关键工序操作控制程序
特殊过程及关键工序控制程序
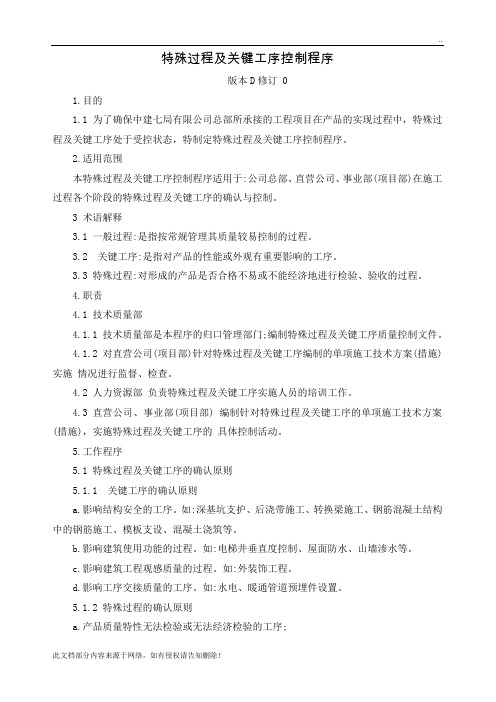
特殊过程及关键工序控制程序版本D修订 01.目的1.1 为了确保中建七局有限公司总部所承接的工程项目在产品的实现过程中,特殊过程及关键工序处于受控状态,特制定特殊过程及关键工序控制程序。
2.适用范围本特殊过程及关键工序控制程序适用于:公司总部、直营公司、事业部(项目部)在施工过程各个阶段的特殊过程及关键工序的确认与控制。
3 术语解释3.1 一般过程:是指按常规管理其质量较易控制的过程。
3.2 关键工序:是指对产品的性能或外观有重要影响的工序。
3.3 特殊过程:对形成的产品是否合格不易或不能经济地进行检验、验收的过程。
4.职责4.1 技术质量部4.1.1 技术质量部是本程序的归口管理部门;编制特殊过程及关键工序质量控制文件。
4.1.2 对直营公司(项目部)针对特殊过程及关键工序编制的单项施工技术方案(措施)实施情况进行监督、检查。
4.2 人力资源部负责特殊过程及关键工序实施人员的培训工作。
4.3 直营公司、事业部(项目部) 编制针对特殊过程及关键工序的单项施工技术方案(措施),实施特殊过程及关键工序的具体控制活动。
5.工作程序5.1 特殊过程及关键工序的确认原则5.1.1 关键工序的确认原则a.影响结构安全的工序。
如:深基坑支护、后浇带施工、转换梁施工、钢筋混凝土结构中的钢筋施工、模板支设、混凝土浇筑等。
b.影响建筑使用功能的过程。
如:电梯井垂直度控制、屋面防水、山墙渗水等。
c.影响建筑工程观感质量的过程。
如:外装饰工程。
d.影响工序交接质量的工序。
如:水电、暖通管道预埋件设置。
5.1.2 特殊过程的确认原则a.产品质量特性无法检验或无法经济检验的工序;b.产品质量特性需经使用后才能暴露出来的工序;c.产品质量特性需经破坏性试验才能暴露出来的工序。
如:基础灌注桩、地下室防水、钢筋焊接、预应力结构、大体积混凝土工程等。
5.2 关键工序及特殊过程的施工控制5.2.1 关键工序的施工控制a.项目部应在《施工组织设计》中明确界定关键工序。
医疗器械关键工序控制程序

医疗器械关键工序控制程序1目的对注塑等关键工序进行控制,确保产品质量满足规定要求。
2适用范围适用于注塑等关键工序的控制。
3职责3.1生产技术部负责编制关键工序的工艺文件,并对其工艺方法进行验证。
3.2设备部负责对关键工序的生产设备和操作人员进行验证。
3.3质管部、办公室参与关键工序的生产设备和操作人员进行验证。
3.4车间应对关键工序的工艺参数进行监视和控制。
4.程序4.1 工序控制点的操作人员严格执行《工艺文件》和《操作规程》,做好检验工作。
4.2 工序控制点的操作人员应对下道工序质量负责,并经常征求下道工序意见,及时向生产技术部反映所遇到的各种质量问题,生产技术部会同质管部一起研究纠正和预防措施,提高工序质量。
工序控制点操作人员应做好工序控制点的记录。
4.3 由生产技术部编制工序控制点的技术、工艺文件,其中包括必要的技术参数和质量记录,质管部编制必要的检验规程。
4.4 工序控制点的实施4.4.1 工序控制点由生产车间负责组织实施,操作人员需经专业培训,操作者必须按《操作规程》进行操作,并做好记录。
4.4.2 质管部负责按《检验规程》,对工序控制点的检测并记录。
4.4.3 工序中的设备控制按《基础设施控制程序》执行。
4.4.4 工序中使用的计量设备按《监测设备控制程序》执行。
4.5检查与考核4.5.1 生产技术部负责制定《关键工序监控点记录表》并实施考核,并作好记录。
4.5.2 生产技术部每月对工序质量控制点的检查考核情况进行汇总。
4.5.3 经考核凡连续三个月未达到规定要求,生产技术部会同有关部门进行分析,并采取纠正和预防措施确保工序质量控制点的有效实施,具体按《纠正措施控制程序》和《预防措施控制程序》执行。
4.5.4 控制点采用统计技术时应按《数据分析控制程序》的要求进行分析。
4.6 当关键工序有环境要求时,应在工序控制点的文件中作出规定并严格执行。
5.相关文件5.1 《人力资源控制程序》5.2 《记录控制程序》5.3 《过程和产品的监测程序》5.4 《关键(灭菌)工序过程控制管理制度》5.5 《验证管理制度》5.6 《工艺纪律检查制度》6.记录保存部门保存期限6.1 《关键工序监控点记录表》生产技术部 4年6.2 《生产工艺验证报告》生产技术部 4年6.3 《图样更改通知单》生产技术部 4年关键工序、特殊过程监控要求检查人:日期:年月日。
CTQ关键工序控制程序(含表格)

CTQ关键工序控制程序(IATF16949-2016)1 目的为规范本公司CTQ相关作业的管理,保证产品关键特性满足客户要求,降低不良率,特制定本程序。
