铣削加工工艺流程分析
最新加工工艺流程

最新加工工艺流程随着科技的不断发展,加工工艺也在不断更新和改进。
下面将介绍一些最新的加工工艺流程。
1.激光切割工艺激光切割工艺是一种通过激光束对材料进行切割的方法。
它具有精度高、速度快、能够切割复杂形状等优点。
其工艺流程一般包括材料准备、机器设定、激光切割、表面处理等步骤。
2.数控铣削工艺数控铣削工艺是一种通过数控机床对材料进行铣削的方法。
它将工件固定在工作台上,通过数控机床上的铣削刀具对工件进行加工。
其工艺流程一般包括工件夹紧、机床设定、程序编制、铣削加工、尺寸检测等步骤。
3.3D打印工艺3D打印工艺是一种通过层层堆叠材料以实现三维物体制造的方法。
它可以直接从计算机模型中生成物体,具有制造周期短、灵活性高等优点。
其工艺流程一般包括设计模型、切片处理、打印加工、后处理等步骤。
4.水刀切割工艺水刀切割工艺是一种通过高压水流对材料进行切割的方法。
它可以对各种材料进行切割,具有无热影响、切割效果好等优点。
其工艺流程一般包括材料固定、加工参数设置、水刀切割、清洗干净等步骤。
5.真空蒸发工艺真空蒸发工艺是一种通过在真空中蒸发物质并在基板上沉积的方法。
它可以制备一些特殊的薄膜材料,具有薄膜质量好、薄膜均匀性高等优点。
其工艺流程一般包括材料准备、真空设定、蒸发沉积、薄膜检测等步骤。
6.电解加工工艺电解加工工艺是一种通过电化学作用对金属材料进行加工的方法。
它具有可以加工复杂形状、加工精度高等优点。
其工艺流程一般包括工件准备、电解液配制、电解加工、表面处理等步骤。
以上是一些最新的加工工艺流程的介绍。
这些工艺都具有自身的特点和优点,在不同的加工场景中可以选择合适的工艺来进行加工。
随着技术的进一步发展,相信还会有更多更先进的加工工艺被开发出来。
典型零件的加工工艺
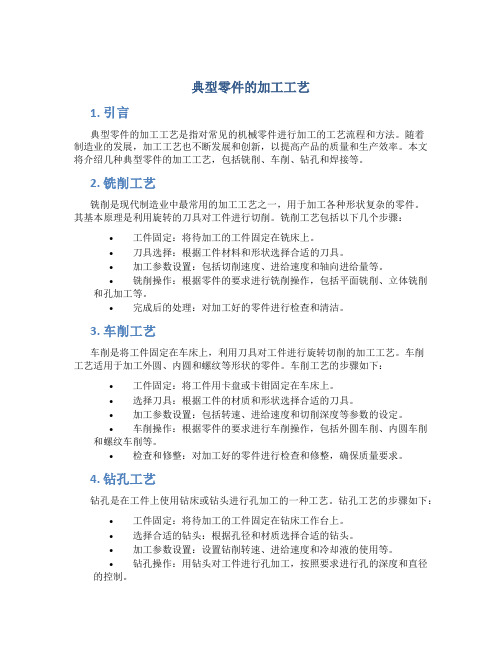
典型零件的加工工艺1. 引言典型零件的加工工艺是指对常见的机械零件进行加工的工艺流程和方法。
随着制造业的发展,加工工艺也不断发展和创新,以提高产品的质量和生产效率。
本文将介绍几种典型零件的加工工艺,包括铣削、车削、钻孔和焊接等。
2. 铣削工艺铣削是现代制造业中最常用的加工工艺之一,用于加工各种形状复杂的零件。
其基本原理是利用旋转的刀具对工件进行切削。
铣削工艺包括以下几个步骤:•工件固定:将待加工的工件固定在铣床上。
•刀具选择:根据工件材料和形状选择合适的刀具。
•加工参数设置:包括切削速度、进给速度和轴向进给量等。
•铣削操作:根据零件的要求进行铣削操作,包括平面铣削、立体铣削和孔加工等。
•完成后的处理:对加工好的零件进行检查和清洁。
3. 车削工艺车削是将工件固定在车床上,利用刀具对工件进行旋转切削的加工工艺。
车削工艺适用于加工外圆、内圆和螺纹等形状的零件。
车削工艺的步骤如下:•工件固定:将工件用卡盘或卡钳固定在车床上。
•选择刀具:根据工件的材质和形状选择合适的刀具。
•加工参数设置:包括转速、进给速度和切削深度等参数的设定。
•车削操作:根据零件的要求进行车削操作,包括外圆车削、内圆车削和螺纹车削等。
•检查和修整:对加工好的零件进行检查和修整,确保质量要求。
4. 钻孔工艺钻孔是在工件上使用钻床或钻头进行孔加工的一种工艺。
钻孔工艺的步骤如下:•工件固定:将待加工的工件固定在钻床工作台上。
•选择合适的钻头:根据孔径和材质选择合适的钻头。
•加工参数设置:设置钻削转速、进给速度和冷却液的使用等。
•钻孔操作:用钻头对工件进行孔加工,按照要求进行孔的深度和直径的控制。
•清洁和检查:对加工好的孔进行清理和检查,确保孔的质量。
5. 焊接工艺焊接是将两个或多个工件通过熔化和凝固的过程连接在一起的工艺。
焊接工艺的步骤如下:•工件准备:准备待焊接的工件,包括清洁和坡口处理等。
•焊接机器设置:根据材料和焊接方式设置焊接机器的参数,包括电流、电压和焊接速度等。
电池极柱铣削工艺流程

电池极柱铣削工艺流程电池极柱铣削工艺是电池制造过程中的重要环节之一,它主要用于对电池极柱进行加工和修整,以满足电池的性能和质量要求。
本文将介绍电池极柱铣削工艺的流程及其关键步骤。
一、准备工作在进行电池极柱铣削之前,需要进行一系列的准备工作。
首先,确定铣削工艺参数,包括铣削刀具的选择、铣削速度、进给速度等。
其次,准备好所需的设备和工装夹具,确保其正常运行和安全使用。
最后,对电池极柱进行检查,确保其尺寸和形状符合要求。
二、粗铣削粗铣削是电池极柱铣削的第一步,其目的是将电池极柱的表面切削至一定的粗糙度,为后续的加工步骤提供良好的加工基准。
在粗铣削过程中,需要注意切削刀具与电池极柱表面的接触状态,确保刀具与工件之间的切削力得到合理分配。
三、精铣削精铣削是电池极柱铣削的关键步骤,其目的是将电池极柱的表面进行进一步的修整和光洁处理,提高其表面质量和精度。
在精铣削过程中,需要采用合适的切削刀具和加工参数,确保电池极柱的尺寸和形状符合要求,并且表面光洁度达到要求。
四、尺寸检测在电池极柱铣削完成后,需要对加工后的电池极柱进行尺寸检测。
尺寸检测可以利用专用的测量仪器和设备进行,以确保电池极柱的尺寸和形状与设计要求相符。
同时,还需对电池极柱的表面质量和光洁度进行检查,以确保其满足质量要求。
五、表面处理电池极柱铣削完成后,还需要进行表面处理,以提高其耐腐蚀性和电导率。
常见的表面处理方法包括喷涂、电镀、热处理等,根据不同的要求选择合适的表面处理方式,确保电池极柱的性能和质量得到进一步提升。
六、质量控制在整个电池极柱铣削工艺流程中,质量控制是非常重要的环节。
通过对每个工艺步骤进行严格的质量控制,可以确保电池极柱的加工质量和性能稳定可靠。
质量控制可以包括工艺参数的监控、加工过程的实时检测以及最终产品的检验等环节。
总结起来,电池极柱铣削工艺流程包括准备工作、粗铣削、精铣削、尺寸检测、表面处理和质量控制等关键步骤。
