JCOE工艺流程图及说明
施工工艺流程图大全
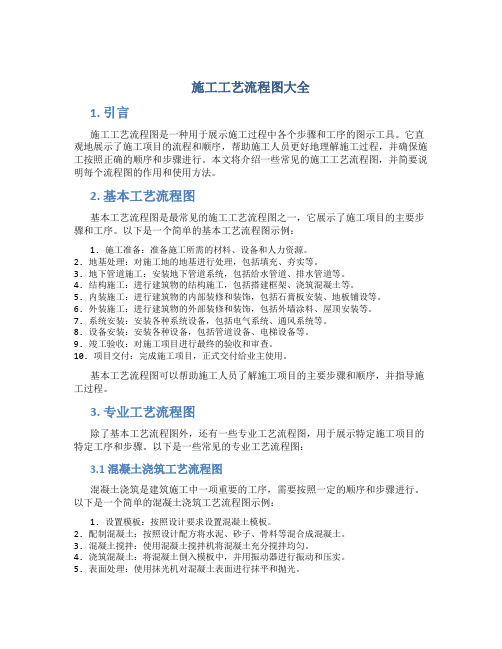
施工工艺流程图大全1. 引言施工工艺流程图是一种用于展示施工过程中各个步骤和工序的图示工具。
它直观地展示了施工项目的流程和顺序,帮助施工人员更好地理解施工过程,并确保施工按照正确的顺序和步骤进行。
本文将介绍一些常见的施工工艺流程图,并简要说明每个流程图的作用和使用方法。
2. 基本工艺流程图基本工艺流程图是最常见的施工工艺流程图之一,它展示了施工项目的主要步骤和工序。
以下是一个简单的基本工艺流程图示例:1. 施工准备:准备施工所需的材料、设备和人力资源。
2. 地基处理:对施工地的地基进行处理,包括填充、夯实等。
3. 地下管道施工:安装地下管道系统,包括给水管道、排水管道等。
4. 结构施工:进行建筑物的结构施工,包括搭建框架、浇筑混凝土等。
5. 内装施工:进行建筑物的内部装修和装饰,包括石膏板安装、地板铺设等。
6. 外装施工:进行建筑物的外部装修和装饰,包括外墙涂料、屋顶安装等。
7. 系统安装:安装各种系统设备,包括电气系统、通风系统等。
8. 设备安装:安装各种设备,包括管道设备、电梯设备等。
9. 竣工验收:对施工项目进行最终的验收和审查。
10. 项目交付:完成施工项目,正式交付给业主使用。
基本工艺流程图可以帮助施工人员了解施工项目的主要步骤和顺序,并指导施工过程。
3. 专业工艺流程图除了基本工艺流程图外,还有一些专业工艺流程图,用于展示特定施工项目的特定工序和步骤。
以下是一些常见的专业工艺流程图:3.1 混凝土浇筑工艺流程图混凝土浇筑是建筑施工中一项重要的工序,需要按照一定的顺序和步骤进行。
以下是一个简单的混凝土浇筑工艺流程图示例:1. 设置模板:按照设计要求设置混凝土模板。
2. 配制混凝土:按照设计配方将水泥、砂子、骨料等混合成混凝土。
3. 混凝土搅拌:使用混凝土搅拌机将混凝土充分搅拌均匀。
4. 浇筑混凝土:将混凝土倒入模板中,并用振动器进行振动和压实。
5. 表面处理:使用抹光机对混凝土表面进行抹平和抛光。
工艺流程图和
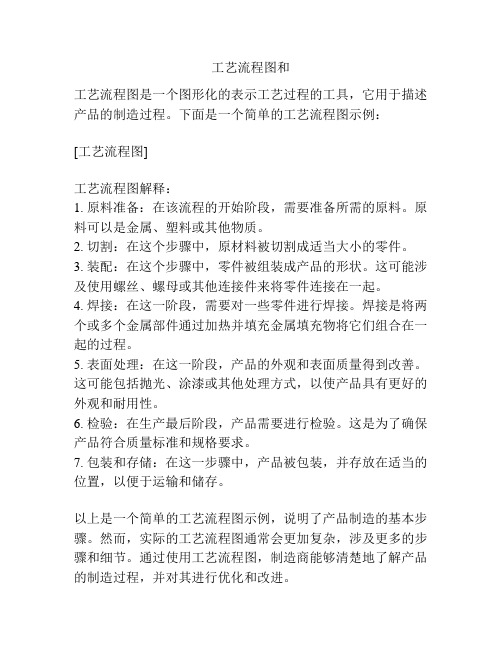
工艺流程图和工艺流程图是一个图形化的表示工艺过程的工具,它用于描述产品的制造过程。
下面是一个简单的工艺流程图示例:[工艺流程图]工艺流程图解释:1. 原料准备:在该流程的开始阶段,需要准备所需的原料。
原料可以是金属、塑料或其他物质。
2. 切割:在这个步骤中,原材料被切割成适当大小的零件。
3. 装配:在这个步骤中,零件被组装成产品的形状。
这可能涉及使用螺丝、螺母或其他连接件来将零件连接在一起。
4. 焊接:在这一阶段,需要对一些零件进行焊接。
焊接是将两个或多个金属部件通过加热并填充金属填充物将它们组合在一起的过程。
5. 表面处理:在这一阶段,产品的外观和表面质量得到改善。
这可能包括抛光、涂漆或其他处理方式,以使产品具有更好的外观和耐用性。
6. 检验:在生产最后阶段,产品需要进行检验。
这是为了确保产品符合质量标准和规格要求。
7. 包装和存储:在这一步骤中,产品被包装,并存放在适当的位置,以便于运输和储存。
以上是一个简单的工艺流程图示例,说明了产品制造的基本步骤。
然而,实际的工艺流程图通常会更加复杂,涉及更多的步骤和细节。
通过使用工艺流程图,制造商能够清楚地了解产品的制造过程,并对其进行优化和改进。
以下是关于工艺流程图的700字的文章:工艺流程图对于制造业来说是至关重要的工具,它能够以图形化的方式表示产品的制造过程。
通过工艺流程图,制造商可以更清楚地了解产品的制造过程,从而找到遇到的问题并进行优化。
下面我们将详细介绍工艺流程图的作用和使用方法。
工艺流程图主要用于描述产品的制造过程。
它包括了从原料准备、加工、装配到成品检验的各个步骤。
通过工艺流程图,制造商可以清楚地了解到每个步骤的具体要求,从而更好地组织生产活动。
工艺流程图中的每个步骤都通过箭头和图形表示,以指示步骤的顺序和流向。
每个步骤都具有特定的符号,例如矩形表示操作步骤,钻孔或切割表示物料的处理步骤,以及菱形表示判断步骤。
