氯化钾镀锌钝化膜变色原因探讨及控制措施
镀锌层彩色钝化常见问题及对策-推荐下载
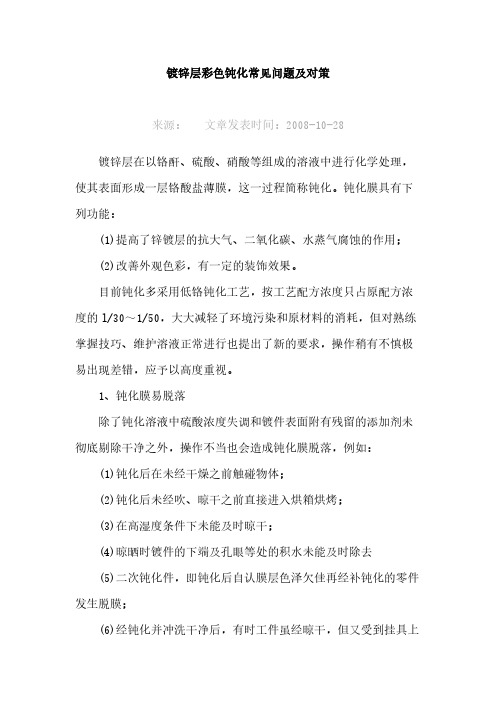
镀锌层彩色钝化常见问题及对策来源:文章发表时间:2008-10-28镀锌层在以铬酐、硫酸、硝酸等组成的溶液中进行化学处理,使其表面形成一层铬酸盐薄膜,这一过程简称钝化。
钝化膜具有下列功能:(1)提高了锌镀层的抗大气、二氧化碳、水蒸气腐蚀的作用;(2)改善外观色彩,有一定的装饰效果。
目前钝化多采用低铬钝化工艺,按工艺配方浓度只占原配方浓度的l/30~1/50,大大减轻了环境污染和原材料的消耗,但对熟练掌握技巧、维护溶液正常进行也提出了新的要求,操作稍有不慎极易出现差错,应予以高度重视。
1、钝化膜易脱落除了钝化溶液中硫酸浓度失调和镀件表面附有残留的添加剂未彻底剔除干净之外,操作不当也会造成钝化膜脱落,例如:(1)钝化后在未经干燥之前触碰物体;(2)钝化后未经吹、晾干之前直接进入烘箱烘烤;(3)在高湿度条件下未能及时晾干;(4)晾晒时镀件的下端及孔眼等处的积水未能及时除去(5)二次钝化件,即钝化后自认膜层色泽欠佳再经补钝化的零件发生脱膜;(6)经钝化并冲洗干净后,有时工件虽经晾干,但又受到挂具上流下的水所润湿而发生部分膜层脱落;(7)钝化溶液温度过高,钝化时间过长而引起的膜层过厚,影响到膜层的结合力。
对于氯化钾光亮镀锌件,若钝化之前未经预处理而脱膜,则必须先经预处理,这是因为氯化钾光亮镀锌件表面附有添加剂,若添加剂未能彻底清洗干净,钝化后必然会引起脱膜,为此,钝化前尚需在沸水中煮3~4min,经冷却后再钝化,这一脱膜问题就能得到解决。
为减少因脱膜而造成返修,在镀件钝化后尚未烘烤之前应做一次检查,当发现有脱膜的应当立即在稀盐酸中退除,用流动水冲洗后重新钝化,这样可以大大简化返修工序。
2、根据钝化溶液温度调节钝化时间溶液温度偏低时成膜速度缓慢,所获的膜层薄,光泽性差,有雾状,需要延长钝化时间,尤其是延长空气中的停留时间才能有所改善,但仍难免“地图”形的花纹出现。
溶液温度偏高时所获钝化膜虽较光亮,色彩自然,但钝化膜结合力差,要防止因钝化时间过长而引起膜层脱落。
氯化钾镀锌镀层出现黑斑点原因及排除

氯化钾镀锌镀层出现黑斑点原因及排除
1、前处理不良:加强镀前处理后再进行试验,观察故障现象是否消失。
若仍未排除故障,则再检查其他原因。
2、镀液中氯化物含量太低,而电流密度过高:取250ml镀液,采用逐渐提高氯化钾(钠)含量进行霍尔槽试验。
若随着氯化物含量的提高,霍尔槽阴极试片上的黑色条纹逐渐向高电流密度端移动并逐渐消失,则表明原镀液中氯化物含量偏低,应根据试验结果补加氯化钾(钠)。
若电流密度过高,则应适当减小阴极电流密度。
3、镀液中有机杂质含量过多:取500ml镀液,加入3g/L左右活性炭,强烈搅拌30min,静置8h后过滤镀液。
将处理前、后的镀液进行霍尔槽试验,若经过处理的镀液,霍尔槽阴极试片镀层比未处理的有明显改善,则说明镀液中有机杂质过多,应根据试验结果确定活性炭的加入量,向镀液中加入活性炭处理,并过滤镀液。
氯化物镀锌低铬彩钝变色与脱膜原因浅析

氯化物镀锌低铬彩钝变色与脱膜原因浅析(时间:2004-4-29 17:46:00 共有386人次浏览)4.5.1 引言笔者在国内是较早接触氯化物镀锌工艺的人员之一。
国内最早推出的氯化物镀锌添加剂为四川拖拉机厂的CT-1。
研制时的生产性试验即在笔者当时所在的国营南光机器厂进行。
由当时机械工业部组织的鉴定会上,笔者为资料审查组组长并负责起草了鉴定意见书。
一般认为其优点为阴极电流效率高(适于铸件电镀)、镀层光亮因而能直接进行低铬钝化、无强络合剂及铵,因而废水处理简单、镀液成分不复杂,易于控制及过滤。
其不足之处为镀液分散能力与深镀能力较差、镀层纯度不够,因而抗蚀力不理想。
由于其利多,因而在国内作为无氰镀锌工艺得到了大面积应用。
多年来的生产实践,感到该工艺的一些缺点已成为不可忽视的重要问题。
其中,低铬彩钝膜的结合力差及钝化膜色泽在存放及使用期间易变淡(包括蓝白钝化层易泛彩),为许多人所头痛。
有的地方环保部门已对废水中的阴离子表面活性剂(ALS)进行监测。
若严格控制表面活性剂排放指标,则对氯化物镀锌将是致命打击。
本文拟就该工艺低铬彩钝脱膜及变色原因作一浅析,并提出一些个人建议。
4.5.2 电镀工艺的问题氯化物镀锌液中无强络合剂,主要靠有机添加剂在阴极界面的吸附来产生阴极极化,从而获得细致光亮的镀层。
添加剂中的表面活性剂含量非常高,这就为彩钝膜易产生色变淡及附着力不良,埋下了祸根。
4.5.2.1 工艺的先天不足众所周知,氯化物镀锌添加剂由主光亮剂、载体光亮剂、辅助光亮剂三大部分组成。
广泛采用的主光亮剂为苄叉丙酮,后来部分采用邻氯苯甲醛。
主光亮剂为阴极消耗型,它们会在阴极还原消耗掉,也有部分直接夹附在镀锌层中。
由于苄叉丙酮不溶于水,必须靠载体光亮剂的增溶作用即表面活性剂生成胶团或胶束,其细微颗粒分散藏隐其中而间接溶于镀液。
早期的载体光亮剂直接采用OP乳化剂、平平加之类的非离子表面活性剂,后来为了提高浊点,专门对HLB 值合适的非离子表面活性剂进行磺化,制成了多种载体光亮剂。
