生产过程预防错混料SOP
错混料管理规范

编号:QP-SP08.01-012
版本/版次:C.0
体系文件
错混料管理规范
生效日期:2018.12.3
1.适用范围
适用于公司范围内所有与原物料,半成品,成品所接触到的部门,以及我司供应商与外发商,提前识别错混料风险并管控好风险。
2. 术语
错混料:原料物,半成品,成品中用错料或混料的现象统称为错混料。
2,每起不符合项,责任班组长负激励5分,责任主管负激励10分;
3,总分100分,月度错混料考d核得分≥90分,团队正激励30分
错混料考核连带3级,总监级(含)以上人员纳入年度绩效考核
2
内部错混料:0起/月
3
供应商来料错混料:0起/月
4
错混料稽查不符合项:5起/月
E) OQC检验时需仔细核对客户签样样品,如没有客户签样样品时,OQC可拒绝做出货检查,所有产品未经OQC检查合格,均不得出货。
标签管理
包装管理
A)包装车间明确划分与标示待包装区,包装区,待检区,合格待入库区等区域,并进行管理。
B) 同一时间只能允许一种物料进入包装区作业,最小包装标签需在线粘贴。
C)装箱完后需及时封箱,并称重管理。
治具模具设有专人管理,并做有<模治具一览表>,记录有款号,机型,名称及数量,遇到共用款型号时,作好明细登记及标识。
在治具/模具时,使用单位需填写领用单,包含款号,机型,名称,借作件数等。
4.4.样品生产时错混料管理
业务部接新产品(以从前未生产过)或客户产品变更消息时及时转交工程技术中心,工程技术中心依据业务提供的相关资料作成BOM,采购依据BOM进行采购,物料回来经品管验收合格后进行入库,仓库通知生产人员领料生产样品,生产人员与仓库人员在领料与发料时应核对原材料厂家型号,批次号,标签标识,数量/重量等内容,经双方仔细核对无误后方可在<发料单>上签名,生产部将领回的物料分类放置并标识,依据客户要求制作业
注塑预防错混料管理规范[模板]
![注塑预防错混料管理规范[模板]](https://img.taocdn.com/s3/m/908139cc5901020206409c35.png)
1. 目的为了预防产品错、混料现象发生,制订规范2. 概述本规范描述了排产、区域划分、转产(清线)、包装、标签、尾数、运输搬运等管理要求。
3. 术语4. 内容4.1权责:4.1.1、作业员:严格按照SOP包装工艺要求对产品进行点数包装作业。
4.1.2、生产组长:负责对作业员点数包装作业的监督、作业指导及落实相关规定。
4.1.3、品检员:对打包的产品进行数量、包装、现品票的核对。
4.1.4、领班:严格按排产计划对转产(清线)、尾数按相关规定落实、并监督执行。
4.1.5、物料组长:按要求对物料区域划分并标识。
4.2转产(清线)管理4.2.1、排产前计划要确认相似产品不能安排在相邻两台机生产,避免产品混淆。
4.2.2、按排产计划提前准备好模具、物料等相关物品。
4.2.3、生产前确认所领物料产品型号、版本是否与生产计划一致。
4.2.4、机台转产时必须将上一个型号产品、首件、不良品、全部清理入库,相关的资料存档。
4.2.5、转产机型做首件时领班必须确认机型、版本是否与生产计划一致。
4.2.6、作业员必须对产品型号、版本了解,经过培训后作业员方可上岗作业。
4.2.7、生产或加工时不可堆积产品。
4.3包装管理4.3.1、点数时一定确认产品数量,不可少放多放,实物必须与SOP要求一致。
4.3.2、吸塑盒及外包箱严格按SOP要求执行,脏、损坏、不符合要求的包材不可以使用。
4.3.3、吸塑盒叠放时必须按要求错位叠放,避免压伤产品。
4.3.4、如打包时发现混料、混版现象,立即对之前生产的产品全部重新全检,并通知检验员注意。
4.3.5、回收包材必须清理完外箱标签、有损坏的不可进入车间。
在使用回收包材前作业员要仔细确认好外箱标签有无撕掉。
4.3.6、对产品型号、版本、数量确认OK后及时装箱并封箱再贴现品票。
4.3.7、尾数箱需贴尾数标签。
4.3.8、同一时间只能允许同一种物料(产品)在包装区作业。
4.4标签管理4.4.1、AB班各组长负责打印现品票(由公司K3系统导出,具体格式要求按不同的客户指定格式、客户格式较特殊时,由专案QE与我司网管协商制作);4.4.2、按每日计划单上的制令单号由K3系统导出现品票,按计划数量打印现品票张数(不可多打)。
如何避免混料(元器件案例)
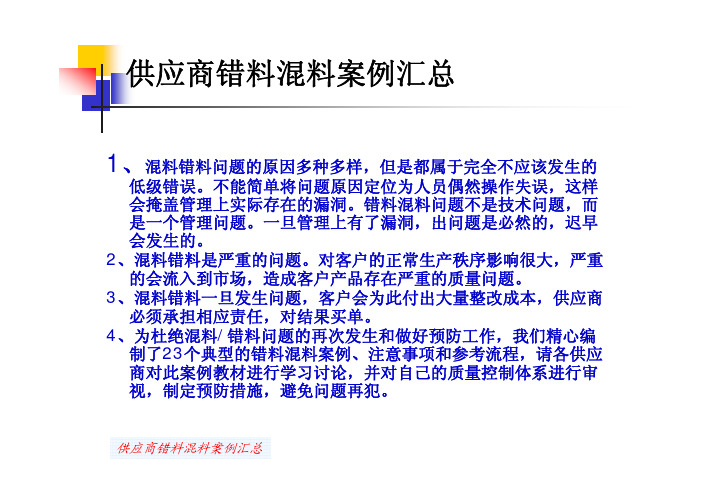
供应商错料混料案例汇总1、混料错料问题的原因多种多样,但是都属于完全不应该发生的低级错误。
不能简单将问题原因定位为人员偶然操作失误,这样 会掩盖管理上实际存在的漏洞。
错料混料问题不是技术问题,而 是一个管理问题。
一旦管理上有了漏洞,出问题是必然的,迟早 会发生的。
2、混料错料是严重的问题。
对客户的正常生产秩序影响很大,严重 的会流入到市场,造成客户产品存在严重的质量问题。
3、混料错料一旦发生问题,客户会为此付出大量整改成本,供应商 必须承担相应责任,对结果买单。
