第4章.金属材料的塑性变形与再结晶
实验七 材料的塑性变形和再结晶

滑移变形具有以下特点: ①滑移在切应力作用下产生(图2)。
图 2 晶体在切应力作用下的变形
②滑移沿原子密度最大的晶面和晶 向发生。
滑移常沿晶体 中原子密度最 大的晶面和晶 向发生,因为 原子密度最大 的晶面之间间 距最大,点阵 阻力最小,原 子密度最大晶 向上原子间最 短,结合力最 弱,因此产生 滑移所需切应 力最小。
因此,一般在室温使用的 结构材料都希望获得细小而均 匀的晶粒。因为细晶粒不仅使 材料具有较高的强度、硬度, 而且也使它具有良好的塑性和 韧性,即具有良好的综合力学 性能。故生产中总是尽可能地 细化晶粒。
2.2 冷塑性变形对金属组织和性能的影响
塑性变形后,金属在组织和性能方面发生四个方面的变化: 1)产生纤维组织,性能由各向同性趋于各向异性。
• 变形金属在加热中一般经历三个过程: (1)回复 (2)再结晶 (3)晶粒长大
变形金属加热时组织和性能变化示意图
回复 再结晶
晶粒长大
组 织
变 内应力
化
性
能 变
强度
化
晶粒度 塑性
(1)回复
(2)再结晶
• 由于再结晶后组织的复原,因而金属的强度、硬度下降, 塑性、韧性提高,加工硬化消失。
再结晶温度(T再): 通常指经大变形度(70~80%)的变形后,在规定
图5a为锌的变形孪晶,其形貌特征为薄透镜状。纯铁在低温 下受到冲击时也容易产生变形孪晶,其形貌如图5b所示,在 这种条件下萌生孪晶并长大的速度大大超过了滑移速度。
a 锌的变形孪晶
100
b 铁的变形孪晶
图5 变形孪晶光学显微形貌
100
工业纯铁压缩变形——滑移线
纯锌冲击变形——孪晶
2.多晶体的塑性变形
金属的塑性变形与再结晶

实验名称:金属的塑性变形与再结晶实验类型:一、实验目的和要求(必填)二、实验内容和原理(必填)三、主要仪器设备(必填)四、实验步骤与实验结果(必填)五、讨论、心得(必填)一、实验目的1.了解冷塑性变形对金属材料的内部组织与性能的影响;2.了解变形度对金属再结晶退火后晶粒大小的影响。
二、实验原理金属塑性变形的基本方式有滑移和孪生两种。
在切应力作用下,晶体的一部分沿某一晶面相对于另一部分滑动,这种变形方式称为滑移;在切应力作用下,晶体的一部分沿某一晶面相对另一部分产生剪切变形,且变形部分与未变形部分的位向形成了镜面对称关系,这种变形方式称为孪生。
(一) 冷塑性变形对金属组织与性能的影响若金属在再结晶温度以下进行塑性变形,称为冷塑性变形。
冷塑性变形不仅改变了金属材料的形状与尺寸,而且还将引起金属组织与性能的变化。
金属在发生塑性变形时,随着外形的变化,其内部晶粒形状由原来的等轴晶粒逐渐变为沿变形方向伸长的晶粒,在晶粒内部也出现了滑移带或孪晶带。
当变形程度很大时,晶粒被显著地拉成纤维状,这种组织称为冷加工纤维组织。
同时,随着变形程度的加剧,原来位向不同的各个晶粒会逐渐取得近于一致的位向,而形成了形变织构,使金属材料的性能呈现出明显的各向异性。
金属经冷塑性变形后,会使其强度、硬度提高,而塑性、韧性下降,这种现象称为加工硬化。
(二) 冷塑性变形后金属在加热时组织与性能的变化金属经冷塑性变形后,由于其内部亚结构细化、晶格畸变等原因,处于不稳定状态,具有自发地恢复到稳定状态的趋势。
但在室温下,由于原子活动能力不足,恢复过程不易进行。
若对其加热,因原子活动能力增强,就会使组织与性能发生一系列的变化。
1.回复当加热温度较低时,原子活动能力尚低,故冷变形金属的显微组织无明显变化,仍保持着纤组织的特征。
此时,因晶格畸变已减轻,使残余应力显著下降。
但造成加工硬化的主要原因未消除,故其机械性能变化不大。
2.再结晶当加热温度较高时,将首先在变形晶粒的晶界或滑移带、孪晶带等晶格畸变严重的地带,通过晶核与长大方式进行再结晶。
“金属的塑性变形与再结晶实验”实验报告.docx

金属的塑性变形与再结晶实验”实验报告、实验目的( 1) 了解冷塑性变形对金属材料的内部组织与性能的影响。
( 2) 了解变形度对金属再结晶退火后晶粒大小的影响。
二、实验原理金属材料在外力作用下,当应力大于弹性极限时,不但会产生弹性变形,还会产生塑性变形。
塑性变形的结果不仅改变金属的外形和尺寸,也会改变其内部的组织和性能。
在冷塑性形变过程,随着变形程度的增大,金属内部的亚晶增多,加上滑移面转动趋向硬位向和位错密度增加等原因,金属的强度和硬度升高,塑性和韧性下降,这种现象称为加工硬化。
加工硬化后的金属内能升高,处在不稳定的状态,并有想稳定状态转变的自发趋势。
若对其进行加热,使其内部原子活动能力增大,随着加热温度逐渐升高,金属内部依次发生回复、再结晶和晶粒长大3 个阶段。
冷塑性变形金属经再结晶退火后的晶粒大小,不仅与再结晶退火时的加热温度有关,,而且与再结晶退火前预先冷变形程度有关。
当变形度很小时,由于金属内部晶粒的变形也很小,故晶格畸变也小,晶粒的破碎与位错密度增加甚微,不足以引起再结晶现象发生,故晶粒大小不变。
当变形度在2%~10% 范围内时,由于多晶体变形的特点,金属内部各个晶粒的变形极不均匀(即只有少量晶粒进行变形) ,再结晶是晶核的形成数量很少,且晶粒极易相互并吞长大,形成较粗大的晶粒,这样的变形度称为临界变形度。
大于临界变形度后,随着变形量的增大,金属的各个晶粒的变形逐步均匀化,晶粒破碎程度与位错密度也随着增加,再结晶时晶核形成的数量也增多,所以再结晶退火后晶粒较细小而均匀。
为了观察再结晶退火后铝片的晶粒大小,必须把退火后的铝片放入一定介质中进行浸蚀,由于各个晶粒内原子排列的位向不同,对浸蚀剂的腐蚀不同,因而亮暗程度不同,就能观察到铝片内的晶粒。
三、实验装置及试件工业纯铝片、铝片拉伸机、浸蚀剂( 15%HF+45%HCL+15%HN ??3+25% ??2??组成的混合酸)、HV-120型维氏硬度计、小型实验用箱式炉、钢皮尺、划针、扳手、放大镜。
第四章金属及合金的塑性变形和再结晶2

(二) 晶粒大小对金属力学性能的影响 金属的晶粒越细,其强度和硬度越高。 金属的晶粒越细,其强度和硬度越高。 因为金属晶粒越 细,晶界总面积 越大, 越大,位错障碍 越多;需要协调 越多; 的具有不同位向 的晶粒越多, 的晶粒越多,使 金属塑性变形的 抗力越高。 抗力越高。
晶 粒 大 小 与 金 属 强 度 关 系
二、多相合金的塑性变形与弥散强化 当合金的组织由多相混合物组成时,合金的塑性变 当合金的组织由多相混合物组成时, 形除与合金基体的性质 有关外, 有关外, 还与第二相的性质、形 还与第二相的性质、 态、大小、数量和分布 大小、 有关。 有关。
固溶体第二相) α+β钛合金 固溶体第二相 β钛合金(固溶体第二相
应变
脆性 材料 塑性材料
通过细化晶粒来同时 提高金属的强度、 提高金属的强度、硬 度、塑性和韧性的方 法称细晶强化 细晶强化。 法称细晶强化。
三、合金的塑性变形
合金可根据组织分为单相固溶体和多相混合物两种. 合金可根据组织分为单相固溶体和多相混合物两种 单相固溶体 合金元素的存在,使合金的变形与纯金属显著不同 合金元素的存在,使合金的变形与纯金属显著不同.
