加工石墨用什么刀具_石墨加工刀具要求
八种常用铣刀的名称和用途
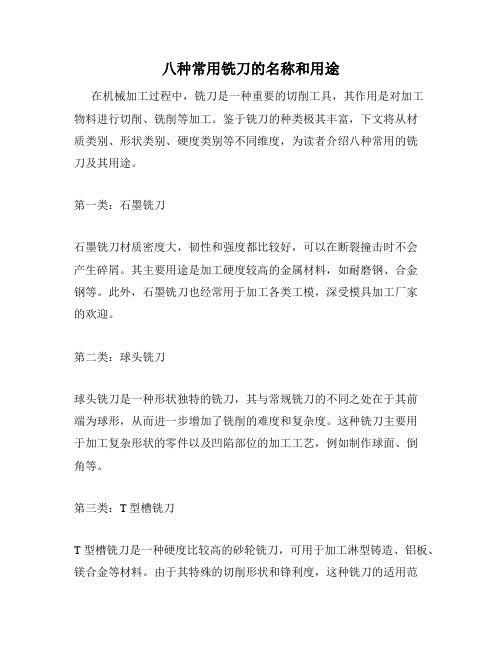
八种常用铣刀的名称和用途在机械加工过程中,铣刀是一种重要的切削工具,其作用是对加工物料进行切削、铣削等加工。
鉴于铣刀的种类极其丰富,下文将从材质类别、形状类别、硬度类别等不同维度,为读者介绍八种常用的铣刀及其用途。
第一类:石墨铣刀石墨铣刀材质密度大,韧性和强度都比较好,可以在断裂撞击时不会产生碎屑。
其主要用途是加工硬度较高的金属材料,如耐磨钢、合金钢等。
此外,石墨铣刀也经常用于加工各类工模,深受模具加工厂家的欢迎。
第二类:球头铣刀球头铣刀是一种形状独特的铣刀,其与常规铣刀的不同之处在于其前端为球形,从而进一步增加了铣削的难度和复杂度。
这种铣刀主要用于加工复杂形状的零件以及凹陷部位的加工工艺,例如制作球面、倒角等。
第三类:T型槽铣刀T型槽铣刀是一种硬度比较高的砂轮铣刀,可用于加工淋型铸造、铝板、镁合金等材料。
由于其特殊的切削形状和锋利度,这种铣刀的适用范围也比较广泛,可用于钢铁冶炼、造船、汽车工业、航空航天等多个领域的铣削加工。
第四类:硬质合金铣刀硬质合金铣刀是一种常用的硬质合金工具,由于其硬度特别高,因此具有很强的耐磨性和韧性。
同时,它也是一种普遍用于加工黄铜、铝合金、红铜等材料的切削机床刀具。
第五类:曲线铣刀曲线铣刀可用于加工各种弧形零件和复杂形状工件,具有加工精度高、切削效率高等优点。
其主要用途是在钢铁冶炼、造船、汽车制造、航空航天等领域中,用于加工曲面部位的钢铁零件、船舶结构件、汽车各类轮轴等。
第六类:整体硬质合金铣刀整体硬质合金铣刀是一种厚重、坚固的铣刀,由整体钨钴硬质合金制成。
与传统的外置夹紧铣刀不同,它具有刚性高、耐磨性高、加工效率高等特点。
此外,由于其硬度高、强度大,因此也被广泛用于加工各种高强度、难加工的金属材料。
第七类:平铣刀平铣刀是一种比较常用的铣刀,其形状为平伸长型,切削刃为直线型或螺旋型。
它的主要作用是用于加工平面,满足不同要求的加工平面需求,如亚光面、高档面等。
此外,平铣刀也常用于加工零件表面的装饰处理,例如制作各种凹凸不平的花纹、图案等。
石墨电极的应用及加工浅析

133中国设备工程Engineer ing hina C P l ant中国设备工程 2018.08 (下)电火花加工是模具制造行业内广泛应用的一项工业技术,它在模具型腔的制造过程中始终发挥着极其重要的作用。
为了保证模具的高质量,电火花加工的重要性是不言而喻的。
作为电火花加工重要因素之一的电极,在沿用传统铜电极进行电火花放电加工的同时不得不开始考虑一些技改的新趋势:在竞争激烈的模具制造行业中,生产率是确保生产成本具有竞争力的关键,要有效的提高生产的效率,新材料新技术的运用,是重要途径。
石墨作为一种新的电极材料,由于其特殊的稳定物理特性而逐渐成为电火花放电加工电极材料的未来趋势。
本文着重研究了以下几个问题:使用石墨电极对比传统铜电极有何优势;如何选择石墨材料;石墨加工对刀具的要求;如何加工石墨电极。
1 使用石墨电极对比传统铜电极有何优势电极材料的选择通常由五大要素决定:可加工性、损耗率、表面光洁度、加工速度、材料成本。
可加工性:石墨比铜具有更好的可加工性,石墨加工较容易,材料去除率高,石墨在铣削加工时速度是铜的3~5倍。
石墨可用于加工形状复杂、表面要求较高的电极。
由于其强度很高,对于超高(50~90mm)、超薄(0.2~0.5mm)的电极加工时不易变形,常常被用于制作后模窄槽或深骨位加工用的电极。
在很多时候,产品都需要有很好的纹面效果,这就要求在做电极时尽量做成整体电极,而整体电极制作时存在种种隐性清角,由于石墨的易修整的特性,使得这一难题很容易得到解决,而铜电极却无法做到。
损耗率:石墨的熔点为3850±50℃,沸点为4250℃,即使经超高温电弧灼烧,重量的损失很小,热膨胀系数也很小。
石墨度随温度提高而加强,在2000℃时,石墨强度提高一倍。
由于石墨在高温下强度而增强,能有效地降低放电损耗(石墨损耗为铜的1/4),从而保证了加工质量。
表面光洁度:在合理的加工参数下,选择合适的石墨材料我们可以得到我们想要的表面光洁度。
