什么是混凝土的离析现象
混凝土离析
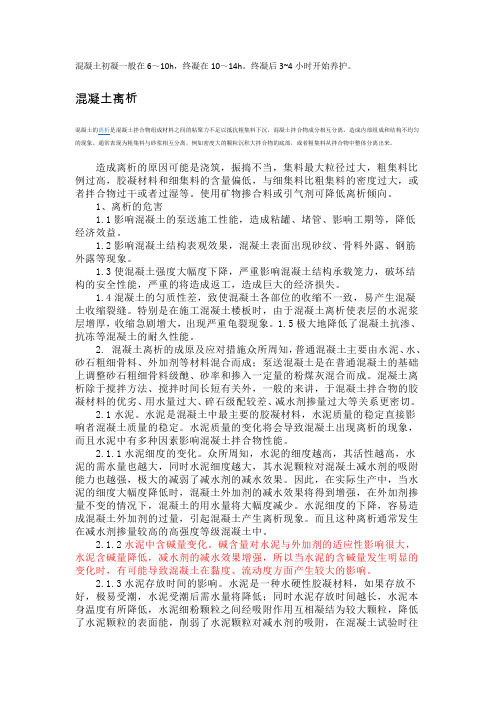
混凝土初凝一般在6~10h,终凝在10~14h。
终凝后3~4小时开始养护。
混凝土离析混凝土的离析是混凝土拌合物组成材料之间的粘聚力不足以抵抗粗集料下沉,混凝土拌合物成分相互分离,造成内部组成和结构不均匀的现象。
通常表现为粗集料与砂浆相互分离,例如密度大的颗粒沉积大拌合物的底部,或者粗集料从拌合物中整体分离出来。
造成离析的原因可能是浇筑,振捣不当,集料最大粒径过大,粗集料比例过高,胶凝材料和细集料的含量偏低,与细集料比粗集料的密度过大,或者拌合物过干或者过湿等。
使用矿物掺合料或引气剂可降低离析倾向。
1、离析的危害1.1影响混凝土的泵送施工性能,造成粘罐、堵管、影响工期等,降低经济效益。
1.2影响混凝土结构表观效果,混凝土表面出现砂纹、骨料外露、钢筋外露等现象。
1.3使混凝土强度大幅度下降,严重影响混凝土结构承载笼力,破坏结构的安全性能,严重的将造成返工,造成巨大的经济损失。
1.4混凝土的匀质性差,致使混凝土各部位的收缩不一致,易产生混凝土收缩裂缝。
特别是在施工混凝土楼板时,由于混凝土离析使表层的水泥浆层增厚,收缩急剧增大,出现严重龟裂现象。
1.5极大地降低了混凝土抗渗、抗冻等混凝土的耐久性能。
2. 混凝土离析的成原及应对措施众所周知,普通混凝土主要由水泥、水、砂石粗细骨料、外加剂等材料混合而成;泵送混凝土是在普通混凝土的基础上调整砂石粗细骨料级酏、砂率和掺入一定量的粉煤灰混合而成。
混凝土离析除于搅拌方法、搅拌时间长短有关外,一般的来讲,于混凝土拌合物的胶凝材料的优劣、用水量过大、碎石级配较差、减水剂掺量过大等关系更密切。
2.1水泥。
水泥是混凝土中最主要的胶凝材料,水泥质量的稳定直接影响者混凝土质量的稳定。
水泥质量的变化将会导致混凝土出现离析的现象,而且水泥中有多种因素影响混凝土拌合物性能。
2.1.1水泥细度的变化。
众所周知,水泥的细度越高,其活性越高,水泥的需水量也越大,同时水泥细度越大,其水泥颗粒对混凝土减水剂的吸附能力也越强,极大的减弱了减水剂的减水效果。
混凝土离析的原因
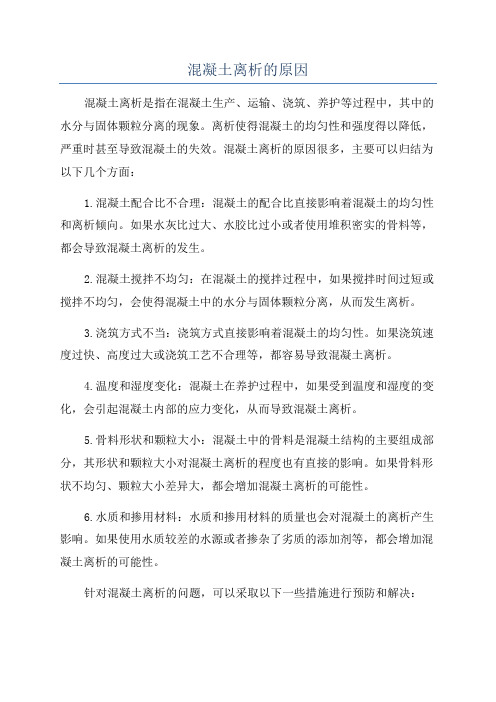
混凝土离析的原因混凝土离析是指在混凝土生产、运输、浇筑、养护等过程中,其中的水分与固体颗粒分离的现象。
离析使得混凝土的均匀性和强度得以降低,严重时甚至导致混凝土的失效。
混凝土离析的原因很多,主要可以归结为以下几个方面:1.混凝土配合比不合理:混凝土的配合比直接影响着混凝土的均匀性和离析倾向。
如果水灰比过大、水胶比过小或者使用堆积密实的骨料等,都会导致混凝土离析的发生。
2.混凝土搅拌不均匀:在混凝土的搅拌过程中,如果搅拌时间过短或搅拌不均匀,会使得混凝土中的水分与固体颗粒分离,从而发生离析。
3.浇筑方式不当:浇筑方式直接影响着混凝土的均匀性。
如果浇筑速度过快、高度过大或浇筑工艺不合理等,都容易导致混凝土离析。
4.温度和湿度变化:混凝土在养护过程中,如果受到温度和湿度的变化,会引起混凝土内部的应力变化,从而导致混凝土离析。
5.骨料形状和颗粒大小:混凝土中的骨料是混凝土结构的主要组成部分,其形状和颗粒大小对混凝土离析的程度也有直接的影响。
如果骨料形状不均匀、颗粒大小差异大,都会增加混凝土离析的可能性。
6.水质和掺用材料:水质和掺用材料的质量也会对混凝土的离析产生影响。
如果使用水质较差的水源或者掺杂了劣质的添加剂等,都会增加混凝土离析的可能性。
针对混凝土离析的问题,可以采取以下一些措施进行预防和解决:1.合理设计配合比:根据混凝土所在的环境和使用要求,合理设计混凝土的配合比,保证水灰比、水胶比和骨料的比例等参数满足要求,减少离析的发生。
2.优化搅拌工艺:在混凝土的搅拌过程中,要保证搅拌时间充分,并采用适当的搅拌设备,确保混凝土均匀搅拌,减少离析现象。
3.控制浇筑速度和高度:在进行混凝土浇筑时,要控制浇筑速度,保证浇筑高度适中,避免过快或过高造成的离析。
4.加强养护措施:在混凝土浇筑后,要及时进行养护,保持适宜的温度和湿度,减少混凝土内部应力变化,防止离析的发生。
5.选择适合的骨料和掺合材料:选择形状均匀、颗粒大小合理的骨料,并保证水质的优良,合理选择和使用掺合材料,减少离析的风险。
混泥土离析
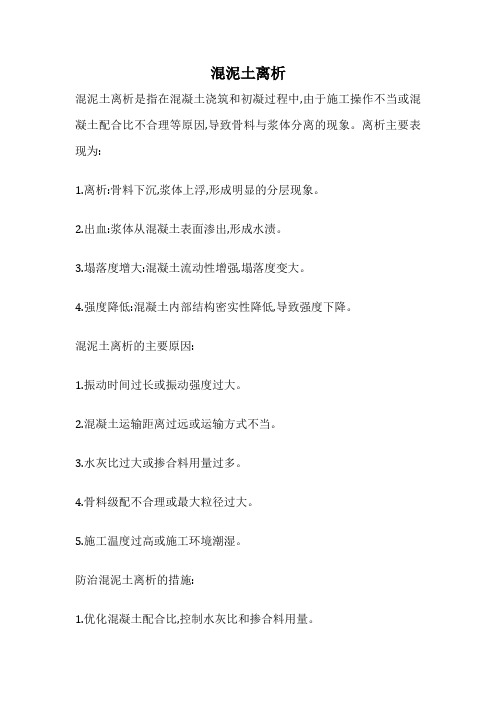
