型芯数控铣削加工工艺
型芯零件数控铣削加工(1)
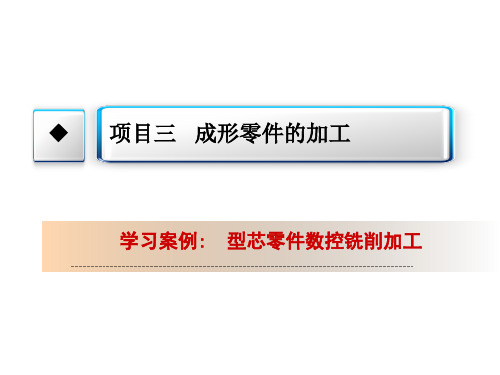
半精铣平坦面
• 由于陡壁加工无法加工干净型芯的平坦表面,这里使用曲面投影加工 平坦表面。
• 1.创建操作 • 2.指定切削区域 • 3.驱动方法 • 4.刀轨设置 • 5.操作
精铣平坦区域
• 精铣平坦面在半精铣平坦区域基础上复制进行, 具体的步骤不在详述。需要改变的主要参数如下:
• 模具型芯的加工路线为:开粗—清残料—铣顶孔—半精铣陡壁—半精 铣平坦面—精铣陡壁—精铣顶孔陡壁—精铣平坦面—清根—精铣顶 孔—精铣分型面。
CAM设置
• 模具型芯由于大部分区域为曲面,加工时 使用的CAM设置为曲面铣模板。具体步骤 如下:
• (1)启动NX6.0,打开模具型芯零件 • (2)单击【开始】|【加工】按钮,弹出
• 切换刀具为D10。 • 每一刀深度改为0.15。 • 添加加工区域(型芯边上的台阶面),清根的加工区域,如图所示。 • 1.创建操作 • 2.修改刀具 • 3.刀轨设置 • 4.操作
精铣分型面
• 由于型芯分型面为平面,因此使用表面铣加工,由于分型面上有较多 的狭窄区域。因此刀具直径不能太大,以免残料过多。
• 1.坐标系设置 • 2.创建切削几何体
创建刀具
• 本例子所需要的刀具比较多,本小节只示范D30 R2刀具的创建。具 体步骤如下:
• (1)在插入刀具条单击创建刀具图标,弹出【创建刀具】对话框。 • (2)单击选择铣刀图标。在名称栏下面输入D30R2,如图所示。 • (3)单击【确定】按钮,弹出【铣刀-5参数】对话框。刀具的参数
◆ 项目三 成形零件的加工
学习案例: 型芯零件数控铣削加工
工作任务
• 本例要加工的零件为某玩具的模具型芯,如图所示。型芯为一模两腔, 材料为420。毛坯为长方体,尺寸为254×154×87。
数控铣削加工工艺PPT课件

定中心装夹 a) 用三爪自定心卡盘装夹 b) 用两顶尖装夹 c) 用自定心虎钳装夹
ห้องสมุดไป่ตู้、组合夹具
组合夹具的基本特点是满足标准化、 系列化、 通 用化的要求,具有组合性、 可调性、 柔性、 应急性和 经济性,使用寿命长,能适应产品加工中的周期短、 成本低等要求,比较适合在加工中心上应用。
数控夹具的调整 a) 平移式 b) 回转式 c) 复合式
1—定位支撑 2—钩形压板 3, 7—滚珠丝杠副 4—步进电动机 5, 6—齿轮 8—滑座 9—活动定位销
平移式自调数控夹具
数控夹具还有哪几种? 数控车床上有吗?
5. 专用夹具
l一夹具体 2一压板 3、7一螺母 4、5一垫圈 6一螺栓 8一弹簧 9一定位键 10一菱形销 11一圆柱销
双刃镗刀分类
结构特点不同
整体式(Ⅰ和Ⅱ) 模块式 (Ⅲ和Ⅳ)
工作特点不同 尺寸是否可调
浮动式(Ⅰ) 固定式(Ⅱ,Ⅲ,Ⅳ) 可调式(Ⅰ, Ⅲ,Ⅳ)
不可调式(Ⅱ)
可转位双刃镗刀的特点及适用场合见表4—3。
(2) 镗刀刀头 分为粗镗刀刀头和精镗刀刀头。
粗镗刀刀头
精镗刀刀头
将精镗刀刀头旋转一周,刀头在半径方向 上移动多少?镗孔直径变化多少?
