福特-8D工作法PDF.pdf
2020年整理福特-8D工作法.pdf

8D报告百科名片8D又称团队导向问题解决方法、8D问题求解法(8D Problem Solving)是福特公司处理问题的一种方法,亦适用于制程能力指数低於其应有值时有关问题的解决,它提供了一套符合逻辑的解决问题的方法,同时对於统计制程管制与实际的品质提升架起了一座桥梁。
简介8D最早是美国福特公司使用的经典质量问题分析手法。
二战期间,美国政府率先采用一种类似8D的流程——“军事标准1520”,又称之为“不合格品的修正行动及部署系统”。
1987年,福特汽车公司首次用书面记录下8D法,在其一份课程手册中这一方法被命名为“团队导向的问题解决法”(Team Oriented Problem Solving)。
当时,福特的动力系统部门正被一些经年累月、反复出现的生产问题搞得焦头烂额,因此其管理层提请福特集团提供指导课程,帮助解决难题。
问题解决8步法8D(8 Disciplines)问题解决8步法8D的原名叫做8 Disciplines,意思是8个人人皆知解决问题的固定步骤。
原始是由Ford公司,全球化品质管制及改善的特殊必备方法,之后已成为QS9000/ISO TS16949、福特公司的特殊要求。
凡是做FORD 的零件,必须采用8D 作为品质改善的工具,目前有些企业并非 FORD 的供应商或汽车业的合作伙伴,也很喜欢用这个方便而有效的方法解决品质问题,成为一个固定而有共识的标准化问题解决步骤。
Discipline 1. 成立改善小组(Form the Team):由议题之相关人员组成,通常是跨功能性的,说明团队成员间的彼此分工方式或担任的责任与角色。
Discipline 2. 描述问题(Describe the Problem):将问题尽可能量化而清楚地表达,并能解决中长期的问题而不是只有眼前的问题。
Discipline 3. 实施及确认暂时性的对策(Contain the Problem):对于解决 D2 之立即而短期行动,避免问题扩大或持续恶化,包含清库存、缩短PM时间、加派人力等。
福特-8D工作法

8D报告百科名片8D又称团队导向问题解决方法、8D问题求解法(8D Problem Solving)是福特公司处理问题的一种方法,亦适用于制程能力指数低於其应有值时有关问题的解决,它提供了一套符合逻辑的解决问题的方法,同时对於统计制程管制与实际的品质提升架起了一座桥梁。
简介8D最早是美国福特公司使用的经典质量问题分析手法。
二战期间,美国政府率先采用一种类似8D的流程——“军事标准1520”,又称之为“不合格品的修正行动及部署系统”。
1987年,福特汽车公司首次用书面记录下8D法,在其一份课程手册中这一方法被命名为“团队导向的问题解决法”(Team Oriented Problem Solving)。
当时,福特的动力系统部门正被一些经年累月、反复出现的生产问题搞得焦头烂额,因此其管理层提请福特集团提供指导课程,帮助解决难题。
问题解决8步法8D(8 Disciplines)问题解决8步法8D的原名叫做8 Disciplines,意思是8个人人皆知解决问题的固定步骤。
原始是由Ford公司,全球化品质管制及改善的特殊必备方法,之后已成为QS9000/ISO TS16949、福特公司的特殊要求。
凡是做FORD 的零件,必须采用8D 作为品质改善的工具,目前有些企业并非FORD的供应商或汽车业的合作伙伴,也很喜欢用这个方便而有效的方法解决品质问题,成为一个固定而有共识的标准化问题解决步骤。
Discipline 1. 成立改善小组(Form the Team):由议题之相关人员组成,通常是跨功能性的,说明团队成员间的彼此分工方式或担任的责任与角色。
Discipline 2. 描述问题(Describe the Problem):将问题尽可能量化而清楚地表达,并能解决中长期的问题而不是只有眼前的问题。
Discipline 3. 实施及确认暂时性的对策(Contain the Problem):对于解决D2 之立即而短期行动,避免问题扩大或持续恶化,包含清库存、缩短PM时间、加派人力等。
8D方法(Ford版)

D5.选择和验证(yànzhèng)基本缘由和 遗漏点的PCA〔续〕
设计(shèjì)验证和报告〔DVP&R〕 FMEA 稳健设计(shèjì)
第十六页,共23页。
D6.实施(shíshī)和确认PCA
• 战略性效果
• 有列出纠正措施的有效性吗?
• 有效性经过验证(yànzhèng)了吗?
