机车单元制动器
某型出口机车用单元制动器故障原因分析及处理

图1防尘套破损及污物进入情况检查时还发现,在加强型支架的下方复位弹簧处存在较多污物(见图,这会造成运动阻力加大,导致闸瓦托复位困难。
此外,闸瓦托上安装的V 形体与调整螺杆的头部本应贴合在一起,但在故障单元制动器上却发生了完全脱离。
V 形体翻转90度,完全失去了限制调整螺杆旋转的功能。
(图3)进一步拆解制动单元,在与皮碗共同组成密封结构的气缸衬套内表面发现有沙粒、灰尘等污物存在,并有明显的划痕,这将直接导致密封失效,造成压缩空气的泄漏。
此外,在拆解中还发现呼吸器存在严重堵塞现象,其他零件未见异常。
我们将故障单元制动器解体清洗,清除污物并更换沙土进入单元制动器内部,致使皮碗和气缸衬套发生严造成制动缸漏风。
污物进入会同时导致制动缸内零件运动阻力增大,造成缓解卡滞,污物进入过多时甚至会使零件受力异常造成损坏。
因防尘套未见老化现象,所以防尘套的破损和丢失很可能是意外受到外力作用导致的。
分析造成防尘套破损的原因存在以下几种可能性:防尘套意外受到外力的直接作用造成损伤,比如尖锐物体的刮划导致破损。
呼吸器被严重堵塞会造成制动时排风不畅,进而导制动缸充风,在风压作用下制动鞲———————————————————————作者简介:王国明(1979-),男,吉林舒兰人,中车大连机车车辆高级工程师,工程硕士,研究于春生(1988-),男,辽宁林中车大连机车车辆有限公司机械装备分厂,研究方向为机械装配。
图2复位弹簧状态图3V 形体状态图4防尘套工作状态示意图风;同时污物也造成制动缸内零件运动阻力增大,造成了缓解卡滞;污物进入过多时甚至会使零件受力异常造成损坏。
该型机车用于煤炭运输,工作环境中的粉尘远大于一般线路,这也加重了污物积聚和进入单元制动器的程度。
3整改措施①首先针对防尘套受外力直接作用造成破损的情况,需用户加强对防尘套的检查维护。
日常应关注防尘套状态,检查是否有破损情况,存在防尘套破损的单元制动器一经发现应尽快修理,避免故障现象的加剧。
单元制动器
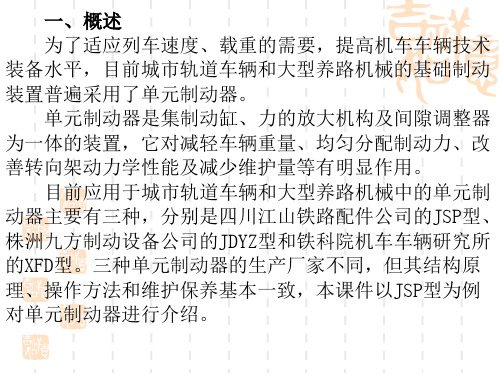
(7)产生弹性变形的制动行程: 当制动缸充入压缩空气时,间隙调整机构移动一段距离“A”后闸瓦贴敷在车
轮踏面上。闸瓦间隙调整机构继续向前移动,产生制动力,在制动力的作用下轮 对发生弹性变形“E”,这时在弹性变形反作用力下离合弹簧1被行程压缩,制动 盘2被夹紧,使导向螺母3不能转动,带动螺杆向前运动,引导齿座被调整后盖的 凹槽挡住不能再继续向前移动,导向螺母3随螺杆向前移动一段距离“E”。在缓 解时,螺杆往回移动一段距离“E”后弹性变形反作用力消失,制动盘2才能松开, 回到正常缓解状态。发生弹性变形这段距离“E”是不被调整补偿的。
3、弧形滑块式径向活动闸瓦托结构,能自动保持均匀闸瓦间隙,防 止闸瓦偏磨
弧形滑块式闸瓦托结构是调整螺杆与闸瓦托通过V型板簧和Ω 型弹簧及弧形 滑块组成的径向活动机构。在制动力作用下,闸瓦托的圆柱型曲面绕球向块转动 以适应闸瓦与踏面的吻合,同时在压簧作用下保持顶角的锁定,如图6所示。
此外,这种结构还有避免偏载、弯曲和冲击载荷的传递,防止调整螺杆弯曲 变形的特点。
2、行车制动缓解 制动缸压缩空气从P口排出,制动皮碗及楔角机构在复原 弹簧的作用下上移,滚动轴承和间隙调整器后退,带动调整螺 杆后退,从而实现了车辆的缓解。
3、停车制动
停车制动皮碗下方的压缩空气排出,停车制动皮碗在主弹簧作用力下迅速 下移,同时带动小调整螺杆下移,小调整螺经过中间隔板的通孔推动制动皮 碗及楔角机构下移,从而产生停车制动作用,如图3所示。
单元制动器内部结构:
塔式 弹簧
滚动轴承
制动 皮碗
停车制动 主弹簧
楔角 机构
间隙调 整器
固定轴承
手动缓 解装置
调整螺母
பைடு நூலகம்
中间隔板 进风口
高速列车单元制动器设计理论及应用

高速列车单元制动器设计理论及应用第一章引言高速列车单元制动器是火车的一项关键技术,起着保证乘客安全和加快列车速度的重要作用。
本文将着重探讨单元制动器的设计理论和应用。
第二章单元制动器的工作原理单元制动器是指每个车轮单独控制刹车的装置。
单元制动器由制动盘、制动鼓、制动爪及电机、减速器等组成。
当乘客需要通过踩制动踏板让火车缓慢停下时,控制系统会发出指令给车轮上的电机,电机通过减速器的作用让制动鼓、制动盘和制动爪共同协作完成刹车动作。
第三章单元制动器的设计理论3.1 制动盘的设计制动盘是刹车系统中的一个重要组成部分,其主要作用是承受制动力,并将制动力通过传动轴传送到车轮上。
为了保证制动盘的性能和可靠性,制动盘的选择和设计是非常关键的。
一般来说,制动盘的选用应该遵循以下几点原则:1)制动盘的厚度应该与车轮轮缘的宽度相当。
2)制动盘的材质要符合材料力学性能要求,并且抗疲劳性能要好。
3)制动盘的钳口与制动鼓(或轮辋)接触的面积要尽可能大,以提高制动效能和制动稳定性。
3.2 制动鼓的设计制动鼓是刹车系统中的重要组成部分,其主要作用是诱导制动力,并将制动力通过制动轮轴传送到车轮上。
制动鼓的外形和内部结构是直接影响制动力的大小和稳定性的因素。
一般来说,制动鼓的外形和内部结构应该符合以下要求:1)制动鼓的外形应该符合制动盘的中心对称。
制动鼓外形不对称会导致轴偏载荷增加。
2)制动鼓内部的通风道应当合理设置和设计,以提高制动稳定性和制动效率。
