倾斜矿体采矿方法
急倾斜矿体采矿方法选择
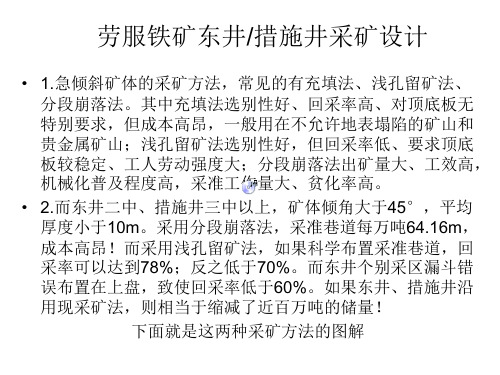
• 1.急倾斜矿体的采矿方法,常见的有充填法、浅孔留矿法、 分段崩落法。其中充填法选别性好、回采率高、对顶底板无 特别要求,但成本高昂,一般用在不允许地表塌陷的矿山和 贵金属矿山;浅孔留矿法选别性好,但回采率低、要求顶底 板较稳定、工人劳动强度大;分段崩落法出矿量大、工效高, 机械化普及程度高,采准工作量大、贫化率高。 • 2.而东井二中、措施井三中以上,矿体倾角大于45°,平均 厚度小于10m。采用分段崩落法,采准巷道每万吨64.16m, 成本高昂!而采用浅孔留矿法,如果科学布置采准巷道,回 采率可以达到78%;反之低于70%。而东井个别采区漏斗错 误布置在上盘,致使回采率低于60%。如果东井、措施井沿 用现采矿法,则相当于缩减了近百万吨的储量! 下面就是这两种采矿方法的图解
结论
• 从前面的解析可以看出,采用无底柱留矿法——既可以 实现深孔爆破,也可以实现浅孔爆破——在劳服铁矿措 施井、东井应用,具有显著的经济优势,不仅可以节省 大量采准工程,而且可以将回采率提高到90%,甚至更 高! • 而且,它是对东井原有采矿方法的继承和扬弃,对原有 巷道布置改动很小。除已经进入回采流程的外,其它的, 只地将各漏斗间的保护矿柱回收即可——升级很省心! • 同时,从这种采矿方法的巷道布置形式可以想在施 工时,就可以先施工脉内巷道;然后通过脉内巷道,来 定位底板巷道! 这对于地质勘探程度不够的矿体,不会产生丝毫的 报废运输巷道,具有无可比拟的经济、技术优势!
首先解析传统的留矿采矿法
• 这种采矿方法除了前面提到的采矿选别 好之外,其应用广泛的另两个优点是: 对设备无要求、管理较简单。 • 我们首先看到的是留矿法的巷道布置, 然后是采矿流程图,最后一幅图是清楚 地说明了“把漏斗布置在上盘时,产全 趴底矿,放矿时形成超大采空区的原 理”。
浅析缓倾斜极薄小矿体的采矿方法
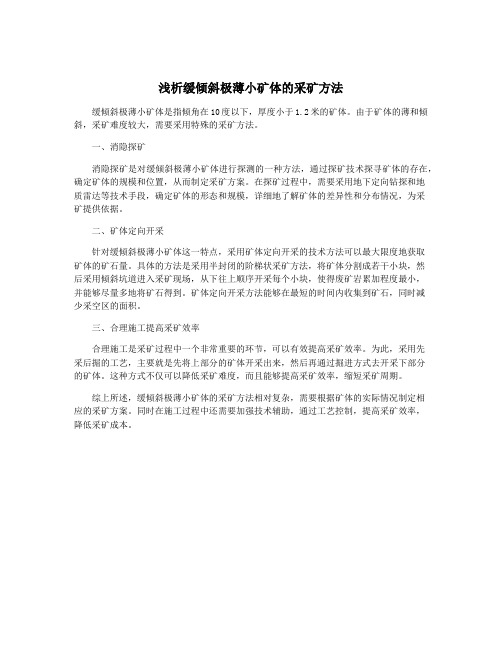
浅析缓倾斜极薄小矿体的采矿方法
缓倾斜极薄小矿体是指倾角在10度以下,厚度小于1.2米的矿体。
由于矿体的薄和倾斜,采矿难度较大,需要采用特殊的采矿方法。
一、消隐探矿
消隐探矿是对缓倾斜极薄小矿体进行探测的一种方法,通过探矿技术探寻矿体的存在,确定矿体的规模和位置,从而制定采矿方案。
在探矿过程中,需要采用地下定向钻探和地
质雷达等技术手段,确定矿体的形态和规模,详细地了解矿体的差异性和分布情况,为采
矿提供依据。
二、矿体定向开采
针对缓倾斜极薄小矿体这一特点,采用矿体定向开采的技术方法可以最大限度地获取
矿体的矿石量。
具体的方法是采用半封闭的阶梯状采矿方法,将矿体分割成若干小块,然
后采用倾斜坑道进入采矿现场,从下往上顺序开采每个小块,使得废矿岩累加程度最小,
并能够尽量多地将矿石得到。
矿体定向开采方法能够在最短的时间内收集到矿石,同时减
少采空区的面积。
三、合理施工提高采矿效率
合理施工是采矿过程中一个非常重要的环节,可以有效提高采矿效率。
为此,采用先
采后掘的工艺,主要就是先将上部分的矿体开采出来,然后再通过掘进方式去开采下部分
的矿体。
这种方式不仅可以降低采矿难度,而且能够提高采矿效率,缩短采矿周期。
综上所述,缓倾斜极薄小矿体的采矿方法相对复杂,需要根据矿体的实际情况制定相
应的采矿方案。
同时在施工过程中还需要加强技术辅助,通过工艺控制,提高采矿效率,
降低采矿成本。
缓倾斜薄矿体采矿方法讨

缓倾斜薄矿体采矿方法讨发布时间:2023-01-30T02:52:23.620Z 来源:《城镇建设》2022年18期作者:张建雄[导读] 开采缓倾斜薄矿体时张建雄云南锡业股份有限公司大屯锡矿云南个旧 661000摘要:开采缓倾斜薄矿体时,能够应用的采矿方法较多,如常见的削壁充填法、全面采矿法等。
虽然采矿工作人员有着较为丰富的经验,但实际也存在着一定的不足之处,工作人员需要根据矿山具体情况选用更加合适的采矿方法,保障最大化挖掘矿山价值。
本文将对缓倾斜薄矿山可用的采矿方法进行研究,以期促进我国缓倾斜薄矿山采矿能力的提升。
关键词:缓倾斜;薄矿体;采矿方法前言:我国缓倾斜薄矿山在整体矿脉含量中占比较大,因此相关人员必须加强对缓倾斜薄矿山的研究,进一步提升矿山企业的经济效益,降低采矿成本,同时也能延长矿山的服务年限,最大化发挥矿山的社会价值。
缓倾斜薄矿山的开采过程相对困难,且回采几率较低,因此实际应用时难以选择适宜的方法,因此相关人员需要深入对采矿方法的研究,便于选择合适的采矿方法。
1.削壁充填法削壁充填采矿法在我国缓倾薄矿山采矿中的应用时间已有几十年,经过长期实践操作,这种方法也在持续的完善,回采方法从原本的水平分层,已经转换为倾斜分层的形式,推进方法也拓展出了壁式和扇形两种方法,逐渐演化成为机械化水平削壁充填法;原本的采准平巷从沿脉走向布置转成了底盘布置;矿房结构从留设矿石顼底柱转换成为了不瞽矿石顶底柱;作业过程中也逐渐加大了机械设备的应用,有效提升了采矿效率,使得作业成本有所降低,技术经济指标受到了明显的改善[1]。