通过科学合理地执行这些步骤,可以保证电池极柱的加工质量和性能达到设计要求,从而提高电池的整体性能和可靠性。
铣削长方体工艺流程
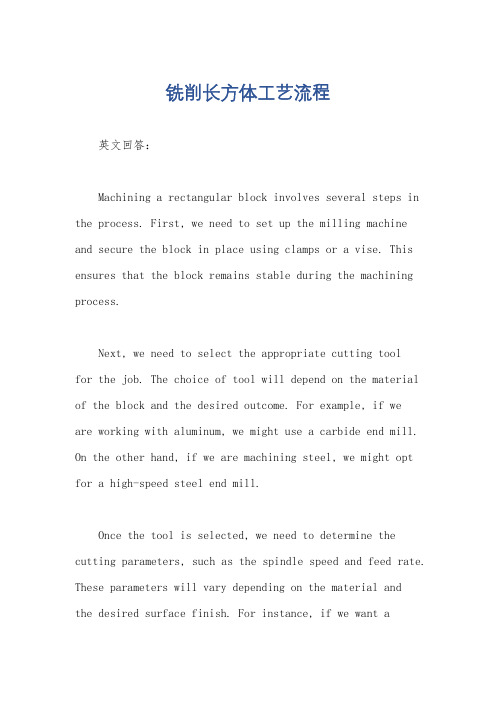
铣削长方体工艺流程英文回答:Machining a rectangular block involves several steps in the process. First, we need to set up the milling machine and secure the block in place using clamps or a vise. This ensures that the block remains stable during the machining process.Next, we need to select the appropriate cutting toolfor the job. The choice of tool will depend on the material of the block and the desired outcome. For example, if weare working with aluminum, we might use a carbide end mill. On the other hand, if we are machining steel, we might opt for a high-speed steel end mill.Once the tool is selected, we need to determine the cutting parameters, such as the spindle speed and feed rate. These parameters will vary depending on the material andthe desired surface finish. For instance, if we want asmooth surface finish, we might choose a lower feed rateand a higher spindle speed.With the machine set up and the cutting parameters determined, we can now begin the milling process. This involves moving the cutting tool across the surface of the block to remove material and create the desired shape. We can use different milling techniques, such as facing, contouring, or pocketing, depending on the specific requirements of the job.Throughout the milling process, it is important to monitor the cutting tool and make adjustments as needed.For example, if we notice that the tool is wearing out or producing poor surface finishes, we might need to changethe tool or adjust the cutting parameters.Once the milling process is complete, we can remove the block from the machine and inspect the finished product. We might need to perform additional operations, such as deburring or polishing, to achieve the desired final result.Overall, the process of milling a rectangular block involves setting up the machine, selecting the cutting tool, determining the cutting parameters, performing the milling operation, and inspecting the final product. It requires careful attention to detail and the ability to make adjustments as needed.中文回答:铣削长方体的工艺流程包括几个步骤。
铣削加工工艺
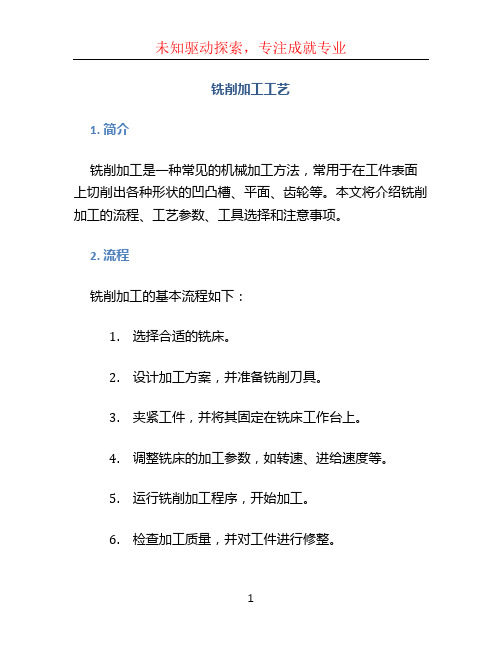
铣削加工工艺1. 简介铣削加工是一种常见的机械加工方法,常用于在工件表面上切削出各种形状的凹凸槽、平面、齿轮等。
本文将介绍铣削加工的流程、工艺参数、工具选择和注意事项。
2. 流程铣削加工的基本流程如下:1.选择合适的铣床。
2.设计加工方案,并准备铣削刀具。
3.夹紧工件,并将其固定在铣床工作台上。
4.调整铣床的加工参数,如转速、进给速度等。
5.运行铣削加工程序,开始加工。
6.检查加工质量,并对工件进行修整。
7.收尾工作和清洁。
3. 工艺参数铣削加工的工艺参数对于加工质量和效率具有重要影响,以下是常见的工艺参数:•切削速度(Cutting Speed):切削刀具在单位时间内通过工件的线速度,一般使用米/分钟(m/min)作为单位。