密排六方晶格金属滑移系少,常以孪生方式变形。 密排六方晶格金属滑移系少,常以孪生方式变形。 体心立方晶格金属只有在低温或冲击作用下才发生 孪生变形。面心立方晶格金属, 孪生变形。面心立方晶格金属,一般不发生孪生变 形,但常发现有孪晶存在,这是由于相变过程中原 但常发现有孪晶存在, 子重新排列时发生错排而产生的, 退火孪晶。 子重新排列时发生错排而产生的,称退火孪晶。
钛合金六方相中的形变孪晶
奥氏体不锈钢中退火孪晶
二、多晶体金属的塑性变形
单个晶粒变形与单晶体相似 多晶 单个晶粒变形与单晶体相似,多晶 体变形比单晶体复杂。 体变形比单晶体复杂。 ㈠晶界及晶粒位向差的影响 1、晶界的影响 、 当位错运动到晶界附近时,受到 当位错运动到晶界附近时, 晶界的阻碍而堆积起来,称位错的 晶界的阻碍而堆积起来 称 塞积。要使变形继续进行 塞积。要使变形继续进行, 则必 须增加外力, 须增加外力 从而使金属的变形 抗力提高。 抗力提高。
金属的塑性变形与再结晶

等轴晶粒,机械性能完全恢复。
(三)再结晶后晶粒大小与变形量的关系
冷变形金属再结晶后晶粒大小除与加 热温度、保温时间有关外,还与金属的预 先变形量有关。 当变形度很小时,金属不发生再结晶。
晶粒 大小
这是由于晶内储存的畸变能很小,不足以
进行再结晶而保持原来状态,当达到某一 变形度时,再结晶后的晶粒特别粗大,该
2
3 4
低碳钢
低碳钢 低碳钢
压缩58%
压缩45%,550℃退火半小时 压缩58%,550℃退火半小时
伸长的晶粒
部分等轴晶 部分等轴晶
5
6 7 8
低碳钢
低碳钢 低碳钢 低碳钢
压缩45%,650℃退火半小时
压缩58%,650℃退火半小时 压缩45%,700℃退火半小时 压缩58%,700℃退火半小时
完全再结晶
c. 对比分析不同变形量,不同退火温度对晶粒大小的影响。
(二)塑性变形后的回复与再结晶
金属经冷塑性变形后,在热力学上处于不稳定状态,
必有力求恢复到稳定状态的趋势。
但在室温下,由于原子的动能不足,恢复过程不易进 行,加热会提高原子的活动能力,也就促进了这一恢复 过程的进行。 加热温度由低到高,其变化过程大致分为回复、再结 晶和晶粒长大三个阶段,当然这三个阶段并非截然分开。
变形度称之临界变形度。
一般金属的临界变形度在2%~10%范 围内。此后,随着变形度的增加,再结晶
临界变形度
预先变形程度
预先变形程度对晶粒度的影响
后的晶粒度逐渐变细。
三、实验方法
1.实验材料及设备 (1)金相显微镜; (2)低碳钢不同变形量及再结晶状态金相样品一套;
编号 1 材料 低碳钢 处理状态 压缩45% 组织 伸长的晶粒
材料科学基础重点总结4 材料形变和再结晶
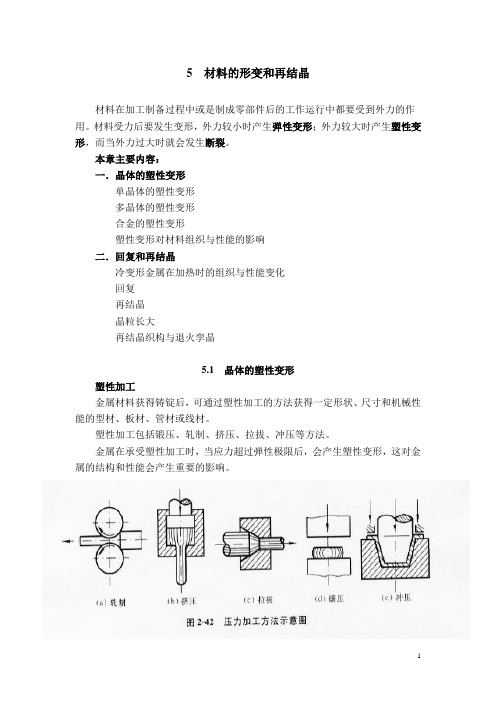
5 材料的形变和再结晶材料在加工制备过程中或是制成零部件后的工作运行中都要受到外力的作用。
材料受力后要发生变形,外力较小时产生弹性变形;外力较大时产生塑性变形,而当外力过大时就会发生断裂。
本章主要内容:一.晶体的塑性变形单晶体的塑性变形多晶体的塑性变形合金的塑性变形塑性变形对材料组织与性能的影响二.回复和再结晶冷变形金属在加热时的组织与性能变化回复再结晶晶粒长大再结晶织构与退火孪晶5.1 晶体的塑性变形塑性加工金属材料获得铸锭后,可通过塑性加工的方法获得一定形状、尺寸和机械性能的型材、板材、管材或线材。
塑性加工包括锻压、轧制、挤压、拉拔、冲压等方法。
金属在承受塑性加工时,当应力超过弹性极限后,会产生塑性变形,这对金属的结构和性能会产生重要的影响。
5.1.1 单晶体的塑性变形单晶体塑性变形的两种方式:滑移孪生滑移:滑移是晶体在切应力的作用下,晶体的一部分相对于另一部分沿着某些晶面和晶向发生相对滑动。
滑移线:为了观察滑移现象,可将经良好抛光的单晶体金属棒试样进行适当拉伸,使之产生一定的塑性变形,即可在金属棒表面见到一条条的细线,通常称为滑移线.滑移带:在宏观及金相观察中看到的滑移带并不是单一条线,而是由一系列相互平行的更细的线所组成的,称为滑移带。
滑移系:塑性变形时位错只沿着一定的晶面和晶向运动,这些晶面和晶向分别称为“滑移面”和“滑移方向”。
一个滑移面和此面上的一个滑移方向结合起来组成一个滑移系。
滑移的临界分切应力τk晶体的滑移是在切应力作用下进行的,但其中许多滑移系并非同时参与滑移,而只有当外力在某一滑移系中的分切应力达到一定临界值时,该滑移系方可以首先发生滑移,该分切应力称为滑移的临界分切应力。
滑移的特点晶体的滑移并不是晶体的一部分相对于另一部分同时做整体的刚性的移动,而是通过位错在切应力作用下沿着滑移面逐步移动的结果,因此实际滑移的临界分切应力τk 比理论计算的低得多。
(滑移面为原子排列最密的面)单晶体滑移时,除滑移面发生相对位移外,往往伴随着晶面的转动。
金属的塑性变形与再结晶

