设备表面及内部缺陷检测
特种设备安全质量检测方法

THANK YOU
感谢各位观看
高性能传感器技术是指利用高精度、高灵敏度的传感器, 实现特种设备的实时监测和数据采集。通过高性能传感器 技术,可以获取设备的各种参数和运行状态,为设备的故 障诊断和性能评估提供准确的数据支持。
高性能传感器技术包括光纤传感器、MEMS传感器等多种 类型,可以根据不同设备的特性和需求,选择合适的传感 器类型。
远程监控与预警系统
远程监控与预警系统是指利用物联网、云计算等技术,实现特种设备的远程监控 和预警。通过实时监测设备的运行状态和参数,及时发现异常情况,并发出预警 信息,有效预防设备故障和事故的发生。
远程监控与预警系统可以实现多设备、多区域的集中监控和预警,提高设备的管 理效率和安全性。
高性能传感器技术
起重机械安全监控系统
起重机械是特种设备中的一种,广泛应用于工业生产和物流领域 。
起重机械安全监控系统是通过安装在起重机械上的传感器和监测 系统,实时监测起重机械的运行状态和参数变化,及时发现异常 情况并采取相应措施的一种检测方法。
监控系统包括起重量监控、起升高度监控、运行轨迹监控等,这 些监控系统能够全面、准确地检测出起重机械的故障和异常情况 ,提高起重机械运行的安全性和可特种设备表面形成磁痕,检测其表面和近表面缺陷。
详细描述
磁粉检测通过在设备表面施加磁场,使其磁化,再撒上磁粉,通过观察磁痕来判断是否存在缺陷。该 方法适用于检测铁磁性材料的设备,如钢铁等,对于表面和近表面缺陷具有较高的检测灵敏度。
涡流检测
总结词
利用电磁感应原理在特种设备中产生涡流,通过分析涡流的变化来检测其表面和近表面 缺陷。
特种设备安全质量检测方法
汇报人:可编辑 2023-12-30
目录
无损探伤方案

无损探伤方案无损探伤是一种非破坏性检测方法,通过使用物理学的原理和科学的仪器设备来检测物体的内部或表面缺陷、杂质、裂纹等。
它广泛应用于航空、航天、核能、军工、建筑、交通等领域。
本文将介绍无损探伤方案的几种常见方法。
一、磁粉探伤法磁粉探伤法是一种适用于铁、钢等金属表面、近表面缺陷的无损探伤方法。
其原理是在被检测物体表面均匀涂有铁磁性粉末,利用外加磁场引导粉末在裂纹、缺陷处留下磁纹,从而发现该处的缺陷。
磁粉探伤法灵敏度高、速度快、成本低,但只适用于铁、钢等铁磁性材料。
二、涡流探伤法涡流探伤法是一种适用于金属、导体等导电材料表面或近表面缺陷的无损探伤方法。
其原理是将交流电源通入探测器,电流在待检测金属或导体中产生涡流,从而形成磁场,利用磁场对探测器产生的信号进行检测,可以发现缺陷。
涡流探伤法灵敏度高、速度快、适用于各种导电材料。
三、超声波探伤法超声波探伤法是一种适用于大多数材料内部缺陷的无损探伤方法。
其原理是利用超声波在材料内部的传播和反射来检测材料内部缺陷。
可以通过探头的不同位置、不同方向进行检测,对材料内部的缺陷、尺寸、定位等都可以进行准确的检测。
超声波探伤法灵敏度高、适用范围广,但在检测厚度较大、表面不平整、材料吸音性较强时可能存在一定的局限性。
四、射线探伤法射线探伤法是一种适用于金属、非金属等大多数材料内部缺陷的无损探伤方法。
其原理是利用电磁波的作用直接透射材料,得到材料内部组织、缺陷等信息来实现无损检测。
射线探伤法灵敏度高、适用范围广,但需要射线源,且辐射可能对人体和环境造成危害,需要进行详细的安全措施。
五、热波探伤法热波探伤法是一种利用材料吸收热能散热规律来检测缺陷的无损探伤方法。
其原理是利用探测器对材料表面施加热源,通过测量热能的传播和分布情况来检测材料内部的缺陷。
热波探伤法适用范围广,可以检测小到几毫米的缺陷,但需要加热、冷却,操作比较繁琐。
综上所述,无损探伤方案是通过选择不同的探测方法和仪器设备,根据被检材料的不同特性来进行无损检测。
探伤检测标准

探伤检测标准探伤检测是指利用各种物理方法和设备对材料或构件进行内部和表面缺陷的检测和评定。
探伤检测标准是对探伤检测过程中所需遵循的规范和要求的总称,它的制定和实施对于保障产品质量、确保安全生产具有重要意义。
本文将就探伤检测标准进行详细介绍。
首先,探伤检测标准的制定是为了规范探伤检测的操作流程和技术要求,以确保检测结果的准确性和可靠性。
各种材料和构件在使用过程中都可能存在各种缺陷,如裂纹、气孔、夹杂等,这些缺陷如果不能及时发现和处理,将对产品的使用安全和性能造成严重影响。
因此,制定统一的探伤检测标准,对于提高产品质量和保障安全生产具有重要意义。
其次,探伤检测标准的内容主要包括了检测方法、设备要求、操作规程、人员资质等方面的规定。
在探伤检测过程中,需要根据具体的材料和构件特点选择合适的检测方法,如超声波检测、射线检测、涡流检测等,同时还需要配备相应的检测设备,并且严格按照操作规程进行操作,确保检测结果的准确性。
此外,参与探伤检测的人员也需要具备相应的资质和经验,才能够胜任这一工作。
再次,探伤检测标准的实施需要依靠相关部门和专业机构进行监督和检查。
在实际的探伤检测工作中,需要严格按照标准的要求进行操作,同时相关部门和专业机构也需要对探伤检测工作进行监督和检查,确保检测结果的准确性和可靠性。
只有通过严格的监督和检查,才能够提高探伤检测工作的质量和水平。
最后,探伤检测标准的不断完善和更新也是非常重要的。
随着科学技术的不断发展和进步,探伤检测方法和设备也在不断更新和改进,因此探伤检测标准也需要与时俱进,不断完善和更新,以适应新的技术和设备的应用。
只有不断完善和更新探伤检测标准,才能够更好地适应现代生产的需要,提高探伤检测工作的质量和效率。
总之,探伤检测标准的制定和实施对于保障产品质量、确保安全生产具有非常重要的意义。
只有严格按照标准的要求进行操作,才能够提高探伤检测工作的质量和水平,确保产品的使用安全和性能。
设备外观检验标准完整版

