表面形变强化技术
机械强度研究现状
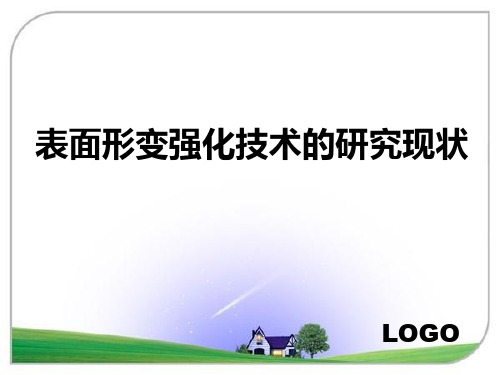
也由于内挤压的特殊工艺性, 要求一定要均匀、缓慢、连续 地挤压孔, 不允许有冲击和暂停现象。
图1
目前主要的滚压加工工具有硬质合金滚轮式滚压工具、滚柱式滚压工具、 硬质合金YZ 型深孔滚压工具、圆锥滚柱深孔滚压工具、滚珠式滚压工具,这 种方法主要应用在大型轴类、套筒类零件内、外旋转表面的加工、滚压螺钉、 螺栓等零件的螺纹以及滚压小模数齿轮和滚花等, 并取得了显著成果, 很好 的提高了经济效益, 如天津大学内燃机研究所唐琦等人通过对370Q 型汽油 机、376Q 型柴油机进行的曲轴负荷分析、强度估算及弯曲疲劳强度实验表 明, 与未滚压曲轴相比教, 经圆角滚压的曲轴疲劳强度增加了92.3% , 安全 系数由1.18 提高到2.28 并大幅度提高曲轴疲劳强度; 还有如柳州南方汽车 缸套厂在对缸套进行滚压试验后发现同一材料、硬度和壁厚的气缸套, 由原 来的直槽改制成为沉割槽, 其破断力在原来基础上提高了35%以上, 技术指 标显著增加, 获得明显效果, 如表1所示。
目前主要应用于以下几种类型: 1. 挤压棒挤压强化。孔壁上涂干膜润滑剂, 施加力的方式为 拉挤或推挤, 适用于大型零部件装配和维修; 2. 衬套挤压强化。孔内装有衬套, 挤压棒用拉挤或推挤方式 通过衬套孔, 适用于各类零部件的装配和修理; 3. 压印模挤压强化。在圆孔或长圆孔周围用压印模挤压出同 心沟槽。适用于大型零部件及蒙皮关键承力部位的孔压印; 4. 旋转挤压强化。使用有一定过盈量, 经向镶有圆柱体的挤 压头, 旋转通过被挤压的孔, 适用于起落架大直径管件和 孔。 由于内挤压特殊的高效而简单的强化工艺, 使得内挤压强 化工艺得到了一系列广泛的应用, 并也取得了良好的效果, 一下是几种常见材料挤压的强化效果见表2, 可知孔挤压后 可大幅度提高疲劳极限。
第七章 表面形变强化技术

渗碳钢经喷丸后的残余压应力
• 常用的渗碳钢经喷丸后,表层的残留奥 氏体有相当大的一部分将转变成马氏体, 因相变时体积膨胀而产生压应力,从而 使得表层残余应力场向着更大的压应力 方向变化。
• 在相同喷丸压力下: • 大直径弹丸喷丸后的压应力较低,压应 力层较深; • 小直径弹丸喷丸后表面压应力较高,压 应力层较浅,且压应力值随深度下降很 快。 • 对于表面有凹坑、凸台。划痕等缺陷或 表面脱碳的工件,通常选用较大的弹丸, 以获得较深的压应力层,使表面缺陷造 成的应力集中减小到最低程度。
喷丸产生的残余压应力
• 经喷丸和滚压 后,金属表面产生 的残余压应力的大 小,不但与强化方 法、工艺参数有关, 还与材料的晶体类 型、强度水平以及 材料在单调拉伸时 的硬化率有关。
残余压应力
• 具有高硬化率的面心立方晶体的镍基或铁 基奥氏体热强合金,表面产生的压应力高, 可达材料自身屈服点的2-4倍。
喷丸强度
• 当弧高度f达到饱和值,试片表面达到全覆 盖率时,以此弧高度f定义为喷九强度。 • 喷丸强度的表示方法是0.25C或fc=0.25, 字母或脚码代表试片种类,数字表示弧高 度值(单位为mm)。
(2)表面覆盖率试验
