铸件表面质量验收规范
铸件表面质量提升验收技术条件

铸件表面质量提升验收技术条件1 范围本文件规定了铸件分类、目测铸件技术要求、检验规则.本标准适用于中国一拖集团有限公司内/外供方采用砂型铸造,金属型铸造方法获得的黑色、有色合金铸件产品。
2 规范性引用文件下列文件对于本文件的应用是必不可少的.凡是注日期的引用文件,仅所注日期的版本适用于本文件。
凡是不注日期的引用文件,其最新版本(包括所有的修改单)适用于本文件.GB/T 6060。
1—1997 表面粗糙度比较样块铸造表面GB/T 15056-1994 铸造表面粗糙度评定方法Q/YT 014.2—2009 图样通用技术要求Q/YT 022。
4—2011 砂型机器造型铸件尺寸公差Q/YT 022。
10—2011 铸铁件机械加工余量Q/YT 303。
1-2011 球墨铸铁件验收技术条件Q/YT 303.2—2011 灰铸铁件验收技术条件Q/YT 303.3—2011 铸造碳钢件验收技术条件Q/YT 303.5-2011 铝合金铸件验收技术条件Q/YT 303。
6-2011 高锰钢履带板验收技术条件Q/YT 303。
7-2011 铜合金铸件验收技术条件Q/YT 303.9-2011 硅锰钢履带板验收技术条件3 铸件分类铸件根据其所处安装位置、工作条件及表面是否加工分三类,其定义和检验项目见表1。
表1 铸件分类4 目测铸件技术要求4.1 一般要求4.1.1 砂型铸造全部外露件和部分外露件表面粗糙度要求Ra25~Ra50。
金属铸造和有色件表面粗糙度要求Ra25,待加工表面允许降低一级。
4.1.2 铸件表面不得有影响零件强度、密封性能及严重影响外观的缺陷。
4.1.3 铸件采购、质量检查和供方可在保证铸件满足铸件验收技术条件的前提下,鼓励三方协商建立铸件外观质量标杆样件(即合格的最低标准实物)库,便于铸件外观质量验收参照标杆样件执行,低于此实物标准时为不合格。
4.2 灰铸铁件及碳钢铸件4.2.1 表面缺陷4.2.1.1 铸件表面不允许有冷隔、裂纹、孔洞贯穿内外表面的缺陷及机械加工不能去除的其它缺陷.4.2.1.2 铸件上的型砂、芯砂、披缝必须清理干净;其中,披缝非加工面不大于 2 mm,加工面不大于 3 mm;4.2.1.3 灰铸铁件表面允许存在的孔洞类缺陷见表 2;表 2 砂型铸造灰铸铁件表面允许存在的孔洞类缺陷4.2.1.4 碳钢铸件表面允许存在的孔洞类缺陷见表 3表 3 碳钢铸件表面允许存在的孔洞类缺陷4.2.1.5 铸件内、外表面应清理干净,不应有浮砂、粘砂、氧化皮。
压铸件品质检验规范

压铸件质检规范1、目的明确压铸件品质验收规范,规范检验动作,使检验、判定规范能达到一致性2、适用范围本规范适用于公司配套的锌合金压铸件的外观检验,包括毛坯、成品)完成铸造后机械加工的产品)。
3、技术要求3.1压铸件质量要求3.1.1压铸件应符合零件图样的规定。
3.1.2表面质量3.1.2.1压铸件表面粗糙度应符合GB/T6060.1的规定。
3.1.2.2压铸件表面不允许有裂纹、欠铸、疏松、气泡和任何穿透性缺陷。
3.1.2.3压铸件表面允许有擦伤、凹陷、缺肉和网状毛刺等缺陷。
但缺陷必须符合表1规定。
表1压铸件表面质量要求缺陷名称缺陷范围数值备注擦伤深度(mm)≤0.10面积不超过总面积的百分数5凹陷凹入深度(mm)≤0.30缺肉深度(mm)≤0.50长度不大于(mm)2所在面上不允许超过的数量2离压铸件边缘距离(mm)≥4间距(mm)≥10网状毛刺高度(mm)≤0.23.1.2.4压铸件的浇口、飞边、溢流口、隔皮、顶杆痕迹等应清理干净。
但允许留有痕迹。
3.1.2.5若图样无特别规定,有关压铸工艺部分的设置,如顶杆位置、分型线的位置、浇口和溢流口位置等由生产厂自行规定。
3.1.2.6压铸件需要特殊加工的表面,如抛光、喷丸、镀铬、涂覆、阳极氧化、化学氧化等须在图样上注明。
3.1.3压铸件机加工平面加工后的表面质量3.1.3.1不允许有影响使用的局部铸态表皮存在。
3.1.3.2不允许有超过表2规定的孔穴存在。
表2压铸件机加工平面允许的孔穴项目最大直径(mm)最大深度(mm)最多个数/cm2边缘间最小距离(mm)孔穴0.50.2243.1.4压铸件机械加工螺纹的表面质量3.1.4.1压铸件机械加工螺纹的头两扣不允许有任何缺陷,其余部分螺纹不允许有表3所规定的孔穴缺陷。
表3机械加工螺纹规定的孔穴缺陷范围螺距(mm)平均直径(mm)≤螺纹工作长度内个数≤深度(mm)≤两孔的边距(mm)≥≤0.751122>0.75 1.54 1.553.1.4.2压铸件不铸底孔加工后的螺纹表面质量见表4的规定。
铸造材料技术要求和验收规范
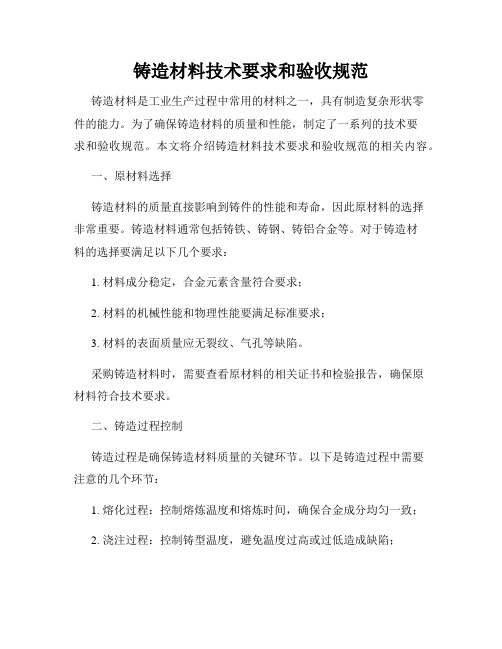
