表面形变强化
表面形变强化名词解释
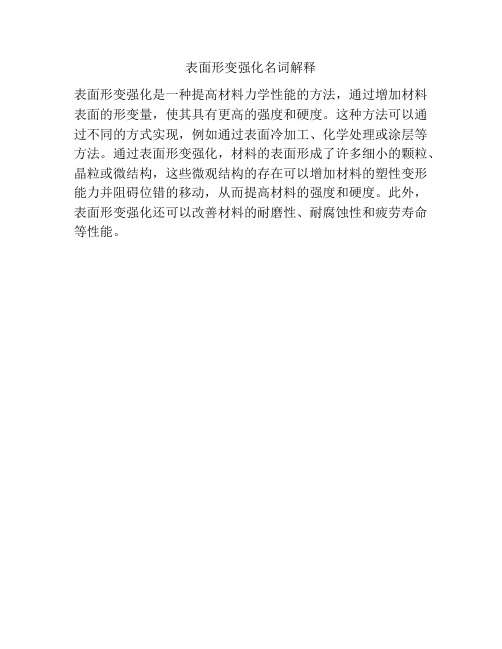
表面形变强化名词解释
表面形变强化是一种提高材料力学性能的方法,通过增加材料表面的形变量,使其具有更高的强度和硬度。
这种方法可以通过不同的方式实现,例如通过表面冷加工、化学处理或涂层等方法。
通过表面形变强化,材料的表面形成了许多细小的颗粒、晶粒或微结构,这些微观结构的存在可以增加材料的塑性变形能力并阻碍位错的移动,从而提高材料的强度和硬度。
此外,表面形变强化还可以改善材料的耐磨性、耐腐蚀性和疲劳寿命等性能。
表面形变强化技术

奥赫弗尔特理论
• 奥赫弗尔特认为,喷丸的残余应力的产生 取决于两个方面的机制: • 一方面由于大量弹丸压人产生的切应力造 成了表面塑性延伸; • 另一方面,由于弹丸的冲击产生的表面法 向力引起了赫芝压应力与亚表面应力的结 合。 • 在大多数材料中这两种机制并存。
喷丸产生的残余压应力
• 经喷丸和滚压 后,金属表面产生 的残余压应力的大 小,不但与强化方 法、工艺参数有关, 还与材料的晶体类 型、强度水平以及 材料在单调拉伸时 的硬化率有关。
• 这种表面形貌和表层组织结构产生的变化,有效 地提高了金属表面强度、耐应力腐蚀性能和疲劳 强度。
二、表面形变强化的主要方法及应用
• (一)表面形变强化的 主要方法 • 1.滚压 • 目前,滚压强化用的滚 轮、滚压力大小等尚无 标准。 • 对于圆角、沟槽等可通 过滚压获得表层形变强 化,并能在表面产生约 5mm深的残余压应力, 其分布如图所示。
残余压应力
• 具有高硬化率的面心立方晶体的镍基或铁 基奥氏体热强合金,表面产生的压应力高, 可达材料自身屈服点的2-4倍。
• 材料的硬化率越高,产生的残余压应力越 大。
表面强化方法
有效地提高了金属表面强度、耐应力腐蚀性能和疲劳强度。
• 表面强化方法还可消除切削加工留下的刀痕; • 表面形变强化手段还可能使表面粗糙度略有增 加,但却使切削加工的尖锐刀痕圆滑,因此可减 轻由切削加工留下的尖锐刀痕的不利影响。
喷丸强度
• 当弧高度f达到饱和值,试片表面达到全覆 盖率时,以此弧高度f定义为喷九强度。 • 喷丸强度的表示方法是0.25C或fc=0.25, 字母或脚码代表试片种类,数字表示弧高 度值(单位为mm)。
(2)表面覆盖率试验
• 喷丸强化后表面弹丸坑占有的面积与总面 积的比值称为表面覆盖率。 • 一般认为,喷丸强化零件要求表面覆盖率 达到表面积的100%即全面覆盖时,才能有 效地改善疲劳性能和抗应力腐蚀性能。
对于表面形变强化技术的现状分析

摘要:表面强化是近年来国内外广泛研究应用的工艺之一。
常用的金属表面形变强化方法主要有滚压、内挤压和喷丸等工艺,其强化效果显著,成本低廉。
笔者主要概括了表面强化技术的分类、目的和作用,分析了形变强化方法的特点以及目前表面强化主要研究方法的现状和发展趋势。
关键词:表面形变;强化技术;滚压;内挤压;喷丸引言材料表面处理技术简称材料表面技术,是材料科学的一个重要分支,是在不改变基体材料的成分和性能(或虽有改变而不影响其使用)的条件下,通过某些物理手段(包括机械手段)或化学手段来赋予材料表面特殊性能,以满足产品或零件使用需要的技术和工艺。
材料表面技术在工业中的应用,大幅度提高了产品(尤其是金属零件)的性能、质量和寿命,并产生了巨大的经济效益,因而深受各国政府和科技界的重视。
1 表面形变强化原理通过机械手段(滚压、内挤压和喷丸等)在金属表面产生压缩变形,使表面形成形变硬化层(此形变硬化层的深度可达0.5~1.5mm),从而使表面层硬度、强度提高。
