大型热轧支撑辊堆焊技术
热轧辊堆焊技术分析研究
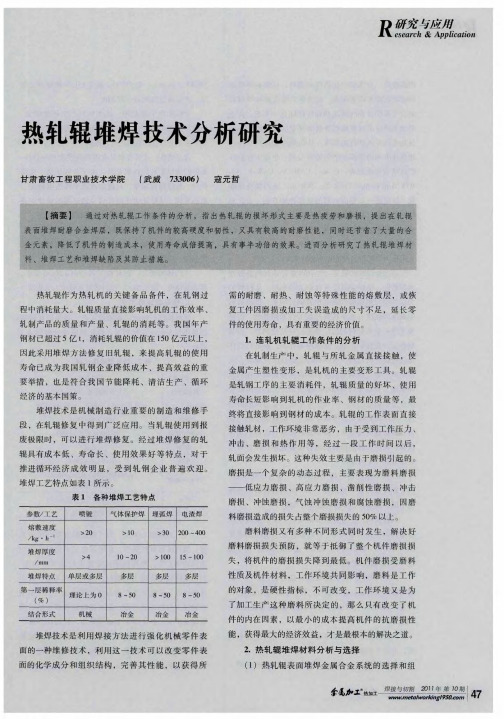
表 面清理 工 作 。堆 焊 前 钢 轧 辊 要 进 行 适 当 的 切 削 , 目的是将 轧槽 表 面上 的裂 纹 、龟 裂 全 部 车 除 。对 于 无 裂纹处 ,要 除 去 工 作表 面 的铁 锈 和 油 污 ,在 车 削
中发现个 别 的 深孔 砂 眼 ,需 要 用 电 钻或 砂 轮 将 砂 眼
R
鲫
织 的确 定
首 先 是 合金 系统 的选 择 :从 影 响热 疲 劳
3 HR 8 C,易加 工 。经 5 0C,保 温 1 h弥 散硬 化 处理 6 ̄ 5 后 ,硬度 可提高 到 4 4 H 。 6~ 7 RC 奥 氏体 加 工 硬 化 钢 :此 类 材 料 焊 后 硬 度 较 低 ,
现局 部过 热 。
热 不均 匀 引起 的 内应 力 最 小 。堆 焊 后 轧 辊 的缓 冷 有 以下几 种方 法 :① 装 入 缓 冷 坑 。 简 易 的 缓 冷坑 是 在 地 面下 用水 泥砌一 个坑 ,上 面有 绝 热材 料 制成 的盖 。 坑 内一 般 可 放 入 干 燥 的 黄 沙 、石 灰 、稻 草 灰 等 。 ②装 入保 温 炉 。轧 辊 预 热 、保 温 炉 的地 方 ,利 用 轧 辊加 热后 的 炉 子 预 热 ,并 将 堆焊 完毕 的轧 辊 装 人 炉 内 ,随炉冷 却 。
堆 焊后 的轧 辊应 立 即进 行 缓冷 ,冷 却 至 I0C O  ̄左
右 出炉 ( 出坑 ) 或 ,然 后进 行机 械加 工 。至 于缓 冷 时
间 ,主要是 以轧 辊 的体 积 为依 据 。对 于小 于 15 重 .t
的轧辊 ,缓 冷 时间 应 在 1 h以 上;对 于 3 2 t以上 的大
可能 造成 这 种 缺 陷 。堆 焊 时应 选 择 合 适 的堆 焊 材 料
轧辊堆焊技术

轧辊堆焊技术轧辊堆焊技术是一种常用的金属表面修复技术,通过在轧辊表面堆积耐磨合金,提高轧辊的耐磨性和使用寿命。
轧辊作为轧制设备中的重要部件,承受着巨大的压力和摩擦,容易出现磨损和裂纹,影响轧制质量和效率,因此轧辊堆焊技术的应用具有重要意义。
轧辊堆焊技术的原理是在轧辊表面堆焊一层耐磨合金,通常采用电弧堆焊或激光堆焊的方法。
堆焊材料的选择非常关键,一般选择硬度高、耐磨性好的合金材料,如钨碳合金、铬铁合金等。
堆焊时需要控制好堆焊层的厚度和均匀性,确保轧辊表面能够达到所需的硬度和耐磨性。
轧辊堆焊技术的优点在于能够有效延长轧辊的使用寿命,降低了设备的维护成本和停机时间,提高了生产效率。
同时,堆焊后的轧辊表面光滑平整,有利于提高产品表面质量,减少生产中的废品率。
另外,堆焊后的轧辊还能够承受更大的工作压力,适应更高强度的轧制工艺,提高了设备的稳定性和可靠性。
然而,轧辊堆焊技术也存在一些挑战和难点。
首先,堆焊工艺需要在高温高压的环境下进行,操作要求高,工艺控制难度大。
其次,堆焊层与轧辊基体之间易产生热应力和变形,需要通过合理的焊接工艺和后续热处理来解决。
此外,堆焊后的轧辊需要经过精细的磨削和抛光处理,确保表面光洁度和精度,增加了生产成本和工艺复杂度。
为了克服这些困难,现代轧辊堆焊技术不断创新和发展。
通过优化堆焊材料、改进堆焊工艺、引入先进的焊接设备和自动化控制系统,提高了堆焊层的质量和一致性。
同时,结合无损检测技术和数值模拟分析,实现对轧辊堆焊过程的实时监测和控制,确保轧辊表面质量和性能达到设计要求。
总的来说,轧辊堆焊技术在金属加工行业中具有重要的应用前景和发展空间。
随着科学技术的不断进步和产业需求的不断提高,轧辊堆焊技术将更加普及和完善,为轧制设备的性能提升和生产效率的提高做出更大贡献。
希望未来能够有更多的创新和突破,推动轧辊堆焊技术向更高水平迈进,为金属加工行业的发展注入新的活力和动力。
热轧支撑辊的堆焊修复强化工艺技术

热轧支撑辊的堆焊修复强化工艺技术介绍了梅山热轧支撑辊的堆焊修复工艺。
热轧支撑辊的堆焊难点主要是堆焊层开裂,通过工艺调整,可解决堆焊层开裂问题。
热轧支撑辊堆焊修复后的使用效果接近新辊,而堆焊成本仅为国产新辊的1/3,经济效益可观。
梅山1422热轧带钢生产线有在线支撑辊20支,全部为铸钢辊,其中有日本和英国等的进口辊,也有国产辊。
支撑辊的损坏形式除了正常磨损外,还有疲劳裂纹、辊面剥落等,有些支撑辊因工作层存在铸造缺陷,而不得不将缺陷厚度范围内的工作层全部车削去除。
支撑辊的工作层尺寸低于下限值时,其服役周期便结束,如作废辊处理,则浪费晾人。
如何充分发挥旧辊的“绿色”再利用潜力,达到降本增效的目的,这是冶金企业非常关心、重视的课题。
为此,我们在成功掌握堆焊修复粗轧工作辊的技术基础上,探索、开发了热轧支撑辊的堆焊修复、强化工艺技术。