这些符号有助于创造一个清晰明了的图形化表示,使制造商能够更容易地掌握和理解产品制造的过程。
工艺流程图标

工艺流程图标工艺流程图是通过图形符号和文字说明展示产品生产过程的一种图形展示方法。
它可以清晰地展示各个环节之间的关系和步骤,帮助人们更好地理解和掌握生产工艺。
下面是一个标准的工艺流程图标:1. 设计:首先,产品的设计部门会根据市场需求和客户的要求设计产品的外观和功能。
设计人员会使用CAD软件进行3D建模和绘图,确定产品的尺寸和结构。
2. 原料采购:在确定好产品的设计方案后,采购部门会根据生产需求确定所需的原材料。
他们会与供应商联系,购买合适的原材料,并确保原材料的质量合格。
3. 材料准备:原材料进入生产车间后,需要进行材料准备工作。
这包括切割、清洗、烘干等操作,以确保原材料的质量和适用性。
4. 加工制造:在材料准备完成后,制造部门会根据产品的设计图纸进行加工制造。
这可能包括焊接、钻孔、切割、铣削等工艺。
制造过程中需要注意生产工艺的控制和质量的把控。
5. 组装:在加工制造完成后,产品需要进行组装。
组装部门会根据产品的装配图纸,将各个零部件组装成完整的产品。
组装过程需要仔细检查每个零部件的质量和安装位置,确保产品的功能和外观达到要求。
6. 检验:组装完成后,产品将会进行质量检验。
质检部门会根据产品标准和要求对产品进行严格的检测,检查产品的尺寸、结构、功能和外观等。
只有经过检验合格的产品才能进行后续的包装和出货。
7. 包装:质检合格的产品将会进行包装。
包装部门会根据产品的尺寸和性质,选择合适的包装材料和包装方法,确保产品在运输过程中不受损坏。
8. 成品入库:最后,包装完成的产品将会入库。
入库部门会对产品进行分类、编号和储存,确保产品的信息和库存量得到准确的记录。
总结:工艺流程图标可以帮助人们更好的了解产品的生产过程。
通过清晰明了的图形和文字描述,人们可以清楚地了解产品的设计、原材料采购、加工制造、组装、检验、包装和入库等各个环节。
工艺流程图标的制作需要考虑清晰易懂、一目了然的原则,使人们能够轻松理解和掌握生产工艺。
建筑工程施工总体工艺流程图

建筑工程施工总体工艺流程图引言建筑工程施工是一项复杂的系统工程,涉及到多个专业领域和环节。
为了更好地管理和控制施工过程,了解建筑工程施工的总体工艺流程图是非常必要的。
本文将详细介绍建筑工程施工的总体工艺流程,包括施工前的准备、施工过程、设备使用、质量控制和验收等环节。
施工前的准备在施工前,需要做好一系列的准备工作,包括设计规划、施工组织、施工现场布置等。
设计规划是建筑工程施工的首要环节,需要根据工程要求和实际情况,制定合理的施工方案和设计图纸。
施工组织则是在设计规划的基础上,合理配置人力、物力、财力等资源,制定科学的施工计划和进度安排。
施工现场布置包括搭建临时设施、布置安全防护设施、划分施工区域等,以确保施工过程的顺利进行。
施工过程建筑工程施工过程包括多个环节,如基础工程、主体结构工程、水电安装工程、装饰装修工程等。
基础工程是建筑工程施工的基础,包括地基处理、基础浇筑、地基防水等环节。
主体结构工程是建筑工程施工的核心,包括墙体、梁、柱等结构部分的施工。
水电安装工程包括水、电、暖等系统的安装。
装饰装修工程则是根据设计要求,对建筑内部和外部进行装修和装饰。
在施工过程中,需要注意以下几点:1、严格按照设计图纸和施工规范进行施工,确保施工质量符合要求。
2、加强施工现场的安全管理,做好安全防范措施,防止安全事故的发生。
3、合理安排施工进度,确保施工进度符合计划要求。
4、做好施工现场的环境保护工作,减少施工对环境的影响。
设备使用在建筑工程施工过程中,需要使用各种机械设备,如挖掘机、装载机、起重机等。
这些机械设备的使用必须符合安全操作规程,确保施工安全。
此外,还需要根据工程需要,合理选择和配置相应的设备,以提高施工效率和质量。
质量控制建筑工程施工的质量控制是整个施工过程中非常重要的环节。
通过质量控制,可以确保施工质量符合要求,保证建筑物的安全性和稳定性。
质量控制应该贯穿整个施工过程,包括原材料的采购、加工制造、施工安装等环节。
JCOE钢管成型工艺