3)制动鼓内壁的表面硬度应该均匀,且波动度应小于等于0.05mm。
3.3 制动爪的设计制动爪是刹车系统中的一个重要组成部分,其主要作用是与制动盘或制动鼓接触,产生制动力。
通常制动爪分单边和双边,对于不同的列车制造商和列车模型,制动爪的设计也会有所不同。
一般来说,制动爪的设计应该符合以下要求:1)制动爪与制动盘或制动鼓的接触面积要足够大,以确保制动效率和制动稳定性。
2)制动爪的行程应该与制动盘或制动鼓能旋转的角度相匹配。
机车单元制动器
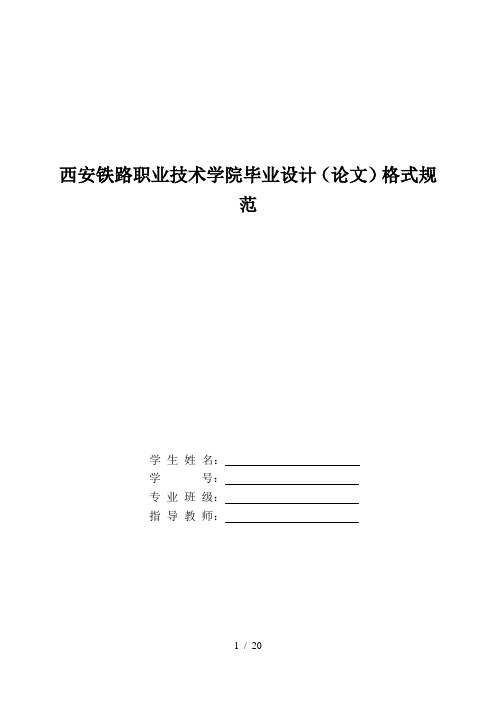
制动器的零部件在温度较低的条件下可能会发生性能上的改变,从而影响制动器的整机性能,因此对制动器须进行低温试验。为了模拟低温环境,制动器和风源系统均应在-40℃下保持一段时间,一般在48h以上。在低温环境下应对制动器进行所有性能试验和气密性试验。
2.3.6
型式试验是针对新研制的制动器,因此以上提到的所有试验均应涵盖在型式试验之中,同时建议型式试验还必须对关键零件的关键质量特性进行专项检
2技术标准探讨
2.1
2.1.1
当前使用的机车单元制动器的缸径规格主要有7寸,7.5寸8寸,其中以7寸缸使用最为广泛,也有采用6.5寸和8寸以上的。缸体直径的规格越少,互换性和简统化程度越高。缸体直径过小将影响制动缸的缓解和常用制动性能,而直径过大,则活塞杆过重,造成动作困难,易使皮碗变形和拉伤缸表面。因此建议制动缸的内径定为6.5寸,7寸,7.5寸,8寸等4个等级。
皮碗的结构种类较多,目前使用的L形皮碗运动阻力大,安装复杂,此结构原套用化工部标准,并不适合于单元制动器使用。国外制动器的皮碗基本上都采用钢骨架结构,其优点是安装、拆卸简便,定位精度高运动阻力小,国产JDYZ-4型制动器亦采用了这种结构,运用效果较好。建议新造制动器皮碗采用钢骨架式结构。
2
间隙调整器分为棘轮棘勾式和非自锁螺纹式两种
的安装一定要牢固、密贴,与闸瓦托的局部间隙不大于lmIn,另外还要保证在闸瓦磨耗到限后容易拆卸旧瓦和安装新瓦。由于理论上制动时闸瓦上下端存在不均匀的磨耗,必须时时保证闸瓦上下端与车轮的间隙均匀,则闸瓦托的定位应能调整闸瓦托的倾斜角度。闸瓦托安装后,与制动器箱体必须容许有少量的横动,以适应轮对与转向架构架的横动,一般情况下此值不小于2mIn。在用于三轴转向架中间轴的制动器应允许有更大的横动量,单侧制动时不小于4—5mIn,双侧制动时必须大于轮对与构架的横动量。国内就出现过因制动器横动量不足造成丝杆弯曲变形的现象,建议在技术标准中予以规定。
TJJW 044-2014 交流传动机车单元制动器暂行技术条件.

8. 2 气密性试验
8.2.1 常温低压气密性试验
2
TJ/JW 044-2014 在常温条件下 , 分别向单元制动器的制动缸、停放制动缸充入 100 kPa 的压缩空气 ,保压 3 min ,
测定 3 min 漏泄量。
8 .2.2 常温高压气密性试验 在常温条件下,分别向机车单元制动器的制动缸、停放制动缸充入 500 kPa 的压缩空气 ,保压 3 min ,
测试结果均应符合本文件 6. 2 、 6. 3 、 6. 5 及 6.6 、 6. 7 中常温条件下的规定,防尘套应无破损。
6. 11 有横移量要求的单元制动器(一般用于中间车轴〉的横移量要求应符合图样要求, 6.12 机车单元制动器的振动冲击试验应符合 GB/T 21563-2008 规定的 2 类试验工况。 6.13 铸钢件未注铸造尺寸公差按 GB/T 6414-1999 的 CT7 级执行。 6.14 传动零部件及机加工件未注形位公差按 GB/T 1184- 1996 的 k 级执行。 6.15 传动零部件及机加工件未注尺寸公差按 GB/T 1804-2000 的 m 级执行。
与
x
图 1 一次调整量、缓解间隙试验示意图
3
TJ/JW 044-2014 8.3.1.3 缓解间隙试验
缓解间隙测试应在闸瓦托组成推出 30 mm......80 rnrn 范围内进行,按 8. 3. 1. 2 测得的 13 与 12 的差值即
为缓解间隙。当闸瓦托组成推出量小于 30 mm 或大于 80 rnrn 时,测得的数据不作为判别依据。
l 范围. . . . . . . . . . . . . . . . . . . . . . . . . . . . . . . . . . . . . . . . . . . . . . . . . . . . . . . . . . . . . . . . . . . . . . . . . . . . .. 1 2 规范性引用文件. . . . . . . . . . . . . . . . . . . . . . . . . . . . . . . . . . . . . . . . . . . . . . . . . . . . . . . . . . . . . . . . . . .. 1 3 术语和定义. . . . . . . . . . . . . . . . . . . . . . . . . . . . . . . . . . . . . . . . . . . . . . . . . . . . . . . . . . . . . . . . . . . . . . . . 