设备外观检验标准 HEN system office room 【HEN16H-HENS2AHENS8Q8-HENH1688】单位名称宁波甬灵精密机械有限有限公司文件编号YLWI/PB-08-02-02-02文件类别三级文件版次A00文件名称设备外观验收标准页次 1 OF 2批准:审核:编制:生效日期:外观缺陷检验表检验内容外观(参考)缺陷样本表面不可有掉漆、气泡、流痕等现象;表面油漆不可有刮痕现象(A级面目光停留5秒钟,B级面目光停留2秒钟,不会有明显缺陷之感)。
各焊接处牢固可靠、焊接匀称美观,无严重的焊积瘤、未熔合、裂纹的现象外观A/B级面的气割表面无明显锯齿状切口、高低不平,歪斜的现象。
C 级面不可有刺手现象。
外观A、B级面,在配打或返修后遗留下的多余孔或槽口等是否修补美观。
设备上各铸件无破裂现象。
焊疤凹凸不平,不可接受。
A级面有明显锯齿状气割切口,不可接收。
因加工错误而重新钻孔,原孔未修补,影响美观;NG!轴座破裂,不可接受。
批准:审核:编制:生效日期:外观缺陷检验表检验内容外观(参考)样本图面无注明保留锐角的各部件,锐角是否倒钝;设备及零、部件的外观A级面无任何锈蚀现象; 外观B级面无明显锈蚀现象;①螺栓与螺母拧紧后,螺栓应露出螺母2个以上的螺距;②沉头螺钉紧固后,钉头应埋入机件内,不得外露;③各螺栓无装配时敲打损伤的痕迹。
一般无精度要求组件的结合面,目视不可有明显不错位现象齿轮的接触面应无碰伤、毛刺现象,(逆转的齿轮,齿的两面均应检查)锐角锋利易伤手,存在安全隐患。
表面锈蚀,不可接收,需去除锈蚀,进行涂防锈油或喷防锈漆的沉头孔钉头紧固后理于机件内可接收,OK!严重错位,不可接收;毛刺,不可接受批准:审核:编制: 生效日期:外观缺陷检验表检验内容外观(参考)样本油箱在盛装油脂前,是否清洁干净;各润滑运动部位是否清洁无任何杂质。
注油孔的封盖(螺帽)无丢失现象产品表面不可乱涂乱画;电机、减速箱等配件的安装方位需合理,与机体以水平/垂直方向对正,不可歪斜。
缺陷检测方法

缺陷检测方法缺陷检测是产品质量控制中至关重要的一环。
在制造过程中,可能存在各种不同类型的缺陷,例如裂痕、气泡、变形等。
缺陷检测的目的是尽早发现这些问题,避免产品在后续的使用中出现安全隐患或影响产品的寿命。
本文将介绍缺陷检测的几种方法及其流程。
一、目视检查法目视检查法是最简单、最常用的缺陷检测方法,它通常在生产流程的最后一步进行。
操作人员使用肉眼观察产品外观是否有明显的缺陷,例如裂纹、凹陷等等。
这种方法的优点是操作简单、成本低,缺点是主观性强,对于微小缺陷的检测效果较差。
1、准备工作目视检查前需要准备好检查产品、检查工具以及检查环境等,确保检查环境光线充足、产品摆放在平稳的位置上、检查工具清洁无污渍。
必须确保操作人员能够观察到产品表面的所有区域。
2、检查步骤目视检查通常按照产品表面形状的复杂程度分为两个阶段。
第一阶段,操作人员需用裸眼自上而下仔细检查产品表面,观察是否有肉眼可见的缺陷;第二阶段,操作人员使用放大镜或显微镜放大视野,进一步检查产品表面,以便发现微小缺陷。
二、放射性检测法放射性检测法是利用放射性同位素的特性,结合探测仪器对材料进行检测的一种方法。
这种方法最初用于工业无损检测中,后来被广泛应用于材料表面和材料内部的缺陷检测。
1、准备工作放射性检测前需要准备同位素源、探测仪器以及防护衣等。
操作人员需要接受相关培训,掌握危险程度和操作安全规范。
2、检测步骤首先将同位素源置于被检测材料一侧,辐射穿透样品并被探测仪测量。
通过测量系数的变化确定样品内部的缺陷有多少,缺陷的大小和位置在显示器上得以反映认证。
三、超声波检测法超声波检测法是利用超声波在物质中的传播和反射能力,对材料进行非破坏性缺陷检测的方法。
该方法常用于金属、塑料、陶瓷等材料的缺陷检测。
1、准备工作超声波检测前需要准备超声波探头、探测仪器以及工作站等设备。
操作人员需要接受相关培训,确保操作安全规范以及qualify or authorize the operation.2、操作步骤操作人员在材料表面施加超声波并通过探测仪器对其进行接收。
机械设备检测方法
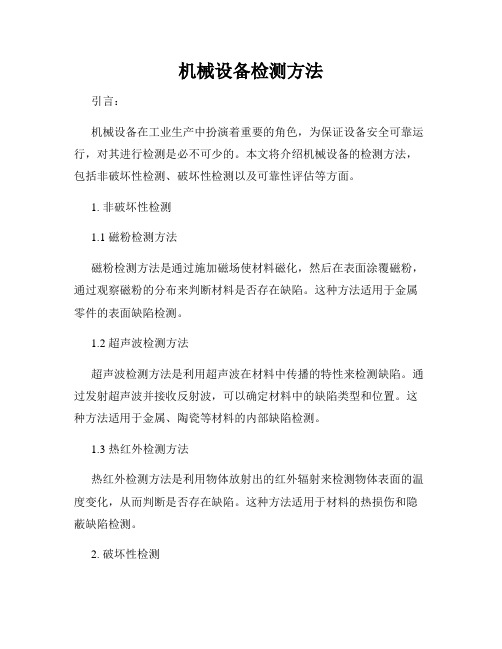
机械设备检测方法引言:机械设备在工业生产中扮演着重要的角色,为保证设备安全可靠运行,对其进行检测是必不可少的。
本文将介绍机械设备的检测方法,包括非破坏性检测、破坏性检测以及可靠性评估等方面。
1. 非破坏性检测1.1 磁粉检测方法磁粉检测方法是通过施加磁场使材料磁化,然后在表面涂覆磁粉,通过观察磁粉的分布来判断材料是否存在缺陷。
这种方法适用于金属零件的表面缺陷检测。
1.2 超声波检测方法超声波检测方法是利用超声波在材料中传播的特性来检测缺陷。
通过发射超声波并接收反射波,可以确定材料中的缺陷类型和位置。
这种方法适用于金属、陶瓷等材料的内部缺陷检测。
1.3 热红外检测方法热红外检测方法是利用物体放射出的红外辐射来检测物体表面的温度变化,从而判断是否存在缺陷。
这种方法适用于材料的热损伤和隐蔽缺陷检测。
2. 破坏性检测2.1 金相显微镜检测方法金相显微镜检测方法是通过对材料进行切割和抛光处理,然后在显微镜下观察材料的组织结构。
通过分析组织结构可以确定材料是否存在缺陷、夹杂物等问题。
2.2 拉伸试验方法拉伸试验方法是对材料进行拉力加载,通过测量材料在拉力下的变形和断裂情况,可以得到材料的力学性能参数,例如强度、延伸率等。
2.3 压力试验方法压力试验方法是对材料进行压力加载,通过测量材料在压力下的变形和破坏情况,可以确定材料的耐压性能。
3. 可靠性评估3.1 故障模式和效应分析(FMEA)故障模式和效应分析是一种系统性的方法,用于识别设备可能存在的故障模式,并评估这些故障对系统功能和可靠性的影响。
3.2 可靠性增长分析(RGA)可靠性增长分析是根据设备运行数据,通过数学和统计分析的方法,对设备的可靠性进行评估和优化,包括MTBF(平均无故障时间)的计算和故障率曲线的绘制等。
3.3 故障树分析(FTA)故障树分析是通过构建逻辑树的方法,分析系统故障的发生概率和结果,以及确定故障发生的原因和关键环节,从而制定相应的修复和预防策略。
特种设备无损检测相关知识
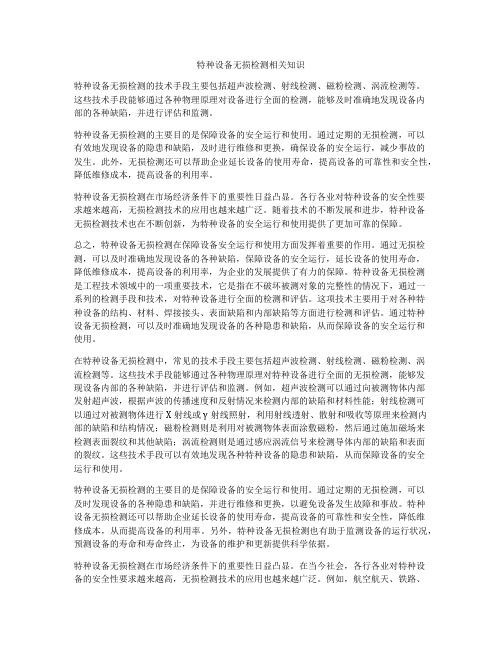
特种设备无损检测相关知识特种设备无损检测的技术手段主要包括超声波检测、射线检测、磁粉检测、涡流检测等。
这些技术手段能够通过各种物理原理对设备进行全面的检测,能够及时准确地发现设备内部的各种缺陷,并进行评估和监测。
特种设备无损检测的主要目的是保障设备的安全运行和使用。
通过定期的无损检测,可以有效地发现设备的隐患和缺陷,及时进行维修和更换,确保设备的安全运行,减少事故的发生。
此外,无损检测还可以帮助企业延长设备的使用寿命,提高设备的可靠性和安全性,降低维修成本,提高设备的利用率。
特种设备无损检测在市场经济条件下的重要性日益凸显。
各行各业对特种设备的安全性要求越来越高,无损检测技术的应用也越来越广泛。
随着技术的不断发展和进步,特种设备无损检测技术也在不断创新,为特种设备的安全运行和使用提供了更加可靠的保障。
总之,特种设备无损检测在保障设备安全运行和使用方面发挥着重要的作用。
通过无损检测,可以及时准确地发现设备的各种缺陷,保障设备的安全运行,延长设备的使用寿命,降低维修成本,提高设备的利用率,为企业的发展提供了有力的保障。
特种设备无损检测是工程技术领域中的一项重要技术,它是指在不破坏被测对象的完整性的情况下,通过一系列的检测手段和技术,对特种设备进行全面的检测和评估。
这项技术主要用于对各种特种设备的结构、材料、焊接接头、表面缺陷和内部缺陷等方面进行检测和评估。
通过特种设备无损检测,可以及时准确地发现设备的各种隐患和缺陷,从而保障设备的安全运行和使用。
在特种设备无损检测中,常见的技术手段主要包括超声波检测、射线检测、磁粉检测、涡流检测等。
这些技术手段能够通过各种物理原理对特种设备进行全面的无损检测,能够发现设备内部的各种缺陷,并进行评估和监测。
例如,超声波检测可以通过向被测物体内部发射超声波,根据声波的传播速度和反射情况来检测内部的缺陷和材料性能;射线检测可以通过对被测物体进行X射线或γ射线照射,利用射线透射、散射和吸收等原理来检测内部的缺陷和结构情况;磁粉检测则是利用对被测物体表面涂敷磁粉,然后通过施加磁场来检测表面裂纹和其他缺陷;涡流检测则是通过感应涡流信号来检测导体内部的缺陷和表面的裂纹。
无损检测方法及设备性能检验流程与标准
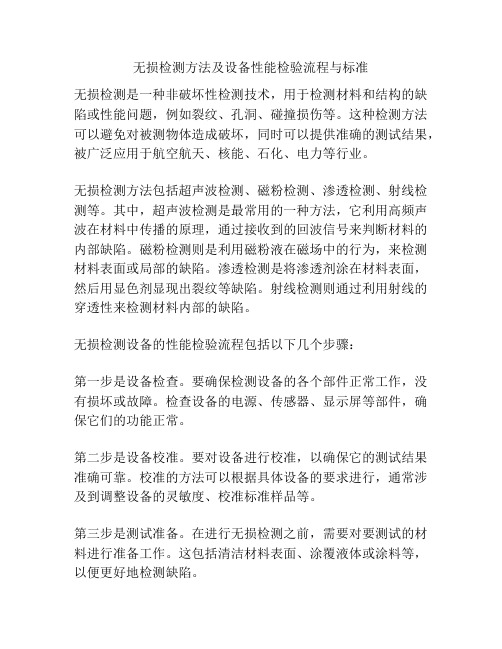
无损检测方法及设备性能检验流程与标准无损检测是一种非破坏性检测技术,用于检测材料和结构的缺陷或性能问题,例如裂纹、孔洞、碰撞损伤等。
这种检测方法可以避免对被测物体造成破坏,同时可以提供准确的测试结果,被广泛应用于航空航天、核能、石化、电力等行业。
无损检测方法包括超声波检测、磁粉检测、渗透检测、射线检测等。
其中,超声波检测是最常用的一种方法,它利用高频声波在材料中传播的原理,通过接收到的回波信号来判断材料的内部缺陷。
磁粉检测则是利用磁粉液在磁场中的行为,来检测材料表面或局部的缺陷。
渗透检测是将渗透剂涂在材料表面,然后用显色剂显现出裂纹等缺陷。
射线检测则通过利用射线的穿透性来检测材料内部的缺陷。
无损检测设备的性能检验流程包括以下几个步骤:第一步是设备检查。
要确保检测设备的各个部件正常工作,没有损坏或故障。
检查设备的电源、传感器、显示屏等部件,确保它们的功能正常。
第二步是设备校准。
要对设备进行校准,以确保它的测试结果准确可靠。
校准的方法可以根据具体设备的要求进行,通常涉及到调整设备的灵敏度、校准标准样品等。
第三步是测试准备。
在进行无损检测之前,需要对要测试的材料进行准备工作。
这包括清洁材料表面、涂覆液体或涂料等,以便更好地检测缺陷。
第四步是测试操作。
根据不同的无损检测方法,进行相应的测试操作。
例如,对于超声波检测,需要设置传感器的位置和方向,并对回波信号进行分析解读。
第五步是测试评估。
根据测试结果,对材料进行评估,判断是否存在缺陷或性能问题。
评估的标准可以根据行业标准或相关规范来确定。
无损检测的相关标准是确保无损检测结果可靠的重要依据。
例如,超声波检测的标准是GB/T 11144-2008《金属材料超声波检测技术通则》、磁粉检测的标准是GB/T 9445-2017《用磁粉检测钢铁零件缺陷的一般规定》等。
这些标准规定了测试方法、设备性能要求、测试结果的评估等内容,确保了无损检测的准确性和可靠性。
总之,无损检测是一种非破坏性的检测方法,可以用于检测材料和结构的缺陷或性能问题。
设备检测(VT、TM、MT、PT、硬度)