第三页,共23页。
8 D(8 Disciplines)(续)
需求时,辅导供方实施整个8D进程以识别系统的基本 缘由:
列出完成8D 进程的工具〔例如:DOE、SPC、 FMEA、散点图、反省单、控制图等等〕;
验证供方运用了适当的工具; 识别当评审8D报告时须讯问的8D进程; 验证供方能否准确执行和文件化8D进程; 确保供方经过启动和封锁效果曾阅历证了基本缘由, 验证供方已完整(wánzhěng)包括一切可疑资料,包括曾经 在装配工厂、运输中、仓库和进程中的零件。
8D方法(fāngfǎ)(Ford 版)
2021/11/9
第一页,共23页。
8 D(8 Disciplines)
福特汽车公司运用8D作为效果处置的方法〔见QS-9000要 求之4.14.1.1〕。当福特的供方具有零件或进程的效果时, 福特要求供方完成8D进程以确定缘由并实施纠正措施 (cuòshī)。 目的:
第十三页,共23页。
D4.定义和验证基本(jīběn)缘由和遗漏 点〔续〕
效果,或效果的征兆或结果被作为基本缘由给出。 质量工具
因果(yīnguǒ)图 FMEA 是/否剖析 实验验证〔DOE〕 稳健设计
第十四页,共23页。
D5.选择和验证基本(jīběn)缘由和遗漏 点的PCA
• 战略性效果 • 措施的日期(rìqī)能否指示? • 声明的措施能否掩盖一切进程的基本缘由? • 声明的措施能否掩盖一切系统的基本缘由? • 措施能否思索效果的时间? • 措施能否充沛思索条件? • 措施能否思索效果的大小? • 质量工具 • 因果图
8d (2)

8D问题解决法简介8D(Eight Disciplines)问题解决法是一种用于解决问题和处理缺陷的系统性方法。
它由福特汽车公司在20世纪80年代发展而来,后来被广泛应用于其他行业。
8D问题解决法以其简单、结构化和有效的特点而受到许多组织的欢迎,特别是在质量管理领域。
问题解决法的八个步骤1. D1 确认问题在D1步骤中,团队需要明确问题的范围和性质。
这是解决问题的第一步,要确保整个团队对问题有一致的理解。
团队成员应该集中精力了解问题的背景、根本原因和可能的影响。
确认问题的关键是要明确、具体和可衡量。
2. D2 组成团队在D2步骤中,需要组建一个跨职能的团队来解决问题。
团队应该包括专业知识和技能各异的成员,以确保从各个角度综合考虑问题。
团队成员应该具备问题解决和团队合作的能力。
3. D3 制定紧急措施在D3步骤中,团队需要采取紧急措施来避免问题进一步恶化。
这些措施应该是迅速、简单和有效的,以减少问题对组织的影响。
团队应该制定具体的行动计划,并明确责任人和截止日期。
4. D4 根本原因分析在D4步骤中,团队需要深入分析问题的根本原因。
这需要使用一些工具和技术,如鱼骨图、5W1H等。
团队应该通过不断提问和追溯问题的根源,找到引起问题的核心因素。
5. D5 制定长期措施在D5步骤中,团队需要制定长期措施来根除问题的根本原因。
这些措施应该是可持续的,并能够防止问题再次发生。
团队应该考虑采取措施的可行性、成本效益和风险。
6. D6 确认措施有效性在D6步骤中,团队需要验证和确认实施的措施是否有效。
这可能需要进行实验、统计和数据分析。
团队应该收集和分析相关数据,并评估措施的效果。
7. D7 未来预防措施在D7步骤中,团队需要制定未来预防措施,以避免类似问题的再次发生。
这些措施可能包括培训、流程改进等。
团队应该考虑如何改进组织的系统和文化,以提高问题解决的能力。
8. D8 团队总结和表彰在D8步骤中,团队需要总结整个问题解决过程,并给予团队成员适当的表彰和奖励。
8D报告步骤通俗完整讲解(附标准范本)

8D报告通俗讲解(附标准范本)8D 报告精品培训完整的8D报告标准范本.xlsx ——附件Excel 可直接打开保存 Issue#问题编号:8D-20180801QCustomer 客户:MD生活电器Date Issue Occurred 问题发生日期:2018.08.03Product 产品:FS4034上盖Date Issue Closed 问题关闭日期:2018.08.10Champion Name 负责人姓名Champion Title 负责人职位Champion Phone Number 负责人电话Champion E-mail Address 负责人电子邮件XXX副总经理XXXXXXXXXXX XXX Team Member Name(s)其他成员姓名Title(s)职位Phone Number(s)电话E-mail Address(es)电子邮件XXX品质部经理XXXXXXXXXXX XXX XXX生产部经理XXXXXXXXXXX XXX XXX质量工程师XXXXXXXXXXX