2 表面形变强化工艺分类表面形变强化主要有喷(抛)丸、滚压和孔挤压等三种工艺。
2.1喷丸强化工艺喷丸是国内外广泛使用的一种在再结晶温度以下的表面强化方法,可显著提高抗弯曲疲劳、抗腐蚀疲劳、抗应力腐蚀疲劳、抗微动磨损、耐蚀点(孔蚀)能力,它具有操作简单、耗能少、效率高、适应面广等优点,是金属材料表面改性的有效方法。
2.1.1喷丸强化的发展状况1908年,美国制造出激冷钢丸,金属弹丸的出现不仅使喷砂工艺获得迅速发展,而且导致了金属表面喷丸强化技术的产生。
1929年,在美国由Zimmerli等人首先将喷丸强化技术应用于弹簧的表面强化,取得了良好的效果[1]。
20世纪40年代,人们就发现了喷丸处理可在金属材料表面上产生一种压缩应力层,可以起到强化金属材料、阻止裂纹在受压区扩展的作用。
到了20世纪60年代,该工艺逐步应用于机械零件的强化处理上。
20世纪70年代以来,该工艺已广泛应用于汽车工业,并获得了较大的经济技术效益,如机车用变速器齿轮、发动机及其他齿轮均采用了喷丸强化工艺,大幅度提高了抗疲劳强度。
表面变形强化
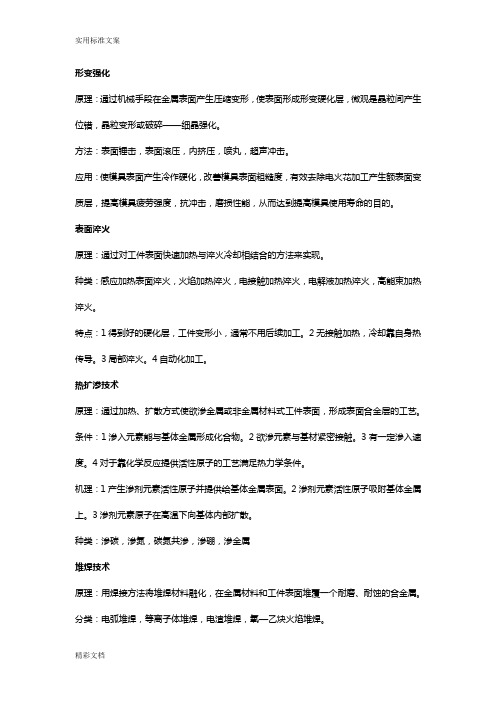
原理:通过机械手段在金属表面产生压缩变形,使表面形成形变硬化层,微观是晶粒间产生位错,晶粒变形或破碎——细晶强化。
方法:表面锤击,表面滚压,内挤压,喷丸,超声冲击。
应用:使模具表面产生冷作硬化,改善模具表面粗糙度,有效去除电火花加工产生额表面变质层,提高模具疲劳强度,抗冲击,磨损性能,从而达到提高模具使用寿命的目的。
表面淬火原理:通过对工件表面快速加热与淬火冷却相结合的方法来实现。
种类:感应加热表面淬火,火焰加热淬火,电接触加热淬火,电解液加热淬火,高能束加热淬火。
特点:1得到好的硬化层,工件变形小,通常不用后续加工。
2无接触加热,冷却靠自身热传导。
3局部淬火。
4自动化加工。
热扩渗技术原理:通过加热、扩散方式使欲渗金属或非金属材料式工件表面,形成表面合金层的工艺。
条件:1渗入元素能与基体金属形成化合物。
2欲渗元素与基材紧密接触。
3有一定渗入速度。
4对于靠化学反应提供活性原子的工艺满足热力学条件。
机理:1产生渗剂元素活性原子并提供给基体金属表面。
2渗剂元素活性原子吸附基体金属上。
3渗剂元素原子在高温下向基体内部扩散。
种类:渗碳,渗氮,碳氮共渗,渗硼,渗金属堆焊技术原理:用焊接方法将堆焊材料融化,在金属材料和工件表面堆覆一个耐磨、耐蚀的合金属。
分类:电弧堆焊,等离子体堆焊,电渣堆焊,氧—乙炔火焰堆焊。
定义:将喷涂材料经特定热源加热至熔融或半熔融状态,通过高速气流使其雾化并喷射到工件表面,形成耐磨、耐蚀以及抗高温等特殊性能涂层的一种表面加工方法。
过程:1加热2雾化3加速飞行4堆积涂层组成:气孔,氧化物,涂层变形颗粒特点:1喷涂材料和基材不受限制2涂层材料广泛3零件没有尺寸形状限制4除火焰喷涂外,其他基材温度较低低压等离子喷涂原理:在低压条件下,将金属或非金属粉末送入刚性非转特型等离子弧焰中,加热至熔融状态随离子焰高速喷涂并沉积到预先处理的工件表面,形成一个特殊性能的涂层。