4、为杜绝混料/错料问题的再次发生和做好预防工作,我们精心编 制了23个典型的错料混料案例、注意事项和参考流程,请各供应 商对此案例教材进行学习讨论,并对自己的质量控制体系进行审 视,制定预防措施,避免问题再犯。
供应商错料混料案例汇总案例1 稳压管来料混料,导致近5000块单板返工和召回的恶 性事故 !【问题描述】同系列器件的型号十分接近(仅电压数值差别)。
此次发货同时发两个物料,刚 好数量相同。
备货人员同时打印两个物料的标签,在贴客户标签时工作疏忽,将型号为 ABC12D30E与ABC12D43E两箱物料的客户标签互相贴错(见下图);而OQC人员检验时工 作敷衍,只检查了外盒正面所贴的客户标签,而没有对照检查侧面的工厂标签(正面客户 标签上的厂家型号与侧面厂家标签不符时就可以检验出来),造成错料。
【原因分析】两个批次同时作业,两箱物料的标签互相贴错。
【影响度】导致客户近5000块单板返工及召回的恶性事故 !此标签 错误此标签 正确供应商错料混料案例汇总案例2 电位器物料与标签不符,造成单板批量返工【问题描述】生产线发现某编码电位器A丝印异常,而料盘标签信息正确。
经测量编带内未启 用电位器阻值,发现实际阻值与标签型号不符,确认为来料错误(标签与实物不符)。
【影响度】立即清查该编码所有库存,发现一共3盘错料。
查该编码发料记录,已有两任务令 使用该错料,涉及200多块单板,500多PCS电位器。
不可混料承诺书

不可混料承诺书我们公司承诺,在我们生产产品时,绝不混入任何低质量的原材料或掺杂有害物质。
我们严格控制每个生产线的流程,以确保我们的每个产品能够符合指定的质量标准。
我们保证所使用的每种原材料都是最优质的,并且从可靠的供应商处采购而来。
在制造过程中,我们严格执行标准操作程序(SOP)和制造指南,每个步骤都根据事先制定的技术规范和质量标准进行操作。
产品出厂前,必须经过严格的质量检测和测试,确保每个产品都符合或超过了行业标准。
我们的不可混料承诺书涵盖了以下内容:原材料的选择和采购我们承诺,原材料的选择和采购将按照以下方针进行:•每个供应商都必须通过仔细的审核程序,确保其提供的原材料符合我们的质量标准。
•我们只使用被认可的供应商提供的原材料,以确保其符合我们的质量要求。
•我们对每一批原材料进行检查,并严格执行相关的质量控制规范和标准。
制造过程的控制我们承诺,在制造过程中,将采取以下措施:•我们严格执行标准操作程序 (SOP),确保整个过程的可重复性并符合质量标准。
•我们致力于不断提高产品的质量,通过使用最新技术、引入新的设备,以及培训员工加强他们的技能和专业知识,来优化制造过程。
•我们将实施全面的质量管理体系 (QMS),以确保每一步都符合我们的质量标准。
产品检测和测试我们承诺,我们将对每个产品进行严格的检测和测试,包括以下内容:•我们将对每个产品进行外观检查、尺寸测试以及功能测试。
•我们将对一定比例的产品进行随机抽检,以确保我们生产的每个产品都符合质量标准。
•我们致力于持续改进和创新,以提高产品的质量和性能。
质量控制我们承诺,我们将实施全面的质量控制措施,包括以下方面:•我们将贯彻执行ISO9001质量管理体系标准,以确保我们生产的每个产品都符合行业标准。
•我们将实施全面的技术变更管理,以确保任何变更都会经过仔细审核并获得批准。
•我们将对整个生产过程进行全面的质量控制,包括原材料选择与采购、制造过程、产品检测和测试,以确保每个产品符合或超过我们承诺的质量标准。
生产车间混料管理流程

生产车间混料管理流程1. 原料准备- 根据生产计划和配方要求,准备所需的原料及其他辅料。
- 检查原料的质量、数量和保质期,确保符合要求。
- 将原料分类存放在指定区域,防止混淆和污染。
2. 设备检查- 检查混料设备的运行状态,确保设备清洁、无故障。
- 对混料设备进行预热或冷却,达到工作温度。
- 检查混料容器、搅拌器、计量装置等配套设备。
3. 配料和预混- 根据配方要求,准确称量各种原料。
- 将称量好的原料按照顺序加入混料设备。
- 对部分原料进行预混,确保均匀分散。
4. 主混合- 启动混料设备,按照规定的程序进行混合。
- 控制混合时间、温度和搅拌速度,确保混合均匀。
- 根据需要,在混合过程中进行取样,检查混合质量。
5. 后处理- 将混合好的料渣卸出,并进行包装或转运。
- 对混料设备进行清洁,准备下一批次的生产。
- 将废弃料和清理残留物等妥善处理。
6. 质量检验- 从混合料中抽取样品,进行理化检测和性能测试。
- 检查混合料的颜色、气味、粘度等指标是否符合要求。
- 对不合格产品采取隔离、返工或报废等措施。
7. 记录和跟踪- 填写混料生产记录,详细记录每个工序的参数和操作情况。
- 建立混合料的批次跟踪系统,确保产品可追溯性。
- 对生产过程中遇到的问题和异常情况进行分析和改进。
以上是生产车间混料管理的基本流程,具体操作细节需根据实际情况进行调整和完善。
良好的混料管理有助于确保产品质量的稳定性和一致性,提高生产效率,并满足相关法规和质量体系的要求。
生物公司防跑料、串料管理规定模版
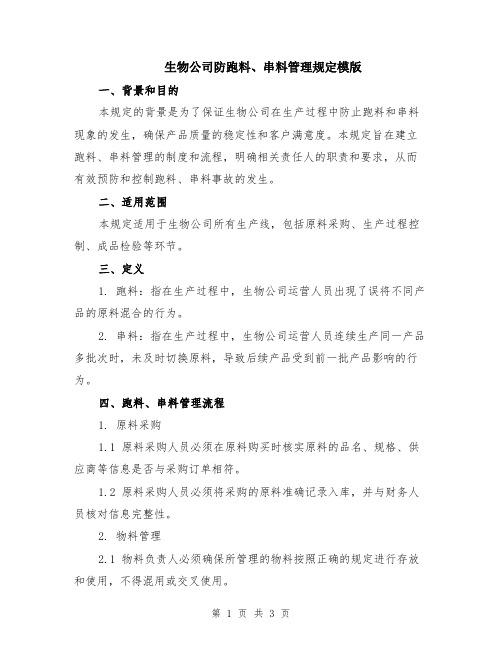