铸造材料技术要求和验收规范铸造材料是工业生产过程中常用的材料之一,具有制造复杂形状零件的能力。
为了确保铸造材料的质量和性能,制定了一系列的技术要求和验收规范。
本文将介绍铸造材料技术要求和验收规范的相关内容。
一、原材料选择铸造材料的质量直接影响到铸件的性能和寿命,因此原材料的选择非常重要。
铸造材料通常包括铸铁、铸钢、铸铝合金等。
对于铸造材料的选择要满足以下几个要求:1. 材料成分稳定,合金元素含量符合要求;2. 材料的机械性能和物理性能要满足标准要求;3. 材料的表面质量应无裂纹、气孔等缺陷。
采购铸造材料时,需要查看原材料的相关证书和检验报告,确保原材料符合技术要求。
二、铸造过程控制铸造过程是确保铸造材料质量的关键环节。
以下是铸造过程中需要注意的几个环节:1. 熔化过程:控制熔炼温度和熔炼时间,确保合金成分均匀一致;2. 浇注过程:控制铸型温度,避免温度过高或过低造成缺陷;3. 热处理过程:根据不同的铸造材料,进行适当的热处理,提高材料的性能;4. 温度控制:铸造材料的温度对最终产品的性能影响很大,需要控制好铸造温度。
三、铸造材料的质量检验铸造材料的质量检验是保证产品质量的重要环节。
以下是一些常见的铸造材料的质量检验方法:1. 成分分析:通过化学分析仪器来检测铸造材料的合金成分,以确保其符合标准要求;2. 金相检验:利用金相显微镜观察铸造材料的显微组织,评估其组织性能;3. 机械性能测试:通过拉伸试验、冲击试验等方法来测试铸造材料的力学性能;4. 铸件表面检查:观察铸件表面是否存在缺陷、夹杂物等;根据不同的铸造材料,可以选择相应的检验方法来确保铸造材料质量。
四、验收规范为了确保铸造材料的质量,制定了一系列的验收规范。
以下是一些常见的验收规范要求:1. 材料的外观质量:表面应无裂纹、气孔、夹杂物等缺陷;2. 成分符合要求:合金成分应符合设计要求,不得低于或高于标准限制;3. 机械性能:铸造材料的抗拉强度、屈服强度、伸长率等力学性能应符合标准;4. 金相组织:铸造材料的金相组织应均匀细致,不得存在夹杂物和非金属夹杂。
铸件质量检验标准

—
—
—
—
—
—
—
—
0.64
0.72
0.80
0.9
1.0
1.1
1.2
1.4
1.6
1.8
2.0
2.2
2.6
2.8
3.2
3.6
4.0
4.6
5
6
7
7
8
9
10
11
13
1600
2500
4000
6300
2500
4000
6300
10000
—
—
—
—
—
—
—
—
—
—
—
—
—
—
—
0.24
0.26
0.28
0.32
0.36
0.40
0.46
0.50
0.56
0.64
0.70
0.78
0.9
1.0
1.1
1.3
1.4
1.6
1.8
2.0
2.2
2.6
2.8
CF3M
ASTM
A351
0.03 1.5 1.5 17~21 0.04 0.04 9~13 2~3
CF8M
ASTM
A351
0.08 1.5 1.5 18~21 0.04 0.04 9~12 2~3
CG3M
ASTM
A351
0.03 1.0 2.0 18~20 0.035 0.03 11~15 3~4
铸件验收标准

1)、清理干净后最大直径不大于 3mm,深度在铸件壁上不大于壁厚的 1/3,在安装边上不大于其厚度的 1/4,且不得超过 1.5mm 的单个孔洞和清理干净后最大直径不大于 1.5mm,深度不大于壁厚的 1/3,且不
注:铸件在机械加工前后发现的小缺陷,经有关部门同意,补焊后可不进行热处理。 24、补焊处需经表面检查和根据工艺需要进行 X 光透视,透视不得小于补焊面积的两倍。焊区内允许的标准
与 X 光透视标准相同。 注:铸件表面上小的明孔洞,补焊后可不透视,(扩修后<1.5cm2 明孔洞)。 25、翘曲的铸件允许矫正,矫正后应检查有无裂纹,必要时需重复进行热处理。
≥80 ≥100 ≥50 ≥90 ≥70 ≥80 ≥70 90-115 ≥70 85~115 ≥80 ≥70 ≥80 ≥50 80-100
注: 1)硬度值除设计部门规定按表 2 检验外,仅作验收依据。
2)当测得的机械性能数值遇界限值时,按本标准规定的有效位数进行修约,修约按 GB1780 的规定,强
二:技术要求和检验
*** 化学成份 ***
1、每一炉次的合金,必须对以下成份进行光谱分析。合金的化学成份分析结果应符合表 1 的规定。同时,
在铸件上标识炉号及炉次号进行追溯。
注:当测得的化学成分数值遇界限值时,按本标准规定的有效位数进行修约,修约规则按 GB1780r 规定。
表 1 化学成份 %
合金 代号
铸件检验标准[1]
![铸件检验标准[1]](https://img.taocdn.com/s3/m/9335f22359fb770bf78a6529647d27284b7337d3.png)