设备:真空喷涂室电源水路供气系统特点:1低压密闭室内进行2粉末完全均匀熔融喷涂3空隙率低4工件预热温度高活化基材表面5冷却慢应力小不易开裂6通入惰性气体不易氧化7能获得不同性能涂层失效分析失效分析1失效2形式:弯曲镦粗塑性变形失效3原因强度不足,刚度不足A材料本身:高温工作过程中,材料的屈服强度低,而产生了塑性变形工艺热处理:室温工作时,选用高强度钢并做硬化处理高温下工作时,选用蠕变强度高的热强钢并做热处理B工作环境:冲击,腐蚀,高温C装配尺寸:镦粗气相沉积(物理化学)联系:1两者都为气体沉积成膜2两种方法得到的涂层成分基本相同区别:1反应方式不同:化学气相沉积利用化学反应物理气相沉积利用蒸发辉光放电和弧光放电2压强不同:化学…是在低压或常压下,物理…是在带负偏压3温度不同:化学…在高温下,物理..在温度较低下4化学模强度高,精度高,可以形成多层性5化学气相沉积的绕镀性好水溶液沉积表面强化一电镀1在含镀层金属的溶液中,被镀材料做阴极,镀层材料或不溶性材料作阳极,在直流电作用下,被镀材料表面获得镀层的方法。
第七章-表面形变强化
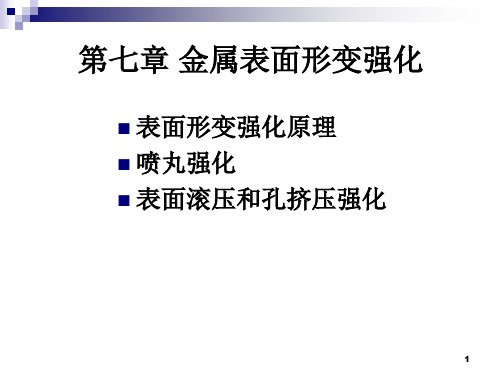
喷丸前后晶粒、亚晶粒位错组态、晶界分布示意图
4
表面残余应力
在表面强化过程中,表面塑性变形带来的表面尺寸变 化引起表面残余应力。下图是滚压处理后的残余应力分布。
5
1)强化后残余应力的分布规律
表面为残余压应力,心部为残余拉应力,最表面层由 于应力松驰,其残余应力稍有降低,故曲线上有“抬头” 现象。
6
3
金属的塑形变形是通过位错运动实现的,在塑性变形过程中, 由于位错间相互作用,使位错密度增加。下图中(a)为喷丸 前组织,晶界与亚晶界比较清晰,晶粒与亚晶粒比较大;(b) 为初始喷丸时,随变形量增加,位错互相作用使位错密度不断 增加,原亚晶界逐步模糊不清、消失;(c)为随喷丸覆盖增 加,弹丸反复冲击金属表面,使一些位错重新排列形成新的亚 晶界。随喷丸时间延长,塑性变形继续进行,位错密度进一步 增加,使晶界逐步消失又组成新的晶界,使晶粒破碎、细化。
21
1. 滚压和孔挤压强化用设备
滚压和孔挤压强化用设备是利用现有冷加工设备如车、 钻床或镗床,再配备用作滚压和孔挤压强化工艺必须的装 置。 (1)滚压强化用装置
在滚压过程中,主要运动是轴的回转运动,辅助运动是 滚子沿轴的回转中心进行转动。适用于圆周类零件的强化。
22
23
(2)孔挤压强化用装置
村套挤压强化装置 压印模挤压强化装置
铸钢丸不同于钢丝切丸,它会破碎,从而在循环使用 时划伤工件,而且铸钢丸硬度越大,抛丸速度越高,破裂 越严重。为了避免破碎,一般喷丸强化选用硬度为 HRC48~52的铸钢丸,喷丸强度较低时可用铸钢丸。喷丸 强度较高时,严禁使用铸钢丸。
10
(3)玻璃丸 玻璃丸由高质量碱玻璃制成,不含铁杂质硬度相当于 HRC46~50,外观为实心球体。使用中破碎率高,造成使 用成本偏大。所以目前仅限用于对表面粗糙度有特殊要求 的关键结构零件。 此外, 还有陶瓷弹丸、聚合塑料弹丸等
4章:表面淬火和表面形变强化技术

• 受控喷丸对材料表面 形貌与性能的影响: 形貌与性能的影响: 1)对硬度的影响 弹丸强度或动能越大, 弹丸强度或动能越大, 则变形层深度越大; 则变形层深度越大; 弹丸硬度越高, 弹丸硬度越高,喷丸 层深度越深; 层深度越深; 被喷零件的硬度越高, 被喷零件的硬度越高, 则喷丸强化层越浅。 则喷丸强化层越浅。
第五节 高能密束表面淬火技术
• 高能密束(>103W/cm2)离子束、激光束、 高能密束( 离子束、激光束、 电子束( 电子束(108~9W/cm2) • 特点: 特点: • 能量作用集中,能量利用率高,具选择性; 能量作用集中,能量利用率高,具选择性; • 加热速度快,温度梯度大,自冷淬火,晶 加热速度快,温度梯度大,自冷淬火, 粒细化和超细化; 粒细化和超细化; • 非接触加热,无机械力,热应力小; 非接触加热,无机械力,热应力小;