氯化钾镀锌典型故障_周长虹 奥邦电镀

些电镀厂的镀液容易产生浮油 ( 漂在液面上的一种 油状有机物 ) 。其产生的原因主要为: ( 1) 前处理除 油不佳, 槽中有大量的有机油脂, 与表面活性剂形成 皂化等 ; ( 2) 镀液中有较多的铁杂质 , 镀液一般很混 浊; ( 3) 氯化钾的质量浓度过高; ( 4) 添加剂配比有 问题 , 添加剂中某类载体过多等 ; ( 5) 镀液的 pH 值 6。 氯化钾镀锌液面浮油的黏度大 , 易黏在槽壁、 挂 具、 滚桶、 阳极及镀件上或沉淀于镀液底部, 难以彻 底清除。氯化钾镀锌液是弱酸性的 , 本身不具有除 油能力。导电盐氯化钾对镀液的浊点有很大影响 , 在高温季节 , 当镀液中有较多铁杂质时, 添加剂的浊 点会大幅下降。随着组合型添加剂中某类载体添加 剂的不断积累, 与电镀液中的悬浮物和镀件中带入 的油污及三价铁离子共同作用 , 形成酸性且黏度大 的油渍, 严重影响镀层质量。 找到液面浮油产生的原因后, 解决起来就比较 容易了。要选择大品牌的氯化钾镀锌添加剂, 保证 前处理后镀件表面无油, 无锈, 无挂灰, 夏天镀液中 氯化钾的质量浓度不应过高 , 控制镀液的 pH 值在 5. 6~ 6. 0, 镀液温度不宜过高 , 对于已产生浮油的镀 液可按大处理方法进行认真处理 , 可除掉已产生的 浮油。
收稿日期: 2010 10 11
3
低铬彩钝较多有机添 加剂。这些有机物由于种种原因会夹杂在镀层中或 吸附在镀层表面。如果添加剂的质量不佳、 添加过 量或镀后清洗不干净 , 都会产生不良后果。 ( 1) 当镀层中夹杂过多的有机物 , 在钝化过程 中因膜首先被溶解, 结果有机物暴露出来 , 夹杂在工 件表面起隔离作用而使膜脱落或褪色。 ( 2) 清洗不彻底, 工件表面吸附的有机物会在 成膜过程中和工件存储过程中把六价铬还原成三价 铬, 过多的三价铬可能会影响彩钝膜的结合力或使 之变浅褪色。 ( 3) 由于钝化前清洗不认真或清洗不够 , 会带 入大量的氯离子 , 虽然少量的氯离子有利于成膜的 进行 , 但过量会使膜过厚而易脱落。 ( 4) 由于镀前处理时没有彻底清除油污及氧化 膜, 造成局部镀层结合力不好 , 导致钝化膜脱落。 ( 5) 镀锌液工艺控制不当, 使镀液不稳定, 局部 导电不良, 造成镀层疏 松、 脆性 大及结合力差等 缺 陷。 ( 6) 钝化剂硫 酸根和氯 离子的质 量浓度过 高 时, 成膜过快过厚, 时间上很难掌握 , 时间短色泽浅 ,
长弯管氯化钾镀锌钝化故障处理
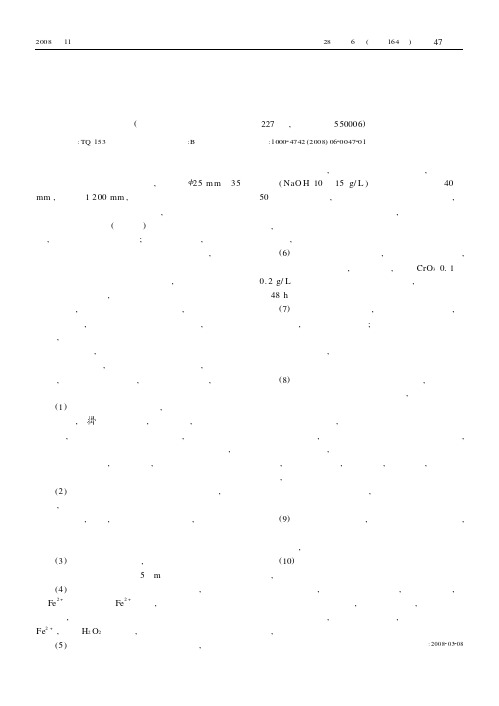
长弯管氯化钾镀锌钝化故障处理童明勇(贵阳市小河经济开发区浦江路227号,贵州贵阳550006)中图分类号:TQ153 文献标识码:B 文章编号:100024742(2008)0620047201 某电镀厂设有氯化钾镀锌生产自动线。
最近承接了一批钢制蛇形的长弯管,其内孔<25m m~35 mm,长度为1200mm,镀锌白钝化业务。
在其加工过程中出现了钝化膜腐蚀变色,尤其是长弯管的管口部分钝化膜腐蚀(长白毛)。
有的钝化件库存一夜后,就出现发雾、发黄现象;彩钝化件变红,甚至出现发黑疵病。
笔者针对上述故障进行了处理,现对处理过程略谈几点体会。
笔者到现场查看了已镀成品,发现镀锌白钝化膜层发蓝雾、发黄,在弯管口上方局部长“白毛”。
经厂方介绍,镀锌件白钝化发生故障后,对所有镀槽进行了大处理,出光、活化、钝化液全部更新,但故障仍存在,未得到介决。
笔者于是查看了最近几天的镀液分析报告单,所有主要技术参数基本正常。
又查看了赫尔槽试片,光亮剂添加情况也正常,同时到车间里,从前处理工序查起,检查了各道工序,针对出现故障现象作了如下分析和处理。
(1)前处理电解除油工序,由于管状镀件容易互相粘合,挂不交叉分挂,管口朝下,很难除去表面油污,尤其是管内油污。
同样道理,酸洗工序也很难将锈除净。
因氯化钾镀液本身没有除油能力,如除油、除锈不干净,带入镀液,极易造成镀锌层钝化后发雾。
(2)氯化钾镀锌光亮剂在夏天温度高时,极易分解,分解物极易和金属离子共沉积。
又由于分解产物易氧化,因此,在高温、潮湿环境中,钝化膜表现为发雾、发黄。
笔者建议应选择耐高温、稳定性高的添加剂。
(3)零件镀锌层太薄,钝化膜也易发黄。
应尽量控制镀锌层厚度不小于5μm。
(4)跌落镀槽中的零件应及时取出,避免镀液内Fe2+的积累。
若Fe2+过高,高电流密度区镀件表面烧焦,钝化后也易产生发雾现象。
平时要控制Fe2+,可用H2O2处理后,过滤。
(5)钢制长弯异形管氯化钾镀锌后,仅靠阴极杠由行车上下移动很难彻底清洗管内残留镀液和有机夹杂物。
氯化钾镀锌主要成分及工艺条件的控制

氯化钾镀锌主要成分及工艺条件的控制前言氯化钾镀锌是上世纪80年代发展起来的一种光亮镀锌工艺。
近年来,我国在电镀添加剂研究开发上取得了显著进展,使得氯化钾镀锌工艺水准达到一个全新的高度,例如:LAN-930氯化钾镀锌工艺较为成功地解决了传统氯化钾镀锌工艺的3大难题:(1)镀层的耐盐雾试验性能比碱性镀锌差;(2)添加剂的分解产物多;(3)铁杂质易超标。
新型氯化钾镀锌添加剂的使用,降低了电镀生产厂商的生产成本,促进了国内电镀锌工艺朝更利于节约成本且环境友好的方向发展。
