DCS系统介绍
DCS介绍

4.操作界面
5.功能演示
谢谢!
和利时DCS系统介绍
1.系统概述
DCS系统采用和利时MACS V系统,采用双 层网络结构,包含两台操作员站(兼服务器),1 个现场控制站。 网络结构:系统网络包含监控网、系统网、 控制网: 监控网(MNET):工业以太网,TCP/IP协议; 系统网(SNET):工业以太网,HSIE协议; 控制网(CNET):Profibus-DP现场总线。 系统冗余:DCS系统实现了控制器冗余,网 络冗余,电源冗余、服务器冗余。
DCS_控制系统简介

DCS是分散控制系统(Distributed Control System)的简称,国内一般习惯称为集散控制系统。
它是一个由过程控制级和过程监控级组成的以通信网络为纽带的多级计算机系统,综合了计算机(Computer)、通讯(Communication)、显示(CRT)和控制(Control)等4C技术,其基本思想是分散控制、DCS是分布式控制系统的英文缩写( Distributed Control System ),在国内自控行业又称之为集散控制系统。
即所谓的分布式控制系统,或在有些资料中称之为集散系统,是相对于集中式控制系统而言的一种新型计算机控制系统,它是在集中式控制系统的基础上发展、演变而来的。
它是一个由过程控制级和过程监控级组成的以通信网络为纽带的多级计算机系统,综合了计算机,通信、显示和控制等4C技术,其基本思想是分散控制、集中操作、分级管理、配置灵活以及组态方便。
在系统功能方面,DCS 和集中式控制系统的区别不大,但在系统功能的实现方法上却完全不同。
工程师站是对DCS 进行离线的配置、组态工作和在线的系统监督、控制、维护的网络节点,其主要功能是提供对DCS4行组态,配置工作的工具软件(即组态软件),并在DCS在线运行时实时地监视DCS网络上各个节点的运行情况,使系统工程师可以通过工程师站及时调整系统配置及一些系统参数的设定,使DCS 随时处在最佳的工作状态之下。
与集中式控制系统不同,所有的DCS都要求有系统组态功能,DCS分散控制系统原理第一讲绪论DCS从1975年问世以来,大约有三次比较大的变革,七十年代操作站的硬件、操作系统、监视软件都是专用的,由各DCS厂家自己开发的,也没有动态流程图,通讯网络基本上都是轮询方式的;八十年代就不一样了,通讯网络较多使用令牌方式;九十年代操作站出现了通用系统,九十年代末通讯网络有部份遵守TCP/IP协议,有的开始采用以太网。
总的来看,变化主要体现在I/O板、操作站和通讯网络。
DCS控制系统介绍
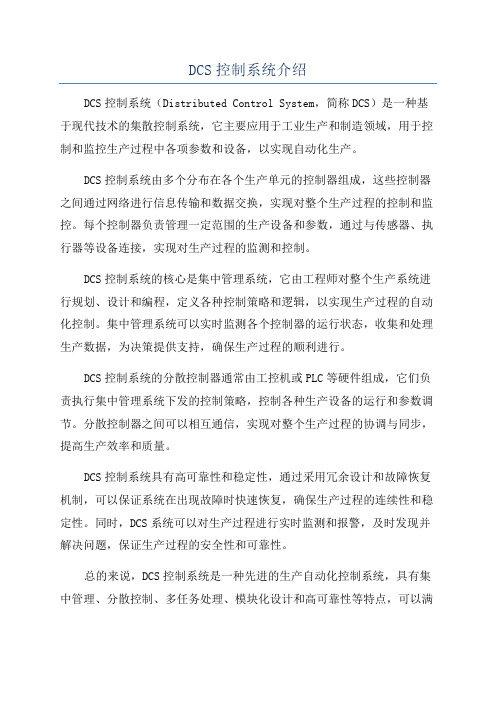
DCS控制系统介绍
DCS控制系统(Distributed Control System,简称DCS)是一种基于现代技术的集散控制系统,它主要应用于工业生产和制造领域,用于控制和监控生产过程中各项参数和设备,以实现自动化生产。
DCS控制系统由多个分布在各个生产单元的控制器组成,这些控制器之间通过网络进行信息传输和数据交换,实现对整个生产过程的控制和监控。
每个控制器负责管理一定范围的生产设备和参数,通过与传感器、执行器等设备连接,实现对生产过程的监测和控制。
DCS控制系统的核心是集中管理系统,它由工程师对整个生产系统进行规划、设计和编程,定义各种控制策略和逻辑,以实现生产过程的自动化控制。
集中管理系统可以实时监测各个控制器的运行状态,收集和处理生产数据,为决策提供支持,确保生产过程的顺利进行。
DCS控制系统的分散控制器通常由工控机或PLC等硬件组成,它们负责执行集中管理系统下发的控制策略,控制各种生产设备的运行和参数调节。
分散控制器之间可以相互通信,实现对整个生产过程的协调与同步,提高生产效率和质量。
DCS控制系统具有高可靠性和稳定性,通过采用冗余设计和故障恢复机制,可以保证系统在出现故障时快速恢复,确保生产过程的连续性和稳定性。
同时,DCS系统可以对生产过程进行实时监测和报警,及时发现并解决问题,保证生产过程的安全性和可靠性。
总的来说,DCS控制系统是一种先进的生产自动化控制系统,具有集中管理、分散控制、多任务处理、模块化设计和高可靠性等特点,可以满
足各种工业生产领域的自动化控制需求,提高生产效率,节约成本,保证生产质量,是工业生产自动化的重要技术手段。
DCS系统介绍范文
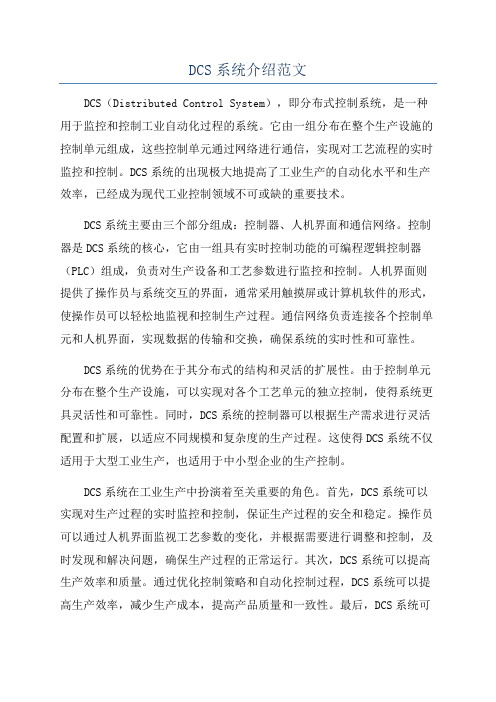
DCS系统介绍范文DCS(Distributed Control System),即分布式控制系统,是一种用于监控和控制工业自动化过程的系统。
它由一组分布在整个生产设施的控制单元组成,这些控制单元通过网络进行通信,实现对工艺流程的实时监控和控制。
DCS系统的出现极大地提高了工业生产的自动化水平和生产效率,已经成为现代工业控制领域不可或缺的重要技术。
DCS系统主要由三个部分组成:控制器、人机界面和通信网络。
控制器是DCS系统的核心,它由一组具有实时控制功能的可编程逻辑控制器(PLC)组成,负责对生产设备和工艺参数进行监控和控制。
人机界面则提供了操作员与系统交互的界面,通常采用触摸屏或计算机软件的形式,使操作员可以轻松地监视和控制生产过程。
通信网络负责连接各个控制单元和人机界面,实现数据的传输和交换,确保系统的实时性和可靠性。
DCS系统的优势在于其分布式的结构和灵活的扩展性。
由于控制单元分布在整个生产设施,可以实现对各个工艺单元的独立控制,使得系统更具灵活性和可靠性。