第一节 表面淬火技术的原理和特点
三、表面淬火层的组织与性能 1.组织 1.组织 • 一般可分为淬火区、 一般可分为淬火区、 • 过渡区、 过渡区、 • 及心部组织; 及心部组织; 2.性能 2.性能 • 大于普淬2~5HRC, 大于普淬2 主要是因为晶粒和精细结构的细化, 主要是因为晶粒和精细结构的细化,以及冷却 快等原因。此外, 快等原因。此外,表面压应力有效抑制裂纹 的萌生与扩展过程,因此可提高疲劳强度。 的萌生与扩展过程,因此可提高疲劳强度。
第二节 感应加热淬火技术
一、基本原理 • 高频磁场→感应电流→集肤效应→电流密度 高频磁场→感应电流→集肤效应→ 电阻)→加热→ )→加热 (电阻)→加热→使受热区快速 升温至Ac3,Acm之上。 Ac3,Acm之上 升温至Ac3,Acm之上。 • 感应加热的工艺参数选择: 感应加热的工艺参数选择: 线圈形状与工件形状有关; 线圈形状与工件形状有关; 功率与淬硬深度有关; 功率与淬硬深度有关;
表面处理第四、五讲表面淬火及表面形变强化
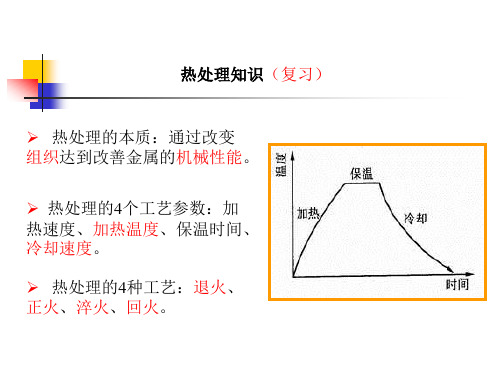
(1) 激光淬火组织 相变硬化区:极细的马氏体; 过渡区:为复杂的多相组织; 基体:原始的基体组织。
图4-7 45钢表面激光淬火 区横截面金相组织
(2) 激光淬硬层的硬度(1)
图4-8 45钢激光淬火区显微 硬度与淬硬层深度的关系
激光淬硬层的硬度(2)
因极快速的加热和冷却,致使激光淬硬层的硬度比常规淬 火高15%~20%。淬硬层的硬度与和钢的淬硬性有关。
超高频冲击淬火 27.12 MHz
(10-30) kW/cm2 (1 ~ 500) ms
(0.05 ~ 0.5) mm 自身冷却
极细针状马氏体 极小
感应加热淬火新技术(2)
2 双频感应加热淬火
对于凹凸不平的工件可采用两种频率交替加热, 较高频率加热时,凸出部位温度较高;较低频率 加热时,低凹部位温度较高。这样可达到均匀硬 化的目的。
2 表面淬火层的性能(1)
(1) 表面硬度:经高频加热淬火的工件其表面硬度比普通 淬火高2~5个HRC。这是由于表面淬火晶粒细化和高的残余 压应力。
表面淬火层的性能(2)
(2) 耐磨性:高频淬火件的耐磨性比普通淬火要高。这是 由于淬硬层中马氏体晶粒极为细小,碳化物高度弥散,淬硬 层硬度和强度都比较高。
1.0 1.75 4.0
* 2.0
空气与燃料 气体体积比
—
9.0 25.0
* —
3 火焰加热淬火方法(1)
为了使工件表面加热均匀,可采取如下方法:
(1) 旋转法:火焰喷嘴 或工件旋转。
适合中小型工件。
火焰加热淬火方法(2) (2) 推进法:工件和火焰喷嘴做相对移动。
适合导轨、大齿轮等工件;
火焰加热淬火方法(3)
4 激光淬火的工艺参数
表面强化技术课件

• 基本过程:将工件放在有足够功率输出 的感应线圈中,在高频交流磁场的作用 下,产生很大的感应电流,并由于集肤 效应而集中分布于工件表面,使表面迅 速加热到钢相变点Ac3或Accm之上,然 后在冷却介质中快速冷却,使工件表面 获得M。
• 2.特点:
• a、加热速度快(感应加热速度可达 103℃ /s,激光加热则可达到105--109℃/s ) 且加热温度要高于整体淬火的温度;
• b、冷却速度快;
• c、表面硬度高(其硬度比普通淬火高 HRC2~4 );
• d、需预备热处理;
• e、适合中高碳钢。
二、感应加热表面淬火
• 1.原理: • 利用感应电流