•进给速度(Feed Rate):每次切割刀具移动的距离。
通常用毫米/转(mm/tooth)表示。
•切削深度(Cutting Depth):切削刀具在每次进给完成后,切入工件的深度。
•切削宽度(Cutting Width):切削刀具在每次进给完成后,切削工件的宽度。
•刀具半径补偿(Tool Radius Compensation):针对切削刀具的尺寸进行补偿,保证加工尺寸的精确度。
4. 工具选择选择合适的铣刀工具对于加工质量和效率至关重要。
以下是常见的铣刀工具类型:•端铣刀:用于切削平面和轮廓。
•刀柄铣刀:用于开槽、切割等操作。
•高铣刀:用于深孔加工。
•槽铣刀:用于加工凹槽和槽口。
具体选择何种铣刀工具需要根据加工要求、工件材料和加工量来进行评估。
5. 注意事项在进行铣削加工时,需要注意以下事项:•安全操作:操作人员应戴上安全帽、眼镜等防护用品。
避免手部接触刀具,确保操作安全。
•刀具使用寿命:定期检查铣刀刃口的磨损情况,及时更换刀具,以确保加工质量。
•清洁工作:加工完成后,注意清理铣床、工作台和周围空间,保持工作环境整洁。
结论铣削加工是一种常见的机械加工方法,本文介绍了铣削加工的流程、工艺参数、工具选择和注意事项。
阶梯轴类机械零件的加工工艺基础知识

阶梯轴类机械零件的加工工艺基础知识阶梯轴是一种用于传递动力的机械零件,通常由两个或更多的阶梯组成。
阶梯轴类机械零件的加工工艺基础知识对于制造高精度、高强度的机械零件至关重要。
以下是一些关于阶梯轴类机械零件的加工工艺基础知识的介绍。
一、材料的选择和准备阶梯轴类机械零件通常由高强度材料制成,如钢、铝、铜等。
在选择材料时,需要考虑到零件的应用场合、性能要求等。
同时,应提前对材料进行严格的选材和检测,以保证材料的质量和机械性能。
二、制作工艺流程1.铣削工艺:阶梯轴类机械零件通常需要进行铣削加工。
铣削加工是通过将铣削刀具沿着工件表面移动,切削出所需形状和尺寸的工艺。
在铣削加工中,需要选择合适的加工刀具和加工工艺参数,并根据零件的几何形状和尺寸进行不同的加工方式。
2.车削工艺:阶梯轴类机械零件的表面通常需要进行车削加工,以提高零件的精度和表面质量。
车削是通过将车床刀具沿着工件轴向移动,实现工件表面的加工。
在车削加工中,需要选择合适的车床刀具和加工工艺参数,并根据零件的几何形状和尺寸进行不同的加工方式。
3.磨削工艺:阶梯轴类机械零件通常需要进行磨削加工,以提高零件的精度和加工表面质量。
磨削是通过磨削刀具在工件表面进行摩擦和切削,实现工件表面的加工。
在磨削加工中,需要选择合适的磨削刀具和加工工艺参数,并根据零件的几何形状和尺寸进行不同的加工方式。
三、加工过程中的质量控制阶梯轴类机械零件的加工过程中需要进行严格的质量控制,以确保零件的几何形状和尺寸的精度,并防止因加工误差导致零件出现失配或故障等情况。
1.使用高精度的测量工具进行测量,如长度计、卡尺等,以确保零件的几何形状和尺寸的精度。
2.使用高质量的加工设备和工具,如铣床、车床、磨床等,以确保加工质量和加工效率。
3.进行各项加工参数的分析和调整,如切削速度、进给量、切削深度等,以优化加工效果和确保加工质量。
4.进行零件的表面处理,如磨光、抛光等,以提高零件的表面质量,并保证零件的防腐性和耐蚀性。
铣削加工工艺流程中的切削深度选择指南
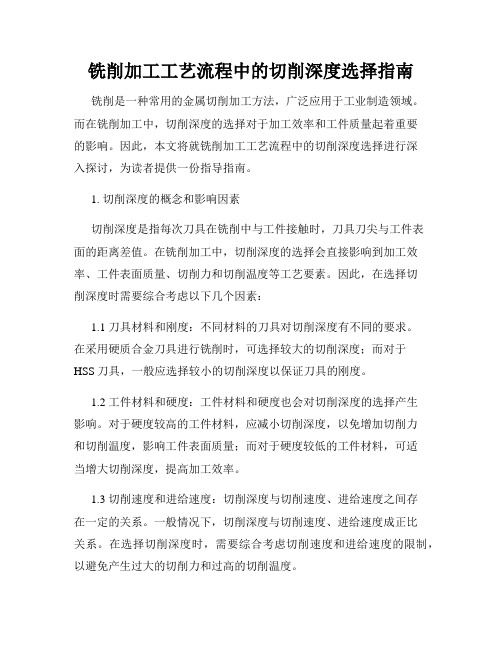
铣削加工工艺流程中的切削深度选择指南铣削是一种常用的金属切削加工方法,广泛应用于工业制造领域。
而在铣削加工中,切削深度的选择对于加工效率和工件质量起着重要的影响。
因此,本文将就铣削加工工艺流程中的切削深度选择进行深入探讨,为读者提供一份指导指南。
1. 切削深度的概念和影响因素切削深度是指每次刀具在铣削中与工件接触时,刀具刀尖与工件表面的距离差值。
在铣削加工中,切削深度的选择会直接影响到加工效率、工件表面质量、切削力和切削温度等工艺要素。
因此,在选择切削深度时需要综合考虑以下几个因素:1.1 刀具材料和刚度:不同材料的刀具对切削深度有不同的要求。
在采用硬质合金刀具进行铣削时,可选择较大的切削深度;而对于HSS刀具,一般应选择较小的切削深度以保证刀具的刚度。
1.2 工件材料和硬度:工件材料和硬度也会对切削深度的选择产生影响。
对于硬度较高的工件材料,应减小切削深度,以免增加切削力和切削温度,影响工件表面质量;而对于硬度较低的工件材料,可适当增大切削深度,提高加工效率。
1.3 切削速度和进给速度:切削深度与切削速度、进给速度之间存在一定的关系。
一般情况下,切削深度与切削速度、进给速度成正比关系。
在选择切削深度时,需要综合考虑切削速度和进给速度的限制,以避免产生过大的切削力和过高的切削温度。
2. 切削深度的选择方法在具体的铣削加工中,如何准确选择合适的切削深度是关键问题之一。
下面将介绍几种常用的切削深度选择方法:2.1 经验法:根据实际经验,根据工件材料、刀具类型和加工要求等因素,通过试切和总结经验来选择切削深度。
这种方法简单易行,但依赖于经验积累,并不能保证最佳的切削深度。
2.2 切削力限制法:根据切削力的大小,限制切削深度,以保证在合理范围内切削力不超过刀具和机床的承载能力。
这种方法可以较好地控制切削力,但需要考虑到刀具和机床的实际情况。
2.3 表面质量限制法:根据工件表面质量要求,选择合适的切削深度。
铣床加工流程

铣床加工流程铣床是一种常见的金属加工设备,广泛应用于机械制造、航空航天、汽车制造等领域。
铣床加工流程是指在铣床上进行金属材料的切削加工过程,下面将详细介绍铣床加工的流程及注意事项。
1. 铣床加工前的准备。
在进行铣床加工之前,首先需要对工件和刀具进行准备。
工件应该进行检查,保证其表面平整、无裂纹和磨损,以确保加工质量。
刀具也需要进行检查和安装,确保刀具的刃部锋利,刀柄固定牢固。
此外,还需要对铣床进行检查和调整,确保设备运转正常。
2. 刀具路径规划。