支撑辊与工作辊直接接触,其主要承受高压力、一定的热应力、疲劳应力及磨损的综合作用,因此,其辊面材质应具有一定的强度、高的疲劳强度、热冲击性能、抗磨损性能。
梅山热轧支撑辊典型规格为:ψ1390mm(辊面直径)×1429mm(辊面长度)×3924mm(总长),重量25444kg/支。
几种梅山热轧支撑辊的化学成分见表1。
热轧支撑辊对堆焊材料的性能要求:(1)较高的硬度60~70HSD,保证其刚度和耐磨性。
(2)高强度,避免断辊。
(3)高疲劳强度,防止网状裂纹和剥落。
(4)良好的热冲击性,防止辊而局部受热产生软点。
(5)良好的焊接性。
据此,我们选择低碳低合金104焊丝配431焊剂作打底层,选择耐磨性较高的Stoody224H焊丝配107焊剂作工作层,堆焊硬面层硬度达67~74HSD,堆焊层成分见表2。
埋弧堆焊电源的型号为ZXG—1000R,自动焊剂烘箱的型号为NZHG6—500内热式鼓风型。
采用自行设计并多次改进的多功能辊体堆焊装置,这是一种适合支撑辊、工作辊等大型辊体堆焊的特种设备(见图1),主要由动力转动装置、支承架、炉体、炉顶工作平台等部分组成。
热轧辊堆焊材料与工艺研究
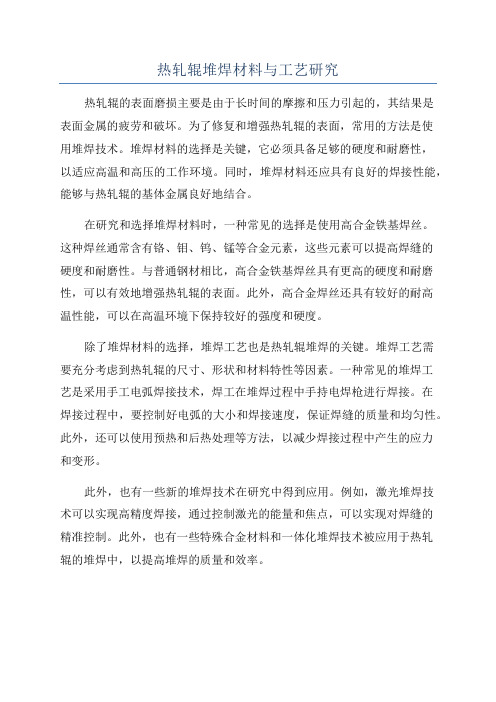
热轧辊堆焊材料与工艺研究
热轧辊的表面磨损主要是由于长时间的摩擦和压力引起的,其结果是
表面金属的疲劳和破坏。
为了修复和增强热轧辊的表面,常用的方法是使
用堆焊技术。
堆焊材料的选择是关键,它必须具备足够的硬度和耐磨性,
以适应高温和高压的工作环境。
同时,堆焊材料还应具有良好的焊接性能,能够与热轧辊的基体金属良好地结合。
在研究和选择堆焊材料时,一种常见的选择是使用高合金铁基焊丝。
这种焊丝通常含有铬、钼、钨、锰等合金元素,这些元素可以提高焊缝的
硬度和耐磨性。
与普通钢材相比,高合金铁基焊丝具有更高的硬度和耐磨性,可以有效地增强热轧辊的表面。
此外,高合金焊丝还具有较好的耐高
温性能,可以在高温环境下保持较好的强度和硬度。
除了堆焊材料的选择,堆焊工艺也是热轧辊堆焊的关键。
堆焊工艺需
要充分考虑到热轧辊的尺寸、形状和材料特性等因素。
一种常见的堆焊工
艺是采用手工电弧焊接技术,焊工在堆焊过程中手持电焊枪进行焊接。
在
焊接过程中,要控制好电弧的大小和焊接速度,保证焊缝的质量和均匀性。
此外,还可以使用预热和后热处理等方法,以减少焊接过程中产生的应力
和变形。
此外,也有一些新的堆焊技术在研究中得到应用。
例如,激光堆焊技
术可以实现高精度焊接,通过控制激光的能量和焦点,可以实现对焊缝的
精准控制。
此外,也有一些特殊合金材料和一体化堆焊技术被应用于热轧
辊的堆焊中,以提高堆焊的质量和效率。
热轧辊堆焊工艺技术

热轧辊堆焊工艺技术热轧辊是用于热轧钢板生产的重要设备之一,其工作环境极为恶劣,长期受到高温高压等多重因素的影响,容易出现磨损、疲劳、断裂等问题,因此,对热轧辊进行修复和保养是非常关键的。
热轧辊的堆焊工艺技术是目前较为常用的修复方法之一。
热轧辊堆焊的目的是在辊面上堆焊一层高硬度的抗磨料,以提高辊面耐磨性能,延长辊筒的使用寿命。
热轧辊堆焊工艺主要包括预处理、堆焊和后处理三个步骤。
首先是预处理。
在进行堆焊前,需要对热轧辊进行彻底的清洗,将辊面上的油脂、氧化物等杂质清除干净,以保证焊接的质量。
其次,对于一些严重磨损或断裂的地方,需要通过铣削或切割等方法将其修整平整,以便于后续的焊接。
然后是堆焊。
选择合适的堆焊材料是非常重要的,通常使用高硬度、高耐磨的合金钢作为抗磨层的材料,可根据实际需要选择不同成分的材料。
堆焊过程中需要注意熔融热的控制,保证焊接层与基体的粘附性和牢固性。
同时,还需注意控制焊接过程中的温度,避免辊面过热或过冷造成的焊接缺陷。
最后是后处理。
堆焊完成后,需要对焊接层进行热处理,以提高焊接层的抗磨性和强度。
热处理的温度和时间需要根据堆焊材料的不同进行合理选择。
热处理结束后,还需对热轧辊进行精细修磨和保养,以消除焊接层表面的不平整和残留应力,确保热轧辊的使用质量和寿命。
需要注意的是,热轧辊堆焊工艺技术虽然能够有效提高热轧辊的使用寿命,但并不能解决所有问题。
有些严重的裂纹或大面积磨损的辊筒可能需要更换,因此,及时的维护和保养仍然是预防和延长热轧辊使用寿命的关键。
总之,热轧辊堆焊工艺技术是一项重要的修复方法,通过选择合适的堆焊材料和控制适当的焊接参数,可以有效提高热轧辊的使用寿命,减少因磨损和断裂引起的生产故障,保证热轧生产线的稳定运行。
同时,定期的维护和保养也是非常重要的,可以进一步延长热轧辊的寿命,提高生产效率。
大型热轧支撑辊堆焊修复技术

热加工
" 焊 接 与 切 割 !! " " #年 第 ! !期 ! !!! "#$ % & ’ !( ) * + , . / 0 1 " 2 (# -
!!!!! !!
ห้องสมุดไป่ตู้
专题技术
! " $ %! & % ’ ( " ) " # * +
!