当前,常用的削壁充填采矿法主要操作如下: 1.1扇形上向式削壁充填法这种采矿方法的采场需要顺着矿脉走向布置,采场的长度在30-50米之间,沿倾斜方向的长度在50-60米之间,采准平巷一般被布置在底盘处,两侧需要设置沿脉天井,在距离采准平巷垂直高度约5米左右的位置,顺着矿脉走向对巷道进行切割。
缓倾斜矿体倾角

缓倾斜矿体倾角一、定义缓倾斜矿体是根据矿体倾角大小进行分类中的一种类型。
一般来说,缓倾斜矿体的倾角范围为5° 30°。
二、开采特点(一)采矿方法选择1. 空场采矿法在缓倾斜矿体开采中,由于矿体倾角相对较小,空场采矿法需要考虑矿石的运搬方式。
例如,在全面法开采时,矿石依靠自重沿采场底板运搬到漏斗或溜井的距离相对较短,但是需要合理布置漏斗间距,以保证矿石能顺利运出。
房柱法开采缓倾斜矿体时,要确定合适的矿柱尺寸和间距。
因为矿体倾角缓,矿柱既要承受顶板压力,又要考虑在开采过程中自身的稳定性,防止因倾角原因造成的侧向压力影响矿柱稳定性。
2. 崩落采矿法对于缓倾斜矿体使用崩落采矿法时,崩落的矿石堆积形状与急倾斜矿体有所不同。
由于倾角缓,崩落矿石在采场底部的堆积角较小,可能会影响出矿效率。
需要合理设计放矿口的位置和放矿顺序,以减少矿石的损失贫化。
例如,在无底柱分段崩落法中,分段高度的确定要考虑矿体的缓倾斜特性。
如果分段高度过高,在放矿过程中,上部崩落的矿石可能无法完全放出,导致矿石损失增加。
(二)开拓系统1. 运输系统缓倾斜矿体的开拓运输系统设计要适应矿体的倾角。
在平硐开拓时,如果矿体倾角较小,平硐的坡度也要相应减小,以保证车辆运输安全和矿石的正常运输。
对于斜井开拓,由于矿体倾角缓,斜井的提升角度也较小。
这就需要选择合适的提升设备,如胶带输送机或小型矿车提升系统。
胶带输送机在缓倾斜矿体运输中具有运输能力大、效率高的优点,但需要考虑胶带的铺设角度和防滑等问题;小型矿车提升系统则需要合理设计轨道坡度,防止矿车出轨。
2. 通风系统缓倾斜矿体的通风系统布置要考虑到采场的形状和矿石运搬方向等因素。
由于矿体倾角缓,采场的通风阻力分布与急倾斜矿体不同。
在进风和回风巷道的布置上,要避免风流短路,保证新鲜风流能有效到达作业面。
例如,可以采用对角式通风系统,使新鲜风流从采场一侧进入,污风从另一侧排出,提高通风效果。
浅析缓倾斜极薄小矿体的采矿方法

浅析缓倾斜极薄小矿体的采矿方法缓倾斜极薄小矿体是指矿层倾角小于10度,矿层厚度小于1.2米的一种矿体类型。
由于矿床的特殊性质,其开采方法需要特殊的技术和设备。
本文将从地质条件、开采方法和设备三个方面对缓倾斜极薄小矿体的采矿方法进行浅析。
一、地质条件缓倾斜极薄小矿体的地质条件对其采矿方法有着重要的影响。
主要包括矿层的倾角、厚度、岩性和性质等。
1. 倾角:缓倾斜极薄小矿体的倾角一般在0-10度之间,通常是水平或接近水平的矿层。
这种矿体的倾角较小,对采矿工艺的布置和采矿设备的选择有一定的影响。
2. 厚度:缓倾斜极薄小矿体的厚度一般小于1.2米,甚至更薄。
这种薄矿层的开采存在一定的困难,需要选择适合的采矿方法和设备。
3. 岩性:缓倾斜极薄小矿体的岩性多样,包括煤炭、铁矿石、铜矿石等。
不同的岩性对采矿方法和设备的选择有不同的要求。
二、开采方法针对缓倾斜极薄小矿体的特点,可以采用以下几种开采方法:1. 直接溜落法:适用于矿层水平或接近水平、较薄的情况。
采用该方法时,可以在矿层上方打一个或多个溜落洞,通过溜落洞将矿石直接运送到地面。
这种方法的优点是简单、快捷,适用于小规模开采。
2. 连续矿体切割法:适用于矿层倾角较小、厚度较薄的情况。
采用该方法时,可以采用刮板输送机或链斗输送机等设备,将矿石连续切割、刮取或挖掘,并通过输送机将矿石送至矿井口。
这种方法的优点是高效、连续,适用于大规模开采。
三、采矿设备针对缓倾斜极薄小矿体的特点,需要选择适合的采矿设备进行开采。
常用的采矿设备包括:1. 刮板输送机:适用于连续矿体切割法开采,可以将切割的矿石连续输送到矿井口。
3. 拖拉机:适用于拖拉机装运法开采,可以将矿石直接装运至矿井口。
4. 掘进机:适用于矿体较硬或需要切割的情况,可以在矿层内进行掘进和切割作业。
结论缓倾斜极薄小矿体的开采方法需要根据具体的地质条件进行选择。
在选择采矿方法和设备时,需要考虑矿层的倾角、厚度、岩性和性质等因素。
急倾斜厚大矿体采矿方法的选择

我们通过计算机数值模拟分析结果可以知道在开采急倾斜厚大矿体时采用空场类采矿方法存在一定的安全隐患所以建议采用有底柱分段构进行调整比如断层附近褶皱的轴部或者断层切割处这些都是极其隐蔽又复杂的部位结合矿山的实际情况以及现有的设备型号
区域治理
综合信息
急倾斜厚大矿体采矿方法的选择
