抽样检验标准
抽样检验标准

16-25
26-50
51-90
91-150
AQL抽样方案
3.正常检验二次抽样方案
批量 151-280 281-500 501-1200 1201-3200 3201-10000 10001-35000 35001-150000 150001-500000 样本 第一次 第二次 第一次 第二次 第一次 第二次 第一次 第二次 第一次 第二次 第一次 第二次 第一次 第二次 第一次 第二次 样本量 20 20 32 32 50 50 80 80 125 125 200 200 315 315 500 500 累计样本量 20 40 32 64 50 100 80 160 125 250 200 400 315 630 500 1000 1.5 0/2 1/2 0/3 3/4 1/3 4/5 2/5 6/7 3/6 9/10 5/9 12/13 7/11 18/19 11/16 26/27 2.5 0/3 3/4 1/3 4/5 2/5 6/7 3/6 9/10 5/9 12/13 7/11 18/19 11/16 26/27 11/16 26/27 4.0 1/3 4/5 2/5 6/7 3/6 9/10 5/9 12/13 7/11 18/19 11/16 26/27 11/16 26/27 11/16 26/27 6.5 2/5 6/7 3/6 9/10 5/9 12/13 7/11 18/19 11/16 26/27 11/16 26/27 11/16 26/27 11/16 26/27
AQL抽样方案
2.正常检验一次抽样方案的使用
抽样表使用举例:(基于严重瑕疵AQL2.5;轻微瑕疵AQL4.0) 抽样表使用举例: 1)假设一批待查验货品的数量为450件(套),则需要随机抽取 50件查验样品 2)对50件样品进行查验,并对发现的瑕疵进行分类和记录 3)出现下列任何情况之一者,此批货品最终的查验结果都为不合格 A.发现的严重瑕疵数大于3 B.发现的次要瑕疵数大于5 C.发现的尺寸不良数根据AQL4.0标准判定不合格
质量抽样检验标准

七、抽樣方案類型:
7.1一次抽樣方案﹔ 7.2二次抽樣方案﹔ 7.3五次抽樣方案。
九、檢查水平及意義
抽樣檢查中,判斷能力用檢查水平表 示,即判斷能力強,檢查水平高﹔
檢查水平是為確定判斷能力而規定的 批量與樣本之間關系的等級﹔
批量N和合格判定數Ac不變,抽樣檢 查的判定能力隨抽樣量n增加而增加 。
质量抽样检验标准
一、抽樣檢查標准的主要區別: MIL-STD-105E . Major/Minor/Critical
c=0 針對檢驗項目,只要有不合格 則一律拒收。
二、品質檢驗應用之抽樣標准
機械電子輕工等行業用標准:
MIL-STD-105E . Major/Minor/Critical PC業界常用標准:
3.2多次抽樣檢查:每次均按規定的樣本大 小抽樣并作檢查,將各次抽樣結果累計與判 定數組作比較,作出合格、不合格或繼續抽 檢的結論,直至可作出判定為止﹔
3.3序貫抽樣檢查:每次只抽取一個樣品檢 查,一個或若干個樣品檢查后,將累計檢查 結果與相應的判斷標准比較,作出合格、不 合格或繼續抽檢的結論。
四、抽樣檢查類型及定義:
4.1正常檢查:當過程平均接近合格質 量水平時所進行的檢查﹔
4.2加嚴檢查:當過程平均顯著劣于合 格質量水平時所進行的檢查﹔
4.3放寬檢查:當過程平均顯著優于合 格質量水平時所進行的檢查﹔
4.4特寬檢查:由放寬檢查判為不合格 的批,重新進行判斷所進行的檢查, 稱為特寬檢查。
பைடு நூலகம்
十、抽樣方案之要素:
批量N 合格質量水平AQL 檢查水平IL 抽樣方案類型
一次/二次/五次 抽樣檢查的嚴格度
抽样检验标准
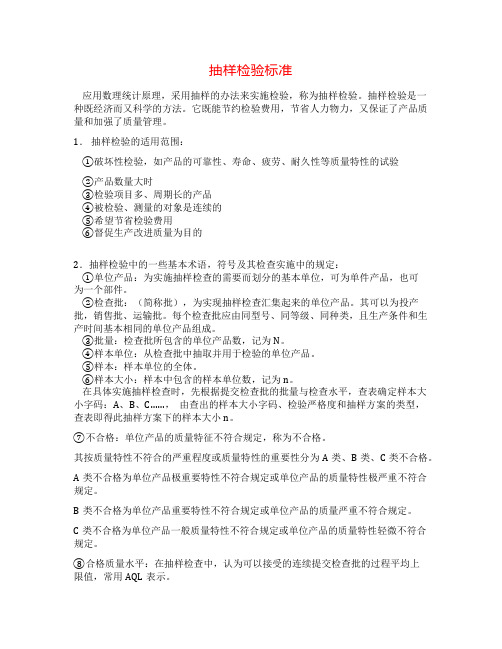
抽样检验标准应用数理统计原理,采用抽样的办法来实施检验,称为抽样检验。
抽样检验是一种既经济而又科学的方法。
它既能节约检验费用,节省人力物力,又保证了产品质量和加强了质量管理。
1.抽样检验的适用范围:①破坏性检验,如产品的可靠性、寿命、疲劳、耐久性等质量特性的试验②产品数量大时③检验项目多、周期长的产品④被检验、测量的对象是连续的⑤希望节省检验费用⑥督促生产改进质量为目的2.抽样检验中的一些基本术语,符号及其检查实施中的规定:①单位产品:为实施抽样检查的需要而划分的基本单位,可为单件产品,也可为一个部件。
②检查批:(简称批),为实现抽样检查汇集起来的单位产品。
其可以为投产批,销售批、运输批。
每个检查批应由同型号、同等级、同种类,且生产条件和生产时间基本相同的单位产品组成。
③批量:检查批所包含的单位产品数,记为N。
④样本单位:从检查批中抽取并用于检验的单位产品。
⑤样本:样本单位的全体。
⑥样本大小:样本中包含的样本单位数,记为n。
在具体实施抽样检查时,先根据提交检查批的批量与检查水平,查表确定样本大小字码:A、B、C……,由查出的样本大小字码、检验严格度和抽样方案的类型,查表即得此抽样方案下的样本大小n。
⑦不合格:单位产品的质量特征不符合规定,称为不合格。
其按质量特性不符合的严重程度或质量特性的重要性分为A类、B类、C类不合格。
