自动插件机PCB设计要求
自动插件PWB设计参考及检查标准-11
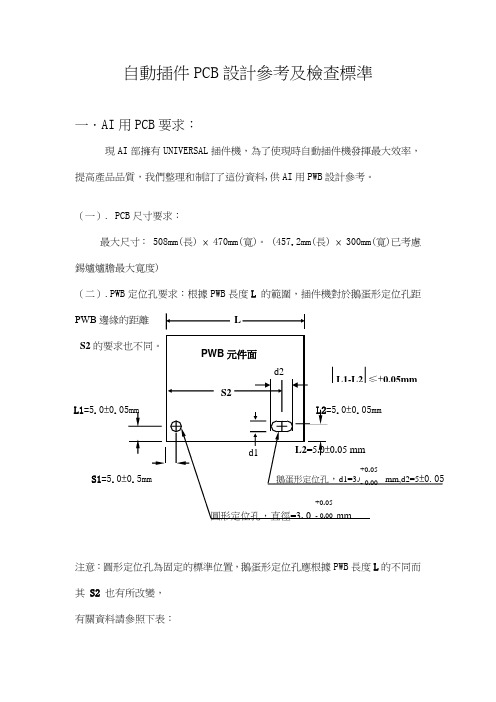
自動插件PCB設計參考及檢查標準一〃AI用PCB要求:現AI部擁有UNIVERSAL插件機,為了使現時自動插件機發揮最大效率,提高產品品質,我們整理和制訂了這份資料,供AI用PWB設計參考。
(一). PCB尺寸要求:最大尺寸: 508mm(長) × 470mm(寬)。
(457.2mm(長) × 300mm(寬)已考慮錫爐爐膽最大寬度)(二).PWB定位孔要求:根據PWB長度L的範圍,插件機對於鵝蛋形定位孔距PWB邊緣的距離注意:圓形定位孔為固定的標準位置,鵝蛋形定位孔應根據PWB長度L的不同而其S2 也有所改變,有關資料請參照下表:另外,當PWB定位孔過多,生產時容易造成PWB取放板方向混淆。
故設計PWB時,只須在該PWB長邊上設計一組定位孔(左邊圓形定位孔+右邊鵝蛋形定位孔)。
(三). 自動插件機元件引腳直徑範圍為: 0.38mm-0.81mm因此,自動插件機可插以下元件:1. 1/16W、1/8W、1/4W 電阻2. 色環電容3. 0.6mm跳線4. 二極體5. 色環電感(四). Universal 臥式插件機元件跨度C的範圍: 5.0mm-20.0mmUNIVERSAL JUMPER WIRE 機跨度C的範圍:5.0mm—33.0mmUNIVERSAL插件機的跨度是連續可變的;因此不再要求元件跨度C設計成5. 0mm、7.5mm等統一尺寸。
設計元件跨度必須同時考慮到元件體長度L,如果L過長,插件機容易打傷元件體或打斷元件引腳,損壞插件機刀具,同時對排料機要求非常嚴格。
如果跨度C過大,插件機速度會降低,插件時易掉件(插件機刀具夾不牢)、元件易浮腳。
目前AI部插件最多的是5.0mm跨度,5.0mm跨度的元件在插件時比較容易出現拱起、損傷元件等壞機;故建議將AI插件元件的最小跨度定為6.0mm,以求大幅度降低壞件率。
根據不同元件,我們定出以下標準:最小跨度的推算:一般元件=MAX L+1.3mm二極體、色環電感=MAX L+2.8mm(五). 元件孔徑要求:現時PWB 供應商工藝品質控制不是很好,如果再加上元件孔徑過小,就不符合插件機的插件要求,那將會極大的增加AI 插件的壞件率,需要增加大量人手去彌補(檢查員檢查和補件)。
PCB设计要求(手工插件)

贴片板的尺寸尽量掌握在长度 100-300mm 之间,插件板的尺寸必尽量掌握在长度 50-330mm 之 根本原则在进展印制板设计时,应考虑本标准所述的四个根本原则。
1.1 电气连接的准确性印制板设计时,应使用电原理图所规定的元器件,印制导线的连接关系应与电原理图导线连接关系相全都,印制板和电原理图上元件序号应一一对应。
注:如因构造、电气性能或其它物理性能要求不宜在印制板上布设的导线,应在相应文件〔如电原理图上〕上做相应修改。
1.2 牢靠性和安全性印制板电路设计应符合电磁兼容和电器安规的要求。
1.3 工艺性印制板电路设计时,应考虑印制板制造工艺和电控装配工艺的要求,尽可能有利于制造、装配和修理,降低焊接不良率。
1.4 经济性印制板电路设计在满足使用的安全性和牢靠性要求的前提下,应充分考虑其设计方法、选择的基材、制造工艺等,力求经济有用,本钱最低。
1 技术要求 1.1印制板的选用1.1.1 印制电路板的层的选择一般状况下,应中选择单面板。
在构造受到限制或其他特别状况下,可以选择用多层板设计。
1.1.2 印制电路板的材料和品牌的选择1.1.2.1 双面板应承受玻璃纤维板FR-4、CEM-3,CEM-22F ,单面板应承受半玻纤板CEM-11.1.2.2 印制板材料的厚度选用 1.6mm ,双面铜层厚度一般为 0.5 盎司,大电流则可选择两面都为 1 盎司, 单面铜层厚度一般为 1 盎司。
特别状况下,假设品质可以得到确保,可以选择其他厚度的印制板。
1.1.2.3 印制板材料的性能应符合企业标准的要求。
1.1.3 印制电路板的工艺要求双面板原则上应当是喷锡板〔除含有金手指的遥控器板和显示板外〕,单面板原则上假设有机插或贴片工艺原则上也必需是喷锡板〔或辘锡〕,以防止焊盘上的抗氧化膜被破坏且储存时间较长后引起焊接质量受到影响,在相关的技术文件的支持下,可承受抗氧化膜工艺的单面板。
1.2 自动插件和贴片方案的选择双面板尽可能承受贴片设计,单面板尽可能承受自动插件方案设计,应避开同一块板既承受贴片方案又同时承受自动插件方案设计,以免铺张设备资源。
插件机PCB板设计规范标准
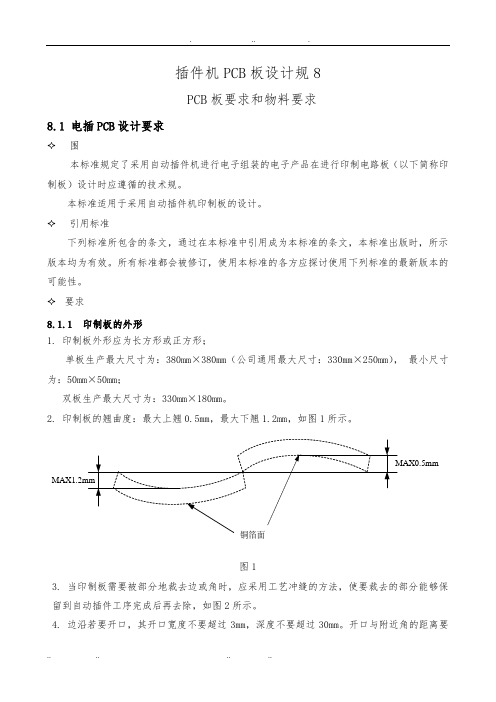
插件机PCB板设计规8PCB板要求和物料要求8.1 电插PCB设计要求✧围本标准规定了采用自动插件机进行电子组装的电子产品在进行印制电路板(以下简称印制板)设计时应遵循的技术规。
本标准适用于采用自动插件机印制板的设计。
✧引用标准下列标准所包含的条文,通过在本标准中引用成为本标准的条文,本标准出版时,所示版本均为有效。
所有标准都会被修订,使用本标准的各方应探讨使用下列标准的最新版本的可能性。
✧要求8.1.1 印制板的外形1. 印制板外形应为长方形或正方形;单板生产最大尺寸为:380mm×380mm(公司通用最大尺寸:330mm×250mm),最小尺寸为:50mm×50mm;双板生产最大尺寸为:330mm×180mm。
2. 印制板的翘曲度:最大上翘0.5mm,最大下翘1.2mm,如图1所示。
图13. 当印制板需要被部分地裁去边或角时,应采用工艺冲缝的方法,使要裁去的部分能够保留到自动插件工序完成后再去除,如图2所示。
