第三章_液压泵详细介绍
第三章 液压泵
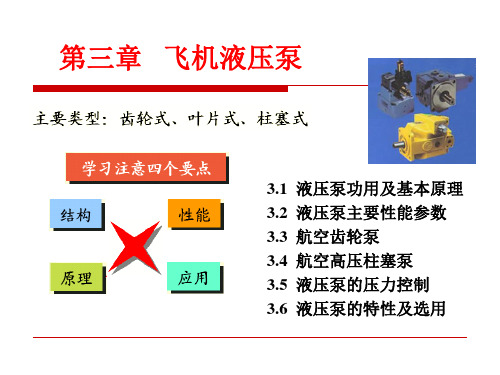
3.6 航空液压泵的特性及选用
3.6.1、液压泵的气穴
广义地说,在某一温度下当油泵吸油腔压力降 低到空气分离压以下时,混溶与油中的空气就分离 出来形成气泡;而当吸油压力继续降低到该温度的 饱和蒸汽压力以下时,油液便汽化沸腾,形成大量 的气泡,这些现象统称为气穴现象。
3.6.1、液压泵的气穴
当气(汽)泡被带到高压油腔时,在高压作用 下,气(汽)泡便急剧溃灭或急剧缩小体积, 从而产生局部液压冲击现象,引起零件表面 的剥蚀损坏,表现为气蚀现象;同时也使得 泵的输出压力不稳定,影响设备正常工作。
3.6.4、液压泵的性能比较及选用
设计液压系统时,应根据所要求的工作情况合 理选择液压泵。
外啮合齿轮泵实物结构
内啮合齿轮泵实物结构
单作用式叶片泵
双作用叶片泵
单柱塞式液压泵
径向柱塞泵
通过齿轮端面与端盖之间的轴向间隙;
轮齿啮合线处的接触间隙。
因此,普通齿轮泵的容积效率比较低,输出压力也 不易提高。在高压齿轮泵中,一般都使用轴向间隙 补偿装置以减少轴向泄漏,提高其容积效率。
3、径向力不平衡
1.齿轮受到来自压油腔 高压油的油压力作用;
2.压油腔的油液沿泵体 内孔和齿顶圆之间的径 向间隙向吸油腔泄漏时, 其油压力是递减的,也 作用于齿轮上。
3.4.5、柱塞泵优缺点及选用
优点:
1、工作压力、容积效率及总效率均最高; 2、可传输的功率最大; 3、较宽的转速范围; 4、较长的使用寿命及功率密度高; 5、良好的双向变量能力。
3.4.5、柱塞泵优缺点及选用
缺点:
1、对介质洁净度要求较苛刻; 2、流量脉动较大,噪声较高; 3、结构较复杂,造价高,维修困难。
排量和流量
第3章液压泵-资料

(3.13)
实际上,齿槽容积比轮齿体积稍大一些,并且齿数越少 差值越大,因此需用3.33 ~ 3.50来代替上式中的值(齿数少 时,取大值),以补偿误差。即齿轮泵的排量为
V(6.66~7)zm2b
(3.13)
由此得齿轮泵的输出流量为
q(6 .66~7)zm 2bnv
(3.15)
齿轮泵的排量和流量(2/2)
消除困油的方法,通常是在两端盖板上开卸荷槽 (图3.8(d)中的虚线),使封闭容积减小时,通过右 边的卸荷槽与压油腔相通;封闭容积增大时,通过左边 的卸荷槽与吸油腔相通。两卸荷槽的间距必须确保在任 何时(2) 径向不平衡力 在齿轮泵中,液体作用在齿轮外缘的压力是不均匀 的,从低压腔到高压腔,压力沿齿轮旋转的方向逐齿递 增,因此齿轮和轴受到径向不平衡力的作用。工作压力 越高,径向不平衡力也越大。径向不平衡力很大时,能 使泵轴弯曲,导致齿顶接触泵体,产生摩擦;同时也加 速轴承的磨损,降低轴承使用寿命。为了减小径向不平 衡力的影响,常采取缩小压油口的办法,使压油腔的压 力油仅作用在一个齿到两个齿的范围内;同时适当增大 径向间隙,使齿顶不和泵体接触。
齿轮泵结构分析(5/5)
通常采用的自动补偿端面间隙装置有浮动轴套式和 弹性侧板式两种。浮动轴套式齿轮泵的浮动轴套是浮动 安装的,轴套外侧的空腔与泵的压油腔相通。所引入压 力油使轴套或侧板紧贴在齿轮侧端面上,泵输出的压力 愈高,贴得愈紧,因而自动补偿端面磨损和减小间隙。 当泵工作时,浮动轴套受油压的作用而压向齿轮端面, 将齿轮两侧面压紧,从而补偿了端面间隙。
V2(R2r2)b
泵的实际输出流量为
q V n v 2 (R 2 r2) b n v
体积对排量无影响。因为 在压油腔,叶片缩回排出的液 体体积补偿了叶片在压油腔所 占的体积。
第三章 液压泵