A类不合格为单位产品极重要特性不符合规定或单位产品的质量特性极严重不符合规定。
B类不合格为单位产品重要特性不符合规定或单位产品的质量严重不符合规定。
C类不合格为单位产品一般质量特性不符合规定或单位产品的质量特性轻微不符合规定。
⑧合格质量水平:在抽样检查中,认为可以接受的连续提交检查批的过程平均上限值,常用AQL表示。
原则上,按不合格的分类分别规定不同的合格质量水平。
对A类规定的合格质量水平要小于对B类规定的合格质量水平,对C类规定的合格质量水平要大于B类规定的合格质量水平。
⑨合格判定数:作出批合格判断样本中所允许的最大不合格品数或不合格数,记为Ac。
抽样检验标准

抽样检验标准抽样检验是统计学中常用的一种分析方法,用于检验研究对象总体的某一特征是否符合某种标准。
在实际应用中,抽样检验通常用于确定某种新产品或者新方法是否比已有产品或者方法更好,或者确定两个或多个研究对象总体之间是否存在差异。
而抽样检验的标准就是我们事先设定的期望结果,用于判断样本数据是否符合我们预期结果。
抽样检验标准主要包括以下几个方面:1. 明确研究对象和样本。
在进行抽样检验前,首先需要明确研究对象是什么,即我们要对哪个总体进行分析。
然后根据总体的特征,确定样本的抽取方法和样本容量。
样本的选择应该是无偏的,即每个个体都有相同的被选中的机会。
2. 明确假设。
在进行抽样检验前,我们需要明确我们的假设。
通常假设有两种类型,即原假设和备择假设。
原假设是我们希望进行推翻的假设,备择假设是我们希望验证的假设。
通过对样本数据进行分析和计算,我们可以判断样本数据是否支持原假设或者备择假设。
3. 选择合适的检验方法。
根据样本数据的类型和我们要检验的特征,我们需要选择合适的检验方法。
常用的检验方法有t检验、卡方检验、ANOVA等。
不同的检验方法适用于不同的情况,选择合适的检验方法可以提高检验的准确性和可靠性。
4. 明确显著性水平。
显著性水平是我们做出推断时允许犯错误的概率。
在进行抽样检验时,我们通常会设定一个显著性水平,比如0.05或者0.01。
显著性水平越小,我们要求的证据越强才能推翻原假设。
抽样检验标准的设定对于得出准确和可靠的结论非常重要。
合理的抽样检验标准可以减少统计误差,并提高检验的准确性和可靠性。
在实际应用中,我们需要根据研究的目的和具体情况来确定抽样检验标准,以便得出科学和有效的结论。
抽样检验标准

抽样检验标准抽样检验是统计学中一种常用的方法,用于判断一个总体的特征是否符合某种假设。
在实际应用中,我们往往无法对整个总体进行观察和研究,因此需要通过对部分样本进行检验来推断总体的特征。
本文将介绍抽样检验的标准及其应用。
首先,抽样检验的标准包括显著性水平和P值。
显著性水平通常用α表示,它代表了在零假设成立的情况下,发生类型I错误的概率。
通常情况下,我们会选择α=0.05作为显著性水平,这意味着我们愿意接受5%的概率来犯下类型I错误。
P 值是在零假设成立的条件下,观察到样本统计量或更极端情况的概率。
如果P值小于显著性水平α,我们就可以拒绝零假设。
其次,抽样检验的标准还包括检验统计量和拒绝域。
检验统计量是根据样本数据计算得到的一个统计量,它用于判断样本数据是否支持零假设。
拒绝域是检验统计量的取值范围,如果检验统计量落在拒绝域内,我们就可以拒绝零假设。
拒绝域的确定通常依赖于显著性水平和检验统计量的分布。
最后,抽样检验的标准还包括样本容量和抽样方法。
样本容量的大小会影响到抽样检验的效果,通常来说,样本容量越大,检验的效果越好。
抽样方法的选择也是至关重要的,不恰当的抽样方法可能会导致样本偏差,进而影响到抽样检验的结果。
在实际应用中,抽样检验广泛应用于医学研究、市场调查、质量控制等领域。
通过对样本数据的检验,我们可以对总体特征进行推断,从而为决策提供依据。
然而,在进行抽样检验时,我们也需要注意样本的代表性、抽样误差以及可能存在的偏差,以确保检验结果的可靠性和有效性。
综上所述,抽样检验是一种重要的统计方法,其标准包括显著性水平、P值、检验统计量、拒绝域、样本容量和抽样方法。
合理地应用抽样检验可以帮助我们进行科学的决策和推断,但在实际操作中也需要注意数据的质量和抽样方法的选择。
希望本文能够帮助读者更好地理解抽样检验的标准及其应用。
抽样检验标准

.说明合用范围1)关于形成过程连续,拥有自然连续性和整体均匀性的流程性资料,不可以进行计数只能进行计量的物料,如没有明确规定抽样查验方式的,按本标准中的相关抽检规定履行。
2)没有明确规定抽样查验方式的其余批量物料,履行本标准中的、、有关规定,这部分物料包含:外购物料、委外加工的零零件、自制零零件等。
引用标准本标准依照GB/T-2003/ISO2859-1:1999计数抽样查验程序拟订。
流程性资料抽检规定规格、型号同样,由同一个供给商供货的同批流程性资料作为一个查验批,关于塑料或树脂、钢材炉批号等同样的物料为一个查验批。
钢材的理化试验,每批抽检一组试样不易睁开的物料在端头进行惯例查验,如线材类等术语及符号批量(N):产品生产批次数,同一个供给商采纳同样材质、技术工艺、车间、人员及设施生产出的产品统称为批次.组成一个批的产品产生条件须尽可能同样采买件:规格、型号同样,由同一个供给商供货的的同批产品。
