球墨铸铁典型铸件工艺设计实例
铸件工艺设计举例

模数计算
S截面 V M S散 L散热热周
6、冷铁设计(铸件区域划分)
Ach…………需要摆放冷铁的面积 V0…………区域的体积 M0…………区域的初始模数 Mr…………区域激冷后的模数
G ቤተ መጻሕፍቲ ባይዱH
M0 Mr 7.4V 0 M0
Gch…………需要摆放的冷铁重量(Kg)
6、冷铁设计(铸件区域划分)
0.25
0.25
-1.2
-0.55
30316
18518
363.8
101.85 560
冒口总体积为420*3=1260 FOSECO的冒口补缩效率按照33%计算,3个冒口可以补缩420CC的铁水量,此值 小于总收缩量560,因此需要将冒口加大一个型号,即
补缩量可以达到550CC。 冒口设计完成。
冒口相关资料
球铁件工艺设计步骤
技术部
张怀国
2011. 02.15
球铁件工艺设计步骤: 1、铸件结构分析(重量计算,模数计算),确定整体方案 2、确定化学成分 3、计算液相线温度、确定浇注温度
4、浇注系统设计(查表+手工计算)
5、冒口设计 6、冷铁设计(铸件区域划分) 7、3D实体绘制(包括冷铁、浇注系统、冒口) 8、MAGMA模拟参数设置 9、MAGMA结果分析 10、工艺继续改进及模拟验证
15.7=22.6*600/(6.9*t*0.45*(107.5)1/2) t=27s
4、浇注系统设计(查表+手工计算)
浇注线速度计算:
V体积=600000/6.9=86957cm3
V直=86957/19.62/27=1.64m/s V横=86957/49/27=0.65m/s V过道=86957/15.7/27=2.05m/s S内浇道=15.7*2=31.4=2-φ40+2φ30=39cm*cm V内浇道=2.05*15.7/39=0.83m/s M内浇口=D/4=1 M内浇口=D/4=0.75 M件*0.2=0.55 内浇口部位要放置冷铁,防止 内浇口倒抽铁水,形成缩孔。 M内浇口< M件*0.2 内浇口出口处速度控制在1m/s以下
《球墨铸铁管安装规范及图示》

能耐低温;
PE 可任意增加管长,减少接头;
管
易于弯曲,不需弯管零件; 接
头可熔接;
缺点
原来弯头、三通处需打水泥固定台防 推,现已新兴开发防滑脱弯头及三通 管件,解决了该缺点;
容易腐蚀; 接头焊接、敷设防锈层费时,费用较 高,涌水地点施工困难; 为抵抗温度变化,需设置可挠管; 大口径管容易扁平; 因为接头钢性,克服变形需使用砂子 铺底,并要求用细沙回填并夯实; 受外压易变形,安全性差; 熔接需专业技术人员; 不适用于300mm以上管径;分支管 施工不易;受紫外线照射易老化,
1
编制说明
球墨铸铁管从国际到国内现已广泛应用于城 镇供水及燃气行业,是用户比较能认可的一种成 熟产品,现从制造、标准、设计、使用等均已形 成系列标准,为了提高球墨铸铁管管道工程的施 工水平,保证工程质量,完成设计意图,满足管 线使用要求,本文特将球墨铸铁管材质、施工要 求作一说明,供同行参考,不足之处请指教
7
一、开挖管 沟 5)挖掘时,防备下雨时雨水流入管沟,活地下渗水
现象,应当准备必要的排水设备; 6)挖掘管沟尺寸(不用钢板支撑时)一般坡度取
0.33,见下表一
8
Байду номын сангаас
一、开挖管 沟
注: (1)埋深度北方地区应大于在当地冻土层以下;
(2)在快速道下、重载车辆路基下埋深管子 处,按设计管道内压及外压的1.5-2倍安全系 数考虑深度,但绝对不能小于⒈2米埋深度; (3)h’为砂垫层厚度;
4.清理胶圈; 必须将砂子和其它杂物清理干净,将胶圈装在插
口上并刷涂以润滑脂;
30
三、K型机械接口管安装要点
1.将管子的承口与另一支管的插口连接起来; 插口外圆及承口内圆之间的圆周间隙必须相对均匀,
球墨铸铁的工艺设计 毕业设计 毕业论文

球墨铸铁的工艺设计第一节工艺特点1.1球墨铸铁的流动性与浇注工艺球化处理过程中球化剂的加入,一方面使铁液的温度降低,另一方面镁、稀土等元素在浇包及浇注系统中形成夹渣。
因此,经过球化处理后铁液的流动性下降。
同时,如果这些夹渣进入型腔,将会造成夹杂、针孔、铸件表面粗糙等铸造缺陷。
为解决上述问题,球墨铸铁在铸造工艺上须注意以下问题:(1)一定要将浇包中铁液表面的浮渣扒干净,•最好使用茶壶嘴浇包。
(2)严格控制镁的残留量,最好在0.06%以下。
(3)浇注系统要有足够的尺寸,以保证铁液能做尽快充满型腔,并尽可能不出现紊流。
(4)采用半封闭式浇注系统,根据美国铸造学会推荐的数据,直浇道、横浇道与内浇道的比例为4:8:3。
(5)内浇口尽可能开在铸型的底部。
(6)在浇注系统中安放过滤网会有助于排除夹渣。
(7)适当提高浇注温度以提高铁液的充型能力并避免出现碳化物。
对于用稀土处理的铁液,其浇注温度可参阅我国有关手册。
对于用镁处理的铁液,根据美国铸造学会推荐的数据,当铸件壁厚为25mm时,浇注温度不低于1315℃;当铸件壁厚为6mm时,浇注温度不低于1425℃。
1.2、球墨铸铁的凝固特性与补缩工艺特点球墨铸铁与灰铸铁相比在凝固特性上有很大的不同,主要表现在以下方面:(1)球墨铸铁的共晶凝固范围较宽。
灰铸铁共晶凝固时,片状石墨的端部始终与铁液接触,因而共晶凝固过程进行较快。
球墨铸铁由于石墨球在长大后期被奥氏体壳包围,其长大需要通过碳原子的扩散进行,因而凝固过程进行较慢,以至于要求在更大的过冷度下通过在新的石墨异质核心上形成新的石墨晶核来维持共晶凝固的进行。
因此,球墨铸铁在凝固过程中在断面上存在较宽的液固共存区域,其凝固方式具有粥状凝固的特性。
这使球墨铸铁凝固过程中的补缩变得困难。
(2)球墨铸铁的石墨核心多。
经过球化和孕育处理,球墨铸铁的石墨核心较之灰铸铁多很多,因而其共晶团尺寸也比灰铸铁细得多。
(3)球墨铸铁具有较大的共晶膨胀力。
球铁齿轮的均衡凝固工艺设计