二、急倾斜犀大矿体采矿方法分析 自改革开放以来,我国经济水平突飞 猛进。对于能源的需求也与日俱增,因此, 地质矿产勘察理论研究显得尤为重要。由 于急倾斜厚大矿体厚重且矿石围岩岩石性 组合形态十分复杂,就如何选择急倾斜厚 大矿体开的开采方法是顺利开展采矿活动 的基础与前提。当前,我国急倾斜厚大矿 体开采所依据的理论就是同位成矿理论, 也就是说在找矿工作就是以同位成矿理论 为指导的。同位成矿理论指的就是在同一 个地区、同一时代与同一种类与不同类型 和不同时代与地区的矿种,具有一定的内 部规律与联系,也就是说不同地域与时代 的矿种也具有稳定的同位成矿特点,这就 为矿产地质勘察工作提供了指引。 且采用空场类采矿方法对急倾斜厚大 矿体进行回采具有较大的难度.甚至会引 起急倾斜厚大矿体结构参数的变动,继而 导致踩空区被破坏,影响回采工作的顺利 进行。所以.还需要以根据协同作用和最 佳配置原理。分析矿区成矿的内在规律和 特点,从而为找矿工作提供积极引导。在 矿山开采之前对采矿方法进行进一步探索 和验证,运用FLAC计算机数值模拟软件 建立模型对采场稳定性与安全性进步性分 析,从而为急倾斜厚大矿体安全生产提供 数据支持和理论依据。 计算机建模计算主要对空区顶底板以 及间柱的应力以及塑性区分布情况进行分 析与考察。准确地发现地质工作中存在的
倾斜薄矿体采矿方法

倾斜薄矿体采矿方法
倾斜薄矿体采矿方法是一种适用于倾斜角度较大、体积较小的薄矿体的采矿方法。
该方法采用开拓式采矿技术,通过在矿体上部进行开拓,逐层向下采掘,同时结合爆破技术和采矿设备的作用,实现对矿体的高效开采。
该方法的主要优点是可以最大限度地利用薄矿体资源,同时减少采矿的浪费和对环境的影响。
与传统采矿方法相比,倾斜薄矿体采矿方法具有更高的采矿效率和更低的成本。
然而,该方法也存在一些挑战和难点,如如何避免地面塌陷和矿井坍塌、如何控制爆破过程中的火灾和爆炸等问题。
因此,需要对采矿技术和设备进行不断的改进和完善,才能更好地实现倾斜薄矿体的高效开采。
- 1 -。
关于缓倾斜薄矿体采矿方法分析
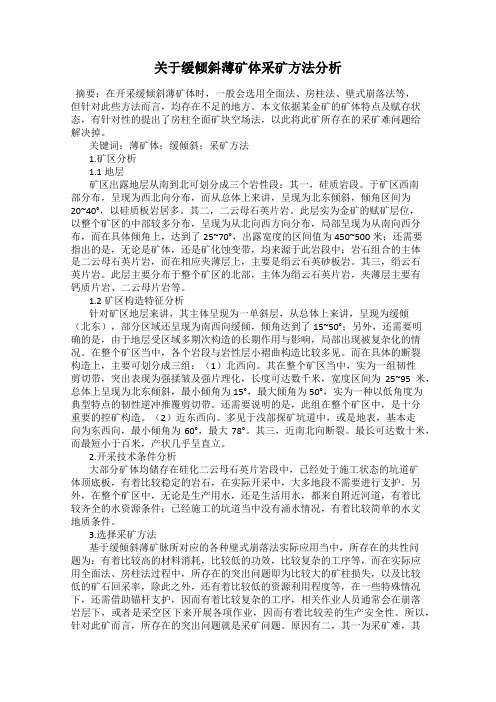
关于缓倾斜薄矿体采矿方法分析摘要:在开采缓倾斜薄矿体时,一般会选用全面法、房柱法、壁式崩落法等,但针对此些方法而言,均存在不足的地方。
本文依据某金矿的矿体特点及赋存状态,有针对性的提出了房柱全面矿块空场法,以此将此矿所存在的采矿难问题给解决掉。
关键词:薄矿体;缓倾斜;采矿方法1.矿区分析1.1地层矿区出露地层从南到北可划分成三个岩性段:其一,硅质岩段。
于矿区西南部分布,呈现为西北向分布,而从总体上来讲,呈现为北东倾斜,倾角区间为20~40°,以硅质板岩居多。
其二,二云母石英片岩。
此层实为金矿的赋矿层位,以整个矿区的中部较多分布,呈现为从北向西方向分布,局部呈现为从南向西分布,而在具体倾角上,达到了25~70°,出露宽度的区间值为450~500米;还需要指出的是,无论是矿体,还是矿化蚀变带,均来源于此岩段中;岩石组合的主体是二云母石英片岩,而在相应夹薄层上,主要是绢云石英砂板岩。
其三,绢云石英片岩。
此层主要分布于整个矿区的北部,主体为绢云石英片岩,夹薄层主要有钙质片岩、二云母片岩等。
1.2矿区构造特征分析针对矿区地层来讲,其主体呈现为一单斜层,从总体上来讲,呈现为缓倾(北东),部分区域还呈现为南西向缓倾,倾角达到了15~50°;另外,还需要明确的是,由于地层受区域多期次构造的长期作用与影响,局部出现被复杂化的情况。
在整个矿区当中,各个岩段与岩性层小褶曲构造比较多见。
而在具体的断裂构造上,主要可划分成三组:(1)北西向。
其在整个矿区当中,实为一组韧性剪切带,突出表现为强揉皱及强片理化,长度可达数千米,宽度区间为25~95米,总体上呈现为北东倾斜,最小倾角为15°,最大倾角为50°,实为一种以低角度为典型特点的韧性逆冲推覆剪切带。
还需要说明的是,此组在整个矿区中,是十分重要的控矿构造。
(2)近东西向。
多见于浅部探矿坑道中,或是地表,基本走向为东西向,最小倾角为60°,最大78°。
倾斜—急倾斜厚矿体采矿方法的探讨

采矿工程M ining engineering倾斜—急倾斜厚矿体采矿方法的探讨杨卫东(河南发恩德矿业有限公司,河南 洛阳 471700)摘 要:由于倾斜—急倾斜厚矿体开采的环境和条件等比较复杂,开采的难度也较大,本文针对倾斜—急倾斜厚矿体采矿方法进行探讨,希望对此类厚矿体的开采提供一定的帮助作用。