铝合金铸造件检验技术条件(试行)1 内容及适用范围本标准根据GB/T 1173-1995及GB/T 9438-1999的相关内容,规定了铝合金铸件的分类和铸件的外观质量、内在质量以及铸件修补等内容的技术要求与检验规则等。
本标准适用于我公司采用金属型铸造所生产的制动器上、下泵体等铸件(不含压力铸造)。
根据工作条件、用途以及在使用过程中如果损坏,所能造成的危害程度,将铸件分类如下:2 技术要求2.1 化学成分2.1.1合金的化学成分根据GB/T 1173-1995的规定,应符合表2-1及表2-2的规定。
2.1.2当使用杂质总和来表示杂质含量时,如无特殊规定,其中每一种未列出的元素含量不大于0.02%。
2.2 状态2.2.1铸件按表2-3的规定,呈铸态或热处理状态供应。
注:在保证合金机械性能前提下,可以不加铍(Be)。
2.3 机械性能2.3.1 每批铸件应按其类别检验机械性能。
2.3.2 合金及其铸件的机械性能应符合表2-3的规定。
2.4外观质量2.4.1铸件在进行表面粗糙度、表面缺陷、尺寸等外观质量检验之前,飞边、溢流口、隔皮等应清理干净、平整,但不可在非加工表面上留有明显的凿痕,且宽度不得超过2mm。
2.4.2铸件的表面粗糙度Ra为6.3μm以上。
2.4.3非加工表面的浇冒口,应清理到与铸件表面齐平;待加工表面的浇冒口残留量应不大于3mm。
2.4.4清除飞翅、夹砂等多肉类缺陷,铸件的内外表面由于型芯及顶杆的磨损所产生的飞边、毛刺应清除干净。
2.4.5根据顾客图样或技术文件的要求,铸件表面可进行喷砂处理。
2.4.6铸件上作为基准用的部位应平整,不允许存在任何凸起痕迹,装饰面上不允许有推杆痕迹(图样上注明)。
2.4.7非加工表面上,由于模具组合镶并或受分型面影响而形成的铸件表面高低不平差值不得超过0.3mm。
2.4. 8非加工表面上,不允许有超过表2-4(Ⅰ)级规定的花纹、麻面和有色斑点。
2.4.9铸件尺寸应符合图样的要求。
01-铸件外观质量检验标准
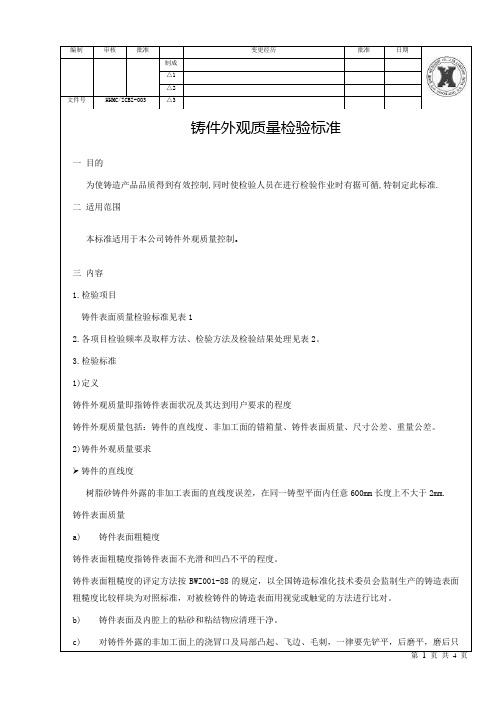
编制审核批准变更经历批准日期
制成
△1
△2
文件号HHMC/ZCBZ-003 △3
铸件外观质量检验标准
一目的
为使铸造产品品质得到有效控制,同时使检验人员在进行检验作业时有据可循,特制定此标准.
二适用范围
本标准适用于本公司铸件外观质量控制.
三内容
1.检验项目
铸件表面质量检验标准见表1
2.各项目检验频率及取样方法、检验方法及检验结果处理见表2。
3.检验标准
1)定义
铸件外观质量即指铸件表面状况及其达到用户要求的程度
铸件外观质量包括:铸件的直线度、非加工面的错箱量、铸件表面质量、尺寸公差、重量公差。
2)铸件外观质量要求
➢铸件的直线度
树脂砂铸件外露的非加工表面的直线度误差,在同一铸型平面内任意600mm长度上不大于2mm. 铸件表面质量
a)铸件表面粗糙度
铸件表面粗糙度指铸件表面不光滑和凹凸不平的程度。
铸件表面粗糙度的评定方法按BWZ001-88的规定,以全国铸造标准化技术委员会监制生产的铸造表面粗糙度比较样块为对照标准,对被检铸件的铸造表面用视觉或触觉的方法进行比对。
b)铸件表面及内腔上的粘砂和粘结物应清理干净。
c)对铸件外露的非加工面上的浇冒口及局部凸起、飞边、毛刺,一律要先铲平,后磨平,磨后只。
铸件表面质量验收标准

铸铁件验收项目及标准铸件的表面质量主要包括铸件的表面缺陷、尺寸精度、形状偏差、表面粗糙度、表面清理质量等;1、铸件表面缺陷的检验1.1表面缺陷检验的一般要求1.1.1铸件非加工表面上的浇冒口必须清理得与铸件表面同样平整,加工面上的浇冒口残留量应符合技术要求,若无要求,则按表8执行;1.1.2在铸件上不允许有裂纹、通孔、穿透性的冷隔和穿透性的缩松、夹渣等机械加工不能去除的缺陷;1.1.3铸件非加工表面的毛刺、披缝、型砂、砂芯等应清理干净;1.1.4铸件一般待加工表面,允许有不超过加工余量范围内的任何缺陷存在;重要加工面允许有不超过加工余量2/3的缺陷存在,但裂纹缺陷应予清除;加工后的表面允许存在直径*长度*深度小于等于2*2*2的非连片孔洞的铸造缺陷;1.1.5作为加工基准面(孔)和测量基准的铸件表面,平整度小于等于2.0 毫米、粗糙度Ra50以内;1.1.6铸件表面气孔、砂眼、夹渣面积不大,但比较分散或者有连片麻点的表面不予接收;1.1.7除技术要求特别注明的铸件外,对于表面有气孔、缩孔、砂眼等缺陷的铸钢件允许补焊,但铸铁件未经允许不得焊补(铸铁件实行一案一判的原则)但补焊面积不允许超过铸件面积的10%,焊接质量应符合JB/T 