石墨电极加工参数2013
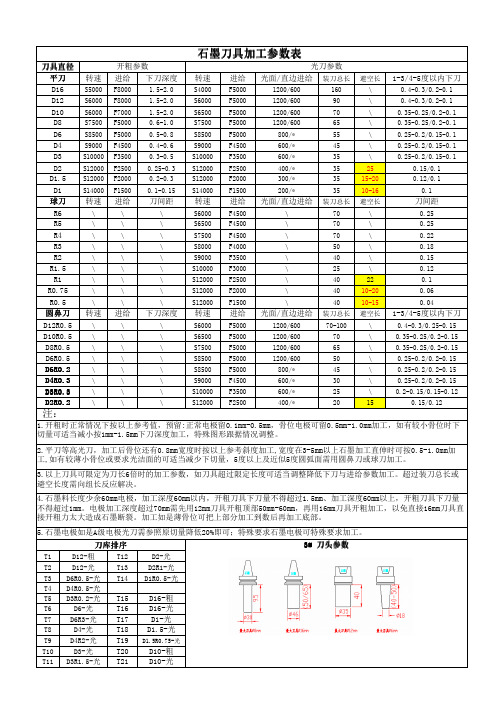
F5000
1200/600
90
\
0.4-0.3/0.2-0.1
D10
S6000 F7000
1.5-2.0
S6500
F5000
D8
S7500 F5000
0.6-1.0
S7500
F5000
1200/600 1200/600
70
\
0.35-0.25/0.2-0.1
65
\
0.35-0.25/0.2-0.1
D6
5.石墨电极如是A级电极光刀需参照原切量降低20%即可;特殊要求石墨电极可特殊要求加工。
刀库排序
T1
D12-粗
T12
D2-光
T2
D12-光
T13
D2R1-光
T3 D6R0.5-光 T14 D1R0.5-光
T4 D4R0.5-光 T5 D3R0.2-光 T15
D16-粗
T6
D6-光
T16
D16-光
T7
D12R0.5 \
\
\
S6000
F5000
1200/600
70-100
\
0.4-0.3/0.25-0.15
D10R0.5 \
\
\
S6500
F5000
1200/600
70
\
0.35-0.25/0.2-0.15
D8R0.5
\
\
\
S7500
F5000
1200/600
65
\
0.35-0.25/0.2-0.15
D6R0.5
\
\
\
S8500
F5000
1200/600
块状石墨加工铣削工艺流程

块状石墨加工铣削工艺流程
块状石墨是一种常用于电池、摩擦材料、导电材料等领域的材料。
以下是一种常见的块状石墨加工铣削工艺流程:
1.准备块状石墨:选择适当尺寸和质量的块状石墨材料。
进
行必要的清洁和检查,确保表面光滑、无裂缝和缺陷。
2.设定铣削刀具:根据加工要求,选择合适的铣削刀具。
铣
削刀具的选择会受到材料硬度、加工精度和加工速度等因
素的影响。
常用的铣削刀具包括平面铣刀、球头铣刀、立
铣刀等。
3.定位和夹紧:将块状石墨安装在工作台上,并使用夹具或
夹具系统进行定位和夹紧,保证工件的稳定性和精度。
4.设定加工参数:根据要求设定合适的加工参数,包括铣削
速度、进给速度、切削深度和切削宽度。
这些参数通常需
要根据实际情况进行试验和调整,以达到最佳的加工效果。
5.开始铣削:启动铣床或CNC铣床,使刀具按照预设路径进
行铣削。
根据加工尺寸和形状要求,选择合适的铣削方式,如面铣、侧铣、端铣等。
6.检查和修整:在铣削过程中,及时检查加工结果,确保尺
寸和表面质量符合要求。
根据需要,可以进行修整、打磨
和抛光等处理,以获得更好的表面光洁度和精度。
7.清洁和保养:完成铣削后,及时清洁工作台、刀具和机床,
保持设备的良好状态。
同时进行必要的保养和润滑,以延
长机床和刀具的使用寿命。
需要注意的是,具体的加工流程和参数设定会根据不同的石墨材料和加工要求有所不同。
CVD金刚石涂层刀具在石墨加工中的应用

第3 0卷 第 5期
燕 山大 学 学 报
J u a f a s a i e s y o r l n h n Un v r i n oY t
Vo _3 .5 l 0 No p. 2 0 et 0 6
20 0 6年 9月
0 00 5 8 9的涂 层工 艺 ,所 涂金 刚石刀 具为 四刃球头
C D 金刚石,是一种高抗磨性 的纯金刚石材料, V
收 稿 日期 :2 0 —30 0 60 —5
作者简介:魏莎 莎 (91 ) ,福建厦 门人。讲师 主要研 究方 向为金属刀具切削技术及数控加工 。 17一 ,女
维普资讯
0 引言
由于航 空航天 、 车等行业 使用材料 的性 能不 汽 断提高 ,轻质 强韧材料 的使用 日渐 增 多,因此加 工 难度 日益 增大 。同时 随着 机床制造 业 的发展 ,数控 机床和加 工 中心 的加工 能力 获得极大提 高 , 并不 断
不含粘接剂,纯度接近 10 0%。硬度、耐磨性和热 导率高, 磨擦系数小, 化学稳定性好, 适用于高的
文章编号:1 0 ・ 9 X (0 6 50 0 —4 0 77 1 2 0 )0 —4 30
C VD金 刚石涂层 刀具在 石墨加工 中的应用
魏 莎莎 ,卢志 红