关键词:急倾斜;厚矿体;采矿方法中图分类号:P694 文献标识码:A 文章编号:1002-5065(2019)07-0054-2Discussion on the mining method of inclined-sloping thick ore bodyYANG Wei-dong(Henan Faende Mining Co., Ltd.,Luoyang 471700,China)Abstract: Due to the complicated environment and conditions of the inclined-sloping thick ore body mining, the mining difficulty is also great. This paper discusses the mining method of the inclined-sloping thick ore body, and hopes to provide certain mining for such thick ore body. Help.Keywords: steep slope; thick ore body; mining method倾斜—急倾斜厚矿体是一种比较特殊的矿体类型,其具有着显著的开采特点,为了实现对此类矿体的安全稳顺利开采,经过不断的发展也是产生了诸多的采矿方法,但是在实际的应用中都存在一定的局限性,为了实现更好的矿体开采效果,本文就以某案例进行分析,对其采矿方法进行深入的研究。
国内外缓倾斜中厚矿体采矿方法现状

2.国外现状
在国外,缓倾斜中厚矿体的采矿方法主要有整体顶板控制法、分段空场法、 无底柱分段崩落法等。整体顶板控制法通过加强顶板管理,提高采场安全性和回 采率,但成本较高。分段空场法则与国内类似,也是通过分段开采来达到控制采 场地压的目的。无底柱分段崩落法则具有较高的回采率,但需要考虑对上部矿体 的破坏影响。
溜井是缓倾斜中厚矿体开采过程中的重要运输设施之一。溜井设计的合理与 否直接影响到矿产资源的运输效率和开采成本。溜井设计需要考虑矿山的地形条 件、开采方案、矿产资源特点等因素,进行综合分析和优化设计。近年来,随着 计算机技术和数值模拟技术的发展,溜井设计正在朝着数字化、智能化的方向发 展。
4.采矿机器人技术
1、空场采矿法
空场采矿法在缓倾斜中厚矿体开采中应用较为广泛,其主要优点在于回采率 高、作业安全、成本较低等。然而,这种方法也存在一些缺点,如对于矿体厚度 和倾角的要求较为严格,回采过程中易产生崩落等。
2、充填采矿法
充填采矿法适用于开采缓倾斜中厚矿体,能够有效防止地表塌陷,提高矿产 资源利用率。但是,这种方法成本较高,工艺复杂,对于充填材料的要求也较高。
2、智能化程度的提高
未来,缓倾斜中厚矿体采矿方法将不断提高智能化程度。通过自动化设备和 系统的应用,实现开采过程的自动化和智能化,提高开采效率和安全性。同时, 利用大数据、云计算等技术对矿山生产进行实时监控和智能分析,优化生产过程, 降低成本,提高效益。
三、总结与展望
缓倾斜中厚矿体采矿方法的现状及发展趋势表明,空场采矿法和充填采矿法 是目前主要的开采方法,但存在一些缺点和限制。未来,随着新技术的应用和智 能化程度的提高,缓倾斜中厚矿体采矿方法将朝着高效、安全、环保的方向发展。
2.采场支护技术
矿体倾斜分类

矿体倾斜分类
矿体倾斜分类是一种将矿体按照不同的倾斜程度进行分类的方法。
矿体的倾斜程度通常可以用倾角或者倾向来表示。
在矿山开采中,倾斜的矿体往往会对开采造成一定的影响。
因此,对矿体的倾斜程度进行分类可以帮助采矿工程师制定合理的开采方案,提高开采效率和安全性。
通常情况下,矿体倾斜分类可以分为四个等级:平缓倾斜、中等倾斜、陡峭倾斜和极陡倾斜。
平缓倾斜通常指倾角在10度以内的矿体,中等倾斜指倾角在10度到30度之间的矿体,陡峭倾斜指倾角在30度到60度之间的矿体,极陡倾斜指倾角在60度以上的矿体。
对于每个不同的倾斜等级,开采方案也会有所不同。
例如,在平缓倾斜的矿体中,可以采用露天采矿或者深井采矿等方式进行开采;而在陡峭或者极陡倾斜的矿体中,需要采用特殊的开采方式,如加强支护、利用较小的采矿机械等。
矿体倾斜分类的目的是为了更好地了解矿体的特点,制定更加科学的开采方案,提高开采效率和安全性。
同时,也可以为矿山经营者提供有用的参考信息,帮助他们更好地管理矿山资源。
- 1 -。
高海拔地区急倾斜薄矿体采矿方法选择和实践
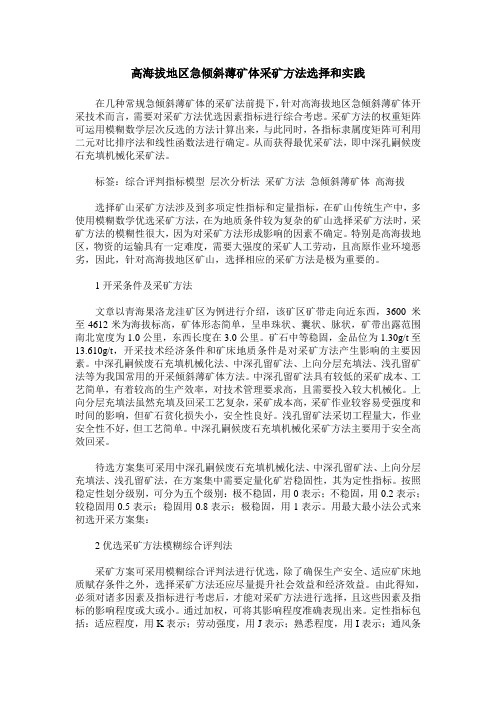
高海拔地区急倾斜薄矿体采矿方法选择和实践在几种常规急倾斜薄矿体的采矿法前提下,针对高海拔地区急倾斜薄矿体开采技术而言,需要对采矿方法优选因素指标进行综合考虑。
采矿方法的权重矩阵可运用模糊数学层次反选的方法计算出来,与此同时,各指标隶属度矩阵可利用二元对比排序法和线性函数法进行确定。
从而获得最优采矿法,即中深孔嗣候废石充填机械化采矿法。
标签:综合评判指标模型层次分析法采矿方法急倾斜薄矿体高海拔选择矿山采矿方法涉及到多项定性指标和定量指标,在矿山传统生产中,多使用模糊数学优选采矿方法,在为地质条件较为复杂的矿山选择采矿方法时,采矿方法的模糊性很大,因为对采矿方法形成影响的因素不确定。
特别是高海拔地区,物资的运输具有一定难度,需要大强度的采矿人工劳动,且高原作业环境恶劣,因此,针对高海拔地区矿山,选择相应的采矿方法是极为重要的。
1开采条件及采矿方法文章以青海果洛龙洼矿区为例进行介绍,该矿区矿带走向近东西,3600米至4612米为海拔标高,矿体形态简单,呈串珠状、囊状、脉状,矿带出露范围南北宽度为1.0公里,东西长度在3.0公里。