XXX XXX 生产车间主管XXXXXXXXXXX XXXAffected Document 相关文件Owner for Update 责任人负责更新Date 日期FMEAXXX 2018.8.15BOM无/Control Plan 控制计划XXX 2018.8.15Drawing 图纸无/Design Standards 设计标准无/Congratulation 肯定团队Closure Statement 关闭声明Verification of Corrective Action: Has the issue been turned on and off? How? Verification through staticalevidence / hypothesis testing. Verification of corrective action for each why made and why shipped is required.纠正措施的确认:该问题处于开启状态还是关闭状态?怎样?通过证据确认/假设检验.针对每个产生的原因和被发运原因的纠正措施都要确认。
福特8D培训-含案例(中文)

123456789
12 6789
9
!"#$ %& '()*
+, '()*
-.89
/012345%&6&5127889
9:8;< !=>?@89
ABC D
EFGH+, I9J01
123456789
12567 !"#$%&'( )6*
1 345678 9
! "#$%!&' 1 )*+, 1 -./012 3 4 5
123456789
123456 89
34
! "# ! $1 % % % 7
( ! 5 %1 ) 7 9 ! " " % ' ' $ * ) " " % & ' % " % . 9 & ' %1 % / % 7
3 1 4 % ) ' % $ ) %
* 7 5 1 ) % 1 % / % 5 & % 5 3 1 ' 67 8 9 '
1234568 9
12 68 9 9 12 68 9
3 5 5 5 89
5 5 5 5 88 5 5 5 88 5 5 5! "88 # $5 5 5 5 ! %88
123456789
福特-8D工作法
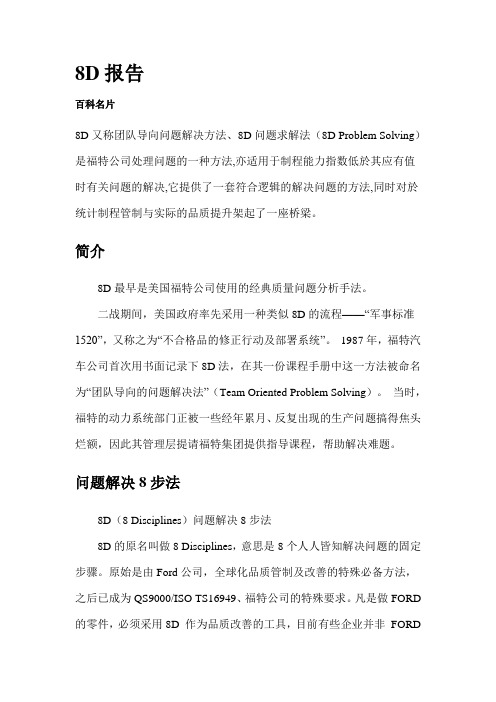
8D报告百科名片8D又称团队导向问题解决方法、8D问题求解法(8D Problem Solving)是福特公司处理问题的一种方法,亦适用于制程能力指数低於其应有值时有关问题的解决,它提供了一套符合逻辑的解决问题的方法,同时对於统计制程管制与实际的品质提升架起了一座桥梁。
简介8D最早是美国福特公司使用的经典质量问题分析手法。
二战期间,美国政府率先采用一种类似8D的流程——“军事标准1520”,又称之为“不合格品的修正行动及部署系统”。
1987年,福特汽车公司首次用书面记录下8D法,在其一份课程手册中这一方法被命名为“团队导向的问题解决法”(Team Oriented Problem Solving)。
当时,福特的动力系统部门正被一些经年累月、反复出现的生产问题搞得焦头烂额,因此其管理层提请福特集团提供指导课程,帮助解决难题。
问题解决8步法8D(8 Disciplines)问题解决8步法8D的原名叫做8 Disciplines,意思是8个人人皆知解决问题的固定步骤。
原始是由Ford公司,全球化品质管制及改善的特殊必备方法,之后已成为QS9000/ISO TS16949、福特公司的特殊要求。
凡是做FORD 的零件,必须采用8D 作为品质改善的工具,目前有些企业并非FORD的供应商或汽车业的合作伙伴,也很喜欢用这个方便而有效的方法解决品质问题,成为一个固定而有共识的标准化问题解决步骤。
Discipline 1. 成立改善小组(Form the Team):由议题之相关人员组成,通常是跨功能性的,说明团队成员间的彼此分工方式或担任的责任与角色。
Discipline 2. 描述问题(Describe the Problem):将问题尽可能量化而清楚地表达,并能解决中长期的问题而不是只有眼前的问题。
Discipline 3. 实施及确认暂时性的对策(Contain the Problem):对于解决D2 之立即而短期行动,避免问题扩大或持续恶化,包含清库存、缩短PM时间、加派人力等。
福特(Ford)8D培训教材

也不要写工作报告
Page 10 of 47
成员包括:
❖ 指导员(CHAMPION) 一般为主管阶层,对小组的进度有 监督, 支持及决策决定 权力.
❖ 组长(LEADER)-负责协调,活动进行的引导,汇总小组的意 见及决策并呈报,尽量不要深入某部份细节,以免迷失方向.
