活塞杆加工工艺规范
活塞杆加工工艺

17.精磨
13.镀后半精磨
12.磨小头
21.磨小头 22.镀后半精磨 23.镀后精磨24.镀后抛光 14.镀后精磨
15.镀后抛光
25.外观检验
16.外观检验
国产加工流程
意大利加工流程
各工序的加工工艺
1、下料:
各工序的加工工艺
1、下料:
★材料领用是关键: 根据生产计划,领取相对应的产品所需原材料的
单,但需注意的问题较多: 1.钢号容易领错误; 2.规格型号容易看错; 3.长度容易出现忽长忽短; 4.端面容易出现斜面大; 5.容易出2、淬前校磨:
活塞杆的加工工艺
因时间关系, 暂讲到这里
活塞杆的加工工艺
谢谢!
活塞杆加工工艺流程
主讲:朱红远
2019年3月
内容说明
活塞杆在减振器的重要性 活塞杆的种类及型号 活塞杆的制作流程 分讲各工序的加工方法,使用设备、 量检具及质量问题点
活塞杆在减振器中的重要性
1.起着联接作用 2.活塞杆失效模式: ⑴.配合尺寸失效时影响装配、异响 ⑵.表面缺陷(划伤、斑点、材料缺陷等)造成的 漏油 ⑶.表面粗糙的不合格,造成漏油 ⑷.活塞杆断裂,后果严重
各工序的加工工艺
使用量具: 下料工序是活塞杆加工工序最简单的工序,控制的尺寸
的也非常单一,就是一个总长; 使用量具就是一个0-500的游标卡尺。 要会使用游标卡尺 使用工装:
剪切模:要定期鉴定(6个月),检查刀块的磨损 程度 磨损后对会加大产品断面的不平整度。
各工序的加工工艺
下料工序的总结: 下料工序是活塞杆加工工序最简单的工序,虽然看似简
⑵、调整定位:根据产品的要求,设定定位装置(最容易出现 因长短定错造成批量报废)
活塞杆加工工艺说明书

活塞杆加工工艺说明书
活塞杆是内燃机中的重要零部件之一,它承受着往复运动时的巨大冲击力和复杂的摩擦力,因此加工工艺的好坏直接影响着活塞杆的使用寿命和性能。
下面将为您介绍活塞杆加工的工艺说明书。
一、材料选择
活塞杆的材料要求比较高,一般选用高品质的合金钢或不锈钢材料,这些材料具有高强度、高耐磨性、高耐腐蚀性和良好的韧性等优点。
二、车削加工
活塞杆的车削加工是其主要的加工工艺之一,其目的是为了保证活塞杆的精度和平滑度。
首先需要在车床上进行粗车,根据活塞杆的尺寸和要求进行车削,要求车削顺序、深度、切削速度和切削深度等参数合理,确保加工精度和表面质量。
三、磨削加工
在车削加工的基础上,还需要进行磨削加工,以提高加工精度和表面平滑度。
磨削工艺一般采用球墨铸铁磨轮,磨削前需进行准备工作,如清洗、校准、结构调整等,以确保磨削的精度和效果。
四、热处理
活塞杆在加工完成后还需要进行热处理,目的是为了消除内部应
力和提高杆的硬度、耐磨性和耐腐蚀性。
热处理方法一般采用淬火加
温处理,加热温度、保温时间、淬火介质和淬火温度等参数需要精确
控制,以确保处理后的活塞杆性能稳定。
五、检验质量
加工完成后的活塞杆需要进行质量检验,检验项目包括尺寸精度、表面平滑度、硬度和耐磨性等指标,以确保产品质量符合标准和要求。
一般采用量具、显微镜、硬度计和摩擦试验机等检测设备进行检验。
在活塞杆加工中,要注意机器设备的维护保养和操作规范,选材、加工和处理要严格按照要求执行,以确保生产出具有优良性能和寿命
长久的活塞杆。
活塞杆的机械加工工艺规程

1.活塞杆的工艺性分析1.1零件图样的分析mm×770mm自身圆度公差为0.005mm。
(1)φ500-025.0mm中心线的同轴度公差为φ0.05mm。
(2)左端M39×2-6g螺纹与活塞杆φ500.0025-mm中心线的同轴度公差为φ0.02mm。
(3)1:20圆锥面轴心线与活塞杆φ500-.0025(4)1:20圆锥面自身圆跳动公差为0.005mm。
(5)1:20圆锥面涂色检查,接触面积不小于80%。
mm×770mm表面渗氮,渗氮层深度0.2~0.3mm,表面硬度62~65HRC。
(6)φ500-025.0材料38CrMoALA是常用的渗氮处理用钢。
1.2零件的工艺分析(1)活塞杆在正常使用中,承受交变载荷作用,φ500mm×770mm处有密封装置往-025.0复摩擦其表面,所以该处要求硬度高又耐磨。
mm×770mm部分经过调质处理和表面渗氮后,芯活塞杆采用38CrMoALA材料,φ500-.0025部硬度为28~32HRC,表面渗氮层深度0.2~0.3mm,表面硬度为62~65HRC。
这样使活塞杆既有一定的韧性,又具有较好的耐磨性。
(2)活塞杆结构比较简单,但长径比很大,属于细长轴类零件,刚性较差,为了保证加工精度,在车削时要粗车、精车分开,而且粗、精车一律使用跟刀架,以减少加工时工件的变形,在加工两端螺纹时要使用中心架。
(3)在选择定位基准时,为了保证零件同轴度公差及各部分的相互位置精度,所有的加工工序均采用两中心孔定位,符合基准统一原则。
(4)磨削外圆表面时,工件易产生让刀、弹性变形,影响活塞杆的精度。
因此,在加工时应修研中心孔,并保证中心孔的清洁,中心孔与顶尖间松紧程度要适宜,并保证良好的润滑。
砂轮一般选择:磨料白刚玉 (WA),粒度60#,硬度中软或中、陶瓷结合剂,另外砂轮宽度应选窄些,以减小径向磨削力,加工时注意磨削用量的选择,尤其磨削深度要小。
活塞杆加工工艺
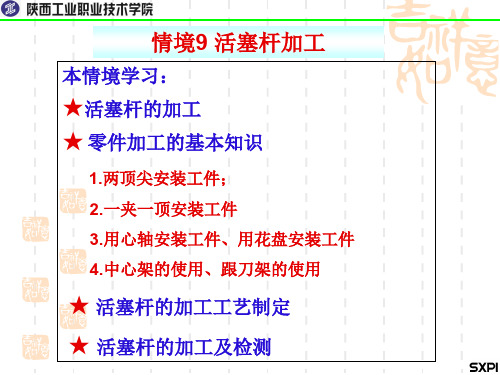
1.开机运行 2.正确安装零件 3.正确安装刀具 4.正确调整机床 5.零件试切 6.打扫机床
