斯气中硫分氧化而来的。
瓦斯气中含硫量越高,烟气露点温度越高。
因而在实际运行程中,必须严格控制瓦斯气含硫量。
2 温度当压力一定时,SO2转化成 SO3的平衡曲线如图2所示。
从该图可以看出低温时对转化成SO3有利。
在850℃以上的高温下,SO3几乎不产生。
在温度相同时,压力升高会增加向SO3方面的转化。
但实际上,因原子氧、SO3触媒及飞灰的作用而变得更为复杂。
3 过量空气系数烟气含氧量越高,由SO2转化为SO3的比例会越大。
因而,在保证充分燃烧的前提下,应尽量采用低过量空气系数,减少SO3的生成量,降低烟气露点温度。
4 水蒸汽烟气中水蒸气的浓度愈大。
水蒸气的分压力也愈大。
只考虑水蒸气的影响,水蒸气对烟气露点的影响如图3所示。
因而在实际运行过程中,应严格控制瓦斯气含水率,降低烟气露点温度。
但在实际过程中,控制瓦斯气含水率非常困难,因而通常是在设计中尽量避开露点或采取相应的防腐措施。
加氢裂化转化率和调节手段

加氢裂化转化率和调节手段加氢裂化是一种重要的石油化工过程,其主要作用是将高分子烃类化合物转化为低碳数的烃类产品,以满足石油产品市场的需要。
在加氢裂化过程中,转化率是一个非常重要的参数,它能够反映出反应器的性能和操作效果。
而为了达到更好的转化率,需要采取一些调节手段来优化加氢裂化的工艺条件。
本文将从加氢裂化转化率和调节手段两方面进行讨论。
一、加氢裂化转化率加氢裂化转化率是指在一定反应条件下,原料烃类化合物发生裂化反应后所转化成的产品的化学反应率。
在加氢裂化过程中,烃类化合物通过裂解反应,生成低碳数的烃类产品。
转化率的高低直接影响到产品的质量和产量,因此是一个重要的工艺指标。
加氢裂化转化率受多种因素影响,包括反应温度、催化剂活性、压力、空速、烃类物料性质等。
一般来说,较高的反应温度和较高的压力会促进裂化反应的进行,从而提高转化率。
过高的温度和压力可能导致催化剂的失活和设备的损坏,因此需要在安全范围内进行调控。
催化剂的选择和活性也对加氢裂化转化率产生影响。
优质的催化剂应具有良好的烃裂解活性和稳定性,能够在较高温度和压力下保持高的转化率。
对于高硫、高金属含量的原料烃类化合物,还需要选择具有较强抗毒性的催化剂,以延长其使用寿命。
二、调节手段为了优化加氢裂化的工艺条件,提高转化率,可以采取一些调节手段来进行调控。
主要的调节手段包括控制反应温度、调整压力、改良催化剂性能、优化原料烃类物料性质等。
1. 调控反应温度控制反应温度是影响加氢裂化转化率的关键因素之一。
通常情况下,提高反应温度会促进裂解反应,从而提高转化率。
过高的温度会导致催化剂的失活和设备的损坏,因此需要在安全范围内进行调控。
可以通过增加或减少热交换器的热载体流量,调节反应器的冷却方式,控制反应温度的升降,以实现对反应温度的有效调控。
2. 调整压力在加氢裂化过程中,适当的压力是保证裂化反应进行的必要条件之一。
通常情况下,提高压力可以促进裂化反应,从而提高转化率。
加氢裂化工程施工

