弯曲工艺与弯曲模设计.pptx
模具设计与制造第6章弯曲工艺与模具设计

06
总结与展望
弯曲工艺与模具设计的现状与挑战
现状
随着制造业的快速发展,弯曲工艺与模具设计在产品制造中占据重要地位。目前,弯曲工艺与模具设 计已经取得了长足进步,能够满足多种复杂形状的加工需求。
挑战
然而,在弯曲工艺与模具设计过程中,仍存在一些挑战,如高精度控制、复杂曲面加工、高效自动化 等方面的问题。
未来发展方向与技术前沿
柔性制造技术
随着个性化需求的增加,柔性制造技术将成为未 来发展的重点。通过柔性制造技术,可以实现快 速、高效、个性化的产品制造,提高生产效率和 降低成本。
增材制造技术
增材制造技术是一种基于数字模型的快速成型技 术,能够实现复杂形状的高精度加工。未来,增 材制造技术有望在弯曲工艺与模具设计中发挥更 大的作用。
模具材料的选择蚀性等。
常用材料
碳素工具钢、合金工具钢、硬质合金、铸铁等。
材料处理
热处理、表面处理等。
模具设计的流程与方法
设计流程
明确设计任务→收集设计资料→设计 出图→审查→修改。
设计方法
经验设计法、解析设计法、计算机辅 助设计法等。
04
弯曲工艺与模具设计的关系
THANK YOU
模具设计对弯曲工艺的影响
模具结构
模具的结构对弯曲工艺的实施具 有重要影响,合理的模具结构可 以提高弯曲效率并降低不良品率。
模具材料
模具材料的选取直接影响弯曲工艺 的效果,选用高强度、耐磨和耐热 的材料可以提高模具的使用寿命和 弯曲质量。
冷却系统
模具中的冷却系统对于控制弯曲过 程中的温度至关重要,合理的冷却 系统设计可以减少热应力,提高产 品质量。
02
弯曲工艺的基本原理
弯曲变形的过程与特点
弯曲模设计PPT课件
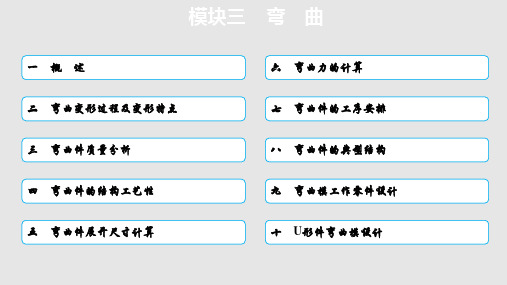
模块三 弯 曲
重点
1. 弯曲变形规律及弯曲件质量影响因素; 2. 弯曲工艺计算方法; 3. 弯曲工艺性分析与工艺方案制定; 4. 弯曲模典型结构与结构设计; 5. 弯曲工艺与弯曲模设计的方法和步骤。
模块三 弯 曲
难点
1.弯曲变形规律及弯曲件质量影响因素; 2.影响回弹的因素与减少回弹的措施 ; 3.弯曲工艺计算; 4.弯曲模典型结构与弯曲模工作零件设计。
三 弯曲件质量分析
(二) 弯裂与最小相对弯曲半径的控制
3
最小弯曲半径rmin的数值
三 弯曲件质量分析
(二) 弯裂与最小相对弯曲半径的控制
4
防止弯裂的措施
不宜采用最小弯曲半径。当零件的弯曲半径小于表3-1所列数值时,为了提高极限弯曲变形程度, 防止弯裂,常采用的措施有退火、加热弯曲、消除冲裁毛刺、两次弯曲(先加大弯曲半径,退火后 再按工件要求小弯曲半径弯曲)、校正弯曲以及对较厚的材料开槽后弯曲。
三 弯曲件质量分析
(三) 弯曲卸载后的回弹
5
减小回弹的措施
(2)从工艺上采取措施 ①采用校正弯曲代替自由弯曲。对冷作硬化的材料先退火,降低其屈服极限σs,以减小回弹,弯曲后再 淬硬。
②采用拉弯代替一般弯曲方法。拉弯的工艺特点是弯曲 之前使坯料承受一定的拉伸应力,其数值使坯料截面内的 应力稍大于材料的屈服强度,随后在拉力作用下同时进行 弯曲。
三 弯曲件质量分析
(三) 弯曲卸载后的回弹
4
回弹值的确定
方法: 先根据经验数值和简单的计算来初步确定模具工作部分尺寸,然后在试模时进行修正。 (1)大变形程度( <5)自由弯曲时的回弹值
卸载后弯曲件圆角半径的变r化/是t很小的,可以不予考虑,而仅考虑弯曲中心角的回弹变化。
弯曲工艺与弯曲模设计

四、通用折彎模
折彎模典型結構
對於小批生產或試制生產的零件,一般採用通用折彎模。 圖3.8.20是經多次V形折彎製造複雜零件的例子。 圖3.8.21是折彎機上用的通用折彎模。 圖3.8.22為通用V形折彎模。 圖3.8.23為通用U形、 形件折彎模結構簡圖。
折彎模結構設計
一、折彎模結構設計應注意的問題
折彎模典型結構
一、單工程折彎模(續)
2.U形件折彎模
圖a所示為開底凹模,用於底部不要求平整的製件。圖b用 於底部要求平整的折彎件。圖c用於料厚允差較大而外側尺 寸要求較高的折彎件,其凸模為活動結構,可隨料厚自動調 整凸模橫向尺寸。圖d用於料厚允差較大而內側尺寸要求較 高的折彎件,凹模兩側為活動結構,可隨料厚自動調整。
折彎工藝與折彎模設計
By TTDC 2008/08/14
折彎的應用為何?