混泥土离析
混泥土离析是指在混凝土浇筑和初凝过程中,由于施工操作不当或混凝土配合比不合理等原因,导致骨料与浆体分离的现象。
离析主要表现为:
1.离析:骨料下沉,浆体上浮,形成明显的分层现象。
2.出血:浆体从混凝土表面渗出,形成水渍。
3.塌落度增大:混凝土流动性增强,塌落度变大。
4.强度降低:混凝土内部结构密实性降低,导致强度下降。
混泥土离析的主要原因:
1.振动时间过长或振动强度过大。
2.混凝土运输距离过远或运输方式不当。
3.水灰比过大或掺合料用量过多。
4.骨料级配不合理或最大粒径过大。
5.施工温度过高或施工环境潮湿。
防治混泥土离析的措施:
1.优化混凝土配合比,控制水灰比和掺合料用量。
2.采用合理的骨料级配和最大粒径。
3.适当调整振实方式和时间。
4.缩短运输距离,采用密闭式运输设备。
5.控制施工温度和环境湿度。
6.可适当添加减水剂或防离析剂等外加剂。
混泥土离析不仅影响混凝土的工作性能,还会降低混凝土的耐久性和抗渗性能,严重时甚至会引起混凝土开裂和脱落。
因此,在施工过程中应高度重视,采取有效措施预防和控制离析现象。
混凝土离析处理方案

混凝土离析处理方案混凝土离析是指混凝土中的骨料和水泥浆体分离的现象,通常表现为混凝土表面出现凹凸不平、骨料外露或者水泥砂浆脱落等情况。
混凝土离析不仅影响混凝土的外观质量,还可能影响混凝土的力学性能和耐久性能,因此需要采取相应的处理方案。
一、混凝土配合比设计。
在混凝土的配合比设计中,应根据混凝土的使用要求和外部环境条件,合理确定水灰比、砂率、骨料粒径等参数,以提高混凝土的坍落度和抗渗性能,减少混凝土离析的可能性。
二、施工工艺控制。
在混凝土浇筑施工中,应严格控制浇筑质量,避免过早脱模、振捣不当、浇筑层次过厚等情况,确保混凝土的密实性和均匀性,减少混凝土内部的空隙和缺陷,从而减少混凝土离析的可能性。
三、养护措施。
混凝土养护过程中,应根据混凝土的配合比和外部环境条件,采取适当的养护措施,如覆盖湿棉被、喷水养护、覆盖塑料薄膜等,以保持混凝土的充分湿养护,促进水泥的充分水化反应,减少混凝土的干缩裂缝和离析现象。
四、表面处理。
对于已经出现离析现象的混凝土表面,可以采取表面修补、喷涂保护剂、覆盖抛光等方式进行处理,以修复混凝土表面的平整度和光洁度,提高混凝土的外观质量和耐久性能。
五、材料选择。
在混凝土的材料选择中,应选择优质的水泥、骨料和外加剂,以提高混凝土的抗渗性能和耐久性能,减少混凝土离析的可能性。
六、质量监控。
在混凝土的生产和施工过程中,应加强对混凝土质量的监控和检验,确保混凝土的配合比、坍落度、密实性等指标符合设计要求,减少混凝土离析的发生。
综上所述,混凝土离析是混凝土施工过程中常见的质量问题,需要在配合比设计、施工工艺控制、养护措施、表面处理、材料选择和质量监控等方面加以重视和处理,以保证混凝土的质量和使用性能,避免混凝土离析对工程质量和安全性造成影响。
混凝土离析原因及措施

混凝土离析原因及措施混凝土离析是指混凝土在浇筑后发生分层现象,即水泥浆体中的水分和颗粒在浇筑过程中分离,使得混凝土表面出现较多的水分,而内部则较为干燥。
这种现象不仅影响混凝土的强度和耐久性,还会影响其外观质量。
本文将从混凝土离析的原因及相关措施进行阐述。
混凝土离析的原因主要有以下几点:1. 骨料选择和搅拌不均匀:骨料在混凝土中起到填充和增强作用,但如果骨料选择不当或搅拌不均匀,就会导致骨料在混凝土中分布不均匀,加剧离析现象的发生。
2. 水泥浆体粘度过大:水泥浆体的粘度过大会导致混凝土内部水分和颗粒难以均匀分布,从而造成离析。
这种情况通常是由于水泥的用量过多或水灰比不合理造成的。
3. 混凝土浇筑方式不当:如果混凝土在浇筑过程中振捣不充分或浇筑速度过快,就会使得混凝土中的颗粒和水分分离,产生离析现象。
4. 环境温度和湿度:环境温度和湿度对混凝土的凝结过程有重要影响。
如果环境温度过高或湿度过低,会加快混凝土的凝结速度,增加离析的风险。
为了避免混凝土离析现象的发生,可以采取以下措施:1. 合理选择骨料:骨料的粒径和形状对混凝土的均匀性有重要影响。
合理选择骨料可以增加混凝土的内聚力,减少离析风险。
2. 控制水灰比:合理控制水灰比可以保证混凝土的流动性和均匀性。
过高的水灰比会导致混凝土流动性过大,易发生离析;而过低的水灰比则会导致混凝土凝结困难,同样容易出现离析现象。
3. 均匀搅拌:在混凝土的搅拌过程中,应确保骨料和水泥充分混合,避免出现局部浆体粘度过高或过低的情况。