生物公司防跑料、串料管理规定模版一、背景和目的本规定的背景是为了保证生物公司在生产过程中防止跑料和串料现象的发生,确保产品质量的稳定性和客户满意度。
本规定旨在建立跑料、串料管理的制度和流程,明确相关责任人的职责和要求,从而有效预防和控制跑料、串料事故的发生。
二、适用范围本规定适用于生物公司所有生产线,包括原料采购、生产过程控制、成品检验等环节。
三、定义1. 跑料:指在生产过程中,生物公司运营人员出现了误将不同产品的原料混合的行为。
2. 串料:指在生产过程中,生物公司运营人员连续生产同一产品多批次时,未及时切换原料,导致后续产品受到前一批产品影响的行为。
四、跑料、串料管理流程1. 原料采购1.1 原料采购人员必须在原料购买时核实原料的品名、规格、供应商等信息是否与采购订单相符。
1.2 原料采购人员必须将采购的原料准确记录入库,并与财务人员核对信息完整性。
2. 物料管理2.1 物料负责人必须确保所管理的物料按照正确的规定进行存放和使用,不得混用或交叉使用。
2.2 物料负责人必须定期检查存放的物料,确保原料存放的整齐和标识的清晰可辨。
2.3 物料负责人必须制定严格的物料投放计划和标准,确保在生产过程中准确投料。
3. 生产过程控制3.1 操作人员必须确保在操作过程中按照正确的生产指令进行操作,不得随意更换或跳过工序。
3.2 操作人员必须严格遵守产品生产批次的切换规定,确保原料的切换和清洗工作有效完成,避免跑料、串料现象的产生。
3.3 操作人员必须及时记录生产信息和操作记录,确保生产过程的可追溯性。
4. 成品检验4.1 成品检验人员必须在每批次成品交付前对产品进行检验,确保产品质量的合格率。
4.2 成品检验人员必须制定严格的检验标准和程序,确保跑料、串料等问题的及时发现和处理。
五、责任人及职责1. 原料采购人员:负责核实原料信息并准确记录入库。
2. 物料负责人:负责物料管理和存放,确保物料的整齐和标识的清晰可辨。
PFEMA(错、漏、混)
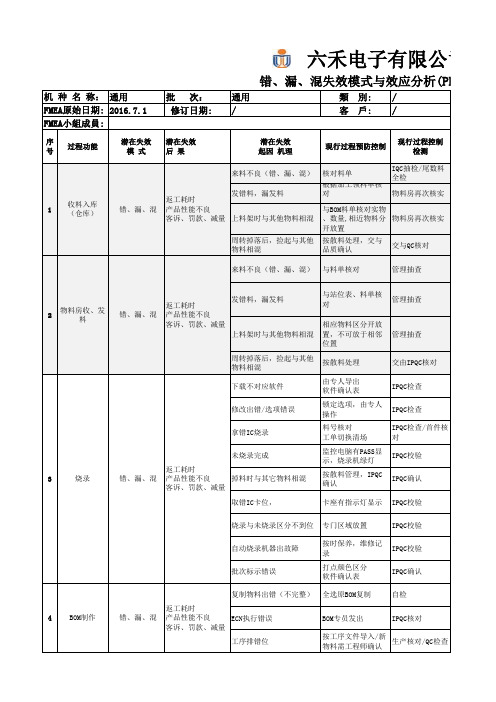
烧错KY
错、漏、混
返工耗时
KY条码漏贴,掉落
产品性能不良
客诉、罚款、减量 送修时混板
按批次下发KY软件/ 条码
IPQC首件
按产品数量领用KY 条码
QA抽检
产品隔离,标示,记 录
QA核查
漏打胶、打错位置
按SOP作业
QA核查
漏贴EVA泡棉及双面胶 包装方式及包材出错 少板
按SOP作业
IPQC检查/首件
按BOM装载/反馈客 户
按SOP作业/目检
IPQC对料 首件,目检
错、漏、混
返工耗时
插件过程中掉板导致掉件
产品性能不良
压条碰撞导致掉件/漏件
客诉、罚款、减量
撞件导致漏件
拉头重投,目检 轻拿轻放 按标准文件作业
目检/IPQC抽检 目检 目检
漏剪脚
1.按SOP作业 2.目检检查
IPQC抽检
外观维修时补错料
按BOM、位置找料 QC检查
卡座有指示灯显示 IPQC校验
4 BOM制作
烧录与未烧录区分不到位 专门区域放置
IPQC校验
自动烧录机器出故障 批次标示错误
按时保养,维修记 录
打点颜色区分 软件确认表
IPQC校验 IPQC确认
复制物料出错(不完整) 全选原BOM复制
自检
返工耗时
错、漏、混 产品性能不良
ECN执行错误
客诉、罚款、减量
由专人导出 软件确认表
锁定选项,由专人 操作
IPQC检查 IPQC检查
拿错IC烧录
料号核对 工单切换清场
IPQC检查/首件核 对
错、漏、混
未烧录完成
返工耗时
产品性能不良
车间防混料流程

车间防混料流程
车间防混料流程主要包括:
1. 物料标识清晰:所有原材料、半成品、成品均需明确标识,包括名称、批次、规格等信息。
2. 分区储存管理:根据产品类别和生产批次设立专用区域进行存储,并确保物料与非本批次产品物理隔离。
3. 先进先出原则:执行物料的先进先出(FIFO)原则,确保旧批次物料在新批次之前使用完毕。
4. 领料核对制度:生产班组领料时需经过严格核对,确认无误后方可领取并投入生产。
5. 过程监控与记录:实施生产过程中的实时监控,确保各环节按规程操作,并详细记录物料流动信息。
6. 设备清理验证:更换批次或产品类型前,必须彻底清洁生产设备,防止残留物造成混料。
预防混料管理办法
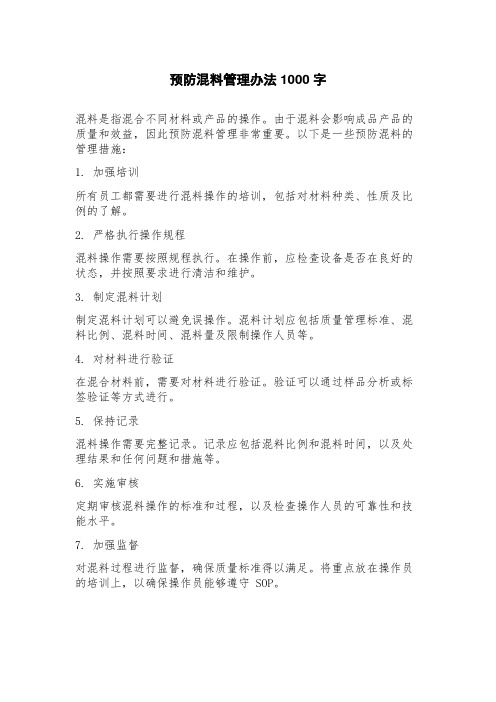
预防混料管理办法1000字
混料是指混合不同材料或产品的操作。
由于混料会影响成品产品的质量和效益,因此预防混料管理非常重要。
以下是一些预防混料的管理措施:
1. 加强培训
所有员工都需要进行混料操作的培训,包括对材料种类、性质及比例的了解。
2. 严格执行操作规程
混料操作需要按照规程执行。
在操作前,应检查设备是否在良好的状态,并按照要求进行清洁和维护。
3. 制定混料计划
制定混料计划可以避免误操作。
混料计划应包括质量管理标准、混料比例、混料时间、混料量及限制操作人员等。
4. 对材料进行验证
在混合材料前,需要对材料进行验证。
验证可以通过样品分析或标签验证等方式进行。