1·氯化钾镀锌成分及工艺条件的控制氯化钾镀锌工艺的常用配方的工艺条件范围是比较宽广的,其主要成分及工艺条件为:氯化锌30~80g/L,氯化钾180~280g/L,硼酸20~30g/L,添加剂适量,pH值4.5~6.0,10~50℃。
1.1 氯化钾镀锌液主要成分的控制1.1.1 氯化锌氯化锌系主盐,溶于水中会大量放热。
当溶液的pH值≥6.2时,有沉淀产生。
锌离子的质量浓度≥90g/L 时,光亮电流密度范围扩大,但镀液的分散能力和深镀能力会有所下降。
锌离子的质量浓度较低时,光亮电流密度的上限下降,高电流密度区易烧焦,此时的深镀能力较好,但镀层沉积速率较慢。
可增加阳极面积,同时保持镀液较低的pH值,从而使锌离子的质量浓度逐渐上升。
对挂镀而言,当氯化锌的质量浓度为60~70g/L 时,镀液的分散能力最好。
氯化钾镀锌液中无强配位剂,其分散能力和深镀能力不如氰化物镀锌,更加不如无氰碱性锌酸盐镀锌。
有人喜欢在氯化钾镀锌液中加入少量氯化铵,但镀液中加入氯化铵后其分散能力和深镀能力均无改善;又会增加电镀废水的达标难度,所以当使用优良氯化钾镀锌光亮剂时,一般不建议加入氯化铵。
1.1.2 氯化钾氯化钾是弱的配位剂和导电盐,其质量浓度应适当。
当其质量浓度恰当时,镀液的导电性最好,过多或过少都会降低镀液的电导率,从而影响镀液的分散能力和深镀能力。
大量氯离子的存在能增加阴极极化,提高镀液的分散能力和深镀能力,促进阳极的正常溶解。
氯化物镀锌常见故障处理
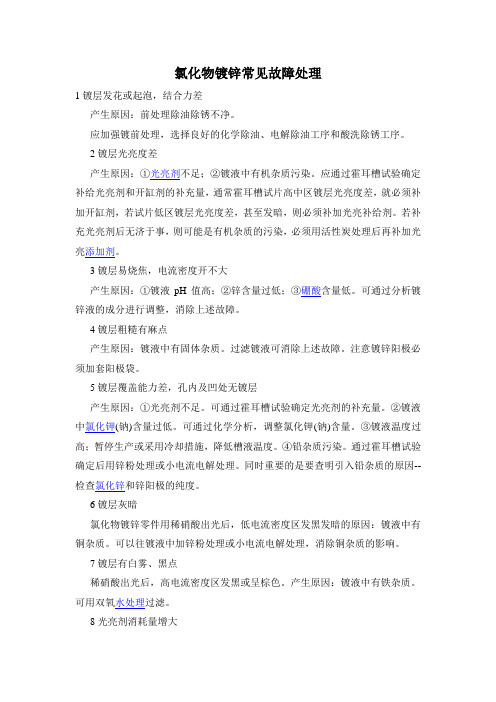
氯化物镀锌常见故障处理1镀层发花或起泡,结合力差产生原因:前处理除油除锈不净。
应加强镀前处理,选择良好的化学除油、电解除油工序和酸洗除锈工序。
2镀层光亮度差产生原因:①光亮剂不足;②镀液中有机杂质污染。
应通过霍耳槽试验确定补给光亮剂和开缸剂的补充量,通常霍耳槽试片高中区镀层光亮度差,就必须补加开缸剂,若试片低区镀层光亮度差,甚至发暗,则必须补加光亮补给剂。
若补充光亮剂后无济于事,则可能是有机杂质的污染,必须用活性炭处理后再补加光亮添加剂。
3镀层易烧焦,电流密度开不大产生原因:①镀液pH值高;②锌含量过低;③硼酸含量低。
可通过分析镀锌液的成分进行调整,消除上述故障。
4镀层粗糙有麻点产生原因:镀液中有固体杂质。
过滤镀液可消除上述故障。
注意镀锌阳极必须加套阳极袋。
5镀层覆盖能力差,孔内及凹处无镀层产生原因:①光亮剂不足。
可通过霍耳槽试验确定光亮剂的补充量。
②镀液中氯化钾(钠)含量过低。
可通过化学分析,调整氯化钾(钠)含量。
③镀液温度过高;暂停生产或采用冷却措施,降低槽液温度。
④铅杂质污染。
通过霍耳槽试验确定后用锌粉处理或小电流电解处理。
同时重要的是要查明引入铅杂质的原因--检查氯化锌和锌阳极的纯度。
6镀层灰暗氯化物镀锌零件用稀硝酸出光后,低电流密度区发黑发暗的原因:镀液中有铜杂质。
可以往镀液中加锌粉处理或小电流电解处理,消除铜杂质的影响。
7镀层有白雾、黑点稀硝酸出光后,高电流密度区发黑或呈棕色。
产生原因:镀液中有铁杂质。
可用双氧水处理过滤。
8光亮剂消耗量增大产生原因:①镀液温度高。
最好采用冷却措施将降低槽液温度或采用间歇生产;②镀液中氯化钾、氯化锌含量过高,使镀液浊点降低,光亮剂析出。
通过分析镀液成分,稀释镀液;③工件除油不净,将大量油污带入镀液中,消耗光亮添加剂中的载体光亮剂。
保证镀锌零件电镀前除油要彻底。
9镀层有条纹产生原因:①光亮剂失调,配槽时添加剂严重不足。
可通过霍耳槽试验,补充添加剂的用量。
镀锌层彩色钝化常见问题及对策-10页word资料

镀锌层彩色钝化常见问题及对策来源:文章发表时间:2008-10-28镀锌层在以铬酐、硫酸、硝酸等组成的溶液中进行化学处理,使其表面形成一层铬酸盐薄膜,这一过程简称钝化。
钝化膜具有下列功能:(1)提高了锌镀层的抗大气、二氧化碳、水蒸气腐蚀的作用;(2)改善外观色彩,有一定的装饰效果。
目前钝化多采用低铬钝化工艺,按工艺配方浓度只占原配方浓度的l/30~1/50,大大减轻了环境污染和原材料的消耗,但对熟练掌握技巧、维护溶液正常进行也提出了新的要求,操作稍有不慎极易出现差错,应予以高度重视。
1、钝化膜易脱落除了钝化溶液中硫酸浓度失调和镀件表面附有残留的添加剂未彻底剔除干净之外,操作不当也会造成钝化膜脱落,例如:(1)钝化后在未经干燥之前触碰物体;(2)钝化后未经吹、晾干之前直接进入烘箱烘烤;(3)在高湿度条件下未能及时晾干;(4)晾晒时镀件的下端及孔眼等处的积水未能及时除去(5)二次钝化件,即钝化后自认膜层色泽欠佳再经补钝化的零件发生脱膜;(6)经钝化并冲洗干净后,有时工件虽经晾干,但又受到挂具上流下的水所润湿而发生部分膜层脱落;(7)钝化溶液温度过高,钝化时间过长而引起的膜层过厚,影响到膜层的结合力。
对于氯化钾光亮镀锌件,若钝化之前未经预处理而脱膜,则必须先经预处理,这是因为氯化钾光亮镀锌件表面附有添加剂,若添加剂未能彻底清洗干净,钝化后必然会引起脱膜,为此,钝化前尚需在沸水中煮3~4min,经冷却后再钝化,这一脱膜问题就能得到解决。