有的方向上,单元的相邻边之比不能超过4∶1。
②在弯曲裂纹前缘上,单元的大小取决于局部曲率的数值。
例如,沿圆环状弯曲裂纹前缘,在15°~30°的角度内至少有一个单元。
③所有单元的边(包括在裂纹前缘上的)都应该是直线。
参考文献[1]薛河,刘金依,徐尚龙,等.ANSYS中断裂参量的计算及分析[J].重型机械,2002(2):47-49.[2]龚曙光.ANSYS在应力分析设计中的应用[J].化工装备技术2002,23(1):29-33.[3]东方人华,祝磊,马赢.ANSYS7.0入门与提高[M].北京:清华大学出版社,2004.1概述对于球铁齿轮这样的铸件,结构严重不均匀,存在轮缘与轮幅交接部位,该部位是较厚大热节,利用传统的过热冒口工艺,往往在该部位产生缩孔缩松,而且缩孔缩松部位较深,往往在齿的根部,导致铸件报废,废品率较高,况且该工艺使用较大的过热冒口,工艺出品率较低,因此,非常有必要对其进行工艺改进。
图1所示的齿轮,直径为1500mm,重量约3500kg,是压缩机用飞轮,有灰铁和球铁两种材质,对于灰铁件,由于呈逐层凝固方式,收缩倾向较小,采用传统的过热冒口工艺一般不会产生缩孔缩松;但对于球铁件而言,由于呈糊状凝固,收缩倾向大,很容易在冒口颈处和几何热节部位产生缩孔缩松,因此,着重研究球铁件。
2传统的过热冒口工艺及存在的问题图2所示的传统的过热冒口工艺,出现缩孔缩松部位是铸件本身的几何热节和冒口径部位,由于铸件本身的几何热节在同样凝固条件下,将晚于其他部位凝固,且该部位散热条件较差,在凝固过程中发生的液态收缩和凝固收缩因没有铁液充分补缩而产生了缩孔。
尽管冒口颈的引入不在热节部位,但过热冒口颈的引入使得本来不是热节的部位形成了新的接触热节。
由于是过热冒口,必须让冒口对铸件进行充分补缩,冒口要晚于铸件凝固,冒口颈不能过早封闭,况且铁液在充满整个型腔过程中过热时间长,该部位散热条件差,凝固时间增加,收缩时间也增加,均衡点后移,不利于胀缩的早期叠加,使得现行的冒口不能进行有效的补缩,这样在冒口颈所形成的接触热节处留下了缩孔。
高强度厚大断面球墨铸铁花盘的铸造工艺设计

\ \
。
铸钢件加工困难 ,缺陷多,所以选用 了高强度球 墨
铸 铁 材 质 ,铸 件 重 4 t 0 ,属 厚 大 断 面 球 墨 铸 铁 件 , 结 构 尺寸 如 附 图所 示 。铸 件特 点 及技 术 要 求如 下 。
—
/
/
() b
B
( )铸件材质QT o —3 1 6 0 ,机加工后硬度要求
台面 的 质 量 和 铸 件 尺 寸 精 度 ,方 便 下 芯 及 砂 芯 固
()铸件加工后需做静平衡试验 ,因而对砂芯 5
的尺 寸 一致性 、分度 和定 位尺 寸等 精 度要 求严 格 。
3_ 0
:
造 参 磊
工
机床铡造业技术专题
定 ,使 各 工序 操 作 方便 ,依 据 厚大 断 面 球 墨铸 铁 件
0. 5。
+ 11 ,主 轴 孔 及 卡爪 槽+1 m1。 起 模斜 度 1 T1 5 I3 T 5 I
5 mm ,砂 芯 间隙 2 mm ,分 型 负数 一4 m。铸 造 圆 a r 角R1 mm。设 计 了6 卡 板 ,测 量 砂 芯 的 尺 寸 精 5 个 度 、分 度 及定 位 尺 寸 。砂 箱 吃砂 量4 0 0 mm,合箱 后
t;
‘
上jI O 1 C 司
1。 5k 上 l 一
C
L ' n
一 《 {
0 0
卜
1 。 5,
L\ 工
I
7 7
拉 筋 共2 个
0
鲁 l 量 f ] } . 量
t / l /
I
缩松 、气 孔 、夹 渣 和 冷隔 等 缺 陷 。不 得有 尺 寸 、化
球墨铸铁铸件的补缩工艺[1]
![球墨铸铁铸件的补缩工艺[1]](https://img.taocdn.com/s3/m/95563257ad02de80d4d84021.png)
收稿日期:2010-09-19; 修订日期:2010-10-20作者简介:牟行辉(1974- ),四川射洪人,工程师.从事铸铁件铸造工艺设计和质量控制工作.Email:m u_xinghu i@V ol.32N o.1Jan.2011铸造技术F OU N DRY T ECH NO LO GY工艺技术 Technology球墨铸铁铸件的补缩工艺牟行辉(陕西秦川机床工具集团有限公司,陕西宝鸡721009)摘要:通过分析和总结在生产实践过程中球墨铸铁铸件产生缩孔缩松缺陷以及成功解决办法,对球铁铸件凝固收缩理论提出理解和看法:铸件的补缩及缺陷产生取决于压力,由于球铁的凝固特性使石墨化膨胀和凝固收缩分离,薄壁件截面凝固差异不明显,石墨化膨胀压力无法有效利用,厚大件的截面凝固的差异大,容易实现石墨化膨胀压力的利用。
铸造补缩工艺的设计原则就是提供并保持这样的压力,对薄壁要强调外部压力补缩,厚壁则充分利用石墨化膨胀压力自补缩。
关键词:球墨铸铁;缩孔缩松;补缩;凝固压力中图分类号:TG255 文献标识码:A 文章编号:1000-8365(2011)01-0007-04Feeding Process of the Ductile Iron CastingsMU Xing -hui(Qinchuan Machine Tool Group C orp.,Baoji 721009,C hina)Abstract:By analyzing and summ arizin g the process of practice in the production of du ctile iron castings produ ced Shrinkage Defects an d successful solution.Make to some un derstand an d view of du ctile iron castings solidification theory:Feeding a castin g depend upon the pressure.For