一 ! 每个大型轧 钢 厂 ! 每 年 都 要 消 耗 大 量 的 该 类 轧 辊 " 由于消耗量大 ! 轧辊 价 格 昂 贵 ! 越 来 越 引 起 技 术 人 员 的 重视 " 轧辊质量的 优 劣 ! 不 仅 直 接 影 响 其 使 用 寿 命 ! 而 且对钢材的质量 # 生 产 率 和 生 产 成 本 都 有 很 大 影 响 " 堆 焊方法修复的复 合 轧 辊 ! 不 但 修 复 成 本 低 ! 而 且 能 提 高 轧辊使用寿命 ! 降低 轧 辊 耗 量 ! 合 理 使 用 并 节 约 合 金 元 素 ! 同时能提高轧机 的 效 益 和 产 品 的 质 量 ! 是 一 种 有 效 的技术经济措施 " 因 此 ! 对 热 轧 板 带 轧 机 支 撑 辊 进 行 堆 焊修复 ! 进一步提高其性能和使用寿命显得十分重要 "
四、堆焊修复工艺
$ % 堆焊材料的选择
% (& 焊丝的选择 ! 针 对 大 型 热 轧 支 撑 辊 的 不 同 材 质 % ## #):+ & " + 9 2 " + 9 9 2 A& 以 及 轧 制 的 特 性 要 )2 求 ! 可选用马氏体不 锈 钢 或 者 耐 磨 性 # 强 韧 性 和 热 稳 定 性好的 + 或+ 9 ] 2 ] A % 9 ] 2 ] 3 ] A ] . H& 低 碳 热 工 具 钢 成 分的埋弧堆焊用药 芯 焊 丝 材 料 进 行 堆 焊 修 复 " 下 表 为 推 荐的堆焊焊丝材料合金成分范围 "
轧辊堆焊埋弧堆焊修复技术

轧辊堆焊埋弧堆焊修复技术随着工业化的发展,轧辊在各种机械设备中扮演着非常重要的角色,它主要用于金属材料的压轧加工,是许多工业生产中不可或缺的部件。
由于轧辊在工作过程中所受到的强大压力和摩擦,导致轧辊表面很容易出现磨损和裂纹等问题,从而影响了轧辊的使用寿命和生产效率。
为了解决这一问题,目前已经出现了多种轧辊修复技术,其中堆焊修复技术和埋弧堆焊修复技术是比较常用且效果较好的方法之一。
轧辊堆焊修复技术是指在轧辊磨损或裂纹部位进行表面堆焊后再经过热处理进行修复,其优点是修复后的轧辊表面硬度、耐磨性和抗裂性能都得到了很好的提高,可以有效延长轧辊的使用寿命。
而埋弧堆焊修复技术则是通过在轧辊磨损或裂纹部位进行埋弧堆焊,然后经过热处理进行修复,也可以达到类似的效果。
对于轧辊堆焊和埋弧堆焊修复技术来说,专业的技术和设备是非常重要的。
需要选择适合的焊接材料和焊接工艺,确保修复后的轧辊表面能够满足工作要求。
需要使用专业的堆焊设备和工具,确保修复过程中的焊接质量和稳定性。
还需要进行合理的热处理工艺,以确保修复后的轧辊表面能够达到理想的硬度和耐磨性能。
除了技术和设备,对于轧辊堆焊和埋弧堆焊修复技术来说,经验丰富的操作人员也是非常重要的。
因为修复过程中需要考虑到轧辊的材料、结构、工作环境等多种因素,需要有一定的经验和技巧才能确保修复效果和修复质量。
在实际应用中,轧辊堆焊和埋弧堆焊修复技术已经得到了广泛的应用,并取得了很好的效果。
通过修复后的轧辊,不仅可以延长轧辊的使用寿命,减少了更换轧辊的频率,也提高了生产效率和产品质量。
这些修复技术也在一定程度上减少了对资源的浪费,降低了生产成本,具有显著的经济和社会效益。
轧辊堆焊和埋弧堆焊修复技术是解决轧辊磨损和裂纹等问题的有效方法,通过选择合适的材料、严格的焊接工艺和合理的热处理工艺,加上经验丰富的操作人员的配合,可以达到较好的修复效果。
相信随着科技的不断发展和完善,轧辊修复技术在未来会有更广泛的应用和更好的发展。
轧辊表面耐磨堆焊工艺技术研究
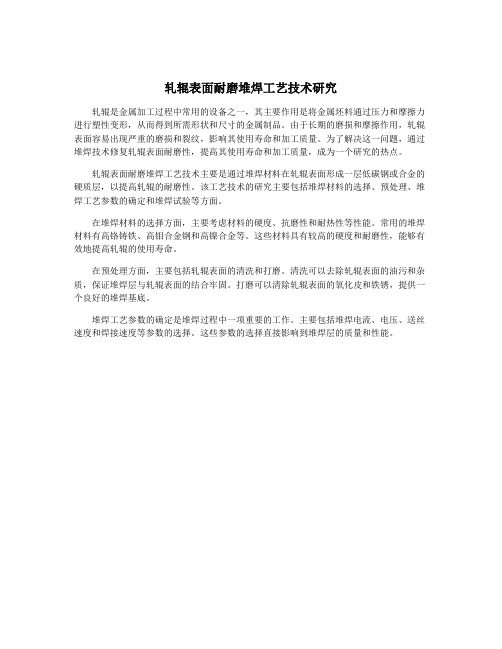
轧辊表面耐磨堆焊工艺技术研究
轧辊是金属加工过程中常用的设备之一,其主要作用是将金属坯料通过压力和摩擦力进行塑性变形,从而得到所需形状和尺寸的金属制品。
由于长期的磨损和摩擦作用,轧辊表面容易出现严重的磨损和裂纹,影响其使用寿命和加工质量。
为了解决这一问题,通过堆焊技术修复轧辊表面耐磨性,提高其使用寿命和加工质量,成为一个研究的热点。
轧辊表面耐磨堆焊工艺技术主要是通过堆焊材料在轧辊表面形成一层低碳钢或合金的硬质层,以提高轧辊的耐磨性。
该工艺技术的研究主要包括堆焊材料的选择、预处理、堆焊工艺参数的确定和堆焊试验等方面。
在堆焊材料的选择方面,主要考虑材料的硬度、抗磨性和耐热性等性能。
常用的堆焊材料有高铬铸铁、高钼合金钢和高镍合金等。
这些材料具有较高的硬度和耐磨性,能够有效地提高轧辊的使用寿命。
在预处理方面,主要包括轧辊表面的清洗和打磨。
清洗可以去除轧辊表面的油污和杂质,保证堆焊层与轧辊表面的结合牢固。
打磨可以清除轧辊表面的氧化皮和铁锈,提供一个良好的堆焊基底。
堆焊工艺参数的确定是堆焊过程中一项重要的工作。
主要包括堆焊电流、电压、送丝速度和焊接速度等参数的选择。
这些参数的选择直接影响到堆焊层的质量和性能。
大型热轧支撑辊堆焊技术

大型热轧支撑辊堆焊修复技术前言众所周知,随着现代化热轧板带轧机向大型化、高速化、自动化方向发展,相应对热轧支撑辊的要求也越来越高。
对于热轧板带轧机使用的大型支撑辊,应能满足如下轧制的特性要求[1]:(1) 具有较高的抗压强度和良好的刚性,足以承受高轧制力和峰值负荷;(2) 具有良好的韧性,以避免断辊、辊身裂纹和表面剥落;(3) 辊身工作层有良好的耐磨损性能和抗疲劳性能,以降低辊耗;(4) 辊身工作层具有均匀的组织和硬度,使得全辊面具有均匀的耐磨损性;(5) 具有良好的耐蚀性,以抵抗热轧过程中高温与润滑或冷却媒介的腐蚀。
基于以上特性要求,由于合金锻钢支撑辊辊身表面硬度可以达到70HSD左右,以及兼有良好的耐磨性和高的机械性能,合金锻钢支撑辊的断裂韧性又优于铸钢支撑辊,因此合金锻钢支撑辊已成为目前热轧板带轧机支撑辊的主要首选。
具有大型热轧支撑辊的热轧板带轧机主要有:宽带钢热连轧机、薄板坯(连铸)连轧机、中厚板轧机、宽厚板轧机等,其热轧支撑辊是各生产线上的重要备品备件之一,每个大型轧钢厂每年都要消耗大量该类轧辊,由于消耗量大,轧辊价格昂贵,越来越引起技术人员的重视。
轧辊质量的优劣,不仅直接影响其使用寿命,而且对钢材的质量、生产率和生产成本都有很大影响。
而采用堆焊方法修复的复合轧辊,不但修复成本低,而且能提高轧辊使用寿命,降低轧辊耗量,合理使用并节约合金元素,同时能够提高轧机的效益和产品的质量,是一种有效的技术经济措施。
因此,对热轧板带轧机支撑辊进行堆焊修复,进一步提高其性能和使用寿命显得十分重要[2~3]。