1 4 分类. . . . . . . . . . . . . . . . . . . . . . . . . . . . . . . . . . . . . . . . . . . . . . . . . . . . . . . . . . . . . . . . . . . . . . . . . . . . . . 1 5 应用环境....... . ...... . ....... ... ....... ... ..... .............. . .......... . I …… … …………….... 1 6 技术要求. . . . . . . . . . . . . . . . . . . . . . . . . . . . . . . . . . . . . . . . . . . . . . . . . . . . . . . . . . . . . . . . . . . . . . . . . . 1 7 制造要求. ... .... . .. . . . . .. ..... .. .. ..... ...... . . . .... .. . .. .. . .. .. . .. . .. . ., . ..... ... 2 8 试验方法.... .. .. ... .. . .... . ... ... ... . . . .... . . ...... . ....... ..... . .. . .. . . ... ....... 2 9 检验规则.... .. ......... ..... ........ . ... . .. . .. ..... . . ..... . ....... .... . . . ...... ... 5
机车单元制动器典型故障分析与处理
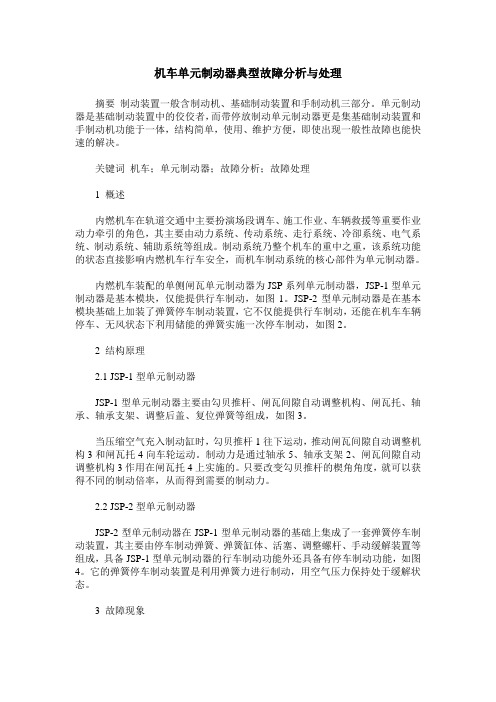
机车单元制动器典型故障分析与处理摘要制动装置一般含制动机、基础制动装置和手制动机三部分。
单元制动器是基础制动装置中的佼佼者,而带停放制动单元制动器更是集基础制动装置和手制动机功能于一体,结构简单,使用、维护方便,即使出现一般性故障也能快速的解决。
关键词机车;单元制动器;故障分析;故障处理1 概述内燃机车在轨道交通中主要扮演场段调车、施工作业、车辆救援等重要作业动力牵引的角色,其主要由动力系统、传动系统、走行系统、冷卻系统、电气系统、制动系统、辅助系统等组成。
制动系统乃整个机车的重中之重,该系统功能的状态直接影响内燃机车行车安全,而机车制动系统的核心部件为单元制动器。
内燃机车装配的单侧闸瓦单元制动器为JSP系列单元制动器,JSP-1型单元制动器是基本模块,仅能提供行车制动,如图1。
JSP-2型单元制动器是在基本模块基础上加装了弹簧停车制动装置,它不仅能提供行车制动,还能在机车车辆停车、无风状态下利用储能的弹簧实施一次停车制动,如图2。
2 结构原理2.1 JSP-1型单元制动器JSP-1型单元制动器主要由勾贝推杆、闸瓦间隙自动调整机构、闸瓦托、轴承、轴承支架、调整后盖、复位弹簧等组成,如图3。
当压缩空气充入制动缸时,勾贝推杆1往下运动,推动闸瓦间隙自动调整机构3和闸瓦托4向车轮运动。
制动力是通过轴承5、轴承支架2、闸瓦间隙自动调整机构3作用在闸瓦托4上实施的。
只要改变勾贝推杆的楔角角度,就可以获得不同的制动倍率,从而得到需要的制动力。
2.2 JSP-2型单元制动器JSP-2型单元制动器在JSP-1型单元制动器的基础上集成了一套弹簧停车制动装置,其主要由停车制动弹簧、弹簧缸体、活塞、调整螺杆、手动缓解装置等组成,具备JSP-1型单元制动器的行车制动功能外还具备有停车制动功能,如图4。
它的弹簧停车制动装置是利用弹簧力进行制动,用空气压力保持处于缓解状态。
3 故障现象在长期的使用过程中,单元制动器出现过闸瓦间隙过小、停放制动不缓解或者缓解过慢现象,现将一些常见故障现象以及分析处理方法整理如下,便于今后在使用、维修的过程中快速地解决类似问题(处理此类故障,机车均做了相应防护措施)。
hxn5b机车单元制动器卡滞原因及改善对策

HXN5B 机车单元制动器卡滞原因及改善对策彭家浪(中车戚墅堰机车有限公司国内贸易中心,江苏 常州 213011)摘要:本文主要阐述HXN5B 型内燃机车在运用过程中出现数起单元制动器卡滞、制动后缓解不正常的现象,通过对故障件及故障发生机理的深入分析发生问题的主要原因,针对调车机车工况、制动频繁等特殊运用条件上,对单元制动器卡滞、制动后缓解不正常并提出一些适应性改进。
提高运用可靠性。
关键词:单元制动器;制动;缓解;丝杆HXN5B 型交流传动调车内燃机车是为解决我国目前各编组站牵引定数不相匹配,解决运力瓶颈而研制的,适用于大、中型编组站的编组、调车作业及小运转。
机车采用踏面制动方式,从机车运用以来,装用的某公司生产的单元制动器发生制动缸不缓解质量问题。
1 单元制动器工作原理 机车基础制动装置是机车制动系统的主要组成部分,是满足机车紧急制动距离要求及确保机车行车安全的重要装置。
其工作的可靠性将直接影响机车运行安全,如果出现不缓解现象,严重情况下会导致机车动轮轮箍驰缓,甚至外窜等恶性事故。
HXN5B 机车采用气动操纵的踏面制动单元制动器。
