甲醇羰基化法
甲醇气相氧化羰基化法碳酸二甲酯工艺技术

甲醇气相氧化羰基化法碳酸二甲酯工艺技术
甲醇气相氧化羰基化法是一种用于合成碳酸二甲酯(DMC)的工艺技术。
该方法以甲醇为原料,通过氧化和羰基化两个主要化学反应步骤来制备DMC。
具体工艺流程如下:
1. 氧化反应:首先,甲醇在催化剂的作用下与氧气反应生成甲醛和水。
这个反应通常在较高的温度下进行,催化剂可以是银基或铜基催化剂。
CH3OH + 1/2 O2→HCHO + H2O
2. 羰基化反应:随后,甲醛与更多的甲醇在另一种催化剂的作用下进行羰基化反应,生成碳酸二甲酯和水。
这个反应同样需要在较高的温度下进行,催化剂一般是基于铜的催化剂。
HCHO + 2 CH3OH →CH3O-CO-OCH3 + H2O
在整个工艺流程中,催化剂的选择和优化、反应器设计、操作条件(如温度、压力和反应时间)以及产物的分离和纯化都是影响最终产品质量和产量的关键因素。
此外,为了提高反应的选择性和降低副产物的生成,通常需要精确控制反应条件和催化剂的使用。
甲醇气相氧化羰基化法具有原料易得、成本相对较低、副产物少和环境友好等优点,因此被认为是合成DMC的有
前途的工艺之一。
然而,该工艺也面临着催化剂的稳定性和寿命、甲醇转化率以及能耗等挑战。
甲醇液相氧化羰基化法工艺流程
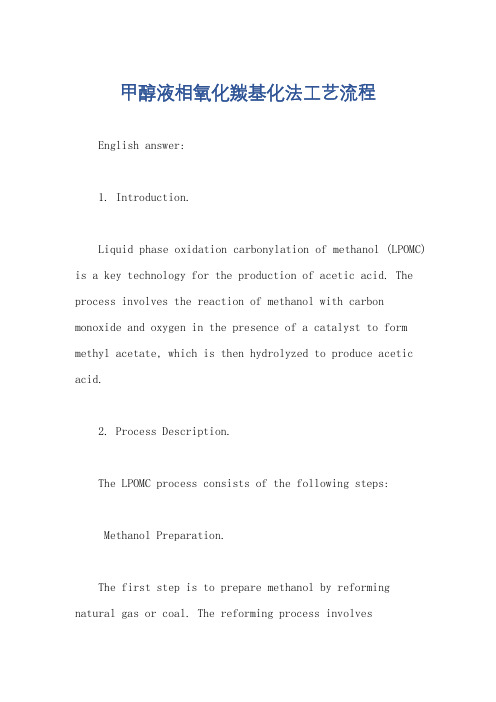
甲醇液相氧化羰基化法工艺流程English answer:1. Introduction.Liquid phase oxidation carbonylation of methanol (LPOMC) is a key technology for the production of acetic acid. The process involves the reaction of methanol with carbon monoxide and oxygen in the presence of a catalyst to form methyl acetate, which is then hydrolyzed to produce acetic acid.2. Process Description.The LPOMC process consists of the following steps:Methanol Preparation.The first step is to prepare methanol by reforming natural gas or coal. The reforming process involvesreacting methane or coal with steam in the presence of a catalyst to produce hydrogen and carbon monoxide. The hydrogen and carbon monoxide are then reacted to form methanol using a methanol synthesis catalyst.Carbonylation.The second step is the carbonylation reaction, which involves reacting methanol with carbon monoxide and oxygen in the presence of a catalyst. The catalyst is typically a rhodium or iridium complex. The reaction takes place in a liquid phase reactor at a temperature of 100-200°C and a pressure of 10-50 bar.Hydrolysis.The third step is the hydrolysis reaction, which involves reacting methyl acetate with water to produce acetic acid. The hydrolysis reaction is typically carried out in a separate reactor at a temperature of 120-150°C and a pressure of 1-5 bar.Acetic Acid Distillation.The fourth step is the acetic acid distillation column. After hydrolysis, the unreacted raw material will be separated to be recycled back to the raw material tank. Acetic acid can be obtained from the