1 堆焊技术要求对于大型热轧支撑辊,堆焊修复的一般技术要求有:(1) 堆焊层应满足特定的化学成分的要求;(2) 堆焊层应具有适宜的金相组织(包括基体组织和碳化物);(3) 堆焊层要具有较高的抗剥落性能、良好的耐磨损性能和抗疲劳性能;(4) 堆焊层应有足够的厚度(最高可达70~80mm);(5) 堆焊层应有良好的可加工性能;(6) 连续埋弧堆焊作业中,焊材工艺性能优良,焊渣具有良好的脱渣性(指不粘渣、自动脱渣);(7) 具有较高的(堆焊)生产效率,同时要求使用后能多次堆焊修复;(8) 堆焊层经热处理后的硬度及硬度均匀性满足支撑辊技术要求;(9) 堆焊层中不得有裂纹、气孔、夹渣等焊接缺陷。
轧辊堆焊埋弧堆焊修复技术
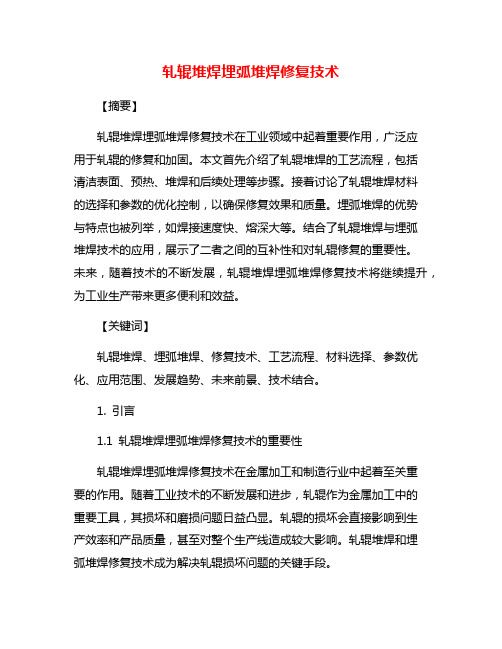
轧辊堆焊埋弧堆焊修复技术【摘要】轧辊堆焊埋弧堆焊修复技术在工业领域中起着重要作用,广泛应用于轧辊的修复和加固。
本文首先介绍了轧辊堆焊的工艺流程,包括清洁表面、预热、堆焊和后续处理等步骤。
接着讨论了轧辊堆焊材料的选择和参数的优化控制,以确保修复效果和质量。
埋弧堆焊的优势与特点也被列举,如焊接速度快、熔深大等。
结合了轧辊堆焊与埋弧堆焊技术的应用,展示了二者之间的互补性和对轧辊修复的重要性。
未来,随着技术的不断发展,轧辊堆焊埋弧堆焊修复技术将继续提升,为工业生产带来更多便利和效益。
【关键词】轧辊堆焊、埋弧堆焊、修复技术、工艺流程、材料选择、参数优化、应用范围、发展趋势、未来前景、技术结合。
1. 引言1.1 轧辊堆焊埋弧堆焊修复技术的重要性轧辊堆焊埋弧堆焊修复技术在金属加工和制造行业中起着至关重要的作用。
随着工业技术的不断发展和进步,轧辊作为金属加工中的重要工具,其损坏和磨损问题日益凸显。
轧辊的损坏会直接影响到生产效率和产品质量,甚至对整个生产线造成较大影响。
轧辊堆焊和埋弧堆焊修复技术成为解决轧辊损坏问题的关键手段。
轧辊堆焊埋弧堆焊修复技术能够有效地修复轧辊表面的裂纹、磨损和变形等问题,延长轧辊的使用寿命,提高生产效率和产品质量。
通过采用合适的堆焊材料和优化的堆焊参数,可以实现轧辊表面的修复和涂覆,使轧辊重新获得理想的工作表面,减少能源消耗和生产成本,提高轧辊的耐磨性和耐腐蚀性。
1.2 轧辊堆焊埋弧堆焊修复技术的应用范围1. 钢铁行业:轧辊是钢铁行业中不可或缺的重要设备,其表面易受磨损和腐蚀的影响。
而轧辊堆焊埋弧堆焊修复技术可以有效地修复和加固轧辊的表面,延长其使用寿命,提高生产效率。
2. 能源行业:在煤矿、电力等领域,轧辊在煤矿输送和发电过程中起着关键作用。
经常受到磨损和冲击的影响,需要进行修复和强化。
轧辊堆焊埋弧堆焊技术可以为其提供良好的修复修理方案。
3. 冶金行业:冶金行业中的轧辊在轧制过程中承受着巨大的压力和摩擦,容易受到磨损和变形。
浅析大型支承辊堆焊修复技术

轧辊是 轧机的易损 部件 。随着钢产 量的增加 ,轧辊 消 耗量 迅速增加 。在众多 可堆 焊修复 的轧 辊 中 ,值 得引起 大
家高 度关注 的是支承辊 。支 承辊和工作 辊一样对 轧制 生产
的稳 定 、板带外 形和表 面质 量产生重要 影响 。因此 ,必须 定期 下线进行 磨削处理 ,同时修整辊形 ,以消 除表面 硬化 层并 恢复辊 面硬度 。当辊径 减小到极 限尺寸后 ,便无 法继 续使用 ;有 的支承辊因局部剥落仅失去少 量工作层而失效 , 如果 直接报废 不但造成 资源浪费 ,也使钢 厂辊耗居高不下 , 生产成本 上升。用堆焊 方法修复支 承辊 至合格 尺寸 ,恢复 使 用性能 ,甚 至超过新 辊的使用寿命 ,无疑 是一件 十分有
端剥落产 生条件首先是 辊 面磨 损 ,并且 由于磨 损导致 辊身 纵截面形成 凸形或 凹形辊 面 ,结果使支 承辊 在这个服
役周 期 内,有一个 较长时 间阶段支承辊不是 整个 辊身与工 作 辊相接 触 ,而仅仅 是辊 面两端端 部 的局 部接 触 。这样 ,
就特别容易引发严重 的辊面两端部位的端剥 落。
4 0
中国 设备工 I o 9 程 21年o月 2
镇 与
碳量不断 降低 的方 向发展 。大致经历三代材料 。 第一 代为高碳 铬钢 ,含碳 量08 % ~ .5 铬量约 . 0 09 %,含
4 支承辊修复实例 . 以湖南华菱涟钢支承辊为例
修 复前 尺寸 为 1 1 .1 mX180 m X53 0 38 r 0 m 3mm,辊 4 a
引发原 因、产生过程及 剥落形式上有 所不 同。显然 ,提 高 辊体材质 质量 、改善辊 形受力情况及 确保轧机处 于 良好的 运行状 态 ,是预 防局部剥落的有效途径 。 3 辊面端剥落 . 端剥落通常被称 之为 “ 掉肩” ,表现形式 是在辊面两端 大块剥落 ,特点是剥 落块的厚度 大约等于辊 身硬化工 作层
轧辊堆焊埋弧堆焊修复技术
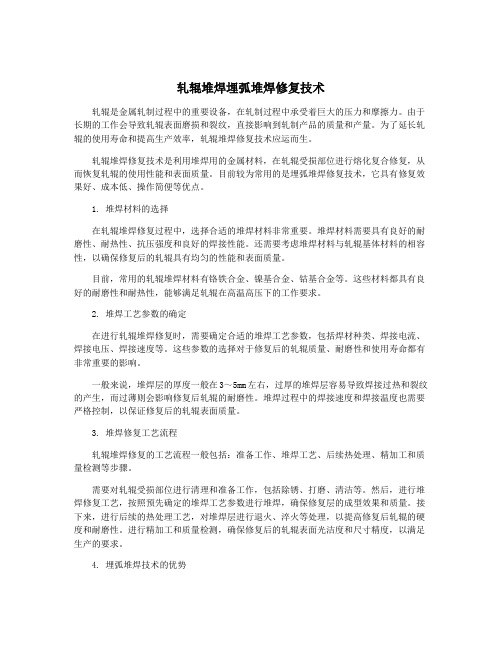
轧辊堆焊埋弧堆焊修复技术轧辊是金属轧制过程中的重要设备,在轧制过程中承受着巨大的压力和摩擦力。
由于长期的工作会导致轧辊表面磨损和裂纹,直接影响到轧制产品的质量和产量。
为了延长轧辊的使用寿命和提高生产效率,轧辊堆焊修复技术应运而生。
轧辊堆焊修复技术是利用堆焊用的金属材料,在轧辊受损部位进行熔化复合修复,从而恢复轧辊的使用性能和表面质量。
目前较为常用的是埋弧堆焊修复技术,它具有修复效果好、成本低、操作简便等优点。
1. 堆焊材料的选择在轧辊堆焊修复过程中,选择合适的堆焊材料非常重要。
堆焊材料需要具有良好的耐磨性、耐热性、抗压强度和良好的焊接性能。
还需要考虑堆焊材料与轧辊基体材料的相容性,以确保修复后的轧辊具有均匀的性能和表面质量。
目前,常用的轧辊堆焊材料有铬铁合金、镍基合金、钴基合金等。
这些材料都具有良好的耐磨性和耐热性,能够满足轧辊在高温高压下的工作要求。
2. 堆焊工艺参数的确定在进行轧辊堆焊修复时,需要确定合适的堆焊工艺参数,包括焊材种类、焊接电流、焊接电压、焊接速度等。
这些参数的选择对于修复后的轧辊质量、耐磨性和使用寿命都有非常重要的影响。
一般来说,堆焊层的厚度一般在3~5mm左右,过厚的堆焊层容易导致焊接过热和裂纹的产生,而过薄则会影响修复后轧辊的耐磨性。
堆焊过程中的焊接速度和焊接温度也需要严格控制,以保证修复后的轧辊表面质量。
3. 堆焊修复工艺流程轧辊堆焊修复的工艺流程一般包括:准备工作、堆焊工艺、后续热处理、精加工和质量检测等步骤。
需要对轧辊受损部位进行清理和准备工作,包括除锈、打磨、清洁等。