实验六 金属的塑性变形与再结晶(Plastic Deformation and Recrystallization of Metals )实验学时:2 实验类型:综合前修课程名称:《材料科学导论》适用专业:材料科学与工程一、实验目的1. 观察显微镜下变形孪晶与退火孪晶的特征;2. 了解金属经冷加工变形后显微组织及机械性能的变化;3. 讨论冷加工变形度对再结晶后晶粒大小的影响。
二、概述1. 显微镜下的滑移线与变形孪晶金属受力超过弹性极限后,在金属中将产生塑性变形。
金属单晶体变形机理指出,塑性变形的基本方式为:滑移和孪晶两种。
所谓滑移,是晶体在切应力作用下借助于金属薄层沿滑移面相对移动(实质为位错沿滑移面运动)的结果。
滑移后在滑移面两侧的晶体位向保持不变。
把抛光的纯铝试样拉伸,试样表面会有变形台阶出现,一组细小的台阶在显微镜下只能观察到一条黑线,即称为滑移带。
变形后的显微组织是由许多滑移带(平行的黑线)所组成。
在显微镜下能清楚地看到多晶体变形的特点:① 各晶粒内滑移带的方向不同(因晶粒方位各不相同);② 各晶粒之间形变程度不均匀,有的晶粒内滑移带多(即变形量大),有的晶粒内滑移带少(即变形量小);③ 在同一晶粒内,晶粒中心与晶粒边界变形量也不相同,晶粒中心滑移带密,而边界滑移带稀,并可发现在一些变形量大的晶粒内,滑移沿几个系统进行,经常看见双滑移现象(在面心立方晶格情况下很易发现),即两组平行的黑线在晶粒内部交错起来,将晶粒分成许多小块。
(注:此类样品制备困难,需要先将样品进行抛光,再进行拉伸,拉伸后立即直接在显微镜下观察;若此时再进行样品的磨光、抛光,滑移带将消失,观察不到。
原因是:滑移带是位错滑移现象在金属表面造成的不平整台阶,不是材料内部晶体结构的变化,样品制备过程会造成滑移带的消失。
)另一种变形的方式为孪晶。
不易产生滑移的金属,如六方晶系的镉、镁、铍、锌等,或某些金属当其滑移发生困难的时候,在切应力的作用下将发生的另一形式的变形,即晶体的一部分以一定的晶面(孪晶面或双晶面)为对称面,与晶体的另一部分发生对称移动,这种变形方式称为孪晶或双晶。
工程材料与热处理 第4章 金属的塑性变形与再结晶

一、滑移
滑移只能在切应力 作用下才会发生, 不同金属产生滑移 的最小切应力(称 滑移临界切应力) 大小不同。钨、钼、 铁的滑移临界切应 力比铜、铝的要大。
10
一、滑移
由于位错每移出 晶体一次即造成 一个原子间距的 变形量, 因此晶 体发生的总变形 量一定是这个方 向上的原子间距 的整数倍。
滑移带
17
二、位错滑移机制
通过位错的移动实现滑移时: 1、只有位错线附近的少数原子移动; 2、原子移动的距离小于一个原子间距; 所以通过位错实现滑移时,需要的力较小;
18
二、位错滑移机制
金属的塑性变形是由滑移这种方式进行的, 而滑移又是通过位错的移动实现的。所以, 只要阻碍位错的移动就可以阻碍滑移的进 行,从而提高了塑性变形的抗力,使强度 提高。金属材料常用的五种强化手段(固 溶强化、加工硬化、晶粒细化、弥散强化、 淬火强化)都是通过这种机理实现的。
35
链条板的轧制
材料为Q345(16Mn) 1200 钢 的自行车链条经 1000 过五次轧制,厚度由 3.5mm压缩到1.2mm, 800 总变形量为65%,硬 600 度从150HBS提高到 400 275HBS;抗拉强度从 200 510MPa提高到980MPa; 0 使承载能力提高了将近 一倍。
滑移方向对滑移所起的作用比滑移面大, 所以面心立方晶格金属比体心立方晶格金 属的塑性更好。 金、银、铜、铝等金属的塑性高于铁、铬 等金属;而铁的塑性又高于锌、镁等金 属。
15
二、位错滑移机制
滑移非刚性滑动,而是由位错的移动实现 的(1934年提出 )。
16
二、位错滑移机制
滑移是晶体内部位错在切应力作用下运动的结果。滑移 并非是晶体两部分沿滑移面作整体的相对滑动, 而是通 过位错的运动来实现的。 在切应力作用下,一个多余半 原子面从晶体一侧到另一侧运动, 即位错自左向右移动 时, 晶体产生滑移。
金属的塑性变形与再结晶

§2 冷塑性变形对金属组织和性能的影响
1.晶粒变形,形成纤维组织:
在外力的作用下,晶粒被拉长或被压扁,当变形足够大时,晶 界变得模糊不清,不易分辨。
“纤维组织”
工业纯铁表面的滑移带
变形前
变形后
变形前后晶粒形状变化示意图
工业纯铁变形度为80%的显微组织
2.亚结构形成,材料加工硬化:
随着变形量的增大,位错密度增大,晶粒破碎成亚晶 粒,晶格产生严重畸变,晶体缺陷(空位、位错、晶界、 亚晶界)增多。滑移的阻力变大,强度与硬度提高,塑 韧性降低。 加工硬化:金属材料经冷塑性变形后,随变形度增加, 强度硬度升高,塑性韧性降低的现象称为加工硬化或形 变强化。加工硬化是提高材料强度的有效手段之一。
滑移系=滑移面*滑移方向
体心立方 6*2=12
面心立方 4*3=12
密排六方 1*3=3
三种典型金属晶体结构的滑移系(密排面和密排方向)
滑移的微观机制
τ τ τ
τ
τ
τ
位错运动造成滑移的示意图