HXN5B 机车用单元制动器主要结构如下:a1 闸瓦托 a2 弹簧闩或楔形制动块 a3 楔形闩 a4 制动闸瓦 b1 托架 b2 吊耳螺杆 b3 螺栓 b4 活塞销 b5 轴承销 d1 压紧环 d2 丝杆 e 带孔螺栓 f1 活塞回位弹簧 f2 扭转弹簧g1 外壳 g2 气缸盖 h1 吊耳 k1 活塞 k2 活塞皮碗k3 凸轮盘 q 波纹管 s 调节机构 s4 连杆头C 常用制动缸压缩空气接口 R 复位六角头图1 单元制动器结构示意图单元制动器的制动:(参见图1)进行制动时,压缩空气通过接口 C 流入制动气缸,并作用在活塞(k1)上,使之逆着活塞回位弹簧(f1)的弹力被向下压。
活塞的运动被传递给可在外壳 (g1)中转动的两个对称安装的凸轮盘(k3)。
丝杆(d2)在凸轮盘的弯道上滚动,从而整个调节机构(s)和闸瓦托(a1)被推入制 动位置。
机车单元制动器典型故障分析与处理

机车单元制动器典型故障分析与处理作者:张海东于春生高锋王明阳齐立志来源:《中国科技博览》2018年第07期[摘要]对于机车来说,制动装置是它最为关键的一个部分,关系到整个车辆的运行状况以及人员安危。
而对于机车的制动装置来说,一般分为三个部分,分别是制动机、基础的制动装置以及手动的制动机。
而在制动装置中,单元制动器则是整个制动装置的核心部分。
因此对于单元制动器的日常的检查和维修则是非常的重要,也是非常的必要的。
而本文主要从机车单元制动器典型的故障分析以及典型故障的处理方法来展开阐述。
[关键词]机车单元制动器故障分析故障处理中图分类号:U269.6 文献标识码:A 文章编号:1009-914X(2018)07-0267-01机车是现代的交通系统中一个非常重要的部分,在很多的场合都可以见到机车的身影,比如像很多的施工现场以及救援现场。
而对于一辆机车来说,制动装置则是组成它的最重要的部分,它的运行状态关系到整辆机车的行驶安全。
而同时单元制动器又是机车制动装置的一个核心组成部分,它的任何一个小的组成环节出现差错对于整辆机车来说都会很大的危害,这也就需要我们对于机车的单元制动器要做好经常的检查,这样的话才可以保证整辆车的正常运行。
然后在对于机车的单元制动器进行维修的时候则需要找专业的地方来进行维修,不可以随便找一些不专业不正规的场所来进行维修,这样的话只会使得机车的驾驶过程更加的危险。
一、机车单元制动器典型故障分析单元制动器是整个制动装置中的核心部分,而由于机车长时间的运行,也会使得机车的制动装置尤其是单元制动器会产生一些问题。
而对于机车的制动装置来说,一旦出现问题则需要及时的处理和解决,绝对不可以拖沓,否则很可能会发生更大的事故。
而对于机车的单元制动器来说,最典型的问题一般是轴箱拉杆定位装置不良的问题以及回位弹簧失效、机械卡滞现象以及停放制动不能缓解这三个问题,因此本文将从这三个问题开始展开论述。
1.1 轴箱拉杆定位装置不良对于大部分类型的机车来说,尤其是对于像HXD2C型机车这样的机车来说,它是属于是一种六轴式的货运型的汽车,而对于这种机车来说,轴箱拉杆的定位则是非常重要的,然而这种车由于经常会拉一些货物,所以某些环节则会非常容易老化。
某型机车单元制动器C5修故障研究及改进措施
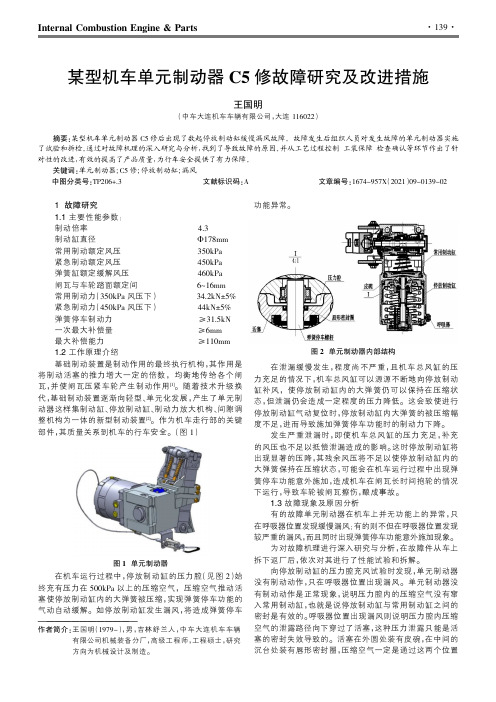
在机车运行过程中,停放制动缸的压力腔(见图终充有压力在500kPa以上的压缩空气,压缩空气推动活塞使停放制动缸内的大弹簧被压缩,实现弹簧停车功能的气动自动缓解。
如停放制动缸发生漏风,将造成弹簧停车在泄漏缓慢发生,程度尚不严重,且机车总风缸的压力充足的情况下,机车总风缸可以源源不断地向停放制动缸补风,使停放制动缸内的大弹簧仍可以保持在压缩状态,但泄漏仍会造成一定程度的压力降低。
这会致使进行停放制动缸气动复位时,停放制动缸内大弹簧的被压缩幅度不足,进而导致施加弹簧停车功能时的制动力下降。
发生严重泄漏时,即使机车总风缸的压力充足,补充的风压也不足以抵偿泄漏造成的影响。
这时停放制动缸将出现显著的压降,其残余风压将不足以使停放制动缸内的大弹簧保持在压缩状态,可能会在机车运行过程中出现弹簧停车功能意外施加,造成机车在闸瓦长时间抱轮的情况下运行,导致车轮被闸瓦擦伤,酿成事故。
1.3故障现象及原因分析有的故障单元制动器在机车上并无功能上的异常,只在呼吸器位置发现缓慢漏风;有的则不但在呼吸器位置发现较严重的漏风,而且同时出现弹簧停车功能意外施加现象。
图2单元制动器内部结构————————————————:王国明(1979-),男,吉林舒兰人,中车大连机车车辆有限公司机械装备分厂,高级工程师,工程硕士,方向为机械设计及制造。
图1单元制动器图5唇形密封圈安装方式改进如前所述,唇形密封圈采用手工压装,要求通过按压唇形密封圈骨架的上端面(图4,A 1-A 2所示环形端面)将唇形密封圈装入活塞的沉台内。
而组装时操作人员手上沾有油脂,极个别情况下可能会手滑按到主唇上(图4,B 1-B 2改进措施针对唇形密封圈安装不正和开裂破损的改进措施设计唇形密封圈专用压装工装,保证在唇形密封圈压装过程中主唇位置得到可靠保护,压装力完全施加在骨架的上端面。
通过压装工装的导向定位功能,控制压装力均确保安装到位,不发生偏斜。
同时加强压装后质量的检查确认。
TJJW 044-2014 交流传动机车单元制动器暂行技术条件

x
图 1
一次调整量、缓解间隙试验示意图
3
TJ/JW 044-2014 8.3.1.3
缓解间隙试验
缓解间隙测试应在闸瓦托组成推出 30