塑料喷丸退漆是近年来发展起来的新工艺。其原 理为:颗粒状塑料在压缩空气的作用下.通过喷 管高速喷射到工件表面在塑料丸较锋利的棱角切 割和冲撞击打双重作用下使漆层表面发生割裂和 剥离,从而达到高效退漆的目的。
6.喷丸新技术-空气火焰超音速表面喷 砂、喷丸
空气火焰超音速表面喷砂、喷丸:空气火焰超音 速表面预处理技术,是利用气体燃料或液体燃料 与高压电气或高压空气.在超音速喷枪燃烧室内 混合燃烧膨胀产生高温高速焰流.从而带动砂粒 或丸粒以超音速喷向零件处理表面。燃烧焰流速 度达1500m/s以上,粒子速度为300—600m/s,从 而可获得高效优质的表面预处理效果。
• 2.机理: 加工硬化机理。即随变形量的 增加,金属强度硬度升高,塑性韧性下 降。
• 原因:a、位错密度随变形量增加而增加, 从而变形抗力增加;b、随变形量增加, 亚结构细化,亚晶界对位错运动有阻碍; c、随变形量增加,空位密度增加;d、 几何硬化。
二、喷丸强化
▪ 1.原理:喷丸强化又称为受控喷丸强化,
第八章表面改性技术(表面形变强化热处理-化学热处理高能束表面改性技术)精品PPT课件
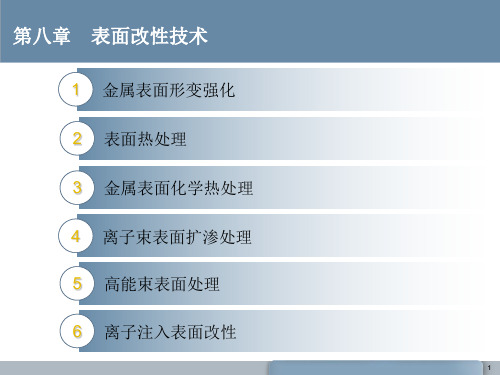
感连
感应加热表面淬火齿轮的截面图
2 中频感应加热表面淬火
• 频率:1500~10000 Hz • 淬透层深度: 2~10 mm • 用途:大中型零件,如大中模数齿轮、直径较大的轴
中频感应加热表面淬火的机车凸轮轴
各种感应器
3 工频感应加热表面淬火
• 频率:50 Hz • 淬透层深度: 10~15 mm以上 • 用途:大型零件,如直径大于300mm的轧辊及轴类零件
第八章 表面改性技术
1 金属表面形变强化 2 表面热处理 3 金属表面化学热处理 4 离子束表面扩渗处理 5 高能束表面处理 6 离子注入表面改性
1
ห้องสมุดไป่ตู้
表面改性技术——定义
定义:表面改性是指采用某种工艺手段 使材料表面获得 与其基体材料的组织结构、性能不同的一种技术。
优点1:材料经过表面改性处理后,既能发挥基体材料的 力学性能,又能使材料表面获得各种特殊性能。
喷丸:工件表面不被破坏, 表面积有所增加。加工时 产生的多余能量就会引会 工件基体的表面强化. 喷砂:工件表面污物被清 除掉,工件表面被微量破坏, 表面积大幅增加,从而增加 了工件与涂/镀层的结合强 度
7
8.2 表面热处理
• 定义:仅对零部件表面加热、冷却,从而改变表层组织和性能 而不改变成分的一种工艺,是最基本、应用最广泛的材料表面 改性技术之一。
• 原理:通过表面层的相变达到强化工件表面的目的。 • 分类:1.感应加热表面淬火
2.火焰加热表面淬火 3.接触电阻加热表面淬火 4.浴炉加热表面淬火 5.电解液加热表面淬火 6.高能束表面淬火 7.其它
8
感应加热的原理
感应加热 表面淬火 示意图
1 高频感应加热表面淬火
表面处理第四、五讲表面淬火及表面形变强化
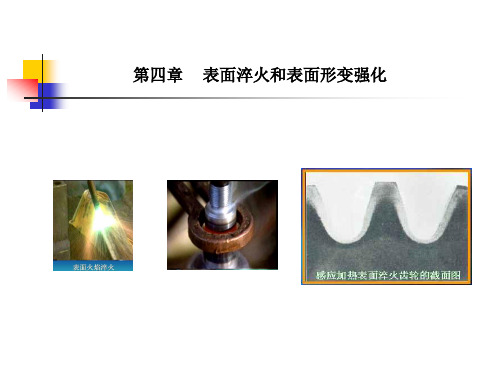
表面淬火层的性能(3) (3) 疲劳强度:高频淬火可显著提高零件的疲劳强度。这 是由于表面产生的压应力可以抑制裂纹的萌生和扩展,使其 缺口敏感性下降。
表 4-2 40Cr 钢不同处理状态下疲劳强度的比较 - 处理状态 疲劳强度 σ 1 N/mm2 200 正火 240 调质 290 调质+表面淬火δ = 5mm 330 调质+表面淬火δ = 9mm
功率密度 加热时间 硬化层深度 工件冷却 淬火层组织 畸 变