the solidification ch aracteristic of th e sph eroidal graph ite cast iron,th e expan sion of the graphitization are not syn chronized shrin k.In thin wall,no fu nction of the the expansion pressure of the graphitization because fewer division of solidification,and the thick wall,the more division with solidification in section,so th e expan sion and the shrink will be segistration.So the inten tion of the feeding process disign are su pporting and keepin g on pressu re.Th e th in wall,pressu re shall be su pported with others,and the thick wall,th e pressu re maybe exploit th e th e the expansion of the graphitization.Key words:Du ctile C ast Iron;Shrinkage;Feedin g;Solidification Pressure1 球铁凝固收缩工艺理论对球墨铸铁件采用什么样的工艺措施解决和防止缩孔缩松,目前的共识是,铸型必须具有足够的刚性和强度,化学成分接近共晶成分、加强球化和孕育处理以产生足够的石墨化膨胀。
球墨铸铁QT600--3表面激光多道淬火工艺的研究

学校代号:10532学号:¥1102W244密级:公开湖南大学工程硕士学位论文球墨铸铁QT600.3表面激光多道淬火工艺的研究导师姓名及职称:刘继常教授桂林高级工程师论文提交日期:2013年5月20日StudyontheprocessesofmultichannellasersurfacequenchingofductilecastironQT600-3byLUODanB.E.(nunanUniversityofArtandScience)2011AthesissubmittedinpartialsatisfactionoftheRequirementsforthedegreeofMasterofEngineeringVehicleEngineeringintheGraduateSchoolofHunanUniversitySupervisorProfessorLIUJichangSeniorEngineerGUILinMay,2013湖南大学学位论文原创性声明本人郑重声明:所呈交的论文是本人在导师的指导下独立进行研究所取得的研究成果。
除了文中特别加以标注引用的内容外,本文不包含任何其他个人或集体已经发表或撰写的成果作品。
对本文的研究做出重要贡献的个人和集体,均已在文中以明确方式标明。
本人完全意识到本声明的法律后果由本人承担。
…名:产日期:邳年6月6日学位论文版权使用授权书本学位论文作者完全了解学校有关保留、使用学位论文的规定,同意学校保留并向国家有关部门或机构送交论文的复印件和电子版,允许论文被查阅和借阅。
本人授权湖南大学可以将本学位论文的全部或部分内容编入有关数据库进行检索,可以采用影印、缩印或扫描等复制手段保存和汇编本学位论文。
本学位论文属于1、保密口,在一年解密后适用本授权书。
2、不保密团。
(请在以上相应方框内打“√”)日期:Zof乡年6月6日作者签名:日期:加侈年6月6日导师签名:球墨铸铁QT600·3表面激光多道淬火工艺的研究摘要球墨铸铁材料因其较高的强度、良好的塑性和韧性,以及便于生产,成本比钢低廉等优良的性能而被广泛应用在工业生产中的各个领域。
常用铸造齿轮材料及其热处理工艺方法
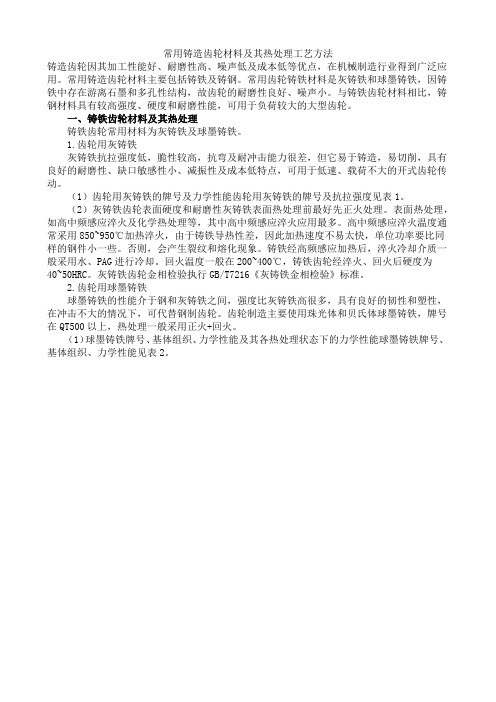
常用铸造齿轮材料及其热处理工艺方法铸造齿轮因其加工性能好、耐磨性高、噪声低及成本低等优点,在机械制造行业得到广泛应用。
常用铸造齿轮材料主要包括铸铁及铸钢。
常用齿轮铸铁材料是灰铸铁和球墨铸铁,因铸铁中存在游离石墨和多孔性结构,故齿轮的耐磨性良好、噪声小。
与铸铁齿轮材料相比,铸钢材料具有较高强度、硬度和耐磨性能,可用于负荷较大的大型齿轮。
一、铸铁齿轮材料及其热处理铸铁齿轮常用材料为灰铸铁及球墨铸铁。
1.齿轮用灰铸铁灰铸铁抗拉强度低,脆性较高,抗弯及耐冲击能力很差,但它易于铸造,易切削,具有良好的耐磨性、缺口敏感性小、减振性及成本低特点,可用于低速、载荷不大的开式齿轮传动。
(1)齿轮用灰铸铁的牌号及力学性能齿轮用灰铸铁的牌号及抗拉强度见表1。
(2)灰铸铁齿轮表面硬度和耐磨性灰铸铁表面热处理前最好先正火处理。
表面热处理,如高中频感应淬火及化学热处理等,其中高中频感应淬火应用最多。
高中频感应淬火温度通常采用850~950℃加热淬火,由于铸铁导热性差,因此加热速度不易太快,单位功率要比同样的钢件小一些。
否则,会产生裂纹和熔化现象。
铸铁经高频感应加热后,淬火冷却介质一般采用水、PAG进行冷却。
回火温度一般在200~400℃,铸铁齿轮经淬火、回火后硬度为40~50HRC。
灰铸铁齿轮金相检验执行GB/T7216《灰铸铁金相检验》标准。
2.齿轮用球墨铸铁球墨铸铁的性能介于钢和灰铸铁之间,强度比灰铸铁高很多,具有良好的韧性和塑性,在冲击不大的情况下,可代替钢制齿轮。
齿轮制造主要使用珠光体和贝氏体球墨铸铁,牌号在QT500以上,热处理一般采用正火+回火。