4. 控制浇筑速度:在混凝土浇筑过程中,应控制浇筑速度,避免过快或过慢。
过快的浇筑速度会导致混凝土内部的颗粒和水分难以均匀分布,而过慢则会导致混凝土过早凝结,同样易发生离析。
5. 控制环境温湿度:在施工过程中,应注意控制环境温度和湿度。
可以采取遮阳、喷水等措施,以保持适宜的施工条件,防止混凝土过早脱水和凝结。
混凝土离析是混凝土施工中常见的质量问题,其主要原因包括骨料选择、水泥浆体粘度、浇筑方式和环境温湿度等。
混凝土离析的原因及补救方法

混凝土离析的原因及补救方法混凝土离析是指混凝土中的骨料和水泥浆体分离的现象,这种问题在混凝土施工中经常出现,严重影响混凝土的质量和使用性能。
混凝土离析的原因主要包括以下几个方面,水灰比偏高、振捣不当、骨料粒径差异、施工工艺不当等。
首先,水灰比偏高是引起混凝土离析的重要原因之一。
过高的水灰比会导致混凝土的流动性增加,但同时也会降低混凝土的抗渗性和抗压强度,使得混凝土在振捣后容易发生离析现象。
其次,振捣不当也是混凝土离析的原因之一。
在混凝土施工中,振捣是非常重要的一个环节,振捣不充分或者振捣时间过长都会导致混凝土的骨料和水泥浆体分离,从而引起离析。
另外,骨料粒径差异也会导致混凝土离析。
当混凝土中的骨料粒径差异较大时,容易造成骨料的沉积和分层,从而引起混凝土的离析现象。
此外,施工工艺不当也是引起混凝土离析的原因之一。
如在浇筑过程中未采取适当的措施防止混凝土的离析,或者浇筑过程中出现了过多的振捣次数和过长的振捣时间,都会导致混凝土的离析现象。
针对混凝土离析问题,我们可以采取一些有效的补救措施来解决。
首先,要合理控制水灰比,选择合适的外加剂来提高混凝土的流动性,同时保证混凝土的抗渗性和抗压强度。
其次,要加强对混凝土的振捣工艺管理,确保振捣的充分和均匀,避免振捣不当导致的离析问题。
另外,要合理选择骨料,控制骨料粒径差异,避免骨料的沉积和分层,减少混凝土的离析现象。
最后,要加强对施工工艺的管理,采取适当的措施防止混凝土的离析,确保混凝土的质量和施工效果。
总之,混凝土离析是混凝土施工中常见的质量问题,我们需要从水灰比、振捣、骨料选择和施工工艺等方面加强管理,采取有效的补救措施来解决混凝土离析问题,确保混凝土的质量和使用性能。
离析混凝土
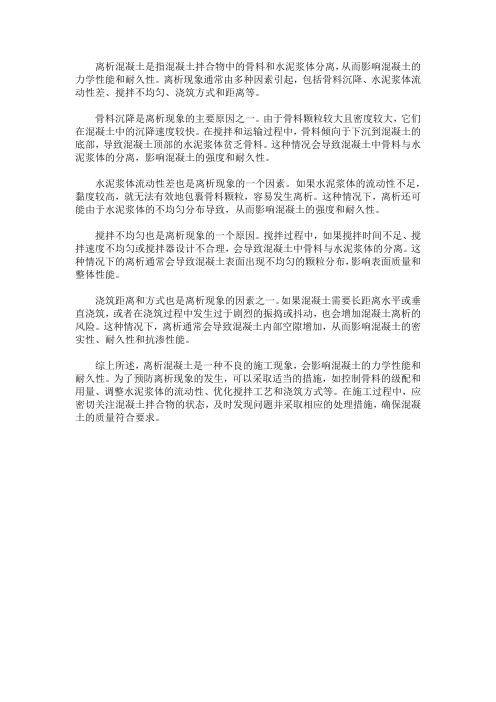
离析混凝土是指混凝土拌合物中的骨料和水泥浆体分离,从而影响混凝土的力学性能和耐久性。
离析现象通常由多种因素引起,包括骨料沉降、水泥浆体流动性差、搅拌不均匀、浇筑方式和距离等。
骨料沉降是离析现象的主要原因之一。
由于骨料颗粒较大且密度较大,它们在混凝土中的沉降速度较快。
在搅拌和运输过程中,骨料倾向于下沉到混凝土的底部,导致混凝土顶部的水泥浆体贫乏骨料。
这种情况会导致混凝土中骨料与水泥浆体的分离,影响混凝土的强度和耐久性。
水泥浆体流动性差也是离析现象的一个因素。
如果水泥浆体的流动性不足,黏度较高,就无法有效地包裹骨料颗粒,容易发生离析。
这种情况下,离析还可能由于水泥浆体的不均匀分布导致,从而影响混凝土的强度和耐久性。
搅拌不均匀也是离析现象的一个原因。
搅拌过程中,如果搅拌时间不足、搅拌速度不均匀或搅拌器设计不合理,会导致混凝土中骨料与水泥浆体的分离。
这种情况下的离析通常会导致混凝土表面出现不均匀的颗粒分布,影响表面质量和整体性能。
浇筑距离和方式也是离析现象的因素之一。
如果混凝土需要长距离水平或垂直浇筑,或者在浇筑过程中发生过于剧烈的振捣或抖动,也会增加混凝土离析的风险。
这种情况下,离析通常会导致混凝土内部空隙增加,从而影响混凝土的密实性、耐久性和抗渗性能。
综上所述,离析混凝土是一种不良的施工现象,会影响混凝土的力学性能和耐久性。
为了预防离析现象的发生,可以采取适当的措施,如控制骨料的级配和用量、调整水泥浆体的流动性、优化搅拌工艺和浇筑方式等。
在施工过程中,应密切关注混凝土拌合物的状态,及时发现问题并采取相应的处理措施,确保混凝土的质量符合要求。
水泥混凝土常见问题分析和处理

水泥混凝土常见问题分析和处理吴守民在水泥混凝土生产过程中常常会发生一些问题,个人根据实践和参考相关资料总结出来的一些看法和认识。
一.混凝土离析离析是混凝土混合料各组分之间的粘结力不足以抵抗粗集料下沉的现象。
主要是混凝土骨料的离析、分层、底抓、硬化、放水、施工性差。