外协件:同一个外协厂按同一图纸,采纳同样的工艺方法的同批产品。
自制件:同一班次按同一图纸,采纳同样的资料、工艺方法和设施的产品。
样本量(n):样本中产品数目样本的抽取:按简单随机抽样(见GB/T-1993的)从批中抽取作为样本。
样本可在制作达成后或在制作时期抽取。
由本企业自制件的首件一定报捡。
二次或多次抽样的样本应从同一批的节余部分抽取。
正常、加严、放宽查验1)观点正常查验:在规定的时段或生产量内均匀过程水平优于可同意的最差过程均匀质量水平可使用正常查验方法。
..加严查验:当早先规定的连续批数查验结果表示,在规定的时段或生产量内均匀过程水平比可同意的最差过程均匀质量水平劣质时,采纳加严查验。
放宽查验:在早先规定连续批数的查验构造表示均匀过程水平优于可接收的质量限时,可进行放宽的查验方法。
2)变换规则和程序首次查验中连续5批或少于5批中有1批是不行接收的,则转移到加严查验。
加严查验后假如首次查验的接连5批已经被以为是可接收的,应恢复正常查验。
抽样检验标准完整版

抽样检验标准HUA system office room 【HUA16H-TTMS2A-HUAS8Q8-HUAH1688】抽样检验标准1. 目的:为使进料检验、过程检验、成品检验时有正确之抽样方法及判定依据。
2. 范围:进料检验、过程检验、成品检验均适用本规范。
3. 权责:由进料、过程、成品检验员负责实施之。
4. 定义:4. 1 单位产品: 为实施抽样检查的需要而划分的基本单位,称为单位产品。
4. 2 检查批: 为实施抽样检查汇集起来的单位产品称之为检查批,简称为批。
4. 3 批量: 批中所包含的单位产品数,称为批量。
4. 4 样本单位: 从批中抽取用检查的单位产品,称为样本单位。
4. 5 样本: 样本单位的全体,称为样本。
4. 6 样本大小: 样本中所包含的样本单位数,称为样本大小。
4. 7 抽样检验:依照批量大小,抽出不同数量的样本,将该样本按其规格进行检验,并将检验的结果与预先决定的品质标准比较,以决定个别的样品是否合格。
4. 8 不良率: 不良品的表示方法。
任何已知数量的制品不良率,为制品中所含的不良品数除以单位产品的总数再乘以100%即得:不良率=? 不良品个数 *100%检验单位产品总数4. 9 检验方法: 用检验、量测、试验或其它方式将单位产品和其规定的要求加以比较的方法。
4. 10 抽样计划: 样本大小和判定数组结合在一起,称为抽样计划。
4. 11 抽样程序: 使用抽样计划判断批合格与否的过程,称为抽样程序。
4. 12类别:根据产品质量性能和使用过程的重要程度,由高到低依次分为A、B、C 三类。
A类:成品及构成产品的最主要原料。
其质量直接影响最终产品的质量性能,严重的可能直接导致产品报废。
B类:半成品及重要原材料。
其质量直接影响产品的质量性能,导致产品重要性能指标的下降。
C类:一般原材料,可以根据情况进行检测,备案。
不会对产品的主要性能产生影响,不直接影响产品的应用性能。
说明:原材料分级规定详见附件《原材料分类》5作业内容:5.1 A类原材料需100%检测,B类抽检,C类凭合格证检验,抽样比率如下:5.2 采购回的物品必须检测其产品合格证,检测其产品规格或技术参数是否符合本公司采购的要求,强制性产品必须检查是否印有3C标志及合格证。
抽样检验标准

抽样检验时,人们常以为要求样本中一个不合格品都不出现的抽样方案是个 好方案,即采用A=0的抽样方案最严格,最放心。其实并不是这样,以下面 三种抽样方案为例: ①N=1000, n=100, A=0②N=1000, n=170, A=1③N=1000, n=240, A=2
从OC曲线可以看出,3种方案在P=2.2% 时的接收概率基本上为0.1左右。但对于 A=0的方案来说,P只要比0%稍大一些, L(p)就迅速减小,这意味着“优质”批 被判为不合格的概率快速增大,这对生 产方很不利。可见,在实际操作当中, 如能增大n的同时也增大A(A≠0)的抽 样方案,比单纯采用A=0的抽样方案更 能在保证批质量的同时保护生产方。
d=0
( ) (
d
Np
N-Np n-d
)
(
N n
)
( (
Np d
N-Np n-d N n
) )
从批的不合格品数Np中抽取d个不合格品的全部组合数;
从批的合格数N-Np中抽取n-d个合格品的全部组合数; 从批量N的一批产品中抽取n个单位产品的全部组合数;
( )
• 二项分布计算法:无限总体计件抽检
A
L(p) =∑
• 批允许不合格品率:在道奇-罗米格抽样表中,把对应于接收概率L(p)=10%的不合 格品率称为批允许不合格品率,记为LTPD。它是孤立批抽样检验的重要参数,严 格控制就能起到保护使用方的作用。目前,国际标准ISO-2859-2:1995和国标 GB/T 13546-92已将LTPD的概念扩展为极限质量LQ,即把对应于很小接收概率的 不合格品率称为极限质量。
• 用给定的抽样方案(n , A)(n - 样本量, A - 批合格判定数)去验收批量N和批质 量p已知的连续检验批时,把检验批判为 合格而接收的概率,记为L(p)。 接收概率的计算方法:
oqc抽样检验标准