2 范围适用于本公司内部的CTQ管理项目,以及CTQ管理出现异常的分析,改善及完善相关活动。
3 定义3.1 CTQ定义:Critical-To-Quality)的意思是质量关键特性点,是指为了满足“关键的需求或关键客户流程需求的产品或服务的一组特征,它是从顾客角度出发,影响顾客满意度的质量特性。
”4 权责本规程由品管部、生产部,技术装备部负责实施,其他部门共同遵守。
5 工作程序5.1 CTQ管理项目的选定:对顾客指定的关键特性,作为优先管理。
对影响产品品质的重要工序的特性和工程特性也作相应管理。
5.2 CTQ关键特性管理图的选定根据产品特性及管理需要,公司选用SPC控制均值-极差控制图.产品名称CTQ特性管理标准测定周期曲轴粗加工吸油管孔直径Φ11—Φ11.03 天/次曲轴精加工长轴圆度0.0015 5pcs/2小时/机长轴靠近支撑面圆度0.0025 5pcs/2小时/机长轴外圆粗糙度Ra0.30 5pcs/2小时/机偏心轴圆度0.0015 5pcs/2小时/机偏心轴表面粗糙度Ra0.20 5pcs/2小时/机长轴直径13.988±0.0035pcs/小时/机偏心轴直径13.980±0.0035pcs/小时/机假如某个时段失控,由SPC人员发送《失控通知单》给生产班长,进行及时调整。
5.3 CTQ工程能力的调查周期及管理项目.在稳定的生产过程中,要求CTQ工程每月测定 1 批, 32件/批。
计算CPK过程能力指数,并通过连续的观察,找到潜在的能力不足设备进行改善。
5.4 CTQ工程能力的计算及评价:对于CTQ关键工序,品管部根据程序测定对应的品质特性数据并进行记录,计算出CPK. 工程能力评价参考如下:等级Cpk 判断工程能力的有无措施A Cpk≥1.67 工程能力很充分可维持现状,或想办法减少成本等B 1.33≤Cpk<1.67 工程能力充分是理想状态,维持现状即可.C 1.00≤Cpk<1.33 工程能力不是很充分可考虑采取必要的措施以达到理想状态D 0.67≤Cpk<1.00 工程能力不足. 有必要工程的管理及改善.E Cpk<0.67 工程能力很不足离品质理想状态远. 需进行品质改善,追究原因,做紧急对策5.5 CTQ工程异常的处理规定品管部对输入的数据进行收集,须每个月进行工程能力分析,检讨。
关键工序质量控制点控制程序

中铁十一局集团桥梁有限公司咸安制梁场关键质量控制点控制程序《关键质量控制点控制程序》主要包括下列内容:1、目的2、适用范围 03、主要引用标准 04、箱梁预制关键质量控制点 04.1箱梁预制的关键质量点 04。
2关键质量控制要点 04.2.1 钢筋闪光对焊施工质量控制点 04.2。
2预应力孔道及保护层厚度控制 (1)4.2.2.1预应力孔道控制 (1)4.2.2。
2保护层厚度控制 (1)4。
2.3混凝土施工质量控制点 (2)4.2。
3。
1原材料控制 (2)4.2。
3.2计量控制 (2)4。
2。
3。
3浇筑检查 (2)4.2。
3。
4取样检查 (2)4。
2.3.5混凝土入模温度控制 (3)4。
2.3.6混凝土浇筑控制 (3)4.2.3.7混凝土养护检查 (3)4.2.3。
8混凝土养护控制 (4)4.2。
3。
9模板检验控制程序 (4)4.2.4张拉质量控制要点控制程序 (4)4。
2.4。
1钢绞线及相关附件 (4)4.2。
4。
2钢绞线数目 (5)4。
2。
4。
3油压千斤顶与油表校正报告 (5)4。
2.4.4后张法预应力施张检查 (5)4.2.4。
5梁体变形检查 (5)4.2.5管道压浆施工质量控制要点控制程序 (5)4。
2.5.1原材料控制 (5)4.2.5。
2计量控制 (5)4.2。
5.3施工检查 (6)4。
2.5。
4取样检查 (6)关键质量控制点控制程序1、目的通过本程序和相关文件的控制旨在对箱梁预制施工各关键质量控制点的施工进行有效的控制、管理和改进,以确保产品符合设计要求,达到预期的质量目标,满足工程质量总目标的要求。
2、适用范围本程序适用于中铁十一局集团桥梁有限公司咸安制梁场箱梁预制施工全过程。
3、主要引用标准TB10210-2001《铁路混凝土与砌体工程施工规范》JGJ18-2003《钢筋焊接及验收规程》TB10415—2007《铁路桥涵工程施工质量验收标准》TB10424—2007《铁路混凝土与砌体工程施工质量验收标准》科技基[2005]101号《客运专线高性能混凝土暂行技术条件》客运专线预应力混凝土预制梁暂行技术条件企业内控标准4、箱梁预制关键工序及质量控制点4.1 箱梁预制的关键工序箱梁预制施工的关键工序有:钢筋闪光对焊;预应力孔道及保护层;混凝土配制、拌和、浇筑、养护、强度;张拉;管道压浆.以上工序只能依据依时间、仪器、仪表、试验报告等判定并由具有合格资质的人员进行作业。
关键工序控制程序(HWH)