混凝土离析会造成混凝土性能各个方面的下降。
具体影响如下:影响混凝土的可泵性能,造成堵管、卡罐,影响工期,降低经济效益。
影响混凝土外观,造成混凝土表面出现砂线、露骨料、露筋等现象。
降低混凝土强度,影响混凝土结构的承载能力,破坏结构的安全性能,甚至造成返工。
混凝土均匀性差,混凝土各部位的收缩不一致,容易产生混凝土收缩裂缝。
水泥浆表面层较厚,导致混凝土表面收缩加大,造成开裂。
5. 极大地降低了混凝土抗渗、抗冻等混凝土的耐久性能。
近年来随着水泥生产中大掺量的使用助磨剂和混合材以及天然砂石资源的日渐枯竭,粗细骨料质量下降原因,带来的混凝土泌水、板结、抓底的质量问题日益增多,已成为继混凝土的裂缝问题之后的第二大病害。
泌水、板结多发生于混凝土入静停状态,因此这一病害又常被称之为“滞后泌水”问题。
“泌水、板结”问题与日常所见的一般泌水现象不同。
在多组分混凝土中,由于各组分的密度不同,水的密度最小。
在混凝土进入模具后的静态状态下,或多或少的水总是浮在一起。
这种上升的现象叫“出血”。
混凝土表面的泌水是饱和氢氧化钙溶液,澄清透明。
只要水蒸发速率大于或等于泄流速度,混凝土表面就不会出现泄流现象。
只有当水的蒸发速率小于流血率时,混凝土表面才会有出血。
但这种泌水出现时混凝土浇筑已完成,砂石仍处于悬浮在水泥砂浆中,不会板结、抓底,不影响混凝土结构的正常凝结硬化,可以认为是正常现象。
“滞后泌水、板结”是指混凝土入模后或入模前,当混凝土处于静停状态时,水泥砂浆从粗骨料中分离析出,使粗骨料失去砂浆的包裹性而出现泌水、板结、抓底的现象。
因此,它不同于常见的混凝土少量泌水,它使混凝土分层,严重影响混凝土结构的匀质性,甚至蜂窝麻面,外观露砂、流痕(图2);在施工中因供料跟不上或因拆管的需要,在暂停时会因“泌水、板结”问题而造成堵管施工事故;特别是钻孔灌注桩结构可能引起工程质量事故。
混凝土中的离析现象原理

混凝土中的离析现象原理混凝土是一种常用的建筑材料,经常用于建造房屋、桥梁、道路等基础设施,但是在混凝土使用过程中,会出现一种叫做离析的现象。
离析是指混凝土中的水泥砂浆与骨料分离,砂浆部分沉降到混凝土底部,而骨料则漂浮到混凝土表面。
离析会影响混凝土的强度和耐久性,因此需要了解离析现象的原理,以便采取措施避免离析的发生。
混凝土中的离析现象是由多种因素共同作用造成的。
首先,混凝土中的骨料具有不同的密度和形状,在混凝土振捣时,骨料会相互碰撞摩擦,产生一定的分离力,导致砂浆与骨料分离。
其次,混凝土中的水泥砂浆含有一定的水分,当混凝土振捣时,水分会被挤压出来,使得砂浆流动性增强,易于分离。
此外,混凝土的振捣方式、振动频率、振动时间等因素也会影响离析现象的发生。
混凝土中离析现象的发生与混凝土的配合比例有关。
如果水泥砂浆的含水量过高,砂浆流动性增强,易于分离。
相反,如果水泥砂浆的含水量过低,混凝土的可塑性减弱,易于发生裂缝,也会影响混凝土的强度和耐久性。
因此,在配制混凝土时,需要根据实际情况控制好水泥砂浆的含水量,以避免离析现象的发生。
除了配合比例外,混凝土中的离析现象还与骨料的选用有关。
骨料的粒径、含水量、表面状态等因素会影响混凝土的流动性和分离力,从而影响离析现象的发生。
一般来说,骨料的粒径越小,含水量越高,表面状态越差,混凝土的离析现象就越容易发生。
因此,在选择骨料时,需要考虑骨料的物理性质和化学性质,以避免离析现象的发生。
最后,混凝土的振捣方式也会影响离析现象的发生。
混凝土的振捣可以采用手工振捣或机械振捣,机械振捣可以分为内振和外振两种方式。
内振是指将振动器插入混凝土中进行振动,外振是指在混凝土表面放置振动器进行振动。
一般来说,内振比外振更容易引起混凝土的离析现象。
因此,在振捣混凝土时,需要根据实际情况选择合适的振捣方式,以避免离析现象的发生。
综上所述,混凝土中的离析现象是由多种因素共同作用造成的。
在混凝土的配制、骨料的选用、振捣方式等方面需要注意控制,以避免离析现象的发生。
混凝土的离析现象

混凝土的离析现象
混凝土是建筑、道路、桥梁等工程中常用的一种基础材料,但是
在混凝土的制作、施工和使用过程中,常常出现离析现象。
离析是指混凝土中骨料与水泥浆分离的现象。
当混凝土中的骨料
重量过大、水泥含量过低或施工时震动不充分,都容易发生离析。
离
析现象导致混凝土质量下降,影响工程的使用寿命和安全性。
因此,
减少混凝土离析是一个非常关键的问题。
那么,如何降低混凝土的离析现象呢?