mm......80 rnrn 范围内进行,按 8. 3. 1. 2 测得的 13 与 12 的差值即
为缓解间隙。当闸瓦托组成推出量小于 30 mm 或大于 80 rnrn 时,测得的数据不作为判别依据。
I
1 6 技术要求. . . . . . . . . . . . . . . . . . . . . . . . . . . . . . . . . . . . . . . . . . . . . . . . . . . . . . . . . . . . . . . . . . . . . . . . . . 1 7 制造要求. ... .... . .. . . . . .. ..... .. .. ..... ...... . . . .... .. . .. .. . .. .. . .. . .. . ., . ..... ... 2
总调整量试验示意图
8. 3. 1.5
停放制动缸缓解试验
向单元制动器的停放制动缸充入设计缓解压力的压缩空气,单元制动器应缓解。
8.3. 1.6
停放制动缸制动试验
将单元制动器停放制动缸内的压缩空气排空,单元制动器应产生制动作用。
8.3. 1.7
停放制动缸手动缓解试验
将单元制动器停放制动缸内的压缩空气排空,单元制动器产生制动作用后,拉动手动缓解装置,单
7
7. 1 7. 2 7. 3
制造要求 单元制动器应按经规定程序批准的图样及本标准的规定制造。 同一规格、型号的机车单元制动器各零部件应具有互换性。
SS4B机车单元制动器结构原理及检修环节要素控制分析
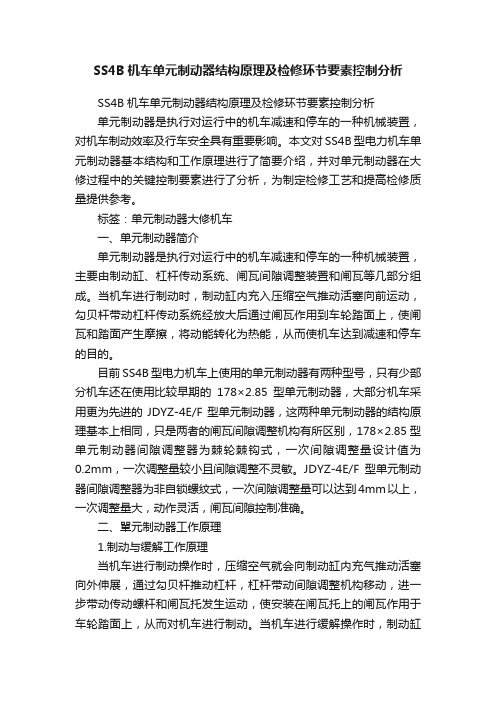
SS4B机车单元制动器结构原理及检修环节要素控制分析SS4B机车单元制动器结构原理及检修环节要素控制分析单元制动器是执行对运行中的机车减速和停车的一种机械装置,对机车制动效率及行车安全具有重要影响。
本文对SS4B型电力机车单元制动器基本结构和工作原理进行了简要介绍,并对单元制动器在大修过程中的关键控制要素进行了分析,为制定检修工艺和提高检修质量提供参考。
标签:单元制动器大修机车一、单元制动器简介单元制动器是执行对运行中的机车减速和停车的一种机械装置,主要由制动缸、杠杆传动系统、闸瓦间隙调整装置和闸瓦等几部分组成。
当机车进行制动时,制动缸内充入压缩空气推动活塞向前运动,勾贝杆带动杠杆传动系统经放大后通过闸瓦作用到车轮踏面上,使闸瓦和踏面产生摩擦,将动能转化为热能,从而使机车达到减速和停车的目的。
目前SS4B型电力机车上使用的单元制动器有两种型号,只有少部分机车还在使用比较早期的178×2.85型单元制动器,大部分机车采用更为先进的JDYZ-4E/F型单元制动器,这两种单元制动器的结构原理基本上相同,只是两者的闸瓦间隙调整机构有所区别,178×2.85型单元制动器间隙调整器为棘轮棘钩式,一次间隙调整量设计值为0.2mm,一次调整量较小且间隙调整不灵敏。
JDYZ-4E/F型单元制动器间隙调整器为非自锁螺纹式,一次间隙调整量可以达到4mm以上,一次调整量大,动作灵活,闸瓦间隙控制准确。
二、單元制动器工作原理1.制动与缓解工作原理当机车进行制动操作时,压缩空气就会向制动缸内充气推动活塞向外伸展,通过勾贝杆推动杠杆,杠杆带动间隙调整机构移动,进一步带动传动螺杆和闸瓦托发生运动,使安装在闸瓦托上的闸瓦作用于车轮踏面上,从而对机车进行制动。
当机车进行缓解操作时,制动缸内的压缩空气就会向外排出,活塞在弹簧反力作用下恢复到原来状态,进而带动杠杆、调整机构和闸瓦托向着制动相反方向运动,闸瓦离开车轮踏面使机车缓解。
O'ZBEKISTON型机车单元制动器的技术难点及解决方案

的转角。 当前踏面制动所采用闸瓦普遍为非抱轮缘结构,
曲线制动时靠 闸瓦相对轮对踏 面的滑移抵消 轮对 相对构
OZ E IT N型机车是株洲 电力机车厂为满 足乌兹 B KSO
别克斯坦国铁要求而研制的大功率客货两用交流传动电 力 机车 。乌兹别克斯 坦 国铁路况普遍 为老线路 、 多曲线 。
aep tfrad v er l l i h et trsl rv a ti u i bae i q af d f n ig r ur n o p r u o r i t oy aa s .T e eut poe t t hs n rk s u ie o r nn e i met ft e w ah ly s s s h t li ru q e y
标 书要求该车转 向架 采用 3 o B 制式 , 轨距 1 2 I 轴重 0I 5 T m、 2 ; 3t基础制 动采用 双侧 踏面制 动 , 闸瓦指定 使用 符合俄 罗斯标 准 G S 04 O T32 9的抱 轮缘铸铁 闸瓦 , 单块闸 瓦质量
收稿 日期 : 0 6 0 — 1 20 — 3 0
维普资讯
第2 9卷
第 3期
电力机 车与城轨 车辆
Ee tc L c moie & Mas rn i e i/s lcr o o t s i v s Ta st hce V
V0 . 9 No 3 12 .
20 0 6年 5月 2 日 0
H h-a UZ ijn .
( S h z0 l tcLcmov o,t.Z uh u 4 2 0 , hn ) C RZ uhuEe r oo t e .Ld. h zo 10 1 C i ci i C a
TJJW 044-2014 交流传动机车单元制动器暂行技术条件.