在进行铣床加工之前,需要根据工件的形状和尺寸,规划刀具的路径。
通过CAD软件或者手工绘制,确定切削路径和切削深度,以确保加工出符合要求的工件。
3. 工件夹紧和定位。
在进行铣床加工之前,需要将工件夹紧在工作台上,并进行定位。
夹紧和定位的准确性直接影响加工质量,因此需要仔细调整夹紧装置和定位装置,确保工件不会移动或者晃动。
4. 铣削加工。
铣削加工是铣床加工的主要过程,通过刀具在工件表面上旋转切削,将工件表面切削成所需的形状和尺寸。
在进行铣削加工时,需要根据刀具路径规划,逐步进行切削,控制切削深度和进给速度,确保加工质量。
5. 清洁和检查。
在完成铣床加工后,需要对工件和铣床进行清洁和检查。
清洁工件表面的切削屑和油污,以便后续的加工或者使用。
同时,需要对工件进行检查,确保加工质量符合要求。
6. 工件卸载。
在完成铣床加工后,需要将工件从工作台上卸载。
在卸载工件时,需要注意操作规范,避免因操作不当导致工件损坏或者人身伤害。
7. 加工记录和总结。
在完成铣床加工后,需要对加工过程进行记录和总结。
记录加工参数、加工时间、加工质量等信息,以便后续的工艺分析和质量控制。
总之,铣床加工流程包括准备、刀具路径规划、工件夹紧和定位、铣削加工、清洁和检查、工件卸载以及加工记录和总结等环节。
在进行铣床加工时,需要严格按照流程进行操作,确保加工质量和安全生产。
铣削长方体工艺流程

铣削长方体工艺流程英文回答:Machining a rectangular prism involves several steps to ensure precise and accurate results. The process typically includes the following steps:1. Planning and preparation: Before starting the machining process, it is essential to carefully plan and prepare the necessary tools, materials, and equipment. This includes selecting the appropriate milling machine, end mills, and fixtures required for the job.2. Material setup: The rectangular prism is securely fixed onto the milling machine table using clamps or other suitable fixtures. It is crucial to ensure that the workpiece is properly aligned and positioned to avoid any inaccuracies during the machining process.3. Tool selection: The choice of end mills depends onthe specific requirements of the job, such as the desired surface finish and the material being machined. For example, a carbide end mill with a high number of flutes may be preferred for machining aluminum, while a coated high-speed steel end mill might be more suitable for stainless steel.4. Roughing: The initial roughing pass involves removing a significant amount of material from the workpiece. This is done using a larger diameter end millwith fewer flutes to quickly remove excess material and shape the rectangular prism closer to the final dimensions.5. Semi-finishing: Once the roughing pass is completed,a smaller diameter end mill with more flutes is used for semi-finishing. This step helps to achieve a smoother surface finish and further refine the dimensions of the rectangular prism.6. Finishing: The final finishing pass is performed using a high-speed machining technique with a smalldiameter end mill and a higher feed rate. This step helpsto achieve the desired surface finish and ensures that thedimensions of the rectangular prism are within the required tolerances.7. Inspection and quality control: After the machining process is completed, the rectangular