为减少因脱膜而造成返修,在镀件钝化后尚未烘烤之前应做一次检查,当发现有脱膜的应当立即在稀盐酸中退除,用流动水冲洗后重新钝化,这样可以大大简化返修工序。
2、根据钝化溶液温度调节钝化时间溶液温度偏低时成膜速度缓慢,所获的膜层薄,光泽性差,有雾状,需要延长钝化时间,尤其是延长空气中的停留时间才能有所改善,但仍难免“地图”形的花纹出现。
溶液温度偏高时所获钝化膜虽较光亮,色彩自然,但钝化膜结合力差,要防止因钝化时间过长而引起膜层脱落。
氯化钾镀锌由原材料引起的故障三例

试片 ,结果显示 :实验 一试片出现的现象和 现在槽 液
赫尔槽试 片现象一致 ,试片发花且低 电流 密度区发灰 不 亮 ,露 底O . 5 c m左 右 。可 以确定 是这 次新 进 的一 批氯化锌有 问题 ,里面含有超标的铅杂质 。
板锌 板 的溶解 度 与镀液 的p H 值 和温 度都相 关 ,通 常 , p H 值低 、槽液 的温度高 ,锌板溶解速度就 比较快 :一般 情 况下 ,要保持足够 的阳极面积 ,以维持 镀液 中锌离子
浓度 ,尽量 少加或不加氯化锌。 在 电镀 原 材 料 中 ,氯化 锌 的质 量还 存 在 较 多 的问 题 ,主要是生产商 没有把铜 、铅杂质 除掉 。所 以,在采
根据 上述故 障 ,对槽液进行处理。往槽 液里加入
2 g / L @ g 锌粉 ,搅拌0 5 h ,沉淀2 h 后过 滤至 清液。最 后 ,阴极挂 瓦楞 铁板 ,按0 . 1 — 0 2 A / d m 小 电流 电解
验 判断 ,应该是 受到铅 杂质 的污染。
电子 因得 不到锌离子而在镀件 上骤集 ,尤其是在 电流密
度较大 的边 角造成 镀层烧 焦。为防止烧焦 ,只好 降低 电
联想 到是加料 之后 出现 的问题 ,于是 问题聚焦 到 原材料 上。由于硼酸还是原 先使 用的,所 以应该不会
出现问题 ,而氯化锌和 氯化钾 是新进 的- - ̄ l : L 。为查 找 问题 出在 哪一种 原料上 ,随即取来 分析纯 的氯化锌和 氯化钾 ,平行做 两组对 比试验 ,分别按 氯化锌5 0 g / L , 氯化 钾2 2 0 g / L ,硼 酸3 0 g / L ,添 加剂 按 正常开 缸 量
低 电流密度 区发黑甚至经硝酸 出光后露 出底层金属 。 根据赫 尔槽 实验 ,取槽液2 5 0 mL ,给 电流0 . 3 A,通 电1 0 mi n ,水 洗 出光 吹干后 观察 试 片 ,试 片发 花且
1氯化钾镀锌钝化后发黑的原因分析
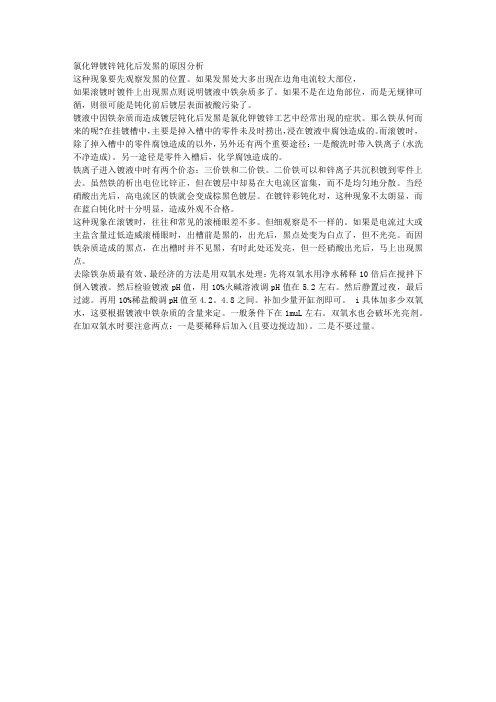
氯化钾镀锌钝化后发黑的原因分析这种现象要先观察发黑的位置。
如果发黑处大多出现在边角电流较大部位,如果滚镀时镀件上出现黑点则说明镀液中铁杂质多了。
如果不是在边角部位,而是无规律可循,则很可能是钝化前后镀层表面被酸污染了。
镀液中因铁杂质而造成镀层钝化后发黑是氯化钾镀锌工艺中经常出现的症状。
那么铁从何而来的呢?在挂镀槽中,主要是掉入槽中的零件未及时捞出,浸在镀液中腐蚀造成的。
而滚镀时,除了掉入槽中的零件腐蚀造成的以外,另外还有两个重要途径:一是酸洗时带入铁离子(水洗不净造成)。
另一途径是零件入槽后,化学腐蚀造成的。
铁离子进入镀液中时有两个价态:三价铁和二价铁。
二价铁可以和锌离子共沉积镀到零件上去。
虽然铁的析出电位比锌正,但在镀层中却易在大电流区富集,而不是均匀地分散。
当经硝酸出光后,高电流区的铁就会变成棕黑色镀层。
在镀锌彩钝化对,这种现象不太朗显,而在蓝白钝化时十分明显,造成外观不合格。
这种现象在滚镀时,往往和常见的滚桶眼差不多。
但细观察是不一样的。
如果是电流过大或主盐含量过低造威滚桶眼时,出槽前是黑的,出光后,黑点处变为白点了,但不光亮。
而因铁杂质造成的黑点,在出槽时并不见黑,有时此处还发亮,但一经硝酸出光后,马上出现黑点。
去除铁杂质最有效、最经济的方法是用双氧水处理:先将双氧水用净水稀释10倍后在搅拌下倒入镀液。
然后检验镀液pH值,用10%火碱溶液调pH值在5.2左右。
然后静置过夜,最后过滤。
再用10%稀盐酸调pH值至4.2。
4.8之间。
补加少量开缸剂即可。
i具体加多少双氧水,这要根据镀液中铁杂质的含量来定。
一般条件下在1muL左右。
双氧水也会破坏光亮剂。
在加双氧水时要注意两点:一是要稀释后加入(且要边搅边加)。
二是不要过量。
浅谈氯化锌的返点及变色

浅谈氯化物镀锌层返点及变色一、前言由于我国改革开放日益深入,各行各业蓬勃发展,同时带来了环境问题的严重挑战,尤其我们电镀行业更加面临着生产工艺日益月新的改革,才能紧跟时代发展的步伐,以前我们的工艺落后,污染严重,比如我们以前使用的氰化物镀锌,由高氰镀锌发展到中氰镀锌,后来由于光亮剂的研发成功的改进为低氰,微氰镀锌,对环境保护起到积极作用,但还不能满足当前适应我们环境保护的要求,但是我们的工艺中还存在着含氰物质,所以氯化物镀锌工艺越来越受到广大电镀界,环保界人士所重视,我国从70年代初发展到至今的氯化物镀锌已得到长足的发展,说明该工艺确有其优点,氯化物镀锌的电流效率高达(95%以上),槽压低,所以比氰化镀锌节约50%以上的电,同时适用各种高碳黑色金属基体的表面镀锌层。