(1)球墨铸铁牌号、基体组织、力学性能及其各热处理状态下的力学性能球墨铸铁牌号、基体组织、力学性能见表2。
(2)球墨铸铁热处理铸造齿轮毛坯的预处理一般采用退火、正火,也可进行正火+回火,或调质处理。
球墨铸铁齿轮的常用热处理工艺见表3。
(3)球墨铸铁金相检验执行GB/T9441《球墨铸铁金相检验》标准。
球墨铸铁轴承盖铸造工艺设计分析.docx
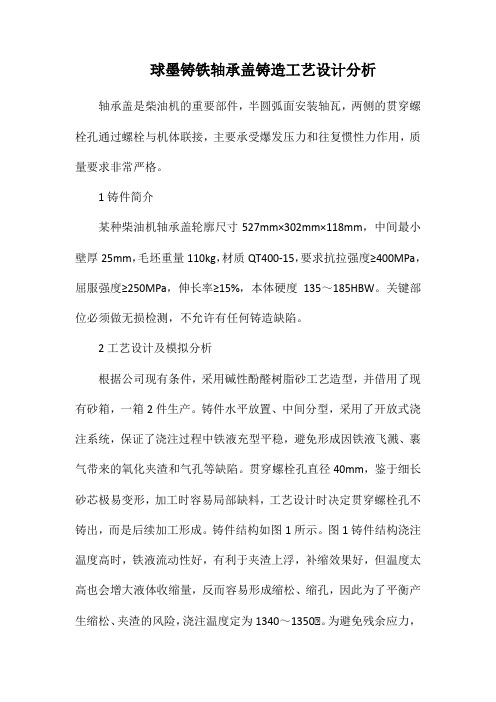
球墨铸铁轴承盖铸造工艺设计分析轴承盖是柴油机的重要部件,半圆弧面安装轴瓦,两侧的贯穿螺栓孔通过螺栓与机体联接,主要承受爆发压力和往复惯性力作用,质量要求非常严格。
1铸件简介某种柴油机轴承盖轮廓尺寸527mm×302mm×118mm,中间最小壁厚25mm,毛坯重量110kg,材质QT400-15,要求抗拉强度≥400MPa,屈服强度≥250MPa,伸长率≥15%,本体硬度135~185HBW。
关键部位必须做无损检测,不允许有任何铸造缺陷。
2工艺设计及模拟分析根据公司现有条件,采用碱性酚醛树脂砂工艺造型,并借用了现有砂箱,一箱2件生产。
铸件水平放置、中间分型,采用了开放式浇注系统,保证了浇注过程中铁液充型平稳,避免形成因铁液飞溅、裹气带来的氧化夹渣和气孔等缺陷。
贯穿螺栓孔直径40mm,鉴于细长砂芯极易变形,加工时容易局部缺料,工艺设计时决定贯穿螺栓孔不铸出,而是后续加工形成。
铸件结构如图1所示。
图1铸件结构浇注温度高时,铁液流动性好,有利于夹渣上浮,补缩效果好,但温度太高也会增大液体收缩量,反而容易形成缩松、缩孔,因此为了平衡产生缩松、夹渣的风险,浇注温度定为1340~1350℃。
为避免残余应力,减少组织内珠光体含量,从而获得良好的韧性,浇注完成后型内冷却时间不小于48h,自然时效,不需要去应力退火。
球墨铸铁具有糊状凝固特性。
由于这种糊状凝固特性以及凝固时间较长,造成凝固时球墨铸铁件的外壳长期处于较软状态,在石墨化膨胀力作用下外壳二次膨胀,松弛了内部压力,容易在铸件热节处形成缩松甚至缩孔,使铸件的致密性下降[1]。
因此,在工艺设计时我们重点关注了缩松问题。
经分析,我们设计了两种工艺方案(见图2),并利用MAGMA软件进行了工艺模拟分析预测,如图3所示。
方案1:上下全冷铁工艺,利用冷铁的激冷效果改变铸件的温度场,并利用石墨膨胀自补缩能力解决缩松缺陷。
方案2:底面冷铁+顶面保温冒口工艺,主要利用冒口的补缩能力解决铸件可能产生的缩松问题。
利用模数法设计球墨铸铁件的冒口冷铁工艺实例_薛蕊莉

(Ningxia Kocel Group Co., Ltd., Yinchuan 750021, Ningxia, China)
Abstract: Calculation of casting modulus is very important for the control of sequence solidification of the casting. In order to solve the dispersed shrinkage of power lining casting, the moduli calculation method was used to design the risers and chills of the ductile iron casting, and the dispersed shrinkage was successfully solved by the method. The results show that the rejection rate of the similar products decreases from 20% to 2% after improvement. Key words:moduli; feeding distance; risers; chills
1 产品参数及原工艺
铸件高度620 mm,外圆最大半径494 mm,顶部内 圆半径372 mm,铸件最大壁厚 (顶部) 81 mm,最小 壁厚38 mm,铸件重366 kg,材质要求为ASTM标准的 A395。原工艺冷铁及冒口工艺见图2,外侧铺满厚度 40 mm的灰铸铁冷铁,内侧在凸出位置放置60 mm厚的 冷铁,冒口为Φ200 mm×200 mm的保温冒口4个。
QT500—7球墨铸铁熔炼工艺设计毕业论文

QT500-7球墨铸铁熔炼工艺设计摘要合金熔炼是铸造生产中的重要环节。
当前,铸造生产中的废品约有50% 与熔炼有关,熔炼铁液的成本约占铸件成本的25%~30% ,合金熔炼对铸件质量和成本有着很大的影响。
我们应该针对不同的铸件材质及技术要求选择不同的熔炼方法。
本设计题目为QT500-7球墨铸铁熔炼工艺设计,体现了球墨铸铁熔炼的设计要求、内容及方向,有一定的设计意义。
通过对该牌号球墨铸铁的设计,进一步加强了设计者熔炼工艺设计的基础知识,为设计其它牌号铸铁的熔炼做好了铺垫和吸取了更深刻的经验。
本设计运用铸造合金熔炼的基础知识,首先分析了QT500-7球墨铸铁的成分及性能要求,为选取熔炼设备及炉料做好了准备;然后选取熔炼设备,计算炉料的比例用量;最后设定球化、孕育方法,确定浇注温度参数,进行质量检测及分析。
本设计着重点在于使用冲天炉-感应电炉双联熔炼球墨铸铁。
由冲天炉熔化铁液并进行化学成分含量的初步确定;在感应电炉中高温精炼,调整铁液的化学成分至规定的范围;进一步清除非金属夹杂物和降低气体含量;提高铁液温度至符合出炉球化要求;最终球化及孕育处理,出炉检测。