5000.7-2007标准要求,补焊后必须退火、机械性能达到图纸要求,且不得有渗漏及影响外观的缺陷;1.2铸件外观质量等级表1 铸件外观质量等级1、一般零部件采用B级精度,在检查过程中,如有一个或多个项目超出B级精度要求的零部件均判定为不合格;2、影响到零部件安全、性能的部位,外观质量采用A级精度,如果有一个或多个项目超出规定级精度要求的零部件均判定为不合格;2、铸件尺寸的检验2.1铸件毛坯尺寸公差铸件尺寸公差应按毛坯图或技术条件规定的尺寸公差等级执行,当技术文件未规定尺寸公差时,则应以GB6414-1999为依据,并按照表2选定公差值(粗线框内为推荐使用公差等级);表2铸件尺寸公差(单位:mm)2.2铸件分型面处最大错型值应不得超过表2所示公差值,当需进一步限制错型量时,应从表3中选取;表 3 错型值(GB6414-1999)2.3铸件加工余量应符合表4的规定,有特殊要求的表面应在技术要求中单独标注加工余量;表4加工余量(单位:mm)3、表面粗糙度检测表面粗糙度总体检测原则依据图纸要求,当图纸无要求是执行国标GB/T15056-1994;3.1一般情况下,表面粗糙度要求Ra50,铸件难以清理的部位,局部允许 Ra100,待加工表面允许降低1级;3.2.使用面积法作为验收依据面积法常用的比较样块评定铸件表面粗糙度;方法如下:3.2.1铸造表面粗糙度比较样块应符合GB6060.1-1997标准;3.2.2按照国标BWZ001-88评定铸件表面粗糙度的等级;3.2.3铸件的浇道、冒口、修补的残余表面及铸造表面缺陷(如粘砂、结疤等)不列为被检表面;3.2.4以铸造表面粗糙度比较样块为对照标准,对被检铸件的铸造表面用视觉或触觉的方法进行对比;3.2.5用样块对比时,应选用适于铸造合金材料和工艺方法的样块进行对比;3.2.6被检的铸造表面必须清理干净,样块表面和被检表面均不得有锈蚀处;3.2.7用样块对比时,砂型铸造表面被检点数应符合表7的规定;特种铸造表面被检点数应按表8的规定加倍;被检点应平均分布,每点的被检面积不得小于与之对比面的面积;表7 被检铸造表面最低检测数3.2.8当被检铸造表面的粗糙度介于比较样块两级参数值之间者,所确定的被检铸造表面的粗糙度等级为粗的一级;3.2.9对被检铸造表面,以其80%的表面所达到的最粗表面粗糙度等级,为该铸造表面粗糙度等级;3.3铸件表面清理检测3.3.1铸件几何形状必须完整,非加工面上的清理损伤不应大于该处的尺寸偏差,加工面上的损伤不应大于该处加工余量的1/2;3.3.2允许铸件表面有少量的局部低凹或打磨痕迹,在直径不大于8mm,并能保证铸件规定的最小的壁厚;3.3.3为去除铸造缺陷而打磨后的铸件表面粗糙度应与一般铸件表面粗糙度基本一致;3.3.4除特殊情况外,铸件表面允许残留的浇冒口、毛刺,多肉残余量应按表 8的要求进行;表8 浇冒口、毛刺、多肉等允许残留量值3.3.5铸件表面须经过防锈处理,保证在铸件进入面加工时不得有任何的锈蚀;3.3.6铸件表面如有油漆要求的,必须按有关涂装规定执行;4、铸件重量检测对于没有特殊要求的铸件,重量偏差可以不作为验收依据;如果技术条件有要求,供需双方协商后,铸件的重量偏差也应作为验收依据,一般应符合表6的规定;表6铸件重量偏差。
Q2024J04铸铁件、碳钢铸件检验规范
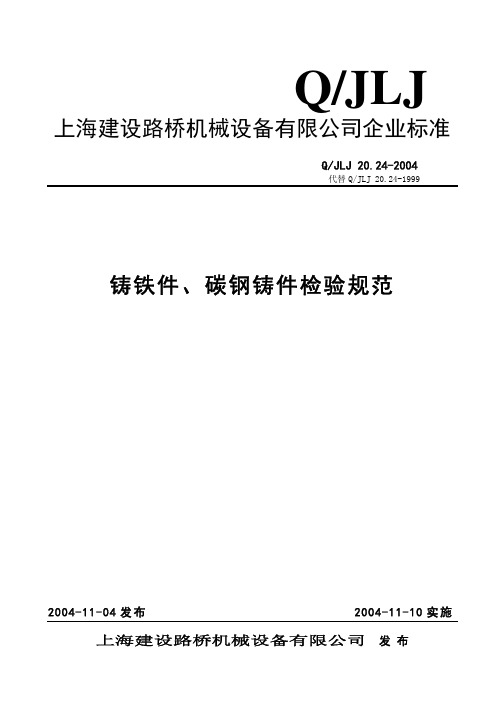
Q/JLJ 上海建设路桥机械设备有限公司企业标准Q/JLJ 20.24-2004代替Q/JLJ 20.24-1999铸铁件、碳钢铸件检验规范2004-11-04发布2004-11-10实施上海建设路桥机械设备有限公司发 布前 言本标准根据国家现有的铸件通用标准及本公司相关的技术文件而制定,指导检验人员用于铸件质量检验。
本标准对Q/JLJ 20.24-1993第3.1和3.3条款进行了修改,补充了相应的理化试验内容,作为进货检验和试验工作指导性文件。
本标准的格式按照GB/T 1.1-2000《标准化工作导则 第1部分:标准的结构和编写规则》进行编辑性修改,具体内容与Q/JLJ 20.24-1999完全一致。
本标准由公司标准化委员会提出;本标准由总工程师室归口;本标准主要起草人:张兰;本标准审核人:陈志兴;本标准标准化审查人:王定华;本标准由公司总工程师李本仁审定;本标准由公司总经理张庆伟批准。
本标准所代替标准的历次发布情况为:——Q/JLJ 20.24-1993、Q/JLJ 20.24-1999。
I铸铁件、碳钢铸件检验规范1 范围本规范规定了质量检查项目和检验频次等事项。
本规范适用于本公司外协铸铁件、碳钢铸件的检验。
不适用高锰钢件及高铬铸铁件。
2 规范性引用文件下列文件中的条款通过本标准的引用而成为本标准的条款。