折彎的應用為何?
折彎的應用為何?
折彎的應用為何?
折彎工藝與折彎模設計
1.有哪些因素影響彎曲的工藝性? 2.彎曲件毛坯展開尺寸計算的依據是什麼? 3.彎曲力如何計算?
折彎件的工程安排
彎曲件的工程安排應根據工件形狀、精度等級、生產批量以 及材料的力學性質等因素進行考慮。彎曲工程安排合理,則 可以簡化模具結構、提高工件質量和勞動生產率。
折彎件的工程安排
一、折彎件的工程安排原則
1.形狀簡單的折彎件:採用一次折彎成形; 形狀複雜的折彎件:採用二次或多次折彎成形。
2.批量大而尺寸較小的折彎件: 盡可能採用級進模或複合模。
3.需多次折彎時: 先彎兩端,後彎中間部分,前次折彎應考慮後次折彎有可
靠的定位,後次折彎不能影響前次已成形的形狀。
4.折彎件形狀不對稱時: 盡量成對折彎,然後再剖切(圖3.7.1)
弯曲工艺与模具设计PPT课件

2. 最小相对弯曲半径及其影响因素
最小相对弯曲半径是指板料弯曲时最外层纤维濒于拉裂时的弯曲半径与板料厚度
的比值
影响最小相对弯曲半径的因素:
1)材料的力学性能:塑性好, rmin/t
小。 2)板料的纤维方向:弯曲线与纤维方向
二、最小弯曲半径值确定 1.最小弯曲半径的近似理论计算
二、最小弯曲半径值确定 2.最小弯曲半径的经验值确定
由于影响最小弯曲半径大小的因素很多,因此计算结果与 实际的rmin有一定的误差,在实际生产中主要是参考经验数据来 确定各种材料的最小弯曲半径。
三、提高弯曲极限变形程度方法
1.弯曲件分两次弯曲,第一次采用较大的弯曲半径(大于 rmin),第二次按要求的弯曲半径弯曲。
接的影响。间隙小,回弹减小。相反,当间隙较大时,材料处 于松动状态,工件的回弹就大。
2. 影响回弹的因素
1)材料的力学性能:屈服极限越大、硬化指数越高,回弹量越大; 弹性模量越大,回弹越小。
2)相对弯曲半径:越大,回弹越大。 3)弯曲中心角:越大,变形区的长度越长,回弹积累值也越大,
故回弹增加。 4)弯曲方式 :校正弯曲的回弹比自由弯曲时大为减小。 5)工件形状: 形状越复杂、一次弯曲的角度越多,回弹越小。 6)模具结构: 带底凹模的回弹小。
弯曲中心角α越大,表示弯曲变形区的长度越长,回弹积 累值也越大,故回弹角Δα越大,但对弯曲半径的回弹影响不大。
二、影响回弹的因素 4.弯曲方式及校正力大小
自由弯曲时的回弹角要比校正弯曲来得大,这是因为校 正弯曲时,材料受到凸、凹模的压缩作用,不仅使弯曲变形 区毛坯外侧的拉应力有所减小,并且在外侧靠近中性层附近 的切向也出现和毛坯内侧切向一样的压缩应力。随着校正力 的增加,切向压应力区向毛坯的外表面不断扩展,以致毛坯 的全部或大部分断面均产生切向压缩应力。这样内、外层材 料回弹的方向取得一致,使其回弹量比自由弯曲时大为减少。 因此校正力越大,回弹值越小。
第3章 弯曲工艺与弯曲模具