关键词:球墨铸铁双联熔炼球化处理孕育处理QT500-7 Ductile Iron Smelting Process DesignAbstractAlloy melting is an important part in casting production. At present, about 50% of the waste in the foundry production is related to the smelting. The cost of the molten iron is about 25% - 30% of the cost of the casting. We should choose different smelting methods fordifferent casting materials and technical requirements.This design topic is QT500-7 nodular cast iron smelting process design, reflects the design requirements, content and direction of ductile iron smelting, there is a certain design significance. Through the design of this type of ductile iron, further strengthen the designers of the basic knowledge of smelting process design for the design of other grades of cast iron to pave the way and draw a more profound experience.The design and use of casting alloy melting of basic knowledge,the first analysis of the QT500-7 nodular cast iron composition and performance requirements for the selection of smelting equipment and charge ready; then select smelting equipment, calculation burden ratio; finally set the ball, inoculation method, to determine the parameters of casting temperature, quality detection and analysis.This design is focused on the use of cupola induction furnace duplex melting of nodular cast iron. By cupola melting iron liquid and preliminary identification of chemical components; in the induction furnace high temperature refining, adjustment of the liquid metal chemical composition to the specified range; further clear non metallic inclusions and reduce the gas content; improve the temperature of molten metal to meet released the ball of the requirements; and eventually the ball and inoculation treatment, detection of released.Key words: Ductile iron, Tecastiron, Spheroidize, Inoculation treatment目录摘要 IAbstract II1 绪论 11.1球墨铸铁的出现 11.2国内外球墨铸铁的发展 11.3球墨铸铁的应用 21.4熔炼工艺及发展 31.5课题来源及意义 42 熔炼工艺方案的确定 52.1熔炼技术要求及分析 52.1.1技术要求 52.1.2材料性能及分析 52.2工艺方案 63 冲天炉熔炼工艺设计 83.1冲天炉熔炼特性及原理 83.1.1冲天炉熔炼概述 83.1.2冲天炉熔炼的技术要求 83.1.3冲天炉的燃烧过程原理 103.2炉料的计算 133.2.1球墨铸铁原铁液的配比要求 13 3.2.2QT500-7原始资料的确定 133.2.3确定元素增减率及增减后成分 14 3.2.4确定配料比并校核 143.2.5炉料计算 153.3熔炼工艺及参数 163.3.1装炉 163.3.2炉前控制 163.3.3铁液出炉 163.3.4脱硫处理 163.4熔炼过程的化学反应 174电炉熔炼工艺设计 204.1感应电炉的熔炼特点 204.1.1感应电炉构造及工作原理 204.1.2感应电炉熔炼的优缺点及其应用 20 4.2熔炼工艺及参数 214.2.1二次脱硫 214.2.2脱磷处理 214.2.3精炼调整 224.3球化工艺 224.3.1球化剂 224.3.2QT500-7球化剂的选用 244.3.3 QT500-7的球化处理工艺 244.3.4球化剂加入量的确定 264.4孕育工艺 274.4.1孕育剂 274.4.2孕育处理工艺 284.5出液浇注 294.5.1浇注温度对性能的影响 29 4.5.2球铁的浇注温度 295质量检验及分析 305.1质量检测 305.1.1炉前三角试片检验法 30 5.1.2火苗判断法 305.1.3炉前快速金相法 305.1.4炉前光谱分析法 305.2缺陷分析 305.2.1球化不良 315.2.2球化衰退 325.2.3石墨漂浮 326 结论 34致谢 36参考文献 371 绪论铸造是机电装备制造业中铸件生产的工艺过程。