4. 边沿若要开口,其开口宽度不要超过3mm,深度不要超过30mm。
开口与附近角的距离要大于35mm ;同一边上不要超过5个开口;尽量避免在长边上开口;如图3所示。
MAX3mm图2 图38.1.2 印制板的插机定位孔1. 采用电插的印制板应在最长的一条边(拼板后)上设置两个电插定位孔。
如图4所示(元件面)。
孔径要求直径为3.5mm 。
(可以用螺丝孔做为定位孔)L 0.15.0 0.1Min3.0图42. 两定位孔的中心轴连线平行于最长边,方便生产时固定PCB ,且距离最长边不要太远,一般5mm 左右。
定位孔周围从孔边向外至少 3mm 围应覆铜箔以增加板的机械强度。
8.1.3 印制板的非电插区1. 在非电插区布置的元件(其插孔在此区)不适用于电插机。
2. 对于卧插元件及立插元件,其非电插区(定位盲区和边缘盲区)为图5所示画有剖线的区域。
(即定位孔中心到电插件元件的本体距离要大于7MM 才能电插)图58.2物料要求8.2.1 元件的插孔1. 元件插孔中心连线的平行度或垂直度如图7所示。
AI插件PCB设计规范最新版本
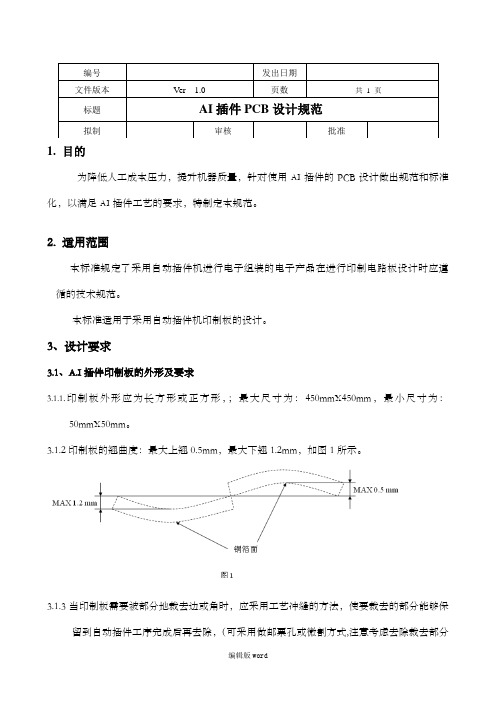
编号发出日期文件版本Ver 1.0 页数共1 页标题AI插件PCB设计规范拟制审核批准1.目的为降低人工成本压力,提升机器质量,针对使用AI插件的PCB设计做出规范和标准化,以满足AI插件工艺的要求,特制定本规范。
2.适用范围本标准规定了采用自动插件机进行电子组装的电子产品在进行印制电路板设计时应遵循的技术规范。
本标准适用于采用自动插件机印制板的设计。
3、设计要求3.1、A.I插件印制板的外形及要求3.1.1.印制板外形应为长方形或正方形,;最大尺寸为:450mmX450mm,最小尺寸为:50mmX50mm。
3.1.2印制板的翘曲度:最大上翘0.5mm,最大下翘1.2mm,如图1所示。
3.1.3当印制板需要被部分地裁去边或角时,应采用工艺冲缝的方法,使要裁去的部分能够保留到自动插件工序完成后再去除,(可采用做邮票孔或微割方式,注意考虑去除裁去部分的方便性)如图2所示。
3.1.4 边沿若要开口,其开口宽度不要超过3mm,深度不要超过30mm。
开口与附近角的距离要大于35mm;同一边上不要超过5个开口;尽量避免在长边上开口;如图3所示。
3.2 印制板的插机定位孔3.2.1.采用AI插件的印制板应在最长的一条边上设置主副两个电插定位孔。
如图4所示(元件面)。
其中左下角为主定位孔,孔径为Ø4.0mm;右下角为副定位孔,其孔径尺寸应为Ø4.0mm的鹅蛋形定位副定位孔主定位孔3.2.2两定位孔的中心轴连线平行于最长边,离最长边的距离为5.0±0.1mm,主定位孔与左边的距离为5.0±0.1mm,副定位孔孔边与右边的距离应不小于3.0mm,定位孔周围从孔边向外至少2mm范围内应覆铜箔以增加板的机械强度。
3.2.3主副两定位孔的中心距L的优选系列为:290mm、235mm、350mm,误差为±0.1。
3.2.4 AI插件PCB定位孔在元件面标记符号图中用方框标示。
AI自动插件机元件及PCB板设计要求
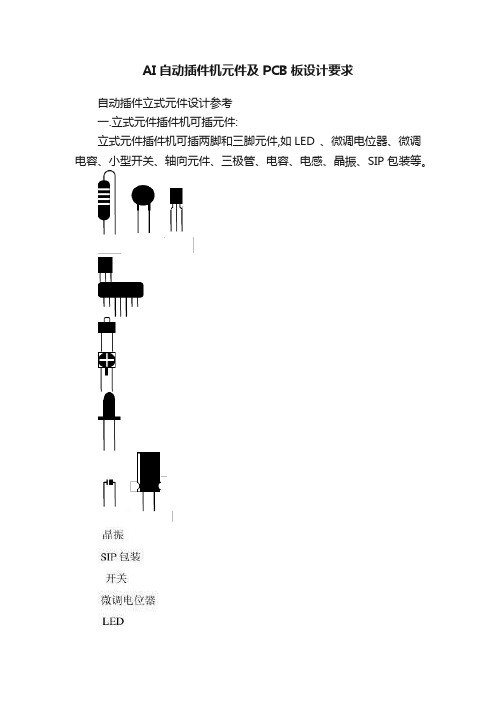
AI自动插件机元件及PCB板设计要求自动插件立式元件设计参考一.立式元件插件机可插元件:立式元件插件机可插两脚和三脚元件,如LED 、微调电位器、微调电容、小型开关、轴向元件、三极管、电容、电感、晶振、SIP 包装等。
二:立式元件要求 1.元件来料必须有编带:2.元件外形尺寸要求 A.两脚元件三.元件密度要求:在进行插件时,如果元件间的密度过大,会令已插入的元件被正要插入的元件碰松(掉).或正要插入的元件被已插入的元件碰飞,这样会造成过多的插件不良。
因此元件的密度在情况允许下应不要过密。
注:MIN(r1,r2)表示取r1和r2中最小的值,例r1=3.0,r2=5.0,则MIN(r1,r2)=3.0四.立式元件孔位要求平行或垂直(偏差不超过0.05mm,同卧式元件要求一样)五.元件极向要求对于有极性的立式元件,如三极管、二极管、电解电容、LED 等,要求极性方向一致,(通常规定X 方向元件负极向左,Y 方向元件负极向上)。
否则自动插件机生产效率降低,编制插件机程序困难,浪费插件机站位(如果方向不一致,同一种元件要占用2个站位,若方向一致,只需一个站位),而且人手补件时较难辨认极性,容易插反. * 此点对于人手插件PCB设计同样适用六. PCB 元件孔跨度C(C1)的要求.七X 方向元件负极全部向左 Y 方向元件负极全部向上 GOOD 极性不统一:负极向左向右向上向下均有 NO GOODD1:元件脚直径 D2:元件孔直径请注意:此孔径比较大,如果用人手插件,会产生浮脚、锡点不良等质量问题。
因此在设计时应明确该元件是手插还是机插。
八. 增加白油保护层如果PCB 铜皮面线路较密,自动插件时容易造成元件与相邻铜皮短路,因此在设计PWB 时应在元件焊盘加白油保护.请注意立式元件的弯脚与卧式元件的弯脚不一样,其元件的弯脚是向两边呈45°弯曲成形的。
其白油层请参考以下图示一:1W,1/2W,1/4W,1/6W,1/8W电阻、1N41418、1N4007二极管和1W以下的稳压管(包括1W)二:卧式元件及输入编带要求A:编带辐度差:42.00mm(±1.00mm)B:元件引线距离(元件间距):5.0mmC:最大允许引线伸出编带外长度:1.0mmD: 元件引线直径:0.41-0.81mmE:元件体直径:最大5.0mmF:元件引线平直度容差:±0.5mmG:元件跨距: 5.08-20.00mm三 PCB设计要求3.1一块拼版PCB上如AI元件小于20PCS以下,一般不考虑作AI处理。