然后,进行堆焊修复工艺,按照预先确定的堆焊工艺参数进行堆焊,确保修复层的成型效果和质量。
接下来,进行后续的热处理工艺,对堆焊层进行退火、淬火等处理,以提高修复后轧辊的硬度和耐磨性。
进行精加工和质量检测,确保修复后的轧辊表面光洁度和尺寸精度,以满足生产的要求。
4. 埋弧堆焊技术的优势埋弧堆焊技术是目前轧辊堆焊修复中比较常用的一种技术,它具有以下几个优势:(1)成本低:埋弧堆焊技术所需的设备和材料成本相对较低,能够有效降低修复成本。
轧辊堆焊埋弧堆焊修复技术

轧辊堆焊埋弧堆焊修复技术轧辊堆焊是在工业生产中常见的一种修复技术,它可以帮助轧辊恢复原有的工作性能,延长使用寿命,提高生产效率。
在轧辊的堆焊修复中,埋弧堆焊技术是一种常用的方法,本文将介绍轧辊堆焊埋弧堆焊修复技术的原理、方法和应用。
轧辊在使用过程中,由于受到工作负荷和磨损的影响,会出现表面磨损、开裂、变形等问题,这些问题会直接影响到轧辊的工作性能和使用寿命。
轧辊堆焊修复技术的原理是在轧辊表面添加高硬度、高耐磨损的合金材料,以弥补表面损失,恢复轧辊的初始尺寸和形状,从而提高其使用寿命和工作性能。
埋弧堆焊技术是一种热源较集中的焊接方法,通过在轧辊表面焊接一层厚度不等的合金焊层,使轧辊的表面得到修复,从而延长使用寿命。
具体来说,埋弧堆焊是在焊接区域内使用一根药芯焊条,通过电流加热将焊条熔化,然后利用焊条的内部药芯将合金材料溶解并与轧辊表面材料混合,形成一层均匀、致密的合金焊层。
埋弧堆焊技术具有熔化热源稳定、焊接参数易控制、熔池保护良好等优点,可以保证焊接质量,因此在轧辊堆焊修复中得到了广泛的应用。
1. 准备工作在进行轧辊堆焊埋弧堆焊修复之前,首先需要对轧辊进行全面的表面清理和检查。
清理轧辊表面的铁锈、油污和氧化皮等杂质,保证焊接过程中的熔化材料与轧辊表面材料充分融合。
同时还需要对轧辊进行全面的尺寸测量和缺陷检测,确定需要修复的位置和尺寸。
2. 焊接工艺在确定需要修复的位置后,根据轧辊的不同部位和损坏程度选择合适的焊接工艺参数,包括焊接电流、电压、焊接速度等。
选择合适的焊接参数可以保证焊接熔化材料的均匀性和致密性,从而保证焊接质量。
在进行焊接过程中,需要注意控制焊接过程中的温度、热变形和残余应力,避免对轧辊产生额外的损害。
同时应注意对焊接过程中的熔化材料进行预热和退火处理,以保证焊接质量和硬度。
3. 后续处理完成焊接后,需要对轧辊进行适当的后续处理工艺,包括粗加工和精加工,以确保焊接处的尺寸和形状达到设计要求。
轧辊堆焊埋弧堆焊修复技术

轧辊堆焊埋弧堆焊修复技术轧辊是热轧生产中使用最广泛的工具,其用途是将钢坯或者其他金属材料加工成所需的厚度和形状。
由于工作环境的恶劣和极端的工作条件,轧辊往往容易磨损和损坏。
如果我们不及时处理和修复轧辊磨损和损坏,不仅会影响热轧生产,更会加大生产成本,危害企业的生产效率和经济效益。
因此,如何及时高效地进行轧辊修复和维护是非常必要的。
一般的轧辊维护包括修磨、硬化、堆焊等多个环节,其中堆焊是其中最为常见的一种维护方式。
堆焊是通过将焊接材料填充在轧辊的磨损部位,使轧辊的使用寿命得以延长的一种技术。
常见的堆焊有手工电弧焊、熔覆焊、气体保护焊、埋弧焊等多种方式。
其中,埋弧焊由于其具有高效、高品质的优点而受到越来越多企业和工程师的青眯和认可。
埋弧焊的原理是在对轧辊进行堆焊的时候,采用电弧熔化和熔融金属热效应来将焊接材料与轧辊表面融合成一体。
相比于手工电弧焊,埋弧焊具有更高的焊接效率和更小的热影响。
同时,在使用过程中不会产生大量的气泡和瑕疵等焊接缺陷。
因此使用埋弧焊可以更有效地保护轧辊的表面质量和机械性能,使其具有更长的使用寿命。
埋弧焊在具体操作中,需要注意的问题比较多,下面列出几点:1.安全问题:埋弧焊涉及焊接高温和高压的环节,要注意焊接作业人员的安全和操作规范,以避免意外事故出现。
2.选材问题:选择合适的焊材对焊接质量和轧辊维修效果有着决定性的作用。
3.设备问题:埋弧焊使用的设备很重要,需要选择一些质量好、稳定性高的设备。
4.技术问题:焊接技术也是保证堆焊质量的关键,需要经过专业的技术培训,熟练掌握焊接技能,才能达到较佳的焊接质量和效果。
综上所述,埋弧焊是轧辊堆焊维护中一种高效、高品质的方法,如何合理、有效的使用埋弧焊技术来对轧辊进行维护和修复是每一个企业和工程师需要掌握和熟悉的工作技能。
对于企业来说,这不仅能提高生产效率,减小生产成本,还能保证产品的质量和市场竞争力。
对于工程师而言,这也是一项非常重要的技术,需要通过不断的实践和学习,不断提高自身的技能水平。
热轧支撑辊堆焊修复工艺

热轧支撑辊堆焊修复工艺1、焊前粗加工|将待修复的热轧支撑辊上车床车削,去除疲劳层,见金属光泽,要求单边尺寸大于或等于3mm,对有局部缺陷的部位可进行局部车削或打磨,根部要圆滑过度。
2、探伤经车削加工后的热轧支撑辊,用超声波、磁粉探伤等检验方法检查内部缺陷和表面裂纹情况。
.对内部缺陷较大或表面裂纹较深者,应该报废处理,不作修复,.以免在使用时发生断辊,对表面裂纹较浅的则继续车削,要确保在堆焊前将裂纹清除干净。
3、预热热轧支撑辊焊前的预热作在专用保温罩内进行,加热的升温速度为10--15℃/h,当温度升至300--320℃时恒温15小时。
4、堆焊(直流反接)4.1过渡层A 焊材:方案一:Multpass104+SSF 方案二:Multpass108+HJ260B 焊接电流:380—420A;C 焊接电压:29—35V;D 焊接速度:300—450mm;E干伸长:25-30mm;F 偏心距:30—40mm;G 搭接量:40--60℅;H: 层间温度:300----350℃.注意:打完底后要彻底清除底层焊剂4.2 工作层A.焊材:方案一:Multpass102+HJ107(HRC46—52, 对Cr3而言);方案二:Multpass224H+HJ107(HRC50—55, 对Cr4或Cr5而言);B.焊接电流:400—450AC.焊接电压:30—35VD焊接速度:300—450mmE.干伸长:25--30mmF. 偏心距:30—40 mmG.搭接量:40--60℅H.层间温度:380--470℃I堆焊尺寸:单边尺寸建议为35mmJ.中间热处理:当单边尺寸焊至15mm后进行一次中间热处理,加热速度为15--20℃/h,加热到560±10℃后保温6--8h,然后按规定的冷却速度20℃/h进行冷却到380℃。
5.焊后回火处理热轧支承辊堆焊完后需立即进炉热处理(要求炉子预先按要求做好相应处理),加热速度为15--20℃/h,加热到560±5℃(为工件表面温度)后保温16--20h,然后按冷却速度15--20℃/h进行冷却到80--100℃出炉。
