天然气MRC液化工艺电气部分技术方案
天然气液化技术介绍
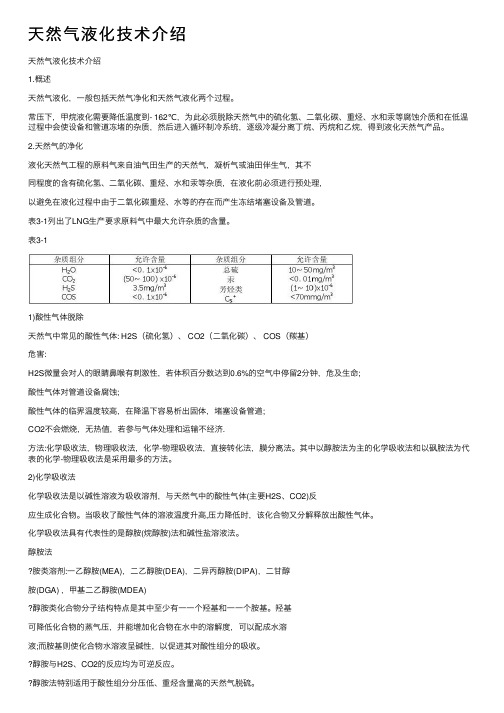
天然⽓液化技术介绍天然⽓液化技术介绍1.概述天然⽓液化,⼀般包括天然⽓净化和天然⽓液化两个过程。
常压下,甲烷液化需要降低温度到- 162℃,为此必须脱除天然⽓中的硫化氢、⼆氧化碳、重烃、⽔和汞等腐蚀介质和在低温过程中会使设备和管道冻堵的杂质,然后进⼊循环制冷系统,逐级冷凝分离丁烷、丙烷和⼄烷,得到液化天然⽓产品。
2.天然⽓的净化液化天然⽓⼯程的原料⽓来⾃油⽓⽥⽣产的天然⽓,凝析⽓或油⽥伴⽣⽓,其不同程度的含有硫化氢、⼆氧化碳、重烃、⽔和汞等杂质,在液化前必须进⾏预处理,以避免在液化过程中由于⼆氧化碳重烃、⽔等的存在⽽产⽣冻结堵塞设备及管道。
表3-1列出了LNG⽣产要求原料⽓中最⼤允许杂质的含量。
表3-11)酸性⽓体脱除天然⽓中常见的酸性⽓体: H2S(硫化氢)、 CO2(⼆氧化碳)、 COS(羰基)危害:H2S微量会对⼈的眼睛⿐喉有刺激性,若体积百分数达到0.6%的空⽓中停留2分钟,危及⽣命;酸性⽓体对管道设备腐蚀;酸性⽓体的临界温度较⾼,在降温下容易析出固体,堵塞设备管道;CO2不会燃烧,⽆热值,若参与⽓体处理和运输不经济.⽅法:化学吸收法,物理吸收法,化学-物理吸收法,直接转化法,膜分离法。
其中以醇胺法为主的化学吸收法和以砜胺法为代表的化学-物理吸收法是采⽤最多的⽅法。
2)化学吸收法化学吸收法是以碱性溶液为吸收溶剂,与天然⽓中的酸性⽓体(主要H2S、CO2)反应⽣成化合物。
当吸收了酸性⽓体的溶液温度升⾼,压⼒降低时,该化合物⼜分解释放出酸性⽓体。
化学吸收法具有代表性的是醇胺(烷醇胺)法和碱性盐溶液法。
醇胺法胺类溶剂:⼀⼄醇胺(MEA),⼆⼄醇胺(DEA),⼆异丙醇胺(DIPA),⼆⽢醇胺(DGA) ,甲基⼆⼄醇胺(MDEA)醇胺类化合物分⼦结构特点是其中⾄少有⼀⼀个羟基和⼀⼀个胺基。
羟基可降低化合物的蒸⽓压,并能增加化合物在⽔中的溶解度,可以配成⽔溶液;⽽胺基则使化合物⽔溶液呈碱性,以促进其对酸性组分的吸收。
常用的天然气液化流程
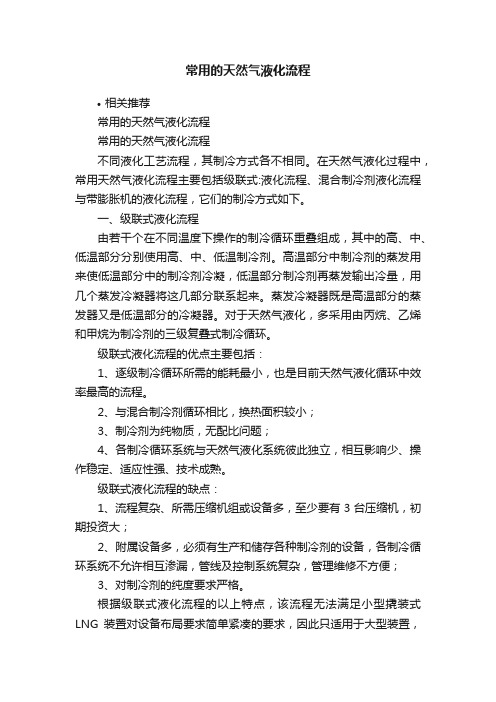
常用的天然气液化流程•相关推荐常用的天然气液化流程常用的天然气液化流程不同液化工艺流程,其制冷方式各不相同。
在天然气液化过程中,常用天然气液化流程主要包括级联式:液化流程、混合制冷剂液化流程与带膨胀机的液化流程,它们的制冷方式如下。
一、级联式液化流程由若干个在不同温度下操作的制冷循环重叠组成,其中的高、中、低温部分分别使用高、中、低温制冷剂。
高温部分中制冷剂的蒸发用来使低温部分中的制冷剂冷凝,低温部分制冷剂再蒸发输出冷量,用几个蒸发冷凝器将这几部分联系起来。
蒸发冷凝器既是高温部分的蒸发器又是低温部分的冷凝器。
对于天然气液化,多采用由丙烷、乙烯和甲烷为制冷剂的三级复叠式制冷循环。
级联式液化流程的优点主要包括:1、逐级制冷循环所需的能耗最小,也是目前天然气液化循环中效率最高的流程。
2、与混合制冷剂循环相比,换热面积较小;3、制冷剂为纯物质,无配比问题;4、各制冷循环系统与天然气液化系统彼此独立,相互影响少、操作稳定、适应性强、技术成熟。
级联式液化流程的缺点:1、流程复杂、所需压缩机组或设备多,至少要有3台压缩机,初期投资大;2、附属设备多,必须有生产和储存各种制冷剂的设备,各制冷循环系统不允许相互渗漏,管线及控制系统复杂,管理维修不方便;3、对制冷剂的纯度要求严格。
根据级联式液化流程的以上特点,该流程无法满足小型撬装式LNG装置对设备布局要求简单紧凑的要求,因此只适用于大型装置,常用于2 X 104~5 X 104m3/d的装置。
通过优化设备的配置,级联式液化流程可以与在基本负荷混合制冷剂厂中占主导地位的带预冷的混合制冷剂循环相媲美。
二、混合制冷剂液化流程该工艺是20世纪60年代末期,由级联式制冷工艺演变而来的,多采用烃类混合物(N2、C1、C2、C3、C4、C5)作为制冷剂,代替级联式制冷工艺中的多个纯组分,其组成根据原抖气的组成和压力确是,利用多组分混合物中重组分先冷凝、轻组分后冷凝的特性,将其依次冷凝、分离、节流、蒸发得到不同温度级的冷量,又据混合制冷剂是否与原料天然气相混合,分为闭式和开式两种混合制冷工艺。
天然气液化工艺与技术

天然气液化工艺与技术摘要:液化天然气在天然气的远洋运输,边远气田气体的利用以及城市燃气调峰中起到了重要的作用。
本文简要介绍了液化天然气(LNG的性质、用途,着重针对天然气的液化工艺进行了详细介绍,并对每种工艺的优缺点进行了分析比较,为国内LNG产业的发展提供了很好的借鉴作用。
一、引言当今世界人口数量的急剧增长,世界经济的快速发展,造成世界能源的需求量也持续增长。
天然气是一种清洁、高效、优质的能源与化工原料,逐渐吸引了人们的目光。
天然气的应用领域也日益广泛,例如发电、工业部门、天然气化工、天然气汽车及天然气合成油等方面。
我国拥有丰富的天然气资源,是世界天然气大国之一。
液化天然气(LNG是一种具有明显优越性的天然气应用形式的,尤其是在天然气的运输和存储方面。