印制板的设计规范(一)(自动插件篇)V02
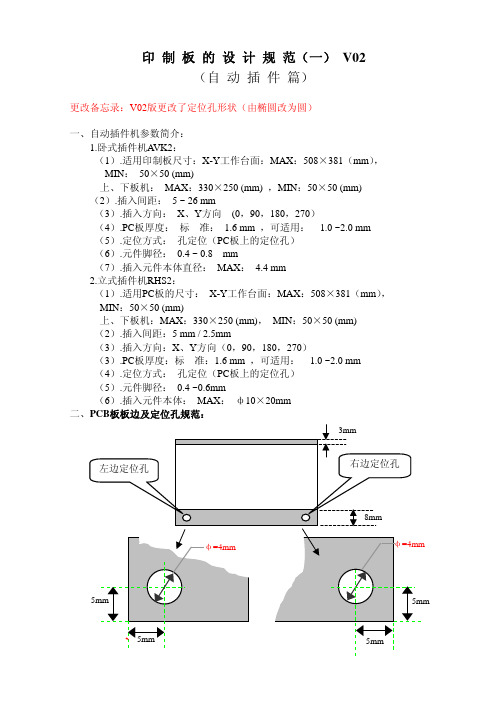
印制板的设计规范(一) V02(自动插件篇)更改备忘录:V02版更改了定位孔形状(由椭圆改为圆)一、自动插件机参数简介:1.卧式插件机A VK2:(1).适用印制板尺寸:X-Y工作台面:MAX:508×381(mm),MIN: 50×50 (mm)上、下板机: MAX:330×250 (mm) ,MIN:50×50 (mm) (2).插入间距: 5 ~ 26 mm(3).插入方向:X、Y方向(0,90,180,270)(4).PC板厚度:标准: 1.6 mm ,可适用: 1.0 ~2.0 mm(5).定位方式:孔定位(PC板上的定位孔)(6).元件脚径: 0.4 ~ 0.8 mm(7).插入元件本体直径: MAX: 4.4 mm2.立式插件机RHS2:(1).适用PC板的尺寸: X-Y工作台面:MAX:508×381(mm),MIN:50×50 (mm)上、下板机:MAX:330×250 (mm), MIN:50×50 (mm)(2).插入间距:5 mm / 2.5mm(3).插入方向:X、Y方向(0,90,180,270)(3).PC板厚度:标准:1.6 mm ,可适用: 1.0 ~2.0 mm(4).定位方式:孔定位(PC板上的定位孔)(5).元件脚径: 0.4 ~0.6mm(6).插入元件本体: MAX:ф10×20mm二、PCB板板边及定位孔规范:说明:上下各留3mm 和8mm 的工艺边,上下工艺边可以根据实际PCB 板位置决定是否需要增加;定位孔的尺寸及位置要求如图所示。
三、自动插件死区:1.板边死区:2.定位孔周围的死区:四、相邻元件的安全距离:1.元件面:两相邻元件的本体之间应间隔0.5mm.2.焊点面:元件脚与元件脚间不会短路。
五、PCB 板孔径:PCB 板孔径由所插元件的引脚直径决定,其关系如下表: (参考公式:PCB 上的打孔直径=元器件引脚直径(单位:mm )+0.4 mm)引脚直径(mm ) PCB 板孔径(mm )0.80±0.05 1.2 0.60±0.05 1.0 0.50±0.05 0.9 0.40±0.05 0.8 +0.1 -0+0.1 -0+0.1 -0+0.1 -0注:立式机台只能插0.6mm 引脚直径的元件。
AI插件PCB设计规范

编号发出日期文件版本Ver 1.0 页数共1 页标题AI插件PCB设计规范拟制审核批准1.目的为降低人工成本压力,提升机器质量,针对使用AI插件的PCB设计做出规范和标准化,以满足AI插件工艺的要求,特制定本规范。
2.适用范围本标准规定了采用自动插件机进行电子组装的电子产品在进行印制电路板设计时应遵循的技术规范。
本标准适用于采用自动插件机印制板的设计。
3、设计要求3.1、A.I插件印制板的外形及要求3.1.1.印制板外形应为长方形或正方形,;最大尺寸为:450mmX450mm,最小尺寸为:50mmX50mm。
3.1.2印制板的翘曲度:最大上翘0.5mm,最大下翘1.2mm,如图1所示。
3.1.3当印制板需要被部分地裁去边或角时,应采用工艺冲缝的方法,使要裁去的部分能够保留到自动插件工序完成后再去除,(可采用做邮票孔或微割方式,注意考虑去除裁去部分的方便性)如图2所示。
3.1.4 边沿若要开口,其开口宽度不要超过3mm,深度不要超过30mm。
开口与附近角的距离要大于35mm;同一边上不要超过5个开口;尽量避免在长边上开口;如图3所示。
3.2 印制板的插机定位孔3.2.1.采用AI 插件的印制板应在最长的一条边上设置主副两个电插定位孔。
如图4所示(元件面)。
其中左下角为主定位孔,孔径为Ø4.0mm ;右下角为副定位孔,其孔径尺寸应为Ø4.0mm 的鹅蛋形定位3.2.2两定位孔的中心轴连线平行于最长边,离最长边的距离为5.0±0.1mm ,主定位孔与左边的距离为5.0±0.1mm ,副定位孔孔边与右边的距离应不小于3.0mm ,定位孔周围从孔边向外至少 2mm 范围内应覆铜箔以增加板的机械强度。
3.2.3主副两定位孔的中心距L 的优选系列为:290mm 、235mm 、350mm ,误差为±0.1。
3.2.4 AI 插件PCB 定位孔在元件面标记符号图中用方框标示。
AI插件机PCB设计规范要求

AI插件机PCB设计规范要求
一、PCB板材要求
1、 PCB板材厚度为 1.6mm,且导电性能要达到高频信号传输的要求;
2、PCB板材的表面经过喷镀耐酸碱处理,并具有很强的耐腐蚀性;
3、PCB板材在结构布局上应确保所需元件的布局空间,并需要考虑
到流线型布局原则;
4、PCB板材结构形状尽量采用矩形,圆形等常规形状,如果需要采
用其他形状应事先经过分析与设计;
二、PCB尺寸及定位要求
1、PCB尺寸应根据具体设计要求确定,尽可能的缩小尺寸,减少冗
余空间;
2、PCB定位孔的位置必须准确,最好采用多个定位孔的形式,以确
保定位的精度;
3、PCB定位孔的尺寸应有效的防止安装后的杂物污染,最好采用圆
孔的形式;
4、PCB定位孔的数量应根据具体的电路设计情况决定,但一般最少
应设置2个定位孔
三、PCB焊接孔要求
1、PCB焊接孔的形状应采用圆孔的形式,防止焊接过程中因孔形状
不标准而产生焊接不良的现象;
2、PCB焊接孔的尺寸应符合焊接工艺要求,最好采用两侧相同尺寸的形式;
3、PCB焊接加工后,需要确保其表面光滑,无毛刺,以确保PCB表面的美观;
4、PCB焊接孔的位置应考虑和其他焊接元件的位置关系,以免在最终安装过程中,出现上下或左右方向的偏差。