凡是注日期的引用文件,其随后所有的修改单(不包括勘误的内容)或修订版均不适用于本标准,然而,鼓励根据本标准达成协议的各方研究是否可使用这些文件的最新版本。
凡是不注日期的引用文件,其最新版本适用于本标准。
GB/T 1348 球墨铸铁件GB/T 6414 铸件尺寸公差GB/T 9439 灰铸铁件GB/T 9441 球墨铸铁金相GB/T 11352 一般工程用铸造碳钢件3 质量检查项目3.1 铸件进厂应含有下列内容的质量证明书a ) 铸造厂名;b ) 炉批号;c ) 材质牌号;d ) 机械性能;e ) 化学成分(铸钢件);f ) 浇注随炉试样(重要铸件);3.2 几何形状和尺寸检查按图纸规定的尺寸检查,毛坯中未注公差的尺寸按 GB/T 6414 检验。
铸件验收标准(原始)

关于铸件的验收标准1.化学成分:对有材质要求的铸件(耐热铸件),供应商应提供化学成分报告,并注明每炉所浇铸件的数量和炉号。
我方进行抽查并委托第三方检验。
2.尺寸检查:对需配合的尺寸,一般重点进行检查,验证模型有无变化。
配合面必须平直,不能有影响装配的变形和缺陷。
3.硬度要求:HT,HB160-230;HC,HB170-260。
4.外观质量:A.砂眼、气孔外露表面不允许有大于直径2毫米的砂眼、气孔;小于2毫米的砂眼、气孔在整个板面上不得多于4处,并必需用耐高温铸工胶修补并打磨平整,否则拒收。
不允许有蜂窝状针孔、气孔。
内部表面允许有部分砂眼、气孔,但不得贯穿整个壁厚。
B.表面粗糙度外露表面应平整、光滑,整体感觉均匀一致,不得有明显的铸造缺陷。
表面的凸凹处理应整体保持均匀,不应有的地方凸凹明显,有的地方凸凹不明显。
允许有小于1毫米的凸起、凹坑并应打磨平整,或粘补后打磨平整。
抛丸露出金属本体光泽,不得有锈或油污。
内部表面允许有大于1毫米、小于2毫米的凸起、凹坑,但不得影响炉子的装配。
C:变形炉板的变形量允许在总长的长度上有1毫米,不允许存在有不规则的变形,否则拒收。
D:冷隔外露表面不允许有冷隔。
内部表面允许有不贯穿壁厚且长度不大于10毫米的冷隔。
E:飞边、毛刺飞边、毛刺、浇口等部位应打磨平整、光滑,不允许有锐利的尖角存在。
F:凡是有裂纹的铸件拒收。
G:修补件在铸件需加工或受力的部位,不允许补焊。
其它部位允许修补但缺陷不得大于2毫米并打磨平整。
郑州平凡实业有限公司管城分公司技术质量部2006-3-8。
铸件表面质量评定准则

本标准规定了铸件表面质量评定的有关技术要求及评定方法;本标准适应于本厂所需铸件的表面质量评定。
1. 技术要求铸件的铸造表面粗糙度应符合产品技术要求,当无明确技术要求时,按Rz8000 验收;铸件的几何形状及尺寸应符合产品图纸及订货协议的要求;清理后的铸件外表面一般不允许有粘砂、氧化皮、结疤和影响零件装配及外表美观的缺陷;除特殊情况外,铸件表面允许存留浇冒口、毛刺、飞边、胀砂、多肉残余量,见表1:2. 评定方法铸造表面粗糙度评定方法(GB15056-942.1.1本标准适用于采用GB6060.1规定的铸造表面粗糙度比较样块对铸件铸造表面粗糙度进行评定,对铸件铸造表面缺陷(如粘砂、结疤等)不列为被检表面; 2.1.2铸件表面粗糙度参数等级:铸件表面粗糙度参数数值等级应符合GB6060.1规定。
2.1.3铸造表面粗糙度比较样块的比对方法:2.131以符合GB6060.1规定的铸造表面粗糙度比较样块,对被检铸件的铸造表面用视觉或触觉的方法进行比较;2.1.3.2试验前被检的铸造表面必须清理干净,样块表面和被检铸造表面都不得有锈蚀;2.1.3.3视觉比对时,应在光线充足的场地用肉眼直观比对,也可用放大镜观察比对;2.1.3.4触觉比对时,应用手指在被检铸造表面和相近2个参数等级比较样块表面触摸,获得同样感觉的那个等级,即为被检铸造表面粗糙度数值;2.1.3.5用样块比对时,应选用适于铸造合金材质和工艺方法的样块进行比对。
2.1.4铸造表面粗糙度等级的评定:2.1.4.1对被检铸造表面均匀划分若干个检测单元,用样块对检测单元逐一进行比对;2.1.4.2划分检测单元的数目应符合表2的规定,每个检测单元面积不得小于样块的面积;2.1.4.3检测单元的表面粗糙度参数值等级应以该表面内表面粗糙度参数值最大的等级评定。
当表面粗糙度介于比较样块两级参数值之间时,以数值大的等级评^定。
2.1.4.4将所有检测单元的表面粗糙度参数值从小到大加以整理,以最小等级起的80%佥测单元数中的最大数值等级定为该铸造表面粗糙度等级,但其余20%佥测单元表面粗糙度参数等级比所定等级不得大于一个等级以上;2.1.4.5当20%佥测单元的表面粗糙度等级比80%佥测单元表面粗糙度等级大二个或二个等级以上时。
铸件检验标准
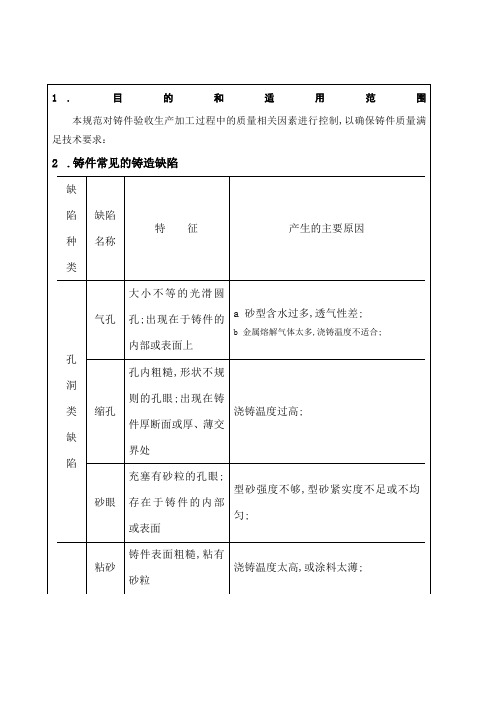
3.