因此,为了合理利用我国天然气资源,进行天然气液化技术的研究与应用是一项具有重大意义的重要工作,同时也对我国今后发展液化天然气工业具有非常重要的现实意义。
二、液化天然气的性质液化天然气,主要成分是甲烷,是地球上公认的最干净的能源。
油气田开采出来的天然气经过脱水、脱酸性气体及重烃组分,去除了一些有价值的成份,如氦,以及一些对下游产业不利的成分如水,和一些高分子碳氢化合物,之后再经冷却降温,最终得到天然气的液态产品。
液化天然气无色、无味、无毒且无腐蚀性,其体积约为同量气态天然气体积的1/625 ,重量仅为同体积水的45%左右,发热量为548 X108J/t。
天然气液化后便于进行经济可靠的运输,储存效率高、占地少、投资省,有利于城市负荷的平衡调节。
液化天然气生产过程中释放出的冷量还可回收利用,并且低温液化还可分离出部分有用的副产品,有利于环境保护,减少城市污染。
三、天然气的液化工艺天然气液化主要包括天然气净化(也称预处理)过程和天然气液化过程两部分,其中天然气液化是核心部分。
通常,从管网来的天然气在进行液化之前要经过预处理进行净化,脱除液化过程的酸性组分、水分、较重烃类及汞等,以免它们在低温下冻结而堵塞、腐蚀设备和管道,之后净化干燥后的原料天然气进入制冷系统的高效换热器不断降温,并逐级冷凝分离丁烷、丙烷、乙烷等气体,最后在常压下将其深冷到-162C左右,天然气便会液化成为液化天然气产品。
一种混合制冷剂循环(MRC)液化天然气流程的理论分析

有’个不同的国家用了混合 & " # (年至& " " "年, 制冷剂循环液化天然气流程。马来西亚准备在 . / 0 1 2 3 4 3建造的第三座 5 6 7 加工厂也将采用这种液化 〔 , 〕 流程 &( 。目前, 我国在天然气液化流程方面的定量 研究工作做得很少, 随着我国天然气的不断勘探、 开 采和使用, 需要对天然气的液化进行深入的研究, 自 主开发这方面的软件。针对带回热的混合制冷剂循 环液化天然气流程进行了系统模拟。带回热的混合
天然气 (4 ) 0 # : 7 ’ # 0 " " # ’ ! # 0 混合制冷剂") / # 0 / 3 # 0 2 ! # 0 / # 0
计算方法
在对流程进行理论分析时, 对流程中的设备进 行模块化处理, 分别编制了压缩机、 气液分离器、 多 股流换热器、 节流阀等设备的计算模块, 在流程计算 中调用这些模块可使流程模拟简化并使程序具有通 用性。流程的计算还涉及到物性计算, 在流程中, 天 然气和混合制冷剂是多组分的混合物且处于相变状 态, 所以怎样才能保证流程计算时相平衡和焓熵等 物性的计算一直能收敛且具有较高的精度也是流程 计算的一个关键。由于篇幅所限, 流程的物性计算 和各设备的模块计算在本文中不再详述。 对于本流程, 可通过以下步骤对此进行理论分 析: ! 输入天然气和混合制冷工质各组分的物性和 其它已知参数; "求取天然气的流量; # 求取混合制 冷剂的流量; 求取低压制冷剂 $调用回热计算模块, 进入压缩机时的温度; % 调压缩机计算模块求取压 调用多股流换热器计算模块得到各 缩机的耗功; & 模块换热器端面及有关节点的参数; ’ 计算最后一 个热端面的各节点的参数。
mrc液化工艺

mrc液化工艺
MRC液化工艺是一种新型的液化技术,它采用了先进的分离技术和高效的能量转换技术,可以将各种物质液化成为易于储存和运输的液态。
MRC液化工艺的应用范围非常广泛,可以用于石油、天然气、化工、医药等领域。
MRC液化工艺的核心技术是分离技术。
它采用了高效的分离设备,可以将混合物中的各种成分分离出来,从而实现液化。
这种分离技术可以有效地提高液化效率,降低能耗,减少环境污染。
MRC液化工艺还采用了高效的能量转换技术。
它可以将各种能源转换成为液化所需的能量,从而实现液化。
这种能量转换技术可以有效地提高液化效率,降低能耗,减少环境污染。
MRC液化工艺的应用非常广泛。
在石油行业中,它可以将原油、石油气等液化成为易于储存和运输的液态。
在天然气行业中,它可以将天然气液化成为LNG,从而实现长距离运输。
在化工行业中,它可以将各种化学物质液化成为易于储存和运输的液态。
在医药行业中,它可以将各种药物液化成为易于储存和运输的液态。
MRC液化工艺是一种非常先进的液化技术,它可以将各种物质液化成为易于储存和运输的液态。
它的应用范围非常广泛,可以用于石油、天然气、化工、医药等领域。
随着技术的不断发展,MRC液化工艺将会在各个领域中发挥越来越重要的作用。
天然气液化项目自控技术方案
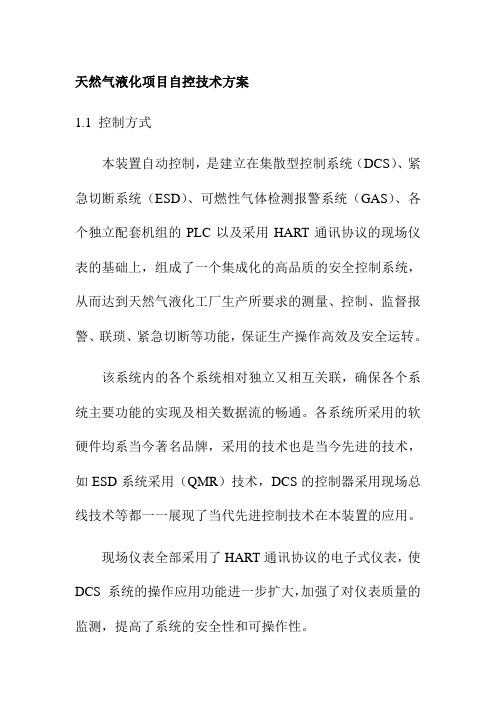
天然气液化项目自控技术方案1.1 控制方式本装置自动控制,是建立在集散型控制系统(DCS)、紧急切断系统(ESD)、可燃性气体检测报警系统(GAS)、各个独立配套机组的PLC以及采用HART通讯协议的现场仪表的基础上,组成了一个集成化的高品质的安全控制系统,从而达到天然气液化工厂生产所要求的测量、控制、监督报警、联琐、紧急切断等功能,保证生产操作高效及安全运转。
该系统内的各个系统相对独立又相互关联,确保各个系统主要功能的实现及相关数据流的畅通。