首先,在混合骨料时,需要将粗细骨料按照一定比例搭配,以免
骨料重量过于不平衡导致离析。
其次,配合比要科学合理,水泥含量
应该控制在一定范围内。
施工过程要求敲打,在混凝土中减少孔隙和
空隙,增强混凝土的紧密性,减少离析的可能性。
最后,可以在原有
的配方基础上添加减水剂等化学剂,调整混凝土的流动性和稳定性,
降低混凝土的离析现象。
除此之外,我们还需要保持施工现场整洁,尽可能减少杂物掺杂。
同时,也需要注意防止因振动、倾斜等原因引起模板倾斜,造成混凝
土流失和离析现象。
总之,混凝土的离析现象是工程中的常见问题,但我们可以通过
科学的配合比、施工技术和控制条件,在工程中减少甚至避免离析的
发生,确保建筑物的质量和安全。
混凝土离析原因及危害
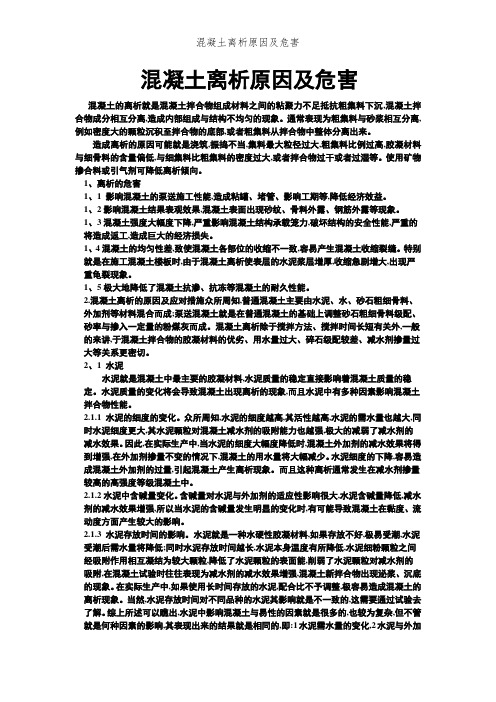
混凝土离析原因及危害混凝土的离析就是混凝土拌合物组成材料之间的粘聚力不足抵抗粗集料下沉,混凝土拌合物成分相互分离,造成内部组成与结构不均匀的现象。
通常表现为粗集料与砂浆相互分离,例如密度大的颗粒沉积至拌合物的底部,或者粗集料从拌合物中整体分离出来。
造成离析的原因可能就是浇筑,振捣不当,集料最大粒径过大,粗集料比例过高,胶凝材料与细骨料的含量偏低,与细集料比粗集料的密度过大,或者拌合物过干或者过湿等。
使用矿物掺合料或引气剂可降低离析倾向。
1、离析的危害1、1 影响混凝土的泵送施工性能,造成粘罐、堵管、影响工期等,降低经济效益。
1、2影响混凝土结果表观效果,混凝土表面出现砂纹、骨料外露、钢筋外露等现象。
1、3混凝土强度大幅度下降,严重影响混凝土结构承载笼力,破坏结构的安全性能,严重的将造成返工,造成巨大的经济损失。
1、4混凝土的均匀性差,致使混凝土各部位的收缩不一致,容易产生混凝土收缩裂缝。
特别就是在施工混凝土楼板时,由于混凝土离析使表层的水泥浆层增厚,收缩急剧增大,出现严重龟裂现象。
1、5极大地降低了混凝土抗渗、抗冻等混凝土的耐久性能。
2.混凝土离析的原因及应对措施众所周知,普通混凝土主要由水泥、水、砂石粗细骨料、外加剂等材料混合而成;泵送混凝土就是在普通混凝土的基础上调整砂石粗细骨料级配、砂率与掺入一定量的粉煤灰而成。
混凝土离析除于搅拌方法、搅拌时间长短有关外,一般的来讲,于混凝土拌合物的胶凝材料的优劣、用水量过大、碎石级配较差、减水剂掺量过大等关系更密切。
2、1 水泥水泥就是混凝土中最主要的胶凝材料,水泥质量的稳定直接影响着混凝土质量的稳定。
水泥质量的变化将会导致混凝土出现离析的现象,而且水泥中有多种因素影响混凝土拌合物性能。
2.1.1 水泥的细度的变化。
众所周知,水泥的细度越高,其活性越高,水泥的需水量也越大,同时水泥细度更大,其水泥颗粒对混凝土减水剂的吸附能力也越强,极大的减弱了减水剂的减水效果。
混凝土离析性能评估标准
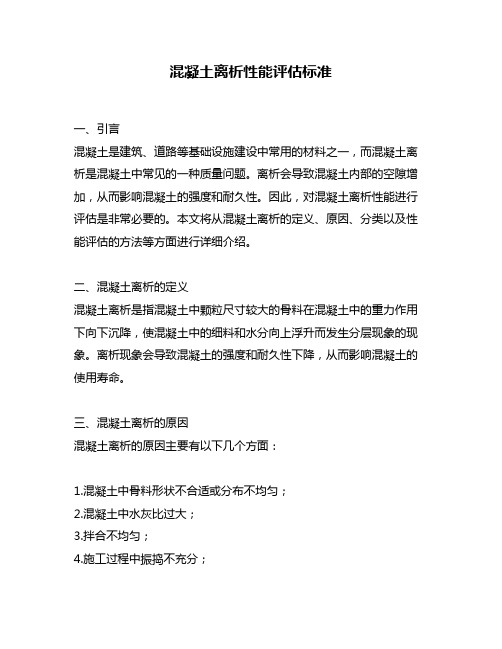
混凝土离析性能评估标准一、引言混凝土是建筑、道路等基础设施建设中常用的材料之一,而混凝土离析是混凝土中常见的一种质量问题。
离析会导致混凝土内部的空隙增加,从而影响混凝土的强度和耐久性。
因此,对混凝土离析性能进行评估是非常必要的。
本文将从混凝土离析的定义、原因、分类以及性能评估的方法等方面进行详细介绍。
二、混凝土离析的定义混凝土离析是指混凝土中颗粒尺寸较大的骨料在混凝土中的重力作用下向下沉降,使混凝土中的细料和水分向上浮升而发生分层现象的现象。
离析现象会导致混凝土的强度和耐久性下降,从而影响混凝土的使用寿命。
三、混凝土离析的原因混凝土离析的原因主要有以下几个方面:1.混凝土中骨料形状不合适或分布不均匀;2.混凝土中水灰比过大;3.拌合不均匀;4.施工过程中振捣不充分;5.温度变化引起的收缩和膨胀;6.混凝土养护不当;7.过度流动性。
四、混凝土离析的分类根据混凝土中骨料的尺寸和密度不同,混凝土离析可以分为以下几种类型:1.重力离析:混凝土中骨料的密度大于混凝土中水浆的密度,骨料会向下沉降,使水浆向上浮升。
2.浮力离析:混凝土中骨料的密度小于混凝土中水浆的密度,骨料会向上浮升,使水浆向下沉降。
3.干缩离析:混凝土中水分蒸发后,混凝土表面变干,使水分向表面移动,造成表面上的混凝土与底部混凝土之间出现空隙,发生干缩离析。
4.温度离析:混凝土在不同温度下收缩和膨胀的速度不同,使混凝土发生分层现象。
五、混凝土离析性能评估的方法混凝土离析性能评估的方法主要包括以下几个方面:1.观察法:通过肉眼观察混凝土表面是否有分层现象,对混凝土离析情况进行初步判断。
2.水浸法:将混凝土样品浸泡在水中,观察是否有细料浮出,从而判断混凝土是否发生离析。
3.压实法:将混凝土样品进行压实,观察是否有分层现象,从而判断混凝土离析情况。
4.超声波检测法:利用超声波探测仪对混凝土进行检测,测量混凝土中声速的变化,从而判断混凝土的离析情况。
水泥混凝土离析的六大原因

水泥混凝土离析的六大原因混凝土离析是指拌合物组成材料之间的粘聚力不足,拌合物成分相互分离,粗集料下沉、砂浆上浮,以致造成混凝土硬化后出现蜂窝、麻面、薄弱夹层等质量缺陷的现象。
导致混凝土出现离析主要有六大原因:一、水泥:水泥质量的稳定直接影响着混凝土质量的稳定,水泥质量的变化有可能会导致混凝土出现离析。
1、水泥细度的变化:水泥细度越高,其活性越高,需水量也越大,水泥颗粒对减水剂的吸附能力也越强,能明显减弱减水剂的减水效果。