JCOE制造技术是上世纪90年代发展起来的一种焊管成型工艺,该工艺的主要成型过程是先将钢板铣边(或刨边)后经纵边预弯,再按J型-C型-O型的顺序成型,每一步冲压均以三点弯曲为基本原理。
由于是多道次渐进压制成型,所以必须解决如下一些问题:如何确定模具形状、上模冲程和下模间距,以及需要多少道次才能保证冲压出最合适的弯曲半径和最佳的开口毛圆管坯。
而这些问题又与钢板材质、不同钢板生产厂的具体力学特性、钢管规格(直径和壁厚)有关,因而非常复杂。
目前主要靠“试错法”,即每当更换新规格或新钢种,就取一定数量的小样进行试压,摸索出合适的冲压量。
试错法比较可靠,但是效率比较低。
由于工艺参数较多,仅通过试错法就相当麻烦。
为了获得一套成熟的工艺,甚至需要几个月的试错过程。
螺旋管螺旋管特点:直缝焊管生产工艺简单,生产效率高,成本低,发展较快。
螺旋焊管的强度一般比直缝焊管高,能用较窄的坯料生产管径较大的焊管,还可以用同样宽度的坯料生产管径不同的焊管。
但是与相同长度的直缝管相比,焊缝长度增加30~100%,而且生产速度较低。
因此,较小口径的焊管大都采用直缝焊,大口径焊管则大多采用螺旋焊。
螺旋管及其标准分类:承压流体输送用螺旋缝埋弧焊钢管(SY5036-83 )主要用于输送石油、天然气的管线;承压流体输送用螺旋缝高频焊钢管(SY5038-83),用高频搭接焊法焊接的,用于承压流体输送的螺旋缝高频焊钢管。
钢管承压能力强,塑性好,便于焊接和加工成型;一般低压流体输送用螺旋缝埋弧焊钢管(SY5037-83),采用双面自动埋弧焊或单面焊法制成的用于水、煤气、空气和蒸汽等一般低压流体输送用埋弧焊钢管。
标准现在螺旋管的常用标准一般分为:SY/T5037-2000 (部标、也叫普通流体输送管道用螺旋缝埋弧焊钢管)、GB/T9711.1-1997 (国标、也叫石油天然气工业输送钢管交货技术条件第一部分:A级钢管(到目前要求严格的有GB/T9711.2 B级钢管))、API-5L (美国石油协会、也叫管线钢管;其中分为PSL1和PSL2两个级别)、SY/T5040-92 (桩用螺旋缝埋弧焊钢管)材质螺旋管材质:Q235A Q23b,0Cr13、1Cr17、00Cr19Ni11、1Cr18Ni9、0Cr18Ni11Nb. Q345 L245 L290 X42 X46 X70 X80 X95直缝钢管高频直缝焊管直缝钢管是焊缝与钢管纵向平行的钢管。
建筑工程施工工艺流程图资料
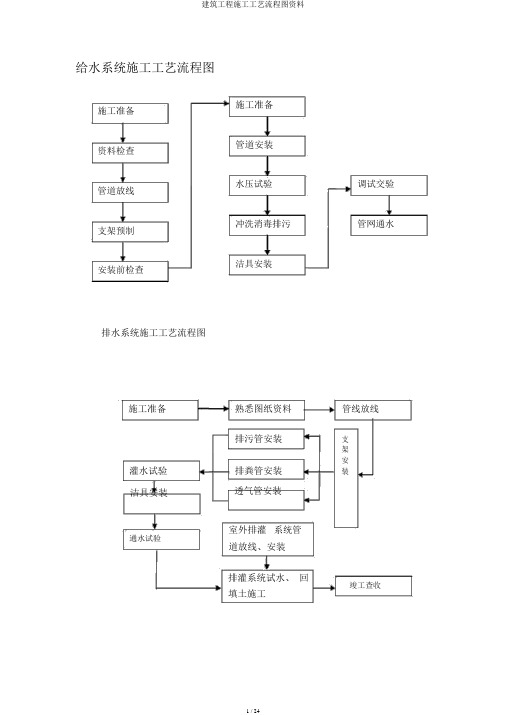
给水系统施工工艺流程图施工准备资料检查管道放线支架预制施工准备管道安装水压试验调试交验冲洗消毒排污管网通水安装前检查洁具安装排水系统施工工艺流程图施工准备熟悉图纸资料管线放线排污管安装支架排粪管安装安灌水试验装洁具安装透气管安装室外排灌系统管通水试验道放线、安装排灌系统试水、回竣工查收填土施工电气安装工程主要工艺流程配合土建专业预埋防雷和接地系统安装电管敷设、箱盒安装插接式母线槽安装桥架安装电管敷设、箱盒安装桥架安装电管敷设、箱盒安装插接式母线槽安装插接式母线槽安装插接式母线槽安装插接式母线槽安装插接式母线槽安装桥架安装插接式母线槽安装土建基础工程主要工艺流程:施工准备测量放线场所平展土方分派桩基工程基坑支护降水土方工程桩基静载测试基础垫层桩基动载测试桩基查收基础工程地下防水基础查收回填土土建主体工程主要工艺流程(混凝土结构):施工准备模板安装工程管线预埋及预留脚手架搭设钢筋安装工程混凝土工程模板拆掉工程管线预埋填充墙工程门窗框安装主体查收施工准备基层办理找规矩、基准线外墙找平层屋面找平层内墙找平层外墙保温屋面保温内墙抹灰外墙饰面层屋面防水层内墙饰面层外脚手架拆掉楼地面工程室外工程门窗扇安装器具安装油漆玻璃分部工程查收施工准备路基挖填土地基办理路基压实垫层砂砾垫层碎石垫层基层粉煤灰三渣二灰土水泥或沥青牢固石人行道侧平石面层人行道面层水泥混凝土面层沥青混凝土面层查收施工准备井点降水沟槽开挖沟槽支护窨井砌筑管道基础管道铺设管道接口磅水查验管道坞膀隶属修建物隐蔽查收沟槽复土百度一下您盘问的要点词是:市办公产开发流程。
若是打开速度慢,能够试一试快速版;若是想保存快照,能够增加到搜藏;若是想更新或删除快照,能够投诉快照。