• 喷丸强化后表面弹丸坑占有的面积与总面 积的比值称为表面覆盖率。 • 一般认为,喷丸强化零件要求表面覆盖率 达到表面积的100%即全面覆盖时,才能有 效地改善疲劳性能和抗应力腐蚀性能。
(4)玻璃弹丸
• 近十几年发展起来的新型喷丸材料, 已在国防工业和飞机制造业中获得广泛应 用。 • 脆性较大 。
(5)陶瓷弹丸
• 弹丸硬度很高,但脆性较大。喷丸后表层 可获得较高的残余应力。
(6)聚合塑料弹丸
• 是一种新型的喷丸介质,以聚合碳酸酯为 原料,颗粒硬而耐磨,无粉尘,不污染环 境,可连续使用,成本低,而且即使有棱 边的新丸也不会损伤工件表面。
对于表面形变强化技术的现状分析

摘要:表面强化是近年来国内外广泛研究应用的工艺之一。
常用的金属表面形变强化方法主要有滚压、内挤压和喷丸等工艺,其强化效果显著,成本低廉。
笔者主要概括了表面强化技术的分类、目的和作用,分析了形变强化方法的特点以及目前表面强化主要研究方法的现状和发展趋势。
关键词:表面形变;强化技术;滚压;内挤压;喷丸引言材料表面处理技术简称材料表面技术,是材料科学的一个重要分支,是在不改变基体材料的成分和性能(或虽有改变而不影响其使用)的条件下,通过某些物理手段(包括机械手段)或化学手段来赋予材料表面特殊性能,以满足产品或零件使用需要的技术和工艺。
材料表面技术在工业中的应用,大幅度提高了产品(尤其是金属零件)的性能、质量和寿命,并产生了巨大的经济效益,因而深受各国政府和科技界的重视。
1 表面形变强化原理通过机械手段(滚压、内挤压和喷丸等)在金属表面产生压缩变形,使表面形成形变硬化层(此形变硬化层的深度可达0.5~1.5mm),从而使表面层硬度、强度提高。
2 表面形变强化工艺分类表面形变强化主要有喷(抛)丸、滚压和孔挤压等三种工艺。
2.1喷丸强化工艺喷丸是国内外广泛使用的一种在再结晶温度以下的表面强化方法,可显著提高抗弯曲疲劳、抗腐蚀疲劳、抗应力腐蚀疲劳、抗微动磨损、耐蚀点(孔蚀)能力,它具有操作简单、耗能少、效率高、适应面广等优点,是金属材料表面改性的有效方法。
2.1.1喷丸强化的发展状况1908年,美国制造出激冷钢丸,金属弹丸的出现不仅使喷砂工艺获得迅速发展,而且导致了金属表面喷丸强化技术的产生。
1929年,在美国由Zimmerli等人首先将喷丸强化技术应用于弹簧的表面强化,取得了良好的效果[1]。
20世纪40年代,人们就发现了喷丸处理可在金属材料表面上产生一种压缩应力层,可以起到强化金属材料、阻止裂纹在受压区扩展的作用。
到了20世纪60年代,该工艺逐步应用于机械零件的强化处理上。
20世纪70年代以来,该工艺已广泛应用于汽车工业,并获得了较大的经济技术效益,如机车用变速器齿轮、发动机及其他齿轮均采用了喷丸强化工艺,大幅度提高了抗疲劳强度。
表面形变强化
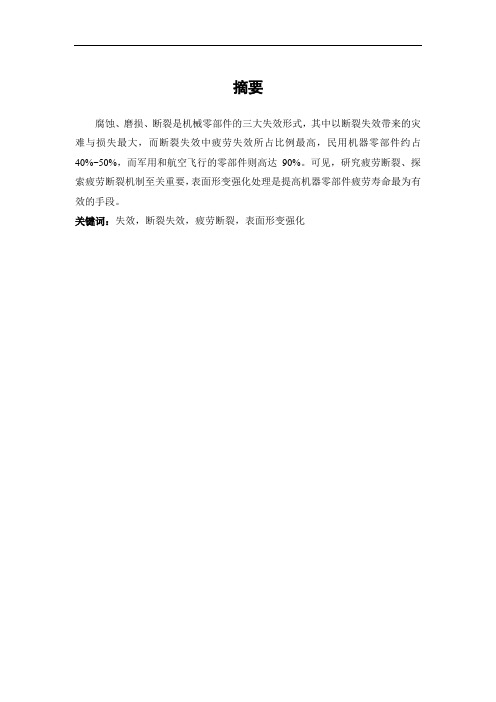
摘要腐蚀、磨损、断裂是机械零部件的三大失效形式,其中以断裂失效带来的灾难与损失最大,而断裂失效中疲劳失效所占比例最高,民用机器零部件约占40%~50%,而军用和航空飞行的零部件则高达90%。
可见,研究疲劳断裂、探索疲劳断裂机制至关重要,表面形变强化处理是提高机器零部件疲劳寿命最为有效的手段。