视频
9-5 零件的检查
在检验工件之前回答下列问题: •根据图样和检测要求确定所需要的量具和检具 •怎样游标卡尺进行测量 •怎样安装工件
9-6 零件加工的评估总结
1.细长轴加工的特点 2.怎样加紧工件 3.如何选择机床附件 4.加工应该注意的问题
8 用花盘安装工件
图图99.9.9
9-2 零件加工的基础知识
9 在花盘弯板安装工件
图9.10
视频
9-3 零件加工的工序卡
零件工序卡
9-4 零件的加工实施
生产准备:接受工作任务,领取图样,工艺,刀具,工装量具,检查 毛坯的质量
工件加工:能按图样加工出产品,产品应该符合尺寸精度,形位 精度,表面精度要求,能用量具检验质量
图9.3
9-2 零件加工的基础知识
活塞杆加工工艺流程

活塞杆加工工艺流程
《活塞杆加工工艺流程》
活塞杆是内燃机中的重要零部件,其加工工艺流程对于活塞杆的质量和性能有着至关重要的影响。
在活塞杆的加工过程中,需要经历多道工序和严格的工艺要求。
首先,活塞杆的原材料需要经过初步的加工,包括锻造、热处理等工艺,以保证其材料的均匀性和机械性能的稳定。
接下来,需要进行粗加工,将原材料切割成标准的尺寸,并进行车削等工艺,以确保其外形的精确度。
随后,进行精密加工,包括外圆磨削、内孔加工等工序,以确保活塞杆的尺寸精度和表面粗糙度符合工艺要求。
同时,还需要进行表面处理,例如镀铬、喷涂等工艺,来提高活塞杆的耐磨性和抗腐蚀性能。
在加工过程中,需要严格控制各道工序的工艺参数,包括切削速度、切削深度、刀具选择等,以确保加工质量和效率。
而且,还需要对加工过程中的温度、振动等因素进行监测和控制,以保证活塞杆在加工过程中不会产生裂纹或变形。
总的来说,活塞杆的加工工艺流程需要严格执行,确保每道工序都符合要求,才能生产出高质量的活塞杆产品。
这样不仅能够保证内燃机的性能和可靠性,也能够提高产品的市场竞争力。
活塞杆制造工艺简介
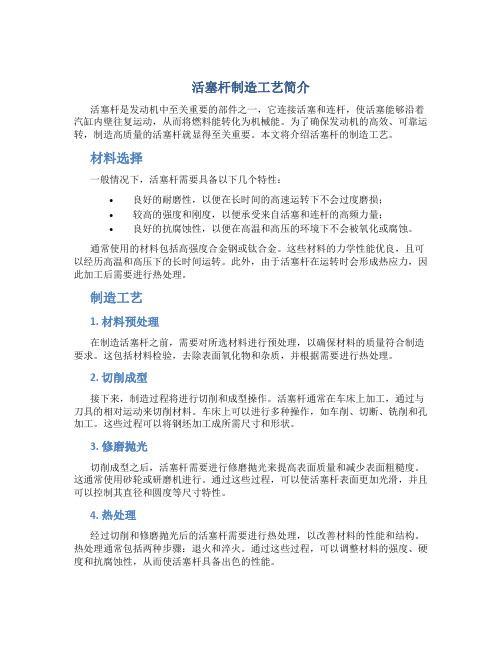
活塞杆制造工艺简介活塞杆是发动机中至关重要的部件之一,它连接活塞和连杆,使活塞能够沿着汽缸内壁往复运动,从而将燃料能转化为机械能。
为了确保发动机的高效、可靠运转,制造高质量的活塞杆就显得至关重要。
本文将介绍活塞杆的制造工艺。
材料选择一般情况下,活塞杆需要具备以下几个特性:•良好的耐磨性,以便在长时间的高速运转下不会过度磨损;•较高的强度和刚度,以便承受来自活塞和连杆的高频力量;•良好的抗腐蚀性,以便在高温和高压的环境下不会被氧化或腐蚀。
通常使用的材料包括高强度合金钢或钛合金。
这些材料的力学性能优良,且可以经历高温和高压下的长时间运转。
此外,由于活塞杆在运转时会形成热应力,因此加工后需要进行热处理。
制造工艺1. 材料预处理在制造活塞杆之前,需要对所选材料进行预处理,以确保材料的质量符合制造要求。
这包括材料检验,去除表面氧化物和杂质,并根据需要进行热处理。
2. 切削成型接下来,制造过程将进行切削和成型操作。
活塞杆通常在车床上加工,通过与刀具的相对运动来切削材料。
车床上可以进行多种操作,如车削、切断、铣削和孔加工。
这些过程可以将钢坯加工成所需尺寸和形状。
3. 修磨抛光切削成型之后,活塞杆需要进行修磨抛光来提高表面质量和减少表面粗糙度。
这通常使用砂轮或研磨机进行。
通过这些过程,可以使活塞杆表面更加光滑,并且可以控制其直径和圆度等尺寸特性。
4. 热处理经过切削和修磨抛光后的活塞杆需要进行热处理,以改善材料的性能和结构。
热处理通常包括两种步骤:退火和淬火。
通过这些过程,可以调整材料的强度、硬度和抗腐蚀性,从而使活塞杆具备出色的性能。
5. 表面处理最后,活塞杆还需要进行表面处理以保护其表面免受腐蚀和磨损。
这通常包括钝化和涂漆。
钝化可以使表面产生一层氧化膜,从而提高其耐腐蚀性。
涂漆则可以在身体表面形成一层保护层,以提高其抗磨损性。
活塞杆的制造工艺涉及到多个环节,包括材料选择、切削成型、修磨抛光、热处理和表面处理等。
活塞杆加工实用工艺要求规范

实用文档xxxx有限公司文件名称:活塞杆加工工艺规范文件编号:GY03-14-2015文件签章有效/受控状态:编制 : 技术工艺科审核:审批:修改记录单版本时间简述A 2015年2月活塞杆加工工艺规范1 引用标准GB/T1800.4-99 孔、轴的极限偏差表 GB/T1801-99 公差配合的选择 GB/T1184-96 形位公差值GB/T1031-95 表面粗糙参数及其数值 厂标等效JB/Z307 GB/T193-81 GB/T196-81 GB/T5786.2-86 GB/T5796.3-86 GB/T6403.5-86 GB/T145-89 GB200-89 GB699-1999 GB908-87 GB/T3-79JB/ZQ0138-80 金属切削加工工艺守则 普通螺纹直径与螺距系列 梯形螺纹基本尺寸 普通螺纹直径与螺距系列 梯形螺纹基本尺寸 砂轮越程槽 中心孔 碳素结构钢 优质碳素结构钢 锻制圆钢和方钢规格普通螺纹的收尾、兼距、退刀槽和倒角单线梯形螺纹的收尾、退刀槽和倒角尺寸2 需用设备(1)100t 开式油压机(2)校直用一组支承滚轮、划针盘、直尺 (3)乙炔氧气加热器 (4)卧式车床C6163,长8m (5)手工交流焊机 (6) 热处理(回火)设备(7) 砂带磨头、外圆磨床、砂盘抛磨头 (8)螺纹检验用环、塞规 3 适用范围本工艺守则适用于加工液压启闭机活塞杆、柱塞杆及部分工业液压缸的活塞杆。