( .集美大学 工程技术学 院,福建 厦 门 3 1 2 ; 2 1 6 0 1 .厦 门金鹭特种合金有 限公 司,福建 厦 门 3 10 ) 6 0 6
步对新材 料及机械 加工 中高速切 削的需要 。 在这些 因素 的影响下 , 进 了切 削刀 具材 料 的高速 发展 。 促 其 中金 刚石和 立 方氮 化硼 等 超 硬刀 具材 料 的高速 发 展为广 泛 采用 新 型硬 韧材 料 和 新型加 工 工艺提 供 了广 阔的应用 前景 。
石墨的机械加工工艺探讨

石墨的机械加工工艺探讨
石墨具有很好的导电和导热性能,所以在电子、光电、航空、航天等行业得到广泛应用。
石墨的机械加工工艺是指将石墨材料进行切削、钻孔、铣削、磨削等加工,以达到所需的尺寸、表面质量和形状。
1. 切削加工:石墨材料的切削加工常用的工具有铣刀、刀具、锯片等。
切削过程中需要注意加工速度、切削深度和刀具刃口的选择,以避免石墨材料的破裂和损坏。
2. 钻孔加工:石墨材料的钻孔可以使用普通的钻头进行,但需要注意控制切屑的产生和排除,以免影响加工质量。
钻孔过程中要适当提高进给速度,减少切削时间。
3. 铣削加工:石墨材料的铣削加工可以利用铣刀进行切削,常用的有立铣刀、球头铣刀等。
铣削加工时需要控制切削速度和进给速度,以免过热引起石墨材料的损坏。
4. 磨削加工:石墨材料的磨削加工可以利用砂轮或磨料进行磨削,常用的有平面磨削和圆柱磨削。
在磨削过程中需要注意选用合适的磨料、磨轮和磨削参数,以获得理想的表面质量。
总的来说,石墨的机械加工工艺需要根据具体的加工要求选择合适的切削、钻孔、铣削和磨削方法,同时要注意控制加工速度、进给速度和刀具、磨料的选择,以避免石墨材料的破裂和损坏,保证加工质量。
加工石墨的刀具选择—PCD刀具

加工石墨的刀具选择—PCD刀具石墨是碳的一种同素异形体,尤其石墨的高磨蚀性、耐高温等性能,广泛应用于模具、坩埚、点击、电池、电刷等领域。
但由于石墨质坚而脆,所以采用车、铣等常规机械加工方法时,旺旺在加工表面会产生崩损现象。
因此车、铣加工石墨模/石墨电极等制品时,切削刀具需具备高的耐磨损性和抗冲击性。
本文就重点介绍一下车、铣加工石墨模具/石墨电极等制品的刀具材质选择,及其加工刀具的规格型号选择。
1、石墨制品的介绍(1)石墨制品之石墨模具的介绍模具作为工业生产中使用极为广泛的基础工艺装备,大到机身外壳,小到一个螺丝,都是根据成型模具,通过冲压、锻压、压铸、挤压、注塑等方式使坯料成为符合产品要求的零件。
模具的形状和加工质量、精度决定着产品的外形和质量。
近年来随着模具行业飞速发展,石墨以其良好的物理和化学性能逐渐成为模具制作的理想选择材料。
现如今许多产业部门,如机电、汽车、家电轻工、电器仪表、通讯、军械等行业的发展均依赖于模具工业的技术提高和发展。
(2)石墨制品之石墨电极的介绍石墨电极是指以石油焦、沥青焦为骨料,煤沥青为黏结剂,经过原料煅烧、破碎磨粉、配料、混捏、成型、焙烧、浸渍、石墨化和机械加工而制成的一种耐高温石墨质导电材料,称为人造石墨电极(简称石墨电极)。
石墨电极的优点是加工较容易,放电加工去除率高,石墨损耗小,因此,部分群基火花机客户放弃了铜电极而改用石墨电极。
目前石墨电极主要用于电弧炼钢炉,矿热电炉,电阻炉等行业,同时石墨电极的毛坯还用于加工成各种坩埚、模具、舟皿和发热体等异型石墨产品。
(3)石墨制品之石墨坩埚的介绍石墨坩埚,又称熔铜包、熔铜等,是指以石墨、粘土、硅石和腊石为原料烧制而成的一类坩埚。
石墨坩埚具有耐高温、导热性能强、热膨胀系数小、抗腐蚀性能好,化学稳定性强,使用寿命长等特点。
被广泛用于合金工具钢冶炼和有色金属(紫铜、黄铜、金、银、锌和铅)及其合金的冶炼。
(4)其他石墨制品介绍除了以上是那种零部件,石墨广泛用于耐火材料、导电材料、耐磨材料、润滑剂、耐高温密封材料、耐腐蚀材料、隔热材料、吸附材料、摩擦材料和防辐射等材料中,这些材料广泛应用于冶金、石油化工、机械工业、电子产业、核工业和国防等。
精雕石墨薄片加工方法

精雕石墨薄片加工方法全文共四篇示例,供读者参考第一篇示例:一、石墨薄片加工方法1. 切割石墨薄片的加工首要步骤是切割,通常采用机械切割方式进行。