(百度和网页的作者没关,不对其内容负责。
百度快照谨为网络故障时之索引,不代表被找寻网站的即时页面。
)房地产开发流程房地产开发活动的复杂化使得越来越多的专业人士开始与开发商共同工作,从而加速了房地产开发专业队伍的发展壮大。
JCOE工艺流程图及说明

JCOE工艺流程图及说明JCOE直缝焊管生产线工艺流程图JCOE直缝焊管生产线工艺流程说明1、钢板准备:将准备生产的钢管所需钢板按顺序堆放好,提前做好产前准备。
并放好相应的原材料标识牌。
2、钢板吊运、标志:正式投产时将相应规格钢板按炉号、批号上料,吊运到横向上料台架上,对钢板表面质量进行检查,并在钢板两端用记号笔填写钢管管号及区分A、B端标识。
3、引熄弧板制作:根据生产订单钢管规格提前制作相应的引熄弧板。
4、焊接引熄弧板:钢板吊运到横向待料台架(长短辊)上后,在钢板的四个角焊接引熄弧板,引熄弧板要焊正焊牢。
5、钢板表面除锈:用负压风除掉钢板表面浮锈及氧化皮等。
6、钢板超声波探伤检查:对钢板及板边进行超声波检测,检查钢板是否存在分层、夹渣、裂纹等质量缺陷。
7、钢板铣边:通过数控铣边机的加工将钢板铣削到成型所需要的板宽;同时按焊接工艺需要的坡口角度及钝边尺寸对钢板两边进行加工。
8、板边除锈、板面清扫:将铣边后的钢板坡口两侧50mm内浮锈除掉,提高焊接合格率;清扫板面铣边残留的铁屑,防止残留铁屑在预弯和成型时被压入管体内。
9、钢板预弯:预弯机将钢板分段进行板边预弯,使其板边达到所要求的曲率半径(圆弧)。
10、JCO成型:成型机通过上下模具对预弯边后的钢板一半进行多次步进压制,将钢板压成横卧的“J”形,再将钢板的另一半通过同样工序压成横卧的“C”形管坯,最后在“C”形管坯中间进行压制,形成开口的“O”形管筒。
11、钢管预焊:预焊机使成型后的管筒合缝并采用Ar+CO2气体保护焊进行连续焊接,开口的管坯合缝状态,将直接影响钢管内、外焊接的质量。
12、预焊后清飞溅:将钢管预焊时飞溅在坡口两侧的飞溅物清除干净。
13、预焊质量检查:检查预焊后的管子焊缝是否有断弧、漏焊、焊接不均匀、气孔等缺陷。
14、预焊焊缝修补:对预焊质量检查岗位检查出来焊缝有缺陷的钢管进行手工修补。
15、钢管标志:在钢管外表面用记号笔写管号。
16、预焊缝清理:对成型过程中钢管内部残留的氧化皮、锈蚀等进行清理,尤其预焊缝坡口内的杂物要清理干净。
化工工艺流程图ppt课件
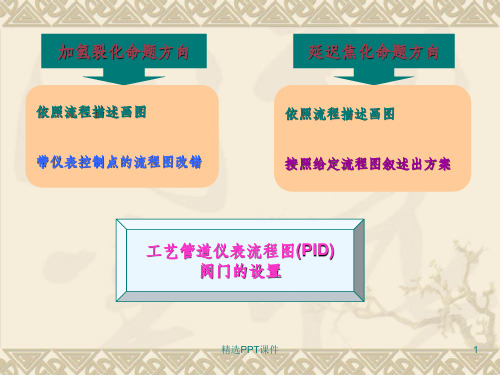
精选PPT课件
13
通过工艺管道及仪表流程图可以了解:
(1)设备的数量、名称和位号。 (2)主要物料的工艺流程。 (3)其他物料的工艺流程。 (4)通过对阀门及控制点分析,了解生产过程
加氢裂化命题方向
依照流程描述画图 带仪表控制点的流程图改错
延迟焦化命题方向
依照流程描述画图 按照给定流程图叙述出方案
工艺管道仪表流程图(PID) 阀门的设置
精选PPT课件
1
化工工艺流程图
精选PPT课件
2
化工工艺流程图
化工工艺流程图是化工工艺图中工艺流 程性质的图样,它是用来表达工03/A-F
TC
原 料-蜡 油 回 流 换 热 器
3102
E-3102/A-F 原 料 -蜡 油 换 热 器
E -3 1 0 1/A -H 原 料 -柴 油 换 热 器
接 C-102底 液 控 原 料 油 去 分 馏 塔 底
蜡 油 自 P-3108来
蜡油回流去分馏塔 蜡油去 E3106
蜡 油 自 P3107来 柴 油 去 E-3105 柴 油 自 P-3105来
P -3 1 0 1/A .B 原料油泵
精选PPT课件
审核
设计
100万 吨 /年 延 迟 焦 化
绘图
东 方 仿 真 22
3.阀门等管件的表示方法 管道上的阀门及其他管件应用细实线按标
准所规定的符号在相应处画出,并标注其规 格代号。
8
工艺原则流程图通常采用按工艺流程顺序, 自左至右展开图的形式表示,设备以示意 的图形或符号表示(表7-2),并用细实线 画出,流程图中的主要物料流程的流程线 用粗实线表示,流程方向用箭头画在流程 线上。
化工工艺流程图详解
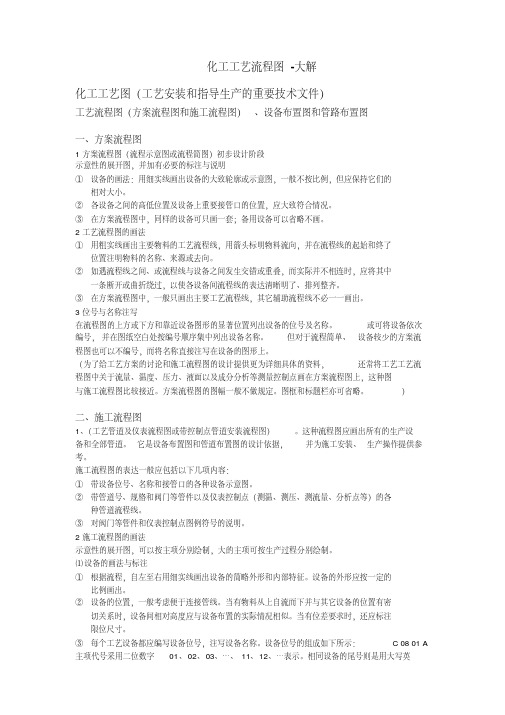
等。 ① 设备的标注