同时,DCS系统的控制器可以根据生产需求进行灵活配置和扩展,以适应不同规模和复杂度的生产过程。
这使得DCS系统不仅适用于大型工业生产,也适用于中小型企业的生产控制。
DCS系统在工业生产中扮演着至关重要的角色。
首先,DCS系统可以实现对生产过程的实时监控和控制,保证生产过程的安全和稳定。
操作员可以通过人机界面监视工艺参数的变化,并根据需要进行调整和控制,及时发现和解决问题,确保生产过程的正常运行。
其次,DCS系统可以提高生产效率和质量。
通过优化控制策略和自动化控制过程,DCS系统可以提高生产效率,减少生产成本,提高产品质量和一致性。
最后,DCS系统可以实现远程监控和控制,使得操作员可以远程监控和控制生产过程,提高生产的灵活性和效率。
总的来说,DCS系统是现代工业生产中不可或缺的重要技术,其优势在于分布式的结构和灵活的扩展性,可以实现对生产过程的实时监控和控制,提高生产效率和质量,确保生产过程的安全和稳定。
DCS系统

DCS系统目前,在连续型流程生产自动控制(PA)或习惯称之为工业过程控制中,有三大控制系统,即DCS(分散控制系统)、PLC(可编程逻辑控制器)和FCS(现场总线控制系统)。
什么是DCSDCS集散控制系统(Distributed Control System)是20世纪70年代中期发展起来的以微处理器为基础的分散型计算机制系统。
它是控制技术(Control)、计算机技术(Computer)、通信技术(Communication)、图形显示(Display)相结合的产物.该装置是利用计算机技术对生产过程进行集中监视、操作、管理和分散制的一种全新的分布式计算机控制系统。
DCS的特点DCS是计算机技术、控制技术和网络技术高度结合的产物。
DCS通常采用若干个控制器(过程站)对一个生产过程中的众多控制点进行控制,各控制器间通过网络连接并可进行数据交换。
操作采用计算机操作站,通过网络与控制器连接,收集生产数据,传达操作指令。
因此,DCS的主要特点归结为一句话就是:分散控制集中管理。
分级递阶控制系统在垂直和水平方向都是分级的。
最简单的DCS系统至少在垂直方向分两级,即:操作管理级和过程控制级。
在水平方向上各个过程控制级之间是相互协调的分级,它们把数据向上送达操作管理级,同时接收操作管理级的指令,各个水平分级间相互也进行数据交换。
DCS系统越大,其垂直方向和水平方向分级的范围也越广。
分级递阶控制系统的优点是各个分级有各自的分工范围,相互之间有协调,通常,这种协调由上一级来完成。
分散控制分散是DCS的一个重要特点。
分散的含义不单是分散控制,还包含了其他意义。
如:地域分散,功能分散,设备分散,危险分散等。
分散的目的是为了使危险分散,提高设备的可利用率。
自治与协调性DCS的各个组成部分是各自为政的自治系统,各自完成各自的功能,相互之间又有联系,数据信息相互交换,各种条件相互制约,在系统的协调下工作。
分散过程控制装置完成数据的采集、信号的处理、计算以及数据输出等功能。
火电厂DCS系统介绍

DCS系统通过计算机网络技术将各个控制 器连接起来,实现集中管理和监控,方便 了操作和管理。
开放性
DCS系统采用开放式设计和标准化的通信 协议,方便与其他系统和设备的连接和集 成。
实时性
DCS系统具有快速的数据处理能力和实时 响应能力,能够及时处理生产过程中的各 种信号和数据。
DCS系统的应用范围
工程师可以使用工程师站进行系统配置、控制逻辑设 计、图形界面制作等任务,以满足生产工艺的需求。
操作站是DCS系统中用于监控现场设备运行状 况的人机界面。
工程师站是用于组态和维护DCS系统的计算机。
通讯设备
01
通讯设备是DCS系统中用于实现各硬件设备之间信 息传输的设备。
02
它包括通讯卡、交换机、中继器等设备,以确保系 统各部分之间的可靠通讯。
蒸汽。
蒸汽驱动涡轮机
蒸汽进入涡轮机,驱动 涡轮机旋转,从而产生
电力。
蒸汽冷凝和回收
蒸汽在涡轮机中释放完 能量后,被冷凝成水, 经过处理后再次循环利
用。
DCS系统在火电厂的配置方案
控制单元
DCS系统通过控制单元实现对火电厂设备的 远程控制和监测。
数据采集
DCS系统实时采集火电厂设备的运行数据, 如温度、压力、流量等。
智能运维
DCS系统将实现智能运维管理,通过实时监测和数据分析, 自动预测设备维护需求和故障风险,提高运维效率和安全 性。
DCS系统的安全性提升
安全防护
DCS系统将加强安全防护措施,采用更加先进的安全技术和加密算 法,保护系统免受网络攻击和恶意软件的侵害。
容错与冗余设计
DCS系统将采用容错与冗余设计,确保系统在发生故障时能够快速 恢复运行,降低对火电厂生产的影响。
DCS控制系统讲解

DCS控制系统讲解DCS(Distributed Control System)是一种分布式控制系统,用于监控和控制制造过程中的各种设备和参数。
DCS系统在工业自动化领域广泛应用,可以管理许多不同的过程,如化工、电力、水处理、石油和天然气等。
DCS系统由多个分布在不同位置的控制节点组成,每个节点可以分别控制一部分设备或过程。
这些节点通过网络连接,互相通信和交换数据,形成一个大规模的控制系统。
这种分布式架构使得DCS系统具有高可靠性和高灵活性,可以实现实时监控和远程控制。
DCS系统的主要组成部分包括以下几个方面:1.控制器:控制器是DCS系统的核心组件,通常由一台或多台计算机组成。
它们负责处理和执行各种控制策略,并将结果发送给其他设备和节点。
控制器还可以接收来自传感器和执行器的数据,并进行实时监测和反馈控制。