bottom, and water can be obtained from the top.3. Process Parameters.The LPOMC process is affected by a number of parameters, including:Temperature.Pressure.Catalyst concentration.Methanol/carbon monoxide ratio.Oxygen/carbon monoxide ratio.4. Catalysts.The catalyst used in the LPOMC process is a key factor in determining the efficiency of the process. The catalyst is typically a rhodium or iridium complex. The choice of catalyst depends on a number of factors, including the desired reaction rate, selectivity, and stability.5. Environmental Considerations.The LPOMC process generates a number of waste products, including carbon dioxide, water, and methanol. The environmental impact of the process can be minimized by recycling the waste products and using energy-efficient technologies.6. Economic Considerations.The LPOMC process is a relatively low-cost process. The major costs associated with the process are the cost of methanol, carbon monoxide, oxygen, and catalyst. The costof the process can be minimized by optimizing the process parameters and using efficient technologies.Chinese answer:1. 简介。
甲醇羰基化论文

甲醇羰基化合成醋酸技术新进展及我国现状摘要:化学工业的主要原料是煤、石油、天然气等能源资源,我国的煤炭资源十分丰富,全国的煤炭保有储量达1万亿吨。
从可持续发展战略的观点出发,新世纪将是以一碳化学为基础的新一代煤化工发展新时期。
发展新一代煤化工具有最大竞争力的是含氧化合物类产品,其中最具代表性的是用途广、产量大的有机酸棗醋酸。
醋酸广泛用于化工、轻工、纺织、农药、医药、电子、食品等工业部门,醋酸下游产品很多,其衍生化学品多达数百种。
自70年代美国孟山都公司首创低压羰基合成醋酸工艺以后,该方法已成为当今世界生产醋酸的主要方法。
甲醇低压羰基合成醋酸工艺确立了一碳化学含氧化合物的产业优势,从此,醋酸及其衍生物的工艺和技术创新一直成为世人追求的发展目标。
关键词:甲醇,乙酸,羰基化,催化一、甲醇羰基化合成醋酸技术发展概况近年来甲醇羰基化法工业化生产醋酸技术的主要进展包括:BP公司的Cativa 工艺、Celanese公司开发出的Celanese低水含量工艺、UOP/Chiyoda开发出UOP/Chiyoda Acetica工艺、Haldor Topsoe的合成气经甲醇/二甲醚生产醋酸新工艺、我国西南化工研究设计院开发的蒸发流程。
以上新技术有的已用于工业化生产装置的改进,有的正在准备用于工业装置的建设或改造。
在醋酸的生产工艺中,甲醇羰基化法是应用最广的技术,占全球总产能的60%以上,而且这种趋势还在不断增长。
以孟山都(Monsanto)/BP工艺为代表的甲醇低压羰基化法是目前工艺最成熟,最为经济,具有先进技术,原料转化率高等优点。
在我国现有的醋酸生产工艺中孟山都(Monsanto)/BP己形成规模的生产。
但需要特别指出的是在该工艺还存在许多诸如能耗高、转化率低等问题。
为促进国内工业化生产,解决存在的技术问题。
鉴于这种情况,设计一套甲醇低压羰基化合成醋酸(10万t/a)工艺装置,以满足国民经济发展的需要。
二、本课题所涉及的问题在国内(外)研究现状及分析1、国外醋酸生产现状及市场分析2007年世界醋酸生产能力为1168.8 万t/a,其中采用甲醇羰基化合成工艺的占66%,乙烯法约占7.2%,乙醛法约占15.3%,其他工艺占11.5%。
甲醇低压羰基化制醋酸

甲醇低压羰基化制醋酸醋酸是最重要的有机酸之一。
全世界产量约6.0Mt/a,主要用于合成醋酸乙烯、醋酸纤维、醋酸酯、金属醋酸盐等,也是制药、染料、农药、感光材料以及其他有机合成的重要原料。