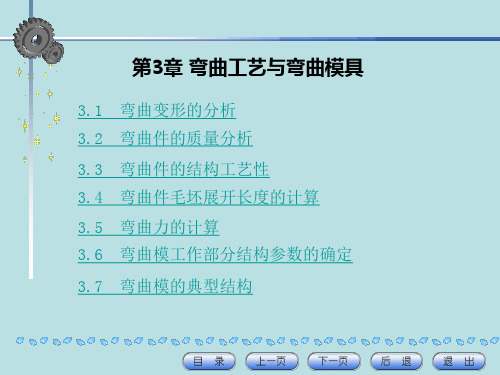
总之影响最小弯曲半径的主要因素如下:
⒈ 材料的机械性能;
⒉ 板材纤维的方向性;
⒊ 弯曲件的宽度; ⒋ 板材的表面质量和剪切断面质量;
⒌ 弯曲角;
⒍ 板材的厚度。 最小弯曲半径可按表3-1选取
表3-1 最小弯曲半径rmi
3.2.2、弯曲时的回弹及控制回弹的措施 1、弯曲回弹现象 弯曲回弹现象产生于弯曲变形结束后的卸载过程,是由其内部产生 的弹性回复力矩造成的。弯曲件卸载后的回弹,表现为弯曲件的弯曲 半径和弯曲角的变化,如图3-6所示。
(a )
(b ) (c) 图3-25 防止尖角处撕裂的措施
0 绪论 一、冲压概念
图3-26所示的零件,根据需要设置了工艺孔、槽及定位孔。图(a) 所示工件弯曲后很难达到理想的直角,甚至在弯曲过程中变宽、开 裂。如果在弯曲前加工出工艺缺口(M×N),则可以得到理想的弯 曲件。图(b)所示的工件,在弯曲处预先冲制了工艺孔,效果与 图(a)相同。图(c)所示的工件,要经过多次弯曲,图中的D是 定位工艺孔,目的是作为多次弯曲的定位基准,虽然经多次弯曲, 该零件仍保持了对称性和尺寸精度,
0 绪论 一、冲压概念
凸模下行,减小到r/t>200时,板料处于线形弹塑性状态,
即板料中心几附近区域为弹性变形,其他部分为塑性变形, 弯曲进行至r/t值大约在(200>r/t>5)时,板料进入线形全塑
性弯曲状态。
当其进一步减小到r/t3~5时,则为立体塑性弯曲,此即模 具弯曲最终状态。
• 窄板(b/t3)弯曲时,宽度 方向可以自由变形,故其应 力b0,内外层的应变状态 是立体的,应力状态是平面 的。 • 宽板(b/t>3)弯曲时,由于 宽度方向材料不能自由变形 (宽度基本不变),即
模具设计第3章弯曲工艺与弯曲模课件

b/t<3窄板弯曲,断面产生了 畸变 ,外窄内宽
3.1.4 弯曲件的结构工艺性
弯曲件的结构工艺性是指弯曲零件的形状、 尺寸、精度、材料以及技术要求等是否符合弯 曲加工的工艺要求。具有良好工艺性的弯曲件, 能简化弯曲的工艺过程及模具结构,提高工件 的质量。
1. 弯曲件的形状 弯曲件形状对称,对应r 相等
播放动画
1-顶杆 2-定位钉 3-模柄 4-凸模 5-凹模 6-下模座
3. L形件弯曲 适用于两直边长度相差较大的单角弯曲件
a)竖边无校正
b)竖边可校正
L形件弯曲
4.复杂零件 多次V形弯曲制造复杂零件举例
3.2.2 U形件弯曲模
1.U形件弯曲模的一般结构形式
U 形 件 弯 曲 模
1.凸模 2.凹模 3.弹簧 4.凸模活动镶块 5.凹模活动镶块 6.定位销 7.转轴 8.顶板 9.凹模活动镶块
弯曲半径r>0.5t: 按中性层不变原理,坯料总长度应等于弯曲 件直线部分和圆弧段长度之和,即:
提问:下面的弯曲件展开长度如何计算?