各系统所采用的软硬件均系当今著名品牌,采用的技术也是当今先进的技术,如ESD系统采用(QMR)技术,DCS的控制器采用现场总线技术等都一一展现了当代先进控制技术在本装置的应用。
现场仪表全部采用了HART通讯协议的电子式仪表,使DCS 系统的操作应用功能进一步扩大,加强了对仪表质量的监测,提高了系统的安全性和可操作性。
1.2 检测和控制方案本装置检测和控制方案中,除了常规仪表和单回路、串级回路外,尚有以下特殊仪表及控制回路。
●冷罐液位测量控制:为了对特大型冷罐低温液位测量、控制采用了SMART 储罐伺服液位计,该仪表可对冷罐液位精确测量±2mm外,还可对罐内介质密度、平均温度进行测量,并采用了4-20mA 输出或用HART总线与DCS进行通讯。
●分析测量:本装置采用了大量分析仪表,对工艺过程质量进行全面监测。
分析仪表有:工业气相色谱仪、水份仪、密度计、浊度计、热值仪、红外分析仪、总硫分析仪、氧分析仪、pH 和电导仪。
●称量控制:采用质量流量计、预设控制器、控制阀与DCS一同组成对槽车罐装的精确定量控制。
●防喘振控制:对循环气压缩机Ⅱ级,都采用了防喘振措施。
它们根据所控段的入口压力及出口段的温度、压力、流量控制相应的旁路流量以达到对压缩机的保护和安全运转。
●程序控制:A-251A/B分子筛干燥器的吸附、再生过程由DCS实现程序控制。
紧急切断(停车)系统(ESD):根据安全等级划分(SLA1001),本装置将有17个安全回路(SILI 13个,SIL 3个,NE 1个)进入EDS系统。
mrc液化工艺
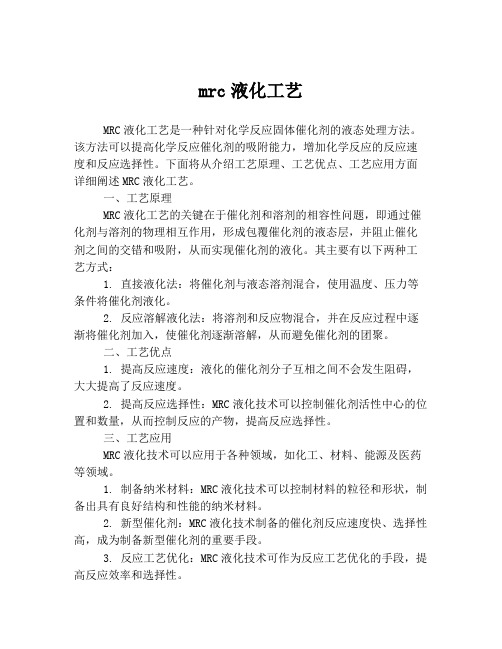
mrc液化工艺
MRC液化工艺是一种针对化学反应固体催化剂的液态处理方法。
该方法可以提高化学反应催化剂的吸附能力,增加化学反应的反应速度和反应选择性。
下面将从介绍工艺原理、工艺优点、工艺应用方面详细阐述MRC液化工艺。
一、工艺原理
MRC液化工艺的关键在于催化剂和溶剂的相容性问题,即通过催化剂与溶剂的物理相互作用,形成包覆催化剂的液态层,并阻止催化剂之间的交错和吸附,从而实现催化剂的液化。
其主要有以下两种工艺方式:
1. 直接液化法:将催化剂与液态溶剂混合,使用温度、压力等条件将催化剂液化。
2. 反应溶解液化法:将溶剂和反应物混合,并在反应过程中逐渐将催化剂加入,使催化剂逐渐溶解,从而避免催化剂的团聚。
二、工艺优点
1. 提高反应速度:液化的催化剂分子互相之间不会发生阻碍,大大提高了反应速度。
2. 提高反应选择性:MRC液化技术可以控制催化剂活性中心的位置和数量,从而控制反应的产物,提高反应选择性。
三、工艺应用
MRC液化技术可以应用于各种领域,如化工、材料、能源及医药等领域。
1. 制备纳米材料:MRC液化技术可以控制材料的粒径和形状,制备出具有良好结构和性能的纳米材料。
2. 新型催化剂:MRC液化技术制备的催化剂反应速度快、选择性高,成为制备新型催化剂的重要手段。
3. 反应工艺优化:MRC液化技术可作为反应工艺优化的手段,提高反应效率和选择性。
综上所述,MRC液化技术在化工及相关领域有广泛应用前景,其在制备新型催化剂、制备纳米材料以及反应工艺优化等方面具有独特的优势。
天然气液化流程工艺选择优化
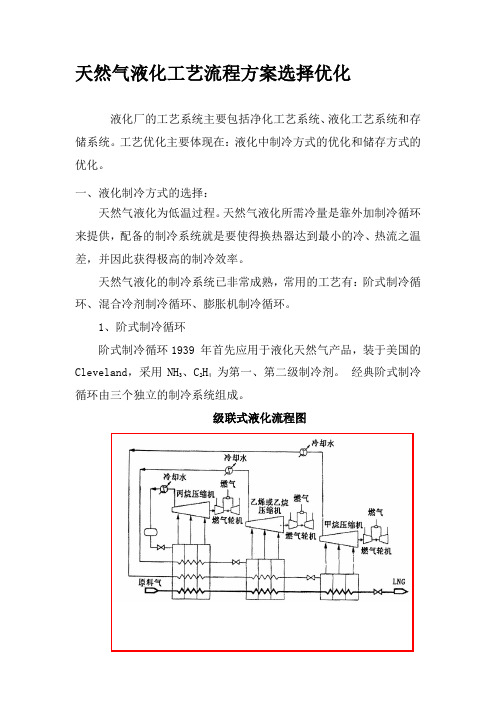
天然气液化工艺流程方案选择优化液化厂的工艺系统主要包括净化工艺系统、液化工艺系统和存储系统。
工艺优化主要体现在:液化中制冷方式的优化和储存方式的优化。
一、液化制冷方式的选择:天然气液化为低温过程。
天然气液化所需冷量是靠外加制冷循环来提供,配备的制冷系统就是要使得换热器达到最小的冷、热流之温差,并因此获得极高的制冷效率。
天然气液化的制冷系统已非常成熟,常用的工艺有:阶式制冷循环、混合冷剂制冷循环、膨胀机制冷循环。
1、阶式制冷循环阶式制冷循环1939 年首先应用于液化天然气产品,装于美国的Cleveland,采用NH3、C2H4为第一、第二级制冷剂。
经典阶式制冷循环由三个独立的制冷系统组成。
级联式液化流程图第一级采用丙烷做制冷剂,经过净化的天然气在丙烷冷却器中冷却到-35~-40℃,分离出戊烷以上的重烃后进入第二级冷却。
由丙烷冷却器中蒸发出来的丙烷气体经压缩机增压,水冷却器冷却后重新液化,并循环到丙烷冷却器。
第二级采用乙烯做制冷剂,天然气在第二级中被冷却到-80~-100℃,并被液化后进入第三级冷却。
第三级采用甲烷做制冷剂,液化天然气在甲烷冷却器中被过冷到-150~-160℃,然后通过节流阀降压,温度降到-162℃后,用泵输送到LNG 贮槽。
甲烷冷却器中蒸发出来的气体经增压、水冷后,在丙烷冷却器中冷却、在乙烯冷却器中液化后,循环到甲烷冷却器。
经典阶式制冷循环,包含几个相对独立、相互串联的冷却阶段,由于制冷剂一般使用多级压缩机压缩,因而在每个冷却阶段中,制冷剂可在几个压力下蒸发,分成几个温度等级冷却天然气,各个压力下蒸发的制冷剂进入相应的压缩机级压缩。
各冷却阶段仅制冷剂不同,操作过程基本相似。
从发展来看,最初兴建LNG 装置时就用阶式制冷循环的着眼点是:能耗最低,技术成熟,无需改变即可移植用于LNG 生产。