滑移实质上是位错在滑移面上运动的结果,在切应力的作用下, 晶体中形成一刃型位错,这一多余半原子面会由左向右逐步移动, 当这个位错移到晶体右边缘时,便在右侧表面形成了滑移量为一个 原子间距大小的台阶。若大量位错在该滑移面上移动出晶体时,就 会在晶体表面产生滑移量达几千埃的宏观可见的台阶(滑移线)。
晶向相对于另一部分发生滑动。 Ψ=45º 软位向 Ψ=0º 或 90º 硬位向
产生滑移的晶面和晶向分别 称为滑移面和滑移方向。
滑移的特征——滑移带和滑移线
滑移带
滑移线
工业纯铁表面的滑移带
滑移系:一个滑移面和该面上的一个滑移方向构成一个滑移系,
每一个滑移系表示晶体在产生滑移时可能采取的一个空间位向。
实验三 金属塑性变形与再结晶

实验三金属塑性变形与再结晶一、实验目的认识金属冷变形加工后及经过再结晶退火后的组织性能和特征变化;研究形变程度对再结晶退火前后组织和性能的影响。
加深对加工硬化现象和回复再结晶的认识。
二、基本原理1、金属冷塑性变形后的显微组织和性能变化金属冷塑性变形为金属在再结晶温度以下进行的塑性变形。
金属在发生塑性变形时,外观和尺寸发生了永久性变化,其内部晶粒由原来的等轴晶逐渐沿加工方向伸长,在晶粒内部也出现了滑移带或孪晶带,当变形程度很大时,晶界消失,晶粒被拉成纤维状。
相应的,金属材料的硬度、强度、矫顽力和电阻等性能增加,而塑性、韧性和抗腐蚀性降低。
这一现象称为加工硬化。
为了观察滑移带,通常将已抛光并侵蚀的试样经适量的塑性变形后再进行显微组织观察。
注意:在显微镜下滑移带与磨痕是不同的,一般磨痕穿过晶界,其方向不变,而滑移带出现在晶粒内部,并且一般不穿过晶界。
2、冷塑性变形后金属加热时的显微组织与性能变化金属经冷塑性变形后,在加热时随着加热温度的升高会发生回复、再结晶、和晶粒长大。
(1)回复当加热温度较低时原子活动能力尚低,金属显微组织无明显变化,仍保持纤维组织的特征。
但晶格畸变已减轻,残余应力显著下降。
但加工硬化还在,固其机械性能变化不大。
(2)再结晶金属加热到再结晶温度以上,组织发生显著变化。
首先在形变大的部位(晶界、滑移带、孪晶等)形成等轴晶粒的核,然后这些晶核依靠消除原来伸长的晶粒而长大,最后原来变形的晶粒完全被新的等轴晶粒所代替,这一过程为再结晶。
由于金属通过再结晶获得新的等轴晶粒,因而消除了冷加工显微组织、加工硬化和残余应力,使金属又重新恢复到冷塑性变形以前的状态。
金属的再结晶过程是在一定的温度范围能进行的,通常规定在一小时内再结晶完成95%所对应的温度为再结晶温度,实验证明,金属熔点越高,再结晶温度越高,其关系大致为:T=0.4T熔。
(3)晶粒长大再结晶完成后,继续升温(或保温),则等轴晶粒以并容的方式聚集长大,温度越高,晶粒越大。
实验二 金属的塑性变形与再结晶

实验二金属的塑性变形与再结晶一、实验目的1、了解工业纯铁经冷塑性变形后,变形量对硬度和显微组织的影响2、研究变形量对工业纯铝再结晶退火后晶粒大小的影响二、实验原理金属在外力作用下,当应力超过其弹性极限时将发生不可恢复的永久变形称为塑性变形。
金属发生塑性变形后,除了外形和尺寸发生改变外,其显微组织与各种性能也发生明显的变化。
经塑性变形后,随着变形量的增加,金属内部晶粒沿变形方向被拉长为偏平晶粒。
变形量越大,晶粒伸长的程度越明显。
变形量很大时,各晶粒将呈现出“纤维状”组织。
同时内部组织结构的变化也将导致机械性能的变化。
即随着变形量的增加,金属的强度、硬度上升,塑性、韧性下降,这种现象称为加工硬化或应变硬化。
在本实验中,首先以工业纯铁为研究对象,了解不同变形量对硬度和显微组织的影响。
冷变形后的金属是不稳定的,在重新加热时会发生回复、再结晶和晶粒长大等过程。
其中再结晶阶段金属内部的晶粒将会由冷变形后的纤维状组织转变为新的无畸变的等轴晶粒,这是一个晶粒形核与长大的过程。
此过程完成后金属的加工硬化现象消失。
金属的力学性能将取决于再结晶后的晶粒大小。
对于给定材料,再结晶退火后的晶粒大小主要取决于塑性变形时的变形量及退火温度等因素。
变形量越大,再结晶后的晶粒越细;金属能进行再结晶的最小变形量通常在2~8%之间,此时再结晶后的晶粒特别粗大,称此变形度为临界变形度。
大于此临界变形度后,随变形量的增加,再结晶后的晶粒逐渐细化。
在本实验中将研究工业纯铝经不同变形量拉伸后在550℃温度再结晶退火后其晶粒大小,从而验证变形量对再结晶晶粒大小的影响。
三、实验设备和材料1、实验设备箱式电阻炉、万能拉伸机、卡尺、低倍4X型金相显微镜、洛氏硬度计等2、实验材料(1)变形度为0%、30%、50%、70%的工业纯铁试样两套,其中一套用于塑性变形后的硬度测定,一套为已制备好的不同变形量下的金相标准试样,用于观察组织(2)工业纯铝试样,尺寸为160mm×20m m×0.5mm,(3)腐蚀液:40mlHNO3+30mlHCl+30mlH2O+5g纯Cu),硝酸溶液四、实验内容及步骤1、测定工业纯铁的硬度(HRB )与变形度的关系,观察不同塑性变形量后工业纯铁的金相显微组织(1)将工业纯铁的试样在万能拉伸实验机上分别进行0%、30%、50%、70%的压缩变形。