ⅰ尺寸标注 设备布置图中只注定位尺寸(设备与设备、设备与建筑物之间)
。
平面定位尺寸是用建筑定位轴线做基准,确定设备中心线或设备支座孔中心线的距离。
尺寸基准的选取原则为: 卧式容器定位以容器的中心线和靠近柱轴线一端的支座为基准,
如
图。立式反应器、塔,槽、罐和换热器以中心线为基准,如图。卧式换热器以换热器的中心
1/2 ″、 4″、 12″、…。英制加厚管道应在公称直径后加注“×
S”,如 4″× S。
③ 管道等级 在管道等级与材料选用表尚未实施前,标注公制管道直径时必须标注外径×
厚度,如: PG0801-50× 2.5 。
④ 隔热(或隔音)代号 有隔热或隔音措施的管道。还要在管道等级号之后加注隔热(或
隔音)的代号。代号的编法可查阅“ 隔热及隔音的代号 ”设计规定( CD41 A7-81)。
线和靠近柱轴线一端的支座为基准, 如图。板式换热器以中心线和某一出口法兰端面为基准,
泵以中心线和出口法兰中心线为基准, 如图。 压缩机以制造厂的基准线和出口法兰中心线为
基准,如图。往复式泵和压缩机以中心线和管口法兰的中心线以及端面为基准。
高度方向的定位尺寸, 一般选择厂房室内地面为基准, 确定设备基础面或设备中心线的
相对大小。 ② 各设备之间的高低位置及设备上重要接管口的位置,应大致符合情况。
③ 在方案流程图中,同样的设备可只画一套;备用设备可以省略不画。
2 工艺流程图的画法 ① 用粗实线画出主要物料的工艺流程线,用箭头标明物料流向,并在流程线的起始和终了
位置注明物料的名称、来源或去向。
② 如遇流程线之间、或流程线与设备之间发生交错或重叠,而实际并不相连时,应将其中
工艺流程图识图基础知识

工艺流程图识图基础知识工艺流程图是工艺设计的关键文件,同时也是生产过程中的指导工具.而在这里我们要讲的只是其在运用于生产实际中大家应了解的基础知识(涉及化工工艺流程设计的内容有兴趣的师傅可以找些资料来看).它以形象的图形、符号、代号,表示出工艺过程选用的化工设备、管路、附件和仪表等的排列及连接,借以表达在一个化工生产中物量和能量的变化过程。
流程图是管道、仪表、设备设计和装置布置专业的设计基础,也是操作运行及检修的指南。
在生产实际中我们经常能见到的表述流程的工艺图纸一般只有两种,也就是大家所知道的PFD和P&ID.PFD实际上是英文单词的词头缩写,全称为Process Flow Diagram,翻译议成中文就是“工艺流程图”的意思。
而P&ID也是英文单词的词头缩写,全称为Piping and Instrumentation Diagram,“&”在英语中表示and。
整句翻译过来就是“工艺管道及仪表流程图"。
二者的主要区别就是图中所表达内容多少的不同,PFD较P&ID内容简单.更明了的解释就是P&ID图纸里面基本上包括了现场中所有的管件、阀门、仪表控制点等,非常全面,而PFD图将整个生产过程表述明白就可以了,不必将所有的阀门、管件、仪表都画出来。
另外,还有一种图纸虽不是表述流程的,但也很重要即设备布置图。
但相对以上两类图而言,读起来要容易得多,所以在后面只做简要介绍。
下面就介绍一下大家在图纸中经常看到的一些内容及表示方法.1 流程图主要内容不管是哪一种,那一类流程图,概括起来里面的内容大体上包括图形、标注、图例、标题栏等四部分,我们在拿到一张图纸后,首先就是整体的认识一下它的主要内容。
具体内容分别如下:a 图形将全部工艺设备按简单形式展开在同一平面上,再配以连接的主、辅管线及管件,阀门、仪表控制点等符号。
b 标注主要注写设备位号及名称、管段编号、控制点代号、必要的尺寸数据等。
聚乙烯工艺流程图(1)ppt课件

1995年Exxon公司开发出超冷凝工艺,使低压气相 反应器的时空产率提高了200% 。
1
聚乙烯
结构式 聚乙烯简介 用途 主要生产工艺 乙烯聚合基本原理 聚乙烯生产发展史 国内外生产状况 最新进展和发展趋势
2
结构式
近年来在核物理,天体物理,反应堆运行中 运用聚乙烯作为催化剂来测
返回3源自简介 聚乙烯(PE)塑料一种,我们常常提的方便袋就是聚乙烯(PE).聚 乙烯是结构最简单的高分子,也是应用最广泛的高分子材料.聚 乙烯是通过乙烯(CH2=CH2 )的加成聚合而成的。