铸件出现铸造缺陷后,并非都是废品,应根据铸件的具体技术要求判断,判断原则如下:
a铸件出现铸造缺陷后,其质量达不到技术要求,而又不能修补时,应列为废品;
b 不重要的铸件或铸件的某些部位即使存在铸造缺陷,如不影响使用或者修补后不影响使用时,可以不列为废品;
c 当铸件出现铸造缺陷,即使技术上可以修补,并且修补后不影响使用,但由于经济上不合算,或因此会给企业造成不良影响时,仍应不修补而列为废品;
浇铸温度过高;
砂眼
充塞有砂粒的孔眼;存在于铸件的内部或表面
型砂强度不够,型砂紧实度不足或不均匀;
粘砂
铸件表面粗糙,粘有砂粒
浇铸温度太高,或涂料太薄;裂纹开裂Fra bibliotek开裂处金属表面氧化
合金化学成分不当,铸件厚薄相差大,结构不合理,金属浇铸温度过高,型砂或泥芯容让性差或落砂过早;
冷隔
未完全融合的缝隙或洼坑,交接处是圆滑的
a为铸件生产和管理部门提供质量信息;保证产品质量;
b铸件的检验主要包括铸件表面质量检验、铸件内在质量检验以及铸件质量的综合鉴定;其中,铸件的表面质量包括铸件的表面缺陷、尺寸精度、质量偏差、表面粗糙度等;
4:铸件外观质量的检验
检验的依据是铸件的有关标准、技术条件和图样;铸件的表面质量主要包括铸件的表面缺陷、尺寸精度、质量偏差、形状偏差、表面粗糙度和铸件表面清理质量等多方面内容;
5、铸件
为保证铸件的表面质量,检验要求一般规定如下;
在铸件上不允许有裂纹、通孔、穿透性的冷隔和穿透性的缩松、夹渣缺陷;
铸件非加工表面的毛刺、披锋、粘砂应清理至与铸件面同样平整;
铸件待加工表面,允许有不超过加工余量范围内的任何缺陷存在,但裂纹缺陷应予清除;
铸造产品生产验收标准-GX
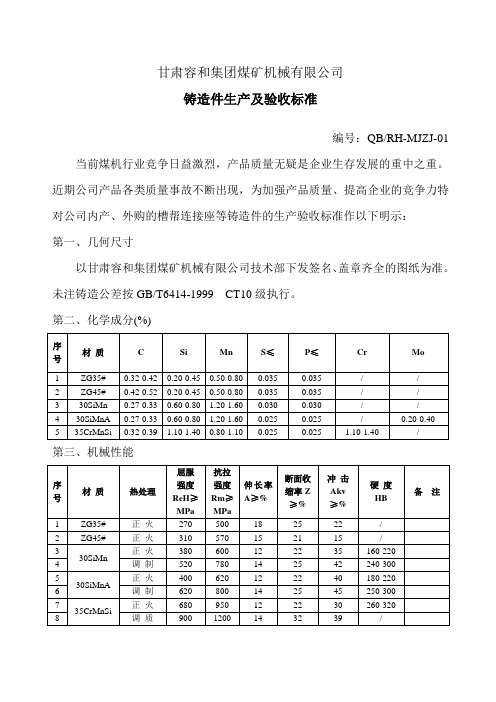
甘肃容和集团煤矿机械有限公司铸造件生产及验收标准编号:QB/RH-MJZJ-01 当前煤机行业竞争日益激烈,产品质量无疑是企业生存发展的重中之重。
近期公司产品各类质量事故不断出现,为加强产品质量、提高企业的竞争力特对公司内产、外购的槽帮连接座等铸造件的生产验收标准作以下明示:第一、几何尺寸以甘肃容和集团煤矿机械有限公司技术部下发签名、盖章齐全的图纸为准。
未注铸造公差按GB/T6414-1999 CT10级执行。
第二、化学成分(%)第三、机械性能第四、金相组织及超声波探伤要求金相组织检验按GB/T8493的规定,正火后的实际晶粒度等级应≥4级,非金属夹杂物≤2级;超声波探伤铲挡板哑铃销凸凹头及推移耳部位不充许存在内在缺陷,其它探伤位置内在缺陷按GB7233-87标准执行。
槽宽900(含900)以上的铲挡板铸件Ⅱ级为合格,槽宽900以下的铲挡板铸件Ⅲ级为合格。
第五、表面缺陷修理办法要求铲挡板凸凹头及推移耳表面缺陷部位缺陷深度≤最小壁厚10%;面积≤125mm2充许补焊,超出上述范围的需经我方评审同意后方可补焊;其它部位缺陷≤最小壁厚的20%,面积超出800mm2时补焊要做好记录便于追溯。
缺陷面积≥3500mm2时不充许补焊予以报废处理。
以上缺陷补焊要在热处理前进行,补焊要先清理缺陷部位,并打磨出金属光泽后方可补焊,补焊后打磨光滑平整。
第六、铸造件归类1、1.5米铲挡板类材质:ZG30SiMn 热处理状态:正火态1.75米铲挡板类材质:ZG30SiMn 热处理状态:调质态1.75米铲挡板类材质:ZG30SiMnA 热处理状态:调质态2、连接座类材质:ZG 30SiMn 热处理状态:正火态3、连接板类材质:ZG 30SiMn 热处理状态:正火态4、拉移座类材质:ZG 30SiMn 热处理状态:正火态5、推移座类材质:30SiMn 热处理状态:正火态6、齿轨插座类材质:ZG35(30SiMn) 热处理状态:正火态7、齿轨类(常规)材质:ZG 30SiMn 热处理状态:调质态齿轨类(高强)材质:ZG35CrMnSi 热处理状态:正火态8、其它铸造产品根据实际情况既定第七、在今后的铸造件生产、采购中供货单位必须向公司提供几何尺寸及化学成分(Ⅰ、1-3件100%提供报告;Ⅱ、3以上10件以下按50%提供报告;Ⅲ、10件以上的批量件按20%提供报告)、热处理及机械性能合格报告单(具体格式见附表)。
QT450-10铸造毛坯件检验规范

1、目的为了规范公司对铸造件质量的检验。
2、适用范围适用于公司内所有球墨铸铁材质的产品。
3、引用标准GB /T5612-2008 铸铁牌号表示法GB/T1348-1988 球墨铸铁件GB 231-84 金属布氏硬度试验法GB/T9441-2009 球墨铸铁金相检验GB/T6414-1999 铸件尺寸公差与机械加工余量GB 6060.1-85 表面粗糙度比较样块铸造表面4、验收标准4.1 铸件材质检验标准:4.1.1 球墨铸件材质验收标准应符合GB1348-1988 球墨铸铁的标准,以机械性能(抗拉强度、延伸率)、金相组织为验收依据,硬度及化学成分做为参考。