因此,当水泥细度突然降低时,外加剂的减水效果会明显增强。
此时,如果外加剂掺量不变,混凝土的用水量将大幅度减少。
如果不及时调整,容易造成外加剂用量过大,产生离析。
2、水泥含碱量的变化:碱含量对水泥与外加剂的适应性影响很大,含碱量降低,减水剂的减水效果增强。
当水泥的含碱量发生明显变化时,可能对混凝土的黏度、流动度产生较大的影响,产生离析。
3、水泥保管与存放时间:水泥如果保管不好,极易受潮,受潮后需水量将降低。
水泥存放时间越长,颗粒之间经吸附作用互相凝结为较大颗粒,降低了水泥颗粒的表面能,削弱了水泥颗粒对减水剂的吸附,表现为减水剂的减水效果增强。
如果不及时调整,容易造成外加剂用量过大,产生离析。
二、外加剂:混凝土减水剂的掺量过大,减水率过高,单方混凝土的用水量减少,有可能使减水剂在搅拌机内没有充分发挥作用,而在运输过程中不断的发生作用,致使混凝土到现场的坍落度大于出机时的坍落度,产生离析。
三、粉煤灰:粉煤灰是混凝土重要的掺和料之一,能极大改善混凝土和易性、密实性及强度性能。
如果粉煤灰质量波动较大,则混凝土质量控制的难度增大,容易产生离析。
1、当粉煤灰的质量突然变好时(如细度从19%变为4%),粉煤灰的需水量降低很大,容易造成混凝土出现离析。
2、当粉煤灰的质量突然变差时(如细度从19%变为38%),由于粉煤灰的很大一部分已失去胶结料的功能,因而外加剂相对胶结料掺量实际上是提高了,容易出现离析。
混凝土离析原理及预防措施

混凝土离析原理及预防措施一、混凝土离析的定义及背景混凝土离析是指混凝土中较大的颗粒物质在振动或水平面倾斜的作用下向上浮动,较小的颗粒物质则被挤向下方,最终导致混凝土中颗粒物质的分层现象。
混凝土离析的存在会影响混凝土的强度、耐久性和使用寿命,因此,混凝土离析的预防和控制是混凝土工程中十分重要的一环。
二、混凝土离析的原因混凝土离析的原因主要有以下几点:1.水灰比过大:水灰比过大会导致混凝土中水分过多,混凝土的稠度降低,加之振动力度不足,混凝土中的颗粒物质难以均匀分布,从而导致离析现象的发生。
2.颗粒物质过大或过小:颗粒物质过大或过小会导致混凝土的稠度不均匀,从而导致混凝土离析。
3.混凝土中添加的外加剂质量不合格:混凝土中添加的外加剂质量不合格会导致混凝土的稳定性下降,从而引起混凝土离析。
4.振动方式不正确:振动方式不正确会导致混凝土中颗粒物质的分布不均匀,从而引起混凝土离析。
5.温度和湿度变化:温度和湿度变化会导致混凝土中水分的变化,从而引起混凝土离析。
三、混凝土离析的预防措施为了避免混凝土离析,需要采取以下预防措施:1.控制水灰比:通过控制水灰比,可以控制混凝土的稠度,从而防止混凝土离析。
2.控制颗粒物质大小:通过控制颗粒物质的大小,可以控制混凝土的稠度,从而防止混凝土离析。
3.选择合格的外加剂:选择合格的外加剂可以提高混凝土的稳定性,从而防止混凝土离析。
4.正确的振动方式:通过采用正确的振动方式,可以使混凝土中颗粒物质分布均匀,从而防止混凝土离析。
5.调整施工时间:调整施工时间可以避免在高温和潮湿的环境下施工,从而防止混凝土离析。
6.加入防离析剂:加入防离析剂可以提高混凝土的流动性和稳定性,从而防止混凝土离析。
四、混凝土离析的处理方法如果混凝土已经发生了离析现象,需要采取以下处理方法:1.重新振动:重新振动可以使混凝土中颗粒物质重新分布,从而消除离析现象。
2.加入水泥石灰浆:加入水泥石灰浆可以使混凝土中的颗粒物质重新结合,从而消除离析现象。
什么是混凝土的离析现象完整版

什么是混凝土的离析现象HEN system office room 【HEN16H-HENS2AHENS8Q8-HENH1688】什么是混凝土的离析现象?混凝土离析是指粗骨料与细骨料分离。
离析后会影响混凝土的浇筑质量,降低强度,造成粗骨料堆积,形象的说就是骨肉分离。
混凝土搅拌时配合比计量要准确,保证搅拌时间一般为90s,控制好坍落度,混凝土自由下落高度不能超过2m,如果浇筑超过2m的可以用溜槽,溜筒等辅助工具。
混凝土拌和物离析的定义,形式及产生原因?上下密度不一,(下大上小)粗细骨料分布不均,混凝土坍塌度过大。
形式表现为下面都是粗骨料。
中间是细骨料。
上面是沙浆。
最上面是水。
原因是在搅和混凝土的过程中参水比例过大。
混凝土离析和泌水的定义1.混凝土离析是指粗骨料与细骨料分离。
离析后会影响混凝土的浇筑质量,降低强度,造成粗骨料堆积,形象的说就是骨肉分离。
混凝土搅拌时配合比计量要准确,保证搅拌时间一般为90s,控制好坍落度,混凝土自由下落高度不能超过2m,如果浇筑超过2m的可以用溜槽,溜筒等辅助工具。
2.混凝土在运输、振捣、泵送的过程中出现粗骨料下沉,水分上浮的现象称为混凝土泌水。
泌水是新拌混凝土工作性一个重要方面。
通常,描述混凝土泌水特性的指标有泌水量(即混凝土拌和物单位面积的平均泌水量)和泌水率(即泌水量对混凝土拌和物之比含水量之比)。
混凝土施工泌水的原因是什么?当前工程施工中发现混凝土有分层离析现象,怎么解决啊?在混凝土施工过程中,通常会出现在运输、振捣、泵送的过程中出现粗骨料下沉,水分上浮的现象称为混凝土泌水。
泌水是新拌混凝土工作性一个重要方面。
通常,描述混凝土泌水特性的指标有泌水量(即混凝土拌和物单位面积的平均泌水量)和泌水率(即泌水量对混凝土拌和物之比含水量之比)。