oqc抽样检验标准一、引言OQC(Outgoing Quality Control)抽样检验是指在产品发货前,对产品进行检验和抽样检测,以确保产品质量符合标准和客户要求。
本文将介绍OQC抽样检验标准的相关内容。
二、OQC抽样检验的目的OQC抽样检验的目的在于确认产品质量是否符合标准要求,以保证产品稳定的质量水平,提高客户满意度和产品的竞争力。
三、抽样检验方法1. 采用国际标准OQC抽样检验应采用国际标准作为基础,如ISO 2859-1(ANSI/ASQ Z1.4)、MIL-STD-105E等,以确保检验结果的准确性和可靠性。
2. 符合产品特性抽样检验时,应根据产品的特性选择合适的抽样方案,例如,对于电子产品可以采用AQL(Acceptable Quality Level)抽样标准,而对于食品可以采用不良品率抽样标准。
3. 考虑不同批次在实际抽样检验过程中,应考虑产品批次的不同,合理划分抽样数量和抽样比例,以确保每个批次的抽样结果都具有代表性。
四、抽样计划1. 确定抽样计划根据产品特性和要求,确定适当的抽样计划,包括抽样数量、抽样比例、抽样方案等。
2. 存在多种方案时的选择当存在多种抽样方案时,可以根据产品的重要性、风险等因素进行权衡,选择最合适的抽样方案。
五、抽样检验标准1. 特性参数根据产品的不同特性,制定相应的抽样检验标准。
例如,对于尺寸参数,可以通过测量抽样检验;对于外观质量参数,可以通过目测抽样检验。
2. 合格判定标准制定明确的合格判定标准,以便对抽样品进行判定。
合格判定标准应基于产品标准和客户要求,确保产品质量符合预期。
六、相关统计学知识OQC抽样检验需要运用一定的统计学知识,以确保抽样结果的准确性和可靠性。
例如,需要了解抽样误差、置信区间、批量变异等相关内容。
七、抽样检验结果处理1. 数据分析对抽样检验结果进行统计与分析,以获得相关的数据指标,如不良品率、平均值等。
2. 合格与否的判定根据抽样检验结果和相应的合格判定标准,对产品进行合格与否的判定。
检验标准和抽样标准一样吗
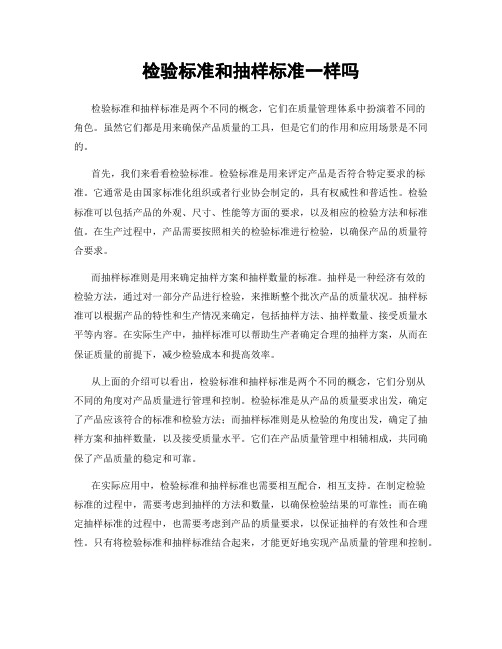
检验标准和抽样标准一样吗检验标准和抽样标准是两个不同的概念,它们在质量管理体系中扮演着不同的角色。
虽然它们都是用来确保产品质量的工具,但是它们的作用和应用场景是不同的。
首先,我们来看看检验标准。
检验标准是用来评定产品是否符合特定要求的标准。
它通常是由国家标准化组织或者行业协会制定的,具有权威性和普适性。
检验标准可以包括产品的外观、尺寸、性能等方面的要求,以及相应的检验方法和标准值。
在生产过程中,产品需要按照相关的检验标准进行检验,以确保产品的质量符合要求。
而抽样标准则是用来确定抽样方案和抽样数量的标准。
抽样是一种经济有效的检验方法,通过对一部分产品进行检验,来推断整个批次产品的质量状况。
抽样标准可以根据产品的特性和生产情况来确定,包括抽样方法、抽样数量、接受质量水平等内容。
在实际生产中,抽样标准可以帮助生产者确定合理的抽样方案,从而在保证质量的前提下,减少检验成本和提高效率。
从上面的介绍可以看出,检验标准和抽样标准是两个不同的概念,它们分别从不同的角度对产品质量进行管理和控制。
检验标准是从产品的质量要求出发,确定了产品应该符合的标准和检验方法;而抽样标准则是从检验的角度出发,确定了抽样方案和抽样数量,以及接受质量水平。
它们在产品质量管理中相辅相成,共同确保了产品质量的稳定和可靠。
在实际应用中,检验标准和抽样标准也需要相互配合,相互支持。
在制定检验标准的过程中,需要考虑到抽样的方法和数量,以确保检验结果的可靠性;而在确定抽样标准的过程中,也需要考虑到产品的质量要求,以保证抽样的有效性和合理性。
只有将检验标准和抽样标准结合起来,才能更好地实现产品质量的管理和控制。
总的来说,检验标准和抽样标准虽然是两个不同的概念,但是它们在产品质量管理中都起着重要的作用。
在实际生产中,我们需要根据产品的特性和生产情况,合理地制定检验标准和抽样标准,以确保产品质量的稳定和可靠。
只有这样,才能满足客户的需求,提升企业的竞争力。
iso2859抽样标准
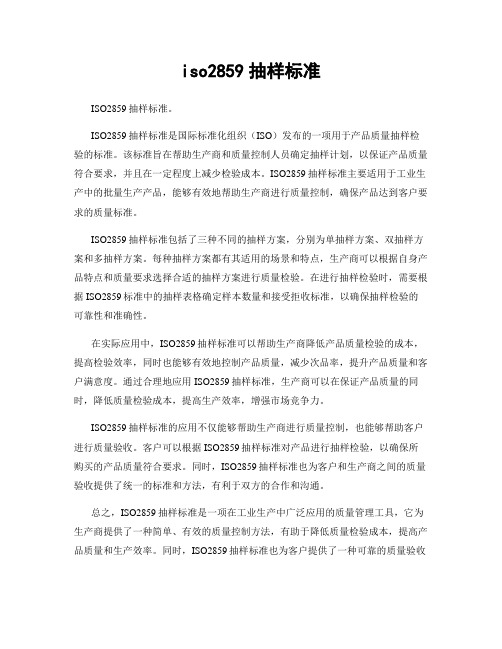
iso2859抽样标准ISO2859抽样标准。
ISO2859抽样标准是国际标准化组织(ISO)发布的一项用于产品质量抽样检验的标准。
该标准旨在帮助生产商和质量控制人员确定抽样计划,以保证产品质量符合要求,并且在一定程度上减少检验成本。
ISO2859抽样标准主要适用于工业生产中的批量生产产品,能够有效地帮助生产商进行质量控制,确保产品达到客户要求的质量标准。
ISO2859抽样标准包括了三种不同的抽样方案,分别为单抽样方案、双抽样方案和多抽样方案。
每种抽样方案都有其适用的场景和特点,生产商可以根据自身产品特点和质量要求选择合适的抽样方案进行质量检验。
在进行抽样检验时,需要根据ISO2859标准中的抽样表格确定样本数量和接受拒收标准,以确保抽样检验的可靠性和准确性。
在实际应用中,ISO2859抽样标准可以帮助生产商降低产品质量检验的成本,提高检验效率,同时也能够有效地控制产品质量,减少次品率,提升产品质量和客户满意度。