生产效益也比氰化物镀锌高出30%-50%左右,但是由于氯化物镀锌的光亮剂的主要成分是载体表面活性剂去乳化光亮剂醛类,因表面活性剂对镀件有一定的附着力,水洗效果不十分好,同时氯化物镀锌对铁,铜,铅等杂质很敏感,所以镀锌件返点变色,也不足为奇了,那么我们怎样才能改变这个缺点呢?靠我们去改变操作工艺或使用原料上去想办法。
二、镀锌层返点变色产生的原因1.镀前处理不良,工件表面的油污清洗不干净,经酸洗后,水洗的难度加大基体表面形成花斑或条纹状,该表面镀层难以沉积或沉积镀层很薄,若工件表面的铁锈处理不完全,镀层只能在锈迹周围沉积,出现黑色斑点,或者如滚镀经过物理作用锈迹渐渐被摩擦被溶解,后期方有镀层沉积,该部位镀层沉积时间短,镀层很薄,光亮度差而出现白色斑点2.阴极电流密度大,阴极区PH值升高过快,镀层中有金属氢氧化物或碱式盐类附于镀层中,而出现斑点。
3.镀液中有机杂质的来源主要是添加剂分解产物和未清洗干净的油污长时间在镀液中积累会使镀层发雾。
4.光亮剂添加太多,会造成阴极无法消耗,形成光亮剂过剩夹入镀锌层,或附着在工件表面,清洗不干净,经钝化后产生酸性胶体状的表面活性剂。
氯化钾镀锌发雾的原因及对策
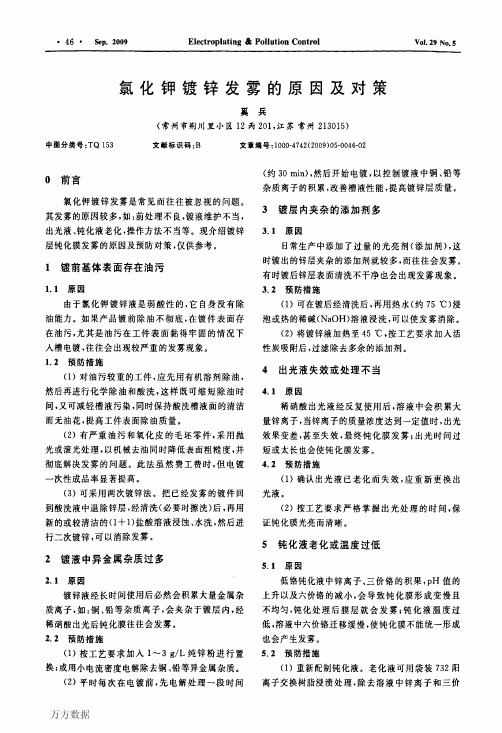
阳极易钝化时,部分呈不溶性阳极态,镀液中主 盐Cu2+的质量浓度下降。而补充硫酸铜,不但成本 比用阳极的高,且难溶解,容易引入杂质,是得不偿
失的。
2.1-2
阳极消耗后补换不及时
作为可溶性阳极,阳极总会不断消耗而变小、变 窄、变薄,表观面积越来越小,阳极电流密度越来越 大,越易钝化。应及时检查阳极,对板状阳极,面积 变小后应及时更换,换下来的小阳极可装于钛阳极 筐中继续使用,并不造成浪费。生产中最严重的是 阳极已溶解只剩下液面上的头子,还认为完好。顺 便提及,不少人问到为何镀锌、镍、铜的阳极溶解后 呈花瓶状,液位下腐蚀最快而成瓶颈状,甚至溶断。 这一现象是由氧差电池(一种宏电池现象)造成的 “水线下腐蚀”:液平面接触空气中的氧,水线下的金 属部分接触含氧较高的水或溶液,下部溶液含氧量 相对较低,上下之间形成氧差宏电池,水线下的部分 成为阳极,液位较下部分成为阴极,故水线下的部分 金属,因电化学腐蚀而加快腐蚀速率,最后呈瓶颈
造成阳极磷膜脱落并钝化。以为少挂阳极就可节省 阳极消耗,反而事与愿违。部分阳极钝化后,剩余未 钝化的阳极电流密度更大,钝化更快。升高槽电压 后,恶性循环,最终可能几乎全部钝化。 当采用板状阳极时,背面几乎不导电,阳极设置 时,板的间距不宜大于10 cm。采用钛阳极筐盛装 磷铜阳极球、块时,导电的比表面积大些,钛篮间距 也不宜大于20
氯化钾镀锌钝化附着力差的原因
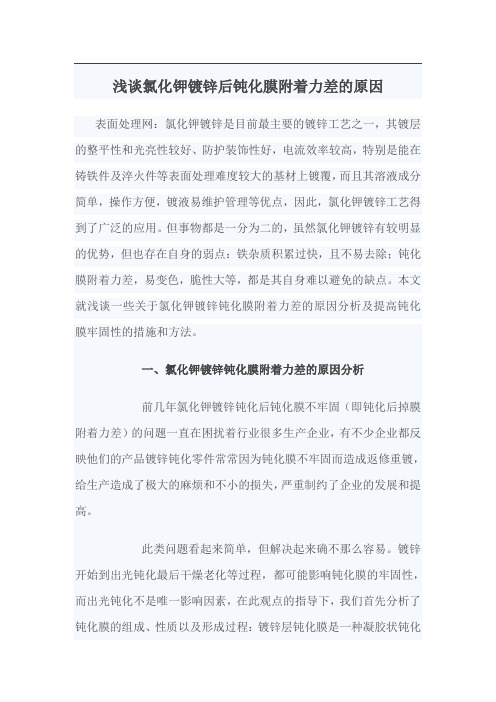
表面处理网:氯化钾镀锌是目前最主要的镀锌工艺之一,其镀层的整平性和光亮性较好、防护装饰性好,电流效率较高,特别是能在铸铁件及淬火件等表面处理难度较大的基材上镀覆,而且其溶液成分简单,操作方便,镀液易维护管理等优点,因此,氯化钾镀锌工艺得到了广泛的应用。
但事物都是一分为二的,虽然氯化钾镀锌有较明显的优势,但也存在自身的弱点:铁杂质积累过快,且不易去除;钝化膜附着力差,易变色,脆性大等,都是其自身难以避免的缺点。
本文就浅谈一些关于氯化钾镀锌钝化膜附着力差的原因分析及提高钝化膜牢固性的措施和方法。
一、氯化钾镀锌钝化膜附着力差的原因分析前几年氯化钾镀锌钝化后钝化膜不牢固(即钝化后掉膜附着力差)的问题一直在困扰着行业很多生产企业,有不少企业都反映他们的产品镀锌钝化零件常常因为钝化膜不牢固而造成返修重镀,给生产造成了极大的麻烦和不小的损失,严重制约了企业的发展和提高。
此类问题看起来简单,但解决起来确不那么容易。
镀锌开始到出光钝化最后干燥老化等过程,都可能影响钝化膜的牢固性,而出光钝化不是唯一影响因素,在此观点的指导下,我们首先分析了钝化膜的组成、性质以及形成过程:镀锌层钝化膜是一种凝胶状钝化膜,其主要成分是三价铬和六价铬的化合物、水、以及金属离子等组成。
其中水是以结晶水的形式存在的。
其膜层是在固液界面上通过各相化学反应过程经历反复的成膜与溶解、扩散的复杂过程所得到的化合物胶体膜。
钝化膜的附着力与形成钝化膜的界面的洁净度、膜层的干燥老化方法及膜层的厚薄有直接关系。
二、防止镀锌钝化膜附着力差的方法和措施1、控制镀锌后锌层表面有机吸附膜的量来增强钝化膜的附着力。
镀锌后锌层表面的洁净与否,对钝化膜的附着力起着决定性的作用,它是决定钝化膜牢固性的关键因素,如果锌层与膜层界面不洁净,牢固性就无从谈起。
在电镀过程中,镀层是在含有锌离子的电解液中在直流电场的作用下锌离子沉积得到镀锌层,在此过程中要使用大量的有机添加剂才能获得较理想的镀锌层,这些添加剂大部分都是不溶性的粘性的透明有机物,它们的主要作用是吸附在阴极表面,形成一个有机膜层来增大阴极极化,使锌离子透过此层膜沉积,使镀层结晶细致、光亮均匀。
镀锌彩色钝化膜脱落褪色的原因探讨及解决

镀锌彩色钝化膜脱落褪色的原因探讨及解决
赵复荣
【期刊名称】《电镀与涂饰》
【年(卷),期】2001(020)005
【摘要】分析了镀锌彩色钝化膜脱落褪色的原因并提出了解决方法.