典型铸铁件铸造工艺设计与实例

典型铸铁件铸造工艺设计与实例叙述铸造生产中典型铸铁件——气缸类铸件、圆筒形铸件、环形铸件、球墨铸铁曲轴、盖类铸件、箱体及壳体类铸件、阀体及管件、轮形铸件、锅形铸件及平板类铸件的铸造实践。
内容涉及材质选用、铸造工艺过程的主要设计、常见主要铸造缺陷及对策等。
第1章气缸类铸件?1.1 低速柴油机气缸体?1.1.1 一般结构及铸造工艺性分析?1.1.2 主要技术要求?1.1.3 铸造工艺过程的主要设计?1.1.4 常见主要铸造缺陷及对策?1.1.5 铸造缺陷的修复?1.2 中速柴油机气缸体?1.2.1 一般结构及铸造工艺性分析?1.2.2 主要技术要求?1.2.3 铸造工艺过程的主要设计?1.3 空气压缩机气缸体?1.3.1 主要技术要求?1.3.2 铸造工艺过程的主要设计? 第2章圆筒形铸件?2.1 气缸套?2.1.1 一般结构及铸造工艺性分析?2.1.2 工作条件?2.1.3 主要技术要求?2.1.4 铸造工艺过程的主要设计?2.1.5 常见主要铸造缺陷及对策?2.1.6 大型气缸套的低压铸造? 2.1.7 气缸套的离心铸造?2.2 冷却水套?2.2.1 一般结构及铸造工艺性分析?2.2.2 主要技术要求?2.2.3 铸造工艺过程的主要设计?2.2.4 常见主要铸造缺陷及对策?2.3 烘缸?2.3.1 结构特点?2.3.2 主要技术要求?2.3.3 铸造工艺过程的主要设计?2.4 活塞?2.4.1 结构特点?2.4.2 主要技术要求? 2.4.3 铸造工艺过程的主要设计?2.4.4 砂衬金属型铸造?第3章环形铸件?3.1 活塞环?3.1.1 概述?3.1.2 材质?3.1.3 铸造工艺过程的主要设计?3.2 L形环?3.2.1 L形环的单体铸造?3.2.2 L形环的筒形铸造?第4章球墨铸铁曲轴?4.1 主要结构特点?4.1.1 曲臂与轴颈的连接结构?4.1.2 组合式曲轴?4.2 主要技术要求?4.2.1 材质?4.2.2 铸造缺陷?4.2.3 质量检验?4.2.4 热处理?4.3 铸造工艺过程的主要设计?4.3.1 浇注位置?4.3.2 模样?4.3.3 型砂及造型?4.3.4 浇冒口系统?4.3.5 冷却速度?4.3.6 熔炼、球化处理及浇注?4.4 热处理?4.4.1 退火处理?4.4.2 正火、回火处理?4.4.3 调质(淬火与回火)处理?4.4.4 等温淬火?4.5 常见主要铸造缺陷及对策?4.5.1 球化不良及球化衰退?4.5.2 缩孔及缩松?4.5.3 夹渣?4.5.4 石墨漂浮?4.5.5 皮下气孔?4.6 大型球墨铸铁曲轴的低压铸造?第5章盖类铸件?5.1 柴油机气缸盖?5.1.1 一般结构及铸造工艺性分析?5.1.2 主要技术要求?5.1.3 铸造工艺过程的主要设计?5.2 空气压缩机气缸盖?5.2.1 一般结构及铸造工艺性分析?5.2.2 主要技术要求?5.2.3 铸造工艺过程的主要设计?5.3 其他形式气缸盖?5.3.1 一般结构?5.3.2 主要技术要求?5.3.3 铸造工艺过程的主要设计?第6章箱体及壳体类铸件?6.1 大型链轮箱体??6.2 增压器进气涡壳体?6.3 排气阀壳体??6.4 球墨铸铁机端壳体??6.5 球墨铸铁水泵壳体?6.6 球墨铸铁分配器壳体?第7章阀体及管件?7.1 灰铸铁大型阀体??7.2 灰铸铁大型阀盖??7.3 球墨铸铁阀体??7.4 管件??7.5 球墨铸铁螺纹管件??7.6 球墨铸铁管卡箍?7.6.1 主要技术要求?7.6.2 铸造工艺过程的主要设计?7.6.3 常见主要铸造缺陷及对策?第8章轮形铸件?8.1 飞轮??8.2 调频轮?8.3 中小型轮形铸件??8.4 球墨铸铁轮盘?第9章锅形铸件? 9.1 大型碱锅?9.2 中小型锅形铸件?第10章平板类铸件?10.1 大型龙门铣床落地工作台??10.2 大型立式车床工作台?10.3 大型床身中段??10.4 大型底座?中国机械工业出版社精装16开定价:299元。
空心球铸造

造型、造芯
• 型芯用铁铸出来的两个内 径为170mm,外径为 182mm的半球,半球在直 径平面处和在球顶处,共 含有五个凸台,凸台高为 9mm • 用做好直径为200mm的木 球和型砂做出直径为 200mm的砂型
• 将两铁半球合到一起放在 200MM的木模做模样所成 的型腔中。
空心无缝球墨铸铁球的制造工艺
材料: 材料:QT500 直径: 直径:Ø 200 MM 壁厚: 壁厚:15 MM 造型方法: 造型方法: 砂型手工造型
要求: 要求: 可以采取任何工艺措施,但不能在球外表面焊接,可以打磨等。 1 可以采取任何工艺措施,但不能在球外表面焊接,可以打磨等。 2 设计出铸造工艺方案 3 画出铸造工艺图 可以5 讨论和查资料, 4 可以5 组,讨论和查资料,运 明任务分工。 明任务分工。 学铸 识 作业, 作业,注
浇注
落砂、清理、 落砂、清理、检验
球墨铸铁管典型工程结构设计分析

1、设计方法简述: 由于球墨铸铁管是定型产品,所以设计过程中对管材的选择更多的是根据管线受力特
点选择各项参数满足要求的球墨铸铁管成品,根据目前国内球墨铸铁管制造标准规定,具 有指导意义的成品参数主要是允许径向变形率、允许工作压力及最大允许工作压力,围绕 这三项指标我们具体拟定了相关的设计方法。
设计过程中先按规范规定确定管道工作压力及管道设计内水压力,通过与管的允许工 作压力及管的最大允许工作压力的关系初步选择管材等级,然后进行空管在外部竖向荷载 作用下的变形复核,通过上述两个步骤初步选定产品,最后按空管在外部竖向荷载作用下 计算管道的环向弯曲强度进行管道强度复核。
ISO 10803
最小壁厚计算:
允 许 工 作 压 力
公称壁厚计算:
DN为公称管径
最小壁厚计算公式是根据管道允许工作压力计算最 小壁厚,再由公称壁厚计算公式计算出公称壁厚进 行选材