prism is carefully inspected to ensure that it meets the specified dimensions and surface finish requirements. This may involve using measuring tools such as calipers, micrometers, or a coordinate measuring machine (CMM).8. Deburring and cleaning: Any sharp edges or burrs resulting from the machining process are removed, and the rectangular prism is thoroughly cleaned to remove any chips or coolant residue.9. Final inspection and packaging: The finished rectangular prism is inspected once again to ensure that it meets all the quality standards. It is then properly packaged and prepared for shipment or further processing.中文回答:铣削长方体的工艺流程包括以下几个步骤,以确保结果精确和准确。
典型薄壁零件数控铣削加工工艺

典型薄壁零件数控铣削加工工艺典型薄壁零件指的是壁厚比较薄的机械零部件,其加工工艺要求高,因为薄壁零件具有易变形、易损坏等特点,所以数控铣削加工工艺尤为重要。
本文将介绍典型薄壁零件数控铣削加工的工艺流程、注意事项以及优化方案。
1. 零件设计和准备在进行数控铣削加工前,首先需要进行零件的设计和准备。
设计时需要根据零件的实际情况,合理确定加工工序、夹持方式和刀具选择。
在准备阶段,需要准备好数控铣床和相应的工具。
2. 夹持工件夹持工件是数控铣削加工的第一步,对于薄壁零件需要特别注意夹持方式。
通常采用夹具夹紧的方式,可以增加工件的稳固性,同时需要保证夹持力不会对薄壁零件造成变形。
3. 刀具选择和加工参数设定选择合适的刀具和加工参数对于数控铣削加工来说至关重要。
对于薄壁零件来说,需要选用合适的刀具和适当的进给速度、转速等加工参数,以减小切削力,降低对工件的影响。
4. 加工操作在进行数控铣削加工时,需要严格按照程序要求进行操作。
特别是在对薄壁零件进行加工时,需要小心谨慎,避免发生碰撞、振动等情况,以免对工件造成损坏。
5. 检测和修整加工完成后,需要对工件进行检测和修整。
特别是对于薄壁零件来说,需要注意检测工件的尺寸精度和表面质量,及时修整不合格的部分。
二、典型薄壁零件数控铣削加工的注意事项1. 选择合适的材料对于薄壁零件来说,材料的选择至关重要。
需要选择具有较好加工性能和机械性能的材料,以减小加工难度和提高工件的使用寿命。
4. 避免振动和冲击在进行数控铣削加工时,需要小心谨慎,避免对薄壁零件产生振动和冲击。
合理选择刀具和加工参数,以避免产生不必要的振动和冲击。
1. 刀具选用对于薄壁零件的数控铣削加工,需要选择具有良好刚性和稳定性的刀具,以减小切削力和振动。
同时应该根据工件的实际情况,选择不同的刀具类型以提高加工效率。
2. 加工参数优化在数控铣削加工时,需要根据薄壁零件的实际情况,合理选择进给速度、转速、切削深度等加工参数,以减小切削力,提高加工效率。
典型零件的数控铣削加工工艺ppt课件

数量 刀长/mm
加工表面
Φ6高速钢立铣刀 1
20
粗加工凸轮槽内外轮廓
2 T02 Φ6硬质合金立铣刀 1
20
精加工凸轮槽内外轮廓
编制
审核
批准
共页 第页
火灾袭来时要迅速疏散逃生,不可蜂 拥而出 或留恋 财物, 要当机 立断, 披上浸 湿的衣 服或裹 上湿毛 毯、湿 被褥勇 敢地冲 出去
六、确定切削用量
火灾袭来时要迅速疏散逃生,不可蜂 拥而出 或留恋 财物, 要当机 立断, 披上浸 湿的衣 服或裹 上湿毛 毯、湿 被褥勇 敢地冲 出去
二、制定工艺过程
• ①普通铣床:铣底平面。GO • ②立式钻床:钻中心孔,钻、镗Φ20、
Φ12两个孔。GO • ③数控铣床:粗铣凸轮槽内外轮廓。GO • ④数控铣床:精铣凸轮槽内外轮廓。GO • ⑤钳工:矫平底面、表面光整、尖边倒
角。 • ⑥表面处理
火灾袭来时要迅速疏散逃生,不可蜂 拥而出 或留恋 财物, 要当机 立断, 披上浸 湿的衣 服或裹 上湿毛 毯、湿 被褥勇 敢地冲 出去
三、确定装夹方案
• 根据零件的结构特点,加工 Φ20、Φ12两个孔时,以底面A 定位(必要时可设工艺孔), 采用螺旋压板机构夹紧。
• 加工凸轮槽内外轮廓时,采用 “一面两孔”方式定位,即以 底面A和Φ20、Φ12两个孔为定 位基准,装夹示意图如下图所 示。
主轴转速 进给速度 背吃刀量 /(r/min) /(mm/min) /mm
1 一面两孔定位,粗 T07 铣凸轮槽内轮廓
2 粗铣凸轮槽外轮廓 T07
3 精铣凸轮槽内轮廓 T08
4 精铣凸轮槽外轮廓 T08
编制
审核
Φ6
Φ6 Φ6 Φ6 批准
铣削长方体工艺流程