5. 保持记录
混料操作需要完整记录。
记录应包括混料比例和混料时间,以及处理结果和任何问题和措施等。
6. 实施审核
定期审核混料操作的标准和过程,以及检查操作人员的可靠性和技能水平。
7. 加强监督
对混料过程进行监督,确保质量标准得以满足。
将重点放在操作员的培训上,以确保操作员能够遵守 SOP。
总之,预防混料管理对于确保产品质量至关重要。
通过合理的规划
计划,质量控制标准和过程监督来预防混料,可以有效地降低成本,提高生产效率并提高产品质量。
SOP卫生管理规定

卫生管理规定1.目的规定产品生产全过程中,为防止污染、混批、混品种事故的发生应采取的措施及管理要求,保证产品的质量2.适用范围本公司产品生产过程的各项卫生管理3.职责厂区卫生环境由人力资源部负责;车间卫生由各车间主任负责;质量部负责对车间环境的监测, 检查所有区域的卫生情况。
4.制定依据GB148815.程序5.1. 环境卫生要求5.1.1厂区应按生产、行政、生活和辅助等功能合理布局,不得互相妨碍。
生产区应在环境清洁、人流物流不穿越或少穿越的地方合理布局。
5.1.2生产厂房周围应绿化,无裸露土面,广植草坪或种植对空气中含尘、含菌浓度不产生有害影响的树木,但不宜种花。
5.1.3生产厂房道路应用整体性好、发尘少的覆面材料。
5.1.4生产厂房、物料库房应封闭良好。
5.1.5厂区卫生由人事行政部维持清洁卫生。
平时由绿化卫生员负责日常打扫及绿化工作,保持厂区成花园式工厂。
5.1.6车间卫生应每班工前、工后有人清洁,物品堆放整齐。
5.1.7车间内垃圾集中堆放,指定专人及时清理出车间。
5.1.8各部门日常垃圾应按废弃物处理要求分类集中存放,定时作废物收购或集中处理。
5.1.9厂房内各项设施应保持清洁,出现问题及时维修或更新;厂房地面、屋顶、天花板及墙壁有破损时,应及时修补。
5.1.10生产、包装、贮存等设备及工器具、生产用管道、裸露食品接触表面等应定期清洁消毒。
5.2工艺卫生5.2.1生产车间内按工艺要求分为一般生产区和洁净区。
车间应定时对洁净区内5.2.2空间、设备进行清洁消毒。
5.2.3为保证各生产工序不相互干扰,防止交叉污染,应合理安排工艺布局。
人、物流分开,出入门分别设置;物料传递线路应短捷、不交叉。
5.2.4人员进出应设换鞋、更衣室;物料进入应经脱包清洁,缓冲暂存室后才进洁净区。
5.3个人卫生5.3.1人体是微生物生长繁殖的良好环境,人体自然活动会产生大量皮屑,因此人体是最大的污染源,特别是传染病人与患有其它有碍卫生疾病的人员更有碍产品卫生。
防错混料管理指导书
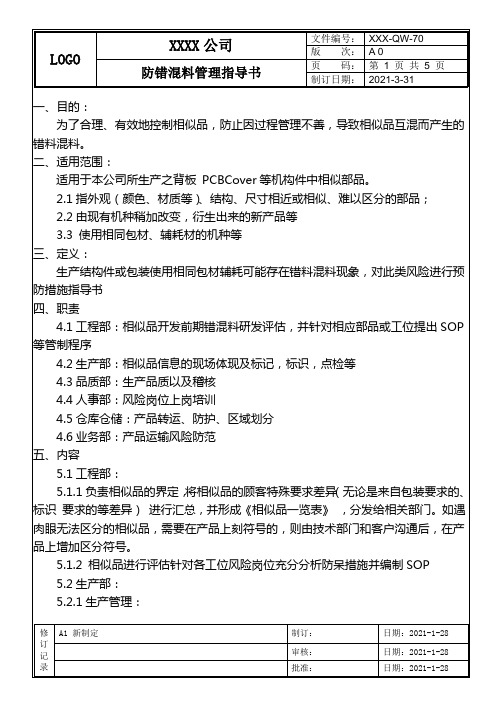
5.3品质部
5.3.1 首件时使用BOM表核对原物料编码,按照图纸或样品进行“六面”外观对比并保留记录
5.3.2 QC需确认生产部门对应是否按照SOP生产、点检表是否点检、线体是否符合规定、清线是否清完全、尾料标签是否及时粘贴等。
5.5.5 相似机种分区域放置并有明显警示标示
5.5.6库房严禁私自开箱作业,需开箱由品质对接生产领入产线作业;外仓严格禁止在仓库私自开箱作业,除客户同意外,仓库单独设立合并箱区域或房间,有摄像头全程监控,经过生产单位、仓库、SC三方共同作业并记录,摄像内容需要保留6个月以上。
5.5.7 第三方SortingT平台或者第三方特殊作业出货对BOX标签与客户标签比对,传递预防错混料管理要求。
5.5.8 纸箱或客户标签破损等原因需要更换纸箱或标签是能由品质人员确认更换(外长由各限地CS更换)
5.6业务部
5.6.1 运输过程中不可对产品进行除运输外的任何操作,并签署错混料相关处罚协议
六、参考文件及使用表单
6.1《首件管控程序》
6.2《相似机种一览表》
6.3《产品BOM(原材开料规格)表、样品》
5.2.1.4相似机种若共用模具且接连生产,产品必须更换LOT号进行区分切冲压领班由品质签署首件后且确认所有尾料清理完成后方可生产;
5.2.1.5 相似品生产时现场放入相似品专属区域,每托粘贴产品标识卡,由品质QC确认OK粘贴ACC标签。
5.2.1.6 品质贴附ACC标签后产品任何部门不可擅自移动或拿取产品,只允许整托运输。QC检验合格封箱之后不允许进行任何操作,包括粘贴标签、合并箱等一切改变状态的行为
预防混料管理办法

预防混料管理办法一、目的规范我司原物料,半成品,成品的管理,防止公司错混料的发生。
二、适应范围车间范围内所有与原材料,半成品,成品所接触到的部门,以及我司供应商。
三、定义错混料:原料物,半成品,成品中用错料或混料的现象统称为错混料。
四、职责4.1业务负责接到订单后将客户订单转化为内部订单责任确认单,并将信息传递至下单员录入系统。
4.2 技术部负责产品BOM的组成和材料性能确认选择。
4.3生产管理部负责下达排产任务单,原材料需求采购和监督任务执行。
4.4供应部依据计划提出的采购需求,进行保障到货。
4.5仓库负责原材料与成品的储存及管理(包括收发及5S管理)。
4.6质量部负责物料,半成品与成品的检验管理。