ISO 10803
外部荷载作用下的变形设计方法
1、根据外部作用竖向荷载计算管道变形率 2、计算管道允许变形率
a、管道内村材料允许变形率 b、管壁抗弯强度条件决定的允许变形率 c、取两项小值作为管道允许变形率 3、判断外荷载引起的变形率是否满足管道允许变形率
5.1、一般规定
5.2、内压强度计算
5.3、径向变形控制
5.3、径向变形控制
5.3、径向变形控制
5.4、环向弯曲强度计算
5.5、稳定计算
5.5、明管支撑结构
(一) 工程设计资料 (二) 各种设计方法计算应用
1、云南省文山州德厚水库工程:
德厚水库工程位于云南省文山州文山市德厚镇,距文山 市35km,是一座以城乡生活和工业供水、农业灌溉为主,兼 顾一定的发电功能的大型水利枢纽。
- 1、下载文档前请自行甄别文档内容的完整性,平台不提供额外的编辑、内容补充、找答案等附加服务。
- 2、"仅部分预览"的文档,不可在线预览部分如存在完整性等问题,可反馈申请退款(可完整预览的文档不适用该条件!)。
- 3、如文档侵犯您的权益,请联系客服反馈,我们会尽快为您处理(人工客服工作时间:9:00-18:30)。
球墨铸铁典型铸件工艺设计实例李魁盛于清华2009-08-273.1 球墨铸铁曲轴(湿砂型铸造、金属型复砂铸造)曲轴是发动机中重要机件之一,发动机全部功率都是通过曲轴输出。
曲轴的主要载荷是承受扭转疲劳、弯曲疲劳和连杆传递来的小能量多次冲击;曲轴轴径与轴瓦的配合,在较高的比压下高速运转,正常情况下为有机油润滑的滑动摩擦磨损。
依据国内外曲轴失效的统计数据,其主要失效方式是交变应力下的疲劳破坏(80%为弯曲疲劳断裂)和轴径的早期磨损烧伤。
根据曲轴服役的工况和主要失效方式,要求曲轴材料不但要有较高的强度、韧性,而且要有一定的硬度。
球墨铸铁曲轴与传统的锻钢曲轴比较,有制造简便、成本低廉、又有吸震耐磨、对表面刻痕不敏感等锻钢材料所不具备的优良特性、球铁与巴氏合金、铅青铜、钢背铝合金的轴瓦均有良好的匹配性。
石墨具有润滑作用和储存润滑油作用,其耐磨性比钢好;球墨铸铁在承受小能量多次冲击载荷条件下,其抗冲击性能也优于钢;球墨铸铁曲轴通过合金化、合理球化、孕育处理等,其在扭转、弯曲疲劳应力状态下的疲劳强度,可达到甚至超过锻钢曲轴。
3.1.1.铸态球墨铸铁曲轴1. 生产性质大量生产。
2. 材质研究和实践证明:球墨铸铁是中小型发动机曲轴的理想材料。
现在,铸态QT600-3、QT700-3牌号球墨铸铁已广泛应用于汽车曲轴;QT800-2、QT900-5牌号热处理球墨铸铁也成功地用于汽车曲轴的生产。
铸态球墨铸铁曲轴与热处理工艺比较,不仅可节约能源、降低成本、缩短生产周期;而且省去了因热处理而产生的曲轴变形所带来的清理和热校直工序。
在满足设计要求的前提下,工厂首先选择了铸态球墨铸铁曲轴这一操作简便,成本低廉的生产方式。
(1) 化学成分及合金元素的选择为了保证球墨铸铁曲轴具有良好的性能:1) 碳当量与C和Si 碳当量控制在4.3%~4.5%之间,可以得到健全的铸件,并具有较好的铸造性能。
碳当量过低易产生白口,过高则会产生石墨飘浮。
图3.1-1是4110型柴油机球铁曲轴的生产统计结果。
碳当量超过4.5%~4.6%,曲轴断面出现石墨漂浮,并且随着碳当量的增加,石墨漂浮层的厚度几乎直线加厚。
应该指出,碳当量不是产生石墨漂浮的惟一因素,曲轴尺寸的大小也是一个重要条件。
曲轴断面尺寸越小,碳当量可能选高一些,也不会出现石墨漂浮,相反,厚大断面曲轴的碳当量应该低一些。
图3.1-1 石墨漂浮层厚度与碳当量的关系w(C)应控制在3.6%~3.9%。
C含量低,石墨不易球化,易出现白口;C含量过高易产生石墨漂浮。
一般w(Si)控制在1.8%~2.2%为宜。
Si来自金属炉料、球化剂和孕育剂。
Si是石墨化元素,影响球墨铸铁的铸造性能和力学性能,通过以下3种途径表现出来:改变石墨大小、分布、圆整度;分解渗碳体,促进生成铁素体;溶解在α-Fe中,强化金属基体。
2) Mn和P Mn和P都是严重偏析元素。
Mn易导致晶界碳化物的形成,铸态球墨铸铁曲轴不采用高Mn来稳定珠光体为好;P易在晶界处形成磷共晶,会造成球铁塑、韧性下降,同时显著降低疲劳强度。
所以Mn和P的含量都应控制。
一般w(Mn)≤O.3%,w(P)≤O.06%为宜。
3) S S是反球化元素,属于有害杂质。
生产中根据原铁水含S量的高低决定球化剂的加入量,原铁水S量越高,加入量越多。
但是,S含量高,即使球化,曲轴内部易出现夹渣,球化衰退很快,不容易浇注出健全的铸件。
所以,希望原铁液的含S量越低越好,一般w(S)≤O.03%,有脱S条件的w(S)≤O.02%最好。
4) 合金元素添加稳定珠光体合金元素是生产铸态球墨铸铁曲轴行之有效的方法。
添加的元素主要有Cu、Sn、Ni、Sb、Cr、Mo、W、V等。
然而后4种元素虽能增加基体组织的珠光体含量,提高球铁的强度和耐磨性,但它们都是碳化物形成元素,容易使材料变脆,降低材料的疲劳强度。
Cu、Sn、Ni、Sb等合金元素共同特点是能促进形成珠光体并细化组织,提高球铁的强度、硬度和耐磨性。
但它们各自稳定珠光体的能力不同。
它们稳定珠光体的能力可以近似地用下式表示:Ni:Cu:Sn:Sb=1:3:30:90稳定珠光体的能力Cu是Ni的3倍,Sn是Cu的lO倍,Sb是Sn的3倍。
Cu能够明显地降低球铁断面敏感性,减少Mn的偏析程度,可使曲轴厚壁处也能达到高的珠光体含量,并可以提高球墨铁的疲劳强度。
Ni能强烈地细化珠光体,提高球铁的塑、韧性。
Mo能显著的稳定球铁奥氏体,促进生成针状组织,增强球墨铸铁的淬透性。
Sb对球化有强烈的干扰作用,加入过量时,不但使石墨畸变,而且与Mg反应生成富锑的脆性相,偏析在晶界,使铸件严重脆化,特别是大大降低了冲击韧性。
Sn加入量大于0.06%时,铸件产生脆性。