AI插件PCB设计规范
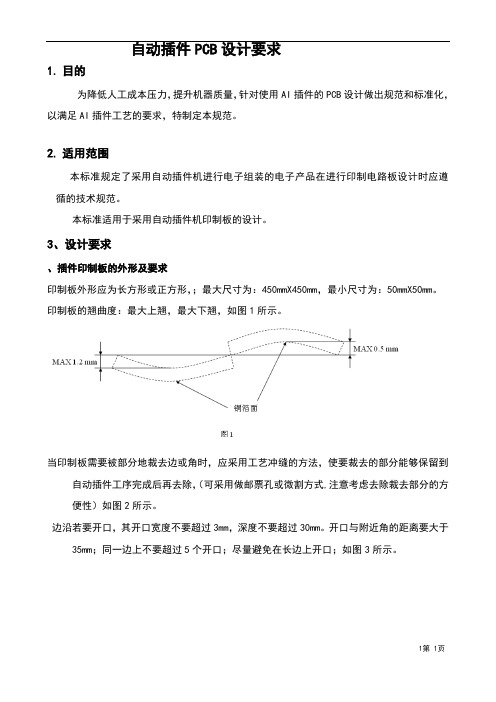
v1.0 可编辑可修改自动插件PCB设计要求1.目的为降低人工成本压力,提升机器质量,针对使用AI插件的PCB设计做出规范和标准化,以满足AI插件工艺的要求,特制定本规范。
2.适用范围本标准规定了采用自动插件机进行电子组装的电子产品在进行印制电路板设计时应遵循的技术规范。
本标准适用于采用自动插件机印制板的设计。
3、设计要求、插件印制板的外形及要求印制板外形应为长方形或正方形,;最大尺寸为:450mmX450mm,最小尺寸为:50mmX50mm。
印制板的翘曲度:最大上翘,最大下翘,如图1所示。
当印制板需要被部分地裁去边或角时,应采用工艺冲缝的方法,使要裁去的部分能够保留到自动插件工序完成后再去除,(可采用做邮票孔或微割方式,注意考虑去除裁去部分的方便性)如图2所示。
边沿若要开口,其开口宽度不要超过3mm,深度不要超过30mm。
开口与附近角的距离要大于35mm;同一边上不要超过5个开口;尽量避免在长边上开口;如图3所示。
印制板的插机定位孔采用AI 插件的印制板应在最长的一条边上设置主副两个电插定位孔。
如图4所示(元件面)。
其中左下角为主定位孔,孔径为Ø;右下角为副定位孔,其孔径尺寸应为Ø的鹅蛋形定位两定位孔的中心轴连线平行于最长边,离最长边的距离为±,主定位孔与左边的距离为±,副定位孔孔边与右边的距离应不小于,定位孔周围从孔边向外至少 2mm 范围内应覆铜箔以增加板的机械强度。
主副两定位孔的中心距L 的优选系列为:290mm 、235mm 、350mm ,误差为±。
主定位孔副定位孔AI插件PCB定位孔在元件面标记符号图中用方框标示。
印制板的非AI插件区在非AI插件区内布置的元件(其插孔在此区内)不适用于AI插件,如该部分确需布件,就需采用手工插件。
对于卧插元件,其非AI插件区(定位盲区和边缘盲区)为图5所示画有斜线的区域,如该部分有元件,需采用手插。
AI自动插件对PCB工艺设计参考

自动插件PCB 设计参考及检查标准(一)项目:电插AI 对PCB 板工艺调整(二)本公司扩大改进持续发展,为节约人力资源,降得成本,因此为了改进DIP 生产,提高效率,用AI 机器代替人工插件,由于AI 机器电插对PCB 板的有一定的工艺要求,所以公司以后接的生产订单相对应的 PCB 有一定的改变。
(三) 改板要求: 改板应由后续的订单开始要求PCB 供应商或PCB 板研发部等,按实际情况能用AI 机器电插的板,尽量改为电插工艺要求。
(四)为了使现时自动插件机发挥最大效率,提高产品质量,我们整理和制订了这份资料,设计PCB 的参考和检验PWB 来料的标准。
卧式自动插件对PCB工艺要求一. PCB 尺寸要求:PCB 的外形最小尺寸 50mm*50mm,最大尺寸450mm*450mm二.PCB 定位孔要求:根据PCB 长度L 的范围,插件机对于鹅蛋形定位孔距PCB 边缘的距离S2 的要求也不同。
S2 也有所改变,有关数据请参照下表:另外,当PCB 定位孔过多,生产时容易造成PCB 取放板方向混淆。
故设计PCB 时,只须在该PCB 长边上设计一组定位孔(左边圆形定位孔+右边 鹅蛋形定位孔)。
三. 自动插件机元件引脚直径范围为: 0.38mm -0.71mm自动插件机可插以下元件:1. 1/16W 、1/8W 、1/4W 电阻2. 电容3. 0.6mm 跳线4. 二极管 例如IN4007,IN40025. 色环电感四. 元件跨度C 的范围: 5.0mm-17.0mm设计元件跨度必须同时考虑到元件体长度L ,如果L 过长,插件机容易打伤 元件体或打断元件引脚,损坏插件机刀具,同时对排料机要求非常严格。
如果跨度C 过大,插件机速度会降低,插件时易掉件(插件机刀具夹不牢)、元件易浮脚。
目前AI 部插件最多的是5.0mm 跨度,5.0mm 跨度的元件在插件时比较容易出现拱起、损伤元件等坏机;故建议将AI 插件元件的最小跨度定为6.0mm ,以求大幅度降低坏件率。
自动插件机用机插实用工艺要求规范

自动插件机用机插工艺规范为进一步提高机插率,达到提效的目的,重新修订了自动插件机用机插工艺规范,自动插件机用机插工艺规范是根据公司已有机插设备的技术规格书拟制的基本技术要求,是专业排版、工艺、质量、认定等部门必须的技术规范,随着技术的更新换代,本规范会出现遗漏和不足之处,希望大家提出宝贵意见并改进之(注:原普通插件机用机插工艺规范、异型插件机用机插工艺规范同时作废,并停止使用)。
1、PCB外形及尺寸要求:[1] 为适应设备线体传动的要求,印制板四角必须倒圆角,R≥2mm;[2] 印制板尺寸必须满足以下条件:设备允许范围长(L)*宽(W)最小尺寸:102mm*80mm;最大尺寸483mm*406mm:为了适应我公司生产线体的要求以及提高机插效率的要求,对于主板和副板拼板的尺寸要求:长(L)*宽(W)最小尺寸:200mm*150mm;最大尺寸400mm*300mm:最佳尺寸330mm*247mm;2、定位孔[1] 用于机插定位的定位孔主要有5个孔,其中三个虚线孔可去掉,如PCB右下角元器件较为密集,则右下角的虚线椭圆孔必须添加,30mm<L1<50mm;[2] 定位孔的尺寸如上图所示,其中A=5mm±0.1mm;[3] 定位孔8mm的范围内应没有焊盘、元器件及走线;丝印标识除外;定位孔周边直径2.5mm范围图一:印制版(机插)定位孔及外型尺寸示意图3、工艺边及工艺夹持边的设计[1] 工艺边夹持边指在生产过程中设备及工装需要夹持的PCB 的边缘部分。