4.7生产部负责对生产中所有原材料,半成品与成品的管理和组织人员生产保证订单按期完成。
五、内容5.1.工艺文件错混料管理5.1.1技术部根据客户新产品、图纸、技术指标或工艺要求,注意图纸版本及产品技术指标细节,转换成我司的技术文件和现场工艺文件,进行受控和发行。
5.1.2专职人员统一管理技术文件,注意图纸编号,图纸版本,技术文件编号,技术文件版本,发行日期,发行换版编号,同时做好回收作废工作,放置图纸错误造成混料。
5.2业务接单/下单错混料管理5.2.1业务接收客户订单时候,经过评审后,将客户相关要求进行记录,按照唯一编号进行比对识别。
5.2.2业务下单时,将相关要求在销售订单责任确认单上进行注明,特别产品包装要求和生产注意事项,对于产品类型相似及包装方式相同的产品重点说明。
5.2.3.特殊产品:系统下单进行唯一编码进行识别,确保下单和系统录入;常规产品:正常系统下单,根据规格进行识别进行。
5.3模具错混料管理5.3.1模具仓库设有专人员管理,并做有专门记录,记录有模具类别,尺寸,领用机台,数量,做好明细登记和标识,同一机台最多两台。
5.3.2相关产品按照规定模具进行配模生产,管控规定。
5.4样品新生产时错混料管理5.4.1业务部接新产品(以从前未生产过)或客户产品变更消息时及时转交技术部,技术部根据业务提供的相关资料做成BOM,同时对材料选型确认指标规定做好规定和要求,供应部依据BOM进行厂家选择,材料选择,物料回来经质量部验收合格后进行入库。
生产部DIP车间物料防错防混管理规范

4.1.3各拉在物料交接及转拉过程中,各拉须安排助拉(物料员)进行操作,在周转时,物料的最小包装须标有物料编号,并要确认物料编号与BOM(或投料单)一致,同时所转接的物料按工单放置在周转箱中,并在周转箱贴上标识(标识产品名称、工单号、工单量)。
1、目的:
为防止生产部(DIP)车间制程过程中出现物料混料、用错物料,特制定此规范。
2、范围:
适用于生产部DIP车间。
3、定义:
3.1错料:生产过程中使用的物料与BOM单\SOP不符合出现的不良现象。
3.2混料:生产过程中同一物料盒内出现2种物料产产生产不良现象。
4、职责:
物料组长:负责物料员的电子元件的识别培训及领料过程中不出现领错料、周转过中的不出现混料。
4.1.8 IE在排工位时,体积、颜色、形状相似的物料不能排在一个工位作业,防止混料,要分开二个人作业,产线在作业时发现此类问题及时反应给IE,由IE修改SOP。
4.1.9下拉过时中如出现掉料的情况,非此位置的作业的人员不得进行补料,应及时向插件助拉或是拉长报告,助拉或是拉长将掉下的物料收集在不良品盒内,重新拿良品物料进行补料,补料时要对照SOP确认无误后补料。
4.2.3后焊段制程出现的少料及不良材料的更换按“修理作业规范”进行。
5、流程图:
无ቤተ መጻሕፍቲ ባይዱ
6、相关文件:
物料损耗控制管理规定PMWI-A-016
修理作业规范PEWI-A-007
制程检验作业规范QAWI-A-003
7、相关记录:
产品补(换)料记录表PRQR007
维修日报表PEQR017
4.1.4转线前由生产线助拉(或拉长)制作首件送检,首件经IPQC和工程PE确认合格后方可进行转线,如在确认中发现生产线送检的有用问题的现象,参照《制程检验作业规范》执行。
PFEMA(错、漏、混)-范例0114
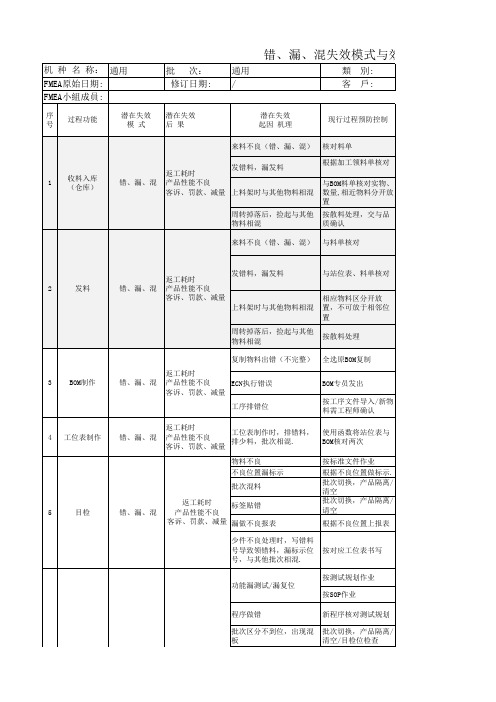
7 4 3 84 7 4 3 84
自动测试全覆盖
8
2
5
80
专人负责制作,锁定 程序,不能修改
7 2 4 56
QA抽检
7 4 2 56
测试员两小时点检 8 2 4 64
QC检查/QA抽检 7 4 1 28
QA检查/主管确认 7 3 2 42
QA核查
6 3 2 36
交由QC核对
5 4 3 60
自检
7 2 3 42
管理者核对
8 2 4 64
生产核对/QC检查 7 3 3 63
工程部确认
9 2 4 72
QA检查/主管确认 5 3 4 60
修后重做
7 3 3 63
QA抽检
7 2 4 56
QA抽检
8 2 3 48
重做目检
6 4 3 72
QC核对
7 2 5 70
IPQC检查/首件 IPQC检查/首件 IPQC检查 QA抽检
客诉、罚款、减量
上料架时与其他物料相混
与站位表、料单核对
相应物料区分开放 置,不可放于相邻位 置
周转掉落后,捡起与其他 物料相混
按散料处理
复制物料出错(不完整) 全选原BOM复制
返工耗时
错、漏、混 产品性能不良
ECN执行错误
客诉、罚款、减量
工序排错位
BOM专员发出
按工序文件导入/新物 料需工程师确认
机 种 名 称: 通用 FMEA原始日期: FMEA小組成員:
序 号
过程功能
潜在失效 模式
批 次: 修订日期:
潜在失效 后果
错、漏、混失效模式与效应分析(PFMEA )
通用
類 別:
生产过程预防错混料SOP
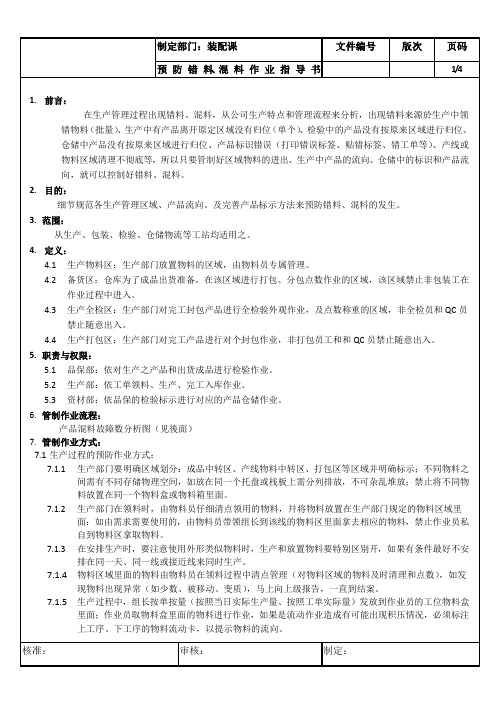