1.目的对公司产品生产过程中的关键工序的确认、控制措施及责任分工做出规定,以确保关键工序持续满足工艺要求。
2.定义与术语2.1 关键工序关键工序:指工序质量特性对产品的性能、寿命、可靠性和经济性有重大影响需要重点控制或与顾客满意相关的工序。
2.2 事故工装、设备故障造成停产四小时以上的为事故。
3.适用范围本程序规定了公司产品生产中关键工序的确认及管理。
本程序适用于压缩机和掘进类产品关键工序的管理。
4 职责4.1 工艺部门负责确定、建立关键工序,并负责牵头实施工艺纪律检查。
4.2 工艺部门负责关键工序工装的归口管理。
4.3 设备科负责关键工序设备的归口管理。
4.4 质量部负责组织关键工序的评审和审核。
4.5 质量部负责关键工序产品的质量检验。
4.6 生产部负责组织关键工序的均衡生产和车间负责关键工序的实施及关键工序工装、设备的日常管理。
5 控制程序5.1 关键工序的建立、确认和变更5.1.1 工艺部门在编制工艺方案时,应提出《关特防工序控制明细》(格式见附表1),确定关键工序的工装、设备及相关控制要求,经工艺部门领导审核、产品总师或副总师批准,下发至有关部门。
5.1.2 工艺部门对关键工序中的控制项目进行更改时,应经过充分试验、验证,经审批后下达更改通知方可执行。
必要时重新确认。
5.1.3 根据产品质量特性和企业质量状况的变化,工艺部门应及时提出关键工序变更建议,阐明变更原因,报总师或副总师批准后实施。
5.2 工艺装备的管理5.2.1 生产单位应建立关键工序的工装、设备台帐,填写工装、设备履历表;对关键工序的工装、设备作出明显标识;关键工序的工装、设备不得随意变更,确需变更时应报工艺部门批准。
5.2.2 关键工序的工装、设备应严格执行“定人定机”的要求,操作者上岗前应进行培训,做到持证操作,并相对稳定。
5.2.3 关键工序的工装、设备应有相应的保养制度,严格进行日常保养,确保其技术状态良好。
5.2.4 关键工序的工装、设备应有周检计划,针对每一工装、设备,由工艺部门对工装进行周期检定并记录,资产部对设备进行周期检定并记录,明确具体检定项目。
医疗器械关键工序控制程序

医疗器械关键工序控制程序1目的对注塑等关键工序进行控制,确保产品质量满足规定要求。
2适用范围适用于注塑等关键工序的控制。
3职责3.1生产技术部负责编制关键工序的工艺文件,并对其工艺方法进行验证。
3.2设备部负责对关键工序的生产设备和操作人员进行验证。
3.3质管部、办公室参与关键工序的生产设备和操作人员进行验证。
3.4车间应对关键工序的工艺参数进行监视和控制。
4.程序4.1 工序控制点的操作人员严格执行《工艺文件》和《操作规程》,做好检验工作。
4.2 工序控制点的操作人员应对下道工序质量负责,并经常征求下道工序意见,及时向生产技术部反映所遇到的各种质量问题,生产技术部会同质管部一起研究纠正和预防措施,提高工序质量。
工序控制点操作人员应做好工序控制点的记录。
4.3 由生产技术部编制工序控制点的技术、工艺文件,其中包括必要的技术参数和质量记录,质管部编制必要的检验规程。
4.4 工序控制点的实施4.4.1 工序控制点由生产车间负责组织实施,操作人员需经专业培训,操作者必须按《操作规程》进行操作,并做好记录。
4.4.2 质管部负责按《检验规程》,对工序控制点的检测并记录。
4.4.3 工序中的设备控制按《基础设施控制程序》执行。
4.4.4 工序中使用的计量设备按《监测设备控制程序》执行。
4.5检查与考核4.5.1 生产技术部负责制定《关键工序监控点记录表》并实施考核,并作好记录。
4.5.2 生产技术部每月对工序质量控制点的检查考核情况进行汇总。
4.5.3 经考核凡连续三个月未达到规定要求,生产技术部会同有关部门进行分析,并采取纠正和预防措施确保工序质量控制点的有效实施,具体按《纠正措施控制程序》和《预防措施控制程序》执行。
4.5.4 控制点采用统计技术时应按《数据分析控制程序》的要求进行分析。
4.6 当关键工序有环境要求时,应在工序控制点的文件中作出规定并严格执行。
5.相关文件5.1 《人力资源控制程序》5.2 《记录控制程序》5.3 《过程和产品的监测程序》5.4 《关键(灭菌)工序过程控制管理制度》5.5 《验证管理制度》5.6 《工艺纪律检查制度》6.记录保存部门保存期限6.1 《关键工序监控点记录表》生产技术部 4年6.2 《生产工艺验证报告》生产技术部 4年6.3 《图样更改通知单》生产技术部 4年。
关键工序的控制程序
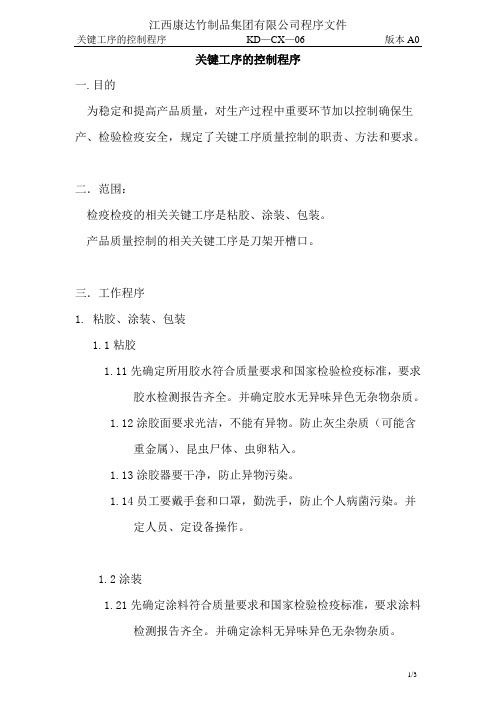
关键工序的控制程序一.目的为稳定和提高产品质量,对生产过程中重要环节加以控制确保生产、检验检疫安全,规定了关键工序质量控制的职责、方法和要求。