【总页数】2页(P53-54)
【作者】赵复荣
【作者单位】阳泉电器厂有限责任公司技术科,
【正文语种】中文
【中图分类】TQ153.15;TQ153.6
【相关文献】
1.氯化钾镀锌钝化膜变色原因探讨及控制措施 [J], 梁远国
2.稀土元素对镀锌层三价铬彩色钝化膜耐蚀性的影响 [J], 刘艳;张建刚;冯立明
3.电镀锌三价铬彩色钝化膜封闭剂的制备 [J], 禚昌岩
4.上海容昆物资合作公司专营水叻[口架]和镀锌三价铬钝化剂新佳高级水溶性透明漆(浸、喷两用)三价铬彩色钝化已通过72h中性盐雾试验 [J],
5.影响镀锌层三价铬彩色钝化膜外观的因素 [J], 汤富民;杜强
因版权原因,仅展示原文概要,查看原文内容请购买。
镀锌层彩色钝化常见问题及对策

镀锌层彩色钝化常见问题及对策来源:文章发表时间:2008-10-28镀锌层在以铬酐、硫酸、硝酸等组成的溶液中进行化学处理,使其表面形成一层铬酸盐薄膜,这一过程简称钝化。
钝化膜具有下列功能:(1)提高了锌镀层的抗大气、二氧化碳、水蒸气腐蚀的作用;(2)改善外观色彩,有一定的装饰效果。
目前钝化多采用低铬钝化工艺,按工艺配方浓度只占原配方浓度的l/30~1/50,大大减轻了环境污染和原材料的消耗,但对熟练掌握技巧、维护溶液正常进行也提出了新的要求,操作稍有不慎极易出现差错,应予以高度重视。
1、钝化膜易脱落除了钝化溶液中硫酸浓度失调和镀件表面附有残留的添加剂未彻底剔除干净之外,操作不当也会造成钝化膜脱落,例如:(1)钝化后在未经干燥之前触碰物体;(2)钝化后未经吹、晾干之前直接进入烘箱烘烤;(3)在高湿度条件下未能及时晾干;(4)晾晒时镀件的下端及孔眼等处的积水未能及时除去(5)二次钝化件,即钝化后自认膜层色泽欠佳再经补钝化的零件发生脱膜;(6)经钝化并冲洗干净后,有时工件虽经晾干,但又受到挂具上流下的水所润湿而发生部分膜层脱落;(7)钝化溶液温度过高,钝化时间过长而引起的膜层过厚,影响到膜层的结合力。
对于氯化钾光亮镀锌件,若钝化之前未经预处理而脱膜,则必须先经预处理,这是因为氯化钾光亮镀锌件表面附有添加剂,若添加剂未能彻底清洗干净,钝化后必然会引起脱膜,为此,钝化前尚需在沸水中煮3~4min,经冷却后再钝化,这一脱膜问题就能得到解决。
为减少因脱膜而造成返修,在镀件钝化后尚未烘烤之前应做一次检查,当发现有脱膜的应当立即在稀盐酸中退除,用流动水冲洗后重新钝化,这样可以大大简化返修工序。
2、根据钝化溶液温度调节钝化时间溶液温度偏低时成膜速度缓慢,所获的膜层薄,光泽性差,有雾状,需要延长钝化时间,尤其是延长空气中的停留时间才能有所改善,但仍难免“地图”形的花纹出现。
溶液温度偏高时所获钝化膜虽较光亮,色彩自然,但钝化膜结合力差,要防止因钝化时间过长而引起膜层脱落。
氯化钾镀锌钝化膜变色原因探讨及控制措施
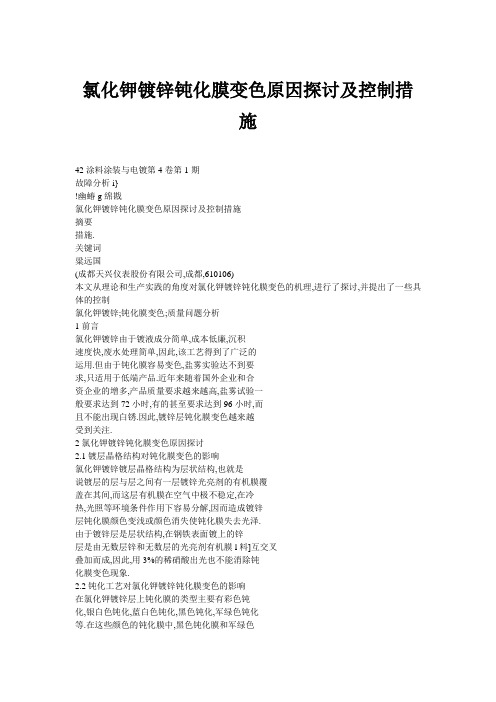
3氯化钾镀锌钝化膜变色的控制措施
笔者经过多年的研究和实践,认为以下一些方
法和措施,对降低氯化钾镀锌钝化膜变色,提高氯化
钾镀锌钝化膜耐腐蚀性能有帮助.
3.1用碱性溶液去除零件表面的光亮剂薄膜
零件从氯化钾镀锌槽中取出后,先经过一道水
洗后浸入碱性溶液中去除表面多余的光亮剂薄膜,
然后再进行其它工序.其工艺流程为:
锌溶液
从氯化钾镀锌溶液的性质和镀层结构分析可
知:要完全去除镀锌层中夹杂的光亮剂薄膜几乎是
不可能的,但是将镀层中的有机物控制在有限的范
围内是完全能够办到的.我们可以通过以下一些措
施来解决问题:
(1)添加剂应采用”少加勤加”的办法.同时,避
免在镀槽工作期间加入.加光亮剂最好是在每班下
班后添加.添加时,应将光亮剂用镀液稀释后加入,
氯化钾镀锌钝化膜变色原因探讨及控制措施
42涂料涂装与电镀第4卷第1期
故障分析i}
!幽蝽g绵戡
氯化钾镀锌钝化膜变色原因成都天兴仪表股份有限公司,成都,610106)
本文从理论和生产实践的角度对氯化钾镀锌钝化膜变色的机理,进行了探讨,并提出了一些具体的控制
氯化钾镀锌;钝化膜变色;质量问题分析
理技术工作,发表论文十余篇.