矿石中等稳固,金品位为1.30g/t至13.610g/t,开采技术经济条件和矿床地质条件是对采矿方法产生影响的主要因素。
中深孔嗣候废石充填机械化法、中深孔留矿法、上向分层充填法、浅孔留矿法等为我国常用的开采倾斜薄矿体方法。
中深孔留矿法具有较低的采矿成本、工艺简单,有着较高的生产效率,对技术管理要求高,且需要投入较大机械化。
上向分层充填法虽然充填及回采工艺复杂,采矿成本高,采矿作业较容易受强度和时间的影响,但矿石贫化损失小,安全性良好。
浅孔留矿法采切工程量大,作业安全性不好,但工艺简单。
中深孔嗣候废石充填机械化采矿方法主要用于安全高效回采。
待选方案集可采用中深孔嗣候废石充填机械化法、中深孔留矿法、上向分层充填法、浅孔留矿法,在方案集中需要定量化矿岩稳固性,其为定性指标。
按照稳定性划分级别,可分为五个级别:极不稳固,用0表示;不稳固,用0.2表示;较稳固用0.5表示;稳固用0.8表示;极稳固,用1表示。
急倾斜矿体采矿方法

急倾斜矿体采矿方法一、急倾斜矿体的特点。
1.1 角度大。
急倾斜矿体啊,那倾斜角度可大得很呢,一般是大于45度,有的甚至接近垂直。
这就像一个陡峭的山坡,人站在上面都觉得摇摇欲坠。
这种矿体的开采难度,就好比是在悬崖峭壁上搞建筑,不是一件轻松的事儿。
1.2 稳定性差。
由于倾斜角度大,矿体的稳定性那是相当差。
就像搭积木,稍微有点风吹草动就可能塌下来。
这就给采矿工作带来了巨大的安全隐患,真可谓是“如履薄冰”。
二、常见的采矿方法。
2.1 留矿采矿法。
这种方法在急倾斜矿体采矿里还挺常用的。
简单来说呢,就是在开采过程中,先把矿石采下来一部分,留下一部分在采场里支撑顶板。
这就像搭架子一样,留着的矿石起到了“顶梁柱”的作用。
不过呢,这种方法也有缺点,比如采场的通风条件可能不太好,就像在一个封闭的小屋里,空气不流通,工人在里面干活可难受了。
2.2 充填采矿法。
充填采矿法就比较讲究了。
采完矿石后,要往采空区充填一些材料,像沙子、石子或者专门的充填物料。
这就像是给挖空的地方打补丁,让矿体的结构更加稳定。
这个方法虽然成本高一些,但是安全系数大大提高了,就像给采矿工作系上了“安全带”。
不过它也有麻烦的地方,充填的过程就像绣花一样,得小心翼翼的,要保证充填的质量,不然就白忙活了。
2.3 崩落采矿法。
崩落采矿法呢,就是通过爆破等手段让矿体崩落下来。
这就像是用炸药把山体炸开一样,动静可不小。
这种方法效率比较高,但是对周围环境的影响也比较大。
而且如果控制不好,就像脱缰的野马,容易造成一些不必要的损失,比如矿石的贫化或者对相邻矿体的破坏。
三、采矿方法的选择。
3.1 安全因素。
选择采矿方法的时候啊,安全肯定是第一位的。
就像我们常说的“安全第一,预防为主”。
如果矿体稳定性特别差,那充填采矿法可能就是比较好的选择,虽然麻烦点,但是能保证工人的安全,这是最重要的。
要是安全都保证不了,那一切都是白搭,就像盖房子没有打好地基一样。
3.2 经济因素。
急倾斜厚大矿体高分层连续充填采矿方法分析

急倾斜厚大矿体高分层连续充填采矿方法分析摘要:分层干式充填采矿法在金矿中应用的越来越广泛,尤其是在缓倾斜薄矿体采矿中已经普遍应用。
上向水平分层干式充填采矿法采矿,能及时的充填、隔绝矿体与空气的接触,杜绝金矿氧化浪费现象的发生。
采用上向水平分层干式封包充填采矿法,矿井回收率达到95%以上,排污少,减少对环境造成的污染。
本文根据本人实际工作经验,首先简要介绍了分层干式充填采矿法的优点,其次介绍了上向水平分层干式充填采矿法相关技术,最后重点介绍了应用效果。
关键词:水平分层;干式充填;采矿法应用改革开放以来,我国各行各业取得良好发展,采矿行业也不例外。
但是,受技术和条件限制,我国采矿作业存在多方面的缺陷,比如工作效率低、矿资源浪费等。
目前,能源紧张问题日益凸显,且采矿事故频发。
因此,在矿业开采中,为了确保安全,同时提高工作效率,需采用有效的采矿法。
缓倾斜薄矿体具有采矿难度高、危险性大等问题,需采用合适的采矿方法。
下文主要分析分层干式充填采矿法在金矿缓倾斜薄矿体采矿的应用。
1、矿体开采技术条件V1是矿床主矿体,矿体赋存在金山-朱林剪切带Ⅰ带中下部,分布于337~328线之间,走向控制长1910m、倾向控制延伸1480m(180~-200m),走向、倾向均未控制完毕。
产状受剪切带主剪切面控制,总体走向北西-南东,倾向北东,0~-105m间,矿体倾角普遍变陡30°~50°,-105m中段以下,倾角变缓10°~25°,与0m以上矿体成明显的反“S”形,平均倾角29°。
矿体形态为透镜状,整体膨胀狭缩明显,局部有分枝复合现象。
矿体平均厚度4.16m,厚度变化系数86.92%。
矿体平均品位5.06×10-6,品位变化系数183.68%,属有用组分分布不均匀矿体。
在321~311线-130~0m标高及311~301线0m标高附近、303~302线-105~-150m标高、308~312线-130~-200m标高3处出现无矿天窗。
浅析缓倾斜极薄小矿体的采矿方法