22
双作用叶片泵
结构组成 – 定子 其内环由两段大半径R 圆弧、两段小半 径 r 圆弧和四段过渡曲线组成 – 转子 铣有Z个叶片槽,且与定子同心,宽度 为b – 叶片 在叶片槽内能自由滑动 – 左、右配流盘 开有对称布置的吸、压油窗口 – 传动轴
2013-7-14
23
2013-7-14
24
工作原理 (动画) • 当转子依顺时针方向旋转时,左上角和右下角的 叶片向转子外伸出,使密封工作腔容积逐渐增大, 形成局部真空,于是经配油盘上相应的腰形窗口 将油吸入,实现吸油过程;右上角和左下角的叶 片向转子内缩进,使密封工作腔容积逐渐缩小, 原来吸入的油液受挤压后经配油盘上相应的窗口 压入系统,实现排油过程。在吸、压油窗口之间 有一段封油区将它们隔开,避免吸、排油口互相 窜通。 排量公式
工作原理是柱塞在液压缸内作往复运动来实现吸 油和压油。与齿轮泵和叶片泵相比,该泵能以最 小的尺寸和最小的重量供给最大的动力,为一种 高效率的泵,但制造成本相对较高,该泵用于高 压、大流量、大功率的场合。它可分为轴向式和 径向式两种形式。 柱塞沿径向放置的泵称为径向柱塞泵,柱塞轴向 布置的泵称为轴向柱塞泵。
2013-7-14 21
2.3叶片液压泵
• 叶片泵分为双作用叶片泵和单作用叶片泵。双作 用叶片泵只能作定量泵用,单作用叶片泵可作变 量泵用。 • 双作用叶片泵因转子旋转一周,叶片在转子叶片 槽内滑动两次,完成两次吸油和压油而得名。 • 单作用叶片泵转子每转一周,吸、压油各一次, 故称为单作用。
2013-7-14
10
液压泵的图形符号
2013-7-14
11
2.2 齿轮泵
• 齿轮泵是利用齿轮啮合原理工作的,根据啮合形 式不同分为外啮合齿轮泵和内啮合齿轮泵。
液压泵和液压马达原理

结束
§3-2 柱塞泵
在第一节所述单柱塞泵中,凸轮使泵 在半周内吸油,半周内排油。因此泵排出 的流量是脉动的,它所驱动的液压缸或液 压马达的运动速度是不均匀的。所以无论 是泵或马达总是做成多柱塞的。常用的多 柱塞泵有径向式和轴向式两大类。
一、径向柱塞泵 二、轴向柱塞泵
1.径向柱塞泵的工作原理 图为径向柱塞泵的工作原理。之所以称为径 向柱塞泵是因为有多个柱塞径向地配置在一个共 同的缸体3内。缸体由电动机带动旋转,柱塞要靠 离心力耍出,但其顶部被定 子2的内壁所限制。定子2是 一个与缸体偏心放置的圆环。 因此,当缸体旋转时柱塞目 前生产中应用不广。
泵的转子K及其轴承上会受到不平衡的液 压力,大小为: P=pBD 式中 P—转子受到的不平衡液压力; p—泵的工作压力; B—定子的宽度; D—定子内直径。 计算泵的几何排量为: q=B[(R+e)2-(R-e)2]=4BRe=2Bde 理论流量为: QT=2Bde 式中 R—定子内半径; e—定子与转子的偏心量;
泵的摩擦损失由两部分组成
容积损失 主要是液压泵内部泄漏造成的流量 损失。容积损失的大小用容积效率表征PV 机械损失 指液压泵内流体粘性和机械摩擦 造成的转矩损失。机械损失的大小用机械效 率表征Pm Pm=MT/MP 液压泵的总效率 泵的总效率是泵的输出功率 与输入功率之比 P=Pm.PV
实际上叶片有一定厚度,叶片所占的空间减 小了密封工作容腔的容积。因此转子每转因叶片 所占体积而造成的排量损失为
式中,s—叶片厚度;θ—叶片倾角。
因此,双作用叶片泵的实际排量为
双作用叶片泵的实际输出流量为
式中,n—叶片泵的转速,ηpv—叶片泵的容积效率 。 叶片泵的流量脉动很小。理论研究表明,当叶 片数为4的倍数时流量脉动率最小,所以双作用叶 片泵的叶片数一般取12或16。
3第三章 液压泵

泵的输出功率可由下式求得 N出 P Q 63 105 53 103 / 60 5565W 总效率为输出功率与输入功率之比 N出 5565 0.795 N 入 7000 机械效率 m
0.795 0.840 v 0.946
maojian@
2 2
R,r 定子圆弧部分的长短半径;
叶片倾角;
s 叶片厚度; z 叶片数。
maojian@
§3-4 柱塞泵
一、径向柱塞泵的工作原理和流量计算
图3—22 径向柱塞泵的工作原理 1—柱塞 2—缸体 3—衬套 4—定子 5—配油轴
maojian@
径向柱塞泵的排量和流量计算:
二、内啮合齿轮泵
内啮合齿轮泵优点: 1.结构紧凑,体积小; 2.零件少,转速可高达10000r/mim; 3.运动平稳,噪声低; 4.容积效率较高。 内啮合齿轮泵缺点: 1.转子的制造工艺复杂。
maojian@
汽车自动变速器的内啮合齿轮泵
maojian@
§3-3 叶片泵
5 6
2)电机驱动功率 P输入 P输出 / 45.9 / 0.9 51kW
maojian@
三、液压泵的类型
1.液压泵类型
柱塞式 轴向柱塞式 径向柱塞式 单作用叶片式 双作用叶片式 外啮合式 内啮合式
maojian@
液 压 泵
叶片式
齿轮式
maojian@
例2:某液压泵输出压力为200×105Pa,转速 n=1450r/min,排量为100 ml/r,该泵的容积效 率为0.95、总效率为0.9,试求这时泵的输出功 率和电动机的驱动功率。
解:1)泵的输出功率: P输出 pq实际 p V nv 200 10 100 10 1450 0.95 45916W 60 45.9kW
03第三章 液压泵x
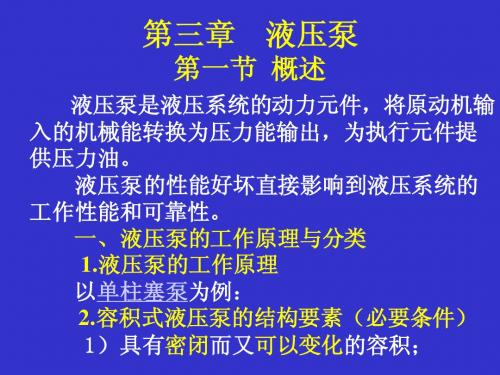
际输入转矩Tt之比。即
m
Tt T Tt Tt Tl 1 1 Tl / Tt
式中Tl——转矩损失。 (6)总效率:泵的实 际输出功率P与实际输入功 率Pr之比,即
P Pr pq
T
Tt qt
q
T
v m
液压泵性能特性曲线 如右图:
4.转速 (1)额定转速:额定压力下,允许液压泵 连续运转的最高转速(容积效率最高)。 (2)最高转速:额定压力下,允许短暂运 行的最大转速(受“汽穴”现象限制)。 (3)最低转速:运行液压泵正常运转的最 低转速(受容积效率的限制)。 5.自吸能力 液压泵正常运转时,并不发生汽穴或汽蚀 的条件下,吸液口允许的最低压力。
(3)工作压力:泵实际工作时的压力,其 大小取决于外负载和排油管路上的压力损失。 液压泵按工作压力分: 低压泵 <2.5 MPa 机床 中压泵 2.5~8 MPa 机床 中高压泵 8~16 MPa 工程、冶金、农 业机械 高压泵 16~32 MPa 工程、冶金、采掘 机械 超高压泵 >32 MPa 液压支架 (4)吸入压力:泵入口处的压力。
外反馈限压变量叶片泵变量原 理
内反馈限压变量叶片泵变量原理
3)限压变量叶片泵 的工作性能(右图) 用在机床液压系统中 要求执行元件有快、慢速 和保压阶段的场合。
叶片泵的特点:
优点:运转平稳,流量均匀,噪声小。 缺点:结构复杂,吸油特性不太好,对 油液的污染比较敏感。
第四节 柱塞泵
一、径向柱塞泵 1.轴配流径向柱塞泵 1)组成:转子 偏心安装; 定子 柱塞——径向装入转子; 配流轴——固定不动。 2)工作原理(右图)
2)设置专门的配流机构; 3)油箱内液体的绝对压力必须恒等于或大 于大气压力。 3.液压泵的分类 液压泵按其在每转一周所能输出的油液体 积是否可调节分成定量泵和变量泵。 按构成密封又可以变化的容积空间的零件 结构来划分:齿轮泵、叶片泵、柱塞泵等。 二、液压泵的压力建立条件及其安装高度 1.压力建立条件——外载荷 液压泵的压力,一般是指其出口截面3-3处 的液压力。根据伯努利方程可得
液压泵