1.醋酸生产方法评述工业上生产醋酸的方法主要有3种:乙醛法、丁烷或轻油氧化法以及甲醇羰基化法。
(1)乙醛法这是比较古老的生产方法。
乙醛可由乙炔、乙烯和乙醇制得,1959年用乙烯直接氧化制乙醛(常称瓦克法)获得成功,现在已成为生产乙醛的主要方法。
乙醛生产醋酸的反应式为:工艺过程为:将含5%~10%乙醛的醋酸液通入空气或氧气氧化,催化剂为醋酸锰或醋酸钴,反应温度50~80℃,反应压力0.1~1.0MPa。
除主产物醋酸外,还有甲醛和甲酸等副产物生成。
乙醛转化率90%以上,醋酸选择性大于94%。
(2)丁烷(或轻油)液相氧化法20世纪50年代初在美国首先实现工业化。
丁烷或轻油在Co,Cr,V或Mn的醋酸盐催化下在醋酸溶液中被空气氧化,反应温度95~100℃,压力1.0~5.47MPa,反应产物众多,分离困难,而且对设备和管路腐蚀性强,虽然能用廉价的丁烷和轻油作原料,除美国、英国等少数国家还继续采用外,其他国家对该法兴趣不大。
(3)甲醇羰基化法以甲醇为原料合成醋酸,不但原料价廉易得,而且生成醋酸的选择性高达99%以上,基本上无副产物,现在世界上有近40%的醋酸是用该法生产的,新建生产装置多考虑采用这一生产方法,表5-5-04列出了目前世界上生产醋酸的2种主要方法的生产成本比较。
由表5-5-04不难看出甲醇法不仅投资省,而且生产费用也低,对乙醛法有明显的优势。
2.甲醇低压羰基化制醋酸的工艺原理(1)化学反应主反应:HI(或CH3I)为助催化剂.副反应:CH3COOH+CH3OH====CH3COOCH3+HO22CH3OH====CH3OCH3+H2OCO+H2O→CO2+H2此外,尚有甲烷、丙酸(由原料甲醇中含有的乙醇羰基化生成)等副产物。
甲醇羰基化反应制醋酸反应原理及工艺流程
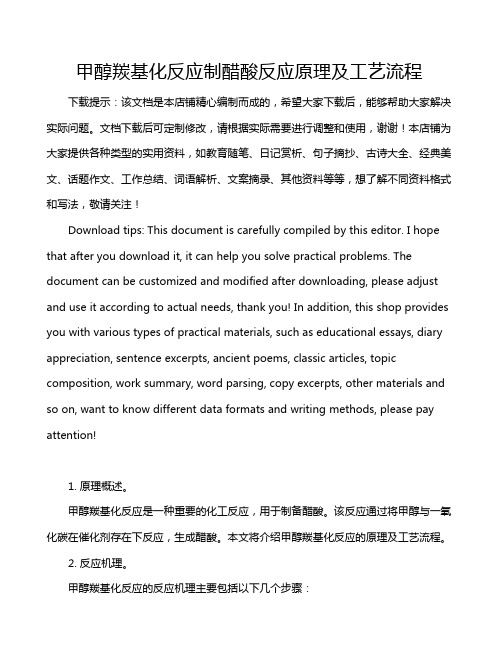
甲醇羰基化反应制醋酸反应原理及工艺流程下载提示:该文档是本店铺精心编制而成的,希望大家下载后,能够帮助大家解决实际问题。
文档下载后可定制修改,请根据实际需要进行调整和使用,谢谢!本店铺为大家提供各种类型的实用资料,如教育随笔、日记赏析、句子摘抄、古诗大全、经典美文、话题作文、工作总结、词语解析、文案摘录、其他资料等等,想了解不同资料格式和写法,敬请关注!Download tips: This document is carefully compiled by this editor. I hope that after you download it, it can help you solve practical problems. The document can be customized and modified after downloading, please adjust and use it according to actual needs, thank you! In addition, this shop provides you with various types of practical materials, such as educational essays, diary appreciation, sentence excerpts, ancient poems, classic articles, topic composition, work summary, word parsing, copy excerpts, other materials and so on, want to know different data formats and writing methods, please pay attention!1. 原理概述。
甲醇羰基化反应是一种重要的化工反应,用于制备醋酸。
甲醇氧化羰基化法

2.2 甲醇氧化羰基化法2CH3OH十CO十1/2O2→(CH3O)2CO十H2O该法以CH3OH、CO和O2为原料,原料价廉易得,投资少,成本低且理论上甲醇全部转化为DMC,无其他有机物生成,受到工业界极大重视,被认为是DMC最有前途的生产方法,也是各大工业国家重点研究、开发的技术路线。
2.2.1 ENI液相氧化羰基化法2CH3OH十1/2O2十2CuCl→2Cu(OCH3)Cl十H2OCO十2Cu(OCH3)Cl→(CH3O)2CO十2CuCl总反应:2CH3OH十1/2O2十CO→(CH3O)2CO十H2O以氯化亚铜为催化剂,反应在两台串联的带搅拌的反应器中分两步进行。
甲醇既为反应物又为溶剂。
反应温度120~130℃,压力2.0~3.0MPa。
典型工艺流程包括氧化羰基化工段及DMC分离回收工段。
采用氯苯作萃取剂分离DMC与甲醇的混合物。
该技术系意大利Ugo Romano等人在长期研究羰基化基础上于1979年开发成功;1983年由意大利Enichem Synthesis公司首次在Ravenna实现工业化。
初始装置规模5500吨/年,1988年扩大到8800吨/年,1993年进一步扩大到12000吨/年。