7.1.6在生产过程中如有非品质部门人员从生产线中拿走物料的,作业员必须禁止其行为;必须报告组长,经组长同意之後才能从生产线中拿走物料;如拿走物料部门要将物料归还给生产部门,必须归还物料交组长,禁止任何非品质部门人员擅自从生产线拿走物料,及擅自将物料放在生产线上的行为,如生产部门发现有该行为,开立处罚单处罚当事人10元人民币。
7.1.7下班前,组长必须进行清线作业(将流水线上的产品全部完工作业,然後将多余物料放置好),禁止停线下班了,生产线物料没有清理的行为。
7.1.8清线过程中要将不良和良品有效的区别开来:不良品用红色盒子装,幷统一拿到返修区由返工人员进行返修作业;待下工序的良品必须标注下工序的物料流动卡,,以提示下工序的流向。
7.1.9如果是停线超过48小时的,必须用上下盖将物料盒里面的物料盖住,幷标注下工序的物料流动卡,以提示下工序的流向。
7.1.10生产及换线依生产现场6S管理规定执行,生产尾数需分开标示区分,生产线上人员需落实自检动作,核对流程卡所示品名规格、数量需与实物一致,避免因换线产品清理不彻底导致混料,核对无误之产品由作业人员填写物料标签标示于产品外包装上。
7.2生产包装过程的预防作业方式:7.2.1包装员必须培训上岗,熟悉各产品的包装方式,所有封箱包装作业必须在包装区域完成。
7.2.2包装台面上禁止放置两种或以上类似产品同时包装作业,必须分开区域、分开作业。
7.2.3包装员的封箱作业前,必须核对内外箱标签;组长在拿标签给包装员时必须自我核对幷交代清楚,及提示注意事项。
7.2.4包装过程如出现标签过多情况或不清晰情况,包装员要立即上报组长重新更换,及交上级清查多数标签的原因,排除少贴、错贴因素之後,才将多於标签销毁处理。
7.2.5如包装因工单数量需要包装尾数箱时,必须在外箱上注明“尾数箱”标识,幷提示品保检验人员特别抽检该箱的标识、数量核对等。
7.2.6所有包装箱在入库前必须用电子称进行称重确认。
预防混料管理办法
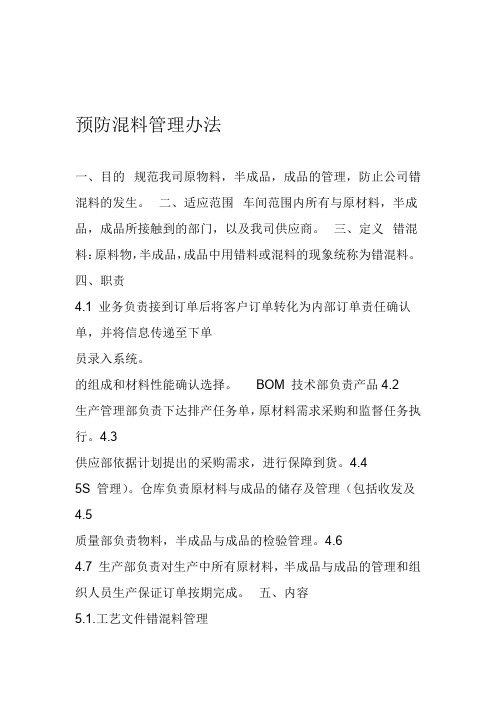
预防混料管理办法一、目的规范我司原物料,半成品,成品的管理,防止公司错混料的发生。
二、适应范围车间范围内所有与原材料,半成品,成品所接触到的部门,以及我司供应商。
三、定义错混料:原料物,半成品,成品中用错料或混料的现象统称为错混料。
四、职责4.1 业务负责接到订单后将客户订单转化为内部订单责任确认单,并将信息传递至下单员录入系统。
的组成和材料性能确认选择。
BOM 技术部负责产品4.2生产管理部负责下达排产任务单,原材料需求采购和监督任务执行。
4.3供应部依据计划提出的采购需求,进行保障到货。
4.45S 管理)。
仓库负责原材料与成品的储存及管理(包括收发及4.5质量部负责物料,半成品与成品的检验管理。
4.64.7 生产部负责对生产中所有原材料,半成品与成品的管理和组织人员生产保证订单按期完成。
五、内容5.1.工艺文件错混料管理5.1.1 技术部根据客户新产品、图纸、技术指标或工艺要求,注意图纸版本及产品技术指标细节,转换成我司的技术文件和现场工艺文件,进行受控和发行。
专职人员统一管理技术文件,注意图纸编号,图纸版本,技术文件编号,技术文件版5.1.2本,发行日期,发行换版编号,同时做好回收作废工作,放置图纸错误造成混料。
5.2 业务接单/ 下单错混料管理5.2.1 业务接收客户订单时候,经过评审后,将客户相关要求进行记录,按照唯一编号进行比对识别。
,特别产品包装要求和生产将相关要求在销售订单责任确认单上进行注明业务下单时,5.2.2对于产品类型相似及包装方式相同的产品重点说明。
,注意事项5.2.3.特殊产品:系统下单进行唯一编码进行识别,确保下单和系统录入;常规产品:正常系统下单,根据规格进行识别进行。
5.3 模具错混料管理5.3.1 模具仓库设有专人员管理,并做有专门记录,记录有模具类别,尺寸,领用机台,数量,做好明细登记和标识,同一机台最多两台。
5.3.2 相关产品按照规定模具进行配模生产,管控规定。
生产过程预防错混料

7.1.6在生產過程中如有非品質部門人員從生產線中拿走物料的,作業員必須禁止其行為;必須報告組長,經組長同意之後才能從生產線中拿走物料;如拿走物料部門要將物料歸還給生產部門,必須歸還物料交組長,禁止任何非品質部門人員擅自從生產線拿走物料,及擅自將物料放在生產線上的行為,如生產部門發現有該行為,開立處罰單處罰當事人10元人民幣。
7.1.7下班前,組長必須進行清線作業(將流水線上的產品全部完工作業,然後將多餘物料放置好),禁止停線下班了,生產線物料沒有清理的行為。
7.1.8清線過程中要將不良和良品有效的區別開來:不良品用紅色盒子裝,幷統一拿到返修區由返工人員進行返修作業;待下工序的良品必須標注下工序的物料流動卡,,以提示下工序的流向。
7.1.9如果是停線超過48小時的,必須用上下蓋將物料盒裏面的物料蓋住,幷標注下工序的物料流動卡,以提示下工序的流向。
7.1.10生產及換線依生產現場6S管理規定執行,生產尾數需分開標示區分,生產線上人員需落實自檢動作,核對流程卡所示品名規格、數量需與實物一致,避免因換線產品清理不徹底導致混料,核對無誤之產品由作業人員填寫物料標籤標示于產品外包裝上。