加氢裂化工程施工一、引言加氢裂化工程是一种重要的炼油工艺,通过将高分子量的原油分解成低分子量的产品,可获得更多的高附加值石油产品。
在实际的施工过程中,加氢裂化工程需要精确的计划和高效的执行,以确保工程的安全、质量和进度。
本文将从施工前的准备工作、施工过程中的技术要点、质量管理和安全管理等方面对加氢裂化工程施工进行详细介绍。
二、施工前的准备工作1. 站点选址加氢裂化工程需要一个相对较大的站点用于设备摆放和施工作业,所以施工前需要进行站点的选址工作。
选址需考虑地质条件、环境保护、供水供电等因素,确保施工过程中的安全和顺利进行。
2. 设备选型和采购在施工前期,需要对加氢裂化工程所需的设备进行选型和采购。
根据工艺设计要求和实际施工场地条件,选择合适的加氢裂化设备,并与设备厂家进行协商和签订采购合同。
3. 施工人员培训加氢裂化工程是一项技术含量较高的工程,所以需要对参与施工的人员进行技术培训。
培训内容包括设备操作、安全生产、质量管理等方面,确保施工人员具备必要的知识和技能。
4. 施工计划制定在施工前,需要制定详细的施工计划,包括施工任务、施工进度、物资采购、人员安排等内容。
施工计划的合理性和可操作性对于整个工程的施工进度和质量具有重要意义。
5. 安全生产和环保措施在施工前期,需要进行安全生产和环保措施的论证和规划。
包括施工现场的安全防护措施、废气废水的处理方案、危险品的储存和运输等内容,确保施工过程中的安全和环保。
三、施工过程中的技术要点1. 设备安装在加氢裂化工程施工中,设备的安装是一个重要的环节。
施工人员需要根据设计图纸进行设备的准确定位和安装,确保设备的安全性和稳定性。
2. 管道安装加氢裂化工程需要大量的管道用于输送原料和产品,所以管道的安装工作非常重要。
在施工过程中,需要对管道的焊接、试压和安装进行严格控制,确保管道的质量和安全。
3. 设备调试在设备安装完毕后,需要对设备进行调试和检测。
通过对设备的空载运行、启动试车等工作,确保设备的正常运行和性能达到设计要求。
加氢裂化
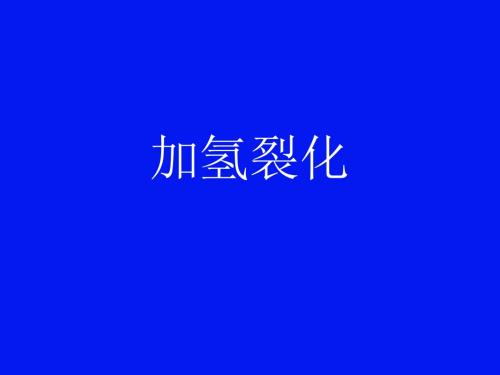
• 催化剂硫化结束后,将高分含硫酸性水计排放、计量,取 样分析其硫含量,必要时应作催化剂硫化的硫平衡估算, 评估催化剂硫化效果;
催化剂的装填
• 反应器催化剂的装填,应力求在晴朗、干燥的天气里进行,并要在反应器催 化剂装填现场搭设防雨棚,遇雨天应停止装填,严防催化剂淋浴受潮。
• 反应器的内构件安装完毕(对已操作过的反应器的内构件吹扫清理干净), 反应系统干燥完成后,方可进行催化剂装填的相应准备工作。
• 撤卸反应器头盖人孔及入口扩散分配器; • 反应器人孔打开以后,检测反应器内的氧含量,并用仪表风吹扫置换,在确
• 催化剂床层基本无温升; • 高分生水量无明显增加;
(7) 催化剂硫化结束后,将反应器入口温度降至270280℃, 引进直馏轻柴油进行催化剂钝化,钝化时间为48小时。然 后换进设计进料,并按预定的指标要求,调整操作后转入 正常运转。
• 催化剂硫化期间应注意的是:
如因故中断硫化剂注入时,应将催化剂床层温度降至
加氢裂化概述产品质量好液体产品收率高等独具的特点能生产从液化石油气石脑油喷气燃料柴油到蒸汽裂解润滑油基础油等多种优质产品和石油化工原料是为大型炼厂和石油化工企业最重要最可靠最灵活和最有效的加工手段vgo是加氢裂化的典型进料它是大分子链烷烃单双多环环烷烃烷基单双多环芳烃及环烷芳烃组成的复杂混合物
加氢裂化
• 催化剂装填结束后,将部分撤卸的顶部分配板安装复位, 再安装好入口扩散分配器和反应器顶部头盖,经旋紧螺栓 后,可进行后续相关作业。(加氢精制段反应器的下部床 层,如果需要可采用催化剂密相装填技术进行装填。密相 装填较普通装填可多装催化剂1015v%,其催化剂排列整 齐有序,反应物流分布均匀,可减少或避免催化剂床层下 沉。密相装填另有专用设备及相应的装填方法。)
加氢裂化装置转化率的判断及影响因素
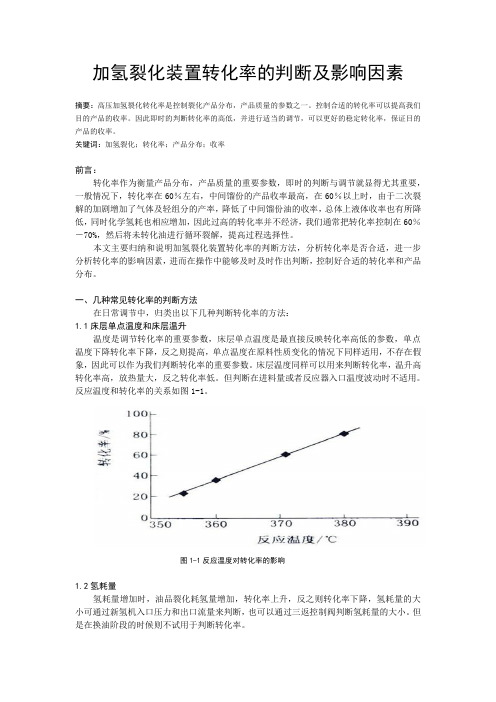
加氢裂化装置转化率的判断及影响因素摘要:高压加氢裂化转化率是控制裂化产品分布,产品质量的参数之一。
控制合适的转化率可以提高我们目的产品的收率。
因此即时的判断转化率的高低,并进行适当的调节,可以更好的稳定转化率,保证目的产品的收率。
关键词:加氢裂化;转化率;产品分布;收率前言:转化率作为衡量产品分布,产品质量的重要参数,即时的判断与调节就显得尤其重要,一般情况下,转化率在60%左右,中间馏份的产品收率最高,在60%以上时,由于二次裂解的加剧增加了气体及轻组分的产率,降低了中间馏份油的收率,总体上液体收率也有所降低,同时化学氢耗也相应增加,因此过高的转化率并不经济,我们通常把转化率控制在60%-70%,然后将未转化油进行循环裂解,提高过程选择性。
本文主要归纳和说明加氢裂化装置转化率的判断方法,分析转化率是否合适,进一步分析转化率的影响因素,进而在操作中能够及时及时作出判断,控制好合适的转化率和产品分布。
一、几种常见转化率的判断方法在日常调节中,归类出以下几种判断转化率的方法:1.1床层单点温度和床层温升温度是调节转化率的重要参数,床层单点温度是最直接反映转化率高低的参数,单点温度下降转化率下降,反之则提高,单点温度在原料性质变化的情况下同样适用,不存在假象,因此可以作为我们判断转化率的重要参数。
床层温度同样可以用来判断转化率,温升高转化率高,放热量大,反之转化率低。
但判断在进料量或者反应器入口温度波动时不适用。
反应温度和转化率的关系如图1-1。
图1-1反应温度对转化率的影响1.2氢耗量氢耗量增加时,油品裂化耗氢量增加,转化率上升,反之则转化率下降,氢耗量的大小可通过新氢机入口压力和出口流量来判断,也可以通过三返控制阀判断氢耗量的大小。
但是在换油阶段的时候则不试用于判断转化率。
1.3冷低分气量转化率高时,产生部分干气和轻烃组分,进入冷低分后使冷低分气量增大,反之,转化率低时,低分气量减少。
这种判断方法比较直观的反映出转化率的变化。
加氢裂化操作规程
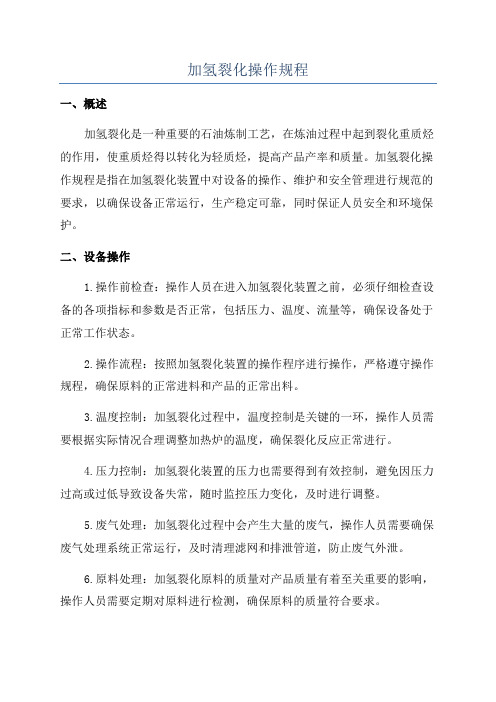