日本Dacail公司投资25亿日元,1988年在姬路市也采用此技术建成了6000吨/年工业化装置。
ENI液相法单程收率32%,选择性按甲醇计近100%。
不足之一是选择性按CO计不稳定(最高时92.3%,最低时仅60%),主要原因是带搅拌的釜式反应器造成CO对DMC选择性为时间减函数;不足之二是腐蚀性大,催化剂寿命短。
除ENI外,世界上其他几大化学公司如ICI、Texaco、Dow化学公司等也竞相开发此技术。
国内,原化工部西南化工研究院80年代中期也进行了液相法甲醇氧化羰基化技术的研究开发,并取得阶段性成果;1994年后又开始试验及工业放大工作,预计中试及工业化进程不会太远。
华中理工大学和原湖北利川市化肥厂联合开发的甲醇液相氧化羰基化合成DMC 技术,采用氯化亚铜复合催化剂及管式反应器循环工艺,在生产操作中省去了ENI 工艺的闪蒸、过滤、甲醇反冲和打浆等复杂的催化剂加入与分离工序。
甲酸生产工艺简介

甲醇羰基化合成甲酸甲酯技术甲酸甲酯是是一种用途广泛的低沸点溶剂(如硝化纤维素、醋酸纤维素等)、有机中间体和药物的合成原料。
国外广泛采用的大规模生产甲酸甲酯的最主要方法是甲醇羰基化法。
其中甲醇羰基化法是甲酸甲酯水解制甲酸的最佳生产工艺,产品成本仅为传统甲醇钠法制甲酸的一半。
我公司自主开发了甲醇羰基化合成甲酸甲酯的新工艺, 技术、设计、设备全部国产化,装置运行连续稳定,各项技术指标达到国际先进水平,生产成本在各种可工业化的甲酸甲酯生产方法中最低。
一、甲醇羰基化合成甲酸甲酯技术工艺流程甲醇羰基法是甲醇与CO在催化剂的作用下,在一定压下发生羰基化反应生成甲酸甲酯,其化学反应式如下:CH3OH + CO →HCOOCH3△H= -29.1KJ/mol工艺流程图如下:甲醇羰基合成甲酸甲酯工艺流程图工艺流程简述:CO气体、甲醇与催化剂混合后在羰基化反应器中,在一定的压力和温度下发生羰基化反应生成甲酸甲酯。
用新鲜甲醇吸收反应器上部的未反应完的CO气体尾气,并经二级冷凝回收尾气夹带的甲酸甲酯、甲醇,冷凝液回流到反应器中。
含有甲酸甲酯的粗产品在加压精馏塔中进行精馏,塔顶采出甲酸甲酯产品,塔底采出采出物经过滤除去废催化剂后,循环回反应器使用。
二、甲醇羰基化合成甲酸甲酯技术特点1.在反应器中装有气体分配器和文丘里喷射器,有利于提高气流分散度和增大气液接触面积,从而可提高反应效率。
2.技术、设计、设备全部国产化,装置运行连续稳定,各项技术指标达到国际先进水平。
三、甲酸甲酯质量指标色泽:无色透明;MF含量:≥96%;水含量:≤0.2%;甲醇含量:≤4.0%,如用户要求,MF含量可以提高到98%。
四、消耗定额原料消耗(以每吨97%甲酸甲酯产品计)公用工程消耗(以每吨97%甲酸甲酯产品计)本公司于2006年在江苏新亚化工有限公司建成了3万吨/年羰基合成制甲酸甲酸生产装置,至今已连续稳定运行了三年,操作状况良好。
60kt/a甲酸甲酯装置投资约1800万元,甲酸甲酯车间成本约2500元/吨,甲醇羰基化经甲酸甲酯合成甲酸技术一、甲醇羰基化经甲酸甲酯制甲酸技术工艺流程甲醇与CO在催化剂的作用下,羰基化反应生成甲酸甲酯后经过加压精馏后得到甲酸甲酯,然后采用自催化水解法进入水解反应制甲酸阶段(包括甲酸甲酯反应与蒸馏、水解反应、甲酸分离、甲酸浓缩等工序),涉及反应式如下:CH3OH + CO →HCOOCH3△H = -29.1KJ/molHCOOCH3 + H2O →HCOOH + CH3OH △H = -2.83Kcal/mol工艺流程图如下:甲醇羰基化经甲酸甲酯制甲酸工艺流程图工艺流程简述:CO和甲醇与催化剂混合后在一定的压力和温度下发生羰基化反应生成甲酸甲酯,用甲醇吸收尾气夹带的甲酸甲酯、甲醇,冷凝液回流到反应器中。
甲醇羰基化制乙酸工艺流程

甲醇羰基化制乙酸工艺流程
甲醇羰基化制乙酸工艺流程是一种重要的化学工艺,它可以将甲醇和一氧化碳在催化剂的作用下反应生成乙酸。
这种工艺具有高效、环保、经济等优点,因此在化工行业中得到了广泛的应用。
该工艺的主要流程如下:
1. 原料准备:将甲醇和一氧化碳按照一定的比例混合,制备成反应物。
2. 催化剂制备:选择合适的催化剂,将其制备成适合反应的形态。
3. 反应器装置:将反应器装置好,保证反应器的密封性和稳定性。
4. 反应过程:将反应物加入反应器中,加热至一定温度,催化剂的作用下,反应物发生羰基化反应,生成乙酸。
5. 分离纯化:将反应产物进行分离纯化,得到纯净的乙酸。
6. 废气处理:对反应过程中产生的废气进行处理,保证环境的安全和卫生。
甲醇羰基化制乙酸工艺流程的优点在于,反应条件温和,反应速度快,产物纯度高,反应产物易于分离纯化,同时还可以回收利用废气,减少环境污染。
因此,该工艺在化工行业中得到了广泛的应用。
甲醇羰基化制乙酸工艺流程是一种高效、环保、经济的化学工艺,
具有广泛的应用前景。
在未来的发展中,我们需要不断地优化工艺流程,提高反应效率和产物质量,为化工行业的发展做出更大的贡献。
甲酸的生产方法