关键词:失效,断裂失效,疲劳断裂,表面形变强化表面形变强化基本原理表面形变强化基本原理是通过机械手段(滚压、内挤压和喷丸等)在金属表面产生压缩变形,使表面形成形变硬化层。
此形变硬化层的深度可达0.5mm~1.5mm。
硬化层中产生两种变化:一是在组织结构上,亚晶粒极大地细化,位错密度增加,晶格畸变度增大;二是形成了高的宏观残余压应力。
这两种变化使得金属表面的强度硬度得到了很大的提高,疲劳寿命也有了很大的改观。
喷丸强化1、喷丸表面强化原理喷丸强化是当前国内外广泛应用的一种表面强化方法,它是将大量的高速运动的弹丸(铸铁丸、钢丸、玻璃丸、硬质合金丸等)喷射到零件表面,犹如无数的小锤反复锤击金属表面,使零件表层和次表层金属发生一定的塑性变形、从而在塑性变形层中产生金属特有的冷作硬化,还产生一层残余压应力。
从而提高工件表面强度、疲劳强度和抗应力腐蚀能力的表面工程技术。
它已被广泛用于弹簧、齿轮、链条、铀、叶片、火车轮等零部件这个技术的关键是要根据零件的材料和形状特点控制弹丸流的速度和控制零件表面与弹丸流之间的相对运动。
2、喷丸强化用弹丸喷丸强化最常用的主要有钢丝切丸、铸钢丸、玻璃丸三种。
喷丸强化用的弹丸必须具备以下特征:a)较高硬度和强度;b)应考虑弹丸质量、密度及规格大小之间的关系;c)要求弹丸不破碎,耐磨损,使用寿命长;(1)钢丝切丸钢丝切丸是用回火高强度钢丝经切割制成,目前使用最多的是用弹簧钢做成的钢丸,它的最适宜的硬度为HRC=45~50。
它的成本较高,因两端由棱角会划伤工件表面,在欧美工业发达国家已经大量使用预钝化去棱角-磨角钢丝切丸。
材料表面强化技术及应用(毕业设计)

前言作为古老又新颖的学科,表面强化技术为致力于改善材料表面化学性质、组织机构、应力状态的性质,在人们生活中被广泛应用。
通过掺杂、扩散、离子注入、化学沉积、电镀以及电子束等技术改变材料表面性质的研究,使得我们能得到更多表面性质优良的金属,使金属得到叫高的抗腐蚀、抗耐磨性,使工业生产设备及产品使用范围更广[1]。
这样,我们能得到更好的表面性质金属及非金属,节约了人类资源,保护和改善了我们的生活环境。
材料表面强化技术已经成为了现在制造业最伟大的创造。
追溯至春秋晚期,我国已应用铜器热镀锡和鎏金技术,从工业革命开始到最近50年,材料表面强化技术得到飞速发展。
本文吸取现代先进技术的优点,对表面技术的应用进行总结,取其精华,去其糟粕,进行综合陈述及比较。
虽然创新很少,但对现有技术的归纳比较在一定程度上更好的促进了表面技术的发展和研究。
本论文重点研究现有的表面强化技术以及这些技术的应用,意在归纳总结,学习传承。
使得我们能更好的学习和了解这些先进的表面技术,为我们以后的研发和应用做好铺垫。
表面强化技术是表面工程的一个分支,是工程科学技术中一个涉及学科广泛、活力很强、成果突出并与生产实践紧密结合的领域,它渗透到航空航天、信息技术、新材料技术以及先进制造技术等前沿技术的各个方面。
从高科技产品到人们日常生活都离不开材料表面强化技术。
离子束、激光束、电子束、微波及超高真空技术的开发,引起了表面工程技术研究和应用的热潮,并成为了世界最关键的技术之一[2]。