随着发展要求而陆续兴建新的LNG 装置,这时经典的阶式制冷循环就暴露出它固有的缺点:1)经典的阶式制冷循环由三个独立的丙烷、乙烯、甲烷制冷循环复迭而成。
天然气工程液化厂项目工艺装置及辅助生产设施设计方案
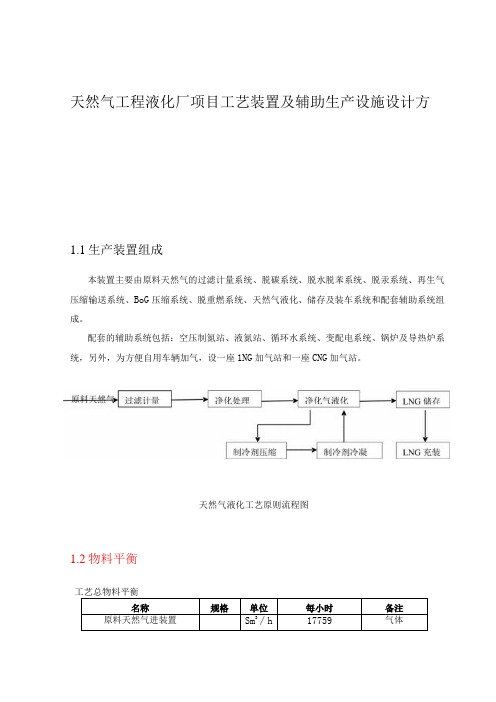
天然气工程液化厂项目工艺装置及辅助生产设施设计方1.1生产装置组成本装置主要由原料天然气的过滤计量系统、脱碳系统、脱水脱苯系统、脱汞系统、再生气压缩输送系统、BoG压缩系统、脱重燃系统、天然气液化、储存及装车系统和配套辅助系统组成。
配套的辅助系统包括:空压制氮站、液氮站、循环水系统、变配电系统、锅炉及导热炉系统,另外,为方便自用车辆加气,设一座1NG加气站和一座CNG加气站。
天然气液化工艺原则流程图1.2物料平衡详细的物料平衡见物料平衡数据表13工艺装置1.3.1工艺原理与特点1.3.1.1净化方案比较针对可研中提出的净化方案,根据工艺状况及原料气的组份特点,提出了新的净化方案,现将两种方案比较如下(以IOOX1O'iW/d为基础):方案A(可研推荐的方案):分子筛脱碳脱水、减压升温再生、再生气加压、TEG脱水后返回上游配气站方案B(实施方案):分子筛脱碳脱水+等压升温再生、再生气加压后等压脱水后返回上游配气站综合比较结果,本设计采用方案B,并经过设计联络会确认。
1.3.1.2净化装置根据天然气体成份和净化气产品质量要求,本净化工艺采用变温变压吸附法(PTSA)脱除天然气中的二氧化碳、硫化氢以及水分;采用恒压变温吸附法(TSA)脱除再生气中的水分;采用专用脱汞剂实现汞的吸附脱除。
下图为不同温度下的吸附等温线示意图:从上图B-C和AfD可以看出:在压力一定时,随着温度的升高,吸附容量逐渐减小;从上图BfA和CfD可以看出:在温度一定时,随着压力的升高吸附容量逐渐增大。
实际上,变温吸附正是利用上图B-C段(或AfD段)的特性来实现的;变压吸附是利用上图BfA段(或CfD 段)的特性来实现的;变温变压吸附过程正是利用上图中吸附剂在A-B及B-C段的特性来实现吸附与解吸的。
吸附剂在常温和压力较高时(A点)大量吸附原料气中的某些杂质组分,然后在高温和压力较低时(C点)使吸附的杂质组分得以充分解析。
天然气液化计算技术

(4)6点 6压力为天然气冷箱入口压力减去各换热器阻力。然后根据 h6=h24及P、H闪蒸计算T6。 (5) 11点 计算11点前先假定10点状态,根据10点温度、压力迭代计算, 寻找满足T6-T11≥3最大的T11。10点压力工程设计取1.49Mpa, 温度在140K-160K之间,经过膨胀机等熵膨胀迭代试算T11, P11取0.4Mpa。 (6)15点 T15=T11-3,P15=P11-ΔP,ΔP=0.1MPa为冷制冷剂通过三个换 热器的总阻力。
1.2 工艺计算前需已知的参数 在工艺计算前,需确定如下已知参数 (1) 冷箱入口天然气温度、压力、流量及各组分的摩尔分数; (2)LNG储罐的存储温度、压力; (3)换热器端面冷、热流体温差,取3℃; (4) 各种机械设备的效率,如压缩机、膨胀机、增压机; (5) 计算中换热器阻力,本计算冷箱总阻力取0.1Mpa,每个 换热器平均分配,由此引起的误差对计算结果的影响在误差允 许范围内。 在丙烷预冷混合制冷剂流程中,还需确定如下参数: (6) 丙烷压缩机出口压力,设计取1.3Mpa; (7) 混合制冷剂的组成及各摩尔分数; C3/MRC混合制冷剂选4种:分别是甲烷、乙烯(或乙烷)、 丙烷、氮气; MRC混合制冷剂选5种或6种,详见操作手册;
KW Kg/h KJ/kg. ℃ KJ/kg. ℃ K
式中 △Ex——多股流换热器火用损失 Gi——换热器中第i股流的流量 Si1——换热器中第i股流入口熵 Si2——换热器中第i股流出口熵 T0——环境温度
1.3.5 水冷器火用 损失
Q t2 n / 3600 T0 S 2 S1 G T0 t t1
天然气液化项目工艺技术方案
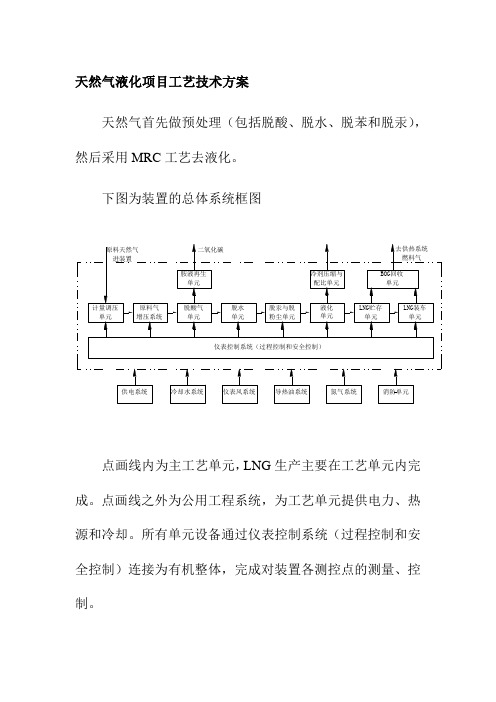
天然气液化项目工艺技术方案天然气首先做预处理(包括脱酸、脱水、脱苯和脱汞),然后采用MRC 工艺去液化。
下图为装置的总体系统框图点画线内为主工艺单元,LNG 生产主要在工艺单元内完成。
点画线之外为公用工程系统,为工艺单元提供电力、热源和冷却。
所有单元设备通过仪表控制系统(过程控制和安全控制)连接为有机整体,完成对装置各测控点的测量、控制。
1.1天然气制液态天然气(LNG)◆原料天然气过滤与调压单元原料天然气从界区来,首先进入过滤分离器,过滤掉可能存在的机械杂质、灰尘,并分离出其中的液体(主要为游离水和液态烃),为后续系统提供洁净的天然气。
洁净的原料天然气进入调压器,将压力调整并稳定至1.0MPa.G,然后经计量后进入后续单元。
原料气进装置设置有事故联锁切断阀,在事故发生后将切断进入装置的原料气源,同时通过旁路放空原料气,保证装置、人员及上游设施的安全。
◆原料天然气脱酸性气单元从原料天然气过滤与压缩单元来的天然气从吸收塔下部进入,自下而上通过吸收塔;再生后的MDEA溶液(贫液)从吸收塔上部进入,自上而下通过吸收塔,逆向流动的MDEA溶液和天然气在吸收塔内充分接触,气体中的H2S和CO2被吸收而进入液相,未被吸收的组份从吸收塔顶部引出,进入脱碳气冷却器和分离器。