4 活塞杆类型基本有三种4.1 实心活塞杆,见图4.14.2中空型活塞杆由杆头、杆身(无缝管)、杆尾组焊而成,见图4.24.3中空带进油管的活塞杆,见图4.3由杆头、杆身、杆尾及内进油管组焊而成。
将4.2、4.3两种活塞杆称为组合活塞杆图4.1图4.2图4.35 备料及毛坯制作5.1 活塞杆常用材料有45#、35#及40Cr,通常情况下,45#、35#是正火态供货。
具体按设计要求。
5.2毛坯余量的确定选用确定活塞杆坯料余量,应根据其长径比、坯料状态(热轧圆钢,锻圆)通常情况热轧圆钢直径余量6~12mm,长度余量5~10mm。
活塞杆加工工艺及程序编制
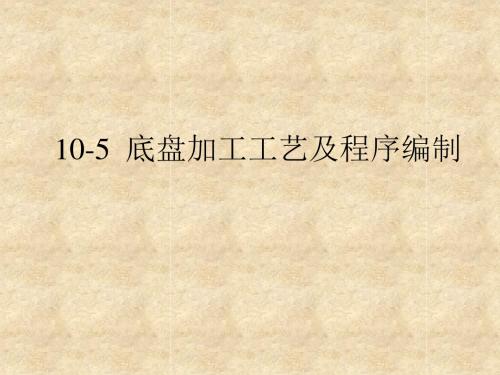
7
8 9 10 11
精铣槽底面转角
M3孔位 底面上M2孔位 平台上M2孔位 铣削第二面散热槽
底盘加工工艺及程序编制
二、计划 选择加工设备、夹具、工具等
• 粗加工用普通铣床。 • 精加工使用数控铣床。
底盘加工工艺及程序编制
二、计划 选择切削用量 成本核算
• 材料费用
•
粗加工费用
轴加工工艺及程序编制
按工序集中的原则划分工序。
加工型腔时,以底面作为主要定位基准,避免了基准 不重合误差,确保底面与其它面之间的垂直度公差。 。
底盘加工工艺及程序编制
二、计划 工艺规程设计 • 确定工序集中和分散程度,确定加工顺序
先加工外侧面,然后加工内腔 。
主要工艺过程
序号 1 2 3 4 5 6 加工内容 粗铣,去除大部分余量 精铣两个凸台上表面 精铣底面 精铣槽底面 精铣内轮廓 精铣内轮廓转角
底盘加工工艺及程序编制
二、计划 工艺规程设计
•确定主要面加工方法和加工方案 :主要面的最高尺 寸公差为8级,表面粗糙度是Ra3.2μm,参照教科书表 3-16,采用粗铣——精铣的加工方案。 •划分加工阶段 :两个阶段。
底盘加工工艺及程序编制
二、计划 工艺规程设计 • 确定工序集中和分散程度,确定加工顺序
底盘加工工艺及程序编制
一、资讯 计算生产纲领,确定生产类型:小批生产 零件分析
• 结构分析
长24和宽18的凸台要求表面质量严格是该零件的显 著特点,表面粗糙度超差,将造成热泵散热不良,严重 影响设备的性能。
底盘加工工艺及程序编制
一、资讯 零件分析
•技术条件分析
尺寸公差 形位公差 表面粗糙度
底盘加工工艺及程序编制
液压缸活塞杆加工注意事项

液压缸活塞杆加工注意事项液压缸活塞杆加工是液压系统中不可或缺的元件之一。
活塞杆的加工质量直接影响到整个液压系统的工作效率和稳定性。
在加工液压缸活塞杆时,需要注意以下几个方面:1. 材料选择:液压缸活塞杆通常采用优质合金钢材料,如45#钢、40Cr等。
这些材料具有良好的机械性能和耐磨性能,能够满足液压系统的工作要求。
2. 尺寸精度:活塞杆的加工要求具有较高的尺寸精度,包括直径精度、圆度精度等。
这些尺寸精度的要求直接影响活塞杆与密封件的配合,对液压系统的工作稳定性和密封性能有着重要影响。
3. 表面加工:活塞杆的表面加工是保证密封性能和耐磨性能的重要环节。
常见的表面加工方法有镀铬和涂覆热喷涂等。
镀铬可以提高活塞杆的硬度和耐磨性,同时也能增加活塞杆与密封件的配合功能。
热喷涂则可以在活塞杆表面形成一层强度较高的涂层,提高耐磨性能。
4. 表面粗糙度:活塞杆的表面粗糙度对其密封性能和润滑性能有着重要影响。
过高的表面粗糙度会增加泄漏的可能性,而过低的表面粗糙度则会影响密封件的润滑效果。
因此,在活塞杆的加工过程中,需要控制好表面粗糙度,确保其在一定范围内。
5. 硬度要求:液压缸活塞杆的硬度要求通常较高,这是为了提高其耐磨性能和使用寿命。
通过调整热处理工艺可以获得合适的硬度值,常见的热处理方法有淬火和回火等。
6. 加工工艺:液压缸活塞杆的加工工艺通常包括车削、研磨和热处理等。
在进行这些加工过程时,需要控制好加工参数,确保尺寸精度和表面质量。
同时,还需要注意刀具的选择和磨损情况,定期检查和更换刀具,以保证加工质量。
7. 装配和检测:在液压缸活塞杆加工完成后,需进行装配和检测。
在装配时,要注意活塞杆与液压缸的配合间隙,确保其滑动自如。
在检测方面,可以采用光学投影仪、测量仪等进行尺寸检测,以及硬度计、金相显微镜等进行质量检测。
总之,加工液压缸活塞杆需要注意材料选择、尺寸精度、表面加工、表面粗糙度、硬度要求、加工工艺、装配和检测等方面的问题。
活塞杆加工工艺规范

活塞杆加工工艺规范Newly compiled on November 23, 2020xxxx 有限公司文件名称:活塞杆加工工艺规范 文件编号:GY03-14-2015 文件签章有效/受控状态: 编 制 : 技术工艺科 审 核:审 批:活塞杆加工工艺规范1 引用标准GB/ 孔、轴的极限偏差表 GB/T1801-99 公差配合的选择 GB/T1184-96 形位公差值GB/T1031-95 表面粗糙参数及其数值 厂标等效JB/Z307 GB/T193-81 GB/T196-81 GB/ GB/ GB/ GB/T145-89 金属切削加工工艺守则 普通螺纹直径与螺距系列 梯形螺纹基本尺寸 普通螺纹直径与螺距系列 梯形螺纹基本尺寸 砂轮越程槽 中心孔GB200-89 GB699-1999 GB908-87 GB/T3-79JB/ZQ0138-80 碳素结构钢 优质碳素结构钢 锻制圆钢和方钢规格普通螺纹的收尾、兼距、退刀槽和倒角单线梯形螺纹的收尾、退刀槽和倒角尺寸 2 需用设备(1)100t 开式油压机(2)校直用一组支承滚轮、划针盘、直尺 (3)乙炔氧气加热器 (4)卧式车床C6163,长8m (5)手工交流焊机 (6) 热处理(回火)设备(7) 砂带磨头、外圆磨床、砂盘抛磨头 (8)螺纹检验用环、塞规 3 适用范围本工艺守则适用于加工液压启闭机活塞杆、柱塞杆及部分工业液压缸的活塞杆。