加氢裂化操作规程一、概述加氢裂化是一种重要的石油炼制工艺,在炼油过程中起到裂化重质烃的作用,使重质烃得以转化为轻质烃,提高产品产率和质量。
加氢裂化操作规程是指在加氢裂化装置中对设备的操作、维护和安全管理进行规范的要求,以确保设备正常运行,生产稳定可靠,同时保证人员安全和环境保护。
二、设备操作1.操作前检查:操作人员在进入加氢裂化装置之前,必须仔细检查设备的各项指标和参数是否正常,包括压力、温度、流量等,确保设备处于正常工作状态。
2.操作流程:按照加氢裂化装置的操作程序进行操作,严格遵守操作规程,确保原料的正常进料和产品的正常出料。
3.温度控制:加氢裂化过程中,温度控制是关键的一环,操作人员需要根据实际情况合理调整加热炉的温度,确保裂化反应正常进行。
4.压力控制:加氢裂化装置的压力也需要得到有效控制,避免因压力过高或过低导致设备失常,随时监控压力变化,及时进行调整。
5.废气处理:加氢裂化过程中会产生大量的废气,操作人员需要确保废气处理系统正常运行,及时清理滤网和排泄管道,防止废气外泄。
6.原料处理:加氢裂化原料的质量对产品质量有着至关重要的影响,操作人员需要定期对原料进行检测,确保原料的质量符合要求。
7.填料更换:加氢裂化装置的填料是一项重要的维护工作,操作人员需要定期对填料进行更换和清理,保证填料的良好状态。
8.安全操作:加氢裂化过程中,操作人员需要严格遵守安全操作规程,佩戴个人防护用具,防止意外伤害发生。
三、设备维护1.定期检查:加氢裂化装置需要定期进行检查和维护,包括设备的各个部位和连接点,确保设备的正常运行。
2.润滑保养:加氢裂化装置中的各种设备和部件需要定期进行润滑保养,确保设备的正常运转和延长设备的使用寿命。
3.设备清洁:加氢裂化装置需要定期进行清洁,除去积灰和杂物,保持设备表面清洁,避免设备堵塞和腐蚀。
4.防腐处理:加氢裂化装置的设备容易受到腐蚀,需要进行防腐处理,定期检查设备表面和内部是否出现腐蚀迹象,及时进行处理。
加氢裂化
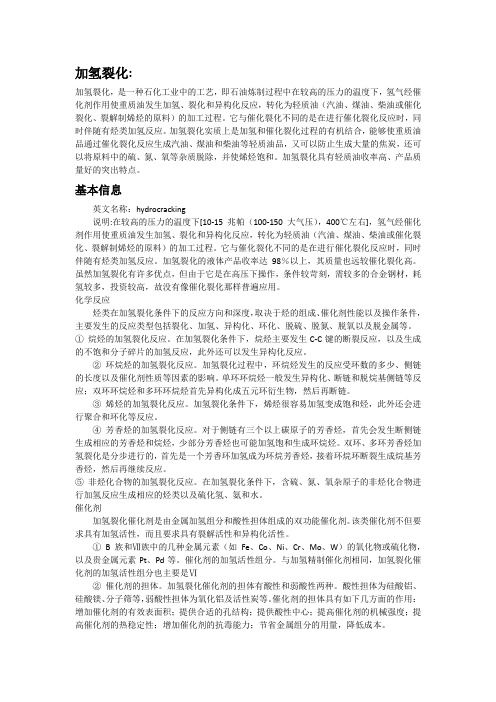
加氢裂化:加氢裂化,是一种石化工业中的工艺,即石油炼制过程中在较高的压力的温度下,氢气经催化剂作用使重质油发生加氢、裂化和异构化反应,转化为轻质油(汽油、煤油、柴油或催化裂化、裂解制烯烃的原料)的加工过程。
它与催化裂化不同的是在进行催化裂化反应时,同时伴随有烃类加氢反应。
加氢裂化实质上是加氢和催化裂化过程的有机结合,能够使重质油品通过催化裂化反应生成汽油、煤油和柴油等轻质油品,又可以防止生成大量的焦炭,还可以将原料中的硫、氮、氧等杂质脱除,并使烯烃饱和。
加氢裂化具有轻质油收率高、产品质量好的突出特点。
基本信息英文名称:hydrocracking说明:在较高的压力的温度下[10-15兆帕(100-150大气压),400℃左右],氢气经催化剂作用使重质油发生加氢、裂化和异构化反应,转化为轻质油(汽油、煤油、柴油或催化裂化、裂解制烯烃的原料)的加工过程。