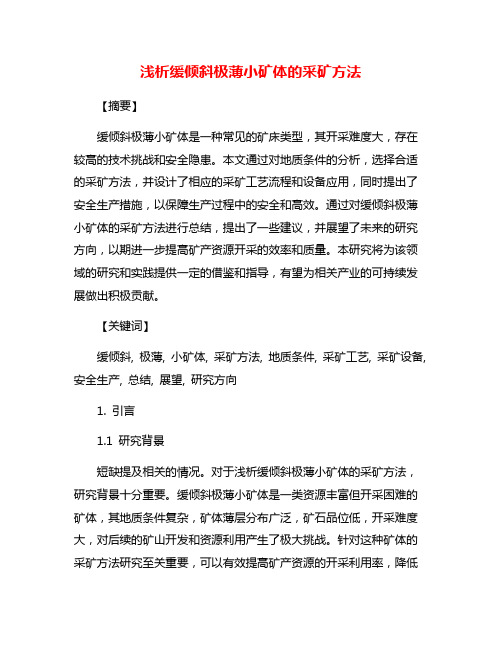
浅析缓倾斜极薄小矿体的采矿方法【摘要】缓倾斜极薄小矿体是一种常见的矿床类型,其开采难度大,存在较高的技术挑战和安全隐患。
本文通过对地质条件的分析,选择合适的采矿方法,并设计了相应的采矿工艺流程和设备应用,同时提出了安全生产措施,以保障生产过程中的安全和高效。
通过对缓倾斜极薄小矿体的采矿方法进行总结,提出了一些建议,并展望了未来的研究方向,以期进一步提高矿产资源开采的效率和质量。
本研究将为该领域的研究和实践提供一定的借鉴和指导,有望为相关产业的可持续发展做出积极贡献。
【关键词】缓倾斜, 极薄, 小矿体, 采矿方法, 地质条件, 采矿工艺, 采矿设备, 安全生产, 总结, 展望, 研究方向1. 引言1.1 研究背景短缺提及相关的情况。
对于浅析缓倾斜极薄小矿体的采矿方法,研究背景十分重要。
缓倾斜极薄小矿体是一类资源丰富但开采困难的矿体,其地质条件复杂,矿体薄层分布广泛,矿石品位低,开采难度大,对后续的矿山开发和资源利用产生了极大挑战。
针对这种矿体的采矿方法研究至关重要,可以有效提高矿产资源的开采利用率,降低成本,保障矿山的安全生产。
本文将就缓倾斜极薄小矿体的采矿方法进行深入探讨,旨在为相关领域的研究提供参考,并为矿山的可持续发展提供支持。
通过研究背景的分析,可以更加清晰地了解该领域的现状和挑战,为后续的研究奠定基础。
1.2 研究意义缓倾斜极薄小矿体在矿业开采中具有一定的挑战性,采矿方法的选择对于提高矿体开采效率、减少资源浪费具有重要意义。
研究缓倾斜极薄小矿体的采矿方法,不仅可以有效利用矿山资源,提高矿产量,还可以减少对地质环境的破坏,保护生态环境,促进绿色矿业的发展。
研究缓倾斜极薄小矿体的采矿方法,还可以提高矿山开采效率,降低生产成本,增加企业的经济效益,推动矿业产业的可持续发展。
深入研究缓倾斜极薄小矿体的采矿方法具有重要的理论和实践意义,对于推动我国矿业工程技术的发展和进步具有积极的推动作用。
2. 正文2.1 地质条件分析地质条件分析是制定缓倾斜极薄小矿体采矿方法的重要基础。
浅析缓倾斜极薄小矿体的采矿方法

浅析缓倾斜极薄小矿体的采矿方法1. 引言1.1 研究背景矿业资源的开发利用一直是人类社会发展的重要支柱之一,而随着传统矿床逐渐枯竭,对于浅埋且倾斜角度较小的极薄小矿体的开采工作变得愈发重要。
这类矿体通常位于矿体顶板与地表之间,矿层倾角很小,矿床厚度极薄,传统的采矿方法在这种情况下已经难以适用。
研究缓倾斜极薄小矿体的采矿方法具有重要的现实意义。
在当前矿业技术的背景下,如何有效地对缓倾斜极薄小矿体进行开采已经成为矿业工作者面临的一项重要挑战。
只有深入了解这类矿体的特点,并结合合适的采矿方法,才能实现对矿产资源的最大化利用,同时确保采矿过程的安全高效进行。
本文旨在浅析缓倾斜极薄小矿体的特点,并探讨适用于这类矿体的不同采矿方法,以期为相关矿业工作者提供参考和借鉴。
通过系统研究缓倾斜极薄小矿体的采矿方法,有望为矿业资源的开发利用提供新思路和新方法。
1.2 研究意义缓倾斜极薄小矿体是指薄层矿体在低倾角地段中的分布,其开采难度大、安全风险高。
对于这一类矿体,矿山企业往往面临诸多困难和挑战。
研究缓倾斜极薄小矿体的采矿方法具有重要的意义。
通过深入研究和探索,可以为矿山企业提供有效的采矿方案,降低开采成本,提高矿石开采率,从而增加企业收益和竞争力。
研究缓倾斜极薄小矿体的采矿方法,有助于提高矿山开采效率,减少资源浪费,保护环境和生态,推动绿色矿山建设。
这一研究领域的深入探索还有助于促进采矿技术的进步和创新,推动矿业行业的可持续发展。
研究缓倾斜极薄小矿体的采矿方法具有重要的理论和实践意义,对提高矿山企业的经济效益、社会效益和环境效益具有重要的推动作用。
1.3 研究目的研究目的是为了探讨如何有效地开采缓倾斜极薄小矿体,提高矿产资源的开采利用率。
针对这种特殊类型的矿体,传统的采矿方法并不适用,因此需要进一步研究和探索新的采矿方法。
通过研究,我们希望找到一种适合该类型矿体的高效、安全、具有可持续性的采矿方法,以满足矿产资源的需求,并减少对环境的影响。
浅析缓倾斜极薄小矿体的采矿方法

浅析缓倾斜极薄小矿体的采矿方法
缓倾斜极薄小矿体是一种典型的难以开采的矿体,其采矿难度主要表现在以下几个方面:
一、地下地质条件复杂,矿体薄、倾角小,需要挖掘出稳定的地下建筑。
二、矿体展布范围较小,资源储量有限,在采矿过程中容易造成过度开采,浪费矿产
资源。
三、采矿作业难度大,要求矿工具备较高的技能和经验。
针对以上的问题,应采用科学合理的采矿方法进行开采。
目前,常用的采矿方法包括:房柱法、侧巷法、切眼法、多级矿岛法和切炭法等。
一、房柱法
房柱法是一种适用于缓倾斜极薄小矿体的采矿方法。
该方法的主要特点是在矿体两旁
开挖直立的立柱,并在立柱之间留有一定宽度的采矿空间。
采矿空间必须配备支架和矿柱,以确保矿体的稳定性。
二、侧巷法
三、切眼法
切眼法是一种适用于缓倾斜极薄小矿体的采矿方法。