感应加热淬火新技术(2) 2 双频感应加热淬火 对于凹凸不平的工件可采用两种频率交替加热, 较高频率加热时,凸出部位温度较高;较低频率 加热时,低凹部位温度较高。这样可达到均匀硬 化的目的。 3 超音频感应加热淬火 采用20kHz ~ 50kHz的频率(超音频波)感应 加热淬火可解决凹凸不平工件表面淬硬层不均匀的 问题。
二、表面淬火与常规淬火的区别 (1) 加热速度越快,奥氏体晶粒越细、硬度越高。
表面淬火与常规淬火的区别 (2)
提高加热速度将使 Ac3 与 Acm线上移,可以防止过热。 快速加热使奥氏体成分不 均匀,易形成贫碳的奥氏体, 合金元素也难实现成分均匀化。
表面淬火与常规淬火的区别 (3)
5.03 10
4
f
mm
感应加热频率越高,淬硬层越浅,但加热速度越快。
感应加热频率与淬硬层的关系
表6-9 感应加热淬火用交流电频率 名 称 高 频 超音频 中 频 工 频 频率范围/Hz (100~500)×103 (20~100)×103 (1.5~10)×103 50 淬硬深度/mm 0.5~2 2~5 2~5 10~15
表面淬火层的组织和硬度分布 硬化层的厚度可用金相法和硬度法测定。
表面淬火和表面形变强化技术资料

曲
轴
喷
曲轴喷丸强化机
丸
强
工艺(设备)种类:
化 机
叶轮式(抛丸式)
压缩空气式(干喷式和湿喷式)
弹丸种类:
铸铁丸、铸钢丸、不锈钢丸、 钢丝切割丸、玻璃丸和陶瓷丸等。
(抛 丸 处 理)
喷砂与喷丸: 目的: 处理后的表面形貌: 形变层深: 喷料动能来源: 喷料种类及尺寸: 自动化程度:
(优点)工艺简单,设备费用低,工件变形小。 (缺点)淬硬层薄,对形状复杂(电阻接触加热法)、尺寸很大(电解液加 热法)的工件不适用。
4.6 几种典型表面淬火工艺的特点比较
感应加热淬火一直是应用最为广泛的表面淬火工艺。 激光淬火应用越来越多。
4.7 表面形变强化技术
一、受控喷丸强化技术
1.受控喷丸技术原理
(2)激光工艺参数 激光功率、光斑直径、扫描速度
淬火层宽度:光斑直径D 淬硬层深度H: H∝P/(Dv) P/(Dv)_比能量(J/cm2)
P-激光功率,v-扫描速度
(3)表面预处理状态 表面组织准备:较细的表面组织
图片
(淬火态最优,细片状珠光体、回火马氏体或奥氏体次之,球状珠光体较差。)
表面“黑化”处理:磷化法、氧化法、喷刷涂料法
二、激光表面熔凝技术原理
定义:
采用激光束将基材表面加热到熔化温度以上,当激光束移开后由于基材 内部导热冷却而使熔化层表面快速冷却并凝固结晶的表面处理工艺。
(液相淬火法)
关键:
使材料表面经历了一个快速熔化一凝固过程
组织:
熔凝层(铸态组织) 相变硬化层 热影响区 基材
性能特点(与激光淬火层相比 ):
2.受控喷丸对材料表面形貌 与性能的影响
- 1、下载文档前请自行甄别文档内容的完整性,平台不提供额外的编辑、内容补充、找答案等附加服务。
- 2、"仅部分预览"的文档,不可在线预览部分如存在完整性等问题,可反馈申请退款(可完整预览的文档不适用该条件!)。
- 3、如文档侵犯您的权益,请联系客服反馈,我们会尽快为您处理(人工客服工作时间:9:00-18:30)。
摘要
腐蚀、磨损、断裂是机械零部件的三大失效形式,其中以断裂失效带来的灾难与损失最大,而断裂失效中疲劳失效所占比例最高,民用机器零部件约占40%~50%,而军用和航空飞行的零部件则高达90%。
可见,研究疲劳断裂、探索疲劳断裂机制至关重要,表面形变强化处理是提高机器零部件疲劳寿命最为有效的手段。
关键词:失效,断裂失效,疲劳断裂,表面形变强化
表面形变强化基本原理
表面形变强化基本原理是通过机械手段(滚压、内挤压和喷丸等)在金属表面产生压缩变形,使表面形成形变硬化层。