切割时可选择合适的切割工具和设备,按照需求将石墨块切割成薄片状。
切割过程中需严格保持工件的平整度和尺寸精度,以确保后续加工的顺利进行。
2. 精雕在切割完成后,需要对石墨薄片进行精雕加工。
精雕主要包括车削、铣削、镗削等加工方式。
这些加工方式能够对石墨薄片进行精细的加工,提高其表面平整度和尺寸精度。
在精雕过程中,需选用适用的刀具和加工参数,确保加工效果达到预期要求。
3. 表面处理石墨薄片经过精雕加工后,可能会出现一定的表面粗糙度和毛刺。
为了提高表面质量,需要进行表面处理。
可以选择抛光、研磨等方式对石墨薄片表面进行处理,使其表面光滑度和平整度得到提高。
4. 清洁石墨材料在加工过程中容易产生切屑和粉尘,为了保证加工质量和工作环境的清洁,需要对石墨薄片进行清洁。
使用合适的清洁剂和设备对石墨薄片表面进行清洁,去除残留的切削碎屑和油污等杂质。
5. 检测最后一步是对加工完成的石墨薄片进行检测。
通过检测可以评估加工质量和尺寸精度,确保产品符合设计要求。
检测方法主要包括外观检查、尺寸测量、表面粗糙度测试等,以保证产品质量和稳定性。
1. 工艺规范在进行石墨薄片加工时,需根据工艺规范选择合适的加工工艺和参数。
加工工艺的不当会导致产品质量下降,甚至造成浪费和损失。
2. 安全保障使用加工设备和工具时,必须严格遵守操作规程和安全标准,确保操作人员的安全。
加工过程中应注意防护措施,避免发生意外事故。
3. 设备维护定期对加工设备进行检查和维护,确保设备的正常运转和性能稳定。
设备维护不当会影响加工质量和生产效率。
4. 材料选用在石墨薄片加工前,需对材料进行仔细筛选和检查,确保材料质量符合要求。
质量差的材料会影响产品加工质量和使用寿命。
5. 加工环境保持加工环境的干净整洁,避免灰尘、杂物等污染石墨薄片。
8 石墨加工刀具参数选择表
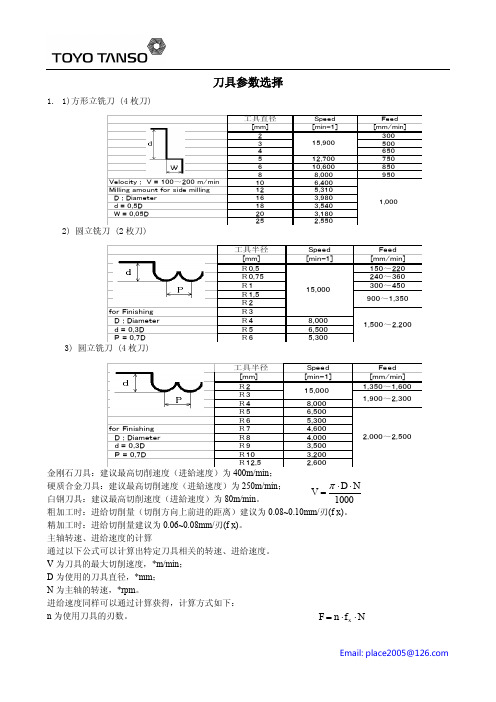
STEP 5mm \ \ \ \ \ 5mm 5mm 3mm 2mm 0.5mm \ \ 2mm 3mm 3mm \ \ \ \ \ \
进给 F \ F8000 F8000 F8000 F4000 \ \ \ \ \ \ \ \ \ \ \ 10000 10000 10000 \ \ \
中光 转速 S \ S10000 S10000 S11000 S12000 \ \ \ \ \ \ \ \ \ \ \ 10000 11000 12000 \ \ \
Velocity : V = 100 ~200 m/min Milling amount for side milling D : Diameter d = 0.5D W = 0.05D
1,000
2) 圆立铣刀 (2 枚刀)
工具半径 [mm] R0.5 R0.75 R1 R1.5 R2 R3 R4 R5 R6 Speed [min-1] Feed [mm/min] 150~220 240~360 300~450 900~1,350 8,000 6,500 5,300
STEP \ 0.7mm 0.6mm 0.5mm 0.3mm \ \ \ \ \ \ \ \ \ \ \ 0.45mm 0.4mm 0.3mm \ \ \
进给 F F3800 F5000 F5000 F5000 F4000 F2000 \ F3500 F3500 F3500 F2000 F1000 F4000 \ \ \ \ \ \ \ \ \
for Finishing D : Diameter d = 0.3D P = 0.7D
2,000 ~2,500
金刚石刀具:建议最高切削速度(进給速度)为 400m/min; DN 硬质合金刀具:建议最高切削速度(进給速度)为 250m/min; V 白钢刀具:建议最高切削速度(进給速度)为 80m/min。 1000 粗加工时:进给切削量(切削方向上前进的距离)建议为 0.08~0.10mm/刃(f x)。 精加工时:进给切削量建议为 0.06~0.08mm/刃(f x)。 主轴转速、进给速度的计算 通过以下公式可以计算出特定刀具相关的转速、进给速度。 V 为刀具的最大切削速度,*m/min; D 为使用的刀具直径,*mm; N 为主轴的转速,*rpm。 进给速度同样可以通过计算获得,计算方式如下: n 为使用刀具的刃数。 F n fx N