二.范围:检疫检疫的相关关键工序是粘胶、涂装、包装。
产品质量控制的相关关键工序是刀架开槽口。
三.工作程序1. 粘胶、涂装、包装1.1粘胶1.11先确定所用胶水符合质量要求和国家检验检疫标准,要求胶水检测报告齐全。
并确定胶水无异味异色无杂物杂质。
1.12涂胶面要求光洁,不能有异物。
防止灰尘杂质(可能含重金属)、昆虫尸体、虫卵粘入。
1.13涂胶器要干净,防止异物污染。
1.14员工要戴手套和口罩,勤洗手,防止个人病菌污染。
并定人员、定设备操作。
1.2涂装1.21先确定涂料符合质量要求和国家检验检疫标准,要求涂料检测报告齐全。
并确定涂料无异味异色无杂物杂质。
1.22涂装面要求光洁,不能有异物。
防止灰尘杂质(可能含重金属)、昆虫尸体、虫卵粘入。
1.23涂装车间要整洁,无灰尘。
要配水帘除尘机除尘。
1.24涂装工具(喷枪、气压泵、毛刷)要干净。
避免油污、杂质污染涂装质量。
1.25员工要戴手套和口罩,勤洗手,防止个人病菌污染。
并定人员、定设备操作。
1.3包装1.31包装产品和材料涂装面要求光洁,不能有异物。
防止灰尘杂质,昆虫尸体、虫卵包入。
1.32包装车间要整洁,独立,无灰尘。
1.33包装工具(气枪、封口机)要干净。
避免油污、杂质污染。
1.34包装员工要戴手套和口罩,勤洗手,防止个人病菌污染。
并定人员、定设备操作。
2. 开槽口2.1场地、人员、设备要求2.11开槽口工序必须在现场作出标识。
由工程技术主管按照客户要求在工艺文件上注明,对刀架槽口的、操作方法、原始记录、控制图表等作出具体规定。
2.12生产部组织对开槽口工序实行定人员、定设备操作。
操做员工应接受专业培训,管理教育,并经考核合格上岗。
2.13开槽工序所用仪器、设备其周检率和合格率均应为100%。
所用仪器设备由设备主管指定专人维护保养。
CTQ关键工序控制程序

CTQ管理控制程序1 目的为规范本公司CTQ相关作业的管理,保证产品关键特性满足客户要求,降低不良率,特制定本程序。
2 范围适用于本公司内部的CTQ管理项目,以及CTQ管理出现异常的分析,改善及完善相关活动。
3 定义3.1 CTQ定义:Critical-To-Quality)的意思是质量关键特性点,是指为了满足“关键的需求或关键客户流程需求的产品或服务的一组特征,它是从顾客角度出发,影响顾客满意度的质量特性。
”4 权责本规程由品管部、生产部,技术装备部负责实施,其他部门共同遵守。
5 工作程序5.1 CTQ管理项目的选定:对顾客指定的关键特性,作为优先管理。
对影响产品品质的重要工序的特性和工程特性也作相应管理。
5.2 CTQ关键特性管理图的选定根据产品特性及管理需要,公司选用SPC控制均值-极差控制图.产品名称CTQ特性管理标准测定周期曲轴粗加工吸油管孔直径Φ11—Φ11.03 天/次曲轴精加工长轴圆度0.0015 5pcs/2小时/机长轴靠近支撑面圆度0.0025 5pcs/2小时/机长轴外圆粗糙度Ra0.30 5pcs/2小时/机偏心轴圆度0.0015 5pcs/2小时/机偏心轴表面粗糙度Ra0.20 5pcs/2小时/机长轴直径13.988±0.0035pcs/小时/机偏心轴直径13.980±0.0035pcs/小时/机5.3 CTQ工程能力的调查周期及管理项目.在稳定的生产过程中,要求CTQ工程每月测定1 批, 32件/批。
计算CPK过程能力指数,并通过连续的观察,找到潜在的能力不足设备进行改善。
5.4 CTQ工程能力的计算及评价:对于CTQ关键工序,品管部根据程序测定对应的品质特性数据并进行记录,计算出CPK.等级Cpk 判断工程能力的有无措施A Cpk≥1.67 工程能力很充分可维持现状,或想办法减少成本等B 1.33≤Cpk<1.67 工程能力充分是理想状态,维持现状即可.C 1.00≤Cpk<1.33 工程能力不是很充分可考虑采取必要的措施以达到理想状态D 0.67≤Cpk<1.00 工程能力不足. 有必要工程的管理及改善.E Cpk<0.67 工程能力很不足离品质理想状态远. 需进行品质改善,追究原因,做紧急对策●品管部对输入的数据进行收集,须每个月进行工程能力分析,检讨。
关键工序控制程序
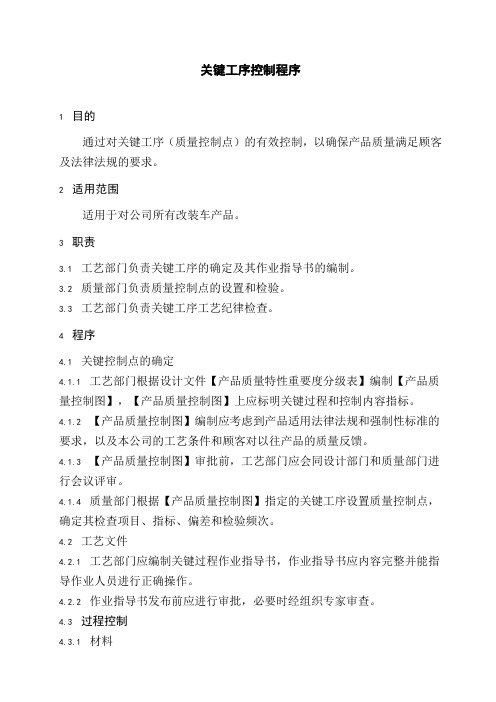
关键工序控制程序1 目的通过对关键工序(质量控制点)的有效控制,以确保产品质量满足顾客及法律法规的要求。
2 适用范围适用于对公司所有改装车产品。
3 职责3.1 工艺部门负责关键工序的确定及其作业指导书的编制。
3.2 质量部门负责质量控制点的设置和检验。
3.3 工艺部门负责关键工序工艺纪律检查。
4 程序4.1 关键控制点的确定4.1.1 工艺部门根据设计文件【产品质量特性重要度分级表】编制【产品质量控制图】,【产品质量控制图】上应标明关键过程和控制内容指标。