2.人机界面(HMI):HMI是DCS系统与操作人员之间的交互界面。
通过HMI,操作人员可以监视和操纵整个制造过程。
HMI通常包括图形显示、报警和故障处理等功能,使操作人员能够及时发现和解决问题。
3.输入/输出(I/O)模块:I/O模块用于连接DCS系统与实际的物理设备和装置。
它们通过传感器和执行器将过程物理量(如温度、压力、流量等)转换成数字信号,并将控制信号传输到执行器。
I/O模块是DCS系统与外界交流的桥梁,确保了信息的准确性和可靠性。
4. 网络通信:DCS系统中的各个节点通过网络连接,实现数据的传输和共享。
网络通信可以根据实际需求采用不同的协议和技术,如以太网、Profibus、Modbus等。
这些网络使得DCS系统具有分布式控制和集中监控的能力。
5.数据存储和处理:DCS系统需要对大量的数据进行存储和处理。
这些数据包括控制参数、过程状态、历史记录等。
数据存储和处理功能可以在DCS系统中实现,也可以通过连接外部数据库和服务器来实现。
DCS系统的工作原理基于控制算法和策略。
控制算法通常是根据过程的特点和需求进行设计和优化的。
DCS系统的基本原理和功能介绍
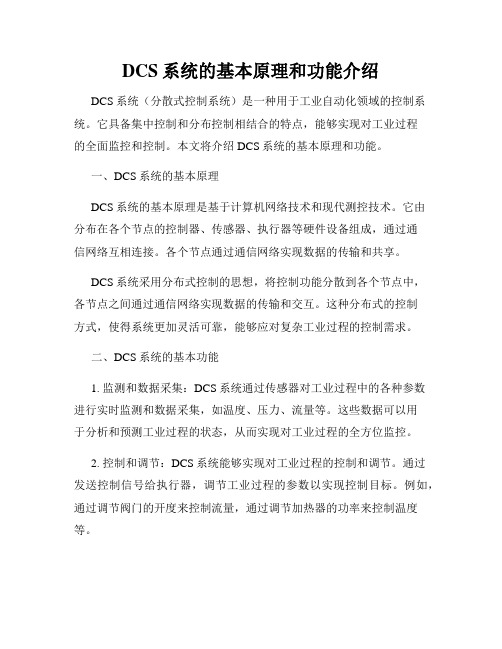
DCS系统的基本原理和功能介绍DCS系统(分散式控制系统)是一种用于工业自动化领域的控制系统。
它具备集中控制和分布控制相结合的特点,能够实现对工业过程的全面监控和控制。
本文将介绍DCS系统的基本原理和功能。
一、DCS系统的基本原理DCS系统的基本原理是基于计算机网络技术和现代测控技术。
它由分布在各个节点的控制器、传感器、执行器等硬件设备组成,通过通信网络互相连接。
各个节点通过通信网络实现数据的传输和共享。
DCS系统采用分布式控制的思想,将控制功能分散到各个节点中,各节点之间通过通信网络实现数据的传输和交互。
这种分布式的控制方式,使得系统更加灵活可靠,能够应对复杂工业过程的控制需求。
二、DCS系统的基本功能1. 监测和数据采集:DCS系统通过传感器对工业过程中的各种参数进行实时监测和数据采集,如温度、压力、流量等。
这些数据可以用于分析和预测工业过程的状态,从而实现对工业过程的全方位监控。
2. 控制和调节:DCS系统能够实现对工业过程的控制和调节。
通过发送控制信号给执行器,调节工业过程的参数以实现控制目标。
例如,通过调节阀门的开度来控制流量,通过调节加热器的功率来控制温度等。
3. 报警和安全保护:DCS系统能够实现对工业过程的报警和安全保护。
当工业过程出现异常情况时,系统可以及时发出警报,通知操作人员进行处理。
同时,系统还能够对工业过程进行安全保护,如防止过高压力、过高温度等因素对系统造成损害。
4. 数据存储和分析:DCS系统能够对采集到的数据进行存储和分析。
通过对历史数据的分析和统计,可以了解工业过程的运行情况,发现问题和优化工艺。
同时还可以用于生成运营报表和质量报告等。
5. 远程操作和监控:DCS系统支持远程操作和监控功能。
操作人员可以通过计算机或移动设备远程监控和操作系统,无需亲临现场。
这种远程操作和监控功能,使得操作更加方便高效,降低了维护成本。
6. 系统管理和配置:DCS系统还包括系统管理和配置的功能。
DCS控制系统介绍三篇

DCS控制系统介绍三篇篇一:DCS控制系统介绍集散控制系统的英文原名为:DistributedControlSystem,简称DCS,通常也称为集散控制系统。
集散控制系统的控制功能,主要由计算机技(computer)、控制技术(Control)、显示技术(CRT)和通信技术(communicate)来完成,一般也称为4C技术,4C技术是DCS系统的四大支柱。
DCS中通信技术更为重要,操作员站的操作、工程师站系统的组态以及现场设备信息的交换都依靠通信技术来完成。
第一节集散控制系统的构成一集散控制系统的构成方式如图是集散控制系统典型结构。
功能分层是集散控制系统的体系特征反映了集散控制系统的“分散控制、集中管理”的特点。
从功能上看可以分为:四个层次,分别是现场控制级的功能;过程装置控制级;车间操作管理级;全厂优化和调度管理级。
从结构看分为:三大块,分别是分散过程控制装置;集中操作和管理系统;通信系统。
图4.1DCS结构(一)集散控制系统的各层功能1、现场控制级的功能(1)微处理器进入现场变送器、传感器和执行器;现场总线的应用。
部分或完全完成过程控制级的功能;(2)采集过程数据,对数据进行数据转换;(3)输出过程操作命令;(4)进行直接数字控制;(5)完成与过程装置控制级的数据通信;(6)对现场控制级的设备进行检测和诊断。
2、过程装置控制级的功能过程装置控制级的结构采用过程控制设备+I/O卡件,其功能是:(1)采集过程数据,进行数据转换和处理;(2)数据的监视和存储;(3)实施连续、批量或顺序控制的运算和输出控制作用;(4)数据和设备的自诊断;(5)数据通信。
3、车间操作管理级的功能车间操作管理级设备有中央控制室操作站、打印机、拷贝机、工程师站、计算站,能完成功能是:(1)数据显示与记录(2)过程操作(含组态操作、维护操作)(3)数据存储和压缩归档(4)报警、事件的诊断和处理(5)系统组态、维护和优化处理(6)数据通信;(7)报表打印和画面硬拷贝。
DCS系统的介绍
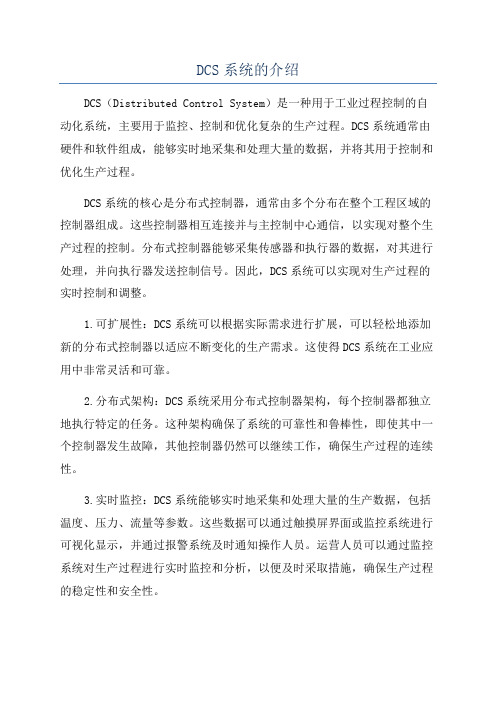
DCS系统的介绍DCS(Distributed Control System)是一种用于工业过程控制的自动化系统,主要用于监控、控制和优化复杂的生产过程。