刀具使用规范
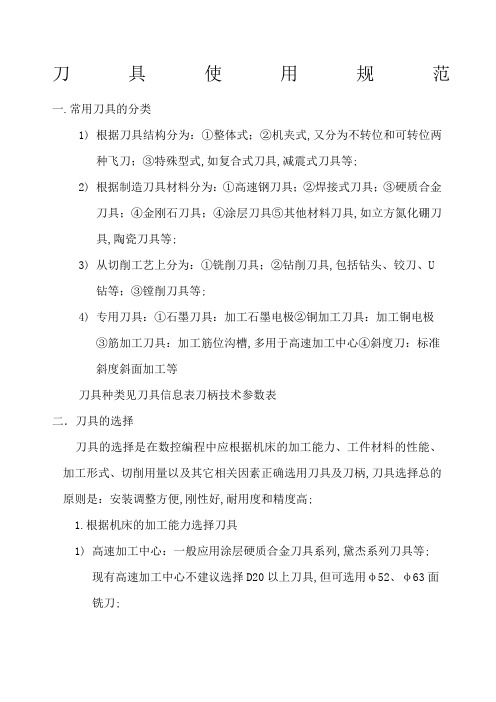
刀具使用规范一.常用刀具的分类1)根据刀具结构分为:①整体式;②机夹式,又分为不转位和可转位两种飞刀;③特殊型式,如复合式刀具,减震式刀具等;2)根据制造刀具材料分为:①高速钢刀具;②焊接式刀具;③硬质合金刀具;④金刚石刀具;④涂层刀具⑤其他材料刀具,如立方氮化硼刀具,陶瓷刀具等;3)从切削工艺上分为:①铣削刀具;②钻削刀具,包括钻头、铰刀、U钻等;③镗削刀具等;4)专用刀具:①石墨刀具:加工石墨电极②铜加工刀具:加工铜电极③筋加工刀具:加工筋位沟槽,多用于高速加工中心④斜度刀:标准斜度斜面加工等刀具种类见刀具信息表刀柄技术参数表二.刀具的选择刀具的选择是在数控编程中应根据机床的加工能力、工件材料的性能、加工形式、切削用量以及其它相关因素正确选用刀具及刀柄,刀具选择总的原则是:安装调整方便,刚性好,耐用度和精度高;1.根据机床的加工能力选择刀具1)高速加工中心:一般应用涂层硬质合金刀具系列,黛杰系列刀具等;现有高速加工中心不建议选择D20以上刀具,但可选用φ52、φ63面铣刀;2)普通加工中心:一般应用飞刀系列,合金系列;现有普通加工中心不建议选择D2以下刀具及高速加工刀具2.根据工件材料选择刀具1)石墨电极:石墨刀具2)铜电极:铜加工刀具,高速钢刀具,合金刀3)淬火材料HRC50以上:硬质合金涂层刀具3.根据加工工件的形状选择刀具选取刀具时,要使刀具的尺寸与被加工工件的表面尺寸相适应:1平面零件周边轮廓的加工,常采用立铣刀;2标准斜度轮廓外形的加工常采用斜度刀;3铣削平面时,应选硬质合金刀片飞刀;4筋位加工采用沟槽刀以及筋加工刀具;5对一些三维曲面,可选择刀具有平刀FLATE CUTTER球刀BALL CUTTER 圆鼻刀TOROIDAL CUTTER;平刀FLATE CUTTER 球刀BALL CUTTER 圆鼻刀TOROIDAL CUTTER 选择特点:a)平刀FLATE CUTTER﹕即端铣刀.模具加工中主要用在清角或清根以及2D铣削中,基本上不推荐来作3D的加工,主要的原因在于它的损耗大,尖部的磨损快,导致加工不能准确到位;b)球刀BALL CUTER:它可用在3D的铣削中,主要的缺点是当加工到平面时,即以球刀的中心切削时,球头刀具的端部切削速度为零,基本为磨削加工,现场加工会变慢,同时,以相同的切削宽度PITCH下,它的面粗度不如圆鼻刀;但它可用作清根清角加工之用;在进行自由曲面加工,为保证加工精度,切削行距一般取得很能密,故球头常用于曲面的精加工;c)圆鼻刀TOROIDAL CUTTER﹕在切削过程中,任何刀具都是R角磨损,相对平刀来讲,圆鼻刀的损耗会慢的很多,更主要的是:圆鼻刀的切削速度不会为零V≠0,切削速度比较稳定;圆鼻刀可以用在2D.3D的加工,在表面加工质量和切削效率方面都优于球头刀;因此,只要在保证不过切的前提下,无论是曲面的粗加工还是精加工,都应优先选择圆鼻刀;圆鼻刀相同直径其齿数也各有不同,像ф52R6有3~5齿,一般情况下,齿数较少的刀具因强度好,排屑良,用于粗加工;齿数多的刀具因齿数多,进给快,用于精加工;3.4按加工形式选择刀具1.粗加工刀具的选择选择粗加工刀具要考虑加工中心的功率,进给及转速,其次要考虑所加工工件的尺寸与形状,要在节省时间的情况下,尽快将粗加工完成,粗加工优先选用大直径刀具;外形Z向面为3D曲面,且Z向深度低于10mm 可用球刀直接分层加工适用于高速加工;a)Z向加工较深大于20时用圆鼻刀等高加工;b)工件外形在3030以下时可以用端刀等高;c)在复杂的3D曲面加工中,为了方便计算残料,可用球刀进行毛坯残料切削;注:圆鼻刀粗加工或面铣切削宽度PITCH值的计算公式: PITCH=0.7刀具直径D-22.中加工刀具的选择a)确保精加工的安全性,包括工件的余量,拐角R的大小;b)精加工前一把刀具的直径一定要小于精加工刀具;c)大直径刀具到小直径刀具逐步切削,直径递减执行减半原则,最后一把刀的R角尽量要小于或等于精加工刀具的R角;d)等高加工的刀具一定要大于粗加工刀具的一半;e)若为大刀D32以上端铣刀粗铣,凹模须用小直径端铣刀中铣.