3
温
53c:;室
2OO6年2月粱远国:氯化钾镀锌钝化膜变色原因探讨及控制措施43
温度室温
时间,S10—20s
先在低铬彩色钝化液中钝化,不经过老化处理,
直接浸入碳酸钡漂白溶液中除去彩色膜,从而可以
形成银白色钝化膜,然后在含O.3%铬酐的热水
(80Y:一9oc【=)中封闭处理.最后放入温度为6oc【=一
氯化钾镀锌一水洗一碱性溶液除膜一水洗—钝
钾盐镀锌故障及其处理方法:低电流密度区镀层灰暗、无光泽

钾盐镀锌故障及其处理方法:
低电流密度区镀层灰暗、无光泽可能原因原因分析及处理方法
(1)镀液温度过
高
详见故障现象l(2)的原因分析及处理方法
(2)添加剂含量
低
详见故障现象l(3)的原因分析及处理方法
(3)氯化锌含量
过高
详见故障现象l(1)的原因分析及处理方法
(4)pH值过高详见故障现象4(2)的原因分析及处理方法
(5)氯化钾含
量过低
详见故障现象3(3)的原因分析及处理方法
(6)阴极电流密度过小
若Dk过小,零件低电流密度区的电流更小,在规定的电镀时间内,该处镀层薄,甚至无镀层沉淀,而出现镀层发暗、无光泽甚至漏镀现象
处理方法:准确测量工件的受镀面积,合理设定电流值
(7)铜杂质过多详见故障现象3(5)的原因分析及处理方法
(8)铅杂质过多
铅杂质含量在0.005g/L时,钝化膜光泽差,其含量大于0.01g/L以上时,零件的低电流密度区镀层不完整,甚至无锌层沉积,随着杂质含量的增多,锌很难在阴极上沉积,严重时,整个阴极上得不到镀层,即使用大电流冲击镀,所得的镀层在3%硝酸中出光,出现黑乎乎的花斑。
铅杂质的来源主要是锌阳极不纯和氯化锌中杂质含量高
处理方法:同故障现象3(5)的处理方法
附:铅杂质检验方法取少量的镀液,用活化的锌片,放在镀液中浸2~3min后取出观察,若锌片表面上有置换铅的颜色,证明原镀液中铅杂质较多,需要进行处理。
氯化钾镀锌故障分析
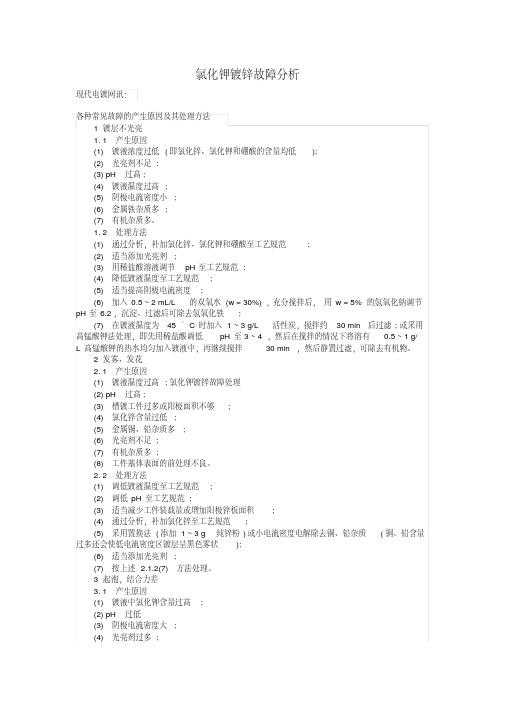
氯化钾镀锌故障分析现代电镀网讯:各种常见故障的产生原因及其处理方法1 镀层不光亮1. 1 产生原因(1) 镀液浓度过低(即氯化锌、氯化钾和硼酸的含量均低);(2) 光亮剂不足;(3) pH 过高;(4) 镀液温度过高;(5) 阴极电流密度小;(6) 金属铁杂质多;(7) 有机杂质多。
1. 2 处理方法(1) 通过分析,补加氯化锌、氯化钾和硼酸至工艺规范;(2) 适当添加光亮剂;(3) 用稀盐酸溶液调节pH 至工艺规范;(4) 降低镀液温度至工艺规范;(5) 适当提高阴极电流密度;(6) 加入0.5 ~ 2 mL/L 的双氧水(w = 30%),充分搅拌后,用w = 5% 的氢氧化钠调节pH 至6.2,沉淀、过滤后可除去氢氧化铁;(7) 在镀液温度为45 °C 时加入 1 ~ 3 g/L 活性炭,搅拌约30 min 后过滤;或采用高锰酸钾法处理,即先用稀盐酸调低pH 至3 ~ 4,然后在搅拌的情况下将溶有0.5 ~ 1 g/ L 高锰酸钾的热水均匀加入镀液中,再继续搅拌30 min ,然后静置过滤,可除去有机物。
2 发雾、发花2. 1 产生原因(1) 镀液温度过高;氯化钾镀锌故障处理(2) pH 过高;(3) 槽镀工件过多或阳极面积不够;(4) 氯化锌含量过低;(5) 金属铜、铅杂质多;(6) 光亮剂不足;(7) 有机杂质多;(8) 工件基体表面的前处理不良。
2. 2 处理方法(1) 调低镀液温度至工艺规范;(2) 调低pH 至工艺规范;(3) 适当减少工件装载量或增加阳极锌板面积;(4) 通过分析,补加氯化锌至工艺规范;(5) 采用置换法(添加 1 ~ 3 g 纯锌粉)或小电流密度电解除去铜、铅杂质(铜、铅含量过多还会使低电流密度区镀层呈黑色雾状);(6) 适当添加光亮剂;(7) 按上述 2.1.2(7)方法处理。
3 起泡,结合力差3. 1 产生原因(1) 镀液中氯化钾含量过高;(2) pH 过低(3) 阴极电流密度大;(4) 光亮剂过多;(5) 金属铁杂质多;(6) 工件基体含有硅。
- 1、下载文档前请自行甄别文档内容的完整性,平台不提供额外的编辑、内容补充、找答案等附加服务。
- 2、"仅部分预览"的文档,不可在线预览部分如存在完整性等问题,可反馈申请退款(可完整预览的文档不适用该条件!)。
- 3、如文档侵犯您的权益,请联系客服反馈,我们会尽快为您处理(人工客服工作时间:9:00-18:30)。
2氯化钾镀锌钝化膜变色原因探讨
2.1镀层晶格结构对钝化膜变色的影响
氯化钾镀锌镀层晶格结构为层状结构,也就是
说镀层的层与层之间有一层镀锌光亮剂的有机膜覆
盖在其间,而这层有机膜在空气中极不稳定,在冷
热,光照等环境条件作用下容易分解,因而造成镀锌
层钝化膜颜色变浅或颜色消失使钝化膜失去光泽.
由于镀锌层是层状结构,在钢铁表面镀上的锌
质量问题分析前言氯化钾镀锌由于镀液成分简单成本低廉沉积速度快废水处理简单因此该工艺得到了广泛的用?但由于钝化膜容易变色盐雾实验达不到要求只适用于低端产品?近年来随着国外企业和合业的增多产品质量要求越来越高盐雾试验一般要求达到72小时有的甚至要求达到96小时而不能出现白锈?因此镀锌层钝化膜变色越来越受到关注?氯化钾镀锌钝化膜变色原因探讨21镀层晶格结构对钝化膜变色的影响氯化钾镀锌镀层晶格结构为层状结构也就是说镀层的层与层之间有一层镀锌光亮剂的有机膜覆热光照等环境条件作用下容易分解因而造成镀锌层钝化膜颜色变浅或颜色消失使钝化膜失去光泽由于镀锌层是层状结构在钢铁表面镀上的锌料互交叉叠加而成因此用3的稀硝酸出光也不能消除钝化膜变色现象?22钝化工艺对氯化钾镀锌钝化膜变色的影响在氯化钾镀锌层上钝化膜的类型主要有彩色钝化银白色钝化蓝白色钝化黑色钝化军绿色钝化等?在这些颜色的钝化膜中黑色钝化膜和军绿色钝化膜的结合力好抗变色能力强中性盐雾试验能够达到96小时以上彩色钝化银白色钝化蓝白色钝化的抗变色能力较差尤其是在高温高湿环境下大量的彩色钝化层颜色消失盐雾试验很难达到72小时?白色钝化膜易失去光泽盐雾试验很难达到铝小时?从钝化工艺看彩色钝化目前各个电镀厂遍使用的是低铬钝化白色钝化使用的是碳酸钡漂白工艺?其工艺参数如下
成都前锋集团公司召开迎春学术技术交流会,成都
市环保局污染管理处和稽查支队领导光临会议.
140余名代表到会.
会议由协会常务副理事长龚承耀主持,协会理
事长费竹龄作协作2005年工作总结和2006年工作
安排的报告.
经协会理事会研究决定增补成都飞亚粉末涂料
涂装实业有限公司,四川宸宇涂装工程有限公司为
常务理事单位,成都航空仪表有限公司为理事单位,
于8oc【=时会造成钝化膜开裂.