DCS系统通常由硬件和软件组成,能够实时地采集和处理大量的数据,并将其用于控制和优化生产过程。
DCS系统的核心是分布式控制器,通常由多个分布在整个工程区域的控制器组成。
这些控制器相互连接并与主控制中心通信,以实现对整个生产过程的控制。
分布式控制器能够采集传感器和执行器的数据,对其进行处理,并向执行器发送控制信号。
因此,DCS系统可以实现对生产过程的实时控制和调整。
1.可扩展性:DCS系统可以根据实际需求进行扩展,可以轻松地添加新的分布式控制器以适应不断变化的生产需求。
这使得DCS系统在工业应用中非常灵活和可靠。
2.分布式架构:DCS系统采用分布式控制器架构,每个控制器都独立地执行特定的任务。
这种架构确保了系统的可靠性和鲁棒性,即使其中一个控制器发生故障,其他控制器仍然可以继续工作,确保生产过程的连续性。
3.实时监控:DCS系统能够实时地采集和处理大量的生产数据,包括温度、压力、流量等参数。
这些数据可以通过触摸屏界面或监控系统进行可视化显示,并通过报警系统及时通知操作人员。
运营人员可以通过监控系统对生产过程进行实时监控和分析,以便及时采取措施,确保生产过程的稳定性和安全性。
4.网络通信:DCS系统采用高速稳定的网络通信协议,可以实现控制器之间的快速数据传输和通信。
这使得控制器可以进行实时的数据交换和协作,以实现协调控制和优化生产过程。
5.灵活的编程语言:DCS系统通常提供多种编程语言和开发工具,使控制系统的编程和调整变得更加灵活和方便。
这些编程语言包括基于图形的编程环境、函数块图、状态图等,可根据用户的需求和经验进行定制。
6.故障诊断和维护:DCS系统通常具备自动故障诊断和维护功能。
系统可以自动监测设备状态和性能,如果发现故障,可以发送警报并定位问题所在。
DCS控制系统介绍
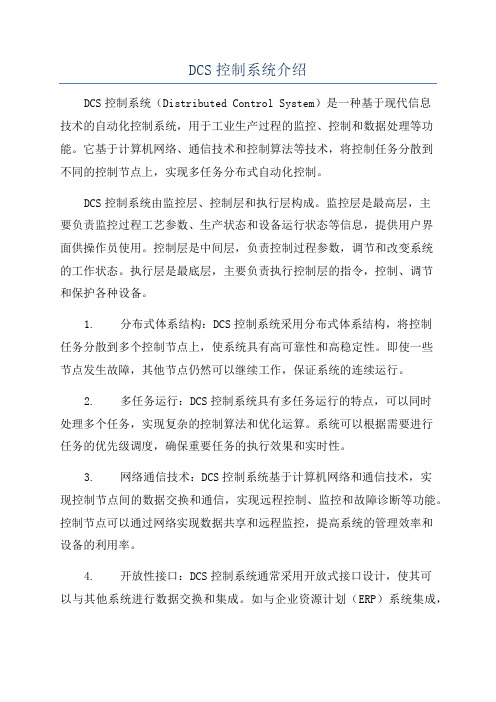
DCS控制系统介绍DCS控制系统(Distributed Control System)是一种基于现代信息技术的自动化控制系统,用于工业生产过程的监控、控制和数据处理等功能。
它基于计算机网络、通信技术和控制算法等技术,将控制任务分散到不同的控制节点上,实现多任务分布式自动化控制。
DCS控制系统由监控层、控制层和执行层构成。
监控层是最高层,主要负责监控过程工艺参数、生产状态和设备运行状态等信息,提供用户界面供操作员使用。
控制层是中间层,负责控制过程参数,调节和改变系统的工作状态。
执行层是最底层,主要负责执行控制层的指令,控制、调节和保护各种设备。
1. 分布式体系结构:DCS控制系统采用分布式体系结构,将控制任务分散到多个控制节点上,使系统具有高可靠性和高稳定性。
即使一些节点发生故障,其他节点仍然可以继续工作,保证系统的连续运行。
2. 多任务运行:DCS控制系统具有多任务运行的特点,可以同时处理多个任务,实现复杂的控制算法和优化运算。
系统可以根据需要进行任务的优先级调度,确保重要任务的执行效果和实时性。
3. 网络通信技术:DCS控制系统基于计算机网络和通信技术,实现控制节点间的数据交换和通信,实现远程控制、监控和故障诊断等功能。
控制节点可以通过网络实现数据共享和远程监控,提高系统的管理效率和设备的利用率。
4. 开放性接口:DCS控制系统通常采用开放式接口设计,使其可以与其他系统进行数据交换和集成。
如与企业资源计划(ERP)系统集成,实现生产计划和物料管理的统一、同时,也可以与其他自动化系统集成,如SCADA系统、MES系统等,实现全面的生产过程控制和管理。
5. 可扩展性:DCS控制系统具有较好的可扩展性,可以根据生产工艺的变化和需求的变化进行扩展和改造。
可以增加新的控制节点,增加新的功能模块,实现对系统的功能和性能的扩展,提高系统的灵活性和适应性。
DCS控制系统在工业生产中有着广泛的应用,包括化工、石油、电力、冶金、食品、制药等行业。
DCS系统的介绍

DCS系统的介绍DCS(分布式控制系统)是一种集成了过程控制、数据采集、通信、运算和显示等功能的自动化控制系统。
它主要应用于诸如发电厂、化工厂、石油化工、冶金、制药、水处理、水电站等领域。
DCS系统通过集中控制器、工作站、输入/输出子系统、通信网络等构成,实现对整个系统的实时监控和自动控制。
1.集中控制器(CPU):集中控制器是DCS系统的核心,负责实时监控和控制系统的各种参数。
它可以处理来自传感器和执行器的输入和输出信号,执行控制算法,并向操作员提供实时数据。
2.工作站:DCS系统通常包括一台或多台工作站,用于操作员监控和操纵系统。
工作站提供了人机界面,使操作员能够查看关键数据、趋势图、报警信息等。
通过工作站,操作员可以对系统进行调整和优化,实现最佳控制效果。
3.输入/输出子系统:输入/输出子系统负责将传感器和执行器与DCS系统进行连接。
它包括模拟输入、模拟输出、数字输入、数字输出等接口模块,用于将各种信号转换为数字信号,以便于集中控制器的处理。
4.通信网络:DCS系统中的各个组件通过通信网络进行连接。
通信网络是实现数据传输和交换的重要一环,它可以是以太网、现场总线、红外线通信等。
通信网络高效稳定的运行是确保DCS系统正常运行的关键。
1.高度集成:DCS系统集成了过程控制、数据采集、通信、运算和显示等功能,可以实现对整个系统的一体化管理,提高工作效率和生产效益。
2.实时监控:DCS系统可以提供实时的数据和趋势图,使操作员对系统状态进行实时监控和分析。
这样,操作员可以及时发现和处理潜在问题,保证生产过程的稳定性和安全性。