二、液压泵的主要性能参数
• • • • •
m /r V 1. 排量 2. 流量 1)理论流量 qt Vn 2)实际流量 q qt ql 3)额定流量
3
液压泵在额定转速、额定压力下,按实验标准规定必须保证的流量。 按实验标准规定,液压泵能够实现连续运转的最高压力称为液 压泵的额定压力
二、液压泵的主要性能参数
V 6.66m zB
2
q 6.66m zBnV
2
2.外啮合齿轮泵的流量计算
q 6.66m zBnV
2
m z mz m
2
mz 不变,减少齿数,
增大模数,可以在不增大 泵体积的前提下提高泵的 输出流量
3.流量脉动率
qmax qmin q
外啮合齿轮泵齿数越少,流量脉 动率就越大,其最大值可达20% 以上。
二、单作用叶片泵
1. 结构: 转子、定子、叶片、配油盘、壳体、端盖等。
特点: ●定子和转子偏心; ●定子内曲线是圆; ●配油盘有二个月牙形 窗口。 ●叶片靠离心力伸出。
2. 工作原理
单作用叶片泵
• 密封工作腔(转子、定子、叶片、配油盘组成) • 吸油过程:叶片伸出→V ↑ → p ↓ →吸油; • 排油过程:叶片缩回→V ↓ → p ↑ →排油。 • 旋转一周,完成一次吸油,一次排油——单作用泵 • 径向力不平衡——非平衡式叶片泵 (一个吸油区,一个排油区)
一种抽吸设备,水平管出口通大气,当水平管内液 体流量达到某一数值时,垂直管子将从液箱内抽吸 液体。液箱表面与大气相通,水平管内液体和被抽 吸液体相同。若不计液体流动时的能量损失,问水 平管内流量达到多大时才能开始抽吸。
10
9 8
7 6 5 4
3第三章液压泵及液压马达(1)

2. 工作原理
3. 流量
q 2 k z m2 b n V
4. 特点
流量和压力的脉动较小;无困油区,噪声较低; 加工难价格高;轮齿接触应力小,泵的寿命较长。
(二)摆线形内啮合齿轮泵
1 . 主要组成
摆线齿轮泵又称为转子泵,由两齿轮及 前后端盖等组成。且两齿轮相差一个齿。
2. 工作原理
吸油 —— 左半部分,轮齿脱开啮合,容积↑ 压油 —— 右半部分,轮齿进入啮合,容积↓
三 液压泵(马达)的性能参数
液压泵(马达)的性能参数主要有: 压力 转速
排量和流量 功率和效率
一、 排量、流量和压力
1. 压 力
⑴ 工作压力(p) —— 液压泵(或马达)工作时输出液体的实际压力。 其值取决于负载(包括管路阻力)。
(2) 额定压力(p n)—— 油泵(或马达)铭牌上标注的压力值。指在 连续运转情况下所允许使用的工作压力。它能使泵(或马达)具有较高的 容积效率和较长的使用寿命。
轴套 采用浮动轴套的中高压齿轮泵结构图
2. 高压内啮合齿轮泵
➢ 轴向间隙补偿原理
与外啮合齿轮泵浮动侧板的补偿相似,也是利用背压使两侧的浮 动侧板紧贴在小齿轮、内齿环和填隙片端面上;磨损后,也可利用背 压自动补偿。
➢ 径向间隙补偿原理
径向半圆支承块(15)的下面也有两个背压室,各背压室均与压 油腔相同。在背压作用下,半圆支承块推动内齿环,内齿环(6)又 推动填隙片与小齿轮齿顶相接触,形成高压区的径向密封。同时,可 自动补偿各相对运动间的磨损。
qt qm
qm q qm
1
q qm
(6) 马达总效率(ηm)
液压马达的总效率是实际输出功率与实际输入功率的比值,即:
m
第三章液压泵讲义与液压马达