轧辊堆焊技术

轧辊堆焊技术
轧辊堆焊技术是一种用于修复轧辊表面磨损的方法。
它的历史可以追溯到20世纪50年代,当时苏联科学家发明了这种方法。
随着时间的推移,这种技术在世界范围内得到了广泛应用。
轧辊堆焊技术的基本原理是在轧辊表面堆焊一层金属材料,以弥补磨损造成的损失。
这种方法可以延长轧辊的使用寿命,减少生产成本。
堆焊材料的选择要根据轧辊的材质和工作条件来确定。
通常使用的堆焊材料有高铬铸铁、高镍合金、钨钼合金等。
轧辊堆焊技术的具体操作步骤如下:
1. 清洗轧辊表面,去除油污和杂质。
2. 用气焊或电弧焊将堆焊材料焊接在轧辊表面上。
3. 将堆焊层磨平,使其与轧辊表面平齐。
4. 进行热处理,使堆焊层与轧辊表面结合更加牢固。
轧辊堆焊技术的优点是可以在不拆卸轧辊的情况下进行修复,减少停机时间和生产成本。
但是,这种方法也存在一些缺点,如堆焊层与轧辊表面的结合强度可能不够,容易出现剥落等问题。
因此,在使用轧辊堆焊技术时,需要根据具体情况进行评估和选择。
轧辊堆焊技术
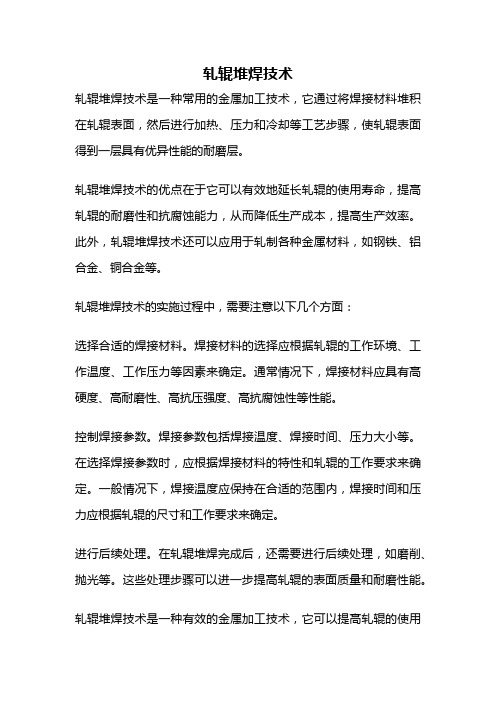
轧辊堆焊技术
轧辊堆焊技术是一种常用的金属加工技术,它通过将焊接材料堆积在轧辊表面,然后进行加热、压力和冷却等工艺步骤,使轧辊表面得到一层具有优异性能的耐磨层。
轧辊堆焊技术的优点在于它可以有效地延长轧辊的使用寿命,提高轧辊的耐磨性和抗腐蚀能力,从而降低生产成本,提高生产效率。
此外,轧辊堆焊技术还可以应用于轧制各种金属材料,如钢铁、铝合金、铜合金等。
轧辊堆焊技术的实施过程中,需要注意以下几个方面:
选择合适的焊接材料。
焊接材料的选择应根据轧辊的工作环境、工作温度、工作压力等因素来确定。
通常情况下,焊接材料应具有高硬度、高耐磨性、高抗压强度、高抗腐蚀性等性能。
控制焊接参数。
焊接参数包括焊接温度、焊接时间、压力大小等。
在选择焊接参数时,应根据焊接材料的特性和轧辊的工作要求来确定。
一般情况下,焊接温度应保持在合适的范围内,焊接时间和压力应根据轧辊的尺寸和工作要求来确定。
进行后续处理。
在轧辊堆焊完成后,还需要进行后续处理,如磨削、抛光等。
这些处理步骤可以进一步提高轧辊的表面质量和耐磨性能。
轧辊堆焊技术是一种有效的金属加工技术,它可以提高轧辊的使用
寿命和生产效率,是轧辊加工过程中不可或缺的一部分。
在实施轧辊堆焊技术时,需要注意以上几个方面,以确保焊接效果和轧辊的使用效果。
轧辊堆焊埋弧堆焊修复技术

轧辊堆焊埋弧堆焊修复技术轧辊是钢铁行业中使用最广泛的辅助设备之一,其主要功能是通过对金属坯料进行压延,以实现金属形状和尺寸的改变。
在使用过程中,轧辊会不可避免地受到高温、高压和严重磨损等影响,因此会出现各种损坏和磨损。
为了延长轧辊的使用寿命和维护设备的正常运转,轧辊堆焊埋弧堆焊修复技术应运而生。
轧辊堆焊埋弧堆焊修复技术是一种通过焊接方法,将适用于轧辊表面磨损或损坏的特殊合金焊丝焊接到轧辊表面,以修复损坏和磨损,提高轧辊的使用寿命的技术。
其主要特点是能够对轧辊进行局部修复,减少了新轧辊的采购成本,延长了轧辊的使用寿命,提高了生产效率,降低了设备维护成本。
1. 减少了设备更换成本:采用轧辊堆焊埋弧堆焊修复技术,能够对轧辊的磨损和损坏进行修复,从而避免了频繁更换轧辊的情况,降低了设备更换的成本。
2. 延长了轧辊的使用寿命:通过修复轧辊表面的磨损和损坏,使其恢复原有的使用状态,延长了轧辊的使用寿命。
3. 提高了生产效率:轧辊堆焊埋弧堆焊修复技术可以缩短轧辊的维修时间,减少了生产停机时间,提高了生产效率。
5. 环保节能:修复轧辊可以减少新轧辊的制造和处理过程中对环境的影响,减少了资源的浪费,符合可持续发展理念。
1. 钢铁冶炼行业:轧辊堆焊埋弧堆焊修复技术可以用于热轧和冷轧生产线上的轧辊修复,延长轧辊的使用寿命。
2. 金属加工行业:各种金属加工设备的轧辊、模具等零部件因受磨损影响而需要进行堆焊修复。
3. 石化行业:石化设备中的轧辊、辊道等零部件也可以采用此技术进行修复。
1. 焊接材料的选择:选择适合轧辊表面磨损和损坏修复的特殊合金焊丝,以确保修复后的轧辊表面性能和使用寿命。
2. 焊接工艺的控制:合理控制焊接电流、电压、焊接速度以及焊接层数,确保对轧辊表面进行均匀覆盖,获得良好的焊接质量。
3. 焊接设备的选择:采用适合轧辊堆焊埋弧堆焊修复的焊接设备,如埋弧焊机、堆焊机等,以确保焊接工艺的稳定和可靠。
4. 焊接人员的培训:进行专业的焊接操作培训,提高焊工的操作技能和质量意识,确保焊接质量。
轧辊堆焊技术

轧辊堆焊技术轧辊堆焊技术是金属加工领域中一种重要的修复与加固方法,通过在轧辊表面堆焊耐磨合金层,可以有效延长轧辊的使用寿命,提高生产效率,降低维护成本,保证生产线的稳定运行。
本文将对轧辊堆焊技术进行详细介绍,包括其原理、工艺流程、应用范围以及优缺点等方面。
一、原理轧辊是金属加工过程中承受巨大压力和磨损的零部件,常常会因磨损而导致表面粗糙、凹凸不平,甚至裂纹等问题,影响生产质量和效率。
轧辊堆焊技术就是利用焊接技术,在轧辊表面堆积一层高硬度、高耐磨性的合金材料,以提高轧辊的耐磨性和使用寿命。
二、工艺流程轧辊堆焊技术的工艺流程主要包括准备工作、清理轧辊表面、选择合适的堆焊材料、堆焊工艺参数的确定、堆焊、后续处理等步骤。
首先,需要对轧辊进行清洗和表面处理,确保堆焊材料能够牢固地附着在轧辊表面。
然后根据轧辊的具体工况和要求,选择合适的堆焊材料,并确定堆焊工艺参数,如焊接电流、电压、送丝速度等。
接下来进行堆焊作业,将合金焊丝逐层堆积在轧辊表面,形成耐磨合金层。
最后进行后续处理,如热处理、机加工等,以确保堆焊层的性能达到要求。
三、应用范围轧辊堆焊技术广泛应用于钢铁、有色金属等行业的热轧、冷轧生产线,以及铝型材、不锈钢板等材料的加工生产中。
通过堆焊技术,可以有效延长轧辊的使用寿命,提高生产效率,减少停机维护时间,降低生产成本,提高产品质量。
四、优缺点轧辊堆焊技术的优点在于可以有效修复和加固轧辊表面,延长使用寿命,提高生产效率;同时可以根据不同需求选择不同的堆焊材料,满足不同的工况要求。
然而,轧辊堆焊技术也存在一些缺点,如堆焊过程中容易产生裂纹、气孔等质量问题,需要严格控制工艺参数和操作技术。
轧辊堆焊技术是一种重要的金属加工修复与加固方法,通过堆焊耐磨合金层,可以有效延长轧辊的使用寿命,提高生产效率,降低维护成本,保证生产线的稳定运行。