设备检测(VT、TM、MT、PT、硬度)作者:赣C者(qq:416978041)一、VT(目视检测)1、VT常常用于目视检查焊缝,焊缝本身有工艺评定标准,都是可以通过目测和直接测量尺寸来做初步检验,发现咬边等不合格的外观缺陷,就要先打磨或者修整,之后才做其他深入的仪器检测。
例如焊接件表面和铸件表面较多VT做的比较多,而锻件就很少,并且其检查标准是基本相符的。
2、检测步骤:用刷子除去内部的结晶(杂质)及锈迹。
仔细的观察设备内部,不能放过任何一个角落,光线不足时应使用白光手电筒照射,查看是否有裂缝,有穿孔的情况,有明显腐蚀的痕迹要用显眼的记号笔标出,并拍照记录,以便下一步做更详细的检测;换热器的管板是重点检查的区域,比较明显的穿孔,裂缝通过VT能够看出,特别是每根列管和管板之间的焊缝一般出现问题的概率大。
3、注意事项:检查过程中要仔细,避免漏掉每一个角落。
二、TM(厚度测定)1、仪器:超声波测厚仪(TT140,北京时代)测厚仪标定:按开机键(OFF/ON)后,在测厚仪的顶部的圆形标定铁块上涂上耦合剂,按下ZERO按钮,将测定探头按压在标定铁块上,显示屏上数字显示为4.0mm,标定结束。
2、注意事项:1)、若被测设备为不锈钢,则要用相应的不锈钢标定块标定;2)、耦合剂涂抹的原则是使探头与被测物之间紧密接触,不能留有空气,因为超声波不能在空气中传导,因此耦合剂的涂抹量自己把握。
3、测定方法:用砂轮机除去测定点的涂漆,使之平滑。
在测定点上涂抹耦合剂,将测厚仪(已标定)的探头按压在被测点上,若屏幕上的数值跳动,有必要稍微移动探头并将探头紧贴设备,直到屏幕左下角显“”标志并数值稳定,屏幕上显示的值即为测定值。
发现数值的问题较大应重复多次测量求均值。
4、测定点的确定:厚度的测定并不是随便在设备上找几个点测定,而是找有代表性或者是容易发生腐蚀的地方进行测定,***换热器设备一般测定的点为筒体的两端,上下封头,进出物料的法兰,都是测定这些位置的同一截面的四个方向,示意图如下:***二冷冷凝器检查规格图:测定的部位为图中的①②③④的东南西北四个方向,a、c、d上下东西(或者南北)四个方向。
混凝土表观及内部缺陷检测报告