第一节 工件在数控铣床/ 加工中心上的装夹
一、 工件的夹紧
1. 夹紧装置应具备的基本要求
(1) 夹紧过程可靠,不改变工件定位后所占据的正确位置。 (2) 夹紧力的大小适当,既要保证工件在加工过程中其位置 稳定不变, 振动小,又要使工件不会产生过大的夹紧变形。 (3) 操作简单、 方便、 省力、 安全。 (4) 结构性好, 夹紧装置的结构力求简单、 紧凑,以便于制 造和维修。
数控铣削加工工艺分析

数控铣削加工工艺分析一、加工工艺1.工艺流程:2.加工特点:(1)高精度:数控铣削加工可以实现高精度的加工,可以满足对零件精度要求较高的应用领域;(2)加工复杂零件:数控铣削加工可以通过合理设置刀具路径和切削参数来加工复杂形状的零件,具有很大的灵活性和可塑性;(3)高效率:数控铣削加工可以实现多种刀具的自动换刀,减少了换刀时间,并且可以通过自动化程度高的设备进行连续加工,提高了生产效率;(5)适应性强:数控铣削加工适用于各种材料的加工,如金属材料、非金属材料和复合材料等。
二、优点1.精度高:数控铣削加工可以实现高精度的加工,满足对尺寸和形状要求严格的零件加工需求;2.加工效率高:数控铣削加工由于采用自动化设备和自动换刀系统,可以减少换刀和人工操作时间,提高了生产效率;3.工艺灵活性好:数控铣削加工可以通过编写不同的加工程序,实现对不同形状和尺寸的零件加工,具有很大的灵活性;4.加工质量好:数控铣削加工减少了人为因素对加工质量的影响,提高了加工质量的稳定性和一致性。
三、应用领域1.机械制造业:数控铣削加工广泛应用于机械制造业,如汽车制造、航空航天、模具制造等,用于加工复杂形状的零件;2.电子工业:数控铣削加工可用于加工电子设备的外壳和零件,提高电子产品的精度和稳定性;3.医疗器械制造业:数控铣削加工可用于制造各种形状复杂的医疗器械,如假肢、人工关节等;4.能源行业:数控铣削加工可用于加工燃气轮机等能源设备的零部件;5.其他行业:数控铣削加工还可应用于船舶制造、冶金设备制造、精密仪器制造等行业。
综上所述,数控铣削加工工艺是一种高精度、高效率的加工方法,具有工艺灵活性和加工质量好的优点。
它在各种行业中有着广泛的应用,对于加工精度要求高、形状复杂的零件是一种不可或缺的加工手段。
数控加工零件的工艺分析与数控铣削加工工艺

数控加工零件的工艺分析与数控铣削加工工艺数控加工是指利用计算机数控系统,通过编写程序控制机床工作来加工零件的一种加工方式。
在工业生产中,数控加工因其高精度、高效率、高灵活性等优点而被广泛应用。
其中数控铣削是一种常见的数控加工方式,本文将从工艺分析、数控铣削加工工艺等方面进行探讨。
一、数控加工零件的工艺分析工艺分析是数控加工的一项前置工作,它的目的是确定加工工艺,选择合适的加工设备和刀具,制定加工程序等,从而保证加工质量和效率。
具体而言,工艺分析主要包括以下几个方面:1. 零件的材质和形状:不同材质的加工性能不同,加工时需要选择相应的切削参数和刀具;而零件的形状和结构也会影响加工难度和精度,需要对其进行全面分析和评估。
2. 加工精度和表面质量要求:根据零件的要求,确定加工精度和表面质量目标,制定相应的切削参数和工艺措施。
3. 工序分析:对零件进行逐个工序分析,确定加工顺序、加工方向、加工路径和刀具选择等重要内容,同时把握好每个工序的加工质量和效率。
4. 刀具选择:根据加工材料、零件形状和要求,选择合适的刀具和刀具尺寸,保证零件的加工质量和加工效率。
5. 加工程序制定:通过数控编程软件,编写机床加工程序,包括各种切削参数、刀具路径、指令参数等信息,为数控加工提供参考。
二、数控铣削加工工艺数控铣削是一种高速旋转的刀具在工件表面上进行切削的加工方式,它广泛应用于金属、塑料等材料制件的加工中。
数控铣削在工件制作中具有大量价值和应用,且数控铣削加工工艺也是半自动化和自动化制造中的重要工艺之一。
要把好铣削的关,需要具备以下几点:1. 刀具选择:刀具的选择是影响加工效率和加工质量的重要因素之一。
首先需要考虑切削材料,选择高速钢、硬质合金、陶瓷等材质的刀具;其次要考虑刀具尺寸和形状,根据零件的要求选择合适的刀具。
2. 切削参数:切削参数包括切削速度、进给量和切削深度等,这些参数的选定与零件材料、刀具材料、刀具尺寸和表面质量等因素密切相关。