通过合理地应用ISO2859抽样标准,生产商可以在保证产品质量的同时,降低质量检验成本,提高生产效率,增强市场竞争力。
ISO2859抽样标准的应用不仅能够帮助生产商进行质量控制,也能够帮助客户进行质量验收。
客户可以根据ISO2859抽样标准对产品进行抽样检验,以确保所购买的产品质量符合要求。
同时,ISO2859抽样标准也为客户和生产商之间的质量验收提供了统一的标准和方法,有利于双方的合作和沟通。
总之,ISO2859抽样标准是一项在工业生产中广泛应用的质量管理工具,它为生产商提供了一种简单、有效的质量控制方法,有助于降低质量检验成本,提高产品质量和生产效率。
同时,ISO2859抽样标准也为客户提供了一种可靠的质量验收方法,有助于保证所购买产品的质量符合要求。
因此,我们应该充分认识和应用ISO2859抽样标准,以推动产品质量管理水平的提升,实现企业可持续发展的目标。
检验抽样标准
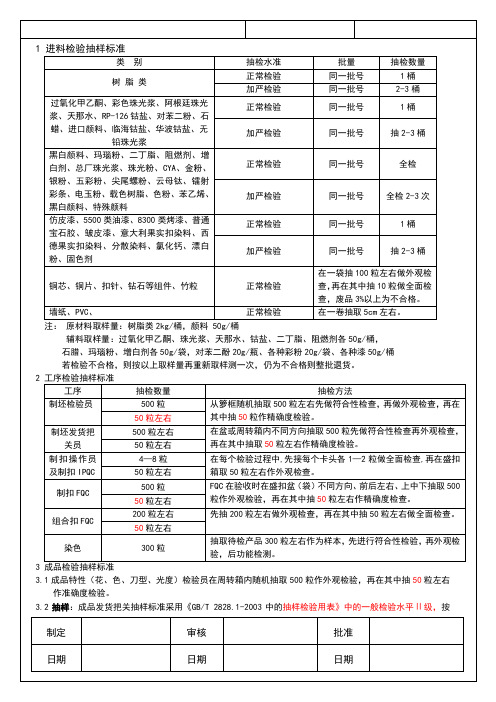
批量范围
AQL值
致命
缺陷
严重缺陷(一类)
严重缺陷(二类)
一般缺陷
A
1250以上
(1250以内全检)
00.01允许拒收0.065允许
拒收
0.4
允许
拒收
0粒
1粒
2粒(0.16%)
3粒
10粒(0.8%)
11粒
B
1250以上
(1250以内全检)
0
0.025
0粒
1粒
0.25
7粒(0.56%)
8粒
2.5
1进料检验抽样标准
类别
抽检水准
批量
抽检数量
树脂类
正常检验
同一批号
1桶
加严检验
同一批号
2-3桶
过氧化甲乙酮、彩色珠光浆、阿根廷珠光浆、天那水、RP-126钴盐、对苯二粉、石蜡、进口颜料、临海钴盐、华波钴盐、无铅珠光浆
正常检验
同一批号
1桶
加严检验
同一批号
抽2-3桶
黑白颜料、玛瑙粉、二丁脂、阻燃剂、增白剂、总厂珠光浆、珠光粉、CYA、金粉、银粉、五彩粉、尖尾螺粉、云母钛、镭射彩条、电玉粉、载色树脂、色粉、苯乙烯、黑白颜料、特殊颜料
4.3致命缺陷:三只眼、一只眼、无眼
4.4严重缺陷(一类):单边废、大崩扣、大气泡、大缺角、正面崩扣、明显不圆、脏扣、花糊、
缺字、字不完整。(参考实样)
4.5严重缺陷(二类):比一类要稍不严重一些,大崩扣、大气泡、大缺角、正面崩扣、明显不圆、脏扣、花糊、缺字、字不完整。(参考实样)
4.6一般缺陷:钻头划、芯子顶、扣不圆、单边厚、字体深浅不一、珠光花、珠光脏点、反面小崩扣、反面小气泡、薄扣、严重刀纹、严重烧扣、严重中一点、花走形。
抽样检验标准

抽样检验标准1.目的为包材,半成品和成品的抽样检验符合质量体系要求,保证抽样方案的合理性,以国家标准GB/T2828.1为引用依据,特制订本标准。
2.范围2.1仅适用于上海浩韵化妆品有限公司检验包材,半成品和成品检验取样作业。
2.2若客户的抽样标准与本标准有出入,则应在符合中华人民共和国法律法规的前提下,按照各户的要求进行抽样检测。
3.权责3.1采购部按此标准采购包装材料。
3.2质量部按此标准检验包材,半成品和成品。
4操作依据4.1本公司所有包材来料与完成品的取样检验按GB/T2828.1-2003正常检验一次抽样方案一般检验水平II级进行,尺寸与功能检验取样按一次抽样方案特殊检验水平S3级进行。
4.2本公司包材与完成品采用正常检验一次抽样方案与加严检验一次抽样方案,不采用放宽检验抽样方案:A)无特殊要求,一般开始采用正常检验一次抽样方案;B)当正常检验抽样连续5批中有2批不合格时,应及时转入加严检验一次抽样方案;C)当加严检验抽样连续5批合格后方可转入正常检验。
4.3批次定义4.3.1 来料检验批次定义:同一批来料,具有相同规格型号的商品为一个检验批次。
4.3.2 制程检验批次定义:制造:由同一生产者在相同生产条件下制造一定量的料体作为一个检验批次;灌装与包装:由同一生产者在相同生产条件下生产的一定数量的同种定量包装商品作为一个检验批次。
4.3.3 成品出货检验批次定义:同一个灌装包装商品作为一个检验批次。
4.4 抽样检验的判定水平(AQL):4.4.1严重缺陷(CR),AQL=0.654.4.2一般缺陷(MA),AQL=1.54.4.3轻微缺陷(MI),AQL=4.05. 操作步骤5.1 确定抽样的箱数:抽样箱数X= N+1 ,N 为总箱数,X 为小数点后第一位数四舍五入的整数值,例:109=10.4,则抽样箱数为10+1=11箱,111=10.5,则抽样箱数为11+1=12箱,箱子的选取要平均分散选取。
抽样检验标准简介
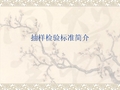
10.1开始时实行“正常”,除非负责部门另有规定。 10.2正常→加严:初次检验中连续5批或少于5批中有2批是不可接收的, 则转移到加严。 10.3加严→正常:加严时接连5批已接收,则恢复正常检验。 10.4正常→放宽: 10.4.1正在采用正常检验时,下列条件同时满足,则从正常转移到放宽 检验。 a:当前的转移得分至少30分; b:生产稳定; c:负责部门同意。 10.4.2转移得分:正常检验开始时,转移得分设定为0,而在检验每个后 续的批以后应更新转移得分: a:一次抽样方案(1)当接收数≥2时,如AQL加严一级后该批被接收, 则转物得分加2分;否则仍为0。(2)当接收数为0或1时,如果该批被 接收,则转物得分加2分;否则仍为0。 b:二次和多次抽样方案(1)当使用二次抽样方案时,如该批在检验第 一样本后被接收,则转移得分加3分;否则仍为0。(2)当使用多次抽 样方案时,如果该批在检验第一样本或第二样本后被接收,则转移得分 加3分,否则仍为0。