混凝土表观及内部缺陷检测报告一、混凝土表观及内部缺陷检测报告的背景咱们在建筑工程里呀,混凝土可是个超级重要的角色呢。
就像人体的骨骼一样,支撑着整个建筑的结构。
但是呢,混凝土也会有出问题的时候,可能表面看着有点奇怪,或者内部藏着一些缺陷。
所以呀,就需要我们来做这个检测啦。
这检测就像是给混凝土做个全面的身体检查,看看它到底有没有生病,健不健康。
二、检测的目标那咱们做这个检测是为啥呢?就是要确保混凝土的质量呗。
要是混凝土有问题,那整个建筑可能就会有危险。
咱们可不能让住在房子里或者在大楼里工作的人处于危险之中呀。
而且呢,对于工程的质量保证来说,这也是非常关键的一环。
三、检测的方法对于混凝土表观的检测,我们可以用肉眼直接观察。
看看混凝土的表面有没有裂缝啦,有没有不平整的地方啦。
就像我们看一个人的脸,有没有痘痘或者伤疤一样。
要是发现了小裂缝,那可不能小看它,这可能就是个大问题的小信号呢。
而对于内部缺陷的检测,就比较复杂啦。
我们可以用超声波检测法。
这个方法就像是给混凝土内部做个B超一样。
超声波在混凝土里面传播,如果遇到缺陷,就会有不一样的反应。
还有钻芯法,就是从混凝土里面钻取一个芯样出来,直接看看它的内部结构。
不过这个方法有点破坏性,就像给混凝土做个小手术一样,不到万不得已咱们也不想用。
四、检测结果经过一系列的检测呀,我们发现了一些情况。
在表观上,有部分混凝土表面存在细微的裂缝,虽然这些裂缝看起来很小,但是也不能掉以轻心。
在内部检测方面呢,通过超声波检测,发现有一些区域的混凝土内部结构不太均匀,存在一些小的空洞。
这就像是蛋糕里面有一些小气泡没搅拌均匀一样。
五、结果分析那这些结果意味着什么呢?表面的裂缝可能是因为混凝土在浇筑的时候,水分蒸发太快了,就像我们皮肤缺水会干裂一样。
而内部的空洞可能是在搅拌混凝土的时候,没有搅拌充分,导致有些地方的材料没有混合好。
这些问题都可能会影响混凝土的强度和耐久性。
六、应对措施那我们得想办法解决呀。
铸件的表面和内部质量检测方法

铸件的表面和内部质量检测方法(图)铸件的检测主要包括尺寸检查、外观和表面的目视检查、化学成分分析和力学性能试验,对于要求比较重要或铸造工艺上容易产生问题的铸件,还需要进行无损检测工作,可用于球墨铸铁件质量检测的无损检测技术包括液体渗透检测、磁粉检测、涡流检测、射线检测、超声检测及振动检测等。
1 铸件表面及近表面缺陷的检测1.1液体渗透检测液体渗透检测用来检查铸件表面上的各种开口缺陷,如表面裂纹、表面针孔等肉眼难以发现的缺陷。
常用的渗透检测是着色检测,它是将具有高渗透能力的有色(一般为红色)液体(渗透剂)浸湿或喷洒在铸件表面上,渗透剂渗入到开口缺陷里面,快速擦去表面渗透液层,再将易干的显示剂(也叫显像剂)喷洒到铸件表面上,待将残留在开口缺陷中的渗透剂吸出来后,显示剂就被染色,从而可以反映出缺陷的形状、大小和分布情况。
需要指出的是,渗透检测的精确度随被检材料表面粗糙度增加而降低,即表面越光检测效果越好,磨床磨光的表面检测精确度最高,甚至可以检测出晶间裂纹。
除着色检测外,荧光渗透检测也是常用的液体渗透检测方法,它需要配置紫外光灯进行照射观察,检测灵敏度比着色检测高。
1.2涡流检测涡流检测适用于检查表面以下一般不大于6~7mm深的缺陷。
涡流检测分放置式线圈法和穿过式线圈法2种。
:当试件被放在通有交变电流的线圈附近时,进入试件的交变磁场可在试件中感生出方向与激励磁场相垂直的、呈涡流状流动的电流(涡流),涡流会产生一与激励磁场方向相反的磁场,使线圈中的原磁场有部分减少,从而引起线圈阻抗的变化。
如果铸件表面存在缺陷,则涡流的电特征会发生畸变,从而检测出缺陷的存在, 涡流检测的主要缺点是不能直观显示探测出的缺陷大小和形状,一般只能确定出缺陷所在表面位置和深度,另外它对工件表面上小的开口缺陷的检出灵敏度不如渗透检测。
1.3磁粉检测磁粉检测适合于检测表面缺陷及表面以下数毫米深的缺陷,它需要直流(或交流)磁化设备和磁粉(或磁悬浮液)才能进行检测操作。
铸件的表面和内部质量检测方法