本文对材料表面强化技术及应用的研究进行了探讨。
1 表面强化技术概述1.1表面强化技术概述表面工程是一个既古老又新颖的学科,人们使用表面工程技术已有悠久的历史。
追溯到几千年前,我国早在春秋战国时期就已经开始应用钢的淬火、铜器热镀锡、鎏金及油漆等古老技术[3]。
但是,表面工程的迅速发展还是从19世纪工业革命开始,20世纪80年代成为世界上10大关键技术,进入20世纪90年代发展势头出现工程研究的热潮,几乎涉及了工业的各个领域,表面工程技术仍是将是主导21世纪的关键技术之一。
4章:表面淬火和表面形变强化技术

• 受控喷丸对材料表面 形貌与性能的影响: 形貌与性能的影响: 1)对硬度的影响 弹丸强度或动能越大, 弹丸强度或动能越大, 则变形层深度越大; 则变形层深度越大; 弹丸硬度越高, 弹丸硬度越高,喷丸 层深度越深; 层深度越深; 被喷零件的硬度越高, 被喷零件的硬度越高, 则喷丸强化层越浅。 则喷丸强化层越浅。
第五节 高能密束表面淬火技术
• 高能密束(>103W/cm2)离子束、激光束、 高能密束( 离子束、激光束、 电子束( 电子束(108~9W/cm2) • 特点: 特点: • 能量作用集中,能量利用率高,具选择性; 能量作用集中,能量利用率高,具选择性; • 加热速度快,温度梯度大,自冷淬火,晶 加热速度快,温度梯度大,自冷淬火, 粒细化和超细化; 粒细化和超细化; • 非接触加热,无机械力,热应力小; 非接触加热,无机械力,热应力小;
第一节 表面淬火技术的原理和特点
三、表面淬火层的组织与性能 1.组织 1.组织 • 一般可分为淬火区、 一般可分为淬火区、 • 过渡区、 过渡区、 • 及心部组织; 及心部组织; 2.性能 2.性能 • 大于普淬2~5HRC, 大于普淬2 主要是因为晶粒和精细结构的细化, 主要是因为晶粒和精细结构的细化,以及冷却 快等原因。此外, 快等原因。此外,表面压应力有效抑制裂纹 的萌生与扩展过程,因此可提高疲劳强度。 的萌生与扩展过程,因此可提高疲劳强度。
第二节 感应加热淬火技术
一、基本原理 • 高频磁场→感应电流→集肤效应→电流密度 高频磁场→感应电流→集肤效应→ 电阻)→加热→ )→加热 (电阻)→加热→使受热区快速 升温至Ac3,Acm之上。 Ac3,Acm之上 升温至Ac3,Acm之上。 • 感应加热的工艺参数选择: 感应加热的工艺参数选择: 线圈形状与工件形状有关; 线圈形状与工件形状有关; 功率与淬硬深度有关; 功率与淬硬深度有关;
表面处理第四、五讲表面淬火及表面形变强化
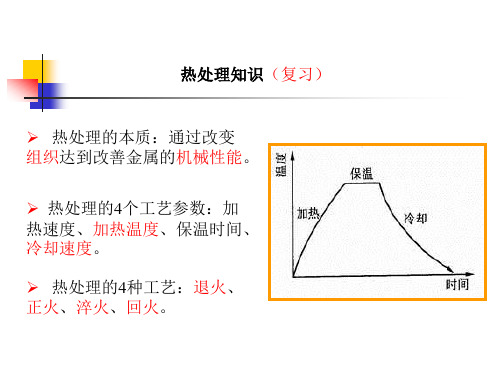
(1) 激光淬火组织 相变硬化区:极细的马氏体; 过渡区:为复杂的多相组织; 基体:原始的基体组织。
图4-7 45钢表面激光淬火 区横截面金相组织
(2) 激光淬硬层的硬度(1)
图4-8 45钢激光淬火区显微 硬度与淬硬层深度的关系
激光淬硬层的硬度(2)
因极快速的加热和冷却,致使激光淬硬层的硬度比常规淬 火高15%~20%。淬硬层的硬度与和钢的淬硬性有关。
超高频冲击淬火 27.12 MHz
(10-30) kW/cm2 (1 ~ 500) ms