[2] 元器件与板边的最小间距为A=5mm ,焊盘与板边的最小间距为4mm ;边缘铜箔不得小于1mm ,如此条件无法保证时,则要增加工艺边来保证PCB 有足够的可夹持边缘。
[4] 另外增加工艺夹持边将降低PCB 的挠度,且提高成本,设计布板应尽量不采用。
[5] 需要机插的PCB ,机插定位孔可以加在增加的工艺夹持边上,工艺夹持边的宽度不仅要满足夹持需要,还要满足机插定位孔的排布需要。
自动插件机用机插工艺规范

自动插件机用机插工艺规范为进一步提高机插率,达到提效的目的,重新修订了自动插件机用机插工艺规范,自动插件机用机插工艺规范是根据公司已有机插设备的技术规格书拟制的基本技术要求,是专业排版、工艺、质量、认定等部门必须的技术规范,随着技术的更新换代,本规范会出现遗漏和不足之处,希望大家提出宝贵意见并改进之(注:原普通插件机用机插工艺规范、异型插件机用机插工艺规范同时作废,并停止使用)。
1、PCB外形及尺寸要求:[1] 为适应设备线体传动的要求,印制板四角必须倒圆角,R≥2mm;[2] 印制板尺寸必须满足以下条件:设备允许范围长(L)*宽(W)最小尺寸:102mm*80mm;最大尺寸483mm*406mm:为了适应我公司生产线体的要求以及提高机插效率的要求,对于主板和副板拼板的尺寸要求:长(L)*宽(W)最小尺寸:200mm*150mm;最大尺寸400mm*300mm:最佳尺寸330mm*247mm;2、定位孔[1] 用于机插定位的定位孔主要有5个孔,其中三个虚线孔可去掉,如PCB右下角元器件较为密集,则右下角的虚线椭圆孔必须添加,30mm<L1<50mm;[2] 定位孔的尺寸如上图所示,其中A=5mm±0.1mm;[3] 定位孔8mm的范围内应没有焊盘、元器件及走线;丝印标识除外;定位孔周边直径2.5mm范围图一:印制版(机插)定位孔及外型尺寸示意图3、工艺边及工艺夹持边的设计[1] 工艺边夹持边指在生产过程中设备及工装需要夹持的PCB 的边缘部分。
[2] 元器件与板边的最小间距为A=5mm ,焊盘与板边的最小间距为4mm ;边缘铜箔不得小于1mm ,如此条件无法保证时,则要增加工艺边来保证PCB 有足够的可夹持边缘。
[4] 另外增加工艺夹持边将降低PCB 的挠度,且提高成本,设计布板应尽量不采用。
[5] 需要机插的PCB ,机插定位孔可以加在增加的工艺夹持边上,工艺夹持边的宽度不仅要满足夹持需要,还要满足机插定位孔的排布需要。
AI插件机PCB设计规范要求

AI插件机PCB设计规范要求随着科技的不断发展和普及,人工智能已经越来越被广泛应用在各个行业中。
在电子工业中,AI插件机PCB已经成为不可或缺的一个重要部分。
然而,为了保证其可靠性和稳定性,在设计中需要遵守一系列规范要求。
本文将详细介绍AI插件机PCB设计规范要求。
一、布局原则1.信号线与电源线分离布局。
这是因为信号线和电源线的电性质不同,如果两者混在一起,会产生互相干扰和噪声。
2.在布局时,要注意信号线的长度和走向。
信号线的长度应该尽量短,走向应该尽量避免过于复杂的弯曲。
这样可以减小信号的衰减和传输错误的概率。
3.电源线的布局也需要考虑好。
一般来说,电源线应该尽量接近负载,且需要规划好电源的限流电阻,以防止过流电流对电路的损坏。
4.信号和电源线的布局应该与功能模块的位置相对应,以最大程度地减少线路长度。
二、元件组合原则1.要求元件品种合理、组合适宜、电路结构合理。
元件的选用应符合可靠性、稳定性和性能的要求。
2.对于信号放大器、滤波器、数据转换器等关键部件,需要选择高质量的元件。
3.元件之间的接口和连接方式应符合标准化和规范化的要求。
在连接中需要注意防止电磁干扰和信号干扰。
三、电源系统设计原则1.对于电源系统的设计,需要考虑到稳定性和可靠性。
为了避免纹波过大,需要选择高质量、低纹波的电源。
2.电源系统需要加入保护电路,以避免超过规定电压范围的电压对电路的损坏。
3.在电源系统的设计中,需要考虑到电池系统、变压器、整流器等元件的选用和位置布置。
四、接口设计原则1.在设计接口时,需要考虑到接口的标准化和匹配性。
尽量使用标准接口,并需要定义接口标准。
2.接口的位置和设计需要易于扩展和升级,以适应未来的使用需求。
3.需规定接口的工作范围和工作温度范围,并对接口线路进行可靠性测试,以确保接口的稳定性和可靠性。
五、测试设计原则1.在测试设计中,需要定义测试结果的准确性和精度,并考虑如何对测试结果进行合理的分析和处理。
自动插件机用机插工艺规范
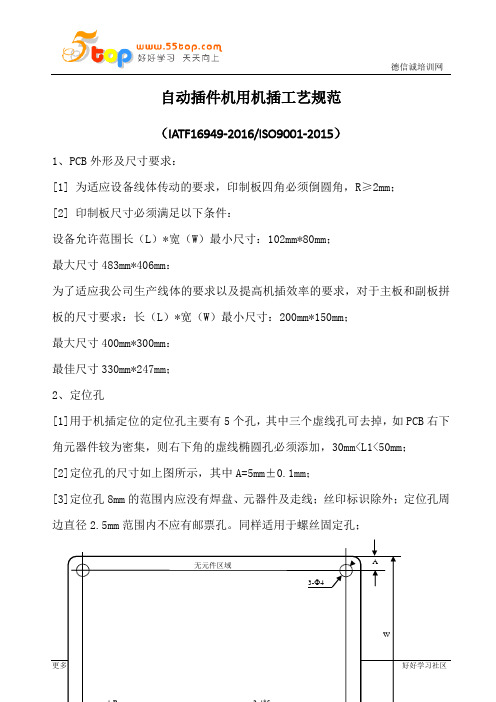
自动插件机用机插工艺规范(IATF16949-2016/ISO9001-2015)1、PCB外形及尺寸要求:[1] 为适应设备线体传动的要求,印制板四角必须倒圆角,R≥2mm;[2] 印制板尺寸必须满足以下条件:设备允许范围长(L)*宽(W)最小尺寸:102mm*80mm;最大尺寸483mm*406mm:为了适应我公司生产线体的要求以及提高机插效率的要求,对于主板和副板拼板的尺寸要求:长(L)*宽(W)最小尺寸:200mm*150mm;最大尺寸400mm*300mm:最佳尺寸330mm*247mm;2、定位孔[1]用于机插定位的定位孔主要有5个孔,其中三个虚线孔可去掉,如PCB右下角元器件较为密集,则右下角的虚线椭圆孔必须添加,30mm<L1<50mm;[2]定位孔的尺寸如上图所示,其中A=5mm±0.1mm;[3]定位孔8mm的范围内应没有焊盘、元器件及走线;丝印标识除外;定位孔周边直径2.5mm范围内不应有邮票孔。
同样适用于螺丝固定孔;图一:印制版(机插)定位孔及外型尺寸示意图3、工艺边及工艺夹持边的设计[1]工艺边夹持边指在生产过程中设备及工装需要夹持的PCB的边缘部分。