铸件的表面和内部质量检测方法(图)铸件的检测主要包括尺寸检查、外观和表面的目视检查、化学成分分析和力学性能试验,对于要求比较重要或铸造工艺上容易产生问题的铸件,还需要进行无损检测工作,可用于球墨铸铁件质量检测的无损检测技术包括液体渗透检测、磁粉检测、涡流检测、射线检测、超声检测及振动检测等。
1 铸件表面及近表面缺陷的检测1.1液体渗透检测液体渗透检测用来检查铸件表面上的各种开口缺陷,如表面裂纹、表面针孔等肉眼难以发现的缺陷。
常用的渗透检测是着色检测,它是将具有高渗透能力的有色(一般为红色)液体(渗透剂)浸湿或喷洒在铸件表面上,渗透剂渗入到开口缺陷里面,快速擦去表面渗透液层,再将易干的显示剂(也叫显像剂)喷洒到铸件表面上,待将残留在开口缺陷中的渗透剂吸出来后,显示剂就被染色,从而可以反映出缺陷的形状、大小和分布情况。
需要指出的是,渗透检测的精确度随被检材料表面粗糙度增加而降低,即表面越光检测效果越好,磨床磨光的表面检测精确度最高,甚至可以检测出晶间裂纹。
除着色检测外,荧光渗透检测也是常用的液体渗透检测方法,它需要配置紫外光灯进行照射观察,检测灵敏度比着色检测高。
1.2涡流检测涡流检测适用于检查表面以下一般不大于6~7mm深的缺陷。
涡流检测分放置式线圈法和穿过式线圈法2种。
:当试件被放在通有交变电流的线圈附近时,进入试件的交变磁场可在试件中感生出方向与激励磁场相垂直的、呈涡流状流动的电流(涡流),涡流会产生一与激励磁场方向相反的磁场,使线圈中的原磁场有部分减少,从而引起线圈阻抗的变化。
如果铸件表面存在缺陷,则涡流的电特征会发生畸变,从而检测出缺陷的存在, 涡流检测的主要缺点是不能直观显示探测出的缺陷大小和形状,一般只能确定出缺陷所在表面位置和深度,另外它对工件表面上小的开口缺陷的检出灵敏度不如渗透检测。
1.3磁粉检测磁粉检测适合于检测表面缺陷及表面以下数毫米深的缺陷,它需要直流(或交流)磁化设备和磁粉(或磁悬浮液)才能进行检测操作。
超声波检测混凝土表观及内部缺陷操作规程
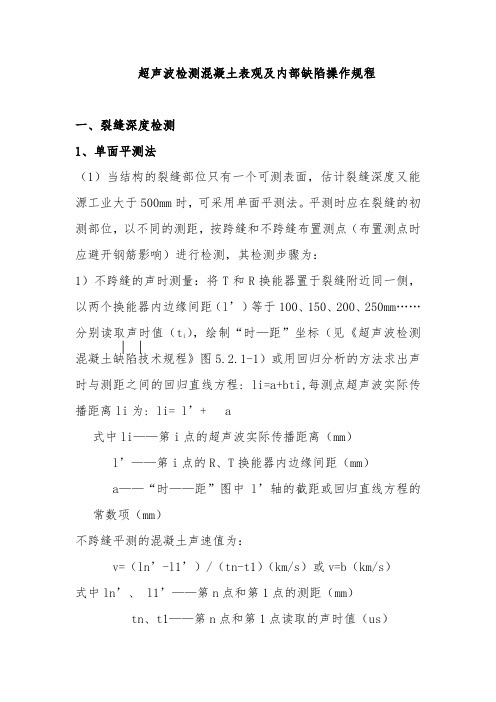
超声波检测混凝土表观及内部缺陷操作规程一、裂缝深度检测1、单面平测法(1)当结构的裂缝部位只有一个可测表面,估计裂缝深度又能源工业大于500mm时,可采用单面平测法。
平测时应在裂缝的初测部位,以不同的测距,按跨缝和不跨缝布置测点(布置测点时应避开钢筋影响)进行检测,其检测步骤为:1)不跨缝的声时测量:将T和R换能器置于裂缝附近同一侧,以两个换能器内边缘间距(l’)等于100、150、200、250mm……分别读取声时值(t i),绘制“时—距”坐标(见《超声波检测混凝土缺陷技术规程》图5.2.1-1)或用回归分析的方法求出声时与测距之间的回归直线方程: li=a+bti,每测点超声波实际传播距离li为: li= l’+ a式中li——第i点的超声波实际传播距离(mm)l’——第i点的R、T换能器内边缘间距(mm)a——“时——距”图中l’轴的截距或回归直线方程的常数项(mm)不跨缝平测的混凝土声速值为:v=(ln’-l1’)/(tn-t1)(km/s)或v=b(km/s)式中ln’、 l1’——第n点和第1点的测距(mm)tn、t1——第n点和第1点读取的声时值(us)b——回归系数2)跨缝的声时测量:(见《超声波检测混凝土缺陷技术规程》CECS21:2000图5.2.1-2)所示,将T、R换能器分别置于以裂缝对称的两侧,l’取100、150、250mm……分别读取声时值t i0,同时观察首波相位的变化。
(2)平测法检测,裂缝深度应按下式计算详见《超声波检测混凝土缺陷技术规程》CECS21:2000式5.2.2-1和5.2.2-2。
(3)裂缝深度的确定方法如下:1)跨缝测量中,当在某测距发现首波反相时,可用该测距及两个相邻测距的测量值按《超声波检测混凝土缺陷技术规程》CECS21:2000式5.2.2-1计算h ci值,取此三点h ci的平均值作为该裂缝的深度值(h c)。
2)跨缝测量中如难于发现首波反相,则以不同测距按式5.2.2-1、5.2.2-2计算h ci及其平均值(m hc)。
无损检测报告

无损检测报告
无损检测报告是一种针对材料、零部件、设备等的表面和内部缺陷进行检测分析的报告。
无损检测是采用非破坏性方法进行的,不会影响被检测物品的使用性能和完整性。
无损检测的目的是寻找和评估材料或设备中的缺陷、裂纹、疲劳、漏洞等问题,以确定是否符合设计要求和使用安全性。
无损检测方法包括超声波检测、射线检测、磁粉检测、涡流检测等。
无损检测报告通常包括以下内容:
1. 被检测物品的基本信息,如名称、规格、编号等。
2. 检测方法和仪器的信息,包括使用的无损检测方法和设备型号。
3. 检测过程的描述,包括检测位置、检测时间、操作人员等。
4. 检测结果的总结,包括缺陷类型、尺寸、位置、分布等。
5. 检测结果的评价和建议,根据检测结果对被检测物品的使用安全性和健康状况进行评估,并提出相应的建议和措施。
无损检测报告对于保证材料和设备的使用安全性至关重要,可以帮助企业和个人了解材料或设备的质量状况,及时采取相应的修复、更换或维护措施,以减少事故风险和经济损失。
设备检查的方法有哪些

设备检查的方法有哪些设备检查方法是指用来检查设备是否正常工作、是否存在故障或缺陷的一种技术手段。
根据不同的设备类型和检查目的,设备检查方法可以分为多种不同的方法。
下面将介绍几种常见的设备检查方法。
1. 目测检查法:目测检查是最常用的一种设备检查方法,它是通过肉眼观察设备的外观和结构来判断设备是否存在故障或缺陷。
在进行目测检查时,可以注意设备的外观是否完好,是否有锈蚀或损坏的地方,以及设备的连接是否牢固等。
2. 测量检查法:测量检查是一种通过测量设备的某些参数来评估设备工作状态的方法。
常见的测量检查方法包括温度测量、电压测量、压力测量等。
通过测量设备的参数,可以判断设备是否正常工作,是否存在异常情况,并进一步确定设备是否需要维修或更换。
3. 振动检查法:振动检查是一种通过检测设备振动状况来评估设备工作状态的方法。
振动检查可以用来检测设备的轴承、传动系统和转子等部件是否存在故障或磨损。
通过振动检查,可以及早发现设备的故障,并采取相应的维修措施,以防止设备进一步损坏。
4. 声音检查法:声音检查是一种通过听设备发出的声音来评估设备工作状态的方法。
通过倾听设备的声音,可以判断设备是否存在异常噪音或异响,以及设备是否正常运转。
一些故障常常会伴随着特殊的声音,通过声音检查可以及时发现设备的故障,以便及早采取维修措施。
5. 化学检查法:化学检查是一种通过化学分析来评估设备工作状态的方法。
在化学检查中,可以通过对设备的润滑油或冷却液等液体进行化学分析,来判断设备是否存在异常情况或故障。
例如,油液的黏度、酸值或金属颗粒的含量等参数可以反映设备的工作状况。
6. 探伤检查法:探伤检查是一种通过使用超声波或磁粉等技术来检测设备内部缺陷或故障的方法。
在探伤检查中,可以通过扫描设备的表面或内部,来检测设备的材料是否存在裂纹、气孔、缺陷或断裂等问题。
探伤检查常用于金属材料的检测,可以帮助及早发现设备的隐患,以避免设备故障或事故的发生。
设备表面及内部缺陷检测