出脱碳气分离器的气体进入原料气干燥单元,冷凝液去MDEA地下槽。
处理后的天然中CO2含量小于50ppmV,H2S含量小于4ppmV。
吸收了H2S和CO2的MDEA溶液称富液,至闪蒸塔,降压闪蒸出的天然体送往界外燃料系统。
闪蒸后的富液与再生塔底部流出的溶液(贫液)换热后,升温到~98℃去再生塔上部,在再生塔进行汽提再生,直至贫液的贫液度达到指标。
出再生塔的贫液经过溶液换热器、贫液泵进入贫液冷却器,贫液被冷却到~40℃,从吸收塔上部进入。
再生塔顶部出口气体经酸气冷却器,进入酸气分离器,出酸气分离器的气体送往安全泄压系统,冷凝液去MDEA 地下槽。
C3MRC天然气液化流程工艺参数优化及用能分析

第 49 卷第 10 期
邓俊哲, 等: C3 / MRC 天然气液化流程工艺参数优化及用能分析
表 1 原料气和混合制冷剂组分
Table 1 Composition of feed gas and mixed refrigerant( mol% )
组分
N2
原料气
混合冷剂
C2
91
5. 4
52. 5
摘 要: 利用化工模拟软件 HYSYS 建立 C3 / MRC 工艺仿真模型, 以现场运行参数对模型进行修正, 在已建模型基础上,
对其进行优化。 以系统能耗为优化目标, 制冷剂的压力以及制冷剂的组成配比为优化变量, 建立优化模型, 得到最优冷剂配比以
及优化后各关键节点的相关参数。 对比优化前后的参数, 发现在当天然气液化率相同时, 保证 LNG 产量不变及产品气品质达标的
3189
335. 1
-122. 7
-84. 05
2970
3189
330
-160
-77. 06
275. 1
-160. 9
-160
-92. 22
270
3189
-161. 9
L-MR
MR19
-75. 47
-104. 80
2970
2910
300
270
270
240
1257
3000
0
-75. 47
-101. 90
—
—
0. 2
n-C5
基于该 C3 / MR 装置的特点, 采用化工模拟软件 HYSYS 对
C3 / MRC 工艺流程 HYSYS 模型如图 1 所示, 该模型以原料气与
32. 5
天然气液化项目初步技术方案措施

50×104Nm3/d天然气液化项目初步技术方案重庆耐德工业股份有限公司2012.6目录一、总论 (1)1概述 (1)2装置组成 (1)二、技术说明 (3)1项目概况 (3)2通用信息 (3)3标准规范 (4)4原料规格 (18)5工艺及控制 (21)6物料平衡 (56)7化学品首次充装(以下为初步计算,最终以详细计算为准) (56)8电气负荷表(以下为初步计算,最终以详细计算为准) (58)9技术性能及保证值 (58)三、预算报价 (60)四、付款方式 (63)五、工期及业绩 (64)1、工程周期 (64)2业绩 (65)一、总论1概述本建设项目为建立50×104Nm3/d天然气液化的工艺和配套公用工程和辅助设施。
建成的天然气液化工厂,具有先进的工艺,消耗及能耗达国内先进水平,在确保工艺性能的基础上最大化实现的设备国产化,操作维护简易,符合国家环保及节能要求。
2装置组成本装置按照设计分工划分为:工艺生产装置区(ISBL)、非工艺生产装置区(OSBL)。
装置组成区域功能描述备注ISBL工艺生产装置区010 原料气分离、计量及再生气增压020 脱酸性气体030 脱水040 脱苯预留接口050 天然气液化060 蒸发气070 冷剂储配080 放空系统OSBL非工艺生产装置区110 LNG储存120 LNG装车210 空压站220 氮压站230 给排水系统240 脱盐水系统250 消防系统260 热媒炉系统310 中心控制室320 变电所区域功能描述备注330 管廊二、技术说明1项目概况项目名称:50×104Nm3/d天然气液化处理建设地点:投资方:建设规模:天然气处理总能力50×104Nm3/d的天然气液化装置,按年开工时间330天考虑。
在计划停工间隔内连续操作3年生产操作弹性:生产能力的50%~110%LNG储存天数约10天(LNG储罐有效工作容积5000m3)设计寿命不小于25年2通用信息(1)缩写词本项目的主要缩写词如下:OSBL 生产装置区域外ISBL 生产装置区域内MCC 电机控制中心Motor Central ControlBOD 设计基础Basis of DesignBEP 基础设计Basic Engineering PackageDDP 详细设计Detail Design PackageEIA 环境影响评价Environmental Impact AssessmentLNG 液化天然气OP 操作压力OT 操作温度DP 设计压力DT 设计温度MW 分子量(2)单位温度:℃压力:MPa.G(说明:MPa.G表示表压,Mpa.A表示绝压)流量:Nm3/h(0℃,0.101325Mpa.A)功率:KW天然气组分组成:mol%一般情况下,本项目将全部采用国际单位制(SI制),除另有说明之外。
天然气液化工艺部分技术方案(MRC)..