3.灵活可扩展:DCS系统可以根据实际需要进行灵活扩展和升级。
用户可以根据生产线的变化进行系统配置和改造,以适应新的生产要求。
4.可靠性高:DCS系统采用了分布式架构,其中集中控制器、工作站和输入/输出子系统等可以实现冗余备份,提高了系统的可靠性和稳定性。
5.易于操作:DCS系统提供了友好的用户界面和操作方法,使操作员能够轻松地操作和管理系统。
(完整版)DCS系统介绍
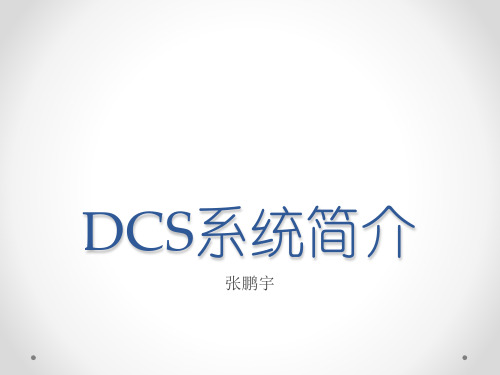
5.2 监控画面组态
5.3 工作站组态
• 用于监视控制显示画面及部分组态功能。
5.4 通讯组态
• 用于组态工作站,打印机及第三方控制器。
六、DCS的基础知识
• I/O信号 • 系统冗余 • DCS系统的特点
6.1 IO信号
• I/O:控制系统需要建立信号的输入和输出通道,这就是 I/O。DCS中的I/O一般是模块化的,一个I/O模块上有一 个或多个I/O通道,用来连接传感器和执行器。
2.2 1940~1970年
• 第三次科技革命开始后,随着计算机技术的发展,人们开 始尝试将计算机用于过程控制。但当时采用的办法是用一 台计算机控制几十甚至上百个回路,这样做的危险性很高, 如果计算机出现故障,会导致很严重的后果,这造成了危 险集中。
2.3 1970~1990年
• 直到上世纪70年代,随着计算机技术的日渐成熟,人们才 开始将危险分散。就是原来靠一台大计算机完成的任务, 现在用几十台微处理器来完成,从而大大降低了危险系数。 至此DCS就诞生了。
• 3.2管理级别分类:现场控制级、过程控制级、过程管理 级、经营管理级
• 3.3网络结构分类:一级网络、二级网络、三级网络
3.1硬件组成
3.2.1现场控制级
• 又称数据采集装置,主要是将过程非控变量进行数据采集 和预处理,而且对实时数据进一步加工处理,供操作站显 示和打印,从而实现开环监视,并将采集到的数据传输到 监控计算机。输出装置在有上位机的情况下,能以开关量 或者模拟量信号的方式,向终端元件输出计算机控制命令。 这一个级别直接面对现场,跟现场过程相连。比如阀门、 电机、各类传感器、变送器、执行机构等等。
3.2.2过程控制级
DCS系统介绍
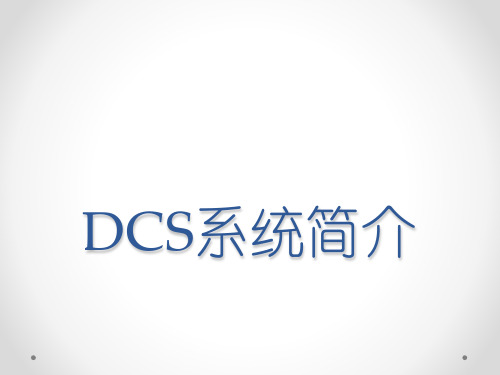
2.1 1930~1940年
• 上世纪三四十年代,工业自动化装置采用的是分散性控制 系统。也就是所有设备都是独立运行,不联网控制。操作 员根据生产需求进行计算后,将独立设备的特性调节到适 合的程度,然后就开始工作。之后采用了气动、电动模拟 仪表组成过程控制系统,实现了一定程度上的集中监视、 操作和分散控制。
4.1.1 早期的DCS机柜
4.1.2系统柜
控制防火墙 冗余数字与模拟 I/O 电源系统 C300 控制器
现场总线接口模件
4.1.3辅助柜
4.1.4 辅操台
4.2 操作站
4.3 网络设备
4.4 可编程控制器PLC
• 可编程逻辑控制器是种专门为在工业环境下应用而设计的 数字运算操作电子系统。它采用一种可编程的存储器,在 其内部存储执行逻辑运算、顺序控制、定时、计数和算术 运算等操作的指令,通过数字式或模拟式的输入输出来控 制各种类型的机械设备或生产过程。
3.2.4经营管理级
• 又称上位机,功能强、速度快、容量大。通过专门的通信 接口与高速数据通路相连,综合监视系统各单元,管理全 系统的所有信息。这是全厂自动化系统的最高一层。只有 大规模的集散控制系统才具备这一级。
3.3网络结构
四、DCS系统的硬件结构
• 现场控制单元:系统柜、辅助柜、辅操台…… • 操作站:服务器、工程师站、操作站……
• 3.2管理级别分类:现场控制级、过程控制级、过程管理 级、经营管理级
• 3.3网络结构分类:一级网络、二级网络、三级网络
3.1硬件组成
3.2.1现场控制级
• 又称数据采集装置,主要是将过程非控变量进行数据采集 和预处理,而且对实时数据进一步加工处理,供操作站显 示和打印,从而实现开环监视,并将采集到的数据传输到 监控计算机。输出装置在有上位机的情况下,能以开关量 或者模拟量信号的方式,向终端元件输出计算机控制命令。 这一个级别直接面对现场,跟现场过程相连。比如阀门、 电机、各类传感器、变送器、执行机构等等。
DCS控制系统介绍
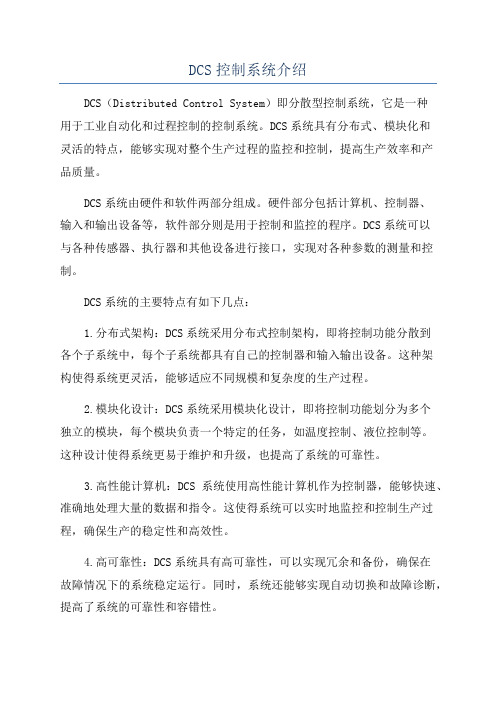
DCS控制系统介绍DCS(Distributed Control System)即分散型控制系统,它是一种用于工业自动化和过程控制的控制系统。
DCS系统具有分布式、模块化和灵活的特点,能够实现对整个生产过程的监控和控制,提高生产效率和产品质量。
DCS系统由硬件和软件两部分组成。
硬件部分包括计算机、控制器、输入和输出设备等,软件部分则是用于控制和监控的程序。
DCS系统可以与各种传感器、执行器和其他设备进行接口,实现对各种参数的测量和控制。
DCS系统的主要特点有如下几点:1.分布式架构:DCS系统采用分布式控制架构,即将控制功能分散到各个子系统中,每个子系统都具有自己的控制器和输入输出设备。
这种架构使得系统更灵活,能够适应不同规模和复杂度的生产过程。
2.模块化设计:DCS系统采用模块化设计,即将控制功能划分为多个独立的模块,每个模块负责一个特定的任务,如温度控制、液位控制等。
这种设计使得系统更易于维护和升级,也提高了系统的可靠性。
3.高性能计算机:DCS系统使用高性能计算机作为控制器,能够快速、准确地处理大量的数据和指令。