第四章 金属的塑性变形与回复再结晶
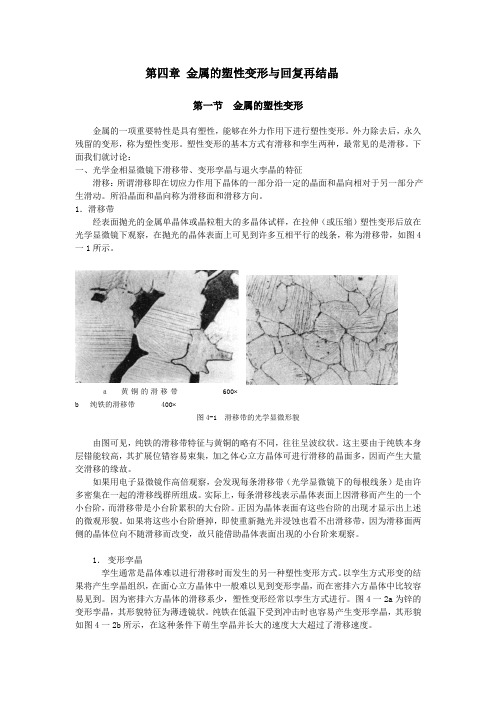
第四章金属的塑性变形与回复再结晶第一节金属的塑性变形金属的一项重要特性是具有塑性,能够在外力作用下进行塑性变形。
外力除去后,永久残留的变形,称为塑性变形。
塑性变形的基本方式有滑移和孪生两种,最常见的是滑移。
下面我们就讨论:一、光学金相显微镜下滑移带、变形孪晶与退火孪晶的特征滑移:所谓滑移即在切应力作用下晶体的一部分沿一定的晶面和晶向相对于另一部分产生滑动。
所沿晶面和晶向称为滑移面和滑移方向。
1.滑移带经表面抛光的金属单晶体或晶粒粗大的多晶体试样,在拉伸(或压缩)塑性变形后放在光学显微镜下观察,在抛光的晶体表面上可见到许多互相平行的线条,称为滑移带,如图4一1所示。
a黄铜的滑移带600⨯b 纯铁的滑移带 400⨯图4-1 滑移带的光学显微形貌由图可见,纯铁的滑移带特征与黄铜的略有不同,往往呈波纹状。
这主要由于纯铁本身层错能较高,其扩展位错容易束集,加之体心立方晶体可进行滑移的晶面多,因而产生大量交滑移的缘故。
如果用电子显微镜作高倍观察,会发现每条滑移带(光学显微镜下的每根线条)是由许多密集在一起的滑移线群所组成。
实际上,每条滑移线表示晶体表面上因滑移而产生的一个小台阶,而滑移带是小台阶累积的大台阶。
正因为晶体表面有这些台阶的出现才显示出上述的微观形貌。
如果将这些小台阶磨掉,即使重新抛光并浸蚀也看不出滑移带,因为滑移面两侧的晶体位向不随滑移而改变,故只能借助晶体表面出现的小台阶来观察。
1.变形孪晶孪生通常是晶体难以进行滑移时而发生的另一种塑性变形方式。
以孪生方式形变的结果将产生孪晶组织,在面心立方晶体中一般难以见到变形孪晶,而在密排六方晶体中比较容易见到。
因为密排六方晶体的滑移系少,塑性变形经常以孪生方式进行。
图4一2a为锌的变形孪晶,其形貌特征为薄透镜状。
纯铁在低温下受到冲击时也容易产生变形孪晶,其形貌如图4一2b所示,在这种条件下萌生孪晶并长大的速度大大超过了滑移速度。
a 锌的变形孪晶100⨯b 铁的变形孪晶 100⨯图4—2 变形孪晶光学显微形貌如果将变形孪晶试样重新磨制、抛光、浸蚀,是否如同滑移带那样也会消失呢?并不是这样的。
第四章金属材料的塑性变形与再结晶
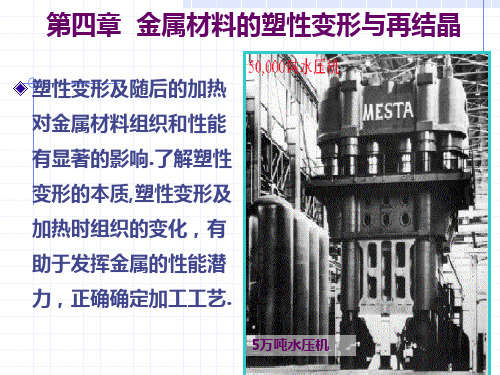
滑移方向上原子间距的 小于孪生方向上的原
整数倍,较大。
子间距,较小。
很大,总变形量大。
有限,总变形量小。
有一定的临界分切 压力 一般先发生滑移
所需临界分切应力远高于 滑移
滑移困难时发生
变形机制
全位错运动的结果 分位错运动的结果 34
(二) 多晶体金属的塑性变形
单个晶粒变形与单晶体相似,多晶体变形比单晶体复杂
① 晶界的特点:原子排列不规则;分布有大量缺陷
② 晶界对变形的影响:滑移、孪生多终止于晶界,极少穿 过。
35
当位错运动到晶界附近时,受到晶界的阻碍而堆积 起来,称位错的塞积。要使变形继续进行, 则必须增加 外力, 从而使金属的变形抗力提高。
36
晶界对塑性变形的影响
Cu-4.5Al合金晶 界的位错塞积
55
(4) 几何硬化:由晶粒转动引 起 由于加工硬化, 使已变形部 分发生硬化而停止变形, 而 未变形部分开始变形。没有 加工硬化, 金属就不会发生 均匀塑性变形。
未变形纯铁
加工硬化是强化金属的重要
手段之一,对于不能热处理
强化的金属和合金尤为重要
变形20%纯铁中的位错
56
2 对力学性能的影响
利弊
d. 孪生本身对金属塑性变形的贡献不大,但形成 的孪晶改变了晶体的位向,使新的滑移系开动, 间接对塑性变形有贡献。
33
总结
滑移
孪生
相同点
晶体位向
位移量 不 同 对塑变的贡献 点
变形应力
变形条件
1 切变;2 沿一定的晶面、晶向进行;3 不 改变结构。 不改变(对抛光面 改变,形成镜面对称关系 观察无重现性)。 (对抛光面观察有重现性)
1、晶粒取向和晶界对塑性变形的影响
第四章金属的塑性变形与再结晶

第四章金属的塑性变形与再结晶铸态组织具有晶粒粗大且不均匀、组织不致密及成分偏析等缺陷,需要经压力加工再使用。
金属的压力加工,就是通过使金属产生一定的塑性变形获得制件。
压力加工不仅改变其外形尺寸,且使内部的组织和性能发生改变。
因此研究金属塑性变形以及变形后材料的组织结构的变化规律,对于深入了解金属材料各项力学性能指标的本质,充分发挥材料强度的潜力,正确制定和改进金属压力加工的工艺,提高产品的质量以及合理使用材料等都具有重要意义。
第一节金属的塑性变形[教学目的] 理解单晶体的塑性变形,掌握多晶体的塑性变形。
[教学重点] 多晶体的塑性变形。
[教学难点] 多晶体的塑性变形。
[教学方法] 讲授。
[教学内容]所有变形中,塑性变形对组织和性能的影响最大。