TB/ T 3145一2007 界定的术语和定义适用于本文件。
4 分类
单元制动器分为带停放制动和不带停放制动两种类型。
5 应用环境
单元制动器在下列使用条件下应能正常工作 :
a) 环境温度为-40 .C........+50 'C; 环境温度为-50 'C 时 ,单元制动器满足基本功能要求: b) 最湿月月平均最大相对湿度不大于 95 % (该月月平均温度最低为 25 'C) ; c) 风、雪、风砂、冰雹、强烈日光辐射、侵蚀性空气、盐雾和臭氧的自然环境条件。
10 RAMS 要求 ..... .... ....... . ..... . ... . . . . .. . . ..... . .. .. .......... . ............. .. ... 6
11 标志、包装、运输和储存......... .. .. .. . ..... . .... .. . ..... . . .... . . . ........ .... ...... 6
TJ/JW 044-2014
交流传动机车单元制动器 暂行技术条件
TJ/JW 044- 2014
目次
前言. . . . . . . . . . . . . . . . . . . . . . . . . . . . . . . . . . . . . . . . . . . . . . . . . . . . . . . . . . . . . . . . . . . . . . . . . . . . . . .. 11
l 范围. . . . . . . . . . . . . . . . . . . . . . . . . . . . . . . . . . . . . . . . . . . . . . . . . . . . . . . . . . . . . . . . . . . . . . . . . . . . .. 1 2 规范性引用文件. . . . . . . . . . . . . . . . . . . . . . . . . . . . . . . . . . . . . . . . . . . . . . . . . . . . . . . . . . . . . . . . . . .. 1 3 术语和定义. . . . . . . . . . . . . . . . . . . . . . . . . . . . . . . . . . . . . . . . . . . . . . . . . . . . . . . . . . . . . . . . . . . . . . . . 1 4 分类. . . . . . . . . . . . . . . . . . . . . . . . . . . . . . . . . . . . . . . . . . . . . . . . . . . . . . . . . . . . . . . . . . . . . . . . . . . . . . 1 5 应用环境....... . ...... . ....... ... ....... ... ..... .............. . .......... . I …… … …………….... 1 6 技术要求. . . . . . . . . . . . . . . . . . . . . . . . . . . . . . . . . . . . . . . . . . . . . . . . . . . . . . . . . . . . . . . . . . . . . . . . . . 1 7 制造要求. ... .... . .. . . . . .. ..... .. .. ..... ...... . . . .... .. . .. .. . .. .. . .. . .. . ., . ..... ... 2 8 试验方法.... .. .. ... .. . .... . ... ... ... . . . .... . . ...... . ....... ..... . .. . .. . . ... ....... 2 9 检验规则.... .. ......... ..... ........ . ... . .. . .. ..... . . ..... . ....... .... . . . ...... ... 5
一种机车单元制动器常规性能测试方法

3 气 动 系统 设 计
在设计气 动系统时 ,主要考虑 的因素为 :气源的处理 ,压 力
的控制 ,在做气密性试验 时,系统本身不能有泄漏 ,回路 可靠 、简
单 ,满足机车单元 制动器各项性能测试要求等 。在该系统中 ,气
源可选用工厂集 中供气或用合适 的空 压机单独供气 ,供气总压
力 一 般 在 600 kPa左 右 。 空 气 干燥 过 滤 器 的作 用 主 要 是 过 滤 掉
压缩空气 中的水分和杂质 ,净化气源 。精密调压 阀的作用是将供
气压力调定至试验所需的压力。二位 三通 电磁换 向阀的功月J是
改变气体通道使气体流动方向发生变化 ,从而改变气动执行元
件 的运 动 方 向 。
在系统末端 ,压力传感器ห้องสมุดไป่ตู้加装 1个尤泄漏的电动球阀 ,主
要是为 了在做制动缸气密性试验 时 ,切除前端气动 系统 中二位
三通 阀、调压 管路 系统等存在 的泄漏量 ,消 除其对制动缸气密性
试验准确性的影响。气动原 理如图 1所示 。
4 传 感 器 选 型
综 合 分 析 各
类 机 车 单 元 制 动
器 的 设计 参 数 ,
其 制 动 缸 气 压 测
试 范 围 为 (0
单元制动器
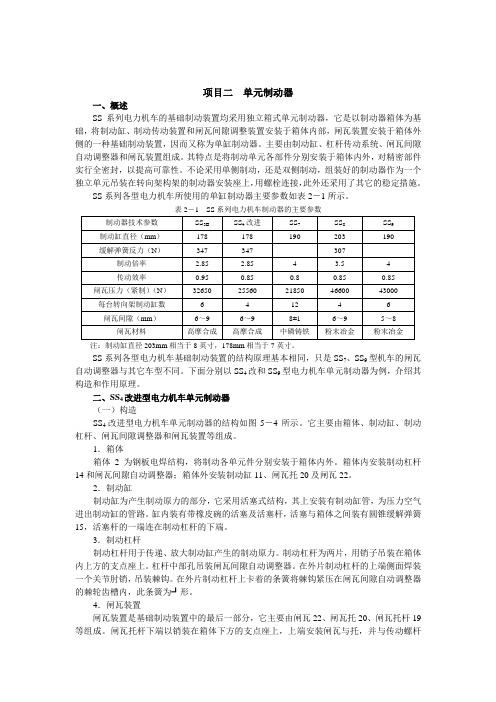
28相连。
闸瓦托上装两块闸瓦,以闸瓦签21串定。