天然气液化工艺部分技术方案(MRC)一、天然气液化属流程工业,具有深冷、高压,易燃、易爆等特征,在生产中具有极高的危险性,既有比较高的温度(280℃)和压力(50Bar),也有低温(-170℃),这些单元之间紧密相连,中间缓冲地带比较小,对参数的变化要求严格,这对LNG液化装置连续生产自动化提出了很高的要求。
LNG装置的制冷剂配比与产量和收率直接相关,因此LNG生产过程中控制品质占有非常突出的位置。
整个生产过程需要很多自动化硬件和配套的软件来实现。
以保证生产装置的安全、稳定、高效运行,不仅是提高效益的关键,而且对生产人员、生产设备,以及整个厂区安全都十分重要。
二、工艺过程简述LNG工艺流程图参见P&ID图1、原料气压缩单元来自界区外的天然气经过过滤器除去部分碳氢化合物、水和其它的液体及颗粒。
35MPa(G)的原料气进入脱CO2单元。
3、脱水脱酸气单元原料气进入2台切换的干燥器,在这里原料气所含有的所有水分和CO2被脱除,干燥器出口原料气中水的露点在操作压力下低于-100℃。
经过分子筛干燥单元,在这里原料气再经过两个过滤器中的一个进行脱粉尘过滤。
4、液化单元进入冷箱的天然气在中被冷却至-35℃,在这个温度点冷箱分离罐中,脱除大部分重烃;天然气继续冷却至-70℃,在这个温度点,天然气在冷箱分离器中,脱除全部重烃,出口的天然气中C5+重烃含量降至70ppm以下;甲烷气继续冷却至-155℃,节流后进入冷箱分离罐中分离,液体部分即为液化天然气被送至液化天然气储罐中储存,气相部分返回冷箱复温后用作分子筛干燥单元的再生气。
5、储运单元来自液化单元的液化天然气进入液化天然气储罐中储存,产量为420m3,储罐容量为4500 m3,储存能力为10天。
6、制冷剂压缩单元按一定比例配比的制冷剂,经过制冷压缩机增压至1.3MPa(G)后经中间冷却器冷却后,进入中间分离罐中分离,气体部分进入制冷剂压缩机二级增压至 4.9MPa(G)并与来自分离罐的液体混合后进入后冷却器冷却,进入分离罐中分离,气体部分流至冷箱顶部,液体部分经制冷剂泵送至冷箱顶部与气体部分混合后进入冷箱换热器冷却,冷却后的低温制冷剂由换热器底部流出,经节流阀节流降压降温后返回换热器,作为返流制冷剂为原料气和正流制冷剂降温液化提供冷量,低压制冷剂复温后出冷箱换热器。
液化天然气第三章天然气液化工艺-给

上面所示的天然气直接膨胀液化流程属于开式循环,即高 压的原料气经冷却、膨胀制冷与回收冷量后,低压天然气 直接(或经增压达到所需的压力)作为商品气去配气管网。若 将回收冷量后的低压天然气用压缩机增压后与原料气相同 的压力后,返回至原料气中开始下一个循环,则这类循环 属于闭式循环。
2)氮气膨胀液化流程
该液化流程由原料气液 化回路和两级N2膨胀液 化循环组成
与混合制冷剂液化流程相比,氮气膨胀液化流程(N2 Cycle)较为简化、紧凑,造价略低。起动快,热态起动 1-2h即可获得满负荷产品,运行灵活,适应性强,易
于操作和控制,安全性好,放空不会引起火灾或爆炸危 险。制冷剂采用单组分气体。但其能耗要比混合制冷剂 液化流程高40%左右。
气液 分离器
F2,P2,T2,z2,H2,S2 F3,P3,T3,z3,H3,S3
调用气液闪蒸函数,计算出口状态两股流的气相和液相流量和 各自的摩尔分数。
调用焓、熵的计算程序,得到经气液分离后的气相和液相的焓、
熵值。
物流混合器模块
液化天然气流程中,混合器作用是混合换热器中节流阀 节流降温后的流体与后续流程返回的制冷剂,它有两方 面的作用:①使制冷剂循环利用;②返回的制冷剂温度 仍较低,可为高温级换热器提供冷量,从而使低温级低 压制冷剂的冷量得到充分的利用。
CII液化流程 法国燃气公司的研究部门开发了新型的混合制冷剂液化流 程,即整体结合式级联型液化流程(Integral Incorporated Cascade),简称为CII液化流程。
代表NG液化技术的发展趋势,具有低成本、可靠性好、易 于操作等优点。
在上海建造的CII液化流程是 我国第一座调峰型天然气液化
液化流程
三部分:混合制冷剂循环;丙烷预冷循环;天然气液化回路。 丙烷预冷循环用于预冷混合制冷剂和天然气,而混合制冷剂循
2天然气液化工艺

天然气液化工艺工业上,常使用机械制冷使天然气获得液化所必须的低温。
典型的液化制冷工艺大致可以分为三种:阶式(Cascade)制冷、混合冷剂制冷、带预冷的混合冷剂制冷。
一、阶式制冷液化工艺阶式制冷液化工艺也称级联式液化工艺。
这是利用常压沸点不同的冷剂逐级降低制冷温度实现天然气液化的。
阶式制冷常用的冷剂是丙烷、乙烯和甲烷。
图3-5[1]表示了阶式制冷工艺原理。
第一级丙烷制冷循环为天然气、乙烯和甲烷提供冷量;第二级乙烯制冷循环为天然气和甲烷提供冷量;第三级甲烷制冷循环为天然气提供冷量。
制冷剂丙烷经压缩机增压,在冷凝器内经水冷变成饱和液体,节流后部分冷剂在蒸发器内蒸发(温度约-40℃),把冷量传给经脱酸、脱水后的天然气,部分冷剂在乙烯冷凝器内蒸发,使增压后的乙烯过热蒸气冷凝为液体或过冷液体,两股丙烷释放冷量后汇合进丙烷压缩机,完成丙烷的一次制冷循环。
冷剂乙烯以与丙烷相同的方式工作,压缩机出口的乙烯过热蒸气由丙烷蒸发获取冷量而变为饱和或过冷液体,节流膨胀后在乙烯蒸发器内蒸发(温度约-100),使天然气进一步降温。
最后一级的冷剂甲烷也以相同方式工作,使天然气温度降至接近-160℃;经节流进一步降温后进入分离器,分离出凝液和残余气。
在如此低的温度下,凝液的主要成分为甲烷,成为液化天然气(LNG)。
阶式制冷是20世纪六七十年代用于生产液化天然气的主要工艺方法。
若仅用丙烷和乙烯(乙烷)为冷剂构成阶式制冷系统,天然气温度可低达近-100℃,也足以使大量乙烷及重于乙烷的组分凝析成为天然气凝液。