为认识塑性变形的规律,首先研究单晶体的塑性变形。
一单晶体的塑性变形单晶体的塑性变形主要通过滑移和孪生方式进行。
1 滑移切应力作用下,晶体的一部分沿着一定晶面(滑移面)上的一定方向(滑移方向)相对于另一部分发生滑动,称为滑移。
外力在一定的晶面分解为垂直于晶面的正应力σN和平行于晶面的切应力τN。
σN引发弹性变形和脆性断裂,断口呈金属光泽;τN引发弹性变形、弹塑性变形和韧性断裂,断口灰暗无光泽。
滑移变形的5个要点:1)滑移只能在切应力作用下发生;2)滑移主要发生在原子排列最紧密或较紧密的晶面上,并沿着这些晶面上原子排列最紧密的方向进行。
(原因:最密排晶面之间的距离最远;最密排晶面上原子与邻近原子之间的阻力最小)3)滑移必然伴随着晶体的转动(正应力引起)。
4)滑移是滑移面上的位错运动造成的。
位错运动所需切应力远远小于刚性的整体滑移所需的切应力。
如铜刚性滑移要1540MPa,实际只有1MPa。
二多晶体的塑性变形1 晶界与晶粒位向的影响①晶界竹节现象多晶体金属中,晶界原子的排列不规则,局部晶格畸变严重,且易产生杂质原子和空位等缺陷的偏聚。
位错运动到晶界附近时容易受到晶界的阻碍。
《机械工程材料(第2版)》电子教案 第4章 金属的塑性变形与再结晶

4.1金属的塑性变形 4.2冷塑性变形对金属性能与组织的影响 4.3回复与再结晶 4.4金属的热塑性变形
4.1 金属的塑性变形
4.1.1单晶体的塑性变形
单晶体受外力作用,当外力较小时,发生弹性变形,当外力超 过一定数值后,发生塑性变形。单晶体的塑性变形主要是以 滑移的方式进行的。即晶体的一部分沿着一定的晶面和晶向 相对于另一部分发生滑动。晶体中能够发生滑移的晶面和晶 向,称为滑移面和滑移方向。滑移面和滑移方向越多,金属 的塑性越好。
在工业生产中,为保持金属经冷塑性变形后的高强度,往 往采取回复处理,以降低内应力,适当提高塑性。例如冷拔 钢丝弹簧加热到250—300℃,青铜丝弹簧加热到120~150℃, 就是进行回复处理,使弹簧的弹性增强,同时消除加工时带 来的内应力。
下一页 返回
4.3 回复与再结晶
2.再结晶
当冷塑性变形金属加热到较高温度时,由于原子活动能力 增加,原子可以离开原来的位置重新排列。由畸变晶粒通过 形核及晶核长大而形成新的无畸变的等轴晶粒的过程称为再 结晶。再结晶过程首先是在晶粒碎化最严重的地方产生新晶 粒的核心,然后晶核吞并旧晶粒而长大,直到旧晶粒完全被 新晶粒代替为止。
上一页 返回
4.2 冷塑性变形对金属性能与组织 的影响
金属的冷塑性变形可使金属的性能发生明显变化,这种变化是 由塑性变形时金属内部组织变化所决定的。
1.形成纤维组织,性能趋于各向异性 2.产生冷变形强化 3.形成形变织构 (择优取向) 4.产生残留应力
返回
4.3 回复与再结晶
1.回复
当加热温度不太高时,原子活动能力有所增加,原子已能 作短距离的运动,使晶格畸变程度大为减轻,从而使内应力 有所降低,这个阶段称为回复。然而这时的原子活动能力还 不是很强,所以金属的显微组织无明显变化,因此力学性能 也无明显改变。、硬度显著下降,塑性显著上升,使变形金属的组织 和性能基本上恢复到变形前的状态。
第四章金属及合金的塑性变形和再结晶3

在回复阶段,金属组织 在回复阶段, 变化不明显,其强度、 变化不明显,其强度、 硬度略有下降, 硬度略有下降,塑性略 有提高,但内应力、 有提高,但内应力、电 阻率等显著下降。 阻率等显著下降。 工业上,常利用回复现 工业上, 象将冷变形金属低温加 热,既稳定组织又保留 加工硬化, 加工硬化,这种热处理 去应力退火。 方法称去应力退火 方法称去过程, 和长大的过程,但不是相 变过程, 变过程,再结晶前后新旧 晶粒的晶格类型和成分完 全相同。 全相同。
SEM-再结晶晶粒在原 再结晶晶粒在原 变形组织晶界上形核 TEM-再结晶晶粒形核 再结晶晶粒形核 于高密度位错基体上
冷变形奥氏体不锈钢 加热时的再结晶形核
由于再结晶后组织的复 原,因而金属的强度、 因而金属的强度、 金属的强度 硬度下降,塑性、 硬度下降,塑性、韧性 提高,加工硬化消失。 提高,加工硬化消失。
冷变形(变形量为 黄铜580C 冷变形 变形量为38%)黄铜 变形量为 黄铜 保温15分后的的再结晶组织 保温 分后的的再结晶组织
冷变形黄铜组织性能随温度的变化
丝织构 板织构 无 有
各向异性导致的铜板 “制耳” 制耳”
形变织构示意图
二、对性能的影响 随冷塑性变形量增加,金属的强度、硬度提高,塑 随冷塑性变形量增加,金属的强度、硬度提高, 性、韧性下降的现象称加工硬化。 韧性下降的现象称加工硬化。 加工硬化
1040钢(0.4%C)
黄铜 黄铜 铜 1040钢 (0.4%C)
第三节 回复与再结晶