型芯零件数控铣削加工(2)

选取零件几何体后返回“铣削几何体”对话框。此时单击“指定 毛坯”按钮 ,并在打开的对话框中选中“自动块”单选按钮, 右侧显示自动块箭头,如图26所示。
图26 指定毛坯
在“操作导航器”工具栏中单击“机床视图”按钮 ,切换 导航器中的视图模式。然后在“插入”工具栏中单击“刀具” 按钮 ,打开“创建刀具”对话框。按照如图27所示的步骤新 建名称为D12R5的刀具,并设置刀具参数。
图27 创建D12R5刀具
继续单击“刀具”按钮 ,并在打开的对话框中按照如图27所 示的步骤新建名称为的D12R0.4的刀具,然后设置刀具参数。
创建D12R0.4刀具
继续单击“刀具”按钮 ,并在打开的对话框中按照如图7所示的步 骤新建名称为的D12R0.4的刀具,然后设置刀具参数。 9.在“插入”工具栏中单击“创建操作”按钮,打开“创建操作”对 话框,参数设置如图29所示,单击“确定”按钮,打开如图30所示 “型腔铣”对话框,设置加工参数。
◆ 项目三 成形零件的加工
学习案例: 型芯零件数控铣削加工
工作任务
3. 在“操作导航器”工具栏 中单击“程序顺序视图”按 钮 ,可将当前操作导航器
切换至程序视图。然后在 “插入”工具栏单击“创建 程序”按钮 ,打开“创建
程序”对话框。此时按照图 23所示的步骤创建程序父节 点,新创建的节点将位于导 航器中。 4. 在“操作导航器”工具栏 中单击“几何视图”按钮 ,
切削仿真
2)在“退刀方法”对话框中输入退刀距离值“20”,然后单击 “确定”按钮关闭该对话框,如图85所示。在“退刀运动”对 话框中输入退刀进给率的值为“1000”,如图86所示。
图85 “退刀方法”对话框
图86 “退刀运动”对话框
数控铣削加工工艺及对刀操作

3.工艺路线的确定
[3]、工序的划分
工序的划分原则:在一次装夹应尽可能完成大部分工序;尽可能 在一台机床上完成整个零件的加工。
工序的划分的几种方式
3.工艺路线的确定
刀具集中分序法
即按所用刀具划分工序,用同一把刀加工完零件上所有可以 完成的部位,在用第二把刀、第三把刀完成它们可以完成的 其它部位。
硬质合金
钨钛钴类 钨钛钽(铌)钴类
纯氧化铝类(白色陶瓷)
陶瓷
TiC添加类(黑色陶瓷)
立方碳化硼 聚晶金刚石
刀具选择
2)、数控铣削对刀具的要求 a、铣刀的刚性要好,已适用于大切削用量的要求,也可适应 切削加工中难以调整切削用量的特点。 b、铣刀的耐用度要高,使磨损减少,提高零件的表面质量与 加工精度。
刀具选择
4)、铣刀的选择
立铣刀的有关尺寸参数,推荐按下述经验数据选取。 刀具半径 R 应小于零件内轮廓面的最小曲率半径 ρ ,一般取 R=(0.8 ~ 0.9)ρ ; 零件的加工高度H≤(1/4-1/6)R, 以保证刀具有足够的刚度; 对不通孔 ( 深槽) ,选取 l=H+(5~ 10)mm(l 为刀具切削部分长度, H 为零件 高度); 加工外型及通槽时,选取l=H+r+(5~10)mm(r为端刃圆角半径); 加工筋时,刀具直径为D=(5~10)b(b为筋的厚度);
制定数 控加工 工艺 方案
确定工 步和进 给路线
选择数 控机床 的类型
数控加 工工艺 技术文 件的定 型与归 档
首件试 加工与 现场问 题处理
编写、 校验和 修改加 工程序
确定切 削参数
选择和 设计刀 具、夹 具与量 具
1.数控铣削加工内容的选择
(1)适合数控铣床加工零件:
型芯加工工艺

型芯加工工艺
1. 型芯加工工艺的概念
型芯加工工艺是指将某种材料加工成具有特定形状和尺寸的零件,用于制造模具或其他工业产品的一种加工方法。
型芯加工工艺通常需要使用高精度的加工设备和工具,以确保加工出的零件满足设计要求。
2. 型芯加工工艺的应用
型芯加工工艺在工业生产中应用广泛,特别是在模具制造、汽车零部件制造、航空航天和电子设备制造等领域。
通过型芯加工工艺,可以制造出高精度、高强度、高耐磨的零件,提高产品的质量和性能。
3. 型芯加工工艺的分类
型芯加工工艺可以分为数控加工和传统加工两种。
数控加工是指利用计算机控制的加工设备进行加工,具有高精度、高效率、高稳定性等优点。