凸模须用飞刀中铣或插铣;f)工件外形在3030以下时可以用端铣刀或球刀中加工.3.精加工刀具的选择选择主要的精加工刀具,加工部位应尽可能遵循80:20原则,80代表80%的部位将被加工到位,20代表20%的部位留给后面的刀具加工, 决定精加工刀具首先应考虑加工中心的转速,其次应考虑工件的形状及尺寸,其选择原则如下:a)检测工件的最小R角及切削加工的最深点,决定刀具的直径及长度;b)加工深度一般不要超过精加工刀具直径的5倍;c)顶部或底部位曲面时需用球刀;d)能用球刀加工的侧壁及斜面应先考虑使用球刀或圆鼻刀;e)侧壁直壁或斜度及底部清角时须用平底铣刀;f)大中平面禁止用球刀光刀;g)凸模外形较大时可用飞刀精铣;h)加工底面必须考虑到刀具避开侧面;i)精铣前必须考虑是否还有多余的残料或角落未清;j)刀具若太长宜用插铣,不宜用等高铣;3.5按刀具直径及刀具长度选择1.用短不用长a)刀具的长度要根据刀具加工深度来决定,一般来说,刀具越短越好,必须考虑到使用时的刚性,必要时可采用加长杆或小直径刀柄;b)加工直壁40mm以内深度用D12;40-80mm用D16;D20,80-100用D25,D32四刃立铣刀;c)在深腔加工时不要一次把刀具夹持太长,可分两段深度加工分两段程序有助于提高加工效率,例:D50刀具加工350mm深腔加工时,先夹150mm长的刀加工,再夹250mm长的刀加工,最后夹350mm长的刀加工分成三段程式.2.用大不用小a)粗加工时尽可能考虑到用大刀;b)Z轴加工越深刀具直径要越大;3.用小不用大a)据加工工件的加工工艺流程及材料特性.应力作用当后续工段有热处理时且凹腔较大占工件1/3以上时,应考虑用小刀以减少热处理应力控制变形b)考虑加工工件受力情况,细小或薄壁工件加工则要考虑尽量用小刀. 建议:较小工件应考虑刀刃长可达到即可. 例如:127高的电极用D3的刀,此电极用D3的刀不可Z 向一刀到底防止损伤工件.另外,选择刀具还要考虑刀具的耐用度和精度以及使用刀具的经济性:“好钢用在刀刃上”对于精密工件选择好的刀具,增加了刀具成本,但由此带来的加工质量和加工效率的提高,则可以使整个加工成本大大降低;在大多数情况下,选择刀具只要满足工件加工要求即可,如修磨刀具,普通合金刀具;程序单注明开粗或半精加工的,应选用旧刀具或修磨刀具,注明精加工的选用新刀具或可用于精加工的刀具磨损量小于0.02MM,重修磨涂层刀具可应用于非精密工件的粗精加工;如整体硬质合金刀具D12球刀与D10球刀价格相差较大,建议优选D10球刀或球飞刀;非标刀具价格高,优选标准刀具;4.数控加工刀具的顺序选择在数控加工中,由于刀具的更换装夹、测量和垫刀多为人工手动进行,辅助时间较长,因此,必须合理安排刀具的排列顺序,一般应遵循以下原则:1)刀具尽量从大到小选择;2)大余量粗加工程序尽可能集中进行,尽量避免粗加工切屑对已精加工面损伤;3)尽量减少刀具数量;4)一把刀具装夹后,应完成其所能进行的所有加工部位;5)粗精加工的刀具应分开使用,即使是相同尺寸规格的刀具;6)先进行曲面精加工,后进行二维轮廓精加工;7)先精加工平面,后精加工侧面;在可能的情况下,应尽可能选择标准刀库配备刀具,充分利用数控机床的自动换刀功能,以提高生产效率等;。
石墨加工的特点

石墨专用刀具的特点是什么石墨专用刀具的特点是什么石墨电极与铜电极相比具有电极消耗小、加工速度快、机械加工性能好、加工精度高、热变形小、重量轻、表面处理容易、耐高温、加工温度高、电极可粘结等优点。
尽管石墨是一种非常容易切削的材料,但由于用作EDM电极的石墨材料必须具有足够的强度以免在操作和EDM 加工过程中受到破坏,同时电极形状(薄壁、小圆角、锐变)等也对石墨电极的晶粒尺寸和强度提出较高的要求,这导致在加工过程中石墨工件容易崩碎,刀具容易磨损。
刀具磨损是石墨电极加工中最重要的问题。
磨损量不仅影响刀具损耗费用、加工时间、加工质量,而且影响电极EDM加工工件材料的表面质量,是优化高速加工的重要参数。
石墨电极材料加工的主要刀具磨损区域为前刀面和后刀面。
在前刀面上,刀具与破碎切屑区的冲击接触产生冲击磨粒磨损,沿工具表面滑动的切屑产生滑动摩擦磨损。