一、冷变形金属在加热时的组织和性能变化 金属经冷变形后 组织处于不稳定状态 有自发恢复 金属经冷变形后, 组织处于不稳定状态, 原子扩散能力小, 到稳定状态的倾向。但在常温下,原子扩散能力小 不稳定状态可长时间维持。加热可使原子扩散能力 不稳定状态可长时间维持。 增加,金属将依次发生回复、再结晶和晶粒长大。 增加,金属将依次发生回复、再结晶和晶粒长大。 回复
- 1、下载文档前请自行甄别文档内容的完整性,平台不提供额外的编辑、内容补充、找答案等附加服务。
- 2、"仅部分预览"的文档,不可在线预览部分如存在完整性等问题,可反馈申请退款(可完整预览的文档不适用该条件!)。
- 3、如文档侵犯您的权益,请联系客服反馈,我们会尽快为您处理(人工客服工作时间:9:00-18:30)。
位错是已滑移区和未滑移区的交界。
思考:
滑移的结果使晶体中的位错扫过滑移面而移到
晶体表面。 ——随着塑性变形 的进行,晶体中的位错 数量将不断减少?
答案是相反的!
——位错的增殖
弗兰克-瑞德位错增殖机理
Si晶体中观察到的弗兰克-瑞德增殖位错
金属材料的塑性变形特性
第四章
(二)孪生
孪生:切应力作用下晶体的一部分
质原子不仅使晶格发生畸变,阻碍位错运动,而且易被吸附在
位错附近,使位错被钉扎住,位错要脱钉,则必须增加外力, 从而使变形抗力提高。
金属材料的塑性变形特性
第四章
(二) 多相合金的塑性变形与弥散强化
合金的塑性变形除与合金基体的性质有关外,还与第二相 的性 质、形态、大小、数量和分布有关。 1、 第二相在晶界呈网状分布时,对合金的强度和塑性不利; 2、 第二相在晶内呈片状分布时,可提高强度、硬度,但会降 低塑性和韧性;
单个晶粒变形与单晶体相似。 而多晶体变形是一个不均匀的塑性变 形过程。
(一)晶界及晶粒位向差的影响
1. 晶界的影响 当位错运动到晶界附近时,由于 晶界处的原子排列紊乱,缺陷和 杂质多,能量高,对位错的滑移 起阻碍作用,位错受到晶界的阻 碍而堆积起来,称位错的塞积。使 位错运动阻力增大,从而使金属 的变形抗力提高。
(3)滑移→位错运动→原子移动的相对位移是原子间距的整 数值→不引起晶格位向的变化; 孪生→晶格切变→原子移动的相对位移是原子间距的分数 值→孪晶晶格位向改变→促进滑移。
(4)孪生产生的塑性变形量小(≤滑移变形量的10%), 但 引起的晶格畸变大。
金属材料的塑性变形特性
第四章
三、 多晶体的塑性变形
金属材料的塑性变形特性
第四章
2、滑移的特点:
(4) 滑移的同时伴随着晶体的转动
转动的原因:晶体滑移使试样两端的拉力不再处
于统一轴线,产生一个力矩使滑移面转动
转动结果:滑移面趋向与拉伸轴平行,使外力作 用在同一直线,使切应力分量大,更易于变形。 滑移后, 滑移面两侧晶体的结构、位向关系未发生变化。
金属材料的塑性变形特性
第四章
回复、再结晶和晶 粒的长大都是减少或消除 结构缺陷的过程。相应材 料的内应力、晶粒尺寸、 强度、塑性等性能也发生
对应变化。
回复与再结晶
第四章
一、 回复
回复是指在加热温度较低时,由于金属中的点缺陷及位错近
距离迁移而引起的晶内某些变化。如空位与其他缺陷合并、
同一滑移面上的异号位错相遇 合并而使缺陷数量减少等,但 仍保持高密度位错。
金属材料的塑性变形特性
第四章
2. 晶粒位向的影响
由于各相邻晶粒位向不同,当一处利于滑移方向晶粒发生滑
移时,必然受到周围位向不同的其他晶粒的约束,使滑移受
到阻碍,从而提高金属塑性变形抗力。
金属材料的塑性变形特性
第四章
(二) 晶粒大小的影响 晶粒越细,其强度和硬度越高。
细晶强化
晶粒越细晶界越 ,不同位向的晶粒也越 滑 移抗力 强度 晶粒越细晶粒数目越 变形均匀性 应力集 中,裂纹过早产生、扩展 塑性、韧性
× √
金属 铜 银 金 镍 镁 锌
金属材料的塑性变形特性
第四章
3、滑移的机理
滑移是通过滑移面上位错(一排原子)的运动来实 现的。
多脚 虫 的 爬 行
金属材料的塑性变形特性
第四章
3、滑移的机理
晶体通过位错运动产生滑移时,只在位错中心的少数 原子发生移动,它们移动的距离远小于一个原子间距,因 而所需临界切应力小,这种现象称作位错的易动性。
沿一定晶面和晶向相对于另一部
分发生均匀的移动。发生切变的
部分称孪生带或孪晶,沿其发生
孪生的晶面称孪生面,孪生的结 果使孪生面两侧的晶体呈镜面对 称。
金属材料的塑性变形特性
第四章
滑移和孪生:
(1) 滑移和孪生均在切应力作用下,沿一定晶面的一定晶向 进行,产生塑性变形。孪生使一部分晶体发生均匀移动, 滑移时伴随的移动只集中在滑移面上。 (2)孪生所需要的临界切应力比滑移大得多,变形速度极快 ,接近于声速。在滑移较难进行时发生孪生。
第四章
加工硬化意义: 1)一种有效的强化手段,对不能用热处理方法强化的合金 尤其重要; 2)均匀塑性变形和压力加工的保证; 3)金属具有较好的变形强化能力,具有防止短时超载断裂 能力,保证构件安全性; 4)↓塑性,↑切削性能 不利:塑性变形困难,给进一步变形带来困难 →中间退火→消除
塑性变形对组织与性能的影响
第四章
第二相在晶内呈弥散质点分布时,可显著提高材料的 强度和硬度,且分散的质点越多、越细,这种对材料