铣削长方体工艺流程英文回答:Machining a rectangular block involves several steps to ensure a precise and accurate final product. Here is astep-by-step process for milling a rectangular block:Step 1: Material preparation.Before starting the milling process, it is essential to have a rectangular block of the desired material. This block should have dimensions slightly larger than the final dimensions required for the finished product. For example, if the final product needs to be 10cm x 5cm x 2cm, the initial block should be around 12cm x 7cm x 3cm.Step 2: Fixturing.The rectangular block needs to be securely fixed onto the milling machine's worktable. This can be done usingclamps or vices, ensuring that the block is held firmly in place and will not move during the milling process.Step 3: Tool selection.Choosing the right tool for milling is crucial to achieve the desired results. For a rectangular block, anend mill or a face mill can be used. The tool should have the appropriate diameter and cutting edges to remove the material efficiently.Step 4: Setting up the milling machine.Proper setup of the milling machine is essential for accurate milling. This includes adjusting the speed, feed rate, and depth of cut based on the material being machined. Additionally, the milling machine's table needs to be aligned correctly to ensure parallelism and perpendicularity.Step 5: Rough milling.In the rough milling stage, the excess material is removed from the rectangular block. The milling tool is used to make multiple passes over the block, gradually reducing its dimensions. Coolant or cutting fluid may be used to prevent overheating and ensure smooth cutting.Step 6: Finishing milling.Once the rough milling is complete, the final dimensions and surface finish are achieved through finishing milling. This involves using a smaller cutting tool to make precise cuts and achieve the desired surface smoothness.Step 7: Quality check.After the milling process, it is crucial to check the dimensions and surface finish of the rectangular block. This can be done using measurement tools such as calipers or a coordinate measuring machine (CMM). Any deviations from the required specifications should be addressed and corrected.中文回答:铣削长方体的工艺流程包括几个步骤,以确保最终产品的精度和准确性。
典型数控铣零件工艺分析及程序编制

技术学院毕业设计题目典型数控铣零件工艺分析及程序编制系别机电工程系专业机电一体化技术班级机电姓名学号 0441 指导教师日期 2011年9月设计任务书设计题目:典型数控铣零件工艺分析及程序编制设计要求:第一:熟悉数控铣床结构及加工性能第二:零件图的分析及确定加工内容第三:AUTO CAD图形的绘制第四:三维图形的绘制第五:选定加工设备第六:切削用量及刀具选择、装夹第七:制定零件的加工工艺路线第八:编写程序,完成加工操作设计进度要求:第一周搜集资料和前期准备工作第二周零件的工艺分析第三周零件的尺寸计算第四周整个零件工艺尺寸的计算部分第五周校核、修改、成文和定稿第六周电子稿的输入和排版第七周毕业答辩指导教师(签名):摘要质量优、性能好、效率高、能耗低、价格廉的机械产品是国民经济各个部门迫切需要的,伴随着科学技术和工业生产的飞速发展,产品设计是决定产品性能、质量水平、市场竞争力和经济效益的重要环节。
数控加工效率高、质量好、加工精度高,数控技术是与机床的自动控制密切结合而发展起来的,如今数控技术已广泛应用于化工生产、石油精炼、造纸、钢铁生产等工艺流程控制及其他各个方面。
近代大工业生产中,机械加工工艺过程的自动化是提高产品质量和生产率的重要措施。