(0.05 ~ 0.5) mm 自身冷却
极细针状马氏体 极小
感应加热淬火新技术(2)
2 双频感应加热淬火
对于凹凸不平的工件可采用两种频率交替加热, 较高频率加热时,凸出部位温度较高;较低频率 加热时,低凹部位温度较高。这样可达到均匀硬 化的目的。
2 表面淬火层的性能(1)
(1) 表面硬度:经高频加热淬火的工件其表面硬度比普通 淬火高2~5个HRC。这是由于表面淬火晶粒细化和高的残余 压应力。
表面淬火层的性能(2)
(2) 耐磨性:高频淬火件的耐磨性比普通淬火要高。这是 由于淬硬层中马氏体晶粒极为细小,碳化物高度弥散,淬硬 层硬度和强度都比较高。
1.0 1.75 4.0
* 2.0
空气与燃料 气体体积比
—
9.0 25.0
* —
3 火焰加热淬火方法(1)
为了使工件表面加热均匀,可采取如下方法:
(1) 旋转法:火焰喷嘴 或工件旋转。
适合中小型工件。
火焰加热淬火方法(2) (2) 推进法:工件和火焰喷嘴做相对移动。
适合导轨、大齿轮等工件;
火焰加热淬火方法(3)
4 激光淬火的工艺参数
表面强化技术课件

• 基本过程:将工件放在有足够功率输出 的感应线圈中,在高频交流磁场的作用 下,产生很大的感应电流,并由于集肤 效应而集中分布于工件表面,使表面迅 速加热到钢相变点Ac3或Accm之上,然 后在冷却介质中快速冷却,使工件表面 获得M。
• 2.特点:
• a、加热速度快(感应加热速度可达 103℃ /s,激光加热则可达到105--109℃/s ) 且加热温度要高于整体淬火的温度;
• b、冷却速度快;
• c、表面硬度高(其硬度比普通淬火高 HRC2~4 );
• d、需预备热处理;
• e、适合中高碳钢。
二、感应加热表面淬火
• 1.原理: • 利用感应电流
塑料喷丸退漆是近年来发展起来的新工艺。其原 理为:颗粒状塑料在压缩空气的作用下.通过喷 管高速喷射到工件表面在塑料丸较锋利的棱角切 割和冲撞击打双重作用下使漆层表面发生割裂和 剥离,从而达到高效退漆的目的。
6.喷丸新技术-空气火焰超音速表面喷 砂、喷丸
空气火焰超音速表面喷砂、喷丸:空气火焰超音 速表面预处理技术,是利用气体燃料或液体燃料 与高压电气或高压空气.在超音速喷枪燃烧室内 混合燃烧膨胀产生高温高速焰流.从而带动砂粒 或丸粒以超音速喷向零件处理表面。燃烧焰流速 度达1500m/s以上,粒子速度为300—600m/s,从 而可获得高效优质的表面预处理效果。
• 2.机理: 加工硬化机理。即随变形量的 增加,金属强度硬度升高,塑性韧性下 降。
• 原因:a、位错密度随变形量增加而增加, 从而变形抗力增加;b、随变形量增加, 亚结构细化,亚晶界对位错运动有阻碍; c、随变形量增加,空位密度增加;d、 几何硬化。
二、喷丸强化
▪ 1.原理:喷丸强化又称为受控喷丸强化,
表面形变强化
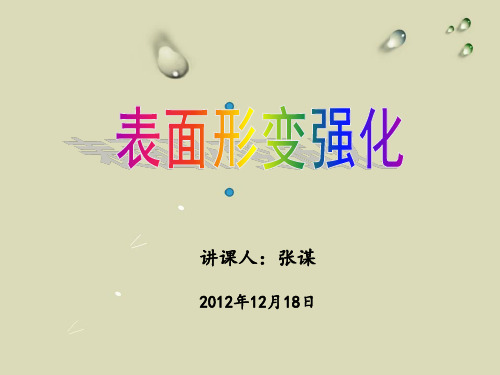
• 3.1 滚压和孔挤压强化用设备 滚压和孔挤压强化用设备是利用现有冷加工设备如车、 钻床或镗床,再配备用作滚压和孔挤压强化工艺必须的装 置。 (1)滚压强化用装置 在滚压过程中,主要运动是轴的回转运动,辅助运动 是滚子沿轴的回转中心进行转动。适用于圆周类零件的强 化。