4 活塞杆类型基本有三种实心活塞杆,见图 中空型活塞杆由杆头、杆身(无缝管)、杆尾组焊而成,见图 中空带进油管的活塞杆,见图由杆头、杆身、杆尾及内进油管组焊而成。
将、两种活塞杆称为组合活塞杆图 图 图5 备料及毛坯制作活塞杆常用材料有45#、35#及40Cr ,通常情况下,45#、35#是正火态供货。
具体按设计要求。
毛坯余量的确定选用确定活塞杆坯料余量,应根据其长径比、坯料状态(热轧圆钢,锻圆)通常情况热轧圆钢直径余量6~12mm,长度余量5~10mm。
介绍活塞杆的机械加工工艺

介绍活塞杆的机械加工工艺大家都知道,活塞杆是我们日常应用于气缸运动执行部件中的一个零件,它是支持活塞做功的一个连接部件。
如果我们是在正常的情况下,进行使用活塞杆的话,其活塞杆就可以起到一个承载交变载荷的作用,从而提高配合性质。
因此活塞杆对于加工方面的要求比较高。
那么您知道活塞杆是怎么进行加工的吗?下面佛山欧贝特活塞杆技术人员为大家介绍一下活塞杆的机械加工工艺。
现在就以上的活塞杆图纸为例,来为大家介绍一下活塞杆机械加工工艺:1、下料:佛山欧贝特活塞杆机械加工工艺过程的第一步骤就是下料,需下棒料φ80mm×760mm 。
在下料时需要用到锯床这个工艺设备。
2、锻造:将棒料自由锻成φ62mm×1150mm。
3、热处理:即进行退火,退火是一种金属热处理工艺。
4、划线:划两端中心孔线。
5 、钳工:钻两端中心孔B2.5。
6 、粗车:在粗车时就先夹一端,顶尖顶另一端,然后再将粗车外圆至φ55mm。
7 、粗车:倒头装夹工件时,需顶另一端中心孔,车外圆至φ55mm接工序6加工处。
8 、热处理:在这个热处理中,主要指的是调质处理,我们需要把调质处理28~32HRC。
9、粗车:夹一端,中心架支承另一端,然后切下右端6mm做试片,进行金相组织检查,端面车平,钻中心孔B2.5 。
10、粗车:在倒头装夹工作时,则需要用中心架支撑另一端,车端面,保证总长1090mm,钻中心孔B2.5 。
11、精车:两顶尖装夹工作,车工件右端M39×2-6g,长60mm,直径方向留加工余量1mm,车φ500025.0-mm×770mm时,要使用跟刀架,保证1:20的锥度并留有加工余量1mm 。
12 、精车:倒头两顶尖装夹工件,车另一端(左端)各部及螺纹M39×2-6g,长度100mm,直径方向留加工余量1mm,六方处外径车至φ48mm,并车六方与φ500025.0-mm连接的锥度。
13、磨:主要修研两中心孔。
减震器活塞杆工艺流程
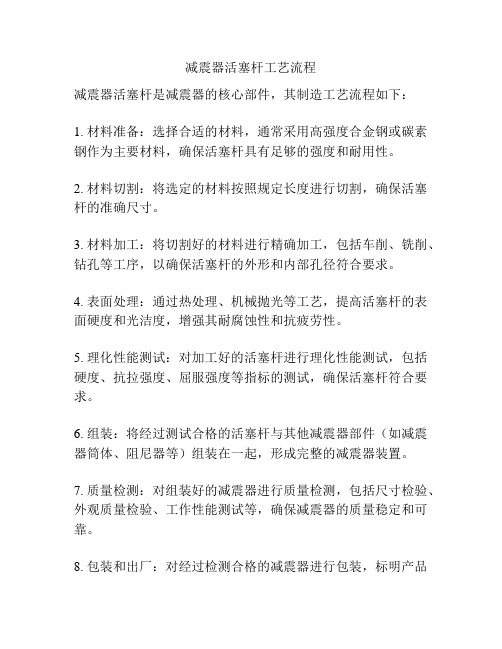
减震器活塞杆工艺流程
减震器活塞杆是减震器的核心部件,其制造工艺流程如下:
1. 材料准备:选择合适的材料,通常采用高强度合金钢或碳素钢作为主要材料,确保活塞杆具有足够的强度和耐用性。
2. 材料切割:将选定的材料按照规定长度进行切割,确保活塞杆的准确尺寸。
3. 材料加工:将切割好的材料进行精确加工,包括车削、铣削、钻孔等工序,以确保活塞杆的外形和内部孔径符合要求。
4. 表面处理:通过热处理、机械抛光等工艺,提高活塞杆的表面硬度和光洁度,增强其耐腐蚀性和抗疲劳性。
5. 理化性能测试:对加工好的活塞杆进行理化性能测试,包括硬度、抗拉强度、屈服强度等指标的测试,确保活塞杆符合要求。
6. 组装:将经过测试合格的活塞杆与其他减震器部件(如减震器筒体、阻尼器等)组装在一起,形成完整的减震器装置。
7. 质量检测:对组装好的减震器进行质量检测,包括尺寸检验、外观质量检验、工作性能测试等,确保减震器的质量稳定和可靠。
8. 包装和出厂:对经过检测合格的减震器进行包装,标明产品
型号、规格和生产日期等信息,随后发货出厂。
整个减震器活塞杆的制造过程需要严格控制每个环节,确保产品的质量和性能符合要求。
在每个工艺步骤中,都需要仔细操作和检验,避免出现材料缺陷、尺寸不准确等问题。
同时,还需要配备专业的检测设备和技术人员,对活塞杆的理化性能进行测试,以保证其在使用过程中的安全和可靠性。
只有通过严谨的工艺流程和质量控制,才能生产出高品质的减震器活塞杆,满足市场和客户的需求。
活塞杆加工工艺及程序编制
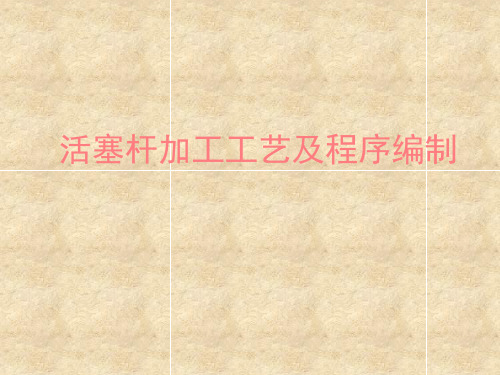
活塞杆加工工艺及程序编制
一、资讯 生产条件:注塑机上的零件,每台数量4件, 该产品年产量50台,备品率10%,机械加工废品 率大约1.5%。 任务要求:制定活塞杆(SC-02)的加工工艺, 编写数控加工程序,通过模拟仿真检验加工程 序。
设备名称 加工中心 数控铣床 数控车床 数控车床 普通车床
二、计划 选择切削用量 成本核算
• • • • • 材料费用 粗加工费用 热处理费用 精加工费用 其它费用
搭中心架,车端面,修中心孔.