分别为正常、加严、放宽三种严格度的α表。
14、使用方风险表
列于GB/T2828.1-2003标准中表6及表7,其
中表6-A、B、C为适用于不合格品率为正常、 加严、放宽严格度的β表;表7为适用于每百 单位产品不合格数的正常、加严、放宽严格 度的β表。
15、分数接收数一次抽样方案(供选择)
GB/T13263—1991 跳批计数抽样程序及抽样表(计数、连续批、 跳批、与GB/T2828.1—2003一起使用)。 GB/T13264—1991 不合格品率的小批计数抽样检查程序及抽样 表(计数,N=10~250,连续批和孤立批,一次、二次)。 GB/T13393—1992 抽样检查导则。 GB/T13546—1992 挑选型计数抽样检查程序及抽样表(计数、 连续批、挑选型)。 GB/T13732—1992 粒度均匀散料抽样检验通则(计量,散料)。 GB/T14162—1993 产品质量监督计数抽样程序及抽样表(计数、 监督抽样、一次)。 GB/T14437—1997 产品质量计数一次监督抽样检验程序及抽样 表(计数、监督抽样、一次、N>250)。 GB/T14900—1994 产品质量平均值的计量一次监督抽样检验程 序及抽样表(计量、监督抽样、一次)。 GB/T15239—1994 孤立批计数抽样检验程序及抽样表(计数、 孤立批、A、B两种模式)。
gb28282003抽样检验标准
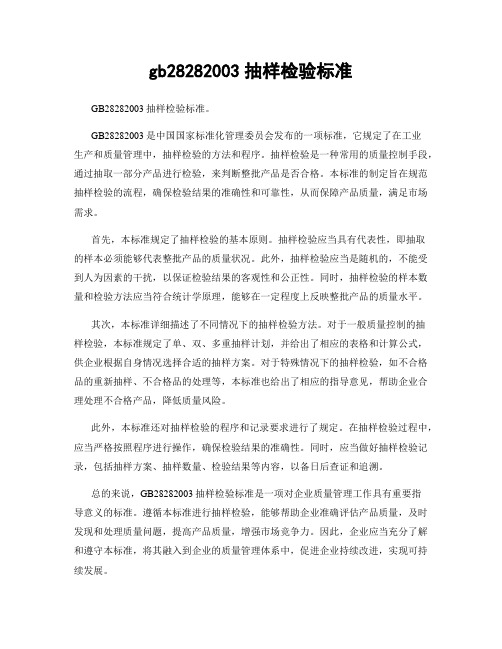
gb28282003抽样检验标准GB28282003抽样检验标准。
GB28282003是中国国家标准化管理委员会发布的一项标准,它规定了在工业生产和质量管理中,抽样检验的方法和程序。
抽样检验是一种常用的质量控制手段,通过抽取一部分产品进行检验,来判断整批产品是否合格。
本标准的制定旨在规范抽样检验的流程,确保检验结果的准确性和可靠性,从而保障产品质量,满足市场需求。
首先,本标准规定了抽样检验的基本原则。
抽样检验应当具有代表性,即抽取的样本必须能够代表整批产品的质量状况。
此外,抽样检验应当是随机的,不能受到人为因素的干扰,以保证检验结果的客观性和公正性。
同时,抽样检验的样本数量和检验方法应当符合统计学原理,能够在一定程度上反映整批产品的质量水平。
其次,本标准详细描述了不同情况下的抽样检验方法。
对于一般质量控制的抽样检验,本标准规定了单、双、多重抽样计划,并给出了相应的表格和计算公式,供企业根据自身情况选择合适的抽样方案。
对于特殊情况下的抽样检验,如不合格品的重新抽样、不合格品的处理等,本标准也给出了相应的指导意见,帮助企业合理处理不合格产品,降低质量风险。
此外,本标准还对抽样检验的程序和记录要求进行了规定。
在抽样检验过程中,应当严格按照程序进行操作,确保检验结果的准确性。
同时,应当做好抽样检验记录,包括抽样方案、抽样数量、检验结果等内容,以备日后查证和追溯。
总的来说,GB28282003抽样检验标准是一项对企业质量管理工作具有重要指导意义的标准。
遵循本标准进行抽样检验,能够帮助企业准确评估产品质量,及时发现和处理质量问题,提高产品质量,增强市场竞争力。
因此,企业应当充分了解和遵守本标准,将其融入到企业的质量管理体系中,促进企业持续改进,实现可持续发展。
抽样检验标准

抽样检验的分类
1.3.1 计数调整型抽样检 验的分类 三种类型: 1.可以调整宽严程度 的检验
2.可以调整检验水平 的检验
3.可以选择抽样检验、 全数检验或免检的检验。
特别适用于选择供方的购进检验 宽严程度分为: 1.正常 2.加严 3.放宽
GB2828基本概念
2.1 检验 为确定产品或服务的各特征是否合格,测定、检查、试验或度量产品 或服务的一种或多种特性,并且与规定要求进行比较的活动。
2.1.1 检验的目的 1)鉴定被检验对象是否符合技术要求,保证检验验收的产品达到规 定的质量水平。 2)提供有关质量信息,以便及时采取措施改进,提高产品质量。
对样品逐个进行检验,发 现d个不合格品
若d≤Ac,接收该批 若d≤Re,拒绝该批
Re=Ac+1
二次抽样方案
简记为(n1,n2 Ac1, Re1; Ac2, Re2 )Re2=Ac2+1
抽取和检验样 本量为n1的第
一样本
若d1≤Ac1, 接收
若Ac1 < d1<Re1
抽取和检验样 本量为n2的第
二个样本
2.9.3 用随机抽样数表抽样(这是实施随机抽样最常用的一种方法) 特点是首先对批的每个产品进行编号,分组,再随机抽取。
2.9.4 利用扑克牌抽样 如a)1~10,b)1~10,混合均匀,再随机抽取。
2.9.5 近似随机抽样 把所有的产品展开摆放,随意分组,再随机抽取。
2.9.6 分层随机抽样 先分层,每一层用随机抽样表抽取,如按班组分层,根据产量按比例抽样