2. 困油现象 动画演示
1) 产生原因:
压
吸
ε> 1,构成闭死容积Vb
2)危害:
Vb由大→小,p↑↑, 油液发 热,轴承磨损。
Vb由小→大,p ↓↓, 汽蚀、 噪声、振动、金属表面剥蚀。
(三)液压马达的转速和容积效率
理论转速:nt= qM /VM 容积效率:
ηMv= qMt / qM =( qM -ql )/ qM = 1- ql / qM
输出转速nM= (qM -ql )/VM= qM /VM ηMv
(四)液压马达的转矩和机械效率
实际输出转矩 TM=TMt-ΔT 理论输出转矩 TMt=Δp VM/ 2π 机械效率ηMm=TM/TMt
q=Vnηv =πDhbnηv =2πzm2bn ηv
三、齿轮泵结构特点
1、泄漏问题
泄漏
齿轮泵存在端面泄漏、径向泄漏和轮齿
啮合处泄漏。其中端面泄漏占80%—85%。
减少泄露的措施:间隙补偿
其中端面间隙补偿采用静压 平衡
在齿轮和盖板之间增加一个 补偿零件,如浮动轴套或浮动侧 板,在浮动零件的背面引入压力 油,让作用在背面的液压力稍大 于正面的液压力,其差值由一层 很薄的油膜承受。
周所排出的液体体积。
2.理论流量qt (m3/s) 是指在不考虑泄漏的情况下,单位时间内排出的
液体体积。
qt =Vn 3.实际流量qp
指液压泵工作时的输出流量。
qp= qt - △ q
4.额定流量qn 指在额定转速和额定压力下泵输出的流量。
(四)功率与效率
1.输入功率: Pi=2πnT 2.输出功率: Po=ppqp 3.容积效率: ηpv =qp /qt 4.总效率: ηp =Po /Pi= ppqp/2πnT=ηpm ηpv 5.机械效率: ηpm = η /ηpv
第三章液压泵新

2) 危害:ηv↓
3) 防泄措施:
a) 减小端面间隙
b) 端面间隙补偿装置
浮动侧板
浮动轴套
防泄措施
a) 减小轴向间隙
小流量:间隙0.025-0.04 mm
大流量:间隙0.04-0.06 mm
b) 轴向间隙补偿装置
浮动侧板
浮动轴套
F1稍大于F2
四、齿轮泵优缺点和用途
优点:体积小,重量轻,结构紧凑,工作可靠,自吸
转的最高压力。
(3)最高压力:短时间运行允许最高压力。
2、排量V:不考虑泄漏情况下,泵(马达)每转一圈
所排出液体的体积,一般由其结构尺寸计算得来。
3、流量q:单位时间内能排出的流体体积。单位:m3/s
(1)理论流量qvt:不考虑泄露
qvt=V×n
(2)实际流量qv:
(3)额定流量qvn: 额定压力、额定转速下泵输出的流量
1—偏心轮
2—柱塞
3—泵体
4—弹簧
5,6—单向阀
c—工作腔
配流装置使密封容积轮流和油箱或负载相通。
容积式液压泵正常工作的三个必备条件
▲1必须具有一个由运动件和非运动件所构成的密闭容
积;
▲2密闭容积的大小作周期性的变化, 容积由小变大—
—吸油,由大变小——压油;
▲3吸油口和排油口应严格分开,并有合适的配流装置,
2) 流量:
q 2B[(R 2 r 2 )
其中:B - 叶片宽度
R - 定子长轴半径
r - 定子短轴半径
θ – 叶片倾角
δ – 叶片厚度
吸
R r
z ]nv
cos
压
三、单作用叶片泵
1. 结构:
转子、定子、叶片、配油盘、壳体、端盖等。
第三章 液压泵与液压马达

(三)液压泵排量和流量
1.排量Vp (m3/r) 是指在不考虑泄漏的情况下,液压泵主轴每转一 周所排出的液体体积。 2.理论流量qt (m3/s) 是指在不考虑泄漏的情况下,单位时间内排出的 液体体积。 qt =Vn 3.实际流量qp 指液压泵工作时的输出流量。 qp= qt - △ q 4.额定流量qn 指在额定转速和额定压力下泵输出的流量。
(动画) 2、工作原理:
旋转一周,完成二次吸油,二次排油——双作用泵
径向力平衡——平衡式叶片泵(两个吸油区,两个排油区)
3、 流量计算
忽略叶片厚度:
V=2π(R2-r2)B q=Vnηv = 2π(R2-r2)Bn ηv
如考虑叶片厚度: V=2π(R2-r2)B -2BbZ(R-r)/cosθ q=Vnηv = 2π(R2-r2)Bn ηv -2BbZ(R-r)/cosθ nηv
2、液压泵进口压力 p 0 0MPa , 出口压力 pp 32MPa , 实际输出流量q 250 L min,泵输入转矩 T pi 1350N m , 输入转速 n 1000r min ,容积效率 0.96 。试求: (1)泵的输入功率 P i ,(2)泵的输出功率 P o ,(3) 泵的总效率 ,(4) 泵的机械效率 m
第三章 液压泵与液压马达
液压泵--动力元件: 将驱动电机的机械能转换成液体的压力能, 供液压系统使用,它是液压系统的能源。
3-1概
ch3液压泵