传统加工则是指使用传统的机械加工设备进行加工,需要手工操作,加工效率较低,但是成本较低。
4. 型芯加工工艺的加工流程
型芯加工工艺的加工流程包括设计、制造型芯、选材、加工、检测等环节。
在设计阶段,需要根据产品的要求进行设计,并确定加工工艺和加工设备。
制造型芯是指根据设计图纸制造出具有特定形状和尺寸的模具零件。
选材阶段需要选择适合产品要求的材料,并进行材料加工和处理。
加工阶段是指使用加工设备进行加工,包括铣削、钻孔、磨削等工艺。
检测阶段需要对加工出的零件进行检测,以确保其质量符合要求。
5. 型芯加工工艺的发展趋势
随着科技的不断发展,型芯加工工艺也在不断发展。
未来,型芯加工工艺将更加注重高效率、高精度、高自动化的发展方向。
同时,型芯加工工艺也将更加注重环保和节能,采用新型材料和新型加工设备,提高加工效率和质量。
数控铣削加工工艺分析
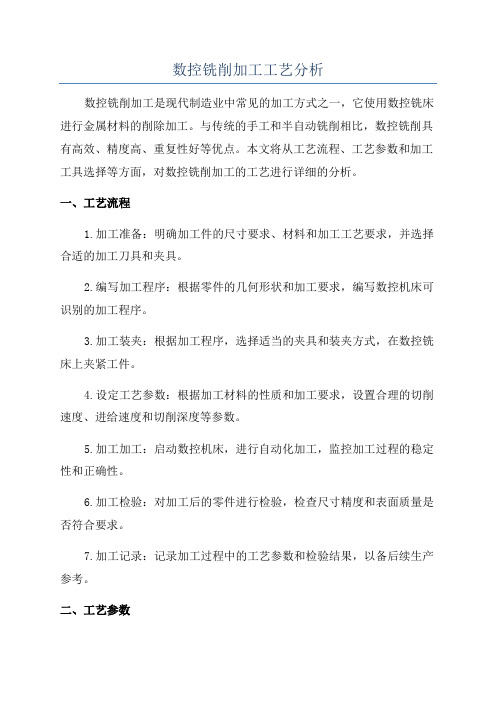
数控铣削加工工艺分析数控铣削加工是现代制造业中常见的加工方式之一,它使用数控铣床进行金属材料的削除加工。
与传统的手工和半自动铣削相比,数控铣削具有高效、精度高、重复性好等优点。
本文将从工艺流程、工艺参数和加工工具选择等方面,对数控铣削加工的工艺进行详细的分析。
一、工艺流程1.加工准备:明确加工件的尺寸要求、材料和加工工艺要求,并选择合适的加工刀具和夹具。
2.编写加工程序:根据零件的几何形状和加工要求,编写数控机床可识别的加工程序。
3.加工装夹:根据加工程序,选择适当的夹具和装夹方式,在数控铣床上夹紧工件。
4.设定工艺参数:根据加工材料的性质和加工要求,设置合理的切削速度、进给速度和切削深度等参数。
5.加工加工:启动数控机床,进行自动化加工,监控加工过程的稳定性和正确性。
6.加工检验:对加工后的零件进行检验,检查尺寸精度和表面质量是否符合要求。
7.加工记录:记录加工过程中的工艺参数和检验结果,以备后续生产参考。
二、工艺参数1.切削速度:是指刀具在单位时间内切削的长度。
根据加工材料的硬度和切削性能,合理选择切削速度,既能保证加工效率,又能保证刀具寿命。
2.进给速度:是指刀具在单位时间内在加工方向上移动的距离。
进给速度的选择应考虑切削力和切削表面的要求。
3.切削深度:是指刀具在一次进给过程中所削除的材料层厚度。
切削深度的选择应使得切削力合理,既能保证加工效率,又能避免切削表面的质量。
4.刀具半径补偿:数控铣床会自动根据刀具半径补偿值进行补偿,使得加工轮廓与设计轮廓一致。
5.加工顺序:根据零件的几何形状和切削力的分布情况,合理选择加工顺序,避免零件变形和加工过程中的切削力过大。
三、加工工具选择1.刀具材料:刀具材料应具有一定的硬度、耐磨性和耐冲击性,常用的刀具材料有硬质合金、高速钢和陶瓷等。
2.刀具形状:根据零件的几何形状和加工要求,选择合适的刀具形状,如平面铣刀、立铣刀、球头铣刀等。
3.切削刃数:根据加工材料的硬度和切削性能,选择合适的刀具刃数,既能保证加工效率,又能保证刀具寿命。
模具型芯的数控加工工艺分析
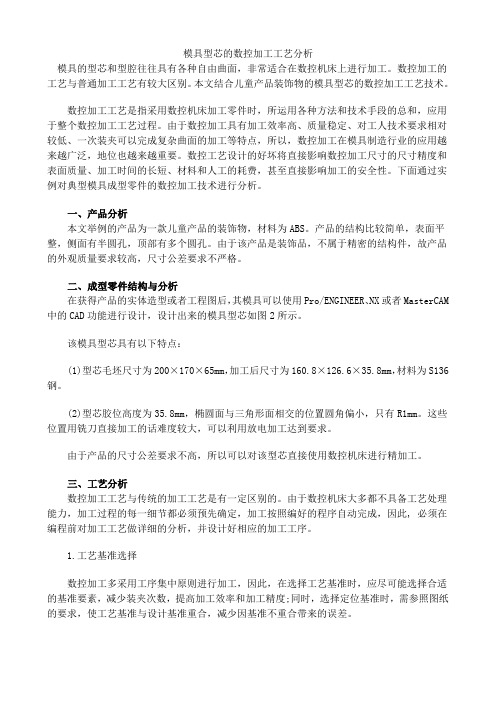
模具型芯的数控加工工艺分析模具的型芯和型腔往往具有各种自由曲面,非常适合在数控机床上进行加工。
数控加工的工艺与普通加工工艺有较大区别。
本文结合儿童产品装饰物的模具型芯的数控加工工艺技术。
数控加工工艺是指采用数控机床加工零件时,所运用各种方法和技术手段的总和,应用于整个数控加工工艺过程。
由于数控加工具有加工效率高、质量稳定、对工人技术要求相对较低、一次装夹可以完成复杂曲面的加工等特点,所以,数控加工在模具制造行业的应用越来越广泛,地位也越来越重要。
数控工艺设计的好坏将直接影响数控加工尺寸的尺寸精度和表面质量、加工时间的长短、材料和人工的耗费,甚至直接影响加工的安全性。
下面通过实例对典型模具成型零件的数控加工技术进行分析。
一、产品分析本文举例的产品为一款儿童产品的装饰物,材料为ABS。
产品的结构比较简单,表面平整,侧面有半圆孔,顶部有多个圆孔。
由于该产品是装饰品,不属于精密的结构件,故产品的外观质量要求较高,尺寸公差要求不严格。