❖ 问5次为什么的做法:
➢对于某个问题,为何会引起?其原因①先搞明白。 ➢为何会引起原因①的发生?将原因②也搞清楚。 ➢为何会引起原因②的发生?将原因③弄明白。 ➢为何会引起原因③的发生?将原因④弄明白。 ➢为何会引起原因④的发生?将原因⑤弄明白。
Page 20 of 47
❖ 用这种方式持续地去做,根本的原因就能显現出来。 ❖ 分析出来的根本的原因必须是能导出具有効果、
且有効率的再发防止对策才行。 ❖ 要注意的是问题发生的原因不一定只有一个。
❖ 通常第一个答案不会是真正的答案 ❖ 5 Why 可以找出真正的原因 ❖ 简单的案子可能4Why,3Why或2Why即找出根本原
因,但复杂的或许要5 Why, 6 Why, 7 Why…
Page 21 of 47
做5 Why 分析时应注意事项
因会影响结果时,不能说有因果关系)。
Page 23 of 47
5 Why 范例: 为何停机
❖ 问1:为什么机器停了? 答1:因为机器超载, 保险丝烧断了
❖ 问2:为什么机器会超载? 答2: 因为轴承的润滑不足
❖ 问3:为什么轴承会润滑不足? 答3: 因为润滑系统失灵了
❖ 问4: 为什么润滑系统会失灵? 答4: 因为润滑系统的轮轴耗损了
8D实施方法含实例

D6、验证纠正措施
1. 换完电线后,至今尚没有发现连接点松动的迹象。 2. 断开电流接触器的电路进行试验,一旦电压不正常,转子 将自动停止工作,直至没电镀的产品从线上取下。 以上工作,小组共同进行了验证,并提请顾客事先的批准。
32
D7、防止再发生的措施
❖电镀工作指导书被修改增加了如下内容: 1)当生产线不正常停止时,操作者不仅要挑选出缺陷产品 ,而且要在工作记录记下数量及当班QC的名字。 2)在电镀线在每天早上启动前,电流接触器的连接点和电 线必须检查。以上,由杨星在12月15日完成。 ❖开发一个包括每天需检查事项的检查清单,例如生产线停 止,不管缺陷产品是否被挑选,制造部和QA需进行审核。 ❖ 依次类推,如果有类似问题,该小组负责纠正并采取适当 的预防措施。
检查数量
状态 缺陷数量
MT001206 19308片
19308片
OK
0
MT001208 14274片
14274片
OK
0
总计
33582片
33582片
OK
0
•2. 我们对操作者进行培训和教育,以让其知道最重要的事情:
•遵守工作程序和指导书以保持顾客产品质量。使其意识到他们在 产品质量保证中的重要职责。我们强调,任何由于不小心引起的错 误是不允许的并且不能重复发生,因为那样将会给顾客带来不必要 的损失。因此我们把给顾客造成损失的错误展示以教育员工。
生管课、销售课、库管课、品保课 • 责属人员:
贾正羽、庄卫年、赵晓明、许 丽
36
D2.问题描述
• 何时 : 1999年11月4日; • 何人 : 浙江精密机械厂; • 何地 : 浙江精密机械厂—包装车间; • 何事 : 包装ALT-5检测器时,使用20μMHT
长安福特8D培训(PDF139页)

Global 8DWelcome课程内容章节:8D过程及分析工具概述D0全球8D过程的准备D1 组建团队D2 陈述问题D3制定ICAs(临时措施)D4 确定并验证根本起因和问题逃出点D5选择并验证PCAs(永久措施)D6 执行并确认PCAs(永久措施)D7 预防问题重现D8 奖励团队及个人的贡献Course Objectives课程目标完成这门课程之后你应该能够:•描述G8D流程的每个步骤•以一个G8D团队成员的身份有效地参与到你的工作中去•帮助福特达到其远景目标:通过提供优秀的产品和令顾客满意的服务成为世界上汽车制造业的主导公司Overview of the G8D Process全球8D过程概述•福特汽车公司解决问题的标准流程•包括8个步骤,再加上一个准备步骤•客观地描述、确定以及解决问题•防止类似的问题再次发生Phases of the G8D Process全球8D过程的阶段•D0 G8D过程的准备•D1 组建团队•D2 描述问题•D3 制定ICAs(临时措施)•D4 确定,并验证根本原因和问题逃出点•D5选择和验证解决根本原因和遗漏点的永久措施(PCAs)•D6 执行并确认PCAs(永久措施)•D7 预防问题的重新发生•D8 奖励团队及个人的贡献Types of Problem situations问题的类型问题有两种类型:•变异引起的问题•从未满足要求的问题Summary 总结•G8D过程概述•G8D过程的阶段•问题的类型D0D0 –“准备G8D”•描述紧急反应措施•确定是否需要紧急反应措施•区别验证和确认•选择、验证、执行以及确认紧急反应措施•确定是否使用G8D过程来解决问题紧急反应措施(ERA)是保护顾客及相关的各方不受症状影响的任何措施,它在确认G8D是否有必要启动时应用。
Emergency Response Actions 紧急反应措施Problems vs. symptoms问题与症状•G8D把症状和问题区分开来•症状是可测量的事件或效果(它们必须是顾客体验到的),它表示一个或多个问题存在•如果没有症状,你就无法得知有问题存在Using Tools to Measure andQuantify Symptoms使用工具测量并量化症状•当症状能被测量或量化时,它才被考虑在内•在福特,通常有许多工具可以用来测量并量化故障---Paynter Chart / Paynter图---Pareto /柏拉图---Run (trend) chart / 运行(趋势)图Paynter charts / Paynter图•帮助追踪一个或多个症状•显示产品作用的效果•以图形或数据表格的形式表示Pareto柏拉图•柏拉图根据成本或是频率将所有潜在问题区域或是问题源排列出来•柏拉图有助于将几个重要数据从一列琐碎的数据中挑选出来Run (Trend) Chart趋势图•趋势图提供了过程随时间变化的信息•趋势图用来辨别数据变化趋势或数据变化状况Determine the need for an ERA确定是否需要ERA•ERA不是一直都必须•应该根据问题的严重性和它对顾客产生的影响来决定是否需要采取ERA•它是基于目前现有的信息而制定的措施•它可能是大到影响停止所有发运,也可能是小到什么都不用做•它是一个须立即执行的措施——你不必花太多时间来研究应急措施(ERA)Select and Verify an ERA选择并验证ERA•为确保ERA可以保护顾客,需要对他进行验证以保证按照期望的方式工作并且还不会产生新的失效模式•你可以在非生产件如样件或是通过计算机模拟的方式对一个ERA进行验证Implement & Validate of an ERA执行并确认ERA在顾客之前的确认包括:•测试•检查•观察•产品和过程中的质量检查顾客确认包括:•三包分析(Paynter图)G8D Application CriteriaG8D的适用标准要实施G8D需要满足七个标准:1.症状被定义2.确定了顾客3.存在性能差距4.原因未知5.管理层致力于从根本起因的层面去解决问题,并采取预防措施防止问题再次发生6.症状很复杂,不可能单凭一个人的能力完成7.问题在别的场所没有发生D0 Summary: /D0总结Prepare for Global 8D/ 准备G8D在这一阶段我们关注了:•用G8D的应用标准来判断是否需要采用G8D来解决问题•选择、验证、实施并确认ERAD1D1 –“Establish the Team”D1-组建团队为什么组建团队?•建立一个团队是G8D过程的真正开始•D1阶段的目的是组建一个团队,并且这个团队有能力和激情去解决一个问题Guidelines for Team Membership团队成员的指导方针当确定团队成员时:•团队成员的人数控制在4到10个之间•选择具有所需技能、知识、资源、权力等,这样的人作为团队成员来解决现有的问题•各类成员之间合理搭配•按需要调整团队成员Team Roles团队角色•团队成员应该以高效率的方式工作•G8D的过程依赖于所有团队成员的努力来达到团队的目标•为达到团队目标,每个成员扮演一个角色The Champion负责人•负责人是一个有权制定(和执行)关于临时措施、永久措施和预防措施的人,他/她在整个过程中支持团队解决问题The Champion负责人•设置优先权•指派团队完成G8D•帮助团队排除部门之间的障碍、获取需要的资源•创造授权环境•与团队一起评估检查清单•行使权利执行团队的建议•作为G8D团队和组织的联系点•转递G8D报告给有关的部门•负责人应该主持第一个会议说明这里需要的是么和对团队的期望是什么The Team Leader团队领导•团队领导是一个在整个G8D过程中负责领导团队成员的人,这个人有领导能力和人际关系的技能The Team Leader团队领导•领导团队成员完成G8D目标•担当团队的事务管理者•与团队一起制定目标和任务•询问和总结团队成员的意见•提出会议和团队活动的议程•主持会议•对G8D过程提出问题(不提供答案)•依照已制定的团队规则管理团队•作为主要联系点支持负责人The Team Member团队成员•团队成员是那些因为自己的经验和知识而被选中参加G8D团队的人,他们是各方面的专家,在团队里可以不履行其他的职责,在G8D过程中团队成员可能会改变The Team Member团队成员•进行调查工作•提出计划•使用他们的判断力、技能、经验和知识•找出答案•在每个G8D步骤提出建议•执行措施Other Roles其它角色•时间管理者•抄写员•调解员Guidelines for Implementing Team Roles实现团队角色的指导方针•角色不是特指某个人,而是指要行使的职责•成员通常要在会议持续期间或是更长的时间内充当某个固定的角色•会议中角色的互换会导致混乱•一些角色是可以共同扮演的•当一个团队领导人提出一项评论时,她或他就自动的偏离了领导这个角色•Champion是G8D流程中的一个角色但不认为是一个团队成员Team Operating Procedures团队运作程序团队运作程序的三个要素:•确定团队运作的基本规则•分配任务、维护和过程观察•使用有效沟通交流的技巧D1 Summary / D1总结本章节我们介绍了如何:•描述确定团队成员的原则•描述团队角色和职责、以及它们如何发挥作用•解释团队运作流程的三个要素D2D2 –“Describe the Problem”D2-“描述问题”•D2驱动G8D的其他步骤,因为在D2中,将问题清楚并且客观的描述会使问题最终得到有效的解决•D2帮助团队将焦点放在实际的问题上,避免直接对问题下结论或者作没有根据的设想D2 Section ObjectivesD2阶段目标•解释描述问题的流程•识别与问题相关的流程图•对问题进行陈述•对问题进行描述•作为描述问题的数据库•驱动了G8D的其他阶段D2 阶段帮助你将焦点放在现有问题上,以避免非常低的效率解决问题:•它帮助你尽可能准确的定义问题Why Describe the Problem?为什么要描述问题?Observations vs. Conclusions观测与结论当你描述一个问题时,你只是观测还是得出了结论?这两者是有很大的区别。
8D福特适用

CONFIDENTIAL – Disclosure or duplication without consent is prohibited.