以上各元素均能不同程度的稳定珠光体,但Cu和Sn的组合合金化,不仅符合高质量、低成本要求,而且还可以加在球化包内,满足一种原铁水生产多种牌号球铁的需要。
(2) 金相组织球墨铸铁曲轴的疲劳强度与石墨和基体的形态、组成、尺寸大小、分布特征以及非金属夹杂物的类别、形状、大小、数量及分布均匀性有密切关系。
1) 石墨形态不仅影响球墨铸铁的静载荷性能,而且更显著地影响动载荷性能。
稀土镁球铁中,球状和团状石墨(球化级别1~3级)的动态性能相差较少,当出现团片状石墨时,性能明显下降,尤其是组织中有厚片状石墨聚集分布时(球化级别6级),疲劳强度约下降20%,而小能量多次冲击韧性下降约5倍。
镁球铁中,球化率65%的球铁比球化率93%的球铁抗拉强度σb下降8.2%,而疲劳强度σ-1下降26%。
当石墨的体积一定时,石墨的平均球径越大,单位面积视场中球墨个数越少,疲劳强度越低。
石墨成行排列,促进疲劳断裂,降低疲劳强度。
实践证明:石墨球越细小,圆整、均布,球铁的疲劳强度就越高。
图3.1-2 w(珠光体)对HBS、σ、αk、δ的影响2) 基体组织随着珠光体量的增加,强度、硬度增加,塑性、韧性下降。
图3.1-2是w(珠光体)与硬度(HBS)、拉抗强度(σb)、冲击韧性(αk)、延伸率(δ)的关系图。
如图所示,当珠光体大于80%时,抗拉强度和布氏硬度值上升比率增加;珠光体大于50%时,延伸率下降梯度减缓,冲击韧性值变化比率变化较小。
图3.1-3是w(珠光体)与疲劳强度(σ-1)的关系图。
如图所示,基体组织中珠光体由O%增加到100%,疲劳强度从230 MPa增加到320 MPa;珠光体由20%增加到80%时,疲劳强度变化不大;当珠光体超过80%进一步增加时,疲劳强度明显增加。
基体组织中珠光体的层片间距越小,疲劳强度越高。
如图3.1-4(a)珠光体层片间距大的球铁疲劳强度小于图3.1-4(b)珠光体层片间距小的球铁疲劳强度。
图3.1-3 w(珠光体)与疲劳强度的关系铁素体的作用:当珠光体量一定,抗拉强度相近的条件下,牛眼状铁素体屈服强度最高,延伸率最低。
综上所述,球墨铸铁中较高的珠光体含量是获得高强度,特别是提高疲劳强度的有效途径。
随着珠光体含量的提高,要依赖基体组织的强化和细化来阻止疲劳裂纹的扩展。
图3.1-4 珠光体基体的二次电子像(a)大层片间距×3000;(b)小层片间距×30003) 夹杂物研究表明,非金属夹杂物的数量、尺寸大小、形状及其分布比石墨更加显著地影响球铁的疲劳强度。
夹杂物越少,形状粒化,颗粒越小,其疲劳强度越高。
所以,生产球墨铸铁曲轴,采用金属净化是必不可少的工艺措施。
通常采用在浇注系统中安放过滤网,净化铁液,图3.1-5是球铁曲轴立浇立冷的工艺方案,在浇注系统中放置了过滤网,起到了良好的净化铁液作用。
(3)力学性能图3.1-6是抗拉强度(σb)与疲劳强度(σ-1)的关系图。
如图所示,随着抗拉强度的提高,最初试棒的疲劳强度亦成正比例的提高;当抗拉强度上升到750 MPa时,疲劳强度不复增加,呈一水平线。
所以,中小球铁曲轴的抗拉强度控制在600~800 MPa为宜,没有必要追求过高的抗拉强度值,以提高疲劳强度比(σ-1/σb),充分发挥材料的强度潜力。
图3.1-5 球铁曲轴立浇立冷工艺方案图3.1-6 抗拉强度与疲劳强度的关系为适应曲轴的服役工况,材料还应有一定的塑性和韧性,通常延伸率大于3%为宜。
同时曲轴材料还应有一定的硬度,一般200HBS~270HBS为宜,以适应曲轴耐磨性的要求。
3.1.2 湿型铸造球墨铸铁曲轴的工艺问题1. 湿型铸造工艺国内目前普遍采用湿砂型铸造,缩孔及缩松的体积约占铸件的4%~10%。
1) 冒口应设置控制压力冒口。
控制压力冒口适于在湿型中铸造模数MC=0.5~2.5cm的球墨铸铁件。
目的在于补给铁液体积收缩而避免缩孔;当曲轴内因凝固而出现石墨化体积膨胀时,让铸件内的多余铁液部分地回充冒口,以减轻型腔内壁承受的压力,避免型壁外移而导致曲轴铸件胀大变形。
又能在铸件内保留一定的压力用来消除缩松。
这种冒口又叫“释压冒口”。
众所周知,球铁具有糊状凝固的特性。
铸件内保留的压力越高,消除缩松的效果越好。
这就要求湿型有较高的、强度和刚度。
采用短冒口颈。
冒口颈的模数依下式确定M n=0.67M r冒口颈的形状可选用圆形、正方形或矩形。
冒口的补缩距离与传统冒口的补缩概念不同,控制压力冒口的补缩距离,不是表明由冒口把铁液输送到铸件的凝固部位,而是表明由凝固部位向冒口回填铁液,能输送多大距离。
该距离与铁液冶金质量和铸件模数密切相关。
冶金质量好,模数大,输送距离也大。
输送距离达不到的部位,铸件内膨胀压力过高,将导致型壁塑性变形,使铸件胀大变形,内部却可能存在缩松。
控制压力冒口的经验:尽量采用内浇道通过边冒口的引入方式;采用大气压力暗冒口为宜;采用扁薄内浇道。
要求浇注后迅速凝固,促使冒口中快速形成大缩孔,以便容纳回填铁液;要求快浇;宜高温浇注。
要求浇温在1371~1427℃±25℃;希望采用冶金质量好的铁液。
一般采用暗冒口。
暗冒口在铸件上的位置可分为顶冒口和侧冒口。
顶冒口放在铸件壁最厚处(即热节)的上面,侧冒口则设在热节的侧面。
工厂凭多年生产经验来确定冒口尺寸。
成批大量生产可以通过解剖铸件来验证。
图3.1-7给出了球墨铸铁曲轴常用侧冒口的尺寸比例范围。
图3.1-7 球墨铸铁曲轴侧暗冒口2.球墨铸铁浇注系统的特点球墨铸铁的铸造性能与普通灰铸铁不同,容易产生皮下气孔、二次氧化夹渣、球化衰退、浇不足和缩松等缺陷。
因此,铸件浇注系统必须保证铁液平稳、畅通、比灰铸铁稍快地充型。
为做到这点,许多工厂采用半封闭或开放式的浇注系统。
其特点是:直浇口小,内浇口、横浇口的截面积均要比直浇口大。
铁液进入型腔的速度低、平稳、无冲击。
但这种浇注系统挡渣效果差。
二次氧化夹渣是球铁曲轴疲劳失效的主要裂纹源,所以,球铁曲轴的浇注系统必须采取挡渣措施,如茶壶嘴式浇包,拔塞外浇口、闸门浇口、过滤网、集渣包等。