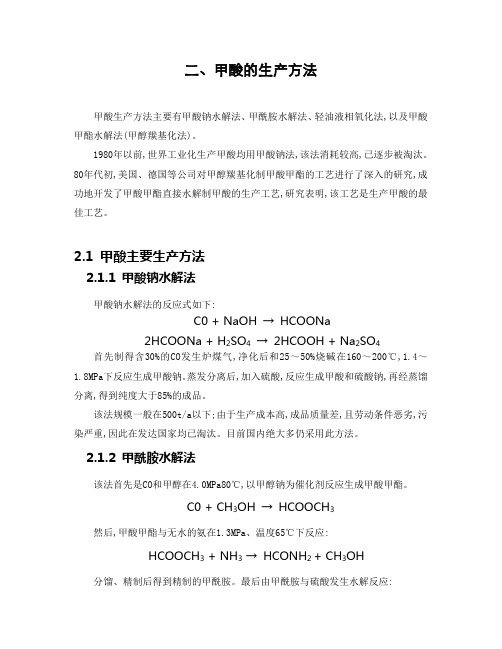
二、甲酸的生产方法甲酸生产方法主要有甲酸钠水解法、甲酰胺水解法、轻油液相氧化法,以及甲酸甲酯水解法(甲醇羰基化法)。
1980年以前,世界工业化生产甲酸均用甲酸钠法,该法消耗较高,已逐步被淘汰。
80年代初,美国、德国等公司对甲醇羰基化制甲酸甲酯的工艺进行了深入的研究,成功地开发了甲酸甲酯直接水解制甲酸的生产工艺,研究表明,该工艺是生产甲酸的最佳工艺。
2.1 甲酸主要生产方法2.1.1 甲酸钠水解法甲酸钠水解法的反应式如下:C0 + NaOH →HCOONa2HCOONa + H2SO4→2HCOOH + Na2SO4首先制得含30%的CO发生炉煤气,净化后和25~50%烧碱在160~200℃,1.4~1.8MPa下反应生成甲酸钠。
蒸发分离后,加入硫酸,反应生成甲酸和硫酸钠,再经蒸馏分离,得到纯度大于85%的成品。
该法规模一般在500t/a以下;由于生产成本高,成品质量差,且劳动条件恶劣,污染严重,因此在发达国家均已淘汰。
目前国内绝大多仍采用此方法。
2.1.2 甲酰胺水解法该法首先是CO和甲醇在4.0MPa80℃,以甲醇钠为催化剂反应生成甲酸甲酯。
C0 + CH3OH →HCOOCH3然后,甲酸甲酯与无水的氨在1.3MPa、温度65℃下反应:HCOOCH3 + NH3 →HCONH2 + CH3OH 分馏、精制后得到精制的甲酰胺。
最后由甲酰胺与硫酸发生水解反应:2HCONH2 + Na2SO4 + 2H2O →2HCOOH + (NH4)2SO4再经干燥、冷凝后即得产品,纯度为90~95%。
该法是德国BASF公司的专利,曾为欧洲甲酸生产的主要方法,流程复杂,成本较高,80年代初随着甲酸甲酯水解工艺的开发成功,已渐被淘汰。
2.1.3 轻油液相氧化法该法主要用于生产醋酸,甲酸为副产品,产量约占各种有机酸总产量的15%;此法由英国BP公司开发成功,70年代曾是国外生产甲酸的主要方法;随着美国孟山都公司甲醇低压羰基合成醋酸技术工业化后,该法已被淘汰。
甲醇氧化羰基化法

• DMC具有优良的溶解性能,其熔、沸点范围窄,表面张 力大,粘度低,介质界电常数小,同时具有较高的蒸发温 度和较快的蒸发速度,因此可以作为低毒溶剂用于涂料工 业和医药行业。从表1可以看出,DMC不仅毒性小,还具 有闪点高、蒸汽压低和空气中爆炸下限高等特点,因此是 集清洁性和安全性于一身的绿色溶剂。
工艺流程
• 谢谢观看
• 代替硫酸二甲酯作甲基化剂 • 代替光气作羰基化剂
传统光气法制取碳酸二甲酯
氧化羰基化法
• 甲醇氧化羰基化法用廉价的CH3OH,CO 和 O2为原料生产,成本低,产物选择性高, 因此被认为是合成DMC最有前途的方法之 一。其主要有液相氧化羰基化法和气相氧 化羰基化法
反应原理 液相甲醇氧化拨基法以下述反应为基础������
甲醇氧化羰基化法制取碳酸二甲酯来自化工122 陈寅 周浩杰
• 碳酸二甲酯(dimethyl carbonate,DMC), 是一种无毒、环保性能优异、用途广泛的 化工原料,它是一种重要的有机合成中间 体,分子结构中含有羰基、甲基和甲氧基 等官能团,具有多种反应性能,在生产中 具有使用安全、方便、污染少、容易运输 等特点。由于碳酸二甲酯毒性较小,是一 种具有发展前景的“绿色”化工产品。
甲醇羰基化制备醋酸汇总
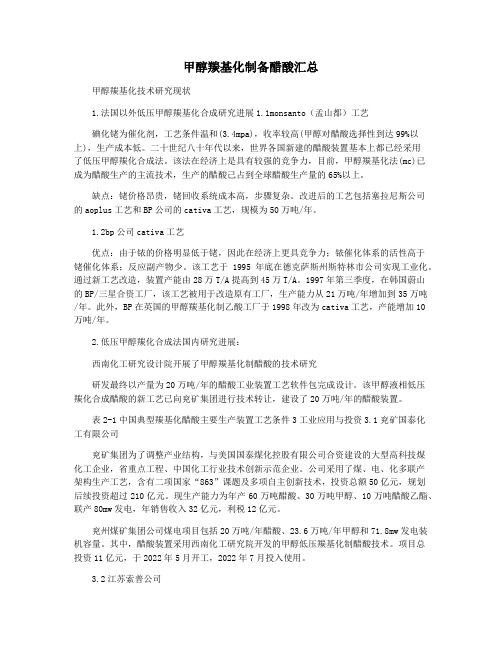
甲醇羰基化制备醋酸汇总甲醇羰基化技术研究现状1.法国以外低压甲醇羰基化合成研究进展1.1monsanto(孟山都)工艺碘化铑为催化剂,工艺条件温和(3.4mpa),收率较高(甲醇对醋酸选择性到达99%以上),生产成本低。
二十世纪八十年代以来,世界各国新建的醋酸装置基本上都已经采用了低压甲醇羰化合成法。
该法在经济上是具有较强的竞争力,目前,甲醇羰基化法(mc)已成为醋酸生产的主流技术,生产的醋酸己占到全球醋酸生产量的65%以上。
缺点:铑价格昂贵,铑回收系统成本高,步骤复杂。
改进后的工艺包括塞拉尼斯公司的aoplus工艺和BP公司的cativa工艺,规模为50万吨/年。
1.2bp公司cativa工艺优点:由于铱的价格明显低于铑,因此在经济上更具竞争力;铱催化体系的活性高于铑催化体系;反应副产物少。
该工艺于1995年底在德克萨斯州斯特林市公司实现工业化。
通过新工艺改造,装置产能由28万T/A提高到45万T/A。
1997年第三季度,在韩国蔚山的BP/三星合资工厂,该工艺被用于改造原有工厂,生产能力从21万吨/年增加到35万吨/年。
此外,BP在英国的甲醇羰基化制乙酸工厂于1998年改为cativa工艺,产能增加10万吨/年。
2.低压甲醇羰化合成法国内研究进展:西南化工研究设计院开展了甲醇羰基化制醋酸的技术研究研发最终以产量为20万吨/年的醋酸工业装置工艺软件包完成设计。
该甲醇液相低压羰化合成醋酸的新工艺已向兖矿集团进行技术转让,建设了20万吨/年的醋酸装置。