二、成型零件结构与分析在获得产品的实体造型或者工程图后,其模具可以使用Pro/ENGINEER、NX或者MasterCAM 中的CAD功能进行设计,设计出来的模具型芯如图2所示。
该模具型芯具有以下特点:(1)型芯毛坯尺寸为200×170×65mm,加工后尺寸为160.8×126.6×35.8mm,材料为S136钢。
(2)型芯胶位高度为35.8mm,椭圆面与三角形面相交的位置圆角偏小,只有R1mm。
这些位置用铣刀直接加工的话难度较大,可以利用放电加工达到要求。
由于产品的尺寸公差要求不高,所以可以对该型芯直接使用数控机床进行精加工。
三、工艺分析数控加工工艺与传统的加工工艺是有一定区别的。
由于数控机床大多都不具备工艺处理能力,加工过程的每一细节都必须预先确定,加工按照编好的程序自动完成,因此, 必须在编程前对加工工艺做详细的分析,并设计好相应的加工工序。
毕业设计——心形凸台零件数控铣削加工工艺及其编程

毕业设计——心形凸台零件数控铣削加工工艺及其编程一、设计内容本设计旨在研究心形凸台的数控铣削加工工艺及其编程,包括零件的加工工艺、工艺参数的选择、数控铣床的编程及调试。
二、设计要求1、了解心形凸台的结构和加工要求,制定合理的加工工艺。
2、根据工艺要求,选择合适的刀具、夹具和切削参数。
3、编制加工程序,并进行调试和优化。
三、工艺分析心形凸台是一种复杂的零件,其形状如图1所示。
此处只介绍一种加工方法。
1、工艺流程(1)选材选料:选用适当材料,具有良好的切削性和耐磨性。
(2)装夹定位:采用行星卡盘强力定位固定工件。
(3)粗铣:采用双刃粗齿铣刀,从外向内进行粗加工,以提高加工效率。
(4)平面加工:采用立铣刀进行面加工。
(5)精铣:采用球头铣刀,沿着轮廓线进行铣削,最后再进行角度切削。
(6)清洗去毛刺:将零件在清洗机中清洗,去除表面毛刺。
2、加工要求(1)不允许出现毛刺、崩边等缺陷。
需要对加工后的零件进行检验,保证工件的准确度和表面质量。
(2)需要根据零件的不同形状和尺寸,选择合适的工具和加工参数,提高加工效率和工件的质量。
(3)加工过程中需要注意安全,保持加工机床干净整洁,防止发生意外事故。
四、数控编程1、数控编程流程(1)了解零件的几何形状和尺寸,制定加工方案。
(2)选择合适的工具和加工参数,设置加工程序。
(3)进行程序检查、编辑和调试,确保编程的正确性和可行性。
(4)进行自动运行,调整参数,优化加工工艺。
2、编程注意事项(1)在编写加工程序时,需要根据加工方案选取合适的刀具,设置切削速度、进给速度、切削深度和工件转速等参数。
(2)在编写程序时,需要注意保证精度和安全性,避免重复加工和出现误差。
(3)需要进行程序的检查和调试,保证程序的正确性和稳定性。
五、总结与展望在本次设计中,通过对心形凸台的加工工艺及数控编程的研究,提高了对数控铣削加工工艺的理解和掌握,加深了对加工技术的认识。
本设计还有一些不足,比如工艺方法仍可以进行更多的探索和研究,加工程序也可以进一步简化和优化,提高加工效率和质量,并且尚未考虑通用性问题。
数控铣削加工工艺与编程
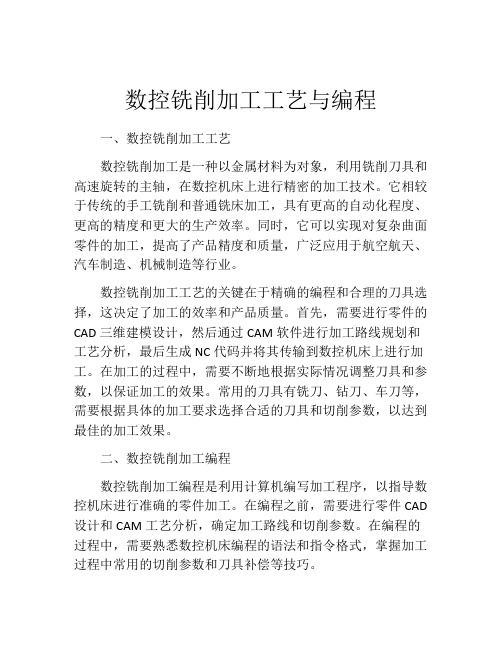
数控铣削加工工艺与编程一、数控铣削加工工艺数控铣削加工是一种以金属材料为对象,利用铣削刀具和高速旋转的主轴,在数控机床上进行精密的加工技术。
它相较于传统的手工铣削和普通铣床加工,具有更高的自动化程度、更高的精度和更大的生产效率。
同时,它可以实现对复杂曲面零件的加工,提高了产品精度和质量,广泛应用于航空航天、汽车制造、机械制造等行业。
数控铣削加工工艺的关键在于精确的编程和合理的刀具选择,这决定了加工的效率和产品质量。
首先,需要进行零件的CAD三维建模设计,然后通过CAM软件进行加工路线规划和工艺分析,最后生成NC代码并将其传输到数控机床上进行加工。
在加工的过程中,需要不断地根据实际情况调整刀具和参数,以保证加工的效果。
常用的刀具有铣刀、钻刀、车刀等,需要根据具体的加工要求选择合适的刀具和切削参数,以达到最佳的加工效果。
二、数控铣削加工编程数控铣削加工编程是利用计算机编写加工程序,以指导数控机床进行准确的零件加工。
在编程之前,需要进行零件CAD 设计和CAM工艺分析,确定加工路线和切削参数。