1—闸瓦定位弹簧;2—箱体;3—棘钩;4—压环;5—密封套;6—门组装(左);7—门组装(右);8—油杯;9—护罩;10—滤尘网;11—制动缸;12—杠杆;13—隔套;14—杠杆;15—圆锥弹簧;16—扭簧卡;17—扭簧止板;18—扭转弹簧;19—闸瓦托杆;20—闸瓦托;21—闸瓦签;22—闸瓦;23—脱钩杆;24—开口销;25—手轮;26—螺盖;27—棘轮;28—传动螺杆;29—传动螺母;30—滑套;31—条簧;32—密封罩;33—螺母;34—闸瓦签圆销。
图2-4 SS4改进型电力机车单元制动器5.闸瓦间隙自动调整器闸瓦间隙自动调整器为使闸瓦与车轮踏面保持一定间隙而设。
SS系列电力机车除SS7、SS9型外,均采用单向自动式闸瓦间隙调整器,即自动减小过大的闸瓦间隙,而增大闸瓦间隙则需人工调整。
它吊装在制动杠杆上部,两端伸出箱体孔部分设密封装置防止灰尘进入箱体内。
伸出箱体一端是调整手轮,一端是传动螺杆,连在闸瓦托与闸瓦托杆上。
闸瓦间隙自动调整器由传动螺杆28与传动螺母29(左旋螺纹结合)、滑套30、棘轮27、棘钩3及调整手轮25等组成。
传动螺母套装在滑套中可转动,传动螺母尾部露出滑套部分有右旋螺纹,其上拧装棘轮与调整手轮。
滑套上有两耳轴销,是为吊装在制动杠杆之间而设。
箱体上部有脱钩机构,主要由脱钩杠杆23及棘钩3组成。
撬起脱钩杠杆的长臂,压迫脱钩销可使棘钩绕关节肘销转动离开棘轮齿槽,以便反向旋转调整手轮使闸瓦离开车轮踏面,进行闸瓦更换。
(二)工作原理如图2-4所示,当制动缸充气时,活塞带动活塞杆左移(活塞同时压缩了圆锥缓解弹簧),推制动杠杆下端并以上螺销为支点向左摆动,制动杠杆带动与它相连的滑套,使传动螺母与传动螺杆推动闸瓦托,使闸瓦压在车轮踏面上实现制动作用。
当制动缸排气时,活塞和活塞杆在缓解弹簧的推动下,使上述各传动零件作反方向运动,闸瓦即离开踏面而缓解。
- 1、下载文档前请自行甄别文档内容的完整性,平台不提供额外的编辑、内容补充、找答案等附加服务。
- 2、"仅部分预览"的文档,不可在线预览部分如存在完整性等问题,可反馈申请退款(可完整预览的文档不适用该条件!)。
- 3、如文档侵犯您的权益,请联系客服反馈,我们会尽快为您处理(人工客服工作时间:9:00-18:30)。
2.1
2.1.1
当前使用的机车单元制动器的缸径规格主要有7寸,7.5寸8寸,其中以7寸缸使用最为广泛,也有采用6.5寸和8寸以上的。缸体直径的规格越少,互换性和简统化程度越高。缸体直径过小将影响制动缸的缓解和常用制动性能,而直径过大,则活塞杆过重,造成动作困难,易使皮碗变形和拉伤缸表面。因此建议制动缸的内径定为6.5寸,7寸,7.5寸,8寸等4个等级。
2.2
2.2.1
考虑机车使用中的不可预期的调拨,单元制动器应能适应中国大陆的一般地理和气候条件。根据实际情况,对机车单元制动器的使用环境条件建议为:海拔
不高于l200m,温度范围为—4o一50℃,在最高月平均气温≤25℃情况下湿度不超过90%。
2.2.2
据《铁路技术管理规程》的规定,机车闸瓦间隙为4~8mm,故单元制动器的设计闸瓦间隙应按此取值。
2.3.3
性能试验主要是验证单元制动器的性能指标是否符合设计的要求。由于每个制动器的性能指标受制造的影响较大,因此对制动器的性能试验应作为例行试
验的一部分。性能试验必须在试验台上进行,建议按以下几个参数分别测试:闸瓦间隙、一次间隙调整量、最大丝杆调节量、闸瓦最大行程、最小动作压力、传动效率,每一个指标的测试次数不少于3次,并应按规定的表格记录。试验压力分别按10okPa,450kPa,60okPa进行。
皮碗的结构种类较多,目前使用的L形皮碗运动阻力大,安装复杂,此结构原套用化工部标准,并不适合于单元制动器使用。国外制动器的皮碗基本上都采用钢骨架结构,其优点是安装、拆卸简便,定位精度高运动阻力小,国产JDYZ-4型制动器亦采用了这种结构,运用效果较好。建议新造制动器皮碗采用钢骨架式结构。
2
间隙调整器分为棘轮棘勾式和非自锁螺纹式两种
2.3.5
制动器的零部件在温度较低的条件下可能会发生性能上的改变,从而影响制动器的整机性能,因此对制动器须进行低温试验。为了模拟低温环境,制动器和风源系统均应在-40℃下保持一段时间,一般在48h以上。在低温环境下应对制动器进行所有性能试验和气密性试验。
2.3.6
型式试验是针对新研制的制动器,因此以上提到的所有试验均应涵盖在型式试验之中,同时建议型式试验还必须对关键零件的关键质量特性进行专项检
2.3.4
制动器在使用过程中各零部件和制动器的安装应有足够的强度,除在设计时进行强度计算外,对新研制的制动器必须进行有关的强度试验。国内尚无这方面的规定和要求,根据UIC的规定和国外的其他资料,对制动器安装的强度可按5g的加速度进行冲击试验后检验安装螺栓和安装座应无变形和裂损;对制动器
内部零部件的强度可在制动缸中充以1000kPa的压力,保压5min以上,检查应无永久变形和裂损。制动器的疲劳强度按2.3.1条进行试验。
2.3.2
此试验是制动器的一个重要的测试项目,目的是确保制动缸不泄漏,保证制动不失效。由于制动器工作压力范围大,不同的压力都有造成泄漏的可能性,应确保制动器在整个工作范围内不泄漏并具有一定的安全量,因而必须对制动缸进行高、中、低压下的气密性试验,可分别按600kPa,450kPa,10okPa进行试验。各压力下的试验均应保压3min以上,总泄漏量控制在10kPa以内。
50kPa。
2.3
机车单元制动器是影响机车行车安全的重要部件,新研制的单元制动器和正式生产的单元制动器必须符合设计要求,因此对单元制动器试验方法的规定应作为单元制动器技术标准的一个重要组成部分予以阐述。
根据对单元制动器的作用原理和安全性的分析,单元制动器至少应进行疲劳、气密性、性能、强度等4个方面的试验。同时为考验制动器在低温下的工作能力,制动器除了要做室温环境的各种试验外,还应对受温度影响较大的项目进行低温试验。
结构。棘轮棘勾式间隙调整器在国外早已淘汰,其缺点是一次调整量太小,间隙调整不灵敏,易自动上闸、犯卡,存在安全隐患。非自锁螺纹间隙调整器一次调整量大,动作灵活,闸瓦间隙控制准确,在技术标准中应规定采用非自锁螺纹的间隙调整器。同时考虑更换闸瓦的方便,制动器应能手动双向调整闸间隙。