影响刀具磨损的几点事项:1、刀具材料刀具材料是决定刀具切削性能的根本因素,对于加工效率、加工质量、加工成本以及刀具耐用度影响很大。
刀具材料越硬,其耐磨性越好,硬度越高,冲击韧性越低,材料越脆。
硬度和韧性是一对矛盾,也是刀具材料所应克服的一个关键。
对于石墨刀具,普通的TiAlN涂层可在选材上适当选择韧性相对较好一点的,也就是钴含量稍高一点的;对于金刚石涂层石墨刀具,可在选材上适当选择硬度相对较好一点的,也就是钴含量稍低一点的;2、刀具的几何角度石墨刀具选择合适的几何角度,有助于减小刀具的振动,反过来,石墨工件也不容易崩缺;(1)前角,采用负前角加工石墨时,刀具刃口强度较好,耐冲击和摩擦的性能好,随着负前角绝对值的减小,后刀面磨损面积变化不大,但总体呈减小趋势,采用正前角加工时,随着前角的增大,刀具刃口强度被削弱,反而导致后刀面磨损加剧。
负前角加工时,切削阻力大,增大了切削振动,采用大正前角加工时,刀具磨损严重,切削振动也较大。
(2)后角,如果后角的增大,则刀具刃口强度降低,后刀面磨损面积逐渐增大。
加工石墨的技巧

加工石墨的技巧
1. 切割:石墨是一种相对脆性较好的材料,可以使用高速钻或金刚石钻头对其进行切割和加工。
在切割过程中要注意切割速度和刀具冷却,以减少石墨断裂或溶解的可能性。
2. 磨削:石墨磨削过程中需要使用钻石磨头,以便达到高精度的加工要求。
要注意磨削过程中的切线速度和刀具正常工作温度,以避免刀具过热。
3. 热处理:石墨的硬度和强度随其晶粒大小和纯度的不同而变化。
常见的热处理方法包括高温清洗,低温退火和水淬硬化。
其中,高温清洗对于去除表面杂质和增加石墨晶体大小极为重要。
4. 拉伸:石墨的机械性能和其晶粒的方向有关。
石墨的晶粒一般呈片状,石墨片与石墨片之间的结合力较弱,因此石墨的组织呈现出层片状。
在拉伸过程中,要注意保持拉伸方向和板层排列方向的一致,以充分发挥石墨的特性。
5. 激光加工:激光加工是一种石墨加工的新技术,可以实现高精度和高效加工石墨。
在激光加工过程中,要注意控制激光功率、扫描方式和局部冷却,以确保加工质量和刀具寿命。
加工石墨用的莱氏体合金刀具

加工石墨用的莱氏体合金刀具
Д.А.МИРЗАЕВ;谢燮揆
【期刊名称】《热处理》
【年(卷),期】1989(000)003
【摘要】在加工电极石墨时,往往采用硬质合金和高速钢刀具。
在刀具切削刃被加热到高于500℃的情况下,采用这些昂贵的合金是行之有效的。
但是,在加工电极石墨时,刀刃温度不超过350℃,亦即不要求刀具具有很大的耐热性。
显然,加工石墨用的刀具可以用不含钴和钨的便宜的铁合金来制造。
本文列举了对这类合金的考查结果及其热处理的选择。
【总页数】4页(P50-53)
【作者】Д.А.МИРЗАЕВ;谢燮揆
【作者单位】
【正文语种】中文
【中图分类】TG15
【相关文献】
1.高温处理对W6Mo5Cr4V2高速钢中莱氏体碳化物的影响 [J], 李虎;谢尘;汪宏斌;吴晓春
2.莱氏体冷作模具钢SKD11成分控制及性能分析 [J], 续维;王庆亮;张洪奎
3.莱氏体钢的锻造 [J], 罗震
4.稀土莱氏体冷作模具钢研究与生产实践 [J], 孙慎宏; 于红
5.石墨电极加工刀具用的莱氏体合金 [J], 陈沾纬
因版权原因,仅展示原文概要,查看原文内容请购买。
加工石墨用什么刀具-石墨加工刀具要求

与铜电极相比,石墨电极具有电极消耗小、加工速度快、机械加工性能好、加工精度高、热变形小、重量轻、表面处理容易、耐高温、加工温度高、电极可粘结等。
尽管石墨是一种非常容易切削的材料,但由于用作EDM电极的石墨材料须具有足够的强度,以免在操作和EDM加工过程中受到破坏,同时电极形状 (薄壁、小圆角、锐变等)也对石墨电极的晶粒尺寸和强度提出了较高要求,这导致在加工过程中石墨工件容易崩碎,刀具容易磨损。
刀具磨损是石墨电极加工中最重要的问题。
磨损量不仅影响刀具损耗费用、加工时间、加工质量,而且影响电极EDM加工工件材料的表面质量,是优化高速加工的重要参数。
石墨电极材料加工的主要刀具磨损区域为前刀面和后刀面。
在前刀面上,刀具与破碎切屑区的冲击接触产生冲击磨粒磨损,沿工具表面滑动的切屑产生滑动摩擦磨损。