表2-1中国典型羰基化醋酸主要生产装置工艺条件3工业应用与投资3.1兖矿国泰化工有限公司兖矿集团为了调整产业结构,与美国国泰煤化控股有限公司合资建设的大型高科技煤化工企业,省重点工程、中国化工行业技术创新示范企业。
公司采用了煤、电、化多联产架构生产工艺,含有二项国家“863”课题及多项自主创新技术,投资总额50亿元,规划后续投资超过210亿元。
现生产能力为年产60万吨醋酸、30万吨甲醇、10万吨醋酸乙酯、联产80mw发电,年销售收入32亿元,利税12亿元。
年产万吨甲醇羰基化制醋酸工艺流程
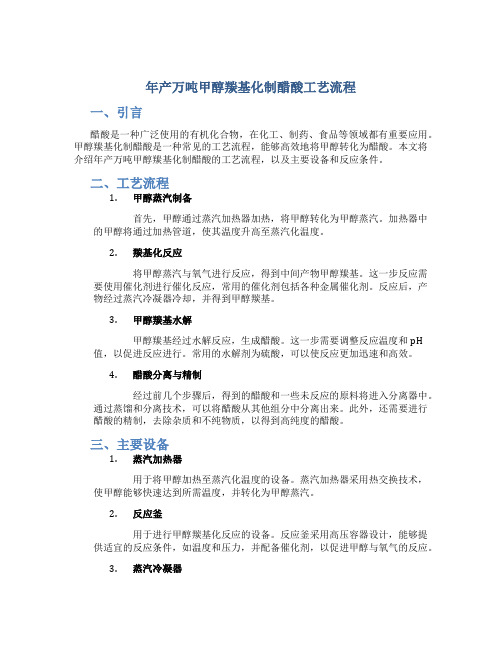
年产万吨甲醇羰基化制醋酸工艺流程一、引言醋酸是一种广泛使用的有机化合物,在化工、制药、食品等领域都有重要应用。
甲醇羰基化制醋酸是一种常见的工艺流程,能够高效地将甲醇转化为醋酸。
本文将介绍年产万吨甲醇羰基化制醋酸的工艺流程,以及主要设备和反应条件。
二、工艺流程1.甲醇蒸汽制备首先,甲醇通过蒸汽加热器加热,将甲醇转化为甲醇蒸汽。
加热器中的甲醇将通过加热管道,使其温度升高至蒸汽化温度。
2.羰基化反应将甲醇蒸汽与氧气进行反应,得到中间产物甲醇羰基。
这一步反应需要使用催化剂进行催化反应,常用的催化剂包括各种金属催化剂。
反应后,产物经过蒸汽冷凝器冷却,并得到甲醇羰基。
3.甲醇羰基水解甲醇羰基经过水解反应,生成醋酸。
这一步需要调整反应温度和pH 值,以促进反应进行。
常用的水解剂为硫酸,可以使反应更加迅速和高效。
4.醋酸分离与精制经过前几个步骤后,得到的醋酸和一些未反应的原料将进入分离器中。
通过蒸馏和分离技术,可以将醋酸从其他组分中分离出来。
此外,还需要进行醋酸的精制,去除杂质和不纯物质,以得到高纯度的醋酸。
三、主要设备1.蒸汽加热器用于将甲醇加热至蒸汽化温度的设备。
蒸汽加热器采用热交换技术,使甲醇能够快速达到所需温度,并转化为甲醇蒸汽。
2.反应釜用于进行甲醇羰基化反应的设备。
反应釜采用高压容器设计,能够提供适宜的反应条件,如温度和压力,并配备催化剂,以促进甲醇与氧气的反应。
3.蒸汽冷凝器用于冷却甲醇羰基产物并将其转化为液体甲醇羰基。
蒸汽冷凝器采用冷却水循环系统,能够有效地降低产物温度,并将产物分离出来。
4.水解反应器用于甲醇羰基水解反应的设备。
水解反应器采用恒温搅拌技术,能够保持恒定的温度和pH值,以加速水解反应的进行。
5.分离器用于将醋酸从其他组分中分离出来的设备。
分离器采用蒸馏和分离技术,能够根据不同的沸点和相对挥发性,将醋酸从混合物中提纯出来。
四、反应条件1.反应温度:羰基化反应温度通常在300-400°C之间,水解反应温度通常在100-150℃之间。
甲醇羰基化法

甲醇羰基化法甲醇低压羰基化法的经济性集中表现在两点:其一,甲醇和一氧化碳在较低的压力就能反应,甲醇的转化率和选择性都高达99%,粗乙酸的浓度高,因此提纯简单,流程紧凑,催化剂长期运转安全可靠,排放的三废少,没有严重的污染;其二,羰基化工艺的初始原料为一氧化碳和甲醇原料来源广泛,价格低廉,不与其他化学加工争夺原料,由于是一步合成,能耗不高,因此生产成本较低。
1880年Geuther在研究甲醇与一氧化碳反应时就发现有痕量的乙酸。
1925-1928年英国Celanese公司的Henry Dreyfus开始研究此反应的催化剂,反应必须在高温和高压才能进行,他们发现以银或铜为促进剂的磷酸是一种有效的催化剂。
反应器的材料只有石墨或黄金作衬里时,才能经受310℃和20MPa (199atm)这样严格条件下的腐蚀.在甲醇羰基化反应中,甲醇的转化率为400,选择性约70%,试验的规模为100kg/天,但在30年代初期就停止了生产。
此后,美国、法国和德国都进行过类似的研究。
1942年德国法本工业公司建设了10吨/夭规模的试验工厂,二次大战后工作重新进行,并开发了碘化镍催化体系,碘化镍比钴等许多其他金属羰基化合物具有较高的催化活性。
反应条件为215℃和14MPa (138atm),反应在气相中进行,所以腐蚀问题并不严重。
BASF公司着重研究了有碘存在下的铜和钴的催化体系,开发了另一条高压羰基化工艺路线1966年美国B0rden化学公司引进BASF技术建r最高生产桃力曾达135000吨/年。
BASF工艺的操作压力高达76MPa (693atm),反应器需用Hastell0yc合金钢来制造。
1966年美国孟山都化学公司开发了另一种完全不同的方法,他们最初用铑—膦一碘系催化剂,可以在较低的温度和压力时反应。
应用此项工艺的总装置生产能力已达180万吨,而且远有增长的趋势。
孟山都低压甲醇碳基化法开发成功后,BASF高压甲醇羰基化工艺实际上已失去工业意义。
浅析甲醇羰基化胺化法合成甲酰胺工艺

第22期 收稿日期:2018-09-04作者简介:方 浩(1992—),安徽安庆人,技术员,主要从事节能环保技术工作。
浅析甲醇羰基化胺化法合成甲酰胺工艺方 浩(安徽节源环保科技有限公司,安徽合肥 230088)摘要:本文针对传统的甲酰胺工艺生产不稳定、技术工艺落后、消耗高、产品分解、变色等因素,介绍了一种甲酰胺生产新工艺,并简述了甲酰胺在国内外的生产现状和价格水平,指出了甲酰胺的发展前景。