θ-叶片安置角。
单作用叶片泵工作原理及结构
双作用叶片泵的结构特点
1、保证叶片与定子内表面的良好接触 原理:将压力油引入叶片底部,平衡叶片 顶部的液压力 存在的问题:叶片经过吸油区时叶片底部 没有液压力,附加的叶片底部的液压力会加 剧叶片的磨损 2、避免困油现象,减少液压冲击和噪声 存在困油现象,通过开卸荷槽来解决
3、使叶片顶部和底部的液压力平衡
减小叶片在吸油区时底部作用油压
减小叶片底部的液压力面积
减小叶片底部的液压力面积
使叶片顶部和底部的液压力平衡
五、单作用叶片泵的结构特点
单作用叶片泵的结构特点
单作用叶片泵与双作用叶片泵的区别
单作用: 1、单数叶片(使流量均匀) 2、 定子、转子和轴受不平衡径向力 3、轴向间隙大,容积效率低 4、叶片底部的通油槽采取高压区通高压、低压区通低压,以 使叶片底部和顶部的受力平衡,叶片靠离心力甩出。 5、叶片常后倾(压力角较小) 双作用: 1、双数叶片(使流量均匀) 2、 定子、转子和轴受平衡径向力 3、叶片底部的通油槽均通以压力油(定子曲线矢径的变化率 较大,在吸油区外伸的加速度较大,叶片的离心力不足以 克服惯性力和摩擦力) 4、叶片常前倾(叶片在吸油区和压油区的压力角变化较大)
摆 线 齿 轮 泵
内啮合渐开线齿轮泵特点
噪声低,无困油现象 压力、流量脉动小
轮齿接触应力小,磨损小,寿命 长
但加工成本较高。
螺杆泵
特点 : 结构紧凑;流量均匀,噪声低;自 吸性能好;转速可以很高,流量大。
双螺杆泵
3-4 叶 片 泵
叶片泵具有结构紧凑、体积小、重量轻、 流量均匀、噪声小、寿命长等优点; 但吸 入特性不太好,对油液的污染比较敏感, 制造工艺要求也比较高。
第三章液压泵

第3章液压泵内容提要本章主要介绍液压动力元件的几种典型液压泵(齿轮泵、叶片泵、柱塞泵的工作原理、性能参数、基本结构、性能特点及应用范围等)。
基本要求、重点和难点基本要求:掌握齿轮泵、叶片泵、柱塞泵的工作原理、性能参数、结构特点。
了解各类泵的典型结构及应用范围。
重点:通过本章学习,要求掌握液压泵的工作原理、功能、性能参数(压力和流量等)、性能特点及应用范围。
难点: ①密闭容积的确定(特别是齿轮泵)。
②容积效率的概念。
③额定压力和实际压力的概念。
④外反馈限压式变量叶片泵的特性。
⑤柱塞泵的变量机构。
3.1液压泵基本概述液压泵作为液压系统的动力元件,将原动机(电动机、柴油机等)输入的机械能(转矩T 和角速度ω)转换为压力能(压力p 和流量q )输出,为执行元件提供压力油。
液压泵.的性能好坏直接影响到液压系统的工作性能和可靠性,在液压传动中占有极其重要的地位。
3.1.1液压泵的工作原理如图3-1所示,单柱塞泵由偏心轮1、柱塞2、弹簧3、缸体4和单向阀5、6等组成,柱塞与缸体孔之间形成密闭容积。
当原动机带动偏心轮顺时针方向旋转时,柱塞在弹簧力的作用下向下运动,柱塞与缸体孔组成的密闭容积增大,形成真空,油箱中的油液在大气压力的作用下经单向阀5进入其内(单向阀6关闭)。
这一过程称为吸油,当偏心轮的几何中心转到最下点O 1/时,容积增大到极限位置,吸油终止。
吸油过程完成后,偏心轮继续旋转,柱塞随偏心轮向上运动,柱塞与缸体孔组成的密闭容积减小,油液受挤压经单向阀6排出(单向阀5关闭),这一过程称为排油,当偏心轮的几何中心转到最上点O 1//时,容积减小至极限位置,排油终止。
偏心轮连续旋转,柱塞上下往复运动,泵在半个周期内吸油、半个周期内排油,在一个周期内吸排油各一次。
图3-1 单柱塞泵工作原理 1-偏心轮 2-柱塞 3-弹簧 4-缸体 5、6-单向阀 7-油箱如果记柱塞直径为d ,偏心轮偏心距为e ,则柱塞向上最大行程e s 2=,排出的油液体积2422e d s d V ππ==。
第三章 液压泵

第一节 概 述
2.分类
➢ 按结构将液压泵分为:
➢齿轮泵 ➢外啮合齿轮泵 ➢内啮合齿轮泵
➢叶片泵 ➢单作用叶片泵
➢双作用叶片泵 ➢柱塞泵
➢径向柱塞泵 ➢轴向柱塞泵
➢ 按排量能否改变可分为: ➢定量泵 ➢变量泵
➢ 根据其排量和排液方向能否改变 又可分为: ➢单向定量泵 ➢双向定量泵 ➢单向变量泵 ➢双向变量泵
➢排量取决于泵的结构参数,而与其工况无关,它是衡量和比较不同泵的供液能 力的统一标准,是液压泵的一个特征参数。
➢ 流量——是指泵在单位时间内排除液体的体积,以Q表示,单位L/min。
➢流量有理论流量、实际流量和额定流量三种。
➢ 理论流量——是指不考虑泄漏的理想情况下泵在单位时间(常指每分钟)内
排出的液体的体积,以Ql表示。
– 在渐开线齿形内啮合齿轮泵中,小齿轮和内齿轮之间要装一块月牙形隔板,以便把吸油腔 和压油腔隔开,见图3-10a所示。
– 摆线齿形内啮合齿轮泵又称摆线转子泵,在这种泵中,小齿轮和内齿轮只相差一齿,因而 不需设置隔板,见图3-10b所示。
量或称空在排量)。
➢对于性能正常的液压泵,其容积效率大小随泵的结构类型不同而异。如
齿轮泵为0.7~0.9,叶片泵为0.8~0.95,柱塞泵为0.9~0.95。
第一节 概 述
2. 机械效率ηj
机械效率是表征泵摩擦损失的性能参数,它等于泵的理论输出功率与
输入功率之比。
Pl
j
Pd
3. 总效率η
总效率是表征泵总功率损失的性能参数,它等于泵的实际输出功率与
➢ 内泄漏——是指泵的排液腔向吸液腔的泄漏; ➢ 外泄漏——是指从泵的吸排液腔向其他自由空间的泄漏。 ➢ 泄漏量的大小取决于运动副的间隙、工作压力和液体黏度等因素,而与泵的运动速度关 系不大。 ➢ 当泵的结构和采用的液体粘度一定时,泄漏量将随工作压力的提高而增大,即压力
第3章液压泵和液压马达