2.1.3
闸瓦的制动行程应等于闸瓦间隙,若闸瓦安装较松,则将在闸瓦与车轮间产生假间隙,增大了制动行程,严重时会导致制动不上闸,酿成重大事故。故闸瓦
2.2.7
标准中应规定制动器闸瓦的最大行程。用制动缸活塞最大行程与制动倍率的比值得出闸瓦能达到的最大行程。实际制动时闸瓦产生制动力的有效行程范围约为5~1lmm,此数值考虑了制动时轮对和制动器箱体的弹性变形量。当制动器运用后,销套产生磨损,配合间隙增大,将对最大行程产生一定的影响,根据设计极限值的规定计算出该影响值最大可达到2~3nlln,闸瓦能达到的最大行程与该影响值的差值不应小于最大有效行程l1mm,否则制动器就存在失效的可能性。因此对闸瓦最大行程应规定为不小于14mm。
关键词:单元制动器;JDYZ-4型;技术标准
引 言
单元制动器由制动缸装配、箱体、间隙调整器、闸瓦托装配、放大杠杆几部分组成。由于闸瓦是易耗件,且运用不固定,故一般不将闸瓦归人单元制动器。制动缸装配由制动缸、活塞、皮碗组成,当向缸中充人压缩空气后,活塞将产生运动,推动杠杆前行,经放大后作用于闸瓦托,进而形成闸瓦压力,有的制动器将活塞与杠杆设计为一体化。
间隙调整器的作用是控制闸瓦间隙,使得在闸瓦和车轮磨耗后,闸瓦与车轮踏面的间隙能自动调整,保证制动时闸瓦的行程不变。闸瓦托装配主要是固定闸瓦并保证闸瓦托的弹性定位。箱体是所有部件的支承和受力件。同时通过箱体与转向架构架的联接实现单元制动器的安装。
单元制动器由制动缸装配、箱体、间隙调整器、闸瓦托装配、放大杠杆几部分组成。由于闸瓦是易耗件,且运用不固定,故一般不将闸瓦归人单元制动器。制动缸装配由制动缸、活塞、皮碗组成,当向缸中充人压缩空气后,活塞将产生运动,推动杠杆前行,经放大后作用于闸瓦托,进而形成闸瓦压力,有的制动器将活塞与杠杆设计为一体化。间隙调整器的作用是控制闸瓦间隙,使得在闸瓦和车轮磨耗后,闸瓦与车轮踏面的间隙能自动调整,保证制动时闸瓦的行程不变。闸瓦托装配主要是固定闸瓦并保证闸瓦托的弹性定位。箱体是所有部件的支承和受力件。同时通过箱体与转向架构架的联接实现单元制动器的安装。图l是主要国产单元制动器的结构示意图。单元制动器主要技术参数有活塞有效面积、制动倍率、传动效率、活塞最大行程、闸瓦最大行程、一次间隙调整量、最大丝杆调节量、缓解弹簧力等。表1为主要单元制动器的技术参数和运用范围。
2.2.5
机车踏面单元制动器在运用过程中,将存在着踏面的磨耗和闸瓦的磨损两种对偶摩擦件,对轮径为250nlln的机车,最大半径磨耗量为50mm,而一般
闸瓦的最大磨损量为25mm,两者的总磨损是75mm。要保持在车轮和闸瓦均磨损到极限时闸瓦与踏面的间隙仍为8mm,在理论上丝杆必须至少能调整75nlln。考虑到适当的安全裕量和变形因素,建议规定制动器丝杆的最大调节量不小于85mm。
西安铁路职业技术学院毕业设计(论文)格式规范
学生姓名:
学号:
专业班级:
指导教师:
摘 要
机车单元制动器是机车走行部分的重要部件。用于对机车施行空气制动,因此它对机车运行的安全性可靠性有着重要的影响。机车采用单元制动器后克服了杠杆式基础制动装置效率低,磨耗大,闸瓦间隙不准确,维修量大的缺点。经过多年的运用表明,其性能稳定,作用可靠,维护性好。在近几年铁道部主要新造机车标书中均明确要求采用单元制动器。当前我国机车上使用的单元制动器生产单位较多,各单位所制造的单元制动器的结构和技术参数以及对试验条件的规定不统一,单元制动器的互换性不强。在同一机务段存在多种单元制动器并存现象,造成使用维护不便。随着机车数量的增多,这种矛盾更加突出。因此,从机车运用的安全性、可维护性考虑,有必要制订统一的单元制动器技术标准。2002年3月,在北京举行的国产JDYZ一4型单元制动器技术评审会上铁道部运输局装备部、铁道部安监司有关领导呼吁尽快制订单元制动器的行业标准,规范全路单元制动器的技术条件,并得到与会专家的认同。本文就机车单元制动器有关技术标准的规定作一探讨
2.2.6
制动器的传动效率是制动器实际输出力与理论计算力的比值。在理论计算力的算法上,国内与国外有所不同,国内的计算是直接采用活塞力乘以制动倍率,而将缓解弹簧的力与制动过程中的摩擦力一并算作制动阻力;国外的计算是将活塞力减去缓解弹簧力后再乘以制动倍率,因而国外制动器给出的传动效率值一般
在0.9以上,而国内的设计惯例一般是不小于0.85。由于缓解弹簧力虽然在制动时起阻力作用,但在缓解过程中却是一种积极作用的力,而且,缓解弹簧力并不是不可控力,完全可通过设计和制造进行量化控制,因而不应将其归咎为阻力。在制动器的设计中,提出传动效率指标主要是要对制动中的各种摩擦等非可控阻力因素采取措施,尽量控制,如提高摩擦部位光洁度、涂润滑脂等。建议今后机车制动器传动效率按国外的方法进行计算。
2.3.1
试验的目的是考验制动器连续工作的能力,由于很难模拟实际运行的条件,一般是进行静态连续制动缓解。目前新研制的制动器只进行10万次制动缓解动作疲劳试验,不足以反映制动器的正常工作寿命。20o2年4月铁道部运输局装备部已下文要求新研制的制动器一律进行40万次动作试验。因此在技术标准中应规定按40万次作疲劳试验,试验后解体检查各零部件的磨耗和变形应在正常范围内,并不得有裂损现象。
制动缸压力不同时传动效率值不同,设计给出的传动效率一般是紧急制动压力(450kPa)下的传动效率。设计传动效率过小,虽不影响紧急制动功能,但将对小压力时的常用制动功能有影响,导致常用制动力偏小。同时制动器的最小动作压力增大,影响灵敏度。国外制动器的传动效率提出的指标有0.9l,0.93,0.95等数据,按国外的算法,可规定国产制动器设计的最小传动效率在450kPa时不小于0.9。
2.2.8
单元制动器的缓解弹簧力的大小决定着制动器能否可靠缓解,对制动器的安全性有重要影响,间隙调整器为非自锁螺纹时,缓解弹簧还将影响间隙调整功能。
缓解弹簧力太大将影响传动效率和最小压力。建议新设计的制动器缓解弹簧力在300~700N之间。