在实际应用中,需要严格控制工艺参数,选择合适的堆焊材料,确保堆焊层的质量和性能达到要求。
轧辊堆焊埋弧堆焊修复技术

轧辊堆焊埋弧堆焊修复技术轧辊是轧机的重要零部件,直接影响到轧机的使用效果和生产效率。
在轧辊使用过程中,由于磨损、冲击、热变形等原因,轧辊表面往往会出现裂纹、磨损等损伤,严重影响到轧机的正常运行。
为了解决轧辊表面损伤问题,提高轧辊的使用寿命,轧辊堆焊埋弧堆焊修复技术应运而生。
轧辊堆焊埋弧堆焊修复技术是一种利用焊接技术对轧辊表面损伤进行修复的技术。
通过堆焊和熔融填充的方式,将耐磨、耐腐蚀的合金材料焊接到轧辊表面,从而修复轧辊损伤,延长轧辊的使用寿命。
这项技术在钢铁、有色金属等行业得到了广泛应用,取得了显著的经济效益和社会效益。
轧辊堆焊埋弧堆焊修复技术主要是通过电弧熔化、热喷涂等方法,将具有较高硬度、耐磨性和耐腐蚀性的合金材料堆焊在轧辊损伤部位,形成一层坚固耐磨的保护层,从而修复轧辊损伤,提高轧辊的使用寿命。
具体原理如下:1. 选择合适的合金材料:根据轧辊损伤的类型和工作环境,选择合适的合金材料进行堆焊修复。
通常选择硬质合金、铁基合金等具有高硬度、高耐磨性和耐腐蚀性的合金材料。
2. 准备轧辊表面:在进行堆焊修复前,需要对轧辊表面进行清理、打磨等处理,确保焊接质量和修复效果。
4. 后续处理:对堆焊修复后的轧辊进行表面处理、热处理等工艺,提高合金层的结合力和耐磨性,保证修复效果。
1. 延长轧辊使用寿命:通过堆焊修复技术,可以在轧辊表面形成一层坚固耐磨的保护层,有效修复轧辊损伤,延长轧辊的使用寿命。
2. 提高轧辊使用效率:修复后的轧辊表面光滑坚固,减少了轧机的摩擦阻力,提高了轧辊的使用效率和生产能力。
3. 经济节能环保:相比更换新轧辊,采用堆焊修复技术可以大大降低成本,减少资源浪费,实现了经济、节能、环保的效果。
4. 可广泛应用:轧辊堆焊埋弧堆焊修复技术适用于各种材质的轧辊,可以在钢铁、有色金属等行业得到广泛应用。
5. 技术成熟可靠:轧辊堆焊埋弧堆焊修复技术经过多年的发展和实践,已经日臻成熟,具有较高的可靠性和稳定性。
- 1、下载文档前请自行甄别文档内容的完整性,平台不提供额外的编辑、内容补充、找答案等附加服务。
- 2、"仅部分预览"的文档,不可在线预览部分如存在完整性等问题,可反馈申请退款(可完整预览的文档不适用该条件!)。
- 3、如文档侵犯您的权益,请联系客服反馈,我们会尽快为您处理(人工客服工作时间:9:00-18:30)。
大型热轧支撑辊堆焊修复技术、尸、-前言众所周知,随着现代化热轧板带轧机向大型化、高速化、自动化方向发展,相应对热轧支撑辊的要求也越来越高。
对于热轧板带轧机使用的大型支撑辊,应能满足如下轧制的特性要求[1] :(1) 具有较高的抗压强度和良好的刚性,足以承受高轧制力和峰值负荷;(2) 具有良好的韧性,以避免断辊、辊身裂纹和表面剥落;(3) 辊身工作层有良好的耐磨损性能和抗疲劳性能,以降低辊耗;(4) 辊身工作层具有均匀的组织和硬度,使得全辊面具有均匀的耐磨损性;(5) 具有良好的耐蚀性,以抵抗热轧过程中高温与润滑或冷却媒介的腐蚀。
基于以上特性要求,由于合金锻钢支撑辊辊身表面硬度可以达到70HSD左右,以及兼有良好的耐磨性和高的机械性能,合金锻钢支撑辊的断裂韧性又优于铸钢支撑辊,因此合金锻钢支撑辊已成为目前热轧板带轧机支撑辊的主要首选。
具有大型热轧支撑辊的热轧板带轧机主要有:宽带钢热连轧机、薄板坯(连铸)连轧机、中厚板轧机、宽厚板轧机等,其热轧支撑辊是各生产线上的重要备品备件之一,每个大型轧钢厂每年都要消耗大量该类轧辊,由于消耗量大,轧辊价格昂贵,越来越引起技术人员的重视。
轧辊质量的优劣,不仅直接影响其使用寿命,而且对钢材的质量、生产率和生产成本都有很大影响。
而采用堆焊方法修复的复合轧辊,不但修复成本低,而且能提高轧辊使用寿命,降低轧辊耗量,合理使用并节约合金元素,同时能够提高轧机的效益和产品的质量,是一种有效的技术经济措施。
因此,对热轧板带轧机支撑辊进行堆焊修复,进一步提高其性能和使用寿命显得十分重要[2~3] 。
1 堆焊技术要求对于大型热轧支撑辊,堆焊修复的一般技术要求有:(1) 堆焊层应满足特定的化学成分的要求;(2) 堆焊层应具有适宜的金相组织(包括基体组织和碳化物);(3) 堆焊层要具有较高的抗剥落性能、良好的耐磨损性能和抗疲劳性能;(4) 堆焊层应有足够的厚度(最高可达70~80mm);(5) 堆焊层应有良好的可加工性能;(6) 连续埋弧堆焊作业中,焊材工艺性能优良,焊渣具有良好的脱渣性(指不粘渣、自动脱渣);(7) 具有较高的(堆焊)生产效率,同时要求使用后能多次堆焊修复;(8) 堆焊层经热处理后的硬度及硬度均匀性满足支撑辊技术要求;(9) 堆焊层中不得有裂纹、气孔、夹渣等焊接缺陷。
(10) 堆焊修复后的大型支撑辊,其上机使用寿命不得低于原辊。
2 堆焊专用设备和辅助装置由于大型热轧支撑辊堆焊修复量大,一次堆焊4~7吨焊丝,连续堆焊时间长,这样就对堆焊设备及相应装备提出了较高的性能要求。
堆焊修复大型热轧支撑辊,堆焊专用设备和辅助装置应具备以下设备能力要求:2.1大型轧辊堆焊专用设备要求(1) 工件转动及支撑系统确保支撑辊实现轴向不窜动的稳定匀速旋转运动,并且转速要无级连续可调;(2) 采用单丝多机头(条件允许,至少4个机头)同时施焊,各机头轴向移动应单独控制,并在堆焊作业时,做到同步、稳定、可靠。
机头移动采用交流变频调速,调速范围满足堆焊支撑辊连续螺旋参数要求;(3) 机头的垂直升降,调整过程须平稳,提升高度范围满足堆焊支撑辊参数要求;(4) 由于连续堆焊作业时间长,要求整个堆焊系统各个部分都要保持稳定、可靠,不出任何故障。
2.2大型轧辊堆焊辅助装置要求辅助系统中必须有带自动测温、控温系统的电加热(或燃气加热)保温罩装置,目的是为了确保支撑辊堆焊作业过程中的层间温度技术要求,这一点对于大型支撑辊的堆焊修复尤其重要。
另外为了满足长时间的连续埋弧堆焊作业需求,焊剂自动送给装置也必须配备。
3堆焊修复工艺3.1堆焊材料的选择3.1.1 焊丝的选择针对大型热轧支撑辊的不同材质(50CrMo 70Cr3Mo 3%CrMo”以及轧制的特性要求,可选用马氏体系不锈钢或耐磨性、强韧性和热稳定性好的Cr-Mo-V (或Cr-Mo-W-V-Nb)低碳热工具钢成分的埋弧堆焊用药芯焊丝材料进行堆焊修复。
下表为推荐的堆焊焊丝材料合金成分范围(参考)。
表堆焊材料合金成分范围(质量分数,%C St Mn Cr Mf Mo W V Nb■1。