这使得系统可以实时地监控和控制生产过程,确保生产的稳定性和高效性。
4.高可靠性:DCS系统具有高可靠性,可以实现冗余和备份,确保在故障情况下的系统稳定运行。
同时,系统还能够实现自动切换和故障诊断,提高了系统的可靠性和容错性。
5. 开放性:DCS系统是一个开放系统,可以与其他系统进行连接和通讯,如MES(Manufacturing Execution System)、ERP(Enterprise Resource Planning)等。
这种开放性使得系统更加灵活,可以实现工厂级别的集成和管理。
DCS系统主要应用于工业生产过程控制,如化工、电力、石油、制药等行业。
它可以实现对生产参数的实时监测和调节,确保产品的质量和安全,提高工艺的稳定性和效率。
总之,DCS控制系统是一种分散型、模块化和灵活的控制系统,能够实现对工业生产过程的监控和控制,提高生产效率和产品质量。
DCS系统介绍

DCS 发展历史
第二阶段:1980—1985.,在这个时期集散控 制系统的技术特点表现为: 1)微处理器的位数提高,CRT显示器的分辨 率提高 2)强化的模块化系统 3)强化了系统信息管理,加强通信功能
DCS 发展历史
第三阶段,1985年以后,集散系统进入第三 代,其技术特点表现为: 1)采用开放系统管理 2)操作站采用32位微处理器 3)采用实时多用户多任务的操作系统
DCS 发展历史
第一阶段:1975-1980年,在这个时期集散控 制系统的技术特点表现为: 1)采用微处理器为基础的控制单元,实现 分散控制,有各种各样的算法,通过组态独立 完成回路控制,具有自诊断功能 2)采用带CRT显示器的操作站与过程单元分 离,实现集中监视,集中操作 3)采用较先进的冗余通信系统
DeltaV I/O Card Types
Outputs
- AO, 8 Channel, 4 to 20 mA, HART – AO, 8 Channel, 4 to 20 mA – I.S. AO, 8 Channel, 4 to 20 mA – DO, 8 Channel, 120/230 VAC, Isolated – DO, 8 Channel, 120/230 VAC, High Side – DO, 8 Channel, 24 VDC, Isolated – DO, 8 Channel, 24 VDC, High Side – High Density DO, 32 Channel, 24 VDC, High Side – I.S. DO, 4 Channel, 12 VDC I.S. Power
DCS 特点
1) 高可靠性。由于DCS将系统控制功能分散在各台计 算机上实现,系统结构采用容错设计,因此某一台计算 机出现的故障不会导致系统其他功能的丧失。此外,由 于系统中各台计算机所承担的任务比较单一,可以针对 需要实现的功能采用具有特定结构和软件的专用计算机, 从而使系统中每台计算机的可靠性也得到提高。 2) 开放性。DCS采用开放式,标准化、模块化和系列 化设计,系统中各台计算机采用局域网方式通信,实现 信息传输,当需要改变或扩充系统功能时,可将新增计 算机方便地连入系统通信网络或从网络中卸下,几乎不 影响系统其他计算机的工作。
DCS系统
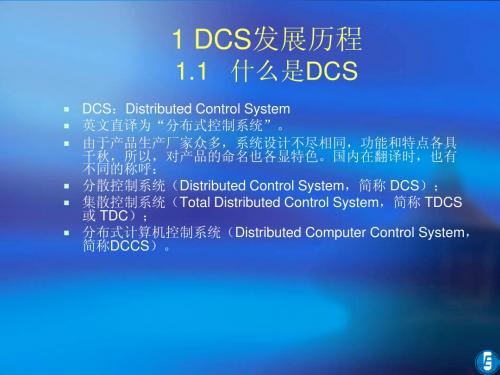
A/D -
D/A
传感器
被控对象
执行机构
模糊控制
对离散过程的控制
程序控制或逻辑控制
以状态控制为主, 非连续对象、非连续过程
按照一定的方式改变被控对象的状态或位置。
有很明显的起点和终点。 要素: 动作时间、动作顺序、逻辑关系
组合仪表、电动单元组合仪表、分布式控制 系统DCS 分为仪表控制系统和计算机控制系统
1.3.2 仪表控制系统的基本概念
指模拟式仪表组成的控制系统
最主要的功能是进行回路控制,对那种最小
过程单元进行的闭环控制或调节。
仪表控制系统的基本概念
输入两个:设定值和测量值 输出一个:对被控过程的控制量 闭环、反馈。
基本功能:
根据控制算法处理测量值和设定值的偏差,并控制
过程减少此偏差。 实例: 水位控制系统
液位控制
飞锤调速器
1.3.3 早期的仪表控制系统 – 基地式仪表
指控制系统(即仪表)与被控对象在机械结
构上是结合在一起的,而且仪表的各个部分, 包括检测、计算、执行及简单的人机界面都 做成了一个整体,就地安装在被控对象之上。 单回路控制
直流电信号(电流或电压)传递现场信号的值。 信号规范: 0-10mA:DDZII 4-20mA:DDZIII 真正的控制系统是从单元式组合仪表出现后才逐步 形成。不仅单回路,还可以串级、复合、几个回路 互动。
电动单元组合仪表(60~70年代)
缺点:构成复杂控制系统困难,故障率高 无法进行数字通信
组装式电子综合控制仪表 (70年代末)
工控DCS系统介绍

工控DCS系统介绍工控DCS(Distributed Control System)系统是一种用于工业过程控制的自动化系统。
它采用分布式控制结构,将整个控制系统分为若干个分散的控制单元,每个控制单元负责一部分的控制任务,并通过通信网络进行数据的传输和共享。
DCS系统广泛应用于化工、电力、石油、制药、水处理等工业领域。
工控DCS系统由硬件和软件两部分组成。
硬件包括控制器、输入输出模块、通信模块、操作面板等。
控制器是DCS系统的核心部件,负责数据处理和控制计算。
输入输出模块用于连接传感器和执行器,实现与外部设备的数据交换。
通信模块用于实现不同控制单元之间的数据传输和通信。