17
D5: Corrective Action
1. Owner and due date: 2. Owner and due date: 3. Owner and due date: 4. Owner and due date: 5. Owner and due date: 6. Owner and due date:
15
D4: Root Cause
5-WHY
Root cause:
WHY
WHY
WHY
CONFIDENTIAL – Disclosure or duplication without consent is prohibited.
16
D4: Root Cause
Verify root cause
WHY
10
D4: Root Cause
Verify root cause
CONFIDENTIAL – Disclosure or duplication without consent is prohibited.
11
D4: Root Cause
5-WHY
Root cause:
WHY
WHY
WHY
CONFIDENTIAL – Disclosure or duplication without consent is prohibited.
3
D3: Containment Action/Short Term action
CONFIDENTIAL – Disclosure or duplication without consent is prohibited.
ford-G8D福特公司8D培训资料
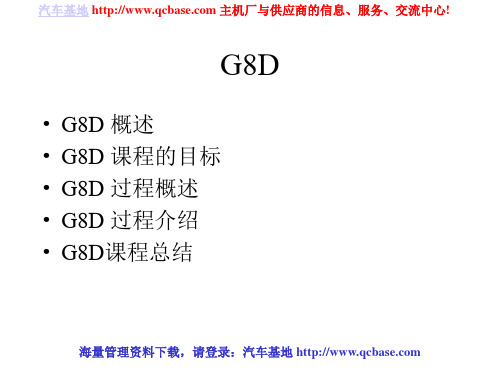
汽车基地 主机厂与供应商的信息、服务、交流中心!
G8D过程概述(续)
• D3 开发临时控制行动。
– 定义、验证和执行临时控制行动以将问题的 影响同内部和外部的顾客隔离开。临时行动 将执行到永久修正计划采用为止。证实临时 行动的有效性.。
G8D概述
• G8D是福特公司解决问题的标准方法。 • 由8个步骤和一个准备步骤组成。 • 这些步骤用来客观地确定、定义和解决 问题并防止相似问题的再次发生。
海量管理资料下载,请登录:汽车基地
汽车基地 主机厂与供应商的信息、服务、交流中心!
D0 准备G8D
• 为什么要为G8D过程作准备
– G8D的过程是很精深的。可能涉及大量的时间、人 员和资源。当然也会浪费大量的时间、人员和资源, 如果使用G8D过程是不合适的。 – G8D的使用标准帮助判别使用G8D过程是合适的。 如果不使用G8D的标准来判定是否使用G8D,那么, 您可能用精深的过程来解决每一个单一的问题。 – 福特公司的最终目标是在卓越的产品和顾客满意度 方面居于行业领先。D0允许执行(ERA)来保护顾 客。ERA也是保持顾客满意度和达到我们目标的重 要部分。
海量管理资料下载,请登录:汽车基地
汽车基地 主机厂与供应商的信息、服务、交流中心!