此形变硬化层的深度可达0.5mm~1.5mm。
硬化层中产生两种变化:一是在组织结构上,亚晶粒极大地细化,位错密度增加,晶格畸变度增大;二是形成了高的宏观残余压应力。
这两种变化使得金属表面的强度硬度得到了很大的提高,疲劳寿命也有了很大的改观。
喷丸强化
1、喷丸表面强化原理
喷丸强化是当前国内外广泛应用的一种表面强化方法,它是将大量的高速运动的弹丸(铸铁丸、钢丸、玻璃丸、硬质合金丸等)喷射到零件表面,犹如无数的小锤反复锤击金属表面,使零件表层和次表层金属发生一定的塑性变形、从而在塑性变形层中产生金属特有的冷作硬化,还产生一层残余压应力。
从而提高工件表面强度、疲劳强度和抗应力腐蚀能力的表面工程技术。
它已被广泛用于弹簧、齿轮、链条、铀、叶片、火车轮等零部件
这个技术的关键是要根据零件的材料和形状特点控制弹丸流的速度和控制零件表面与弹丸流之间的相对运动。
2、喷丸强化用弹丸
喷丸强化最常用的主要有钢丝切丸、铸钢丸、玻璃丸三种。
喷丸强化用的弹丸必须具备以下特征:
a)较高硬度和强度;
b)应考虑弹丸质量、密度及规格大小之间的关系;
c)要求弹丸不破碎,耐磨损,使用寿命长;
(1)钢丝切丸
钢丝切丸是用回火高强度钢丝经切割制成,目前使用最多的是用弹簧钢做成的钢丸,它的最适宜的硬度为HRC=45~50。
它的成本较高,因两端由棱角会划伤工件表面,在欧美工业发达国家已经大量使用预钝化去棱角-磨角钢丝切丸。
预钝化钢丝切丸分为G1、G2、G3三种类型,具有良好的综合机械性能。
一般要求钢丝切丸硬度越高越好,一般应不低于工件硬度。
(2)铸钢丸
铸钢丸是将金属熔化后的钢液,经雾化成丸、烘干、选圆、二次淬火、回火筛分制成。
其硬度可根据回火温度不同,获得不同硬度的铸钢丸,组织为回火屈
氏体或回火马氏体。
铸钢丸不同于钢丝切丸,他会破碎,从而在循环使用时划伤工件,而且铸钢丸硬度越大,抛丸速度越高,破裂越严重。
为了避免破碎,一般喷丸强化选用硬度为HRC48~52的铸钢丸,喷丸强度较低时可用铸钢丸。
喷丸强度较高时,严禁使用铸钢丸。
(3)玻璃丸
玻璃丸由高质量碱玻璃制成,不含铁杂质硬度相当于HRC46~50,外观为实心球体。
使用中破碎率高,造成使用成本偏大。
所以目前仅限用于对表面粗糙度有特殊要求的关键结构零件。
此外,还有陶瓷弹丸、聚合塑料弹丸等。
需要注意的是,强化用的弹丸与清理、成型、校形用的弹丸不同,必须是因球形,切忌有棱角,以免损伤零件表面。
一般来说,黑色金属制件可以用铸铁丸、钢丸和玻璃丸。
有色金属和不锈钢制件则应避免采用铸铁或钢丸进行喷丸强化,因为附着于零件表面的铁粉会导致零件表面的电化学腐蚀。
3喷丸强化用设备
喷丸强化用的设备主要有两种结构形式:气动式与机械离心式。
一、气动式喷丸机
气动式喷丸机以压缩空气驱动弹丸达到高速度后撞击工件的受喷表面。
这种喷丸机工作室内可以安置多个喷嘴,因其方位调整方便,能最大限度地适应受喷零件的几何形状。
而且可通过调节压缩空气的压力来控制喷丸强度,操作灵活,一台喷九机可喷多个零件。
适用于要求喷丸强度低、品种多、批量少、形状复杂、尺寸较小的零部件。
它的缺点是功耗大,生产效率低。
按弹丸运动方式可分为吸入式、重力式、直接加压式三种类型。
a、吸入式喷丸机
压缩空气从喷嘴射出时,在喷嘴内腔导丸口处形成负压,将下部贮丸箱的弹
丸吸入喷嘴内腔,随压缩空气由喷嘴射出,喷向被强化零件表面。
b、重力式喷丸机、
将弹丸提升到一定高度,借助弹丸自重由上至下流入喷嘴,由压缩空气带动,由喷嘴喷向被强化零件。
c、直接加压式喷丸机