阶式制冷循环的特点是蒸发温度较高的冷剂除将冷量传给工艺气外,还使冷量传给蒸发温度较低的冷剂,使其液化并过冷。
分级制冷可减小压缩功耗和冷凝器负荷,在不同的温度等级下为天然气提供冷量,因而阶式制冷的能耗低、气体液化率高(可达90%),但所需设备多、投资多、制冷剂用量多、流程复杂。
图3-6[3]为阶式制冷液化流程。
为了提高冷剂与天然气的换热效率,将每种冷剂分成2~3个压力等级,即有2~3个冷剂蒸发温度,这样3种冷剂共有8~9个递降的蒸发温度,冷剂蒸发曲线的温度台阶数多,和天然气温降曲线较接近,即传热温差小,提高了冷剂与天然气的换热效率,也即提高了制冷系统的效率,见图3~7[6]。
- 1、下载文档前请自行甄别文档内容的完整性,平台不提供额外的编辑、内容补充、找答案等附加服务。
- 2、"仅部分预览"的文档,不可在线预览部分如存在完整性等问题,可反馈申请退款(可完整预览的文档不适用该条件!)。
- 3、如文档侵犯您的权益,请联系客服反馈,我们会尽快为您处理(人工客服工作时间:9:00-18:30)。
一、概述天然气液化属流程工业,具有深冷、高压,易燃、易爆等特征,在生产中具有极高的危险性,既有比较高的温度(280℃)和压力(50Bar),也有低温(-170℃),这些单元之间紧密相连,中间缓冲地带比较小,对参数的变化要求严格,这对LNG液化装置连续生产自动化提出了很高的要求。
LNG装置的制冷剂配比与产量和收率直接相关,因此LNG生产过程中控制品质占有非常突出的位置。
整个生产过程需要很多自动化硬件和配套的软件来实现。
以保证生产装置的安全、稳定、高效运行,不仅是提高效益的关键,而且对生产人员、生产设备,以及整个厂区安全都十分重要。
二、工艺过程简述LNG工艺流程图参见P&ID图1、原料气压缩单元来自界区外的天然气经过过滤器除去部分碳氢化合物、水和其它的液体及颗粒。
35MPa(G)的原料气进入脱CO2单元。
3、脱水脱酸气单元原料气进入2台切换的干燥器,在这里原料气所含有的所有水分和CO2被脱除,干燥器出口原料气中水的露点在操作压力下低于-100℃。
经过分子筛干燥单元,在这里原料气再经过两个过滤器中的一个进行脱粉尘过滤。
4、液化单元进入冷箱的天然气在中被冷却至-35℃,在这个温度点冷箱分离罐中,脱除大部分重烃;天然气继续冷却至-70℃,在这个温度点,天然气在冷箱分离器中,脱除全部重烃,出口的天然气中C5+重烃含量降至70ppm以下;甲烷气继续冷却至-155℃,节流后进入冷箱分离罐中分离,液体部分即为液化天然气被送至液化天然气储罐中储存,气相部分返回冷箱复温后用作分子筛干燥单元的再生气。
5、储运单元来自液化单元的液化天然气进入液化天然气储罐中储存,产量为420m3,储罐容量为4500 m3,储存能力为10天。
6、制冷剂压缩单元按一定比例配比的制冷剂,经过制冷压缩机增压至1.3MPa(G)后经中间冷却器冷却后,进入中间分离罐中分离,气体部分进入制冷剂压缩机二级增压至 4.9MPa(G)并与来自分离罐的液体混合后进入后冷却器冷却,进入分离罐中分离,气体部分流至冷箱顶部,液体部分经制冷剂泵送至冷箱顶部与气体部分混合后进入冷箱换热器冷却,冷却后的低温制冷剂由换热器底部流出,经节流阀节流降压降温后返回换热器,作为返流制冷剂为原料气和正流制冷剂降温液化提供冷量,低压制冷剂复温后出冷箱换热器。
二、控制系统及自动化仪表(一)工艺过程对自动控制的要求1、高度的自动化LNG液化工艺连续性强,安全要求高,中间缓冲余量小,操作频繁要求高,没有控制系统难以保证生产过程的安全平稳及优化,因此LNG液化装置采用DCS,ESD,FGS系统集中在控制室,从而实现高度自动化集中管理。
2、高质量的仪表LNG需要很多仪表,整套装置仪表设备几百台,每台仪表的正常运行都关系到某一参数或设备的工作节点的正常操作。
除考虑易燃易爆场所的要求外,每个仪表具有高的可靠性和稳定性。
现场仪表精度在 1.0,1.5,远传仪表达到0.25级以上。
3、高精度的计量仪表采用高精度的仪表用来检测LNG的入口天然气流量和LNG,LPG装车的计量。
入口天然气采用涡轮转子流量计,精度0.5级,LNG、LPG装车采用科氏质量流量计进行计量,流量精度0.05,密度精度0.0002g/cm3。
4、在线分析仪表在LNG的生产过程中,入口天然气的成分发生变化对制冷剂的配比有很大的影响,对天然气和制冷剂的在线分析是十分重要的,以防止LNG液化装置的能耗过大。
冷箱对入口天然气的含水量要求也是十分严格的,否则长期运行将堵塞冷箱。
5、防爆防雷LNG装置内有防爆区和非防爆区,非防爆区包括有明火的锅炉单元,PSA 制氮和仪表空气单元。
其它入冷箱单元、预处理单元、纯化单元、压缩机厂房等为防爆区域,在这些区内的所有仪表采用本安型仪表,特殊状态时采用隔爆型和正压防爆型仪表。
自控系统在LNG液化装置中占有十分重要的地位,DCS、ESD系统构成复杂的数据网络,容易受到各种原因导致的浪涌电压的干扰和破坏。
现场变送器、模拟数字信号控制回路、调节阀、电磁阀和分别加装防雷模块予以保护,电源系统采用3级防护、分级泄放的电源防护系统。
以及做好等电位连接。
(二)电源和气源1、电源DCS和ESD系统设置2台15KVA的UPS(不间断电源)供电,UPS的供电时间1小时。
系统内使用的电源分别为24VDC和220VAC。
2、气源仪表气源系统由2台无油压缩机、水分离罐、再生干燥器、储气罐组成。
压力:0.7MPa露点:-40℃(0.7MPa时)温度:常温,无油无尘2台120m3/h的压缩机互为备用,10m3(1.0MPa)空气储罐。
不间断供气时间30分钟。
(三)仪表选型1、温度仪表LNG装置的温度范围-170℃到300℃,装置的测温元件全部采用Pt100热电阻来实现。
热电阻均为铠装型,按不同的区域配置保护管。
特殊设备如冷箱内的温度检测采用铝保护管。