在编程的过程中,需要熟悉数控机床编程的语法和指令格式,掌握加工过程中常用的切削参数和刀具补偿等技巧。
编程的第一步是确定加工坐标系和切削速度。
加工坐标系是数控机床的工作坐标系,其坐标轴的方向和位置需要与零件CAD设计的坐标系一致,才能使零件加工的精度和效率最佳。
切削速度是在加工过程中刀具和工件的相对速度,需要根据刀具的刃口材料、硬度和工件材料进行调整,以达到最佳的加工效果。
其次,需要编写切削路径和刀具指令。
切削路径是指刀具在工件表面上的运动轨迹,要尽可能地减少切削时间和切削力,以保证零件表面的精度和质量。
刀具指令是指对刀具运动的详细描述,包括切削深度、切削速度、切削方向、回刀位置等。
最后,需要进行NC程序的调试和参数优化。
调试是指通过模拟运行和实物测试等手段,不断检查和调整程序的正确性和合理性,确保加工过程的稳定性和精度。
数控铣削加工工艺的主要内容

数控铣削加工工艺
数控铣削加工工艺的实质,就是在分析零件精度和表面 粗糙度的基础上,对数控铣削的加工方法、装夹方式、切削 加工进给路线、刀具选择和切削用量等工艺内容进行正确而 合理的选择。
下列加工内容比较适宜采用数控铣削加工: ① 零件上的平面曲线轮廓表面(如图所示)特别是由数学表达
① 需要进行长时间占机人工进行调整的加工和粗加工。
② 零件毛坯上的加工余量不大或者不太稳定的加工部位。
③ 必须使用细长铣刀加工的部位,一般指狭长深槽和加工精 度要求不高的筋板处连接曲线。
数控机床编程与操作
式给出的非圆曲线和列表曲线建立的空间曲线。 ② 由给出数学模型的空间曲面或通过测量数据建立起来的空间
曲面。 ③形状复杂、尺寸繁多、零件画线和检测都比较困难的零件加
工部位。
数控铣削加工工艺
④ 能够在一次装夹中铣削加工出多部位的零件表面或零件 形状。
⑤ 用普通的铣床进行加工的观察、检测困难的零件加工, 以及各种内、外凹凸槽形状的零件的加工。 ★下列内容不适宜采用数控铣削加工:
型芯数控铣削加工工艺
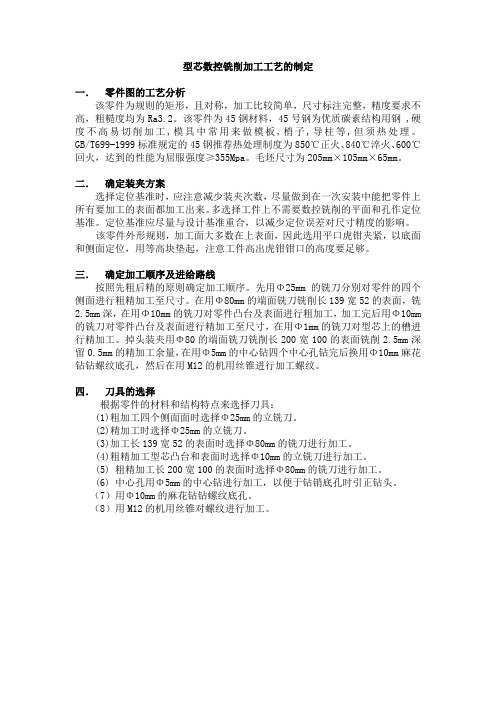
型芯数控铣削加工工艺的制定一.零件图的工艺分析该零件为规则的矩形,且对称,加工比较简单,尺寸标注完整,精度要求不高,粗糙度均为Ra3.2。
该零件为45钢材料,45号钢为优质碳素结构用钢 ,硬度不高易切削加工,模具中常用来做模板,梢子,导柱等,但须热处理。
GB/T699-1999标准规定的45钢推荐热处理制度为850℃正火、840℃淬火、600℃回火,达到的性能为屈服强度≥355Mpa。
毛坯尺寸为205mm×105mm×65mm。
二.确定装夹方案选择定位基准时,应注意减少装夹次数,尽量做到在一次安装中能把零件上所有要加工的表面都加工出来。
多选择工件上不需要数控铣削的平面和孔作定位基准。
定位基准应尽量与设计基准重合,以减少定位误差对尺寸精度的影响。
该零件外形规则,加工面大多数在上表面,因此选用平口虎钳夹紧,以底面和侧面定位,用等高块垫起,注意工件高出虎钳钳口的高度要足够。
三.确定加工顺序及进给路线按照先粗后精的原则确定加工顺序。
先用Φ25mm的铣刀分别对零件的四个侧面进行粗精加工至尺寸。
在用Φ80mm的端面铣刀铣削长139宽52的表面,铣2.5mm深,在用Φ10mm的铣刀对零件凸台及表面进行粗加工,加工完后用Φ10mm 的铣刀对零件凸台及表面进行精加工至尺寸,在用Φ1mm的铣刀对型芯上的槽进行精加工。
掉头装夹用Φ80的端面铣刀铣削长200宽100的表面铣削2.5mm深留0.5mm的精加工余量,在用Φ5mm的中心钻四个中心孔钻完后换用Φ10mm麻花钻钻螺纹底孔,然后在用M12的机用丝锥进行加工螺纹。
四.刀具的选择根据零件的材料和结构特点来选择刀具:(1)粗加工四个侧面面时选择Φ25mm的立铣刀。
(2)精加工时选择Φ25mm的立铣刀。
(3)加工长139宽52的表面时选择Φ80mm的铣刀进行加工。
(4)粗精加工型芯凸台和表面时选择Φ10mm的立铣刀进行加工。
(5) 粗精加工长200宽100的表面时选择Φ80mm的铣刀进行加工。
数控铣削加工工艺部分课件

每刃进给量0.1mm/齿,铣刀刃数10齿、 主轴转速500min-1,求工作台进给速 度?