4.1.1.3 壳体毛坯件的球墨铸铁材质正火后其珠光体(正火索氏体)组织等级在3级以上。
4.1.2 材质检验取样规范4.1.2.1机械性能检查:机械性能测试的试块,每班次每种牌号至少浇注三根,若铸件进行热处理,必须连同试块一同进行热处理。
二根用于生产厂测试性能(第一根合格则该批次合格,余下试块(留有生产日期、包次标识)留存。
若第一根试块不合格,测试剩余二根,若第二根不合格则该批次产品全部报废,若第二根合格,应加试第三根,合格则判定该炉产品合格,若第三根不合格则该批次产品全部报废)。
材质检验报告(原档)保存期为5年。
4.1.2.2金相组织检查:球铁铸件从每包铁水的最后一型附铸金相试块或铸件本体进行金相检验,依次往前直到合格(或本包铁水所浇铸件检验完)为止。
附铸试块应能代表本体。
若试块不好,应对铸件本体破件进行检验。
若金相检验由问题,加倍抽查。
金相本体试块应按天分类以月为单位保存,保存期为6个月,检验报告保存期5年。
球化等级要求在3级以上,石墨大小要求为5~7级。
4.1.2.3化学成分检查:每天必须分析每炉铁水(炉前)及至少两炉铸件(炉后)的化学成分。
炉前主要化验C、Si和S,炉后所有元素全部化验。
每天第一炉溶清后必须检测C、Si、Mn、P和S,之后C、Si每炉化验检测。
压铸件产品外观质量验收标准
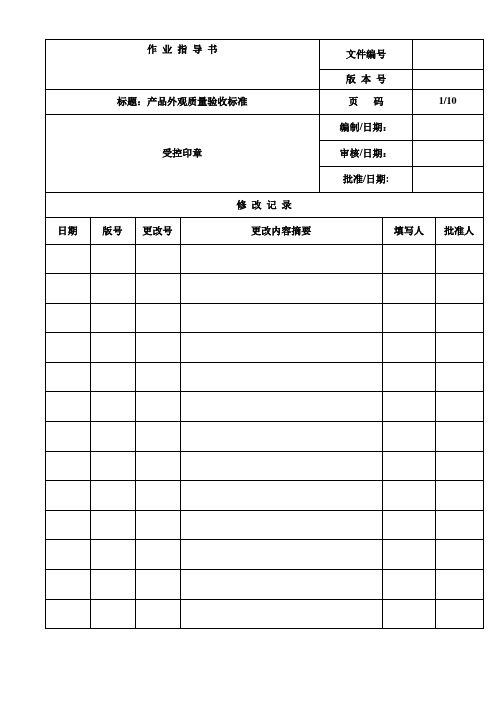
1 目的本标准定义来料或成品外观质量的基本要起,并作为允收/拒收准则。
2 适用范围来料或成品。
3 检测面的分级:A级面:使用者经常看到的面,如产品的上表面、正面、需要丝印的面等.B级面:在不移动的情况下,使用者偶尔能看到的面,如产品的后面、侧面等。
C级面:产品在移动或被打开时才能看到的面,如产品的底面,内部零件的表面等。
4 检测条件4。
1、所有检验均应在正常照明,并模拟最终使用条件下进行。
检测过程中不使用放大镜,所检验表面和人眼呈45°角。
A级面在检测时应转动,以获得最大反光效果。
B级面和C级面在检测期间不必转动。
光源=40W荧光灯500毫米了4.2、A级面停留10秒,B级面停留5秒,C级面停留3秒。
5 金属件外观检验标准5.1 允收总则5。
1.1 可接受的缺陷不能影响该零件的装配和功能,否则将被拒收。
5.1.2 缺陷允收定义了900mm2的区域内各类缺陷的最大允收数量。
但是,两个区域或两个以上明显缺陷不能相连。
5.2缺陷定义5。
2。
1生锈/氧化:暴露在空气中的金属表面发生的化学反应,包括变黄以及出现其它异常.5.2。
2变色:底色或预期的颜色发生改变,或零件表面的颜色不一致。
5.2.3刮伤:零件表面的呈条状的浅沟,包括露底与不露底.5。
2.4压痕:由尖锐物件在零件表面造成的沟痕,指甲能够感受到.5。
2。
5镀痕/流痕:由于镀层厚度不均匀造成零件表面上波纹状或条状异常的区域。
5。
2.6痕迹:指基体材料的小坑、折弯痕或其他痕迹,涂装后仍无法消除。
5.2.7灰尘或油脂:在制造过程中产生并留在零件表面上的赃污(未清洗).5.2。
8斑点/颗粒:涂装面或零件表面任何非预期的异物。
5。
2。
9凹坑:零件表面弹坑状的缺陷。
5.2.10模压痕:因成形模具在零件表面造成的工艺痕,所有零件的模压痕的位置和大小都一样,均匀分布5.3 缺陷允收表每个面的缺陷数量不能超过允收的界限,如下表所示:缺陷允收表6 液体/粉末喷涂外观标准6。
- 1、下载文档前请自行甄别文档内容的完整性,平台不提供额外的编辑、内容补充、找答案等附加服务。
- 2、"仅部分预览"的文档,不可在线预览部分如存在完整性等问题,可反馈申请退款(可完整预览的文档不适用该条件!)。
- 3、如文档侵犯您的权益,请联系客服反馈,我们会尽快为您处理(人工客服工作时间:9:00-18:30)。
222精密机械企业标准
编号:YQB/0004-2016-A
铸件表面质量验收规
发布时间:2016年 7 月 13 日实施时间:2016年 7 月 13 日
222精密机械发布
1、目的
为加强本公司对铸件的质量控制,保证本公司产品的外观质量及加工性能,特制订铸件表面质量验收规;
2、适用围
本规适用于公司所有外来铸铁(钢)件的外观质量验收,包括表面缺陷、尺寸精度、表面粗糙度的验收;
3、引用标准
(1)JB/T 5000.4-2007 重型机械通用技术条件第4部分铸铁件;
(2)JB/T 5000.6-2007 重型机械通用技术条件第6部分铸钢件;
(3)GB6414-1999 铸件尺寸公差与机械加工余量;