7.2生產包裝過程的預防作業方式:7.2.1包裝員必須培訓上崗,熟悉各產品的包裝方式,所有封箱包裝作業必須在包裝區域完成。
7.2.2包裝檯面上禁止放置兩種或以上類似產品同時包裝作業,必須分開區域、分開作業。
7.2.3包裝員的封箱作業前,必須核對內外箱標籤;組長在拿標籤給包裝員時必須自我核對幷交代清楚,及提示注意事項。
7.2.4包裝過程如出現標籤過多情況或不清晰情況,包裝員要立即上報組長重新更換,及交上級清查多數標籤的原因,排除少貼、錯貼因素之後,才將多於標籤銷毀處理。
7.2.5如包裝因工單數量需要包裝尾數箱時,必須在外箱上注明“尾數箱”標識,幷提示品保檢驗人員特別抽檢該箱的標識、數量核對等。
7.2.6所有包裝箱在入庫前必須用電子稱進行稱重確認。
防止混料管理制度
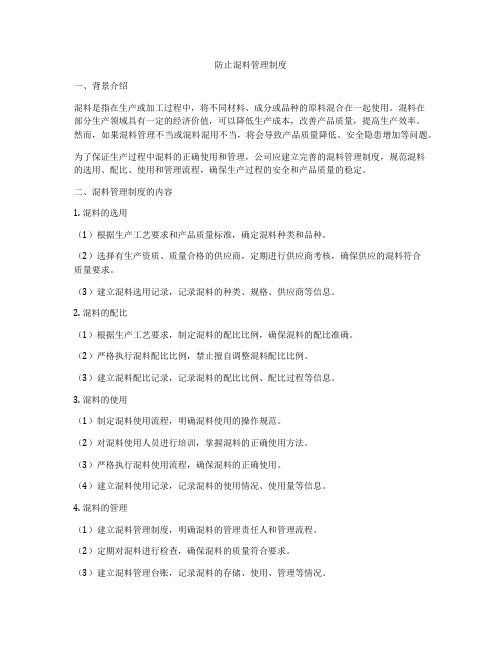
防止混料管理制度一、背景介绍混料是指在生产或加工过程中,将不同材料、成分或品种的原料混合在一起使用。
混料在部分生产领域具有一定的经济价值,可以降低生产成本,改善产品质量,提高生产效率。
然而,如果混料管理不当或混料混用不当,将会导致产品质量降低、安全隐患增加等问题。
为了保证生产过程中混料的正确使用和管理,公司应建立完善的混料管理制度,规范混料的选用、配比、使用和管理流程,确保生产过程的安全和产品质量的稳定。
二、混料管理制度的内容1. 混料的选用(1)根据生产工艺要求和产品质量标准,确定混料种类和品种。
(2)选择有生产资质、质量合格的供应商,定期进行供应商考核,确保供应的混料符合质量要求。
(3)建立混料选用记录,记录混料的种类、规格、供应商等信息。
2. 混料的配比(1)根据生产工艺要求,制定混料的配比比例,确保混料的配比准确。
(2)严格执行混料配比比例,禁止擅自调整混料配比比例。
(3)建立混料配比记录,记录混料的配比比例、配比过程等信息。
3. 混料的使用(1)制定混料使用流程,明确混料使用的操作规范。
(2)对混料使用人员进行培训,掌握混料的正确使用方法。
(3)严格执行混料使用流程,确保混料的正确使用。
(4)建立混料使用记录,记录混料的使用情况、使用量等信息。
4. 混料的管理(1)建立混料管理制度,明确混料的管理责任人和管理流程。
(2)定期对混料进行检查,确保混料的质量符合要求。
(3)建立混料管理台账,记录混料的存储、使用、管理等情况。
(4)对混料的存储条件进行要求,确保混料的存储环境干净、干燥、通风、避光等。
(5)建立混料的追溯体系,确保混料的来源可查。
5. 混料的风险评估(1)对每批混料进行风险评估,明确混料的使用风险和控制措施。
(2)建立混料风险评估记录,记录混料的风险评估结果和控制措施。
(3)定期对混料的风险进行评估,及时调整控制措施。
6. 混料质量的控制(1)建立混料质量监控制度,对混料的质量进行监控和控制。
- 1、下载文档前请自行甄别文档内容的完整性,平台不提供额外的编辑、内容补充、找答案等附加服务。
- 2、"仅部分预览"的文档,不可在线预览部分如存在完整性等问题,可反馈申请退款(可完整预览的文档不适用该条件!)。
- 3、如文档侵犯您的权益,请联系客服反馈,我们会尽快为您处理(人工客服工作时间:9:00-18:30)。
7.1.6在生产过程中如有非品质部门人员从生产线中拿走物料的,作业员必须禁止其行为;必须报告组长,经
组长同意之後才能从生产线中拿走物料;如拿走物料部门要将物料归还给生产部门,必须归还物料交组
长,禁止任何非品质部门人员擅自从生产线拿走物料,及擅自将物料放在生产线上的行为,如生产部门
发现有该行为,开立处罚单处罚当事人10 元人民币。
7.1.7下班前,组长必须进行清线作业(将流水线上的产品全部完工作业,然後将多余物料放置好),禁止停
线下班了,生产线物料没有清理的行为。
7.1.8清线过程中要将不良和良品有效的区别开来:不良品用红色盒子装,幷统一拿到返修区由返工人员进行
返修作业;待下工序的良品必须标注下工序的物料流动卡,,以提示下工序的流向。
7.1.9如果是停线超过48 小时的,必须用上下盖将物料盒里面的物料盖住,幷标注下工序的物料流动卡,以
提示下工序的流向。
7.1.10生产及换线依生产现场6S 管理规定执行,生产尾数需分开标示区分,生产线上人员需落实自检动作,
核对流程卡所示品名规格、数量需与实物一致,避免因换线产品清理不彻底导致混料,核对无误之产品
由作业人员填写物料标签标示于产品外包装上。
7.2生产包装过程的预防作业方式:
7.2.1包装员必须培训上岗,熟悉各产品的包装方式,所有封箱包装作业必须在包装区域完成。
7.2.2包装台面上禁止放置两种或以上类似产品同时包装作业,必须分开区域、分开作业。
7.2.3包装员的封箱作业前,必须核对内外箱标签;组长在拿标签给包装员时必须自我核对幷交代清楚,及提示
注意事项。
7.2.4包装过程如出现标签过多情况或不清晰情况,包装员要立即上报组长重新更换,及交上级清查多数标签的
原因,排除少贴、错贴因素之後,才将多於标签销毁处理。