(2)孔挤压强化用装置
压印模挤压强化装置 村套挤压强化装置
当弧高度f达到饱和值,试片表面达到全覆盖率时, 以此弧高度f定义为喷丸强度。 喷丸强度的表示方法是0.25C或fc=0.25,字母或脚码 代表试片种类,数字表示弧高度值(单位为mm)。
(2)表面覆盖率 所谓覆盖率是指强化后表面弹痕占据的面积与总强化 表面的比值。要求大于100%。喷丸覆盖率的影响因素:零 件材料的硬度、弹丸直径、喷射角度及距离、喷丸时间等。
挤压棒挤压强化装置
旋压挤压强化装置
四、机械镀
• 2. 喷丸强化
2.1 2.2 2.3 2.4 喷丸强化用弹丸 喷丸强化用设备 喷丸工艺 喷丸强化的应用
• 3. 表面滚压和孔挤压强化 • 4. 机械镀
一、基本原理
1.1 概述 腐蚀、磨损、断裂是机械零部件的三大失效形式,其 中以断裂失效带来的灾难与损失最大,而断裂失效中疲劳 失效所占比例最高,民用机器零部件约占40%~50%,而军 用和航空飞行的零部件则高达90%。 可见,研究疲劳断裂、探索疲劳断裂机制至关重要, 表面形变强化处理是提高机器零部件疲劳寿命最为有效的 手段。
第七章-表面形变强化
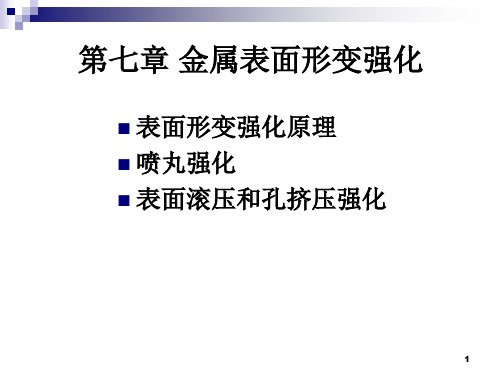
喷丸前后晶粒、亚晶粒位错组态、晶界分布示意图
4
表面残余应力
在表面强化过程中,表面塑性变形带来的表面尺寸变 化引起表面残余应力。下图是滚压处理后的残余应力分布。
5
1)强化后残余应力的分布规律
表面为残余压应力,心部为残余拉应力,最表面层由 于应力松驰,其残余应力稍有降低,故曲线上有“抬头” 现象。
6
3
金属的塑形变形是通过位错运动实现的,在塑性变形过程中, 由于位错间相互作用,使位错密度增加。下图中(a)为喷丸 前组织,晶界与亚晶界比较清晰,晶粒与亚晶粒比较大;(b) 为初始喷丸时,随变形量增加,位错互相作用使位错密度不断 增加,原亚晶界逐步模糊不清、消失;(c)为随喷丸覆盖增 加,弹丸反复冲击金属表面,使一些位错重新排列形成新的亚 晶界。随喷丸时间延长,塑性变形继续进行,位错密度进一步 增加,使晶界逐步消失又组成新的晶界,使晶粒破碎、细化。
21
1. 滚压和孔挤压强化用设备
滚压和孔挤压强化用设备是利用现有冷加工设备如车、 钻床或镗床,再配备用作滚压和孔挤压强化工艺必须的装 置。 (1)滚压强化用装置
在滚压过程中,主要运动是轴的回转运动,辅助运动是 滚子沿轴的回转中心进行转动。适用于圆周类零件的强化。
22
23
(2)孔挤压强化用装置
村套挤压强化装置 压印模挤压强化装置
铸钢丸不同于钢丝切丸,它会破碎,从而在循环使用 时划伤工件,而且铸钢丸硬度越大,抛丸速度越高,破裂 越严重。为了避免破碎,一般喷丸强化选用硬度为 HRC48~52的铸钢丸,喷丸强度较低时可用铸钢丸。喷丸 强度较高时,严禁使用铸钢丸。
10
(3)玻璃丸 玻璃丸由高质量碱玻璃制成,不含铁杂质硬度相当于 HRC46~50,外观为实心球体。使用中破碎率高,造成使 用成本偏大。所以目前仅限用于对表面粗糙度有特殊要求 的关键结构零件。 此外, 还有陶瓷弹丸、聚合塑料弹丸等