D0 准备G8D
• 紧急反应行动(ERA)
– 紧急反应行动是在决定是否采用G8D时用来 保护顾客和受影响的各方的任何行动。 – 顾客是经历症状的一个人、组织或驾驶员。 例如,一个驾驶员由于空调问题将车开来维 修,驾驶员就是顾客。 – 受影响的各方是指将被症状影响的人、组织 或驾驶员。例如,处理空调保修的服务人员 是受影响的各方。
• D8 表彰个人和小组的贡献
- 1、下载文档前请自行甄别文档内容的完整性,平台不提供额外的编辑、内容补充、找答案等附加服务。
- 2、"仅部分预览"的文档,不可在线预览部分如存在完整性等问题,可反馈申请退款(可完整预览的文档不适用该条件!)。
- 3、如文档侵犯您的权益,请联系客服反馈,我们会尽快为您处理(人工客服工作时间:9:00-18:30)。
8D报告百科名片8D又称团队导向问题解决方法、8D问题求解法(8D Problem Solving)是福特公司处理问题的一种方法,亦适用于制程能力指数低於其应有值时有关问题的解决,它提供了一套符合逻辑的解决问题的方法,同时对於统计制程管制与实际的品质提升架起了一座桥梁。
简介8D最早是美国福特公司使用的经典质量问题分析手法。
二战期间,美国政府率先采用一种类似8D的流程——“军事标准1520”,又称之为“不合格品的修正行动及部署系统”。
1987年,福特汽车公司首次用书面记录下8D法,在其一份课程手册中这一方法被命名为“团队导向的问题解决法”(Team Oriented Problem Solving)。
当时,福特的动力系统部门正被一些经年累月、反复出现的生产问题搞得焦头烂额,因此其管理层提请福特集团提供指导课程,帮助解决难题。
问题解决8步法8D(8 Disciplines)问题解决8步法8D的原名叫做8 Disciplines,意思是8个人人皆知解决问题的固定步骤。
原始是由Ford公司,全球化品质管制及改善的特殊必备方法,之后已成为QS9000/ISO TS16949、福特公司的特殊要求。
凡是做FORD 的零件,必须采用8D 作为品质改善的工具,目前有些企业并非 FORD 的供应商或汽车业的合作伙伴,也很喜欢用这个方便而有效的方法解决品质问题,成为一个固定而有共识的标准化问题解决步骤。
Discipline 1. 成立改善小组(Form the Team):由议题之相关人员组成,通常是跨功能性的,说明团队成员间的彼此分工方式或担任的责任与角色。
Discipline 2. 描述问题(Describe the Problem):将问题尽可能量化而清楚地表达,并能解决中长期的问题而不是只有眼前的问题。
Discipline 3. 实施及确认暂时性的对策(Contain the Problem):对于解决 D2 之立即而短期行动,避免问题扩大或持续恶化,包含清库存、缩短PM时间、加派人力等。
Discipline 4. 原因分析及验证真因(Identify the Root Cause):发生 D2 问题的真正原因、说明分析方法、使用工具(品质工具)的应用。
Discipline 5. 选定及确认长期改善行动效果(Formulate and Verify Corrective Actions):拟订改善计划、列出可能解决方案、选定与执行长期对策、验证改善措施,清除 D4 发生的真正原因,通常以一个步骤一个步骤的方式说明长期改善对策,可以应用专案计划甘特图(Gantt Chart),并说明品质手法的应用。
Discipline 6. 改善问题并确认最终效果(Correct the Problem and Confirm the Effects):执行 D5 后的结果与成效验证。
Discipline 7. 预防再发生及标准化(Prevent the Problem):确保 D4 问题不会再次发生的后续行动方案,如人员教育训练、改善案例分享(Fan out) 、作业标准化、产出BKM、执行FCN 、分享知识和经验等。
Discipline 8. 恭喜小组及规划未来方向(Congratulate the Team):若上述步骤完成后问题已改善,肯定改善小组的努力,并规划未来改善方向。
8D适用范围该方法适用于解决各类可能遇到的简单或复杂的问题;8D方法就是要建立一个体系,让整个团队共享信息,努力达成目标。
8D本身不提供成功解决问题的方法或途径,但它是解决问题的一个很有用的工具;亦适用于过程能力指数低于其应有值时有关问题的解决;面对顾客投诉及重大不良时,提供解决问题的方法。
8D法是美国福特公司解决产品质量问题的一种方法,曾在供应商中广泛推行,现已成为国际汽车行业(特别是汽车零部件产家)广泛采用来解决产品质量问题最好的、有效的方法。
8D工作方法的8个步骤8D是解决问题的8条基本准则或称8个工作步骤,但在实际应用中却有9个步骤:D0:征兆紧急反应措施D1:小组成立D2:问题说明D3:实施并验证临时措施D4:确定并验证根本原因D5:选择和验证永久纠正措施D6:实施永久纠正措施D7:预防再发生D8:小组祝贺D0:征兆紧急反应措施目的:主要是为了看此类问题是否需要用8D来解决,如果问题太小,或是不适合用8D来解决的问题,例如价格,经费等等,这一步是针对问题发生时候的紧急反应。
关键要点: 判断问题的类型、大小、范畴等等。
与D3不同,D0是针对问题发生的反应,而D3是针对产品或服务问题本身的暂时应对措施。
D1:小组成立目的:成立一个小组,小组成员具备工艺/产品的知识,有配给的时间并授予了权限,同时应具有所要求的能解决问题和实施纠正措施的技术素质。
小组必须有一个指导和小组长。