该方法的主要特点是钻孔开采。
采矿工人在矿体两侧钻孔,然后在孔内放置爆炸物,产生爆炸震动将矿石从岩石中分离出来,然后通过装载机将矿石取出进行运输。
四、多级矿岛法
五、切炭法
以上就是缓倾斜极薄小矿体的一些采矿方法的简介和特点。
不同的采矿方法适用于不
同的地质环境和矿体条件,需要进行合理的选择和取舍。
在采矿过程中,还需要注意安全
生产,合理利用资源,确保采矿经济效益。
浅析缓倾斜极薄小矿体的采矿方法

浅析缓倾斜极薄小矿体的采矿方法
缓倾斜极薄小矿体的采矿方法包括传统的采空区法和现代的综放采矿法。
传统的采空
区法通常适用于煤炭采矿,其缺点是资源利用率低、安全隐患高,现代的综放采矿法在保
证安全的前提下,能够有效地提高资源利用率。
综放采矿法主要包括割缝法、块裂法和长壁法。
其中,割缝法适用于矿体倾角小于15度、矿层厚度小于1米的地质条件下,通过在煤层顶板开采一定宽度的割缝,使煤层自上
而下均匀落到采空区中,实现高效利用。
块裂法适用于矿体倾角小于30度、矿层厚度小于1.2米的地质条件下,采用顶板控制开采块状煤体,使其自上而下落到采空区中。
长壁法
适用于矿体倾角小于45度、煤层厚度在1.2米以上的地质条件下,以矿层为基准面,采用顶板和底板控制双向开采,实现高效率采矿。
采用综放采矿法的优势在于能够有效地减少采空区的面积,实现全面利用,提高资源
利用率。
同时,综放采矿法采用顶板和底板控制的方式,具有较高的安全性,减少了采煤
工人的伤亡事故。
然而,缓倾斜极薄小矿体采矿面临的挑战也很明显。
首先,由于矿体倾角小、厚度薄,采矿难度较大。
其次,由于煤层顶板厚度薄,顶板强度较弱,采矿时易发生顶板塌落事故。
此外,由于矿体所在地形和地貌的差异,采矿方法的选择也需要根据具体情况进行调整。
在缓倾斜极薄小矿体的采矿中,综放采矿法是目前较为适用的方法。
但是,为了提高
采矿效率和安全性,需要对采矿工艺进行研究和优化。
同时,还需要加强采空区治理和矿
山环保工作,实现可持续发展。
- 1、下载文档前请自行甄别文档内容的完整性,平台不提供额外的编辑、内容补充、找答案等附加服务。
- 2、"仅部分预览"的文档,不可在线预览部分如存在完整性等问题,可反馈申请退款(可完整预览的文档不适用该条件!)。
- 3、如文档侵犯您的权益,请联系客服反馈,我们会尽快为您处理(人工客服工作时间:9:00-18:30)。
倾斜矿体的采矿方法探讨
【摘要】:该矿体为缓倾斜至倾斜中厚矿体,矿石储量大,品位高,矿体形态复杂,连续性较好,矿体和下盘围岩稳固性中等,上盘围岩稳固性较差,矿体上部出露地表,已用露天开采方式开采完毕,现已转入地下开采。
在矿山由露采转入地采的上部各中段,主要采矿方法为多步骤小跨度阶段空场嗣后充填采矿法。
由于矿体从浅表至深部具有品位由高至低、倾角由小至大、矿化边界由较稳定向不稳定方向发展的趋势,因而,矿山必须充分发掘采矿工艺在提高回收率和降低采矿综合成本方面的潜力,克服原有采矿方法的采场生产能力小、生产效率低、电耙顺坡扒矿安全隐患大、采矿贫化率高、采场顶板暴露面大、空区胶结充填费用高和采准布置复杂、工程量大等缺点,以实现复杂难采矿体的安全、高效、低成本、低贫损开采的多重目标。
【关键词】:倾斜矿体开采方法
一、矿体开采技术难点
1.1深部矿体开采技术条件有以下特点:
(1)矿体倾角为35°~40°,这是高效率采矿方法应用的难点,其一是因为矿体倾角不够陡,无法在采场内实现重力放矿,使采场的出矿工艺变得复杂;其二是由于矿体倾角不够缓,高效率的无轨出矿设备无法直接在回采矿体下盘底板上运行,同时也使电耙的使用受到限制;
(2)矿体水平厚度为5~8m,属于中厚偏薄矿体,使用大型高效
采矿机械将受到空间的制约;
(3)矿体沿走向连续性好,分步骤回采将导致矿柱损失或胶结充填的高成本;
(4)矿体边界不稳定,局部膨大缩小、尖灭再现屡见,矿体品位分布极不均匀,矿体中常有形态、厚度各异的夹石产出,回采贫化损失控制十分困难;
二、采矿方法优化选择
2.1 采矿方法优化选择
就深部矿体赋存条件而言,深部矿体的采矿方法只能限于在空场采矿法和充填采矿法中选用。
因此,初步拟定可供选择的采矿方法主要有4个方案,即方案1,盘区机械化上向分层充填连续采矿法;方案2,电耙出矿上向水平分层充填连续采矿法;方案3,电耙出矿爆力运搬采矿法;方案4,电耙出矿分段空场嗣后充填采矿法。
通过对各方案可望达到的技术经济指标和存在的优、缺点进行比较,方案4由于采准工程量大、采场准备时间长、综合生产能力低而被淘汰。
在余下方案的综合经济比较中,各方案的经济指标虽有区别,但差距不大,优劣势不明显,为全面准确地评价各方案,达到最优化目标,用模糊数学方法对3个方案进行了综合评判,其中主要考虑方案的安全因素(b1)、经济因素(b2)、资源因素(b3)、效率因素(b4)。
而安全因素(b1)中又主要考虑顶板安全(c1)和通风条件(c2);经济因素(b2)中主要考虑采矿成本(c3)、采切比(c4)、采矿损失率(c5)、采矿贫化率(c6)和采矿效率(c7);