4.1.2 【产品质量控制图】编制应考虑到产品适用法律法规和强制性标准的要求,以及本公司的工艺条件和顾客对以往产品的质量反馈。
4.1.3 【产品质量控制图】审批前,工艺部门应会同设计部门和质量部门进行会议评审。
4.1.4 质量部门根据【产品质量控制图】指定的关键工序设置质量控制点,确定其检查项目、指标、偏差和检验频次。
4.2 工艺文件4.2.1 工艺部门应编制关键过程作业指导书,作业指导书应内容完整并能指导作业人员进行正确操作。
4.2.2 作业指导书发布前应进行审批,必要时经组织专家审查。
4.3 过程控制4.3.1 材料关键工序所用原辅材料、配件和半成品应经质量部门检验接收,流入本工序加工前操作人员应予复验,确保其适用性。
复验发现不适用及时标识并通知检验人员。
4.3.2 设备设备管理部门根据工艺要求,配置适宜的设备,确保其精度和加工能力;制造工程部根据工艺要求制造工艺工装。
设备管理部门应编制设备工装安全操作规程、检修计划和维护保养细则。
操作人员按【设备维护保养细则】的要求,对设备工装进行日常维护保养。
设备维修人员应【设备年度检修计划】的要求,对设备工装的功能、精度和安全防护进行周期检修。
4.3.3 人员操作人员应经过培训、考核合格;法律法规对岗位有要求的按其要求执行。
操作人员应能看懂设计文件、工艺文件,应能正确操作设备工装,应知晓质量控制点验收标准。
关键工序控制程序
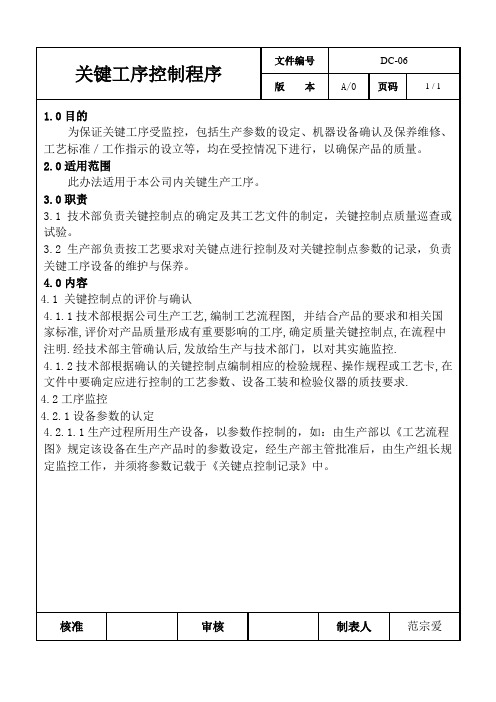
4.2工序监控
4.2.1设备参数的认定
4.2.1.1生产过程所用生产设备,以参数作控制的,如:由生产部以《工艺流程图》规定该设备在生产产品时的参数设定,经生产部主管批准后,由生产组长规定监控工作,并须将参数记载于《关键点控制记录》中。
定期对使用中的设备进行维护和保养,以保持其运行能力,且保存设备维修以及保养记录,具体操作按《设备管理规定》执行。
核准
审核
制表人
核准
审核
制表人
范宗爱
关键工序控制程序
文件编号
DC-07
版本
A-0
页码
2 / 3
核准
审核
制表人
关键工序控制程序
文件编号
DC-7
版本
A-0
页码
3 / 3
熔融加热℃.
焊接加热温度与加热时间的经验调整法建议采用软规范(即加热时
间升高,加热温度降低),具体调整方法是将加热时间确定,将加热温度自低温向高温调整,每焊一次将刚焊后的窗角掰开,观察焊接渣口情况,当渣口刚刚泛黄时,将温度下调5℃即可;
关键工序控制程序
文件编号
DC-06
版本
A/0
页码
1 / 1
1.0目的
为保证关键工序受监控,包括生产参数的设定、机器设备确认及保养维修、工艺标准/工作指示的设立等,均在受控情况下进行,以确保产品的质量。
2.0适用范围
此办法适用于本公司内关键生产工序。
3.0职责
3.1技术部负责关键控制点的确定及其工艺文件的制定,关键控制点质量巡查或试验。
食品生产关键质量控制点操作控制程序
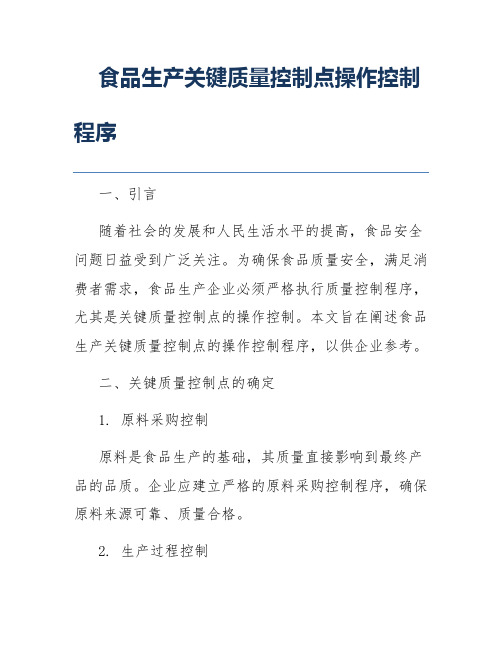
食品生产关键质量控制点操作控制程序一、引言随着社会的发展和人民生活水平的提高,食品安全问题日益受到广泛关注。
为确保食品质量安全,满足消费者需求,食品生产企业必须严格执行质量控制程序,尤其是关键质量控制点的操作控制。
本文旨在阐述食品生产关键质量控制点的操作控制程序,以供企业参考。
二、关键质量控制点的确定1. 原料采购控制原料是食品生产的基础,其质量直接影响到最终产品的品质。
企业应建立严格的原料采购控制程序,确保原料来源可靠、质量合格。
2. 生产过程控制生产过程是食品质量形成的关键环节,企业应制定科学的生产工艺流程,并对关键工序进行严格控制。
3. 设备与工具控制设备与工具的性能直接影响到食品生产的质量和效率,企业应定期对设备进行维护、校准和清洁,确保其正常运行。
4. 人员培训与管理员工是食品生产的关键因素,企业应加强对员工的培训和管理,确保其具备相应的技能和素质。
5. 包装与储存控制包装和储存是食品质量保持的关键环节,企业应制定合理的包装和储存制度,确保产品在运输和储存过程中质量稳定。
6. 产品检验与放行控制产品检验是确保食品质量的最后防线,企业应建立严格的检验制度,对产品进行全面、准确的检验,确保其符合质量标准。
三、关键质量控制点的操作控制程序1. 原料采购控制(1)建立供应商评估体系,对供应商进行定期评估和筛选。
(2)对原料进行严格检验,确保其符合质量标准。
(3)对原料进行标识和追溯,确保原料来源可追溯。
2. 生产过程控制(1)制定科学的生产工艺流程,明确关键工序和操作规范。
(2)对关键工序进行严格控制,确保生产过程符合标准。
(3)定期对生产设备进行维护和校准,确保设备正常运行。