它与催化裂化不同的是在进行催化裂化反应时,同时伴随有烃类加氢反应。
加氢裂化的液体产品收率达98%以上,其质量也远较催化裂化高。
虽然加氢裂化有许多优点,但由于它是在高压下操作,条件较苛刻,需较多的合金钢材,耗氢较多,投资较高,故没有像催化裂化那样普遍应用。
化学反应烃类在加氢裂化条件下的反应方向和深度,取决于烃的组成、催化剂性能以及操作条件,主要发生的反应类型包括裂化、加氢、异构化、环化、脱硫、脱氮、脱氧以及脱金属等。
①烷烃的加氢裂化反应。
在加氢裂化条件下,烷烃主要发生C-C键的断裂反应,以及生成的不饱和分子碎片的加氢反应,此外还可以发生异构化反应。
②环烷烃的加氢裂化反应。
加氢裂化过程中,环烷烃发生的反应受环数的多少、侧链的长度以及催化剂性质等因素的影响。
单环环烷烃一般发生异构化、断链和脱烷基侧链等反应;双环环烷烃和多环环烷烃首先异构化成五元环衍生物,然后再断链。
③烯烃的加氢裂化反应。
加氢裂化条件下,烯烃很容易加氢变成饱和烃,此外还会进行聚合和环化等反应。
加氢裂化操作规程2017.终

Q/SY 中国石油长庆石化公司企业标准Q/CSZ 12 051-2017120万吨/年加氢裂化装置操作规程2017年12月26日发布 2018年01月01日实施中国石油长庆石化公司发布编审批表项目部门姓名签字日期编写操作人员杨团波王爱平魏伟李明董海文韩晓飞齐向前张铖技术人员陈伟安王文平范雯姝刘刚尹向昆魏长序部门审核生产运行组组长刘黎明机动设备组组长刘衷铭安全环保组组长师俊运行一部魏宏斌处室会签生产运行处陈洪机动设备处索涛质量安全环保处罗茂强批准廉金龙版本更新记录版本号日期再版原因更改内容页码Q/CSZ 6 801-2006 2006年10月初版见评审修订记录Q/CSZ 6 801-2009 2009年12月换版修订见评审修订记录Q/CSZ 6 801-2012 2012年12月换版修订见评审修订记录Q/CSZ 6 801-2012 2013年12月年度修订见评审修订记录Q/CSZ 6 801-2012 2014年12月年度修订见评审修订记录Q/CSZ 12 051-2015 2015年12月年度修订见评审修订记录Q/CSZ 12 051-2016 2016年12月换版修订见评审修订记录Q/CSZ 12 051-2017 2017年12月年度修订见评审修订记录本规程是根据中国石化洛阳石油化工工程公司设计及生产实际情况提出。
本标准作为指导、组织装置试生产的依据。
本规程起草单位:中国石油长庆石化公司运行一部。
管理和使用方法:1. 操作规程的遵守1.1 操作规程规定了管理人员和操作人员必须严格按照指定的操作路线执行指定的操作。
1.2 如在操作过程中出现事故,装置负责人可以指挥当前的操作返回上一个稳定的操作状态。
1.3 严禁对已经执行的操作重新标记,如果需要重新操作可以使用另外一份操作规程,原规程存档备查。
1.4 在一些特殊条件下,装置负责人可以根据具体情况调整操作,在操作完成后必须备案并说明原因。