关键词:甲酸甲酯;甲醇;羰基化;甲酰胺中图分类号:TQ226.3;F426.72 文献标识码:A 文章编号:1008-021X(2018)22-0117-02 甲酰胺(Formamide,简称FA),分子式为HCONH2,分子量45.041,无色略有氨味的透明液体,1863年由霍夫曼用甲酸甲酯与氨反应合成。
甲酰胺是一种重要的有机化工原料和高沸点极性溶剂,其溶解性极好,被广泛用做溶剂,软化剂和有机合成中间体[1],在塑料、纤维、合成等工业部门以及医药、染料、香料、轻工等行业都有广泛的应用[2-3]。
国外工业化生产甲酰胺最早在20世纪80年代,而在国内起步较晚。
在工业初期,甲酰胺是通过甲酸和甲醇酯化法合成的。
该工艺落后,成本高,且含酸污水的排放造成了严重的环境污染。
随着人们环保意识的提高,众多研究机构和学者们纷纷投入到绿色新型合成路线的研发中,有效地促进了甲酰胺产品的发展。
1 甲醇羰基化胺化法合成甲酰胺工艺1.1 甲醇羰基化法制甲酸甲酯工序1.1.1 工艺原理采用净化后的CO气体与脱水后的甲醇进行羰基化反应,制取中间产品甲酸甲酯[4-5]。
化学反应式:CO+CH3OH→HCOOCH3该反应采用提纯后的CO与甲醇在催化剂甲醇钠和一定的温度压力下,进行羰基化反应合成甲酸甲酯。
1.1.2 工艺流程叙述甲醇羰基化法制甲酸甲酯的工艺流程框图如图1所示。
图1 甲醇羰基化法制甲酸甲酯工艺流程框图 CO气经气体分布器进入反应器下部。
- 1、下载文档前请自行甄别文档内容的完整性,平台不提供额外的编辑、内容补充、找答案等附加服务。
- 2、"仅部分预览"的文档,不可在线预览部分如存在完整性等问题,可反馈申请退款(可完整预览的文档不适用该条件!)。
- 3、如文档侵犯您的权益,请联系客服反馈,我们会尽快为您处理(人工客服工作时间:9:00-18:30)。
甲醇羰基化法
甲醇低压羰基化法的经济性集中表现在两点:其一,甲醇和一氧化碳在较低的压力就能反应,甲醇的转化率和选择性都高达99%,粗乙酸的浓度高,因此提纯简单,流程紧凑,催化剂长期运转安全可靠,排放的三废少,没有严重的污染;其二,羰基化工艺的初始原料为一氧化碳和甲醇原料来源广泛,价格低廉,不与其他化学加工争夺原料,由于是一步合成,能耗不高,因此生产成本较低。
1880年Geuther在研究甲醇与一氧化碳反应时就发现有痕量的乙酸。
1925-1928年英国Celanese公司的Henry Dreyfus开始研究此反应的催化剂,反应必须在高温和高压才能进行,他们发现以银或铜为促进剂的磷酸是一种有效的催化剂。
反应器的材料只有石墨或黄金作衬里时,才能经受310℃和20MPa (199atm)这样严格条件下的腐蚀.在甲醇羰基化反应中,甲醇的转化率为400,选择性约70%,试验的规模为100kg/天,但在30年代初期就停止了生产。
此后,美国、法国和德国都进行过类似的研究。
1942年德国法本工业公司建设了10吨/夭规模的试验工厂,二次大战后工作重新进行,并开发了碘化镍催化体系,碘化镍比钴等许多其他金属羰基化合物具有较高的催化活性。
反应条件为215℃和14MPa (138atm),反应在气相中进行,所以腐蚀问题并不严重。
BASF公司着重研究了有碘存在下的铜和钴的催化体系,开发了另一条高压羰基化工艺路线1966年美国B0rden化学公司引进BASF技术建r最高生产桃力曾达135000吨/年。
BASF工艺的操作压力高达76MPa (693atm),反应器需用Hastell0yc合金钢来制造。
1966年美国孟山都化学公司开发了另一种完全不同的方法,他们最初用铑—膦一碘系催化剂,可以在较低的温度和压力时反应。
应用此项工艺的总装置生产能力已达180万吨,而且远有增长的趋势。
孟山都低压甲醇碳基化法开发成功后,BASF高压甲醇羰基化工艺实际上已失去工业意义。
a、高压甲醇羰基化法甲醇、一氧化碳在含水的乙酸溶液中,以羰基钴为催化剂,碘甲烷为助催化剂组成的钴一碘催化体系,反应在约250℃和70MPa (693atm)下进行。
甲醇羰基化是放热反应,每公斤乙酸放热2219kJ,反应器中的热量依靠连续加进原料甲醇和一氧化碳予以吸收,反应热平衡则由甲醇原料预热器来调节。
粗酸和未反应的气体从反应器顶
部排出,冷却后,膨胀降压至1.01MPa(约l0atm),粗酸送分离系统放空气经碘甲烷回收后放空。
粗酸先经脱轻塔,脱除低沸物,再脱除催化剂,脱水,精制获得99.8%的成品乙酸。
以甲醇计乙酸的收率约90%,以一氧化碳计乙酸的收率为59%。
副产3.5%的甲烷和4.5%的液体物料(以生成乙酸计)。
主反应和主副反应如下:
副反应产物的生成量直接与催化剂的用量和水加入量有关。
在这些副反应中,一氧化碳
和水发生的水一气变接反应是最麻烦的,它产生的氢还会在该体系中发生一系列的加氢反应,从而生成甲烷和乙醛,乙醛加氢、氢醛化,醇醛缩合和醋化等生成许多副产物,生成量约占乙酸生成量的45%,其中主要是丙酸。
二甲醚可以和甲醇一起作为原料与一氧化碳反应生成乙酸.消耗定额列于表8.2.2-8.