操作面板提供人机界面,方便操作员对系统进行监控和控制。
DCS系统的软件部分包括操作系统、数据库、控制算法等。
操作系统为系统的运行提供支持。
数据库用于存储和管理系统中的数据。
控制算法是DCS系统的核心,通过对输入信号的处理和计算,生成控制指令,实现对工业过程的控制。
工控DCS系统的特点有以下几个方面。
首先,系统具有高度的可靠性和稳定性。
由于分布式控制结构和冗余设计,即使一些控制单元发生故障,其他控制单元仍可继续工作,确保系统的连续运行。
其次,系统具有灵活性和可扩展性。
由于采用分布式控制结构,系统的控制单元可以随着工艺的变化进行调整和扩展,以满足不同的生产需求。
再次,系统具有高效的数据传输和共享能力。
通过通信网络,各个控制单元可以快速地交换数据,实现实时监控和远程操作。
此外,系统还具有友好的人机界面和强大的故障诊断功能,方便操作员对系统进行监控和维护。
工控DCS系统在工业生产中发挥着重要的作用。
首先,它可以提高生产的自动化水平,降低劳动强度,提高生产效率。
其次,它可以减少生产过程中的人为误操作,提高产品质量和安全性。
同时,DCS系统还可以实现对工业过程的精确控制和监测,使生产过程更加稳定可靠。
另外,DCS 系统还可以远程监控和操作,为企业提供更灵活的管理方式。
- 1、下载文档前请自行甄别文档内容的完整性,平台不提供额外的编辑、内容补充、找答案等附加服务。
- 2、"仅部分预览"的文档,不可在线预览部分如存在完整性等问题,可反馈申请退款(可完整预览的文档不适用该条件!)。
- 3、如文档侵犯您的权益,请联系客服反馈,我们会尽快为您处理(人工客服工作时间:9:00-18:30)。
驱动
V/I转换
ST9351双路光隔离DIO模块具有智能型、双路光隔离、数 字量混合输入输出特点,能够输入24VDC电平信号或集电极开 路输出驱动信号。通过软件设置,可以实现开关量的输入检测 和开关量输出控制。
ST9361单路光隔离PI计频模块具有智能型、光隔离、支持多 种脉冲量信号(包括:方波、正弦波、锯齿波)输入特点。 频率范围:0~30kHz 电平范围:0~5V, 逻辑0; 8~30V,逻辑1。
Distributed Control System 分散控制系统/分布式控制系统 集散控制系统
DCS由过程控制级和过程监控级组成,综合计算机,通信、显示和
控制等4C技术,其基本思想是分散控制、集中操作、分级管理、配置 灵活以及组态方便。
PLC基础知识
Programmable Logic Controller
•独立的24V电源;
•模板自身过流保护功能; •DO通道输出现场干接点容许通过电流5A;
ST9271万能调理模板采用通用输入、
智能调理、灵巧总线技术;支持配置16块
智能I/O模块,所有模块全隔离、全隔离配 电,实现通道与通道之间、通道与模板之
间的全隔离,支持冗余控制网Cnet。
采样信号类型: 电压:0~20mV、0~100mV、0~5V、1~5V; 电流:0~10mA、4~20mA; 热电阻:Pt100、Cu50; 热电偶:B、E、J、K、S、T;
• 军工级CPU,8M存储区; • 双冗余的通讯驱动; • 实时数据库掉电不丢失;
• 控制模板间自动进行实时数据交换和模板状态诊断;
• 丰富的面板指示灯; • 最多可连接32块I/O模板; • 采用E2PROM存储器; • 带电热插拔
32路集成型开关量输入输出调理模板ST9262
•32路DIO通道自由配置; •支持冗余控制网CNet; •支持带电插拔; •现场信号与系统间采用光电隔离,隔离电压1500V; •通道与通道之间隔离;
•浙江中自庆安新能源技术 有限公司 •浙江中自机电控制技术有 限公司
客户服务部
生产中心
销售
生产、装配 培训 发送现场 28993283
售后服务部
技术支持
客户服务部
设计工程部
工程设计
调试开车
调试工程部
维修、疑问 28993266
自动化产品的研发生产
Chitic工业控制应用软件
ChiticCTS700
……
32块I/O模板
主要特点如下: • 多主工作方式:通信方式灵活,无需地址等节点信息; • 采用非破坏性总线仲裁技术: 网络节点信息分成不同的优先级,高优先级的数据最多可在134us 内得到传输; •CAN现场总线: 节点在错误严重情况下具有自动关闭输出功能,使总线上其他节点
的操作不受影响。
冗余 MNet 非冗余
其功能如下:
• 可从运行有数据服务软件的操作站(或专用服务器)上获取系统过程
参数和系统运行信息,同时向下传送上层管理计算机的调度指令和生产
指导信息;
• • 企业内多组装置或生产过程的管理数据通讯; 大型工业过程各子系统间的协调控制与调度管理;
•
工厂级的综合管理、调度、统计和决策等;
系统网SNet是连接SunyTDCS9200工程师站、操作员站、现场控制 站和通讯组件的实时工业网络。它是传送过程控制实时信息的通道,通 过挂接在其上的数据通讯组件可以与其他厂商的控制系统或智能仪表相 连,也可通过运行有数据服务软件的操作站或专用服务器把过程控制信 息向上层的信息管理网传送。 •双冗余网络 •最大节点96点 •通讯速率10M/100M •传输介质:五类非屏蔽双绞线/光纤
向现场24V二线制、三线制变送器隔离配电的功能。每个模块支持一个
模拟量输入点。
电压:0~20mV、0~100mV、0~5V、
1~5V; 电流:0~10mA、4~20mA;
热电阻:Pt100、Cu50;
热电偶:B、E、J、K、S、T;
SNet
CNet
SmartBus
校准信号