◆选择石墨加工刀具时应注意以下因素1.刀具材料刀具材料是决定刀具切削性能的因素,对于加工效率、加工质量、加工成本以及刀具耐用度影响很大。
刀具材料越硬,其耐磨性越好,硬度越高,冲击韧性越低,材料越脆。
硬度和韧性是矛盾的,也是刀具材料所应解决的一个问题。
对于石墨刀具,普通的TiAlN涂层可在选材上适当选择韧性相对好一点的,也就是钴含量稍高一点的;对于金刚石涂层石墨刀具,可在选材上适当选择硬度相对高一点的,也就是钴含量稍低一点的。
2.刀具几何角度石墨专用刀具选择合适的几何角度,有助于减小刀具的振动,反过来,石墨工件也不容易崩缺。
2.1前角采用负前角加工石墨时,刀具刃口强度较好,耐冲击和摩擦的性能好,随着负前角绝对值的减小,后刀面磨损面积变化不大,但总体呈减小趋势,采用正前角加工时,随着前角的增大,刀具刃口强度被削弱,反而导致后刀面磨损加剧。
负前角加工时,切削阻力大,增大了切削振动,采用大正前角加工时,刀具磨损严重,切削振动也较大。
2.2后角如果后角增大,则刀具刃口强度降低,后刀面磨损面积逐渐增大。
刀具后角过大后,切削振动加强。
- 1、下载文档前请自行甄别文档内容的完整性,平台不提供额外的编辑、内容补充、找答案等附加服务。
- 2、"仅部分预览"的文档,不可在线预览部分如存在完整性等问题,可反馈申请退款(可完整预览的文档不适用该条件!)。
- 3、如文档侵犯您的权益,请联系客服反馈,我们会尽快为您处理(人工客服工作时间:9:00-18:30)。
加工石墨用什么刀具_石墨加工刀具要求
内容来源网络,由深圳机械展收集整理!
更多数控刀具,就在深圳机械展!
与铜电极相比,石墨电极具有电极消耗小、加工速度快、机械加工性能好、加工精度高、热变形小、重量轻、表面处理容易、耐高温、加工温度高、电极可粘结等。
尽管石墨是一种非常容易切削的材料,但由于用作EDM电极的石墨材料须具有足够的强度,以免在操作和EDM加工过程中受到破坏,同时电极形状 (薄壁、小圆角、锐变等)也对石墨电极的晶粒尺寸和强度提出了较高要求,这导致在加工过程中石墨工件容易崩碎,刀具容易磨损。
刀具磨损是石墨电极加工中最重要的问题。
磨损量不仅影响刀具损耗费用、加工时间、加工质量,而且影响电极EDM加工工件材料的表面质量,是优化高速加工的重要参数。
石墨电极材料加工的主要刀具磨损区域为前刀面和后刀面。
在前刀面上,刀具与破碎切屑区的冲击接触产生冲击磨粒磨损,沿工具表面滑动的切屑产生滑动摩擦磨损。
◆选择石墨加工刀具时应注意以下因素
1.刀具材料
刀具材料是决定刀具切削性能的因素,对于加工效率、加工质量、加工成本以及刀具耐用度影响很大。
刀具材料越硬,其耐磨性越好,硬度越高,冲击韧性越低,材料越脆。
硬度和韧性是矛盾的,也是刀具材料所应解决的一个问题。
对于石墨刀具,普通的TiAlN涂层可在选材上适当选择韧性相对好一点的,也就是钴含
量稍高一点的;对于金刚石涂层石墨刀具,可在选材上适当选择硬度相对高一点的,也就是钴含量稍低一点的。
2.刀具几何角度
石墨专用刀具选择合适的几何角度,有助于减小刀具的振动,反过来,石墨工件也不容易崩缺。
2.1前角
采用负前角加工石墨时,刀具刃口强度较好,耐冲击和摩擦的性能好,随着负前角绝对值的减小,后刀面磨损面积变化不大,但总体呈减小趋势,采用正前角加工时,随着前角的增大,刀具刃口强度被削弱,反而导致后刀面磨损加剧。
负前角加工时,切削阻力大,增大了切削振动,采用大正前角加工时,刀具磨损严重,切削振动也较大。
2.2后角
如果后角增大,则刀具刃口强度降低,后刀面磨损面积逐渐增大。
刀具后角过大后,切削振动加强。
2.3螺旋角
螺旋角较小时,同一切削刃上同时切入石墨工件的刃长较长,切削阻力较大,刀具承受的切削冲击力大,因而刀具磨损、铣削力和切削振动都比较大。
当螺旋角大时,铣削合力的方向偏离工件表面的程度大,石墨材料因崩碎而造成的切削冲击加剧,因而刀具磨损、铣削力和切削振动也都有所增大。
因此,刀具角度变化对刀具磨损、铣削力和切削振动的影响是前角、后角及螺旋角综合产生的,所以在选择时要多加注意。
内容来源网络,由深圳机械展收集整理!
更多相关内容,就在深圳机械展!。