解决办法:降低混凝土的水灰比增加大骨料减少含气量加强振捣混凝土泌水什么原因?水泥与外加剂适应性不好,如何解决、?石子的颗粒级配是和1-3的石子,请高手解答水泥与外加剂适应性不好,是要外加剂厂家来人调的,这个不是问题。
混凝土的离析名词解释
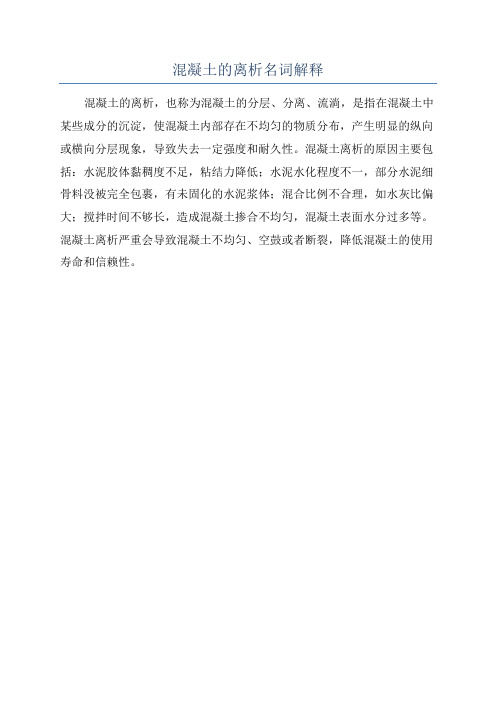
混凝土的离析名词解释
混凝土的离析,也称为混凝土的分层、分离、流淌,是指在混凝土中某些成分的沉淀,使混凝土内部存在不均匀的物质分布,产生明显的纵向或横向分层现象,导致失去一定强度和耐久性。
混凝土离析的原因主要包括:水泥胶体黏稠度不足,粘结力降低;水泥水化程度不一,部分水泥细骨料没被完全包裹,有未固化的水泥浆体;混合比例不合理,如水灰比偏大;搅拌时间不够长,造成混凝土掺合不均匀,混凝土表面水分过多等。
混凝土离析严重会导致混凝土不均匀、空鼓或者断裂,降低混凝土的使用寿命和信赖性。
混凝土离析性能检测规范

混凝土离析性能检测规范混凝土离析性能检测规范1. 引言混凝土离析性是指混凝土在浇筑过程中发生的固体颗粒与水分的分离现象。
离析性的存在会对混凝土的强度、耐久性和外观造成不良影响。
准确评估和检测混凝土离析性对确保混凝土结构的质量至关重要。
本文将介绍混凝土离析性能检测规范,以帮助大家更好地理解和应用相关标准。
2. 背景混凝土离析性是由于混凝土中的固体颗粒沉积、水分分离或流动造成的。
当水分向上升或流动时,会引起较大颗粒在混凝土表面聚集,从而导致离析现象。
离析性的存在对于混凝土结构的质量和性能有不利影响,例如降低强度、损坏混凝土表面的外观和导致耐久性问题。
3. 混凝土离析性能检测规范3.1 检测方法混凝土离析性能检测可以采用以下方法之一或结合使用:(1) 观察法:通过裸眼观察混凝土表面是否出现分离、沉积或流动现象。
(2) 镜面法:在混凝土表面放置平整镜子,观察镜像中是否存在离析现象。
(3) 拉绳法:将一根细绳横放在混凝土表面,通过观察绳子表面是否出现分离或沉积现象来评估离析性能。
(4) 砂带法:将一横切面砂带平放在混凝土表面,观察砂带是否被固体颗粒覆盖或水分分离。
3.2 评估标准混凝土离析性能的评估可以根据以下几个方面进行:3.2.1 离析程度离析程度是指混凝土表面的固体颗粒沉积或流动的程度,通常用四级制进行分类:(1) 0级:无离析现象,表面平整均匀。
(2) 1级:轻微离析现象,有些细颗粒沉积。
(3) 2级:中度离析现象,较多的颗粒沉积和流动。
(4) 3级:严重离析现象,大量颗粒沉积和流动。
3.2.2 局部性局部性指离析现象的集中程度,包括:(1) 广泛性:离析现象分布范围广泛,覆盖整个混凝土表面。
(2) 局部性:离析现象分布范围局部,只出现在混凝土表面的特定区域。
3.2.3 深度深度是指固体颗粒沉积或流动的程度,可通过测量最大沉积深度或流动距离来评估。
4. 标准解读与应用4.1 标准编号和名称混凝土离析性能检测的标准编号和名称为:标准编号:GB/T 50080-2016标准名称:混凝土铺面沉陷、裂缝和离析检测与评定标准4.2 标准要求该标准规定了混凝土铺面离析性能的检测方法、评定标准及分类要求。
混凝土离析性能评估标准
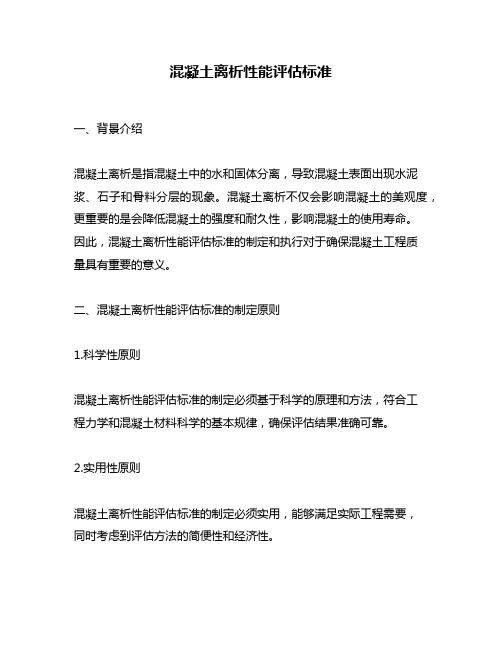
混凝土离析性能评估标准一、背景介绍混凝土离析是指混凝土中的水和固体分离,导致混凝土表面出现水泥浆、石子和骨料分层的现象。
混凝土离析不仅会影响混凝土的美观度,更重要的是会降低混凝土的强度和耐久性,影响混凝土的使用寿命。
因此,混凝土离析性能评估标准的制定和执行对于确保混凝土工程质量具有重要的意义。
二、混凝土离析性能评估标准的制定原则1.科学性原则混凝土离析性能评估标准的制定必须基于科学的原理和方法,符合工程力学和混凝土材料科学的基本规律,确保评估结果准确可靠。
2.实用性原则混凝土离析性能评估标准的制定必须实用,能够满足实际工程需要,同时考虑到评估方法的简便性和经济性。
3.可操作性原则混凝土离析性能评估标准的制定必须考虑到具体操作的可行性,能够方便地应用于工程实践中,同时考虑到人力、物力和财力等方面的限制。
三、混凝土离析性能评估标准的主要内容1.定义和分类混凝土离析是指混凝土中水泥浆、石子和骨料分层的现象。
根据混凝土离析的程度和类型,可以将其分为轻度离析、中度离析和严重离析等不同类型。
2.检测方法混凝土离析性能评估需要进行一系列的检测,主要包括外观观察、厚度测量、渗透性测定、力学性能测试等多个方面。
其中,外观观察为最基本的检测方法,可以直观地判断混凝土是否发生离析现象。
渗透性测定可以检测混凝土的水渗透性,进一步评估离析深度和程度。
力学性能测试可以评估混凝土的强度和耐久性,对于混凝土离析性能的评估具有重要的作用。
3.评估指标混凝土离析性能评估的主要指标包括离析深度、离析程度、渗透性、强度和耐久性等多个方面。
其中,离析深度和离析程度是评估离析性能的基本指标。
渗透性可以进一步评估离析的程度和深度。
强度和耐久性是评估混凝土离析性能的重要指标,可以反映混凝土的使用寿命和安全性。
4.评估结果的判定根据评估指标的不同,混凝土离析性能评估的结果也会有所不同。
根据评估结果的不同,可以将混凝土分为优良、合格、亚合格和不合格等不同等级。
什么是混凝土的离析现象

什么是混凝土的离析现象混凝土离析是指粗骨料与细骨料分离。