工
每齿进给量。
(答)
艺
(答)
的
由公式、
由公式、 vf=fz×z×n=0.1×10×500=500mm/m in,
制 定
fz=Vf÷(z×n)=500÷(10×500)=0. 1mm/tooth
求出每齿进给量为0.1mm/齿
的
孔口倒角——精镗(或铰)加工方案
制
定
29
第6章 数控铣削加工工艺
课堂讨论7 :孔加工方法的选择
数
控
镗
铣 削
请仔细观察如下视频,说明零件中
加 工
各孔加工采用的是什么方法?为什么?
工
艺
的
制
定
30
第6章 数控铣削加工工艺
ห้องสมุดไป่ตู้
螺纹加工
螺纹加工方法的选择
螺纹加工主要方法: 攻螺纹、铣螺纹
数 控
内螺纹的加工根据孔径的大小,一般情
27
第6章 数控铣削加工工艺
课堂讨论6 :顺铣与逆铣
数
控
镗
铣
请仔细观察如下视频,说明铣削轮廓采用的是
削 加
顺铣还是逆铣?
工
工
艺
的
制
定
28
第6章 数控铣削加工工艺
孔加工
孔加工方法的选择
孔加工主要方法: 钻削、扩削、铰削、 铣削和镗削
数
控
孔加工的常用方法选择:
镗
对于直径大于φ30mm的已铸出或锻出的毛坯孔的孔加工,一般
立铣刀直径 : 12mm
vc
: 200m/min
毕业设计——心形凸台零件的数控铣削加工工艺及其编程

心形凸台零件的数控铣削加工工艺及其编程【摘要】本文主要介绍了心形凸台零件的数控铣削加工工艺及其编程,开篇首先介绍了数控技术的概述并对数控技术原理加以解释,紧接着对零件图进行了简要的分析并确定其加工方式,然后确定零件的毛坯、定位基准、装夹方式、刀具、量具、切削用量等等,再制定出合理的加工方案,并制定相关的工艺文件,最后编制出零件的加工程序,在编制程序时运用了自动编程与手工编程相结合的方法编制,自动编程的应用大大减少了编程时的计算量,同时也使得程序更加准确无误。
本文对本公司一项心形凸台产品阐述加工中心对其复杂形状的工件加工,主要分析了心形凸台零件的结构特点、加工要求、制定加工工艺、选择刀具夹具以及确定切削用量等。
利用数控车床高精度的特性,对于高精度要求再适合不过。
对于高精度要求的加工,位置误差的把握。
在加工中零件对尺寸的高要求,自己对数控车床使用也越发熟悉。
我相信自己一定能独立的完成一项加工。
【关键词】:数控编程;工艺分析;切削用量;加工方案;绪论错误!未定义书签。
一、零件的图样分析5(一) ..........................................................零件的结构特点分析5(二) ..........................................................零件的技术要求分析5二、零件的工艺规程设计6(一) ................................................................. 毛坯的选择6(二) ............................................................. 定位基准的选择6(三) ............................................................. 装夹方式的选择6(四) ..........................................................表面加工方法的选择6(五) ............................................................. 加工顺序的安排7(六) ............................................................. 工艺路线的确定7(1) .................................................. 可能采取的工艺路线方案7(2) ........................................................工艺路线方案比较8(3) ......................................................工艺路线的最终确定8三、设备及其工艺装备的确定9(一) ................................................................. 机床的选择9(二) ................................................................. 夹具的选择9(三) ................................................................. 刀具的选择9四、切削用量的选取11五、工艺卡片11(一) ................................................................. 工艺过程卡11(二) ............................................................. 数控加工工序卡12六、数控加工程序的编制13(一) ............................................................. 编程方法的选择13(二) ............................................................编程坐标系的确定13(三) ............................................................... 加工程序清单13引言本课题来源于丹阳市永和铝材有限公司。