ST9321单路全隔离电流AO模块具有智能型、全隔离、输出保护 特点,能够输出0-10mADC、4-20mADC或0-20mADC信号。
机笼
控制模板 远程光纤通讯模板 16-32路万能调理模板
32路集成型开关量输入输出混合模板
用于安装控制模板、I/O模
板,并为各模板提供工作电流、 通讯接口和现场I/O信号的转接 功能。
控制模板负责协
调处理控制站内部所
实时数据 存储器
SNet驱动
有功能模板的数据交 流和控制运算。
CPU
CNet驱动
现同时32路DI信号输入,进行事件 发生时间的顺序记录。
SOE事件顺序记录模板
ST9233将记录的各输入的实时变 化放入模板缓冲区,并发送至控制
模板ST9161保存记录,各先后事
件相互独立,互不干扰。分辨率为 1ms(毫秒),每个控制站事件记
录容量为10240个。
ST9142:本地模板/主通讯模板 ST9143:远程模板/从通讯模板
操作站
工程师站
GPS
大屏幕显示
控制站
通讯组件
第三方设备
控制网络CNet是控制站内部使用的 冗余实时网络,实现控制站内部的各个智 能I/O模板和控制模板之间的互联和信息 传递。控制网采用双绞线或光纤为通讯介 质,最大通讯速率1Mbps,控制网络超过 34米,使用光纤进行连接。 其作用如下: I/O模板向控制站模板传递实时采集数 据及自诊断信息; I/O模板主控制器向各I/O模块发送配置 信息、系统运算结果及操作指令
安全可靠、实用高效、放心满意的服务。
DCS集散控制系统、FCS现场 总线控制系统、工业控制应 用软件平台、智能仪表等产 品的研发、生产和销售,提 供满足石油石化、精细化工、 生物制药、环保水处理、热 电、建材、造纸等行业自动 控制需求的自动化解决方案。
工业装备自动化领域产品研 发、市场营销及工程服务业 务。主要产品:纺机设备控 制器、开关磁阻电机及驱动 控制器、数据管理站、智能 仪器仪表设备等,应用于纺 织机械、数控机床、包装机 械、工程机械、金属热处理 等行业。
•通用模拟量输入,不需硬件调整;
•模板基于SmartBus灵巧总线技术;
•信号调理模块实现现场信号类型切换、程控放大、非线性补偿、温度补 偿、量程转换、故障诊断等功能;模块标识、通道标定及配置数据支持冗余控制网CNet;
32路SOE事件顺序记录模板实
致力于太阳能发电、风力发 电领域的信息化研究,提供 光伏发电监控系统、太阳能 电池生产控制系统、风力发
电控制系统及风电机组在线
状态监测系统等
依托集团强大电气后盾, 提供电厂自动化控制系统、 光伏电站监控系统、智能 电器监控软件等电力自动 化解决方案,已广泛应用 于太阳能电站、风力发电、 智能电网等领域。
• 冗余控制模板,无扰动切换; • 系统电源冗余配置; • 运算与处理分散至各I/O模块; • 现场总线取代并行总线; • 模块采用智能调理与信号隔离配电技术;
• 软件及硬件均可监视模板状态;
• 支持带电插拔;
控制站硬件包括:公共部件、功能模板、调理模块、控制站附件。
散热组件 系统电源组件
转接端子板/ 转接端子盒
可编程逻辑控制系统 PLC是由摸仿原继电器控制原理发展起来的,二十世
纪七十年代的PLC只有开关量逻辑控制,首先应用的是汽车 制造行业。它以存储执行逻辑运算、顺序控制、定时、计
数和运算等操作的指令;并通过数字输入和输出操作,来
控制各类机械或生产过程。
• 高可靠性:冗余设计、独立处理器、隔离技术、电磁兼容 • 系统开放:开放接口
正泰建筑 正泰太阳能
浙江正泰中自控制工程有限公司是工业自动化领域的领先供应商。公 司致力于过程自动化、装备自动化、电力自动化和新能源信息化等前沿技 术的研究与应用开发。公司自成立以来,已先后为国内外石油石化、精细 化工、生物制药、环保水处理、建材、造纸、冶金、电力、纺织、新能源
等行业近三千家用户提供了各种高品质的自动化产品与服务。
正泰中自拥有一流的研发、生产、工程、服务、管理人才队伍,通过 不断的技术积累,引进国际最新技术,进行产学研创新合作,正泰中自积
聚了产品研发、工程设计、服务实施等方面深度服务于行业用户的能力,
立志成为“控制工程的经典专家”。公司在创造经济效益的同时,努力为 广大客户的生产效率提升、节能降耗、环境保护及传统产业转型升级提供
TDCS9200系统介绍
TDCS9200 System Introduction
培训讲师:杨文瑶
1998年
浙江浙大中自集成控制股份有限公司成立
2005年
浙江正泰中自控制工程有限公司成立
2008年
产业重组、自动化产业均转移到浙江正泰 中自控制工程有限公司
正泰仪器仪表
正泰中自 正泰电器 正泰汽车
正泰电气
太原绿控自动化工程 有限公司
哈尔滨绿控自动化控 制技术开发有限公司
北京办事处 新疆办事处 济南绿控自动化工程 有限公司 上海绿控自动化技术 有限公司 安徽安尼石油化工自 动化工程有限公司 浙江正泰中自控制工 程有限公司 四川中自万控自动化 系统工程有限公司 深圳市绿控自动化系 统工程有限公司
西安绿控自动化设备 有限公司
• 功能强大:庞大算法块群、构件结构
• 集中监视 • 分散控制
• 扩展性强
• 软件灵活:符合Windows界面风格 • 维护简便:规范化、自诊断、通用输入
工程师站 操作站
网络
控制站
管理网络MNet是TDCS9200集散控制系统的最高一级网络,采用以 太网,实现工厂级的信息传递和管理,是实现全厂综合管理的信息通道。 MNet 网络使用以太网,符合IEEE802.3标准,其通讯速率为 10M/100M/1000Mbps;传输介质为5类非屏蔽双绞线或光纤。