数控机床的诞生,较好解决了精密复杂多品种单件或小批量机械零件加工自动化的问题。
为了能充分发挥、利用数控机床的各种功能,使数控机床能安全、可靠、高效的工作,在这里选择了一件最适宜在数控机床上进行加工的零件作为设计,并严格按照毕业设计要求,进行包括数控加工工艺分析、数控刀具及切削参数的选择、工件装夹方式与数控夹具的选择、程序编制中的数字计算、数控加工程序的编制等。
本设计主要介绍数控加工技术概述、数控加工的铣削基础、数控加工工艺设计及数控加工工艺文件、数控加工的工具系统、数控加工夹具、典型形状零件的数控加工工艺、数控铣削的加工工艺。
由于本课题所选的零件属于板类零件,二维加工,而且内、外轮廓的几何要素都是由直线和圆弧组成的,故采用手工编程方式即可完成全部数控编程任务。
数控铣削加工工艺分析
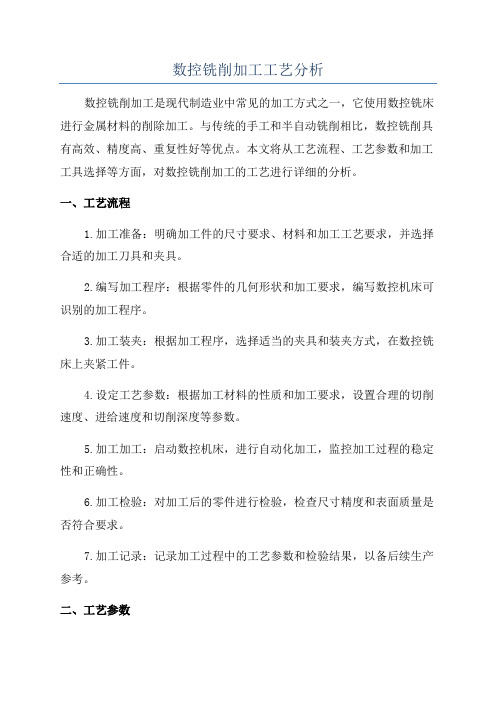
数控铣削加工工艺分析数控铣削加工是现代制造业中常见的加工方式之一,它使用数控铣床进行金属材料的削除加工。
与传统的手工和半自动铣削相比,数控铣削具有高效、精度高、重复性好等优点。
本文将从工艺流程、工艺参数和加工工具选择等方面,对数控铣削加工的工艺进行详细的分析。
一、工艺流程1.加工准备:明确加工件的尺寸要求、材料和加工工艺要求,并选择合适的加工刀具和夹具。
2.编写加工程序:根据零件的几何形状和加工要求,编写数控机床可识别的加工程序。
3.加工装夹:根据加工程序,选择适当的夹具和装夹方式,在数控铣床上夹紧工件。
4.设定工艺参数:根据加工材料的性质和加工要求,设置合理的切削速度、进给速度和切削深度等参数。
5.加工加工:启动数控机床,进行自动化加工,监控加工过程的稳定性和正确性。
6.加工检验:对加工后的零件进行检验,检查尺寸精度和表面质量是否符合要求。
7.加工记录:记录加工过程中的工艺参数和检验结果,以备后续生产参考。
二、工艺参数1.切削速度:是指刀具在单位时间内切削的长度。
根据加工材料的硬度和切削性能,合理选择切削速度,既能保证加工效率,又能保证刀具寿命。
2.进给速度:是指刀具在单位时间内在加工方向上移动的距离。
进给速度的选择应考虑切削力和切削表面的要求。
3.切削深度:是指刀具在一次进给过程中所削除的材料层厚度。
切削深度的选择应使得切削力合理,既能保证加工效率,又能避免切削表面的质量。
4.刀具半径补偿:数控铣床会自动根据刀具半径补偿值进行补偿,使得加工轮廓与设计轮廓一致。
5.加工顺序:根据零件的几何形状和切削力的分布情况,合理选择加工顺序,避免零件变形和加工过程中的切削力过大。
三、加工工具选择1.刀具材料:刀具材料应具有一定的硬度、耐磨性和耐冲击性,常用的刀具材料有硬质合金、高速钢和陶瓷等。
2.刀具形状:根据零件的几何形状和加工要求,选择合适的刀具形状,如平面铣刀、立铣刀、球头铣刀等。
3.切削刃数:根据加工材料的硬度和切削性能,选择合适的刀具刃数,既能保证加工效率,又能保证刀具寿命。
零件铣削加工工艺流程分析

零件铣削加工工艺流程分析作者:尚雯来源:《科学与信息化》2019年第32期摘要本文介绍了数控铣削加工工艺流程的一般内容,对数控铣削中的装夹方法,刀具选择,工序安排以及加工工艺过程的优化等一般工艺内容进行了研究,明确了零件在加工过程中所应注意的问题,解决较薄零件的加工问题、并减少了装夹次数,有效避免重復定位带来的加工误差等原因,提高了加工质量及加工效率。
关键词工艺分析;刀具;零件精度1 数控加工工艺数控铣削加工工艺关系到加工的效果和成败,是程编前的重要工艺准备工作之一。
根据加工实践,数控铣加工工艺流程分析所要解决的主要问题大致可归纳为选择并确定数控铣削加工部位及工序内容,包括零件装夹及刀具的选择,加工精度的保证和各种参数的选择。
2 数控铣削工艺分析2.1 铣削工艺分析(1)工艺准备时根据具体零件考虑装夹方法。
为保证零件加工完后的精确性,应尽可能在一次装夹中完成所有能加工表面的加工工序,所以要选择便于各个表面都能加工到的不同定位方式;如果需要二次装夹,应该采用统一的基准定位。
在数控加工中若没有统一的定位基准,会因工件重新安装可能产生定位误差,从而使加工后的两个面上的轮廓位置及尺寸不协调,因此,为保证二次装夹加工后其相对位置的准确性,一定要采用统一的定位基准。
(2)合理安排工序控制变形。
零件的内腔与外形应尽量采用统一的几何类型和尺寸,这样可以减少刀具规格和换刀次数,方便编程。
铣削外形时,在保证外形精确度的同时注意表面质量,尤其对于零件上装配部分的加工,在安排工序和选择刀具的同时应根据具体零件特点,考虑变形所产生的误差。
(3)刀具的选择。
刀具的选择是数控加工工艺中重要内容之一,它不但影响机床的加工效率,而且直接影响加工的质量。
与传统的加工方法相比,数控加工对刀具的要求更高。
不仅要求精度高、刚度好、耐用度高,而且要求尺寸规整、稳定、安装调整更为方便。
这就要求采用新型优质材料制造数控加工刀具,并优选刀具参数设置。
铣加工工艺流程

铣加工工艺流程铣加工是一种常见的机械加工工艺,通过铣削刀具对工件进行切削加工,可以实现各种复杂形状的加工。
铣加工工艺流程包括工件准备、夹紧固定、工艺参数设置、刀具选择、加工操作等多个环节,下面将详细介绍铣加工的工艺流程。
一、工件准备。
首先需要对待加工的工件进行准备,包括清洁表面、检查工件尺寸、确定加工方向等。
清洁表面可以保证加工质量,检查工件尺寸可以确定加工余量,确定加工方向可以避免因为方向问题导致的加工误差。
二、夹紧固定。
在进行铣加工之前,需要将工件夹紧固定在工作台或夹具上,确保工件在加工过程中不会移动或晃动。
夹紧固定要求牢固可靠,不得影响加工表面的平整度和精度。
三、工艺参数设置。
在进行铣加工之前,需要根据工件材料、形状、加工要求等因素,设置合理的工艺参数,包括切削速度、进给速度、切削深度等。
合理的工艺参数可以提高加工效率,保证加工质量。