高压羰基化反应器是用Hastell0y C合金钢衬里的塔式反应器,反应器内设置循环管由上升的气体提供能量达到擞拌混合的目的,也藉以保持反应器温度的均恒.
b,低压甲醇羰基化方法F.E. Parlik和J.F. R0th等在BASF工艺的基础上选用了铭一碘为主体催化刘的新的合成方法,反应可以在较温和的条件下进行。
这种方法在工业上称为孟山都法。
低压甲醇羰基化反应历程和高压法完全不同.该反应分五步进行。
RhLm是锥的羰基和碘的络合物,是一种具有一价阴离子的二碘二羰基铑,是低压甲醇羰基化催化荆的活性组份。
反应之初,碘甲烧与络合物先发生氧化加成反应,继而发生一氧化碳的配位络合,一氧化碳的顺式抽入形成酰基络合物,最后是酰基络合物水解生成乙酸和RhLm,构成催化循环过程。
全部反应过程中,碘甲烷与铑络合物的氧化加成反应速度最慢,因此是反应控制步骤.甲醇与一氧化碳在低压羰基化反应动力学表明,两者都对反应速度呈零级,而对铑和碘离子的浓度都呈一级反应,水和乙酸都不参与主反应,因此反应动力学表达式用下式来表示:
r=k(Rh)(I)
低压甲醇羰基化反应,生成乙酸的选择可达99%,所以,虽然也有副产物生成,但其量甚微,兹将此法的主副化学反应列述于下:
原料甲醇先经预热器预热送入反应器底部,同时一氧化碳由压缩机送入反应器,反应温度175-200℃,一氧化碳分压l .01-1 .52MPa。
由闪蒸塔釜来的母液,脱轻塔塔顶的轻馏份和脱水塔顶的水和乙酸一并送回反应器。
反应液经减压直接送至闪蒸塔,在此分离出粗乙酸、轻组份和含催化剂的母液。
含轻组份的粗醋酸以气相送至脱轻塔,于塔顶馏出碘甲烷.乙酸甲醋,二甲醚、水和少量甲醇。
塔釜为含水乙酸,送脱水塔,在塔顶除去水,塔釜为乙酸再送脱重组份塔,在脱重组份塔的侧线引出成品乙酸。
塔釜为含丙酸等高级竣酸的乙酸溶液,送焚烧炉烧却或进一步化工利用。
未反应的一氧化碳和副反应生成的甲烷、二氧化碳等气体在反应器顶部经高压冷凝后减压,再经轻组份回收塔回收碘甲烷后焚烧放空,生产流程如图8.2.2-6示。
_
孟山都法中母体催化剂是铑的卤化物,以碘化铑为好,商品三碘化铑也可直接使
用.助催化剂是碘甲烷,一般工厂自行配套生产碘甲烷,以减少运输造成的损失。
送入羰基化反应器之前,需把三碘化铑先制备成均相催化剂溶液,贮存备用.制备方法是将一定数量的碘化铑加入含碘甲烷的醋酸水溶液中,搅拌下升温至80-150℃和在0.2-1 . 0MPa通入一氧化碳直至全部溶解为止。
这种均相催化剂在生产过程中往返于反应器和闪蒸器之间而不失活,一般在使用一年以内无需再生。
铑的消耗不大于170mg/t乙酸。
催化剂再生是除去溶液中的
其他金属离子和反应液中的高聚物,即将碘化铑进行一次纯化。
纯化方法,一是离子交换法,羰基铑络合物以阴离子形式存在,用离子交换法除去其中的阳离子:另一是沉淀法,羰基铑络合物受热分解,如对溶液添加少量甲醇,常压下加热回流即可使绝大部分的铑以碘化铑的形式沉淀,而其他金属离子存在于乙酸溶液中。
两法均可用于工业生产,但两法均会有少量铑的损失。
碘甲烷助催化剂的制备分两步进行。
先将碘溶解于含氢碘酸的水溶液,在铑催化剂存在下,升温加压,一氧化碳作还原剂,碘与水反应生成氢碘酸,再降温降压,注入甲醇,甲醇与氢碘酸反应生成碘甲烷。
反应式如下式所示
低压羰基化反应液由甲醇、碘甲烷、水和乙酸组成,原料甲醇的起始浓度约8-20%,(重量.下同),碘甲烷的浓度约10-15%,乙酸和水作反应介质的溶钊,浓度分别为60-75%和8 -20%,由于反应过程发生一氧化碳和水的变换反应消耗一部分水,因此水也要在适当的部位予以补充反应液中铑离子的浓度约10的负4次方到10的负2次方mol/L。
为了保证催化剂的稳定,反应系统的压力和温度控制十分重要.通常反应器的热平衡是由闪蒸器的返回母液和原料甲醇预热器来承担。
反应系统提供的粗乙酸,经脱轻组份、脱水和脱重组份三塔分离可获得合格的成品乙酸,质量可达到药典级和食品级标准;孟山都法的质量指标见表8.2.2-9。
分离工艺中,除去微量的碘离子是比较困难的,除依靠物理过程外还得借助某些化学过程,但与其他合成工艺却完全不同,这里仅需要在脱水塔加入少量的低碳醇,如甲醇,就能把在塔内富集的氢碘酸转化为碘甲烷,然后从塔顶排出。
再在脱重塔添加少量的碱金属的氢氧化物可除去痕量的碘,使成品乙酸中的碘离子浓度降至40ppb以下,消耗定额列于表8.2.2-8。
低压甲醇羰基化用内衬Hastell0y合金的机械搅拌高压釜,目前使用的耐蚀材料的年腐蚀率可控制在0.1mm以下。
装置各工段大量物料的循环,尤其是反应系统的多股物流的物料平衡,需要自动在线分析仪和电子计算机控制系统予以保证。
三废包括含乙酸的排放气废水、废液和废渣,但数量不多。
排放气中约含40-80%的一氧化碳,其他为氢、二氧化碳、氮、氧和微量的乙酸、碘甲烷,集中于火炬燃烧后放空。
废水用石灰水中和,含丙酸、高碳羧酸和少量金属离子的废液需送焚烧炉处理。
少量的废渣
可作坑埋处理。