- 1、下载文档前请自行甄别文档内容的完整性,平台不提供额外的编辑、内容补充、找答案等附加服务。
- 2、"仅部分预览"的文档,不可在线预览部分如存在完整性等问题,可反馈申请退款(可完整预览的文档不适用该条件!)。
- 3、如文档侵犯您的权益,请联系客服反馈,我们会尽快为您处理(人工客服工作时间:9:00-18:30)。
奥赫弗尔特理论
• 奥赫弗尔特认为,喷丸的残余应力的产生 取决于两个方面的机制: • 一方面由于大量弹丸压人产生的切应力造 成了表面塑性延伸; • 另一方面,由于弹丸的冲击产生的表面法 向力引起了赫芝压应力与亚表面应力的结 合。 • 在大多数材料中这两种机制并存。
喷丸产生的残余压应力
• 经喷丸和滚压 后,金属表面产生 的残余压应力的大 小,不但与强化方 法、工艺参数有关, 还与材料的晶体类 型、强度水平以及 材料在单调拉伸时 的硬化率有关。
• 这种表面形貌和表层组织结构产生的变化,有效 地提高了金属表面强度、耐应力腐蚀性能和疲劳 强度。
二、表面形变强化的主要方法及应用
• (一)表面形变强化的 主要方法 • 1.滚压 • 目前,滚压强化用的滚 轮、滚压力大小等尚无 标准。 • 对于圆角、沟槽等可通 过滚压获得表层形变强 化,并能在表面产生约 5mm深的残余压应力, 其分布如图所示。
残余压应力
• 具有高硬化率的面心立方晶体的镍基或铁 基奥氏体热强合金,表面产生的压应力高, 可达材料自身屈服点的2-4倍。
• 材料的硬化率越高,产生的残余压应力越 大。
表面强化方法
有效地提高了金属表面强度、耐应力腐蚀性能和疲劳强度。
• 表面强化方法还可消除切削加工留下的刀痕; • 表面形变强化手段还可能使表面粗糙度略有增 加,但却使切削加工的尖锐刀痕圆滑,因此可减 轻由切削加工留下的尖锐刀痕的不利影响。
喷丸强度
• 当弧高度f达到饱和值,试片表面达到全覆 盖率时,以此弧高度f定义为喷九强度。 • 喷丸强度的表示方法是0.25C或fc=0.25, 字母或脚码代表试片种类,数字表示弧高 度值(单位为mm)。
(2)表面覆盖率试验
• 喷丸强化后表面弹丸坑占有的面积与总面 积的比值称为表面覆盖率。 • 一般认为,喷丸强化零件要求表面覆盖率 达到表面积的100%即全面覆盖时,才能有 效地改善疲劳性能和抗应力腐蚀性能。
• 注意:强化用的弹丸与清理、成型、校形 用的弹丸不同,必须是圆球形,不能有棱 角毛刺,否则会损伤零件表面。 • 一般来说,黑色金属制件可以用铸铁丸、 铸钢丸、钢丝切割丸、玻璃丸和陶瓷丸。
• 有色金属如铝合金、镁合金、钛合金和不 锈钢制件则需采用不锈钢丸、玻璃丸和陶 瓷丸。
2.喷丸强化用的设备
• 喷丸采用的专用设备,按驱动弹丸的方式 可分为: • 机械离心式喷丸机和气动式喷丸机两大类。 • 喷丸机又有干喷和湿喷之分。 • 于喷式工作条件差,湿喷式是将弹丸混合 在液态中成悬浮状,然后喷丸,因此工作 条件有所改善。
(1)机械离心式喷丸机
• 机械离心式喷丸机又称叶轮式喷丸机或抛丸机。 • 工作时,弹丸由高速旋转的叶片和叶轮离心力加 速抛出。 • 弹丸离开叶轮的切向速度为45m/s-75m/s。 这种喷丸机功率小,生产效率高,喷丸质量稳定, 但设备制造成本较高。 • 主要适用于要求喷丸强度高、品种少批量大、形 状简单尺寸较大的零部件。