四、刀具选择。
根据工件的材料和加工要求,选择合适的铣削刀具。
不同的工件材料和加工要求需要选择不同的刀具材料、刀具形状和刀具参数,以保证加工质量和效率。
五、加工操作。
在完成以上准备工作之后,可以进行铣加工操作。
操作人员需要根据工艺要求,控制好切削速度、进给速度和切削深度,保证加工质量。
同时需要及时清理切屑,保持加工环境整洁。
六、加工检验。
在完成铣加工之后,需要对加工表面进行检验,包括尺寸检验、表面质量检验等。
通过检验可以确定加工质量是否符合要求,如果不符合要求,需要进行修磨或重新加工。
综上所述,铣加工工艺流程包括工件准备、夹紧固定、工艺参数设置、刀具选择、加工操作和加工检验等多个环节。
合理的工艺流程可以保证铣加工的质量和效率,提高加工的竞争力。
加工工艺流程范文
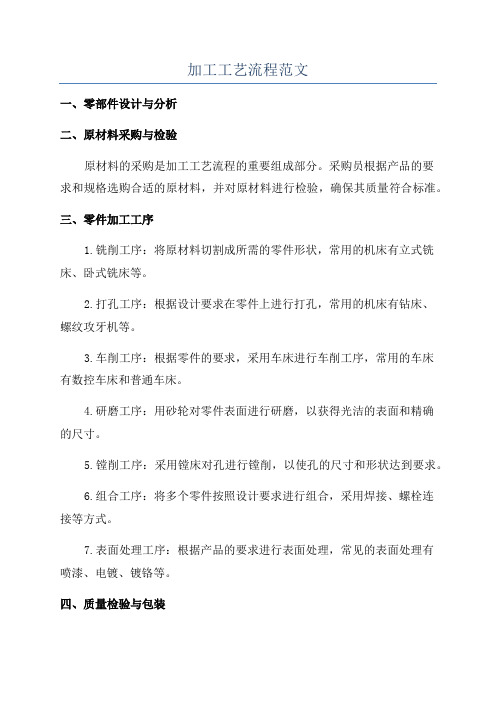
加工工艺流程范文一、零部件设计与分析二、原材料采购与检验原材料的采购是加工工艺流程的重要组成部分。
采购员根据产品的要求和规格选购合适的原材料,并对原材料进行检验,确保其质量符合标准。
三、零件加工工序1.铣削工序:将原材料切割成所需的零件形状,常用的机床有立式铣床、卧式铣床等。
2.打孔工序:根据设计要求在零件上进行打孔,常用的机床有钻床、螺纹攻牙机等。
3.车削工序:根据零件的要求,采用车床进行车削工序,常用的车床有数控车床和普通车床。
4.研磨工序:用砂轮对零件表面进行研磨,以获得光洁的表面和精确的尺寸。
5.镗削工序:采用镗床对孔进行镗削,以使孔的尺寸和形状达到要求。
6.组合工序:将多个零件按照设计要求进行组合,采用焊接、螺栓连接等方式。
7.表面处理工序:根据产品的要求进行表面处理,常见的表面处理有喷漆、电镀、镀铬等。
四、质量检验与包装在加工工艺流程的每个环节,都需要对零件进行质量检验,以确保产品的质量符合标准。
常用的质量检验方法有外观检验、尺寸检验、物理性能检验等。
检验合格的零件会进行包装,以保护零件不受损坏。
五、产品交付与售后服务经过上述一系列的加工工艺流程,最终制成的产品将进行交付给客户,并提供售后服务。
售后服务包括产品的安装、调试、保养和维修等,以确保产品在使用过程中正常运行。
以上是汽车零部件加工工艺流程的一个简单介绍。
加工工艺流程的具体内容和步骤会根据不同的产品和工艺要求而有所差异。
加工工艺流程的设计及实施需要工程师、技术员和操作工等多个部门的协作。
- 1、下载文档前请自行甄别文档内容的完整性,平台不提供额外的编辑、内容补充、找答案等附加服务。
- 2、"仅部分预览"的文档,不可在线预览部分如存在完整性等问题,可反馈申请退款(可完整预览的文档不适用该条件!)。
- 3、如文档侵犯您的权益,请联系客服反馈,我们会尽快为您处理(人工客服工作时间:9:00-18:30)。
铣削加工工艺流程分析
铣削加工是一种常见的机械加工方法,广泛应用于制造行业。
本文
将对铣削加工的工艺流程进行详细分析,并探讨其在工业生产中的应用。
一、铣削加工的定义与概述
铣削加工是指利用铣床或数控铣床对工件进行物理切削,以达到加
工目的的一种工艺方法。
铣床通过旋转刀具进行切削,同时将工件在X、Y、Z三个坐标轴上进行移动,以完成加工过程。
二、铣削加工的工艺流程分析
1. 准备工作
铣削加工前需要做好充分的准备工作。
首先,根据工件设计图纸确
定加工尺寸和要求;其次,准备好所需的铣床、夹具、刀具等设备和
工具;最后,对加工设备进行检查和调整,并确保刀具磨损情况良好。
2. 夹紧工件
将待加工的工件安装到铣床的工作台上,并通过合适的夹具进行固定。
夹紧夹具需要保证工件的稳定性和正确的加工位置,以确保加工
精度。
3. 选择合适的刀具
根据工件的材质、形状和加工要求选择合适的刀具。
刀具的选择应
综合考虑切削力、切削速度和切削质量等因素,以获得最佳的加工效果。
4. 设定切削参数
根据所选刀具和工件的特点,设定合适的切削参数,包括进给速度、转速、切削深度等。
切削参数的设定需要综合考虑加工效率和切削质
量之间的平衡。
5. 进行铣削加工
根据设定的切削参数,启动铣床,开始进行铣削加工。
在整个加工
过程中,操作人员需要密切关注加工状态,确保加工精度和安全。
6. 检验加工质量
铣削加工完成后,对加工后的工件进行检验和测量。
通过使用测量
工具,比如千分尺、游标卡尺等,对加工尺寸进行检查,以确保加工
质量符合要求。
三、铣削加工的应用领域
铣削加工广泛应用于各个制造行业,特别是机械制造和零部件加工
领域。
以下是铣削加工的一些常见应用领域:
1. 汽车制造
铣削加工在汽车制造过程中扮演着重要的角色。
通过铣削加工,可
以精确地加工汽车发动机零部件、车身结构件等,提高汽车的精度和
性能。
2. 航空航天工业
铣削加工在航空航天工业中也起到至关重要的作用。
航空发动机的
叶片、螺栓等零部件需要通过铣削加工来保证其高精度和可靠性。
3. 电子设备制造
铣削加工也被广泛应用于电子设备制造行业。
例如,手机外壳、电
脑机箱等零部件需要通过铣削加工来实现其外形精细加工和装配要求。
四、铣削加工的优势和挑战
铣削加工相比其他机械加工方法具有以下优势:
1. 灵活性高:铣削加工适用于各种复杂形状和曲面的加工需求,能
够满足各种精度和形状的零部件加工要求。
2. 高效性:铣削加工设备具有高速切削能力,能够实现高效率的加
工过程,提高生产效率。
然而,铣削加工也存在一些挑战:
1. 加工难度大:某些工件形状复杂,加工难度大,需要经验丰富的
操作人员和高精度的设备来完成。
2. 成本较高:铣削加工设备投资和维护成本较高,对企业来说是一
项较大的财务开支。
五、总结
铣削加工是一种常见的机械加工方法,通过切削工具在工件上进行切削,实现零部件的精确加工。
本文对铣削加工的工艺流程进行了详细分析,并探讨了其在各个制造领域的应用。
尽管铣削加工具有一定的挑战和成本压力,但其灵活性和高效性使其成为现代制造业中不可或缺的一部分。