调头, 搭中心架,车端面至总长,车对Φ35X7台阶.
夹Φ35外圆,顶右端,精车外圆Φ48及两端20°倒角;
精车5条环形槽; 精车Φ20外圆.
活塞杆加工工艺及程序编制
二、计划 选择加工设备、夹具、工具等
• 粗加工用普通车床。 • 半精加工及精加工使用数控车床。
活塞杆加工工艺及程序编制
活塞杆加工工艺及程序编制
一、资讯 计算生产纲领,确定生产类型:小批生产
零件分析
• 功用: Φ40f8 外圆集导向、定位和安装 三项功能 于一身; 锯齿形环槽承受150kN的拉力 。
活塞杆加工工艺及程序编制
一、资讯
零件分析
• 结构与技术条件分析:尺寸公差、形位公差和表 面粗糙度。 • 材料特性:调质处理后,可获得强度、塑性和韧 性都很好的机械性能。
型号 常州多棱TH5640 大连机床XD40 沈阳机床CK6140 济南第一机床CK616i 6150/6140
数量 3台 10台 5台 16台 若干
普通铣床
数控车床
立式、卧式
CL-20A
2台
1台
加工中心
数控车床
DMC-63V
活塞杆工艺流程

两顶尖
工位器具编号
工位器具名称
工序工时(分)
准终
单件
工步号
工步内容
工艺装备
主轴转速
切削速度
进给量
切削深度
进给次数
工步工时
r/min
m/min
mm/r
mm
机动
辅助
1
安装
0
0
0
0
2
车外圆至φ51mm
590
13
0.36
3.5
1
3
车左端M39x2-6g
363.4
80
0.7
1
1
车φ50x770mm至接口处
第五部分:夹具总装图...............................................................................................20
第六部分:夹具零件一..............................................................................................21
车
间
工
段
设备
工艺装备
工时
准终
单件
055
磨
修研两中心孔
研磨机
060
磨
两顶尖装夹工件,精磨1:20锥度至图样要求
M131W
跟刀架、磨具
装夹:见工序图[60]
065
磨
两顶尖装夹,粗磨φ50x770mm
M131W
游标卡尺、砂轮
装夹:见工序图[65]
070
热处理
渗氮处理,深度0.25-0.35mm
活塞杆在加工中的技术要求

活塞杆在加工中的技术要求第一篇:活塞杆在加工中的技术要求活塞杆在加工中的技术要求活塞杆在加工中的技术要求,是它很重要的一个特点。
可以说,加工技术的好坏会直接影响产品的质量和使用寿命。
活塞杆的加工首先是采用滚压加工,因为在表面层会留有表面残余压应力,它是有助于表面微小裂纹的封闭,能够阻碍侵蚀作用的扩展,从而提高表面抗腐蚀能力,延缓疲劳裂纹的产生和扩大,也能够提高活塞杆的疲劳强度。
然后,通过滚压使表面形成一层冷作硬化层,以减少接触面的弹性和塑性变性,从而提高油缸杆表面的耐磨性,避免了磨削引起的灼伤。
另外,滚压后,它的粗糙度会减小,有利于提高它的配合性质,降低活塞运动时对密封件或者密封圈所造成的磨损,提高油缸整体结构的使用寿命。
第二篇:钢筋加工安全技术要求钢筋加工安全技术要求一、现场施工一般要求1、进入施工现场人员必须正确戴好合格的安全帽,系好下颚带,锁好带扣;2、作业时必须按规定正确使用个人防护用品,着装要整齐,严禁赤脚和穿拖鞋、高跟鞋进入施工现场;3、新进场的作业人员,必须首先参加入场安全教育培训,经考试合格后方可上岗,未经教育培训或考试不合格者,不得上岗作业;4、从事特种作业的人员,必须持证上岗,严禁无证操作,禁止操作与自己无关的机械设备;5、施工现场禁止吸烟,禁止追逐打闹,禁止酒后作业;6、施工现场的各种安全防护设施、安全标志等,未经领导及安全员批准严禁随意拆除和挪动。
二、钢筋加工机具的使用要求1、一般要求1)、机械的安装应该保持结实稳固,且保持水平位置。
固定式机械应有可靠的基础;移动式机械作业时必须契紧行走轮。
2)、加工较长的钢筋时,必须有专人帮扶,并听从操作人员指挥,不得任意推拉。
3)、作业后,堆放好成品,清理场地,切断电源,锁好开关箱,做好润滑工作。
2、钢筋调直切断机1)、料架、料槽安装平直,并对准导向管、调直筒和下切刀孔的中心线。
2)、用手转动飞轮,检查传动机构和工作装置,调整间隙,紧固螺栓,确认正常后,起动空运转,并检查轴承无异响,齿轮噬合良好,运转正常后,方可作业。
活塞杆机械加工工艺

活塞杆机械加工工艺1. 简介活塞杆是发动机的关键部件之一,起着连接活塞和连杆的作用。
活塞杆的机械加工工艺对其质量和性能有着重要影响。
本文将介绍活塞杆机械加工工艺的步骤和注意事项。
2. 加工工艺步骤2.1 初加工2.1.1 材料准备首先要选择适合的活塞杆材料,常用的有45号钢、40Cr、20Cr等。
材料应具有足够的强度和耐磨性,同时要考虑加工性能和成本。
根据所需长度,将原材料进行切割。
在切割过程中要注意锯片的选用和切割速度,以防止表面出现裂纹或过热变形。
2.1.3 粗切削使用车床或铣床对材料进行粗加工,将其切削成近似形状的圆柱体。
这一步骤主要是为了减小后续加工工序的工作量,提高加工效率。
2.2.1 长度控制通过测量和标记,控制活塞杆的长度。
在车床上,可以使用外径卡尺等工具进行测量,确保活塞杆的长度符合要求。
2.2.2 精车加工使用车床对活塞杆进行精车加工,使其外径和形状达到要求。
在加工过程中,要注意控制切削速度和进给量,以保证加工质量。