表面形变强化是提高金属材料疲劳强度的重要工艺措施之一
• 一、表面形变强化原理
• 基本原理是通过机械手段(滚压、内挤压 和喷丸等)在金属表面产生压缩变形,使表面 形成形变硬化层,此形变硬化层的深度可达 0.5mm~1.5mm。
在形变硬化层中产生两种变化:
• 一是在组织结构上,亚晶粒极大地细化, 位错密度增加,晶格畸变度增大; • 二是形成了高的宏观残余压应力。
2.内挤压
• 内孔挤压是使孔的内表面获得形变强化的 工艺措施,效果明显
3.喷丸
• 利用高速弹丸强烈冲击零部件表面,使之 产生形变硬化层并引进残余压应力。 • 喷丸强化已广泛用于弹簧、齿轮、链条、 轴、叶片、火车轮等零部件; • 可显著提高抗弯曲疲劳、抗腐蚀疲劳、抗 应力腐蚀疲劳。抗微动磨损、耐点蚀(孔 蚀)能力。
• 弹簧钢丝(或不锈钢丝)切制成段制成。
• 钢弹丸的组织最好为回火马氏体或贝氏体。使用寿命比铸 铁弹丸高 20倍左右。
(4)玻璃弹丸
• 近十几年发展起来的新型喷丸材料, 已在国防工业和飞机制造业中获得广泛应 用。 • 脆性较大 。
(5)陶瓷弹丸
• 弹丸硬度很高,但脆性较大。喷丸后表层 可获得较高的残余应力。
(6)聚合塑料弹丸
• 是一种新型的喷丸介质,以聚合碳酸酯为 原料,颗粒硬而耐磨,无粉尘,不污染环 境,可连续使用,成本低,而且即使有棱 边的新丸也不会损伤工件表面。
• 常用于消除酚醛或金属零件毛刺和耀眼光 泽。
(7)液态喷丸介质
• 包括二氧化硅颗粒和氧化铝颗粒等。 • 喷丸时用水混合二氧化硅颗粒,利用压 缩空气喷射。
3.喷丸强化工艺参数的确定
• 合适的喷丸强化工艺参数要通过: • 喷丸强度试验和表面覆盖率试验来确定。 • 喷对试片进行单 面喷丸时,初期的 弧高度变化速率快, 随后变化趋缓,当 表面的弹丸坑占据 整个表面(即全覆 盖率)之后,弧高 度无明显变化,这 时的弧高度达到了 饱和值。
(2)气动式喷丸机
• 气动式喷丸机以压缩空气驱动弹丸达到高速度后撞 击工件的受喷表面。 • 这种喷丸机工作室内可以安置多个喷嘴,因其方位 调整方便,能最大限度地适应受喷零件的几何形状。 • 而且可通过调节压缩空气的压力来控制喷丸强度, 操作灵活,一台喷九机可喷多个零件。
• 适用于要求喷丸强度低、品种多、批量少、形状复 杂、尺寸较小的零部件。它的缺点是功耗大,生产 效率低。
(二)喷丸表面形变强化工艺及应用
• 1.喷丸材料 • (1)铸铁弹丸:冷硬铸铁弹丸是最早使 用的金属弹丸。
• 铸铁弹丸易于破碎,损耗较大,要及时分离排除破碎 弹丸,否则会影响零部件的喷丸强化质量。目前这种 弹丸已很少使用。
• • (2)铸钢弹丸:铸钢弹丸的品质与碳含 量有很大关系。
(3)钢丝切割弹丸
• 气动式喷丸机根据弹丸进人喷嘴的方式又 可分为: • 吸人式、重力式和直接加压式三种。 • 吸入式喷丸机结构简单,多使用密度较小 的玻璃弹丸或小尺寸金属弹丸,适用于工 件尺寸较小、数量较少、弹丸大小经常变 化的场合,如实验室等。 • 重力式喷丸机结构比吸人式复杂,适用于 密度和直径较大的金属弹丸。