离析后会影响混凝土的浇筑质量,降低强度,造成粗骨料堆积,形象的说就是骨肉分离。
混凝土搅拌时配合比计量要准确,保证搅拌时间一般为90s,控制好坍落度,混凝土自由下落高度不能超过2m如果浇筑超过2m的可以用溜槽,溜筒等辅助工具。
混凝土拌和物离析的定义,形式及产生原因上下密度不一,(下大上小)粗细骨料分布不均,混凝土坍塌度过大。
形式表现为下面都是粗骨料。
中间是细骨料。
上面是沙浆。
最上面是水。
原因是在搅和混凝土的过程中参水比例过大。
混凝土离析和泌水的定义1.混凝土离析是指粗骨料与细骨料分离。
离析后会影响混凝土的浇筑质量,降低强度,造成粗骨料堆积,形象的说就是骨肉分离。
混凝土搅拌时配合比计量要准确,保证搅拌时间一般为90s,控制好坍落度,混凝土自由下落高度不能超过2m如果浇筑超过2m的可以用溜槽,溜筒等辅助工具。
2.混凝土在运输、振捣、泵送的过程中出现粗骨料下沉,水分上浮的现象称为混凝土泌水。
泌水是新拌混凝土工作性一个重要方面。
通常,描述混凝土泌水特性的指标有泌水量(即混凝土拌和物单位面积的平均泌水量)和泌水率(即泌水量对混凝土拌和物之比含水量之比)。
混凝土施工泌水的原因是什么当前工程施工中发现混凝土有分层离析现象,怎么解决啊在混凝土施工过程中,通常会出现在运输、振捣、泵送的过程中出现粗骨料下沉,水分上浮的现象称为混凝土泌水。
泌水是新拌混凝土工作性一个重要方面。
通常,描述混凝土泌水特性的指标有泌水量(即混凝土拌和物单位面积的平均泌水量)和泌水率(即泌水量对混凝土拌和物之比含水量之比)。
解决办法:降低混凝土的水灰比增加大骨料减少含气量加强振捣混凝土泌水什么原因水泥与外加剂适应性不好,如何解决、石子的颗粒级配是和1-3的石子,请高手解答水泥与外加剂适应性不好,是要外加剂厂家来人调的,这个不是问题。
混凝土泌水,这个首先你可以做一下外加剂的压力泌水和常压泌水试验,看看是不是外加剂的问题,如果不是那,你就要检查自己的配合比了,看看砂率够不够了,骨料级配合不合适,骨料吸水率,适当的减少一点水泥浆,这个泌水如果不是外加剂的问题多数就是砂率,或者矿物掺合料的掺量了,你可以试试, 主要是我不知道你所说的泌水是混凝土在什么状态上出现的泌水。
- 1、下载文档前请自行甄别文档内容的完整性,平台不提供额外的编辑、内容补充、找答案等附加服务。
- 2、"仅部分预览"的文档,不可在线预览部分如存在完整性等问题,可反馈申请退款(可完整预览的文档不适用该条件!)。
- 3、如文档侵犯您的权益,请联系客服反馈,我们会尽快为您处理(人工客服工作时间:9:00-18:30)。
什么是混凝土的离析现象?
混凝土离析是指粗骨料与细骨料分离。
离析后会影响混凝土的浇筑质量,降低强度,造成粗骨料堆积,形象的说就是
骨肉分离。
混凝土搅拌时配合比计量要准确,保证搅拌时间一般为90s,控制好坍落度,
混凝土自由下落高度不能超过2m,如果浇筑超过2m的可以用溜槽,溜筒等辅助工具。
混凝土拌和物离析的定义,形式及产生原因?
上下密度不一,(下大上小)粗细骨料分布不均,混凝土坍塌度过大。
形式表
现为下面都是粗骨料。
中间是细骨料。
上面是沙浆。
最上面是水。
原因是在搅和混凝土的过程中参水比例过大。
混凝土离析和泌水的定义
1.混凝土离析是指粗骨料与细骨料分离。
离析后会影响混凝土的浇筑质量,降低强度,造成粗骨料堆积,形象的说就是
骨肉分离。
混凝土搅拌时配合比计量要准确,保证搅拌时间一般为90s,控制好坍落度,
混凝土自由下落高度不能超过2m,如果浇筑超过2m的可以用溜槽,溜筒等辅助工具。
2.混凝土在运输、振捣、泵送的过程中出现粗骨料下沉,水分上浮的现象称为
混凝土泌水。
泌水是新拌混凝土工作性一个重要方面。
通常,描述混凝土泌水特
性的指标有泌水量(即混凝土拌和物单位面积的平均泌水量)和泌水率(即泌水量
对混凝土拌和物之比含水量之比)。
混凝土施工泌水的原因是什么?当前工程施工中发现混凝土有分层离析现象,怎
么解决啊?
在混凝土施工过程中,通常会出现在运输、振捣、泵送的过程中出现粗骨料下沉,水分上浮的现象称为混凝土泌水。
泌水是新拌混凝土工作性一个重要方面。
通常,描述混凝土泌水特性的指标有泌水量(即混凝土拌和物单位面积的平均泌
水量)和泌水率(即泌水量对混凝土拌和物之比含水量之比)。
解决办法:
降低混凝土的水灰比
增加大骨料
减少含气量
加强振捣
混凝土泌水什么原因?水泥与外加剂适应性不好,如何解决、?石子的颗粒级配
是0.5和1-3的石子,请高手解答
水泥与外加剂适应性不好,是要外加剂厂家来人调的,这个不是问题。
混凝土泌水,这个首先你可以做一下外加剂的压力泌水和常压泌水试验,看看
是不是外加剂的问题,如果不是那,你就要检查自己的配合比了,看看砂率够
不够了,骨料级配合不合适,骨料吸水率,适当的减少一点水泥浆,这个泌水
如果不是外加剂的问题多数就是砂率,或者矿物掺合料的掺量了,你可以试试,主要是我不知道你所说的泌水是混凝土在什么状态上出现的泌水。
水泥混凝土表观密度怎么算(水泥:砂:石子:水:外加剂:外掺料
=367:746:1096:160:3.56:78)
一般做法:在做配合比设计的时候可以假设一个表观密度,一般2400左右。
然后在做混凝土试配后,实测混凝土表观密度。
根据实测的数据调整配合比。
通常砂石的密度、集浆比、含气量等都会影响混凝土的表观密度。
混凝土水泥
用量越大,混凝土表观密度越大。