[2]元器件与板边的最小间距为A=5mm,焊盘与板边的最小间距为4mm;边缘铜箔不得小于1mm,如此条件无法保证时,则要增加工艺边来保证PCB有足够的可夹持边缘。
[3]另外增加工艺夹持边将降低PCB的挠度,且提高成本,设计布板应尽量不采用。
[4]需要机插的PCB,机插定位孔可以加在增加的工艺夹持边上,工艺夹持边的宽度不仅要满足夹持需要,还要满足机插定位孔的排布需要。
[5]工艺夹持边与PCB可用邮票孔或者V形槽连接。
4、元器件及焊盘排布方向和位置[1]焊盘之间的距离是减少连焊的最重要因素,非连接需要的焊盘间距在任何情况下应保持至少0.5mm(DIP等IC器件无法保证应用焊接面丝印隔离)的最小距离。
见图二。
PCB应用自动插件机的要求

PCB应用自动插件机的要求范围:本文适用针对PANASONIC的Panasert A VK2(立式),Panasert RHS2(卧式)自动插件机的PCB设计。
参考文件:Panasonic Panasert RHS2 ,Panasonic Panasert A VK2定义:元件本体:指元件除引脚外的外尺寸。
一般要求:1.PCB尺寸要求:中号托盘330*250mm 和大号托盘508*350mm2.拼板的注意要点:2.1.主板因面积、重量大,按照330*250MM的托盘设计,垂直方向拼3PCS较为合适。
2.2.显示板可以垂直、横向两个方向拼板,但不宜超过330*250MM。
2.3.为提高插件机的效率,一个拼板至少应大于100个可插的点。
2.4.使用自动插件机,元件孔径需加大,但孔径必须≥0.9mm。
*直接调用服务器上的PCBGROUP\\LIBRARY中结尾带"@"的封装库,可以确保插件元件的正确选择及孔径/孔距合适。
原本就调用标准库的PCB更改成应用于插件机的比较方便,直接在原有封装名后加"@"即可。
2.6.立式元件:元件直径>0.5mm,孔径为1.0mm,元件直径≤0.5mm,孔径为0.9mm.电路中相邻并且相同性质的元件应排成准确的一排,并且是同一方向的有利于插件机的工作。
元件孔位坐标(以插件机定位孔中心为准)在格点上有利于插件机准确对位,例如一孔(X=80.1mm,y=50.5mm),减少出现(X=80.03,Y=50.344)此类的孔坐标。
3.插件机对PCB设计的各项具体要求:3.1.元件弯角有30度、45度3.2.元件的弯脚长度为1.2mm-1.8mm3.3.卧式元件弯脚朝元件中心,两脚的立式元件弯脚为向外弯45度,并且两脚互相平行。
3.4.由于弯脚有可能超出焊盘范围,须特别注意弯脚对电气间隙、爬电距离的影响。
3.5.设计一块电路板开始时就应考虑是否会应用在自动插件机上,如果要使用自动插件机,则孔径外都按照自动插件机的设计。
插件机物料要

• 一、PCB板要求 • 二、物料要求
电插PCB板要求
• 范围
本标准规定了采用自动插件机进行电子组装的电子产品在进行印制 电路板(以下简称印制板)设计时应遵循的技术规范。 本标准适用于采用自动插件机印制板的设计。
•
引用标准
下列标准所包含的条文,通过在本标准中引用成为本标准的条文, 本标准出版时,所示版本均为有效。所有标准都会被修订,使用本 标准的各方应探讨使用下列标准的最新版本的可能性:
MAX 3 mm MAX 35 mm
MAX 30 mm
图2
图3
电插PCB要求
二、 印制板的插机定位孔 1.采用电插的印制板应在最长的一条边上设置主副两个电插定位孔。如 图4所示(元件面)。其中左下角为主定位孔,孔径为Ø4.0mm;右 下角为副定位孔,其孔径尺寸应为Ø4.0mm的鹅蛋形定位孔
元件面
。
物料要求
十、元件包装要求
• 立式元件编带规格 元件供给部和包装规格 能够收纳于元件分配头形式,上段为编带用包装箱(袋)、下段为能够 使用此包装箱和编袋用卷盘。
包装盒规格
物料要求
立式元件包装要求 编带立式元件成品
物料要求
• 卧式元件编带规格
物料要求
注 1. ※印符合JIS标准。其他是新泽谷规格。 2. 使用序列编带时,按照上述尺寸。 3. 引线,请使用镀锡处理后的锡材。 4. 从52mm编带插入5mm间距时,需要另行与本公司联络。 5. 52mm编带具有负公差的W尺寸,需要52mm特殊对应的料架 (51 mm) 。 6. 52 mm编带,具有正公差的W尺寸,使用52mm 特殊对应的料架(51 mm) 时,元件中心发生偏移的可能性较大。 7. 中央卡盘不能使用玻璃二极管等,强度弱的元件。 8. 插入间距在元件中心容许偏移范围内时,元件强度弱的元件无需定 中心 也可插入。(使用52mm特殊对应料架时) 9. 由于元件主体的边缘形状,对中心效果会有偏移的可能性。 10.元件主体的长度,最长为15mm。在此以上时请另行与本公司联络。 11. U尺寸 (U = S + T + W + T + S) 请设置在65.5 mm 以下。
自动插件机PCB设计要求

_1. 范围本标准规定了采用自动插件机进行电子组装的电子产品在进行印制电路板(以下简称印制板)设计时应遵循的技术规范。
本标准适用于采用自动插件机印制板的设计。
2. 引用标准下列标准所包含的条文,通过在本标准中引用成为本标准的条文,本标准出版时,所示版本均为有效。
所有标准都会被修订,使用本标准的各方应探讨使用下列标准的最新版本的可能性: 3. 要求3.1 印制板的外形:3.1.1 印制板外形应为方形,最大尺寸为:450mmX450mm , (如果要插对窗设计宽为200MM*350MM 为佳)3.1.2 印制板的翘曲度:最大上翘1.5mm ,最大下翘1.0mm ,如图1所示。