L
l1
l2
l3
π α1 180
(r1
xt
)
π α2 180
S / E 越大,回弹越大。
E1>E2
1 2
.
1 2
图a)
E3=E4
3 4
3 4
图b)
材料的力学性能对回弹值的影响 1、3-退火软钢 2-软锰黄铜 4-经冷变形硬化的软钢
应尽量选择屈服极限小、n值小的材料以获得 形状规则、尺寸精确的弯曲件。
(2)相对弯曲半径r/t r/t越小,变形程度越大,回弹量减小。
例:1mm厚铝板、65Mn板,弯曲时易裂,退火后 再弯,则弯曲正常。
弯曲工艺与模具设计

第三章弯曲工艺与模具设计弯曲是使材料(板料、棒料、管材等)产生塑性变形,形成具有一定角度或一定曲率零件的冲压工艺。
它属于成形工序,是冲压的基本工序之一,各种常见弯曲件如图4-1所示。
根据所使用的工具及设备的不同,可以把弯曲工序分为使用模具在普通压力机上进行的压弯及在专门的弯曲设备上进行的折弯、滚弯、拉弯等。
虽然各种弯曲方法使用的工具及设备不同,但其变形过程和变形特点有共同规律。
(【1】p108)第一节弯曲变形过程及特点一、弯曲变形过(本节内容摘自【2】p148)V形弯曲是最基本的弯曲变形,任何复杂弯曲都可以看成是由多个v形弯曲组成。
所以以v形弯曲为代表分析弯曲变形的过程。
弯曲过程中,当坯料上受到凸模压力(弯曲力矩)时,坯料的曲率半径会发生变化。
图4-3所示为一副常见的v形件弯曲。
其弯曲过程简述如下:弯曲开始前,先将平板毛坯放入模具定位板中定位,然后凸模下行,实施弯曲,直到板料与凸模、凹模完全贴紧(此时冲床下行至下死点),然后开模(此时冲床上行至上死点),再从模具中取出v形件。
其受力情况如图4-4所示,弯曲过程分析如图4-5所示。
在板材A处,凸模施加外力2F,在凹模支撑点B1,B2处则产生反力与这外力构成了弯曲力矩M=FxL,该我弯曲力矩使板材产生弯曲变形。
弯曲变形可分成弹性变形阶段、塑性变形阶段和矫正弯曲阶段。
(1)弹性变形阶段:在凸模的压力下,板料受弯曲力矩M的作用,坯料变形区应力最大的内、外表面的材料没有产生变形,变形区内的材料仅产生弹性变形,且是自由弯曲,此时如果消除弯曲力矩时,坯料将恢复原状。
如图4-5(a)所示。
(2)塑性变形阶段:坯料变形区内、外表面的应力分量满足塑性条件,进入塑性变形状态。
此时如果消除弯曲力矩时,坯料将不能恢复原状。
随着凸模进一步下行,塑性变形有表面向中心进一步扩展。
板料与凹模v形表面逐渐靠紧,同时曲率半径和曲率力臂逐渐变小,即r0>r1>r2>r k,L0>L1>L2>L k。
弯曲工艺与弯曲模设计(ppt 68页)

3. 塑性弯曲阶段
当凸模到达下止 点时,毛坯被紧 紧地压在凸模与 凹模之间,使毛 坯内侧弯曲半径 与凸模的弯曲半 径吻合,完成弯 曲过程,变形由 弹—塑性弯曲过 渡到塑性弯曲。
•5
弯曲分类
自由弯曲 校正弯曲
当弯曲过程结束,凸模、凹模、毛 坯三者相吻合后,凸模不再下压的 弯曲工序,回弹量较大。
当弯曲过程结束,凸模、凹模、毛 坯三者相吻合后,凸模继续下压, 产生刚性镦压,使毛坯产生进一步 塑性变形,从而对弯曲件的弯曲变 形部分进行校正的弯曲工序。
7,8-活动凹模;10-下模座;11-滚柱
•22
4.2.3 帽形件弯曲模
1.使用两套U形弯曲模
图 4-19 两次弯曲成形
•23
2.一次弯曲成形
有回弹。较少 使用此方法
图 4-20 一次弯曲成形
图 4-21 复合弯曲模一次弯曲成形
1-凸凹模;2-活动凸模;3-凹模;4-顶板
•24
4.2.4 Z形件弯曲模