效率因素(b4)中主要考虑采矿效率(c7)和生产能力(c8)。
计算得出方案1、方案2、方案3的特征值分别为0.878、0.635和0.511,根据最大隶属度原则,方案1为最优方案。
2.2 采场稳定性数值模拟与参数优化
2.2.1 采场稳定性分析
对水平厚度为15m单层矿体进行了模拟计算。
在整个中段高度内,随着回采高度的不断增加,顶板内的最大拉应力不断减小,而采场周边或矿柱内的最大主应力和最大剪应力以及顶板最大下沉量则
不断增加。
对于上向充填法而言,最关键的是采场顶板的稳定性,顶板拉应力是最值得关注的因素。
当采场跨度为5m时,顶板内的最大拉应力值仅为0.872mpa;当采场跨度增大至10m时,顶板最大拉应力值为2.384mpa;采场跨度为15m时,顶板最大拉应力值为3.103mpa。
2.2.2 采场结构参数优化
采场顶板拉应力是导致上向分层充填法顶板失稳的根本原因,顶板拉应力的大小又与采场跨度和顶板面积直接相关。
然而,分层回采采场跨度一般依矿体厚度而定,为控制顶板拉应力的大小,可调节采场沿走向长度值,以控制暴露面积的大小。
根据数值计算结果,推荐的采场极限暴露面积为400~600m2,原则上跨度大时取小值,跨度小时取大值以这一数据为基础。
2.3 工业试验
试验矿块为ⅰ号矿体-180~-130m水平,矿块长约30m,最大水
平厚度22m,平均厚度15m,平均品位3.5g/t,矿体倾角30°~40°,矿体受一条产状为28°∠87°后期断裂影响,造成矿体水平和垂直方向错动。
矿体为断裂形成的碳酸盐化硅质碎裂岩,属中等稳固,下盘围岩稳固性中等,上盘围岩稳固性较差。
矿石和围岩体重为2.8t/m3,松散系数为1.5。
矿体与围岩分界线不明显,局部分支复合、膨大缩小,夹石常现,经取样分析来确定矿体界线。
每隔12.5m 高度从斜坡道掘进一条距矿体下盘边界水平距离约30~35m、与矿体走向平行的分段平巷,从分段平巷沿矿块长度中线向采场下向掘进采场联络斜巷,并在矿体中掘进入行通风充填天井,第一分段采场联络斜巷到达矿体后,再水平掘进拉底平巷至矿体上盘边界,形成拉底平巷,脉外溜井与各分段平巷相通,所有采出矿石通过溜井放出。
自拉底平巷开始,先用挑顶刷帮的方式将拉底平巷扩大为高约3.5m,宽约6m的切割槽,并揭露矿体的水平全厚,然后以切割槽两壁为凿岩工作面,全宽拉底至采场两端边界,形成采场的拉底空间。
凿岩使用7655型气腿式凿岩机和“一”字型钎头水平凿岩,炮孔直径ф38~40mm,深度3.3m。
采用多段毫秒微差爆破工艺,对于顶板暴露面或矿柱周边处的边孔,采用光面爆破工艺,对充填体则采用留护壁的保护措施,以减少爆破对回采周边的破坏和影响。
由正交试验得出落矿最佳爆破参数为孔距0.9m,排距0.7m,装药系数0.7;光面爆破最佳参数为孔距0.6m,光爆层厚度0.7m,装药线密度0.25kg/m。
采场通风采用主导风流加局扇实现工作面通风,新鲜风流从下盘中段运输平巷进入采场工作面,污风从采场通风充
填井至上中段回风系统排出。
回采工作面的矿石用电动铲运机搬运至采场下盘脉外溜井中,溜至中段运输水平装矿平巷装车运出。
为减少出矿中尾砂充填料混入而造成贫化,工作面出矿时,底板上先保留厚度0.2~0.3m的矿石作为垫层,待分层回采结束前最终清除。
出矿过程中的大块(大块率一般为1%~2%)集中于工作面经二次爆破破碎后再搬运至溜井中。
在分层回采完毕并验收合格后,清理完工作面残矿并挑顶垫高联络道底板或封闭出口、安设充填脱水管、架设充填管道、架设采场端部砂袋隔墙等,即可实施充填。
充填料为粒径+0.074mm的分级尾砂,不加任何胶结剂。
当暴露面积在允许范围内时,采场顶板除局部极不稳固或破坏严重时需采用长锚索及锚杆支护外,一般情况不需支护。
试验中采用stl-12型微振监测定位预报系统对顶板实施动态跟踪监测和冒顶定位预报,有效地保障了采场作业设备和人员安全。
工业试验得到的主要技术经济指标为:单元生产能力为185.7t/d,采矿损失率为2.25%,采矿贫化率为3.39%,千吨采切比为37.45m3/kt,凿岩工效为84t/工班,出矿工效为46.4t/工班。
三、几点结论
(1)盘区机械化上向分层尾砂充填连续采矿法,采用下盘脉外采准、分层连续回采、水平浅孔光面落矿、铲运机出矿、人工隔墙分级尾砂充填、微振监测定位预报系统,动态跟踪监测顶板安全的综合配套工艺,实现了倾斜多变难采中厚矿体的安全、高效、低贫损、无界限连续回采。
(2)工业试验所取得的技术指标,在同类矿山中处于领先水平。
(3)采用下盘脉外采准布置和连续采矿工艺,采准工程量少,消除了间柱和中段矿柱损失,无轨出矿设备调节能力强,可同时服务于多个采场,作业效率高;分层回采工艺可灵活调整回采边界、剔除夹石和有效降低矿体边缘损失。
(4)采用人工隔墙分级尾砂充填工艺,用不加任何胶结剂的分级尾砂充填后,亦能实现充填体的自立,大大降低了充填成本。
(5)采用stl-12型微振监测定位预报系统监测采区岩体,实现空间定位和冒顶预报,大大增强了采场作业人员和设备的安全性。