(4)GB/T6060.1-1997 表面粗糙度比较样块;
(5)GB/T15056-1994 铸造表面粗糙度评定方法;
(6)Q/XC5101-2001 铸铁件通用技术条件;
(7GB/T11351-1989 铸件重量公差
4、名词解释
(1)全数选别:检验项目100%检测;
5、验收项目及标准
铸件的表面质量主要包括铸件的表面缺陷、尺寸精度、形状偏差、表面粗糙度、表面清理质量等;
5.1铸件表面缺陷的检验
5.1.1表面缺陷检验的一般要求
(1)铸件非加工表面上的浇冒口必须清理得与铸件表面同样平整,加工面上的浇冒口残留量应符合技术要求,若无要求,则按表8执行;
(2)在铸件上不允许有裂纹、通孔、穿透性的冷隔和穿透性的缩松、夹渣等机械加工不能去除的缺陷;
(3)铸件非加工表面的毛刺、披缝、型砂、砂芯等应清理干净;
(4)铸件一般待加工表面,允许有不超过加工余量围的任何缺陷存在;重要加工面允许有不超过加工余量2/3的缺陷存在,但裂纹缺陷应予清除;加工后的表面允许存在直径*长度*深度小于等于2*2*2的非连片孔洞的铸造缺陷;
(5)作为加工基准面(孔)和测量基准的铸件表面,平整度小于等于2.0毫米、粗糙度Ra50以;
(6)铸件表面气孔、砂眼、夹渣面积不大,但比较分散或者有连片麻点的表面不予接收;
(7) 除技术要求特别注明的铸件外,对于表面有气孔、缩孔、砂眼等缺陷的铸钢件允许补焊,但铸铁件未经允许不得焊补(铸铁件实行一案一判的原则)但补焊面积不允许超过铸件面积的10%,焊接质量应符合JB/T 5000.7-2007标准要求,补焊后必须退火、机械性能达到图纸要求,且不得有渗漏及影响外观的缺陷;
5.1.2铸件外观质量等级
表1 铸件外观质量等级
5.2 铸件尺寸的检验
5.2.1铸件毛坯尺寸公差
铸件尺寸公差应按毛坯图或技术条件规定的尺寸公差等级执行,当技术文件未规定尺寸公差时,则应以GB6414-1999为依据,并按照表2选定公差值(粗线框为推荐使用公差等级);
表2铸件尺寸公差(单位:mm)
5.2.2铸件分型面处最大错型值应不得超过表2所示公差值,当需进一步限制错型量时,应从表3中选取;
表3 错型值(GB6414-1999)
5.2.3铸件加工余量应符合表4的规定,有特殊要求的表面应在技术要求中单独标注加工余量;
表4 加工余量(单位:mm)
5.3表面粗糙度检测
表面粗糙度总体检测原则依据图纸要求,当图纸无要执行国标
GB/T15056-1994;
5.3.1一般情况下,表面粗糙度要求 Ra50,铸件难以清理的部位,局部允许 Ra100,待加工表面允许降低1级;
5.3.2.使用面积法作为验收依据
面积法常用的比较样块评定铸件表面粗糙度;方法如下:
(1)铸造表面粗糙度比较样块应符合GB6060.1-1997标准;
(2)按照国标BWZ001-88评定铸件表面粗糙度的等级;
(3)铸件的浇道、冒口、修补的残余表面及铸造表面缺陷(如粘砂、结疤等)不列为被检表面;
(4)以铸造表面粗糙度比较样块为对照标准,对被检铸件的铸造表面用视觉或触觉的方法进行对比;
(5)用样块对比时,应选用适于铸造合金材料和工艺方法的样块进行对比;
(6)被检的铸造表面必须清理干净,样块表面和被检表面均不得有锈蚀处;
(7)用样块对比时,砂型铸造表面被检点数应符合表7的规定;特种铸造表面被检点数应按表8的规定加倍;被检点应平均分布,每点的被检面积不得小于与之对比面的面积;
表7 被检铸造表面最低检测数
(8)当被检铸造表面的粗糙度介于比较样块两级参数值之间者,所确定的被检铸造表面的粗糙度等级为粗的一级;
(9)对被检铸造表面,以其80%的表面所达到的最粗表面粗糙度等级,为该铸造表面粗糙度等级;
5.3.3铸件表面清理检测
5.3.1铸件几何形状必须完整,非加工面上的清理损伤不应大于该处的尺寸偏差,加工面上的损伤不应大于该处加工余量的1/2;
5.3.2允许铸件表面有少量的局部低凹或打磨痕迹,在直径不大于 8mm,并能保证铸件规定的最小的壁厚;
5.3.3为去除铸造缺陷而打磨后的铸件表面粗糙度应与一般铸件表面粗糙度基本一致;
5.3.4除特殊情况外,铸件表面允许残留的浇冒口、毛刺,多肉残余量应按表8的要求进行;
表8 浇冒口、毛刺、多肉等允许残留量值
5.3.5铸件表面须经过防锈处理,保证在铸件进入面加工时不得有任何的锈蚀;
5.3.6铸件表面如有油漆要求的,必须按有关涂装规定执行;
5.4铸件重量检测
5.4.1对于没有特殊要求的铸件,重量偏差可以不作为验收依据;如果技术条件有要求,供需双方协商后,铸件的重量偏差也应作为验收依据,一般应符合表6的规定;
表6 铸件重量偏差
6.铸件外观图片参考
——本规由222品质部提出
编制:雪刚审核:雪刚批准:。