2.4包装储存条件对钝化膜变色的影响
氯化钾镀锌钝化膜层中有很多孔,在这些微孔
中和钝化膜中含有酸碱性水分.这样的产品如果用
塑料袋或塑料纸密封包装,然后在库房中存放较长
时间,尤其是在夏天,这些含有酸碱的水分就会变成
蒸汽而不能散发,使零件处于一种类似于盐雾试验
的环境中,从而造成大量产品的镀锌钝化膜层变色
锌溶液
从氯化钾镀锌溶液的性质和镀层结构分析可
知:要完全去除镀锌层中夹杂的光亮剂薄膜几乎是
不可能的,但是将镀层中的有机物控制在有限的范
围内是完全能够办到的.我们可以通过以下一些措
施来解决问题:
(1)添加剂应采用”少加勤加”的办法.同时,避
免在镀槽工作期间加入.加光亮剂最好是在每班下
班后添加.添加时,应将光亮剂用镀液稀释后加入,
增补袁诗璞为常务理事.
东道主前锋集团公司副总经理林光代表前锋集
团对与会代表表示欢迎,对成都表面工程行业协会
一
年来的工作给予高度评价,并祝协会在新的一年
取得更大成绩.
黄渭澄,袁诗璞,曾祥德分别就电镀铜,锌,锌铁
合金及环保要求等进行了技术交流.
成都航空仪表公司热表厂汪炳康,成都天鹅电
镀厂何古兴分别介绍了企业管理的经验.
或腐蚀.
3氯化钾镀锌钝化膜变色的控制措施
笔者经过多年的研究和实践,认为以下一些方
法和措施,对降低氯化钾镀锌钝化膜变色,提高氯化
钾镀锌钝化膜耐腐蚀性能有帮助.
3.1用碱性溶液去除零件表面的光亮剂薄膜
零件从氯化钾镀锌槽中取出后,先经过一道水
洗后浸入碱性溶液中去除表面多余的光亮剂薄膜,
然后再进行其它工序.其工艺流程为:
质,未被老化的钝化膜较为疏松.因此,钝化膜必须
老化,老化的温度与钝化膜的质量关系密切.一般
温度范围是6o℃一8o℃,温度过低老化效果较差,
温度过高会造成钝化膜开裂,抗腐蚀性能降低.
3.5改善包装储存条件
镀锌件的包装应采用透气良好的有孔塑料箱或
者采用纸盒,并要储存在通风良好的干燥环境中.
在酸性环境中不适于储存,否则钝化膜很快会失去
会上宣读了国家发改委2005年柏号令,调整
国家对氰化电镀的政策,文件规定:”氰化电镀金,
银,铜基合金及预镀铜打底工艺,暂缓淘汰.”
会后代表们还进行了广泛的交流和联谊活动,
共祝新年J陕乐,新年更兴旺.
本刊代表出席了会议.
(晓禾)
结合力差,甚至用手即可擦掉,从而严重影响电镀锌
的防腐性能和外观.
钝化膜是否老化或老化温度是否合适,都对氯
化钾镀锌钝化膜的耐蚀性能和抗变色性能有影响.
大部分的电镀厂家都没有进行老化处理,而是用离
心机去除零件上的水分,或者在太阳下晒干,钝化膜
没有老化或者老化不好.适合老化的温度范围为
6oc【=一8oc【=,低于6oc【=时,钝化膜老化效果不好,高
层是由无数层锌和无数层的光亮剂有机膜l料]互交叉
叠加而成,因此,用3%的稀硝酸出光也不能消除钝
化膜变色现象.
2.2钝化工艺对氯化钾镀锌钝化膜变色的影响
在氯化钾镀锌层上钝化膜的类型主要有彩色钝
化,银白色钝化,蓝白色钝化,黑色钝化,军绿色钝化
等.在这些颜色的钝化膜中,黑色钝化膜和军绿色
钝化膜的结合力好,抗变色能力强,中性盐雾试验能
Yuanguo
(ChengdutianxinginstrmnentandmeterCo.,Ltd,Chengdu,610106)
AilsUm~ThemechanismofchromatingfilmchangecoloronKC1zincplatingarediscussedfromthetheoryandprac-
氯化钾镀锌一水洗一碱性溶液除膜一水洗—钝
化一水洗一甩干一老化.
碱性溶液的配方为:
NaOH,g/L80—120
ZnO.g/L8一l2
温度室温
时间,min3—5
经过该方法处理过的镀锌件,其钝化膜的结合
能力得到显着改善.中性盐雾试验能够增长3—8
小时(与同批同槽同一产品比较).
3.2科学合理地添加光亮剂.定期用活性炭处理镀
3.3采用逆流漂洗方法,减少镀后锌层表面上覆盖
的光亮剂薄膜
涂料涂装与电镀第4卷第1期
逆流漂洗是一种节约用水,并且能够随时保持
最后一道水清洁的好方法,采用该方法清洗的镀锌
件,其表面上光亮剂的残留物会大大降低,从而有效
地增强镀锌钝化膜的抗变色能力.
3.4严格控制老化温度
镀锌层钝化膜含水分比较多,而且含有酸碱物
(1)低铬彩色钝化:[艺:
铬酐(C103),g/L
硝酸(刖o3),mL/I
硫酸(H2SO4),mI/L
pH值
温度时间Βιβλιοθήκη s(2)碳酸钡漂白工艺:铬酐(C),g/L
碳酸钡(BaCO3),g/L
3—7
20—30
0.5一l
收稿日期:2005—12_lO
作者简介:梁远t~(1962一),男,重庆垫江人,大学蕾斗学历,工程师,成都机械工程学会电镀涂装分会理事.长期从事表面处
1前言
氯化钾镀锌由于镀液成分简单,成本低廉,沉积
速度快,废水处理简单,因此,该工艺得到了广泛的
运用.但由于钝化膜容易变色,盐雾实验达不到要
求,只适用于低端产品.近年来随着国外企业和合
资企业的增多,产品质量要求越来越高,盐雾试验一
般要求达到72小时,有的甚至要求达到96小时,而
且不能出现白锈.因此,镀锌层钝化膜变色越来越
rice.ThecontrolmethodsRredescribedinthepaper.
KeywordsKCIzincplating;changecolorofchromatingfilm;amalysisaboutqualityproblem
成都表面工程行业协会召开迎春学术技术交流会
成都表面工程行业协会于2OO6年1月10日在
对槽液的处理间隔时间都较长,而且处理方法简单,
造成有机物的分解产物聚集在镀液中,使电镀层中
夹杂的有机物就大量存在,从而造成电镀锌层变色
严重.
目前大部分电镀厂家为了减少污染物的排放.
想方设法控制用水量,这样造成电镀锌后的清洗水
中聚集了大量的有机物,而使镀锌层表面上有较多
有机物清洗不彻底就进入钝化槽钝化.致使钝化膜
并搅拌通电处理,让添加的光亮剂不被分解而均匀
地分散在镀液中,从而减少小分子有机物的吸附.
(2)应定期用活性炭处理镀液中被分解的小分
子有机物.活性炭的加入量为4g/L一6g/L.一般
应一个月处理一次,有条件的厂家最好配备连续过
滤机,随时保持槽液处于干净透明状态,这样生产出
来的产品质量稳定,抗变色能力好.
理技术工作,发表论文十余篇.
3
温
53c:;室
2OO6年2月粱远国:氯化钾镀锌钝化膜变色原因探讨及控制措施43
温度室温
时间,S10—20s
先在低铬彩色钝化液中钝化,不经过老化处理,
直接浸入碳酸钡漂白溶液中除去彩色膜,从而可以
形成银白色钝化膜,然后在含O.3%铬酐的热水
(80Y:一9oc【=)中封闭处理.最后放入温度为6oc【=一
够达到96小时以上.彩色钝化,银白色钝化,蓝白
色钝化的抗变色能力较差,尤其是在高温高湿环境
下,大量的彩色钝化层颜色消失,盐雾试验很难达到
72小时.白色钝化膜易失去光泽,盐雾试验很难达
到铝小时.
从钝化工艺看,彩色钝化目前各个电镀厂家普