精车加工后的活塞杆表面应平整光滑,无明显划痕。
2.2.3 柱状度检测精车加工后,需要对活塞杆的柱状度进行检测。
可以使用测微计或环形卡尺等工具进行测量,确保活塞杆的直径误差在规定范围内。
2.2.4 精磨加工对活塞杆进行精磨加工,以提高其表面质量和尺寸精度。
精磨后,活塞杆的表面应光洁度高,尺寸偏差小。
2.3 热处理2.3.1 预处理在进行热处理之前,需要对活塞杆进行预处理。
一般采用退火或正火处理,以消除内部应力和改善材料的织构。
2.3.2 淬火对活塞杆进行淬火处理,以提高其硬度和强度。
淬火过程中要控制冷却速度和温度,避免出现裂纹和变形。
2.3.3 回火淬火后的活塞杆过硬,需要进行回火处理,以提高其韧性和抗疲劳性能。
回火温度和时间的选择要根据具体材料和要求决定。
2.4 表面处理2.4.1 抛光对活塞杆进行抛光处理,以提高其表面光洁度。
抛光可以采用机械抛光或化学抛光,使活塞杆表面光滑亮丽。
活塞杆零件机械加工工艺规程及定位方案设计
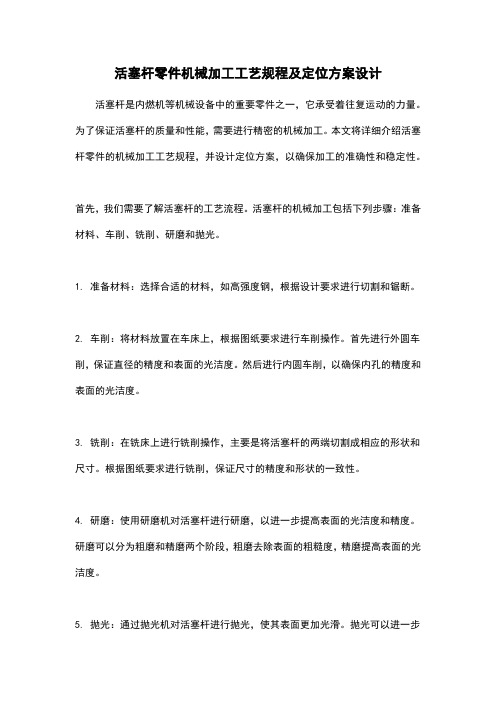
活塞杆零件机械加工工艺规程及定位方案设计活塞杆是内燃机等机械设备中的重要零件之一,它承受着往复运动的力量。
为了保证活塞杆的质量和性能,需要进行精密的机械加工。
本文将详细介绍活塞杆零件的机械加工工艺规程,并设计定位方案,以确保加工的准确性和稳定性。
首先,我们需要了解活塞杆的工艺流程。
活塞杆的机械加工包括下列步骤:准备材料、车削、铣削、研磨和抛光。
1. 准备材料:选择合适的材料,如高强度钢,根据设计要求进行切割和锯断。
2. 车削:将材料放置在车床上,根据图纸要求进行车削操作。
首先进行外圆车削,保证直径的精度和表面的光洁度。
然后进行内圆车削,以确保内孔的精度和表面的光洁度。
3. 铣削:在铣床上进行铣削操作,主要是将活塞杆的两端切割成相应的形状和尺寸。
根据图纸要求进行铣削,保证尺寸的精度和形状的一致性。
4. 研磨:使用研磨机对活塞杆进行研磨,以进一步提高表面的光洁度和精度。
研磨可以分为粗磨和精磨两个阶段,粗磨去除表面的粗糙度,精磨提高表面的光洁度。
5. 抛光:通过抛光机对活塞杆进行抛光,使其表面更加光滑。
抛光可以进一步提高活塞杆的表面质量和亮度。
在进行活塞杆的机械加工时,为了确保加工的准确性和稳定性,需要使用定位方案。
定位方案设计应考虑以下因素:1. 确定加工定位点:根据活塞杆的形状和尺寸,确定加工定位点的位置。
通常选择活塞杆的两端作为定位点,以确保加工的一致性。
2. 选择适当的定位方式:根据加工工艺和设备的特点,选择合适的定位方式。
常用的定位方式有直接定位、间接定位和复合定位等。
3. 设计定位夹具:根据活塞杆的形状和尺寸,设计定位夹具。
夹具应具有良好的刚性和稳定性,以确保加工的准确性和稳定性。
4. 确定加工顺序:根据活塞杆的形状和尺寸,确定加工的顺序。
通常先进行外圆车削,再进行内圆车削和其他加工操作。
通过以上的工艺规程和定位方案设计,可以确保活塞杆零件的机械加工质量和性能。
同时,加工过程中要严格按照工艺规程进行操作,定期检查和维护设备,以保证加工的准确性和稳定性。
活塞杆加工工艺
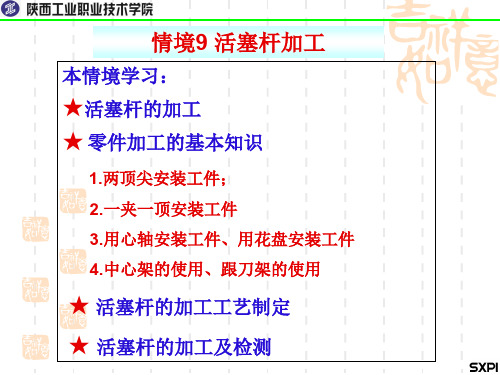
图图99.9.9
9-2 零件加工的基础知识
9 在花盘弯板安装工件
图9.10
视频
9-3 零件加工的工序卡
零件工序卡
9-4 零件的加工实施
生产准备:接受工作任务,领取图样,工艺,刀具,工装量具,检查 毛坯的质量
工件加工:能按图样加工出产品,产品应该符合尺寸精度,形位 精度,表面精度要求,能用量具检验质量
5s管理:穿好劳动防护用品,严格按照操作规程,注意安全, 保持机床和环境的卫生,注意日常保养
9-4-1 生产准备
零件图样 工艺卡片 刀具准备 量具准备 其他工装 毛坯检验
明确图纸的要求 明确工艺卡片的要求 刀具的准备 按照工艺卡片准备量具 其他工装的准备 检查材料,热处理、规格缺陷 等
9-4-2 工件加工与管理
图9.3
9-2 零件加工的基础知识
3. 一夹一顶安装工件
图9.4
9-2 零件加工的基础知识
4. 用心轴安装工件
图9.5
9-2 零件加工的基础知识
5 中心架的使用
图9.6
视频
9-2 零件加工的基础知识
6 跟刀架的使用
图9.7
9-2 零件加工的基础知识
7 跟刀架支承车削细长轴
图9.8
9-2 零件加工的基础知识
刀具的选用
分
工件的装夹
析
车削工艺卡
9-1-1 零件样图
图 9.1活塞杆
9-1-2 活塞杆加工工艺过程
9-1-2 活塞杆加工工艺过程
9-1-2 活塞杆加工工艺过程
9-1-2 活塞杆加工工艺过程
9-2 零件加工的基础知识
1、用两顶尖安装工件
图9.2
9-2 零件加工的基础知识
油缸活塞杆的机械加工工艺流程

油缸活塞杆的机械加工工艺流程展开全文油缸活塞杆的机械加工工艺流程,活塞杆的质量好坏,直接关系到油缸的质量、寿命、承载等技术要求。
技术要求1、1:20锥度接触面积不少于80%。
2、φ50mm部分氮化层深度为0.2~0.3mm,硬度62~65HRC。
3、材料38CrMoALA。
零件图样分析1)φ50mm×770mm自身圆度公差为0.005mm。
2)左端M39×2-6g螺纹与活塞杆φ50mm中心线的同轴度公差为φ0.05mm。
3)1:20圆锥面轴心线与活塞杆φ50mm中心线的同轴度公差为φ0.02mm。
4)1:20圆锥面自身圆跳动公差为0.005mm。
5)1:20圆锥面涂色检查,接触面积不小于80%。