开放实验室实验讲义(设备表面及内部缺陷检测)实验一 内部缺陷检测-超声波检测(一)、超声波探伤 1.超声波探伤原理超声波探伤是利用人耳无法感觉到的高频声波(>20000Hz)射入被检物并用探头接收信号从而检测出材料内部或表面缺陷的方法。
探伤用超声波频率一般在0.5-25MHz 之间。
超声波波长与频率f 和传播速度c 的关系为:入=c/f (1-1) 在气体和液体中只有纵波,纵波声速c :为:C L =(K/ρ)1/2(1-2) 式中 ρ-密度(kg /m 3);K-体积弹性模量(N /m 2)。
声阻抗Z 为:Z =ρ·C (1-3) 当声波由介质1垂直入射到介质2时,声能反射率只为:Z=(Z 2-Z 1)2/(Z 1+Z 2)2(1-4)式中Z 1与Z 2--介质1与介质2的声阻抗。
声能透射率T 为:式中 αl -纵波入射角;βl 与βs 队-纵波折射角与横波折射角;γL 与γS -纵波反射角与横波反射角;c l1与c l2-两种介质户纵波声速;c s1与c s2-两种介质中横波声速。
若入射波为横波,有ss s sl l l l s s 2211c sin c sin c sin c sin αγββγα==== (1-7) 式中 αs -横波入射角。
第一临界角为使纵波折射角等于90。
时的纵波入射角(αlI ) 有2l 1l l c /c sin i =α (1-8)第二临界角为使横波折射角等于90。
时的纵波入射角(o ,n),有 ;2l 1l lII c /c sin =α (1-9)超声波近场区(Fresuel 区)长度N 为N=D2/4λ (1-10) 式中D-发射体(晶片)直径;λ-波长。
远场区(Franhofer区)声束发散,强度与距离平方成反比。
发射体为圆形时,声束在远场区之半扩散角60(指向角)由下式决定:sin 0=1.22λ/D (1-11) 超声波在介质中传播会发生声强的衰减,、规律为:I=I0e-2αδ (1-12) 式中I。
无损检测技术的标准与规范解读

无损检测技术的标准与规范解读无损检测技术是一种能够在不破坏材料或构件完整性的情况下,对其内部缺陷或表面缺陷进行检测和评估的方法。
它在工业、航空、航天、核能等领域中具有重要的应用价值。
然而,为了保证检测的准确性和可靠性,需要有一系列的标准与规范来规范和指导无损检测技术的实施。
1. 标准与规范的意义标准与规范是无损检测技术实施中必不可少的依据,它们起到统一和规范无损检测操作流程、技术参数、设备使用要求等方面的作用。
标准与规范能够确保不同实施单位在无损检测过程中遵循相同的标准,评估结果的可比性也因此得到了保证。
此外,标准与规范中还包含了对人员培训、设备校准和维护等方面的要求,从而保证了无损检测技术的质量和可靠性。
2. 主要的标准与规范在无损检测技术领域,有许多国内外的标准与规范可供参考与使用。
其中,国际标准组织(ISO)发布的《非破坏性测试-术语和定义》(ISO 5577)和《非破坏性检测-通用要求》(ISO 9712)是应用最广泛的两个标准。
这两个标准确立了无损检测技术的术语和定义,规定了无损检测人员的资质要求,以及无损检测的通用要求等。
此外,还有美国无损检测协会(ASNT)发布的一系列标准和规范,如《无损检测术语和定义》(ASNT SNT-TC-1A)和《无损检测人员资格和认证》(ASNT CP-105)等。
3. 标准与规范的内容标准与规范对无损检测技术的各个方面都有详细的规定。
首先,它们定义了不同检测方法的术语和定义,如超声波检测、射线检测、磁粉检测等。
其次,标准与规范规定了无损检测人员的资质和培训要求,包括培训课程的内容、考核标准和证书颁发条件等。
此外,它们还对无损检测设备的选择、校准和维护提出了明确的要求,确保了检测结果的准确性和可靠性。
4. 标准与规范的应用标准与规范的应用是无损检测技术实施的基础工作。
无损检测实施单位在进行无损检测之前,需要根据具体的标准与规范,制定相应的操作流程和技术参数,确保检测的准确性和可靠性。
机械产品外观检验标准
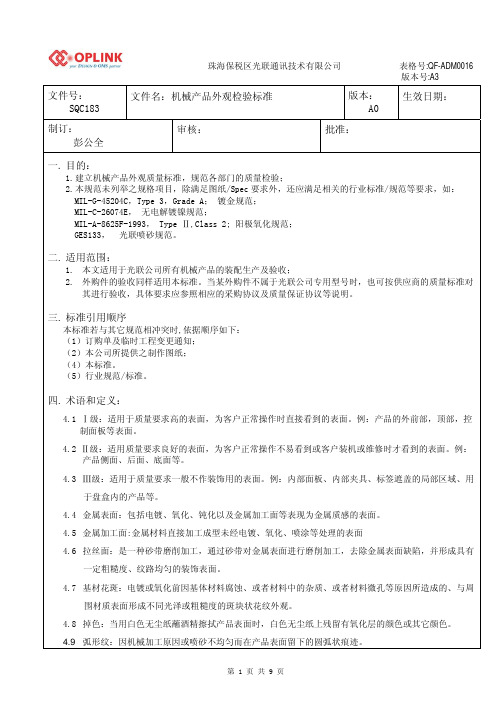
珠海保税区光联通讯技术有限公司表格号:QF-ADM0016版本号:A3文件号:SQC183文件名:机械产品外观检验标准版本:A0生效日期:制订:彭公全审核:批准:一. 目的:1. 建立机械产品外观质量标准,规范各部门的质量检验;2. 本规范未列举之规格项目,除满足图纸/Spec要求外,还应满足相关的行业标准/规范等要求,如:MIL-G-45204C,Type 3,Grade A; 镀金规范;MIL-C-26074E, 无电解镀镍规范;MIL-A-8625F-1993, Type Ⅱ,Class 2; 阳极氧化规范;GES133, 光联喷砂规范。
二. 适用范围:1. 本文适用于光联公司所有机械产品的装配生产及验收;2. 外购件的验收同样适用本标准。
当某外购件不属于光联公司专用型号时,也可按供应商的质量标准对其进行验收,具体要求应参照相应的采购协议及质量保证协议等说明。
三. 标准引用顺序本标准若与其它规范相冲突时,依据顺序如下:(1)订购单及临时工程变更通知;(2)本公司所提供之制作图纸;(4)本标准。
(5)行业规范/标准。
四. 术语和定义:4.1 Ⅰ级:适用于质量要求高的表面,为客户正常操作时直接看到的表面。
例:产品的外前部,顶部,控制面板等表面。
4.2 Ⅱ级:适用质量要求良好的表面,为客户正常操作不易看到或客户装机或维修时才看到的表面。
例:产品侧面、后面、底面等。
4.3 Ⅲ级:适用于质量要求一般不作装饰用的表面。
例:内部面板、内部夹具、标签遮盖的局部区域、用于盘盒内的产品等。
4.4 金属表面:包括电镀、氧化、钝化以及金属加工面等表现为金属质感的表面。
4.5 金属加工面:金属材料直接加工成型未经电镀、氧化、喷涂等处理的表面4.6 拉丝面:是一种砂带磨削加工,通过砂带对金属表面进行磨削加工,去除金属表面缺陷,并形成具有一定粗糙度、纹路均匀的装饰表面。
4.7 基材花斑:电镀或氧化前因基体材料腐蚀、或者材料中的杂质、或者材料微孔等原因所造成的、与周围材质表面形成不同光泽或粗糙度的斑块状花纹外观。
pt探伤操作规程