2、流量仪表除了用于计量的入口天然气流量计(涡轮转子流量计)和LNG、LPG装车流量计(科氏质量流量计),均采用截流装置配差压变送器来进行测量。
截流装置采用孔板来实现,取压方式法兰取压。
气体流量配压力和温度补偿,差压变送器的差压范围选择6KPa(6000mmH2O)。
重要的位置采用流量开关作为ESD紧急停车系统信号检测。
如:原料气压机和制冷剂压机的水冷系统。
3、压力仪表压力参数的检测通过压力变送器将信号传送到控制室供DCS或ESD系统使用,关键位置配压力开关将信号传送至ESD或DCS系统用于报警和联锁。
就地仪表采用不锈钢压力表和普通压力表实现,压机和泵的出口采用耐震压力表。
4、液位仪表需要远传的液位信号根据不同的介质采用不同的检测方式,预处理部分选择法兰差压变送器把信号传到控制室,冷箱内重烃类T>-70℃的液位采用电容式液位计实现。
LNG采用差压变送器传输信号。
关键部位如;LNG储罐使用2套液位检测系统。
就地液位指示采用磁浮子液位计和玻璃板液位计。
需要报警和联锁的液位计采用液位开关实现。
5、调节阀LNG装置的调节阀主要有低温调节阀和常温调节阀,冷箱内使用的低温调节阀采用长颈型单座调节阀,颈长:600mm,阀体材质为铝合金。
常温型调节阀根据不同的介质、压力、Cv值选用不同结构形式的调节阀,所有的调节阀都配有阀门定位器,关键阀门有阀位信号返回器何手轮装置。
如冷箱制冷剂J-T阀。
低温阀不设置前后截止阀和旁通阀,常温调节阀设置前后阀和旁通阀组。
6、1分析仪表LNG装置采用的在线分析仪表有:1台在线工业色谱仪和1台实验室色谱分别用于天然气成分和制冷剂成分的在线分析,主要分析的有:甲烷,乙烷,丙烷,异物烷,二氧化碳等。
采用的方式PCD和FID检测室。
在线露点仪,分析进冷箱的天然气露点。
7、仪表防护保温远传仪表安装在仪表箱内,需要冬季保温的采用防爆电伴热加以解决。
(四)集散式控制系统(DCS)集散控制系统(DCS)主要实现主要工艺参数的显示、趋势记录、历史事件的记录、报警、控制、打印、制表及流程图画面动态显示等功能。
DCS系统为整个系统的核心,工艺过程的所有常规控制、复杂控制和逻辑控制均由DCS来完成,当工艺参数越限时,能记忆、显示、打印并报警。
1、DCS系统组成DCS系统采用浙大中控JX-300XP系统,JX-300XP覆盖了大型集散系统的安全性、冗余功能、网络扩展功能、集成的用户界面及信息存取功能,除了具有模拟量信号输入输出、数字量信号输入输出、回路控制等常规DCS的功能,还具有高速数字量处理、高速顺序事件记录(SOE)、可编程逻辑控制等特殊功能;它不仅提供了功能块图(SCFBD)、梯形图(SCLD)等直观的图形组态工具,又为用户提供开发复杂高级控制算法(如模糊控制)的类C语言编程环境SCX。
系统规模变换灵活,可以实现从一个单元的过程控制,到全厂范围的自动化集成。
系统配置图如下:2、 DCS 配置的原则A 、系统由过程站、数据通讯系统和人机接口组成。
系统易于组态、易于使用、易于扩展。
B 、DCS 系统作为整个系统的处理整个工艺过程的参数的显示、趋势记录、历史事件的记录、报警、控制、打印、制表及流程图画面动态显示等功能。
当工艺参数超越设定值时,能记忆、显示、打印并报警。
对操作人员的操作过程进行记录。
关键参数修改权限设置。
C 、 DCS 系统配置满足装置任何工况下的监控要求(包括紧急故障处理),CPU及通信总线负荷率控制在设计规定的指标之内并留有20%裕度。
D 、 DCS 处理器采用100%冗余配置,重要 I /O 点应考虑采用非同一板件的冗余配置,每个I/O 机架应有20%的在线I/O 备用量。
E 、 系统电源有可靠的后备手段采用在线式UPS 电源,备用电源的切换时间应小于5ms 。
系统电源故障在控制室内设有独立于DCS 之外的声光报警。
F 、 主系统DCS 及与主系统连接的所有相关系统(包括ESD 、压缩机PLC 、装车独立的PLC)的通信负荷率不大于 50%,其接口设备(板件)通过冗操作站*2工程师站不属系统供货范围打印机端子柜继控制柜安全栅 柜系统机柜PIMS 系统余总线连接稳定可靠。
G、DCS的系统接地设计按照(HG/T-20513-2000)技术要求进行,所有进入DCS系统的控制信号的电缆采用的屏蔽电缆,且有良好的单端接地。
H、所有的执行机构、阀门等外围设备,在失电、失气、失信号或DCS 系统失灵的情况下,能够向安全方向动作或保持原位(安装保位阀)。
I、DCS系统容量以最终P&ID图为准,留有20%余量。
系统具有强大可扩展性,只需增加I/O模板就可以实现对系统的扩展。
J、在线修改功能,系统可以在线修改程序而不影响系统的运行。
K、DCS系统采用分布式控制,I/O远程单元可以安装在现场控制箱内。
通过冗余总线方式与处理器连接。
L、系统的兼容性,可以与RS485,RS232等多种方式与其他不同的系统连接。
WebField JX-300XP 系统配置清单1用户:哈工大雪贝低温设备有限公司项目:系统规模系统配置(五)ESD联锁停车系统天然气液化属流程工业,具有低温、高压,易燃、易爆等特征,在生产中具有极高的危险性,因此实现生产装置的安全、稳定、高效运行不仅是提高效益的关键,而且对生产人员、生产设备,人员安全都十分重要。
在本装置采用国际先进的ESD(Emergency Shut down,紧急停车)系统实现装置的安全控制。
LNG液化装置ESD系统构成:液化单元和公用工程区实现联锁保护控制,以确保装置在发生电力、循环水装置或仪表系统等公共故障时天然气的切断与排放得到有效的控制。
当装置区发生火灾等紧急情况时,ESD接收FGS 系统的信号,控制停止切断相关的设备。
ESD设备采用的是西门子公司的AS414F/HF系统对装置进行联锁控制,安全级别达到SIL2。