1.1.4.3按工序流程分类
抽样检验标准

说明1.0适用范围1)对于形成过程连续,具有自然连续性和整体均匀性的流程性材料,不能进行计数只能进行计量的物料,如没有明确规定抽样检验方式的,按本标准中的有关抽检规定执行;2)没有明确规定抽样检验方式的其他批量物料,执行本标准中的、、有关规定,这部分物料包括:外购物料、委外加工的零部件、自制零部件等;1.1引用标准本标准依据GB/T -2003/ISO 2859-1:1999 计数抽样检验程序制定;2.0流程性材料抽检规定2.1规格、型号相同,由同一个供应商供货的同批流程性材料作为一个检验批,对于塑料或树脂、钢材炉批号等相同的物料为一个检验批;2.2钢材的理化试验,每批抽检一组试样2.3不易展开的物料在端头进行常规检验,如线材类等3.0术语及符号3.1批量N:产品生产批次数,同一个供应商采用相同材质、技术工艺、车间、人员及设备生产出的产品统称为批次.构成一个批的产品产生条件须尽可能相同采购件:规格、型号相同,由同一个供应商供货的的同批产品;外协件:同一个外协厂按同一图纸,采用相同的工艺方法的同批产品;自制件:同一班次按同一图纸,采用相同的材料、工艺方法和设备的产品;3.2样本量n:样本中产品数量3.3样本的抽取:按简单随机抽样见GB/T -1993的从批中抽取作为样本;样本可在制作完成后或在制作期间抽取;由本公司自制件的首件必须报捡;二次或多次抽样的样本应从同一批的剩余部分抽取;3.4正常、加严、放宽检验1)概念正常检验:在规定的时段或生产量内平均过程水平优于可允许的最差过程平均质量水平可使用正常检验方法;加严检验:当预先规定的连续批数检验结果表明,在规定的时段或生产量内平均过程水平比可允许的最差过程平均质量水平低劣时,采用加严检验;放宽检验:在预先规定连续批数的检验结构表明平均过程水平优于可接收的质量限时,可进行放宽的检验方法; 2)转换规则和程序初次检验中连续5批或少于5批中有1批是不可接收的,则转移到加严检验; 加严检验后如果初次检验的接连5批已经被认为是可接收的,应恢复正常检验; 接连5批被接收的可申请放宽检验,放宽检验由QC 申请得到QA 审核后执行; 放宽检验后只要出现一个批未被接收则恢复正常检验;3.5接收质量限AQL :AQL 是抽样计划的参数,一般认为是对过程不合格率的规定认为可接受的最大值;除另有规定外,正常检验采用标准AQL =附录2与附录5表3.6 检验水平IL :除另有规定外,本标准使用Ⅱ水平; 3.7 合格判定数A C :批合格样本中所允许的最大不合格数; 3.8 不合格判定数R C :批不合格样本中所不允许的最小不合格数;4.0 检验程序及方法4.1 确定批量数;由报捡者将需要报捡批的规格和数量报QC;4.2 确定样本量字码;根据报捡数和检验水平IL Ⅱ级,查附表1确定样本量字码; 4.3根据选定的检验严格程度,查相应的抽样检查表:1) 检索正常检验一次抽样方案,查附表2 2) 检索加严检验一次抽样方案,查附表3 3) 检索放宽检验一次抽样方案,查附表4 4.4根据接收质量限AQL,查样本量n 、合格判定数A C 、不合格判定数R C 值1) 在表中,根据抽样方案代码向右,在样本栏查得样本量n;再从代码所在行、AQL 所在列的交叉格中;读出A C , R C ;2) 如果该交叉格中不是数字而是箭头,沿着箭头方向,读出箭头所指第一的个A C , R C ,然后由此A C , R C 所在行向左,再样本栏读出相应样本量n;这时第1步查出的样本量作废; 3) 当样本量n 大于批量N 时,则作全数检查; 5.0样本检验结果为不合格品数≥R C,则拒收该批;样本检验结果为不合格品数≤A C 则接收该批;5.1不合格处理:检验中不合格均按不合格程序处理;5.2已经接收批中的不合格品均应返工或以合格品代替;5.3如果样本中存在致命不合格项,只要发现有一件这种类型的不合格存在,应拒收所有产品;5.4正常抽样样本数量少于或等于12件的,应全检;数量大于12件的,抽检数量参考附录5表;附录1:样本量字码附录2:正常检验一次抽样方案附录3:加严检验一次抽样方案附录4:放宽检验一次抽样方案附录5:AQL=抽样方案实用表附录1:样本量字码附录 2 正常检验一次抽样方案主表 GB/T ISO 2859-1:1999使用箭头下面的第一个抽样方案;如果样本量等于或超过批量,则执行100%检验; Re ----拒收数使用箭头上面的第一个抽样方案;Re ----拒收附录3加严检验一次抽样方案主表 GB/T ISO 2859-1:1999使用箭头下面的第一个抽样方案;如果样本量等于或超过批量,则执行100%检验; Re ----拒收数使用箭头上面的第一个抽样方案; Re ----拒收附录4放宽检验一次抽样方案主表 GB/T ISO2859-1:1999放宽检验一次抽样方案主表AC----接受数Re ----拒收数附录5:抽样方案实用表:AQL=,检验水平Ⅱ。
- 1、下载文档前请自行甄别文档内容的完整性,平台不提供额外的编辑、内容补充、找答案等附加服务。
- 2、"仅部分预览"的文档,不可在线预览部分如存在完整性等问题,可反馈申请退款(可完整预览的文档不适用该条件!)。
- 3、如文档侵犯您的权益,请联系客服反馈,我们会尽快为您处理(人工客服工作时间:9:00-18:30)。