排量和流量 功率和效率
台州学院
机械工程学院
1、泵的压力
(1)工作压力 pp
- 液压泵工作时输出的实际压力
- pp的大小取决于负载
台州学院
机械工程学院
(2)额定压力 pn
- 泵在正常工作条件下,按试验标准规定连续运转的 最高压力。即泵工作时允许达到的最高压力
- pn的大小受泵本身的结构强度和泄漏决定
台州学院
机械工程学院
消除困油的方法
方法:在泵前后两盖板上开卸荷槽(如图虚线方框),以消
除困油。
吸油腔
压油腔
a
原则:两槽间距a为最小困油容积,隔开吸压油腔(图b)
当密封容积减小, p↑,使之通压油腔(图a) 当密封容积增大,p↓,使之通吸油腔 (图c)
注意:两卸荷槽的间距应确保不使吸、压油腔相通
台州学院
排量
- 轴转过一周泵排出的油液体积
齿槽 轮齿
- 近似为两个齿轮的齿槽容积之和
- 设齿槽容积=轮齿容积,则排量 V=一个齿轮的齿槽容积+轮齿容积
- 则齿轮泵排量(动画):
B
P
A
V
4 2 m2 zb
2 ( z 2) m ( z 2) m b 2
- 实际,齿槽容积>轮齿容积, π取3.33,
台州学院
机械工程学院
一、双作用叶片泵
- 泵轴转一周,完成两次吸油和压油
动画按钮 台州学院
机械工程学院
1、双作用叶片泵的结构组成
定子:内表面椭圆形,包括
- 两段大半径R圆弧 - 两段小半径r圆弧 - 四段过渡曲线
定子 转子
第三章—液压泵和液压马达

第三章 液压泵和液压马达
该泵配油盘上的吸油窗口和压油窗口对泵的中心线是对称的 。如图所示,泵工作时,油泵出口压力经泵内通道作用在小柱塞 面积上,这样柱塞上的作用力 F PA与弹簧的作用力方向相反。 当PA=KSX0时,柱塞上所受的液压力与弹簧初始力相平衡,此时的 压力P称为泵的限定压力,用PB表示则: PB=KSX0/A 系统的压力P< PB 时,则:PA<KSX0 这表明定子不动,最大偏心距保持不变,泵也保持最大流量。 当系统的压力P> PB 时,则: PA>KSX0 这表明压力油的作用力大于弹簧的作用力,使定子向右移动, 弹簧被压缩,偏心距e减小,泵的流量也随之减小。
第三章 液压泵和液压马达
3.5 柱塞式液压泵
柱塞式液压泵按柱塞在转子内排列方式不同,分为径 向柱塞泵和轴向柱塞泵,轴向柱塞泵又可分为斜盘和斜轴两 大类。柱塞泵由于间隙泄露小、构件受力合理,所以可在高、 超高压力下满意地工作,广泛用于高压、大功率的液压传动 系统中。
第三章 液压泵和液压马达
柱塞泵的优点: 1.参数高:额定压力高,转速高,泵 的驱动功率大; 2.效率高,容积效率为95%左右,总效率为90%左 右; 3.寿命长; 4.变量方便,形式多; 5.单位功率的重量轻; 6.柱塞泵主要零件均受压应力,材料强度性能可得 以充分利用;
第三章 液压泵和液压马达
应用举例 限压式变量叶片泵对既要实现快速行 程,又要实现工作进给(慢速移动)的执行元件来说 是一种合适的油源;快速行程需要大的流量,负载压 力较低,正好使用其AB段曲线部分;工作进给时负载 压力升高,需要流量减小,正好使用其BC段曲线部分。 例如组合机床动力滑台的进给系统、定位和加紧系统 等。 机床加工件:未加工之前或回程要求快;加工时 流量小、速度慢。
第三章 液压泵与液压马达