3. 设备与工具控制(1)制定设备维护计划,定期对设备进行维护和清洁。
(2)对工具进行定期校准和更换,确保其性能稳定。
(3)培训员工正确使用和维护设备与工具。
4. 人员培训与管理(1)制定员工培训计划,定期对员工进行技能和素质培训。
CTQ关键工序控制程序
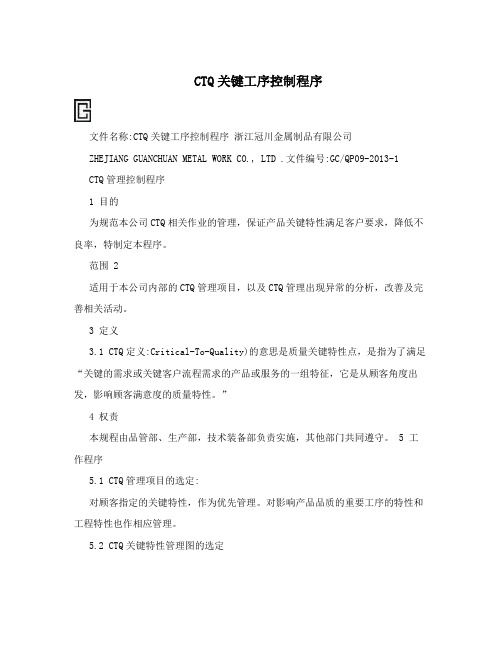
0.0025 长轴靠近支撑面圆度 5pcs/2小时/机
Ra0.30 长轴外圆粗糙度 5pcs/2小时/机
0.0015 曲轴精加工 偏心轴圆度 5pcs/2小时/机
Ra0.20 偏心轴表面粗糙度 5pcs/2小时/机
长轴直径 13.988?0.003 5pcs/小时/机
,由品管部确认后方可出货。 字样
, CTQ工程能力改善后的首批须经首件全检后经部门主管确认后方可量产。 6 相关表单
《SPC控制图》
《纠正和预防措施单》
制订: 审核: 批准;
范围 2
适用于本公司内部的CTQ管理项目,以及CTQ管理出现异常的分析,改善及完善相关活动。
3 定义
3.1 CTQ定义:Critical-To-Quality)的意思是质量关键特性点,是指为了满足“关键的需求或关键客户流程需求的产品或服务的一组特征,它是从顾客角度出发,影响顾客满意度的质量特性。”
4 权责
偏心轴直径 13.980?0.003 5pcs/小时/机 假如某个时段失控,由SPC人员发送《失控通知单》给生产班长,进行及时调整。 5.3 CTQ工程能力的调查周期及管理项目.
在稳定的生产过程中,要求CTQ工程每月测定 1 批, 32件/批。计算CPK过程能力指数,并通过连续的观察,找到潜在的能力不足设备进行改善。
离品
究原因,做紧急对策 5.5 CTQ工程异常的处理规定
, 品管部对输入的数据进行收集,须每个月进行工程能力分析,检讨。 , 品管部检验员发现数据脱离管理基准线或发现异常点时,告知相关部门。 , 由生产部联合品质部及相关部门对工程能力进行检讨并发出《纠正和预防措施单》。 , 对CTQ工程能力不足时生产的批次须安排人员进行检验。并标示”工程能力不足”
关键工序的识别和控制程序
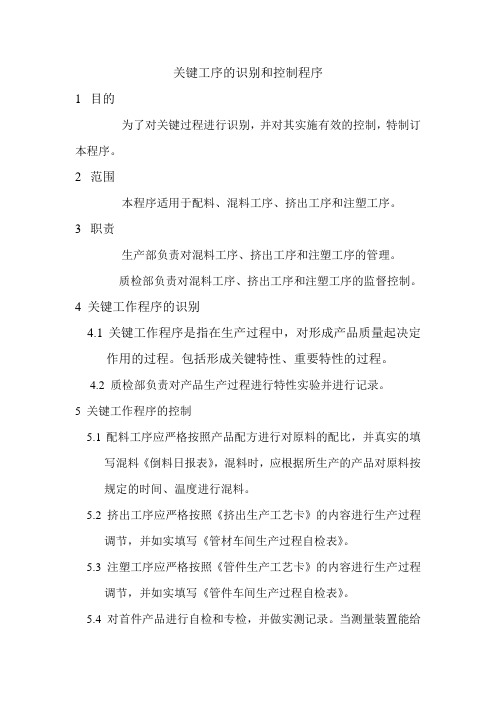
关键工序的识别和控制程序
1目的
为了对关键过程进行识别,并对其实施有效的控制,特制订本程序。
2范围
本程序适用于配料、混料工序、挤出工序和注塑工序。
3职责
生产部负责对混料工序、挤出工序和注塑工序的管理。
质检部负责对混料工序、挤出工序和注塑工序的监督控制。
4 关键工作程序的识别
4.1关键工作程序是指在生产过程中,对形成产品质量起决定
作用的过程。
包括形成关键特性、重要特性的过程。
4.2 质检部负责对产品生产过程进行特性实验并进行记录。
5 关键工作程序的控制
5.1配料工序应严格按照产品配方进行对原料的配比,并真实的填
写混料《倒料日报表》,混料时,应根据所生产的产品对原料按规定的时间、温度进行混料。
5.2 挤出工序应严格按照《挤出生产工艺卡》的内容进行生产过程
调节,并如实填写《管材车间生产过程自检表》。
5.3 注塑工序应严格按照《管件生产工艺卡》的内容进行生产过程
调节,并如实填写《管件车间生产过程自检表》。
5.4 对首件产品进行自检和专检,并做实测记录。
当测量装置能给
出具体测量值时,应记录实测的数据。
5.5按照有关可追溯性的要求,做好记录,并予以保存,确保其可
追溯性。
6 关键工作程序的管理
6.1 不定期的检查关键工序的工艺条件、过程记录和质量检验记
录的登记情况。
7 记录
《管材车间生产过程自检表》
《管件车间生产过程自检表》。
关键工序流程程序模板
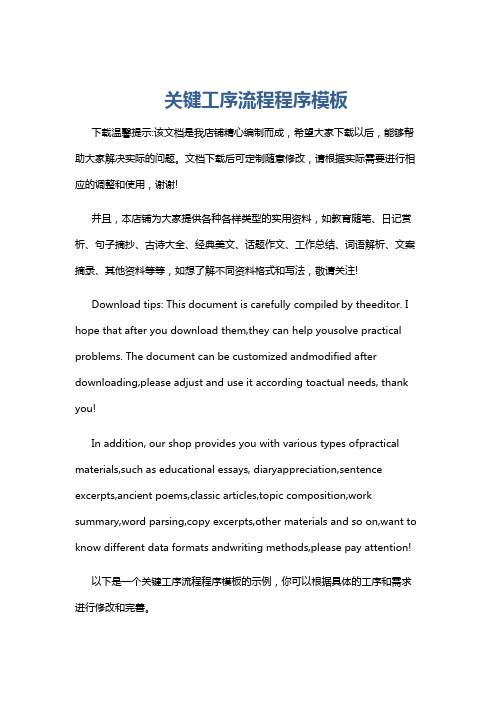
关键工序流程程序模板下载温馨提示:该文档是我店铺精心编制而成,希望大家下载以后,能够帮助大家解决实际的问题。
文档下载后可定制随意修改,请根据实际需要进行相应的调整和使用,谢谢!并且,本店铺为大家提供各种各样类型的实用资料,如教育随笔、日记赏析、句子摘抄、古诗大全、经典美文、话题作文、工作总结、词语解析、文案摘录、其他资料等等,如想了解不同资料格式和写法,敬请关注!Download tips: This document is carefully compiled by theeditor. I hope that after you download them,they can help yousolve practical problems. The document can be customized andmodified after downloading,please adjust and use it according toactual needs, thank you!In