1
3000↑
20
0
1
制定日
2009年4月1日
进料抽样检验标准
编号
JT-QA-SOP-027
制定单位
品保课
页数
共6页第06页
版次
1
4.抽样检验标准运用:
A凡批量或交货量小于最小抽样数时实施全检。
B厂商交货质量不良连续发生2次或以上者,进料检验时并对该厂商加严20%抽检,连续10批抽检合格,方可恢复到正常检验抽检数量,如经过加严抽检依然达不到质量要求,并对该厂商实施现场查核及技术指导,并要求该厂商期限内整改。
扬州暻泰车材实业有限公司
制定日
2009年4月1日
抽样检验标准
编号
JT-QA-SOP-0027
修订日
2010年07月10日
页数
共6页第01页
制定单位
品保课
版次
2
抽样检验标准
管 制 文 件
列 入 移 交
核 准
审 核
作 成
杨武勤
发行范围:品保课
制定日
2009年4月1日
抽样检验标准
编号
JT-QA-SOP-0027
编号
JT-QA-SOP-027
制定单位
品保课
页数
共6页第03页
版次
2
一.目的
为了验证进料、制程、终检、出货的产品质量,控制不良品流入下道工序,减少成本浪费,针对厂外、厂内的零部件、成品进行检验所提供抽样依据而制订此标准。
一、范围
适用于公司所有原物料、零部件、辅助材料、成品出货等。
二、内容
1.定义:
抽样:根据送检原物料、零部件、辅助材料、成品的数量按照《抽样检验标准》所抽取的样品进行检验,将其检验结果与《抽样判定标准》进行比较,而判定出此批量允收或拒收。
3
0
1
b.适用于进料原物料、零部件性能测试抽样检验之标准
交货批量
抽样个数
Ac(允收数)
Re(拒收数)
1~149
1
0
1
150~499
2
0
1
500~2999
3
0
1
3000↑
4
0
1
C.线组抽样检验标准说明:
交货批量
抽样个数
Ac(允收数)
Re(拒收数)
1~149
5
0
1
150~499
10
0
1
500~2999
15
C.抽样附表一ANSI/ASQCZ1.4二级标准AQL1.5A的减量10%,正常,加压20%,免检四种检验方式互相转换时机如下:
说明:①至正常交货检验连续10批允收可采用减量检验,减量检验后有1批拒收或
待确认即恢复正常检验。
②自减量检验算起连续5批允收采用免检。
③免检作业中有1批拒收或待确认,即恢复到正常检验。
2.职掌
进料、制程、出货检验过程中,品保检验人员根据《抽样检验标准》进行抽样检验,以判定原物料、零部件、成品验收品质的良与否而确保品质质量,防止不良品流入下道工序影响生产及出货。
3.抽样检验标准说明:
3.1、交货与生产为CAPA客户的产品检验时,必须遵守ANSI/ASQCZ1.4.AQL0.4抽样检验标准执行,至少每1000件零件抽样15件进行检验,如原物料为钢卷、栈板或各独立包装中之百分之二十抽取样本进行检验,CAPA产品允收数为”0”管理。
适于零部件、成品尺寸抽样检验标准如下:
批量
抽样个数
AC(允许数)
RE(拒收数)
1~149
2
0
1
150~499
3
0
1
500~2999
5
0
1
3000以上
8
0
1
5.性能抽样检验说明:
a.适用于成品性能测试抽样检验之标准如下:
生产批量
抽样个数
AC(允许数)
RE(拒收数)
1~149
1
0
1
150~499
2
0
1
500以上
④正常检验连续5批中有2批拒收需采用加严检验,加严检验后连续5批检验均合格即恢复到正常检验。
五.品质不稳定处理办法
针对厂商交货质量持续发生不良时,由品保课提出要求通知采购主管联系厂商,到厂商现场指导品质技术,及查核整个生产流程是否符合生产质量要求,针对查核的问题点要求厂商在期限内完成整改,并提交整改措施由品保课确认整改效果,如经整改后依然无法满足质量要求,并针对此厂商加严10%抽检,如果加严抽检依然无法满足质量要求,由品保单位提出扣款申請单,对该厂商进行扣款,详细处理方式见进料管理办法。
制定单位
品保课
页数
共6页第02页
版次
2
内容修改记录栏
版次
日期
原案内容
修改内容
修改者
备注
0
2009-4-1
新制定
孟杰
1
2009-11-8
增规
追加CAPA相关要求
修订3至页(追加第3页3.1及3.2.1)
杨武勤2Βιβλιοθήκη 2010-09-08整合
将进料、制程、终检、出货检验抽样整合
杨武勤
制定日
2009年4月1日
抽样检验标准
备注说明:抽取数量对应的箭头“↑”时抽取数量看上面一栏 ,如果抽取数量对应的箭头“↓”时抽取数量看下面一栏,例91-150抽取数量的箭头向下应该抽取32,而不是抽取20。
制定日
2009年4月1日
进料抽样检验标准
编号
JT-QA-SOP-027
制定单位
品保课
页数
共6页第05页
版次
1
4.尺寸抽样检验标准说明:
3.1.1、除CAPA产品外,其它产品按照ANSI/ASQCZ1.4二级标准AQL1.5抽样标准进行抽样检验,
※外观品质判定基准必须依照客户所核准的样本。
制定日
2009年4月1日
抽样检验标准
编号
JT-QA-SOP-027
制定单位
品保课
页数
共6页第04页
版次
2
3.2、ANSI/ASQCZ1.4.AQL0.4抽样标准