吸
2、径向压力不 平衡问题
措施:
减少压油口的
尺寸
开压力平衡槽
3、泄漏问题
齿顶 端面 啮合处 措施: 弹性侧板 浮动轴套
高压齿轮泵
四、内啮合齿轮泵 与外啮合齿 轮泵相比,内 啮合渐开线齿 轮泵具有流量 脉动小,结构 紧凑,重量轻, 噪音小,效率 高,无困油现 象等一系列优 点。
1 T pV m 2
q n V V
3.6.2 叶片马达
叶片马达的工作原理
3.6.3 轴向柱塞马达
1.轴向柱塞式液压马达的工作原理
TZ FT l
4
d 2 ptg R sin i
1 1 2 1 T pVm p d DZtg m pd 2 DZtg m 2 2 4 8
二、轴向柱塞泵
录像
1、工作原理
2、流量计算
V
4
d DZtg 2Fra bibliotekq
4
d DZn V tg
2
3、结构要点 (1)缸体端面间隙自动补偿。 (2)滑履结构:柱塞与滑履为球面接触,滑履与斜 盘为平面接触,改善了受力状态。 (3)变量机构:改变斜盘倾角可以改变其排量。
3.6 液压马达
3.6.1 液压马达的主要性能参数 1.液压马达的转矩 2.液压马达的转速
二、 双作用叶片泵 (动画)
1、工作原理 组成:定子、转子、叶 片、配流盘、泵轴、 泵体等。
2、流量计算
V=2π(R2-r2)b q=Vnηv = 2π(R2-r2)b ηv (忽略叶片厚度) 如考虑叶片厚度 V=2π(R2-r2)b -2bsz(R-r)/cosθ q=Vnηv = 2π(R2-r2)bn ηv -2bsz(R-r)/cosθ nηv
- 1、下载文档前请自行甄别文档内容的完整性,平台不提供额外的编辑、内容补充、找答案等附加服务。
- 2、"仅部分预览"的文档,不可在线预览部分如存在完整性等问题,可反馈申请退款(可完整预览的文档不适用该条件!)。
- 3、如文档侵犯您的权益,请联系客服反馈,我们会尽快为您处理(人工客服工作时间:9:00-18:30)。
pB A 因为,pB A k s x0 x0 ks pB A 代入pA k s ( x0 x) pA k s ( x) ks
pA pB A pA pB A k s x x ks A( p pB ) = ks A( p pB ) 因为e e0 x e0 ks
2
(3)脉动率 随着啮合点位置的不断改变,吸、排油腔的每一 瞬时的容积变化率是不均匀的,因此齿轮泵的瞬 时流量是脉动的。
q max q min 100% q
三、外啮合齿轮泵的结构特点 1、困油 (1)困油现象的原理: 齿轮泵要平稳工作, 齿轮啮合的重叠系数 必须大于1,就在两对 轮齿同时啮合的这一小 段时间内,留在齿间的 油液困在两对轮齿和前后泵盖所形成的一个 密闭空间中
第三节 叶片泵
一、 单作用叶片泵 1.结构和原理
2.排量和流量的计算 (1)排量:
V zV 4 Re B
1 4 2 2 V V1 V2 B [( R e) ( R e) ] Re B 2 z
R为定子的内半径;e为转 子与定子之间的偏心矩; B为定子的宽度;β 为相 邻两叶片间的夹角,β =2π /z,z为叶片的个数
二、外啮合齿轮泵的流量与排量计算
1.齿轮泵的排量——可以近 似地等于其中一个齿轮的所有 轮齿体积与齿间槽容积之和。
d a d 2ha mz 2ha m
( z 2h )m ( z 2)m d f d 2h f mz 2(ha c )m
( z 2ha 2c )m
c) 使叶片顶端和底部的液压作用力相平衡 ――-双叶片,弹簧式叶片
三、双级叶片泵和双联叶片泵 1.双级叶片泵 由两个普通压力的单级叶片泵装在一个泵 体内在油路上串接而成。
2.双联叶片泵 由两个单级叶片泵 装在一个泵体内在油 路上并联组成 四、限压式变量叶片泵 1、结构和工作原理 能借助输出压力大小自 动改变偏心距e的大小 来改变输出流量。
二 双作用叶片泵 1、原理
2、 排量和流量 (1)排量: 1)不考虑叶片的厚度和 倾角影响时双作用叶片 泵的排量为 1 2z (R 2 r 2 )B V 2 2 2 2 2 ( R r ) B
Rr V 2 ( R r ) B 2 bzB cos 2)考虑时 Rr 2 2 2 B[ ( R r ) bz ] cos
(2)流量 1)理论流量 qt=Vn=4π ReBn
2)实际流量
q= qtη v=4π ReBnη 转速为n,泵的容积效率为η v
v
3、特点 (1)为变量泵结构。 (2)叶片与相应的油腔相通,并仅靠离 心力的作用顶在定子内表面。 (3)转子上受有不平衡径向力,压力增大, 不平衡力增大,不宜用于高压
2、特性曲线 AB段:工作压力p< pB , 输出流量qA不变,但供 油压力增大,泄漏流量 ql也增加,故实际流量 q减少 BC段:工作压力p> pB ,弹 簧压缩量增大,偏心量减 少,泵的输出流量减少。当定子的偏心量e=0, 则pc = pmax ,此时的压力为截止压力。
pc p max k s ( e0 x 0 ) A
q qt v Vn v
②机械损失和机械效率
机械损失是指液压泵在转矩上的损失。 机械损失用机械效率来表征。
Tt为理论转距, T为实际输入转距
Tt 1 m T 1 Tl Tt
(2)液压泵的功率 1) 输入功率Pi
输入功率指作用在液压泵主轴上的机械功率,当输入转矩 为Ti,角速度为ω时
二、液压泵的主要性能参数 1、压力 (1)工作压力 液压泵实际工作时的输出压 力称为工作压力。 (2)额定压力 液压泵在正常工作条件下, 按试验标准规定连续运转的最高压力称为 液压泵的额定压力。 (3)最高允许压力 在超过额定压力的条件 下,根据试验标准规定,允许液压泵短暂 运行的最高压力植,称为液压泵的最高允 许压力。