addition, our shop provides you with various types ofpractical materials,such as educational essays, diaryappreciation,sentence excerpts,ancient poems,classic articles,topic composition,work summary,word parsing,copy excerpts,other materials and so on,want to know different data formats andwriting methods,please pay attention!以下是一个关键工序流程程序模板的示例,你可以根据具体的工序和需求进行修改和完善。
关键工序质量控制点控制程序
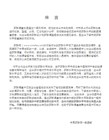
关键工序质量控制点控制程序一、隧道关键工序质量控制1、隧道开挖线放样⑴隧道掘进前放开挖轮廓线,要求按设计进行放开挖线,报现场工程师和测量监理工程师一起检查,合格后进行布制钻孔眼,孔眼间距,进行钻孔作业。
⑵隧道每开挖完一次进行检查,协作队伍检查开挖断面是否符合设计要求,欠挖部位进行凿除处理,合格后报现场工程师和监理工程师一起检查,合格后进行下道工序施工。
2、锚杆施工锚杆孔钻好后先自检,合格后报现场工程师、质检员和现场监理工程师一起检查,检查断面锚杆孔深、锚杆数量、锚杆孔环向间距及纵向间距、锚杆孔的角度和锚杆规格尺寸是否符合设计,合格后进行锚杆孔注浆、锚杆安装和挂钢筋网等相关后续作业,且所有锚杆必须安装垫板。
3、超前小导管施工超前小导管孔钻好后先自检,合格后报现场工程师、质检员和现场监理工程师一起检查,检查断面超前小导管孔深、超前小导管数量、超前小导管环向间距及纵向间距、超前小导管孔的角度和超前小导管规格长度是否符合设计,合格后进行超前小导管安装、注浆等相关后续作业。
4、钢筋网片加工制作及安装施工⑴钢筋网片加工必须有标准模具,控制好钢筋间距及焊接质量并符合设计要求,施工队伍先自检合格后报现场工程师检查,合格后由现场工师通知现场监理工程师一起检查。
⑵钢筋网片安装完成后,施工队伍先自检合格后报现场工程师检查,合格后由现场工师通知质检员及现场监理工程师一起检查;检查内容:钢筋网片搭接长度、钢筋网眼间距、钢筋网片保护层、钢筋网片层数是否符合设计要求。
5、钢拱架加工制作及安装施工⑴钢拱架加工必须有冷弯机等机具,控制好工字钢弯曲弧度及尺寸、钢板尺寸及孔径、焊接质量并符合设计要求,施工队伍先自检合格后报现场工程师检查,合格后由现场工师通知现场监理工程师一起检查。
⑵钢拱架安装完成后,施工队伍先自检合格后报现场工程师检查,合格后由现场工师通知质检员及现场监理工程师一起检查;检查内容:钢拱架位移偏差(包括横向和纵向)是否符合设计要求、钢拱架间距、钢拱架保护层、钢拱架搭接是否符合设计要求。
关键工序的识别与控制程序

关键工序检验规程1.目的:规定了关键工序质量控制的职责、方法和要求,以确保产品符合规定的质量要求;2.范围:适用于本公司锚杆、托盘生产过程中关键工序的质量控制。
3.职责3.1技术科负责提供关键工序技术文件。
3.2机电科负责提供关键工序质量控制文件,并负责对关键工序进行监督检查。
3.3机厂锚杆车间负责本程序在关键工序的实施,3.4机厂技术负责人负责确保关键工序所用设备、仪器的准确性。
3.5检验员负责关键工序产品特性的检验。
4.工作程序4.1根据生产的实际情况,确定如下工序为关键工序:即:压圆及滚丝工序4.2关键工序必须在现场作出标识。
4.3关键工序由技术科在工艺文件上注明,对控制的项目具体内容、操作方法、原始记录、控制图表等作出具体规定。
4.4锚杆车间对关键工序实行三定,即定工序、定人员、定设备。
4,4.1人员控制a.关键工序人员均应接受专业培训,管理教育,并经考核合格方能上岗。
b.关键工序人员必须了解螺纹滚压加工的基本知识,相关国家标准,熟练掌握加工工艺,人员保持相对稳定性。
c.关键工序人员能熟练使用质量控制图表等统计技术。
4.4.2设备控制a.关键工序所用仪器、仪表、设备其周检率和合格率均应为100%。
b.关键工序所用仪器设备由设备操作者负责维护保养并作好《设备维修保养记录》,c.仪器设备出现异常按《设备管理制度》进行处理。
4.5质量控制4.5.1关键工序操作工必须执行首件送检制度,经检查员确认合格后方可进行工作4.5.2关键工序操作工每加工100件必须自检一次,检验结果必须符合工艺要求,否则要分析原因并进行整改。
整改后的首件必须经检验员确认合格。
4.5.3车间检验员必须坚持巡检制度,每班不得少于4次,每次抽检数量不得少于6件。