图 4-17 使用回转凹模的U形件弯曲模
1-凸模;2-定位板;3-弹簧;4-回转凹模;5-限位钉
•21
使用斜楔的U形件弯曲模
弹簧将毛坯先弯曲 成U形。受弹簧弹力 限制,该结构只适
用于弯曲薄板。
图 4-18 使用斜楔结构的U形件弯曲模
1-斜楔;2-凸模支杆;3,9-弹簧;4-上模座;5-凸模;6-定位销;
2)校正法 校正压力集中施加在弯曲变形区,使其塑性变形成 分增加,弹性变形成分减小,从而使回弹量减小。
图 4-31 校正法示意图
•35
4.4 弯曲工艺计算
4.4.1 弯曲件展开长度的计算
弯曲件展开长度的计算 依据弯曲件的形状、弯 曲半径、弯曲方向的不 同而不同。
- 1、下载文档前请自行甄别文档内容的完整性,平台不提供额外的编辑、内容补充、找答案等附加服务。
- 2、"仅部分预览"的文档,不可在线预览部分如存在完整性等问题,可反馈申请退款(可完整预览的文档不适用该条件!)。
- 3、如文档侵犯您的权益,请联系客服反馈,我们会尽快为您处理(人工客服工作时间:9:00-18:30)。
图 4-5 中性层位置的确定
中性层弯曲半径,mm; r 弯曲半径,mm; t 材料厚度,mm; x 中性层位移系数,x小于0.5,可查表确定。
3.变形区厚度和板料长度
弯曲中性层向内偏移。中性层内移的结果是: 内层纤维长度缩短,导致厚度增加;外层纤
当r / t 4时: 维拉长,厚度相应减薄。由于厚度增加量小
3. 塑性弯曲阶段
当凸模到达下止 点时,毛坯被紧 紧地压在凸模与 凹模之间,使毛 坯内侧弯曲半径 与凸模的弯曲半 径吻合,完成弯 曲过程,变形由 弹—塑性弯曲过 渡到塑性弯曲。
弯曲分类
自由弯曲 校正弯曲
当弯曲过程结束,凸模、凹模、毛 坯三者相吻合后,凸模不再下压的 弯曲工序,回弹量较大。
当弯曲过程结束,凸模、凹模、毛 坯三者相吻合后,凸模继续下压, 产生刚性镦压,使毛坯产生进一步 塑性变形,从而对弯曲件的弯曲变 形部分进行校正的弯曲工序。
第四章 弯曲工艺与弯曲模
学习目标 了解弯曲工艺及弯曲件的结构工艺性分析; 理解弯曲变形过程分析; 理解弯曲件的质量问题及防止措施; 掌握弯曲工艺设计和弯曲模具典型结构组 成及工作过程分析。
4.1 弯曲工艺及弯曲件工艺性
4.1.1 弯曲工艺
1. 弯曲
弯曲是指把金属坯料弯成一定角度或形状的过程,是 冲压生产中应用较广泛的一种工艺。弯曲时所使用的 模具称为弯曲模。
以避开尺寸突变处,并满足 b t;h t r b / 2
图 4-12 止裂孔、止裂槽
6.弯曲件的尺寸标注和精度
尺寸标注 注意事项
尺寸标注时要考虑弯曲工艺的特点,尽量避免对由 于回弹和变形而引起的变形区进行尺寸标注。
精度要求 不高于IT13级,角度公差大于 15'
图 4-13 孔位置标注
4.2 弯曲模典型结构
图 4-8 弯曲方向对弯曲半径的影响
3.弯曲件的直边高度
直边高度H过小,那么直边在弯曲模上支承的长度也过 小,不易形成足够的弯矩,弯曲件的形状难以控制。
H 2t
当弯曲边带有斜 度时,应保证
如果
可加大直边高度,待弯
H 2t 曲成形后,再将直边的
高出部分切除。
H (2 ~ 4)t,且H 3mm
于变薄量,因此板料总厚度在弯曲变形区内 变薄。同时,由于体积不变,故变形区的变 薄使板料长度略有增加。
4.变形区横断面的变形
b/t 3
b/t 3
窄板
弯曲时,宽度方向的变形不受约束。 由于弯曲变形区外侧材料受拉而引 起板料宽度方向收缩,内侧材料受 压引起板料宽度方向增厚,其横断 面形成外窄内宽的扇形。
2. 弯曲方法