0.50-0 50-11.50-0.50-100-0.10-0.10-10351.20 1 8014.500 8Q 2 5C 2 900 30030工柞层20.10-0.20roo- 4.50-Qg Q加亠2,00 〜<].304).70 2 00 6.50 1.5C 2.90o.ea 3.S0工忤熹20.2(b 1.50* 1 QQ'0.4Q-0.200.70 2.502E0A0 08-020-0.80-0.50-040-0.20-0.120.60 1 20 1 DO 1 300 4C辛I底.层由于大型热轧支撑辊母材的含碳量或合金含量过高,为确保母材和堆焊金属之间的良好冶金结合,即保证二者具有强韧性俱佳的结合性能,推荐在工作层材料堆焊前,先使用低碳抗压强度较高的焊丝材料进行过渡层堆焊。
为进一步降低母材和堆焊层界面的脆化以避免支撑辊使用过程中产生局部剥落,在过渡层材料堆焊前,可先实施打底层材料的堆焊。
为满足大型热轧支撑辊的轧制特性要求以及堆焊技术要求,辊身工作层堆焊金属基体组织设计为强度高、相对韧性好的单一低碳回火马氏体,同时在基体上分布着均匀细小的弥散合金碳化物。
由于针对原辊使用中发生的辊面局部剥落情况,经微观断口组织分析,造成的原因大多为片状或长条状的非金属夹杂物,因此,这里特别强调,要对焊丝材料的纯度提出较高的要求,即尽可能降低S、P、H以及有害的非金属夹杂物(硫化物、硅酸盐、氧化物等)含量。
焊丝规格为:①4.0m m或①5.0mm3.1.2 焊剂选用国产经专门研制生产的碱性烧结焊剂。
碱性烧结焊剂的渣系为:MgO-AI2O3-CaF2-SiO2 碱度BIIW约为:1.8,化学活性系数Af 为:0.15。
选用原因:(1) 提高焊剂碱度可以降低焊缝金属的含氧量和含硫量,提高其韧性和抗裂能力;(2) 为解决高温脱渣问题,应降低焊剂的化学活性(熔炼焊剂HJ260的化学活性系数Af-0.46 )并加强脱氧。
应用实践表明:选用的国产碱性烧结焊剂比HJ260 HJ108 SJ301等焊剂具有更优良的工艺性能,尤其是具有优良的高温脱渣性能,完全能满足大型热轧支撑辊的堆焊要求。
3.2堆焊修复工艺方案采用下述工艺流程对大型热轧支撑辊进行堆焊修复:图1大型热轧支撑辊堆焊修复工艺流程图3.2.1 堆焊用辊坯整备堆焊修复前,对旧辊辊坯进行疲劳层车削、超声和磁粉(或渗透)探伤、局部缺陷焊补、保证堆焊工作层厚度车削的整备工作。
(1) 辊颈探伤在辊面加工前,对辊颈进行超声波和渗透探伤,若发现有严重缺陷(特别是辊身与辊颈过渡区内),则终止对该辊的后道加工。
(2) 辊面车削加工将辊面疲劳层完全去除,并车削至保证堆焊层厚度要求。
(3) 局部缺陷焊补对于局部缺陷,首先要确保缺陷完全清除,车削较深之处,可采用打底和过渡层焊材进行焊补,使之平整。
(4) 辊面探伤对已车削辊面进行检测,检查疲劳层是否车削净及辊身是否存在裂纹等缺陷,若仍有缺陷,则需继续车削,消除隐患。
如果超声探伤出辊坯有严重内伤,则不允许再进行该辊坯的堆焊修复工作。
3.2.2 焊前准备工作辊坯预热前,要在辊身的两端装上挡环。
挡环为焊接式(一次性),用薄钢板(厚度 > 6mm 制成,并环向对接点焊在辊身两端。
挡环的作用是托住焊剂,防止在堆焊时发生熔渣流淌,从而保证在辊身两端得到良好的堆焊层形状。
323 预热预热的主要目的是降低堆焊过程中堆焊金属及热影响区的冷却速度,降低淬硬倾向并减少焊接应力,防止母材和堆焊金属在堆焊过程中发生相变导致裂纹产生。
预热温度的确定需依据母材以及堆焊材料的碳含量和合金含量而定,参考经验公式:T^F) =1020-63a.%C) - 72(%Mh)-63(%^ )-36(%Z)-36(%Cr)一】十2 7' %Co) + 54< %Al)其中,堆焊过程中应控制预热及层间温度高于Ms点,避免堆焊金属发生马氏体相变及淬回火效应,使整个堆焊层焊完之后在热处理电炉中同时进行马氏体转变,只有这样才能保证堆焊层的组织、硬度均匀性。
由于大型热轧支撑辊母材及堆焊材料的合金含量均相对偏高,再加之支撑辊的尺寸及堆焊厚度均较大,焊接应力大,故应尽量提高预热和层间温度,又考虑到实际操作上容许程度,将预热温度确定为400~450C,焊道层间温度控制在350C以上。
在预热过程中要求:预热升温速度w 25C/h ;预热保温时间根据支撑辊外径尺寸大小来确定(原则是确保辊坯从外到里热透)。
3.2.4 保温堆焊作业(1) 施焊前,选用焊丝和配用烧结焊剂分别按其要求进行烘焙,以去除水份。
(2) 使用具有下降电源特性的直流电源,配备带自动测温、控温系统的电加热(或燃气加热)保温罩装置和焊剂自动送给装置,在大型轧辊自动埋弧堆焊专用设备上,进行多机头单丝圆周方向连续螺旋自动埋弧堆焊。
(3) 堆焊过程必须连续施焊,中途不允许停止。
如遇意外情况停焊时,在层间温度保温装置不能保证支撑辊层间温度时,应尽快进炉按预热温度要求保温。
(4) 进行圆周方向螺旋线堆焊时,为防止在辊身两端出现“缺肉”现象,在辊身的两端,即始焊部位和终焊部位,均应先沿圆周方向堆焊一周(即在不移动堆焊机头的情况下堆焊一周),然后再进行螺旋线堆焊。
同时为保证各堆焊层间硬度的均匀性,要求堆焊时应使各堆焊层间的焊道位置相互错开1/2焊道宽度。
(5) 对于①4.0mm药芯焊丝,要求:焊接电流:400~450A焊接电压:27~32V焊接速度:400~500mm/mi n(指轧辊堆焊层转动圆周线速度)焊道搭接:相邻焊道搭接须大于50%具体搭接量应视焊道平整光滑情况。
焊接极性:采用直流反接。
电源特性:采用具有弧压反馈的下降特性。
焊弧导前距离:取决于轧辊直径。
一般在12.7~50.8m m范围内,具体导前距离视焊道成形情况。
焊丝伸出长度:25~35mm焊道层间温度:350~400C3.2.5 中间去应力热处理由于大型热轧支撑辊的堆焊厚度较大(最厚达70~80mm,如果一次连续堆焊完成,将使得堆焊金属产生非常大的焊接累积应力(尽管始终保持在较高的预热和层间温度下),该累积应力的存在,将大大增加堆焊辊产生裂纹的倾向,严重时将发生支撑辊开裂的严重事故。
因此在堆焊厚度到一定范围时,须进行中间去应力热处理,以降低或消除焊接累积应力。
稳妥的措施是在堆焊20~30mn后,进行一次中间去应力热处理。
去应力热处理温度要求控制在480~500C,时间则由堆焊厚度来确定。
3.2.6焊后热处理焊后热处理的主要目的是为改善焊后组织和消除焊接应力。
堆焊修复支撑辊的焊后热处理应在专用的热处理电炉中进行,要求炉内温度均匀性好,温度测定准确,控温过程精确。