pt探伤操作规程PT(液体渗透检测)是一种常用的无损检测方法,用于检测材料表面和焊接接头内部的缺陷。
下面是PT探伤操作规程的概述。
一、检测前准备1. 验证设备和试剂:确认PT设备和试剂的有效期,检查设备是否正常工作。
2. 准备工作区域:确保工作区域干净、整洁,并将检测区域隔离。
二、检测准备1. 清洁待检测表面:使用溶剂或清洁剂,将待检测表面清洁干净,确保表面无杂质和油污。
2. 遮盖无需检测区域:使用胶带或其他遮盖材料,将无需检测的区域遮盖起来。
三、试剂处理1. 倒入溶剂罐:将合适的溶剂倒入容器中,用于清洗待检测表面。
2. 倒入吸收剂罐:在吸收剂罐中倒入足够的吸收剂,用于吸收试剂。
四、涂覆试剂1. 涂覆试剂:使用喷涂器或刷子,在待检测表面均匀涂覆试剂,确保涂层均匀且覆盖全面。
2. 等待渗透:根据试剂的要求,等待规定的渗透时间,使试剂渗透入缺陷。
3. 清洗试剂:使用溶剂罐中的溶剂,彻底清洗待检测表面上多余的试剂。
五、应用显像剂1. 喷涂显像剂:使用喷涂器,将显像剂均匀喷洒在已清洗干净的表面上。
2. 等待反应时间:根据显像剂的要求,等待规定的反应时间,使显像剂与试剂反应。
3. 清洗显像剂:使用溶剂罐中的溶剂,彻底清洗表面上多余的显像剂。
六、观察和评估1. 观察缺陷:使用裸眼或适当的光源,观察是否有显现出的缺陷,如裂纹、孔洞等。
2. 评估缺陷:根据缺陷的尺寸、形状、深度和位置,评估其对材料安全性和性能的影响。
七、记录和报告1. 记录结果:将检测结果详细记录,包括检测日期、位置、人员等信息。
2. 编写报告:根据记录的结果,编写检测报告,详细描述检测的缺陷和评估结果。
八、清理和维护1. 清理设备:在检测完成后,清洁设备和试剂罐,并妥善存放。
2. 维护设备:定期检查设备的维护情况,如更换滤芯、校准设备等。
以上是PT探伤操作规程的概述,实际操作中应根据具体情况进行调整和细化。
此规程的目的是保证操作的准确性和可靠性,确保探测到材料中的缺陷,从而保证材料的安全性和可靠性。
结构混凝土表观及内部缺陷检测