2. 在操作规程上做标记2.1 标记通常由内操作员在控制室进行;2.2 标记在每项具体操作以及确认状态的前面的操作性质代号内;2.3 为了避免外操作员频繁往来于现场和控制室之间,方便外操作员准确执行操作,可以为外操作员提供一份编好页码、注明日期的操作规程复印件。
加氢裂化技术

加氢裂化技术
加氢裂化技术是一种炼油工业中常用的重油加工技术,旨在通过在高温高压下通过加氢和裂化反应,将重质石油馏分转化为高质量的轻质馏分。
该技术的基本原理是将重油在催化剂的催化作用下,在高温(约500-550°C)和高压(约30-70条)的条件下,与氢气进行反应。
加氢裂化反应中,重油分子中的长链烷烃会被断裂成较短的链烷烃,并通过与氢气的反应而饱和,形成较低碳数的烷烃和环烷烃。
加氢裂化技术的主要目标是提高石油产品的产率和质量,具体应用包括以下几个方面:
1. 改善汽油产率:加氢裂化技术可以将重油中的高分子长链烷烃裂解为较短的链烷烃,从而增加汽油的产量,并提高其辛烷值,使其适用于高性能汽车发动机。
2. 降低重油的黏度:重油中高分子长链烷烃的裂解和饱和反应可以降低其分子量和粘度,使得处理后的产品易于输送和加工。
3. 控制沥青质量:加氢裂化技术可以通过裂解重油中的沥青分子,将其转化为更轻的烃类,从而改善沥青的质量,并根据市场需求调整其粘度和温度特性。
4. 降低硫含量:加氢裂化过程中,硫化物在反应中与氢气反应生成硫化氢,从而降低产品中的硫含量,减少对环境的污染。
5. 降低氮含量:透过高温高压下的加氢过程,氮化物在反应中与氢气反应形成氨气,从而降低产品中的氮含量,减少对环境和催化剂的不利影响。
加氢裂化技术在炼油工业中得到了广泛应用,可以使得重质石油馏分无需经过深度加工,就能够得到更高产率和更高质量的产品。
- 1、下载文档前请自行甄别文档内容的完整性,平台不提供额外的编辑、内容补充、找答案等附加服务。
- 2、"仅部分预览"的文档,不可在线预览部分如存在完整性等问题,可反馈申请退款(可完整预览的文档不适用该条件!)。
- 3、如文档侵犯您的权益,请联系客服反馈,我们会尽快为您处理(人工客服工作时间:9:00-18:30)。
加氢裂化质量控制指标和工艺技术条件
1.1 原材料性质指标
1.1.1原料性质指标
对加氢裂化工艺过程而言,其可加工的原料馏份范围很宽,在制取不同目的产品时对原料组分或馏份的要求局限不大,但从维持装置长周期运行方面来讲则要根据装置设计特点,严格控制原料性质,所以我装置原料性质要求如下表:
表16、原料性质指标
1.1.2 氢气性质指标
装置用氢主要由乙烯制氢装置和本装置所带重整氢、低分气提纯装置供应,操作条件下主要指标如下:
表17、氢气性质指标
1.1.3 高压注水性质指标
反应高压注水选用一电供应脱盐水,对水质要求如下:
表18. 高压注水性质指标
1.2 产品质量指标
表19、主要产品质量指标
*夏季柴油干点365℃,冬季柴油干点355℃。
☆当航煤做柴油组分时,闪点≮50℃,干点执行柴油标准
1.3化验分析项目
表20、装置化验分析项目。