弹丸与压缩空气首先在混合室内混合,再通过导丸管共同进入喷嘴,由喷嘴射出,喷向被强化零件。
二、机械离心式抛丸机
机械离心式喷丸机又称叶轮式喷丸机或抛丸机。
工作时,弹丸由高速旋转的叶片和叶轮离心力加速抛出。
弹丸离开叶轮的切向速度为45m/s-75m/s。
这种喷丸机功率小,生产效率高,喷丸质量稳定,但设备制造成本较高。
主要适用于要求喷丸强度高、品种少、批量大、形状简单、尺寸较大的零部件。
离心式抛丸机工作原理与重力式气动喷丸机基本相同,不同之处在于用抛丸器代替了喷嘴。
4喷丸工艺
在实际生产中是通过弹丸(尺寸、硬度、破碎率等)、喷丸强度、表面覆盖率、表面粗糙度这4个参数来检验、控制和评定喷丸强化质量的。
一、喷丸强度
影响喷丸强度的工艺参数主要有:弹丸直径、弹流速度、弹丸流量、喷丸时间等。
弹丸直径越大,速度越快,弹丸与工件碰撞的动量越大,喷丸的强度就越大。
喷丸形成的残余压应力可以达到零件材料抗拉强度的60%,残余压应力层的深度通常可达0.25mm,最大极限值为1mm左右。
喷丸强度需要一定的喷丸时间来保证,经过一定时间,喷丸强度达到饱和后,再延长喷丸时间,强度不再明显增加。
对于喷丸强度,我们可以采用弧高度试片来测量。
如图所示,。
其中:h:试片厚度
a:测量圆周直径
ƒ:弧高度
d:残余应力层的深度
σ:平均残余压应力
二、表面覆盖率
所谓覆盖率是指强化后表面弹坑占据的面积与总强化表面的比值。
喷丸覆盖率的影响因素有:零件材料的硬度、弹丸直径、喷射角度及距离、喷丸时间等。
在规定的喷丸强度条件下,零件的硬度低于或等于标准试片硬度时,覆盖率能达到100%;反之,覆盖率会下降。
在相同的弹丸流量下,喷嘴与工件的距离越长、喷射的角度越小、弹丸直径越小,达到覆盖率要求的时间就越短。
喷丸强化时,应选择大小合适的弹丸、喷射角度及距离,使喷丸强度和覆盖率同时达到要求值。
通常覆盖率要求在100% - 200%,有些零件,如曲轴应用可能要求覆盖率高于200%。
二、表面粗糙度的影响因素
表面粗糙度的影响因素:零件材料的强度和硬度、弹丸直径、喷射角度及速度、零件的原始表面粗糙度。
在其他条件相同的情况下,零件材料的强度和表面硬度值越高,塑性变形越困难,弹坑越浅,表面粗糙度值越小;弹丸的直径越小,速度越慢,弹坑就越浅,表面粗糙度值就变小;喷射的角度大,弹丸速度的法向分量越小,冲击力越小,弹坑越浅,弹丸的切向速度越大,弹丸对表面的研磨作用就越大,表面粗糙度值
就越小;零件的原始表面粗糙度也是影响因素之一,原始表面越粗糙,喷丸后表面粗糙度值降低越小;相反,表面越光滑,喷丸后表面变得粗糙。
当对零件进行高强度的喷丸后,深的弹坑不但加大表面粗糙度值,还会形成较大的应力集中,严重削弱喷丸强化的效果。
喷丸强化工艺适应性较广;工艺简单、操作方便;生产成本低,经济效益好,强化效果明显。
近年来,随着计算机技术发展,带有信息反馈监控的喷丸技术已在实际生产中得到应用,使强化的质量得到了进一步提高。
如喷丸强化在汽车的螺旋弹簧、板簧、扭杆、齿轮、传动元件、轴承、连杆、凸轮轴、曲轴等组件上均有应用。
5喷丸强化的应用
一、喷丸强化提高疲劳寿命
(1)提高表面镀零件的疲劳强度。
(2)对于钢之零件的喷丸,材料硬度、强度越高,喷丸强化对疲劳强度提高得越大。
(3)铝合金及钛合金零件的喷丸强化。
(4)焊接件的喷丸强化。
(5)弹簧的喷丸强化。
(6)齿轮的喷丸强化。
(7)连杆喷丸强化。
二、喷丸强化提高金属材料抗应力疲劳腐蚀
应力腐蚀都是从金属表面开始的,表面呈拉应力状态时,腐蚀进程就会加快;反之,表面压应力就会一直腐蚀的发展。
表面滚压和孔挤压强化。