跨缝的时声测量
声时值 ti (μ s)
波幅值 dB
声时值 tOi (μ s)
波幅值 dB
裂缝深 度值h (mm)
裂缝的 是否首 深度hc 波反向 (mm)
a=
年
月
日
第
页,共
页
QJ0104d
结构混凝土表观及内部缺陷试验检测记录表
试验室名称: 工程部位/用途 试验依据 样品描述 试验条件
主要仪器设备及编号
记录编号: 委托/任务编号 样品编号 样品名称 试验日期
结构类型 裂缝位置 裂缝类型 裂缝宽度(mm) 最小值 最大值 允许最大值 裂缝长度
不跨缝的时声测量 两换能 器内边 缘距离 l’ (mm) 时声与 测距的 回归方 程l’= a+bti 超声波 实测传 播距离 li (mm) 声速值v (km/s) 单值 平均
- 1、下载文档前请自行甄别文档内容的完整性,平台不提供额外的编辑、内容补充、找答案等附加服务。
- 2、"仅部分预览"的文档,不可在线预览部分如存在完整性等问题,可反馈申请退款(可完整预览的文档不适用该条件!)。
- 3、如文档侵犯您的权益,请联系客服反馈,我们会尽快为您处理(人工客服工作时间:9:00-18:30)。
--页脚-- 开放实验室实验讲义(设备表面及内部缺陷检测)实验一内部缺陷检测-超声波检测(一)、超声波探伤1.超声波探伤原理超声波探伤是利用人耳无法感觉到的高频声波(>20000Hz)射入被检物并用探头接收信号从而检测出材料内部或表面缺陷的方法。
探伤用超声波频率一般在0.5-25MHz之间。
超声波波长与频率f和传播速度c的关系为:入=c/f (1-1) 在气体和液体中只有纵波,纵波声速c:为:C L=(K/ρ)1/2 (1-2)式中ρ-密度(kg/m3);K-体积弹性模量(N/m2)。
声阻抗Z为:Z=ρ·C (1-3) 当声波由介质1垂直入射到介质2时,声能反射率只为:Z=(Z2-Z1)2/(Z1+Z2)2 (1-4) 式中Z1与Z2--介质1与介质2的声阻抗。
声能透射率T为:式中αl-纵波入射角;βl与βs队-纵波折射角与横波折射角;γL与γS-纵波反射角与横波反射角;c l1与c l2-两种介质户纵波声速;c s1与c s2-两种介质中横波声速。
若入射波为横波,有s ssslllls s2211csincsincsinc sinαγββγα====(1-7)式中αs-横波入射角。
第一临界角为使纵波折射角等于90。
时的纵波入射角(αlI) 有2l 1l l c /c sin i =α (1-8)第二临界角为使横波折射角等于90。
时的纵波入射角(o ,n),有 ;2l 1l lII c /c sin =α (1-9)超声波近场区(Fresuel 区)长度N 为N=D 2/4λ (1-10)式中 D-发射体(晶片)直径;λ-波长。
远场区(Franhofer 区)声束发散,强度与距离平方成反比。
发射体为圆形时,声束在远场区之半扩散角60(指向角)由下式决定:sin θ0=1.22λ/D (1-11)超声波在介质中传播会发生声强的衰减,、规律为: I=I 0e-2αδ(1-12)式中 I 。
-超声波初始强度;I-超声波透过厚度为6(cm)的介质时的强度;α-线衰减系数(Np/cm ,1Np/cm =868.6dB/m);用分贝值K p (K H )表示衰减变化或放大率,即:K p =201gP /P oK H =201gH /H 。
(dB) (1-13)式中 P o 或H 。
-声压或波高基准值;P 或H-声压或波高的测量值(或要求值)。
材料厚度等于半波长或其整数倍时,将发生共振,有t=n ·c/2f (1-14) 式中 t-共振厚度;c-声速;f-频率;n-整数。
表1-1为超声波探伤按不同方式分类简表。
A 型脉冲反射法探伤是目前使用的主要方法。
表1-1超声波探伤分类简表2.脉冲反射法探伤过程与探伤条件脉冲反射探伤法按超声波在介质中传播方式分类及用途列于表1-2。
表1-2 脉冲反射法分类越低。
(2).探头晶片尺寸的选用影响晶片尺寸选用的因素列于表1-3 (3).折射角的选用横波探伤用斜探头主要采用35º-70º的折射角。
管材探伤时,探头折射角β的选定应满足下式:表1-3与晶片尺寸有关的因素β<arcsin(1-t2) (1-15)式中 t-管材壁厚; φ-管材外径。
(4).耦合剂的选用耦合剂的选择以保证良好的透声性为准则,应尽量选用其声阻抗与试件声阻抗相近的介、质为耦合剂。
(5).灵敏度的选择与调节探伤灵敏度是指“在规定范围内对底面反射波与同深度平底孔反射波分贝差值为: 2s2lg20G πφλφ= (1-16)式中 L-波长; s-声程;φ-要求发现的平底孔型缺陷的最小直径。
若要求发现横通孔型缺陷,则。
2s2lg 10G πφλφ= (1-17)式中 φ-要求发现的核通孔型缺陷的最小直径。
3.缺陷定位缺陷在工件中h-缺陷在试件中的位置。
斜角探伤法缺陷定位基本公式如下:h =s ·cos β (1-19)P =s ·sin β (1-20) 式中 s-声程;β-折射角;k-缺陷至探测面垂直距离;P-缺陷至入射点水平距离。
斜角探伤,当缺陷位于半跨距以远,则按下述公式定位:h 1=2T 一S 1·cos β (1-21) h 1,5=S 1,5cos β-2T (1-22) h 2=4T-S 2·cos β (1-23)h 2,5=S 2,5cos β-4T (1-24)式中 T-试件厚度;h 1、h 1,5、h 2、h 2,5-分别为0.5跨距至l 跨距内、1跨距外至1.5跨距内、1.5跨距外至- 2跨距内及2跨距外至2.5跨距内缺陷至探测面垂直距离;s 1、s 1,5、s 2、s 2,5-分别为与上述各跨距范围相应之声程;β-折射角。
式(1-28)~式(1-33)适用于平板试件。
4.缺陷方法列于表1-5。
表1-5 超声波探伤缺陷定量方法AVG曲线中标准化距离A为:A=X/N (1-25) 式中 (1-26)式中d-平底孔当量直径;D-探头晶片直径。
JBll52-81规定A试块上实测数据绘制而成。
探头移动法定量,平板试件中缺陷倾斜时,缺陷指示长度l按下式修正:L=l/cosφ下式修正:L=l(r十x)/r (1-29)式中 r-试件内孔半径。
5.超声波探伤方法应用与比较超声波探伤可检测气孔、夹杂、裂纹、缩孔及未焊透等缺陷,用于锻件、轧制件、焊缝、材及铸件等的检验。
最易于检出长度方向与超声波束方向垂直的缺陷。
超声波探伤方法分类比较列于表1-6。
表1-6超声波探伤方法比较三、实验设备及材料1.超声波探伤仪(1台)4.试样: 2块/组。
四、实验内容与步骤12.每组学生对试样进行缺陷检测(1)用超声波检,缺陷大小每个试样,应在不同方位测定。
4.实验中应注意安全操作。
六、实验报告内容1.实验目的;2.简述你了解的检测设备名称及用途;3.讨论超声波检测的实验方法;4.画出缺陷组织示意图,指出其大用范围?(2)钢中内部缺陷类别不同时对缺陷图象及检测灵敏度有何影响?实验二表层缺陷检测实验一、实验目的1.学习和认识材料的表层缺陷检测方法;2.了解和认识磁粉探伤、涡流探伤的原理与过程。
二、实验概述适合于表层缺陷检测的主要方法为磁力探伤、及涡流探伤。
(一)、磁粉探伤1.磁粉探伤原理与过程磁目前应用最广泛的是磁粉法。
被检物在磁场中磁化后,缺陷部位产生漏磁磁场;在被检物表面撒上磁粉,缺陷处有磁粉附着从而显示出缺陷。
缺陷长度方向与磁场方向相垂直是磁粉探伤的最重要条件。
磁场强度H(A/m)与在材料中产生的磁通密度B的关系为;B=μ H(T) (2-1)式中μ-磁导率(H/m)。
在导体周围的磁场强度为:H=0.16A/r(A/m) (2-2)式中A-导体中电流(A);料及铁锈等去掉,以免影响探伤效果。
用干磁粉时要求试件表面干燥。
探伤过程中,如果前次磁化的残留剩磁可能影响磁痕解释,则在图中磁粉探伤不允许有剩磁的零件也必须退磁。
探伤后尚须经奥氏体化热处理的零件可不退滋。
退磁方法与电流种类有关。
直流电:反复换向并逐渐减小磁化电流至交流电:以较小的分挡或连续减少磁化电流至很低的值。
2.磁化方法基本磁化方法列于表2-1。
按照被检工件形状和预计的缺陷选择磁化方对工件分别进行周向磁化和纵向磁化,以免漏检。
可以采用能取得互相垂直磁场的复合磁化方法。
复合磁化只适用于连续法。
采用旋转磁场探伤仪时,工件被旋转磁场磁化,磁化方向随时间变化而旋转,可检测工件各个方向的缺陷。
旋转磁场磁为剩磁法。
表2-1 磁化方法采用交流磁化,则检出近表面缺陷能力差,而检出表面缺陷能力强。
采用直流(或半波整流)可检出近表面缺陷。
3.磁化规范可用灵敏度试片法确定磁化规范(ASTM A275-82)。
A型标准试片使用时,用连续法敷粉,根据显示在选用不同检验方法和磁化方法时,零件被磁化后最终状态的磁性都应保持以下的磁感应强度:连续法为600∽800mT(601000ghT(8000∽10000高斯)。
4.探伤灵敏度磁粉探伤灵敏度是指可发现表面或近表面缺陷的最小尺寸,即绝对灵敏度。
某些磁化方法可达到的灵敏度见表2-2。
表2-2探伤灵敏度磁粉探伤灵敏度取决于磁粉或磁悬液的性质、磁化方法与规范、金属磁特性及缺陷的位置等。
对于际探伤中,可采用示灵敏度试片验证被测工件是否达到要求的探伤灵敏度。
5. 磁粉与磁悬液磁粉粒度应均匀,平均粒度为5-10μ,最大粒度小于5μm,荧光磁粉粒度为2∽5μ。
表2-3所列为几种磁悬液的的成份和配制方法。
表2-4所列为JB741-80《钢制焊接压力容器技术条件》中规定的萤光磁悬液配方。
表2-3磁悬液配置法也可用普通肥皂代替,但均匀与稳定性差表2-4 JB741-80 规定的6.磁痕分析表2-5所列为各种缺陷磁痕磁力探伤适用于铁磁性材料表面或近表面缺陷检测。
可检测裂纹、气孔、夹杂等缺陷。
磁力探伤方法分类比较列于表2-7。
表2-5缺陷磁痕一般特征(二)、涡流探伤1.涡流探伤原理被检物置于检测线圈所产生的交变磁场中感应出涡流,而涡流又在被检物附近产生附加交变磁场。
在被检物缺陷压与位相等)的变化可以捡出缺陷。
检测线圈的特性用阻抗的两个分量-电阻R 与感抗X 表示。
X =27πfL (2-3)式中 f-交变磁场频率(Hz);L-线圈电感(H)。
被检物的物理性质、几何因素、检测线圈的大小与形状及线圈交变磁场频率等对线圈阻抗的影响,可用阻其中,线圈填充系数(v)为试样横截面积与线圈横截面积之比:v =D 2/d 2 (2-4)式中 D-圆柱试样直径;d-线圈有效直径。
圆柱形试样之特征频率为:f g =5066小μr σD 2 (Hz) (2-5)式中 直径,(c 。
无式样时之(空载)电压E 0为:)(10428020V H D fn E -⨯=ππ (2-6)式中 f-线圈激励频率(Hz);D-次级线圈直径(cm);n-次级线圈匝数;H 0-线圈激励磁场强度(Oe)。
归一化的线圈电压(有试样线圈电压除以“空载”电压的感抗分量)虚数部分为: )reat eff L imagr L L E E μνμνωω+-==1(00(2-7) 归一化的线圈电压实数部分为: )ima g eff L r L R R E E μνμω=-=000reat (2-8)归一化阻抗实数部分与虚数部分的复数阻抗平面可同时表示μeff 实数部分离取决于直径变化方,向与电导率变化方向的夹角,夹角大则分离容易。
频率比J /J8大于4时效果较佳。
铁磁性圆柱体,在阻抗平面的上半部分,电导率变化与直径变化效应和相对磁导率效应的分离效果较好。
表面效应由下式表达:频率(Hz);σ-电导率,电阻率的倒数(S /m); μ-磁导率(H /m)。
“标准透入深度”δ为涡流密度下降到表面密度的1/e 倍即36.8%J 。