方法: 压弯、折弯、滚弯、拉弯 使用设备:
压力机、折弯机、滚弯机(卷板机)、 拉弯机等。
图 4-1 弯曲方法示意图
4.1.2 弯曲变形过程
1.弯曲的开始阶段
弯曲圆角半径r很大, 弯曲力矩很小,仅引 起材料的弹性变形。 随着凸模进入凹模深 度的增大,凹模与板 料的接触位置发生变 化,弯曲力臂ι逐渐 减小,弯曲圆角半径 也随之逐渐减小。
图 4-9 直边高度要求
4.弯曲件孔边距 设孔边到弯曲半径r的中心的最小距离为s
t 2mm s t 不满足 t 2mm s 2t
先弯曲后冲孔或改变零件形状; 增加工艺孔
图 4-10 弯曲件孔边距
图 4-11 防止孔变形的措施
5.止裂孔、止裂槽 当局部弯曲某一段边缘时,为了防止尖角处由于应力集中而 产生裂纹,可增添工艺孔、工艺槽或将弯曲线移一定距离,
1.V形弯曲模
凸、凹模之间的 间隙是靠调节压 力机的装模高度 来控制,所以对 材料的厚度公差 要求不严。可实 现校正弯曲,弯 曲件的回弹小, 平面度好。
图 4-14 V形件弯曲模 1-顶杆;2-定位钉;3-模柄;4-凸模;5-凹模;6-下模座
2.L形弯曲模 在弯曲时固定工件长边弯曲短边。竖起的短边无法得到校正, 因而回弹弹较大。
图 4-2 V形件弯曲变形过程
2.弹-塑性弯曲外表面首 先开始出现塑性变形,并逐渐向毛坯内部扩展,变形由弹 性弯曲过渡到弹—塑性弯曲。
后向弯曲
促使材料塑性变形 的弯曲力矩是逐渐 增大的。由于弯曲 力臂l逐渐减小, 因此弯曲力处于不 断上升的趋势。凸 模继续下行,板料 与凸模V形斜面接 触后被后向弯曲。
弯曲模具结构可分为五个部分:
工作零件(凸模、凹模,凸凹模) 定位零件(定位板、定位钉等) 顶件及压料装置 导向零件(常用导柱导套式) 固定零件(模架、固定板、墊板、模柄、紧固件等)
模具应用举例
4.2.1 V形件弯曲模
形状简单,能一次弯曲成形。常用的方法有两种:一种是 沿弯曲件的角平分线方向弯曲,称为V形弯曲;另一种是垂 直于一直边方向的弯曲,称为L形弯曲。
宽板
弯曲时,材料在宽度方向上的变形 会受到相邻金属的限制,其变形区
断面几乎不变,基本保持为矩形。
图 4-6 板料厚度方向变形情况
4.1.4 弯曲件的结构工艺性
1.弯曲件的形状 弯曲件良好的工艺性,不仅能简化弯曲工序和弯曲模的设 计,而且还能提高弯曲件的精度、节约材料、提高生产率。
左右不对称,弯曲时由于工件 受力不平衡将会产生滑动现象 影响工件精度。
图 4-15 L形件弯曲模 1-凸模;2-凹模;3-定位销;4-压料板;5-挡块;6-定位板
4.2.2 U形件弯曲模
1.U形件弯曲模
有回弹 现象
图 4-16 U形件弯曲模
1-模柄;2-上模座;3-凸模;4-推杆;5-凹模;6-下模座;7-顶杆;8-顶件块;9-圆柱销;10-定位销
图 4-7 弯曲件的对称性
2.最小弯曲半径 最小弯曲半径指弯曲件弯曲部分的内角半径,用r表示。 弯曲半径过小,毛坯在弯曲时,其外表面的变形就可能会超过 材料的变形极限而产生裂纹。因此弯曲工艺受最小弯曲半径 rmin的限制。
由于难以准确地建 立最小弯曲半径与 影响因素的关系, 所以最小弯曲半径 一般由试验确定。
4.1.3 弯曲变形特点
1.弯曲变形区的位置
弯曲变形的区域主要发生 在弯曲圆角区,即弯曲带 中心角α范围内。
弯曲带中心角α 弯曲角θ
α+ θ=180o
图 4-3 弯曲变形后网格变化 图 4-4 弯曲角与弯曲带中心角
2.应变中性层
在拉伸与压缩之间存在 一个既不伸长也不缩短 的中间纤维层,称为应 变中性层。