编辑本段结构式
CH2=CH2+CH2=CH2+······→—CH2—CH2—CH2—
CH2······
简写:nCH2=CH2→—[—CH2—CH2—CH2—CH2—]—
聚合压力大小:高压、中压、低压;
聚合实施方法:淤浆法、溶液法 、气相法;
产品密度大小:高密度、中密度、低密度。
4
聚乙烯是半结晶热塑性材料。它们的 化学结构、分子量、聚合度和其他性 能很大程度上均依赖于使用的聚合方 法。聚合方法决定了支链的类型和支 链度。结晶度取决于聚合物的化学结 构和加工条件。
中高密度聚乙烯产品
密度范围: 0.916—0.961 g/cm3
返回
分子量:3—25万
39
低压气相流化床反应示意图
40
低压气相流化床聚乙烯装置
分项工程的施工工艺框图和标准说明(doc 13页)

分项工程的施工工艺框图和标准说明(doc 13页)5.1路基填筑施工工艺框图说明:(1)HEC混凝土路面基层为6%水泥稳定碎石层,厚度10cm;(2)基层混合料采用强制式搅拌站集中拌制,15t自卸汽车运输;(3)水泥稳定碎石采用PY180平地机一层摊铺,3Y—12/15型压路机碾压;(4)碾压好的水泥稳定碎石层采取洒水养生。
基层准备安装轨模摊铺振捣修整与光面纹理制作拆模与养生填缝与开通砼拌制和运输检查模板尺寸、位置、标高安装胀缝、填缝板并检查安装传力杆、安装钢筋切、锯缩缝压制缩缝或5.3 路面面层施工工艺框图说明:(1)隧道路面为HEC混凝土面板,厚度32cm,路拱横坡2%;(2)HEC混凝土采用HZS25型拌和站集中拌制,MR4500型混凝土搅拌运输车运输;(3)路面混凝土选用HT6000型轨模式摊铺机铺筑,摊铺机不能铺料的边角部位采取人工铺料;(4)路面混凝土采取覆盖洒水养生;(5)采用刻纹机制作路面纹理,切缝机割锯缝槽,灌缝机填缝。
5.4 桥梁施工工艺框图和文字说明5.4.1桥梁工程总体施工工艺框图桥梁施工人员、设文字说明:1、本框图为桥梁工程总体施工工艺流程框图,施工组织中对不同桥型细化了具体的施工方法,本节中分别示出了其施工工艺框图2、桥面铺装及附属结构根据每座桥具体的施工图确定。
5.4.2磨子沟T型梁桥施工工艺框图文字说明:本框图为磨子沟普通混凝土T型梁桥施工工艺流程框图,具体施工工艺和方法详见桥梁工程施工方案。
5.4.3 桥梁钻孔灌注桩施工工艺框图文字说明:本框图为磨子沟桥基础钻孔灌注桩施工工艺框图,施工时根据具体的地质及水文条件调整施工方法及工艺。
5.4.4 大奔流沟钢筋混凝土空心板桥施工工艺框图文字说明:本框图为大奔流沟钢筋混凝土空心板桥施工工艺流程框图,具体施工工艺和方法详见桥梁工程施工方案。
5.5 隧道施工工艺框图和文字说明5.5.1洞口石方明挖及边坡支护(1) 洞口石方明挖及边坡支护施工工艺框图此图为洞口石方明挖及边坡支护施工工艺框图,具体施工工艺和施工方法见1.3.4.1节第(3)部分。
COE新型制管工艺应用研究(1)

COE新型制管工艺应用研究陈昌1,裴银柱2,黄克坚1,张坤鹏2,王良塑1(1. 番禺珠江钢管有限公司,广州510000;2. 番禺珠江钢管(连云港)有限公司,连云港222000)摘要:为了解决小口径直缝埋弧焊管的质量不稳定、效率低等生产技术难题,综合考察了UOE、JCOE、HFW焊管制造工艺。
在对钢管成型技术,预焊技术和扩径技术进行分析的基础上,开发出COE 直缝埋弧焊管制造工艺。
应用实践表明:采用COE制管工艺极大地提高了小口径埋弧焊管的生产效率,降低了生产成本,且焊管管体成型好、产品质量稳定。
关键词:COE;高频预焊;水压扩径;小口径埋弧焊管Research on the application COE pipe TechnologyChen chang ,Pei yinzhu ,Huang kejian,Zhang kunpeng, Wang liangsu(1.Panyu Chu Kong Steel Pipe Co., Ltd. Guangzhou 510000, China2.Panyu Chu Kong Steel Pipe (Lianyungang)Co., Ltd. Lianyungang 222000,China)Abstract: In order to solve the technical difficulties such as unstable quality, low efficiency etc., during the production of small diameter submerged arc welded pipe, the fabrication process of UOE, JCOE and HFW welded pipe is investigated comprehensively. A new kind of manufacturing technology which named COE has been developed on the basis of analysis the steel pipe forming technology, pre welding technology and expanding technology. Actual application practices showed that COE technology is suitable for the production of small diameter submerged arc welded pipe particularly with high efficiency, low cost and excellent quality.Key words: COE; pre welding with high frequency; hydraulic expanding; submerged arc welded pipe with small diameter前言直缝埋弧焊管与其他种类钢管相比,具有产品规格覆盖范围广、制造精度高、焊接性能稳定等优点,主要应用于油气管线工程建设领域。
- 1、下载文档前请自行甄别文档内容的完整性,平台不提供额外的编辑、内容补充、找答案等附加服务。
- 2、"仅部分预览"的文档,不可在线预览部分如存在完整性等问题,可反馈申请退款(可完整预览的文档不适用该条件!)。
- 3、如文档侵犯您的权益,请联系客服反馈,我们会尽快为您处理(人工客服工作时间:9:00-18:30)。
JCOE直缝焊管生产线工艺流程图
JCOE直缝焊管生产线工艺流程说明
1、钢板准备:将准备生产的钢管所需钢板按顺序堆放好,提前做好产前准备。
并放好相应的原材料标识牌。
2、钢板吊运、标志:正式投产时将相应规格钢板按炉号、批号上料,吊运到横向上料台架上,对钢板表面质量
进行检查,并在钢板两端用记号笔填写钢管管号及区分A、B端标识。
3、引熄弧板制作:根据生产订单钢管规格提前制作相应的引熄弧板。
4、焊接引熄弧板:钢板吊运到横向待料台架(长短辊)上后,在钢板的四个角焊接引熄弧板,引熄弧板要焊正
焊牢。
5、钢板表面除锈:用负压风除掉钢板表面浮锈及氧化皮等。
6、钢板超声波探伤检查:对钢板及板边进行超声波检测,检查钢板是否存在分层、夹渣、裂纹等质量缺陷。
7、钢板铣边:通过数控铣边机的加工将钢板铣削到成型所需要的板宽;同时按焊接工艺需要的坡口角度及钝边
尺寸对钢板两边进行加工。
8、板边除锈、板面清扫:将铣边后的钢板坡口两侧50mm内浮锈除掉,提高焊接合格率;清扫板面铣边残留
的铁屑,防止残留铁屑在预弯和成型时被压入管体内。
9、钢板预弯:预弯机将钢板分段进行板边预弯,使其板边达到所要求的曲率半径(圆弧)。
10、JCO成型:成型机通过上下模具对预弯边后的钢板一半进行多次步进压制,将钢板压成横卧的“J”形,再将钢
板的另一半通过同样工序压成横卧的“C”形管坯,最后在“C”形管坯中间进行压制,形成开口的“O”形管筒。
11、钢管预焊:预焊机使成型后的管筒合缝并采用Ar+CO2气体保护焊进行连续焊接,开口的管坯合缝状态,将
直接影响钢管内、外焊接的质量。
12、预焊后清飞溅:将钢管预焊时飞溅在坡口两侧的飞溅物清除干净。
13、预焊质量检查:检查预焊后的管子焊缝是否有断弧、漏焊、焊接不均匀、气孔等缺陷。
14、预焊焊缝修补:对预焊质量检查岗位检查出来焊缝有缺陷的钢管进行手工修补。