3.1.3 当印制板需要被部分地裁去边或角时,应采用工艺冲缝的方法,使要裁去的部分能够保留到自动插件工序完成后再去除,如图2所示。
3.1.4 边沿若要开口,其开口宽度不要超过3mm ,深度不要超过3.0mm 。
开口与附近角的距离要大于3.5mm ;同一边上不要超过5个开口;尽量避免在长边上开口;如图3所示。
图2图1MAX 3 mm_3.2_印制板的插机定位孔3.2.1采用电插的印制板应在最长的一条边上设置主副两个电插定位孔。
如图4所示(元件面)。
其中左下角为主定位孔,孔径为Ø3.5mm;右下角为副定位孔,其孔径尺寸应为Ø3.5mm的鹅蛋形定位孔或圆孔。
3.2.2两定位孔的中心轴连线平行于最长边,主定位孔与左边的距离为5.0±0.1mm,副定位孔孔边与右边的距离应不小于3.0mm,定位孔周围从孔边向外至少 2mm范围内应覆铜箔以增加板的机械强度。
3.2.3主副两定位孔的中心距L的优选系列为:290mm、235mm、350mm。
3.2.4电插定位孔在元件面标记符号图中用方框标示。
3.3印制板的非电插区3.3.1在非电插区内布置的元件(其插孔在此区内)不适用于自动插机。
3.3.2对于卧插元件,其非电插区(定位盲区和边缘盲区)为图5所示画有剖线的区域。
自动插件要求

自 動 插 件 作 業 要 求一. 基板要求:圖11. 基板最大尺寸: 508mm*381mm 最小尺寸: 80mm*150mm2. 基板上下板邊6mm 範圍內不能插件.圖23. 基板厚度為1.6±0.15mm.圖34. 基板變形要求: 上彎 Max 0.5mm 下彎Max 1.2mm.1.6±0.15mm圖45.基板之零件孔需為線徑+0.3/0.4mm之喇叭孔.但最小孔徑不得小於0.8mm圖56.基板上之跳線零件兩腳之孔距為5mm~20mm,立式零件類之兩外腳孔中心距固定為2.5mm或5mm;7.基板上臥式零件1/8w電阻兩孔距為6mm-17.5mm, 1/4w電阻兩孔距為10mm-20mm,1/2w電阻兩孔距為13.5mm-20mm.8.臥式零件之間最小之間距為2.5mm, 臥式跳線之間距離大於0.5mm立式零件本體之間距離要大於0.5mm.9.二.零件要求:1.臥式零件需為內徑為52mm之編帶.2.立式零件需為腳距與PCB板孔距相符,固定為2.5mm或5mm之編帶料.3.臥式零件本體長度L≦15mm, 高度H≦3.5mm, 零件腳腳徑d在0.4mm≦d≦0.8mm .4.立式零件之本體寬度W為: 1.5mm≦W≦10mm, 零件高度H≦20mm.三.其它1.AI立式零件之剪腳如下:圖6線徑+0.3/0.4mm0゚方向之電容腳 90゚方向之電容腳 腳長1.98±0.2mm 腳長1.98±0.2mm圖80゚方向之電晶體腳腳長1.98±0.2mm 腳長1.98±0.2mm2. AI 臥式零件之剪腳如下:圖10圖110゚方向之臥式零件腳 90゚方向之臥式零件腳 腳長1.98±0.2mm 腳長1.98±0.2mm3. 因AI 零件彎腳之原因, 故基板在設計時, 需考量兩零件之位置, 以避免AI 插件後零件腳相碰短路.4. 自動插件彎腳后引腳孔中心與相鄰PAD 之間距離不得<2.0mm.四. PCB MSD 零件腳距及PAD 要求電阻(Refolw solder Pad ) 電容(Refolw Solder Pad )。
- 1、下载文档前请自行甄别文档内容的完整性,平台不提供额外的编辑、内容补充、找答案等附加服务。
- 2、"仅部分预览"的文档,不可在线预览部分如存在完整性等问题,可反馈申请退款(可完整预览的文档不适用该条件!)。
- 3、如文档侵犯您的权益,请联系客服反馈,我们会尽快为您处理(人工客服工作时间:9:00-18:30)。
1. 范围
本标准规定了采用自动插件机进行电子组装的电子产品在进行印制电路板(以下简称印制板)设计时应遵循的技术规范。
本标准适用于采用自动插件机印制板的设计。
2. 引用标准
下列标准所包含的条文,通过在本标准中引用成为本标准的条文,本标准出版时,所示版本均为有效。
所有标准都会被修订,使用本标准的各方应探讨使用下列标准的最新版本的可能性: 3. 要求
3.1 印制板的外形:
3.1.1 印制板外形应为方形,最大尺寸为:450mmX450mm , (如果要插对窗设计宽为
200MM*350MM 为佳)
3.1.2 印制板的翘曲度:最大上翘1.5mm ,最大下翘1.0mm ,如图1所示。
3.1.3 当印制板需要被部分地裁去边或角时,应采用工艺冲缝的方法,使要裁去的部分能够保留
到自动插件工序完成后再去除,如图2所示。
3.1.4 边沿若要开口,其开口宽度不要超过3mm ,深度不要超过3.0mm 。
开口与附近角的距离要
大于3.5mm ;同一边上不要超过5个开口;尽量避免在长边上开口;如图3所示。
图2
图 1
圆孔
图 3
MAX 3 mm
3.2
印制板的插机定位孔
3.2.1 采用电插的印制板应在最长的一条边上设置主副两个电插定位孔。
如图4所示(元件
面)。
其中左下角为主定位孔,孔径为Ø3.5mm ;右下角为副定位孔,其孔径尺寸应为Ø3.5mm 的鹅蛋形定位孔或圆孔。
3.2.2 两定位孔的中心轴连线平行于最长边,主定位孔与左边的距离为5.0±0.1mm ,副定位孔孔
边与右边的距离应不小于3.0mm ,定位孔周围从孔边向外至少 2mm
范围内应覆铜箔以增加板的机械强度。
3.2.3 主副两定位孔的中心距L 的优选系列为:290mm 、235mm 、350mm 。
3.2.4 电插定位孔在元件面标记符号图中用方框标示。
3.3 印制板的非电插区
3.3.1 在非电插区内布置的元件(其插孔在此区内)不适用于自动插机。