6)φ50mm×770mm表面渗氮,渗氮层深度0.2~0.3mm,表面硬度62~65HRC。
工艺分析1)活塞杆在正常使用中,承受交变载荷作用,φ50mm×770mm处有密封装置往复摩擦其表面,所以该处要求硬度高又耐磨。
活塞杆采用38CrMoALA材料,φ50mm×770mm部分经过调质处理和表面渗氮后,芯部硬度为28~32HRC,表面渗氮层深度0.2~0.3mm,表面硬度为62~65HRC。
这样使活塞杆既有一定的韧性,又具有较好的耐磨性。
2)活塞杆结构比较简单,但长径比很大,属于细长轴类零件,刚性较差,为了保证加工精度,在车削时要粗车、精车分开,而且粗、精车一律使用跟刀架,以减少加工时工件的变形,在加工两端螺纹时要使用中心架。
3)在选择定位基准时,为了保证零件同轴度公差及各部分的相互位置精度,所有的加工工序均采用两中心孔定位,符合基准统一原则。
4)外圆表面时(磨削后还可以用滚压工艺,使活塞杆耐磨性提高),工件易产生让刀、弹性变形,影响活塞杆的精度。
因此,在加工时应修研中心孔,并保证中心孔的清洁,中心孔与顶尖间松紧程度要适宜,并保证良好的润滑。
砂轮一般选择:磨料白刚玉(WA),粒度60#,硬度中软或中、陶瓷结合剂,另外砂轮宽度应选窄些,以减小径向磨削力,加工时注意磨削用量的选择,尤其磨削深度要小。
- 1、下载文档前请自行甄别文档内容的完整性,平台不提供额外的编辑、内容补充、找答案等附加服务。
- 2、"仅部分预览"的文档,不可在线预览部分如存在完整性等问题,可反馈申请退款(可完整预览的文档不适用该条件!)。
- 3、如文档侵犯您的权益,请联系客服反馈,我们会尽快为您处理(人工客服工作时间:9:00-18:30)。
xxxx有限公司文件名称:活塞杆加工工艺规范文件编号:GY03-14-2015文件签章有效/受控状态:编制 : 技术工艺科审核:审批:修改记录单活塞杆加工工艺规范1 引用标准GB/T1800.4-99 孔、轴的极限偏差表 GB/T1801-99 公差配合的选择 GB/T1184-96 形位公差值GB/T1031-95 表面粗糙参数及其数值 厂标等效JB/Z307 GB/T193-81 GB/T196-81 GB/T5786.2-86 GB/T5796.3-86 GB/T6403.5-86 GB/T145-89 GB200-89 GB699-1999 GB908-87 GB/T3-79JB/ZQ0138-80 金属切削加工工艺守则 普通螺纹直径与螺距系列 梯形螺纹基本尺寸 普通螺纹直径与螺距系列 梯形螺纹基本尺寸 砂轮越程槽 中心孔 碳素结构钢 优质碳素结构钢 锻制圆钢和方钢规格普通螺纹的收尾、兼距、退刀槽和倒角单线梯形螺纹的收尾、退刀槽和倒角尺寸2 需用设备(1)100t 开式油压机(2)校直用一组支承滚轮、划针盘、直尺 (3)乙炔氧气加热器 (4)卧式车床C6163,长8m (5)手工交流焊机 (6) 热处理(回火)设备(7) 砂带磨头、外圆磨床、砂盘抛磨头 (8)螺纹检验用环、塞规 3 适用范围本工艺守则适用于加工液压启闭机活塞杆、柱塞杆及部分工业液压缸的活塞杆。
4 活塞杆类型基本有三种4.1 实心活塞杆,见图4.14.2中空型活塞杆由杆头、杆身(无缝管)、杆尾组焊而成,见图4.2 4.3中空带进油管的活塞杆,见图4.3由杆头、杆身、杆尾及内进油管组焊而成。
将4.2、4.3两种活塞杆称为组合活塞杆图4.1图4.2图4.3 5 备料及毛坯制作5.1 活塞杆常用材料有45#、35#及40Cr,通常情况下,45#、35#是正火态供货。
具体按设计要求。
5.2毛坯余量的确定选用确定活塞杆坯料余量,应根据其长径比、坯料状态(热轧圆钢,锻圆)通常情况热轧圆钢直径余量6~12mm,长度余量5~10mm。
锻圆直径余量15~25mm,长度余量28~38mm,详见表5.表5.2 棒材外径双面切削余量 L/D mm注:1、热轧圆钢应校直 2、锻圆应保证粗车光出,不留黑皮5.3校直5.3.1实心活塞杆:在压力机上进行校直,工件安放在两个滚轮架上,用划针座先离开滚轮架300~500mm,每隔400~500mm转动工件,测其最高、最低点,并标记位置数值,然后放在压力机上进行校直。
也可直接置于压力机工作台上,用肉眼看出弓高点,用液压机校直。
5.3.2对于杆身为无缝管的中空活塞杆,采用火焰校直法:将无缝管杆身置放在两个滚轮架上,用座盘划针距滚轮架300~500mm以后间隔500~1000mm,转动工件测其最高点、最低点并标记位置、数值,并划好“◇”加热区,弓度向上,用乙炔火焰在加热区域上进行加热,利用其自重下垂(或加压重件)进行校直。
5.3.3无缝管杆身内孔应进行除锈、磷化处理,否则将污染液压油。
5.4组合活塞杆零件制造5.4.1组合活塞杆各部组成零件名称杆头:用于装活塞的一端称活塞杆杆头,简称杆头。
杆尾:露出油缸体外部的一端称活塞杆杆身,简称杆尾。
杆身:杆头、杆尾之间的中间段(无缝管)称活塞杆身,简称杆身。
进油管:连接于杆头、杆尾,并穿过杆身的管子称为进油管。
5.4.2杆头的制造:按零件图制作,其长度满足活塞档距焊缝40~60 mm,并留端面余量,见表5.2,必须钻通孔,孔径φ18~φ25,外孔口车成锥角60°倒角,长5~10,其外圆同杆身,焊接坡口按“手工电弧焊守则”3.5节图3.5。
5.4.3杆尾的制造:基本上同5.4.2,不同的是不钻通孔,但外端面可不钻中心孔。
中心孔规格见图表5.4.4杆身的制造:车支承档,将卡箍套入工件离一端1~2m,长径比大于50宜装入两个卡箍,四爪夹一端,架上中心架,划针盘校调,车端面,车支承档,车坡口,钻(修)中心锥孔面,调面,拆移中心架,车另一个支承档,车焊接坡口。