15、钢管标志:在钢管外表面用记号笔写管号。
16、预焊缝清理:对成型过程中钢管内部残留的氧化皮、锈蚀等进行清理,尤其预焊缝坡口内的杂物要清理干净。
17、钢管内焊:根据工艺选择相应的焊接参数及焊丝、焊剂等,对钢管内坡口进行自动埋弧焊接,确保达到要求
的焊缝形貌和理化性能值。
18、钢管内焊清渣:将钢管内焊后焊缝和内管壁上残留的焊剂及焊渣等清理干净。
19、钢管内焊缝检查:对内焊缝形貌进行检查如焊缝高度、错边、咬边、内搭焊等。
20、钢管预焊缝清除:当外焊缝高度无法满足要求时,需去除掉预焊缝以保证外焊后焊缝的高度满足要求,避免
因预焊而造成焊缝质量缺陷。
21、钢管外焊:根据工艺选择相应的焊接参数及焊丝、焊剂,对钢管外坡口进行焊接,确保达到要求的焊缝形貌
和理化性能值。
22、钢管外焊清渣:将外焊完成的钢管外焊缝及钢管外壁上残留的焊剂及焊渣等清除干净。
23、钢管内外焊缝检查、补焊:对完成内、外焊工艺的钢管进行焊缝质量检查,如焊缝高度、错边、焊偏、咬边、
内外搭焊等。
并对肉眼能发现的缺陷进行修补。
24、切除引熄弧板:钢管内、外焊缝检查合格或焊缝缺陷修补完成后,人工用火焰将引熄弧板切除掉。
25、1#超声波探伤检查:超声波检查装置校准好通道后对焊缝进行自动超声波探伤检查,检查焊缝是否有焊接缺
陷,如气孔、裂纹、未焊透、未融合、夹渣、夹珠等,并对缺陷进行判定与标记。
26、超声波手探与标记:对自动超声波探伤管端部位探测不到的盲区进行手工超声波探伤,并对有缺陷的位置及
缺陷类型进行标记。
27、1#X光检查:在射线室内对钢管焊缝进行X射线检查,检查焊缝是否有焊接缺陷,如气孔、裂纹、未焊透、
未融合、夹渣、夹珠等,并对缺陷进行判定、标记。
28、检测后补焊:对超声波和X射线检查后判定为有缺陷的钢管按要求进行补焊修复处理,修复完成后再次进行
超声波与射线检查。
29、机械内扩径:扩径机对检测合格的钢管进行机械内扩径,使其达到标准要求的管径,满足椭圆度、直线度设
计要求。
通过机械扩径消除钢管因成型造成的鲍辛格效应;消除焊接时产生的焊缝热影响区残余内应力;通过扩径的冷作硬化提高钢管屈服强度。
30、机械定减径:定减径机通过缩径工艺将钢管管径、圆度、直线度等达到标准要求。
通过机械减径消除钢管因
成型造成的鲍辛格效应;消除焊接时产生的焊缝热影响区残余内应力;通过减径的冷作硬化大大提高钢管屈服强度。
尤其是大壁厚、小直径、海洋管线管,通过定减径工艺可以显著提高钢管的承压能力。
31、钢管火焰平头:对有轴向错边的钢管进行火焰平头,将钢管两个端面切平,便于水压机封水和保护水压机密
封圈。
32、取样:根据要求对钢管进行理化取样。
33、管端内外焊缝修磨:将钢管两端一定长度范围的内、外焊缝根据要求进行修磨处理。
34、钢管水压试验:水压机对钢管进行打水压试验,检查管体及焊缝是否有缺陷。
打压压力及稳压时间根据要求
执行。
35、钢管整圆矫直:整圆矫直机对直线度和圆度不达标的钢管进行二次矫正,以保证钢管完全达到标准要求。
36、2#超声波检查:超声波装置对扩径和打水压后发生应力变化的钢管进行二次超声波焊缝检查,确认焊缝是否
有缺陷。
37、超声波手探:对自动超声波探伤管端探不到的盲区进行手工超声波探伤,确认管端焊缝是否有缺陷。
38、2#X光检查:在射线室对扩径和打水压后发生应力变化的钢管进行二次X射线焊缝检查,确认焊缝是否有缺
陷。
39、管端X光片检查:对钢管两端焊缝及热影响区250mm区域进行管端X射线拍片、洗片和评片,以确认管端
焊缝和热影响区是否有缺陷。
40、钢管补焊修磨:对二次超声波和X射线检查确认有缺陷的钢管在标准允许下进行补焊修磨,最终保证钢管质
量合格。
41、钢管次品切断、取样:对二次超声波和X射线检查确认有缺陷根据相关标准不能补焊或判废的管段进行次品
切除;对钢管进行理化取样。
42、管端倒棱:根据标准和客户要求用倒棱机将钢管两端车削出相应的钝边和坡口。
43、管端磁粉探伤检查:用磁粉无损检测方式对管端进行缺陷检查。
44、钢管称重、测长:对每根钢管进行称重和长度测量。
45、钢管喷标:按照标准和客户要求对钢管进行喷标识。
46、客户检查:客户对钢管尺寸、外观等进行抽查。
47、钢管入库:经检验合格的钢管进行入库存放。