关键要点: 成员资格,具备工艺、产品的知识;目标 ;分工 ;程序 ;小组建设D2:问题说明目的:用量化的术语详细说明与该问题有关的内/外部顾客抱怨,如什么、地点、时间、程度、频率等。
“什么东西出了什么问题”方法:质量风险评定,FMEA分析关键要点:收集和组织所有有关数据以说明问题;问题说明是所描述问题的特别有用的数据的总结;审核现有数据,识别问题、确定范围;细分问题,将复杂问题细分为单个问题;问题定义,找到和顾客所确认问题一致的说明,“什么东西出了什么问题”,而原因又未知风险等级。
D3:实施并验证临时措施目的:保证在永久纠正措施实施前,将问题与内外部顾客隔离。
(原为唯一可选步骤,但发展至今都需采用)方法:FMEA、DOE、PPM关键要点: 评价紧急响应措施;找出和选择最佳“临时抑制措施”;决策 ;实施,并作好记录;验证(DOE、PPM分析、控制图等)D4:确定并验证根本原因目的:用统计工具列出可以用来解释问题起因的所有潜在原因,将问题说明中提到的造成偏差的一系列事件或环境或原因相互隔离测试并确定产生问题的根本原因。
方法:FMEA、PPM、DOE、控制图、5why法关键要点: 评估可能原因列表中的每一个原因;原因可否使问题排除;验证;控制计划D5:选择并验证永久纠正措施目的:在生产前测试方案,并对方案进行评审以确定所选的校正措施能够解决客户问题,同时对其它过程不会有不良影响。
方法:FMEA关键要点: 重新审视小组成员资格;决策,选择最佳措施;重新评估临时措施,如必要重新选择;验证;管理层承诺执行永久纠正措施;控制计划D6:实施永久纠正措施目的:制定一个实施永久措施的计划,确定过程控制方法并纳入文件,以确保根本原因的消除。
在生产中应用该措施时应监督其长期效果。
方法:防错、统计控制关键要点: 重新审视小组成员;执行永久纠正措施,废除临时措施;利用故障的可测量性确认故障已经排除;控制计划、工艺文件修改D7:预防再发生目的:修改现有的管理系统、操作系统、工作惯例、设计与规程以防止这一问题与所有类似问题重复发生。
关键要点:选择预防措施;验证有效性;决策 ;组织、人员、设备、环境、材料、文件重新确定D8:小组祝贺目的:承认小组的集体努力,对小组工作进行总结并祝贺。
关键要点: 有选择的保留重要文档;流览小组工作,将心得形成文件;了解小组对解决问题的集体力量,及对解决问题作出的贡献;必要的物质、精神奖励。
对8D工作方法的评价1.优点发现真正肇因的有效方法,并能够采取针对性措施消除真正肇因,执行永久性矫正措施。
能够帮助探索允许问题逃逸的控制系统。
逃逸点的研究有助于提高控制系统在问题再次出现时的监测能力。
预防机制的研究有助于帮助系统将问题控制在初级阶段。
2.缺点8D培训费时,且本身具有难度。
除了对8D问题解决流程进行培训外,还需要数据挖掘的培训,以及对所需用到的分析工具(如帕累托图、鱼骨图和流程图,等等)进行培训。
[1]参考资料8D报告百科名片8D又称团队导向问题解决方法、8D问题求解法(8D Problem Solving)是福特公司处理问题的一种方法,亦适用于制程能力指数低於其应有值时有关问题的解决,它提供了一套符合逻辑的解决问题的方法,同时对於统计制程管制与实际的品质提升架起了一座桥梁。
目录1.简介8D最早是美国福特公司使用的经典质量问题分析手法。
二战期间,美国政府率先采用一种类似8D的流程——“军事标准1520”,又称之为“不合格品的修正行动及部署系统”。
1987年,福特汽车公司首次用书面记录下8D法,在其一份课程手册中这一方法被命名为“团队导向的问题解决法”(Team Oriented Problem Solving)。
当时,福特的动力系统部门正被一些经年累月、反复出现的生产问题搞得焦头烂额,因此其管理层提请福特集团提供指导课程,帮助解决难题。
问题解决8步法8D(8 Disciplines)问题解决8步法8D的原名叫做8 Disciplines,意思是8个人人皆知解决问题的固定步骤。
原始是由Ford公司,全球化品质管制及改善的特殊必备方法,之后已成为QS9000/ISO TS16949、福特公司的特殊要求。
凡是做FORD 的零件,必须采用8D 作为品质改善的工具,目前有些企业并非 FORD 的供应商或汽车业的合作伙伴,也很喜欢用这个方便而有效的方法解决品质问题,成为一个固定而有共识的标准化问题解决步骤。
Discipline 1. 成立改善小组(Form the Team):由议题之相关人员组成,通常是跨功能性的,说明团队成员间的彼此分工方式或担任的责任与角色。
Discipline 2. 描述问题(Describe the Problem):将问题尽可能量化而清楚地表达,并能解决中长期的问题而不是只有眼前的问题。
Discipline 3. 实施及确认暂时性的对策(Contain the Problem):对于解决 D2 之立即而短期行动,避免问题扩大或持续恶化,包含清库存、缩短PM时间、加派人力等。
Discipline 4. 原因分析及验证真因(Identify the Root Cause):发生 D2 问题的真正原因、说明分析方法、使用工具(品质工具)的应用。
Discipline 5. 选定及确认长期改善行动效果(Formulate and Verify Corrective Actions):拟订改善计划、列出可能解决方案、选定与执行长期对策、验证改善措施,清除 D4 发生的真正原因,通常以一个步骤一个步骤的方式说明长期改善对策,可以应用专案计划甘特图(Gantt Chart),并说明品质手法的应用。
Discipline 6. 改善问题并确认最终效果(Correct the Problem and Confirm the Effects):执行 D5 后的结果与成效验证。