k S e0 k S x 0 p B A k S x0 , pC A AB段:调5改e0,当e0 , q A , x0 , p B 当e0 , q A , x0 , p B BC 段:调10改x0,当x0 ,p B ,pC , k S ,保持p B 不变,即p B A(不变) k S x0 k S e0 k S x 0 而pC ,pC A 即k S ,p B 不变,pC ,陡了
• 当pA<ksx0时 定子相对于转子的偏向量最大, 输出流量最大; ks弹簧刚度,x0弹簧的预压 缩量。 • 当pBA=ksx0时 为转折点。 式中pB调定压力, • 当pA>ksx0时 定子相对于转子的偏向量减小, 输出流量减小;
定子移动后的偏心量e为 e = e0-x 其中,设定子的最大偏心量为e0,偏心量减 小时,弹簧的附加压缩量为x 定子的受力平衡方程式为 pA= ks( x0+x)
又因为q= qtηv=4πReBnηv
可以看出,泵的工作压力愈高,偏心量愈 小,泵的输出流量也愈小。
A( p pB ) 当e 0时,即0=e0 ks k s e0 ApB k s e0=A( p pB ) p A k s e0 k s x0 又因为pB A k s x0 p A k s (e0 x0 ) p A 此时的输出流量为零.
2 2
z
(2)流量: 1)理论流量
Rr qt Vn 2 B[ ( R r ) bz ]n cos
2 2
Rr q qt v 2 B[ ( R r ) bz ]n v cos
2 2
2)实际流量
转速为n,容积效率为η v
3、结构特点 ⑴配油盘 a) 封油区所对应的夹角必 须等于或稍大于两个叶片 之间的夹角。 b) 在配油盘上开三角槽 c) 叶片根部与高压油腔 相通,保证叶片紧压在定子内表面上。
a
( z 2 0.5)m
V
z 2m 4
2
z 2m B 2m zB
2 2
齿间槽的容积比轮齿的体积稍大,故通常取 2 V= 6.66m zB 2.流量 2 (1)理论流量 qt 6.66m zBn (2)实际流量
q 6.66m zBn v
⑵定子内表面曲线 要求: a) 叶片不发生脱空 b) 获得尽量大的理论 排量 c) 减小冲击,以降低 噪声,减少磨损 d) 提高叶片泵流量的均匀性,减小流量脉动。
⑶ 叶片倾角: • 压力角: 定子对 叶片的法向反力FN与 叶片沿槽运动方向的 夹角。 • 倾角:叶片与径向 半径的夹角。
4、提高双作用叶片泵压力的措施 a)减小作用在叶片底部的油液压力――阻尼 槽,内装式小减压阀 b) 减小叶片底部承受压力油的作用面积―― 母子叶片,阶梯式叶片
(2)危害: 径向不平衡力很大时能使轴弯曲,齿顶与 壳体接触,同时加速轴承的磨损,降低轴 承的寿命。 (3)措施: 通常采取减小压油口的办法 。减少齿轮的 齿数,这样减小了齿顶圆直径,承压面积 减小。 适当增大径向间隙,使齿轮在压力 作用下,齿顶不和壳体接触。
4、外啮合齿轮泵优缺点 (1)优点: 是结构简单,尺寸小,重量轻,制造方便, 价格低廉,工作可靠,自吸能力强(容许的 吸油真空度大),对油液污染不敏感,维护 容易。 (2)缺点: 是流量和压力脉动较大,噪声大,排量不 可变。一些机件承受不平衡径向力,磨损 严重,泄漏大,工作压力的提高受到限制。
(3)实际流量q 液压泵在某一具体工况下, 单位时间内所排出的液体体积称为实际流 量 q=qt一ql ql为泄漏和压缩损失的流量 (4)额定流量qn 在正常工作条件下,该 试验标准规定(如在额定压力和额定转速 下)必须保证的流量。
3 、功率和效率 (1)液压泵的功率损失 ①容积损失和容积效率 容积损失是指液压泵在流量上的损失, 液压泵的容积损失用容积效率来表征。 ql q qt ql v 1 qt qt qt
第二章 液压动力元件
第一节 液压泵概述 一、 泵的工作原理和分类 1.液压泵的工作原理 依靠密封容积变化的原理
液压泵
注射器
2.液压泵的特点 (1)具有若干个密封且又可以周期性变化的 空间。 (2)油箱内液体的绝对压力必须恒等于或大 于大气压力。 (3)具有相应的配流机构。 3.液压泵分类 (1)按输出可否调节分:定量泵和变量泵 (2)按结构形式分为:齿轮式、叶片式和柱 塞式
(2)困油现象的危害: 开始使闭死容积中的压力急剧升高,使轴 承受到很大的附加载荷,同时产生功率损 失及液体发热等不良现象;然后溶解于液 体中的空气便析出产生气泡,产生气蚀现 象,引起振动和噪声。
(3)消除困油现象: 在齿轮泵的两侧端盖 上铣两条卸荷槽。一 般是非对称式,往往 向吸油腔偏移;必须 保证在任何时候都不 能使吸油腔与压油腔相互串通。
四、螺杆泵和内啮合齿轮泵 1.螺杆泵 (1)工作原理:螺 杆泵实质上是一种外 啮合的摆线齿轮泵,
(2)优缺点: 1)优点: 结构简单、紧凑,体积小,重量轻,运转 平稳,输油均匀,噪声小,容许采用高转 速,容积效率较高(达90%~95%),对油液 的污染不敏感 2)缺点: 是螺杆形状复杂,加工较困难,不易保证 精度。
液压泵,其各个参数和压力之间的关系
4.液压泵的噪声 液压泵的噪声包括机械噪声和液压噪声。 人们常用声压级来衡量噪声的大小,其中 p0是以频率1000HZ时2×10-5N/m2的声压为 基准。
p L 20 lg p0
第二节 齿轮泵
齿轮泵按结构不同,分为外啮合齿轮泵 和内啮合齿轮泵。 一、 外啮合齿轮 泵的工作原理
3.限压式变量叶片泵与双作用叶片泵的区别 (1)限压式变量叶片泵叶片的顶部和底部的液压力 基本平衡,而双作用叶片泵的叶片在吸油区不平衡, 所以在吸油区定子内表面严重磨损。 (2)叶片也有倾角,但倾斜方向(顺着转子转动方向 后倾)正好与双作用叶片泵(前倾)相反。 (3)限压式变量叶片泵结构复杂,轮廓尺寸大,相 对运动的机件多,泄漏较大,轴上受有不平衡的径 向液压力,噪声较大,容积效率和机械效率都没有 双作用叶片泵高;但是,它能按负载压力自动调节 流量,在功率使用上较为合理,可减少油液发热。