数控铣削加工工艺及对刀操作PPT课件

进给速度的选择同样重要,过快或过 慢的进给速度都可能导致加工质量下 降或损坏刀具。
切削深度的选择
切削深度
根据工件材料、铣刀直径和加工要求等参数,合理选择切削深度,以确保切削 效率和加工质量。
总结
切削深度的选择对切削效率和加工质量均有影响,过大的切削深度可能导致刀 具损坏或加工质量下降。
刀具的选择与使用
05
数控铣削加工的未来发展与挑战
数控铣削加工技术的发展趋势
80%
智能化
随着人工智能和机器学习技术的 不断发展,数控铣削加工将更加 智能化,能够实现自适应加工和 智能优化。
100%
高效化
为了提高加工效率和降低成本, 数控铣削加工将不断优化切削参 数和加工路径,实现高效、高精 度的加工。
80%
柔性化
随着个性化需求的增加,数控铣 削加工将更加柔性化,能够快速 适应不同工件和加工需求的调整 。
数控铣削加工面临的挑战与问题
加工精度要求高
随着产品质量的不断提高,对 数控铣削加工的精度要求也越 来越高,如何保证高精度加工 是当前面临的重要问题。
切削参数优化
切削参数的优化是提高数控铣 削加工效率和加工质量的关键 ,但如何实现切削参数的合理 匹配和优化仍是一个挑战。
引入智能化技术
利用人工智能和机器学习技术,实现 加工过程的自适应控制和智能优化, 提高加工效率和精度。
THANK YOU
感谢聆听
详细描述
数控铣削加工是指利用数控机床进行铣削加工的一种技术,通过 计算机控制机床的运动和切削参数,实现高精度、高效率、高柔 性的加工。相比于传统铣削加工,数控铣削加工具有更高的加工 精度和更广泛的加工范围,能够满足各种复杂零件的加工需求。
- 1、下载文档前请自行甄别文档内容的完整性,平台不提供额外的编辑、内容补充、找答案等附加服务。
- 2、"仅部分预览"的文档,不可在线预览部分如存在完整性等问题,可反馈申请退款(可完整预览的文档不适用该条件!)。
- 3、如文档侵犯您的权益,请联系客服反馈,我们会尽快为您处理(人工客服工作时间:9:00-18:30)。
型芯数控铣削加工工艺的制定
一.零件图的工艺分析
该零件为规则的矩形,且对称,加工比较简单,尺寸标注完整,精度要求不高,粗糙度均为Ra3.2。
该零件为45钢材料,45号钢为优质碳素结构用钢 ,硬度不高易切削加工,模具中常用来做模板,梢子,导柱等,但须热处理。
GB/T699-1999标准规定的45钢推荐热处理制度为850℃正火、840℃淬火、600℃回火,达到的性能为屈服强度≥355Mpa。
毛坯尺寸为205mm×105mm×65mm。
二.确定装夹方案
选择定位基准时,应注意减少装夹次数,尽量做到在一次安装中能把零件上所有要加工的表面都加工出来。
多选择工件上不需要数控铣削的平面和孔作定位基准。
定位基准应尽量与设计基准重合,以减少定位误差对尺寸精度的影响。
该零件外形规则,加工面大多数在上表面,因此选用平口虎钳夹紧,以底面和侧面定位,用等高块垫起,注意工件高出虎钳钳口的高度要足够。
三.确定加工顺序及进给路线
按照先粗后精的原则确定加工顺序。
先用Φ25mm的铣刀分别对零件的四个侧面进行粗精加工至尺寸。
在用Φ80mm的端面铣刀铣削长139宽52的表面,铣2.5mm深,在用Φ10mm的铣刀对零件凸台及表面进行粗加工,加工完后用Φ10mm 的铣刀对零件凸台及表面进行精加工至尺寸,在用Φ1mm的铣刀对型芯上的槽进行精加工。
掉头装夹用Φ80的端面铣刀铣削长200宽100的表面铣削2.5mm深留0.5mm的精加工余量,在用Φ5mm的中心钻四个中心孔钻完后换用Φ10mm麻花钻钻螺纹底孔,然后在用M12的机用丝锥进行加工螺纹。
四.刀具的选择
根据零件的材料和结构特点来选择刀具:
(1)粗加工四个侧面面时选择Φ25mm的立铣刀。
(2)精加工时选择Φ25mm的立铣刀。
(3)加工长139宽52的表面时选择Φ80mm的铣刀进行加工。
(4)粗精加工型芯凸台和表面时选择Φ10mm的立铣刀进行加工。
(5) 粗精加工长200宽100的表面时选择Φ80mm的铣刀进行加工。
(6) 中心孔用Φ5mm的中心钻进行加工,以便于钻销底孔时引正钻头。
(7)用Φ10mm的麻花钻钻螺纹底孔。
(8)用M12的机用丝锥对螺纹进行加工。
数控加工刀具卡片
五.切削用量的选择
切削用量是依据零件材料特点、刀具性能及加工精度要求确定。
本零件加工时切削速度取40~60m/min,粗铣时取低一些,精铣时取高一些,进给速度取60mm/min。
槽深5mm,铣削余量分5次完成,每次背吃刀量取0.5mm,剩下1mm 同精铣一起完成。
加工孔和螺纹时根据实际情况选择切削速度与每转进给量。
六.填写数控加工工序卡
型芯的数控加工工序卡片如下表所示。
型芯数控加工工序卡。