7.2.5如包装因工单数量需要包装尾数箱时,必须在外箱上注明“尾数箱”标识,幷提示品保检验人员特别抽检
该箱的标识、数量核对等。
7.2.6所有包装箱在入库前必须用电子称进行称重确认。
7.3生产检验过程的预防作业方式:
7.3.1检验QC 人员的检验区域由其上级进行定位之後知会生产部门;除非代班和品质分析行为,禁止出现串
位、换位拿物料检验,如检验QC 串位、换位拿物料,依照作业。
7.3.2IPQC 人员按照生产规定的区域或工位拿对应的物料进行循回检验或品质分析完毕之後,必须归还原来区
域或工位;
7.3.3FQC人员抽检成品,抽样需分线别分产品逐一抽取,检验完成后需原包装放回,不可同时抽取多种产品,
避免检验后放错箱、包等;抽检完毕之後,必须在所抽取的外箱或外包装上加盖FQC
小章,标示该箱或该包有抽检作业。
如下工序发现标示该箱或该包有抽检作业里面出现错料、混料的,下工序负责人或生产部门开立开立处罚单处罚当事人10 元人民币。
7.4仓储过程的预防作业方式:
7.4.1成品入库时,仓管员见单点数入库,依照仓库规定的区域进行仓储放置作业,除非盘点作业,禁止仓储
人员擅自从成品箱里面拿货。
7.4.2如有发货作业,仓管员见单点数发货;如有尾数,在外箱上注明尾箱标识。
7.4.3禁止将类似产品放置在一个物料栈板上;如有类似产品需要放置在一个货架上面,必须制作醒目标示注明
区别要点,必要时制作区别看板放置在醒目位置。
7.5成品检验过程的预防作业方式:
OQC在仓库备货完毕之後,进行检验作业。
原则上依照作业。
7.6出货备料检验过程的预防作业方式:
7.6.1出货备货时,必须由仓管点数从成品仓拉到备货区进行打包作业;禁止在成品仓内部进行备货作业。
7.6.2包装作业员依出货需求对产品进行打包作业,包装员必须先完成尾数包装再清点整包。
7.6.3在备货过程中,因打包区域受限,禁止多产品同时点数、打包;待包产品时依出货数量多寡,依由多至
少先后顺序包装处理,并对打包完成之产品进行标示。
7.6.4资材部仓管员依出货明细对包装好之产品进行备料,供OQC检验员作出货前检验。
7.6.5如若出货需求更改而需对打包完成之产品重新进行分箱、合箱,需在QC人员监督情况下进行作
业,没有得到QC 人员认可禁止执行分箱、合箱动作
7.6.6如因品质异常因素,需要重工的,必须退回产线,由产线返工幷重新更新标识;禁止由仓库人员自我在
仓库返工,不更新标识情况。
7.6.7所有客户出货标识、标示必须依照业务出货明细规定执行:由专职打印标签人员来打印标签,标签打印
记录在《出货标签核对登记表》中,幷报OQC 确认及包装组长自检方能交包装员张贴;标签的使用数
量必须有交接记录,包装过程如出现标签过多情况或不清晰情况,包装员要立即上报组长重新更换,及
交上级清查多数标签的原因,排除少贴、错贴因素之後,才将多於标签销毁处理;设置专人对所有包装
用条码设备进行100%扫描确认;如有零、尾箱,必须在外箱上注明“尾数箱”标识,幷提示品保检验人
员特别抽检该箱的标识、数量核对等。
768 资材部仓管员依出货通知将OQC检验合格之产品进行装车出货作业。
如正在运输或装柜过程,有产品倒箱造成产品散出或包装破坏情况,必须依照7.6.6作业,禁止不经确认私自重新进行分箱、合箱作业。
8.表格记录:
无
9.关联程序或SOP
仓储管理程序
产品标识和追溯性控制程序
増康讣00»轉I刿入捌®昭目r 辭QC工作碱規刪£俶融韓矚管删法〉p 倉管每月程站晒•核对斥•務・・F &S2& • f 主融im對
农十所有楙I干倔域頤,不准同一俪放mai膨 f 6W帕耳晒•刃入棺光項目L倉耳慈立Aim顺:•築止興工倆魁人貝炳倉進出倉联tty 主管抽査他
f皿監督怖
出貨品卫須給#OQC檢鮒,OQOmt列入檢騎珀目-> OQC監督執行
直劇斜制度:•熱止茯周阿酣•同一畐城同時備綁i貨轉"► OCC監督執行外请上刪(凍品緒•以方紳别 f
WOQCI作沛诙讹(成融口粉朝世騰法》
下併俪澀咆)蘆品“出成品机斜
---- 不同產品就製r~出匍辭iq嘶
OQCfi閱M的检歸A域檢
励
:净止在同-佣RI •同Tff壕新簡多珈WW
-包賢枷
不霖似包找產品机农■囊耐8爲立的包翹■ ■帑止在同卡閒•同域包焚多橋帥广f防止瑕包裝進入立时吹删删,
類毗癒品況魏一》類似產品幣止在安帰Hi近住產探同時連作
一►阪止冷績包盘■ IPQC監習散
行
厂甫灣不艮品用小奸封閉保存-以阪止商创不艮 -倔H諦部至朝清理盒于內不艮
一不良品混灾X~~r—一*不艮品用潢色貨紅色盒子匪放•返修伐朗取走不良品進行返修一返修工作臺期詣•返珂一產品
1—所丽編產品卫缠皱工撤•包桔爲龟耕一返修工作臺班展•返工軍一產品
類似產品混製入—Fm產品崇止在安排在KW注盍採同時運作
所
-混入不
工程殷計理属覓空怠包戻•包磁可以空別
品必極過返工撤-包括爲时T —返修工作豪理朋,返理一產品
停働料必須应口保存一停縫4孙畤的生產楙燔虧胃線毘理一> 將停演制度删耐匕賤配空產管理飾法》
倉管鳩描加和核對貨单的數屋比例5% 將倉管工作矢除率列入管理舉效
倉管线立俘月理初度。