支撑挡外径大于活塞杆公称直径0.5 mm~2mm,圆度公差﹤0.03。
6 组装、焊接按图组装到位,定位焊、焊接,见“手工焊接工艺守则”和“气保焊工工艺守则”并按要求探伤,合格后转下道工序。
7 热处理活塞杆通常粗加工后精加工前安排热处理,常有(1)正火(2)回火去应力(3)调质,根据设计要求采用。
7.1活塞杆(含锻圆、组合活塞杆的杆头、杆尾、杆身)均为正火态供货。
7.2用热轧圆钢做活塞杆,下料后可直接调质。
7.3锻圆经粗车,探伤检验合格后,进行调质处理。
7.4组合杆经焊接、探伤合格后,可进行回火去应力处理,如要求进行调质处理,可不进行回火去应力处理,直接进行调质处理。
8 车8.1 工件装夹校正实心杆:将卡箍套装于实心杆某一适当位置,离杆端500~1000mm(视长径比可装套入一个或两个卡箍)四爪夹一端,架,座盘式划针校正毛坯工件外圆。
组合杆:四爪夹、架、顶、校。
8.2 车支承档,钻中心孔,车长度实心杆:具有双拖板的车床,可在近卡处车支承档及另一头支承档,外圆大于设计名义尺寸1-2 mm,粗糙度达Ra3.2,失园度﹤0.03,车平面钻中心孔,(按坯料直径钻B型中心孔)见表8.2对于新热轧圆钢,毛坯圆度较好的,可不用卡箍,直接架于中心架上,靠近卡爪处车支承档,调面,架,车支承档、平面、钻中心孔。
(中心孔规格见表8.2)对于较短的实心圆钢,可预先在端面上划出中心孔位,在钻床或用手电钻、镗床钻中心孔。
尾座顶尖应调整达到与车床主轴同轴切与轨道平行,确保工件外圆柱面不产生锥度。
组合杆:修支承挡,移中心架,重校,车平面,修车中心孔锥面,锥度60°。
表8.2 棒料直径与中心孔规格 mm8.3粗车外圆夹、架、顶、校、粗车导向档、螺纹档外圆,留下道工序(半精车、精车)余量2~3mm,样调头,夹、架、顶校,粗车导向档、活塞档、螺纹档(卡槽),留下道加工余量2~3mm,在粗车中拆移中心架,新支承档粗糙度达Ra3.2,不园度﹤0.03mm。
8.4半精车、精车外圆调头粗车好后,应重新调整中心架支承,修中心孔,调整顶紧度,半精车活塞杆导向段,留下道工序(抛磨)余量0.3~0.4mm,具体车至导向段外圆最大尺寸=设计最大直径尺寸-2倍最大镀层厚度+0.4导向段外圆最小尺寸=设计最小直径尺寸-2倍最小镀层厚度+0.3例如活塞杆导向段尺寸φ100-0.043 ,镀层;乳白铬、硬铬层0.08~0.10mm,则半精车导向段尺寸为φ100+0.15导向段近活塞档处有台阶应留越程槽,越程槽底径精车至镀前尺寸(或设计尺寸),砂带、抛盘越轮槽长度30~40mm。
半精车、精车活塞档及其它结构要素(密封槽、台阶、倒角、退刀槽、螺纹、端面中心螺孔等)液压启闭机油缸中活塞螺纹很重要,应按图及标准车制螺纹退刀槽、螺纹、端面中心螺孔等)液压启闭机油缸中活塞杆螺纹很重要,应按图及标准车制螺纹退刀槽、肩距等见表8.4,用螺纹检测车制的螺纹。
表8.4 普通螺纹、梯形螺纹肩距、退刀槽摘录GB3-79 JB/GQ0138-80mm 调头,保护夹,架,顶,校,半精车、精车另一段导向段及其他结构要素达要求。
说明:调头保护夹是指如螺纹应用铜制同螺矩垫块,如光轴配合档应用软钢垫或砂布垫于卡爪与工件外圆之间。
9 加工其他结构要素部位9.1刨(铣)活塞杆头部扁身9.2在镗、铣床上铣杆端“+”字销定槽9.3划钻锁定孔(或配作)9.4划钻杆端面孔(或螺孔)9.2、9.4会增加或影响后道工序的定位夹紧,可按排在最后。
10 镀前磨削10.1镀前磨削尺寸、精度、粗糙度应保证经济、镀层厚度,合适的抛磨量,无论磨床磨削、砂带抛盘磨削,其镀前尺寸确定如下(详见镀前尺寸计算一文)镀前最大尺寸=设计最大尺寸-2倍最大镀层厚度+C镀前最小尺寸=设计最小尺寸-2倍最小镀层厚度+CC为修正系数(1)为镀后抛膜量一般0.01~0.005,(2)公差修正数,上式计算后,公差值较小,难易控制,则C可取-0.01~0.005或缩小镀层厚度公差。
10.2磨削方法A、保护夹,架,顶,校(或夹、顶校)装夹工件B、活塞杆长度,直径适于磨床上加工,应按排外圆磨上磨削C、用砂带磨头或砂盘磨头进行磨削,砂带磨削详见“砂带磨头使用说明书”。
粗磨用60#粒度,恒压磨削,半精磨用100#粒度,半软硬态磨削,精磨用150-180#粒度,砂带抛磨达到尺寸、粗糙度要求。
10.3检验外圆尺寸,粗糙度Ra0.4-0.6,观察是否有其他缺陷。
11 在标有镀层的外圆进行电镀,不得产生镀层缺陷,本产品导向段常用镀层如下:a、乳白铬厚0.04~0.05mm,厚铬层0.04~0.05mmb、乳白铬厚0.02~0.03mm,硬铬厚硬铬层0.05~0.06mmc 硬铬层0.05mm~0.06mm12 镀后磨削12.1 工件保护夹,架,顶,校(或保护夹,顶校)用砂带磨头 150#~180#砂带,在软档对镀层外圆进行抛光达Ra0.4,也可用细粒度抛盘抛光赌层外圆,粗糙度达Ra0.4,在近台肩处用细砂带手工研抛要求12.2检验外圆尺寸精度,粗糙度,镀层厚度等。
13 修补活塞杆在精加工中(镀前精加工,镀后光整加工)流转过程中,由于材质问题,流转过程中碰伤,擦毛,表面裂纹等不影响整体质量的缺陷,必须进行修补。
根据缺陷情况可采用氩弧焊或冷焊机进行补焊,细锉锉至于外圆平整,金刚砂纸打磨光或用刷镀法进行局部修补。
说明:本工艺规范仅供编制工艺参考,具体按设计活塞杆要求合理取舍,合理按排程序。
(注:范文素材和资料部分来自网络,供参考。
只是收取少量整理收集费用,请预览后才下载,期待你的好评与关注)。