- 1、下载文档前请自行甄别文档内容的完整性,平台不提供额外的编辑、内容补充、找答案等附加服务。
- 2、"仅部分预览"的文档,不可在线预览部分如存在完整性等问题,可反馈申请退款(可完整预览的文档不适用该条件!)。
- 3、如文档侵犯您的权益,请联系客服反馈,我们会尽快为您处理(人工客服工作时间:9:00-18:30)。
受控状态:
程序文件
关键控制点操作控制程序
第一版
1.目的
为加强对关键工序控制点的重点控制,严格工艺纪律,保证生产操作按规定方法和程序进行,确保生产出满足规定要求的产品,特制定本程序文件。
2.范围
2.1本程序适用于公司所有关键工序控制点操作过程的控制和管理。
3.职责
3.1 科技处负责关键工序工艺流程的策划,关键工序控制点的确定,关键工序控制点的工艺考核,《安全操作法》的制定、管理和监督执行。
3.2调度处负责《生产事故处理预案》的制定、管理和考核,对《安全操作法》的执行情况
进行抽查。
3.3 动力车间(仪表工段)负责关键工序生产过程DCS 控制系统的维护与管理。
3.4生产车间负责关键工序《安全操作法》和《生产事故处理预案》的起草和培训、组织演练和检查操作法的执行情况。
车间负责本部门关键质量控制点操作控制程序的起草。
4 工作程序
4.0 程序图 4.1 操作过程
4.1.1开停车及正常操作规定
《安全操作法》严格规定了各关键工序正常操作、正常开停车及紧急开停车的操作方法。
关键工序操作人员必须严格按照关键工序《安全操作法》的规定进行操作。
4.1.2《安全操作法》
4.1.2.1 编写:公司所有关键工序应制定相应的《安全操作法》。
《安全操作法》由科技处组织安排有关人员依据产品生产过程特点、工艺流程和工艺参数等技术要求起草编写,经科技处及相关处室审核,由生产副总和总工程师批准后发布、执行。
4.1.2.2 发放:《安全操作法》应发放到相关岗位操作人员和管理人员。
4.1.2.3 执行
(1)《安全操作法》由车间主任、工段长、设备员、安全员等对执行情况进行严格的检查,保证各项操作要求得到落实和执行。
工艺员重点对车间关键控制点工艺指标进行检
查。
(2)车间应对关键工序岗位操作人员进行《安全操作法》知识的培训和考核,人力资源处对指导、培训和考核情况进行检查。
具体执行《人力资源管理控制程序》。
(3)科技处应对车间工艺执行情况进行检查,并保留记录,对查出问题进行处理。
(4)调度处在组织日常生产过程中,对关键工序生产岗位操作法的执行情况进行随机检查。
上述培训、工艺检查、考核应留有检查记录,作为考核的依据。
4.1.2.4 管理
关键工序《安全操作法》由科技处按照《工艺管理制度》进行管理。
4.1.2.5 修改
操作法在贯彻执行过程中,若发现与生产实际不相吻合的地方,车间工艺员经核实、分析原因后,及时向科技处提出修改申请。
具体执行《工艺管理制度》。
4.1.3 《生产事故处理预案》
4.1.3.1编写
《生产事故处理预案》由调度处组织安排有关车间起草编写,经调度处及相关处室审核、汇编,由生产副总批准后发布、执行。
《生产事故处理预案》应发放到相关车间、处室、生产岗位的有关人员。
4.1.3.2 执行与管理
《生产事故处理预案》应作为生产过程异常情况处理的重要依据,车间和相关部门要积
极组织员工对进行学习和演练,不断提高处理异常情况的能力。
4.1.3.3 修改
当某种产品生产工艺过程出现较大变化时,车间应对生产应急预案提出相应修改意见,经调度处审核、生产副总经理批准后发布修订。
具体执行《文件控制程序》。
4.1.4DCS控制系统
4.1.4.1 动力车间对DCS控制系统进行全面的维护和管理,按照《安全操作法》的要求设置、修改工艺参数,确保正常运行。
使用车间按照规范进行操作,提供系统正常运行所需的环境和安全。
4.1.4.2 明确设定操作人员和仪表工段的权限、保密要求,确保安全运行。
4.1.4.3 动力车间组织编制《DCS控制系统使用管理办法》,形成的记录按《质量记录控制程序》执行。
4.2岗位操作原始记录要求
4.2.1操作原始记录必须真实准确;
4.2.2操作原始记录一律用圆珠笔或钢笔逐项进行填写,某些项目无需填写时,用“/”填写,不得空项。
4.2.3各项记录一旦完成,任何部门或个人不得擅自修改。
如出现笔误或后证实记录不准确,可在原始记录上采用划改的形式进行修改,但须签更改人姓名。
4.2.4原始操作记录由各部门整理后自己保存,保存期限为3年。
5.相关和支持性文件
5.1《质量记录控制程序》
5.2《人力资源管理控制程序》
5.3《工艺管理制度》
5.4《DCS控制系统使用管理办法》
5.5《生产车间事故处理预案》
5.6《文件控制程序》
6. 质量记录
6.1《生产岗位原始记录》
6.2《工艺检查记录》
6.3《工艺(配方)变更申请单》
更改栏。