3.3.2 对于卧插元件,其非电插区(定位盲区和边缘 盲区)为图5所示画有剖线的区域。
3.3.3 对于立插元件,其非电插区为图6所示画有剖线的区域。
3.3.4 为防止工装、夹具等损伤印制板边沿的印制线,应避免在印制板边沿3mm 范围内布宽度
1mm 以下的电路走线。
图 4 5.0±0.1 Min 3.0
元件的插孔
3.4.1 元件插孔中心连线的平行度或垂直度如图7所示。
3.4.2 元件插孔的中心距CS :
卧插元件CS=5.5~20mm ,如图7示 立插元件CS=2.5/5.0±0.1mm ,如图8所示。
3.4.3 元件插孔直径Ø
卧插元件: Ø=1.3±0.1mm (塑封整流二极管等0.8mm 引线的元件)
Ø=1.1±0.1mm (1/2W 、1/4W 电阻、电感、跳线等0.6mm 引线的元件) Ø=1.0±0.1mm (1/6W 、1/8W 电阻、玻璃二极管等0.5mm 引线的元件)
立插元件: Ø=1.1±0.1mm (0.6mm 引线的元件)
Ø=1.3±0.1mm (0.8mm 引线的元件)
3.4 元件形体的限制
3.5.1 卧插元件:对元件形体作如下限制
长度 L = 0 ~(CS-3.5)mm (元件两孔跨距=元件本体长度+3.5mm) 本体直径 D = 0.4 ~ 5.0mm 引线直径 d = 0.4 ~ 0.8mm 跳线直径D =0.5~0.8MM
3.5.2 立插元件:如图10所示,其元件体能够被容纳最大高度可为18MM ,最大直径为10MM
图 5 图 6
2.5±0.1
2.5±0.1
3.5 自动插元件的切脚形状
3.6.1 卧插元件:其在印制板上的切铆形状如图11a 所示,其中CL=1.5-2.2±0.5mm ,可调
CA=0-35±10°可调, h ≈0.1mm 。
K >1.75MM
3.6.2 立插元件:其在印制板上的切铆形状如图11b 所示,其中CL=1.5-2.2±0.3mm ,可调
CA=10-35±10°可调。
3.6 元件排布的最大允许密度
3.7.1 卧插元件:各种可能的最密排布其相邻的最小间距如图12所示。
d
c
a
b
X 轴 Y 轴 Z 轴
K L K
CL
CA
h CA
CL
N 型头
图 11a 图 11b
图12
元件密度要求:
PWB上元件密度越大,自插机走位越小,因此效率越高。
但是,元件密度过大插件时会打伤打断邻近元件,损坏刀具。
下图是插件机能够接受的最大密度:
元件铜皮设计:
自插机插件时,一直存在如下问题:
1.元件角度过大,容易掉件和产生浮脚
2.元件角度过小,容易和相邻铜皮短路
`
a
a过大,易掉件和浮脚 a过小,易和相邻的铜皮短路
为彻底解决以上问题,建议EG 设计PWB 时,采用以下方法:
.
卧式元件与SMT元件间的密度Y
要求:X≤0.05mm Y≤0.05mm
插件元件面::
A 依孔为中心距2MM范围内不可有贴片元件,
B:依孔为中心距2MM到3MM围内不可高于1MM的贴片元件。
C:依孔为中心距5MM范围内不可有2MM贴片元件。
根据贴片元件的尺寸设计。
如图1所示
.
插件剪脚面:
A
A
B C
D
A :2MM 范围内不可有贴片元件,5MM 范围内不可高于2MM 贴片元件。
B :2MM 范围内不可有贴片元件,5MM 范围内不可高于2MM 贴片元件。
C :3MM 范围内不可有贴片元件。
D :8MM 范围内不可有贴片元件。
根据贴片元件的尺寸设计。
3.7.2 立插元件:
a )立插元件的排布应考虑已卧插的元件对立插元件的影响,还应避免立插元件引脚向外成
形时可能造成的相邻元件引脚连焊(直接相碰或过波峰焊时挂锡),如图13所示。
b )立插元件最密排布时其相邻立插元件本体(包括引脚)之间的最小距离应不小于
1mm ,立插元件与卧插元件之间应有适当的间距。
如图14所示。
图 14 .
.
插件面:立式元件与贴片元件的要求。
● (W )4mm ×(L )10mm 的范围内不可有SMT 元件。
● (W )8mm ×(L )14mm 的范围内不可有高度大于1mm 的SMT 元件。
● (W )14mm ×(L )14mm 的范围内不可有高度大于5mm 的SMT 元件。
●
●
立式元件与贴片元件低面间的密度:
Bottom Side SMT 元件与Radial 元件的密度
由于Radial 插件机的元件剪断弯脚部件在进行Radial 插件时会与PCB 的Bottom Side 有较近的距离,为此对Bottom Side 的SMT 元件与Radial 元件孔的距离有要求。
2.5±0.1
2.5±0.1
5.0±0.1 5.0±0.1
图9
15
.
图10
● (W )4mm ×(L )9mm 的范围内不可有SMT 元件。
● (W )10mm ×(L )16mm 的范围内不可有高度大于1mm 的SMT 元件。
● (W )13mm ×(L )22mm 的范围内不可有高度大于5mm 的SMT 元件。
● Bottom Side 的元件高度不可大于6mm 。
3.7 焊盘
3.8.1 焊盘的设计应考虑到元件引脚切铆成形时的方向,应有利于焊接,应考虑到波峰焊时元件
引脚不至于与相邻印制线路短路。
3.8.2 卧插元件的焊盘宜设计成长圆形,插孔在焊盘中的位置如图15a 所示;立插元件的焊盘宜
设计成插孔和焊盘为圆形,插孔位置如图15b 所示或如图10以元件脚打弯方向设计更佳。
3.8 所有机插元件应在标记符号图上标上位号,包括短路跳线、铆钉、需机插的插针等,铆钉、插
针需每个孔每个针标上位号,短路跳线、铆钉、插针可只在元件面标注。
图 15a 图 15b 卧插
立插。