的强化作用越强。
这种强化方法称弥散强化或沉淀强化。
弥散强化
塑性变形对组织与性能的影响
第四章
§ 4.2 塑性变形对组织与性能的影响
一、塑性变形对金属组织结构的影响: 1、晶粒发生变形, 沿形变方向被拉长或压扁。 纤维组织形成 金属在外力作用下发生塑性变形时,随着变 形量的增加晶粒形状发生变化,沿变形方向被拉长或压扁。 当拉伸变形量很大时,晶粒变成细条状,金属中的夹杂物也பைடு நூலகம்被拉长,形成所谓纤维组织。
铜多晶试样拉伸后形成的滑移带
σ
金属材料的塑性变形特性
第四章
四、 合金的塑性变形(二元)
(一) 单相固溶体合金的塑性变形 固溶强化
单相固溶体合金组织与纯金属相同,其塑性变形过程也与多晶 体纯金属相似。但随溶质含量增加,固溶体的强度、硬度提高, 塑性、韧性下降,称固溶强化。 固溶强化的原因,是由于溶质原子与位错相互作用的结果,溶
第四章
2、使金属的性能产生各向异性。 3、影响金属的物理、化学性能 金属经塑性变形后,使电 阻增大,耐蚀性降低。 4、产生残余应力 (去除外力后残留于且平衡于金属内部的应 力)。 第一类内应力——宏观,表面和心部,塑性变形不均匀造成; 第二类内应力——微观,晶粒间或晶内不同区域变形不均; 第三类内应力——超微观,晶格畸变(>90%)。 内应力(特别是第一、二类)的存在,使金属强度降低,易产 生应力腐蚀,引起零件加工、淬火过程中的变形和开裂。因此, 金属在塑性变形后,通常要进行退火处理,以消除或降低内应 力
。
塑性变形对组织与性能的影响
第四章
2、亚结构形成 金属经大的塑性变形时,由于位错的密度增大和发生交互 作用,大量位错堆积在局部地区,并相互缠结, 形成不均 匀的分布,使晶粒分化成许多位向略有不同的小晶块,而 在晶粒内产生亚晶粒。
5%冷变形纯铝中的位错网
金属变形后的亚结构
塑性变形对组织与性能的影响
金属材料的塑性变形特性
第四章
2、滑移的特点:
(2) 滑移常沿晶体中原子密度最大 的晶面和晶向发生 ——原子密度最大的晶面和晶
向之间原子间距最大,结合力最弱,
产生滑移所需切应力最小。
沿其发生滑移的晶面和晶向分别叫做滑移面和滑移方向。 通常是晶体中的密排面和密排方向。
金属材料的塑性变形特性
第四章
2、滑移的特点:
第四章
3、形变织构 金属塑性变形到很大程度(70%以上)时,由于晶粒发生转动, 使各晶粒的位向趋近于一致,形成特殊的择优取向,这种有 序化的结构叫做形变织构。 丝织构——各晶粒的一定晶向平行于拉拔方向 板织构——各晶粒的一定晶面和晶向平行于轧制方向
丝织构 板织构
形变织构示意图
变形前 变形后 各向异性导致的“制耳”
2、滑移的特点:
(1)滑移只能在切应力的作用下发生。
正应力只能引起弹性 变形及解理断裂。 只有在切应力的作用下 金属晶体才能产生塑性变
形。
外力在晶面 切应力作 上的分解 用下的变 形
锌单晶拉 伸照片
正应力σ :仅使晶格产生弹性伸长,当超过原子间结合力时,使 将晶体拉断; 切应力τ :使晶格产生弹性歪扭,在超过滑移抗力时引起滑移 面两侧的晶体发生相对滑动。 产生滑移的最小切应力称临界切应力。
金属材料的塑性变形特性
第四章
(三) 多晶体金属的塑性变形过程
多晶体中首先发生滑移的是滑移系与外力夹角等于或接近于 45°的晶粒。当塞积位错前端的应力达到一定程度,加上 相邻晶粒的转动,使相邻晶粒中原来处于不利位向滑移系
上的位错开动,从而
使滑移由一批晶粒传 递到另一批晶粒,当 有大量晶粒发生滑移 σ 后,金属便显示出明 显的塑性变形。
珠光体
金属材料的塑性变形特性
第四章
3、第二相在晶内呈颗粒状弥散分布时
不可变形颗粒(硬)不易被切变,因而阻碍了位错的运动,
形成位错环,提高了变形抗力。
颗粒钉扎作用的电镜照片
金属材料的塑性变形特性
第四章
可变形颗粒(软颗粒)将被位错切开,对位错有一定的阻滞 作用。
电 镜 观 察 位错切割第二相粒子
金属材料的塑性变形特性
第4章 金属材料的塑性变形 与再结晶
§ § § § 4.1 4.2 4.3 4.4 金属材料的塑性变形特性 塑性变形对组织与性能的影响 回复与再结晶 金属材料的热加工
金属材料的塑性变形特性
第四章
§ 4.1 金属材料的塑性变形特性
金属经熔炼浇注成铸锭以后,通常要进行各种压力加工,如 轧制、挤压、冷拔、锻压、冲压等,以获得具有一定形状、 尺寸和力学性能的型材、板材、管材或线材,以及零件毛坯 或零件,并可以消除铸造过程中的某些缺陷。压力加工的实 质就是塑性变形。
第四章
3、滑移的机理
把滑移设想为刚性整体滑动所需的理论临界切应力值比
实际测量临界切应力值大3-4个数量级!
计算值 (MN/m2) 6400 4500 4500 11000 3000 4800 实测值 计算值与实 (MN/m2) 测值之比 1.0 0.5 0.92 5.8 0.83 0.94 6400 9000 4900 1900 3600 5100